DOI:
10.1039/D3RA01898A
(Review Article)
RSC Adv., 2023,
13, 15261-15273
Microwave-enhanced hydrogen production: a review
Received
23rd March 2023
, Accepted 29th April 2023
First published on 18th May 2023
Abstract
Currently, the massive use of fossil fuels, which still serve as the dominant global energy, has led to the release of large amounts of greenhouse gases. Providing abundant, clean, and safe renewable energy is one of the major technical challenges for humankind. Nowadays, hydrogen-based energy is widely considered a potentially ideal energy carrier that could provide clean energy in the fields of transportation, heat and power generation, and energy storage systems, almost without any impact on the environment after consumption. However, a smooth energy transition from fossil-fuel-based energy to hydrogen-based energy must overcome a number of key challenges that require scientific, technological, and economic support. To accelerate the hydrogen energy transition, advanced, efficient, and cost-effective methods for producing hydrogen from hydrogen-rich materials need to be developed. Therefore, in this study, a new alternative method based on the use of microwave (MW) heating technology in enhanced hydrogen production pathways from plastic, biomass, low-carbon alcohols, and methane pathways compared with conventional heating methods is discussed. Furthermore, the mechanisms of MW heating, MW-assisted catalysis, and MW plasma are also discussed. MW-assisted technology usually has the advantages of low energy consumption, easy operation, and good safety practices, which make it a promising solution to supporting the future hydrogen society.
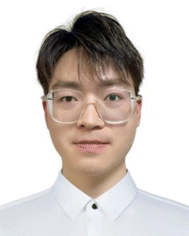 Jun Zhao | Jun Zhao is currently pursuing a PhD degree at the Technical Institute of Physics and Chemistry, Chinese Academy of Sciences in Beijing. His current research focus is on microwave-assisted catalytic reactions, including the upcycling of plastic materials and hydrogen generation from hydrocarbons. |
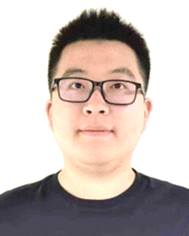 Duanda Wang | Duanda Wang is currently a graduate student at the Technical Institute of Physics and Chemistry, Chinese Academy of Sciences in Beijing. He received his Bachelor of Science degree in Chemistry from Purdue University, US, in 2018 and Master of Science degree in Analytical and Polymer Science from Warwick University, UK, in 2020. His current research focus is on micro–nano materials synthesis and their applications in metal ions separation. |
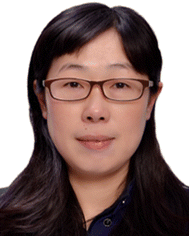 Lei Zhang | Lei Zhang received her Master and PhD degrees from the Northeast Normal University (2005) and the Technical Institute of Physics and Chemistry, Chinese Academy of Sciences in Beijing (2008), respectively. She was a senior engineer at the postdoctoral workstation of Shengli Oilfield Co., Ltd, SINOPEC from 2009 until 2012, after which she joined the Technical Institute of Physics and Chemistry. Her research interests are in colloidal and interfacial chemistry. |
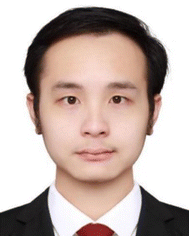 Minyi He | Minyi He graduated with a Bachelor's degree from Central South University (2021). Currently, he is a Master's candidate at the Technical Institute of Physics and Chemistry, Chinese Academy of Sciences in Beijing. His research interests include the microwave-assisted catalytic pyrolysis of waste biomass and microwave-assisted degradation of organic solid waste. |
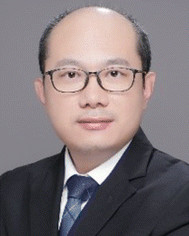 Wangjing Ma | Wangjing Ma received his PhD degree from the Graduate School of Chinese Academy of Sciences in Beijing, China (2007). He was an Assistant and Associated Professor at the Technical Institute of Physics and Chemistry, the Chinese Academy of Sciences from 2007 until now, during which time he also worked at the University of Oxford, UK, as a visiting Professor of Chemistry (2014–2015), and then as a Postdoctoral Research Fellow (2016) at Oxford University. His research interests are microwave-enhanced catalysis in plastic upcycling and heterogeneous catalysis in olefins isomerization. |
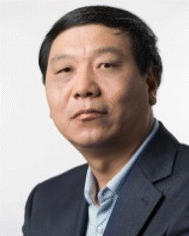 Sui Zhao | Sui Zhao received his B.S. degree from Peking University (1985) and MS degree from the Institute of Photographic Chemistry, Chinese Academy of Sciences (1988). He has served as Professor of Chemistry, Doctoral Advisor, and Director of the Research Group for Enhanced Oil Recovery at the Technical Institute of Physics and Chemistry, Chinese Academy of Sciences (from 1999 to now). His research interests in the latter years are microwave-enhanced catalysis in plastic upcycling and heterogeneous catalysis. |
1. Introduction
Approaching the deadline for carbon neutrality draws attention to the urgent need for clean energies to substitute fossil fuels. These unrenewable energy sources generate greenhouse gas when consumed, which enhances the greenhouse effect, promoting global warming, and intensifying extreme weathers.1–3 Besides the environmental hazards of using fossil fuels, their significance as raw materials in industries, pharmacies, agriculture, etc., makes them too valuable to be depleted as energy sources in the expected future. These facts emphasize the necessity to find alternatives to fossil energy for future sustainable development.
Hydrogen energy is a promising substitution for carbon-based fuels owing to its abundance in nature, harmless emission,4–6 and extremely high energy production per mass content (142 MJ), which is three times that of gasoline (44 MJ).7–13 However, as a gaseous fuel, it has an extremely low mass density, which means a low energy density, whereby it produces a quarter of energy compared to gasoline per volumetric content. On the other hand, hydrogen is not an energy source like those fossil fuels harvested from nature, but is an energy carrier that is produced from consuming other sources.14–16 It can be stored for subsequent uses as energy or in materials for use in fertilizer production, the oil refining industry, food, metal processing, and other fields.17 As the most abundant element in the universe, its multiple access points, including water, minerals, and organic compounds, make hydrogen a highly desired energy source that will be essential for the future society.
While hydrogen has the potential to be an essential alternative to fossil fuels in our society, the currently reported hydrogen production methods mainly involve the classical fossil fuel steam conversion (accounting for over 80%) and natural gas-based conversion (accounting for over 70%).17 The reason for this is that the low reliability of renewable energy sources requires high feasibility energy storage, but hydrogen gas is not suitable for storage in terms of the transportation efficiency, facility safety, and construction costs of hydrogen facilities. This mismatch in generation and consumption hinders the transition to a hydrogen economy.18–20 Therefore, a more flexible perspective of hydrogen production is required, which should not only focus on developing hydrogen production technologies from renewable energy sources but also on discovering a new route to release hydrogen from hydrogen-rich materials that can be synthesized by renewable energy sources, which can help realize the transportation of hydrogen in a non-gaseous form.21
The future hydrogen society will use hydrogen as the major energy carrier instead of gasoline or natural gas, especially for vehicles and factories,14,15 but the most significant challenge in realizing this future is achieving efficient hydrogen storage. The direct increment in hydrogen density requires high-pressure compression at 700 bar (40 g H2 per L) or low-temperature liquefaction at −253 °C (70 g H2 per L) for hydrogen storage and transportation.11,22,23 In principle, there are two hydrogen storage methods that could potentially solve the above problems, physical hydrogen storage and chemical hydrogen storage. Physical hydrogen storage involves adsorbing hydrogen in porous materials, like molecular sieves, MOFs, or carbon materials;24–29 while chemical hydrogen storage aims to release hydrogen by decomposing hydrogen-rich molecules, and also a reversible hydrogen storage–release process under appropriate conditions. Chemical hydrogen storage could store a decent amount of hydrogen, but the key question is how to release the hydrogen. This concerns the material design, and may also influence current hydrocarbon material recycling.
Microwaves are electromagnetic waves with 0.001–1 m wavelength and 0.3–300 GHz frequency. Generally, mobile, radar and television satellite communications are all operated in this frequency band.30 For microwave heating, two frequencies referred to as 915 MHz and 2.45 GHz are reserved by the Federal Communications Commission (FCC) for industrial, scientific, and medical purposes. Compared to traditional heating methods that rely on thermal conduction and convection, like oil baths or heating jackets, microwave heating or microwave dielectric heating pushes electromagnetic wave energy directly and preferentially to the absorbing media, which means that substrates are more evenly heated rather than heated from the surface to the core, external to internal.31 This method began to be utilized by households in the 1970s, and in 1990 it was applied in many fields, especially material processing and microwave chemical reactions, including mineral processing,32 metal oxide reduction,33 leaching,34 sintering, and the manufacturing of ceramic materials.35 Currently, microwave-assisted pyrolysis technologies are rapidly growing, and playing a key role in the treatment of waste plastics,36 rubber waste,37 sewage sludge,38 biomass,39 and contaminated soil.40 The key reason microwave heating is favored by industry is the high energy utilization and temperature elevation rate driven by well-distributed microwave absorbing media, which allows a high energy conversion efficiency and even heating of substrates.41,42 Also, since the energy efficiency is higher and the system average temperature is reduced, there are fewer side reactions and better product selectivity. Besides the merits for the reaction progress, microwave reactors usually have compact structures, easy installation processes, simple operation methods, and good safety. Therefore, microwave-enhanced hydrogen production is a promising solution for the hydrogen society to support storing hydrogen in non-gaseous compounds and releasing it when needed in a convenient and affordable way.
In this paper, microwave-enhanced hydrogen production from plastic waste, biomass, low-carbon alcohols, and methane pathways are discussed. This paper aims to understand how microwave heating technology works and compares the differences between microwave heating and traditional heating methods in the hydrogen production process. At present, hydrogen is still mainly produced from non-renewable resources, such as steam reforming of coal, oil, and natural gas, so a full understanding and study of microwave heating technology will help to understand the advantages, disadvantages, and applicability of this technology in promoting the conversion of non-renewable resources to renewable resources for hydrogen production.
2. Mechanism of microwave heating
Microwaves are electromagnetic waves whose wavelengths range from 0.001–1 m and a corresponding frequency range of 0.3–300 GHz, and are composed of two perpendicular and oscillating electric (E) and magnetic (H) fields.30,43 During the microwave heating process, the irradiated object interacts with the microwaves, and its temperature increases. The microwave absorption property of matter is related to the electric and magnetic loss tangents (tan
δε (eqn (1)) and tan
δμ (eqn (2)), respectively).44 |
 | (1) |
|
 | (2) |
where the real parts ε′ and μ′ represent the electromagnetic waves storage ability, and the imaginary parts ε′′ and μ′′ represent the attenuation ability of electric energy and magnetic energy, respectively. The greater the loss factor, the stronger the attenuation. In the microwave heating process, three types of materials are mainly involved that correspond to different heating mechanisms. For Class I (liquids such as water and alcohol), when microwave radiation acts on water molecules, the state of electron distribution of the water molecules will change rapidly, and then the polarization of the molecules will change due to the applied alternating electric field, resulting in orientation polarization, which induces a rotational motion of the molecules with the microwave frequencies. In this process, some friction between adjacent molecules may occur and will generate thermal energy. For Class II (inorganic solids), even though without molecules in this type of material, however, in a similar way as with liquids, the electrons and atoms (ions) in inorganic solids also can be excited by applied electromagnetic waves, and some friction will also exist during their motion, thus leading to a temperature increase. For Class III (metallic materials), microwave radiation will generate an induction current or a magnetic spin correlation phenomenon in the presence of an external magnetic field, then the electron motion and lattice vibration will be enhanced, which promotes heat generation.
3. Hydrogen produced from plastic waste
Owing to their light weight, good chemical resistance, flexible modifiability, and decent commercial accessibility, plastics have become ubiquitous in electronics, packaging, and construction. Since the 1950s, the rapid development of the plastics industry has made great contributions to the prosperity of human society. In 2018, global plastic production surpassed 350 million tons and has continued to increase. Despite the convenience brought by plastics, their negative impact on the natural environment and human health has become a growing concern, as evidenced by the mounting plastic pollution.45–48 Although the gradual global awareness of the hazards of plastics has now motivated the promotion of related activities, technologies, and policies, these are still far from sufficient, since recycling rates are as low as 20%.45,49 Consequently, recycling through upcycling processes has become an urgent imperative to combat the harmful effects of plastic waste that would otherwise be relegated to landfills, incineration, or directly released into the environment.
Plastics are rich sources of hydrogen, which makes them ideal for microwave-assisted catalytic upgrading to produce hydrogen once discarded; hence not only generating profits but also contributing to pollution reduction.50–54 Typically, iron-, cobalt-, and nickel-based catalysts are the most commonly used for this recycling due to their ability to activate carbon–hydrogen bonds. Specifically, these catalysts are capable of selectively promoting the cleavage of carbon–hydrogen bonds to generate hydrogen.55–58 As magnetic substances, these three metal-based catalysts are highly responsive to microwaves, converting them into heat rapidly. Qian59 et al. synthesized a Co-doped Fe–Al catalyst and used it in an LDPE dehydrogenation reaction, and found that the Fe1Co1Al2 catalyst could yield 61.39 mmol (g plastic)−1 hydrogen under microwave irradiation, which was almost two times higher than conventional heating. Meanwhile, Co-doping is not only conducive to the conversion of catalysts into FeCo alloys with enhanced activities but also can effectively inhibit the formation of Fe3C, thereby altering the carbon diffusion pathway and promoting the formation of nanotubes and hydrogen production (Fig. 1a). Huang60 et al. synthesized CeO2 with iron/nickel nanoparticles-loaded carbon nanotubes (Fe/Ni–CeO2@CNTs) substrates, which could be used to effectively convert high-density polyethylene (HDPE) plastics to high-purity hydrogen (91.5 vol%, 50.2 mmol (g plastic)−1) and carbon nanotubes under microwave radiation. The synergistic effect of Fe/Ni bimetallic particles and the CeO2-induced reforming reaction significantly improved the selectivity and yield of H2. It also achieved remarkable results in deconstructing low-density polyethylene (LDPE) and polypropylene (PP) waste as well, with hydrogen selectivities and yields up to 90.0 vol% and 48.31 mmol (g plastic)−1, respectively, achieving near-zero carbon emissions (Fig. 1b). Song61 et al. studied the effects of Fe and FeAl2O4 ratios and structure properties of the catalyst on the dehydrogenation efficiency of HDPE. The results showed that the best catalytic activity and absorption characteristics of the Fe–FeAl2O4 catalyst were achieved when the loading of Fe was 30 wt%, in which electromagnetic field distribution simulations proved that the catalyst was heated in the form of eddy current loss. A hydrogen yield of 47.3 mmol (g plastic)−1 and hydrogen selectivity of 84.96 vol% were obtained in the HDPE plastic dehydrogenation reaction (Fig. 1c).
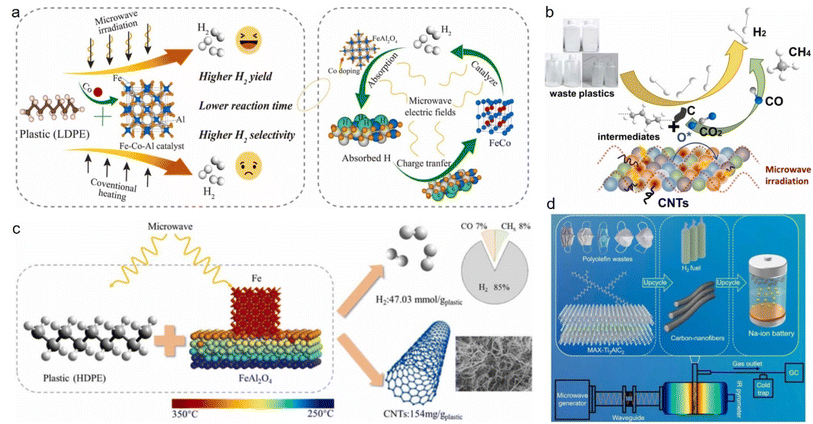 |
| Fig. 1 Microwave-assisted enhanced hydrogen production from plastics via different catalysts. (a) Microwave-initiated decomposition of plastic over an Fe–Co–Al catalyst.59 (b) Schematic diagram of the decomposition of waste plastics over Fe/Ni–CeO2@CNTs catalyst in a microwave radiation field.60 (c) Reaction mechanism of HDPE to prepare hydrogen and carbon nanotubes on Fe/FeAl2O4 under microwave irradiation.61 (d) Microwave-initiated upcycling of polyolefin plastic wastes over MAX-catalyst and the application of carbon nanofibers.62 | |
All the aforementioned catalysts for the dehydrogenation process are made from Fe and Ni because of their strong ability to activate carbon–hydrogen bonds. Alternatively, Ti3AlC2 (MAX) has decent dehydrogenation activity as well. Since titanium and iron belong to the same period of transition metal elements, Lu62 et al. speculated that TiC in Ti3AlC2 could selectively catalyze the upgrading of plastics, like FeC3, to produce H2 and filamentous carbon. They found that Ti3AlC2 was capable of deconstructing LDPE, HDPE, and PP as a microwave acceptor and a catalyst, giving H2 yields of 51.3, 49, and 46 mmol (g plastic)−1, respectively (Fig. 1d).
Table 1 presents a comparison between microwave heating and conventional heating methods in plastic dehydrogenation to illustrate the benefits of microwave-assisted catalytic technology. As mentioned, traditional heating methods typically employ a two-stage process involving plastic pyrolysis at high temperatures to produce low-molecular-weight hydrocarbon compounds, which are then subjected to a catalytic reforming method to generate hydrogen. However, this approach suffers from several significant drawbacks, including a high energy consumption, complex procedures, substantial carbon dioxide emissions (approximately 12 kg CO2 per 1 kg of hydrogen produced), and low hydrogen selectivity.63 In contrast, microwave heating methods facilitate the one-step production of high yields of hydrogen and offer numerous advantages, such as a low energy consumption and high efficiency.
Table 1 Comparison of the catalytic performance of microwave heating and conventional heating methods in plastic dehydrogenation
Type |
Plastic |
Catalyst |
Pyrolysis temp. (°C) |
Catalytic temp. (°C) |
Steam (Y/N) |
H2 yield (mmol (gplastic)−1) |
Ref. |
Microwave (one-step) |
LDPE |
Fe–Co–Al |
— |
600–900 |
N |
61.39 |
59 |
HDPE |
Fe/Ni–CeO2@CNTs |
— |
800 |
N |
50.2 |
60 |
LDPE |
|
|
|
|
48.3 |
|
PP |
|
|
|
|
48.3 |
|
HDPE |
Fe–FeAl2O4 |
— |
300–450 |
N |
47.3 |
61 |
HDPE |
Ti3AlC2 |
— |
900–1000 |
N |
49 |
62 |
LDPE |
|
|
|
|
51.3 |
|
PP |
|
|
|
|
46 |
|
HDPE |
FeAlOx |
— |
300–380 |
N |
55.6 |
64 |
PP |
|
|
|
|
51.4 |
|
PS |
|
|
|
|
26.9 |
|
PE |
Fe–Ni |
— |
400 |
N |
51.8 |
65 |
Pyrolysis- reforming (two-step) |
Plastic mixture |
Ni–Fe/MCM41 |
500 |
800 |
N |
38.1 |
66 |
Plastic mixture |
Ni–Fe |
500 |
800 |
N |
42.3 |
67 |
PP |
Fe, Ni |
500 |
800 |
Y |
25.14 |
68 |
HDPE |
Ni/ZSM5 |
500 |
850 |
Y |
66.09 |
69 |
PP |
NiMnAl 424 |
500 |
800 |
Y |
56.6 |
70 |
|
NiMnAl 444 |
|
|
|
37.2 |
|
PP |
Fe/SiO2-S |
600 |
800 |
N |
15.4 |
71 |
|
Fe/SiO2-L |
|
|
|
25.6 |
|
|
Ni/SiO2-S |
|
|
|
18.1 |
|
|
Ni/SiO2-L |
|
|
|
22.6 |
|
4. Hydrogen produced from biomass
Renewable resource biomass is another ideal source to generate hydrogen.12,72–75 Currently, the main methods for converting biomass into hydrogen are biological and thermochemical methods. Despite the attractive prospect of generating hydrogen by the biological method in terms of its sustainability, the poor photosynthetic conversion and COD removal efficiency limit its practical application.76 As mentioned, thermochemical methods usually require high temperature to activate the pyrolysis and initiate hydrogen production and are thus beset by the issues of high energy consumption and by-products generation.77,78 Microwave-assisted pyrolysis can achieve rapid high-temperature heating, which can offer significant advantages in transforming biomass into hydrogen. Qiao79 et al. prepared a novel graphene aerogel with few defects by the microwave heating for chemically pre-reducing graphene aerogel. Under microwave irradiation, a high-temperature arc of more than 1000 °C (difficult to achieve by existing heating methods) could be generated by the aerogel, which could promote the rapid pyrolysis of biomass, whereby H2-rich gas could be obtained with hydrogen yields of 3.31, 4.35, 2.25, and 2.90 g per g biomass from the microwave-assisted pyrolysis of four common solid biomasses (poplar branches, rice husks, straw, and corn Stover). Parvez77 et al. compared the yield differences of gas, oil, and coke produced by the pyrolysis of Bakelite under conventional and microwave heating at 600 °C, 700 °C, and 800 °C, and found that the corresponding energy (higher heating value) of the produced gas under microwave heating was higher than those of conventional heating at the selected three temperatures. In addition, by using Aspen Plus™ for hydrogen plant simulation, the results showed that by producing 120 g H2 per kg Bakelite, the microwave heating performance was 15% more efficient than conventional systems.
Therefore, microwaves can enhance the chemical reaction process, improving the hydrogen production efficiency of thermochemical methods (such as pyrolysis and gasification) and strengthening the energy efficiency in promoting biological hydrogen production.80–82 However, further improvements are needed in the future to modify the advantages and limitations of the process. It is also necessary to perform a techno-economic assessment based on the production, costs, technical level, and industrial scalability in order to apply this technology to actual production.
5. Hydrogen produced from low-carbon alcohols
The reforming of low-carbon alcohols (methanol, ethanol, propanol, butanol, etc.) is a very promising approach for hydrogen generation, since their low sulfur contents, high volumetric energy density, high hydrogen/carbon ratio, and biodegradability make them desired media for energy transport.83–86 Compared with other compounds (e.g., that have a plastic reforming temperature above 700 °C),58,67,87 low-carbon alcohols can be reformed at relatively low temperatures, for instance, methanol composed only of carbon–hydrogen bonds, and the hydrogen extraction process can be carried out at a low temperature of about 200–300 °C; while the reforming temperature of ethanol is only about 400 °C.88–92 Besides, producing hydrogen from low-carbon alcohols has certain advantages: (1) in low-carbon alcohol compounds (which are easy to store and transport), reforming is expected to realize in situ hydrogen production, which helps to overcome the shortcomings of storage and transportation;92–95 (2) availability of accessible and abundant resources;96 (3) CO and CO2 produced by the dehydrogenation of low-carbon alcohols can be used as raw materials to be reconverted into the initial compounds under appropriate conditions (temperature, pressure, etc.), so as to transport hydrogen on demand.97–101
An external energy supply is required for reforming low-carbon alcohols since it is an endothermic reaction. This could either involve using conventional heat sources (e.g., steam, electric heating, or an oil bath) or alternative energy sources, such as plasma or microwaves in a reactor. Generally, the reaction rate depends on the energy induction rate, whereby the efficiency of conventional heating methods relies on the heat transfer efficiency and the system temperature usually has a low efficiency and poor selectivity for thermal conduction. In contrast, microwave-assisted heating can realize a rapid, selective, and volumetric heating process, which possesses benefits unachievable by traditional heating methods, namely a higher conversion and selectivity with a reduced system temperature required. Furthermore, microwave plasma exhibits a higher conversion rate (>90%) than DBD plasma technology due to its high stability and repeatability under various operating conditions and the possibility of operating at atmospheric pressure.102
When utilizing microwave plasma technology to reform low-carbon alcohols for hydrogen production, they operate in working atmospheres in nitrogen, argon, and oxygen gas, corresponding to nitrogen, argon, oxygen plasma,103,104 etc. The corresponding plasma produces massive high-energy electrons, active groups, and excitation ions, thus promoting the reforming to produce hydrogen.105–109 Fig. 2 illustrates a microwave plasma hydrogen production system; comprising a magnetron generator, microwave power supplying and measuring system, microwave plasma source (MPS), impedance matching elements, gas supply and flow control system, gas analysis system, and optical emission spectroscopy (OES) system.110 Wang111 et al. used non-catalytic microwave plasma technology to refine methanol into hydrogen. A 3.3% molar fraction of methanol in the experiment showed a conversion rate greater than 97%, while the selectivity of H2 increased from 77.5% to 85.8% when the applied power was increased from 800 W to 1400 W. Rincón112 et al. found that low argon flow rates significantly promoted the hydrogen selectivity. Two atmospheric pressure microwave plasma sources could be used to withstand large ethanol flow rates, which enabled a nearly complete decomposition (>99%) of ethanol under various operating conditions while achieving high hydrogen yields. In addition, the technology is expected to be expandable to the industrial scale because of the relatively low specific energy required for ethanol decomposition. Compared with the steam reforming method, the direct introduction of liquid alcohols can save energy for gasification and improve the economic benefits. Czylkowski113 et al. used nitrogen plasma to effectively decompose ethanol droplets into hydrogen-rich products while improving the production rate and energy efficiency.
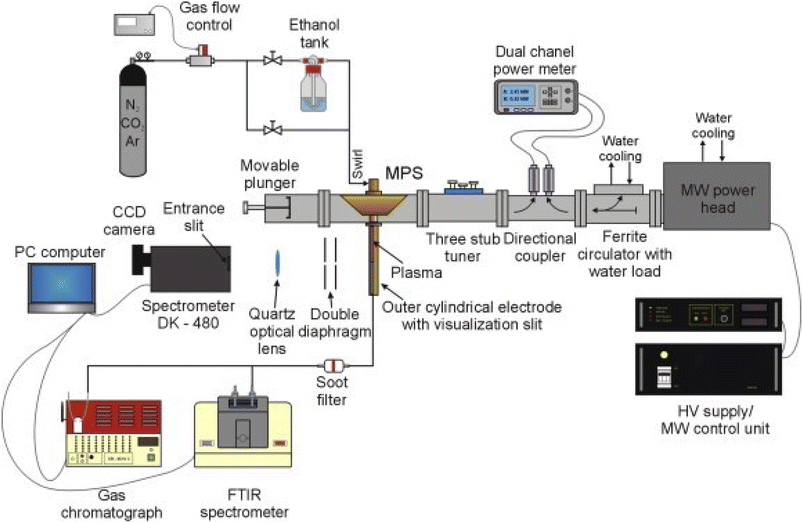 |
| Fig. 2 Diagram of a microwave plasma hydrogen production system.110 | |
Microwave plasma reforming technology is not limited to reforming single alcohols, like methanol,114,115 ethanol,110,116,117 propanol, and others, it can also simultaneously decompose low-carbon alcohol mixtures to prepare hydrogen,102,118 which is more conducive to practical application without the expenditure for the separation and purification of alcohol mixtures. In addition, Table 2 also discusses the operating parameters and hydrogen selectivity of microwave-assisted hydrogen production from alcohol compounds.
Table 2 Summary of microwave-assisted hydrogen production from alcohols
Feed |
Catalyst |
Reaction parameters |
H2 selectivity (S)/production rate |
Ref. |
Methanol |
— |
Pressure: 1 atm |
S(H2) = 85.5% |
111 |
|
|
Working gas: N2 |
|
|
Methanol |
CuO–ZnO–Al2O3 |
Pressure: 1 atm |
S(H2) = 85–96% |
119 |
|
|
Working gas: N2 |
|
|
|
|
Methanol : water: 1 : 1 |
|
|
Methanol |
CuZnO/Al2O3 |
Pressure: 1 atm |
S(H2) = 70% |
115 |
|
PdZnO/Al2O3 |
Working gas: N2 |
|
|
Ethanol |
— |
Pressure: 1 atm |
728 NL h−1 |
103 |
|
|
Working gas: N2 |
|
|
Ethanol |
— |
Pressure: 1 atm |
1016 NL h−1 |
104 |
|
|
Working gas: N2 |
|
|
Ethanol |
— |
Pressure: 1 atm |
210 NL h−1 |
110 |
|
|
Working gas: N2/Ar/CO2 |
|
|
Ethanol |
— |
Pressure: 1 atm |
1043 NL h−1 |
113 |
|
|
Working gas: N2 |
|
|
Ethanol |
— |
Pressure: 1 atm |
751 NL h−1 |
120 |
|
|
Working gas: N2/CO2 |
|
|
|
|
Ethanol : water: 1 : 1 |
|
|
Ethanol |
— |
Pressure: 1 atm |
1150 NL h−1 |
121 |
Isopropanol |
|
Working gas: N2/CO2 |
1116 NL h−1 |
|
Ethanol |
Pyrolysis residue of sewage sludge |
Pressure: 1 atm |
S(H2) = 52.2% |
122 |
|
|
Working gas: N2 |
|
|
6. Hydrogen produced from methane
Methane is considered the second major greenhouse gas just following carbon dioxide, and the annual emissions of methane are yet to grow rapidly.123,124 Thus, diversifying the utilization of methane is indeed essential to reduce methane emissions, address global warming, and carbon neutrality ultimately. As a high hydrogen-to-carbon compound, methane is naturally suitable as a feedstock to produce syngas: a mixture of hydrogen, carbon monoxide, and carbon dioxide gases.125–128 Syngas can be transformed by a Fischer–Tropsch synthesis into raw materials required by various chemical products, like ammonia, methanol, and hydrocarbons,129,130 achieving methane removal and resource utilization.
Methane reforming methods include the steam reforming of methane131,132 (eqn (3)), the partial oxidation of methane133–135 (eqn (4)), methane dry reforming136–138 (eqn (5)), and methane thermal decomposition139,140 (eqn (6)). Currently, methane steam reforming is still the main approach to produce syngas, but requires a large amount of superheated steam to maintain high temperature, resulting in huge energy costs. Meanwhile, the methane steam reforming process is a strongly endothermic reaction that usually needs to be operated at 800–900 °C high temperatures. Unfortunately, regular catalysts tend to be quickly inactivated under such harsh conditions.141 Compared with the methane steam reforming method, the partial oxidation method with exothermic properties can be carried out under mild conditions; nevertheless, it is relatively difficult to produce syngas from the partial oxidation method of methane. From an environmental aspect, methane dry reforming can convert methane and carbon dioxide into syngas, which utilizes greenhouse gases simultaneously, but the required reaction temperature is >700 °C, which incurs the same problem that catalysts may sinter and fail.
|
CH4 + H2O ↔ 3H2 + CO ΔH298K = +206 kJ mol−1
| (3) |
|
CH4 + 1/2O2 ↔ 2H2 + CO ΔH298K = −8.5 kJ mol−1
| (4) |
|
CH4 + CO2 ↔ 2H2 + 2CO ΔH298K = +247 kJ mol−1
| (5) |
|
CH4 ↔ 2H2 + C ΔH298K = +74 kJ mol−1
| (6) |
The microwave-assisted heating method can efficiently restructure methane into syngas through catalytic or plasma pathways. Li142 et al. primarily used Fe2O3 as a catalyst for the pyrolysis of biomass to obtain a large surface area, porous, Fe-rich biomass-derived carbon, and then applied this for microwave-assisted methane reforming and achieved a high methane conversion (800 °C). Furthermore, the conversion rate of CH4 and CO2 was relatively stable in a long–term reaction of 160 min, and the gaseous products contained a syngas content of 88.79% and H2/CO ratio of 0.92 on average. Compared with traditional heating methods, microwave-assisted heating can not only play a significant role in enhancing chemical reactions, but also has a positive effect on catalyst preparation (Fig. 3a). Stefanidis143 et al. adopted conventional and microwave-assisted hydrothermal methods to prepare various ruthenium-doped strontium titanate (SrTiO3) perovskite catalysts, and found that SrTiO3 catalyst synthesis through microwave irradiation could efficiently convert CH4 and CO2 into syngas (H2/CO = 0.9) (Fig. 3b). Furthermore, microwave plasma technology also exhibited excellent performance in methane reforming, and could be operated in catalyst-free conditions. For instance, Czylkowski144 et al. studied the hydrogen production efficiency of methane by combining steam reforming (CO2 and water steam) in a metal cylinder microwave plasma source (MPS) provided by waveguide, which could achieve a hydrogen production energy yield of 42.9 g (H2) per kW per h by optimizing the absorbed microwave power, working gas composition and flow rate, and other process input parameters, while the plasma steam reforming of methane could operate stably at high gas flow rates (thousands NL per h) (Fig. 3c). Sun145 et al. injected methane into water and realized the wet reforming of liquid phase methane by directly coupling liquid phase microwave discharge plasma. When the microwave input power was 900 W, the methane conversion rate and hydrogen concentration were 94.3% and 74.0%, respectively. In addition, through optimization of the electrode structure while improving the stability of the plasma system, a higher hydrogen yield and hydrogen energy efficiency were obtained, and the highest energy efficiency for hydrogen production was about 0.92 mmol kJ−1 (Fig. 3d). Moreover, the performance comparison of different catalysts has shown in Table 3.
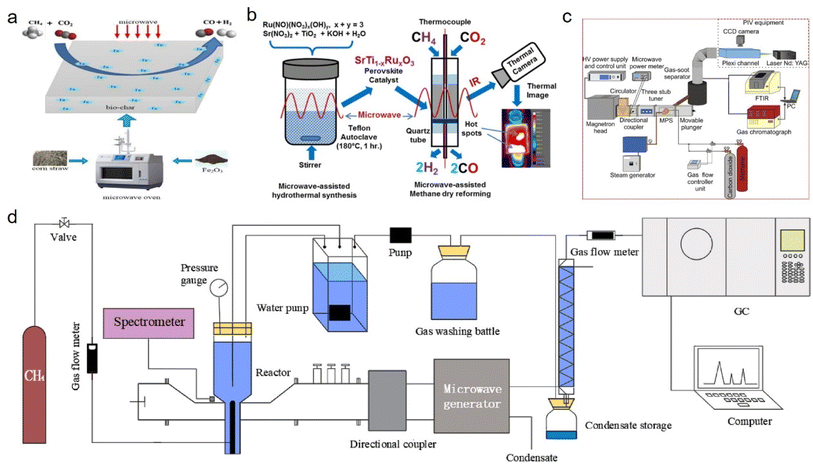 |
| Fig. 3 (a) Porous Fe-rich biomass-derived carbon142 and (b) ruthenium-doped strontium titanate (SrTiO3) perovskite143 catalysts applied for microwave-assisted methane dry reforming. (c) and (d) Sketch of microwave plasma enhanced hydrogen production via the steam reforming of methane.144,145 | |
Table 3 Summary of microwave-assisted methane dry reforming based on different catalysts
Catalysts |
Temp. (°C) |
VHSV (L gcat−1 h−1) |
Microwave-assisted heating |
Conventional heating |
H2/CO |
Ref. |
CH4 conversion (%) |
CO2 conversion (%) |
CH4 conversion (%) |
CO2 conversion (%) |
Potassium-rich char |
800 |
0.166 |
95 |
100 |
81 |
93 |
0.7 |
146 |
Activated carbon |
600–900 |
0.16 |
100 |
100 |
72 |
80 |
0.7–1.4 |
147 |
Biochar |
800 |
0.6 |
93.8 |
89.4 |
79 |
71.2 |
0.71–0.88 |
148 |
SiC·SiO2 |
810 |
— |
27 |
17 |
— |
— |
0.97 |
149 |
12%Fe–SiC·SiO2 |
|
|
>95 |
>95 |
|
|
|
|
FY5 |
800 |
0.3 |
>96 |
>97 |
— |
— |
0.67 |
150 |
50% FY5 + 50% Ni/Al2O3 |
|
3 |
>88 |
>93 |
— |
— |
1 |
|
Biochar |
600–1000 |
— |
40–100 |
45–100 |
— |
— |
0.91–3 |
151 |
Ni–CeO2 |
850 |
— |
65 |
84 |
— |
— |
1.1–1.5 |
152 |
2Ta–Ni |
|
|
82 |
83 |
|
|
|
|
2Cr–Ni |
|
|
92 |
99 |
|
|
|
|
2Fe–Ni |
|
|
79 |
85 |
|
|
|
|
7Ru/SrTiO3 |
700 |
3 |
90.2 |
88.5 |
— |
— |
0.88 |
143 |
|
|
4.5 |
91.7 |
89.4 |
|
|
0.9 |
|
|
|
6 |
93.9 |
90.3 |
|
|
0.89 |
|
|
|
7.5 |
93.4 |
90.4 |
|
|
0.89 |
|
|
|
9 |
94 |
91.2 |
|
|
0.89 |
|
|
|
10.5 |
94.6 |
91.8 |
|
|
0.89 |
|
|
|
12 |
61.8 |
63.6 |
|
|
0.85 |
|
|
|
13.5 |
53.5 |
64.9 |
|
|
0.86 |
|
Char + Na |
975 |
2.4 |
72 |
93 |
— |
— |
— |
153 |
Char + K |
|
|
73 |
92 |
|
|
|
|
Char + Ca |
|
|
79 |
83 |
|
|
|
|
Char + Mg |
|
|
80 |
82 |
|
|
|
|
Char + Ni |
|
|
92.7 |
86.7 |
|
|
|
|
CoMo2/Al2O3 |
— |
10 |
80 |
93 |
— |
— |
0.8 |
154 |
7. Conclusion
Microwave-assisted technology offers an effective and cost-efficient means of generating hydrogen. During microwave-assisted heating, the heating characteristics of materials rely on their loss factor, and high loss factors are advantageous for achieving increased heating rates and reaction temperatures. Various literature reviews have indicated that electromagnetic waves are capable of selectively interacting with catalysts in the process of hydrogen production from waste plastics, which leads to a rapid heating of the catalyst particles and the catalytic cracking of carbon–hydrogen bonds in plastics to produce hydrogen. Additionally, the resulting hydrogen can quickly dissociate from the active sites on the catalysts to avoid undesirable side reactions. The utilization of microwave-assisted technology in enhancing biomass hydrogen production provides a promising avenue for sustainable hydrogen generation, since biomass resources are abundant worldwide, and as the bed temperature can quickly attain the required temperature for thermochemical reactions, thereby reducing the energy consumption of the reactions and side reactions. In contrast, low-carbon alcohol reforming can be conducted at a lower temperature, and low-carbon alcohols possess abundant resources and high hydrogen content, which makes them suitable for on-demand hydrogen production, thus overcoming the challenges related to hydrogen storage and transportation. Furthermore, carbon monoxide and carbon dioxide produced during methanol reforming can be converted back into methanol directly by industrial direct hydrogenation methods. Based on this, the selective decomposition of methanol into hydrogen and carbon monoxide using microwave catalysis or microwave plasma technology can help achieve a reversible hydrogen storage system by hydrogenating the separated carbon monoxide. Finally, microwave catalysis and microwave plasma technology can efficiently convert the two main greenhouse gases into synthesis gas under low energy consumption conditions in methane reforming, which can be utilized to synthesize high-value chemicals.
This literature review suggests several recommendations for future research endeavors:
(1) Due to the difficulty in obtaining pure plastic and biomass in practice in real life, it is essential to focus on hydrogen production by mixed impure organic sources to actually assess practical feasibility, thereby reducing the sorting cost and improving the universality of microwave-enhanced hydrogen production in the future. Second, more extensive research is required on the reaction mechanism of the process to facilitate the development of catalysts that can demonstrate stable performance, high dehydrogenation activity, and resistance to impurities. Furthermore, to improve the efficiency of co-processing biomass and plastic waste, further research needs to be conducted on various factors, such as the particle size, heating rate, microwave power, heating mode (continuous or intermittent), and mass ratio, to ultimately aid the understanding and for guiding catalyst design to realize ideal performance, gas composition, and hydrogen production, and leading to an enhancement in the co-processing efficiency.
(2) Biomasses are renewable resources whose efficient development and utilization can play a pivotal role in addressing global energy and ecological environmental concerns. Nonetheless, the direct use of biomass as a hydrogen storage medium to enable on-demand hydrogen production remains challenging. To promote the advancement of a hydrogen-based society, establishing and evaluating the following technical issues need to be addressed: converting biomass into syngas via microwave-assisted pyrolysis technology, followed by transforming the syngas into high-hydrogen-content methanol that is easily storable and transportable; studying the feasibility of in situ hydrogen production by combining the advantages of microwave reactions with regard to the compact structure, easy installation, and ease of operation; methodically investigating the factors that influence the preparation of syngas from biomass, methanol production from syngas, and hydrogen production from methanol decomposition (e.g., catalyst particle size, specific surface area) to achieve the optimal efficiency.
(3) The preparation of syngas through methane reforming usually requires high-temperature conditions, which imposes limitations on traditional heating methods. Fortunately, microwave plasma technology presents notable advantages over traditional techniques, including higher conversion rates and energy efficiency, better chemical selectivity, greater processing capacity, and improved discharge uniformity in methane reforming reactions. Microwave plasma is capable of effectively catalyzing methane and carbon dioxide in a non-equilibrium state. Nonetheless, to advance this technology from the laboratory scale toward commercialization, optimization of the process parameters, such as microwave power, pressure, reactant composition, flow rate, catalyst composition, preparation method, and the cost, is required to achieve greater energy and conversion efficiency, and to surmount the technical and economic obstacles.
In short, although microwave-assisted methods have already played a significant role in the domain of hydrogen production to date, further developments necessitate a meticulous optimization of the key parameters, such as microwave power, catalyst structure, and reaction pressure, to achieve better products. Additionally, an economic assessment of the microwave-assisted hydrogen production process is required to fully ascertain its benefits and promote its implementation in large-scale production.
Conflicts of interest
There are no conflicts to declare.
Acknowledgements
The authors acknowledge financial support from the National Key R&D Program of China (No. 2019YFA0708700), TIPC Director's Fund of Technical Institute of Physics and Chemistry, Chinese Academy of Sciences, Key Laboratory of Photochemical Conversion and Optoelectronic Materials, Technical Institute of Physics and Chemistry, Chinese Academy of Sciences.
References
- A. Hasanbeigi, M. Arens and L. Price, Renewable Sustainable Energy Rev., 2014, 33, 645–658 CrossRef CAS
. - B. Koerner and J. Klopatek, Environ. Pollut., 2002, 116, S45–S51 CrossRef CAS PubMed
. - R. Quadrelli and S. Peterson, Energy Policy, 2007, 35, 5938–5952 CrossRef
. - M. Qin, L. Chen, H. Zhang, M. Humayun, Y. Fu, X. Xu, X. Xue and C. Wang, Chem. Eng. J., 2023, 454, 140230 CrossRef CAS
. - H. Sun, L. Li, M. Humayun, H. Zhang, Y. Bo, X. Ao, X. Xu, K. Chen, K. Ostrikov, K. Huo, W. Zhang, C. Wang and Y. Xiong, Appl. Catal., B, 2022, 305, 121088 CrossRef CAS
. - B. Chen, M. Humayun, Y. Li, H. Zhang, H. Sun, Y. Wu and C. Wang, ACS Sustainable Chem. Eng., 2021, 9, 14180–14192 CrossRef CAS
. - C. Acar and I. Dincer, Int. J. Hydrogen Energy, 2020, 45, 3396–3406 CrossRef CAS
. - P. E. Dodds, I. Staffell, A. D. Hawkes, F. Li, P. Grünewald, W. McDowall and P. Ekins, Int. J. Hydrogen Energy, 2015, 40, 2065–2083 CrossRef CAS
. - D. B. Levin and R. Chahine, Int. J. Hydrogen Energy, 2010, 35, 4962–4969 CrossRef CAS
. - J. A. Turner, Science, 2004, 305, 972–974 CrossRef CAS PubMed
. - N. Armaroli and V. Balzani, ChemSusChem, 2011, 4, 21–36 CrossRef CAS PubMed
. - Y. Kalinci, A. Hepbasli and I. Dincer, Int. J. Hydrogen Energy, 2009, 34, 8799–8817 CrossRef CAS
. - G. Nicoletti, N. Arcuri, G. Nicoletti and R. Bruno, Energy Convers. Manage., 2015, 89, 205–213 CrossRef
. - W. Lubitz and W. Tumas, Chem. Rev., 2007, 107, 3900–3903 CrossRef CAS PubMed
. - K. Mazloomi and C. Gomes, Renewable Sustainable Energy Rev., 2012, 16, 3024–3033 CrossRef CAS
. - Y. Kojima, Int. J. Hydrogen Energy, 2019, 44, 18179–18192 CrossRef CAS
. - A. I. Osman, N. Mehta, A. M. Elgarahy, M. Hefny, A. Al-Hinai, A. a. H. Al-Muhtaseb and D. W. Rooney, Environ. Chem. Lett., 2022, 20, 153–188 CrossRef CAS
. - D. Wei, X. Shi, R. Qu, K. Junge, H. Junge and M. Beller, ACS Energy Lett., 2022, 7, 3734–3752 CrossRef CAS
. - R. Moliner, M. J. Lázaro and I. Suelves, Int. J. Hydrogen Energy, 2016, 41, 19500–19508 CrossRef CAS
. - S. S. Penner, Energy, 2006, 31, 33–43 CrossRef CAS
. - D. R. Palo, R. A. Dagle and J. D. Holladay, Chem. Rev., 2007, 107, 3992–4021 CrossRef CAS PubMed
. - Z. Dong, A. Mukhtar and H. Lin, Top. Catal., 2021, 64, 481–508 CrossRef CAS
. - J. W. Makepeace, T. He, C. Weidenthaler, T. R. Jensen, F. Chang, T. Vegge, P. Ngene, Y. Kojima, P. E. de Jongh, P. Chen and W. I. F. David, Int. J. Hydrogen Energy, 2019, 44, 7746–7767 CrossRef CAS
. - M. Dincǎ, A. Dailly, Y. Liu, C. M. Brown, D. A. Neumann and J. R. Long, J. Am. Chem. Soc., 2006, 128, 16876–16883 CrossRef PubMed
. - A. M. Seayad and D. M. Antonelli, Adv. Mater., 2004, 16, 765–777 CrossRef CAS
. - F. L. Darkrim, P. Malbrunot and G. P. Tartaglia, Int. J. Hydrogen Energy, 2002, 27, 193–202 CrossRef CAS
. - J. L. C. Rowsell and O. M. Yaghi, Angew. Chem., Int. Ed., 2005, 44, 4670–4679 CrossRef CAS PubMed
. - D. J. Collins and H.-C. Zhou, J. Mater. Chem., 2007, 17, 3154–3160 RSC
. - R. Ströbel, J. Garche, P. T. Moseley, L. Jörissen and G. Wolf, J. Power Sources, 2006, 159, 781–801 CrossRef
. - R. R. Mishra and A. K. Sharma, Composites Part A: Applied Science and Manufacturing, 2016, 81, 78–97 CrossRef CAS
. - M. Bartoli, M. Frediani, C. Briens, F. Berruti and L. Rosi, Processes, 2019, 7, 658 CrossRef CAS
. - S. W. Kingman and N. A. Rowson, Miner. Eng., 1998, 11, 1081–1087 CrossRef CAS
. - N. Standish and H. Worner, Journal of Microwave Power and Electromagnetic Energy, 1990, 25, 177–180 Search PubMed
. - M. Al-Harahsheh and S. W. Kingman, Hydrometallurgy, 2004, 73, 189–203 CrossRef CAS
. - D. Palaith, R. Silberglitt, C. C. M. Wu, R. Kleiner and E. L. Libeld, MRS Online Proc. Libr., 1988, 124, 255 CrossRef CAS
. - C. Ludlow-Palafox and H. A. Chase, Ind. Eng. Chem. Res., 2001, 40, 4749–4756 CrossRef CAS
. - B. Adhikari, D. De and S. Maiti, Prog. Polym. Sci., 2000, 25, 909–948 CrossRef CAS
. - J. A. Menéndez, M. Inguanzo and J. J. Pis, Water Res., 2002, 36, 3261–3264 CrossRef PubMed
. - J. Li, J. Dai, G. Liu, H. Zhang, Z. Gao, J. Fu, Y. He and Y. Huang, Biomass Bioenergy, 2016, 94, 228–244 CrossRef CAS
. - Z. Kawala and T. Atamańczuk, Environ. Sci. Technol., 1998, 32, 2602–2607 CrossRef CAS
. - C. O. Kappe, Controlled Microwave Heating in Modern Organic Synthesis, Angew. Chem., Int. Ed., 2004, 43, 6250–6284 CrossRef CAS PubMed
. - D. A. Jones, T. P. Lelyveld, S. D. Mavrofidis, S. W. Kingman and N. J. Miles, Resour., Conserv. Recycl., 2002, 34, 75–90 CrossRef
. - M. Bhattacharya and T. Basak, Energy, 2016, 97, 306–338 CrossRef
. - S. Horikoshi and N. Serpone, RF Power Semiconductor Generator Application in Heating and Energy Utilization, Springer, Singapore, 2020 Search PubMed
. - R. Geyer, J. R. Jambeck and K. L. Law, Sci. Adv., 2016, 3, e1700782 CrossRef PubMed
. - D. Hoornweg, P. Bhada-Tata and C. Kennedy, Nature, 2013, 502, 615 CrossRef PubMed
. - S. S. Lam and H. A. Chase, Energies, 2012, 5, 4209–4232 CrossRef CAS
. - J. R. Jambeck, R. Geyer, C. Wilcox, T. R. Siegler, M. Perryman, A. Andrady, R. Narayan and K. L. Law, Science, 2015, 347, 768–771 CrossRef CAS PubMed
. - K. Lee, Y. Jing, Y. Wang and N. Yan, Nat. Rev. Chem., 2022, 6, 635–652 CrossRef PubMed
. - Y. Yan, H. Zhou, S.-M. Xu, J. Yang, P. Hao, X. Cai, Y. Ren, M. Xu, X. Kong, M. Shao, Z. Li and H. Duan, J. Am. Chem. Soc., 2023, 145, 6144–6155 CrossRef CAS PubMed
. - S. S. Sharma and V. S. Batra, J. Chem. Technol. Biotechnol., 2020, 95, 11–19 CrossRef CAS
. - N. Wang, X. Li, M.-K. Hu, W. Wei, S.-H. Zhou, X.-T. Wu and Q.-L. Zhu, Appl. Catal., B, 2022, 316, 121667 CrossRef CAS
. - R.-X. Yang, S.-L. Wu, K.-H. Chuang and M.-Y. Wey, Renewable Energy, 2020, 159, 10–22 CrossRef CAS
. - B. Zhang, H. Zhang, Y. Pan, J. Shao, X. Wang, Y. Jiang, X. Xu and S. Chu, Chem. Eng. J., 2023, 462, 142247 CrossRef CAS
. - J. Alvarez, S. Kumagai, C. Wu, T. Yoshioka, J. Bilbao, M. Olazar and P. T. Williams, Int. J. Hydrogen Energy, 2014, 39, 10883–10891 CrossRef CAS
. - C. Wu and P. T. Williams, Int. J. Hydrogen Energy, 2010, 35, 949–957 CrossRef CAS
. - G. Lopez and L. Santamaria, Nat. Catal., 2020, 3, 861–862 CrossRef CAS
. - J. C. Acomb, C. Wu and P. T. Williams, Appl. Catal., B, 2016, 180, 497–510 CrossRef CAS
. - W. Li, K. Qian, Z. Yang, X. Ding, W. Tian and D. Chen, Appl. Catal., B, 2023, 327, 122451 CrossRef CAS
. - J. Wang, Y. Pan, J. Song and Q. Huang, J. Anal. Appl. Pyrolysis, 2022, 166, 105612 CrossRef CAS
. - L. Yao, B. Yi, X. Zhao, W. Wang, Y. Mao, J. Sun and Z. Song, J. Anal. Appl. Pyrolysis, 2022, 165, 105577 CrossRef CAS
. - Q. Cao, H.-C. Dai, J.-H. He, C.-L. Wang, C. Zhou, X.-F. Cheng and J.-M. Lu, Appl. Catal., B, 2022, 318, 121828 CrossRef CAS
. - I. Barbarias, G. Lopez, J. Alvarez, M. Artetxe, A. Arregi, J. Bilbao and M. Olazar, Chem. Eng. J., 2016, 296, 191–198 CrossRef CAS
. - X. Jie, W. Li, D. Slocombe, Y. Gao, I. Banerjee, S. Gonzalez-Cortes, B. Yao, H. AlMegren, S. Alshihri, J. Dilworth, J. Thomas, T. Xiao and P. Edwards, Nat. Catal., 2020, 3, 902–912 CrossRef CAS
. - P. Zhang, M. Wu, C. Liang, D. Luo, B. Li and J. Ma, J. Hazard. Mater., 2023, 445, 130609 CrossRef CAS PubMed
. - D. Yao, H. Yang, Q. Hu, Y. Chen, H. Chen and P. T. Williams, Appl. Catal., B, 2021, 280, 119413 CrossRef CAS
. - D. Yao, Y. Zhang, P. T. Williams, H. Yang and H. Chen, Appl. Catal., B, 2018, 221, 584–597 CrossRef CAS
. - D. Yao and C.-H. Wang, Appl. Energy, 2020, 265, 114819 CrossRef CAS
. - D. Yao, H. Yang, H. Chen and P. T. Williams, Appl. Catal., B, 2018, 227, 477–487 CrossRef CAS
. - C. Wu, M. A. Nahil, N. Miskolczi, J. Huang and P. T. Williams, Process Saf. Environ. Prot., 2016, 103, 107–114 CrossRef CAS
. - X. Liu, Y. Zhang, M. A. Nahil, P. T. Williams and C. Wu, J. Anal. Appl. Pyrolysis, 2017, 125, 32–39 CrossRef CAS
. - T. Lepage, M. Kammoun, Q. Schmetz and A. Richel, Biomass Bioenergy, 2021, 144, 105920 CrossRef CAS
. - D. B. Pal, A. Singh and A. Bhatnagar, Int. J. Hydrogen Energy, 2022, 47, 1461–1480 CrossRef CAS
. - R. Mishra, H. C. Ong and C.-W. Lin, Energy Convers. Manage., 2023, 284, 116983 CrossRef CAS
. - Y. Tang, J. Dong, Y. Zhao, G. Li, Y. Chi, E. Weiss-Hortala, A. Nzihou, G. Luo and C. Ye, ACS Omega, 2022, 7, 36468–36478 CrossRef CAS PubMed
. - P. C. Hallenbeck, M. Abo-Hashesh and D. Ghosh, Bioresour. Technol., 2012, 110, 1–9 CrossRef CAS PubMed
. - A. M. Parvez, T. Wu, M. T. Afzal, S. Mareta, T. He and M. Zhai, Fuel Process. Technol., 2019, 184, 1–11 CrossRef CAS
. - A. Suresh, A. Alagusundaram, P. S. Kumar, D.-V. N. Vo, F. C. Christopher, B. Balaji, V. Viswanathan and S. Sankar, Environ. Chem. Lett., 2021, 19, 3609–3629 CrossRef CAS
. - W. Liu, H. Jiang, X. Zhang, Y. Zhao, S. Sun and J. Qiao, J. Mater. Chem. A, 2019, 7, 27236–27240 RSC
. - X. Shi, P. Li, X. Wang, J. Song, S. Fang, C. Chang and S. Pang, Energy, 2022, 261, 125307 CrossRef CAS
. - A. A. Arpia, W.-H. Chen, S. S. Lam, P. Rousset and M. D. G. de Luna, Chem. Eng. J., 2021, 403, 126233 CrossRef CAS
. - N. Zhou, J. Zhou, L. Dai, F. Guo, Y. Wang, H. Li, W. Deng, H. Lei, P. Chen, Y. Liu and R. Ruan, Bioresour. Technol., 2020, 314, 123756 CrossRef CAS PubMed
. - T. Wu, J. Wang, W. Zhang, L. Zuo, H. Xu and B. Li, Energy, 2023, 273, 127252 CrossRef CAS
. - T. Zhu, J. Liu, Q. Wang, X. Zhu and B. Sun, J. Energy Inst., 2023, 108, 101246 CrossRef CAS
. - Y. Xu, M. Liu, M. Wang, T. Ren, K. Ren, Z. Wang, X. Li, L. Wang and H. Wang, Appl. Catal., B, 2022, 300, 120753 CrossRef CAS
. - L. Lin, Q. Yu, M. Peng, A. Li, S. Yao, S. Tian, X. Liu, A. Li, Z. Jiang, R. Gao, X. Han, Y.-w. Li, X.-d. Wen, W. Zhou and D. Ma, J. Am. Chem. Soc., 2021, 143, 309–317 CrossRef CAS PubMed
. - C. Wu, M. A. Nahil, N. Miskolczi, J. Huang and P. T. Williams, Environ. Sci. Technol., 2014, 48, 819–826 CrossRef CAS PubMed
. - S. Sá, H. Silva, L. Brandão, J. M. Sousa and A. Mendes, Appl. Catal., B, 2010, 99, 43–57 CrossRef
. - H. Silva, C. Mateos-Pedrero, P. Ribeirinha, M. Boaventura and A. Mendes, React. Kinet., Mech. Catal., 2015, 115, 321–339 CrossRef CAS
. - P. Ribeirinha, C. Mateos-Pedrero, M. Boaventura, J. Sousa and A. Mendes, Appl. Catal., B, 2018, 221, 371–379 CrossRef CAS
. - P. Mierczynski, K. Vasilev, A. Mierczynska, W. Maniukiewicz, M. I. Szynkowska and T. P. Maniecki, Appl. Catal., B, 2016, 185, 281–294 CrossRef CAS
. - Y. Choi and H. G. Stenger, Appl. Catal., B, 2002, 38, 259–269 CrossRef CAS
. - A. Basile, A. Parmaliana, S. Tosti, A. Iulianelli, F. Gallucci, C. Espro and J. Spooren, Catal. Today, 2008, 137, 17–22 CrossRef CAS
. - S. Ahmed and M. Krumpelt, Int. J. Hydrogen Energy, 2001, 26, 291–301 CrossRef CAS
. - A. M. Ranjekar and G. D. Yadav, Ind. Eng. Chem. Res., 2021, 60, 89–113 CrossRef CAS
. - G. Bozzano and F. Manenti, Prog. Energy Combust. Sci., 2016, 56, 71–105 CrossRef
. - L. Wang, Y. Yi, H. Guo and X. Tu, ACS Catal., 2018, 8, 90–100 CrossRef CAS
. - R. van den Berg, G. Prieto, G. Korpershoek, L. I. van der Wal, A. J. van Bunningen, S. Lægsgaard-Jørgensen, P. E. de Jongh and K. P. de Jong, Nat. Commun., 2016, 7, 13057 CrossRef CAS PubMed
. - M. Zabilskiy, V. L. Sushkevich, M. A. Newton and J. A. van Bokhoven, ACS Catal., 2020, 10, 14240–14244 CrossRef CAS
. - Z. Zhang, J. Tong, X. Meng, Y. Cai, S. Ma, F. Huo, J. Luo, B.-H. Xu, S. Zhang and M. Pinelo, ACS Sustainable Chem. Eng., 2021, 9, 11503–11511 CrossRef CAS
. - M. Bowker, ChemCatChem, 2019, 11, 4238–4246 CrossRef CAS PubMed
. - J. Henriques, N. Bundaleska, E. Tatarova, F. M. Dias and C. M. Ferreira, Int. J. Hydrogen Energy, 2011, 36, 345–354 CrossRef CAS
. - B. Hrycak, D. Czylkowski, R. Miotk, M. Dors, M. Jasinski and J. Mizeraczyk, Open Chem., 2015, 13, 317–324 CAS
. - D. Czylkowski, B. Hrycak, M. Jasiński, M. Dors and J. Mizeraczyk, Eur. Phys. J. D, 2017, 71, 321 CrossRef
. - C. Du, J. Mo, J. Tang, D. Huang, Z. Mo, Q. Wang, S. Ma and Z. Chen, Appl. Energy, 2014, 133, 70–79 CrossRef CAS
. - B. Ulejczyk, Ł. Nogal, M. Młotek and K. Krawczyk, Energy, 2019, 174, 261–268 CrossRef CAS
. - Y. Xin, B. Sun, X. Zhu, Z. Yan, X. Zhao, X. Sun and T. Ohshima, Int. J. Hydrogen Energy, 2020, 45, 1588–1596 CrossRef CAS
. - R. Rincón, A. Marinas, J. Muñoz and M. D. Calzada, Int. J. Hydrogen Energy, 2014, 39, 11441–11453 CrossRef
. - M. Jiménez, R. Rincón, A. Marinas and M. D. Calzada, Int. J. Hydrogen Energy, 2013, 38, 8708–8719 CrossRef
. - B. Hrycak, D. Czylkowski, R. Miotk, M. Dors, M. Jasinski and J. Mizeraczyk, Int. J. Hydrogen Energy, 2014, 39, 14184–14190 CrossRef CAS
. - Y.-F. Wang, Y.-S. You, C.-H. Tsai and L.-C. Wang, Int. J. Hydrogen Energy, 2010, 35, 9637–9640 CrossRef CAS
. - R. Rincón, J. Muñoz, F. J. Morales-Calero, J. Orejas and M. D. Calzada, Appl. Energy, 2021, 294, 116948 CrossRef
. - D. Czylkowski, B. Hrycak, M. Jasiński, M. Dors and J. Mizeraczyk, Int. J. Hydrogen Energy, 2018, 43, 21196–21208 CrossRef CAS
. - N. Bundaleska, D. Tsyganov, R. Saavedra, E. Tatarova, F. M. Dias and C. M. Ferreira, Int. J. Hydrogen Energy, 2013, 38, 9145–9157 CrossRef CAS
. - T. Durka, G. D. Stefanidis, T. Van Gerven and A. I. Stankiewicz, Int. J. Hydrogen Energy, 2011, 36, 12843–12852 CrossRef CAS
. - R. Rincón, A. Marinas, J. Muñoz, C. Melero and M. D. Calzada, Chem. Eng. J., 2016, 284, 1117–1126 CrossRef
. - W. Guo, X. Zheng, Z. Qin, Q. Guo and L. Liu, ACS Omega, 2021, 6, 33533–33541 CrossRef CAS PubMed
. - F. M. Dias, N. Bundaleska, J. Henriques, E. Tatarova and C. M. Ferreira, J. Phys.: Conf. Ser., 2014, 516, 012002 CrossRef
. - W.-H. Chen, T.-C. Cheng and C.-I. Hung, Int. J. Hydrogen Energy, 2011, 36, 333–344 CrossRef CAS
. - D. Czylkowski, B. Hrycak, R. Miotk, M. Jasiński, M. Dors and J. Mizeraczyk, Int. J. Hydrogen Energy, 2015, 40, 14039–14044 CrossRef CAS
. - R. Miotk, B. Hrycak, D. Czylkowski, M. Dors, M. Jasinski and J. Mizeraczyk, Plasma Sources Sci. Technol., 2016, 25, 035022 CrossRef
. - W. Deng, S. Liu, J. Ma and Y. Su, Int. J. Hydrogen Energy, 2018, 43, 15762–15772 CrossRef CAS
. - R. W. Howarth, Energy Sci. Eng., 2014, 2, 47–60 CrossRef CAS
. - M. Saunois, A. R. Stavert and B. Poulter, et al., Earth Syst. Sci. Data, 2020, 12, 1561–1623 CrossRef
. - M. Keller, A. Matsumura and A. Sharma, Chem. Eng. J., 2020, 398, 125612 CrossRef CAS
. - S. T. Wismann, J. S. Engbæk, S. B. Vendelbo, F. B. Bendixen, W. L. Eriksen, K. Aasberg-Petersen, C. Frandsen, I. Chorkendorff and P. M. Mortensen, Science, 2019, 364, 756–759 CrossRef CAS PubMed
. - B. J. Leal Pérez, J. A. Medrano Jiménez, R. Bhardwaj, E. Goetheer, M. van Sint Annaland and F. Gallucci, Int. J. Hydrogen Energy, 2021, 46, 4917–4935 CrossRef
. - H. Zhang, W. Wang, X. Li, L. Han, M. Yan, Y. Zhong and X. Tu, Chem. Eng. J., 2018, 345, 67–78 CrossRef CAS
. - D. J. Wilhelm, D. R. Simbeck, A. D. Karp and R. L. Dickenson, Fuel Process. Technol., 2001, 71, 139–148 CrossRef CAS
. - I. K. Stoll, N. Boukis and J. Sauer, Chem. Ing. Tech., 2020, 92, 125–136 CrossRef CAS
. - E. Meloni, M. Martino, A. Ricca and V. Palma, Int. J. Hydrogen Energy, 2021, 46, 13729–13747 CrossRef CAS
. - H. Zhang, Z. Sun and Y. H. Hu, Renewable Sustainable Energy Rev., 2021, 149, 111330 CrossRef CAS
. - A. P. E. York, T. Xiao and M. L. H. Green, Top. Catal., 2003, 22, 345–358 CrossRef CAS
. - R. K. Singha, A. Shukla, A. Yadav, L. N. Sivakumar Konathala and R. Bal, Appl. Catal., B, 2017, 202, 473–488 CrossRef CAS
. - K. T. Dinh, M. M. Sullivan, P. Serna, R. J. Meyer, M. Dincă and Y. Román-Leshkov, ACS Catal., 2018, 8, 8306–8313 CrossRef CAS
. - M. Usman, W. M. A. Wan Daud and H. F. Abbas, Renewable Sustainable Energy Rev., 2015, 45, 710–744 CrossRef CAS
. - N. A. K. Aramouni, J. G. Touma, B. A. Tarboush, J. Zeaiter and M. N. Ahmad, Renewable Sustainable Energy Rev., 2018, 82, 2570–2585 CrossRef CAS
. - W.-J. Jang, J.-O. Shim, H.-M. Kim, S.-Y. Yoo and H.-S. Roh, Catal. Today, 2019, 324, 15–26 CrossRef CAS
. - T. Keipi, H. Tolvanen and J. Konttinen, Energy Convers. Manage., 2018, 159, 264–273 CrossRef CAS
. - H. Kim and J. Kim, Energies, 2021, 14, 6451 CrossRef CAS
. - A. L. García-Lario, G. S. Grasa and R. Murillo, Chem. Eng. J., 2015, 264, 697–705 CrossRef
. - L. Li, K. Yan, J. Chen, T. Feng, F. Wang, J. Wang, Z. Song and C. Ma, Sci. Total Environ., 2019, 657, 1357–1367 CrossRef CAS PubMed
. - L. S. Gangurde, G. S. J. Sturm, M. J. Valero-Romero, R. Mallada, J. Santamaria, A. I. Stankiewicz and G. D. Stefanidis, Chem. Eng. Process., 2018, 127, 178–190 CrossRef CAS
. - D. Czylkowski, B. Hrycak, M. Jasiński, M. Dors and J. Mizeraczyk, Energy, 2016, 113, 653–661 CrossRef CAS
. - Q. Wang, J. Wang, T. Zhu, X. Zhu and B. Sun, Int. J. Hydrogen Energy, 2021, 46, 34105–34115 CrossRef CAS
. - A. Domínguez, Y. Fernández, B. Fidalgo, J. J. Pis and J. A. Menéndez, Energy Fuels, 2007, 21, 2066–2071 CrossRef
. - B. Fidalgo, A. Domínguez, J. J. Pis and J. A. Menéndez, Int. J. Hydrogen Energy, 2008, 33, 4337–4344 CrossRef CAS
. - L. Li, H. Wang, X. Jiang, Z. Song, X. Zhao and C. Ma, Fuel, 2016, 185, 692–700 CrossRef CAS
. - F. Zhang, Z. Song, J. Zhu, J. Sun, X. Zhao, Y. Mao, L. Liu and W. Wang, Int. J. Hydrogen Energy, 2018, 43, 9495–9502 CrossRef CAS
. - B. Fidalgo and J. A. Menéndez, Fuel Process. Technol., 2012, 95, 55–61 CrossRef CAS
. - L. Li, Z. Yang, J. Chen, X. Qin, X. Jiang, F. Wang, Z. Song and C. Ma, Fuel, 2018, 215, 655–664 CrossRef CAS
. - T. Odedairo, J. Ma, J. Chen, S. Wang and Z. Zhu, J. Solid State Chem., 2016, 233, 166–177 CrossRef CAS
. - L. Li, J. Chen, K. Yan, X. Qin, T. Feng, J. Wang, F. Wang and Z. Song, J. CO2 Util., 2018, 28, 41–49 CrossRef CAS
. - H. Nguyen, G. Pham, R. Ran, R. Vagnoni, V. Pareek and S. Liu, Catal. Sci. Technol., 2018, 8, 5315–5324 RSC
.
|
This journal is © The Royal Society of Chemistry 2023 |
Click here to see how this site uses Cookies. View our privacy policy here.