DOI:
10.1039/C2RA20340E
(Review Article)
RSC Adv., 2012,
2, 6380-6388
Chemical treatment technologies for waste-water recycling—an overview
Received
23rd February 2012
, Accepted 2nd April 2012
First published on 4th April 2012
Abstract
The global population is increasing and because of this, the world may experience great fresh water scarcity. Our water resources are limited and, hence, water treatment and recycling methods are the only alternatives for getting fresh water in the coming decades. Therefore, there is a great need for the development of a suitable, inexpensive and rapid wastewater treatment techniques and reuse or conservation methods in the present century. The different types of water treatment and recycling techniques have been discussed in terms of their basic principles, applications, costs, maintenance and suitability. Additionally, a systematic approach to water treatment and recycling involving their understanding, evaluation and selection parameters has been presented. A brief guideline for the selection of the appropriate technologies for specific applications has been evaluated. This review adds to the global discussions on water scarcity solutions.
1. Introduction
Water, is of utmost importance in our daily lives, hence, the need to improve and preserve its quality is growing continuously. Point and non-point sources are contaminating our valuable water resources. The main water pollution sources are from industrial, domestic and agricultural activities and other environmental and global changes. The surface and ground water in many places around the world is contaminated and not fit for drinking purposes. By 2020, the global population is supposed to reach up to 7.9 billion1 and because of this the world may experience the great scarcity of fresh water.2,3
In view of this, attempts have been made to compare various water treatment and recycling technologies. Efforts have also been carried out to introduce an approach for water treatment and recycling methods. A comparison of the technologies has been presented by discussing their performance, sludge production, life period and operation. The purpose of this article is to provide guidelines for the selection of the technologies or their combinations for various applications so that one can select the exact and correct technology.
2. Water pollutants
Prior to discussing water treatment and reclamation, one should be aware about the qualitative and quantitative nature of water pollutants. Many pollutants are present in wastewater but toxicity is only observed beyond a certain limit called the permissible limit. The type of pollutants present in the wastewater depends upon the nature of the industrial, agricultural and municipal wastewater releasing activities. The different types of water pollutants may be categorized as inorganic, organic, and biological in nature. The most common inorganic water pollutants are heavy metals, which are highly toxic and carcinogenic in nature. Additionally, nitrates, sulphates, phosphates, fluorides, chlorides and oxalates also have some serious hazardous effects. The toxic organic pollutants are from pesticides which includes insecticides, herbicides, fungicides; polynuclear hydrocarbons (PAHs), phenols, polychlorinated biphenyls, halogenated aromatic hydrocarbons, formaldehyde, polybrominated biphenyls, biphenyls, detergents, oils, greases etc. In addition to these, normal hydrocarbons, alcohols, aldehydes, ketones, proteins, lignin, pharmaceuticals etc. are also found in wastewater. Different types of microbes thriving in wastewater may be responsible for different type of diseases. The harmful microbes include bacteria, fungi, algae, plankton, amoeba, viruses and other worms. These water pollutants remain either in solvated, colloidal or in suspended form.4–6
3. Wastewater treatment and recycling technologies
Wastewater treatment and reuse is an important issue and scientists are looking for inexpensive and suitable technologies. Water treatment technologies are used for three purposes i.e. water source reduction, wastewater treatment and recycling. At present, unit operations and processes are combined together to provide what is called primary, secondary and tertiary treatment. Primary treatment includes preliminary purification processes of a physical and chemical nature while secondary treatment deals with the biological treatment of wastewater. In tertiary treatment processes, wastewater (treated by primary and secondary processes) is converted into good quality water that can be used for different types of purpose, i.e. drinking, industrial, medicinal etc. supplies. In the tertiary process, up to 99% of the pollutants are removed and the water is converted into the safe quality for a specific use. In a complete water treatment plant, all these three processes are combined together for producing good quality and safe water. The complete scheme of wastewater treatment is shown in Fig. 1.
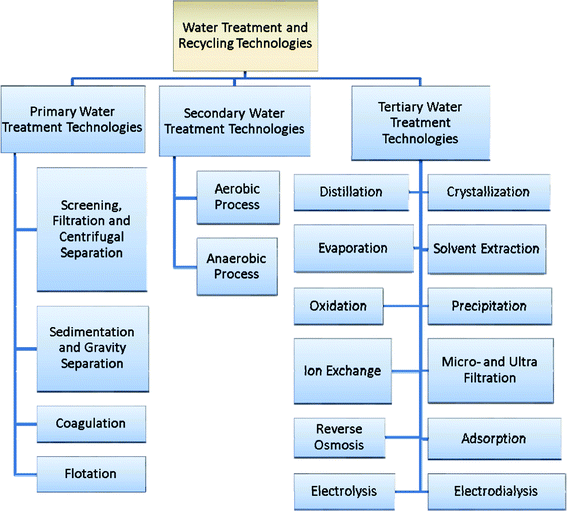 |
| Fig. 1 Illustration of the classification of chemical treatment and water recycling technologies. | |
Despite the development of various technologies for water treatment and reclamation, economic, effective and rapid water treatment and reclamation at a commercial level is still a challenging problem. The management of the removed pollutants (sludge) should be kept in mind. The systematic approach of water treatment and recycling technologies involves the understanding of the technology that includes construction and operational cost, along with the maintenance and management of removed pollutants. A comparison of these wastewater treatment and reclamation technologies in terms of their applicability, suitability and costs is presented in Table 1. Water treatment and recycling technologies have been classified (Fig. 1) under the following headings.
Table 1 Applicability, suitability and costs of wastewater treatment and reclamation technologiesb
Wastewater technologies |
Applicability |
Suitability |
Costs (US$ per one million liters of treated water) |
Rarely used.
Abbreviations: Sl: soluble, Ss: suspended, I: inorganics, O: organics, V: volatiles, B: biologicals, R: reclamation, T: treatment and Sr: source reduction.
|
Primary technologies
|
|
|
|
Screening, filtration and centrifugal |
Ss & Sl IOB |
RSrT |
25–450 |
Separation |
|
|
|
Sedimentation and gravity separation |
Ss IOB |
RSrT |
5–10 |
Coagulation |
Ss & Sl I |
RT |
25–500 |
Flotation |
Ss IOB |
RT |
5–25 |
|
Secondary technologies
|
|
|
|
Aerobic |
Sl & Ss O |
RT |
20–200 |
Anaerobic |
Sl & Ss O |
RT |
20–200 |
|
Tertiary technologies
|
|
|
|
Distillation |
Sl IOB |
RT |
15–2000 |
Crystallizationa |
Sl IO |
RSrT |
50–150 |
Evaporationa |
Sl & Ss IOB |
RSrT |
15–200 |
Solvent extraction |
Sl OV |
RSrT |
250–2500 |
Oxidationa |
Sl IO |
RSrT |
100–2000 |
Precipitationa |
Sl IO |
RT |
20–500 |
Ion Exchange |
Sl IO |
RSrT |
50–200 |
Micro- and ultra-filtration |
Sl IOB |
RSrT |
15–400 |
Reverse osmosis |
Sl IOB |
RSrT |
20–450 |
Adsorption |
Ss & Sl IOB |
RSrT |
50–150 |
Electrolysis |
Sl IO |
RSrT |
— |
Electrodialysis |
Sl IO |
RSrT |
15–400 |
3.1 Primary water treatment technologies
3.2 Secondary water treatment technologies
3.3 Tertiary water treatment technologies
3.1 Primary water treatment technologies
In this category, water is treated at the primary level using screening, filtration, centrifugation, sedimentation, coagulation, gravity and flotation methods. Normally, these methods are used when water is highly polluted. Brief descriptions of these methods are given below.
3.1.1 Screening, filtration and centrifugal separation.
The main idea of screening is to remove the solid waste present in the wastewater and it is used for the removal of pieces of cloth, paper, wood, cork, hair, fiber, kitchen refuse, fecal solids etc. from wastewater. Generally, screening is used as the very first step in a wastewater treatment operation. The screens of various sizes are used for this purpose and the size of the screen is selected as per the requirement i.e. size of the solids present in the wastewater.
In filtration process, water is passed through a medium having fine pores. Normally, a set-up with a pore size of about 0.1 to 0.5 μm is used for this purpose. It is used for the removal of suspended solids, greases, oils, bacteria etc. Different filters, such as membranes and cartridges can be used. The filtration process can be used to remove solids of size below 100 mg l−1 and to remove oil of 25 mg l−1 which can be reduced by up to 99%. The filtration process is utilized for water treatment. Water produced by filtration is used for adsorption, ion exchange or membrane separation processes. Besides, potable water is produced by filtration systems. The cost of filtration varies from 25 to 450 US$ per million liters of treated water.3,7
Centrifugal separation is used to remove suspended non-colloidal solids (size up to 1 μm). The wastewater is applied to centrifugal devices and rotated at different speeds and the solids (sludges) are separated and discharged. The extent of separation of suspended solids is directly proportional to their densities. In addition to this, the speed of the centrifugal machine is also responsible for the removal of suspended solids. Applications include the source reduction and separation of oils and greases. The different types of centrifugal machines available and in use are solid-bowl, basket type, counter flow and counter current flow. The cost of the wastewater treatment ranges 25 to 450 US$ per million liters of treated water.3,7
3.1.2 Sedimentation and gravity separation.
In this process, the suspended solids, grits and silts are removed by allowing water to be undisturbed/semi-disturbed for different time intervals in various types of tank. The suspended solids settle under the influence of gravity.3,7–9 The settling time depends upon the size and density of the solids or the velocity if the water is in motion. Sometimes, alums are added to augment the sedimentation process. Gravity separation can reduce the suspended solids by up to 60% only. Generally, sedimentation is carried out prior to conventional treatment processes. It is very useful method for the treatment of effluents obtained from the paper and refinery industries. Water treated in this process is used for industrial water supply, water for ion exchange and membrane processes. The technique is also used for source reduction. The cost of the treated water varies from 5 to 10 US$ per million liters.
3.1.3 Coagulation.
Sometimes, the suspended solids do not settle down under the sedimentation and gravity method and, hence, non-settlable solids are allowed to settle by the addition of certain chemicals, this process is called as coagulation.3,10 Alum, starch, iron materials, activated silica and aluminum salts are available for use. In addition, synthetic cationic, anionic and non-ionic polymers are effective but are usually more costly than natural coagulants. pH, temperature and contact time are most important controlling factors in the coagulation process. In biological treatment units, microbes and any organics floating in the water are removed by the addition of certain coagulants. It is the main component of wastewater treatment units and the applications include wastewater treatment, recycling, and removal of pollutants.
3.1.4 Flotation.
Flotation is a common and essential component of a conventional water treatment plant. The suspended solids, oils, greases, biological solids etc. are removed by adhering them with either air or gas in the flotation process.3,11 The solids get adhered to gas or air and form agglomerates, which in turn accumulate at the waters surface and which can ultimately be skimmed off easily. Some chemicals, such as alum, activated silica etc. help in the flotation process. Compressed air is allowed to pass through the water, which helps in the flotation process. Electro-flotation (electro-flocculation) has been used as an effective process for water treatment and recycling purposes. Up to 75% of suspended solids are removed while up to 99% of oil and grease are removed by this process. It is an effective method for the treatment of wastewater from the paper and refinery industries. The cost varies from 5 to 25 US$ per million liters of treated water.3,12
3.2. Secondary water treatment technologies
Secondary water treatment includes biological routes for the removal of soluble and insoluble pollutants by microbes.3,13,14 Water is circulated in a reactor that maintains a high concentration of microbes. The microbes, usually bacterial and fungal strains, convert the organic matter into water, carbon dioxide and ammonia gas.15–19 Sometimes, the organic matter is converted into other products such as alcohol, glucose, nitrate etc. Additionally, the microbes detoxify toxic inorganic matter. The wastewater should be then free from toxic organics and inorganics. The maximum concentrations of total dissolved solids (TDS), heavy metals, cyanides, phenols and oil should not exceed by 16
000, 2.0, 60.0, 140, and 50 mg l−1 respectively. The biological treatment includes the aerobic and anaerobic digestion of wastewater. Depending on the materials used, the cost of biological treatment varies between 20 and 200 US$ per million liters.
3.2.1 Aerobic processes.
When air or oxygen is freely available in dissolved form in wastewater then the biodegradable organic matter undergos aerobic decomposition, caused by aerobic and facultative bacteria.20,21 The extent of the process depends on the availability of oxygen, retention time, temperature and the biological activities of the bacteria. Besides, the rate of the biological oxidation of organic pollutants may be increased by the addition of some chemicals required for bacterial growth. The technique is effective for the removal of biological oxygen demand (BOD), chemical oxygen demand (COD), dissolved and suspended organics, volatile organics, nitrates, phosphates etc. The concentration of biodegradable organics can be reduced by up to 90%. The disadvantage of the method is the production of a large quantity of bio-solids, which require further costly treatment and management. The aerobic process is carried out by trickling filters or activated sludge processes or oxidation ponds.
A simplified representation of aerobic decomposition is given by the following equation.
| Organic matter + O2 + Bacteria → CO2 + H2O + Bacteria + Byproducts | (1) |
3.2.2 Anaerobic process.
If free dissolved oxygen is not available in the wastewater then anaerobic decomposition, called putrefaction, occurs. Anaerobic and facultative bacteria convert the complex organic matter into simpler organic compounds based on nitrogen, carbon and sulphur. The important gases evolved in this process are nitrogen, ammonia, hydrogen sulphide and methane. This method is used to reduce the biological load of wastewater.22–27
The anaerobic process is represented by the following equation.
| Organic matter + Bacteria → CO2 + CH4 + Bacteria + Byproducts | (2) |
3.3. Tertiary water treatment technologies
Tertiary water treatment technologies are very important in wastewater treatment strategy as these are used to obtain safe water for human consumption. The techniques used for this purpose are distillation, crystallization, evaporation, solvent extraction, oxidation, coagulation, precipitation, electrolysis, electrodialysis, ion exchange, reverse osmosis and adsorption. These methods are described below.
3.3.1 Distillation.
In the distillation process, water is purified by heating it up to 100 °C (boiling point) at which liquid water is vaporized leaving behind the pollutants.28 The vapors thus generated are cooled into liquid water. The wastewater should be free from volatile impurities and water produced by this technique is about 99% free from impurities. Various types of boilers with multistage and double distillation are used in this process. The size of the boilers depends on the water quantity requirements. The applications of distillation in water treatment and reclamation include water supplies in laboratories and medicinal preparations. In addition, distillation is an effective tool for the preparation of potable water from the sea and brackish water. The cost of water production varies between 15 and 2000 US$ per million liters.
3.3.2 Crystallization.
Crystallization is a process in which pollutants are removed by raising their concentrations up to a point where they start to crystallize out. This situation is created either by evaporation, by lowering the temperature of the water or by mixing other solvents. It is useful for the treatment of wastewater with high concentrations of TDS including soluble organics and inorganics. During this process, the other constituents like bicarbonate, ammonia, sulfite etc. break down into various gases and, therefore, crystallization, sometimes, may be used for pH control. Generally, crystallization is used for the wastewater released by cooling towers, coal and gas fired boilers, and the paper and dying industries. It is also used for source reduction. Forced circulation, draft tube baffle, surface cooled crystallizers and fluidized suspensions are used for crystallization. The treated water in this process is of good quality and its cost ranges from 50 to 150 US$ per million liters.29
3.3.3 Evaporation.
Evaporation is a natural process and, is generally, used to reduce the waste liquid volume but in modern developments it has been used as water treatment method.28,30 Water surface molecules escape from the surface under the natural conditions and the escaped molecules are collected in the form of pure liquid water. Mechanical evaporators have also been used for water recycling process. Sometimes vacuum evaporation has been used for the wastewater recycling. Evaporation is effective for the removal of inorganic and organic (except volatile organic) contaminants and it works even at very high concentrations (about 10%) of pollutants. Foaming, scaling and fouling along with the presence of suspended solids and carbonates are the major problems associated with this technique as they create a maintenance problem. Evaporation applications include the treatment of wastewater containing fertilizer, petroleum, and from the pharmaceutical and food processing industries. It is also used for the water supply to ion exchangers and membrane processes. Water from evaporation has been used in cooling in towers and boilers. It can be used as a technique of water source reduction. The cost of water production varies between 15 and 200 US$ per million liters.
3.3.4 Solvent extraction.
Organic solvents, immiscible with water and having the capacity to dissolve pollutants, are added to wastewater for the removal of pollutants; this technique is called solvent extraction.31,32 The most commonly used solvents are benzene, hexane, acetone and other hydrocarbons. Sometimes, a small quantity of the solvent remains mixed with the water, which is recovered by using the distillation technique. The technique is only effective in removing organics, oils and greases. However, certain metal ions and actinide chemicals may be removed by this method. It is used for recycling and water treatment. It has been used for water source reduction too. The cost varies between 250 and 2500 US$ per million liters of clean water.
3.3.5 Oxidation.
In chemical oxidation, organic compounds are oxidized into water and carbon dioxide or some other products such as alcohols, aldehydes, ketones and carboxylic acids which are easily biodegradable.33 Chemical oxidation is carried out by potassium permanganate, chlorine, ozone, H2O2, Fenton's reagent (H2O2 and Fe catalyst) and chlorine dioxides.34–41 The rate of chemical oxidation depends on the nature of oxidants and pollutants. Besides, pH, temperature and presence of catalyst etc. also play a crucial role in the rate of chemical oxidation. By this method, pollutants such as ammonia, phenols, dyes, hydrocarbons and other organic pollutants may be removed. The cost of water production ranges from 100 to 2000 US$ million liters of clean water.
3.3.6 Advanced oxidation process.
A single oxidation system as stated above is sometimes not sufficient for the total decomposition of organic pollutants present in waste water. Advanced Oxidation Processes (AOPs) are processes involving the simultaneous use of more than one oxidation process, and involve the accelerated production of the highly reactive hydroxyl free radical.42–44 These processes include techniques like Fenton's reagent oxidation, ultra violet (UV) photolysis and sonolysis, and are capable of degrading the organic pollutants at ambient temperature and pressure. The main advantage of the advanced oxidation process is that organic contaminants are commonly oxidized to CO2. A wide variety of advanced oxidation processes are available like chemical oxidation processes using ozone,45 combined ozone and peroxide,46 ultra violet enhanced oxidation such as UV/Fenton or photo-Fenton,47,48 UV/hydrogen peroxide, UV/ozone,49 UV/air wet air oxidation and catalytic wet air oxidation (where air is used as the oxidant).
Photocatalysis is also one of a series of advanced oxidation processes for organic pollutant degradation.50–54 In photocatalysis, light energy from a light source (UV or solar) excites an electron from the valence band of the photocatalyst to the conduction band with a series of reactions which results in the formation of hydroxyl radicals. The hydroxyl radicals have high oxidizing potential and therefore can attack most organic pollutants causing oxidation. Various chalcogenides (oxides such as TiO2, ZnO, ZrO2, CeO2, etc. or sulfides such as CdS, ZnS, etc.) have been used as photocatalysts in the photocatalytic process and the process is found suitable for a wide range of organic pollutants.55–58 Sonolysis, i.e., use of ultrasonic waves has been used for the decolorization and degradation of organic pollutants. The mechanism proposed for the sonochemical process is usually based on the formation of short-lived radical species generated in violent cavitation events.59
3.3.7 Precipitation.
In precipitation the dissolved contaminants are converted into solid precipitates by reducing their solubilities and the precipitates are skimmed off easily from the waters surface.60 It is effective for the removal of metal ions and organics but the presence of oil and grease may cause a problem in precipitation. The solubility of the dissolved pollutants is decreased either by adding some chemicals or by lowering the temperature of the water. Adding some organic solvents to the water may also reduce solubility of the contaminant but this technique is costly at a commercial level. These chemicals react with the soluble pollutants to form precipitates. The most commonly used chemicals for this purpose are alum, sodium bicarbonates, ferric chloride, ferrous sulphate and lime. pH and temperature are the main controlling factors for the precipitation process. The removal of about 60% of the pollutants can be achieved by the precipitation. The applications of this method include wastewater treatment from the nickel and chromium plating industries and water recycling. The specific applications include water softening and removal of heavy metals and phosphate from water. The major problem associated with precipitation is the management of the large volume of sludge produced. The cost varies from 20 to 500 US$ per million liters of treated water.
3.3.8 Ion exchange.
Toxic ions present in wastewater are exchanged with the non-toxic ions from a solid material called an ion exchanger.61–65 Ion exchangers are of two types i.e. cation and anion exchangers which have the capacity to exchange cations and anions respectively. Ion exchangers are resins of natural or synthetic origin having active sites on their surfaces. The most commonly used ion exchangers are sodium silicates, zeolites, polystyrene sulfonic acid, and acrylic and metha-acrylic resins. It is a reversible process and requires low energy contents. Ion exchange is used for the removal of low concentrations of inorganics and organics (up to 250 mg l−1). The concentration of organics and inorganics can be reduced by up to 95%. Applications include the production of potable water, water for industries, pharmacy, softening, fossil fuels, different industries. It has also been used for source reduction purposes. Sometimes, the pre-treatment of the water is required; if oil, grease and high concentrations of organics and inorganics are present. One million liters of wastewater is treated by investing 50 to 200 US$.
3.3.9 Micro- and ultra-filtration.
Micro-filtration is required for the removal of particles of 0.04 to 1 μm in size (Fig. 2) provided the total suspended solids do not exceed 100 mg l−1. The filters used in this process are made of cotton, wool, rayon, cellulose, fiberglass, polypropylene, acrylics, nylon, asbestos and fluorated hydrocarbon polymers. These are arranged in different fashions such as tubular, disc, plates, spiral, and hollow fibers. The life of cartridges varies from 5 to 8 years depending upon the concentration of the dissolved solids. The pre-removal of suspended solids is an important factor for promoting the the long life of filters. In this method, the operational pressure is about 1–3 bar.66–70 The cost of the treated water varies from 15 to 400 US$ per million liters.
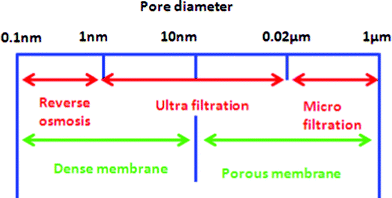 |
| Fig. 2 Filtration spectrum; micro-, ultra-filtration and reverse osmosis. | |
3.3.10 Reverse osmosis.
Reverse osmosis or hyper-filtration, is the method of water purification that relies on the membranes' development technology.71–75 It has received great attention as the best water recycling process. A pressure greater than the osmotic pressure is applied. Various membranes are used in this process such as cellulose, polyether, and polyamide. To achieve the required filtration, membranes are arranged in tubular, disc, plate, spiral, and hollow fiber forms. For pollutant removal, the partition coefficients of the solutes and the free energy of interaction between the water and membrane are important parameters. Additionally, pH, pressure, size and the molecular weight of the solute, and the time of operation are considerable factors.
Reverse osmosis has been used as a separation and concentration technique at macro and micro levels for the removal of large, non-polar, ionic and toxic soluble pollutants. The effectiveness and the application of RO on a large scale is based on the fact that the total dissolved solids, organic dissolved matter and bacteria can be removed by up to 99%. Reverse osmosis is used for the treatment of wastewater from sanitary waste, municipal leachates, and different industries.76,77 Besides, the rejection of bacteria, virus and other microbes is one hundred percent and, therefore, it is used in the preparation of ultra pure water for use in pharmacy, medicines and electronics. In addition, it has been used for the purpose of source reduction. RO is today's most economic process for potable water production from saline water.
The working efficiency of a RO membrane is expressed in terms of percentage rejection (PR%) or the removal ratio of solutes and expressed as:
or
where,
CF is the molar concentration of solute in the feed water,
CP is the molar concentration of solute in the permeate (filtrate) and
E is the membrane working efficiency.
The performance of the membrane process is also measured by permeate flux. In desalination and wastewater treatment processes, the solvent or permeate flux is referred to the water and defined as the volume of permeate flux produced per unit membrane area for a time interval and is given by the following equation.
where MF is the membrane flux,
VP is the volume of permeate over time
t, and
SA is the surface area of the membrane.
Separation of pollutants in RO depends on the basis of partition coefficients of solutes between water and membrane involving the free energy of interaction between water and membrane sites. The percentage of rejection is directly proportional to the number of carbon atoms or the molecular weights of organic/inorganic species but this was not found to be a complete description because of the geometry of the molecule, i.e., steric configuration and branching overshadow the former properties.
The design of reverse osmosis units plays a role to achieve efficient seawater desalination. Fig. 3 demonstrates the basic scheme of desalination by reverse osmosis in a system that does not apply energy recovery or pressure conversion devices. Membranes can be connected in series as shown in Fig. 4. The flow rate of water through the membrane is given as:
Frate is the flow rate;
Kf is the flow rate factor which is determined by the properties of the membrane and its area;
Ppump is the pressure generated by the pump and controlled by the pressure controller;
Ps is the osmotic pressure of the concentrated salt water. It has to be noted that the energy in such systems can be recovered with a turbine and an auxiliary pump.
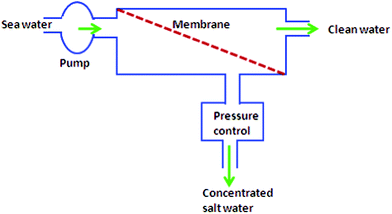 |
| Fig. 3 Basic design of reverse osmosis. | |
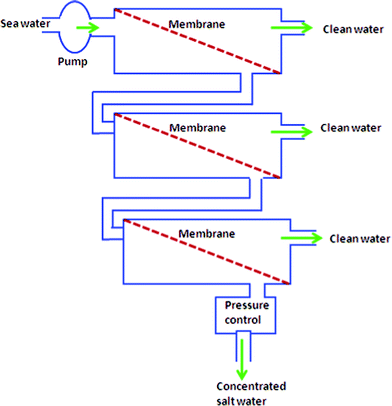 |
| Fig. 4 Modules of connecting membranes in series. | |
The life of RO membranes has been considered to be two to five years depending upon the nature of the wastewater being treated. The flux and the quality of the permeate may decrease over a long period of time due to membrane fouling. After a long period of time, humic acids, bacterial slimes or hardness scales may accumulate on the RO membranes. Phenols have also been found to clog the membranes. To increase the efficiency and life of the membrane, pre-treatment is necessary to minimize the concentration of colloidal and dispersed solids. Physico-chemical coagulation with lime has been used to minimize colloids, turbidity, dispersed oil phases, metal ions and suspended matters. Sodium hydroxide solution (pH 9–11) has been used to clean RO membranes in case of silica and sulphate fouling.78,79 Besides, silica can also be removed from membranes by ion retarding resins that has a high affinity for strong acids, together with conversion of the weak acid [Si(OH)4] into much stronger acid (H2SiF6). The bacterial inhibitor solutions are circulated (to check the bacterial growth) in to RO tubules or discs before stopping the process for a long period.79
3.3.11 Adsorption.
Adsorption80 is a surface phenomenon and defined as the increase in the concentration of a particular component at the surface or interface between two phases. There are some parameters, such as pH, temperature, concentration of pollutants, contact time, particle size of the adsorbent and nature of adsorbents and the pollutants that affect the adsorption efficiency. Pre-filtration is required due to the presence of suspended particles and oils that reduce the efficiency of the adsorption. Different types of adsorbents are used in adsorption process. Most commonly used adsorbents are activated carbon, fly ashes, metal oxides, zeolites, moss, biomass, and geothites. Recently, nanomaterials, such as carbon nanotubes and composites of carbon nanotubes81–90 have been utilized for the removal of heavy metals and organic pollutants. At an industrial level, pollutants are removed from wastewater by using the columns and contractors filled with the required adsorbents. First all the adsorption is carried out in a batch process and the conditions are optimized. The developed and optimized conditions (batch process) are transferred to the column and contractor experiments. Well-known models of Langmuir, Freundlich, Hutchins, Reichenberg, etc. verify the feasibility of the adsorption. The extent of the pollutant removal varies from 90 to 99%. Adsorption is used for source reduction, wastewater treatment and reclamation for potable, industrial and other purposes. The basic problems associated with adsorption are the regeneration of columns and column life. Moreover, the management of the exhausted adsorbent is also a challenging issue for scientists. The cost of the treated water ranges 50 to 150 US$ per million liters.
3.3.12 Electrolysis.
Electrolysis is a technique in which soluble materials are either deposited or decomposed on the surface of the electrodes by electrochemical redox reaction is called electrolysis.91–94 In this method, most metal ions are deposited on the electrode surface while organics are decomposed into carbon dioxide and water or in some other product, which are low or non-toxic.95,96 Besides, it has also been used for the removal of turbidity and color from wastewater. This method is effective for the removal of TDS below 200 mg l−1 and, therefore, requires the pre-treatment of the wastewater. The factors that control the process are pH, temperature, amount of current applied and contact time. Electrolysis, as the technique of wastewater treatment, is not developed completely so far and is still in its development stage. It has been rarely used at a commercial level for wastewater treatment. However, its applications include the treatment of some industrial effluents especially those enriched with metal ions and some organics. It may be used as a water source reduction technique. The advantages of this technique comprise the further utilization of the deposited metal ions without any waste management problems.
3.3.13 Electrodialysis.
Water soluble ions are allowed to pass through ion selective semi-permeable membranes under the influence of electric current.97,98 The ion selective membranes are made of ion exchange material and are selective in nature. They may be cation or anion exchangers which permits the out flow of cations and anions respectively. The process is operated either in a continuous or batch mode having two electrodes on which a voltage is applied. To obtain the desired degree of demineralization, the membranes are arranged either in a parallel or series fashion.99,100 The dissolved solids removal depends on pH, temperature, amount of current applied, nature of pollutants, selectivities of the membranes, wastewater flow rate, fouling and scaling of wastewater and number and configuration of stages. The applications include the production of potable water from brackish water. Besides, this technique has been used for water source reduction. A maximum concentration of 200 mg l−1 of TDS can be reduced up to 90% by electrodialysis. The membrane fouling occurred as in case of reverse osmosis. To solve such problem and to enhance the flux, carbon nanotubes have been involved in the composite membranes.87,101
4. Selection of wastewater technologies
The selection of the treatment technologies depends on the type of the wastewater and the requirements (economy aspect). Highly polluted water having color and containing solid waste is first treated with primary and secondary processes followed by the tertiary water treatment technologies. If the BOD is negligible then a secondary process is not required. If the water is colorless without any solids and is polluted due to inorganic, organic and biological pollutants, then only tertiary water treatment is required. Generally, groundwater is polluted by toxic metal ions and anions and only tertiary water technologies are required for its treatment. Contrarily, surface water contaminated by inorganic, organic and biological pollutants requires secondary and tertiary treatment methods. Generally, wastewater is highly polluted and it may be colored with solid waste containing inorganic, organic, biological pollutants, which requires a good hyphenation of primary, secondary and tertiary treatment technologies. The choice of the tertiary water treatment technologies depends on the types of the pollutants present in the water and the optimum selection can be done by considering the above cited discussions. A brief presentation of the selection of water treatment technologies is given in Fig. 1.
5. Waste management
It is clear from the above discussion that waste is generated in every water purification and recycling technology. Therefore, waste management is very important from the point of view of the environment and health. This is because, generally, waste products are toxic. The waste generated may enter water resources and contaminant it again. A large amount of solid waste is generated in screening, filtration, centrifugal separation, sedimentation and gravity separation, coagulation, flotation, aerobic process, anaerobic process, evaporation and precipitation processes. Micro- and ultra-filtration and reverse osmosis produce water containing a high concentration of pollutants. On the other hand some gases are produced in electrolysis and the anaerobic processes which are dangerous to the environment. In adsorption, the production of exhaustive adsorbents is quite high. Many methods have been developed and used for the management of waste products generated during water treatment processes. The most important waste management method is the recycling of waste products into useful products such as fertilizers, fillers, building material etc. Some toxic waste products have been burnt and their ash used as fertilizers. Suggestions have also been made to bury the waste products under ground in airtight iron or plastic containers. Nowadays, fly ash, red mud, sand etc. are being used as the useful and economic adsorbents for the removal of pollutants from water. The large quantities of these exhausted adsorbents produced have been successfully used as fillers and building materials.
6. Conclusions
The water treatment technologies discussed in this article differ from each other in terms of their principles, scope of application, speed and economy. The feasibility of any water recycling technique at a commercial level depends on the cost of construction, maintenance and operation. Sludge management is also an important factor for the selection of a technology. Taking all these points into consideration, adsorption is considered the best and most universal technique as it is used for the removal of a wide variety of organic and inorganic pollutants. It is also a rapid process with a low cost of construction, maintenance and operation. Reverse osmosis is widely used and is a popular technique as the quality of water is good but the cost of construction and maintenance is comparatively high. Other techniques such as micro- and ultra-filtration, ion exchange, electrodialysis, solvent extraction, distillation etc. are used for specific purposes but their use is restricted at potable and industrial levels. The total cost of the treated water comprises the expenditure involved in the primary, secondary and tertiary process and, therefore, there is a great need to hyphenate all these process in an economic way.
References
-
T. Dyson, Population and food: global trends and future prospects, Routledge. London, 1996 Search PubMed.
-
R. L. Droste, Theory and Practice of Water and Wastewater Treatment,John Wiley & Sons, Inc., New York, 1997 Search PubMed.
-
L. B. Franklin, Wastewater Engineering: Treatment. Disposal and Reuse,McGraw Hill, Inc., New York, 1991 Search PubMed.
-
V. Gaston, International Regulatory Aspects for Chemicals,Vol. I, CRC Press, Inc., New York, 1979 Search PubMed.
-
D. H. Hutson and T. R. Roberts, Environmental Fate of Pesticides,Vol. 7, John Wiley & Sons, New York, 1990 Search PubMed.
-
D. Z. John, Hand Book of Drinking Water Quality: Standards and Controls,Van Nostrand Reinhold, New York, 1990 Search PubMed.
-
N. Nemerow and A. Dasgupta, Industrial and Hazardous Waste Treatment,Van Nostrand Reinhold, New York, 1991 Search PubMed.
-
N. P. Cheremisinoff, Handbook of Water and Wastewater Treatment Technologies,Butterworth-Heinemann, Boston, 2002 Search PubMed.
- O. Marmagne and C. Coste, Am. Dyest. Rep., 1996, 85, 15–20 CAS.
- A. A. Latifossglu, G. Surucu and M. Evirgen, Water Pollut. IV: Model., Meas., Predict., 4th Int. Conf., 1997, 733–742 CAS.
- I. O. Sinev, O. P. Sinev and S. N. Linevich, Izobreteniya, 1997, 26, 369–370 Search PubMed.
- T. Clark and T. Stephenson, Environ. Technol., 1998, 19, 579–590 CrossRef CAS.
- M. T. Kato, J. A. Field and G. Lettinga, Water Sci. Technol., 1997, 36, 375–382 CrossRef CAS.
- G. A. Zinkus, W. D. Byers and W. W. Doerr, Chem. Eng. Prog., 1998, 94, 19–31 CAS.
- C. I. Pearce, J. R. Lloyd and J. T. Guthrie, Dyes Pigm., 2003, 58, 179–196 CrossRef CAS.
- Y. Fu and T. Viraraghavan, Bioresour. Technol., 2001, 79, 251–262 CrossRef CAS.
- A. R. Pendashteh, A. Fakhru'L-Razi, T. G. Chuah, A. B. D. Radiah, S. S. Madaeni and Z. A. Zurina, Environ. Toxicol., 2010, 31, 1229–1239 CAS.
- A. Joss, E. Keller, A. C. Alder, A. Göbel, C. S. McArdell, T. Ternes and H. Siegrist, Water Res., 2005, 39, 3139–3152 CrossRef CAS.
- A. Joss, S. Zabczynski, A. Göbel, B. Hoffmann, D. Löffler, C. S. McArdell, T. A. Ternes and H. Siegrist, Water Res., 2006, 40, 1686–1696 CrossRef CAS.
- B. E. Barragan, C. Costa and M. Carmen Marquez, Dyes Pigm., 2007, 75, 73–81 CrossRef CAS.
- Q. Tian and J. Chen, Journal of Dong Hua University, 2000, 17, 61–63 CAS.
- C. Fux, M. Boehler, P. Huber, I. Brunner and H. Siegrist, J. Biotechnol., 2002, 99, 295–306 CrossRef CAS.
- F. P. Van Der Zee and S. Villaverde, Water Res., 2005, 39, 1425–1440 CrossRef CAS.
- O. Bernard, Z. Hadj-Sadok, D. Dochain, A. Genovesi and J. P. Steyer, Biotechnol. Bioeng., 2001, 75, 424–438 CrossRef CAS.
- N. Bernet, N. Delgenes, J. C. Akunna, J. P. Delgenes and R. Moletta, Water Res., 2000, 34, 611–619 CrossRef CAS.
- A. M. Talarposhti, T. Donnelly and G. K. Anderson, Water Res., 2001, 35, 425–432 CrossRef CAS.
- S. Venkata Mohan, V. Lalit Babu and P. N. Sarma, Enzyme Microb. Technol., 2007, 41, 506–515 CrossRef.
-
P. R. Bom, PCT Int. Appl., 1998 Search PubMed, WO 9825679 (Cl. B01D1).
- F. Vander Ham, G. J. Witkamp, J. deGrauw and G. M. van Rosmalen, Chem. Eng. Process., 1998, 37, 207–213 CrossRef CAS.
- G. A. Zinkus, W. D. Byers and W. W. Doerr, Chem. Eng. Prog., 1998, 94, 19–31 CAS.
- J. W. Ahn and J. G. Ahn, Chawn Risaikring, 1997, 6, 48–54 CAS.
- D. W. Hall and A. S. Joseph, Environ. Prog., 1990, 9, 98–105 CrossRef CAS.
- R. J. Bigda, Chem. Eng. Prog., 1995, 89, 62–66 Search PubMed.
- P. R. Gogate and A. B. Pandit, Adv. Environ. Res., 2004, 8, 501–551 CrossRef CAS.
- T. A. Ternes, J. Stüber, N. Herrmann, D. McDowell, A. Ried, M. Kampmann and B. Teiser, Water Res., 2003, 37, 1976–1982 CrossRef CAS.
- M. M. Huber, A. Göbel, A. Joss, N. Hermann, D. Löffler, C. S. McArdell, A. Ried and U. Von Gunten, Environ. Sci. Technol., 2005, 39, 4290–4299 CrossRef CAS.
- M. Pérez, F. Torrades, X. Domènech and J. Peral, Water Res., 2002, 36, 2703–2710 CrossRef.
- L. Szpyrkowicz, C. Juzzolino and S. N. Kaul, Water Res., 2001, 35, 2129–2136 CrossRef CAS.
- V. Kavitha and K. Palanivelu, Chemosphere, 2004, 55, 1235–1243 CrossRef CAS.
- J. A. Zazo, J. A. Casas, A. F. Mohedano, M. A. Gilarranz and J. J. Rodríguez, Environ. Sci. Technol., 2005, 39, 9295–9302 CrossRef CAS.
- P. Bautista, A. F. Mohedano, J. A. Casas, J. A. Zazo and J. J. Rodriguez, J. Chem. Technol. Biotechnol., 2008, 83, 1323–1338 CrossRef CAS.
- J. Yoon, Y. Lee and S. Kim, Water Sci. Technol., 2001, 44, 15–21 CAS.
- C. Comninellis, A. Kapalka, S. Malato, S. A. Parsons, I. Poulios and D. Mantzavinos, J. Chem. Technol. Biotechnol., 2008, 83, 769–776 CrossRef CAS.
- M. N. Chong, B. Jin, C. W. K. Chow and C. Saint, Water Res., 2010, 44, 2997–3027 CrossRef CAS.
- J. J. Wu, C.-C. Wu, H.-W. Ma and C.-C. Chang, Chemosphere, 2004, 54, 997–1003 CrossRef CAS.
- I. A. Balciolu and M. Ötker, Chemosphere, 2003, 50, 85–95 CrossRef.
- M. Y. Ghaly, G. Härtel, R. Mayer and R. Haseneder, Waste Manage., 2001, 21, 41–47 CrossRef CAS.
- W. Gernjak, T. Krutzler, A. Glaser, S. Malato, J. Caceres, R. Bauer and A. R. Fernández-Alba, Chemosphere, 2003, 50, 71–78 CrossRef CAS.
- S. Esplugas, D. M. Bila, L. G. T. Krause and M. Dezotti, J. Hazard. Mater., 2007, 149, 631–642 CrossRef CAS.
- J. A. Herrera Melián, J. M. Doña Rodríguez, A. Viera Suárez, E. Tello Rendón, C. Valdés Do Campo, J. Arana and J. Pérez Peña, Chemosphere, 2000, 41, 323–327 CrossRef.
- K. Kabra, R. Chaudhary and R. L. Sawhney, Ind. Eng. Chem. Res., 2004, 43, 7683–7696 CrossRef CAS.
- D. Robert and S. Malato, Sci. Total Environ., 2002, 291, 85–97 CrossRef CAS.
- L. Prieto-Rodriguez, S. Miralles-Cuevas, I. Oller, A. Agüera, G. L. Puma and S. Malato, J. Hazard. Mater., 2012, 211–212, 131–137 CrossRef CAS.
- H. Lachheb, E. Puzenat, A. Houas, M. Ksibi, E. Elaloui, C. Guillard and J.-M. Herrmann, Appl. Catal., B, 2002, 39, 75–90 CrossRef CAS.
- X. Z. Li and F. B. Li, Environ. Sci. Technol., 2001, 35, 2381–2387 CrossRef CAS.
- B. Neppolian, H. C. Choi, S. Sakthivel, B. Arabindoo and V. Murugesan, J. Hazard. Mater., 2002, 89, 303–317 CrossRef CAS.
- M. Cristina Yeber, J. Rodríguez, J. Freer, N. Durán and H. D. Mansilla, Chemosphere, 2000, 41, 1193–1197 CrossRef.
- X. Z. Li, H. Liu, L. F. Cheng and H. J. Tong, Environ. Sci. Technol., 2003, 37, 3989–3994 CrossRef CAS.
- E. Naffrechoux, S. Chanoux, C. Petrier and J. Suptil, Ultrason. Sonochem., 2000, 7, 255–259 CrossRef CAS.
-
Y. Nagasaki, Jpn.Kokai Tokyo Jp., 1998 Search PubMed, 1057967 [9857967] (Cl. C02F1).
-
J. T. McNulty, in Ion Exchange Technology, ed. D. Naden, M. Streat, Ellis Norwood Ltd., London, 1984 Search PubMed.
- A. Dabrowski, Z. Hubicki, P. Podkościelny and E. Robens, Chemosphere, 2004, 56, 91–106 CrossRef CAS.
- T. Xu, J. Membr. Sci., 2005, 263, 1–29 CrossRef CAS.
- M. Vaca Mier, R. Lopez Callejas, R. Gehr, B. E. Jimenez Cisneros and P. J. J. Alvarez, Water Res., 2001, 35, 373–378 CrossRef CAS.
- S. Rengaraj and S.-H. Moon, Water Res., 2002, 36, 1783–1793 CrossRef CAS.
-
W. Lorch, Hand Book of Water purification, 2nd ed., Ellis Horwood Ltd., London, 1981 Search PubMed.
- W. J. Koros, Chem. Eng. Prog., 1995, 91, 68–81 CAS.
- A. Bick, G. Oron, L. Gilierman and Y. Manor, Water Sci. Technol.: Water Supply, 2003, 3, 379–384 CAS.
- Z. Wu, S. Chen and Y. Zhao, Shanghai Huanjing Kexue, 1997, 16, 29–31 CAS.
- R. A. Mamigonyan and Yu. V. Gutin, Khim. Neftegazov. Mashinostr., 2003, 8, 5–7 Search PubMed.
- C. Bellona, J. E. Drewes, P. Xu and G. Amy, Water Res., 2004, 38, 2795–2809 CrossRef CAS.
- C. Fritzmann, J. Löwenberg, T. Wintgens and T. Melin, Desalination, 2007, 216, 1–76 CrossRef CAS.
- L. F. Greenlee, D. F. Lawler, B. D. Freeman, B. Marrot and P. Moulin, Water Res., 2009, 43, 2317–2348 CrossRef CAS.
- H. Ozaki and H. Li, Water Res., 2002, 36, 123–130 CrossRef CAS.
- C. Y. Tang, Q. S. Fu, A. P. Robertson, C. S. Criddle and J. O. Leckie, Environ. Sci. Technol., 2006, 40, 7343–7349 CrossRef CAS.
-
B. Weber, F. Holz, in Effective Industrial Membrane Processes: Benefits and Opportunities, ed. M. K. Turner, Elsevier Publ. Ltd., Essex, 1991 Search PubMed.
-
A. R. Williams, in Effective Industrial Membrane Processes: Benefits and Opportunities, ed. M. K. Turner, Elsevier Publ. Ltd., Essex, 1991 Search PubMed.
- B. Culkin and A. Plotkin, Chem. Eng. Prog., 1998, 94, 29–33 CAS.
- L. Sun, E. M. Perdue and J. F. McCarthy, Water Res., 1995, 29, 1471–1477 CrossRef CAS.
- V. K. Gupta, R. Jain and S. Varshney, J. Hazard. Mater., 2007, 142, 443–448 CrossRef CAS.
- I. Ali and V. K. Gupta, Nat. Protoc., 2007, 1, 2661–2667 CrossRef.
-
D. F. Samuel
M. A. Osman, Adsorption Processes for Water Treatment. Butterworths, Boston, 1987 Search PubMed.
- V. K. Gupta, A. Mittal, R. Jain, M. Mathur and S. Sikarwar, J. Colloid Interface Sci., 2006, 303, 80–86 CrossRef CAS.
- V. K. Gupta, I. Ali and V. K. Saini, J. Colloid Interface Sci., 2007, 315, 87–93 CrossRef CAS.
- V. K. Gupta, A. Mittal, L. Kurup and J. Mittal, J. Colloid Interface Sci., 2008, 319, 30–39 CrossRef CAS.
- V. K. Gupta and I. Ali, Environ. Sci. Technol., 2008, 42, 766–770 CrossRef CAS.
- V. K. Gupta, S. Agarwal and T. A. Saleh, J. Hazard. Mater., 2011, 185, 17–23 CrossRef CAS.
- V. K. Gupta, R. Jain, S. Malathi and A. Nayak, J. Colloid Interface Sci., 2010, 348, 628–633 CrossRef CAS.
- V. K. Gupta, R. Jain, M. N. Siddiqui, T. A. Saleh, S. Agarwal, S. Malati and D. Pathak, J. Chem. Eng. Data, 2010, 55, 5225–5229 CrossRef CAS.
- V. K. Gupta, A. Mittal, A. Malviya and J. Mittal, J. Colloid Interface Sci., 2009, 335(1), 24–33 CrossRef CAS.
- K. Jüttner, U. Galla and H. Schmieder, Electrochim. Acta, 2000, 45, 2575–2594 CrossRef.
- R. J. Coin and M. J. Niksa, Environ. Prog., 1996, 15, 122–127 CrossRef CAS.
- S. H. Lin and M. L. Chen, Water Res., 1997, 31, 868–876 CrossRef CAS.
- S. Zor, B. Yazici, M. Erbil and H. Galip, Water Res., 1998, 32, 579–586 CrossRef CAS.
- M. Y. A. Mollah, P. Morkovsky, J. A. G. Gomes, M. Kesmez, J. Parga and D. L. Cocke, J. Hazard. Mater., 2004, 114, 199–210 CrossRef CAS.
- M. Kobya, O. T. Can and M. Bayramoglu, J. Hazard. Mater., 2003, 100, 163–178 CrossRef CAS.
- V. Gottberg, J. M. Antonia and L. R. Siwak, Int. Desalin. Water Reuse Q., 1998, 7, 33–37 Search PubMed.
- X. Tongwen, Resour., Conserv. Recycl., 2002, 37, 1–22 CrossRef.
- A. B. Ribeiro, E. P. Mateus, L. M. Ottosen and G. Bech-Nielsen, Environ. Sci. Technol., 2000, 34, 784–788 CrossRef CAS.
- M. R. Jakobsen, J. Fritt-Rasmussen, S. Nielsen and L. M. Ottosen, J. Hazard. Mater., 2004, 106, 127–132 CrossRef CAS.
- V. K. Gupta, S. Agarwal and T. A. Saleh, Water Res., 2011, 45(6), 2207–2212 CrossRef CAS.
|
This journal is © The Royal Society of Chemistry 2012 |
Click here to see how this site uses Cookies. View our privacy policy here.