DOI:
10.1039/D2QI02237K
(Review Article)
Inorg. Chem. Front., 2023,
10, 37-48
Electrode/electrolyte additives for practical sodium-ion batteries: a mini review
Received
19th October 2022
, Accepted 18th November 2022
First published on 5th December 2022
Abstract
Electrical energy storage systems have attracted immense attention to the rapid development of intermittent renewable energy sources. Lithium-ion batteries (LIBs) have achieved unbelievable success, having been applied in mobile electronic devices for the last few decades and conquered the electric vehicles market. However, the cost of lithium is increasing, and its availability, in the long run, is a big question. In this line, a variety of systems beyond LIBs are proposed. Amongst them, sodium-ion batteries (SIBs) stand out owing to the sodium resources and the similar kind of “rocking chair” mechanism compared with LIBs. The development of cathodes and anodes for SIBs has reached a bottleneck. For practical applications, additives are vital and are the most effective and economical methods for enhancing the actual performances of batteries. In addition, additives also can improve the safety of SIBs remarkably. In general, electrolyte additives are widely explored owing to their ability to stabilize the formation of the solid electrolyte interphase (SEI) and the cathode electrolyte interphase (CEI). At the same time, the formation of SEI and CEI layers needs abundant Na ions during the charge–discharge process. A small amount of suitable additive can bring vast, salient benefits to SIBs. Thus, this review focuses not only on the role of electrolyte additives with the properties of the formation of stable SEI and CEI but also on improving the cycling life, thermal stability, and safety.
1. Introduction
It is widely acknowledged that gaseous emissions from the applications of fossil fuels result in air pollution, ecological damage, and global warming.1–4 Hence, alternative energy sources, such as solar radiation, wind, and tide, have attracted much attention because these energy sources are renewable and eco-friendly.5–8 These energy sources are limited in time and space due to the day and night cycle and the unstable climate, leading to the requirement for energy storage.9–11 The development of electrical energy storage (EES) systems makes the storage of these indirect sources feasible.12,13 Prof. Whittingham performed the early research on lithium-ion batteries (LIBs) back in 1975, but the commercial LIB era in the field of large grid storage systems originated in 1991. LIBs with LiCoO2 as the positive electrode and petroleum coke as the negative electrode were produced by the SONY and Asahi Kasei team, which promoted the commercialization of LIBs. Recently, LIBs achieved great success by virtue of their high energy density and long lifetime.14–20 Even though the cost of lithium is increasing rapidly due to its uneven distribution and the lack of resources, the demand for LIBs for consumer electronics, communication, computers and electrified vehicles is still growing rapidly.21–26
The high-quality lithium resources in the world are mostly distributed in Australia and South America, where there may be political issues. In addition, the price of lithium resources has been increasing in recent years, reaching almost dozens of times that of sodium resources. With the increasing pressure owing to the geopolitical and ethical concerns about lithium resources, batteries other than LIBs, such as sodium-ion batteries (SIBs), potassium-ion batteries (KIBs), zinc-ion batteries (ZIBs), magnesium-ion batteries (MIB), aluminum-ion batteries (AIBs) and so on, have attracted considerable attention in the recent past.27–34 Among these batteries, SIBs stand out owing to the similar “rocking-chair” charging and discharging mechanisms compared with LIBs and the abundance and low cost of sodium.35,36 In addition, the standard electrode potential of Na/Na+ (−2.71 V vs. SHE) is similar to that of Li/Li+ (−3.04 V vs. SHE), which results in similar voltage windows.37 Using an aluminum collector for both the anode and cathode for SIBs makes the system cheaper and lighter than LIBs compared with a copper collector for the anode.38 Although the intercalation reactions are very similar for both LIBs and SIBs, graphite serves as a state-of-the-art anode for LIBs but fails to accommodate the Na ions due to the poor thermodynamic stability of the Na-based binary graphite intercalation compound. As a result, graphite is unfit for SIBs via conventional intercalation processes using ester-based solvents. However, solvent-co-intercalation is certainly possible for Na ions using ether-based solvents, which results in the formation of a ternary graphite intercalation compound.39–43 Hence, hard carbon (HC) was reported as an efficient insertion host for Na ions and has been widely accepted as the carbonaceous anode for fabricating high-energy-density SIBs. Although LIBs have been applied in diverse fields, the first-generation main components of a battery are a cathode, an anode, an electrolyte, and a separator. The additives are vital to improving electrochemical performance, safety, conductivity, mechanical properties, and so on for practical applications.48,49 The additives are widely known as the simplest, most effective, and most economical methods for enhancing the actual performances of batteries. Although the additives used in the electrolyte are reported in a few reviews, the additives used in the cathode and anode are not reported. In general, the additives used in electrolytes stabilize the formation of the solid electrolyte interphase (SEI) and the cathode electrolyte interphase (CEI) to enhance the electrochemical performance of the batteries and subsequently improve cell safety.50–53 There are many fundamental requirements for the SEI layer, such as providing a path for ion transfer, protecting electrodes from solvent molecules and being stable during the charge-discharge processes. Similar to the SEI layer, the purpose of CEI are to prevent the dissolution of active material into the electrolyte and suppressing the further oxidation of electrolyte components. It is widely acknowledged that the formation of the SEI and other irreversible side reactions will reduce the reversible capacity of the batteries.54–56 The removal of lithium/sodium ions from the electrolyte and cathode will result in a low coulombic efficiency (CE), inferior capacity and poor energy density and mean cycling stability of the cell. Therefore, the sodium compensation strategy is suggested to address this problem. On the lab scale, electrochemical and direct metal foil contacting electrodes (spontaneous sodiation) are the two main procedures employed for the pretreatment of electrodes.57–60 For practical and large-scale applications, the incorporation of sodium or lithium powder into an anode, cathode pretreatment, and cathode self-sacrificial additives are three main approaches that are widely used.61 Among these methods, the cathode self-sacrificial additive method attracts great attention by virtue of its easy operation. Hence, adding a sacrificing electrode material as an additive is one of the most efficient methods to supply extra ions.62–65 As discussed above, the electrolyte, the SEI and the CEI are important for SIBs, which may affect the capacity, rate performance, safety and so on. The evolution and development of rechargeable batteries are shown in Fig. 1. It is expected that the green energy and practical batteries can make the Earth green.
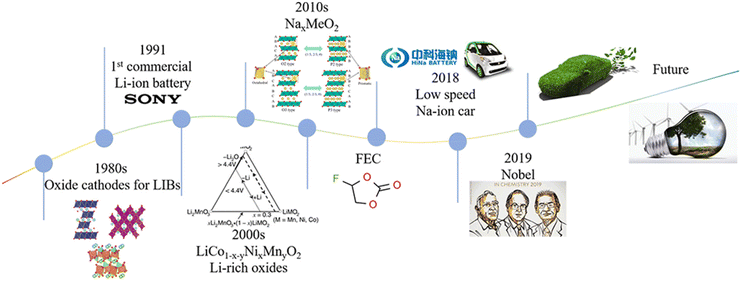 |
| Fig. 1 The schematic illustration of the development of LIB and SIB timelines.38,44–47 | |
This review focuses on not only the additives used in the electrolyte but also the sacrificial additives used in the electrode materials. At the same time, this review pays attention to the accessible capacity, rate performance, long-cycle performance, safety, and cost. The demand for LIBs has caused an unprecedented boom which has led to the rapidly rising price of lithium and calls for better replacements like SIBs. Besides studying the suitable cathodes, anodes, and electrolytes for assembling the batteries, exploring various additives is also crucial. We hope this critical review can bring more insights into such additives.
2. Basic requirements for additives
The actual requirements for additives are excellent reversible capacity, outstanding cycling performance, good safety, and inexpensiveness. From the most basic concept of the electrolyte, the lowest unoccupied molecular orbital (LUMO) and the highest occupied molecular orbital (HOMO) are the two most important factors (Fig. 2).1,50 The energy separation (Eg) of the LUMO and HOMO is the optimal operating “window” of the electrolyte, which means to ensure the stability of the cell, the energy level of the cathode (μC) should be lower than the LUMO and the energy level of the anode (μA) should be higher than the HOMO. Under these circumstances, the inevitable side reactions can be minimized during the cell operation. However, the energy levels of most anode materials are higher than that of the LUMO. In addition, the cathode, anode, and electrolyte will keep changing during the cycling processes, resulting in changes in energy levels and side reactions. Hence, additives used in the electrolyte are essential for forming a superior electrode/electrolyte interphase on the cathode and anode. It is expected that the LUMO energy of an additive is lower than that of the salts and solvents to be consumed first for forming the SEI layers and regulating their properties. The SEI and CEI layers must provide efficient pathways for Na+ ion transfer during the processes of sodiation and desodiation process. It is also important that the SEI and CEI layers can work as barriers to protect the electrodes from solvent molecule attack and subsequent dissolution into the electrolyte. During the charge and discharge processes, the SEI layers must be stable during the change in the unit-cell volume. In addition, the HOMO energy of the additive needs to be higher than that of the electrolyte for forming the CEI layers and controlling the quality of the passivation layer.66
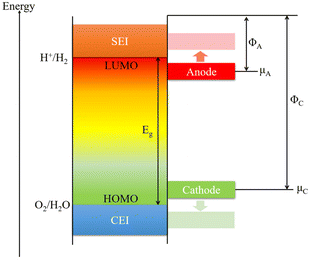 |
| Fig. 2 The schematic illustration of the open-circuit energy of the electrolyte. The energy level of the anode and cathode are, μA and μC, respectively; ΦA and ΦC are the anode and cathode work functions; Eg is the window of the electrolyte for thermodynamic stability. | |
During the initial charge process, the formation of SEI layers will irreversibly consume partial sodium ions from the electrolyte and cathode. Adding sacrificing electrode materials is an acceptable way to generate excess sodium ions. But for practical applications, there are several requirements such as low cost, simple operation, non-toxic, non-flammable, moderate operating voltage, and so on. First, the additives should be readily decomposed to generate excessive Na-ions. Second, the molecular weight should be as small as possible, and capacity utilization should be high to improve the specific energy.67 These basic requirements for compensating additives are shown in Fig. 3.
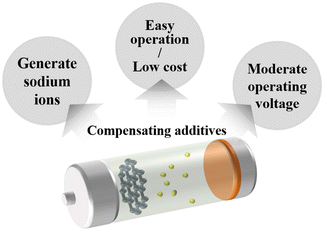 |
| Fig. 3 The basic requirements for compensating additives. | |
3. Electrolyte additives
The most extensively explored electrolyte additive is fluoroethylene carbonate (FEC). FEC manipulates the stable and robust SEI formation and enhances the cycling performance of SIBs. The FEC can be preferentially reduced to form SEI layers to prevent the main electrolyte constituents from continued consumption during cycling. Besides, the SEI layers also need to provide a pathway for the migration of sodium ions and prevent the release of electrode particles. Komaba et al.45 studied several additives for SIBs, which are well-established from LIB perspectives, such as FEC, difluoroethylene carbonate (DFEC), ethylene sulfite (ES), and vinylene carbonate (VC). Amongst them, FEC showed the best electrochemical performance and the capacity retention rate was greatly enhanced as shown in Fig. 4a. It is widely acknowledged that the energy of Na–graphite is unstable in conventional carbonate ester-based electrolytes, resulting in Na-ions being hard to intercalate into graphite. Stevens and Dahn68 reported that hard carbon (HC) could be used as a prospective anode material for SIBs. In such a process, glucose was pyrolyzed to 1000 °C and it exhibited high reversible capacity as shown in Fig. 4b. However, the reversibility of HC, which is wholly related to the precursor, particle size, pore size, distribution, and preparation technology, is the main problem needing to be addressed. Komaba's group69 has reported that stable SEI layers could be formed on the surface of HC with the addition of FEC. In addition, it is established that the performances of cathode materials can be significantly impacted by FEC as shown in Fig. 4c. The addition of FEC is beneficial for forming stable CEI layers on the surface of both layered oxides and polyanionic compounds. Such CEI layers can suppress the continued oxidation of the main electrolyte components and inhibit the dissolution of the active material into the electrolyte. Hence, FEC is a good additive for improving the performances of SIBs. Some other co-additives are used along with FEC for achieving extended electrochemical activities; for example, Choi's group70 reported that the combination of FEC and tris(trimethylsilyl)phosphite (TMSP) with Sn4P3 anodes exhibits good capacity retention characteristics (Fig. 4d). They revealed that there are several functions of this binary additive combination such as forming a protective surface film, alleviating electrolyte decomposition and preventing the formation of the Na15Sn4 phase. The FEC additive can create a NaF-rich SEI layer and the TMSP additive can eliminate HF from the electrolyte decomposition.
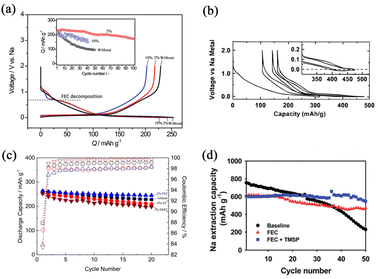 |
| Fig. 4 (a) Initial charge–discharge curves of HC electrodes without FEC, with 2% FEC and with 10% FEC. The inset shows the cycling performances. Reproduced with permission.45 Copyright 2011, American Chemical Society. (b) Charge–discharge potential profiles for glucose pyrolyzed to 1000 °C. Reproduced with permission.68 Copyright 2000, Electrochemical Society. (c) Cycling performances of HC electrodes with 1% FEC, with free additive, with 1% VC and with 1% DFEC. Reproduced with permission.69 Copyright 2016, Wiley. (d) Cycling performances of Sn4P3 electrodes without additive, with FEC, and with FEC and TMSP. Reproduced with permission.70 Copyright 2015, The Royal Society of Chemistry. | |
The VC, another well-known film-forming additive for LIBs, has also been studied from the SIB perspective. Dahbi et al.71 investigated the effect of FEC and VC additives on black phosphorus electrodes. They revealed that stable SEI layers consisting of mainly organic species could be formed by adding VC, whereas the SEI layers formed in the presence of FEC alone consist of mainly inorganic species, as shown in Fig. 5b. A large number of organic fragments was observed in the electrolyte with VC additives, such as m/z = 55(C5H7+), 57(C4H9+), 67(C5H7+), 69(C5H9+), 71(C5H11+) and 83(C6H11+) as shown in Fig. 5c. In addition, a small number of inorganic components was also observed, such as m/z = 59(Na3F2+) and 81(Na3CO3+). Such results prove that the SEI layers in the electrolyte with VC additives are composed of inorganic and organic moieties. These compounds play significant roles as the components of SEI layers for preventing the active material from dissolving and improving the electrochemical performances. Chen et al.72 introduced VC as an additive to the ether-based electrolyte to extend the electrochemical stability window. It is revealed in Fig. 5d that the HOMO energy of VC is similar to that of NaCF3SO3-diglyme (DGM), synergistically oxidized with DGM to form an undivided CEI layer on the cathode. Such a CEI layer enhances the oxidation stability of ether-based electrolyte solutions by preventing further decomposition of the electrolyte as shown in Fig. 5e.
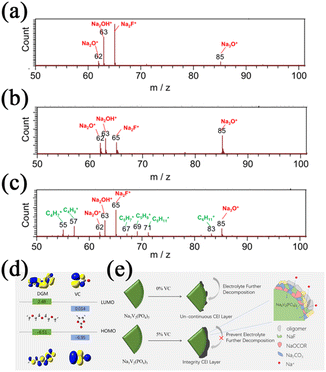 |
| Fig. 5 TOF-SIMS positive ion spectra after two cycles (a) without additive; (b) with FEC; and (c) with VC. Reproduced with permission.71 Copyright 2016, American Chemical Society. (d) The HOMO and the LUMO energy levels of DGM and VC. (e) The schematic illustration of the function of the VC additive on the surface of the Na3V2(PO4)3 electrodes. Reproduced with permission.72 Copyright 2021, Elsevier. | |
Except for these additives, many other additives have also been studied, such as sodium bis(fluorosulfonyl)imide (NaFSI), sodium bis(trifluoromethanesulfonyl)imide (NaTFSI), potassium bis(trifluoromethylsulfonyl)imide (KTFSI), N,N-bis(trifluoromethylsulfonyl)aniline (PTFSI), succinic anhydride (SA) and so on. Wang et al.73 proved that NaFSI can improve the cycling performance by enhancing interaction between the cations and the solvent molecules, besides its inherent fire-extinguishing properties, which contribute to the safety of SIBs (Fig. 6a). Chou's group74 developed a non-flammable (Fig. 6b) electrolyte consisting of sodium NaTFSI, TMP, bis(2,2,2trifluoroethyl) ether (BTFE) and VC in the molar ratio of 0.53
:
1
:
1.5
:
0.15. BTFE is used as a diluent to reduce the viscosity and improve the ionic conductivity of the electrolyte. It is critical that the solvated structure destroyed by BTFE can be recovered by the polar additive VC by reducing the free TMP molecules. As discussed above, VC also can facilitate the formation of a stable SEI in this work. Owing to the stable organic–inorganic interphase formed by these additives, the cells can realize long-term cycling stability as exhibited in Fig. 6c. Wang's group75 introduced potassium bis(trifluoromethylsulfonyl)imide (KTFSI) as a bifunctional electrolyte additive. They reported that K+ and TFSI− can cooperate to enhance the electrochemical performances as shown in Fig. 7. Under the electrostatic shielding of K+ cations, Na dendrite formation can be prevented. The TFSI− anions can promote the formation of an SEI layer containing sodium nitride and oxynitrides. PTFSI is similar to those additives, which can form a stable SEI layer (Fig. 8a).76
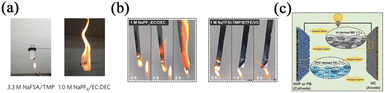 |
| Fig. 6 (a) Flammability tests of 3.3 M NaFSA/TMP and 1.0 M NaPF6/EC : DEC. Reproduced with permission.73 Copyright 2018, Springer Nature. (b) Flammability tests of 1 M NaPF6-EC/DEC and 1.2 M NaTFSI-TMP/BTFE/VC. (c) The schematic illustration of the formation of the CEI and SEI in the 1.2 M NaTFSI-TMP/BTFE/VC electrolyte. Reproduced with permission.74 Copyright 2021, Wiley. | |
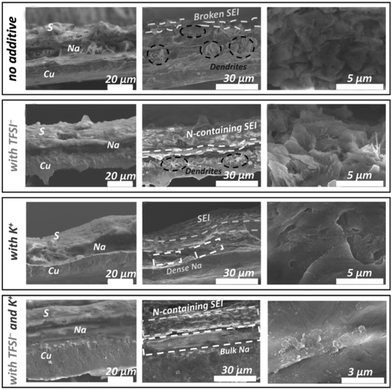 |
| Fig. 7 A comparison of the different conditions of electrochemical Na deposition and removal of the Cu current collector with NaTFSI, KOTf, and KTFSI in the electrolyte. Reproduced with permission.75 Copyright 2018, Wiley. | |
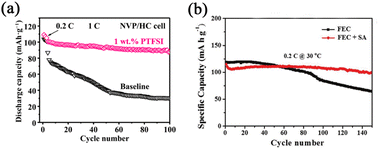 |
| Fig. 8 (a) Cycling performance of NVP/HC full cells with 1 wt.% PTFSI and without additive. Reproduced with permission.76 Copyright 2022, Tsinghua University Press. (b) Cycling performance of Na/NLNMC cells in FEC containing electrolyte without and with SA. Reproduced with permission.77 Copyright 2021, Wiley. | |
The SA was also investigated as a synergistic co-additive to FEC by Sun's group.77 It is reported that a uniform and stable SEI layer formation is evident (Fig. 8b). Furthermore, the CO2 generation of cells is alleviated by adding SA, which means it can suppress the decomposition of electrolytes during cycling. Less CO2 generation is vital in practical applications of cell safety.
Safety-related concerns are also critical in assessing and appraising SIBs in actual large-scale applications. In this regard, additives with the properties of thermal stability and safety receive great attention. Biphenyl (BP), as one of the well-known overcharge protection additives of LIBs, was selected by Feng et al.78 as an overcharge protection additive for SIBs. BP can be electro-polymerized at 4.3 V, as shown in Fig. 9a, to protect the batteries from overcharging, and it can consume the overcharge current. Trimethyl phosphate (TMP), a widespread industrial fire retardant, was studied by Wang et al.79 as a good non-flammable additive. TMP may hinder the combustion chain branching reactions by scavenging the hydrogen radicals of the gas phase. Fang's group80 investigated four different nonflammable additives, including TMP, tri(2,2,2-trifluoroethyl) phosphite (TFEP), dimethyl methylphosphonate (DMMP), and methyl nonafluorobutyl ether (MFE) for SIB applications. They reported that a non-flammable MFE-based electrolyte used with Prussian blue cathode and carbon nanotube anode exhibits the best performance among other additives. Feng et al.81 also showed that introducing 5 wt.% EFPN into a 1 M NaPF6/EC–DEC solution can make the electrolyte non-flammable, as shown in Fig. 9b. However, these additives have many problems such as low ionic conductivity, high viscosity, low flash points, negative effect on the electrode and so on. More attention must be attracted to addressing these issues.
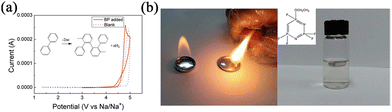 |
| Fig. 9 (a) CV curves of 1 M NaPF6 in EC/DEC with and without 3% BP. The inset shows the overcharge protection mechanism of BP. Reproduced with permission.78 Copyright 2015, The Royal Society of Chemistry. (b) Flammability tests of 1 M NaPF6/EC–DEC with and without 5% EFPN. Reproduced with permission.81 Copyright 2015, The Royal Society of Chemistry. | |
Compared with the additives for LIBs, the studies of additives in the electrolyte for SIBs are still in the early stages. Although the accumulated knowledge from LIBs can guide the additives for SIBs, it is worth mentioning that the additives explored for LIBs are not necessarily beneficial for SIBs. Furthermore, it is time to pay attention to the additives for SIBs in the electrolyte due to the uneven distribution of Li resources combined with the high cost. It is also highly desirable to study novel electrolyte additives to enhance the electrochemical performances (cycling stability, reversible capacity, rate performance, safety, and so on) of SIBs.
4. Compensating additives
Electrolyte additives are introduced for stabilizing the SEI and CEI layers, while forming such layers needs to consume a number of Na-ions during the charge–discharge process. Hence, compensating additives is a promising way to address this problem. Some compensating additives have been introduced and reported, such as NaN3, Na3P, Na2O2, Na2NiO2, Na2CO3, Na2C2O4, and NaCrO2. It is expected that more compensating additives can be studied, which can be applied in practical SIBs in the future.
Singh et al.82 used NaN3 as a sacrificial salt to solve the issue of sodium deficiency. With the addition of 5 wt.% NaN3 in the cathode, the first cycle of irreversible capacity loss can be significantly improved by 50% as shown in Fig. 10a and b. However, NaN3 is an insulator at room temperature with a high band gap, leading to low conductivity and leaving large pores in the foil. Hence, Zhang et al.83 reported that the use of Na3P as an additive shows the closest capacity compared with Na metal. With the addition of Na3P, the reversible capacity and energy density show substantial increases of more than 10%, as shown in Fig. 10c and d. It is also regrettable that Na3P readily reacts with water or an acid to form toxins, which is bad for practical production. Guo's group84 prepared a Na2O2 (Na2O2 Alfa 95%)-containing acetonitrile (ACN) slurry for dispersing on the surface of the electrode (Fig. 11a). EDS mapping clearly shows the different layers (Fig. 11b). As a result, the stable SEI layer can be formed by the addition of Na2O2. There is no adverse effect on the electrochemical performance of the cathode.
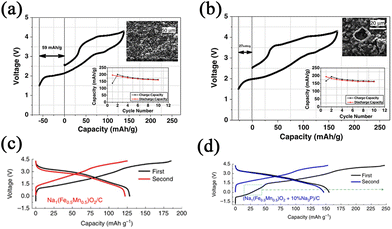 |
| Fig. 10 Initial charge–discharge curves of Na2/3Fe1/2Mn1/2O2 (a) without NaN3 and (b) with NaN3. The insets show the cycling performances and SEM micrographs after 10 cycles. Reproduced with permission.82 Copyright 2013, Elsevier. (c) Initial charge–discharge curves of P′2-Na1Fe0.5Mn0.5O2 made by Na ball milling. (d) Initial charge–discharge curves of P′2-Na1Fe0.5Mn0.5O2/Na3P. Reproduced with permission.83 Copyright 2016, Springer Nature. | |
 |
| Fig. 11 (a) Schematic diagram of preparing the electrode. (b) SEM image of the Na2O2/KB electrode and EDS mapping. Reproduced with permission.84 Copyright 2021, American Chemical Society. | |
Na2CO3, Na2NiO2, and Na2C4O4 are also studied owing to their high theoretical capacity. Considering Na2CO3 is eco-friendly and chemically stable in air, Ma's group85 explored Na2CO3 as compensating additive. The addition of 32 wt.% Na2CO3 shows the best electrochemical activity (Fig. 12a), but a concentration of more than 30% is unacceptable for practical applications. Li2NiO2, in which Li extraction induces a structural collapse, has also been reported as a sacrificing positive additive.67 Similarly, Goodenough's group86 characterized the chemical and electrochemical performances of Na2NiO2 as a compensating additive for SIBs. During electrochemical oxidation, Na2NiO2 can be converted into NaNiO2 and Na+ ions with a voltage plateau of about 2.1 V. The extra Na+ ions can be supplied to compensate for irreversible Na+ loss during the formation of the passivation layer. In addition, the reversible cathode capacity is increased by 23.5%, as illustrated in Fig. 12b. A NaCrO2 cathode with NaNiO2 shows better cycling stability than pure NaCrO2 cathode (Fig. 12c). It is reported by Armand et al.87 that the Na2C4O4 additive is safe, environmentally benign, and cost-effective and can provide extra specific capacity of 256 mAh g−1. Na2C4O4 can decompose at 3.6 V to supply Na+ ions and liberate CO2. The rate capability and galvanostatic cycling performances are shown in Fig. 12d, and the addition of Na2C4O4 benefits the formation of a stable SEI layer, resulting in improved capacity retention. Compared to NaN3 with the flake-like morphology, Na2C4O4 with the fibrous network can be evenly distributed on the electrode surface.
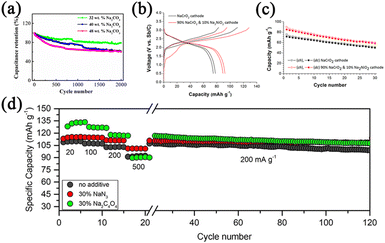 |
| Fig. 12 (a) Cycling performances of different contents of Na2CO3. Reproduced with permission.85 Copyright 2021, Elsevier. (b) Initial charge–discharge curves of the NaCrO2 cathode with and without NaNiO2. (c) Cycling performances of the NaCrO2 cathode with and without NaNiO2. Reproduced with permission.86 Copyright 2015, American Chemical Society. (d) Rate capability and galvanostatic cycling of NVOPF without the additive, with 30% NaN3 and with 30% Na2C4O4. Reproduced with permission.87 Copyright 2018, Wiley. | |
However, the capacity utilization of Na2CO3, Na2NiO2, and Na2C4O4 is 20, 40, and 70%, respectively, which is unsatisfactory. In terms of capacity utilization, NaCrO2 was reported by Xu et al.88 After NaCrO2 releases the inner Na-ions, the electrochemical activity of NaCrO2 will be lost, which will not affect the electrochemical performances of the battery. Fig. 13a and b demonstrates that the full cell with NaCrO2 shows 90 mAh g−1 with a capacity retention of 80% after 50 cycles and enhanced energy density. The capacity utilization of NaCrO2 is close to 93%. However, the irreversible capacity of NaCrO2 is just 230 mAh g−1, but the toxicity of Cr limits further exploration. Guo's group89 reported Na2C2O4 as an additive with high theoretical capacity (400 mAh g−1) and capacity utilization (99%). Intending to solve the problem of the higher oxidation potential, they matched Na2C2O4 with an appropriate conductive additive that has a large specific surface area. As a result, the oxidation potential is reduced from 4.41 to 3.97 V, near the charging potential of the positive electrodes. As shown in Fig. 13c, the full cell with Na2C2O4 exhibits the initial specific discharge capacity of 99 mAh g−1. In addition, the capacity retention of the full cell is as high as 90% after 50 cycles (Fig. 13d).
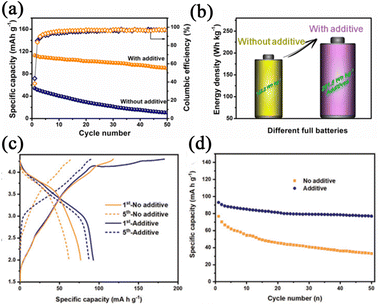 |
| Fig. 13 (a) Cycling performances of full cells with and without additives. (b) Comparison of the energy density of full cells with and without additives. Reproduced with permission.88 Copyright 2019, Elsevier. (c) Charge–discharge profiles of full cells with and without Na2C2O4. (d) Cycling performance at 0.2 C. Reproduced with permission.89 Copyright 2020, Wiley. | |
As discussed above, these compensating additives still have inherent problems that need to be addressed. The research activities on compensating additives are similar to those of electrolyte additives. Although the cost of SIBs is lower than that of LIBs, the issues of SIBs are worse than those of LIBs. Hence, the addition of compensating additives is considered one of the best ways to address the problems to improve the electrochemical performances.
5. Summary and prospects
In summary, electrolyte and compensating additives have a significant influence on the reversibility, cycling stability, rate performance, thermal stability, and of course, safety of SIBs. A comparison table of the electrolyte/electrode additives for SIBs is shown in Table 1. For electrolyte additives, FEC with suitable LUMO and HOMO energies is one of the best candidates for manipulating the SEI and CEI formations and enhancing the electrochemical performance. Compensating additives like Na2C2O4 may be good ones with high theoretical capacity and capacity utilization. However, it is regrettable that the research on these additives is based on the results of LIBs. In addition, the anionic oxygen redox reaction has attracted more attention because it can provide extra capacity. The electrolyte and compensating additives that fit the electrode with an anionic oxygen redox reaction are critical.
Table 1 The comparison of electrolyte/electrode additives for SIBs
Additive |
Type |
Cathode & anode |
Electrolyte |
Capacity (mAh g−1) |
Retention rate (capacity increase) |
Ref. |
FEC |
Electrolyte additive |
NaNi1/2Mn1/2O2/hard carbon |
1 M NaClO4 in PC |
245 |
+35% (50 cycles) |
45
|
FEC |
Electrolyte additive |
Hard carbon/Na |
1 M NaPF6 in PC |
250 |
+45% (80 cycles) |
69
|
FEC + TMSP |
Electrolyte additive |
Sn4P3/Na |
1 M NaClO4 in EC/PC (1 : 1) |
852 |
+70% (50 cycles) |
70
|
FEC (5%) |
Electrolyte additive |
Black P/Na |
1 M NaPF6 in EC/DEC (1 : 1) |
1587 |
+30% (25 cycles) |
71
|
VC (1%) |
|
|
|
1615 |
+30% (25 cycles) |
|
VC |
Electrolyte additive |
Na3V2(PO4)3@C/FeS@C |
1 M NaCF3SO3-DGM |
114.6 |
|
72
|
NaFSA |
Safety additive |
Hard carbon/Na |
3.3 M NaFSA/TMP |
230 |
+100% (1200 cycles) |
73
|
NaTFSI |
Safety additive |
NVP/Na |
1.2 M NaTFSI-TMP/BTFE/VC |
100 |
|
74
|
KTFSI |
Electrolyte additive |
Na/Cu |
1 M NaOTf n TEGDME |
|
|
75
|
PTFSI |
Safety additive |
Hard carbon/Na |
1 M NaPF6 in EC/DEC (1 : 1) |
200 |
|
76
|
EFPN |
Safety additive |
Na0.44MnO2/acetylene black |
1 M NaPF6 in EC/DEC (1 : 1) |
100 |
|
81
|
NaN3 |
Compensating additive |
Na2/3Fe1/2Mn1/2O2/Na |
1 M NaClO4 in EC/PC (1 : 1) |
170 |
+32 mAh g−1 |
82
|
Na3P |
Compensating additive |
NaFe0.5Mn0.5O2/C |
1 M NaClO4 in EC/DMC (1 : 1) |
150 |
+25 mAh g−1 |
83
|
Na2O2 |
Compensating additive |
Na2/3Ni1/3Mn1/2Ti1/3O2/HC |
1 M NaPF6 in EC/DEC (1 : 1) with 5 vol.% FEC |
100 |
+35 mAh g−1 |
84
|
Na2CO3 |
Compensating additive |
Activated carbon/HC |
1 M NaClO4 in EC/PC (1 : 1) with 5 vol.% FEC |
100 |
|
85
|
Na2NiO2 |
Compensating additive |
NaCrO2/Sb@C |
1 M NaClO4 in EC/DEC (1 : 1) with 10 vol.% FEC |
90 |
+15 mAh g−1 |
86
|
Na2C4O4 |
Compensating additive |
Na3(VO)2(PO4)2F/SP@Na |
1 M NaClO4 in EC/PC (1 : 1) with 5 vol.% FEC |
120 |
+30 mAh g−1 |
87
|
NaCrO2 |
Compensating additive |
Na3(VO)2(PO4)2F/HC |
1 M NaClO4 in EC/DEC (1 : 1) with 5 vol.% FEC |
115 |
+50 mAh g−1 |
88
|
Na2C2O4 |
Compensating additive |
Na2/3Ni1/3Mn1/3Ti1/3O2/HC@SP |
1 M NaClO4 in PC with 5 vol.% FEC |
99 |
+30 mAh g−1 |
89
|
However, the research activities of SIB additives are still in the infancy stage. Based on the studies learned from LIBs, the additives show great potential in enhancing the electrochemical performance and cell safety. Hence, some thoughts on the future developmental directions of additives are given as follows:
(i) Cost is always the key issue for practical applications. Adding a small number of additives can significantly improve performance. In addition, non-toxic and simple operations are also necessary for the cost. Considering compensating additives, capacity utilization is the key to enhancing the performance at a low cost.
(ii) Energy density is one of the important points for evaluating the performances of practical SIBs. Irreversible consumption of sodium ions during cycling processes is inevitable and hence using appropriate electrolyte additives to form the SEI and CEI for reducing the ongoing consumption and adding compensating additives to compensate for the loss of sodium ions are necessary with the aim of enhancing the energy density.
(iii) Although FEC is one of the best electrolyte additives, it is incompatible with many anodes, especially heteroatom-doped carbons. New electrolyte additives should be studied for use with FEC as co-additives or replaced with FEC. Ether solvents are also desirable compounds compared with esters, which can be considered. Solid-state electrolytes (SSE) are also considered by virtue of their great mechanical strength, good thermal stability, and high security. It is reported that nonaqueous liquid electrolytes, quasi-solid-state electrolytes and all-solid-state electrolytes show outstanding performance in SIBs.
(iv) The molecular weight of compensating additives should be as small as possible; hence the additives can be easily decomposed to provide Na+ ions in the appropriate voltage range. The generation of gaseous products, such as N2, CO2, and O2, is acceptable because there is pre-charge formation in industrial production which can release those gases. But low conductivity, toxicity, and incomplete decomposition during the first cycle are unacceptable and should be thoroughly investigated. The direct sodium compensation method is also one of the acceptable appraoches for the losses owing to the irreversible consumption of sodium ions. However, the high activity of sodium metal is the major problem leading to security and cost concerns. Seeking a new sodium compensation strategy, which is smarter and cheaper, is the best thing to do now.
(v) Safety is one of the challenges in engineering the battery pack. The flammability of the electrolyte corresponds to the safety of the whole battery. The choice of electrolyte additives is based on not only the suitable LUMO and HOMO energies but also the ability to suppress the flammability.
(vi) The viscosity and dielectric constant of the solvent, which are related to the ionic conductivity, are also important. Reducing the viscosity can enhance ion migration. Weakening the dielectric constant can suppress the dissociation of electrolytes.
(vii) More and more research about cathodes for the anionic oxygen redox reaction has been reported in the recent past, which is mainly responsible for the translation of higher capacity. Hence, additives for the anionic oxygen redox reaction, which often occurs at high voltage, must be on the agenda.
Author contributions
Zhi-Xiong Huang: investigation, writing – original draft, and visualization. Xue-Li Zhang: investigation and writing – original draft. Xin-Xin Zhao: investigation and conceptualization. Yuanyuan Zhao: modification and software. Vanchiappan Aravindan: writing – review & editing. Yu-Hang Liu: modification. Hong-bo Geng: resources and supervision. Xing-Long Wu: resources, writing – review & editing, and supervision.
Conflicts of interest
There are no conflicts to declare.
Acknowledgements
This work was financially supported by the National Natural Science Foundation of China (no. 52173246), the Natural Science Foundation of Jilin Province (no. 20220508141RC), the Science and Technology Development Plan of Suzhou (ZXL2021176), Natural Science Foundation of the Jiangsu Higher Education Institutions (22KJA430009) and the 111 Project (no. B13013). VA acknowledges the financial support from the Science and Engineering Research Board, a statutory body of the Department of Science and Technology, Govt. of India, through the Start-up Research Swarnajayanti Fellowship (SB/SJF/2020-21/12).
References
- J. B. Goodenough and Y. Kim, Challenges for rechargeable Li batteries, Chem. Mater., 2010, 22, 587–603 CrossRef CAS.
- Y. Su, X. Rong, A. Gao, Y. Liu, J. Li, M. Mao, X. Qi, G. Chai, Q. Zhang, L. Suo, L. Gu, H. Li, X. Huang, L. Chen, B. Liu and Y.-S. Hu, Rational design of a topological polymeric solid electrolyte for high-performance all-solid-state alkali metal batteries, Nat. Commun., 2022, 13, 4181 CrossRef CAS.
- Y.-X. Song, Y. Shi, J. Wan, B. Liu, L.-J. Wan and R. Wen, Dynamic visualization of cathode/electrolyte evolution in quasi-solid-state lithium batteries, Adv. Energy Mater., 2020, 10, 2000465 CrossRef CAS.
- Y. Qian, S. Hu, X. Zou, Z. Deng, Y. Xu, Z. Cao, Y. Kang, Y. Deng, Q. Shi, K. Xu and Y. Deng, How electrolyte additives work in Li-ion batteries, Energy Storage Mater., 2019, 20, 208–215 CrossRef.
- J. Yue, J. Zhang, Y. Tong, M. Chen, L. Liu, L. Jiang, T. Lv, Y.-s. Hu, H. Li, X. Huang, L. Gu, G. Feng, K. Xu, L. Suo and L. Chen, Aqueous interphase formed by CO2 brings electrolytes back to salt-in-water regime, Nat. Chem., 2021, 13, 1061–1069 CrossRef CAS.
- H. Zhang, L. Huang, H. Xu, X. Zhang, Z. Chen, C. Gao, C. Lu, Z. Liu, M. Jiang and G. Cui, A polymer electrolyte with a thermally induced interfacial ion-blocking function enables safety-enhanced lithium metal batteries, eScience, 2022, 2, 201–208 CrossRef.
- J.-L. Yang, X.-X. Zhao, W.-H. Li, H.-J. Liang, Z.-Y. Gu, Y. Liu, M. Du and X.-L. Wu, Advanced cathode for dual-ion batteries: Waste-to-wealth reuse of spent graphite from lithium-ion batteries, eScience, 2022, 2, 95–101 CrossRef.
- Z. Shilin, S. Liang, F. Qining, Z. Fangli, W. Zhijie, Z. Jinshuo, Z. Shiyong, M. Jianfeng and G. Zaiping, Challenges and prospects of lithium–CO2 batteries, Nano Res. Energy, 2022, 1, e9120001 CrossRef.
- X. He, Y. Ni, Y. Hou, Y. Lu, S. Jin, H. Li, Z. Yan, K. Zhang and J. Chen, Insights into the ionic conduction mechanism of quasi-solid polymer electrolytes through multispectral characterization, Angew. Chem., Int. Ed., 2021, 60, 22672–22677 CrossRef CAS PubMed.
- Z. Tian, Y. Zou, G. Liu, Y. Wang, J. Yin, J. Ming and H. N. Alshareef, Electrolyte solvation structure design for sodium ion batteries, Adv. Sci., 2022, 9, 2201207 CrossRef CAS.
- Y. Liu, J. Li, Q. Shen, J. Zhang, P. He, X. Qu and Y. Liu, Advanced characterizations and measurements for sodium-ion batteries with NASICON-type cathode materials, eScience, 2022, 2, 10–31 CrossRef.
- G. Liu, J. Gao, M. Xia, Y. Cheng, M. Wang, W. Hong, Y. Yang and J. Zheng, Strengthening the interfacial stability of the silicon-based electrode via an electrolyte additive—Allyl phenyl sulfone, ACS Appl. Mater. Interfaces, 2022, 14, 38281–38290 CrossRef CAS.
- Y. Liang, C.-Z. Zhao, H. Yuan, Y. Chen, W. Zhang, J.-Q. Huang, D. Yu, Y. Liu, M.-M. Titirici, Y.-L. Chueh, H. Yu and Q. Zhang, A review of rechargeable batteries for portable electronic devices, InfoMat, 2019, 1, 6–32 CrossRef CAS.
- M. Armand and J. M. Tarascon, Building better batteries, Nature, 2008, 451, 652–657 CrossRef CAS PubMed.
- J. Chou, Y. Zhao, X.-T. Li, W.-P. Wang, S.-J. Tan, Y.-H. Wang, J. Zhang, Y.-X. Yin, F. Wang, S. Xin and Y.-G. Guo, Hydrogen isotope effects on aqueous electrolyte for electrochemical lithium-ion storage, Angew. Chem., Int. Ed., 2022, 61, e202203137 CrossRef PubMed.
- R. Usiskin, Y. Lu, J. Popovic, M. Law, P. Balaya, Y.-S. Hu and J. Maier, Fundamentals, status and promise of sodium-based batteries, Nat. Rev. Mater., 2021, 6, 1020–1035 CrossRef CAS.
- X. Zhang, J.-P. Hu, N. Fu, W.-B. Zhou, B. Liu, Q. Deng and X.-W. Wu, Comprehensive review on zinc-ion battery anode: Challenges and strategies, InfoMat, 2022, 4, e12306 CAS.
- T. Wang, L. Lu and C. Sun, A long life solid-state lithium–oxygen battery enabled by a durable oxygen deficient flower-like CeO2 microsphere based solid electrolyte, Inorg. Chem. Front., 2022, 9, 2508–2516 RSC.
- W. Peng, J. Zhang, S. Li, J. Liang, R. Hu, B. Yuan and G. Chen, Rationally integrated nickel sulfides for lithium storage: S/N co-doped carbon encapsulated NiS/Cu2S with greatly enhanced kinetic property and structural stability, Inorg. Chem. Front., 2022, 9, 2023–2035 RSC.
- P. Wang, Y. Song, Z. Xu, N. Li, J. Sun, B. Hong and Y. Lai, Hierarchical MoxC@NC hollow microsphere with incorporated Mo vacancies as multifunctional confined reactors for high-loading Li–S batteries, Inorg. Chem. Front., 2022, 9, 2194–2203 RSC.
- J. W. Choi and D. Aurbach, Promise and reality of post-lithium-ion batteries with high energy densities, Nat. Rev. Mater., 2016, 1, 16013 CrossRef CAS.
- J. Peng, D. Wu, F. Song, S. Wang, Q. Niu, J. Xu, P. Lu, H. Li, L. Chen and F. Wu, High current density and long cycle life enabled by sulfide solid electrolyte and dendrite-free liquid lithium anode, Adv. Funct. Mater., 2022, 32, 2105776 CrossRef CAS.
- Z.-Q. Lei, Y.-J. Guo, E.-H. Wang, W.-H. He, Y.-Y. Zhang, S. Xin, Y.-X. Yin and Y.-G. Guo, Layered oxide cathode-electrolyte interface towards Na-ion batteries: Advances and perspectives, Chem. – Asian J., 2022, 17, e202200213 CAS.
- J.-Y. Liang, X.-D. Zhang, X.-X. Zeng, M. Yan, Y.-X. Yin, S. Xin, W.-P. Wang, X.-W. Wu, J.-L. Shi, L.-J. Wan and Y.-G. Guo, Enabling a durable electrochemical interface via an artificial amorphous cathode electrolyte interphase for hybrid solid/liquid lithium-metal batteries, Angew. Chem., 2020, 132, 6647–6651 CrossRef.
- X. Yin, Z. Lu, J. Wang, X. Feng, S. Roy, X. Liu, Y. Yang, Y. Zhao and J. Zhang, Enabling fast Na+ transfer kinetics in the whole-voltage-region of hard-carbon anodes for ultrahigh-rate sodium storage, Adv. Mater., 2022, 34, 2109282 CrossRef CAS PubMed.
- W.-J. Kwak, S. Chae, R. Feng, P. Gao, J. Read, M. H. Engelhard, L. Zhong, W. Xu and J.-G. Zhang, Optimized
electrolyte with high electrochemical stability and oxygen solubility for lithium–oxygen and lithium–air batteries, ACS Energy Lett., 2020, 5, 2182–2190 CrossRef CAS.
- M. Song, H. Tan, D. Chao and H. J. Fan, Recent advances in Zn-ion batteries, Adv. Funct. Mater., 2018, 28, 1802564 CrossRef.
- J.-Z. Guo, Z.-Y. Gu, X.-X. Zhao, M.-Y. Wang, X. Yang, Y. Yang, W.-H. Li and X.-L. Wu, Flexible Na/K-ion full batteries from the renewable cotton cloth–derived stable, low-cost, and binder-free anode and cathode, Adv. Energy Mater., 2019, 9, 1902056 CrossRef CAS.
- Z. Huang, Y. Duan, Q. Jing, M. Sun, B. Tang and S. Shi, Assembly of Mn3O4 nanoparticles at low temperature on graphene with enhanced electrochemical property for zinc-ion battery, J. Alloys Compd., 2021, 864, 158316 CrossRef CAS.
- G. Wang, M. Zhu, Y. Zhang, C. Song, X. Zhu, Z. Huang, Y. Zhang, F. Yu, G. Xu, M. Wu, H.-K. Liu, S.-X. Dou and C. Wu, Double interface regulation: Toward highly stable lithium metal anode with high utilization, InfoMat, 2022, 4, e12293 CAS.
- J. Geng, C. Sun, J. Xie, H. Dong, Z. Wang, H. Wei, Y. Cheng, Y. Tian and H. Geng, Topological transformation construction of a CoSe2/N-doped carbon heterojunction with a three-dimensional porous structure for high-performance sodium-ion half/full batteries, Inorg. Chem. Front., 2022, 9, 3176–3186 RSC.
- Z. Zhang, Y. Wang, J. Guan, T. Zhang, P. Li, Y. Hao, L. Duan, Z. Niu and J. Liu, Direct conversion of solid g-C3N4 into metal-ended N-doped carbon nanotubes for rechargeable Zn–air batteries, Inorg. Chem. Front., 2022, 9, 3428–3435 RSC.
- H. Yu, L. Fan, H. Yan, C. Deng, L. Yan, J. Shu and Z.-B. Wang, Nickel ferrocyanides for aqueous ammonium ion batteries, Inorg. Chem. Front., 2022, 9, 2001–2010 RSC.
- L. Guojin, L. Xinliang, W. Yanbo, Y. Shuo, H. Zhaodong, Y. Qi, W. Donghong, D. Binbin, Z. Minshen and Z. Chunyi, Building durable aqueous K-ion capacitors based on MXene family, Nano Res. Energy, 2022, 1, e9120002 CrossRef.
- J.-Y. Hwang, S.-T. Myung and Y.-K. Sun, Sodium-ion batteries: Present and future, Chem. Soc. Rev., 2017, 46, 3529–3614 RSC.
- Z.-X. Huang, X.-L. Zhang, X.-X. Zhao, Y.-L. Heng, T. Wang, H. Geng and X.-L. Wu, Hollow Na0.62K0.05Mn0.7Ni0.2Co0.1O2 polyhedra with exposed stable {001} facets and K riveting for sodium-ion batteries, Sci. China Mater., 2022 DOI:10.1007/s40843-022-2157-8.
- Y. Marcus, Thermodynamic functions of transfer of single ions from water to nonaqueous and mixed solvents: Part 3 – Standard potentials of selected electrodes, Pure Appl. Chem., 1985, 57, 1129–1132 CrossRef CAS.
- Z.-X. Huang, Z.-Y. Gu, Y.-L. Heng, E.-H. Ang, H.-B. Geng and X.-L. Wu, Advanced layered oxide cathodes for sodium/potassium-ion batteries: Development, challenges and prospects, Chem. Eng. J., 2023, 452, 139438 CrossRef CAS.
- S. Komaba, T. Hasegawa, M. Dahbi and K. Kubota, Potassium intercalation into graphite to realize high-voltage/high-power potassium-ion batteries and potassium-ion capacitors, Electrochem. Commun., 2015, 60, 172–175 CrossRef CAS.
- W. Ling, N. Fu, J. Yue, X.-X. Zeng, Q. Ma, Q. Deng, Y. Xiao, L.-J. Wan, Y.-G. Guo and X.-W. Wu, A flexible solid electrolyte with multilayer structure for sodium metal batteries, Adv. Energy Mater., 2020, 10, 1903966 CrossRef CAS.
- Z.-Y. Gu, J.-Z. Guo, J.-M. Cao, X.-T. Wang, X.-X. Zhao, X.-Y. Zheng, W.-H. Li, Z.-H. Sun, H.-J. Liang and X.-L. Wu, An advanced high-entropy fluorophosphate cathode for sodium-ion batteries with increased working voltage and energy density, Adv. Mater., 2022, 34, 2110108 CrossRef CAS.
- W.-W. Han, R. E. A. Ardhi and G.-C. Liu, Dual impact of superior SEI and separator wettability to inhibit lithium dendrite growth, Rare Met., 2022, 41, 353–355 CrossRef CAS.
- L. Fang, C. Wang, L. Huangfu, N. Bahlawane, H. Tian, Y. Lu, H. Pan, M. Yan and Y. Jiang, Enabling full conversion reaction with high reversibility to approach theoretical capacity for sodium storage, Adv. Funct. Mater., 2019, 29, 1906680 CrossRef CAS.
- A. Manthiram, A reflection on lithium-ion battery cathode chemistry, Nat. Commun., 2020, 11, 1550 CrossRef CAS PubMed.
- S. Komaba, T. Ishikawa, N. Yabuuchi, W. Murata, A. Ito and Y. Ohsawa, Fluorinated ethylene carbonate as electrolyte additive for rechargeable Na batteries, ACS Appl. Mater. Interfaces, 2011, 3, 4165–4168 CrossRef CAS PubMed.
- K. McColl, R. A. House, G. J. Rees, A. G. Squires, S. W. Coles, P. G. Bruce, B. J. Morgan and M. S. Islam, Transition metal migration and O2 formation underpin voltage hysteresis in oxygen-redox disordered rocksalt cathodes, Nat. Commun., 2022, 13, 5275 CrossRef CAS PubMed.
- R. A. House, U. Maitra, M. A. Pérez-Osorio, J. G. Lozano, L. Jin, J. W. Somerville, L. C. Duda, A. Nag, A. Walters, K.-J. Zhou, M. R. Roberts and P. G. Bruce, Superstructure control of first-cycle voltage hysteresis in oxygen-redox cathodes, Nature, 2020, 577, 502–508 CrossRef CAS PubMed.
- H. Cheng, Q. Sun, L. Li, Y. Zou, Y. Wang, T. Cai, F. Zhao, G. Liu, Z. Ma, W. Wahyudi, Q. Li and J. Ming, Emerging era of electrolyte solvation structure and interfacial model in batteries, ACS Energy Lett., 2022, 7, 490–513 CrossRef CAS.
- J. Zhao, M. Xie, H. Zhang, R. Yi, C. Hu, T. Kang, L. Zheng, R. Cui, H. Chen, Y. Shen and L. Chen, In situ modification strategy for development of room-temperature solid-state lithium batteries with high rate capability, Acta Phys.-Chim. Sin., 2021, 37, 2104003 Search PubMed.
- G. G. Eshetu, M. Martinez-Ibañez, E. Sánchez-Diez, I. Gracia, C. Li, L. M. Rodriguez-Martinez, T. Rojo, H. Zhang and M. Armand, Electrolyte additives for room-temperature, sodium-based, rechargeable batteries, Chem. – Asian J., 2018, 13, 2770–2780 CrossRef CAS PubMed.
- L. Fang, N. Bahlawane, W. Sun, H. Pan, B. B. Xu, M. Yan and Y. Jiang, Conversion-alloying anode materials for sodium ion batteries, Small, 2021, 17, 2101137 CrossRef CAS.
- Y. Hualin and L. Yanguang, Towards practical lean-electrolyte Li–S batteries: Highly solvating electrolytes or sparingly solvating electrolytes?, Nano Res. Energy, 2022, 1, e9120012 CrossRef.
- G.-D. Yang, B. Li, Y.-H. Song, L. Ding, S.-G. Gong, X.-L. Wu, J.-P. Zhang, Y.-F. Li and H.-Z. Sun, Modifying surface of Ni foam via hierarchical lithiophilic nanoarrays for stable lithium metal anodes, Electrochim. Acta, 2022, 430, 141035 CrossRef CAS.
- S. H. Lee, J.-Y. Hwang, J. Ming, H. Kim, H.-G. Jung and Y.-K. Sun, Long-lasting solid electrolyte interphase for stable Li-metal batteries, ACS Energy Lett., 2021, 6, 2153–2161 CrossRef CAS.
- J. Wan, Z. Zuo, Z.-Z. Shen, W.-P. Chen, G.-X. Liu, X.-C. Hu, Y.-X. Song, S. Xin, Y.-G. Guo, R. Wen, Y. Li and L.-J. Wan, Interfacial evolution of the solid electrolyte interphase and lithium deposition in graphdiyne-based lithium-ion batteries, J. Am. Chem. Soc., 2022, 144, 9354–9362 CrossRef CAS.
- T. Jiao, G. Liu, Y. Zou, X. Yang, X. Zhang, A. Fu, J. Zheng and Y. Yang, A novel trimethylsilyl 2-(fluorosulfonyl)difluoroacetate additive for stabilizing the Ni-rich LiNi0.9Co0.05Mn0.05O2/electrolyte interface, J. Power Sources, 2021, 515, 230618 CrossRef CAS.
- M. Liu, J. Zhang, S. Guo, B. Wang, Y. Shen, X. Ai, H. Yang and J. Qian, Chemically presodiated hard carbon anodes with enhanced initial coulombic efficiencies for high-energy sodium ion batteries, ACS Appl. Mater. Interfaces, 2020, 12, 17620–17627 CrossRef CAS PubMed.
- J.-Y. Hwang, S.-T. Myung, J. U. Choi, C. S. Yoon, H. Yashiro and Y.-K. Sun, Resolving the degradation pathways of the O3-type layered oxide cathode surface through the nano-scale aluminum oxide coating for high-energy density sodium-ion batteries, J. Mater. Chem. A, 2017, 5, 23671–23680 RSC.
- E. de la Llave, V. Borgel, K.-J. Park, J.-Y. Hwang, Y.-K. Sun, P. Hartmann, F.-F. Chesneau and D. Aurbach, Comparison between Na-ion and Li-ion cells: Understanding the critical role of the cathodes stability and the anodes pretreatment on the cells behavior, ACS Appl. Mater. Interfaces, 2016, 8, 1867–1875 CrossRef CAS PubMed.
- J. Tang, D. K. Kye and V. G. Pol, Ultrasound-assisted synthesis of sodium powder as electrode additive to improve cycling performance of sodium-ion batteries, J. Power Sources, 2018, 396, 476–482 CrossRef CAS.
- H.-J. Liang, B.-H. Hou, W.-H. Li, Q.-L. Ning, X. Yang, Z.-Y. Gu, X.-J. Nie, G. Wang and X.-L. Wu, Staging Na/K-ion de-/intercalation of graphite retrieved from spent Li-ion batteries: In operando X-ray diffraction studies and an advanced anode material for Na/K-ion batteries, Energy Environ. Sci., 2019, 12, 3575–3584 RSC.
- Q. Li, G. Liu, H. Cheng, Q. Sun, J. Zhang and J. Ming, Low-temperature electrolyte design for lithium-ion batteries: Prospect and challenges, Chem. – Eur. J., 2021, 27, 15842–15865 CrossRef CAS PubMed.
- H. Che, X. Yang, H. Wang, X.-Z. Liao, S. S. Zhang, C. Wang and Z.-F. Ma, Long cycle life of sodium-ion pouch cell achieved by using multiple electrolyte additives, J. Power Sources, 2018, 407, 173–179 CrossRef CAS.
- J. Zheng, G. Tan, P. Shan, T. Liu, J. Hu, Y. Feng, L. Yang, M. Zhang, Z. Chen, Y. Lin, J. Lu, J. C. Neuefeind, Y. Ren, K. Amine, L.-W. Wang, K. Xu and F. Pan, Understanding thermodynamic and kinetic contributions in expanding the stability window of aqueous electrolytes, Chem, 2018, 4, 2872–2882 CAS.
- W. H. Guan, Q. Y. Lin, Z. Y. Lan, W. L. Pan, X. Wei, W. P. Sun, R. T. Zheng, Y. H. Lu, J. Shu, H. G. Pan, M. Yan and Y. Z. Jiang, Approaching the theoretical capacity limit of Na2FeSiO4-based cathodes with fully reversible two-electron redox reaction for sodium-ion
battery, Mater. Today Nano, 2020, 12, 100098 CrossRef.
- H.-J. Liang, Z.-Y. Gu, X.-X. Zhao, J.-Z. Guo, J.-L. Yang, W.-H. Li, B. Li, Z.-M. Liu, W.-L. Li and X.-L. Wu, Ether-based electrolyte chemistry towards high-voltage and long-life Na-ion full batteries, Angew. Chem., Int. Ed., 2021, 60, 26837–26846 CrossRef CAS.
- H. Park, T. Yoon, Y.-U. Kim, J. H. Ryu and S. M. Oh, Li2NiO2 as a sacrificing positive additive for lithium-ion batteries, Electrochim. Acta, 2013, 108, 591–595 CrossRef CAS.
- D. A. Stevens and J. Dahn, High capacity anode materials for rechargeable sodium-ion batteries, J. Electrochem. Soc., 2000, 147, 1271–1273 CrossRef CAS.
- M. Dahbi, T. Nakano, N. Yabuuchi, S. Fujimura, K. Chihara, K. Kubota, J.-Y. Son, Y.-T. Cui, H. Oji and S. Komaba, Effect of hexafluorophosphate and fluoroethylene carbonate on electrochemical performance and the surface layer of hard carbon for sodium-ion batteries, ChemElectroChem, 2016, 3, 1856–1867 CrossRef CAS.
- J. Y. Jang, Y. Lee, Y. Kim, J. Lee, S.-M. Lee, K. T. Lee and N.-S. Choi, Interfacial architectures based on a binary additive combination for high-performance Sn4P3 anodes in sodium-ion batteries, J. Mater. Chem. A, 2015, 3, 8332–8338 RSC.
- M. Dahbi, N. Yabuuchi, M. Fukunishi, K. Kubota, K. Chihara, K. Tokiwa, X.-f. Yu, H. Ushiyama, K. Yamashita, J.-Y. Son, Y.-T. Cui, H. Oji and S. Komaba, Black phosphorus as a high-capacity, high-capability negative electrode for sodium-ion batteries: Investigation of the electrode/electrolyte interface, Chem. Mater., 2016, 28, 1625–1635 CrossRef CAS.
- J. Shi, L. Ding, Y. Wan, L. Mi, L. Chen, D. Yang, Y. Hu and W. Chen, Achieving long-cycling sodium-ion full cells in ether-based electrolyte with vinylene carbonate additive, J. Energy Chem., 2021, 57, 650–655 CrossRef CAS.
- J. Wang, Y. Yamada, K. Sodeyama, E. Watanabe, K. Takada, Y. Tateyama and A. Yamada, Fire-extinguishing organic electrolytes for safe batteries, Nat. Energy, 2018, 3, 22–29 CrossRef CAS.
- Z. Yang, J. He, W.-H. Lai, J. Peng, X.-H. Liu, X.-X. He, X.-F. Guo, L. Li, Y. Qiao, J.-M. Ma, M. Wu and S.-L. Chou, Fire-retardant, stable-cycling and high-safety sodium ion battery, Angew. Chem., Int. Ed., 2021, 60, 27086–27094 CrossRef CAS PubMed.
- Q. Shi, Y. Zhong, M. Wu, H. Wang and H. Wang, High-performance sodium metal anodes enabled by a bifunctional potassium salt, Angew. Chem., 2018, 130, 9207–9210 CrossRef.
- W. Zhang, F. Zeng, H. Huang, Y. Yu, M. Xu, L. Xing and W. Li, Enhanced interphasial stability of hard carbon for sodium-ion battery via film-forming electrolyte additive, Nano Res., 2022 DOI:10.1007/s12274-022-4583-0.
- J.-J. Fan, P. Dai, C.-G. Shi, Y. Wen, C.-X. Luo, J. Yang, C. Song, L. Huang and S.-G. Sun, Synergistic dual-additive electrolyte for interphase modification to boost cyclability of layered cathode for sodium ion batteries, Adv. Funct. Mater., 2021, 31, 2010500 CrossRef CAS.
- J. Feng, L. Ci and S. Xiong, Biphenyl as overcharge protection additive for nonaqueous sodium batteries, RSC Adv., 2015, 5, 96649–96652 RSC.
- X. Wang, E. Yasukawa and S. Kasuya, Nonflammable trimethyl phosphate solvent-containing electrolytes for lithium-ion batteries: I. Fundamental properties, J. Electrochem. Soc., 2001, 148, A1058 CrossRef CAS.
- J. Feng, Z. Zhang, L. Li, J. Yang, S. Xiong and Y. Qian, Ether-based nonflammable electrolyte for room temperature sodium battery, J. Power Sources, 2015, 284, 222–226 CrossRef CAS.
- J. Feng, Y. An, L. Ci and S. Xiong, Nonflammable electrolyte for safer non-aqueous sodium batteries, J. Mater. Chem. A, 2015, 3, 14539–14544 RSC.
- G. Singh, B. Acebedo, M. C. Cabanas, D. Shanmukaraj, M. Armand and T. Rojo, An approach to overcome first cycle irreversible capacity in P2-Na2/3[Fe1/2Mn1/2]O2, Electrochem. Commun., 2013, 37, 61–63 CrossRef CAS.
- B. Zhang, R. Dugas, G. Rousse, P. Rozier, A. M. Abakumov and J.-M. Tarascon, Insertion compounds and composites made by ball milling for advanced sodium-ion batteries, Nat. Commun., 2016, 7, 10308 CrossRef CAS.
- Y.-J. Guo, Y.-B. Niu, Z. Wei, S.-Y. Zhang, Q. Meng, H. Li, Y.-X. Yin and Y.-G. Guo, Insights on electrochemical behaviors of sodium peroxide as a sacrificial cathode additive for boosting energy density of Na-ion battery, ACS Appl. Mater. Interfaces, 2021, 13, 2772–2778 CrossRef CAS.
- C. Sun, X. Zhang, C. Li, K. Wang, X. Sun and Y. Ma, A presodiation strategy with high efficiency by utilizing low-price and eco-friendly Na2CO3 as the sacrificial salt towards high-performance pouch sodium-ion capacitors, J. Power Sources, 2021, 515, 230628 CrossRef CAS.
- K. Park, B.-C. Yu and J. B. Goodenough, Electrochemical and chemical properties of Na2NiO2 as a cathode additive for a rechargeable sodium battery, Chem. Mater., 2015, 27, 6682–6688 CrossRef CAS.
- D. Shanmukaraj, K. Kretschmer, T. Sahu, W. Bao, T. Rojo, G. Wang and M. Armand, Highly efficient, cost effective, and safe sodiation agent for high-performance sodium-ion batteries, ChemSusChem, 2018, 11, 3286–3291 CrossRef CAS PubMed.
- B. Shen, R. Zhan, C. Dai, Y. Li, L. Hu, Y. Niu, J. Jiang, Q. Wang and M. Xu, Manipulating irreversible phase transition of NaCrO2 towards an effective sodium compensation additive for superior sodium-ion full cells, J. Colloid Interface Sci., 2019, 553, 524–529 CrossRef CAS.
- Y.-B. Niu, Y.-J. Guo, Y.-X. Yin, S.-Y. Zhang, T. Wang, P. Wang, S. Xin and Y.-G. Guo, High-efficiency cathode sodium compensation for sodium-ion batteries, Adv. Mater., 2020, 32, 2001419 CrossRef CAS.
|
This journal is © the Partner Organisations 2023 |
Click here to see how this site uses Cookies. View our privacy policy here.