DOI:
10.1039/C4RA08437C
(Communication)
RSC Adv., 2014,
4, 52680-52685
A process of converting cellulosic fibers to a superhydrophobic fiber product by internal and surface applications of calcium carbonate in combination with bio-wax post-treatment
Received
9th August 2014
, Accepted 16th October 2014
First published on 16th October 2014
Abstract
To convert cellulosic fibers to a superhydrophobic fiber product (i.e., cellulosic paper), the simple concept involving wet-end and surface applications of calcium carbonate in combination with bio-wax post-treatment was proposed and demonstrated.
Introduction
The utilization of renewable lignocellulosic feedstocks for the production of materials, chemicals, and energy fits well within the goal of a green economy. In the traditional pulp and paper industry, the concept of converting the pulp/paper production process into an integrated lignocellulosic biorefinery by efficient utilization of the lignocelluloses would be strategic in upgrading/transforming the industry.1–4 As an integrated component of this concept, the efficient and value-added applications of cellulosic fibers are rather promising.5–10
Cellulosic fibers are the basic materials for the production of various paper-based materials. In this regard, the wet-end addition of mineral fillers prior to paper-sheet formation is a common practice for the production of printing/writing papers. The main contributions of filler addition are cost/energy savings and improvement of critical properties including sheet formation, brightness, opacity, gloss, and printability/writability;11 in some sense, the development of filler technologies for maximizing the benefits concerning the use of fillers or enabling value-added applications is critical for the paper industry.12–17 On the other hand, surface engineering of cellulosic paper by pigment coating is commercially adopted to deliver improved surface properties.18,19 This process is particularly useful for the production of high quality paper grades, allowing for high qualities in terms of print image and surface appearance.
Fiber networks are the essential skeleton of cellulosic paper products. However, due to the hydrophilic nature of cellulosic fibers, cellulosic paper is inherently hydrophilic. Although internal/surface sizing is commercially used to impart hydrophobicity to cellulosic paper, the traditional sized paper products are far from superhydrophobic, which is defined as a water contact angle of above 150°.20,21 Rendering cellulosic paper superhydrophobic would allow broader applications, and these paper-based products may be used as liquid/food packages, paper-boxes/cups, cup/food plates, bio-active paper, disposable lab-ware, and lab-on-paper devices.20,22–47
Essentially, the published literature on the fabrication of superhydrophobic paper is predominately based on surface engineering of paper by creating a proper combination of surface roughness and hydrophobicity, which leads to superhydrophobicity development. In this regard, various processes have been proposed and demonstrated, including:
• Multi-layer deposition of polydiallyldimethylammonium chloride and mineral particles on paper, followed by hydrophobication post-treatment.38
• Surface addition of emulsified bio-wax mixture, followed by annealing post-treatment.29
• Surface treatment with paraffin wax dissolved/dispersed in an ethanol/water medium.39
• Surface treatment with fluoro-containing polymers or silica/polystyrene-based composite.26,40,45
• Sequential surface treatments with cellulose stearoyl ester dissolved in toluene and cellulose stearoyl ester nanoparticles.27
• Combining oxygen plasma etching with plasma deposition of a hydrophilic diamond-like carbon coating.28
• Fluorocarbon plasma treatment of mineral-filler-containing paper.31
• Surface addition of hydrophobically modified mineral nanoparticles suspended in ethanol.32,35,41,42
• Soaking of paper in poly(hydroxybutyrate)/chloroform solution, followed by treatment with ethanol–water mixture.33,34,43
• Surface treatment with mineral particles and cellulose nanofibers, followed by dipping in a solution of alkyl ketene dimer in n-heptane.20
• Use of hydrophobic mineral particles as a coating pigment in combination with hydrophobication post-treatment.44,47
• Surface treatment by rapid expansion of supercritical carbon oxide containing a crystallizing wax.37
Differing from previous reports related to the fabrication of superhydrophobic paper,20,22–47 based on the well-established commercial practices pertaining to the production of traditional filled/pigment-coated paper products, the simple concept of combining wet-end filler addition (i.e., internal application of filler particles) and pigment coating (i.e., surface application of pigment particles) with bio-wax post-treatment for the fabrication of superhydrophobic paper was proposed and demonstrated in this preliminary study. It was hypothesized that wet-end filler addition and pigment coating would contribute to paper surface roughening, and the hydrophobication post-treatment with environmentally-friendly bio-wax would lead to the construction of superhydrophobic surfaces.
Materials and methods
Materials
Bleached chemical pulp (cellulosic fibers) was supplied by Mudanjiang Hengfeng Paper Co., Ltd, China. This pulp was refined in a Valley beater to a beating degree of 46° SR. The micro-sized precipitated calcium carbonate particles (see Fig. 1) for wet-end filler addition and pigment coating were purchased from Guangxi Guilin Wuhuan Co., Ltd., China and Dujiangyan Calcium Product Co., Ltd, China, respectively. Bio-wax (beeswax) was purchased from Hebei Haifeng Wax Industry Co., Ltd., China. Carboxylated styrene–butadiene latex and alkyl ketene dimer emulsion were supplied by Mudanjiang Hengfeng Paper Co., Ltd, China. Cationic polyacrylamide (Percol® 182) and bentonite (Hydrocol® AP1) were provided by BASF (China) Co., Ltd. Sodium hexametaphosphate and ethanol were all analytical reagents.
 |
| Fig. 1 Scanning electron microscope images of precipitated calcium particles used for wet-end filler addition (left) and pigment coating (right) (SEM, QUANTA 200, Japan). | |
Conversion of cellulosic fibers to superhydrophobic paper
Essentially, three sequential steps were applied for the conversion of cellulosic fibers to superhydrophobic paper. These include paper-sheet formation involving the wet-end addition of precipitated calcium carbonate particles, pigment coating of the filled paper-sheets involving the surface application of precipitated calcium carbonate particles, and post-treatment with bio-wax.
Paper-sheet formation. In an aqueous medium, cellulosic fibers and precipitated calcium carbonate were sufficiently mixed. Alkyl ketene dimer emulsion (dosage: 0.11 wt%) was added, and the mixture was stirred at 500 rpm for 3 min. Upon increasing the stirring speed to 1500 rpm, cationic polyacrylamide (dosage: 0.05 wt%) was added, and the mixture was stirred for 2 min. The stirring speed was then lowered to 500 rpm, and was stirred for 30 s. Subsequently, bentonite (dosage: 0.5 wt%) was added, and stirring was continued for another 2 min. It should be noted that the dosages of additives (in terms of their dry weight) were based on the total weight of cellulosic fibers and filler, and the weight ratio of fibers to filler was 4
:
1. This filler addition level is a typical one for the current commercial production of printing papers. Paper-sheets with a target basis weight of 90 g m−2 were prepared using a ZQJ1-B 200 mm sheet former (China). The wet paper-sheets were pressed at 0.4 MPa for 5 min prior to drying (120 °C, 5 min).
Pigment coating. Two grams of precipitated calcium carbonate was added to a 100 ml beaker containing 10 ml distilled water, followed by the addition of 10 ml of hexametaphosphate solution (0.5 wt%) and 10 ml of carboxylated styrene–butadiene latex dispersion (1 wt%). The mixture was then diluted to a total weight of 30 g by adding extra distilled water, followed by sufficient mixing with the aid of ultrasonic treatment (130 W, 20 min). The freshly prepared aqueous mixture was used as the coating color for pigment coating of the paper-sheets. A simple method of dip coating (45 s) was adopted. Upon the completion of dip coating, the paper-sheets were oven-dried at 105 °C for 1 h.
Bio-wax post-treatment. To a 250 ml beaker, 10 g of bio-wax and 100 ml of ethanol were added, and the beaker was sealed. Under stirring at 300 rpm, the mixture was heated to 80 °C to allow the substantial dissolution of bio-wax. The pigment-coated paper-sheets were then treated with bio-wax/ethanol solution by dip coating for 2 min, followed by over-drying at 105 °C for 1 h.
Contact angle measurements and SEM/AFM observations
Water droplets (5 μl) were dropped onto the paper surfaces, and static contact angles were measured on a Contact Angle System (OCA20, Dataphysics Co., Germany). Images pertaining to the interaction of the paper with the water droplet during water contact measurement were also collected. The morphologies of the samples were observed by using a field emission scanning electron microscope (SEM, JEOL, JSM-7500F) and an atomic force microscope (AFM, Bruker, Multimode 8).
Results and discussion
Concept of converting cellulosic fibers to superhydrophobic paper by combining wet-end filler addition and pigment coating with bio-wax post-treatment
In accordance with an integrated lignocellulosic biorefinery, the conversion of cellulosic fibers to value-added superhydrophobic paper-based products has much potential. Differing from the published reports,20,22–47 a process concept pertaining to the fabrication of superhydrophobic paper by a combination of wet-end filler addition, pigment coating, and bio-wax post-treatment was proposed in the current study.
The process flow pertaining to the proposed concept is shown in Fig. 2. In this concept, three key elements are essential for the fabrication of superhydrophobic paper. The wet-end addition of filler particles (i.e., the mineral fillers commonly used in the paper industry) during the paper-sheet formation process followed by paper drying leads to the construction of rough paper surface. This micro-roughening impact can reasonably be induced by the presence of mineral filler particles in fiber networks.47 Subsequently, the coating of the filled paper with pigment particles in combination with paper drying further enhances paper surface roughness.46 Finally, hydrophobication of the rough paper surface with bio-wax (with the aid of an ionic solvent, i.e., ethanol)48 would result in the construction of superhydrophobic paper surface.
 |
| Fig. 2 Process flow pertaining to the proposed concept of converting cellulosic fibers to superhydrophobic paper by a combination of wet-end filler addition, pigment coating, and bio-wax post-treatment. | |
A feature of the proposed concept is that it is essentially based on the well-known commercial practices of wet-end filler addition and pigment coating associated with paper production; in particular, the micro-sized calcium carbonate filler particles are used for paper surface micro-roughening. On the other hand, the use of environmentally-friendly bio-wax such as beeswax instead of oil-derived materials/chemicals may facilitate the use of the product in such occasions as food storage/packaging.
Impact of wet-end filler addition, pigment coating, and bio-wax post treatment
For the demonstration of the proposed concept, it is essential to evaluate the impact of the process steps involving wet-end filler addition, pigment coating, and bio-wax post-treatment. The results are shown in Fig. 3–7.
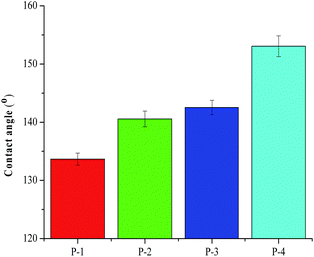 |
| Fig. 3 Water contact angles of paper samples: (P-1) bio-wax-treated paper; (P-2) filled and bio-wax-treated paper; (P-3) pigment-coated and bio-wax-treated paper; (P-4) filled, pigment-coated, and bio-wax treated paper. | |
Various chemicals including wax and alkyl ketene dimer can be used for the hydrophobication of cellulosic paper or other substrates. However, on a flat surface, no chemical has a water contact angle of higher than 125°.24 Thus, the combination of surface roughening with hydrophobication is a prerequisite for superhydrophobication of any substrate. In this work, bio-wax treatment of unfilled and uncoated paper led to the construction of paper-based material with a water contact angle of about 134° (see Fig. 3), presumably due to the favorable surface roughening impact associated with the interaction of bio-wax with ethanol (an ionic solvent).48
The wet-end addition of filler particles prior to paper sheet formation is a useful approach to modification of fiber networks. As shown in Fig. 3, the wet-end addition of precipitated calcium carbonate filler in combination with bio-wax treatment resulted in a significant increase in water contact angle. A similar impact of pigment coating was also observed. Basically, the combination of either wet-end filler addition or pigment coating with bio-wax treatment resulted in the fabrication of hydrophobic paper with a water contact angle of 140° to 143°.
Interestingly, the combined use of wet-end filler addition, pigment coating, and bio-wax post-treatment led to the fabrication of paper with a water contact angle of about 153° (see Fig. 3). Thus, the proposed concept was effective in converting cellulosic fibers to superhydrophobic paper. According to mass balance analysis, the contents of precipitated calcium carbonate particles (used for wet-end filler addition and pigment coating) and bio-wax, relative to the weight of cellulosic fibers in the paper, were about 27 wt% and about 5 wt%, respectively (see Fig. 4).
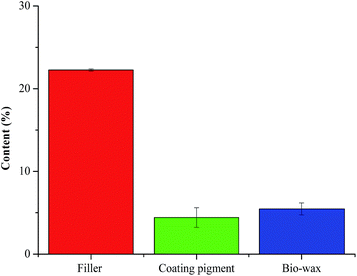 |
| Fig. 4 Contents of filler, coating pigment, and bio-wax in the superhydrophobic paper (relative to the weight of cellulosic fibers in the paper, wt%). | |
As shown in Fig. 5, the internal and surface applications of calcium carbonate particles resulted in significant changes in paper surface morphology, and the presence of these mineral particles in combination with subsequent deposition of bio-wax might would be favorable for superhydrophobicity development. The AFM images shown in Fig. 6 might be indicative of the surface roughening impact associated with the addition of mineral particles.
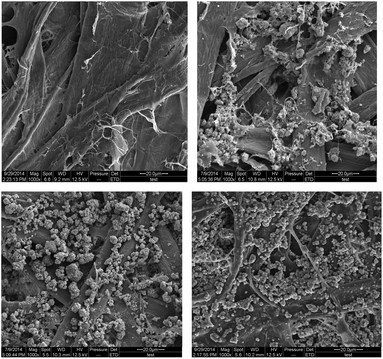 |
| Fig. 5 SEM images of paper samples: (top, left) unfilled paper; (top, right) filled paper; (bottom, left) filled and pigment-coated paper; (bottom, right) filled, pigment-coated, and bio-wax treated paper. | |
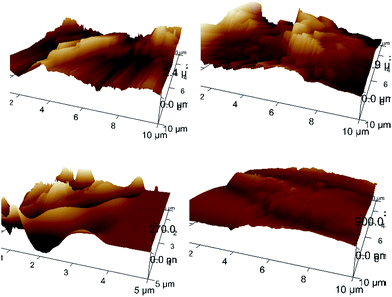 |
| Fig. 6 AFM images of paper samples: (top, left) unfilled paper; (top, right) filled paper; (bottom, left) filled and pigment-coated paper; (bottom, right) filled, pigment-coated, and bio-wax treated paper. | |
The interaction of water droplet with the paper showed its high water-repellency, and the water droplet could not roll off even when the paper was turned upside down (see Fig. 7). This indicated that the proposed process concept led to the fabrication of “sticky” superhydrophobic paper, which allows for easy control/manipulation of droplets in potential applications such as those related to microfluidics and chemical/biological assays.49,50
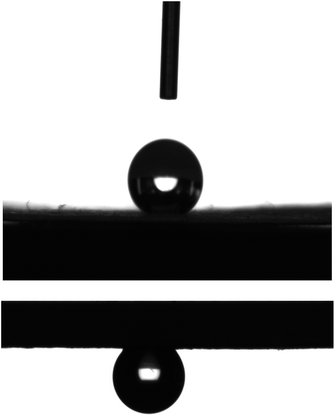 |
| Fig. 7 Interaction of superhydrophobic paper with water droplet. | |
Conclusions
The process concept involving the integration of wet-end filler addition and pigment coating with bio-wax post-treatment for converting cellulosic fibers to superhydrophobic paper was proposed and demonstrated. Pronounced synergistic impacts of these three process steps were identified. The use of precipitated calcium carbonate particles as filler/pigment in combination with paper surface hydrophobication with beeswax led to the fabrication of sticky superhydrophobic paper with a water contact angle of about 153°.
Acknowledgements
The authors would like to acknowledge support from the Fundamental Research Funds (DL12CB08) for the Central Universities of China, the National Natural Science Foundation of China (Grant no. 31100439), the Program for New Century Excellent Talents in University (NCET-12-0811), and the Program for Returned Overseas Chinese Scholars from the Ministry of Human Resources and Social Security of China. The insightful and helpful comments/suggestions from the anonymous reviewers are also greatly appreciated.
Notes and references
- A. R. P. van Heiningen, Pulp Pap. Can., 2006, 107(6), 38 CAS.
- M. Iakovlev, X. You, A. R. P. van Heiningen and H. Sixta, RSC Adv., 2014, 4, 1938 RSC.
- G. Yang, M. S. Jahan, L. Ahsan, L. Zheng and Y. Ni, Bioresour. Technol., 2013, 138, 253 CrossRef CAS PubMed.
- P. Fatehi, J. Ryan and Y. Ni, Bioresour. Technol., 2013, 131, 308 CrossRef CAS PubMed.
- M. A. Hubbe, A. Ayoub, J. S. Daystar, R. A. Venditti and J. J. Pawlak, BioResources, 2013, 8, 6556 Search PubMed.
- V. Jafari, S. R. Labafzadeh, A. King, I. Kilpeläinen, H. Sixta and A. R. P. van Heiningen, RSC Adv., 2014, 4, 17469 RSC.
- Y. Lei, X. Qian, J. Shen and X. An, Bioresour. Technol., 2013, 131, 134 CrossRef CAS PubMed.
- J. A. Sirviö, H. Liimatainen, J. Niinimäki and O. Hormi, RSC Adv., 2013, 3, 16590 RSC.
- Y. Tang, J. A. Mosseler, Z. He and Y. Ni, Ind. Eng. Chem. Res., 2014, 53, 10119 CrossRef CAS.
- H. Wang, N. Leaukosol, Z. He, G. Fei, C. Si and Y. Ni, Cellulose, 2013, 20, 1587 CrossRef CAS.
- M. Laufmann and S. Hubschmid, Mineral fillers in papermaking (Book chapter), Handbook of Paper and Board, 2nd edn, 2013, vol. 1, pp. 109–143 Search PubMed.
- Y. Zhao, Z. Hu, A. J. Ragauskas and Y. Deng, Tappi J., 2005, 4(2), 3 CAS.
- Y. Deng, P. Jones, L. McLain and A. J. Ragauskas, Tappi J., 2010, 9(4), 31 CAS.
- M. Ding and W. Liu, China Pulp Pap., 2012, 31(9), 15 CAS.
- M. A. Hubbe and R. A. Gill, TAPPI Paper Summit – Spring Technical and International Environmental Conference, 2014 Search PubMed.
- X. Huang, Z. Sun, X. Qian, J. Li and J. Shen, Ind. Eng. Chem. Res., 2014, 53, 6426 CrossRef CAS.
- J. Wang, W. Liu, H. Li, H. Wang, Z. Wang, W. Zhou and H. Liu, Chem. Eng. J., 2013, 228, 272 CrossRef CAS PubMed.
- B. Li, H. Mou, Y. Li and Y. Ni, Ind. Eng. Chem. Res., 2013, 52, 11980 CrossRef CAS.
- H. Liu, Y. Wang, Z. Yuan, X. Zou, Y. Zhou and Y. Ni, Colloids Surf., A, 2014, 452, 154 CrossRef CAS PubMed.
- T. Arbatan, L. Zhang, X.-Y. Fang and W. Shen, Chem. Eng. J., 2012, 210, 74 CrossRef CAS PubMed.
- S. Wang and L. Jiang, Adv. Mater., 2007, 19, 3423 CrossRef CAS.
- B. Balu, A. D. Berry, D. W. Hess and V. Breedveld, Lab Chip, 2009, 9, 3066 RSC.
- D. Barona and A. Amirfazli, Lab Chip, 2011, 11, 936 RSC.
- Y. Deng and H. Yang, 2008, http://www.tappi.org/content/events/08nano/papers/08nan28.pdf.
- C. Du, J. Wang, Z. Chen and D. Chen, Appl. Surf. Sci., 2014, 313, 304 CrossRef CAS PubMed.
- M. Elsharkawy, T. M. Schutzius and C. M. Megaridis, Lab Chip, 2014, 14, 1168 RSC.
- A. Geissler, F. Loyal, M. Biesalski and K. Zhang, Cellulose, 2014, 21, 357 CrossRef CAS PubMed.
- L. Li, S. Roethel, V. Breedveld and D. W. Hess, Cellulose, 2013, 20, 3219 CrossRef CAS PubMed.
- W. Zhang, P. Lu, L. Qian and H. Xiao, Chem. Eng. J., 2014, 250, 431 CrossRef CAS PubMed.
- B. Mesic, C. Kugge and L. Järnström, Tappi J., 2010, 9(11), 33 CAS.
- M. N. Mirvakili, S. G. Hatzikiriakos and P. Englezos, ACS Appl. Mater. Interfaces, 2013, 5, 9057 CAS.
- H. Ogihara, J. Xie and T. Saji, Colloids Surf., A, 2013, 434, 35 CrossRef CAS PubMed.
- M. P. Sousa and J. F. Mano, Cellulose, 2013, 20, 2185 CrossRef CAS PubMed.
- M. P. Sousa and J. F. Mano, ACS Appl. Mater. Interfaces, 2013, 5, 3731 CAS.
- X. Tang, S. Nan, T. Wang, Y. Chen, F. Yu, G. Zhang and M. Pei, RSC Adv., 2013, 3, 15571 RSC.
- H. Teisala, M. Tuominen, M. Stepien, J. Haapanen, J. M. Mäkelä, J. J. Saarinen, M. Toivakka and J. Kuusipalo, Cellulose, 2013, 20, 391 CrossRef CAS.
- O. Werner, C. Quan, C. Turner, B. Pettersson and L. Wågberg, Cellulose, 2010, 17, 187 CrossRef CAS PubMed.
- H. Yang and Y. Deng, J. Colloid Interface Sci., 2008, 325, 588 CrossRef CAS PubMed.
- Z.-Q. Yuan, H. Chen, J.-X. Tang, J.-D. Zhang, D.-J. Zhao, H.-F. Gong and P. Shi, China Pulp Pap., 2007, 26(10), 12 Search PubMed.
- X. Huang, X. Wen, J. Cheng and Z. Yang, Appl. Surf. Sci., 2012, 258, 8739 CrossRef CAS PubMed.
- J. Li, H. Wan, Y. Ye, H. Zhou and J. Chen, Appl. Surf. Sci., 2012, 261, 470 CrossRef CAS PubMed.
- H. Ogihara, J. Xie, T. Okagaki and T. Saji, Langmuir, 2012, 28, 4605 CrossRef CAS PubMed.
- C. G. Obeso, M. P. Sousa, W. Song, M. A. Rodriguez-Pérez, B. Bhushan and J. F. Mano, Colloids Surf., A, 2013, 416, 51 CrossRef PubMed.
- M. Zhang, C. Wang, S. Wang, Y. Shi and J. Li, Appl. Surf. Sci., 2012, 261, 764 CrossRef CAS PubMed.
- Z. Hu and Y. Deng, Ind. Eng. Chem. Res., 2010, 49, 5625 CrossRef CAS.
- Z. Hu, X. Zen, J. Gong and Y. Deng, Colloids Surf., A, 2009, 351, 65 CrossRef CAS PubMed.
- L. Huang, K. Chen, C. Lin, R. Yang and R. A. Gerhardt, J. Mater. Sci., 2011, 46, 2600 CrossRef CAS PubMed.
- M. Ruda, US Patent Application 20130330543, 12 Dec 2013.
- Y. Lai, F. Pan, C. Xu, H. Fuchs and L. Chi, Adv. Mater., 2013, 25, 1682 CrossRef CAS PubMed.
- L. Li, J. Tian, M. Li and W. Shen, Colloids Surf., B, 2013, 106, 176 CrossRef CAS PubMed.
|
This journal is © The Royal Society of Chemistry 2014 |
Click here to see how this site uses Cookies. View our privacy policy here.