DOI:
10.1039/C5RA21876D
(Paper)
RSC Adv., 2015,
5, 105844-105850
Properties of edible films based on pullulan–chitosan blended film-forming solutions at different pH
Received
20th October 2015
, Accepted 8th December 2015
First published on 9th December 2015
Abstract
Influences of solution pH on the properties of pullulan–chitosan blended (Pul–Chi) films and the rheological properties of film-forming solutions were investigated. The extended conformation of chitosan in a pH 4.0 solution increased the intermolecular interactions with pullulan compared to the more compact coiled form, resulting in higher tensile strength and barrier properties of the Pul–Chi film and higher viscosity of the film-forming solution. The water solubility (Ws) of the Pul–Chi film decreased to 35% above pH 4.0. Water content, thickness and percentage elongation (E%) all decreased with decreasing pH. Fourier Transform infrared spectroscopy (FTIR) analysis suggested that the formation of –NH3+ and intermolecular hydrogen bonds increased the amide II bending mode. At pH values below 4.0, shielding of the protonated amine groups caused a decrease in bending frequency. An X-ray diffraction (XRD) peak for crystallite chitosan was not observed in Pul–Chi films. The properties of Pul–Chi films depended on the conformation changes of chitosan molecules and can be controlled by pH.
Introduction
Consumer demand for safe and natural food packaging materials has spurred the research and development of films, coatings and packaging that are derived from food grade polysaccharides, proteins and lipids. Food based packaging materials are also sustainable, biodegradable and environmentally friendly.1–4 Due to excellent biodegradability and unique gas barrier properties, pullulan and chitosan are potentially useful film and packaging materials.5–7
Pullulan is flavorless and has good oxygen barrier properties, but its films have low transparency and poor mechanical properties. In solution pullulan is a random coil polymer with newtonian flow behavior that is little affected by pH.8,9 Improved mechanical properties of films have been reported when pullulan is combined with proteins or polysaccharides.10–13 Chitosan forms more transparent and flexible films. The properties of composite films of chitosan and pullulan were studied by Lazaridou and Biliaderis. They reported that the glass transition temperature and molecular interactions that affect physical properties of pullulan–chitosan blended films were highly sensitive to the water content.14 The properties of the films with different ratios of pullulan to chitosan prepared in our laboratory have been previously studied, and the composite films formed with a 1
:
1 ratio of pullulan and chitosan from a 2% acetic acid solution were found to have the best properties.15
The physical properties of edible films are highly dependent not only on its chemical composition, but pH and solvent as well. And the properties of the film-forming solutions may also contribute information about the molecular confirmation and interactions of the polymers in the final film.9,16 Because chitosan contains amine groups, its film properties are influenced by pH and solvent. Kienzle-Sterzer et al. reported differences in mechanical properties of chitosan films with acetic or propionic acid.17 They showed that physical properties, such as the storage modulus was linearly related to the polymer junction density, but that differences in acid types also affect film properties due to differences that originate in solution molecular conformation, ultimately affecting molecular topology in the film. Kim et al.18 reported that as pH increased, water vapor permeability (WVP) and total soluble matter (TSM) of chitosan films tended to increase, while tensile strength (TS) decreased significantly. Fourier-transform infrared spectroscopy suggested that peak shifts were possibly due to interactions with plasticizers or organic acid anions at different pH values. Zhong et al.19 investigated the properties of kudzu starch–chitosan composite films formed from solutions with different organic acids. Films formed in acetic acid as the solvent had the greatest mechanical strength and lowest solubility, while films formed from lactic acid solution had the most flexible.
In our current study, we found that Pul–Chi films had different physical properties that depend on the pH of the film-forming solutions. These changes were shown to be related to the conformation of the chitosan polymer as well as the effect of moisture content on glass to rubber transition. Properties of film-forming solutions and the mechanical and barrier properties of the Pul–Chi films were investigated in this study. FTIR (Fourier transform infrared spectroscopy) and XRD (X-ray diffractograms) were also used to examine the interaction between the components in the films.
Materials and methods
Materials
Pullulan (Mw = 600
000 Da) was obtained from the Tokyo Kasei Kogyo Co., Ltd (Tokyo, Japan). Chitosan (Mw = 300
000 Da, 85% deacetylated) was purchased from Zhejiang Aoxing Biotechnology Co., Ltd (Taizhou, China). All other chemicals used in this study were of analytical grade. Distilled water was used for the preparation of all solutions.
Preparation of films
Film-forming solutions were prepared using chitosan and pullulan at the concentration of 4% with different ratios (chitosan weight of dry matter: 0%, 25%, 50%, 75% and 100%, w/w). Glycerol with the concentration of 15% (respect to the polysaccharide, w/w) was then added into the solution, and stirred for 2 h. Film solutions of different pH values (pH 5, 4.5, 4, 3.5 and 3) were prepared at room temperature by adjusting the pH of the solutions with 4 M sodium hydroxide or hydrochloric acid solutions. Solutions were filtered to remove particulates and allowed to stand overnight to remove bubbles.
Films were prepared by the casting-evaporation method as previously described.15 The film-forming solution used for film preparation was 2% chitosan and 2% pullulan (mass ratio of chitosan to pullulan was 1
:
1) dispersion. Twenty-five milliliters of the dispersion was cast onto a 11 cm × 11 cm level bottom, rimmed acrylic plates and dried at 45 °C. The films were peeled from the plates, and conditioned in a desiccator cabinet with Mg(NO3)2·5H2O saturated solution (relative humidity at 53%, 25 °C) for 72 h.
Viscosity of film-forming solutions
The viscosities of the film-forming solutions were determined at 25 °C over a shear rate range of 1–100 s−1 using a dynamic rheometer (AR-G2, TA Instruments, USA) equipped with cone-plate geometry (4° angle and 40 mm). All measurements were performed in triplicate.
Water solubility and water content of films
The water solubility of the Pul–Chi films was measured on films dried to a minimum water content by storing in a desiccator (0% RH) for 10 days. The dried films were cut into squares (20 mm × 20 mm) and weighed (W0). The film squares were placed in 5 mL deionized water and shaken for 5 min at 50 rpm on an oscillating water bath (25 °C). The undissolved films were dried in a vacuum drying oven (100 °C) to constant weight (W1). The water solubility (Ws) of the films was calculated as: Ws = (W0 − W1)/W0 × 100%. The moisture content of the films was analyzed using AACC method 44–40 (2000).20 All the tests were carried out in triplicate.
Mechanical properties
Film thickness was reported as the mean of the measurements at 10 different points on each specimen taken with a micrometer (Guilin, China). Tensile strength and percent elongation of films were measured by using a texture analyzer (Stable Micro Systems, Surrey, UK) after equilibration at 53% RH according to ASTM 828-88 with some modifications.21 The analysis were performed on 20 mm × 80 mm strips. The initial grip separation and crosshead speed were set at 50 mm and 0.5 mm s−1, respectively. Percentage elongation (E%) and tensile strength of the film was calculated with following equations:
l1 is the initial length of the film, l is the length of the film at the break point. The results were the average measurements on eight samples.
Water vapor permeability
Water vapor permeability (WVP) and water vapor transmission rate (WVTR) were determined by the silica gel method (ASTM E96-00) with some modifications.19 After equilibration at 53% RH for 72 h, films were sealed in cups containing silica gel (the distance between the film and the silica gel was 9 mm). Test cups were placed in a cabinet at 25 °C and 90% RH (BaCl2 saturated solution). The weight changes were monitored by periodic weighing every 2 h for 24 h. The gradient is equal to the slope of the regression line of the weight increase vs. time. WVP values were calculated according to the previous methods22,23 as follows:
WVTR = slope/S = P × D × ln[(P − PA3)/(P − PA2)]/R × T × Z |
WVP = WVTR × X/(PA1 − PA2) |
where S = film area; P = total pressure; D = diffusivity of water through air at 25 °C; R = gas law constant; T = absolute temperature (298 K); Z = mean stagnant air gap height (9 mm); X = film thickness (mm); PA1 = water vapor partial pressure at film outer surface in the cabinet; PA2 = corrected water vapor partial pressure at film inner surface in cup; PA3 = water vapor partial pressure at silica gel surface.
Oxygen barrier properties
60 mL jars filled with 30.0 mL of fresh soybean oil were covered with different films and sealed using bungee. After storing at 60 °C for 10 days, the peroxide value (PV) of the soybean oil samples was determined by titration of peroxides with sodium thiosulfate.24 All tests were carried out in triplicate.
FTIR analysis
FTIR absorbance spectra were recorded on a spectrometer (Nicolet Nexus 470, Thermo Electron, Waltham, USA) using the digital attenuated total reflectance (ART) accessory. Samples of chitosan, pullulan, and the films were scanned from 700 to 4000 cm−1. Each spectrum obtained at a resolution of 4 cm−1, was an average of 64 consecutive scans.
XRD analysis
The X-ray diffraction patterns were made from samples of films using a diffractometer (BrukerD8 AXS, Bruker BioSpin, Rheinstetten, Germany) at target voltage 40 kV and target current 40 mA with 0.154 nm CuK radiation. Diffractograms were recorded in duplicate from 2θ of 2° to 40° with a scanning speed of 4° min−1. Films were preserved in a desiccator (0% RH) before testing.
Statistical analysis
The averages, standard deviations and Duncan's t-test were calculated using SAS Software (Release 8.0, SAS Institute Inc., Raleigh, NC).
Results and discussion
Viscosity of Pul–Chi film-forming solutions
Practically, a moderate viscosity of the film-forming solution is desirable.25 Low-viscosity solutions are readily affected by environmental conditions during drying, resulting in uneven mechanical properties of the film. High-viscosity solutions are difficult to pour forming nonuniform films.
Our previous study showed that the viscosity of the film-forming solutions with different chitosan to pullulan mass ratios all behaved like newtonian solutions at pH 3.0–5.0.15 Although pullulan is a much larger molecule (600
000 Da) compared to chitosan (300
000 Da), the viscosity of pullulan (Fig. 1a, 0% chitosan) was very low, suggesting that it existed in a compact conformation. The viscosities of the 1
:
1 Pul–Chi blended solutions at different pHs are shown in Fig. 1b. Pullulan viscosity was independent on the solution pH,8,9 so the viscosity of the Pul–Chi solution below pH 5.0 was mainly due to 2% chitosan content as shown by the linear dependence on chitosan content in Pul–Chi solutions in Fig. 1a.
 |
| Fig. 1 (a) Viscosity of film-forming solutions with different chitosan content in Pul–Chi dry matter at pH 4.0. (b) Effect of pH on the viscosity of the Pul–Chi film-forming solutions. | |
As the pH decreased from 5.0 to 4.0, the protonation of the amine (–NH2) groups resulted in repulsion between positively charged neighboring ammonium ions and unfolding of the chitosan polymer to form a more linear structure. Further decrease in pH (from pH 4.0 to 3.0) led to a small reduction in viscosity (Fig. 1b). The decreasing viscosity may be due to the increased concentration of Cl− ions from the HCl used to acidify the solutions. The association of Cl− with –NH3+ may shield the repulsion between –NH3+ groups. The shielded repulsion relaxed the linear polymer to a more random coil conformation, leading to a decrease in viscosity.
Effect of pH on the water solubility and water content of the Pul–Chi films
Water and other small molecules such as glycerol and acetate reduce the glass transition temperature and act as plasticizers. We had previously shown that chitosan films formed in 2% acetic acid, pullulan films in water, and their blends in acetic acid were completely soluble.15 In this study, water solubility (Ws) of the 1
:
1 Pul–Chi films formed above pH 3.5 decreased to about 35% (Fig. 2). Since pullulan is completely water soluble and accounts for 50% of the mass, the insolubility was mostly due to chitosan. At pH below 5.0, the increasing hydrochloric acid concentration reduced the intramolecular hydrogen bonds between chitosan or pullulan molecules, making the film more soluble. Osmotic effects may also contribute to film dissolution. At lower pH, counterions may migrate into the film, changing the osmotic pressure and facilitating water movement and swelling of the film.26
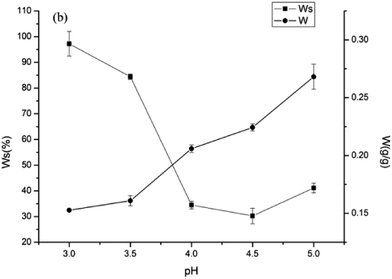 |
| Fig. 2 Effect of pH on the water solubility (Ws) and water content (W) of the Pul–Chi films. | |
While the Ws decreased with increasing pH, the water content (W) of the blended films increased with increasing pH. W is measured in an atmosphere of fixed humidity, while the film is immersed in water for the Ws measurement. It is hypothesized that the electrostatic repulsion between –NH3+ stretched the molecular chain of chitosan, increasing its surface area and interaction with pullulan molecules by intermolecular hydrogen bonds, which would favor the formation of junction network structure for the blended films. With increasing H+ concentration, the increased intermolecular hydrogen bonds decreased the distance between polymer chains, restrained the deformation of the chitosan and pullulan polymers and reduced the free space available for the absorption of water. At higher pH, the coiled structure of chitosan would increase the amount of intermolecular space, and more water molecules were able to enter into the network structure of the films, resulting in the higher W. Additionally, the increase of acetate when adjusting pH using sodium hydroxide at higher pH may promote the sensitivity of films to humidity due to its hydrophilic nature.27
Effect of pH on the mechanical properties of the Pul–Chi films
Tensile strength (TS), percentage elongation (E%) and thickness of the Pul–Chi films prepared in solutions of different pH are presented in Table 1. The TS of the film increased 2.7 times when the solution pH decreased from 5.0 to 4.0, but did not change when further decreasing the pH from 4.0 to 3.0. Lazaridou et al. showed that the storage modulus (E′) for pullulan was highly dependent on moisture content. At a moisture content of about 12%, E′ started a rapid decrease at 30 °C.9 In this study, moisture content of the films ranged from 15–30%, suggesting relatively lower Tg and E′. The higher moisture content at higher pH (Fig. 2), the lower E′ and TS of the films. Higher moisture content also enhanced molecular mobility of the film and increased the free volume in the film matrix, resulting in higher E%.
Table 1 Effect of pH on the mechanical properties of the Pul–Chi filmsa
Films with different pH |
Thickness (μm) |
TS (MPa) |
E% |
Values are given as mean ± standard deviation. Different letters in the same column indicate significantly different (p < 0.05). |
pH = 5.0 |
88.0 ± 2.7A |
18.8 ± 1.4C |
45.60 ± 3.89%A |
pH = 4.5 |
74.2 ± 4.3B |
36.3 ± 2.3B |
32.70 ± 2.94%B |
pH = 4.0 |
60.3 ± 5.5C |
69.5 ± 3.2A |
2.79 ± 0.28%C |
pH = 3.5 |
57.3 ± 3.2C |
69.3 ± 3.3A |
2.51 ± 0.37%C |
pH = 3.0 |
56.6 ± 2.3C |
69.7 ± 4.9A |
2.65 ± 0.19%C |
On the other hand, the molecular basis of the increasing TS with decreasing pH is because of the increased intermolecular hydrogen bonds due to the protonated chitosan molecule favoring the formation of networks. Viscosity of the film forming solution may be a predictor of mechanical properties since both increasing viscosity and mechanical strength depend on inter-molecular polymer interactions. As seen in Fig. 3, TS was positively correlated with viscosity, while E% was negatively correlated with viscosity. Kienzle-Sterzer et al. has shown that the Young's modulus increases with increasing junction density within chitosan films.17 So the viscosity of the film forming solution is also a practical concern in the manufacture of films.
 |
| Fig. 3 Relationship between (a) film tensile strength and viscosity of film-forming solution; (b) film elongation and viscosity of film-forming solution. | |
Both thickness and E% decreased from pH 5.0 to 4.0 and then remained unchanged. Water in the film is a plasticizer. The coil conformation of chitosan at higher pH would increase the voids in the film matrix and decrease polymer–polymer intermolecular interactions, resulting in the increased flexibility and elongation of the film.
Effect of pH on oxygen and water vapor permeability of the Pul–Chi films
The peroxide value (PV) a measure of oil oxidation was used as an indirect measure of oxygen permeability. PV was determined in soybean oil in jars covered with the Pul–Chi films. The WVP, WVTR and the PV values of films made from solutions with different pH are shown in Table 2. WVTR, WVP and PV decreased when the pH decreased from 5.0 to 4.0, but no significant changes were found when the pH was reduced to 3.0. These results were consistent with the changes in mechanical properties with pH (Table 1). Kim et al.18 reported increasing WVP of chitosan films as pH increased from 3.0 to 5.0. WVP and WVTR are believed to be dependent on the increasing number of “available” polar (–OH) groups.28 At low pH, the number of available –OH groups decreased due to the hydrogen bonds interaction between chitosan and pullulan molecules, and the diffusion of water vapor was impeded. Insaward et al. also reported that the increase in the number of intermolecular bonds resulted in a polymeric network with decreasing free volume, and water vapor permeated through the film matrix at a reduced rate.29 The more highly structured matrix of the film also improved the oxygen barrier properties and reduced the PV value at lower pH.
Table 2 Effect of pH on water vapor and oxygen permeability of the Pul–Chi filmsa
Films with different pH |
WVP (g mm m−2 h−1 kPa−1) |
WVTR (g m−2 h−1) |
PV (meq kg−1) |
Values are given as mean ± standard deviation. Different letters in the same column indicate significantly different (p < 0.05). |
pH = 5.0 |
1.04 ± 0.02A |
30.06 ± 0.58A |
106.67 ± 2.81A |
pH = 4.5 |
0.93 ± 0.07B |
23.78 ± 1.67B |
94.42 ± 1.57B |
pH = 4.0 |
0.41 ± 0.01D |
18.79 ± 1.32C |
88.24 ± 0.13C |
pH = 3.5 |
0.45 ± 0.01C |
19.93 ± 0.68C |
87.87 ± 0.13C |
pH = 3.0 |
0.42 ± 0.03CD |
18.32 ± 1.00C |
87.13 ± 2.37C |
FTIR analysis
FTIR has been used to study intermolecular interactions between chitosan and starch.26 The effect of pH on the FTIR of the Pul–Chi films is shown in Fig. 4. The peak at 1150 cm−1 corresponded to the stretching of the (1 → 4) glycosidic bond and the bands from 1022 to 1152 cm−1 were due to the stretching of C–O bonds. The N–H bending (amide II) of chitosan was observed at about 1550 cm−1 at pH 5.0. The decrease of pH from 5.0 to 4.0 resulted in a shift of the N–H (amide II) peak to higher wave numbers (pH 4.5: 1558.5, pH 4: 1559.4 cm−1, pH 3.5: 1556.2 cm−1). At lower pHs, the extension of the chitosan polymer increased exposure of the amino groups, enhancing hydrogen bonds interactions with pullulan. The hydrogen bonds which require more energy for the N–H bend were shifted to higher wave numbers. The shift of the NH bend has been reported by Mathew who showed that characteristic peaks of starch and the amide peaks of chitosan shifted to a higher wave number, indicating the interaction between the NH3 of the chitosan and hydroxyl groups of starch.26 However, when the pH was further decreased from 4.0 to 3.0, the peak of N–H (amide II) was shifted to lower wave numbers (pH 3: 1531.2 cm−1). This is probably due to shielding of the positively charged (–NH3+) by the counter ions (–Cl−) from hydrochloric acid. The shielding of the positive charges may also result in more coil conformation, leading to less interaction with pullulan and more void in the film matrix. Possible mechanism for pH dependence of chitosan–pullulan interactions is shown in Fig. 5. The changes in N–H bending model supported the results of previously described mechanical and physical properties. Additionally, the peaks at 1550 cm−1 and 1409 cm−1 were relatively sharp at pH 4.5 and 5.0 (Fig. 4). This was probably due to the sharp characteristic peaks of sodium acetate when adjusting pH using sodium hydroxide. The sodium acetate was uniformly dispersed within the film matrix, which did not affect the peaks of pullulan and chitosan especially at lower pH values.
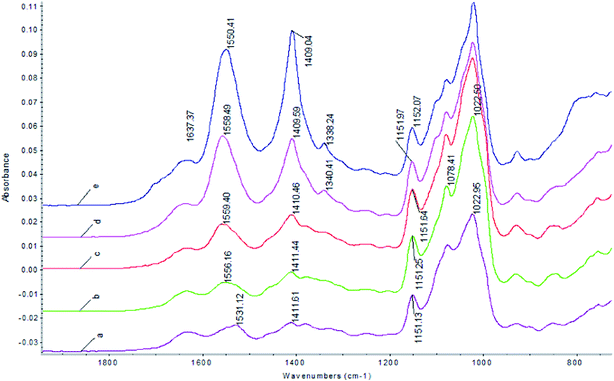 |
| Fig. 4 Effect of pH on the FTIR of the Pul–Chi films: (a) pH = 3.0, (b) pH = 3.5, (c) pH = 4.0, (d) pH = 4.5, (e) pH = 5.0. | |
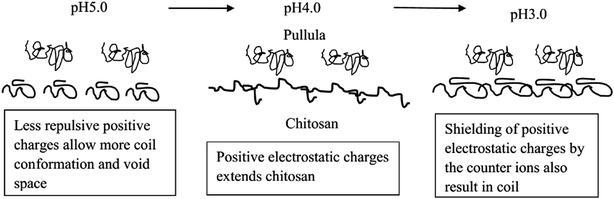 |
| Fig. 5 Possible mechanism for pH dependence of chitosan–pullulan interactions. | |
XRD analysis
In our previous study, the X-ray diffraction pattern of films containing only chitosan or pullulan was determined.11 It showed that chitosan films had three peaks between 2θ = 7–20° corresponding to the hydrated crystalline structure and a broad peak around 2θ = 23°, representing an amorphous structure. Pullulan films had a broad peak around 2θ = 13.4°, indicating an amorphous structure. The three crystal peaks observed in chitosan films could not be found in the films composed of the mixture of chitosan and pullulan at any pH (Fig. 6). Strong interactions between chitosan and pullulan might have prevented the close packing of the chitosan molecules necessary for the formation of regular crystallites. Two broad peaks were observed at 2θ = 12.5° and 23° for pullulan and chitosan, respectively in the Pul–Chi film at pH 4.5. Only a weak broad peak was found as the pH decreased to 4, 3.5 and 3. Intra-molecular hydrogen bonds of chitosan was relatively strong at pH 4.5, so the peak around 2θ = 23° for chitosan still persisted in the X-ray diffractogram of the Pul–Chi film. The sharp peak at 2θ = 17 at pH 5.0 is due to the crystallite of sodium acetate.
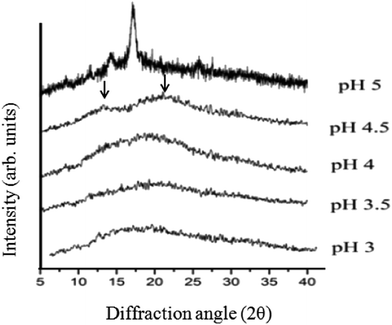 |
| Fig. 6 Effect of pH on the XRD pattern of the Pul–Chi films. | |
Conclusions
The physical properties of the films formed from pullulan–chitosan blended solutions at different pH showed to depend mainly on the conformation of chitosan molecules. With the pH decreasing from 5.0 to 4.0, electrostatic repulsive forces between protonated amine groups of chitosan led to a conformational change from compact coil to extended conformation. More intermolecular hydrogen bonds were possible to form between chitosan and pullulan in the extended conformation at pH 4.0, resulting in an observed higher tensile strength and barrier properties of the film and higher viscosity of the film-forming solution. Water content, thickness and E% all decreased gradually as the pH decreased. As pH further decreased to 3.0, shielding of the protonated amine groups caused some loss of extended structure. The Pul–Chi films with different physical properties can be obtained by controlling the pH value of the film-forming solutions. During the drying process the possible influence of gradual volatilization of HCl on the blending of pullulan and chitosan will be studied in our future work.
Acknowledgements
This work was financially supported by National 125 Program 2013AA1022207; NSFC 31171686; the Natural Science Foundation of Jiangsu Province 2012556; 111 Project B07029 and PCSIRT0627.
References
- I. Arvanitoyannis and C. G. Biliaderis, Food Chem., 1998, 62, 333–342 CrossRef CAS.
- F. Liu, J. Antoniou, Y. Li, J. Yi, W. Yokoyama, J. Ma and F. Zhong, J. Agric. Food Chem., 2015, 63, 3987–3995 CrossRef CAS PubMed.
- F. Debeaufort, J.-A. Quezada-Gallo and A. Voilley, Crit. Rev. Food Sci. Nutr., 1998, 38, 299–313 CrossRef CAS.
- P. Guerrero, M. G. O'Sullivan, J. P. Kerry and K. Caba, RSC Adv., 2015, 5, 8182–8189 RSC.
- M. Heike, G. Stéphane, P. Patrick and C. Véronique, J. Agric. Food Chem., 2004, 52, 6585–6591 CrossRef PubMed.
- H. Zhao, S. Zhang, Q. Li, Y. Li, B. Liu, F. Besenbacher and M. Dong, RSC Adv., 2012, 2, 2732–2735 RSC.
- M. A. Garcia, A. Pinotti and N. E. Zaritzky, Starch-Staerke, 2006, 58, 453–463 CrossRef CAS.
- T. D. Leathers, Appl. Microbiol. Biotechnol., 2003, 62, 468–473 CrossRef CAS PubMed.
- A. Lazaridou, C. G. Biliaderis and V. Kontogiorgos, Carbohydr. Polym., 2003, 52, 151–166 CrossRef CAS.
- C. Biliaderis, A. Lazaridou and I. Arvanitoyannis, Carbohydr. Polym., 1999, 40, 29–47 CrossRef CAS.
- E. Kristo, C. G. Biliaderis and A. Zampraka, Food Chem., 2007, 101, 753–764 CrossRef CAS.
- M. E. Gounga, S. Y. Xu and Z. Wang, J. Food Eng., 2007, 83, 521–530 CrossRef CAS.
- Q. Tong, Q. Xiao and L.-T. Lim, Food Res. Int., 2008, 41, 1007–1014 CrossRef CAS.
- A. Lazaridou and C. G. Biliaderis, Carbohydr. Polym., 2002, 48, 179–190 CrossRef CAS.
- J. Wu, F. Zhong, Y. Li, C. Shoemaker and W. Xia, Food Hydrocolloids, 2013, 30, 82–91 CrossRef CAS.
- S. Y. Park, K. S. Marsh and J. W. Rhim, J. Food Sci., 2002, 67, 194–197 CrossRef CAS.
- C. A. Kienzle-Sterzer, D. Rodriguez-Sanchez and C. Rha, Die Makromolekulare Chemie, 1982, 183, 1353–1359 CrossRef CAS.
- K. M. Kim, J. H. Son, S. K. Kim, C. L. Weller and M. A. Hanna, J. Food Sci., 2006, 71, E119–E124 CrossRef CAS.
- Y. Zhong, X. Song and Y. Li, Carbohydr. Polym., 2011, 84, 335–342 CrossRef CAS.
- AACC, Approved methods of the AACC, American Association of Cereal Chemists, St Paul, MN, 2000 Search PubMed.
- ASTM, Annual book of ASTM standards, American Society for Testing and Materials, Philadelphia, PA, 1989 Search PubMed.
- A. Gennadios, C. L. Weller and C. H. Gooding, J. Food Eng., 1994, 21, 395–409 CrossRef.
- T. H. McHugh, R. Avena-Bustillos and J. Krochta, J. Food Sci., 1993, 58, 899–903 CrossRef CAS.
- S. Ou, Y. Wang, S. Tang, C. Huang and M. G. Jackson, J. Food Eng., 2005, 70, 205–210 CrossRef.
- D. Peressini, B. Bravin, R. Lapasin, C. Rizzotti and A. Sensidoni, J. Food Eng., 2003, 1, 25–32 CrossRef.
- S. Mathew, M. Brahmakumar and T. E. Abraham, Biopolymers, 2006, 82, 176–187 CrossRef CAS.
- F. Liu, J. Antoniou, Y. Li, J. Ma and F. Zhong, Food Hydrocolloids, 2015, 45, 140–149 CrossRef CAS.
- L. Cheng, A. Abd Karim, M. Norziah and C. Seow, Food Res. Int., 2002, 35, 829–836 CrossRef CAS.
- A. Insaward, K. Duangmal and T. Mahawanich, J. Agric. Food Chem., 2015, 63, 9421–9426 CrossRef CAS PubMed.
|
This journal is © The Royal Society of Chemistry 2015 |
Click here to see how this site uses Cookies. View our privacy policy here.