DOI:
10.1039/C5RA25135D
(Communication)
RSC Adv., 2016,
6, 16461-16466
Functionalized mesoporous silica nanoparticles as a catalyst to synthesize a luminescent polymer/silica nanocomposite†
Received
26th November 2015
, Accepted 13th January 2016
First published on 15th January 2016
Abstract
A bi-functionalized silica nanoparticle catalyst was synthesized by both generating rare earth oxide nanoparticles in the pore channels of the mesoporous silica support and grafting salicylaldimine cobalt complex on the surface of the silica. The nanocatalyst shows a strong green luminescence upon irradiation with ultraviolet light and also shows high activity for the polymerization of isoprene. The core–shell structure of this nanocomposite can protect the rare earth oxide from dissolving in hydrochloric acid. This process could produce a novel luminescent polymer/silica composite, and the polymer/silica nanocomposite formed also shows green luminescence.
Composite materials have been extensively studied since a long period of time. When inorganic phases in the organic/inorganic composites are made nanosized, they are called nanocomposites.1,2 The organic/inorganic nanocomposites are generally polymers with nanoscale inorganic building blocks. They combine the advantages of inorganic materials (e.g., thermal stability and rigidity) and organic materials (e.g., flexibility, ductility, and processability).3 Moreover, they usually also exhibit the special properties of the nanofillers, which can lead to materials with improved properties.4–6 An important feature of organic/inorganic nanocomposites is the size of the fillers, which leads to a dramatic increase in interfacial area as compared with traditional composites.7–9 This interfacial area creates a significant volume fraction of interfacial polymer with properties different from the bulk polymer. Among these nanofillers, silica is considered to be very important.10–12 Polymer/silica nanocomposites have attracted academic and industrial interest.13–16 Among the numerous inorganic/organic nanocomposites, polymer/silica composites are the most commonly reported in the literature. They have received a lot of attention and have been employed in a variety of applications.17–21 Principally, three methods for the preparation of polymer/silica nanocomposites can be used: blending,22–24 sol–gel process,25–28 and in situ polymerization.29–32 There are several advantages to the in situ polymerization method, such as ease of handling, the speed of the process, and better performance of the final products.
Rare earth oxides have been widely investigated as important functional materials in the fields of luminescence devices, optical films, and bioimaging due to their optical and chemical properties resulting from their 4f electrons. In these systems, rare earth ions typically possess a trivalent state.33,34 CeO2 is not a good candidate for Tb sensitization in luminescence applications because the state of cerium in CeO2 is Ce4+, which cannot serve as the sensitizer to Tb3+, and only a small amount of Ce3+ ions can contribute to the energy transfer from Ce3+ to Tb3+. The mechanism of Ce3+ to Tb3+ energy transfer has been investigated in many hosts.35,36 In these systems, Ce3+ ions can substitute for host lattice sites and serve as an effective sensitizer to help Tb3+ ions to emit efficiently.37–39
According to our previous studies, salicylaldimine cobalt complex functionalized mesoporous silica nanoparticles can show excellent catalytic activity for the polymerization of alkenes.40 Herein, we synthesized a type of luminescent nanocatalyst by immobilizing salicylaldimine cobalt complexes on the surface of rare earth oxide-containing mesoporous silica nanoparticles. Moreover, a novel method has been developed to synthesize the luminescent polymer/silica nanocomposite using the supported mesoporous silica nanoparticles as the catalyst for the in situ polymerization of isoprene. The nanoparticles can act as both the catalyst for the polymerization and the inorganic core of the luminescent nanocomposite. To the best of our knowledge, it is the first attempt to synthesize a rare earth oxide-containing luminescent polymer/silica nanocomposite with a core–shell structure. In addition, this polymer/silica nanocomposite can also exhibit a green luminescence.
Experimental section
Chemicals
Tetraethoxysilane (TEOS 98%), an aqueous solution of cetyltrimethylammonium chloride (CTAC, C16H33N(CH3)3Cl, 25 wt% in water), 3-aminopropyltriethoxysilane (3-APTES, 99%), diethanolamine (DEA, NH(CH2CH2OH)2, 99%), salicylaldehyde, isoprene, methylaluminoxane (MAO, 99%), and other organic solvents and inorganic compounds were purchased from Beijing Chemical Works and used as received without further purification. Toluene was used after purification using conventional methods.
Catalyst preparation
Mesoporous silica nanoparticles were prepared according to a literature procedure with slight modification.41 TEOS was added into an aqueous solution containing CTAC, ethanol, and DEA. The following is a typical synthesis example: 6.4 ml of water, 1.8 g of ethanol, 1.04 g of a 25 wt% CTAC solution, and 0.02 g of DEA were mixed and stirred in a water bath at 40 °C for 30 min. Then, 0.73 ml of TEOS was added dropwise to the mixture over 2 min with stirring. The solution turned white gradually. A further 2 h of stirring was necessary and then the mixture was cooled to room temperature. The as-prepared mesoporous silica nanoparticles were collected through centrifugation, washed three times with absolute ethanol and the surfactant extraction was performed by stirring the dried material in 120 ml of ethanol containing HCl at reflux for 24 h. Finally, the product was dried under vacuum overnight. This mesoporous material was designated as MSN.
We synthesized the luminescent rare earth oxide-containing nanoparticles according to a literature procedure with slight modification.42 Cerium nitrate hexahydrate (Ce(NO3)3·6H2O, 7.30 g, 0.017 mol), terbium nitrate hexahydrate (Tb(NO3)3·6H2O, 0.770 g, 0.0017 mol), and citric acid monohydrate (7.85 g, 0.0374 mol) were dissolved in water and the solutions were then mixed. The molar ratio of the total metals (Ce and Tb) to citric acid was 1
:
2. The aqueous solution containing the nitrates of cerium and terbium and citric acid was added to 3.62 g of MSN using the incipient wetness technique. After the addition, the material was dried in an oven at 80 °C for 24 h under vacuum to obtain a metal–citrate complex in MSN. It was then calcined at 170 °C and 550 °C for 2 h and 3 h in air, respectively, and the resulting solid was denoted as CTM.
The synthetic route of CTMCo is shown in Scheme 1. The organic modification of CTM with 3-aminopropyltriethoxysilane (3-APTES) was performed by stirring 1 g of CTM with 1.8 g (8.1 mmol) of 3-APTES in dry toluene and refluxing for 24 h under a nitrogen atmosphere. The resulting white solid of NH2–CTM was centrifuged and washed with absolute ethanol. The solid was then refluxed with salicylaldehyde (10 mmol, 1.29 g) in methanol (20 ml) for 3 h. The resulting yellow solid was then collected by centrifugation, dried under vacuum overnight, and the solid was designated as CTMS. Finally, the nanocatalysts were prepared by mixing a solution of cobalt nitrate (10 mmol) in methanol and adding the yellow solid to obtain a suspension, which was stirred at room temperature for 12 h. The solid was centrifuged, washed with methanol and dried under vacuum. The catalysts thus obtained were designated as CTMCo.
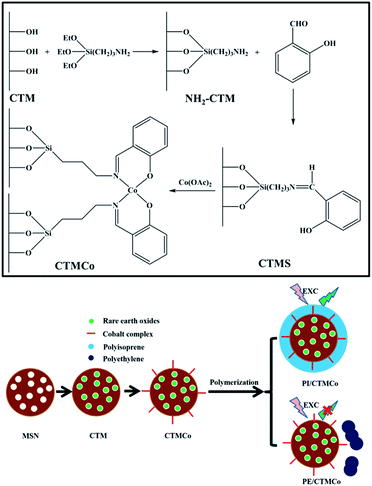 |
| Scheme 1 Synthetic route used to prepare CTMCo (top) and the nanocomposites (bottom). | |
Catalyst characterization
The particle morphologies and dimensions of the samples were determined by scanning electron microscopy (SEM) using a JEOL JSM-6700F operating at an accelerating voltage of 5 kV and transmission electron microscopy (TEM) using a JEOL JEM-3010 transmission electron microscope operating at 300 kV. Fourier transform infrared spectra (FTIR) were recorded with a JASCOFT/IR-420 spectrophotometer within the wavenumber range of 4000–400 cm−1 at a resolution of 4 cm−1 using the KBr pressed pellet technique. The thermogravimetric analysis (TGA) curves were recorded on a TA TGA Q500 thermal analyzer at a heating rate of 10 °C min−1 under nitrogen atmosphere. Inductively coupled plasma (ICP) analyses were carried out on a Perkin-Elmer Optima 3300DV ICP instrument. All the samples were dissolved in an aqueous solution of HF. The adsorption–desorption isotherms of nitrogen were measured at 77 K using a Micromeritics TriStar 3000 system. The pore size distributions were calculated from the adsorption branches of the N2 adsorption–desorption isotherms on the basis of the BJH model. The samples were outgassed at 373 K for 3 h before each measurement.
Catalytic reactions
All the operations were carried out under an atmosphere of dry nitrogen. Isoprene (0.5 g) and 10 ml of toluene were introduced into a 25 ml dried glass reactor, and the solution obtained was brought to 20 °C. MAO (500 μmol) and the nanocatalyst (1 μmol) were then added sequentially as suspensions in toluene. The polymerization was terminated with methanol containing a small amount of hydrochloric acid. The polymer was coagulated and repeatedly washed with methanol and then dried in vacuum at room temperature. This nanocomposite was designated as PI/CTMCo. The yield of polyisoprene (PI) was 95%. As a comparison, the polyethylene (PE)/silica nanocomposite was synthesized using ethylene as the precursor and this nanocomposite was named as PE/CTMCo.
Results and discussion
Salicylaldimine was used as the ligand due to its good coordination capacity. Salicylaldimine cobalt complexes were anchored onto the surface of the rare earth oxide-containing mesoporous silica by the grafting method. The diffused reflectance FT-IR spectra of CTM, CTMS, and CTMCo are shown in Fig. 1. In the CTM sample, the water bending vibration at 1630 cm−1 is observed, which can be assigned to the hydrophilic silanols on the silica surface after template removal (Fig. 1a).41 The IR spectra show the presence of C–H vibration bands in the 1550–1250 cm−1 region of the IR spectra of CTMS; these bands are absent in the case of CTM (Fig. 1a). This clearly indicates that 3-APTES has been anchored onto the CTM. The IR spectrum of CTMS (before complexation) shows a band at 1635 cm−1, which can be attributed to the C
N stretching frequency of the imine group. The IR spectra of CTMS and CTMCo are shown in Fig. 1b. A new band around 1624 cm−1 appeared and was assigned to the C
N stretching frequency of the complexation. According to a study by Srinivas, this shift can be attributed to the complexation of metal ions with the C
N bond.43 More specifically, the stretching vibration bands at 2953, 2885 cm−1 and 1242, and 742 cm−1 can be assigned to aliphatic C–H stretching and C–Si stretching vibrations, which were observed for both CTMS and CTMCo.
 |
| Fig. 1 (a) IR spectra of CTM (black), CTMS (red), and CTMCo (blue). (b) Comparison of IR spectra of CTMS (black) and CTMCo (red). | |
The N2 adsorption–desorption isotherms of the mesoporous silica nanoparticles are shown in Fig. 2 and correspond to a type IV adsorption isotherm, suggesting mesoporosity. The results also show that MSN has a BET surface area of 692 m2 g−1 and a pore volume (Vp) of 0.28 (cm3 g−1). The average pore diameter was calculated to be 27.0 Å using the BJH method. Moreover, CTMCo has a BET surface area of 88 m2 g−1 and a pore volume (Vp) of 0.08 (cm3 g−1). The average pore diameter was calculated to be 18.2 Å using the BJH method. As expected, the surface area of CTMCo considerably decreases compared to that found for MSN, which is consistent with the presence of anchored organic ligands and cerium and terbium oxides in the pore channels. Upon functionalization with the cobalt complexes and cerium and terbium oxides, the pore volumes are drastically reduced. This can be attributed to loading with organics and oxides, which occupy the void spaces inside the mesopores. The decrease in pore volume clearly suggests that the complexes and oxide are located in the mesopores.
 |
| Fig. 2 N2 adsorption/desorption isotherms of MSN (black) and CTMCo (red). | |
The TGA curve for CTMCo (as shown in Fig. 3) shows a major weight loss of 23 wt% in the temperature range of 200–600 °C. This mass loss can be corresponded to the decomposition of the cobalt complexes. The EDX spectrum of CTMCo is shown in Fig. S2,† which clearly confirms the presence of Ce, Tb, and Co in the catalyst. To obtain evidence of the uniform dispersion of cerium and terbium oxides in CTMCo, quantification of the elemental composition using EDX was carried out at three arbitrary points on the different catalyst particles. The quantitative analysis of Ce, Tb, and Co at the three different arbitrary points shows no significant change in their relative intensities. This provides a strong indication that most of the Ce and Tb are uniformly distributed in the support materials. Moreover, the ICP analysis results also show that the molar ratio of Ce/Tb is around 10. The XRD patterns and EDS elemental mappings of CTM are shown in Fig. S3 and S4, respectively.†
 |
| Fig. 3 The TGA data for CTMCo. | |
SEM and TEM were used to study the morphology of CTM, CTMS, and CTMCo. The images of the samples show that all the nanoparticles have a uniform size and spherical shape. As shown in Fig. 4, the SEM images of the samples show that they all consist of spherical nanoparticles and all the nanoparticles are highly monodisperse. Moreover, the shapes of the catalysts are retained after immobilization with the organic groups and complexation. The nature of the complexes does not have a significant impact on the morphology of CTM. As shown in Fig. 5a, the TEM image of CTMCo shows that the nanostructure of the catalyst was retained. According to the SEM and TEM images, it is worth noting that there are no oxides outside the silica nanoparticles, and that all the oxides are located in the pore channels, which are in agreement with the EDX results.
 |
| Fig. 4 SEM images of (a) CTM, (b) CTMS, and (c) CTMCo. | |
 |
| Fig. 5 (a) TEM image of CTMCo. (b) SEM image and (c) TEM image of PI/CTMCo. | |
SEM and TEM were also used to study the structure of PI/CTMCo. The SEM image of PI/CTMCo is shown in Fig. 5b; the polymerization products are made up of nanoparticles. The monomers polymerize on the surface of the nanocatalysts. The catalyst should polymerize the monomers to produce a polymer that reproduces the particles size distribution of the nanocatalyst. The morphology of the resulting nanocomposite particles by TEM reveals that the polymer forms on the surface of CTMCo. The strong contrast between the pale edge and dark center in Fig. 5c is also proof for the core–shell structure.
The mesoporous silica nanoparticles act as both the catalyst support and the inorganic core of the nanocomposite. The great differences in the properties of the polymer and silica can often cause phase separation. Thus, the interfacial interaction between the two phases of the nanocomposites was the most decisive factor. Silane coupling agents can lead to much stronger interactions between PI and the silica surface. The hydrolysable groups of the silane coupling agents react with hydroxyl groups on the SiO2 surface, and the alkyl chain of the silane coupling agents may react with PI. The silane coupling agents on the surface of CTM connected the silica and PI. The introduced functional groups could also participate in the polymerization, resulting in graft polymers on the silica surface.40 However, as shown in Fig. S5,† phase separation occurs in the PE/CTMCo samples. This indicates that PE and silica are not compatible and the alkyl chain of the silane coupling agents might not react with PE.
According to the characterization data mentioned above, we can conclude that the preparation of the cobalt complexes supported on the rare earth oxide-containing mesoporous silica nanoparticles was successful. In addition, this catalyst can show high activity for the polymerization of isoprene, forming the polyisoprene/silica nanocomposite with a core–shell structure.
The luminescence properties of both the nanocatalysts and the nanocomposites were characterized by their excitation and emission spectra. Both CTMCo and PI/CTMCo show a strong green luminescence upon irradiation with ultraviolet light. The excitation and emission spectra of CTMCo are shown in Fig. 6. The maximum absorption of CTMCo is located around 288 nm. Upon excitation at 288 nm, the CTMCo catalyst gives a characteristic Tb3+ emission. The emissions at 488, 542, 584, and 620 nm for CTMCo can be assigned to the transitions from the 5D4 level to the 7FJ (J = 6, 5, 4, 3) levels, of which the 5D4 → 7F5 emission is the most prominent. No emission from the ligand can be observed, which indicates that the ligands absorb and transfer energy efficiently to the central Tb3+ ion. In addition, the halfwidth of the strongest band is less than 10 nm, indicating that CTMCo exhibits high fluorescence intensity and color purity. PI/CTMCo shows the same luminescence character as the CTMCo catalyst with lower intensity. The luminescence property of PE/CTMCo was also characterized by the excitation and emission spectra. However, a broad emission between 450 nm and 530 nm can be seen in Fig. S6,† which may be caused by Ce3+ emission.42 Because the polymerization was terminated with methanol containing hydrochloric acid, the rare earth oxides could dissolve in this solution.44 However, because the PI/CTMCo nanoparticles possess core–shell structure, the polymer on the surface can prevent the rare earth oxides in the pore channels from dissolving in the acid solution. These nanoparticles are not sensitive to the acid solution.
 |
| Fig. 6 Excitation (a) and emission (b) spectra for CTMCo (black) with lex = 288 nm and PI/CTMCo (red) with lex = 288 nm. | |
Conclusions
We synthesized a type of luminescence nanocatalyst that can catalyse the polymerization of isoprene on the surface of the nanoparticles to obtain a luminescent polymer/silica nanocomposite with these nanoparticles. Here, the nanoparticles can act as both the catalyst support and the inorganic core of the luminescent nanocomposite. This is the first synthesis of a rare earth oxide-containing luminescent polymer/silica nanocomposite with a core–shell structure, which could be used as a new luminescence material. This process opens a new approach for the preparation of luminescent polymer/silica nanocomposites.
Notes and references
- J. Wen and G. L. Wilkes, Chem. Mater., 1996, 8, 1667–1681 CrossRef CAS.
- H. Althues, J. Henle and S. Kaskel, Chem. Soc. Rev., 2007, 36, 1454–1465 RSC.
- H. Zou, S. S. Wu and J. Shen, Chem. Rev., 2008, 108, 3893–3957 CrossRef CAS PubMed.
- C. Sanchez, P. Belleville, M. Popall and L. Nicole, Chem. Soc. Rev., 2011, 40, 696–753 RSC.
- J. I. Amalvy, M. J. Percy, S. P. Armes and H. Wiese, Langmuir, 2001, 17, 4770–4778 CrossRef CAS.
- H. Goda and C. W. Frank, Chem. Mater., 2001, 13, 2783–2787 CrossRef CAS.
- C. Barthet, A. J. Hickey, D. B. Cairns and S. P. Armes, Adv. Mater., 1999, 11, 408–490 CrossRef CAS.
- M. J. Percy, C. Barthet, J. C. Lobb, M. A. Khan, S. F. Lascelles, M. Vamvakaki and S. P. Armes, Langmuir, 2000, 16, 6913–6920 CrossRef CAS.
- H. Mori, D. C. Seng, M. F. Zhang and A. H. E. Muller, Langmuir, 2002, 18, 3682–3693 CrossRef CAS.
- H. Jo and F. D. Blum, Chem. Mater., 1999, 11, 2548–2553 CrossRef CAS.
- Z. J. Hou, L. Y. Liu, L. Xu, Z. L. Xu, W. C. Wang, F. M. Li and M. X. Ye, Chem. Mater., 1999, 11, 3177–3180 CrossRef CAS.
- Q. W. Feng, J. G. Xu, H. Dong, S. X. Li and Y. Wei, J. Mater. Chem., 2000, 10, 2490–2494 RSC.
- H. Mori, A. H. E. Muller and J. E. Klee, J. Am. Chem. Soc., 2003, 125, 3712–3713 CrossRef CAS PubMed.
- K. Kamata, Y. Lu and Y. N. Xia, J. Am. Chem. Soc., 2003, 125, 2384–2385 CrossRef CAS PubMed.
- B. McCaughey, C. Costello, D. H. Wang, J. E. Hampsey, Z. Z. Yang, C. J. Li, C. J. Brinker and Y. F. Lu, Adv. Mater., 2003, 15, 1262–1266 CrossRef.
- Y. S. Kang, H. I. Lee, Y. Zhang, Y. J. Han, J. E. Yie, G. D. Stucky and J. M. Kim, Chem. Commun., 2004, 1524–1525 RSC.
- G. K. Agarwal, J. J. Titman, M. J. Percy and S. P. Armes, J. Phys. Chem. B, 2003, 107, 12497–12502 CrossRef CAS.
- G. Garnweitner, B. Smarsly, R. Assink, W. Ruland, E. Bond and C. J. Brinker, J. Am. Chem. Soc., 2003, 125, 5626–5627 CrossRef CAS PubMed.
- R. L. Liu, Y. F. Shi, Y. Wan, Y. Meng, F. Q. Zhang, D. Gu, Z. X. Chen, B. Tu and D. Y. Zhao, J. Am. Chem. Soc., 2006, 128, 11652–11662 CrossRef CAS PubMed.
- R. Ravindranath, P. K. Ajikumar, N. B. M. Hanafiah, W. Knoll and S. Valiyaveettil, Chem. Mater., 2006, 18, 1213–1218 CrossRef CAS.
- E. Dovgolevsky, S. Kirmayer, E. Lakin, Y. Yang, C. J. Brinker and G. L. Frey, J. Mater. Chem., 2008, 18, 423–427 RSC.
- E. Moncada, R. Quijada and J. Retuert, Nanotechnology, 2007, 18, 335606–335613 CrossRef.
- M. Z. Rong, M. Q. Zhang, Y. X. Zheng, H. M. Zeng, R. Walter and K. Friedrich, Polymer, 2001, 42, 167–183 CrossRef CAS.
- L. F. Cai, X. B. Huang, M. Z. Rong, W. H. Ruan and M. Q. Zhang, Polymer, 2006, 47, 7043–7050 CrossRef CAS.
- B. M. Novak, Adv. Mater., 1993, 5, 422–433 CrossRef CAS.
- G. Schottner, Chem. Mater., 2001, 13, 3422–3435 CrossRef CAS.
- C. Sanchez, B. Julián, P. Belleville and M. Popall, J. Mater. Chem., 2005, 15, 3559–3592 RSC.
- F. Mammeri, E. Le Bourhis, L. Rozes and C. Sanchez, J. Mater. Chem., 2005, 15, 3787–3811 RSC.
- P. Espiard and A. Guyot, Polymer, 1995, 36, 4391–4395 CrossRef CAS.
- S. Reculusa, C. Mingotaud, E. Bourgeat-Lami, E. Duguet and S. Ravaine, Nano Lett., 2004, 4, 1677–1682 CrossRef CAS.
- A. L. Qu, X. F. Wen, P. H. Pi, J. Cheng and Z. R. Yang, J. Colloid Interface Sci., 2008, 317, 62–69 CrossRef CAS PubMed.
- J. L. Luna-Xavier, A. Guyot and E. Bourgeat-Lami, J. Colloid Interface Sci., 2002, 250, 82–92 CrossRef CAS PubMed.
- K. Binnemans, Chem. Rev., 2009, 109, 4283–4374 CrossRef CAS PubMed.
- J.-C. G. Bünzli, Chem. Rev., 2010, 110, 2729–2755 CrossRef PubMed.
- C. M. Zhang, C. X. Li, C. Peng, R. T. Chai, S. S. Huang, D. M. Yang, Z. Y. Cheng and J. Lin, Chem.–Eur. J., 2010, 16, 5672–5680 CrossRef CAS PubMed.
- P. P. Yang, Z. W. Quan, C. X. Li, Z. Y. Hou, W. X. Wang and J. Lin, J. Solid State Chem., 2009, 182, 1045–1054 CrossRef CAS.
- F. Ye, T. Mori, D. R. Ou, J. Zou and J. Drennan, Mater. Res. Bull., 2007, 42, 943–949 CrossRef CAS.
- D. P. Dutta, N. Manoj and A. K. Tyagi, J. Lumin., 2011, 131, 1807–1812 CrossRef CAS.
- A. A. Ansari, S. P. Singh and B. D. Malhotra, J. Alloys Compd., 2011, 509, 262–265 CrossRef CAS.
- D. H. Tang, L. Zhang, Y. L. Zhang, Z. A. Qiao, Y. L. Liu and Q. S. Huo, J. Colloid Interface Sci., 2012, 369, 338–343 CrossRef CAS PubMed.
- Z. A. Qiao, L. Zhang, M. Y. Guo, Y. L. Liu and Q. S. Huo, Chem. Mater., 2009, 21, 3823–3829 CrossRef CAS.
- X. M. Wang, D. J. Zhang, Y. T. Li, D. H. Tang, Y. Xiao, Y. L. Liu and Q. S. Huo, RSC Adv., 2013, 3, 3623–3630 RSC.
- M. M. Bhadbhade and D. Srinivas, Inorg. Chem., 1993, 32, 5458–6122 CrossRef CAS.
- J. T. Kong, S. Y. Shi, L. C. Kong, X. P. Zhu and J. R. Ni, Electrochim. Acta, 2007, 53, 2048–2054 CrossRef CAS.
Footnote |
† Electronic supplementary information (ESI) available. See DOI: 10.1039/c5ra25135d |
|
This journal is © The Royal Society of Chemistry 2016 |
Click here to see how this site uses Cookies. View our privacy policy here.