DOI:
10.1039/C4RA13329C
(Paper)
RSC Adv., 2015,
5, 12248-12256
Fabrication of MnOx heterogeneous catalysts from wet sludge for degradation of azo dyes by activated peroxymonosulfate†
Received
28th October 2014
, Accepted 15th January 2015
First published on 15th January 2015
Abstract
For dewatering and resource utilization of sewage sludge, catalyst preparation paralleled with sewage sludge dewatering, was explored. In order to obtain a better understanding of this strategy, an anaerobic sludge based MnOx catalyst (MnOx/HCAS) was characterized, and tested in activation of Oxone for dye degradation in aqueous solution. The multi-valence oxidation states of manganese were formed in MnOx/HCAS. The catalyst exhibits high catalytic activity towards Oxone for the degradation of dyes in aqueous solution. The kinetic data followed first order kinetics with an activation energy of 21.87 kJ mol−1. The evaluation of the reusability of MnOx/HCAS showed that MnOx/HCAS exhibited high stability in recycled tests without losing its activity. The removal of a variety of anionic dyes also demonstrates an excellent catalytic performance of MnOx/HCAS. To investigate stabilization of heavy metals in the catalyst, a leaching test was conducted, and the result showed that heavy metals can be solidified to prevent their leaching into solution. The effect of different kinds of wet sludge was investigated. And all these sludge based MnOx catalysts exhibit good catalytic performance with azo dyes with degradation rates more than 98%, which decides its unquestionable possibility for fabrication of MnOx heterogeneous catalysts from wet sludge and its practical applications.
1. Introduction
Currently wastewater treatment sludge (WWTS) is among the waste biomass produced in abundant quantity with high water content (up to about 98 wt%),1 making the disposal of WWTS a pressing environmental problem. The traditional disposal alternatives for sewage sludge include landfill, composting, land application following aerobic and anaerobic digestion, and incineration, none of which are exempt from the risk of contaminating the environment, and threatening human health.2–4 The associated regulations are also becoming stricter.5,6 Converting waste into useful products can alleviate the disposal problems and offer a new reserve for depleting resources.7–10 As an alternative, hydrothermal treatment technology (HTT) was developed to harness energy from wet sewage sludge to avoid high-energy costs prior to drying. In previous studies on HTT of wet sewage sludge, hydrothermal liquefaction (HTL) was applied for the production of crude bio-oil at elevated temperature (250–380 °C) and pressure (10–25 MPa),11 as well as the production of hydrogen (H2) and methane (CH4) through hydrothermal gasification.12 However, high reaction temperature means high cost and will bring severe operational issues such as corrosion and scaling.13 Thus, the interests of recent studies have focused on hydrothermal carbonization (HTC). An important technique for the production of various carbonaceous materials and hybrids, usually applied at mild temperatures (≤200 °C), and in pure water inside closed recipients and under self generated pressure. There is no drying in HTC because water serves as the reaction medium. Therefore, wet sludge is suitable for HTC. Furthermore, there are some other advantages in HTC: (1) the reaction temperature of HTC is usually much lower than other carbonization methods, such as pyrolysis or hydrothermal gasification and (2) HTC can reduce greenhouse gas emission, as only a small amount of gas, particularly CO2, is generated.14
In the meantime, it should be noticed that hydrothermal method also has been applied for the preparation of many catalysts with excellent catalytic activities. For example, Yao et al. proposed a facile approach for preparing Co3O4-reduced graphene oxide via hydrothermal synthesis under basic conditions and applied it for the decomposition of phenol.15 However, Co2+ is highly toxic and can cause some health problems. Thus, attempts to use less toxic Mn oxides have been reported recently. MnO2 is also widely used in heterogeneous catalysis due to its physical and chemical properties.16–18 Capitalizing this fact, we conjectured that it might be possible to develop a strategy that integrates wet sludge treatment with catalyst preparation by hydrothermal carbonization. To the best of our knowledge, no such work has been reported before. Since sewage sludge is a complex mixture of various components containing carbohydrates, humic substances, heavy metals and so on. Therefore, in order to obtain a better understanding of this strategy, the following questions need be answered: (1) it is not clear whether the combination of wet sludge treatment and catalyst preparation by hydrothermal process is feasible; (2) how about the efficiency and stability of such prepared catalysts and (3) can we stabilize and solidify these toxic heavy metals in catalysts in order to prevent their leaching?
To decipher the puzzle, we synthesized an effective MnOx heterogeneous catalyst from wet sludge via hydrothermal carbonization under mild conditions (120 °C or 200 °C) and the prepared catalysts were used for the catalytic degradation of azo dyes by activated peroxymonosulfate (Oxone). As we know, wastewater discharged from dyeing processes is one of the biggest contributors to textile effluent; this comprises mainly residual dyes and auxiliary chemicals.19,20 Among these dyes, azo dyes represent the largest class of dyes.21,22 In the meantime, sulfate radicals initiators such as Oxone have been explored due to their high oxidation power.23
2. Materials and methods
2.1. Materials
MnSO4·H2O and (NH4)2S2O8 were obtained from National Medicines Co., Ltd, Shanghai, China. Peroxymonosulfate (Oxone, 2KHSO5·KHSO4·K2SO4) was purchased from Sigma-Aldrich. C. I. Acid Red 73 (AR 73) and other dyes were obtained from Gracia Chemical Technology Co., Ltd. (Chengdu, China). The purities of dyes were over 99.5% (chemical structures are shown in Fig. S1 in ESI†). The anaerobic sludge (AS) was obtained from the Qi-ge wastewater treatment plant, Hangzhou, China (the physicochemical characteristics of anaerobic sludge are presented in Table S1 in ESI†). Other types of sludge from different wastewater treatment plant, including primary, secondary and digested sewage, were chosen in this study. The high-purity water used in this study was produced using a UPK/UPT ultrapure water system. Other chemical reagents were of analytical grade and used without any further purification.
2.2. Fabrication of MnOx heterogeneous catalyst from wet sludge
The MnOx/HCAS catalyst was prepared by one-pot hydrothermal synthesis in a laboratory-scale stainless-steel autoclave (GSH-0.5 L, Shandong, China) equipped with an electric stirrer (Fig. S2†). The stainless-steel container was filled with a volume of 0.2 L anaerobic sludge (water content: 80.01%), subsequently, 0.020 M MnSO4·H2O was added progressively to the reactor with vigorous stirring at room temperature to obtain a well-mixed solution, and left to stand for 12 h. Then, 0.024 M (NH4)2S2O8 was placed into the autoclave with stirring and maintained at 120 °C and 200 °C for 12 h, which were regulated by a programmable controller. The target temperature and the reaction duration were set in the control panel. The resulting product was centrifuged, decanted, washed with deionized water and dried at 80 °C in air. In addition, other types of sludge based MnOx catalysts were prepared under the same conditions stated above.
To investigate the combine effect of sludge treatment and catalyst preparations, two possible approaches were examined. The first involved adding separate anaerobic sludge and MnSO4·H2O into the stainless-steel container simultaneously, then treating them for 12 h at 120 °C and 200 °C, respectively (MnOx/HCAS-120 and MnOx/HCAS-200). And the second involved pretreating anaerobic sludge by HTC process at 200 °C for 12 h and then adding MnSO4·H2O, finally treating them by HTC process at 120 °C for 12 h (MnOx/HCAS-200-120). Also two control experiments as mentioned above, HCAS-120 and HCAS-200 were conducted. The degradation studies (pH 7) were carried out in order to optimize the suitable preparation conditions for maximum catalytic activity, and the results were given in Table S2.† It can be seen that the adsorption experiments indicated that MnOx/HCAS or HCAS materials had less adsorption for AR 73 (<3%). In method 1, the degradation rate of AR 73 by MnOx/HCAS-120 with Oxone was 98.3% after 30 min, much higher than the MnOx/HCAS-200 catalyst (10.2%). Also, in method 2, the MnOx/HCAS-200-120 showed high degradation of AR 73 (98% after 30 min). These results suggested that the temperature of catalyst preparation is more important than the support for combination of sludge treatment and MnOx catalyst. To obtain a high catalytic activity of the catalyst, low preparation temperature should be controlled since low preparation temperature means low energy consumption. Therefore, the combination of sewage sludge treatment with catalyst preparation is feasible. In comparison with MnOx/HCAS-200-120, the preparation process of MnOx/HCAS-120 was more convenient. Thus, MnOx/HCAS-120 was chosen as the optimal catalyst in this study.
The MnOx/HCAS was characterized by X-ray diffraction (XRD), scanning electron microscopy (SEM), X-ray absorption near-edge spectroscopy (XANES) and Soft X-ray scanning transmission X-ray microscopy (STXM). The details are described in Text S1 in ESI.† Nitrogen adsorption and desorption isotherms at 77 K were measured using NOVA2000e surface area & pore size analyzer (Quantachrome, USA). The specific surface area was calculated by Brunauer–Emmet–Teller (BET) equation.
2.3. Experimental procedures and analysis
To evaluate the activity of catalytic oxidation of dye, batch experiments were carried out in 250 mL conical flasks at 25 °C with constant stirring at 150 rpm. A desired amount of Oxone was added to the dye solution (100 mL). Solution pH was adjusted by H2SO4 or NaOH. Then the reaction was initiated once the catalyst was added. At predetermined time internals, aqueous phase samples (2.5 mL) were withdrawn and immediately filtered (0.22 μm) to remove the catalyst solids. Subsequently, the concentrations of remnant dye were analyzed using a Shimadzu UV-2401PC UV-vis spectrometer (Tokyo, Japan) at its absorbance maximum.
The mineralization of dye solution was determined by measuring the decrease of chemical oxygen demand (COD) of the supernatant solution. The supernatant solution was refluxed with potassium dichromate in the presence of silver and mercury sulfate at 100 °C for 2 h. The refluxed solution was then titrated with ferrous ammonium sulfate (FAS) using ferroin as an indicator. Similar conditions were used for the blank sample (distilled water). COD was calculated by using the formula: COD (mg L−1) = (A − B) × N × 8 × 1000/C, where A is the volume of FAS required for the blank (mL), B is the volume of FAS required for the effluent sample (mL), N is the normality of FAS, and 8 is the milliequivalent weight of oxygen and C is the volume of supernatant solution or distilled water (mL).
For the stability test of the catalyst, the used catalyst was collected by centrifugation, washed with deionized water and dried at 80 °C in air. Catalyst dose and other reaction conditions remained the same for the subsequent runs. Furthermore, inductively coupled plasma mass spectrometry (ICP-MS) elemental analysis was performed in the present study. The leaching test was conducted with 50 mg L−1 of dye solution prepared at a liquid–solid ratio of 100 mL/0.1 g (pH 7.0 ± 0.2) and stirred at 150 rpm for 30 min. After centrifugation, the supernatant solution was analyzed using flow injection coupled with ICP-MS (ELAN DRC-e ICP-MS from Perkin-Elmer company). The total contents of heavy metals in MnOx/HCAS catalyst before and after reaction were extracted by acid digestion (using HNO3/HClO4/HF) and then were examined by ICP-MS.
3. Results and discussion
3.1. Characterization of catalyst
The chemical property of AS, HCAS-120, and HCAS-200 was studied. The changes in the major elemental composition (C, H, O and N) of AS, HCAS-120 and HCAS-200 were quantified and the results were listed in Table 1. It can be seen that the C content decreased with the increasing reaction temperature as a result of oxygenating reactions (AS: 14.75%, HCAS-120: 13.56%, and HCAS-200: 9.02%), which were particularly evident at 200 °C. This is because the polysaccharide decomposed into CO2 and water at the temperature above 180 °C.24 At the same time, H and O contents also decreased due to dehydration and decarboxylation reactions during HTC processes. Besides, H/C and O/C ratios declined with the rise of the temperature, indicating an increasing degree of carbonization of AS.
Table 1 Chemical compositions of AS and HCASa
Samples |
Ultimate analysis (wt%) |
Molar ratio |
C |
H |
O |
N |
H/C |
O/C |
HCAS-120: the anaerobic sludge (AS) was treated by hydrothermal method at 120 °C; HCAS-200: the anaerobic sludge (AS) was treated by hydrothermal method at 200 °C. |
AS |
14.75 |
3.27 |
13.34 |
2.13 |
2.66 |
0.68 |
HCAS-120 |
13.56 |
2.86 |
11.41 |
1.62 |
2.53 |
0.63 |
HCAS-200 |
9.02 |
1.90 |
7.18 |
0.59 |
2.52 |
0.60 |
The prepared samples were first characterized by XRD to identify its crystallographic structure. The XRD patterns of HCAS (a), pure MnO2 (b) and MnOx/HCAS (c) are shown in Fig. S3.† The XRD pattern of HCAS reveals the presence of important amount of quartz, and the peak at 2θ = 26.3° can be attributed to the diffraction of the (002) plane of the disordered carbon structure, due to the carbonization of anaerobic sludge. The characteristic peaks of carbon structure were also observed in the XRD pattern of MnOx/HCAS. Additionally, no significant signals corresponding to pure MnO2 phase (JCPDS no. 72-1982)25 in the XRD pattern of MnOx/HCAS were observed. This may be attributed to the small MnO2 crystalline size or the presence of an amorphous MnO2 phase deposited onto the HCAS, as previously reported.26–28 According to the results of BET surface area, HCAS presented the highest BET surface area (55.469 m2 g−1), whereas MnOx/HCAS presented the lowest surface area (37.402 m2 g−1). The BET surface area of MnOx/HCAS decreased because of the in situ synthesis of MnOx nano-particles into the HCAS.
The morphology and structure of HCAS and MnOx/HCAS were further examined with SEM. As shown in Fig. 1a and b, the HCAS particles were irregular and in a relatively agglomerated state in the range of micrometers. This may be caused by extracellular polymeric substances (EPS), which exists in flocs and cellular tissues of anaerobic sludge.29 When simultaneous wet sludge treatment and MnOx catalyst preparation were conducted, it can be observed that the shape of the MnOx/HCAS particles (Fig. 1c and d) is also irregular, but the agglomeration is relieved, because the in situ synthesis of MnOx onto HCAS, to some extent may hinder EPS agglomeration into larger particles by binding onto HCAS.
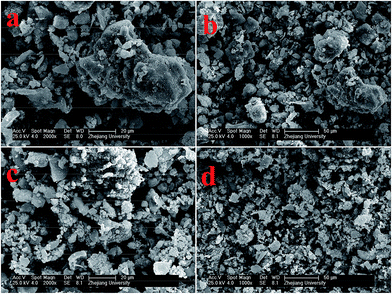 |
| Fig. 1 (a and b) SEM images of HCAS (anaerobic sludge treated by hydrothermal method). (c and d) SEM images of MnOx/HCAS (MnOx-loaded HCAS through hydrothermal process). | |
In addition, the valence state of manganese in MnOx/HCAS catalyst was determined from XANES. Fig. 2 shows the normalized Mn K-edge XANES spectra of the MnOx/HCAS sample with a series of reference compounds such as pure Mn metal, MnO, Mn3O4, Mn2O3 and MnO2. It can be observed that the position of manganese absorption edge shifts with the increase of the oxidation state of Mn atoms. For MnOx/HCAS catalyst, the Mn K-edge XANES data exhibit edge shifts in the region between the Mn K-edges of Mn2O3 and MnO2 reference compounds, indicating that the average oxidation states of manganese in MnOx/HCAS sample must be between 3+ and 4+.30
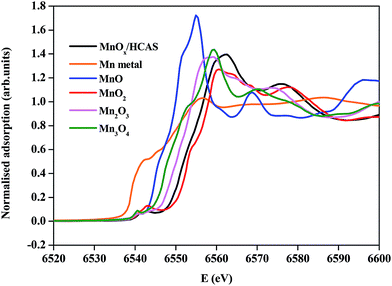 |
| Fig. 2 Normalized Mn K-edge XANES data of MnOx/HCAS sample and Mn reference samples (Mn metal, MnO, Mn3O4, Mn2O3 and MnO2). | |
3.2. Catalytic performance
The experiments were performed in different processes to investigate the degradation efficiency of AR 73, including Oxone alone, MnOx/Oxone, and MnOx/HCAS/Oxone. Also the control experiments were investigated to determine the adsorption abilities of MnOx, MnOx/HCAS and HCAS. As shown in Fig. 3, for Oxone alone, dye degradation showed a minor change and was less than 8% after 30 min, suggesting that Oxone itself fails to induce oxidation degradation of the dye. In the absence of Oxone, the catalysts MnOx, MnOx/HCAS and HCAS also presented low adsorption efficiencies with only 2–6% removal. However, with the co-existence of Oxone and MnOx or MnOx/HCAS, AR 73 concentration decreased significantly and the degradation rate reached over 98%. However, nano-MnOx is very difficult to be separated from water, and this becomes the major limitation for the application of nano-materials in the field of wastewater treatment. In addition, other anionic dyes were also effectively degraded by MnOx/HCAS/Oxone (Table 2). The catalytic oxidation of dyes would be due to the synergistic effect of MnOx/HCAS and Oxone. MnOx/HCAS can induce the decomposition of Oxone and produce sulfate radicals as shown in the following equations. |
HSO5− + MnO2/HCAS → SO5−˙ + OH− + Mn2O3/HCAS
| (1) |
|
HSO5− + Mn2O3/HCAS → SO4−˙ + H+ + MnO2/HCAS
| (2) |
|
SO4−˙ + H2O → HO˙ + H+ + SO42−
| (3) |
|
 | (4) |
 |
| Fig. 3 Degradation efficiency of AR 73 (Initial concentration 50 mg L−1, 100 mL, T = 25 °C, pH 7.0 ± 0.2, samples dosage 0.1 g, Oxone dosage 1.0 g L−1). | |
Table 2 Degradation efficiency of common anionic dyesa
Dyes |
Degradation rate (%) |
Pictures of experiment |
The initial concentration 50 mg L−1, 10 mL, T = 25 °C, pH 7.0 ± 0.2, MnOx/HCAS catalyst dosage 0.01 g, Oxone dosage 1.0 g L−1. |
AR1 |
98.5 |
Control |
AB25 |
96.9 |
 |
AB40 |
96.2 |
AB62 |
99.9 |
AB113 |
96.5 |
MnOx/HCAS |
AB193 |
97.7 |
 |
RB74 |
97.4 |
RR11 |
95.4 |
RR24 |
95.2 |
|
To identify the dominating radical species in MnOx/HCAS/Oxone system, quenching studies were performed. SO5−˙ radical would not contribute to dye degradation because of its lower redox potential. Therefore, Methanol (MeOH) and tert-butyl alcohol (TBA) were selected as quenching agents since MeOH is widely used as the scavenger of SO4−˙ and HO˙ while TBA is the effective quenching agent for HO˙.31 In the absence of quenching agents, dye degradation was very fast and reached 98% in 30 min. However, as shown in Fig. S4,† MeOH and TBA indeed inhibited the dye degradation. It can be seen that the degradation rates were 42% and 78% in the presence of MeOH (0.3 mol L−1) and TBA (0.3 mol L−1) in 30 min, respectively. In comparison to the decrease in dye degradation rate in the presence of TBA, relatively significant decrease in the presence of MeOH indicated that SO4−˙ as radical species were predominantly produced during the decomposition of Oxone by MnOx/HCAS. The results justified the involvements of both SO4−˙ and HO˙ radical mechanism in the MnOx/HCAS/Oxone system.
3.3. Effects of inorganic salts and reaction temperature
In general, a great amount of inorganic salts are employed in various dyeing processes and the strength of dissolved inorganic ions in dyestuff wastewater may affect the efficiency of dye degradation reaction.32 However, there is usually a large salinity range.33,34 In this study, the influences of two common inorganic salts at the range of 1–150 mg L−1 (NaCl and NaHCO3) on the catalytic degradation of dye solutions were assessed and the experimental results are presented in Fig. 4a and b, respectively. It can be obviously seen that NaCl had a positive effect on dye degradation and the progressive increase in degradation was identified with the increasing concentration of NaCl solution from 1 to 150 mg L−1 by comparing with control (without inorganic salts). Wang et al. reported a xanthene dye Rhodamine B degradation in Fe(II)/Oxone system and found that in the presence of Cl− can significantly improve dye degradation,35 which is similar to the observation in this study. It is known that Cl− can be oxidized by SO4−˙ to form chlorine radicals, which may result in a series of secondary oxidants, such as Cl˙, Cl2−˙ and HOCl. These secondary oxidants were likely to enhance the dye degradation, involving the reaction of chlorine radicals and free available chlorine species. However, for MnOx/HCAS/Oxone system at a lower concentration (1 mg L−1), the NaHCO3 showed a negligible effect on dye degradation. But above 1 mg L−1, NaHCO3 showed negative influences on dye degradation (Fig. 4b). The degradation rate of AR 73 gradually decreased from 91% to 72% after 30 min, as the dosage of NaHCO3 increased from 10 to 150 mg L−1. One possible explanation was that the NaHCO3 would mostly act as HO˙ and SO4−˙ scavengers at high concentrations (>10 mg L−1) and therefore inhibit dye degradation.36
 |
| Fig. 4 (a and b) Effect of inorganic salts on AR 73 degradation (initial concentration 50 mg L−1, 100 mL, T = 25 °C, pH 7.0 ± 0.2, MnOx/HCAS catalyst dosage 0.1 g, Oxone dosage 1.0 g L−1). (c) Effect of reaction temperature on AR 73 degradation (initial concentration 50 mg L−1, 100 mL, pH 7.0 ± 0.2, MnOx/HCAS catalyst dosage 0.1, Oxone dosage 1.0 g L−1 g−1). | |
The effect of temperature (15, 25, 35 and 45 °C) on dye degradation was also investigated. It can be seen from Fig. 4c that increasing temperature had a positive effect on AR 73 degradation for the MnOx/HCAS catalyst. The results showed that increasing the reaction temperature from 15 to 45 °C enhanced the AR 73 degradation efficiency from 64 to 94% in 15 min. This is due to the fast Oxone decomposition at high temperatures, which in turn generates more active radicals than that at low temperatures. Based on the first order kinetics, the reaction rate constants were determined and the dependence of rate constants on the temperature obeyed the Arrhenius relationship with R2 = 0.9968 as shown in the inset of Fig. 4c. The activation energy (Ea) for the degradation process was calculated to be 21.87 kJ mol−1. For Oxone activation by heterogeneous MnOx/HCAS catalyst in dye degradation, few investigations have been reported on the kinetics and activation energies. However, previous investigations showed that the activation energy of reactions on different heterogeneous catalysts is between 49.01–69.23 kJ mol−1, such as 49.01 kJ mol−1 on CoxFe3−xO4–Rhodamine B, 49.50 kJ mol−1 on Co–graphene hybrid-Orange II and 69.23 kJ mol−1 on porous Fe2O3–Rhodamine B.37–39 Even though it is unlikely for a comparison of the catalytic activity among various heterogeneous catalysts because of the difference in experimental conditions, the results suggest that MnOx/HCAS catalyst will be a promising catalytic material for oxidation processes.
3.4. Stability of MnOx/HCAS
In general, the most important aspect for catalyst is its efficiency and stability.40 Owing to the high activity of MnOx/HCAS catalyst in activation of Oxone for the generation of active radicals and the subsequent degradation of AR 73, it is essential to evaluate the reusability of the spent catalyst. As shown in Fig. 5a, MnOx/HCAS catalyst showed high catalytic performance during five recycling runs, with dye degradation efficiencies more than 98% and COD removal efficiencies varied from 43.5% to 45.0%.
 |
| Fig. 5 (a) Degradation of AR 73 in the recycle experiment (initial concentration 50 mg L−1, 100 mL, T = 25 °C, pH 7.0 ± 0.2, MnOx/HCAS catalyst dosage 0.1 g, Oxone dosage 1.0 g L−1). (b) Concentrations of heavy metals in MnOx/HCAS catalyst before and after reaction, as well as leaching in the remnant solution. | |
In addition, because of the physical–chemical processes that are involved in activated wastewater sludge treatment, sludge tends to accumulate heavy metals existing in the wastewater. Stabilization and solidification of heavy metals in catalysts must be considered to prevent heavy metals leaching into solution during wastewater treatment. To investigate whether it is safe to use HCAS as support for MnOx, ICP-MS elemental analysis was performed. It can be seen from Fig. 5b that the concentration of heavy metals from the supernatant solution after reaction was very low, except for Zn and Cu. The leaching concentration of both Zn and Cu in supernatant solution was 0.014 mg L−1, which is far less than the limits reported in drinking water by US Environmental Protection Agency.41 Besides, there is no dramatic change for the contents of the heavy metals in MnOx/HCAS catalyst after the reaction. To further investigate the stability of heavy metals in catalysts, based on a dual-energy ratio-contrast image method, the spatial distributions of above mentioned heavy metals, except Pb (Pb was not allowed to be determined), Cd and Co (the contents were too low), were depicted with soft X-ray scanning transmission X-ray microscopy (STXM) images at different energies (detailed procedure is presented in the ESI Text S1 and NEXAFS spectra of Fe, Ni, Zn, Cu and Cr reference at the L-edge are shown in the ESI Fig. S5†). Fig. 6 shows the STXM analysis of element distribution of Fe, Ni, Zn, Cu and Cr in the MnOx/HCAS catalyst before reaction and after five recycling runs. The distributions of these heavy metals were basically unchanged though the MnOx/HCAS catalyst was reused up to 5 cycles. It is, therefore, concluded from the above results that heavy metals can be solidified in the MnOx/HCAS catalyst, which pose no harmful impact on the environment.
 |
| Fig. 6 STXM analysis of dual-energy element distribution of heavy metals in the MnOx/HCAS catalyst before reaction and after five recycling runs. | |
3.5. Effect of different kinds of wet sludge
Sludge, originating from the treatment process of waste water, is the residue generated during the primary (physical and/or chemical), secondary (biological) and the tertiary (additional to secondary, often nutrient removal) treatment. There are three main categories of sludge: (1) sludge originating from the treatment of urban waste water, consisting of domestic waste water or in a mixture with industrial waste water and run-off from rain water, (2) sludge originating from the treatment of industrial waste water, and (3) sludge from drinking water treatment. The complicated structures of sludge may affect the preparation and performance of the catalysts. Therefore, in order to investigate the effect of different kinds of wet sludge on the catalyst preparation, aerobic and anaerobic sludge from different wastewater treatment plants, including primary, secondary and digested sewage, were chosen as catalyst supports in this study. As shown in Fig. 7, all these sludge-based MnOx catalysts exhibit excellent catalytic performances to azo dyes with degradation efficiencies more than 98% after 30 minutes of contact. Without adding Oxone, all these sludge-based MnOx catalysts have low adsorption efficiencies with less than 30% removal, which also decided the possibility of practical applications for fabrication of MnOx heterogeneous catalyst from wet sludge.
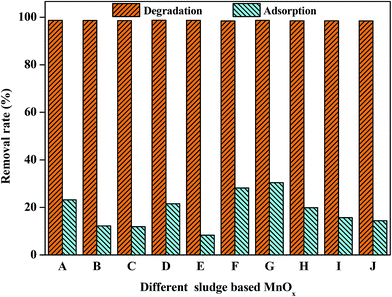 |
| Fig. 7 Degradation and adsorption of AR 73 by different sludge based MnOx (initial concentration 50 mg L−1, 10 mL, T = 25 °C, pH 7.0 ± 0.2, Oxone dosage 1.0 g L−1, catalysts dosage 0.01 g, A: anaerobic sludge obtained from brewery; B: anaerobic sludge obtained from paper mill; C: aerobic sludge obtained from secondary treatment for urban waste water; D: anaerobic sludge obtained from pig farm; E: anaerobic sludge obtained from chemical factory; F: anaerobic sludge obtained from primary treatment for dyeing wastewater; G: anaerobic sludge obtained from secondary treatment for dyeing wastewater; H: anaerobic sludge obtained from tertiary treatment for dyeing wastewater; I: aerobic sludge obtained from secondary treatment for dyeing wastewater; J: aerobic sludge obtained from secondary treatment for textile wastewater). | |
3.6. Technical implications
Resource utilization of sewage sludge has recently received considerable attention. However, dewatering is a key bottleneck. Our experimental work confirmed the feasibility of combination of sewage sludge treatment with catalyst preparation and indicated this strategy as an attractive new alternative technology for sewage sludge treatment. It operates under mild conditions without dewatering wet sewage sludge and addition of high energy input (temperature: 120 °C). The HTC reaction products were separated into water-soluble and water-insoluble parts. As well demonstrated in many previous studies on thermo-chemical conversion of biomass, the water-soluble products consist mainly of carbohydrates, acetic acids, aldehydes and pyran derivatives, all of which are oxygen-containing compounds.42,43 However, more attention should be paid on the water-soluble fraction which can be easily separated by decanting. For future studies, the water-soluble organics will be analyzed and utilization of the liquid products will be investigated.
The variety of sewage sludge from different wastewater plants has complex characterization. Organic matter, heavy metals and microstructures in sewage sludge would have a significant impact on its resource utilization. Therefore, further studies are needed to explore the effects of these factors in detail. In addition, as we know, contaminants are harmful to human and environment, especially heavy metal contaminants.44–46 Therefore, although our study suggested heavy metal's stability in sewage sludge, more toxicity test should be addressed in future for risk assessment.
4. Conclusion
A low-cost catalyst material, anaerobic sludge based MnOx catalyst (MnOx/HCAS) was characterized. This catalyst showed high efficiency in activation of Oxone for the generation of active radicals and the subsequent degradation of AR 73. In the meantime, after the MnOx/HCAS catalyst was reused in five runs, AR 73 degradation efficiency can still be more than 98% and COD removal efficiencies varied from 43.5% to 45.0%. Furthermore, heavy metals in the catalyst had been solidified in the MnOx/HCAS catalyst to prevent their leaching into solution and pose no harmful impact on the environment. In addition, different kinds of wet sludge based MnOx catalysts also exhibit excellent catalytic performance to azo dye. Thus, this green, technically feasible, highly efficient and cost effective catalyst is very attractive and implies a potential for practical application for dye wastewater treatment.
Acknowledgements
The authors acknowledge financial support from 863 Research Project (2013AA065202), the Fundamental Research Funds for the Central Universities and Zhejiang University of Technology, Zhejiang, P.R. China “the Opening Foundation of the Environmental Engineering Key Discipline”.
References
- P. Azadi, E. Afif, H. Foroughi, T. S. Dai, F. Azadi and R. Farnood, Appl. Catal., B, 2013, 134–135, 265–273 CrossRef CAS PubMed.
- Y. J. Yao, R. Shen, K. G. Pennell and E. M. Suuberg, Environ. Sci. Technol., 2013, 47, 906–913 CrossRef CAS PubMed.
- L. L. Niu, C. Xu, Y. J. Yao, K. Liu, F. X. Yang, M. L. Tang and W. P. Liu, Environ. Sci. Technol., 2013, 47, 12140–12147 CrossRef CAS PubMed.
- Y. J. Yao, R. Shen, K. G. Pennell and E. M. Suuberg, Environ. Sci. Technol., 2013, 47, 1425–1433 CAS.
- A. Murray, A. Horvath and K. L. Nelson, Environ. Sci. Technol., 2008, 42, 3163–3169 CrossRef CAS.
- J. L. Hong, J. M. Hong, M. Otaki and O. Jolliet, Waste Manage., 2009, 29, 696–703 CrossRef CAS PubMed.
- J. Matos, M. Rosales, A. García, C. Nieto-Delgado and J. R. Rangel-Mendez, Green Chem., 2011, 13, 3431–3439 RSC.
- M. Balakrishnan, V. S. Batra, J. S. J. Hargreaves and I. D. Pulford, Green Chem., 2011, 13, 16–24 RSC.
- R. R. N. Marquesa, F. Stüber, K. M. Smith, A. Fabregat, C. Bengoa, J. Font, A. Fortuny, S. Pullket, G. D. Fowler and N. J. D. Graham, Appl. Catal., B, 2011, 101, 306–316 CrossRef PubMed.
- S. J. Yuan and X. H. Dai, Appl. Catal., B, 2014, 154–155, 252–258 CrossRef CAS PubMed.
- D. R. Vardon, B. K. Sharma, J. Scott, G. Yu, Z. C. Wang, L. Schideman, Y. H. Zhang and T. J. Strathmann, Bioresour. Technol., 2011, 102, 8295–8303 CrossRef CAS PubMed.
- J. A. Onwudili, P. Radhakrishnan and P. T. Williams, Environ. Technol., 2013, 33, 529–537 CrossRef PubMed.
- E. Afif, P. Azadi and R. Farnood, Appl. Catal., B, 2011, 105, 136–143 CrossRef CAS PubMed.
- S. M. Kang, X. L. Li, J. Fan and J. Chang, Ind. Eng. Chem. Res., 2012, 51, 9023–9031 CrossRef CAS.
- Y. J. Yao, Z. H. Yang, H. Q. Sun and S. B. Wang, Ind. Eng. Chem. Res., 2012, 51, 14958–14965 CrossRef CAS.
- S. H. Liang, F. Teng, G. Bulgan, R. L. Zong and Y. F. Zhu, J. Phys. Chem. C, 2008, 112, 5307–5315 CAS.
- L. L. Xu, X. F. Li, J. Q. Ma, Y. Z. Wen and W. P. Liu, Appl. Catal., A, 2014, 485, 91–98 CrossRef CAS PubMed.
- T. T. Truong, Y. Z. Liu, Y. Ren, L. Trahey and Y. G. Sun, ACS Nano, 2012, 6, 8067–8077 CrossRef CAS PubMed.
- Y. Z. Wen, W. Q. Liu, Z. H. Fang and W. P. Liu, J. Environ. Sci., 2005, 17, 766–769 CAS.
- C. S. Shen, Y. Z. Wen, Z. L. Shen, J. Wu and W. P. Liu, J. Hazard. Mater., 2011, 193, 209–215 CrossRef CAS PubMed.
- X. F. Li, X. Liu, L. L. Xu, Y. Z. Wen, J. Q. Ma and Z. C. Wu, Appl. Catal., B, 2015, 165, 79–86 CrossRef CAS PubMed.
- Y. Z. Wen, C. S. Shen, Y. Y. Ni, S. P. Tong and F. Yu, J. Hazard. Mater., 2012, 201–202, 162–169 CrossRef CAS PubMed.
- L. X. Hu, F. Yang, W. C. Lu, Y. Hao and H. Yuan, Appl. Catal., B, 2013, 134–135, 7–18 CrossRef CAS PubMed.
- C. Areeprasert, P. T. Zhao, D. C. Ma, Y. F. Shen and K. Yoshikawa, Energy Fuels, 2014, 28, 1198–1206 CrossRef CAS.
- D. P. Dubal, D. S. Dhawale, R. R. Salunkhe and C. D. Lokhande, J. Electrochem. Soc., 2010, 157, 812–817 CrossRef PubMed.
- H. Chen and J. He, J. Phys. Chem. C, 2008, 112, 17540–17545 CAS.
- C. H. Kuo and C. K. Lee, Carbohydr. Polym., 2009, 77, 41–46 CrossRef CAS PubMed.
- M. L. Chacón-Patiño, C. Blanco-Tirado, J. P. Hinestrozab and M. Y. Combariza, Green Chem., 2013, 15, 2920–2928 RSC.
- G. K. Parshetti, Z. Liu, A. Jain, M. P. Srinivasan and R. Balasubramanian, Fuel, 2013, 111, 201–210 CrossRef CAS PubMed.
- N. N. Tušar, D. Maucec, M. Rangus, I. Arcon, M. Mazaj, M. Cotman, A. Pintar and V. Kaucic, Adv. Funct. Mater., 2012, 22, 820–826 CrossRef.
- Y. H. Guan, J. Ma, Y. M. Ren, Y. L. Liu, J. Y. Xiao, L. Q. Lin and C. Zhang, Water Res., 2013, 47, 5431–5438 CrossRef CAS PubMed.
- C. S. Shen, Y. Shen, Y. Z. Wen, H. Y. Wang and W. P. Liu, Water Res., 2011, 45, 5200–5210 CrossRef CAS PubMed.
- X. R. Xu and X. Z. Li, Sep. Purif. Technol., 2010, 72, 105–111 CrossRef CAS PubMed.
- S. Y. Yang, P. Wang, X. Yang, L. Shan, W. Y. Zhang, X. T. Shao and R. Niu, J. Hazard. Mater., 2010, 179, 552–558 CrossRef CAS PubMed.
- Y. R. Wang and W. Chu, J. Hazard. Mater., 2011, 186, 1455–1461 CrossRef CAS PubMed.
- L. Zhao, Z. Z. Sun, J. Ma and H. L. Liu, J. Mol. Catal. A: Chem., 2010, 322, 26–32 CrossRef CAS PubMed.
- F. Ji, C. L. Li, X. Y. Wei and J. Yu, Chem. Eng. J., 2013, 231, 434–440 CrossRef CAS PubMed.
- S. N. Su, W. L. Guo, Y. Q. Leng, C. L. Yi and Z. M. Ma, J. Hazard. Mater., 2013, 244–245, 736–742 CrossRef CAS PubMed.
- Y. J. Yao, C. Xu, J. C. Qin, F. Y. Wei, M. N. Rao and S. B. Wang, Ind. Eng. Chem. Res., 2013, 52, 17341–17350 CrossRef CAS.
- W. P. Liu, L. L. Xu, X. F. Li, C. S. Shen, S. Rashid, Y. Z. Wen, W. P. Liu and X. H. Wu, RSC Adv., 2015, 5, 2449–2456 RSC.
- U.S. Environmental Protection Agency Washington, DC, 2011. Drinking Water Standards and Health Advisories, http://www.epa.gov/index.html.
- C. B. Xu and J. Lancaster, Water Res., 2008, 42, 1571–1582 CrossRef CAS PubMed.
- M. Goto, R. Obuchi, T. Hirose, T. Sakaki and M. Shibata, Bioresour. Technol., 2004, 93, 279–284 CrossRef CAS PubMed.
- L. M. Wang, W. P. Liu, C. X. Yang, Z. Y. Pan, J. Y. Gan, C. Xu, M. R. Zhao and D. Schlenk, Environ. Sci. Technol., 2007, 31, 6124–6128 CrossRef.
- J. Liu, Y. Yang, Y. Yang, Y. Zhang and W. P. Liu, Toxicology, 2011, 282, 47–55 CrossRef CAS PubMed.
- Y. Yang, H. H. Ma, J. H. Zhou, J. Liu and W. P. Liu, Chemosphere, 2014, 96, 146–154 CrossRef CAS PubMed.
Footnote |
† Electronic supplementary information (ESI) available. See DOI: 10.1039/c4ra13329c |
|
This journal is © The Royal Society of Chemistry 2015 |
Click here to see how this site uses Cookies. View our privacy policy here.