DOI:
10.1039/D3IM00009E
(Minireview)
Ind. Chem. Mater., 2023,
1, 155-174
Industrially applied and relevant transformations of 1,3-butadiene using homogeneous catalysts
Received
23rd January 2023
, Accepted 7th April 2023
First published on 12th April 2023
Abstract
In recent decades, the use of 1,3-butadiene as a comparably cheap and abundant raw material for new applications has attracted more and more interest, specifically in the chemical industry. The present review covers several of the most important homogeneously catalyzed processes and technologies which are currently used or have the potential to produce fine and bulk chemicals from 1,3-butadiene. As an example, palladium-catalyzed telomerizations provide valuable chemicals through the selective dimerization of 1,3-dienes with the simultaneous addition of various nucleophiles, which can be used for the synthesis of 1-octene, 1-octanol, and various lactones. On the other hand, direct carbonylation allows the selective introduction of functional groups onto 1,3-dienes, such as carbonyl, carboxyl or ester groups. The key to success in achieving these industrially relevant conversions of 1,3-butadiene was mainly the development of innovative efficient catalysts. We hope this review will make readers familiar with the industrially applied and relevant transformations of 1,3-butadiene and inspire them to further explore new and advanced systems.
Keywords: 1,3-Butadiene; Industrial chemistry; Carbonylation reaction; Bulk chemicals; Telomerization.
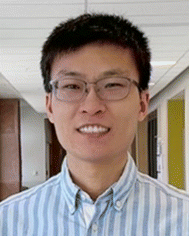 Ji Yang | Dr. Ji Yang received a Master's degree at the Shanghai Institute of Organic Chemistry (SIOC, CAS) in 2017 and continued his graduate research at the Leibniz Institute for Catalysis e.V. (LIKAT Rostock, Germany) from 2017 to 2020, where he developed a carbonylation path to a nylon precursor. He is currently a Postdoctoral Research Fellow in the University of Maryland where his research is focused on the development of extreme materials and catalysts. |
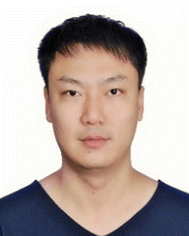 Peng Wang | Peng Wang received his Ph.D. degree in physical chemistry from East China Normal University in 2018. Then he worked as a post-doc in Shanghai institute of Organic Chemistry (SIOC) and Leibniz Institute for Catalysis (LIKAT) from 2018 to 2022. He is currently a R&D Engineer. His research interests focus on the hydroformylation of unsaturated hydrocarbons. |
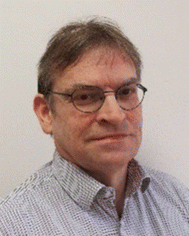 Helfried Neumann | Dr. Helfried Neumann studied chemistry at the University Erlangen, Germany, and finished his PhD studies there in 1995 under the supervision of Rainer Herges and Paul Rague von Schleyer. In 1996, he joined the Institute of Organic Catalysis in Rostock (IfOK, which was later renamed to Leibniz-Institute für Katalyse e.V.) and became project leader since 1998. His current research activities are concerned with carbonylation reactions, “hydrogen-borrowing” concept, perfluoroalkylation of arenes and the development of new ligands. |
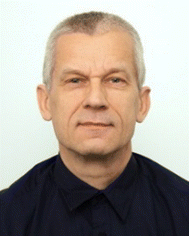 Ralf Jackstell | Dr. Ralf Jackstell received a teacher degree in chemistry and mathematics at the University of Rostock in 1994. In 1998 he received his PhD degree in phosphororganic chemistry at the University of Rostock. Since that time, he has been working at LIKAT in Rostock as group and currently topic leader in “Applied carbonylations”. His main research studies are related to carbonylation and hydrogenation reactions and have been published in >170 publications. |
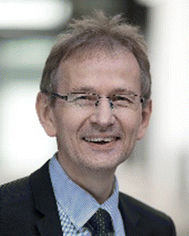 Matthias Beller | Matthias Beller is scientific director of the Leibniz-Institute for Catalysis, Rostock, Germany, and Vice-president of the Leibniz Association and a member of the German National Academias “Leopoldina” and “Acatech”. The research of his group focuses on homogeneous and heterogeneous catalysis for the sustainable synthesis of fine/bulk chemicals and energy technologies and has been published in >1100 articles (https://www.catalysis.de/en/people/beller-matthias). |
1 Introduction
1.1 General properties of 1,3-butadiene
In the chemical industry, the term butadiene (BD) generally refers to 1,3-butadiene with CAS number 106-99-0, which can be regarded as the most simple conjugated 1,3-diene with the chemical structure H2C
CH–CH
CH2.1 As a comparison, the thermodynamically less stable 1,2-butadiene with CAS number 590-19-2, which has two cumulated double bonds with the formula H2C
C
CH–CH3, has only minor importance.2 Considering the physical properties, its flash point (85 °C) and ignition temperature (415 °C) are relatively low. When mixed with atmospheric oxygen at 101.3 kPa and 20 °C, unstable 1,3-butadiene tends to form explosive peroxides between the concentrations of 1.1 and 16.3 vol%.
Regarding its special structure and configurations, the planar σ-trans conformer of 1,3-butadiene is more stable, in which case the two pairs of double bonds are facing opposite directions.3 This configuration not only minimizes the steric hindrance but also maximizes the orbital overlap between double bonds. In contrast, the σ-cis configuration with a 0° dihedral angle is approximately 3.9 kcal mol−1 higher in energy than the σ-trans conformation with a C2–C3 dihedral angle of 180°.4 However, 1,3-butadiene needs to adopt this s-cis configuration to participate in concerted addition reactions. Similarly, a collaborative study combined with experiments and DFT calculation has revealed that the double bond length of σ-trans-butadiene is 133.8 pm. Compared to the bond length of 133.0 pm in ethylene, the slight change in bond length is taken as evidence of a delocalized π structure and a modest degree of partial double bond quality in the middle C2–C3 single bond, in consensus with the resonance theory. A comparison of bond energies also reveals that 1,3-butadiene is stabilized thermodynamically. When comparing the hydrogenation energy, 57.1 kcal mol−1 released by 1,3-butadiene is slightly less than 60.6 kcal mol−1 of twice isolated C
C bond energy, which can be taken as a resonance stabilization energy of 3.5 kcal mol−1.5,6
1.2 Discovery and history of 1,3-butadiene
In 1863, 1,3-butadiene was first isolated by the French chemist Joseph-Bienaimé Caventou from the pyrolysis of pentanol. Then, in 1886, the structural formula was identified with conjugated double bonds.7 1,3-Butadiene was also obtained and analyzed by Henry Edward Armstrong when he investigated the pyrolysis of petroleum.8 An important milestone of butadiene chemistry was the discovery of the Russian chemist Sergei Lebedev in 1910, who found that 1,3-butadiene could be polymerized to obtain an elastic material with properties similar to those of natural rubber. This discovery opened the door for the use of 1,3-butadiene in the chemical industry.9 Following in 1929, chemists Walter Bock and Eduard Tschunker at IG Farben in Germany invented a novel material by copolymerizing styrene and 1,3-butadiene that can be used as automobile tires.10,11 The widespread convenience of this material led to a flow in demand for 1,3-butadiene, so processes of manufacturing 1,3-butadiene were developed rapidly at that time, including catalytic processes through alcohols developed in Russia and the USA, and acetylene synthesis routes developed in Germany.
1.3 Today's industrial production
Despite the delicate structure of 1,3-butadiene, especially the easily converted unsaturated double bonds, it is the 36th highest industrially produced chemical and economically the most important unsaturated C4 hydrocarbon. The production capacity of 1,3-butadiene is expected to increase from 14.2 million metric tons in 2020 to almost 16 million metric tons worldwide by 2025 (Fig. 1).12–16
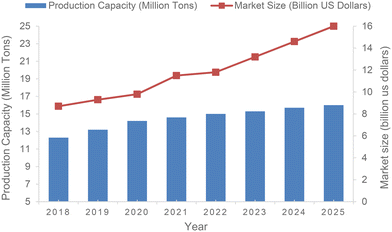 |
| Fig. 1 Production volume and market size of 1.3-butadiene. | |
Currently, 1,3-butadiene is favorably produced from C4 fractions isolated by cracking of naphtha and crude oil. When heated to a high temperature of 900 °C, these feedstocks are dehydrogenated to obtain unsaturated hydrocarbons containing 1,3-butadiene.17 In addition, 1,3-butadiene can also be prepared by heterogeneous dehydrogenation of n-butane. As a representative example, the first such industrialized plant, manufacturing 65
000 tons of 1,3-butadiene annually, began operations in Houston in 1957.18,19 This plant commercially used the Houdry Catadiene process (HCP), which involves treating butane at high temperatures with an aluminum and chromium catalyst.1 Additionally, 1,3-butadiene is also produced from ethanol in some parts of the world including China, Eastern Europe and India. In this latter process, 1,3-butadiene is manufactured at 400–450 °C by utilizing various metal oxide catalysts, and alternatively at 325–350 °C using tantalum catalyst supported on porous silica.20 It is noteworthy that significant development studies are currently underway to produce 1,3-butadiene from renewable resources via not only classical chemocatalytic but also biocatalytic transformations.
1.4 Main uses and applications
Nowadays, 1,3-butadiene is one of the most important bulk chemicals, which has a wide range of applications and has penetrated all aspects of our daily life. There are 16
211 publications/patents from 2010 to 2022 published with the key word 1,3-butadiene in the Web of Science Core Database (Fig. 2, search time on November 1, 2022). These publications show a trend that research on 1,3-butadiene is becoming more and more emphasized. Also, after analyzing these data it is obvious that the main applications of 1,3-butadiene lie in the field of polymer materials. As a representative product, polybutadiene rubber (PBR) has adjustable tough or elastic properties depending on the proportions of raw materials used in its preparation.21,22 Meanwhile, styrene–butadiene rubber (SBR) is the most common material for making automobile tires.23–25 The powerful properties of these rubber polymers bring tires with performance-enhancing components in terms of rolling resistance and traction. With the rapid development of the electronic industry, acrylonitrile–butadiene–styrene (ABS) has become the largest engineering thermoplastic resin, widely used in mobile phones, household appliances, computers, and office products.26,27 Simultaneously, numerous chemicals produced from 1,3-butadiene are also widely used to manufacture paper coatings, turf, carpets, gloves, wetsuits, toys and other consumer products. Considering that there are already various reviews/books on industrial polymers based on 1,3-butadiene for readers to refer to,21–27 this review will not duplicate this section but center on industrial transformation examples and some promising progress in recent research to produce other bulk chemicals. In particular, we will focus on the development of catalytic systems achieving transformations of 1,3-BD towards functionalized products with high atom economy and avoiding environmental pollution.
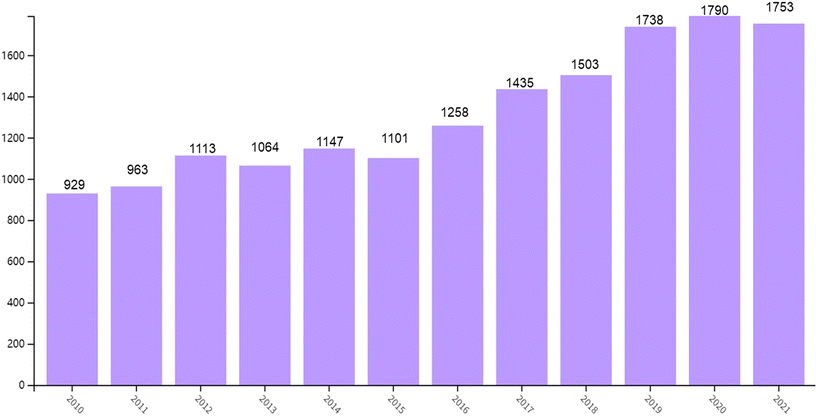 |
| Fig. 2 Number of publications from 2010 to 2021 with the key word butadiene. | |
2 Selected current applications in industry
2.1 1-Octene via telomerization with methanol (Dow process)
Dow Chemical developed and patented a commercial route in 1992 to produce 1-octene based on the telomerization of 1,3-butadiene and MeOH as shown in Scheme 1.28 The process has been in industrial operation in Tarragona since 2008 using crude C4 fractions from cracking furnaces as raw materials. The key intermediate in this process is 1-methoxy-2,7-octadiene (1-MOD), which was synthesized in the presence of a palladium/triarylphosphine catalytic system.29,30 Later on, Oxeno Ind. (now Evonik Industries) patented and applied similar processes utilizing palladium salts in the presence of N-heterocyclic carbenes in 2002 and 2005.31,32 Overall, the relevant process can be described as follows: the initially obtained telomerization product 1-MOD is completely hydrogenated to 1-methoxyoctane with >99% yield. Subsequently, base-catalyzed cracking at high temperature leads to 1-octene with 97% yield and methanol for recycling. According to the information of relevant patents,28–30 great reaction efficiency and high selectivity were obtained in the second and third steps, and related products could be basically obtained by quantitative conversion. Therefore, the first step, i.e., the telomerization of 1,3-butadiene with methanol, determines the overall efficiency of the process.
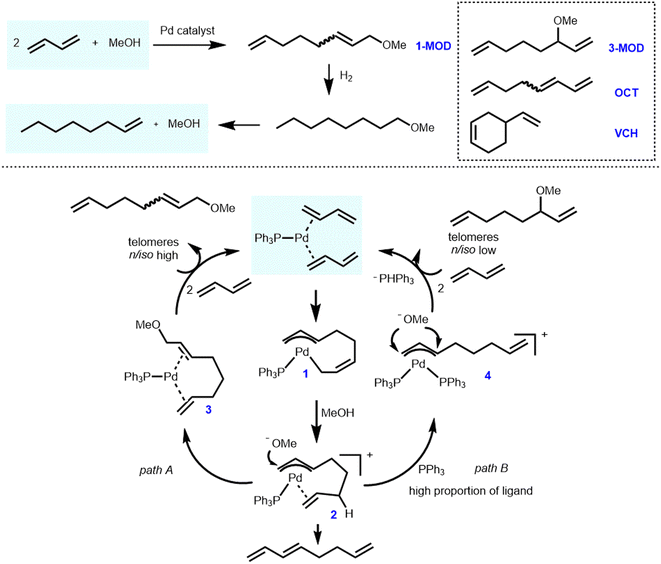 |
| Scheme 1 Simplified Dow process and mechanism for the telomerization of 1,3-butadiene with methanol. | |
Originally, the telomerization reaction of 1,3-butadiene was discovered in 1967 by Smutny at Shell and Takahashi at Osaka University independently.33,34 The name telomerization refers to the oligomerization of 1,3-dienes with a nucleophile (in terms of “telogen”). Interestingly, the nucleophile can be of various proton-containing types such as alcohols,35–51 polyols,52–58 acids,59–62 water,63–77 ammonia,78,79 amines,80–90 and biomass-based components.91–100 Therefore, this highly efficient and promising reaction has been intensively studied in many renowned industrial and academic laboratories.101
2.1.1 Mechanism.
In the presence of a suitable catalyst, the telomerization of 1,3-butadiene and MeOH produces initially 1-methoxyocta-2,7-diene (1-MOD) as the main product. Simultaneous formation of 3-methoxyocta-1,7-diene (3-MOD) and 1,3,7-octatriene (OCT) as dimerization products and 4-vinylcyclohexene (VCH) produced by a concerted pericyclic Diels–Alder reaction are often observed, too.
With the aim of improving the efficiency and selectivity, the mechanism of this reaction has attracted extensive attention. Jolly and colleagues first investigated this process, specifically the η3-allylpalladium intermediate analyzed by NMR.102 Later on, some of us have also conducted in-depth research on the mechanism utilizing representative palladium/phosphine catalysts. Thereby, we not only clearly revealed the related side reactions but also showed the multiple roles of phosphine ligands in this catalytic process.103–105 The extended reaction mechanism is as follows (Scheme 1).104,105 Initially, two molecules of 1,3-butadiene are oxidatively coupled at a low-coordinated ligand–palladium(0) center to form ligand–palladium–(η3,η1-octadiendiyl) active species 1. Selective protonation of species 1 by MeOH at the C6 site results in the ligand–palladium–(η3,η2-octadiendiyl) complex 2. Subsequent attack of the methoxy group at the allylic position (site 1 or 3) leads to linear or branched (1- or 3-substituted) products, respectively. Both intermediates 1 and 2 were characterized and studied in detail. More specifically, the linear/branched selectivity of this reaction was significantly affected by the nature of the phosphine ligand. The formation of Pd–bimolecular phosphine or Pd–PPh3–butadiene complex 4 was enhanced respectively by increased triphenylphosphine/Pd ratio or increased concentration of 1,3-butadiene, leading to a larger extent of branched product 3-MOD. At the same time, an insufficient amount of phosphine makes the system less stable, resulting in irretrievable phosphine oxidation and precipitation of palladium metal. Furthermore, some of us were involved in computational studies on telomerization intermediates to assist in further understanding of this process.106
2.1.2 Catalyst developments.
The ligand presumably used in the Dow process is a triarylphosphine, which is available relatively inexpensively on an industrial scale.107 Simple triphenylphosphine generally leads only to a moderately efficient catalyst with unsatisfactory linear/branched selectivity.94 Therefore, extensive research has been devoted to the development of novel catalysts with improved performance.
Several functionalized triaryl phosphines containing oxygen atoms were employed in this reaction and selected results are summarized in Fig. 3. By altering the electronic and steric properties of the ligand as well as the position and amount of hemilabile coordination groups, the catalytic efficiency of triaryl phosphine ligands substituted with methoxy groups was determined. For example, introducing one methoxy substituent on the aryl ring of the phosphine could increase the conversion of 1,3-butadiene by 26% and the selectivity of 1-MOD by 15%.30,42 By using ligands 7 and 8, which possess two or three ortho-MeO groups, respectively, up to 94% selectivity was obtained. Furthermore, ligand 9 with para-methoxy groups exhibited the best catalytic activity with a catalyst TON of 22
784. Trialkyl phosphines were also studied for this process by Carlini and co-workers.41,42 As a general rule, the tested ligands proved to be more productive than PPh3 at low reaction temperature (60 °C). Regarding the selectivity towards 1-MOD, linear triethylphosphine 12 and tributylphosphine 13 showed higher selectivity than PPh3, while sterically hindered triisopropylphosphine 14 and tricyclohexylphosphine 15 preferably formed 1,3,7-octatriene as the formal dimerization product.
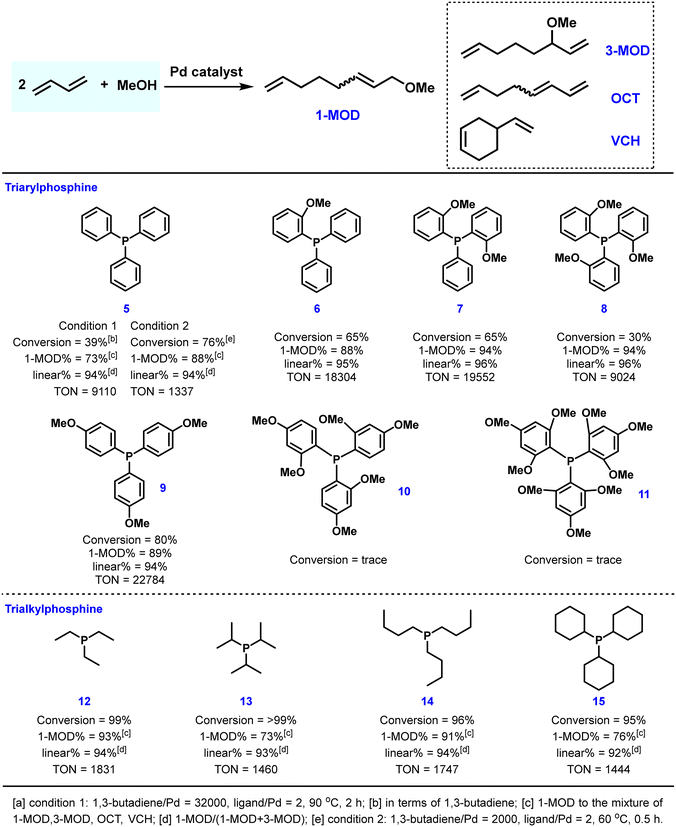 |
| Fig. 3 Performance of selected monophosphine ligands used in the palladium-catalyzed telomerization reaction of 1,3-butadiene with methanol. | |
In order to improve catalyst stability and shorten the induction period for the formation of the active catalyst species, different palladium complexes were also investigated as catalyst precursors. Inspired by the easily prepared monophosphine–Pd(0)–(1,6-diene) catalyst reported by Pörschke,108 several enhancements were made by some of us for the telomerization of 1,3-butadiene with methanol. For example, the reaction can proceed smoothly even at −10 °C by using a triphenylphosphine–palladium–(η2,η2-allylether) catalyst 16.40 At the same time, such catalysts, including 1,3-divinyltetramethyldisiloxane (dvds) 17, are stable in air and easy to handle.
Van Leeuwen and collaborators studied the structure effects of bulky phosphines 18–20 in detail (see Fig. 4), which were used for cross-coupling reactions previously.109,110 Ligands with a xanthene backbone exhibited superior properties, especially regarding selectivity, activity and stability. Among these phosphines, ligand 18 showed highly satisfactory results, reaching a TOF of 140
000 h−1 in 5 min at 100 °C with up to 84% selectivity for 1-MOD. Further, the modified electron-rich ligand 19 showed to be a more outstanding monoXantphos ligand, increasing 1,3-butadiene conversion to 95% and selectivity for 1-MOD to 93% at 90 °C. Under industrial production conditions, monoSPANphos 20 was a very active ligand at low temperature with better stability at 90 °C for this reaction. Through structural and activity analysis, the reasonable backbone design and the coordination properties of oxygen atoms were considered to be the reason for this better performance.111
 |
| Fig. 4 Other ligand development for the palladium-catalyzed telomerization of 1,3-butadiene with methanol. | |
Essentially, classical bidentate phosphine ligands with diverse structures were also studied for the Dow telomerization reaction (Fig. 4). In the case of diphosphine ligands, such as dppm, dppe, and dppp (n = 1–3), these ligands exhibited lower activity compared to PPh3. Yet, the conversion significantly improved from DPPB 24 to DPPH 25 (n = 4 to 6) as the bite angle of the ligands increased. To allow for easier catalyst recycling, we further developed bidentate phosphines 26 and 27 with a binaphthyl backbone for the reaction of 1,3-butadiene and MeOH under organic or two-phase conditions.112 So far, the bidentate phosphine catalysts with the highest selectivity towards 1-MOD were ligand 28 and 29 (92–96% selectivity at 70 °C).113
N-Heterocyclic carbenes (NHCs) are also very important ligands for catalysts applied in telomerization reactions due to their similar properties to phosphine ligands.114–117 Hence, a series of structurally diverse NHC–Pd catalysts 30–34 were developed and investigated. In these studies, triphenylphosphine was used as a reference to compare the activities of different N-heterocyclic carbenes. As presented in Table 1, at a low temperature of 50 °C, triphenylphosphine did not catalyze the conversion of 1,3-butadiene (entry 3). However, in comparison, NHC 30 showed obvious activity and yielded 57% of the products (entry 7). When the reaction temperature was further increased to 70–90 °C, catalyst 30 exhibited an amazing activity for complete conversion of 1,3-butadiene with 97% linear selectivity (entries 10 and 6). To verify the activity and stability of this powerful catalytic system, even using a very small catalyst dosage (0.00033 mol%) led to complete conversion of the reaction and gave 89% yield of the desired products with high productivity (entry 8, TON = 267
000, TOF up to 100
000 h−1). Further reducing the catalyst loading of 30 at 90 °C resulted in an efficiency of 1
540
000 in 97% linear selectivity.38–40,118,119 Remarkably, the selectivity to the desired linear product stayed fixed at about 97% even at different temperatures. Most importantly, this Pd–carbene catalytic system exhibited excellent activity and stability even when using C4 crack as a source of 1,3-butadiene (C4 crack = 42% 1,3-BD, 25% isobutene, 16% 1-butene, 5% 2-butene, 5% isobutane and 7% others). This system has been utilized by Evonik on a continuous pilot plant scale with a capacity of tons in Marl, Germany.38,119
Table 1 Comparison between N-heterocyclic carbene and phosphines for the telomerization of 1,3-BD with MeOH
Entry |
Ligand |
Pd(OAc)2 (mol%) |
T (°C) |
MOD yield (%) |
Chemoselectivityb (%) |
Linear : branched |
TON |
Conditions: 1.0 mol% NaOH, methanol/1,3-butadiene = 2, 16 h.
Chemoselectivity = MOD/product mixture × 100%.
Conditions: Pd loading = 0.001 mol%, 16 h, 1.0 mol% NaOMe, methanol/1,3-butadiene = 2.
|
1a |
PPh3 |
0.001 |
90 |
79 |
90 |
12 : 1 |
78 700 |
2c |
PPh3 |
0.001 |
70 |
26 |
87 |
24 : 1 |
26 000 |
3a |
PPh3 |
0.001 |
50 |
2 |
— |
13 : 1 |
2000 |
4a |
PnBu3 |
0.001 |
90 |
57 |
90 |
10 : 1 |
57 000 |
5a |
17 |
0.001 |
90 |
60 |
77 |
10 : 1 |
60 000 |
6a |
30 |
0.001 |
90 |
≥98 |
99 |
36 : 1 |
98 000 |
7a |
30 |
0.001 |
50 |
57 |
>99 |
82 : 1 |
57 000 |
8a |
30 |
0.00033 |
90 |
89 |
98 |
41 : 1 |
267 000 |
9a |
30 |
0.00005 |
90 |
77 |
99 |
49 : 1 |
1 540 000 |
10c |
30 |
0.001 |
70 |
96 |
>99 |
49 : 1 |
96 000 |
11c |
31 |
0.001 |
70 |
93 |
99 |
49 : 1 |
93 000 |
12c |
32 |
0.001 |
70 |
96 |
>99 |
49 : 1 |
96 000 |
13c |
33 |
0.001 |
70 |
90 |
97 |
12 : 1 |
90 000 |
14c |
34 |
0.001 |
70 |
2 |
— |
10 : 1 |
2000 |
In addition to the studies of conditions and catalysts, other aspects, including catalyst recovery, two-phase production systems, continuous reaction in loop reactors, ionic liquids as solvents, etc., have been studied by various research groups in detail.35,36,120 Similar to the Dow process, several major companies have also investigated the expansion of nucleophiles. For instance, Shell developed the telomerization of 1,3-butadiene with acetic acid.121,122 Evonik reported the telomerization of 1,3-butadiene with formic acid,123,124 giving a formate that can be used for the decarboxylation process to produce octa-1,7-diene as a 1-octene precursor.125
2.2 1-Octanol via telomerization with water (Kuraray process)
Compared with telomerization with methanol, the telomerization process with water as a nucleophile is more challenging. Nevertheless, the production of 2,7-octadien-1-ol by telomerization of 1,3-butadiene with water is also a very attractive process. Analogously to the aforementioned Dow process, 1-octanol as target chemical can be obtained from 1,3-BD via initial telomerization and subsequent hydrogenation of 2,7-octadien-1-ol. This specific telomerization reaction was first reported by Atkins in 1970.126 Thereafter, the process has been studied extensively by industrial companies, such as Kuraray,127–130 BASF,131,132 Arkema133 and Mitsubishi.134,135 Representatively, Kuraray has implemented this process in production in Japan (>5000 T annually).136 Crucial for the success of this process is the reaction of 1,3-butadiene with water in a basic (pH >7) aqueous sulfolane solution, which contains the palladium catalyst, a phosphonium salt, e.g. 2-(diphenylphosphino)benzenesulfonic acid sodium, as precursor of the phosphine ligand, and carbonate or bicarbonate or tertiary amines.137
In contrast to the telomerization of 1,3-butadiene with methanol, the one with water is positively influenced by the presence of carbon dioxide.138,139 Surprisingly, carbon dioxide can effectively inhibit the here unwanted dimerization process of 1,3-butadiene. Even more, an effective concentration of carbon dioxide can accelerate the progress of telomerization and improve the selectivity of the linear product. Based on these observations, Kuntz and co-workers developed a reaction protocol that uses carbonate instead of carbon dioxide to avoid pressure equipment.140,141 Finally, it is worth mentioning that Monflier and co-workers described a positive effect on related telomerization reactions using a cationic surfactant instead of organic solvent.70,142
2.3 Production of adiponitrile by double hydrocyanation reaction of 1,3-butadiene
Another industrially important catalytic conversion of 1,3-butadiene with an annual output of one million tons is the DuPont adiponitrile (ADN) process.143 ADN is a central chemical intermediate not only used to manufacture polyamides144,145 but also widely used to produce 1,6-hexanediamine (as shown in Scheme 2),146 adipic acid, and adipamide as well as several pharmaceutical and agricultural products. Originally in industry, 1,4-dichloro-2-butene derived from the chlorination of 1,3-butadiene was used as a precursor for the synthesis of adiponitrile, which was then further reacted with cyanide salts to produce adiponitrile. Considering the strong corrosiveness of chlorine and the high waste contamination of the process, simpler processes with better atom economy were extremely desired.147,148 In 1954, Arthur and co-workers first discovered the Co2(CO)8-catalyzed hydrocyanation of olefins with HCN as an economical source of nitriles.149 Further, Drinkard presented a tailored Ni((ArO)3P)4 catalyst system for the hydrocyanation reaction with higher activity.150 Researchers therefore shifted their interest to the double hydrocyanation of 1,3-butadiene, which in principle allows for 100% atom economy. The hydrocyanation of 1,3-butadiene proceeds through relatively stable π-allyl nickel cyanide intermediates. The isolation of the 16-electron complex [Ni(P(O-tolyl)3)] containing a bulky monophosphite provided a rational beginning to study how various aspects of the catalytic system interact with nickel.149 The formation and decomposition of nickel hydrides and specifically [HNi(CN)L3] in solution was investigated in detail by Tolman by 1H and 31P NMR spectroscopy.151 It should be noted at this point that the research performed in this route has led to several important discoveries in organometallic chemistry.149,150 At the same time, DuPont put this process into production for the first time in 1971.151 The DuPont process can be basically described as follows: in the presence of Ni catalyst, 1,3-butadiene and HCN are quickly converted to a mixture of pentenenitriles (linear to branched isomers in a 2
:
1 ratio). It is worth noting that experiments showed that electronic effects play only a minor role compared to steric effects in determining the catalytic activity and selectivity of the Ni complexes investigated. Therefore, monodentate phosphites were replaced by bulky bidentate ligands, which create catalysts superior in terms of activity and efficiency. Subsequently, various biphenol-based diphosphate Ni0 complexes were synthesized and applied in butadiene hydrocyanation. Such Ni catalysts, although less selective, showed a catalyst turnover at least four times higher than that of the industrially applied DuPont system [Ni(P(O-tolyl)3)]. In order to obtain the selective product, it is important to carry out the fast isomerization of different intermediates. In this respect, the addition of Lewis acids, such as ZnCl2, facilitates the isomerization of 2M3BN. The kinetic preference for the isomerization of an internal alkene to a terminal alkene contrast with the thermodynamic preference for the conjugated isomer 2PN. The isomerization of the internal alkene 3PN to the terminal alkene 4-pentenenitrile (4PN) is a decisive step in the hydrocyanation of 3PN. With the help of an additional Lewis acid, the branched by-products can be reversibly isomerized into the terminal olefin isomer. In general, through the above processes, first, the hydrocyanation reaction of 1,3-butadiene led to the desired 4-pentenenitrile with >90% selectivity.152 Next, 4-pentenenitrile reacted at a second stage with HCN at lower temperature (about 50 °C) to produce adiponitrile, typically in 50% yield and 92% linear selectivity.153
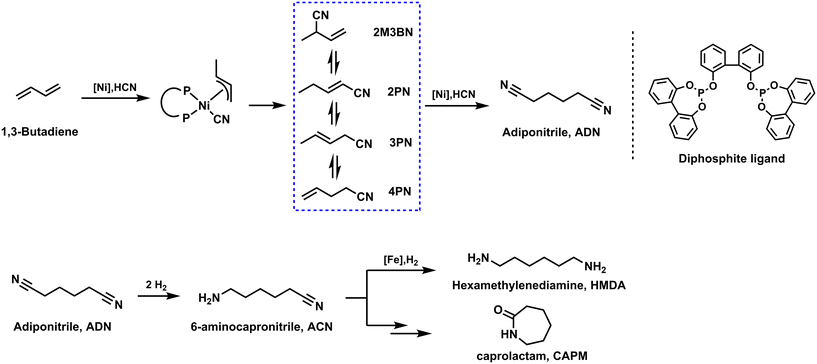 |
| Scheme 2 Simplified scheme for the synthesis of adiponitrile from 1,3-butadiene. | |
3 Potential uses of 1,3-buatdiene in the future
3.1 Adipates via catalytic carbonylation of 1,3-butadiene
Adipates and adipic acid are core intermediates of the polymer industry. About 75% of the total adipate production is consumed by nylon manufacturing.154 The current global annual output of adipates exceeds 5
000
000 tons with an average growth rate of 4%, whose market size is expected to exceed USD 11 billion by 2025.155,156 A main problem in adipate manufacture is the environmental pollution by waste acid exhaust and nitrous oxide gases. For example, in 2016, the production of adipic acid alone released 20% of the 37.3 million metric tons of all gas emissions (CO2, CH4 and NO2) by the chemical industry in the U.S.157 Notably, the global warming potential of the major nitrous oxide emissions is 300 times higher than that of carbon dioxide.158 In order to balance the growing demand for adipates and reduce the negative impact on the environment, greener and atom-economical chemical processes need to be implemented urgently.159
In this regard, metal-catalyzed carbonylation reactions of 1,3-butadiene to adipates are promising alternative ways for manufacturing versatile adipates, among which the linear selective dihydroformylation of 1,3-butadiene is of great interest to industry and academic laboratories.160–162 However, this double hydroformylation reaction is extremely challenging due to slow reaction rate, regioselectivity problems, and low product stability, especially in basic or acidic media, inevitably forming a large number of unwanted by-products. Simultaneously, the aldol addition reactivity of aldehyde intermediates leads to incompatibility between this process and typical industrial distillation techniques.163 Therefore, in 2016 Hofmann and co-workers developed an isomerizing hydroformylation process in which pentenal intermediates were converted to acetates in situ to avoid side products.164 Fundamental insights into the reaction pathways of this rhodium-catalyzed dihydroformylation were obtained; the adipaldehyde selectivity was found to be strongly dependent on the bite angle and the backbone structure of the ligand used in the reaction.165 Regarding state-of-the-art catalysts, ligand 35 provided 50% yield of adipic aldehyde from 1,3-butadiene, or 93% yield starting from 4-pentenal (Fig. 5).166 Recently, QIBEBT-phosphite 38 developed by Yang and co-workers exhibited a slightly improved yield of 54% to adipic dialdehyde from 1,3-butadiene.167 However, unfortunately these results seem to be still insufficient for industrial applications.168
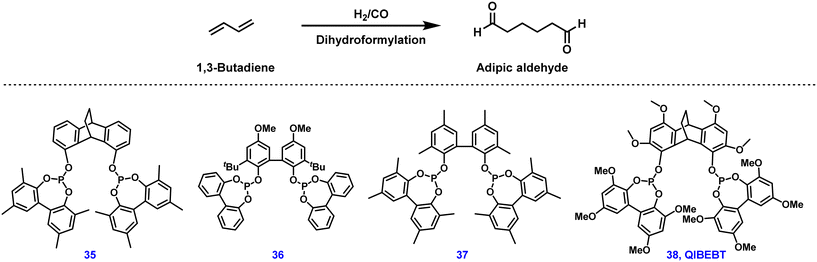 |
| Fig. 5 Representative ligands for linear selective dihydroformylation of 1,3-butadiene. | |
Besides the dihydroformylation process, carbonylation reactions of 1,3-butadiene utilizing alcohol/water as nucleophiles to synthesize adipates directly constitute also highly attractive reactions to both academia and industry. Clearly, these 100% atom-economic reactions would make the production of adipate/acid more environmentally friendly (Fig. 6). However, again such catalytic processes also face various challenges: (i) the catalyst should mediate two diverse carbonylation processes continuously, which places elevated demands on the activity and stability of the catalyst; (ii) in order to obtain a linear dicarbonylation product, the reaction intermediates must undergo a particularly thermodynamically unfavorable isomerization; and (iii) various side conversions such as telomerization, hydroalkoxylation, carboxytelomerization and (co)polymerization must be suppressed to improve the yield of adipates.183
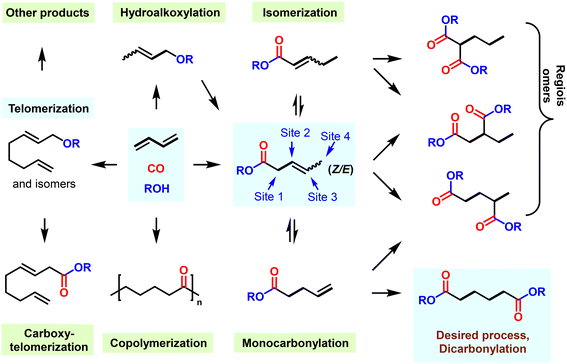 |
| Fig. 6 The complex reaction network for the synthesis of adipates from 1,3-butadienes. | |
Back in 2002, some of us uncovered a suitable alkoxycarbonylation of 1,3-dienes using a palladium-based catalyst in combination with the ligand DPPB 24, resulting in 3-methyl pentanoate with a yield of 69% (Fig. 7a).169 By 2014, it was found that under similar conditions, the yield of 3-methyl pentanoate could be increased to 85% under acid-free conditions when Xantphos was used as the ligand.170 Afterwards, diverse site-selective monocarbonylation reactions through the regulation of ligands were described in 2015. Detailed experimental studies have shown that different catalysts induce various reaction pathways. As an example, Xantphos selectively catalyzed the production of β,γ-unsaturated esters, while 2-pyridyl-diphenylphosphine 40 preferably led to α,β-unsaturated ester products (Fig. 7b). The above-described processes realized the conversion of 1,3-butadiene to methyl-3-penetenoate in good yields. In addition, chemical procedures for the conversion of methyl-3-pentenoate to adipic acid/esters have also been established in >90% yield and about 80% selectivity, but the most prominent disadvantage is that the related processes are very complicated and involve multi-step processing.171–174 Earlier in 1987, Drent and co-workers showed elegantly that the use of the ligand 2-pyridyl-diphenylphosphine 40 allows for exceptional activity in the carbonylation of propylene. It was speculated that the active catalytic species was stabilized by the hemilabile P–N coordination of the ligand.175 Inspired by Drent's work, some of us introduced the 2-pyridyl unit into various bidentate phosphines. Among these obtained ligands, 1,2-bis((tert-butyl(pyridinyl)phosphanyl)methyl)benzene (pytbpx, 41) exhibited superior activity in carbonylation of ethylene (Lucite α-process). DFT calculations on the elementary steps showed that the pyridyl group is immediately protonated, which promoted the formation of the active [Pd–H] species (Fig. 7c). After the insertion of alkene and carbon monoxide, the corresponding Pd–acyl species was reversibly formed. Notably, the formed intermediate is stabilized by hemilabile coordination of the pyridyl group. Then, metal–ligand cooperation significantly increases the rate of alcoholysis of the acyl palladium complex.176 This finding greatly improved the efficiency of the overall catalyst system, which allowed a general alkoxycarbonylation of olefins including demanding tetrasubstituted ones. As an example, the efficient carbonylation of ethylene exhibited a TON of >1
425
000 and selectivity of >99%.177
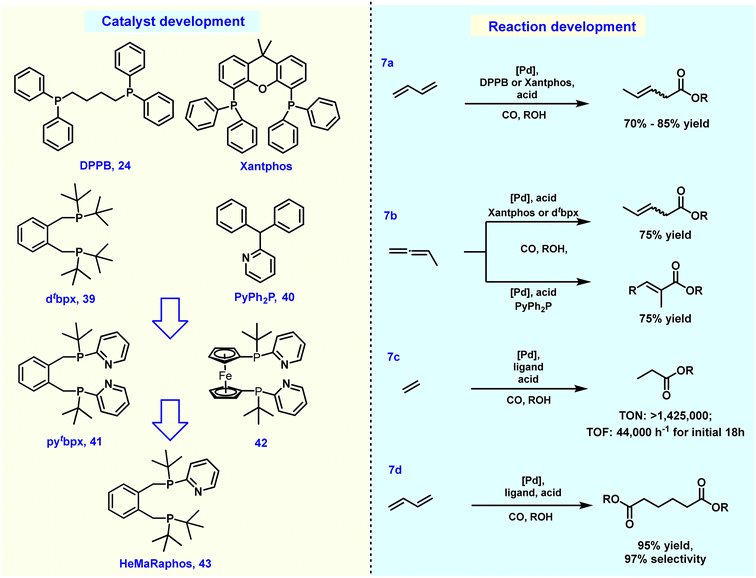 |
| Fig. 7 Ligand advancements and reaction development for palladium-catalyzed carbonylation of 1,3-butadiene. | |
From 2000 to 2008, Drent and co-workers at Shell developed interesting two-step processes for the synthesis of adipic acid. Here, pentenoic acids were produced in the first step and then distilled out from the reaction system and exposed to a second carbonylation stage with a higher concentration of water as nucleophile. This second step involved an induction period of more than 5 hours. Although such a continuous process simplified the relevant steps and operations, due to the altered conditions of both steps, the overall process still has some limitations such as adjustment of reaction medium, charging/discharging of carbon monoxide gas and adding additional water.178–181 In this respect, the direct conversion of 1,3-butadiene to adipates would be advantageous. For this purpose, the multifunctional catalyst HeMaRaphos 43 was designed, which integrated two basic backbones controlling reactivity and selectivity: the steric and electron-rich di-tert-butylphosphino portion could assist fast isomerization of C
C bonds, while the tert-butyl-2-pyridyl phosphino group enabled the generation of the active Pd–hydride complex and enhanced the key alcoholysis step. Indeed, by utilizing the Pd–HeMaRaphos catalyst, an excellent yield of 95% and linear selectivity of 97% was obtained for the synthesis of adipates by dicarbonylation of 1,3-butadiene (Fig. 7d). In addition, the catalytic system was also effective for the conversion of numerous other nucleophiles.177,182–185 With respect to the industrial realization of such a process, it is important to note that apart from the technical success, the implementation of such a methodology will strongly depend on the development of the different feedstock prices (e.g. benzene versus 1,3-butadiene).
3.2 Telomerization of 1,3-butadiene with CO2 to EVP
Since the beginning of the industrial revolution, the continuously increasing emissions of carbon dioxide have been a major contributor to global warming. The resulting problems urge a need to develop more sustainable technologies to realize a circular economy for human society. Clearly, reducing CO2 releases are a core issue requiring many efforts. In this regard, using carbon dioxide as an eco-friendly and available reagent for chemical transformations provides the possibility to synthesize a variety of useful chemical products. However, due to its most oxidized state and its inertness, the utilization of carbon dioxide usually requires a large amount of energy input.186–188 This energy input can be provided externally, e.g. by heating, or intrinsically by using “energy-rich” substrates. As an example for the latter case, here we present the telomerization of 1,3-butadiene with CO2 as a straightforward route towards interesting fine chemical building blocks (e.g., 3-ethyl-6-vinyltetrahydro-2H-pyran-2-one, EVP). This reaction was first explored by Inoue and Musco in the 1970s.189,190 After that, to improve the reaction efficiency, a large number of palladium-based catalytic systems have been developed.191–195 As a more recent representative, some of us presented a Pd2dba3/TOMPP system requiring no complex reaction systems or expensive additives and catalyzed the formation of the desired EVP in 67% yield (Scheme 3).191 Recently, Dong and co-workers developed the triphenylphosphine-based ligand 44 as a promoter-free telomerization system, which achieved remarkable improvements of both activity (TON up to 4540) and selectivity (EVP and δ-lactone isomers up to 97%) by simply introducing a hydroxyl group into the PPh3 ligand.195 Specifically, the activity depends on the position of the hydroxyl group. In contrast to the inactivity of catalysts with o-hydroxyl-substituted triphenylphosphine, catalysts with p-hydroxyl-substituted ligands manifested high activity with good selectivity towards the CO2-incorporated δ-lactone. These results validated that embedding one weak coordination phenolic hydroxyl group into the parent PPh3 ligand could dramatically improve the activity of the resulting Pd catalyst. In addition, Bay reported a very efficient and selective system in 2018 by using Pd(OAc)2 and tris(p-methoxyphenyl)phosphine 9 as catalysts in the presence of p-hydroquinone and N,N-diisopropylethylamine as additives. A high catalyst turnover number of 4500 and excellent selectivity of 96% for EVP were achieved after 5 hours at 70 °C.196 Currently, EVP is being synthesized on a mini-plant scale,197 which indicates the potential of further upscaling to realize industrialization, especially with the current emphasis on carbon neutrality.
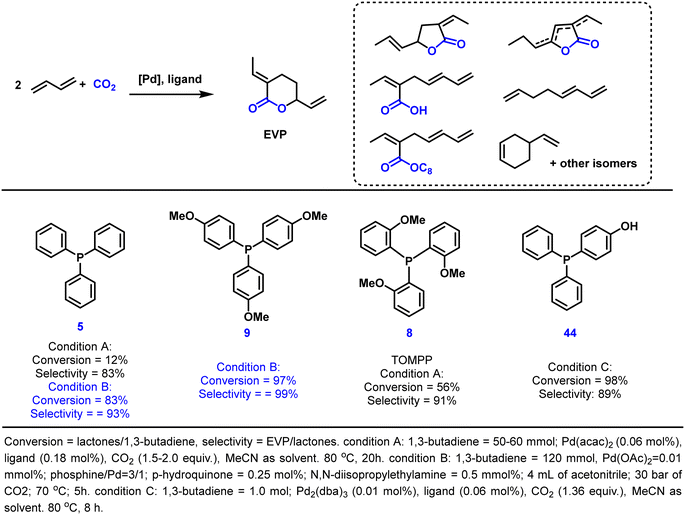 |
| Scheme 3 Telomerization of 1,3-butadiene with CO2 and representative catalytic systems. | |
Since EVP has multiple functional groups, it can be transformed into a variety of interesting fine chemicals and monomers for polymers.198,199 For example, hydrogenation to 2-ethylheptanoic acid, which is used widely not only in lubricants but also as a stabilizer for PVC, has been described.200 In addition, the transformation to synthesize high-performance polymers using EVP as a monomer has received attention in recent years.201–205 For example, Nozaki reported the first homopolymerization of EVP in 2014 via radical polymerization.206 A novel polymer with lactone repeating units was obtained (Mn = 5.7 kg mol−1, Đ = 1.3), which was later used for post-polymerization modifications by hydrolysis or aminolysis to obtain multifunctional materials.
3.3 Other chemical transformations
In addition to the aforementioned processes, 1,3-butadiene undergoes numerous other interesting transformations. For example, cyclodimerization of 1,3-butadiene is highly attractive from an industrial point of view.207 The current process makes use of a nickel(0)/phosphine catalyst system.208 The obtained cyclooctadiene (COD) can react with ethylene via olefin metathesis to produce 1,5-hexadiene, which is a valuable intermediate, e.g. to produce suberaldehyde by hydroformylation. On the other hand, COD can undergo selective hydrogenation to produce the important chemical cyclooctene or direct hydrogenation to cyclooctane, which is further oxidized to suberic acid that is used as a nylon 6/8 precursor.209 Similarly, vinylcyclohexene (VCH) can also be obtained by Diels–Alder reaction from two molecules of 1,3-butadiene. VCH has been further converted into ethylbenzene or styrene. Interestingly, in contrast to the synthesis of COD under Ni(0) catalysts, two molecules of 1,3-butadiene can produce also divinyl cyclobutane in significant yields when a Ti-bipyridyl catalyst is used.210
Epoxidation of 1,3-butadiene has been developed by Eastman Chemical as an efficient route to synthesize 3,4-epoxy-1-butene under mild conditions using a silver-based catalyst and air as oxidant.211,212 The resulting epoxide has been directly converted to 1,4-butanediol further on, or thermally rearranged to 2,5-dihydrofuran. In addition, numerous academically interesting functionalizations of 1,3-butadiene have been reported in recent years, including hydroboration,213–215 hydrosilylation,216–218 hydroamination,219–222etc. The exploration of these novel methodologies might provide more possibilities of converting 1,3-butadiene into industrially relevant chemicals in the future.
4 Summary and outlook
1,3-Butadiene is a major aliphatic feedstock for the chemical industry and the most important 1,3-diene. Its efficient and selective conversion towards a variety of products continues to attract significant attention from many researchers in both the chemical industry and academia. Its specific chemical structure allows for many unique and efficient transformations, which laid the foundation for its irreplaceable chemical value. In this review, we summarize currently used catalytic transformations of 1,3-butadiene from the perspective of industrial production apart from polymerization. Specifically, we focus on the application of homogeneous catalysts and provide representative examples for the readers. For example, palladium-catalyzed telomerization of 1,3-butadiene offers versatile platform chemicals for the production of 1-octene, 1-octanol, and higher-value EVP lactones through the participation of diverse nucleophiles. Meanwhile, efficient difunctionalization of 1,3-butadiene provides a straightforward access for the synthesis of various polymer precursors, including adiponitrile, adipaldehyde, and adipic diesters. For all these chemical processes, the development of efficient catalytic systems plays a key role to enable atom-economic and selective processes. Although significant progress has been made in various conversions of 1,3-butadiene, further advancements are needed in many areas to come up with new practical applications. In this respect, artificial intelligence technologies to predict the performance of a ligand in an efficient way can help to develop improved systems more efficiently. Indeed, currently machine learning and artificial intelligence applications are receiving a boost in performance and information from both academic research and industry. Machine learning might become an outstanding tool to accelerate catalyst discovery by enabling extensive prediction of immeasurable compositions, driving exploration to quickly discover the performance optima, and quantitatively considering the structure and activity–structure–property relationships. Therefore, instead of a traditional synthesis–structure–property relationship based on sometimes a not clear image of the catalytic mechanism, data-focused mathematical models may progressively understand and facilitate property prediction, guided optimization, and fundamental understanding of catalysts. In the context of a sustainable chemical industry a key issue for the future use of 1,3-butadiene will be its origin. Cleary, at present the vast majority of 1,3-butadienes is fossil based as a by-product of naphtha cracking. However, there is increasing interest in producing this feedstock from biobased ethanol with lower environmental impact. If this will be realized, we believe that 1,3-butadiene will be even more widely employed in the chemical industry of the future to produce a variety of intermediates for daily life products.
Author contributions
J. Y. and P. W. contributed equally. J. Y. and M. B. conceived this review. M. B., H. N. and R. J. planned parts of the here described research. J. Y., P. W. and M. B. wrote the paper.
Conflicts of interest
The authors declare no conflict of interest.
Acknowledgements
We acknowledge funding from the European Union's Horizon 2020 research and innovation programme under the Marie Skłodowska-Curie grant agreement no. 859910 as well as from the BMBF, Germany, and the State of Mecklenburg-Western Pomerania. We thank our cooperation partners in the telomerization and carbonylation reactions mentioned here from our own research.
References
-
J. Grub and E. Löser, “Butadiene” in Ullmann's encyclopedia of industrial chemistry, Wiley-VCH, Weinheim, 2012 Search PubMed.
- Y. Wang, W. Feng, M. Lei and R. Liu, Theoretical calculation of rate constants for the thermal isomerization from 1, 2-butadiene to 1, 3-butadiene, Sci. China, Ser. B: Chem., 1998, 41, 60–64 CrossRef CAS.
- R. L. Lipnick and E. W. Garbisch, Conformational analysis of 1,3-butadiene, J. Am. Chem. Soc., 1973, 95, 6370–6375 CrossRef CAS.
- J. H. Baraban, M.-A. Martin-Drumel, P. B. Changala, S. Eibenberger, M. Nava, D. Patterson, J. F. Stanton, G. B. Ellison and M. C. McCarthy, The molecular structure of gauche-1,3-butadiene: Experimental establishment of non-planarity, Angew. Chem., Int. Ed., 2018, 57, 1821–1825 CrossRef CAS PubMed.
-
K. Peter, C. Vollhardt, N. E. Schore and W. H. Freeman, Organic chemistry: Structure and function, Macmillan Higher Education, New York, 7th edn, 2014 Search PubMed.
-
F. A. Carey, Organic chemistry, McGraw-Hill, London, 5th edn, 2002 Search PubMed.
- V. Caventou, Ueber eine mit dem zweifach-gebromten Brombutylen isomere Verbindung und über die bromhaltigen Derivate des Brombutylens, Justus Liebigs Ann. Chem., 1863, 127, 93–97 CrossRef.
- H. E. Armstrong and A. K. Miller, The decomposition and genesis of hydrocarbons at high temperatures. The products of the manufacture of gas from petroleum, J. Chem. Soc., 1886, 74–93 RSC.
- P. I. Kyriienko, O. V. Larina, S. O. Soloviev, S. M. Orlyk, C. Calers and S. Dzwigaj, Ethanol conversion into 1,3-butadiene by the Lebedev method over MTaSiBEA zeolites (M = Ag, Cu, Zn), ACS Sustainable Chem. Eng., 2017, 5, 2075–2083 CrossRef CAS.
- J. L. White, First of a series: Pioneering polymer industry developments: Bayer and the first synthetic rubber first of a series, Int. Polym. Process., 1999, 14, 114 CrossRef CAS.
-
W. Klein, H. Meis and E. Tschunker, DE Pat., 515143C, 1927 Search PubMed.
- Production capacity of butadiene worldwide in 2018 and 2025, https://www.statista.com/statistics/-1067436/global-butadiene-production-capacity/, (accessed October 2022).
- Butadiene Market – Growth, Trends, Covid-19 Impact, and Forecasts (2022–2027), https://www.mordorintelligence.com/industry-reports/butadiene-market?gclid=EAIaIQobChMI6dL4tced-wIVEQznCh151wsjEAMYASAAEgIaZPD_BwE, (accessed October 2022).
- H. Duan, Y. Yamada and S. Sato, Future prospect of the production of 1,3-butadiene from butanediols, Chem. Lett., 2016, 45, 1036–1047 CrossRef CAS.
- W. C. White, Butadiene production process overview, Chem.-Biol. Interact., 2007, 166, 10–14 CrossRef CAS PubMed.
- Global Butadiene Market Outlook to 2024, https://www.globenewswire.com/news-release/2019/03/29/1788422/0/en/Global-Butadiene-Market-Outlook-to-2024-Rapidly-Increasing-Automotive-Production-Creating-a-Demand-for-Butadiene-Rubber.html, (accessed October 2022).
-
H. P. Sun and J. P. Wristers, Butadiene, in Encyclopedia of Chemical Technology, John Wiley & Sons, New York, 4th edn, 1992, pp. 663–690 Search PubMed.
- E. R. Bridgwater, Present status of synthetic rubber, Ind. Eng. Chem., 1941, 33, 1342–1346 CrossRef CAS.
- C. E. Starr Jr. and W. F. Ratcliff, Impurities in petroleum butadiene from copper salt process, Ind. Eng. Chem., 1946, 38, 1020–1025 CrossRef.
-
I. Kirshenbaum, Butadiene, in Encyclopedia of Chemical Technology, ed. M. Grayson, John Wiley & Sons, New York, 3rd edn, 1978, vol. 4, pp. 313–337 Search PubMed.
- P. W. Cornell, Butadiene for synthetic rubber: A wartime challenge, Chem. Eng. Commun., 1989, 82, 1–19 CrossRef CAS.
- A. Kumar, S. Mohanty and V. K. Gupta, Butadiene rubber: Synthesis, microstructure, and role of catalysts, Rubber Chem. Technol., 2021, 94, 393–409 CrossRef CAS.
- A. Goyal and P. Agarwal, Use of co-polymer of styrene butadiene rubber-a seismically innovative approach towards energy dissipation, Procedia Eng., 2016, 173, 1800–1807 CrossRef CAS.
- R. J. Dhanorkar, S. Mohanty and V. K. Gupta, Synthesis of functionalized styrene butadiene rubber and its applications in SBR-silica composites for high performance tire applications, Ind. Eng. Chem. Res., 2021, 60, 4517–4535 CrossRef CAS.
- S. Basak and A. Bandyopadhyay, Styrene-butadiene-styrene-based shape memory polymers: Evolution and the current state of art, Polym. Adv. Technol., 2022, 33, 2091–2112 CrossRef CAS.
- S. Kotova, N. Buhtiyarova and S. Mikhailov, Improved properties of nitrile butadiene rubber, Rubber World, 2013, 248, 18–20 CAS.
- H. Wang, L. Yang and G. L. Rempel, Homogeneous hydrogenation art of nitrile butadiene rubber: A review, Polym. Rev., 2013, 53, 192–239 CrossRef CAS.
-
R. C. Bohley, G. B. Jacobsen, H. L. Pelt, B. J. Schaart, M. Schenk, D. A. G. van Oeffelen and DOW Benelux, WO Pat., 9210450, 1992 Search PubMed.
-
G. B. Jacobsen, H. L. Pelt, B. J. Schaart and DOW Benelux, WO Pat., 199109822, 1991 Search PubMed.
-
F. Benvenuti, J. Patton, S. Vermaire-Louw, P. Margl, H. Hagen, D. Beigzadeh and DOW Benelux, WO Pat., 2010019360, 2010 Search PubMed.
-
D. Röttger, A. Tuchlenski and Oxeno Olefinchemie GmbH, WO Pat., 02062732, 2002 Search PubMed.
-
J. Krissmann, D. Röttger, C. Borgmann, K. Kämper, F. Nierlich, A. Kaizik, U. Knipenberg, R. Malzkorn and Oxeno Olefinchemie GmbH, WO Pat., 2005000772, 2005 Search PubMed.
- E. J. Smutny, Oligomerization and dimerization of butadiene under homogeneous catalysis. Reaction with nucleophiles and the synthesis of 1,3,7-octatriene, J. Am. Chem. Soc., 1967, 89, 6793–6794 CrossRef CAS.
- S. Takahashi, T. Shibano and N. Hagihara, The dimerization of butadiene by palladium complex catalysts, Bull. Chem. Soc. Jpn., 1967, 41, 454–460 CrossRef.
- A. Behr and J. Leschinski, Application of the solvent water in two-phase telomerisation reactions and recycling of the homogeneous palladium catalysts, Green Chem., 2009, 11, 609–613 RSC.
- A. Behr, P. Bahke and M. Becker, Palladium-katalysierte telomerisation von kohlendioxid mit butadien im labor- und miniplantmaßstab, Chem. Ing. Tech., 2004, 76, 1828–1832 CrossRef CAS.
- E. J. Smutny, Linear telomerization of conjugated dienes, Ann. N. Y. Acad. Sci., 1973, 214, 125–142 CrossRef CAS PubMed.
- R. Jackstell, S. Harkal, H. Jiao, A. Spannenberg, C. Borgmann, D. Röttger, F. Nierlich, M. Elliot, S. Niven, K. Cavell, O. Navarro, M. S. Viciu, S. P. Nolan and M. Beller, An industrially viable catalyst system for palladium-catalyzed telomerizations of 1,3-butadiene with alcohols, Eur. J. Chem., 2004, 10, 3891–3900 CrossRef CAS PubMed.
- R. Jackstell, A. Frisch, M. Beller, D. Röttger, M. Malaun and B. Bildstein, Efficient telomerization of 1,3-butadiene with alcohols in the presence of in situ generated palladium(0)carbene complexes, J. Mol. Catal., 2002, 185, 105–112 CrossRef CAS.
- R. Jackstell, M. G. Andreu, A. Frisch, K. Selvakumar, A. Zapf, H. Klein, A. Spannenberg, D. Röttger, O. Briel, R. Karch and M. Beller, A highly efficient catalyst for the telomerization of 1,3-dienes with alcohols: First synthesis of a monocarbenepalladium(0)–olefin complex, Angew. Chem., Int. Ed., 2002, 41, 986–989 CrossRef CAS PubMed.
- F. Benvenuti, C. Carlini, M. Marchionna, R. Patrini, A. M. R. Galletti and G. Sbrana, Homogeneous telomerization of 1,3-butadiene with alcohols in the presence of palladium catalysts modified by hybrid chelate ligands, J. Mol. Catal., 1999, 140, 139–155 CrossRef CAS.
- F. Benvenuti, C. Carlini, M. Lami, M. Marchionna, R. Patrini, A. M. R. Galletti and G. Sbrana, Telomerization of 1,3-butadiene with alcohols catalyzed by homogeneous palladium(0) complexes in the presence of mono- and diphosphine ligands, J. Mol. Catal., 1999, 144, 27–40 CrossRef CAS.
- R. Patrini, M. Lami, M. Marchionna, F. Benvenuti, A. M. R. Galletti and G. Sbrana, Selective synthesis of octadienyl and butenyl ethers via reaction of 1,3-butadiene with alcohols catalyzed by homogeneous palladium complexes, J. Mol. Catal., 1998, 129, 179–189 CrossRef CAS.
- A. Behr, T. Beckmann and H. Nachtrodt, Multiphase telomerisation of butadiene with phenol: Optimisation and scale-up in different reactor types, Dalton Trans., 2009, 6214–6219 RSC.
- R. Palkovits, A. N. Parvulescu, P. J. C. Hausoul, C. A. Kruithof, R. J. M. Klein Gebbink and B. M. Weckhuysen, Telomerization of 1,3-butadiene with various alcohols by Pd/TOMPP catalysts: New opportunities for catalytic biomass valorization, Green Chem., 2009, 11, 1155–1160 RSC.
-
H. Ishino and H. Iwasaki, WO Pat., 2004065006, 2004 Search PubMed.
- M. Camargo, P. Dani, J. Dupont, R. F. de Souza, M. Pfeffer and I. Tkatchenko, Cationic cyclopalladated complexes: New catalyst precursors for the telomerization of butadiene with alcohols, J. Mol. Catal., 1996, 109, 127–131 CrossRef CAS.
- P. Grenouillet, D. Neibecker, J. Poirier and I. Tkatchenko, Higher telomers in the Pd-catalyzed reaction of butadiene with alcohols, Angew. Chem., Int. Ed. Engl., 1982, 21, 767–768 CrossRef.
- J. Beger and H. Reichel, Dienoligomerisierung. VII. Palladiumkomplexkatalysierte dimerisierung und telomerisierung von butadien im alkoholischen medium, J. Prakt. Chem., 1973, 315, 1067–1076 CrossRef CAS.
-
R. M. Hanes and National Distillers and Chemical Corporation, US Pat., 4642392, 1987 Search PubMed.
-
R. M. Hanes and National Distillers and Chemical Corporation, US Pat., 4831183, 1989 Search PubMed.
- R. Palkovits, I. Nieddu, C. A. Kruithof, R. J. M. Klein Gebbink and B. M. Weckhuysen, Palladium-based telomerization of 1,3-butadiene with glycerol using methoxy-functionalized triphenylphosphine ligands, Eur. J. Chem., 2008, 14, 8995–9005 CrossRef CAS PubMed.
- R. Palkovits, I. Nieddu, R. J. M. Klein Gebbink and B. M. Weckhuysen, Highly active catalysts for the telomerization of crude glycerol with 1,3-butadiene, ChemSusChem, 2008, 1, 193–196 CrossRef CAS PubMed.
- A. D. Behr and M. Urschey, Highly selective biphasic telomerization of butadiene with glycols: Scope and limitations, Adv. Synth. Catal., 2003, 345, 1242–1246 CrossRef CAS.
- A. Grotevendt, R. Jackstell, D. Michalik, M. Gomez and M. Beller, Efficient and selective telomerization of 1,3-butadiene with diols catalyzed by palladium–carbene complexes, ChemSusChem, 2009, 2, 63–70 CrossRef CAS PubMed.
- R. Jackstell, A. Grotevendt, M. G. Andreu and M. Beller, A practical palladium-catalyzed telomerization for the synthesis of functionalized alcohols, Org. Process Res. Dev., 2009, 13, 349–353 CrossRef CAS.
- A. Behr, J. Leschinski, C. Awungacha, S. Simic and T. Knoth, Telomerization of butadiene with glycerol: Reaction control through process engineering, solvents, and additives, ChemSusChem, 2009, 2, 71–76 CrossRef CAS PubMed.
- M. Perree-Fauvet and Y. Chauvin, Telomerisation du butadiene par les alcools fluores catalysee par les complexes du palladium, Tetrahedron Lett., 1975, 16, 4559–4562 CrossRef.
- A. Behr, T. Beckmann and P. Schwach, Multiphase telomerisation of butadiene with acetic acid and acetic anhydride, J. Organomet. Chem., 2008, 693, 3097–3102 CrossRef CAS.
- W. E. Walker, R. M. Manyik, K. E. Atkins and M. L. Farmer, Palladium complex catalyzed reactions of conjugated dienes. II solvent and ligand effects on the reaction of butadiene with acetic acid, Tetrahedron Lett., 1970, 11, 3817–3820 CrossRef.
- D. Rose and H. Lepper, The palladium-catalysed reaction of butadiene with acetic acid in the presence of phosphites, J. Organomet. Chem., 1973, 49, 473–476 CrossRef CAS.
-
R. Fletcher and British Petroleum Company Ltd., GB Pat., 1505317, 1976 Search PubMed.
- R. A. Sheldon, Green solvents for sustainable organic synthesis: State of the art, Green Chem., 2005, 7, 267–278 RSC.
- U. M. Dzhemilev, V. V. Sidorova and R. V. Kunakova, Synthesis of unsaturated alcohols by telomerization of H2O with 1,3-dienes catalyzed by palladium complexes, Bull. Acad. Sci. USSR, Div. Chem. Sci., 1983, 32, 525–529 CrossRef.
-
T. Maeda, Y. Tokitoh, N. Yoshimura and Kuraray Co. Ltd., EP Pat., 296550, 1987 Search PubMed.
-
Y. Tokitoh, N. Yoshimura and Kuraray Co. Ltd., EP Pat., 287066, 1988 Search PubMed.
- B. I. Lee, K. H. Lee and J. S. Lee, The effects of reaction variables on the palladium-catalyzed reactions of butadiene with water, J. Mol. Catal., 2001, 166, 233–242 CrossRef CAS.
- B. I. Lee, K. H. Lee and J. S. Lee, Telomerization of butadiene with water catalyzed by heterogeneous palladium catalysts, J. Mol. Catal., 2000, 156, 283–287 CrossRef CAS.
- E. Monflier, P. Bourdauducq, J.-L. Couturier, J. Kervennal, I. Suisse and A. Mortreux, Solvent free telomerization of butadiene with water into octadienols in the presence of nonionic surfactant: Efficient micellar catalysis, Catal. Lett., 1995, 34, 201–212 CrossRef CAS.
- E. Monflier, P. Bourdauducq, J.-L. Couturier, J. Kervennal and A. Mortreux, Palladium catalyzed telomerization of butadiene with water in a two phase system: Drastic effect of the amine structure on the rate and selectivity, J. Mol. Catal., 1995, 97, 29–33 CrossRef CAS.
- E. Monflier, P. Bourdauducq, J.-L. Couturier, J. Kervennal and A. Mortreux, Highly efficient telomerization of butadiene into octadienol in a micellar system: A judicious choice of the phosphine/surfactant combination, Appl. Catal., 1995, 131, 167–178 CrossRef CAS.
-
K. Wada, K. Sato, Y. Kasori, Y. Misu and Mitsubishi Kasei Corp., EP Pat., 361304, 1989 Search PubMed.
-
M. Röper, W. Bertleff, D. Köffer and BASF AG, DE Pat., 3806305, 1989 Search PubMed.
-
A. Thome, W. Bertleff and BASF AG, US Pat., 5043487, 1990 Search PubMed.
-
D. L. Packett and Union Carbide Corp., US Pat., 5169981, 1991 Search PubMed.
-
E. Monflier, P. Bourdauducq, J.-L. Couturier and Elf Atochem S.A., US Pat., 5345007, 1993 Search PubMed.
-
J. R. Livingston and Exxon Chemical Patents Inc., US Pat., 5302750, 1993 Search PubMed.
- T. Prinz and B. Driessen-Hölscher, Biphasic catalyzed telomerization of butadiene and ammonia: Kinetics and new ligands for regioselective reactions, Eur. J. Chem., 1999, 5, 2069–2076 CrossRef CAS.
- T. Prinz, W. Keim and B. Driessen-Hölscher, Two-phase catalysis: A strategy for avoiding consecutive reactions as exemplified in the telomerization of butadiene and ammonia, Angew. Chem., Int. Ed. Engl., 1996, 35, 1708–1710 CrossRef CAS.
- A. Grotevendt, M. Bartolome, D. J. Nielsen, A. Spannenberg, R. Jackstell, K. J. Cavell, L. A. Oro and M. Beller, Efficient catalysts for telomerization of butadiene with amines, Tetrahedron Lett., 2007, 48, 9203–9207 CrossRef CAS.
- M. S. Viciu, F. K. Zinn, E. D. Stevens and S. P. Nolan, Telomerization of amines mediated by cationic N-heterocyclic carbene (NHC) palladium complexes, Organometallics, 2003, 22, 3175–3177 CrossRef CAS.
- G. S. Fonseca, R. F. de Souza and J. Dupont, Biphasic telomerization of 1,3-butadiene with HNEt2 catalyzed by palladium/sulphonated–phosphine complexes, Catal. Commun., 2002, 3, 377–380 CrossRef.
- F. Ragaini, T. Longo and S. Cenini, Addition of ethyl urethane to olefins: A new approach to the synthesis of aliphatic carbamates, J. Mol. Catal., 1996, 110, L171–L175 CrossRef CAS.
- T. Antonsson and C. Moberg, Palladium-catalyzed telomerization of dienes and tertiary allylic amines. A novel reaction involving cleavage of the carbon-nitrogen bond, Organometallics, 1985, 4, 1083–1086 CrossRef CAS.
- J. Tsuji and M. Takahashi, Palladium-catalyzed telomerization of butadiene with ammonia, J. Mol. Catal., 1980, 10, 107–114 CrossRef CAS.
- T. Shigetoshi, S. Toshiki and H. Nobue, The dimerization of butadiene by palladium complex catalysts, Bull. Chem. Soc. Jpn., 1968, 41, 454–460 CrossRef.
- J. Beger and F. Meier, Dienoligomerisierung. XV. palladiumkomplexkatalysierte telomerisierung von butadien mit aminen und dimerisierung in gegenwart von ketoximen, J. Prakt. Chem., 1980, 322, 69–80 CrossRef CAS.
- C. Moberg, Reaction of tertiary allylic amines with butadiene catalyzed by palladium, Tetrahedron Lett., 1981, 22, 4827–4830 CrossRef CAS.
- T. Antonsson, A. Langlét and C. Moberg, Stereochemistry of palladium-catalyzed telomerization of butadiene with diethylamine, J. Organomet. Chem., 1989, 363, 237–241 CrossRef CAS.
- A. Groult and A. Guy, Reaction of aminoalcohols with butadiene catalysed by palladium complexes, Tetrahedron, 1983, 39, 1543–1550 CrossRef CAS.
- V. Desvergnes-Breuil, C. Pinel and P. Gallezot, Green approach to substituted carbohydrates: telomerisation of butadiene with sucrose, Green Chem., 2001, 3, 175–177 RSC.
- K. Hill, B. Gruber and K. J. Weese, Palladium catalyzed telomerization of butadiene with sucrose: A highly efficient approach to novel sucrose ethers, Tetrahedron Lett., 1994, 35, 4541–4542 CrossRef CAS.
- I. Pennequin, J. Meyer, I. Suisse and A. Mortreux, A further application of TPPTS in catalysis: Efficient sucrose-butadiene telomerization using palladium catalysts in water, J. Mol. Catal., 1997, 120, 139–142 CrossRef CAS.
- B. Estrine, S. Bouquillon, F. Hénin and J. Muzart, Telomerization of butadiene with L-arabinose and D-xylose in DMF: Selective formation of their monooctadienyl glycosides, Eur. J. Org. Chem., 2004, 2004, 2914–2922 CrossRef.
- F. Hénin, A. Bessmertnykh, A. Serra-Muns, J. Muzart and H. Baillia, Palladium-catalyzed telomerization of butadiene with tri-O-acetylated pentoses as a convenient route to 2,7-octadienyl glycosides, Eur. J. Org. Chem., 2004, 2004, 511–520 CrossRef.
- A. Bessmertnykh, F. Hénin and J. Muzart, Palladium-catalysed telomerization of butadiene with aldoses: A convenient route to non-ionic surfactants based on controlled reactions, J. Mol. Catal., 2005, 238, 199–206 CrossRef CAS.
- J. Mesnager, C. Quettier, A. Lambin, F. Rataboul, A. Perrard and C. Pinel, Telomerization of butadiene with starch in water: Role of the surfactants, Green Chem., 2010, 12, 475–482 RSC.
- J. Mesnager, C. Quettier, A. Lambin, F. Rataboul and C. Pinel, Telomerization of butadiene with starch under mild conditions, ChemSusChem, 2009, 2, 1125–1129 CrossRef CAS PubMed.
- C. Donzé, C. Pinel, P. Gallezot and P. L. Taylor, Palladium-catalyzed telomerization of butadiene with starch, Adv. Synth. Catal., 2002, 344, 906–910 CrossRef.
- P. J. C. Hausoul, P. C. A. Bruijnincx, R. J. M. K. Gebbink and B. M. Weckhuysen, Base-free Pd/TOMPP-catalyzed telomerization of 1,3-butadiene with carbohydrates and sugar alcohols, ChemSusChem, 2009, 2, 855–858 CrossRef CAS PubMed.
- J. Tsuji, Addition reactions of butadiene catalyzed by palladium complexes, Acc. Chem. Res., 1973, 6, 8–15 CrossRef CAS.
- P. W. Jolly, η3-Allylpalladium compounds, Angew. Chem., Int. Ed. Engl., 1985, 24, 283–295 CrossRef.
- F. Vollmüller, J. Krause, S. Klein, W. Mägerlein and M. Beller, Control of chemo- and regioselectivity in the palladium-catalyzed telomerization of butadiene with methanol − catalysis and mechanism, Eur. J. Inorg. Chem., 2000, 2000, 1825–1832 CrossRef.
- N. D. Clement, L. Routaboul, A. Grotevendt, R. Jackstell and M. Beller, Development of palladium–carbene catalysts for telomerization and dimerization of 1,3-dienes: From basic research to industrial applications, Eur. J. Chem., 2008, 14, 7408–7420 CrossRef CAS PubMed.
- F. Vollmüller, W. Mägerlein, S. Klein, J. Krause and M. Beller, Palladium-catalyzed reactions for the synthesis of fine chemicals, 16 – highly efficient palladium-cCatalyzed telomerization of butadiene with methanol, Adv. Synth. Catal., 2001, 343, 29–33 CrossRef.
- C.-F. Huo, R. Jackstell, M. Beller and H. Jiao, Mechanistic study of palladium-catalyzed telomerization of 1,3-butadiene with methanol, J. Mol. Model., 2010, 16, 431–436 CrossRef CAS PubMed.
-
R. C. Bohley, G. B. Jacobsen, H. L. Pelt, B. J. Schaart, M. Schenk and D. A. G. van Oeffelen, WO Pat., 199210450, 1992 Search PubMed.
- J. Krause, G. Cestaric, K.-J. Haack, K. Seevogel, W. Storm and K.-R. Pörschke, 1,6-Diene complexes of palladium(0) and platinum(0): Highly reactive sources for the naked metals and [L−M0] fragments, J. Am. Chem. Soc., 1999, 121, 9807–9823 CrossRef CAS.
- T. E. Barder, S. D. Walker, J. R. Martinelli and S. L. Buchwald, Catalysts for Suzuki−Miyaura coupling processes: Scope and studies of the effect of ligand structure, J. Am. Chem. Soc., 2005, 127, 4685–4696 CrossRef CAS PubMed.
- M. J. L. Tschan, E. J. García-Suárez, Z. Freixa, H. Launay, H. Hagen, J. Benet-Buchholz and P. W. N. M. van Leeuwen, Efficient bulky phosphines for the selective telomerization of 1,3-butadiene with methanol, J. Am. Chem. Soc., 2010, 132, 6463–6473 CrossRef CAS PubMed.
- M. J. L. Tschan, H. Launay, H. Hagen, J. Benet-Buchholz and P. W. N. M. van Leeuwen, Telomerisation of buta-1,3-diene and methanol: Superiority of chromanyl-type phosphines in the Dow process for the industrial production of 1-MOD, Chem. – Eur. J., 2011, 17, 8922–8928 CrossRef CAS PubMed.
-
A. Tafesh, M. Beller, J. Krause and Hoechst Research and Technology Deutschland GmbH, WO Pat., 199808794, 1998 Search PubMed.
-
E. Drent, M. R. Eberhard, R. H. van der Made, P. G. Pringle and Shell, WO Pat., 2003040065, 2003 Search PubMed.
- E. Peris and R. H. Crabtree, Recent homogeneous catalytic applications of chelate and pincer N-heterocyclic carbenes, Coord. Chem. Rev., 2004, 248, 2239–2246 CrossRef CAS.
- N. Marion and S. P. Nolan, Well-defined N-heterocyclic carbenes−palladium(II) precatalysts for cross-coupling reactions, Acc. Chem. Res., 2008, 41, 1440–1449 CrossRef CAS PubMed.
- C. Samojłowicz, M. Bieniek and K. Grela, Ruthenium-based olefin metathesis catalysts bearing N-heterocyclic carbene ligands, Chem. Rev., 2009, 109, 3708–3742 CrossRef PubMed.
- D. Shen, Y. Xu and S.-L. Shi, A bulky chiral N-heterocyclic carbene palladium catalyst enables highly enantioselective Suzuki–Miyaura cross-coupling reactions for the synthesis of biaryl atropisomers, J. Am. Chem. Soc., 2019, 141, 14938–14945 CrossRef CAS PubMed.
- S. Harkal, R. Jackstell, F. Nierlich, D. Ortmann and M. Beller, Development of a highly selective and efficient catalyst for 1,3-butadiene dimerization, Org. Lett., 2005, 7, 541–544 CrossRef CAS PubMed.
-
D. Röttger, M. Beller, R. Jackstell, H. Klein, K.-D. Wiese and Oxeno Olefinchemie GmbH, WO Pat., 2004002931, 2004 Search PubMed.
- L. Magna, Y. Chauvin, G. P. Niccolai and J.-M. Basset, The importance of imidazolium substituents in the use of imidazolium-based room-temperature ionic liquids as solvents for palladium-catalyzed telomerization of butadiene with methanol, Organometallics, 2003, 22, 4418–4425 CrossRef CAS.
-
L. H. Slaugh and Shell, US Pat., 5030792, 1991 Search PubMed.
-
E. Drent, W. W. Jager and Shell, EP Pat., 1671940, 2004 Search PubMed.
-
K. Nozaki and Shell, EP Pat., 12472, 1980 Search PubMed.
- C. U. Pittman, R. M. Hanes and J. J. Yang, Selective hydrodimerization of 1,3-butadiene to 1,7-octadiene, J. Mol. Catal., 1982, 15, 377–381 CrossRef CAS.
-
V. Brehme, M. Neumann, F. Bauer, D. Röttger and Evonik Degussa GmbH, WO Pat., 2008003559, 2008 Search PubMed.
- K. E. Atkins, W. E. Walker and R. M. Manyik, Palladium catalyzed transfer of allylic groups, Tetrahedron Lett., 1970, 11, 3821–3824 CrossRef.
-
N. Yoshimura, M. Tamura and Kuraray Co Ltd, GB Pat., 2074156A, 1981 Search PubMed.
-
N. Yoshimura, M. Tamura and Kuraray Co Ltd, US Pat., 4417079, 1983 Search PubMed.
-
Y. Tokitoh, N. Yoshimura and Kuraray Co Ltd, EP Pat., 0287066A2, 1988 Search PubMed.
-
T. Tsuda, Y. Tokitoh, K. Watanabe, T. Hori and Kuraray Co Ltd., US Pat., 5994590A, 1998 Search PubMed.
-
M. Roeper, W. Bertleff, D. Koeffer and BASF SE, US Pat., 4962243, 1990 Search PubMed.
-
A. Thome, W. Bertleff and BASF SE, US Pat., 5043487, 1991 Search PubMed.
-
E. Monflier, P. Bourdauducq, J. Couturier and Arkema France SA, US Pat., 5345007, 1994 Search PubMed.
-
K. Wada, K. Sato, Y. Kasori, Y. Misu and Mitsubishi Kasei Corp, US Pat., 4990698, 1991 Search PubMed.
-
K. Sato, I. Nakajima, Y. Misu and Mitsubishi Kasei Corp, US Pat., 5283377, 1994 Search PubMed.
-
Y. Tokitoh, N. Yoshimura and Kuraray Co Ltd, US Pat., 5057631, 1991 Search PubMed.
-
Y. Tokitoh, T. Higashi, K. Hino, M. Murasawa, N. Yoshimura and Kuraray Co Ltd, EP Pat., 0436226A1, 1990 Search PubMed.
-
J. R. Livingston and ExxonMobil Chemical Patents Inc., US Pat., 5302750, 1994 Search PubMed.
-
C. Miyazawa, T. Mori, H. Kameo and S. Isogai, WO Pat., 1994000410A1, 1994 Search PubMed.
-
E. Kuntz and Rhone Poulenc Industries SA, US Pat., 4142060A, 1979 Search PubMed.
-
E. Kuntz and Rhone Poulenc Industries SA, US Pat., 4260750A, 1981 Search PubMed.
-
E. Monflier, P. Bourdauducq and J. L. Couturier, WO Pat., 199418147, 1994 Search PubMed.
-
P. W. N. M. van Leeuwen, in Homogeneous Catalysis: Understanding the Art, Springer, Netherlands, Dordrecht, 2004, pp. 229–237 Search PubMed.
-
S. Krill, in Applied homogeneous catalysis with organometallic compounds. A comprehensive handbook in three, Wiley-VCH, Weinheim, 2002, vol. 2 Search PubMed.
-
C. Patois, M. Spagnol and Rhodia Fiber and Resin Intermediates SAS, US Pat., 6204379B1, 2001 Search PubMed.
- S. Alini, A. Bottino, G. Capannelli, R. Carbone, A. Comite and G. Vitulli, The catalytic hydrogenation of adiponitrile to hexamethylenediamine over a rhodium/alumina catalyst in a three phase slurry reactor, J. Mol. Catal., 2003, 206, 363–370 CrossRef CAS.
-
C. A. Tolman, R. J. McKinney, W. C. Seidel, J. D. Druliner and W. R. Stevens, in Advances in Catalysis, ed. D. D. Eley, H. Pines and P. B. Weisz, Academic Press, 1985, vol. 33, pp. 1–46 Search PubMed.
-
C. R. Harris and EI Du Pont de Nemours and Co., US Pat., 2427601A, 1945 Search PubMed.
- P. Arthur, Jr., D. C. England, B. C. Pratt and G. M. Whitman, Addition of hydrogen cyanide to unsaturated compounds, J. Am. Chem. Soc., 1954, 76, 5364–5367 CrossRef.
-
W. C. Drinkard and R. V. Lindsey, US Pat., 3496215A (DuPont), 1970 Search PubMed.
- C. A. Tolman, J. Am. Chem. Soc., 1970, 92, 6785–6790 CrossRef CAS.
- D. S. P. Cardoso, B. Šljukić, D. M. F. Santos and C. A. C. Sequeira, Organic electrosynthesis: From laboratorial practice to industrial applications, Org. Process Res. Dev., 2017, 21, 1213–1226 CrossRef CAS.
- L. Bini, C. Müller and D. Vogt, Mechanistic studies on hydrocyanation reactions, ChemCatChem, 2010, 2, 590–608 CrossRef CAS.
- E. Skoog, J. H. Shin, V. Saez-Jimenez, V. Mapelli and L. Olsson, Biobased adipic acid – The challenge of developing the production host, Biotechnol. Adv., 2018, 36, 2248–2263 CrossRef CAS PubMed.
- J. Rios, J. Lebeau, T. Yang, S. Li and M. D. Lynch, A critical review on the progress and challenges to a more sustainable, cost competitive synthesis of adipic acid, Green Chem., 2021, 23, 3172–3190 RSC.
- Adipic Acid Market Size Worth $8.0 Billion By 2024, https://www.grandviewresearch.com/press-release/global-adipic-acid-market, (accessed October 2022).
-
S. Eggleston, L. Buendia, K. Miwa, T. Ngara and K. Tanabe, Institute for Global Environmental Strategies (Japó). 2006 IPCC Guidelines for National Greenhouse Gas Inventories, 2006 Search PubMed.
-
Agency USEP, Inventory of US greenhouse gas emissions and sinks: 1990–2015, US Environmental Protection Agency, Washington, DC, 2017 Search PubMed.
- T. Beardslee and S. Picataggio, Bio-based adipic acid from renewable oils, Lipid Technol., 2012, 24, 223–225 CrossRef CAS.
- B. Fell and W. Rupilius, Dialdehydes by hydroformylation of conjugated dienes, Tetrahedron Lett., 1969, 10, 2721–2723 CrossRef.
- S. Bertozzi, N. Campigli, G. Vitulli, R. Lazzaroni and P. Salvadori, Selective hydroformylation of open-chain conjugated dienes promoted by mesitylene-solvated rhodium atoms to give β,γ unsaturated monoaldehydes, J. Organomet. Chem., 1995, 487, 41–45 CrossRef CAS.
- S. E. Smith, T. Rosendahl and P. Hofmann, Toward the rhodium-catalyzed bis-hydroformylation of 1,3-butadiene to adipic aldehyde, Organometallics, 2011, 30, 3643–3651 CrossRef CAS.
- G. W. J. Fleet and P. J. C. Harding, Convenient synthesis of bis(triphenylphosphine) copper(I) tetrahydroborate and reduction of acid chlorides to aldehydes, Tetrahedron Lett., 1979, 20, 975–978 CrossRef.
- J. Mormul, J. Breitenfeld, O. Trapp, R. Paciello, T. Schaub and P. Hofmann, Synthesis of adipic acid, 1,6-hexanediamine, and 1,6-hexanediol via double-n-selective hydroformylation of 1,3-butadiene, ACS Catal., 2016, 6, 2802–2810 CrossRef CAS.
- S.-M. Yu, W. K. Snavely, R. V. Chaudhari and B. Subramaniam, Butadiene hydroformylation to adipaldehyde with Rh-based catalysts: Insights into ligand effects, Mol. Catal., 2020, 484, 110721–110727 CrossRef CAS.
- S. E. Smith, T. Rosendahl and P. Hofmann, Toward the rhodium-catalyzed bis-hydroformylation of 1,3-butadiene to adipic aldehyde, Organometallics, 2011, 30, 3643–3651 CrossRef CAS.
-
Y. Yang, Z. Wang and Qingdao Institute of Bioenergy and Bioprocess Technology of CAS, CN Pat., 110343209A, 2019 Search PubMed.
- B. Fell and W. Rupilius, Dialdehydes by hydroformylation of conjugated dienes, Tetrahedron Lett., 1969, 10, 2721–2723 CrossRef.
- M. Beller, A. Krotz and W. Baumann, Palladium-catalyzed methoxycarbonylation of 1,3-butadiene: Catalysis and mechanistic studies, Adv. Synth. Catal., 2002, 344, 517–524 CrossRef CAS.
- X. Fang, H. Li, R. Jackstell and M. Beller, Palladium-catalyzed alkoxycarbonylation of conjugated dienes under acid-free conditions: Atom-economic synthesis of β,γ-unsaturated esters, Angew. Chem., Int. Ed., 2014, 53, 9030–9034 CrossRef CAS PubMed.
- J. Liu, Q. Liu, R. Franke, R. Jackstell and M. Beller, Ligand-controlled palladium-catalyzed alkoxycarbonylation of allenes: Regioselective synthesis of α,β- and β,γ-unsaturated esters, J. Am. Chem. Soc., 2015, 137, 8556–8563 CrossRef CAS PubMed.
- X. Li, Y. Ding, G. Jiao, J. Li, L. Ya and H. Zhu, Hydroformylation of methyl-3-pentenoate over a phosphite ligand modified Rh/SiO2 catalyst, J. Nat. Gas Chem., 2008, 17, 351–354 CrossRef CAS.
-
H. F. Wolters, S. L. Lane, W. Buijs, N. F. Haasen, F. E. Herkes and DuPont Co., US Pat., 5700934, 1997 Search PubMed.
- Z. Q. Hou, L. G. Luo, C. Z. Liu, Y. Y. Wang and L. Y. Dai, Synthesis of ethyl-6-aminohexanoate from caprolactam and ethanol in near-critical water, Chem. Pap., 2014, 68, 164–169 CAS.
- E. Drent, P. Arnoldy and P. H. M. Budzelaar, Efficient palladium catalysts for the carbonylation of alkynes, J. Organomet. Chem., 1993, 455, 247–253 CrossRef CAS.
- K. Dong, R. Sang, Z. Wei, J. Liu, R. Dühren, A. Spannenberg, H. Jiao, H. Neumann, R. Jackstell, R. Franke and M. Beller, Cooperative catalytic methoxycarbonylation of alkenes: uncovering the role of palladium complexes with hemilabile ligands, Chem. Sci., 2018, 9, 2510–2516 RSC.
- K. Dong, X. Fang, S. Gülak, R. Franke, A. Spannenberg, H. Neumann, R. Jackstell and M. Beller, Highly active and efficient catalysts for alkoxycarbonylation of alkenes, Nat. Commun., 2017, 8, 14117–14124 CrossRef PubMed.
-
E. Drent, R. Ernst, W. W. Jager, C. A. Krom and Shell USA Inc., US Pat., 080269459, 2008 Search PubMed.
-
E. Drent, R. Ernst, W. W. Jager, C. A. Krom and Shell USA Inc., US Pat., 7348454B2, 2008 Search PubMed.
-
J. Adrianus, M. V. Broekhoven, E. Drent, R. Ernst, W. W. Jager, C. A. Krom and Shell USA Inc, US Pat., 20090131630, 2009 Search PubMed.
-
E. Drent, R. Ernst and W. W. Jager, WO Pat., 2004103948A1, 2004 Search PubMed.
- J. Liu, K. Dong, R. Franke, H. Neumann, R. Jackstell and M. Beller, Selective palladium-catalyzed carbonylation of alkynes: An atom-economic synthesis of 1,4-dicarboxylic acid diesters, J. Am. Chem. Soc., 2018, 140, 10282–10288 CrossRef CAS PubMed.
- J. Yang, J. Liu, H. Neumann, R. Franke, R. Jackstell and M. Beller, Direct synthesis of adipic acid esters via palladium-catalyzed carbonylation of 1,3-dienes, Science, 2019, 366, 1514–1517 CrossRef CAS PubMed.
- J. Yang, J. Liu, Y. Ge, W. Huang, H. Neumann, R. Jackstell and M. Beller, Direct and selective synthesis of adipic and other dicarboxylic acids by palladium-catalyzed carbonylation of allylic alcohols, Angew. Chem., Int. Ed., 2020, 59, 20394–20398 CrossRef CAS PubMed.
- J. Yang, J. Liu, Y. Ge, W. Huang, F. Ferretti, H. Neumann, H. Jiao, R. Franke, R. Jackstell and M. Beller, Efficient palladium-catalyzed carbonylation of 1,3-dienes: Selective synthesis of adipates and other aliphatic diesters, Angew. Chem., 2021, 60, 9527–9533 CrossRef CAS PubMed.
- P. Braunstein, D. Matt and D. Nobel, Carbon dioxide activation and catalytic lactone synthesis by telomerization of butadiene and carbon dioxide, J. Am. Chem. Soc., 1988, 110, 3207–3212 CrossRef CAS.
- T. Sakakura, J.-C. Choi and H. Yasuda, Transformation of carbon dioxide, Chem. Rev., 2007, 107, 2365–2387 CrossRef CAS PubMed.
- M. Aresta, A. Dibenedetto and A. Angelini, Catalysis for the valorization of exhaust carbon: From CO2 to chemicals, materials, and fuels. technological use of CO2, Chem. Rev., 2014, 114, 1709–1742 CrossRef CAS PubMed.
- Y. Sasaki, Y. Inoue and H. Hashimoto, Reaction of carbon dioxide with butadiene catalysed by palladium complexes. Synthesis of 2-ethylidenehept-5-en-4-olide, J. Chem. Soc., Chem. Commun., 1976, 605–606 RSC.
- A. Musco, C. Perego and V. Tartiari, Telomerization reactions of butadiene and CO2 catalyzed by phosphine Pd(0) complexes: (E)-2-ethylidenehept-6-en-5-olide and octadienyl esters of 2-ethylidenehepta-4,6-dienoic acid, Inorg. Chim. Acta, 1978, 28, L147–L148 CrossRef CAS.
- M. Sharif, R. Jackstell, S. Dastgir, B. Al-Shihi and M. Beller, Efficient and selective palladium-catalyzed telomerization of 1,3-butadiene with carbon dioxide, ChemCatChem, 2017, 9, 542–546 CrossRef CAS.
- J. M. Balbino, J. Dupont and J. C. Bayón, Telomerization of 1,3-butadiene with carbon dioxide: A highly efficient process for δ-lactone generation, ChemCatChem, 2018, 10, 206–210 CrossRef CAS.
- T. A. Fassbach, R. Kirchmann, A. Behr and A. J. Vorholt, Recycling of homogeneous catalysts in reactive ionic liquid – solvent-free aminofunctionalizations of alkenes, Green Chem., 2017, 19, 5243–5249 RSC.
- A. Behr and M. Becker, The telomerization of 1,3-butadiene and carbon dioxide: process development and optimization in a continuous miniplant, Dalton Trans., 2006, 4607–4613 RSC.
- Z. Yang, C. Shen and K. Dong, Hydroxyl group-enabled highly efficient ligand for Pd-catalyzed telomerization of 1,3-butadiene with CO2, Chin. J. Chem., 2022, 40, 2734–2740 CrossRef CAS.
- J. M. Balbino, J. Dupont and J. C. Bayón, Telomerization of 1,3-butadiene with carbon dioxide: A highly efficient process for δ-lactone generation, ChemCatChem, 2018, 10, 206–210 CrossRef CAS.
- A. Behr and M. Heite, Telomerization of carbon dioxide and 1,3-butadiene: Process development in a miniplant, Chem. Eng. Technol., 2000, 23, 952–955 CrossRef CAS.
- A. Behr and V. A. Brehme, Bimetallic-catalyzed reduction of carboxylic acids and lactones to alcohols and diols, Adv. Synth. Catal., 2002, 344, 525–532 CrossRef CAS.
- A. Behr and V. A. Brehme, Homogeneous and heterogeneous catalyzed three-step synthesis of 2-ethylheptanoic acid from carbon dioxide, butadiene and hydrogen, J. Mol. Catal., 2002, 187, 69–80 CrossRef CAS.
-
A. Behr, B. Turkowski, R. Roll, R. Schöbel and G. Henze, in Regulated Systems for Multiphase Catalysis, ed. W. Leitner and M. Hölscher, Springer Berlin Heidelberg, Berlin, Heidelberg, 2008, pp. 19–52 Search PubMed.
- M. Sugiura, N. Sato, S. Kotani and M. Nakajima, Lewis base-catalyzed conjugate reduction and reductive aldol reaction of α,β-unsaturated ketones using trichlorosilane, Chem. Commun., 2008, 4309–4311 RSC.
- A. Behr and V. A. Brehme, Homogeneous and heterogeneous catalyzed three-step synthesis of 2-ethylheptanoic acid from carbon dioxide, butadiene and hydrogen, J. Mol. Catal., 2002, 187, 69–80 CrossRef CAS.
- R. M. Rapagnani, R. J. Dunscomb, A. A. Fresh and I. A. Tonks, Tunable and recyclable polyesters from CO2 and butadiene, Nat. Chem., 2022, 14, 877–883 CrossRef CAS PubMed.
- D. K. Schneiderman and M. A. Hillmyer, Aliphatic polyester block polymer design, Macromolecules, 2016, 49, 2419–2428 CrossRef CAS.
- Y. Lou, L. Xu, N. Gan, Y. Sun and B.-L. Lin, Chemically recyclable polyesters from CO2, H2, and 1,3-butadiene, Innovation, 2022, 3, 100216–100222 CAS.
- R. Nakano, S. Ito and K. Nozaki, Copolymerization of carbon dioxide and butadiene via a lactone intermediate, Nat. Chem., 2014, 6, 325–331 CrossRef CAS PubMed.
- A. Yamamoto, K. Morifuji, S. Ikeda, T. Saito, Y. Uchida and A. Misono, Diethylbis(bipyridine)iron. Butadiene cyclodimerization catalyst, J. Am. Chem. Soc., 1968, 90, 1878–1883 CrossRef CAS.
- R. Matusiak, Y. Castanet and A. Mortreux, Dimerisation of butadiene catalyzed by nickel-tris[(1H,1H,2H,2H-perfluorodecyl)phenyl]phosphites complexes in fluorocarbon–hydrocarbon biphasic medium, J. Mol. Catal., 2004, 224, 217–223 CrossRef CAS.
- M. Benaissa, A. M. Alhanash, M. Eissa and M. S. Hamdy, Solvent-free selective hydrogenation of 1,5-cyclooctadiene catalyzed by palladium incorporated TUD-1, Catal. Commun., 2017, 101, 62–65 CrossRef CAS.
- V. V. Pagar and T. V. RajanBabu, Tandem catalysis for asymmetric coupling of ethylene and enynes to functionalized cyclobutanes, Science, 2018, 361, 68–72 CrossRef CAS PubMed.
- J. J. Cowell, A. K. Santra and R. M. Lambert, Ultraselective epoxidation of butadiene on Cu{111} and the effects of Cs promotion, J. Am. Chem. Soc., 2000, 122, 2381–2382 CrossRef CAS.
-
C. S. Denton, C. R. TullyMax, R. Senatore and Chevron Phillips Chemical Co LP, US Pat., 6034254A, 2000 Search PubMed.
- D. Fiorito and C. Mazet, Ir-catalyzed selective hydroboration of 2-substituted 1,3-dienes: A general method to access homoallylic boronates, ACS Catal., 2018, 8, 9382–9387 CrossRef CAS.
- R. J. Maza, E. Davenport, N. Miralles, J. J. Carbó and E. Fernández, Transition-metal-free allylic borylation of 1,3-dienes, Org. Lett., 2019, 21, 2251–2255 CrossRef CAS PubMed.
- S. Peng, J. Yang, G. Liu and Z. Huang, Ligand controlled cobalt catalyzed regiodivergent 1,2-hydroboration of 1,3-dienes, Sci. China: Chem., 2019, 62, 336–340 CrossRef CAS.
- H. L. Sang, S. Yu and S. Ge, Cobalt-catalyzed regioselective stereoconvergent Markovnikov 1,2-hydrosilylation of conjugated dienes, Chem. Sci., 2018, 9, 973–978 RSC.
- K. Kobayashi, S. Teratani, Y. Izumori, K. Hayasaka and H. Nakazawa, Hydrosilylation of diene derivatives catalyzed by Fe-iminobipyridine complexes aiming at syntheses of organosilane compounds containing a terminal olefin portion, Bull. Chem. Soc. Jpn., 2019, 92, 105–114 CrossRef CAS.
- H. Wen, K. Wang, Y. Zhang, G. Liu and Z. Huang, Cobalt-catalyzed regio- and enantioselective markovnikov 1,2-hydrosilylation of conjugated dienes, ACS Catal., 2019, 9, 1612–1618 CrossRef CAS.
- C. Li, R. Y. Liu, L. T. Jesikiewicz, Y. Yang, P. Liu and S. L. Buchwald, CuH-catalyzed enantioselective ketone allylation with 1,3-dienes: Scope, mechanism, and applications, J. Am. Chem. Soc., 2019, 141, 5062–5070 CrossRef CAS PubMed.
- J. Yang, F. G. Delolo, A. Spannenberg, R. Jackstell and M. Beller, A selective and general cobalt-catalyzed hydroaminomethylation of olefins to amines, Angew. Chem., 2022, 61, e202112597 CAS.
- S. Tobisch, Organolanthanide-mediated intermolecular hydroamination of 1,3-dienes: Mechanistic insights from a computational exploration of diverse mechanistic pathways for the stereoselective hydroamination of 1,3-butadiene with a primary amine supported by an ansa-neodymocene-based catalyst, Eur. J. Chem., 2005, 11, 6372–6385 CrossRef CAS PubMed.
- O. Löber, M. Kawatsura and J. F. Hartwig, Palladium-catalyzed hydroamination of 1,3-dienes: A colorimetric assay and enantioselective additions, J. Am. Chem. Soc., 2001, 123, 4366–4367 CrossRef PubMed.
Footnote |
† These authors contributed equally to this work. |
|
This journal is © Institute of Process Engineering of CAS 2023 |