DOI:
10.1039/D2NJ04901E
(Paper)
New J. Chem., 2023,
47, 3266-3275
Synthesis of SiO2@MnCo2O4 core–shell nanorattles using layered double hydroxide precursors and studies on their peroxidase-like activity†
Received
5th October 2022
, Accepted 9th January 2023
First published on 10th January 2023
Abstract
The current work demonstrates a simple soft chemical approach to synthesize SiO2@MnCo2O4 core–shell nanorattles using SiO2@MnCo-LDH (layered double hydroxide) precursors. XRD analysis indicates the formation of MnCo2O4 nanoparticles (NPs) on SiO2 spheres. FESEM images show hierarchical flower-like MnCo2O4 NPs on the surface of the SiO2 spheres. TEM micrographs show the interstitial space between the core (SiO2) and the shell (MnCo2O4), indicating the core–shell nanorattle morphology of SiO2@MnCo2O4. BET adsorption–desorption isotherms of the SiO2@MnCo2O4 core–shell nanorattles indicate their mesoporous nature with high surface area. Optical studies indicate O2− → Mn2+ and O2− → Co3+ charge-transfer transitions and d–d transition in pure MnCo2O4 NPs and the SiO2@MnCo2O4 core–shell nanorattles. XPS measurements indicate the presence of Si4+, Mn2+, Co2+, Mn3+, Co3+, and O2− in the SiO2@MnCo2O4 core–shell nanorattles. The SiO2@MnCo2O4 core–shell nanorattles show paramagnetic and superparamagnetic behavior at 300 K and 5 K, respectively. After characterization, the SiO2@MnCo2O4 core–shell nanorattles were explored for peroxidase-like activity for the first time. The SiO2@MnCo2O4 core–shell nanorattles act as a peroxidase nanozyme and exhibit better peroxidase-like activity than pure MnCo2O4 NPs and horseradish peroxidase.
Introduction
Recently, core–shell NPs have received considerable attention due to their remarkable properties. Combining two different materials (core and shell) changes the properties of the original core and the shell.1 Among core–shell NPs, core–shell nanorattles or yolk–shell nanoparticles possess interesting morphological features. Core–shell nanorattles or yolk–shell nanostructures have advantages because of their core@void@shell configuration. Core–shell nanorattles possess enhanced properties due to the void space between the core and the shell.1,2 Core–shell nanorattles based on metal oxides have several promising applications such as in drug delivery, catalysis, sensing, Li-ion batteries, and adsorption.2,3 Lee et al. have reported Au@SiO2 yolk–shell structures as catalyst for the reduction of p-nitrophenol.4 Kandula et al. have reported peroxidase-like activity of SiO2@Co3O4 nanorattles.5 Chen et al. have reported lithium storage properties of α-Fe2O3@SnO2 nanorattles.6 Rokicinska et al. have reported Co3O4@SiO2 core–shell nanorattles for catalytic combustion of toluene.7 Hu et al. have reported α-Fe2O3@SiO2 and SnO2@SiO2 core–shell nanorattles as anticancer drug carriers.8
Silica (SiO2) is an amorphous insulator, which is stable at high temperatures and in water. The spherical morphology and porous nature of SiO2 make it a good candidate as a core material for the synthesis of silica-based core–shell NPs/nanorattles.9 SiO2-based nanorattles have been studied for various applications such as Co@SiO2 core–shell nanorattles as catalysts,10 α-Fe2O3@SiO2 and SnO2@SiO2 core–shell nanorattles as anticancer drug carriers,8 SiO2@Co3O4 core–shell nanorattles as nanozymes,5 rattle-type gold nanorods/SiO2 nanocomposites for chemo-photothermal therapy,11 Au@SiO2 yolk–shell nanostructures as catalyst for reduction of p-nitrophenol,4 and Fe0@SiO2 nanoparticles as catalyst for Fenton-like reaction.12
MnCo2O4 is a spinel-type metal oxide in which Mn2+ ions occupy octahedral (Oh) sites, and Co2+ and Co3+ ions occupy both tetrahedral (Td) and Oh sites.13 Due to the high oxidation potential of cobalt and high electron transport ability of manganese, MnCo2O4 exhibits exceptional electrochemical and physicochemical properties.14 MnCo2O4 nanoparticles are used in diverse applications such as asymmetric supercapacitors, anode materials in Li-ion batteries, photocatalysis, adsorption, and oxygen reduction.14–18 MnCo2O4-based core–shell NPs have been used in different applications. For example, Wang et al. have reported MnCo2O4@MnCo2S4 core–shell nanostructures for asymmetric supercapacitors.19 Zhao et al. have reported MnCo2O4@Ni(OH)2 core–shell flowers with ultrahigh specific capacitance.20 Li et al. have reported MnCo2O4@NiCo2O4 core–shell NPs for dye-sensitized solar cells.21 Sun et al. have reported MnCo2O4@C core–shell nanowires for water splitting.22 Zhao et al. have reported Co3O4@MnCo2O4 core–shell nanowire arrays for electrochemical energy storage.23 Mehrez et al. have reported MnCo2O4@NiMoO4 core–shell nanowire arrays for supercapacitor applications.24
Enzymes are biocatalysts that catalyze several biochemical reactions with high efficiency and selectivity.25 Natural enzymes have several limitations. They have low stability, complex storage requirements, high cost, and less adaptability under harsh environmental conditions.26 To overcome the drawbacks of natural enzymes, nanomaterials have been used as an alternative. Metal oxide-based nanozymes have been explored to mimic different natural enzymes such as peroxidase, ferroxidase, catalase, and superoxide dismutase.26,27 Horseradish peroxidase oxidizes different substrates in the presence of hydrogen peroxide.28 In the literature, different metal oxide-based nanozymes have been used as a peroxidase mimic. For example, Chen et al. have reported CuO nanoparticles for peroxidase-like activity.29 Fu et al. have investigated the peroxidase-like activity of Fe3O4 nanoparticles for cancer therapy.30 Gao et al. have reported MnCo2O4 nanofibers as a catalyst for peroxidase-like activity.31 Ma et al. have reported photoinduced peroxidase-like activity of NiCo2O4@MnO2 nanozymes.32
Multi-functional core–shell NPs and nanorattles have been synthesized using various soft chemical synthesis routes. For example, Wang et al. have reported the synthesis of MnCo2O4@MnCo2S4 core–shell nanostructures using the hydrothermal method.19 Zhao et al. have reported the synthesis of MnCo2O4@Ni(OH)2 core–shell flowers using homogeneous precipitation.20 Mehrez et al. have reported the synthesis of MnCo2O4@NiMoO4 core–shell nanowires using hydrothermal method.24 Zhang et al. have reported the preparation of Co@CoO core–shell nanocomposites using solvothermal method.33 Gao et al. have reported the synthesis of NiCo2O4@SnO2 hetero-nanostructures using the hydrothermal method.34 Kandula et al. have reported the preparation of SiO2@NiCo2O4 core–shell nanorattles using homogeneous precipitation.35
The current work demonstrates a reliable and cost-effective synthetic strategy to prepare SiO2@MnCo2O4 nanorattles via calcination of SiO2@MnCo-LDH precursors at 500 °C. The MnCo2O4 nanoparticles deposit on the surface of the SiO2 spheres creating a hollow space (void) between the core and shell. The influence of [Mn2+
:
Co2+] ratio on the thickness of the MnCo2O4 shell and void distance between the core (SiO2) and shell (MnCo2O4) has been investigated. The SiO2@MnCo2O4 core–shell nanorattles exhibit better peroxidase-like activity than pure MnCo2O4 NPs using 3,3′,5,5′-tetramethylbenzidine (TMB) as the substrate. To the best of the authors’ knowledge, there is no report on the synthesis of SiO2@MnCo2O4 core–shell nanorattles and the SiO2@MnCo2O4 nanorattles have been employed as a peroxidase mimic for the first time.
Experimental
Reagents
Tetraethyl orthosilicate (98%, Sigma-Aldrich), ammonia solution (25%, Rankem), Mn(NO3)2.4H2O (97%, Sigma-Aldrich), Co(NO3)2.6H2O (98%, Merck), urea (99.5%, Rankem), 3,3′,5,5′-tetramethylbenzidine (98%, Spectrochem Chemicals), ethanol (99.9%, Changshu Hongsheng Fine Chemical Co., Ltd.), and H2O2 (30%, Rankem, AR). All the chemicals were used as received.
Synthesis of silica microspheres
SiO2 microspheres were synthesized using a previously reported StÖber's method.36 About 3.7 mL of tetraethyl orthosilicate was added (dropwise) to a mixture of 88 mL of EtOH and 12 mL of NH4OH solution with constant stirring. The reaction mixture was continuously stirred at RT for 24 h to get a white-colored product. The product was centrifuged, washed with EtOH, and dried in an oven overnight at 70 °C.
Synthesis of SiO2@MnCo2O4 core–shell nanorattles
First, SiO2@MnCo-LDH precursors were prepared using different molar ratios of [Mn2+
:
Co2+]. The synthetic parameters for the SiO2MnCo-LDH precursors are given in Table 1. In a typical synthetic experiment, Mn(NO3)2·4H2O, Co(NO3)2·6H2O and urea were dissolved in 100 mL of distilled water in a 250 mL beaker. Then, SiO2 microspheres (100 mg) were dispersed in the aqueous solution and sonicated for 10 minutes. The contents were heated at 85 °C for six hours with constant stirring. The product was collected by centrifuging and washing with deionized water and ethanol, followed by drying in an oven at 60 °C for about 12 h. The as-prepared SiO2@MnCo-LDH precursors were calcined at 500 °C (in a muffle furnace) for 3 h (heating rate = 2 °C per minute) in air to get the corresponding SiO2@MnCo2O4 samples. The as-prepared SiO2@MnCo-LDH precursors, prepared using different molar ratios of [Mn2+
:
Co2+] (0.25
:
0.5, 0.5
:
1, and 1
:
2), will henceforth be referred to as SiO2@MnCo-LDH-0.25, SiO2@MnCo-LDH-0.5, and SiO2@MnCo-LDH-1, respectively. The SiO2@MnCo2O4 samples, obtained on calcination, will henceforth be referred to as SiO2@MnCo2O4-0.25, SiO2@MnCo2O4-0.5, and SiO2@MnCo2O4-1, respectively.
Table 1 Synthetic details of SiO2@MnCo-LDH samples and their nomenclature
Sample code |
[Mn2+] : [Co2+] |
SiO2 (mg) |
Urea (g) |
Temperature (°C) |
Time (h) |
SiO2@MnCo-LDH-0.25 |
0.25 : 0.5 |
100 |
1.0 |
85 |
6 |
SiO2@MnCo-LDH-0.5 |
0.5 : 1 |
100 |
1.0 |
85 |
6 |
SiO2@MnCo-LDH-1 |
1 : 2 |
100 |
1.0 |
85 |
6 |
MnCo-LDH |
1 : 2 |
— |
1.0 |
85 |
6 |
Peroxidase-like activity and kinetic analysis
The peroxidase-like activity of the SiO2@MnCo2O4 nanorattles was studied utilizing tetramethylbenzidine (TMB) and H2O2 as a substrate, and oxidizing agent, respectively. About 300 μL of 3 mM TMB solution (DMSO) and 31 μL of 100 mM H2O2 were mixed with 3 mL of acetate buffer (0.1 M, pH = 5). Then, 30 μL of catalyst dispersion (1 mg of SiO2@MnCo2O4 catalyst dispersed by sonication in 1 mL of deionized water) was added to the reaction mixture. The absorbance values (@λmax = 652 nm) of the reaction mixture were measured using a UV-Vis spectrophotometer (Shimadzu UV-2600) up to 10 minutes. Kinetic experiments were performed by changing various experimental parameters, such as TMB concentration (0.05 to 0.5 mM), pH (2–12), catalyst dose (5–60 μL), and H2O2 concentration (5–200 mM). The kinetic parameters (Km and Vmax) were estimated using the Michaelis–Menten equation and Lineweaver–Burk reciprocal plots.32 The Michaelis–Menten equation is as follows.
1/V = (Km/Vmax) (1/[S]) + 1/Vmax |
where Km and Vmax denote the Michaelis–Menten constant and maximum reaction velocity, respectively. V and [S] denote reaction velocity and concentration of the substrate (TMB), respectively.
Terephthalic acid was employed as a probe molecule to prove the role of hydroxyl radicals in the peroxidase-like activity of the SiO2@MnCo2O4 nanorattles. In a cuvette, buffer (3 mL, pH = 5) and 100 mM H2O2 (31 μL) were mixed, followed by the addition of 30 μL of catalyst dispersion (SiO2@MnCo2O4). The reaction mixture was then treated with 0.5 mL of aqueous terephthalic acid solution (0.5 mM). A spectrofluorometer (Horiba Scientific, Fluoromax-4) was used to measure the PL spectra of the solution (λexc = 315 nm) up to 50 minutes.
Characterization
Powder X-ray diffraction patterns of all the samples were recorded using a Bruker AXS D8 Advance powder X-ray diffractometer (Cu-Kα (λ = 1.5406 Å), scan speed = 1° min−1) in the 2θ range of 5° to 90°. FT-IR spectra of the samples (using KBr pellets) were recorded using a Thermo Nicolet Nexus FT-IR spectrophotometer (4000 to 400 cm−1). A PerkinElmer Pyris Diamond instrument was used to perform thermal gravimetric analysis (TGA) of the SiO2@MnCo-LDH precursors; the precursors were heated at a rate of 10 °C min−1 in air between 30 °C and 1000 °C. A Carl Zeiss Gemini scanning electron microscope (operating voltage = 20 kV) was used to examine the morphology of the samples. For elemental analysis, the SEM attached with an EDXA unit was employed. The core–shell nanorattles were imaged using an FEI Tecnai G2 20S-TWIN transmission electron microscope (operating voltage = 200 kV). Using a Quantum Design MPMS3 superconducting quantum interference device, the magnetic properties of the SiO2@MnCo2O4 core–shell nanorattles were studied. X-ray photoelectron spectroscopy (XPS) measurements were performed on a Physical Electronics make (PHI 5000 Versa Probe III) spectrometer (Al-Kα radiation, energy = 1486.6 eV). Physisorption of N2 at 77 K was used to determine surface area of the SiO2@MnCo2O4 core–shell nanorattles using a Quantachrome BET surface area analyzer (model = Nova 2200e).
Results and discussion
The results related to SiO2@MnCo-LDH precursors are given in the ESI.† The results related to SiO2@MnCo2O4 core–shell nanorattles are discussed below.
SiO2@MnCo2O4 core–shell nanorattles
Phase analysis.
Pure MnCo2O4 NPs and SiO2@MnCo2O4 core–shell NPs were obtained on calcination of MnCo-LDH and SiO2@MnCo-LDH samples at 500 °C, respectively. The XRD patterns of the MnCo2O4 and SiO2@MnCo2O4 samples are shown in Fig. 1. The XRD pattern of MnCo2O4 matches with the pattern of cubic MnCo2O4 (JCPDS file no. 23-1237). The peaks observed at 2θ = 18.1°, 30.4°, 35.9°, 43.9°, 53.5°, 58.4°, and 64.5° are ascribed to (111), (220), (311), (400), (422), (511), and (440) reflections of cubic MnCo2O4. The XRD patterns of the SiO2@MnCo2O4-0.25 and SiO2@MnCo2O4-0.5 samples show peaks at 2θ = 35.9° and 64.5° attributed to the (311) and (440) planes of MnCo2O4.
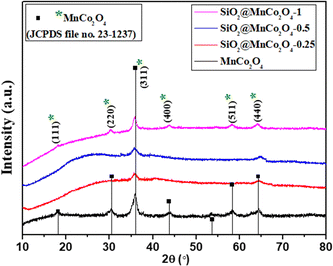 |
| Fig. 1 XRD patterns of MnCo2O4 and SiO2@MnCo2O4 samples obtained by calcination of LDH precursors (Table 1) at 500 °C. | |
The XRD pattern of SiO2@MnCo2O4-1 shows peaks at 2θ = 18.1°, 30.2°, 35.9°, 43.7°, 58.3°, and 64.3° due to (111), (220), (311), (400), (511), and (440) reflections of MnCo2O4. The estimated crystallite size (using the Scherrer formula) of MnCo2O4 are 9.3 nm, 6.4 nm, 3.5 nm, and 7.5 nm for MnCo2O4, SiO2@MnCo2O4-0.25, SiO2@MnCo2O4-0.5, and SiO2@MnCo2O4-1, respectively. The SiO2@MnCo2O4 samples possess smaller crystallites of MnCo2O4 compared to pristine MnCo2O4 NPs.
FT-IR analysis
Fig. S5 (ESI†) displays the FT-IR spectra of MnCo2O4 and SiO2@MnCo2O4 samples (SiO2@MnCo2O4-0.25, SiO2@MnCo2O4-0.5, and SiO2@MnCo2O4-1). The IR spectra of all the samples exhibit bands at about 3438 cm−1, and 1637 cm−1 assigned to stretching and bending vibrational modes of physisorbed H2O molecules. The IR spectrum of MnCo2O4 shows IR bands around 659 cm−1 and 568 cm−1 attributed to stretching vibration of Co–O and Mn–O bonds, respectively.14 The IR spectra of all the SiO2@MnCo2O4 samples display characteristic bands of SiO2 at 1105 cm−1 and 486 cm−1 due to υ-(Si–O–Si) and δ-(Si–O–Si), respectively.5 In the IR spectra of the SiO2@MnCo2O4 samples, the bands observed at about 660 cm−1 and 565 cm−1 are assigned to the stretching vibrations of Co–O and Mn–O bonds, respectively.14
Morphological studies and elemental analysis
Fig. 2(a–d) displays FESEM images of pure MnCo2O4 and SiO2@MnCo2O4 samples (SiO2@MnCo2O4-0.25, SiO2@MnCo2O4-0.5, and SiO2@MnCo2O4-1). The FESEM image of pure MnCo2O4, (Fig. 2(a)) shows nanosheets (flake-like structures). The FESEM images of the SiO2@MnCo2O4 samples (Fig. 2(b–d)) show that the SiO2 spheres are uniformly covered with MnCo2O4 nanoparticles. Table S4 (ESI†) summarizes the EDX analysis results for all SiO2@MnCo2O4 samples (after calcination at 500 °C). The results indicate that Si, Mn, Co, and O are present uniformly in all the SiO2@MnCo2O4 core–shell NPs. The weight % of Mn and Co in the SiO2@MnCo2O4 samples varies according to the [Mn2+]
:
[Co2+] ratio used during the synthesis of their precursors (SiO2@MnCo-LDH).
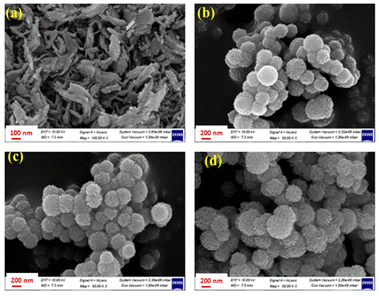 |
| Fig. 2 FE-SEM images of (a) MnCo2O4, (b) SiO2@MnCo2O4-0.25, (c) SiO2@MnCo2O4-0.5, and (d) SiO2@MnCo2O4-1 core–shell samples calcined at 500 °C. | |
Fig. 3(a–e) shows the TEM images of SiO2, pristine MnCo2O4, and SiO2@MnCo2O4 samples (SiO2@MnCo2O4-0.25, SiO2@MnCo2O4-0.5, and SiO2@MnCo2O4-1). A summary of the TEM results is given in Table 2. The TEM image of SiO2 (Fig. 3(a)) shows spherical particles with mean diameter of 175 ± 14 nm. Fig. 3(b) displays the TEM image of pristine MnCo2O4, showing its flake-like morphology (nanosheet). The mean thickness of MnCo2O4 nanosheets is 9.3 ± 3.6 nm. The TEM images (Fig. 3(c–e)) of SiO2@MnCo2O4 samples (SiO2@MnCo2O4-0.25, SiO2@MnCo2O4-0.5, and SiO2@MnCo2O4-1) show interstitial space (void) between the core (SiO2) and the shell (MnCo2O4). Such nanoparticles are known in the literature as core–shell nanorattles or nanoparticles with yolk–shell morphology.37,38 The TEM images also reveal that the MnCo2O4 shell has a porous flower-like structure. From Table 2, it is observed that the mean size of the SiO2 core in the SiO2@MnCo2O4 core–shell nanorattles varies from 171 ± 13 nm to 190 ± 15 nm. The mean thickness of the MnCo2O4 shell lies in the range of 38 ± 8 nm to 60 ± 12 nm. The average void distance between the SiO2 core and MnCo2O4 shell varies from 16 ± 3 nm to 30 ± 6 nm. The mean thickness of the nanosheets of MnCo2O4 (shell) in the SiO2@MnCo2O4 core–shell nanorattles varies from 2.6 ± 0.9 nm to 3.3 ± 0.4 nm. The synthetic conditions play an important role in the nanorattle formation. As the concentration (molar ratio) of metal salts used during the synthesis of SiO2@MnCo-LDH precursors (i.e. Mn(NO3)2·4H2O and Co(NO3)2·6H2O) increases from 0.25
:
0.5 to 1
:
2, more MnCo2O4 NPs are formed on the surface of the SiO2 spheres, which leads to a thick coating of MnCo2O4 NPs on the surface of the SiO2 spheres. When lower concentration of metal salts is used, a thin coating of MnCo2O4 NPs occurs and thus in the SiO2@MnCo2O4-0.25 sample, the thin coating of MnCo2O4 leads to a good TEM image. EDS mapping and elemental line profiles of SiO2@MnCo2O4 from TEM measurements were done and the results are shown in Fig. S6 and S7 (ESI†). The EDS elemental mapping images and elemental line profile of the SiO2@MnCo2O4 core–shell nanorattles indicate uniform distribution of elements (Si, Mn, Co and O) in the SiO2@MnCo2O4 core–shell nanorattles. The line scan EDS images show that the Mn and Co content is more towards the edge of the spherical particles and the Si content is more in the center of the particles. This suggests coating of MnCo2O4 on the SiO2 spheres.
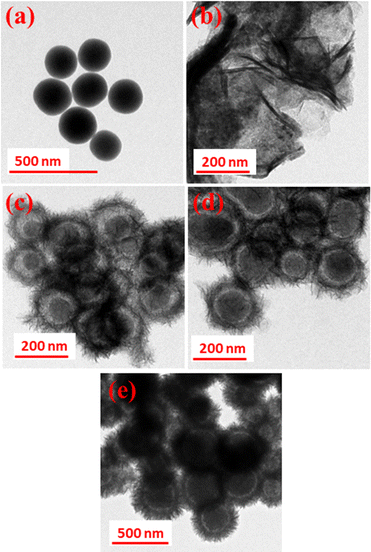 |
| Fig. 3 TEM images of (a) SiO2, (b) MnCo2O4, (c) SiO2@MnCo2O4-0.25, (d) SiO2@MnCo2O4-0.5 and (e) SiO2@MnCo2O4-1 core–shell samples calcined at 500 °C. | |
Table 2 Summary of TEM results of SiO2@MnCo2O4 core–shell nanorattles
Sample code |
Core size (nm) |
Shell thickness (nm) |
Void distance (nm) |
Flake thickness in the shell (nm) |
SiO2@MnCo2O4-0.25 |
182 ± 13 |
38 ± 8 |
30 ± 6 |
2.6 ± 0.9 |
SiO2@MnCo2O4-0.5 |
171 ± 13 |
41 ± 10 |
16 ± 3 |
3.2 ± 0.6 |
SiO2@MnCo2O4-1 |
190 ± 15 |
60 ± 12 |
22 ± 4 |
3.3 ± 0.4 |
The SAED patterns of pure MnCo2O4 NPs and SiO2@MnCo2O4 samples (SiO2@MnCo2O4-0.25, SiO2@MnCo2O4-0.5, and SiO2@MnCo2O4-1) are displayed in Fig. S8(a–d) (ESI†). The SAED pattern of pure MnCo2O4 (Fig. S8(a), ESI†) shows rings which indicate the polycrystalline nature of the MnCo2O4 NPs. The observed rings are attributed to (220), (311), (400), (422), and (440) reflections of cubic MnCo2O4. The SAED patterns of SiO2@MnCo2O4-0.25, SiO2@MnCo2O4-0.5, and SiO2@MnCo2O4-1 core–shell nanorattles (Fig. S8(b–d), ESI†) also show rings, which suggests the polycrystalline nature of all the SiO2@MnCo2O4 nanorattles. The observed rings correspond to the (311) and (422) planes of cubic MnCo2O4.
BET surface area analysis
BET surface area measurements were carried out to determine the surface area, pore size, and pore volume of the SiO2@MnCo2O4 core–shell nanorattles. SiO2 and MnCo2O4 nanoparticles exhibit a surface area of 88 m2 g−1 and 79 m2 g−1, respectively. The core–shell nanorattles (SiO2@MnCo2O4-0.25, SiO2@MnCo2O4-0.5, and SiO2@MnCo2O4-1) exhibit surface area of 278 m2 g−1, 302 m2 g−1, and 356 m2 g−1, respectively. The higher surface area of the SiO2@MnCo2O4 nanorattles is attributed to the void space between the core (SiO2) and the shell (MnCo2O4). Adsorption–desorption isotherms were recorded for pure MnCo2O4 nanoparticles and SiO2@MnCo2O4-1. As shown in Fig. S9(a) (ESI†), the adsorption-desorption isotherm of the MnCo2O4 nanoparticles shows the characteristics of a porous material with open wedge pores. The adsorption–desorption isotherm of SiO2@MnCo2O4-1 (Fig. S9(b), ESI†) matches with a type IV isotherm.39 The MnCo2O4 nanoparticles exhibit an average pore size and pore volume of 6.2 nm and 0.12 cm3 g−1, respectively. The SiO2@MnCo2O4-1 exhibits an average pore size and pore volume of 5.0 nm and 0.44 cm3 g−1, respectively.
Mechanism of formation of SiO2@MnCo2O4 core–shell nanorattles
Fig. S10 (ESI†) shows the proposed mechanism of formation of SiO2@MnCo2O4 core–shell nanorattles. In the first step, Mn2+ and Co2+ ions from the aqueous solution attach to the OH groups present on the surface of the SiO2 spheres via electrostatic interaction. At 85 °C, hydrolysis of urea leads to the production of NH4+ and OH− ions. The OH− ions react with Mn2+ and Co2+ ions present on the surface of SiO2 forming MnCo-LDH via nucleation and coalescence processes. Finally, flower-like structures consisting of MnCo-LDH nanosheets are formed on the surface of the SiO2 spheres via Ostwald ripening.40,41 The flower-like SiO2@MnCo-LDH precursors are converted into SiO2@MnCo2O4 core–shell nanorattles via calcination at 500 °C with retention of the morphology.
Time-dependent TEM studies were carried out to understand better the formation of SiO2@MnCo-LDH nanorattles. The TEM images of SiO2@MnCo-LDH-0.25 recorded after different reaction times (1 h, 2 h, 3 h, 4 h, and 6 h) are shown in Fig. S11 (ESI†). After a reaction time of 1 h, MnCo-LDH crystallites are loosely attached on the outer surface of the SiO2 spheres. These MnCo-LDH crystallites act as seed for the nucleation and recrystallization. As the reaction progresses (2 h, 4 h), Ostwald ripening (inside-out) dominates and smaller crystallites of MnCo-LDH present in the interior region dissolve, which initiates the hollowing process. Finally, after 6 h, a close-packed MnCo-LDH shell is formed on the surface of the SiO2 spheres with a void space between the core and shell. SiO2@MnCo2O4 core–shell nanorattles are obtained on calcination of SiO2@MnCo-LDH at 500 °C with the retention of the morphological features of the LDH precursor.
Optical properties of SiO2@MnCo2O4 core–shell nanorattles
The optical properties of MnCo2O4 nanoparticles and SiO2@MnCo2O4 core–shell nanorattles were studied using UV-Vis diffuse reflectance spectroscopy (DRS). The UV-Vis DRS spectra of the MnCo2O4 nanoparticles and SiO2@MnCo2O4 core–shell nanorattles are shown in Fig. S12 (ESI†). The DRS spectra of the MnCo2O4 NPs and SiO2@MnCo2O4 nanorattles show broad bands at 250 nm and 470 nm, attributed to O2− → Mn2+ and O2− → Co3+ charge-transfer transitions of MnCo2O4, respectively.43,44 The DRS spectra of all the samples exhibit a broad band at about 738 nm due to d-d transitions of Mn2+ and Co3+ of MnCo2O4 NPs.42,43
XPS analysis
The oxidation states of Si, Mn, Co, and O in SiO2, MnCo2O4 NPs and SiO2@MnCo2O4-1 nanorattles were determined using XPS analysis.
Fig. S13 (ESI†) displays the XPS spectrum of SiO2. The Si 2p spectrum of SiO2 shows a peak at 103.8 eV, indicating the existence of Si4+. The O 1s spectrum of SiO2 shows peaks at 532.7 eV and 533.8 eV, indicating the existence of lattice oxygen and surface hydroxyl oxygen in SiO2, respectively.44Fig. 4(a and b) shows the XPS spectra of pure MnCo2O4 NPs and SiO2@MnCo2O4-1. The Mn 2p spectrum of pure MnCo2O4 NPs (Fig. 4(a)) shows peaks due to Mn 2p3/2 (642.1 eV (Mn2+) and 643.5 eV (Mn3+) and Mn 2p1/2 (654.0 eV). The Co 2p spectrum of MnCo2O4 NPs (Fig. 4(a)) shows peaks due to Co 2p3/2 (780.1 eV (Co2+) and 782.1 eV (Co3+) and Co 2p1/2 (795.2 eV (Co2+) and 797.3 eV (Co3+)). The peaks observed at 788.0 eV and 803.8 eV correspond to satellite peaks. The O 1s spectrum of pure MnCo2O4 NPs shows peaks at 530.1 eV and 531.9 eV, assigned to lattice oxygen of MnCo2O4 and surface hydroxyl oxygen, respectively.45,46 The Si 2p XPS spectrum of SiO2@MnCo2O4-1 (Fig. 4(b)) shows a peak at 102.7 eV, suggesting the presence of Si4+. The Mn 2p spectrum of SiO2@MnCo2O4-1 (Fig. 4b) exhibits peaks due to Mn 2p3/2 (642.2 eV (Mn2+) and 644 eV (Mn3+)) and Mn 2p1/2 (654.2 eV (Mn3+)). The Co 2p spectrum of SiO2@MnCo2O4-1 (Fig. 4b) shows peaks due to Co 2p3/2 (781.1 eV (Co2+) and 782.7 eV (Co3+)) and Co 2p1/2 (796.8 eV (Co2+) and 797.8 eV (Co3+)). Two satellite peaks are also observed at 787.5 eV and 803.5 eV. The O 1s spectrum of SiO2@MnCo2O4-1 (Fig. 4b) exhibits peaks at 530.2 eV and 531.4 eV due to lattice oxygen of MnCo2O4 and surface hydroxyl oxygen, respectively.44–46
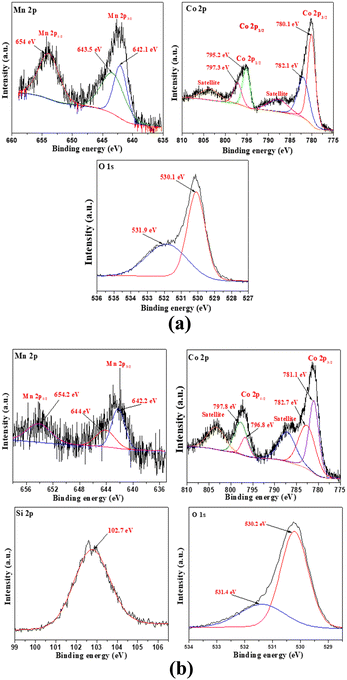 |
| Fig. 4 XPS spectra of (a) MnCo2O4 NPs and (b) SiO2@MnCo2O4-1 core–shell nanoparticles calcined at 500 °C. | |
Magnetic properties
Magnetic hysteresis (M–H) plots of pure MnCo2O4 NPs and SiO2@MnCo2O4 nanorattles were recorded at RT (300 K) and 5 K up to an applied field of 40 kOe. The M–H curves of pure MnCo2O4 NPs and SiO2@MnCo2O4 samples (SiO2@MnCo2O4-0.25, SiO2@MnCo2O4-0.5, and SiO2@MnCo2O4-1) are shown in Fig. 5. At 300 K, the absence of hysteresis and negligible coercivity indicate paramagnetic nature of the pure MnCo2O4 NPs and all the SiO2@MnCo2O4 samples. Table 3 gives the coercivity and magnetization values of pure MnCo2O4 NPs and SiO2@MnCo2O4 samples at 5 K. At 5 K, the M–H hysteresis loop of the MnCo2O4 nanoparticles exhibits coercivity of 5.0 kOe and magnetization of 6.8 emu g−1 (@40 kOe), indicating hard ferromagnetic behavior. At 5 K, the negligible coercivity and finite magnetization of all the SiO2@MnCo2O4 samples indicate superparamagnetic behavior. The coercivity values for SiO2@MnCo2O4-0.25, SiO2@MnCo2O4-0.5, and SiO2@MnCo2O4-1 at 5 K are 0.05 kOe, 0.02 kOe, and 0.09 kOe, respectively. For SiO2@MnCo2O4-0.25, SiO2@MnCo2O4-0.5, and SiO2@MnCo2O4-1, the magnetization values (@40 kOe) at 5 K are 46.5 emu g−1, 36.3 emu g−1, and 25.5 emu g−1, respectively.
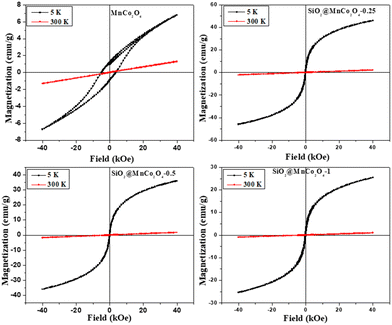 |
| Fig. 5
M–H curves for MnCo2O4 NPs and SiO2@MnCo2O4 core–shell nanorattles at 300 K and 5 K. | |
Table 3 Summary of magnetic parameters of MnCo2O4 NPs and SiO2@MnCo2O4 core–shell NPs at 5 K
Sample code |
Coercivity (Hc, kOe) |
Magnetization (emu g−1) |
Crystallite size (nm) |
MnCo2O4 |
5.00 |
6.8 |
9.3 |
SiO2@MnCo2O4-0.25 |
0.05 |
46.5 |
6.4 |
SiO2@MnCo2O4-0.5 |
0.02 |
36.3 |
3.5 |
SiO2@MnCo2O4-1 |
0.09 |
25.5 |
7.5 |
At low temperature, the dominance of magneto-crystalline anisotropy leads to higher coercivity and magnetization of the MnCo2O4 nanoparticles and SiO2@MnCo2O4 samples.47 The lower coercivity of SiO2@MnCo2O4 nanorattles compared to pure MnCo2O4 nanoparticles is attributed to the diamagnetic SiO2 phase in the nanorattles.48 The higher magnetization of SiO2@MnCo2O4 samples compared to pure MnCo2O4 NPs is attributed to smaller crystallite size of MnCo2O4 NPs in the SiO2@MnCo2O4 samples. In the MnCo2O4 nanoparticles, SiO2@MnCo2O4-0.25, SiO2@MnCo2O4-0.5, and SiO2@MnCo2O4-1, the crystallite size of MnCo2O4 are 9.3 nm, 6.4 nm, 3.5 nm, and 7.5 nm, respectively. The ZFC and FC magnetization curves recorded under 2 kOe for pure MnCo2O4 NPs and SiO2@MnCo2O4 nanorattles (SiO2@MnCo2O4-0.25, SiO2@MnCo2O4-0.5, and SiO2@MnCo2O4-1) are shown in Fig. 6. The ZFC and FC curves of pure MnCo2O4 NPs display a bifurcation at about 100 K and a hump at 25 K, which are assigned as irreversible temperature (Tirr) and blocking temperature (TB), respectively. All the SiO2@MnCo2O4 core–shell nanorattles show overlapped ZFC and FC curves without any hump, indicating superparamagnetic nature of the samples despite the absence of a maximum in the ZFC curve. The absence of maxima in the ZFC curves of the SiO2@MnCo2O4 samples is due to the absence of ferrimagnetic ordering in these samples.49–52
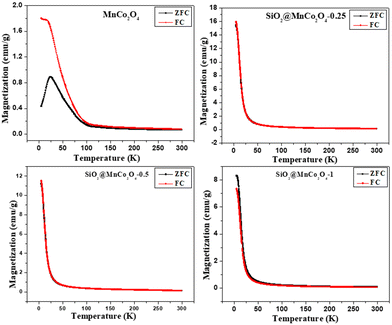 |
| Fig. 6 ZFC and FC curves for MnCo2O4 NPs and SiO2@MnCo2O4 core–shell nanorattles. | |
Peroxidase-like activity of SiO2@MnCo2O4 nanorattles
The current study demonstrates the peroxidase-like activity of pure MnCo2O4 nanoparticles and SiO2@MnCo2O4 core–shell nanorattles (SiO2@MnCo2O4-0.25, SiO2@MnCo2O4-0.5, and SiO2@MnCo2O4-1). The SiO2@MnCo2O4 core–shell nanorattles were tested as catalyst for peroxidase-like activity using TMB and H2O2 as substrate and oxidizing agent, respectively. The oxidation of TMB using SiO2@MnCo2O4 core–shell nanorattles in the presence of H2O2 leads to formation of TMB˙+ (blue-colored charge transfer complex). The UV-Vis spectrum of TMB˙+ consists of a characteristic absorption maximum at 652 nm.28 An intense blue-colored solution is obtained using SiO2@MnCo2O4 as the catalyst compared to pure MnCo2O4 NPs, which suggests the role of SiO2@MnCo2O4 as the catalyst in peroxidase-like activity.
The UV-Vis spectral results (abs. vs. time plots) and % relative efficiency of peroxidase-like activity for pure MnCo2O4 NPs and SiO2@MnCo2O4 core–shell NPs are shown in Fig. 7 and Fig. S14 (ESI†), respectively. As shown in Fig. 7, compared to pure MnCo2O4 nanoparticles, SiO2@MnCo2O4 nanorattles show better peroxidase-like activity. SiO2@MnCo2O4-1 exhibits the best peroxidase-like activity among the SiO2@MnCo2O4 samples.
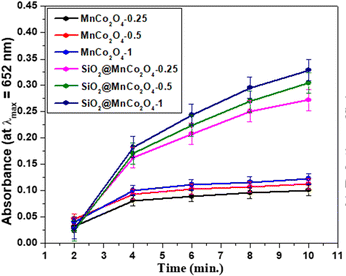 |
| Fig. 7 Peroxidase-like activity of MnCo2O4 NPs and SiO2@MnCo2O4 core–shell nanorattles as indicated by time dependent absorbance. | |
Influence of physicochemical conditions on the peroxidase-like activity
In the current study, various experimental parameters were varied to achieve optimal conditions for the peroxidase-like activity of the SiO2@MnCo2O4 core–shell nanorattles. Studies were carried out to investigate the effect of varying pH (2–12) and amount of catalyst (5 μL – 60 μL of dispersion) on the peroxidase-like activity of the SiO2@MnCo2O4 core–shell nanorattles. The influence of varying pH (2–12) on the peroxidase-like activity (Fig. S15(a), ESI†) reveals the maximum peroxidase-like activity of SiO2@MnCo2O4 core–shell nanorattles at pH = 5. At low pH (<5), protonation of amino groups of TMB occurs. The protonation of amino groups leads to the retardation of electron transfer from the substrate (TMB) to the catalyst surface (SiO2@MnCo2O4-1). Hence, in a strongly acidic medium, the peroxidase-like activity of SiO2@MnCo2O4-1 decreases. When pH >5, production of O2 and H2O occurs via the break-down of H2O2 in the presence of more hydroxyl ions, which leads to suppression of the peroxidase-like activity of SiO2@MnCo2O4-1.53,54 A linear variation of the peroxidase-like activity of SiO2@MnCo2O4-1 with an increment in catalyst dose from 5 μL to 60 μL of dispersion (1 mg catalyst dispersed by sonication in 1 mL H2O) is observed (Fig. S15(b), ESI†). A leaching experiment was carried out to understand further the peroxidase-like activity of SiO2@MnCo2O4-1. In a typical experiment, SiO2@MnCo2O4-1 (30 μL dispersion) was incubated in 3 mL buffer (pH = 5) for about 30 minutes. The supernatant solution obtained by centrifugation was further examined for peroxidase-like activity by adding TMB and H2O2 solutions. The UV-Vis spectrum of the leached solution was recorded in kinetic mode up to 10 minutes (Fig. S16, ESI†). The negligible absorbance shown by the leached solution confirms the role of MnCo2O4 NPs in the peroxidase-like activity and the activity is not due to leached ions.
Kinetic studies
Steady state-kinetic studies on the peroxidase-like activity of SiO2@MnCo2O4-1 nanorattles were performed using different substrates (i.e., TMB and H2O2). The kinetic results at different TMB concentrations by fixing H2O2 concentration and vice versa are shown in Fig. S17(a and b) (ESI†). The kinetic parameters (Km and Vmax) were determined from the slope and intercept values of Lineweaver–Burk reciprocal plots (Fig. S18(a and b), ESI†). The Km and Vmax values for SiO2@MnCo2O4-1 core–shell nanorattles are summarized in Table 4. Table 4 also gives the kinetic parameters for different metal oxide nanoparticles and core–shell NPs reported in the literature.5,54–60 The Michaelis–Menten constant (Km) is inversely proportional to the catalyst's affinity towards a substrate; a smaller Km value indicates higher affinity of a catalyst towards the substrate.54 The Km and Vmax values for SiO2@MnCo2O4-1 core–shell nanorattles towards TMB are 0.032 mM and 1.596 × 10−8 Ms−1, respectively. The Km and Vmax values for SiO2@MnCo2O4-1 core–shell nanorattles towards H2O2 are 2.7 mM and 0.532 × 10−8 Ms−1, respectively. The reported Km and Vmax values for MnCo2O4 nanoparticles towards TMB are 0.063 mM and 2.17 × 10−5 Ms−1, respectively.51 For the natural peroxidase enzyme (HRP), the reported Km and Vmax values towards TMB are 0.434 mM and 10 × 10−8 Ms−1 and towards H2O2, the values are 3.70 mM and 8.71 × 10−8 Ms−1, respectively.55 The observed Km value for SiO2@MnCo2O4-1 nanorattles towards TMB, in the present study, is smaller than that of MnCo2O4 nanoparticles and natural peroxidase enzyme (HRP). These results indicate high affinity of SiO2@MnCo2O4-1 core–shell nanorattles towards TMB with better peroxidase-like activity.
Table 4 Comparison of steady-state kinetic parameters (Km and Vmax) for SiO2@MnCo2O4 core–shell nanorattles with those reported in the literature
Catalyst |
Substrate |
K
m (mM) |
V
max (Ms−1) |
Reference |
SiO2@Co3O4 CSNPs |
TMB |
0.087 |
0.012 × 10−8 |
5
|
SiO2@Co3O4 CSNPs |
H2O2 |
25.2 |
0.015 × 10−8 |
5
|
MnCo2O4 nanoparticles |
TMB |
0.063 |
2.17 × 10−5 |
54
|
HRP |
TMB |
0.434 |
10.0 × 10−8 |
54
|
HRP |
H2O2 |
3.70 |
8.71 × 10−8 |
55
|
MnO2 nanoparticles |
TMB |
0.04 |
5.78 × 10−6 |
56
|
Co3O4 nanoparticles |
TMB |
0.037 |
6.27 × 10−8 |
57
|
Co3O4 nanoparticles |
H2O2 |
140.07 |
12.1 × 10−8 |
57
|
Co3O4@NiO CSNPs |
TMB |
0.036 |
— |
58
|
Co3O4@NiO CSNPs |
H2O2 |
8.17 |
— |
58
|
Fe3O4@CoFe-LDH |
TMB |
0.395 |
— |
59
|
Fe3O4@CoFe-LDH |
H2O2 |
47.6 |
— |
59
|
TiO2@CeOx |
TMB |
0.28 |
6.5 × 10−9 |
60
|
TiO2@CeOx |
H2O2 |
6.29 |
34 × 10−9 |
60
|
SiO2@MnCo2O4-1 |
TMB |
0.032 |
1.596 × 10−8 |
This work |
SiO2@MnCo2O4-1 |
H2O2 |
2.7 |
0.532 × 10−8 |
This work |
Mechanism of peroxidase-like activity of SiO2@MnCo2O4 nanorattles
Fig. 8 shows the mechanism for the peroxidase-like activity of SiO2@MnCo2O4 nanorattles. In the first step, adsorption of tetramethylbenzidine (TMB) molecules occurs on the surface of SiO2@MnCo2O4 nanorattles. This promotes nitrogen electron pair donation from the NH2 groups of TMB towards the surface of SiO2@MnCo2O4, resulting in high electron density over SiO2@MnCo2O4.31,54,61 The SiO2@MnCo2O4 core–shell nanorattles reduce H2O2 into OH− and OH˙ species. The OH− and OH˙ species facilitate the oxidation of TMB into TMB˙+ (a blue-colored CT complex). The rattle-like hierarchical structure of MnCo2O4 NPs present on the surface of SiO2 spheres eases interaction between tetramethylbenzidine and the catalytic active centers (Mn2+ and Co2+) leading to improved peroxidase-like activity of the SiO2@MnCo2O4 nanorattles.
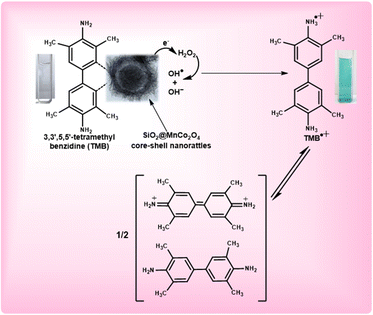 |
| Fig. 8 Proposed mechanism of peroxidase-like activity of SiO2@MnCo2O4 core–shell nanorattles using TMB as a substrate. | |
In the current study, high surface area and rattle-like morphology of SiO2@MnCo2O4 lead to enhanced peroxidase-like activity. The higher peroxidase-like activity of SiO2@MnCo2O4-1 compared to the other samples is attributed to its high surface area (356 m2 g−1). The SiO2@MnCo2O4 core–shell nanorattles, synthesized in the current study, exhibit high surface area due to their rattle-type porous morphology. The high surface area of the SiO2@MnCo2O4 core–shell nanorattles is helpful for enhanced peroxidase-like activity. The rattle-type porous nature of hierarchical MnCo2O4 NPs on the surface of SiO2 spheres provides less steric hindrance for the TMB molecules to interact with the catalytic centres (Mn2+ and Co2+).62,63 This promotes electron transfer from the SiO2@MnCo2O4 core–shell nanorattles towards H2O2 resulting in faster chemical reduction of H2O2.
Fig. S19 (ESI†) shows the fluorescence spectra for the detection of OH˙. radicals produced during the peroxidase-like activity. Terephthalic acid (probe molecule, λexc = 315 nm) produces fluorescent 2-hydroxyterephthalic acid (λem = 425 nm) on reacting with hydroxyl radicals. It can be noted that the fluorescence intensity increases with time due to increasing production of hydroxyl radicals. The PL results suggest the role of hydroxyl radicals in the peroxidase-like activity of SiO2@MnCo2O4 nanorattles.
Detection of H2O2 using SiO2@MnCo2O4 nanorattles
SiO2@MnCo2O4 core–shell nanorattles were used for the detection of H2O2 using peroxidase-like activity. A calibration plot (Fig. S20, ESI†) was recorded for SiO2@MnCo2O4-1 with varying concentration of H2O2 (linear range = 0.05 mM to 1 mM). The equation given below was used for determining the limit of detection (LOD) of H2O2.
Limit of detection = 3 × (Standard deviation due to blank/Slope) |
The standard deviation was estimated by recording the absorption spectra of a blank solution (i.e. [H2O2] = 0) three times. The slope was calculated from the absorbance (@λmax = 652 nm) versus [H2O2] plot (Fig. S20(b), ESI†). The estimated LOD value for H2O2 using SiO2@MnCo2O4 core–shell nanorattles is 0.083 mM and it is comparable with that reported in the literature.58,63
Conclusions
The current work demonstrates a simple and cost-effective synthetic strategy to synthesize SiO2@MnCo2O4 core–shell nanorattles via calcination of SiO2@MnCo-LDH precursors at 500 °C. MnCo2O4 NPs deposit on the surface of SiO2 spheres creating a hollow space (void) between the core and shell. The [Mn2+
:
Co2+] ratio affects thickness of the MnCo2O4 shell and void distance between the core (SiO2) and the shell (MnCo2O4). XRD results confirm the formation of MnCo2O4 NPs in the SiO2@MnCo2O4 samples. FESEM and TEM analyses show nanorattle-like morphology of all the SiO2@MnCo2O4 samples. The mean shell thickness and void distance between the SiO2 core and MnCo2O4 shell in the SiO2@MnCo2O4 core–shell nanorattles vary from 38 ± 8 nm to 60 ± 12 nm and 16 ± 3 nm to 30 ± 6 nm, respectively. BET measurements indicate higher surface area of SiO2@MnCo2O4 core–shell nanorattles (278 m2 g−1 to 356 m2 g−1) compared to the constituents. XPS analysis confirms the presence of Si4+, Mn2+, Co2+, Mn3+, Co3+, and O2− in the SiO2@MnCo2O4 nanorattles. Magnetic measurements indicate paramagnetic and superparamagnetic behavior of SiO2@MnCo2O4 nanorattles at 300 K and 5 K, respectively. The SiO2@MnCo2O4 nanorattles exhibit better peroxidase-like activity than pure MnCo2O4 NPs and horseradish peroxidase. The peroxidase-like activity of the core–shell nanorattles can be useful for several sensing applications, such as the detection of glucose, H2O2, ascorbic acid, hydroquinone, protein, and dopamine.
Conflicts of interest
There are no conflicts of interest to declare.
Acknowledgements
Pankaj Rana expresses his gratitude to the UGC and the Ministry of Education, Government of India for awarding him a fellowship (JRF/SRF). The authors express gratitude to Institute Instrumentation Centre (IIC), IIT Roorkee for providing the necessary instrumentation facilities. The authors are also thankful to the Department of Metallurgical and Materials Engineering, IIT Roorkee for providing the TEM facility.
References
- A. M. El-Toni, M. A. Habila, J. P. Labis, Z. A. Alothman, M. Alhoshan, A. A. Elzatahry and F. Zhang, Nanoscale, 2016, 8, 2510–2531 RSC.
- M. Priebe and K. M. Fromm, Chem. – Eur. J., 2015, 21, 3854–3874 CrossRef CAS PubMed.
- J. Liu, R. Harrison, J. Z. Zhou, T. T. Liu, C. Yu, G. Q. Lu, S. Z. Qiao and Z. P. Xu, J. Mater. Chem., 2011, 21, 10641–10644 RSC.
- J. Lee, J. C. Park and H. Song, Adv. Mater., 2008, 20, 1523–1528 CrossRef CAS.
- S. Kandula and P. Jeevanandam, RSC Adv., 2015, 5, 5295–5306 RSC.
- J. S. Chen, C. M. Li, W. W. Zhou, Q. Y. Yan, L. A. Archer and X. W. Lou, Nanoscale, 2009, 1, 280–285 RSC.
- A. Rokicinska, M. Zurowska, P. Łatka and P. Kustrowski, Catalysts, 2021, 11, 1097 CrossRef CAS.
- Y. Hu, X. T. Zheng, J. S. Chen, M. Zhou, C. M. Li and X. W. Lou, J. Mater. Chem., 2011, 21, 8052–8056 RSC.
- B. J. Jankiewicz, D. Jamiola, J. Choma and M. Jaroniec, Adv. Colloid Interface Sci., 2012, 170, 28–47 CrossRef CAS PubMed.
- N. Yan, Z. Zhao, Y. Li, F. Wang, H. Zhong and Q. Chen, Inorg. Chem., 2014, 53, 9073–9079 CrossRef CAS PubMed.
- Y. Yu, M. Zhou, W. Zhang, L. Huang, D. Miao, H. Zhu and G. Su, Mol. Pharmaceutics, 2019, 16, 1929–1938 CrossRef CAS PubMed.
- C. Liu, J. Li, J. Qi, J. Wang, R. Luo, J. Shen, X. Sun, W. Han and L. Wang, ACS Appl. Mater. Interfaces, 2014, 6, 13167–13173 CrossRef CAS PubMed.
- T. Zhang, Z. Li, L. Wang, P. Sun, Z. Zhang and S. Wang, ChemSusChem, 2018, 11, 2730–2736 CrossRef CAS PubMed.
- T. Pettong, P. Iamprasertkun, A. Krittayavathananon, P. Sukha, P. Sirisinudomkit, A. Seubsai, M. Chareonpanich, P. Kongkachuichay, J. Limtrakul and M. Sawangphruk, ACS Appl. Mater. Interfaces, 2016, 8, 34045–34053 CrossRef CAS PubMed.
- B. Wang, S. Wang, Y. Tang, C. W. Tsang, J. Dai, M. K. H. Leung and X. Y. Lu, Appl. Energy, 2019, 252, 113452 CrossRef CAS.
- W. Yang, J. Hao, Z. Zhang, B. Lu, B. Zhang and J. Tang, Catal. Commun., 2014, 46, 174–178 CrossRef CAS.
- S. Tarighi and N. M. Juibari, ChemistrySelect, 2019, 4, 6506–6515 CrossRef CAS.
- Y. Liang, H. Wang, J. Zhou, Y. Li, J. Wang, T. Regier and H. Dai, J. Am. Chem. Soc., 2012, 134, 3517–3523 CrossRef CAS PubMed.
- X. Wang, L. Xu, K. Song, R. Yang, L. Jia, X. Guo, X. Jing and J. Wang, Colloids Surf., A, 2019, 570, 73–80 CrossRef CAS.
- Y. Zhao, L. Hu, S. Zhao and L. Wu, Adv. Funct. Mater., 2016, 26, 4085–4093 CrossRef CAS.
- Z. Li, S. Liu, L. Li, W. Qi, W. Lai, L. Li, X. Zhao, Y. Zhang and W. Zhang, Sol. Energy Mater. Sol. Cells, 2021, 220, 110859 CrossRef CAS.
- C. Sun, J. Yang, Z. Dai, X. Wang, Y. Zhang, L. Li, P. Chen, W. Huang and X. Dong, Nano Res., 2016, 9, 1300–1309 CrossRef CAS.
- L. Zhao, M. Yang, Z. Zhang, Y. Ji, Y. Teng, Y. Feng and X. Liu, Inorg. Chem. Commun., 2018, 89, 22–26 CrossRef CAS.
- J. A. A. Mehrez, K. A. Owusu, Q. Chen, L. Li, K. Hamwi, W. Luo and L. Mai, Inorg. Chem. Front., 2019, 6, 857–865 RSC.
- L. Wang, Y. Min, D. Xu, F. Yu, W. Zhou and A. Cuschieri, Chem. Commun., 2014, 50, 11147–11150 RSC.
- Y. C. Yang, Y. T. Wang and W. L. Tseng, ACS Appl. Mater. Interfaces, 2017, 9, 10069–10077 CrossRef CAS PubMed.
- Z. Chen, J. J. Yin, Y. T. Zhou, Y. Zhang, L. Song, M. Song, S. Hu and N. Gu, ACS Nano, 2012, 6, 4001–4012 CrossRef CAS PubMed.
- J. Mu, Y. Wang, M. Zhao and L. Zhang, Chem. Commun., 2012, 48, 2540–2542 RSC.
- W. Chen, J. Chen, Y. Bin Feng, L. Hong, Q. Y. Chen, L. F. Wu, X. H. Lin and X. H. Xia, Analyst, 2012, 137, 1706–1712 RSC.
- S. Fu, S. Wang, X. Zhang, A. Qi, Z. Liu, X. Yu, C. Chen and L. Li, Colloids Surf., B, 2017, 154, 239–245 CrossRef CAS PubMed.
- M. Gao, X. Lu, M. Chi, S. Chen and C. Wang, Inorg. Chem. Front., 2017, 4, 1862–1869 RSC.
- Y. Ma, M. Zhu, Q. He, M. Zhao and H. Cui, ACS Sustainable Chem. Eng., 2022, 10, 5651–5658 CrossRef CAS.
- L. Zhang, P. Hu, X. Zhao, R. Tian, R. Zou and D. Xia, J. Mater. Chem., 2011, 21, 18279–18283 RSC.
- G. Gao, H. B. Wu, S. Ding and X. W. Lou, Small, 2015, 11, 432–436 CrossRef CAS PubMed.
- S. Kandula and P. Jeevanandam, Eur. J. Inorg. Chem., 2015, 4260–4274 CrossRef CAS.
- W. Stober, A. Fink and E. Bohn, J. Colloid Interface Sci., 1968, 26, 62–69 CrossRef.
- P. Yang, F. Wang, X. Luo, Y. Zhang, J. Guo, W. Shi and C. Wang, ACS Appl. Mater. Interfaces, 2014, 6, 12581–12587 CrossRef CAS PubMed.
- J. Xu, J. Liu, R. Che, C. Liang, M. Cao, Y. Li and Z. Liu, Nanoscale, 2014, 6, 5782–5790 RSC.
- L. Kumar, H. Chauhan, N. Yadav, N. Yadav, S. A. Hashmi and S. Deka, ACS Appl. Energy Mater., 2018, 1, 6999–7006 CrossRef CAS.
- S. Liu, S. C. Lee, U. Patil, I. Shackery, S. Kang, K. Zhang, J. H. Park, K. Y. Chung and S. Chan Jun, J. Mater. Chem. A, 2017, 5, 1043–1049 RSC.
- J. Yan, Z. Fan, W. Sun, G. Ning, T. Wei, Q. Zhang, R. Zhang, L. Zhi and F. Wei, Adv. Funct. Mater., 2012, 22, 2632–2641 CrossRef CAS.
- N. Y. Tashkandi and R. M. Mohamed, Ceram. Int., 2022, 48, 13216–13228 CrossRef CAS.
- P. Prieto, J. F. Marco, A. Serrano, M. Manso and J. de la Figuera, J. Alloys Compd., 2019, 810, 151912 CrossRef CAS.
- J. Mahajan and P. Jeevanandam, Mater. Today Commun., 2021, 26, 102085 CrossRef CAS.
- S. Wang, Y. Hou and X. Wang, ACS Appl. Mater. Interfaces, 2015, 7, 4327–4335 CrossRef CAS PubMed.
- R. Huang, J. Lin, J. Zhou, E. Fan, X. Zhang, R. Chen, F. Wu and L. Li, Small, 2021, 17, 1–9 Search PubMed.
- F. M. M. Borges, D. M. A. Melo, M. S. A. Câmara, A. E. Martinelli, J. M. Soares, J. H. de Araújo and F. A. O. Cabral, J. Magn. Magn. Mater., 2006, 302, 273–277 CrossRef CAS.
- S. K. Yadav and P. Jeevanandam, J. Nanoparticle Res., 2016, 18, 1–25 CrossRef CAS.
- M. Iacob, D. Sirbu, C. Tugui, G. Stiubianu, L. Sacarescu, V. Cozan, A. Zeleňáková, E. Čižmár, A. Feher and M. Cazacu, RSC Adv., 2015, 5, 62563–62570 RSC.
- T. H. Dolla, K. Pruessner, D. G. Billing, C. Sheppard, A. Prinsloo and P. Ndungu, Mater. Today Proc., 2018, 5, 10488–10495 CrossRef.
- P. Pramanik, S. Thota, S. Singh, D. C. Joshi, B. Weise, A. Waske and M. S. Seehra, J. Phys.: Condens. Matter, 2017, 29, 425803 CrossRef PubMed.
- Y. He, N. Li, W. Li, X. Zhang, X. Zhang, Z. Liu and Q. Liu, Sens. Actuators, B, 2021, 326, 128850 CrossRef CAS.
- X. Zhao, S. Zhao, S. Li, X. Yao, X. Zhu, W. Chen, G. Fan, Z. Liu, Q. Liu and K. Yue, ACS Appl. Nano Mater., 2021, 4, 8706–8715 CrossRef CAS.
- E. Ding, J. Hai, F. Chen and B. Wang, ACS Appl. Nano Mater., 2018, 1, 4156–4163 CrossRef CAS.
- X. Q. Zhang, S. W. Gong, Y. Zhang, T. Yang, C. Y. Wang and N. Gu, J. Mater. Chem., 2010, 20, 5110–5116 RSC.
- X. Liu, Q. Wang, H. Zhao, L. Zhang, Y. Su and Y. Lv, Analyst, 2012, 137, 4552–4558 RSC.
- J. Dong, L. Song, J. J. Yin, W. He, Y. Wu, N. Gu and Y. Zhang, ACS Appl. Mater. Interfaces, 2014, 6, 1959–1970 CrossRef CAS PubMed.
- Y. Zhu, Z. Yang, M. Chi, M. Li, C. Wang and X. Lu, Talanta, 2018, 181, 431–439 CrossRef CAS PubMed.
- W. Yang, J. Li, M. Wang, X. Sun, Y. Liu, J. Yang and D. H. L. Ng, Colloids Surf., B, 2020, 188, 110742 CrossRef CAS PubMed.
- L. Artiglia, S. Agnoli, M. C. Paganini, M. Cattelan and G. Granozzi, ACS Appl. Mater. Interfaces, 2014, 6, 20130–20136 CrossRef CAS PubMed.
- J. Mu, L. Zhang, G. Zhao and Y. Wang, Phys. Chem. Chem. Phys., 2014, 16, 15709–15716 RSC.
- L. Huang, K. Chen, W. Zhang, W. Zhu, X. Liu, J. Wang, R. Wang, N. Hu, Y. Suo and J. Wang, Sens. Actuators, B, 2018, 269, 79–87 CrossRef CAS.
- W. Huang, T. Lin, Y. Cao, X. Lai, J. Peng and J. Tu, Sensors, 2017, 17, 217–228 CrossRef PubMed.
|
This journal is © The Royal Society of Chemistry and the Centre National de la Recherche Scientifique 2023 |
Click here to see how this site uses Cookies. View our privacy policy here.