DOI:
10.1039/C4RA10611C
(Paper)
RSC Adv., 2014,
4, 53335-53343
Substrate placement angle-dependent growth of dandelion-like TiO2 nanorods for solid-state semiconductor-sensitized solar cells†
Received
17th September 2014
, Accepted 7th October 2014
First published on 7th October 2014
Abstract
Hierarchical nanostructures grown directly on transparent conducting oxides hold the promise of overcoming the limitations of current semiconductor-sensitized solar cells based on random networks of nanoparticles. Here, we develop a facile substrate placement angle-dependent hydrothermal process to grow dandelion-like TiO2 nanostructures directly on transparent conductive oxides. TiO2 nanocrystals grown in solution during the synthesis process are found to promote the dandelion-like structure. By using these TiO2 nanostructures as photoanodes, Sb2S3 as the sensitizer, and P3HT as the hole-transporting material, we demonstrate fabrication of all-solid-state semiconductor-sensitized solar cells, which yield solar power conversion efficiency up to 4.71%. Electrochemical impedance spectroscopy indicates that moderate rod fusion at the base beneficially reduces electron recombination in the device. This work provides an innovative method for growing branched, one-dimensional TiO2 nanostructures that can be used for energy harvesting and storage.
Introduction
Semiconductor-sensitized solar cells (SSSCs) have received considerable interest as a promising avenue for converting solar energy to electricity at low cost.1 Solar power conversion efficiency (PCE) up to 6.2% has been reported for SSSCs that use liquid electrolytes.2 However, due to electrolyte leakage and corrosion, liquid electrolytes pose a challenge to long-term cell stability. One way to address this issue is to replace liquid electrolytes with solid-state hole transport materials (HTMs) such as CuSCN,3–5 P3HT,6,7 PCPDTBT,8 or spiro-OMeTAD.9–11
The performance of solid-state SSSCs has been limited by inefficient charge carrier transport through the photovoltaic devices. Typically, the photoanode in SSSCs is a porous thin film of sintered TiO2 nanoparticles. Although TiO2 nanoparticle film provides a large surface area, the electron diffusion coefficient of the nanoparticle film is several orders of magnitude smaller than that of its bulk single crystal, primarily due to scattering of electrons at the contacts between the nanoparticles.12,13 Inefficient transport of electrons increases the probability of photogenerated electron and hole recombination, which leads to loss of PCE.14–17 One approach to improve electron transport is to replace the nanoparticle-based mesoporous TiO2 film with vertically ordered one-dimensional (1-D) nanostructures because 1-D nanostructures provide direct electron pathways, enhance transport rate, and promote the lifetime of photogenerated electrons.12,18–23 In addition, vertically oriented nanostructures may provide larger interspaces for filling with HTMs.19,24
One challenge of using 1-D nanostructures in SSSCs is that, compared to mesoporous films, they typically have a low internal surface area, resulting in insufficient sensitizer loading and, therefore, low light harvesting efficiency.25 Recently, synthesis of hierarchical structures that resemble the shapes of flowers and leaves in nature by growing whiskers and clusters on the top and side surfaces of 1-D nanostructures has drawn considerable attention as an effective approach to increase the internal surface area while keeping the rapid electron transport advantage of the 1-D nanostructures.26–30 However, synthesis of these hierarchical structures directly on transparent conductive oxides and, in particular, fabrication of all solid-state SSSCs that incorporate these hierarchical nanostructures remain challenging.
In this paper, we report the synthesis of dandelion-like TiO2 nanorods (NRs) directly on transparent conducting oxides by a substrate placement angle-dependent hydrothermal method, as well as the fabrication of all solid-state SSSCs using the dandelion-like TiO2 NR arrays as photoanodes. By using Sb2S3 as the semiconductor sensitizer and P3HT as the HTM, a solar power conversion efficiency of 4.71% could be achieved using the fabricated SSSCs.
Experimental section
Synthesis of dandelion-like TiO2 NRs
Fluorine-doped tin oxide (FTO) glass (F:SnO2, 13 Ω per square, Aldrich) was cleaned by ultrasonication in water, acetone, and ethanol, followed by ultraviolet treatment for 30 min. TiO2-coated FTO (TiO2-FTO) was prepared by spray pyrolysis at 450 °C, using a solution of titanium(IV) isopropoxide dissolved in ethanol and acetylacetone. In a typical synthesis of dandelion-like TiO2 NRs, 0.5 mL of titanium(IV) butoxide (97%, Aldrich) was first added into 30 mL HCl aqueous solution, made by diluting HCl (36% by weight) with deionized water at 1
:
1 volume ratio, under vigorous stirring. The solution was stirred for 10 min before being transferred to a 50 mL Teflon-lined stainless steel autoclave. Afterwards, two substrates (FTO and TiO2-FTO) were placed at 75 degrees against the wall of the Teflon liner with the conducting side facing down. The autoclave was sealed and placed in an oven at 150 °C for 4 h. After cooling the autoclave to room temperature, the TiO2 NRs were washed with deionized water and ethanol repeatedly and subsequently dried in nitrogen flow.
Deposition of Sb2S3
As a photosensitizer, Sb2S3 was deposited on TiO2 NRs by the following procedure.31 SbCl3 (99.99%, Aldrich) (650 mg) was first dissolved in acetone (5 mL), then 1 M Na2S3O3 (98%, Aldrich) solution (25 mL) and enough deionized water was added to bring the final volume to 100 mL. The TiO2 NR substrate was immersed facedown in the prepared solution against the beaker at 7 °C for 1 h, 2 h and 3 h, respectively. Then the substrate was removed, annealed at 330 °C for 30 min in nitrogen, and cooled in air to form a Sb2O3 passivation layer for reduction of electron recombination.4
Material characterization
The synthesized nanostructures were examined by field emission scanning electron microscopy (FESEM, Hitachi S-4800), X-ray diffractometry (XRD, X'Pert Pro MPD) using Cu Kα radiation (1.5405 Å) operating at 40 kV and 40 mA, and transmission electron microscopy (TEM, JEM-2010HR) at an accelerating voltage of 200 kV.
Fabrication and characterization of SSSCs
P3HT solution in 1,2-dichlorobenzene (15 mg mL−1) was spin-coated onto Sb2S3-sensitized TiO2 NRs at 2500 rpm. In order to improve the contact between P3HT and the gold electrode, poly(3-4-ethylenedioxythiophene) doped with poly(4-stylenesulfonate) (PEDOT:PSS; Baytron AI 4083) diluted with two volumes of methanol was deposited onto the P3HT/Sb2S3/NR layer by spin-coating at 2000 rpm. The PEDOT:PSS/P3HT/Sb2S3/NR layer was then annealed at 90 °C for 30 min in a vacuum oven. Gold film, deposited by thermal evaporation using a metal mask at 5 × 10−5 Torr, was used as the counter electrode, providing an active area of 16 mm2 for each device.
SSSCs were characterized under illumination of AM 1.5 simulated sunlight at a power density of 100 mW cm−2, using a solar simulator (Oriel 91192, Newport, USA) calibrated with a standard crystalline silicon solar cell (PEC-SI01, Peccell Technologies, Inc., Japan). Electrochemical impedance spectra were recorded in the dark condition at a 600 mV bias voltage using a CHI 650C electrochemical analyzer (CH Instrument Corp., USA).
Results and discussion
Influence of substrates on dandelion-like TiO2 cluster growth
A hydrothermal method was used to grow dandelion-like TiO2 NRs on transparent conducting substrates in an aqueous solution of titanium(IV) butoxide and HCl at 150 °C, as described in the Experimental section. Firstly, TiO2 NRs were grown on bare FTO glass and incorporated in SSSCs. Then, the same method was used to grow TiO2 NRs on FTO glass coated with a TiO2 nanoparticle layer as a hole blocking layer in SSSCs.
To study the influence of the substrate on NR growth, TiO2 NRs grown on TiO2-coated FTO were compared with those grown on bare FTO substrate. While the lengths of the NRs were about equal on both substrates (1.3 μm), the width of the NRs grown on the TiO2-coated substrate was significantly larger (∼230 nm versus ∼80 nm) with less coverage density (∼2.6 × 109 cm−2 versus ∼4.6 × 109 cm−2) (Fig. 1). In addition, the NRs on the TiO2-coated substrate were less vertically aligned and had a greater degree of fusion at their base (Fig. 1g, h and S1†). These differences in TiO2 NR morphology could be explained by the different substrate surface roughness, where the as-prepared TiO2 nanoparticle layer on FTO might further act as crystal seeds and support for NR growth. The differences in nucleation might affect the NR alignment uniformity, leading to larger widths and smaller coverage density of the NRs on TiO2-coated FTO.
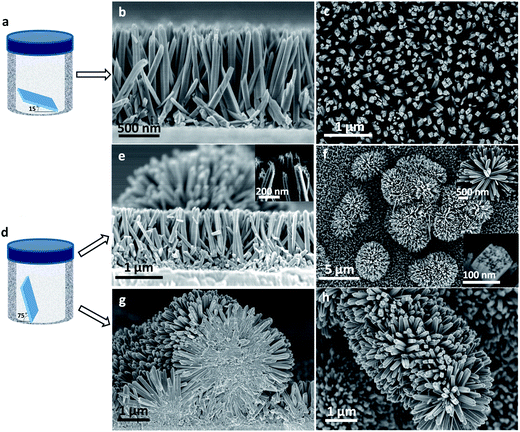 |
| Fig. 1 Schematic illustrations of substrate placement and SEM images of dandelion-like TiO2 NRs. (a) Schematic illustration of the case with substrate placement angle of 15 degrees. (b) Cross-sectional SEM image of TiO2 NRs grown on bare FTO glass at a substrate placement angle of 15 degrees. (c) Top-view SEM image of TiO2 NRs grown on bare FTO glass at a substrate placement angle of 15 degrees. (d) Schematic illustration of the case with substrate placement angle of 75 degrees. (e) Cross-sectional SEM image of TiO2 NRs grown on bare FTO glass at a substrate placement angle of 75 degrees (NR-FTO). Inset is a close-up image of the NR-FTO at the tips. (f) Top-view SEM image of NR-FTO. Top right inset is a close-up image of an individual small dandelion-like TiO2 cluster. Bottom right inset is a close-up image of an individual NR at the tip (a sub-NR cluster). (g) Cross-sectional SEM image of TiO2 NRs grown on TiO2 nanoparticle layer coated FTO glass at a substrate placement angle of 75 degrees (NR-TiO2-FTO). (h) Top-view SEM image of NR-TiO2-FTO. | |
Interestingly, we found that the angle of substrate placement in the reactor greatly affected the growth and morphology of the TiO2 NRs. When the FTO substrates were placed at 15 degrees relative to the bottom of the autoclave (Fig. 1a), fairly well vertically aligned TiO2 NRs with lengths around 1.3 μm and widths around 80 nm, similar to those reported by Liu and Aydil,32 grew on the substrate (Fig. 1b and c). However, when the substrates were placed at a steeper angle of 75 degrees against the Teflon-liner (Fig. 1d), many dandelion-like TiO2 NR clusters were found formed among or on top of the vertically aligned TiO2 NRs (Fig. 1e and f). These NRs (denoted as NR-FTO) showed similar length and width, regardless of the placement angle. Fig. 1g and h present the SEM images of NRs synthesized using TiO2 nanoparticle-coated FTO as substrate at a substrate placement angle of 75 degrees (denoted as NR-TiO2-FTO). SEM images of NR-TiO2-FTO synthesized at a substrate placement angle of 15 degrees are depicted in Fig. S1.† Moreover, SEM image reveals that the substrate placement angle-dependent morphologies also form when TiO2-coated FTO glass was used as the substrate (Fig. 1g, h and S1†). To rule out the influence of growth time on morphology, we increased growth time to 8 hours by using TiO2-coated FTO glass as substrate, substrate placement angle of 15 degrees and adding slightly more titanium(IV) butoxide (0.75 mL) while keeping other parameters unchanged. SEM images are shown in Fig. S2.† Flat surface without any dandelion-like TiO2 nanorod clusters was observed in this occasion. Therefore, we concluded that the morphology is only dependent on the substrate placement angle, regardless of the substrate types.
Investigation of dandelion-like TiO2 cluster growth mechanism
Under close SEM inspection, the NR tips reveal bunches of small and short sub-NRs (inset of Fig. 1e and bottom right inset of Fig. 1f), which have previously been described in the literature.33,34 Free TiO2 particles, which were discovered on the bottom of the autoclave after the reaction, confirmed that the nanocrystals formed homogenously in the solution during the reaction process. As is shown in Fig. 2a, we speculate that these nanocrystals play a vital role in the substrate placement-dependent morphologies. When the substrates are placed steeply in the autoclave, the downward substrate surface and the sub-NRs could trap and retain the germinated TiO2 nanocrystals or other solid impurities from the solution, allowing the adsorbed nanocrystals to act as nucleating centers for further growth of NRs.35 Furthermore, trapping the TiO2 nanocrystals or solid impurities in the interstices of sub-NRs may cause stress to sub-NR clusters alignment, leading to radial rather than parallel growth (Fig. 2a). These factors could facilitate the formation of dandelion-shaped nanostructures. However, when the substrates are placed relatively horizontal, solution-germinated TiO2 nanocrystals and solid impurities are less likely to come into contact with sub-NRs as they sink, resulting in fewer nucleating center particles being adsorbed by the downward substrate. Consequently, only well-aligned vertically oriented TiO2 NRs grow in this case.
 |
| Fig. 2 (a) Growth schematic illustration of dandelion-like TiO2 NRs. (i) A sub-NRs. (ii) Trapping nanocrystals from solution by the sub-NRs. (iii) A dandelion-like cluster. (b) Top-view SEM image of TiO2 NRs synthesized by using SiO2 deposited TiO2 NRs on TiO2 nanoparticle layer coated FTO substrate at the substrate placement angle of 15 degrees (NR-SiO2-NR-TiO2-FTO). (c) An individual dandelion-like TiO2 NR cluster from NR-SiO2-NR-TiO2-FTO. | |
To verify the proposed mechanism for the growth of dandelion-like TiO2 NRs described above, SiO2 nanocrystals, rather than TiO2 nanocrystals for avoiding epitaxial growth along the sub-NR clusters, were introduced as solid impurities to fill the interstices of the sub-NR clusters. We hypothesize that if the interstices of vertically aligned sub-NRs are filled with the inert SiO2 nanocrystals, then dandelion-like NRs will form when the substrate is placed back into the hydrothermal reactor, regardless of placement angle. To test this hypothesis, we took a NR-TiO2-FTO array grown at 15 degrees and deposited a monolayer of octadecyltrichlorosilane (OTS, 5 μL OTS in 20 mL hexane) onto the tips of the TiO2 NRs (marked as OTS-NR-TiO2-FTO).36,37 The OTS-NR-TiO2-FTO was treated with ultraviolet ozone for ten minutes to transform OTS into SiO2 nanocrystals (marked as SiO2-NR-TiO2-FTO). Afterwards, the SiO2-NR-TiO2-FTO was placed back in the reactor at a substrate placement angle of 15 degrees. Dandelion-like TiO2 NR clusters, composed of smaller NRs (width of 80–100 nm), were observed growing on the larger vertical NRs instead of vertical growth, supporting the hypothesis that filled interstitial nanocrystals lead to hierarchical growth (Fig. 2b and c).
Characterization of dandelion-like TiO2 NRs
Dandelion-like TiO2 NRs were subsequently characterized by XRD, TEM and selected-area electron diffraction (SAED). The diffraction peaks of NRs grown on two substrates (NR-FTO and NR-TiO2-FTO) agree well with the standard rutile structure (Fig. 3a). Additionally, the XRD spectra provide information on the NR orientation. For both NR patterns, the relative intensity of the (002) peak at 62.8° increased compared to the standard rutile pattern. The (002) peak is 6.7% relative to the intensity of the (110) peak for the standard rutile structure, whereas 32.8% for NR-TiO2-FTO, and 110.0% for NR-FTO. This result indicates that the preferential growth of the NRs was in the [001] direction.35 The smaller increase in relative intensity for NR-TiO2-FTO implies that the NRs on the TiO2-FTO substrate were less oriented with respect to the substrate surface. TEM and SAED measurements (Fig. 3b) further confirmed the single crystallinity of the TiO2 NRs and their aligned growth. Lattice fringes with interplanar spacings of d110 = 3.2 Å, d001 = 2.9 Å were consistent with rutile TiO2. From the HRTEM (Fig. 3b), we observed that the NR grows in the [001] direction, which was consistent with the observed XRD pattern. The measured Raman active modes at 236, 447 and 610 cm−1 also support the formation of rutile TiO2 (Fig. S4†).38 The preferential rutile growth can be explained by the small lattice mismatch between the tetragonal FTO interface (a = b = 0.4687 nm) and rutile TiO2 (a = b = 0.4594).32
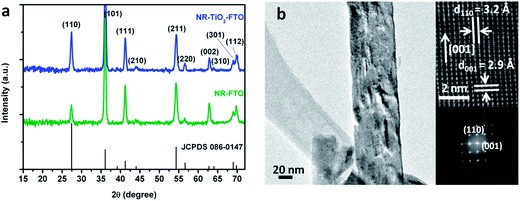 |
| Fig. 3 (a) XRD patterns of TiO2 NRs on two substrates. (b) High-resolution TEM image of a TiO2 NR and the corresponding SAED pattern. | |
The mechanism for anisotropic growth of 1D TiO2 NRs can be rationalized from two aspects. From thermodynamic considerations, the growth rates of different crystal faces of rutile TiO2 are different and follow the sequence (001) > (101) > (100) > (110).35 Kinetically, HCl is believed to slow down the hydrolysis rate of the precursor and reduce the surface energy of the crystal. Chloride ions preferentially adsorb onto the (110) crystal plane of TiO2 nanocrystal, inhibiting further growth of this plane.32,39,40 Both thermodynamic and kinetic factors can promote anisotropic growth of TiO2 in the [001] direction to form a 1-D NR structure.
Fabrication and characterization of SSSCs using dandelion-like TiO2
In order to fabricate SSSCs using the dandelion-like TiO2 nanostructures as photoanodes, we used Sb2S3 as the photosensitizer, because of its previously reported high absorption coefficient (∼1.8 × 105 cm−1 at 450 nm) and suitable energy band gap (∼1.7 eV) for harvesting visible light.6,8,41,42 Sb2S3 was deposited onto the TiO2 NRs via a previously reported chemical bath deposition process.31 The quality of the Sb2S3 layer can be optimized by changing the precursor concentration or the deposition time while keeping other conditions constant. Herein, we adjusted the latter parameter to study various qualities of the sensitizing layer. As the deposition durations increased, the color of Sb2S3-NR-FTO after annealing turned brown to dark brown, and eventually black (Fig. S3†), which indicated that more and more Sb2S3 crystals were deposited onto the nanostructures. Fig. 4a–c present the SEM images of Sb2S3 deposited on NR-FTO with deposition times of 1 h, 2 h, and 3 h, labeled as Sb2S3-NR-FTO (1 h), Sb2S3-NR-FTO (2 h), and Sb2S3-NR-FTO (3 h), respectively. It can be observed that, compared to Sb2S3-NR-FTO (1 h) covered with little Sb2S3 (Fig. 4a), and Sb2S3-NR-FTO (3 h) with even some of its interstices between NRs filled with Sb2S3 crystals (Fig. 4c), Sb2S3-NR-FTO (2 h) is uniformly covered with Sb2S3 nanocrystals without blocking the interstices (Fig. 4b), allowing the hole transport material to eventually fill in the interstices. A cross-sectional image of Sb2S3-NR-TiO2-FTO (2 h) is also shown in Fig. 4d. From the SEM image, it is clear that the dandelion-shaped nanostructure retained its original morphology without blocked interstices after a 2 h deposition of the sensitizer on its sidewall. The XRD patterns of Sb2S3-NR-FTO with different deposition times (Fig. 4e), after deducting the peaks of the rutile TiO2 (JCPDS 086-0147), match well with the standard stibnite crystalline structure of Sb2S3 (JCPDS 042-1393). The peak at 45.9° arose from the oxidation of Sb2S3-NR-FTO when cooled in the air after annealing in nitrogen (Fig. 4e). This indicates that a Sb2O3 passivation layer formed, which may retard recombination in the photovoltaic application.4 In addition, the Sb2S3 peak intensity increases as the growth time elongates, implying that more Sb2S3 crystals anchor onto the NRs. Fig. 4f depicts TEM images of a TiO2 NR covered by Sb2S3 nanocrystals after 2 h of deposition, where the surface of a TiO2 NR is densely covered by Sb2S3 nanocrystals. The HRTEM image (inset of Fig. 4f) shows the lattice interplanar spacing of 3.56 Å corresponds well with that of the stibnite (130) interplanar spacing.43,44 In addition, Raman peaks located at 189, 251, 371, and 450 cm−1 can be assigned to crystalline Sb2S3 (Fig. S5†).43
 |
| Fig. 4 Sb2S3-sensitized TiO2 NRs. (a–c) SEM images of Sb2S3-sensitized TiO2 NRs on bare FTO with different Sb2S3 deposition times. (a) 1 h [Sb2S3-NR-FTO (1 h)]. (b) 2 h [Sb2S3-NR-FTO (2 h)] (c) 3 h [Sb2S3-NR-FTO (3 h)]. (d) SEM image of Sb2S3-NR-TiO2-FTO (2 h) (e) XRD pattern of [Sb2S3-NR-FTO (2 h)]. (f) High-resolution TEM image of Sb2S3 crystals deposited on a TiO2 NR after 2 h deposition of Sb2S3. | |
Furthermore, we fabricated SSSCs using dandelion-like TiO2 NRs as the photoanodes, Sb2S3 as the sensitizer, and P3HT as the HTM. Their performance was characterized. To the best of our knowledge, these devices were the first SSSCs fabricated using dandelion-like TiO2 NRs. A schematic SSSC structure is shown in Fig. 5. The details of the device fabrication process are recounted in the Experimental section. In this report, devices incorporating different Sb2S3 deposition times are fabricated. The UV-vis absorption spectra of these sensitized TiO2 NRs are shown in Fig. 6a. Due to similar TiO2 NRs photoanodes, the spectra show almost identical absorption between 200 and 400 nm, which is mainly attributed to the absorption of TiO2 NRs. However, above 400 nm, absorption significantly increases as the deposition time increases from 1 h to 2 h, but only a slight increase is observed as the deposition time continues to increase from 2 h to 3 h. The increase in absorption above 400 nm can be attributed to the increased thickness of Sb2S3 layer on the TiO2 NRs. Fig. 6b shows the photocurrent–voltage (J–V) characteristics of the SSSCs as a function of the different deposition times of Sb2S3. The extracted photovoltaic parameters are summarized in Table 1. We found that the performance of the SSSCs is strongly dependent on the deposition time of the Sb2S3 crystals. As the deposition time increases from 1 h to 2 h, the short-circuit current density (Jsc), open-circuit voltage (Voc), fill factor (FF), and PCE increase from 8.26 to 14.66 mA cm−2, 535.10 to 570.82 mV, 48.89 to 56.29%, and 2.16 to 4.71%, respectively. Such a significant increase is likely caused by the improved coverage of Sb2S3 on TiO2 NRs, which leads to increased absorption of light above 400 nm (as shown in Fig. 6a). However, as the deposition time continues to increase from 2 h to 3 h, Jsc, Voc and PCE are all observed to decrease, despite the slightly increased light absorption. This effect likely occurs because, after 3 h deposition, Sb2S3 crystals start to fill the spaces between the TiO2 NRs, thus blocking interstices from HTM filling. Incomplete filling of HTM results in poor hole transfer, which deteriorates the performance of SSSCs.
 |
| Fig. 5 Schematic device structure of SSSC that incorporates the dandelion-like TiO2 NRs. | |
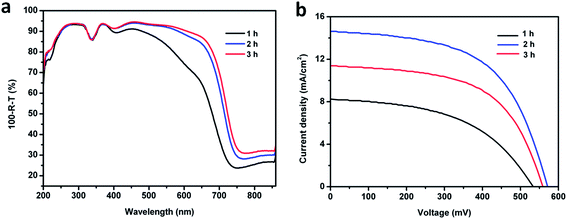 |
| Fig. 6 (a) Absorption spectra of Sb2S3-NR-FTO with different Sb2S3 deposition times. (b) J–V characteristics of SSSCs using Sb2S3-NR-FTO with different deposition times of Sb2S3 as the photoanodes. | |
Table 1 Photovoltaic characteristics of SSSCs that use Sb2S3-NR-FTO as the photoanodes with different deposition times of Sb2S3
Sb2S3 deposition time (h) |
Jsc (mA cm−2) |
Voc (mV) |
FF (%) |
PCE (%) |
1 |
8.26 |
535.10 |
48.89 |
2.16 |
2 |
14.66 |
570.82 |
56.29 |
4.71 |
3 |
11.37 |
558.45 |
57.08 |
3.62 |
Theoretically, when the TiO2 NRs grown directly on bare FTO glass (NR-FTO) are used as the photoanodes, there might arise a structural problem with the SSSC device. As shown in Fig. 5, after filling the spaces between the TiO2 NRs with HTM, the HTM is likely in contact with FTO, which will cause back injection of electrons. Therefore, we also fabricated SSSCs using the TiO2 NRs grown on TiO2-coated FTO (NR-TiO2-FTO) as the photoanode, where a 30 nm thick layer of TiO2 nanoparticles served as a hole blocking layer. The performance of SSSC based on NR-TiO2-FTO (labeled as device 2) was compared with the one based on NR-FTO (labeled as device 1) in Fig. 7. In this experiment, the deposition time of Sb2S3 was kept at 2 h for both devices.
 |
| Fig. 7 Characterization of SSSCs that incorporate two dandelion-like TiO2 NRs (NR-FTO and NR-TiO2-FTO). (a) Absorption spectra of Sb2S3-NR-FTO (2 h) and Sb2S3-NR-TiO2-FTO (2 h). (b) EQEs of SSSCs using Sb2S3-NR-FTO (2 h) (device 1) and Sb2S3-NR-TiO2-FTO (2 h) (device 2) as the photoanode. (c) J–V characteristics of device 1 and device 2. (d) Nyquist plots of device 1 and device 2 at 600 mV forward bias (inset is the equivalent circuit model). | |
Fig. 7a shows the absorption spectrum of Sb2S3-sensitized NR-TiO2-FTO (Sb2S3-NR-TiO2-FTO) in comparison with that of Sb2S3-NR-FTO, where the deposition times of Sb2S3 are both 2 h. It is observed that Sb2S3-NR-TiO2-FTO has lower absorption than Sb2S3-NR-FTO almost in the whole wavelength region. The external quantum efficiency (EQE) of device 2 is also measured to be lower than that of device 1 in almost the whole visible light range (Fig. 7b). This is likely because less Sb2S3 was loaded on NR-TiO2-FTO than on NR-FTO due to the smaller internal surface area of NR-TiO2-FTO, caused by its smaller surface coverage density, larger diameter compared to NR-FTO, and a greater degree of fusion at the root of the NRs (Fig. 1g and S1†). Jsc (10.71 mA cm−2), Voc (515.54 mV), and PCE (2.71%) of device 2 are all much smaller than those of device 1, which we believe is a direct result of the low EQE. However, the dark J–V curve of device 2 in Fig. 7c shows a lower dark current than that of device 1, which may be explained by the effect of the TiO2 nanoparticle hole-blocking layer in NR-TiO2-FTO.
Usually, as mentioned above, a compact TiO2 nanoparticle layer is prepared to act as a hole blocking layer that will reduce electron–hole recombination in SSSCs. However, seen from Fig. 1b and e, moderate nanorod bottom fusion makes the nanorods adhered to each other at the bottom where closed to the substrate. Theoretically, such fusion part could act as hole blocking layer by itself. To clarify this hypothesis, electrochemical impedance spectroscopy (EIS) was further employed to investigate the electron transfer and recombination in these two devices. Fig. 7d shows the Nyquist plots of device 1 and device 2 at 600 mV forward bias, where two semicircles are observed. Generally, in Nyquist plots of SSSCs, the semicircle in the high frequency region represents the hole transporting resistance of the HTMs, while those in the intermediate frequency offer information on the recombination resistance.2,3 The EIS data may be fitted with the equivalent circuit model (shown as inset in Fig. 7d), using Rt and Ct to depict hole transport resistance and the chemical capacitance in the P3HT, respectively, and Rr shunted with Cr to represent electron–hole recombination that takes place in SSSCs. By fitting the data to the equivalent circuit model, the resultant EIS parameters are presented in Table 2. To our surprise, the resistance for recombination in device 1 is only slightly smaller than that in device 2, which is manifested by showing an even comparable sized second semicircle in Nyquist plot to the one for device 2. Towards this point, we believe this is because the moderate NR fusion of NR-FTO at the root has acted as blocking layer by itself, just as the proposed speculation. Therefore, it is believed that, the fabrication of 1-D nanomaterial-based photovoltaic devices could be simplified with better design of the 1-D TiO2 nanomaterial with moderate root fusion, and the loss of carriers due to recombination could further be reduced. Meanwhile, judging from the relative smaller recombination resistance but higher PCE for device 1 than those of device 2, we could conclude that the higher specific surface area aroused by the higher nanorod coverage density and smaller width for device 1 might dominate over the smaller recombination resistance in affecting the photovoltaic performance in this study.
Table 2 EIS characteristics of SSSC based on Sb2S3-NR-FTO (2 h) (device 1) and SSSC based on Sb2S3-NR-TiO2-FTO (2 h) (device 2) at 600 mV forward bias
Device |
Rs (Ω) |
Rt (Ω) |
Ct (μF) |
Rr (Ω) |
Cr (μF) |
1 |
13.6 ± 0.3 |
115.3 ± 1.4 |
0.53 ± 0.01 |
134.9 ± 2 |
3.84 ± 0.01 |
2 |
19.8 ± 0.3 |
120.6 ± 1.8 |
1.11 ± 0.01 |
152.6 ± 2 |
2.06 ± 0.01 |
To study the advantages of the dandelion-like TiO2 NR based device 1, it was compared with other devices in the literatures. A reported TiO2 nanoparticle-based device has an only slightly better PCE of 5.13% compared to the best device reported here, which has a PCE of 4.71%.6 However, the device here outperformed the one in literature in Jsc. Moreover, our device has a larger PCE (4.71%) than the reported vertically-aligned TiO2 nanorod based device with its PCE of 4.5%.18 This can be explained by the relative bigger length of the present TiO2 NRs than the reported one (1.3 μm compared to 900 nm) and addition dandelion-like TiO2 NR clusters. Both factors will help to overcome the drawback of small surface area for 1-D materials and benefit affording larger specific surface area for sensitizer loading.24,45,46 Considering the active area of the reported device is double that of the present one (31.4 mm2 compared to 16 mm2),18 the device of 16 mm2 size using Sb2S3 sensitized TiO2 NRs without dandelion-like TiO2 clusters which was synthesized on bare FTO at a substrate placement angle of 15° was fabricated as a reference device. SEM images of such Sb2S3 sensitized TiO2 NRs and device are shown in Fig. S7a and b.† From the J–V characteristic curve in Fig. S7c,† one can see that, although it produces a comparable Voc of 544.55 mV, both Jsc of 12.09 mA cm−2 and PCE of 3.35% are inferior to those of the dandelion-like TiO2 cluster-based device (Jsc of 14.66 mA cm−2 and PCE of 4.71%). By comparing the two TiO2 NRs, we attribute the promising trend in PCE and Jsc to the large specific surface area due to large coverage density and the additional dandelion-like TiO2 morphology.
Furthermore, the stability of device 1 was monitored by keeping it in air with relative humidity of 35% at 25 °C over two months. Optimistically, less than 5% degradation of the initial PCE was observed. The good stability should be partly originated from the inert reactivity of Sb2S3 with O2 at low temperature, and partly because of the Sb2O3 passivation layer formed when cooling in air after annealing which keeps Sb2S3 away from O2.
Conclusion
In conclusion, we have developed a facile substrate placement angle-dependent hydrothermal process to grow dandelion-like TiO2 NRs directly on bare FTO and TiO2 nanoparticle-coated FTO substrates. The morphologies of the nanostructures are highly dependent on the angle between the downward substrate and the reaction container bottom. In the growth process of dandelion-like TiO2 NRs, TiO2 nanocrystals grown in the solution are believed to act as promoter to shape the dandelion-like nanostructures. By using these TiO2 NRs as photoanodes, Sb2S3 as the sensitizer, and P3HT as the HTM, we have demonstrated fabrication of all solid-state SSSCs, which yield PCE up to 4.71%. The PCE is higher than the vertical NR photoanode based device. By analyzing the EIS, the moderate NR root fusion acted positively to reduce recombination in this device. We anticipate that with better design of the synthesis process, the performance of the SSSCs may be further improved by increasing the coverage density with moderate fusion at the starting of the NRs. The substrate placement angle-dependent synthesis method opens another door for synthesizing 1-D based branched TiO2 for energy storage, photocatalysis and sensing.
Acknowledgements
This work was supported by the State Scholarship Fund of China Scholarship Council and the National Science Foundation of China (21273241).
Notes and references
- G. Hodes and D. Cahen, Chem. Rev., 2012, 45, 705–713 CAS
. - K. Yan, L. Zhang, J. Qiu, Y. Qiu, Z. Zhu, J. Wang and S. Yang, J. Am. Chem. Soc., 2013, 135, 9531–9539 CrossRef CAS PubMed
. - P. P. Boix, G. Larramona, A. Jacob, B. Delatouche, I. Mora-Sero and J. Bisquert, J. Phys. Chem. C, 2012, 116, 1579–1587 CAS
. - Y. Itzhaik, O. Niitsoo, M. Page and G. Hodes, J. Phys. Chem. C, 2009, 113, 4254–4256 CAS
. - S. Nezu, G. Larramona, C. Choné, A. Jacob, B. Delatouche, D. Péré and C. Moisan, J. Phys. Chem. C, 2010, 114, 6854–6859 CAS
. - J. A. Chang, J. H. Rhee, S. H. Im, Y. H. Lee, H. Kim, S. I. Seok, M. K. Nazeeruddin and M. Grätzel, Nano Lett., 2010, 10, 2609–2612 CrossRef CAS PubMed
. - J. A. Chang, S. H. Im, Y. H. Lee, H. Kim, C. Lim, J. H. Heo and S. I. Seok, Nano Lett., 2012, 12, 1863–1867 CrossRef CAS PubMed
. - S. H. Im, C. Lim, J. A. Chang, Y. H. Lee, N. Maiti, H. Kim, M. K. Nazeeruddin, M. Grätzel and S. I. Seok, Nano Lett., 2011, 11, 4789–4793 CrossRef CAS PubMed
. - S. Moon, Y. Itzhaik, J. Y. Um, S. M. Zakeeruddin, G. Hodes and M. Grätzel, J. Phys. Chem. Lett., 2010, 1, 1524–1527 CrossRef CAS
. - J. Burschka, N. Pellet, S. Moon, R. H. Baker, P. Gao, M. K. Nazeeruddin and M. Grätzel, Nature, 2013, 499, 316–319 CrossRef CAS PubMed
. - M. Liu, M. B. Johnston and H. J. Snaith, Nature, 2013, 501, 395–398 CrossRef CAS PubMed
. - M. Law, L. E. Greene, J. C. Johnson, R. Saykally and P. Yang, Nat. Mater., 2005, 4, 455–459 CrossRef CAS PubMed
. - J.-J. Wu, G.-R. Chen, C.-C. Lu, W.-T. Wu and J.-S. Chen, Nanotechnology, 2008, 19, 105702 CrossRef PubMed
. - J. H. Bang and P. V. Kamat, Adv. Funct. Mater., 2010, 20, 1970–1976 CrossRef CAS
. - P. V. Kamat, J. Phys. Chem. C, 2008, 112, 18737–18753 CAS
. - G. Hodes, J. Phys. Chem. C, 2008, 112, 17778–17787 CAS
. - M. Ye, D. Zheng, M. Wang, C. Chen, W. Liao, C. Lin and Z. Lin, ACS Appl. Mater. Interfaces, 2014, 6, 2893–2901 CAS
. - J. C. Cardoso, C. A. Grimes, X. Feng, X. Zhang, S. Komarneni, M. V. B. Zanoni and N. Bao, Chem. Commun., 2012, 48, 2818–2820 RSC
. - H.-S. Kim, J.-W. Lee, N. Yantara, P. P. Boix, S. A. Kulkarni, S. Mhaisalkar, M. Grätzel and N.-G. Park, Nano Lett., 2013, 13, 2412–2417 CrossRef CAS PubMed
. - A. Kongkanand, K. Tvrdy, K. Takechi, M. Kuno and P. V. Kamat, J. Am. Chem. Soc., 2008, 130, 4007–4015 CrossRef CAS PubMed
. - K. S. Leschkies, R. Divakar, J. Basu, E. Enache-Pommer, J. E. Boercker, C. B. Carter, U. R. Kortshagen, D. J. Norris and E. S. Aydil, Nano Lett., 2007, 7, 1793–1798 CrossRef CAS PubMed
. - D. R. Baker and P. V. Kamat, Adv. Funct. Mater., 2009, 19, 805–811 CrossRef CAS
. - W.-T. Sun, Y. Yu, H.-Y. Pan, X.-F. Gao, Q. Chen and L.-M. Peng, J. Am. Chem. Soc., 2008, 130, 1124–1125 CrossRef CAS PubMed
. - C. Xu, J. Wu, U. Desai and D. Gao, Nano Lett., 2012, 12, 2420–2424 CrossRef CAS PubMed
. - Q. Zhang, C. S. Dandeneau, X. Zhou and G. Cao, Adv. Mater., 2009, 21, 4087–4108 CrossRef CAS
. - L. Passoni, F. Ghods, P. Docampo, A. Abrusci, J. Martí-Rujas, M. Ghidelli, G. Divitini, C. Ducati, M. Binda, S. Guarnera, A. L. Bassi, C. S. Casari, H. J. Snaith, A. Petrozza and F. D. Fonzo, ACS Nano, 2013, 7, 10023–10031 CrossRef CAS PubMed
. - F. Sauvage, F. D. Fonzo, A. L. Bassi, C. S. Casari, V. Russo, G. Divitini, C. Ducati, C. E. Bottani, P. Comte and M. Grätzel, Nano Lett., 2010, 10, 2562–2567 CrossRef CAS PubMed
. - S. H. Ko, D. Lee, H. W. Kang, K. H. Nam, J. Y. Yeo, S. J. Hong, C. P. Grigoropoulos and H. J. Sung, Nano Lett., 2011, 11, 666–671 CrossRef CAS PubMed
. - Y. Qiu, K. Yan, H. Deng and S. Yang, Nano Lett., 2012, 12, 407–413 CrossRef CAS PubMed
. - M. Ye, H. Liu, C. Lin and Z. Lin, Small, 2013, 9, 312–321 CrossRef CAS PubMed
. - S. Messina, M. T. S. Nair and P. K. Nair, Thin Solid Films, 2007, 515, 5777–5782 CrossRef CAS PubMed
. - B. Liu and E. S. Aydil, J. Am. Chem. Soc., 2009, 131, 3985–3990 CrossRef CAS PubMed
. - W. Guo, C. Xu, X. Wang, S. Wang, C. Pan, C. Lin and Z. L. Wang, J. Am. Chem. Soc., 2012, 134, 4437–4441 CrossRef CAS PubMed
. - M. Lv, D. Zheng, M. Ye, L. Sun, J. Xiao, W. Guo and C. Lin, Nanoscale, 2012, 4, 5872–5879 RSC
. - A. Kumar, A. R. Madaria and C. Zhou, J. Phys. Chem. C, 2010, 114, 7787–7792 CAS
. - D. L. Angst and G. W. Simmons, Langmuir, 1991, 7, 2236–2242 CrossRef CAS
. - M. E. Mc Govern, K. M. R. Kallury and M. Thompson, Langmuir, 1994, 10, 3607–3614 CrossRef CAS
. - P. Sun, X. Zhang, C. Wang, Y. Wei, L. Wang and Y. Liu, J. Mater. Chem. A, 2013, 1, 3309–3314 CAS
. - X. Feng, K. Shankar, O. K. Varghese, M. Paulose, T. J. Latempa and C. A. Grimes, Nano Lett., 2008, 8, 3781–3786 CrossRef CAS PubMed
. - H. G. Yang, C. H. Sun, S. Z. Qiao, J. Zou, G. Liu, S. C. Smith, H. M. Cheng and G. Q. Lu, Nature, 2008, 453, 638–642 CrossRef CAS PubMed
. - M. Y. Yersavel and J. A. Haber, Thin Solid Films, 2007, 515, 7171–7176 CrossRef PubMed
. - G. Peng, J. Wu, Y. Zhao, X. Xu, G. Xu and A. Star, RSC Adv., 2014, 4, 46987–46991 RSC
. - G. Wang and C. L. Cheung, Mater. Lett., 2012, 67, 222–225 CrossRef CAS PubMed
. - J. Zhong, X. Zhang, Y. Zheng, M. Zheng, M. Wen, S. Wu, J. Gao, X. Gao, J.-M. Liu and H. Zhao, ACS Appl. Mater. Interfaces, 2013, 5, 8345–8350 CAS
. - C. Xu, J. Wu, U. V. Desai and D. Gao, J. Am. Chem. Soc., 2011, 133, 8122–8125 CrossRef CAS PubMed
. - M. Lv, D. Zheng, M. Ye, J. Xiao, W. Guo, Y. Lai, L. Sun, C. Lin and J. Zuo, Energy Environ. Sci., 2013, 6, 1615–1622 CAS
.
Footnote |
† Electronic supplementary information (ESI) available. See DOI: 10.1039/c4ra10611c |
|
This journal is © The Royal Society of Chemistry 2014 |
Click here to see how this site uses Cookies. View our privacy policy here.