DOI:
10.1039/C6RA13354A
(Paper)
RSC Adv., 2016,
6, 76795-76801
Surface modification of ferrite nanoparticles with dicarboxylic acids for the synthesis of 5-hydroxymethylfurfural: a novel and green protocol†
Received
23rd May 2016
, Accepted 26th July 2016
First published on 27th July 2016
Abstract
Surface modification of nanomaterials is one of the rapidly growing research areas. Ferrite nanoparticles (inverse spinels) with an average diameter of about 14 nm were modified with various structurally divergent dicarboxylic acids. Successful surface modification allows them to prevent the nanoparticle aggregation. The modified materials showed good catalytic activity in the dehydration of fructose to 5-hydroxymethylfurfural (5-HMF) under solvent free conditions for the first time. 5-HMF was synthesized in high yields under heterogeneous conditions. The flexible ligand-modified ferrites showed better catalytic activity than the rigid ligand-modified ferrites.
Introduction
The catalytic activity of nanomaterials is dependent on the structure and composition of its surface. Surface properties can change in response to variations in the environment because these nanomaterials possess unique properties like high surface area and accessibility of various active facets.1–4 The utilization of nanomaterials in various directions is increasing rapidly after surface modification (SM) due to changes in their properties at the surface.5–7 Various methods have been employed for SM, among which silane polymer and surfactant assisted methods are predominating.8 Carboxylic acids and amines were used as versatile surface modifiers to significantly improve the performance of materials due to the enhanced surface reactivity.9–13 Particularly, monocarboxylic acids (long chain fatty acids) and primary amines are well known surface modifiers of TiO2 and palladium. Step-wise SM of magnetite nanoparticles (MNPs) was carried out using aminopropylsilane, the phosphonate group and alkyl substituted carboxylates.14–16 However, SM of MNPs with dicarboxylic acids have not been known for catalytic applications. Although there are a large number of surface modified materials, including metal oxides, the true potential application of them is yet to be explored. Hence, the development of highly active surface modified catalysts for the synthesis of useful compounds is of great importance.
Development of new catalysts for the sustainability of green protocols is rapidly growing.17–19 Among the current biofuel sources, 5-hydroxymethylfurfural (5-HMF) converted from biomass is a versatile and key intermediate.20–22
Synthesis of 5-HMF has been realized using homogeneous acid-catalysed dehydration of mono and polysaccharides23 in the presence of water,24–27 isopropyl alcohol,28–31 ionic liquid32 and also in a biphasic system.33,34 The direct acid-catalysed dehydration of glucose to 5-HMF in water exhibits very low yields.35–39 Different metal halides in ionic liquids have been extensively studied as efficient dehydrating catalysts with moderate to good yields.40–42 In the direction of heterogeneous catalysis, metal–organic frame works,43 aluminium doped zirconium phosphate44 and niobium catalysts45 act as potential candidates for dehydration of sugar to 5-HMF. Well known metal oxides like sulphated zirconia,46 sulfonic acid and ionic liquid functionalized silica,47 mixed metal oxides,48 ion exchange resins, amberlyst, metal phosphoric acids, functionalized CNTs and Mg-NHCs49–53 have been used as heterogeneous catalysts for the dehydration of sugar. However, one drawback is that the selectivity towards 5-HMF is either low or it has a lower reactivity or separation of the reaction mixture from the catalyst is tedious.
In this context, herein, we report the covalent SM of ferrites (inverse spinels) using various structurally divergent dicarboxylic acids and the subsequent utilization in 5-HMF synthesis (Scheme 1).
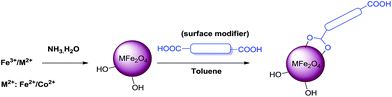 |
| Scheme 1 Surface modification of ferrites with various dicarboxylic acids. | |
The inverse spinels selected for SM in our present case are the superparamagnetic material Fe3O4 and the electromagnetic material cobalt ferrite (CoFe2O4). The surface of these two inverse spinels were modified with various divergent dicarboxylic acids including oxalic acid (L1), succinic acid (L2), malic acid (L3), tartaric acid (L4) and terephthalic acid (L5) (Fig. 1). We choose these acids because they were readily available; and moreover, dicarboxylic acids have not been used as surface modifiers for this catalytic application to the best of our knowledge. Moreover, it is well known that acids catalysed the dehydration of sugar molecules.
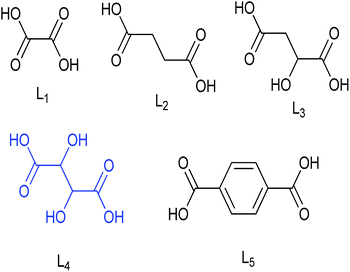 |
| Fig. 1 Various flexible and rigid dicarboxylic acids used for surface modification of ferrites. | |
Surface modified ferrites provide the first example of an isolable and reusable heterogeneous catalyst in the dehydration of fructose under solvent-free conditions (Scheme 2). Solvent is required for the separation of 5-HMF from the reaction mixture. This work represents a novel method and is more advantageous towards addressing environmental concerns in the synthesis of 5-HMF.
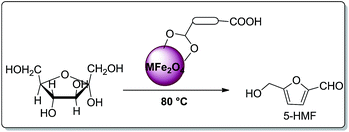 |
| Scheme 2 Surface modified ferrites catalysed the dehydration of fructose. | |
Experimental section
Catalyst characterization
All the reactions were performed in oven-dried flasks. All chemicals were purchased from Aldrich and used directly as received. Analysis of the reactions was done by HPLC from a Shimadzu company instrument with a dual pump using a C-18 column. Concentrations (c) are given in g per 100 mL. Infrared spectra were recorded on a Varian Associated FT-IR 3100 Excalibur with an ATR unit. The wave numbers (n) of recorded IR-signals are quoted in cm−1. Powder X-ray diffraction (XRD) measurements were performed using a Bruker D8 Discover X-ray diffractometer. It was equipped with a chromium target at the source (radiation, λ = 2.2897 Å). The data was collected after minimizing the fluorescence correction of ferrite powders. All the data was collected over the 2-theta range of 20 to 120° at a scan rate of 1.0° per second in the diffraction patterns. The measured XRD data were evaluated using DIFFRAC, EVA and universal software supplied with the Bruker instrument. Correlation was done using PDF-2 release 2013 using ICDD powder diffraction reference files. The diffraction patterns were compared with the supplied reference powder diffraction files (ICDD-PDF cards) for Fe3O4 and CoFe2O4. Thus, surface modified ferrite powders were matched with reference patterns of PDF 01-071-6336 for MNP and PDF 00-028-1086 for cobalt iron oxides for phase identification.
The scanning electron microscopy (SEM) measurements were carried out using a field emission instrument (LEO 1530VP). Samples for SEM analysis were prepared on carbon-coated copper grids; the instrument used was a ZEISS Libra 200FE scanning electron microscope operated at 5 kV and equipped with a field emission gun, an in-column filter (Omega-filter) and a high-angle annular dark-field (HAADF) detector. All micrographs were taken with a 4k × 4k CCD camera and analysed with the software package Digital Micrographs (Version 1.71.38, Gatan Company). EDX mapping was carried out with an EDAX elemental analyser attached to the FE-SEM. A Tecnai FEI transmission electron microscope (TEM) operated at 200 kV accelerating voltage was utilised to evaluate the microstructure of the as-prepared catalyst. X-ray photoelectron spectroscopy (XPS) was performed using an ESCALAB250 instrument by Thermo VG Scientific. Unless stated otherwise, monochromatic Al Kα-radiation was used (15 kV, 150 W, ∼500 μm spot diameter) with the transmission function of the analyser having been calibrated using a standard copper sample. When necessary, charge compensation was achieved using a “Flood-Gun” (∼6 eV/0.05 mA). Spectra were recorded with a pass energy of 80 eV for survey spectra and 30 eV for core level spectra. For non-magnetic samples, a magnetic lens was used to enhance the signal to noise ratio.
Synthesis of ferrites
The MNPs were prepared by the so called wet-impregnation method as reported in the literature.54 The ultra-fine MNPs were prepared by co-precipitating aqueous solutions of ferrous ammonium sulphate [(NH4)2Fe(SO4)2·6H2O] with a ferric chloride (FeCl3) mixture in an alkaline medium. Ferrous ammonium sulphate (0.98 g, 2.5 mmol) was added to ferric chloride (0.81 g, 5 mmol) in 200 mL of water (i.e., stoichiometry ratio Fe2+
:
Fe3+ = 1
:
2) and the resultant mixture was kept at 80 °C for 30 min. To this solution, 0.02 N NH4OH was added dropwise under constant stirring until complete precipitation occurs. Magnetite is formed by conversion of metal chloride into hydroxides (which takes place immediately) and hydroxides into ferrites. The resultant solution was maintained at 80 °C for another 2 h. Then, the brown coloured precipitate obtained was washed several times with distilled water. The precipitate was then separated with the help of an external magnet and was kept for drying at 80 °C. Finally, the thus prepared MNPs were calcined at 400 °C for 2 h to get a free-flowing powder.
Synthesis of cobalt ferrite nanoparticles
Cobalt ferrite nanoparticles were synthesized similar to that of MNPs using cobalt chloride 0.59 g (2.5 mmol) (CoCl2·6H2O) instead of ferrous ammonium sulphate.
Surface modification of ferrites
Surfaces of ferrites were modified with various dicarboxylic acids immediately after their synthesis. In an oven dried round bottomed flask, ferrite (1 mmol) was added to dicarboxylic acid (0.1 mmol) in dry toluene (5.0 mL). Later, the reaction mixture was stirred at 80 °C for 6 h and the surface modified ferrites were separated with the help of an external magnet. The thus obtained brown coloured precipitate was finally washed with dry toluene (2 × 10.0 mL) and the resultant solid was dried at 80 °C for 5 h.
Synthesis of 5-HMF from fructose
In an oven dried flask, 180 mg of fructose and 30 mg of surface modified-ferrites were mixed and sonicated. The mixture was without solvent. The brown coloured mixture was kept at 80 °C until a yellow colour appeared. Later, 2.0 mL of HPLC water was added to the reaction mixture to separate the desired product. Later, the surface modified catalyst was recovered with the help of an external magnet. The yellow aqueous reaction mixture was analysed by HPLC and UV-visible spectroscopy (Scheme 3).
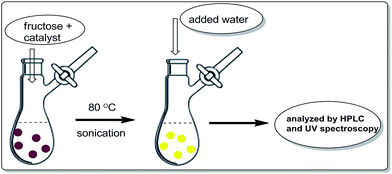 |
| Scheme 3 Schematic representation of 5-HMF synthesis using surface modified ferrites. | |
Results and discussion
The composition and phase purity of the as synthesised and surface modified catalysts were characterized by XRD using a chromium Kα source. It was found that the intensities of the diffraction peaks were consistent with the standard pattern. The sample shows very broad peaks, indicating the ultra-fine nature and small crystallite of the particles. It is obviously seen that all the diffraction peaks can be indexed very well to MNPs (Fig. 2) and cobalt ferrites (Fig. 3). The obtained XRD pattern illustrated that, after modification, the characteristic peaks have been broadened, suggesting that dicarboxylic acids grafted onto the lattice planes of MNPs and cobalt ferrite from all directions. Cubic single phase systems have been observed and the size of the crystals were calculated using the Debye–Scherrer formula. The crystallite size was found to be 13.5 nm for freshly prepared magnetite and 8.5, 9.7, 7.7, 7.8 nm after the SM with ligands L1, L2, L3, L4 and L5, respectively. The decrease of particle size after SM is due to the interaction of iron with the modifier in the place of Fe–Fe interactions, and therefore, prevents agglomeration of the MNPs. The phase identification and quantification is given in Table S1.† The crystalline size of surface modified cobalt ferrite was found to be 9.8, 6.2, 6.7, 6.9 and 7.2 nm after the SM with ligands L1, L2, L3, L4 and L5, respectively (Fig. 3).
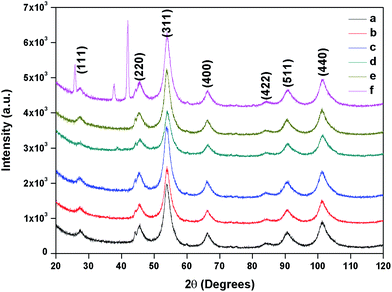 |
| Fig. 2 XRD of (a) freshly prepared magnetite, (b) surface modified with L1, (c) with L2, (d) with L3, (e) with L4 and (f) with L5. | |
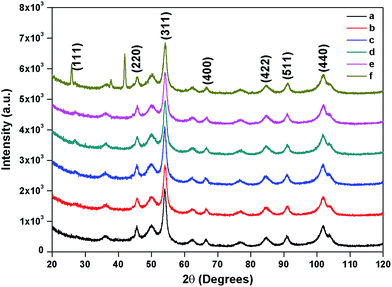 |
| Fig. 3 XRD of (a) freshly prepared cobalt ferrite (b) surface modified with L1 (c) with L2 (d) with L3 (e) with L4 (f) with L5. | |
In addition, FT-IR spectroscopy revealed that the surface of MNPs was modified (Fig. 4). The Fe–O stretching vibration frequency at 580 cm−1 was observed for freshly prepared MNPs and also after SM. Notably, the stretching frequency at 1100 cm−1 is present is due to the presence of C–C bonds of the surface modifiers (Fig. 4b–f). Moreover, the stretching frequency at 1415 cm−1 confirms the presence of carboxylate groups. Of particular note is that C–H and C
C stretching vibration frequencies are observed at 786 cm−1 and 1576 cm−1 for the aromatic group of L5-modified MNPs (Fig. 4f). In addition, the presence of the –O–H stretching frequency in all the cases, at nearly 3400 cm−1, and the deformed vibration of O–H at 1630 cm−1 is also present (due to the coordinated surface –O–H groups with Fe-atoms). These findings revealed that a significant SM of the ferrite nanoparticles occurred. All stretching frequency assignments are given in Table S2.† Similarly, modified CoFe2O4 samples were also characterized by FT-IR and the results are included in the ESI (Fig. S2†). Furthermore, the surface modified catalyst was characterized using scanning electron microscopy/energy-dispersive X-ray analysis (SEM-EDX). The SEM of magnetite shows the presence of rod type structures and the surface is composed of well-aligned small nanoparticles for L1–L4 modified particles and a pi-stacked structure for L5 modified particles (Fig. S3†).
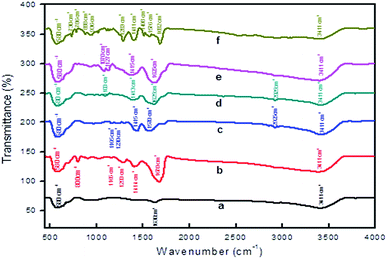 |
| Fig. 4 FT-IR spectroscopy of (a) freshly prepared MNPs, surface modification with L1 (b), L2 (C), L3 (d), L4 (e) and L5 (f). | |
We commenced our study with the dehydration of fructose using L1 modified MNP as a catalyst system. We were pleased to find that running the reaction without solvent at 80 °C, the fructose conversion was 18% with 84% selectivity for 5-HMF. In order to better understand the role of the surface modifier, the reaction was also carried out without SM. The conversion of fructose could take place only <5% either with Fe3O4 or CoFe2O4 (Table 1, entry 1 and 2). In order to understand the role of L1, various surface modified ferrites were prepared. Then, these modified ferrites were tested in the dehydration of fructose at 80 °C. Remarkably, when the surfaces of MNPs were modified with L3 and L5, fructose was dehydrated in 21% and <5%, respectively (Table 1, entry 5 & 7). Although it shows good conversion (up to 86%) with L2 modified catalyst, there was less selectivity towards 5-HMF (Table 1, entry 4).
Table 1 Synthesis of 5-HMF using different surface modifiersa
Entry |
Catalyst |
Time (h) |
Conversion (%) |
Selectivity (%) |
Reaction conditions: catalyst, 30 mg and fructose, 180 mg at 80 °C. After recycling of the catalyst for five times. |
1 |
Fe3O4 |
24 |
<5% |
— |
2 |
CoFe2O4 |
24 |
<5% |
— |
3 |
Fe3O4–L1 |
12 |
18 |
84 |
4 |
Fe3O4–L2 |
12 |
86 |
<5% |
5 |
Fe3O4–L3 |
10 |
21 |
96.4 |
6 |
Fe3O4–L4 |
3 |
98, 91b |
87, 83b |
7 |
Fe3O4–L5 |
10 |
<5% |
— |
8 |
CoFe2O4–L1 |
18 |
12 |
82 |
9 |
CoFe2O4–L2 |
24 |
16 |
— |
10 |
CoFe2O4–L3 |
24 |
29 |
95 |
11 |
CoFe2O4–L4 |
1 |
96 |
89 |
12 |
CoFe2O4–L5 |
24 |
— |
— |
This may be due to the flexible linear chain structure of L2 ligand, which forms bridging or chelating chemisorptions with MNPs (Fig. 5). Although conversion of fructose was less, selectivity towards 5-HMF is high with malic acid (L3 modified MNPs). Notably, the yield of 5-HMF drastically increased when the surface was modified with L4, (L)-tartaric acid (Table 1, entry 6). This may be due to the availability of both hydroxyl and carboxylic acid groups which are responsible for higher catalytic activity.16,20 However in the case of L2 and L5, the catalyst may not possesses free COOH; hence, either no selectivity or no catalytic activity was observed (Table 1, entry 4, 7, 9 and 12). This may be due to the binding orientation of the ferrites with surface modifiers (Fig. 5), which may not favour the formation of 5-HMF. It is reasonable to assume that L2, L3 and L4 (flexible ligands) form chelating chemisorptions with MNPs. However, L5 forms the layer-by-layer structure, stacked one above the other (Fig. 6), as confirmed from SEM (by interacting one ligand with two particles at the same time) (Fig. 5, structures ii and v).
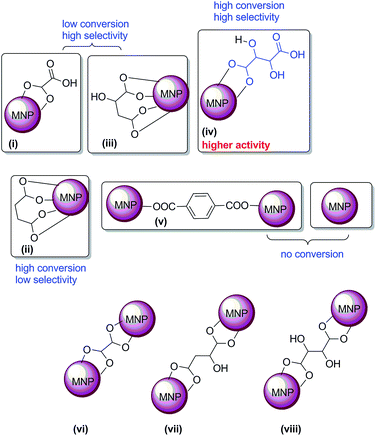 |
| Fig. 5 Possible interactions of MNPs with various surface modifiers. | |
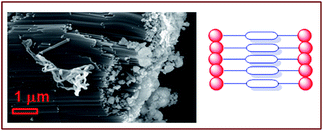 |
| Fig. 6 SEM image of surface modified MNPs with L5. | |
The major by-products formed in the present case are over oxidized products 2,5-furandicarboxylic acid and levulinic acid. Remarkably, the selectivity towards 2,5-furandicarboxylic acid is more when L2 modified ferrites were used in the dehydration reaction. Moreover, naked ferrites are known for their oxidation of aldehydes and alcohols.55 According to the observation that both carboxylic acid and hydroxyl groups accelerate the formation of 5-HMF, we envision that the interaction of surface modifiers with ferrite is as shown in the Fig. 5.
From all this data, we can rule out the possibility of catalytic activity with the vi, vii & viii orientations in Fig. 5. If this happens, it could have showed less selectivity, like as in the case of L2-modified MNP, and almost no reactivity, like as in the case of L5-modified MNP (Fig. 5). To the best of our knowledge, this is the first heterogeneous report for the synthesis of 5-HMF under solvent-free conditions (Table S3†).
The proposed detailed dehydration mechanism of fructose to 5-HMF is represented in Scheme 4. First, the acidic part of the surface modified catalyst interacts with the OH group of fructose; and as a result, one water molecule is removed from the moiety. The proton of the biomass transfers to the catalyst; and thereby, the surface modified catalyst regains its acidic property and is re-activated for removal of another water molecule. Finally 5-HMF is produced after removal of three molecules of water (Scheme 4).
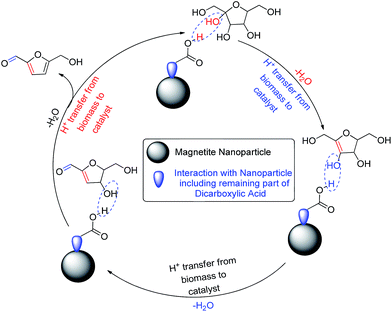 |
| Scheme 4 Proposed mechanism for the dehydration of fructose using surface modified MNPs. | |
Catalyst recycling
In order to investigate the possibility of recycling the surface modified MNPs, the solid catalyst was separated from the reaction mixture by an external magnet. The separated catalysts were washed several times with ethanol. The recyclability of surface modified MNP was carried out by adding fresh fructose to the recovered catalyst. No efficiency loss was observed in the dehydration of four successive runs under identical reaction conditions (Fig. 7). In the case of cobalt ferrite nanoparticles, ligand L4 also exhibited higher catalytic activity of up to 96% conversion with 89% selectivity after one hour (Table 1, entry 11).
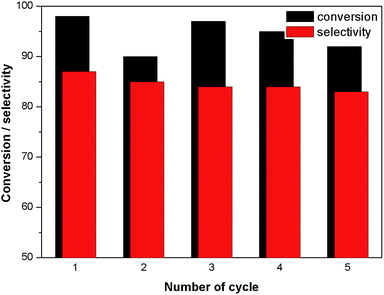 |
| Fig. 7 Reusability of surface modified MNPs in the dehydration of fructose. | |
The surface modified catalyst was characterized by XPS before and after recycling. After recycling of the catalyst five times, the binding energies for Fe(II) and Fe(III) were not changed. However, a small increase in the concentration of Fe(III) was observed (Fig. 8). Moreover, their SM by attachment with organic molecules stabilised and prevented oxidation of the ferrites.
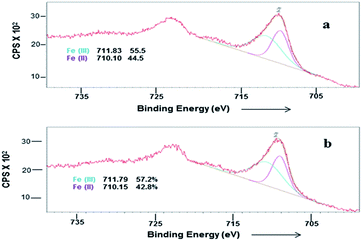 |
| Fig. 8 XPS of the surface modified magnetite nanoparticle before and after recycling. | |
Additionally, the surface modified MNPs were characterized by HR-TEM. HR-TEM images of surface modified MNPs show that the average size of MNPs was 11 nm in diameter and 18 nm after recycling (Fig. 9).
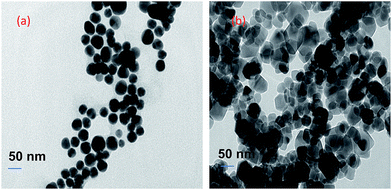 |
| Fig. 9 HR-TEM of surface modified MNPs before and after the catalytic reaction. | |
Conclusion
In summary, we have modified the surface of MNPs and CoFe2O4 NPs using dicarboxylic acids, for the first time, for the dehydration of fructose. The surface functional groups played a major role in the synthesis of 5-HMF under solvent-free conditions. The binding mode of ligand and orientation of the surface modifier played a major role in the yields and selectivity. The catalyst could be easily removed after the reaction.
Acknowledgements
The authors thanks to DST-SERB with file number: SR/NM/NS-1169/2012 for financial support.
Notes and references
- I. E. Watchs and K. Rautray, ACS Catal., 2012, 2, 1235–1246 CrossRef
. - A. Roucoux, J. Schulz and H. Patin, Chem. Rev., 2002, 102, 3757–3778 CrossRef CAS PubMed
. - M. Moreno-Manas and R. Pleixats, Acc. Chem. Res., 2003, 36, 638–643 CrossRef CAS PubMed
. - C. Burda, X. Chen, R. Narayanan and M. A. EI-Sayed, Chem. Rev., 2005, 105, 1025–1102 CrossRef CAS PubMed
. - S. P. Pujari, L. Scheres, A. T. M. Marcelis and A. Zuilhof, Angew. Chem., Int. Ed., 2014, 53, 6322–6356 CrossRef CAS PubMed
. - M.-A. Neouze and U. Schubert, Monatsh. Chem., 2008, 139, 183–195 CrossRef CAS
. - Z. Elbhiri, Y. Chevalier, J.-M. Chovelon and N. R. Jaffrezic, Talanta, 2000, 52, 495–498 CrossRef CAS PubMed
. - F. Hua, M. T. Swihart and E. Ruckenstein, Langmuir, 2005, 21, 6054–6056 CrossRef CAS PubMed
. - M. Buchholz, M. Xu, H. Noei, P. Weidler, A. Nefedov, K. Fink, Y. Wang and C. WÖll, Surf. Sci., 2016, 643, 117–123 CrossRef CAS
. - T. Xu, M. Schwarz, K. Werner, S. Mohr, M. Amende and J. Libuda, Chem.–Eur. J., 2016, 22, 5384–5396 CrossRef CAS PubMed
. - S. Ding, Y. Xing, M. Radsoz and Y. Shen, Macromolecules, 2006, 39, 6399–6405 CrossRef CAS
. - M. A. White, J. A. Johnson, J. T. Koberstein and N. J. Turro, J. Am. Chem. Soc., 2006, 128, 11356–11357 CrossRef CAS PubMed
. -
(a) E. Amstad, J. Kohlbrecher, E. Muller, T. Schweitzer, M. Textor and E. Reimhult, Nano Lett., 2011, 11, 1664–1670 CrossRef CAS PubMed
;
(b) H. Fan, Z. Chen, C. J. Brinker, J. Claswon and T. Alam, J. Am. Chem. Soc., 2005, 127, 13746–13747 CrossRef CAS PubMed
. - Surface Modification of Nanomaterials for Application in and Natural Fiber Fillers, ed. V. Mittal, Wiley-VCH, Weinheim, 1st edn, 2015, pp. 1–28 Search PubMed
. - M.-A. Neouze and U. Schubert, Monatsh. Chem., 2008, 139, 183–195 CrossRef CAS
. - M. Shaikh, M. Sahu, P. K. Gavel and K. V. S. Ranganath, Catal. Commun., 2015, 64, 18–21 CrossRef CAS
. - M. Poliakoff and P. Licence, Nature, 2007, 450, 810–812 CrossRef CAS PubMed
. - C. L. Hill, Nature, 1999, 401, 436–437 CrossRef CAS PubMed
. - H. Zhao, J. E. Holladay, H. Brown and Z. C. Zhang, Science, 2007, 316, 1597–1600 CrossRef CAS PubMed
. - L. Hadian-Dehkordi and H. Hosseini-Monfared, Green Chem., 2016, 18, 497–507 RSC
. - M. B. Gawande, A. Velhinho, I. D. Nogueira, C. A. A. Ghumman, O. M. N. D. Teodorod and P. S. Branco, RSC Adv., 2012, 2, 6144–6149 RSC
. - T. Wang, M. W. Nolte and B. H. Shanks, Green Chem., 2014, 16, 548–572 RSC
. - L. Qi, Y. F. Mui, S. W. Lo, M. Y. Lui, G. R. Akien and I. T. Horvath, ACS Catal., 2014, 4, 1470–1477 CrossRef CAS
. - D. Wu and M. Hakkarainen, ACS Sustainable Chem. Eng., 2014, 2, 2172–2181 CrossRef CAS
. - M. Bicker, J. Hirth and H. Vogel, Green Chem., 2003, 5, 280–284 RSC
. - G. Yi, S. P. Teong, X. Li and Y. Zhang, ChemSusChem, 2017, 7, 2131–2135 CrossRef PubMed
. - L. Lai and Y. Zhang, ChemSusChem, 2011, 4, 1745–1748 CrossRef CAS PubMed
. - X. Qi, M. Watanabe, T. M. Aid and R. L. Smith Jr, Green Chem., 2010, 12, 1855–1860 RSC
. - J. N. Chheda, Y. Roman-Leshkov and J. A. Dumesic, Green Chem., 2007, 9, 342–350 RSC
. - T. D. Swift, H. Nguyen, A. Anderko, V. Nikolakis and D. G. Vlachos, Green Chem., 2015, 17, 4725–4735 RSC
. - H. Ning, J. L. song, M. Q. Hou, D. Z. Yang, H. L. Fan and B. X. Han, Sci. China: Chem., 2013, 56, 1578–1585 CrossRef CAS
. - S. Asghari and F. Yoshida, Ind. Eng. Chem. Res., 2006, 45, 2163–2173 CrossRef
. - N. Jiang, R. Huang, W. Qi, R. Su and Z. He, BioEnergy Res., 2012, 5, 380–386 CrossRef CAS
. - T. Thananatthanachol and T. B. Rauchfuss, Angew. Chem., Int. Ed., 2010, 122, 6766–6768 CrossRef
. - A. Ranoux, K. Djanashvili, I. W. C. E. Arends and U. Hanefeld, ACS Catal., 2013, 3, 760–763 CrossRef CAS
. - C. M. Cai, N. Nagane, R. Kumar and C. E. Wyman, Green Chem., 2014, 16, 3819–3829 RSC
. - L. Hu, Y. Sun and L. Lin, Ind. Eng. Chem. Res., 2012, 51, 1099–1104 CrossRef CAS
. - H. Li, W. Xu, T. Huang, S. Jia, Z. Xu, P. Yan, X. Liu and Z. C. Zhang, ACS Catal., 2014, 4, 4446–4454 CrossRef CAS
. - L. Wu, J. Song, B. Zhang, B. Zhou, H. Zhou, H. Fun, Y. Yang and B. Han, Green Chem., 2014, 16, 3935–3941 RSC
. - G. Yong, Y. Zhang and J. Y. Ying, Angew. Chem., Int. Ed., 2008, 120, 9485–9488 CrossRef
. - F. Ilgen, D. Ott, D. Kralisch, C. Reil, A. Palmberger and B. König, Green Chem., 2009, 11, 1948–1954 RSC
. - J. Zhou, Z. Xia, T. Huang, P. Yan, W. Xu, Z. Xu, J. Wang and Z. C. Zhang, Green Chem., 2015, 17, 4206–4216 RSC
. - J. Chen, K. Li, L. Chen, R. Liu, X. Huang and D. Ye, Green Chem., 2014, 16, 2490–2499 RSC
. - V. V. Ordomsky, J. C. Schouten, J. van der Schaaf and T. A. Nijhuis, ChemCatChem, 2012, 4, 129–133 CrossRef CAS
. - K. Nakajima, Y. Baba, R. Noma, M. Kitano, J. N. Kondo, S. Hayashi and M. Hara, J. Am. Chem. Soc., 2010, 133, 4224–4227 CrossRef PubMed
. -
(a) X. Qi, M. Watanabe, T. M. Aida and R. L. Smith Jr, Catal. Commun., 2009, 10, 1771–1775 CrossRef CAS
;
(b) H. P. Yan, Y. Yang, D. M. Tong, X. Xiang and C. W. Hu, Catal. Commun., 2009, 10, 1558–1563 CrossRef CAS
. -
(a) L. Hu, X. Tang, Z. Wu, L. Lin, J. Xu, N. Xu and B. Dai, Chem. Eng. J., 2015, 263, 299–308 CrossRef CAS
;
(b) Q. X. Bao, K. Qiao, D. Tomida and C. Yokoyama, Catal. Commun., 2008, 9, 1383–1388 CrossRef CAS
. -
(a) Y. Wang, X. Tong, Y. Yan, S. Xue and Y. Zhang, Catal. Commun., 2014, 50, 38–43 CrossRef CAS
;
(b) R. Kourieh, V. Rakic, S. Bennici and A. Auroux, Catal. Commun., 2013, 30, 5–13 CrossRef CAS
;
(c) K. Yamaguchi, T. Sakurada, Y. Ogasawara and N. Mizuno, Chem. Lett., 2011, 40, 542–543 CrossRef CAS
. -
(a) G. A. Halliday, R. J. Young and V. V. Grushin, Org. Lett., 2003, 5, 2003–2005 CrossRef CAS PubMed
;
(b) J. N. Chheda and J. A. Dumesic, Catal. Today, 2007, 123, 59–70 CrossRef CAS
;
(c) X. H. Qi, M. Watanabe, T. M. Aida and R. L. Smith, Green Chem., 2008, 10, 799–805 RSC
;
(d) S. Q. Hu, Z. F. Zhang, Y. X. Zhou, J. L. Song, H. L. Fan and B. X. Han, Green Chem., 2009, 11, 873–877 RSC
. -
(a) K. Shimizu, R. Uozumi and A. Satsuma, Catal. Commun., 2009, 10, 1849–1853 CrossRef CAS
;
(b) X. H. Qi, M. Watanabe, T. M. Aida and R. L. Smith, Green Chem., 2009, 11, 1327–1331 RSC
;
(c) A. Takagaki, M. Ohara, S. Nishimura and K. Ebitani, Chem. Commun., 2009, 6276–6278 RSC
;
(d) C. Lansalot-Matras and C. Moreau, Catal. Commun., 2003, 4, 517–520 CrossRef CAS
. - M. Chidambaram and A. Bell, Green Chem., 2010, 12, 1253–1262 RSC
. - K. V. S. Ranganath, M. Sahu, M. Shaikh, P. K. Gavel, S. Khilari and P. Das, New J. Chem., 2016, 40, 4468–4471 RSC
. - M. Shaikh, M. Sahu, P. K. Gavel, S. Khilari, T. G. Reddy, D. Pradhan and K. V. S. Ranganath, Catal. Commun., 2016, 84, 89–92 CrossRef CAS
. - H. E. Ghandoor, H. M. Zidan, M. M. H. Khalil and M. I. M. Ismail, Int. J. Electrochem. Sci., 2012, 7, 5734–5745 Search PubMed
. - M. Shaikh, M. Satanami and K. V. S. Ranganath, Catal. Commun., 2014, 54, 91–93 CrossRef CAS
.
Footnote |
† Electronic supplementary information (ESI) available: Phase quantification of XRD, FT-IR stretching frequencies, detailed experimental procedure, SEM analysis, UV and HPLC spectras are available. See DOI: 10.1039/c6ra13354a |
|
This journal is © The Royal Society of Chemistry 2016 |