DOI:
10.1039/D2NH00472K
(Communication)
Nanoscale Horiz., 2023,
8, 127-132
Microbatteries with twin-Swiss-rolls redefine performance limits in the sub-square millimeter range†
Received
7th October 2022
, Accepted 3rd November 2022
First published on 22nd November 2022
Abstract
To maintain the downscaling of microelectronic devices with footprints less than one square millimeter, next-generation microbatteries should occupy the same area and deliver adequate energy for running a new generation of multi-functional microautonomous systems. However, the current microbattery technology fails in accomplishing this task because the micrometer-sized electrodes are not compatible with on-chip integration protocols and technologies. To tackle this critical challenge, an on-chip Swiss-roll microelectrode architecture is employed that exploits the self-assembly of thin films into ultra-compact device architectures. A twin-Swiss-roll microelectrode on a chip occupies a footprint of 0.045 mm2 and delivers an energy density up to 458 μW h cm−2. After packaging, the footprint of a full cell increases to 0.11 mm2 with a high energy density of 181 μW h cm−2. The volumetric energy density excluding the chip thickness is 16.3 mW h cm−3. These results open opportunities for deploying microbatteries as energy and power sources to drive smart dust microelectronics and microautonomous systems.
New concepts
A fundamental barrier against the take-off of smart dust capable of detecting everything from light to vibrations to temperature that aims to revolutionize the Internet of Things is the spatial and time limitations of the power supply by energy conversion devices. A tiny battery of the same size could address this challenge. However, the integration of batteries into smart dust devices is plagued by the large gap in size between microbatteries and smart dust, as well as by the lack of energy supply for microbatteries to drive electronic functions. In this work, we develop microscale Swiss rolls on a chip by the self-assembly of nanomembranes, which is known as the micro-origami technology. The footprint of the battery based on the micro-Swiss-roll electrodes enters the deep submillimeter range (<0.1 mm2). Moreover, the micro-Swiss-roll electrode mimics the most successful way to create an energy-dense battery: winding electrode materials up. As such, the energy density is around 0.46 mW h cm−2, comparable to batteries two orders of magnitude larger (>1 mm2). The micro-origami technology is expected to provide a new platform to create energy-dense batteries less than one millimeter across.
|
Introduction
Microelectronic chips have already entered the sub-1 mm2 size region and they need on-board electricity to drive their functions.1–3 As the tiny footprint sets stringent requirements for on-chip process flows and materials choices, the power supply is often provided by easy-to-fabricate miniaturized energy harvesters like piezoelectric generators or solar cells.4–6 Unfortunately, these harvesters are often plagued by discontinuous supply of electricity because the external energy sources (vibration or solar light) are either location- or time-dependent. Batteries, instead, can ensure a stable current supply as their energy storage ability does not depend on external conditions.7–12 However, on-chip microbatteries urgently need to be downscaled to the same footprint as their microelectronic counterparts and they must be capable of delivering adequate energy to continuously drive the many functions demanded by ever more complex microautonomous systems.13
Engineering 2D active thin-film materials into three-dimensional (3D) structures is an effective way to enhance the energy storage ability of microbatteries while maintaining a small footprint.14–19 3D microbatteries often consist of interdigitated electrodes with a large aspect ratio of height to footprint in an attempt to maximize material loading of the electrode.20–22 The energy density of such a 3D microbattery can reach up to 1 mW h cm−2.23 However, its footprint is larger than 9 mm2 and very few prototypes with an area of less than 1 mm2 have been reported. It is thus important to develop a novel technology to produce the 3D structure with a reduced footprint while keeping high electroactive materials loading. Alternatively, a micro-origami self-assembly process is able to transform a large-area thin film into a micrometer-sized Swiss-roll, which bypasses this technological difficulty.24 The fabrication of the Swiss-rolls follows an on-chip processing route which is compatible with the manufacturing of microelectronic devices.25
Herein, a self-assembly process is demonstrated to create a high-performance microbattery using Swiss-roll microelectrodes. A pair of patterned thin films (Ti and Au) is wound up into a compact microstructure, in this way shrinking the footprint of the Swiss-roll microelectrode by ten times compared to that of the flat thin film, merely occupying a final area of 0.021 mm2. The Swiss-roll microelectrodes are generated by depositing MnO2 and Zn. The energy density of the Zn–MnO2 microbattery with a footprint of less than 0.1 mm2 attains 458 μW h cm−2.
Results and discussion
Reshape a 2D flat layer into a 3D mesostructured Swiss-roll
A micro-origami technology is utilized to create Swiss-roll microelectrodes (Fig. 1a). Three layers (photoresist, Ti, and Au) are consecutively deposited and patterned on a chip surface. During deposition differential strain builds up between the Ti and Au layer (Ti/Au layer).26 Upon releasing the strain by etching away the photoresist sacrificial layer the Ti/Au layer winds up automatically forming a Swiss roll. First of all, the diameter depends on the thickness of Ti/Au layer. As shown in Fig. S1 (ESI†), the diameter of the Swiss-roll electrode increases with the increasing thickness of the Ti/Au layer. Here we use 30 nm Ti and 30 nm Au for further development. Microscale holes are also patterned into the Ti and Au layers (Fig. 1b) to achieve better contact between the electrode materials and the electrolyte. As the holes in the Ti/Au layer greatly influence the built-in strain the finite element method (FEM) is used to investigate the effect of the perforated design on the final 3D Swiss-roll structure. The size of the single hole unit cell is defined as a square with the side length (L = 12 μm; Fig. 1c). The filling factor k is defined as the aspect ratio of the square-hole to the unit cell. The simulation result shows that the diameter of the first winding of the Swiss-roll increases as k becomes larger, which is confirmed by the scanning electron microscope (SEM) images (Fig. 1c, Swiss-roll-single). Fig. 1d (left panel) provides details of the diameter change of the Swiss-roll as a function of k. As the first winding largely determines the diameter of the Swiss-roll an increase in diameter of Swiss-rolls after multiple windings (Fig. 1c, Swiss-roll-multiple) is observed. Since the diameter of the multiple-winding Swiss-roll is more than 10 μm larger than the first winding, one can infer that interlayer gaps do exist between neighboring windings (Fig. 1d, right panel). A large interlayer gap is beneficial for loading more electroactive materials into the microelectrodes to achieve a higher energy storage capacity. Fig. S2 (ESI†) shows the variation of the interlayer gap in the Swiss-roll as a function of k. As the interlayer gap reaches the maximum when k = 0.5, this k value is used as the design parameter in the following experiments.
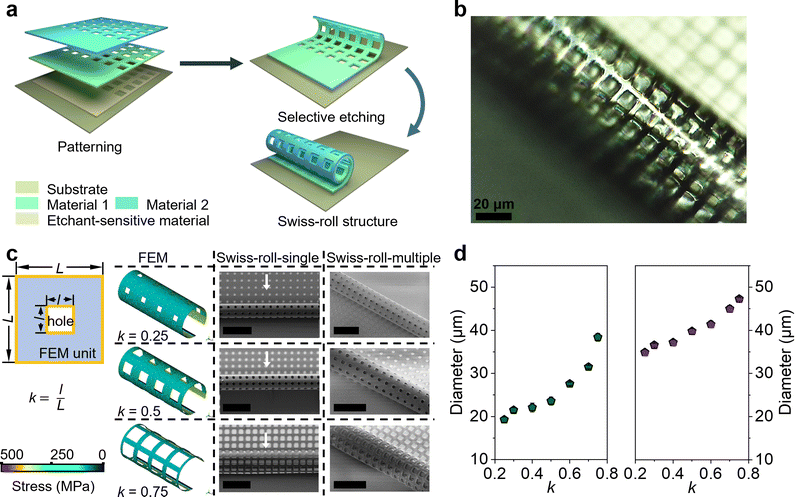 |
| Fig. 1 Rational design of a 3D mesostructured Swiss-roll. (a) Schematic of the self-assembly process of a mesostructured Swiss-roll from a 2D layer precursor. (b) Optical microscope image of a mesostructured Swiss-roll (k = 0.75). (c) FEM simulations and SEM images of Swiss-rolls. Scale bars in SEM images: 50 μm. White arrows indicate rolling direction. (d) Diameter of Swiss-roll as a function of k value (left: Swiss-roll-single; right: Swiss-roll-multiple). | |
The construction of Swiss-roll microelectrodes
To use the hollow Swiss-rolls as microelectrodes for an on-chip battery, the start edge for the micro-origami process is defined by anchoring the other three edges to the chip. Two perforated Ti/Au layers roll up against each other and form a twin tube architecture on a single chip (Fig. 2a). The footprint area of one perforated Swiss-roll is about 0.021 mm2 (calculated from Fig. S3, ESI†). Then electroactive materials are deposited into the Ti/Au Swiss-roll current collectors to build a battery. Owing to the high stability in the air,27–31 MnO2 and Zn are used for deposition (Fig. 2a). The top (Fig. 2b) and side (Fig. 2c) views of the MnO2 tubular structure show that MnO2 is successfully deposited into the Swiss roll. A small amount of MnO2 (0.8 μg) is loaded onto the Swiss-roll microelectrodes after 7 min deposition (the measurement of the weight is explained in the ESI†). The magnified SEM image in Fig. 2d shows the porous structure of the deposited MnO2. Raman spectroscopy shows two peaks at 575 and 657 cm−1 (Fig. S4a, ESI†), which can be ascribed to the symmetric stretching vibration of the Mn–O bond in the MnO6 octahedron and the Mn–O vibration along the chain of the MnO2 framework, respectively.32–34 The XRD diffraction peaks at 37.4°, 42.6°, 56.8°, and 64.7° further confirm the formation of MnO2 (Fig. S4b, ESI†).35 Zn metal corrosion in mild aqueous electrolyte is one of the main reasons for Zn battery with poor cycling performance.36,37 In order to mitigate the corrosion induced capacity decay, excessive Zn (2.3 μg) was deposited into the Swiss-roll microelectrodes (Fig. 2e). Fig. 2f shows that the Swiss-roll is filled by Zn. The magnified SEM image (Fig. 2g) reveals the vertical growth of Zn nanosheets on the Au surface. XRD peaks of the deposited Zn are indexed to the hexagonal phase of Zn (JCPDS, No. 04-0831) (Fig. S4c, ESI†). Fig. S5 (ESI†) shows that the perforation reduces Young's modulus and stiffness of Swiss-roll electrodes, but the loading of Zn and MnO2 strengthens the mechanical properties to allow for stable operation. The perforated Swiss-roll electrodes also show higher capacity than those without holes (Fig. S6a, ESI†) because the thickness of deposited materials (e.g., MnO2) in the perforated Swiss-roll electrode (Fig. S6b, ESI†) is much higher than in the unperforated Swiss-roll electrode (Fig. S6c, ESI†).
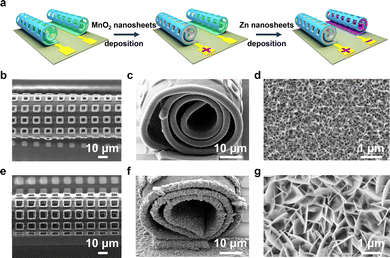 |
| Fig. 2 Manufacture of mesostructured Swiss-roll microelectrodes. (a) Schematic of the Zn–MnO2 Swiss-roll microbattery fabrication process. Top (b) and side view (c) SEM images of mesostructured Swiss-roll microcathode. (d) Magnified SEM image of the MnO2 morphology. Top (e) and side (f) view of mesostructured Swiss-roll microanode. (g) Magnified SEM image of the Zn nanosheet morphology. | |
Electrochemical performance of microbattery
As the degradation of the Zn microanode is the main reason for battery failure, we first evaluated the Zn anode performance in the electrolyte. Fig. 3a displays the long-term galvanostatic cycling performance of a planar Zn anode (1 mm2) at a current density of 200 μA cm−2. The Zn/Zn symmetric cell shows stable voltage profiles for over 110 hours with a low overpotential of 34 mV confirming the excellent deposition/stripping reversibility of the Zn anode. Such low overpotential is attributed to the bulky CF3SO3− anions that decrease the number of water molecules surrounding Zn2+ cations, facilitating Zn2+ transportation and charge transfer.38 Swiss-roll microelectrodes of MnO2 and Zn are encapsulated by a SU8 box with a length of 600 μm and width of 190 μm (Fig. S7, ESI†). More specifically, the SU8 box is fabricated by a standard photolithography process (the details are described in the ESI†). One droplet of aqueous solution containing Zn(CF3SO3)2 (3 mol L−1) and Mn(CF3SO3)2 (0.025 mol L−1) is added to the SU8 box. To prevent evaporation of the electrolyte, a SU8 cover was placed onto the box. Fig. 3b shows the cyclic voltammetry (CV) curve of the Swiss-roll microbattery in the potential range of 0.8 to 1.8 V at a scan rate of 0.1 mV s−1. The CV curve of the first cycle demonstrates two cathodic peaks located at 1.39 V and 1.21 V corresponding to the zinc ion insertion in MnO2 and conversion reaction to MnOOH and Mn2O3, respectively.39,40 During the anodic scan, two peaks located at around 1.62 and 1.68 V are observed, which are attributed to the extraction of protons and zinc ions from cathode, respectively.41,42 In the following cycles, the cathodic peak at 1.39 V shifts to 1.42 V. A strong anodic peak at around 1.65 V emerges during the anodic sweep. Fig. 3c shows the galvanostatic charge/discharge (GCD) curves of the Swiss-roll microbattery after a conditioning cycle at a current density of 200 μA cm−2 (footprint of one Swiss-roll microelectrode: 0.021 mm2). One pair of charge/discharge plateaus are observed at 1.65 V and 1.42 V, consistent with the CV curves. Fig. 3d indicates that the energy storage performance of the Swiss-roll microbattery is remarkably promoted by simply increasing the deposition time of MnO2. The footprint capacity increases from 41 to 345 μA h cm−2 as the deposition time increases from 1 to 7 min (Fig. 3d). The gravimetric capacity and energy density of the MnO2 Swiss-roll microelectrode are 194 mA h g−1 and 257 mW h g−1, respectively, which are comparable to other MnO2 based Zn ion batteries (Table S1, ESI†). The Swiss-roll microelectrode delivers a high footprint capacity of 130 μA h cm−2 at a current density of 500 μA cm−2 (Fig. 3e). The footprint capacity recovers to 300 μA h cm−2 when the current density is reduced to 200 μA cm−2. Although the initial coulombic efficiency is less than 100% (90%) due to the structural change of MnO2,43 a reversible footprint capacity of 115 μA h cm−2 at the current of 500 μA cm−2 is attainable over 147 cycles with the coulombic efficiency of around 100% (Fig. S8, ESI†). Moreover, the cycling performance of the Swiss-roll microbattery is improved to 300 cycles with a reversible footprint capacity of 96 μA h cm−2 and a coulombic efficiency of around 99% (Fig. 3f) by increasing the Zn thickness to about 1 μm (Fig. S9, ESI†). As a higher thickness means a lower utilization rate of Zn anode, it is still necessary to improve the Zn reversibility at a high utilization rate. By contrast, planar electrodes with the same footprint area as the Swiss-roll microbattery show a low capacity of only 4 μA h cm−2 and short cycle life of less than 50 cycles (Fig. 3f). The poor performance of the planar electrodes is attributed to the delamination of MnO2 from the current collector (Fig. S10, ESI†). In addition, the lifetime capacity of the Swiss-roll microelectrodes is 19.3 μA h (26 μW h) able to power a low-power (16 nW) temperature sensing microsystem with data processing capability for about two month,44 demonstrating the practicability for the target application scenarios.
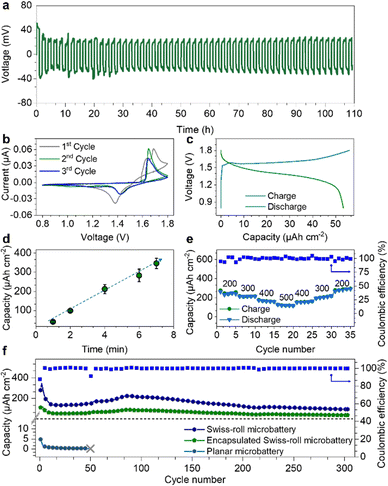 |
| Fig. 3 Electrochemical performance of the Swiss-roll microbattery. (a) Galvanostatic cycling of Zn/Zn planar symmetrical cell at a current density of 200 μA cm−2. (b) CV curve of the Swiss-roll microbattery collected at a scan rate of 0.1 mV s−1. (c) GCD curves at a current density of 200 μA cm−2 (1 min MnO2 deposition). (d) Effect of the MnO2 deposition time on the areal capacity of microbatteries. (e) Rate performance of microbattery. (f) Cycling performance of Swiss-roll microbattery, encapsulated Swiss-roll microbattery, and planar microbattery at a current density of 500 μA cm−2. | |
Fig. 4a compares the areal energy density of various microbatteries.23,45–51 Microbatteries have two common architectures: layered thin films and interdigitated electrode strips on the surface.45–47 Despite the high attainable energy density, they are larger than 1 mm2 because of difficulties in shrinking the size, such as maintaining the structural integrity with a small footprint and accuracy of layering down tiny films. With a small footprint area, the cycling performance is often compromised (less than 50 cycles) because the instability issues of materials and electrode structure are amplified at a small scale.45,46 For the first time, the electrode footprint (0.045 mm2) enters an unexplored regime of less than 0.1 mm2. Based on the electrode footprint, the energy density is 458 μW h cm−2. After a simple package by a SU8 box on a chip (Fig. S7, ESI†), the footprint of a full cell is slightly larger than 0.1 mm2 (0.11 mm2). The capacity and energy density of the on-chip packaged Swiss-roll micobattery are 136 μA h cm−2 and 181 μW h cm−2, respectively. The volumetric capacity and energy density excluding the chip thickness are 12.2 mA h cm−3 and 16.3 mW h cm−3, respectively. With the comparable energy density, the Swiss-roll microbattery is about one order of magnitude less than microbatteries with other architectures.45,47,51 More importantly, the cycling stability is among the best of microbatteries. Swiss-roll microelectrode also show the potential to achieve a higher energy density by using high-capacity materials (e.g., silicon, germanium).48,50
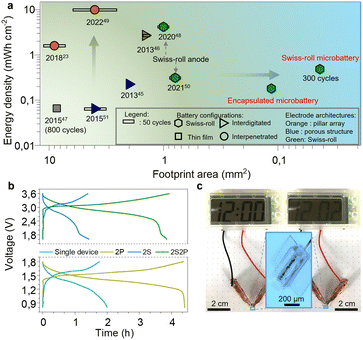 |
| Fig. 4 Comparison of Swiss-roll microbattery performance. (a) Comparison of areal energy density, footprint area, and cycling performance of Swiss-roll microbatteries with previously reported ones. (b) GCD curves of microbatteries connected in series and parallel. (c) Digital photographs of Swiss-roll microbattery powering a digital watch for two min (inset is the encapsulated Swiss-roll microbattery). | |
The microbattery can be connected in series and in parallel. The operation voltage doubles when two microbatteries are connected in series (Fig. 4b, upper panel). The charge/discharge time of two microbatteries connected in parallel (Fig. 4b, bottom panel) is twice that of the single one indicating twice capacity. Moreover, four microbatteries are assembled into a hybrid configuration, where two microbatteries are connected in series and then the series-connected microbatteries are connected in parallel (Fig. 4b, upper panel). This hybrid configuration attains a large capacity and high operational voltage. To demonstrate the feasibility for practical applications, the encapsulated microbattery is used as the power supply for electronic devices. As shown in Fig. 4c, the microbattery can power a digital watch with a screen for 2 min, implying that the Swiss-roll microbattery hold great promise in applications of integrated electronic devices.
Conclusions
In summary, a new strategy is presented to construct a microbattery with a footprint smaller than 0.1 mm2. The self-assembly process of thin films driven by inherent built-in strain forms a Swiss-roll structure that mimics the most rational electrode design for bulk batteries. As a result, the loading of MnO2 onto and into a microelectrode with a minimal footprint (0.021 mm2) can be substantially increased for achieving a high capacity of up to 345 μA h cm−2. Paired with a Zn Swiss-roll microanode, twin Swiss-roll electrodes occupy a small footprint of 0.045 mm2 and deliver an energy density of 458 μW h cm−2. Meanwhile, the on-chip packaged Swiss-roll micobattery with a footprint area of 0.11 mm2 achieves a high capacity of up to 136 μA h cm−2 and an energy density of 181 μW h cm−2. Furthermore, the on-chip fabrication procedure allows to build battery arrays in parallel in a single manufacturing run encouraging further development towards a new generation of microbatteries for autonomous microelectronic systems.
Author contributions
Yang Li, Minshen Zhu, Feng Zhu, Qunhong Weng, and Oliver G. Schmidt conceived the idea. Yang Li, Minshen Zhu, Feng Zhu, and Qunhong Weng designed experiments. Yang Li performed the experiment. Dmitriy D. Karnaushenko performed the FEM simulation. Lixiang Liu and Jiang Qu carried out XRD experiment. Yang Li, Jinhui Wang, and Vineeth Kumar Bandari contributed on the fabrication of microbattery. Yang Li, Panpan Zhang, and Zhe Qu contributed on the characterizations. Rachappa Ravishankar carried out AFM measurement. Fei Li and Hongmei Tang participated in analysis of the data. Yang Li, Minshen Zhu, Feng Zhu, Qunhong Weng, and Oliver G. Schmidt analyzed the results and wrote the manuscript with inputs from all authors.
Conflicts of interest
There are no conflicts to declare.
References
- N. Ilyas, J. Wang, C. Li, D. Li, H. Fu, D. Gu, X. Jiang, F. Liu, Y. Jiang and W. Li, Adv. Funct. Mater., 2021, 32, 2110976 CrossRef.
- K. Zhu, C. Wen, A. A. Aljarb, F. Xue, X. Xu, V. Tung, X. Zhang, H. N. Alshareef and M. Lanza, Nat. Electron., 2021, 4, 775–785 CrossRef CAS.
- Y. Li, M. Zhu, V. K. Bandari, D. D. Karnaushenko, D. Karnaushenko, F. Zhu and O. G. Schmidt, Adv. Energy Mater., 2022, 12, 2103641 CrossRef CAS.
- X. G. Guo, Z. G. Xue and Y. H. Zhang, NPG Asia Mater., 2019, 11, 1–7 CrossRef.
- D. Karnaushenko, T. Kong, V. K. Bandari, F. Zhu and O. G. Schmidt, Adv. Mater., 2020, 32, 1902994 CrossRef CAS PubMed.
- L. Liu and S. Choi, Biosens. Bioelectron., 2021, 177, 112970 CrossRef CAS PubMed.
- C. Y. Liu, E. I. Gillette, X. Y. Chen, A. J. Pearse, A. C. Kozen, M. A. Schroeder, K. E. Gregorczyk, S. B. Lee and G. W. Rubloff, Nat. Nanotechnol., 2014, 9, 1031–1039 CrossRef CAS PubMed.
- M. S. Zhu, Z. G. Wang, H. F. Li, Y. Xiong, Z. X. Liu, Z. J. Tang, Y. Huang, A. L. Rogach and C. Y. Zhi, Energy Environ. Sci., 2018, 11, 2414–2422 RSC.
- J. J. Shi, S. L. Wang, X. Chen, Z. C. Chen, X. Y. Du, T. Ni, Q. Wang, L. M. Ruan, W. Zeng and Z. X. Huang, Adv. Energy Mater., 2019, 9, 1901957 CrossRef CAS.
- Z. Lin, B. Xiao, M. Huang, L. Yan, Z. Wang, Y. Huang, S. Shen, Q. Zhang, L. Gu and W. Zhong, Adv. Energy Mater., 2022, 12, 2200855 CrossRef CAS.
- S. Shen, Z. Hu, H. Zhang, K. Song, Z. Wang, Z. Lin, Q. Zhang, L. Gu and W. Zhong, Angew. Chem., Int. Ed., 2022, 61, 202206460 Search PubMed.
- Z. Wang, S. Shen, Z. Lin, W. Tao, Q. Zhang, F. Meng, L. Gu and W. Zhong, Adv. Funct. Mater., 2022, 32, 2112832 CrossRef CAS.
- J. X. Zhao, H. Y. Lu, X. X. Zhao, O. I. Malyi, J. H. Peng, C. H. Lu, X. F. Li, Y. Y. Zhang, Z. Y. Zeng, G. C. Xing and Y. X. Tang, ACS Mater. Lett., 2020, 2, 1041–1056 CrossRef CAS.
- S. H. Zheng, X. Y. Shi, P. Das, Z. S. Wu and X. H. Bao, Adv. Mater., 2019, 31, 1900583 CrossRef CAS PubMed.
- L. Zhou, W. W. Ning, C. Wu, D. Zhang, W. F. Wei, J. M. Ma, C. C. Li and L. B. Chen, Adv. Mater. Technol., 2019, 4, 1800402 Search PubMed.
- K. Miyamoto, T. Sasaki, T. Nishi, Y. Itou and K. Takechi, iScience, 2020, 23, 101317 CrossRef CAS PubMed.
- Z. Y. Lyu, G. J. H. Lim, J. J. Koh, Y. Li, Y. W. Ma, J. Ding, J. L. Wang, Z. Hu, J. Wang, W. Chen and Y. F. Chen, Joule, 2021, 5, 89–114 CrossRef CAS.
- M. S. Zhu and O. G. Schmidt, Nature, 2021, 589, 195–197 CrossRef CAS PubMed.
- Z. Qu, M. Zhu, Y. Yin, Y. Huang, H. Tang, J. Ge, Y. Li, D. D. Karnaushenko, D. Karnaushenko and O. G. Schmidt, Adv. Energy Mater., 2022, 12, 2200714 CrossRef CAS.
- J. W. Deng, X. Y. Lu, L. X. Liu, L. Zhang and O. G. Schmidt, Adv. Energy Mater., 2016, 6, 1600797 CrossRef.
- X. F. Wang, Y. Chen, O. G. Schmidt and C. L. Yan, Chem. Soc. Rev., 2016, 45, 1308–1330 RSC.
- Y. Li, J. Qu, F. Li, Z. Qu, H. Tang, L. Liu, M. Zhu and O. G. Schmidt, Nano Mater. Sci., 2021, 3, 140–153 CrossRef.
- J. I. Hur, L. C. Smith and B. Dunn, Joule, 2018, 2, 1187–1201 CrossRef CAS.
- B. Bao, B. Rivkin, F. Akbar, D. D. Karnaushenko, V. K. Bandari, L. Teuerle, C. Becker, S. Baunack, D. Karnaushenko and O. G. Schmidt, Adv. Mater., 2021, 33, 2101272 CrossRef CAS PubMed.
- Y. Lee, V. K. Bandari, Z. Li, M. Medina-Sanchez, M. F. Maitz, D. Karnaushenko, M. V. Tsurkan, D. D. Karnaushenko and O. G. Schmidt, Nat. Commun., 2021, 12, 4967 CrossRef CAS PubMed.
- T. M. Li, V. K. Bandari, M. Hantusch, J. H. Xin, R. Kuhrt, R. Ravishankar, L. Q. Xu, J. D. Zhang, M. Knupfer, F. Zhu, D. H. Yan and O. G. Schmidt, Nat. Commun., 2020, 11, 3592 CrossRef PubMed.
- P. H. Yang, C. Z. Feng, Y. P. Liu, T. Cheng, X. L. Yang, H. D. Liu, K. Liu and H. J. Fan, Adv. Energy Mater., 2020, 10, 2002898 CrossRef CAS.
- J. Cao, D. D. Zhang, Y. L. Yue, X. Wang, T. Pakornchote, T. Bovornratanaraks, X. Y. Zhang, Z. S. Wu and J. Q. Qin, Nano Energy, 2021, 84, 105876 CrossRef CAS.
- G. J. Liang and C. Y. Zhi, Nat. Nanotechnol., 2021, 16, 854–855 CrossRef CAS PubMed.
- S. Wang, Z. S. Yuan, X. Zhang, S. S. Bi, Z. Zhou, J. L. Tian, Q. C. Zhang and Z. Q. Niu, Angew. Chem., Int. Ed., 2021, 60, 7056–7060 CrossRef CAS PubMed.
- M. S. Zhu, J. P. Hu, Q. Q. Lu, H. Y. Dong, D. D. Karnaushenko, C. Becker, D. Karnaushenko, Y. Li, H. M. Tang, Z. Qu, J. Ge and O. G. Schmidt, Adv. Mater., 2021, 33, 2007497 CrossRef CAS PubMed.
- C. Julien, M. Massot, R. Baddour-Hadjean, S. Franger, S. Bach and J. P. Pereira-Ramos, Solid State Ionics, 2003, 159, 345–356 CrossRef CAS.
- C. M. Julien and M. Massot, Mater. Sci. Eng., B, 2003, 100, 69–78 CrossRef.
- C. M. Julien, M. Massot and C. Poinsignon, Spectrochim. Acta, Part A, 2004, 60, 689–700 CrossRef CAS PubMed.
- Q. W. Tang, L. H. Jiang, J. Liu, S. L. Wang and G. Q. Sun, ACS Catal., 2014, 4, 457–463 CrossRef CAS.
- J. N. Hao, X. L. Li, X. H. Zeng, D. Li, J. F. Mao and Z. P. Guo, Energy Environ. Sci., 2020, 13, 3917–3949 RSC.
- Q. Li, Y. B. Wang, F. N. Mo, D. H. Wang, G. J. Liang, Y. W. Zhao, Q. Yang, Z. D. Huang and C. Y. Zhi, Adv. Energy Mater., 2021, 11, 2003931 CrossRef CAS.
- N. Zhang, F. Y. Cheng, Y. C. Liu, Q. Zhao, K. X. Lei, C. C. Chen, X. S. Liu and J. Chen, J. Am. Chem. Soc., 2016, 138, 12894–12901 CrossRef CAS PubMed.
- W. Sun, F. Wang, S. Hou, C. Yang, X. Fan, Z. Ma, T. Gao, F. Han, R. Hu, M. Zhu and C. Wang, J. Am. Chem. Soc., 2017, 139, 9775–9778 CrossRef CAS PubMed.
- Y. Huang, J. Mou, W. Liu, X. Wang, L. Dong, F. Kang and C. Xu, Nano-Micro Lett., 2019, 11, 49 CrossRef CAS PubMed.
- L. T. Ma, Q. Li, Y. R. Ying, F. X. Ma, S. M. Chen, Y. Y. Li, H. T. Huang and C. Y. Zhi, Adv. Mater., 2021, 33, 2007406 CrossRef CAS PubMed.
- Y. Yang, C. Y. Liu, Z. H. Lv, H. Yang, Y. F. Zhang, M. H. Ye, L. B. Chen, J. B. Zhao and C. C. Li, Adv. Mater., 2021, 33, 2007388 CrossRef CAS PubMed.
- H. L. Pan, Y. Y. Shao, P. F. Yan, Y. W. Cheng, K. S. Han, Z. M. Nie, C. M. Wang, J. H. Yang, X. L. Li, P. Bhattacharya, K. T. Mueller and J. Liu, Nat. Mater., 2016, 1, 16039 CrossRef CAS.
- M. Fojtik, D. Kim, G. Chen, Y.-S. Lin, D. Fick, J. Park, M. Seok, M.-T. Chen, Z. Foo, D. Blaauw and D. Sylvester, IEEE J. Solid-State Circuits, 2013, 48, 801–813 Search PubMed.
- J. H. Pikul, H. Gang Zhang, J. Cho, P. V. Braun and W. P. King, Nat. Commun., 2013, 4, 1732 CrossRef PubMed.
- K. Sun, T. S. Wei, B. Y. Ahn, J. Y. Seo, S. J. Dillon and J. A. Lewis, Adv. Mater., 2013, 25, 4539–4543 CrossRef CAS PubMed.
- F. Le Cras, B. Pecquenard, V. Dubois, V. P. Phan and D. Guy-Bouyssou, Adv. Energy Mater., 2015, 5, 1501061 CrossRef.
- H. M. Tang, D. D. Karnaushenko, V. Neu, F. Gabler, S. T. Wang, L. X. Liu, Y. Li, J. W. Wang, M. S. Zhu and O. G. Schmidt, Small, 2020, 16, 2002410 CrossRef CAS PubMed.
- M. Sternad, G. Hirtler, M. Sorger, D. Knez, K. Karlovsky, M. Förster and H. M. R. Wilkening, Adv. Mater. Technol., 2021, 7, 2100405 CrossRef.
- Q. Weng, S. Wang, L. Liu, X. Lu, M. Zhu, Y. Li, F. Gabler and O. G. Schmidt, Cell Rep., 2021, 2, 100429 CAS.
- H. L. Ning, J. H. Pikul, R. Y. Zhang, X. J. Li, S. Xu, J. J. Wang, J. A. Rogers, W. P. King and P. V. Braun, Proc. Natl. Acad. Sci. U. S. A., 2015, 112, 6573–6578 CrossRef CAS PubMed.
|
This journal is © The Royal Society of Chemistry 2023 |
Click here to see how this site uses Cookies. View our privacy policy here.