From microkinetic model to process: understanding the role of the boron nitride surface and gas phase chemistry in the oxidative dehydrogenation of propane†
Received
8th November 2023
, Accepted 22nd January 2024
First published on 9th February 2024
Abstract
After naphtha steam cracking, endothermic propylene production via direct dehydrogenation (PDH) is one of the most energy-intensive processes in the chemical industry. The exothermic alternative, oxidative dehydrogenation of propane (ODHP), has been investigated for decades over metal-oxide catalysts but still lacks the propylene selectivity necessary for industrial viability. Recently proposed boron-based catalysts for ODHP show improved selectivity to propylene via a surface-initiated gas-phase free radical mechanism that is remarkably selective. Aiming at process improvements that can further boost propylene selectivity, we investigated the mechanism(s) by which propylene selectivity is lost. We find that surface-mediated propylene marginally affects the initial selectivity to propylene. We hypothesize this is likely due to the initial n-propyl vs. i-propyl radical formation rate over the surface as compared to the gas-phase chemistry. This suggests that shifting the reaction flux more towards the gas phase could improve the selectivity. However, we also observed that propylene predominantly over-oxidizes in the gas-phase but not over the surface. Turning to the gas-phase chemistry, we are unable to boost the selectivity above that of the underlying background reactivity in a tube, despite the use of radical accelerants such as NO and O3. Our work suggests that future process improvements should focus on tuning the radical distribution in the gas-phase chemistry.
Introduction
Propylene is a key platform chemical used to produce commodity polymers and chemicals such as polypropylene, acrolein, acrylonitrile, and propylene oxide.1,2 Due to the displacement of naphtha with ethane-rich shale gas as a feed for steam crackers, propylene production from steam cracking has not kept pace with expected demand, motivating the development of on-purpose propylene production technologies.3 A key on-purpose technology is the direct dehydrogenation of propane at elevated temperatures (550–700 °C) using environmentally-challenging (Catofin – Cr) or expensive (Oleflex – Pt) catalysts.4 Commercial dehydrogenation processes are remarkably productive but require constant catalyst regeneration due to inevitable coking.3 This requires complex process technology, leading to high CAPEX and CO2 production from catalyst regeneration.2
Oxidative dehydrogenation of propane (ODHP) is an attractive alternative technology that avoids the need for high temperatures by exothermically generating propylene from propane and oxygen. It also has the added benefit of (potentially) greater process stability, avoiding coke formation and concomitant catalyst regeneration. Metal oxide catalysts that have been studied for this process (V, Mo, Cr) suffer from poor selectivity to propylene, even at modest propane conversions, due to the facile overoxidation of propylene to COx combustion products.5 The highly reactive allylic C–H bonds in propylene typically lead to a large gap in the relative kinetic barriers of propane and propylene overoxidation, making it challenging to develop selective oxidation systems with suitable selectivity.6 This challenge has motivated significant investigation into catalytic materials that can avoid propylene overoxidation.5
Recent discoveries demonstrate that alternatives to metal oxide systems are capable of oxidizing propane to propylene with enhanced selectivity to propylene. In 2016, hexagonal boron nitride was shown to be selective in the oxidation of propane to propylene,7 and subsequently many boron-containing catalysts were shown to be active and selective as well.8–17 Further investigation revealed that boron-based catalysts undergo an induction period, forming a boron oxyhydroxide layer that likely kicks off surface-initiated, radical gas-phase propagated propane oxidation.18–23 In particular, microkinetic modeling suggests that propane is typically activated by oxidants such as
radical that leads to formation of n-propyl and i-propyl radicals, key intermediates in the formation of propylene via H-abstraction by O2.21,24 The relative ratio of n-propyl vs. i-propyl radicals formed has tremendous implications for the selectivity of the process, and the ratio is determined by the nature of the H-abstracting species.21 Indeed, more reactive H-abstractors discriminate less between primary and secondary C–H bonds, leading to a higher fraction of primary to secondary radicals as compared to less reactive H-abstractors.
Remarkably, the gas-phase chemistry alone appears to dominate the activity of boron-based catalysts under relevant reactor conditions. Schlögl and co-workers showed that many apparently inert reactor filler materials (silica, silicon carbide, boron nitride, and more) are capable of producing nearly identical propylene selectivity vs. propane conversion trends, albeit with different reactivity which points towards different initiation abilities.25 In a separate report, Deshlahra and co-workers used NO to mediate the radical gas-phase oxidation of propane.26 Subsequent microkinetic modeling attributed the catalytic activity of NO to its propensity for forming ˙OH radicals through a gas-phase redox cycle, accelerating similar propane dehydrogenation pathways.27 Lindstedt, Deshlahra, Schlögl and respective co-workers have all demonstrated that microkinetic modeling of the gas-phase chemistry alone captures the general selectivity of boron-based catalysts quite well.24,25,27 The advantage of using BN is to initiate the reaction under milder conditions. Kinetic modelling that incorporates boron-based active sites have implicated various surface structures in enhanced ODH reactivity.28,29
These reports highlighting the role of gas-phase reactivity also identify the curse of radical gas-phase selective oxidation chemistry; it is challenging to improve the selectivity to propylene beyond that of the underlying gas-phase oxidation processes that take over and enable the high productivity of these catalysts. By contrast, relatively little is known about the surface-based reactivity of boron-based catalysts that provide active sites for propane initiation. Xiao and co-workers demonstrated that isolated hydroxylated boron in a zeolite shows first-order reactivity in propane, in contrast to the second-order reactivity typically observed over gas-phase dominated boron-based catalysts.7,16 Alexandrova and co-workers used ensemble methods to propose metastable boron nitride active sites that could initiate propane activation and generate water in kinetically relevant steps.21 Nonetheless, little ODHP investigation has been done under surface-dominated conditions. In this report we return to boron nitride and seek to isolate the effect of the catalyst surface on performance. By comparing the reactivity on boron nitride to that in the gas-phase we distinguish the reactivity of the surface chemistry. We find that boron-based catalysts show a slightly lower selectivity to propylene compared to the gas-phase chemistry. The gas-phase chemistry, meanwhile, can be altered through reactor parameters or the use of radical mediators such as O3 and NO. However, these radical mediators do not demonstrate an improvement in the selectivity to propylene. To better understand these processes, we utilize microkinetic modeling to examine the limits of propylene selectivity under gas phase-dominated conditions. Our work suggests that further study is required to identify novel ways to improve the selectivity of these gas-phase radical processes.
Experimental
Reactions
Reactive gas mixtures were prepared from UHP N2 (Airgas, 99.99%), UHP O2 (99.994%), and either instrument-grade C3H8 (Matheson, 99.5%) or research-grade propane (Airgas, 99.99%). NO was supplied from a mixture of 4020 ppm NO in N2 (Airgas) while O3 was generated from a VMUS-DG ozone generator (see ESI† for details). The mass flowrate of each gas was controlled by Bronkhorst EL-Flow Select mass flow controllers and gases were mixed prior to entry in the reactor. The reactor consisted of a 52 cm long quartz tube (inner diameter was varied between experiments) inside a Carbolite split-tube furnace (VST 12/300). SiC was passivated via calcination at 900 °C for 12 h before crushing, sieving, and retaining the 180–425 micron fraction. For hBN reactions, the 7 mm ID tube was packed with approximately 100 mg of 180–425 micron hexagonal boron nitride diluted in 500 mg of passivated SiC leading to a bed approximately 2 cm in length. The 4 mm ID tube was packed with approximately 50 mg of 180–425 micron hexagonal boron nitride diluted in 250 mg of passivated SiC leading to a bed approximately 2.75 cm in length. For B2O3 reactions, 50 mg of 60 mesh B2O3 was mixed with 250 mg of passivated SiC (4 mm tube) or 950 mg quartz chips (7 mm tube). For gas-phase reactions, a 12–18 cm section of a 9 mm ID tube was used for reactions and a 9 cm section of the 4 mm ID tube was used for reactions. For all reactions, a 3 mm quartz concentric thermowell was placed in the center of the reactor, with a K-type thermocouple fixed either within the reactive zone (7 mm/9 mm ID tube), or just adjacent to the reactive zone (4 mm ID tube). The catalyst bed was held in place with quartz wool and the remainder of the reactor was packed with either quartz chips or a quartz rod to limit reactor dead volume and act as a radical quench. All reactions were conducted at approximately atmospheric pressure with less than 3 psig pressure drop and 1 psig back pressure.
Prior to reaction, catalysts were activated at 550 °C under a feed of 30% C3H8/15% O2/55% N2 until propane conversion was stable. During reactions, reactor effluent was directed to an online gas chromatograph (GC) instrument (Inficon MicroGC Fusion). The GC was outfitted with 4 columns (5A Mol Sieve, U-Bond, Alumina Na2SO4, and Rxi-1 ms) and μTCDs capable of analyzing permanent gases, C1–C4 alkanes and olefins, some C1–C3 alcohols, some C1–C3 aldehydes, acetone, and propylene oxide. Peak overlap prevented complete resolution of some of the trace oxygenates. For propylene reactions only conversion was reported, and therefore a detailed carbon balance was not determined. The carbon balance from propane reactions closed to within 100 ± 3%.
Carbon balance, conversion, and selectivity were calculated as follows:
where the sum over
i indicates a sum over all
i products,
ν indicates carbon number,
A indicates GC response area, N
2fac is defined as

(to account for dilution due to product formation) and RF indicates GC response factor.
Modeling
Microkinetic modeling was performed in Cantera.30 The model consisted of an isothermal plug flow reactor model and a microkinetic mechanism adapted from a recent publication in the combustion literature by Liao and co-workers studying low-temperature ignition of C3H8–O2 flames with O3.31 This model was further appended by a model published recently by Deshlahra and co-workers studying NO-initiated propane ODH.27 We note that the gas-phase reactions likely exhibit a laminar flow profile and therefore rigorous modelling of the rate of reaction should account for this. Plug-flow modelling was utilized for simplicity and because the selectivity vs. conversion data showed good agreement with experiment. The microkinetic mechanism and model scripts can be accessed from the ESI.†
Safety considerations
Selective oxidations must be operated outside the flammable regime to ensure personnel and equipment safety. Experiments were primarily performed at propane-rich conditions (2
:
1 C3H8
:
O2) to ensure that even with significant conversion the reactor fluid would not enter the flammable regime for a C3H8
:
O2 mixture.32
O3 is a toxic gas even at low concentrations.33 To ensure personnel safety, the O3 generator and an O3 destroyer were housed in a fume hood with a small portion of the generated ozonated O2 stream directed to the reactor. An O3 monitor was used to verify no detectable O3 was present in the general lab atmosphere.
Results and discussion
Role of the surface
To identify the factors controlling propylene selectivity, we compared the performance of hBN and gas-phase reactions in an empty 7 mm tube (Fig. 1). We find that boron nitride is substantially more productive, ca. 5–10×, on a volumetric basis (ESI† Table S1). Gas-phase reactivity alone requires high temperatures to generate high space–time-yields. However, the two systems show a similar selectivity loss at increasing conversion, suggesting their relative rates of propylene overoxidation to formation are similar.34
 |
| Fig. 1 Selectivity to propylene vs. conversion for hBN and empty tube. Conditions: 550 °C, 30% C3H8/15% O2/55% N2, 680–2200 L−1 h−1 (hBN) or 100–200 L−1 h−1 (empty tube). | |
Next, we switched the hydrocarbon in the feed from propane to propylene and observed a dramatic reduction in conversion at identical reactor conditions (Fig. 2). This is in line with observations that propylene is remarkably inactive over boron-based catalysts.35 Introduction of NO, a known accelerant of gas-phase chemistry,26 shows slight improvement in propane conversion over the existing conversion. By contrast, the introduction of NO to propylene significantly boosts propylene conversion, suggesting that gas-phase pathways, rather than surface-mediated pathways, are likely responsible for this overoxidation.
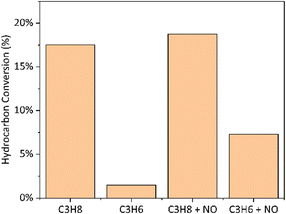 |
| Fig. 2 Comparison of conversion of C3H8 and C3H6 over hBN in the presence/absence of NO. Conditions: 550 °C, 7 mm tube, ∼30% C3H8 or C3H6/15% O2/0 or 150 ppm NO/∼55% N2, 40 mLn min−1 total flow, 100 mg hBN diluted in 500 mg SiC. | |
Both surface-initiated and gas-propagated reactivities contribute to the performance of boron-based catalysts, yet it is difficult with our current understanding to estimate the kinetic chain length (i.e., the rate of propagation over initiation).21 Previous studies demonstrated that modulating reactor parameters and catalyst composition can influence the relative contributions of surface- and gas-driven reactivities.8,19,36 To further assess the influence of the surface on propylene selectivity, the same dilution of boron nitride in silicon carbide was run in a 4 mm tube. Previous studies from our group showed that under a regime of kinetic control this geometry reduces gas-phase reactivity, likely by altering the linear velocity of the gas through the reactive zone of the tube and therefore the relative rates of radical generation and quenching.19 Comparing the performance in the 7 mm and 4 mm tubes, we observed a ca. 3–4× reduction in rate of propane consumption in the 4 mm tube (ESI† Table S1), but we observed no difference in the selectivity to propylene between the two tubes (Fig. 3). This suggests that the difference in productivity may primarily be due to differences in gas-phase radical chain length rather than the introduction of significant surface-mediated reactivity.
 |
| Fig. 3 Propylene selectivity vs. propane conversion over boron nitride at various feed dilutions. Each run maintained a 2 : 1 C3H8 : O2 ratio but with a different feed dilution to achieve the stated feed fraction of C3H8. Conditions: 550 °C, 20–80 mLn min−1, 1 : 5 dilution of boron nitride in passivated silicon carbide (50 mg hBN in 4 mm tube and 100 mg hBN in 7 mm tube). All runs were performed in a 4 mm tube unless otherwise noted. | |
Next, we diluted the propane and oxygen in the feed while maintaining their ratio. Given that boron nitride catalysts have been shown to be second order in the partial pressure of propane,21 we expected this to further bias the reactivity towards any surface-mediated chemistry. At increased dilution we observed the expected loss in selectivity due to a change in oxygen partial pressure (Fig. 3). We also observed a marginal reduction in initial selectivity to propylene compared to gas-only reactivity (ESI† Fig. S6). However, we do not observe any significant differences in the slope of propylene overoxidation between boron nitride-catalyzed ODH and background reactivity. This suggests that any surface-based reactivity provides negligible selectivity control, though it is vital for productivity.
Understanding gas-phase selectivity trends
Given the observations that gas-phase reactivity appears to apply selectivity control, we sought to understand what effect operating parameters can have on this trendline. The contact time, and therefore conversion, of the catalyst plays a significant role in determining the degree of selectivity to propylene in a given measurement. As highlighted in Fig. 3, at isoconversion O2 partial pressure also plays a significant role in selectivity. We corroborated this with experiments at various C3H8
:
O2 feed ratios over B2O3 (ESI† Fig. S5). We also observed that temperature significantly affects selectivity to propylene over boron-nitride catalyst at isoconversion (Fig. 4).
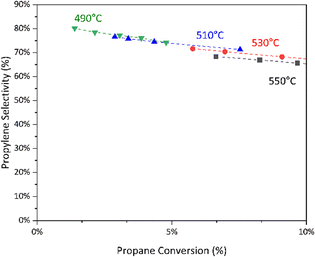 |
| Fig. 4 Propylene selectivity vs. propane conversion over boron nitride at various temperatures. Conditions: 490–550 °C, 30% C3H8/15% O2/55% N2, 100 mg hBN diluted in 500 mg passivated SiC, 29–94 gC3H8 ghBN−1 h−1, 7 mm ID tube. | |
To understand these trends, we constructed a gas-phase microkinetic model, adapted from the literature.27,31 We modeled the system as an isothermal plug-flow reactor and found that this reasonably predicts the selectivity vs. conversion trend (Fig. 5). However, we find that the model underpredicts the conversion of propane (ESI† Fig. S5). Hydrogen peroxide, a major by-product of radical gas-phase propane oxidation predicted by the model, is relatively volatile under these conditions and may be difficult to model accurately. By modifying the decomposition activation energy of hydrogen peroxide we find substantial improvement in the predicted propane conversion with a slight reduction in the accuracy of the modelled selectivity (ESI† Fig. S7 and S8).
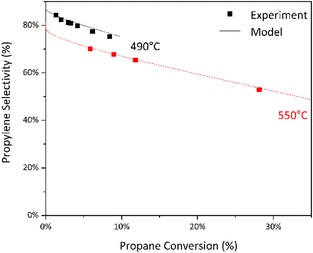 |
| Fig. 5 Microkinetic model prediction vs. experimental observations for gas-phase selectivity vs. conversion at 490 °C and 550 °C. Conditions: 490–550 °C, 30% C3H8/15% O2/55% N2, 67–200 L−1 h−1, 9 mm ID tube. | |
Utilizing the microkinetic model, we find good agreement between our data, previous observations,21 and modelling results. A simplified scheme of the major avenues of carbon flux predicted by the model is shown in Fig. 6. We find that temperature does not significantly modulate the ratio of i- vs. n-propyl formed initially, although it does influence the role of ˙OOH in forming i-propyl radicals. The major role of temperature is to increase the importance of beta cleavage of n-propyl radicals, leading to loss of propylene selectivity. Similarly, we find that the oxygen feed percentage affects the importance of n-propyl beta-scission and it also influences the amount of propane activated by ˙OOH (ESI† Fig. S9).
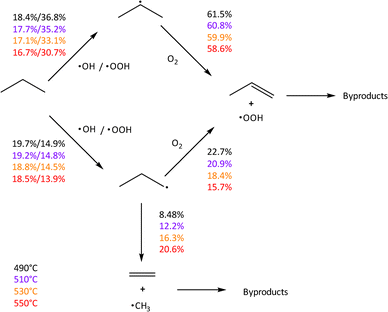 |
| Fig. 6 Major pathways for carbon flux in the gas-phase as predicted by the microkinetic model. Percentages represent the percentage of total carbon flux from C3H8 that goes through a specific pathway when measured at 5% conversion. Note that minor flux pathways (e.g. H abstraction of C3H8 from different oxidants) are not included in this simplified diagram. Carbon flux from O2 abstraction of H from i- and n-propyl radicals represents combined flux of direct abstraction and O2 addition followed by subsequent dissociation. Conditions: 30% C3H8/15% O2/55% N2. Because radical gas-phase processes appeared to control propylene selectivity at meaningful conversions, we sought to focus on the gas-phase chemistry. We introduced NO and O3 in the feed as radical initiators, hypothesizing that alternate chemistries might improve the selectivity to propylene. We observed significant improvement in the light-off of propane conversion (Fig. 7). The introduction of O3 can significantly boost the reactivity of propane in an empty tube relative to the background reactivity. | |
 |
| Fig. 7 Light-off of propane conversion from the introduction of O3 or NO. Conditions: 490 °C, 30% C3H8/∼15% O2/∼55% N2, 67–200 L−1 h−1, 9 mm ID tube section. | |
However, we observe a reduced initial selectivity to propylene (Fig. 8) that we attribute to unselective reactions of propane with highly reactive atomic O formed through O3 decomposition prior to the isothermal region of the reactor. At higher conversions we see all three systems trending towards the same selectivity vs. conversion distribution, suggesting similar mechanisms of propylene formation and loss take place in all three systems.
 |
| Fig. 8 Selectivity vs. conversion for radical-activated gas-phase reactions. Conditions: 490 °C, 30% C3H8/∼15% O2/∼55% N2, 67–200 L−1 h−1, 9 mm ID tube section. | |
Stepping back, we build on a model of propylene generation postulated in a previous model from our group,21 bolstered by our recent computational findings showing boron nitride metastable sites can activate propane and water.37 Propane activation may occur in the gas-phase from HOO˙ and ˙OH radicals or on the surface of hBN. These radicals abstract a H atom from propane, leading to the formation of i-propyl and n-propyl radicals. These in turn react with O2 to form propylene or ethylene plus ˙CH3, with the latter leading to byproducts (Fig. 6). Because the radical gas-phase chemistry takes over at high conversion, it is difficult to improve the selectivity beyond that of the underlying background reactivity. Future research should focus on improved methods of quenching or modifying the gas-phase reactivity to avoid propylene overoxidation.
Conclusions
In this work we seek to understand what levers affect propylene selectivity. We find that propylene predominantly overoxidizes in the gas-phase, with the surface likely playing a role of generating radicals that simply accelerate the gas-phase chemistry. Radical accelerants such as O3 and NO play a similar role of accelerating the background reactivity, but they do not modify the underlying selectivity to propylene. Only operating conditions such as temperature or oxygen partial pressure show an impact on propylene selectivity. Further selectivity improvements would require limiting the background oxidation of propylene, i.e. modifying the pathways of the gas-phase radical propagation.
Author contributions
U. Kurumbail – conceptualization, data curation, formal analysis, investigation, methodology, software, writing – original draft. W. P. McDermott – conceptualization, investigation, methodology, writing – review & editing. E. A. Lebrón-Rodríguez – investigation, methodology, writing – review & editing. I. Hermans – conceptualization, funding acquisition, project administration, supervision, writing – review & editing.
Conflicts of interest
All the authors are named as co-inventors on US Patent # 11680030 pertinent to ozone-mediated oxidative dehydrogenation. I. Hermans is co-inventor on US Patent # 10961170 pertinent to boron-mediated propane dehydrogenation and oxidative coupling of methane.
Acknowledgements
This material is based upon work supported by the National Science Foundation Graduate Research Fellowship Program under Grant No. DGE-1747503. Any opinions, findings, and conclusions or recommendations expressed in this material are those of the author(s) and do not necessarily reflect the views of the National Science Foundation. Support was also provided by the Graduate School and the Office of the Vice Chancellor for Research and Graduate Education at the University of Wisconsin-Madison with funding from the Wisconsin Alumni Research Foundation. The authors would like to acknowledge Tracy Drier for making quartz glassware for this project, Steve Myers for assistance with reactor construction, Blaise Thompson for assistance with electrical and controls questions, and Kevin de Ras for helpful discussions on kinetic modeling. The authors acknowledge financial support of the U.S. Department of Energy. Office of Science, Office of Basic Energy Science, under award DE-SC0017918 (catalytic and mechanistic investigation of boron-based ODH catalysts).
References
- J. J. H. B. Sattler, J. Ruiz-Martinez, E. Santillan-Jimenez and B. M. Weckhuysen, Catalytic Dehydrogenation of Light Alkanes on Metals and Metal Oxides, Chem. Rev., 2014, 114(20), 10613–10653, DOI:10.1021/cr5002436
.
- J. H. Carter, T. Bere, J. R. Pitchers, D. G. Hewes, B. D. Vandegehuchte, C. J. Kiely, S. H. Taylor and G. J. Hutchings, Direct and Oxidative Dehydrogenation of Propane: From Catalyst Design to Industrial Application, Green Chem., 2021, 23(24), 9747–9799, 10.1039/D1GC03700E
.
- J. Sheng, B. Yan, W.-D. Lu, B. Qiu, X.-Q. Gao, D. Wang and A.-H. Lu, Oxidative Dehydrogenation of Light Alkanes to Olefins on Metal-Free Catalysts, Chem. Soc. Rev., 2021, 50(2), 1438–1468, 10.1039/D0CS01174F
.
- S. Chen, X. Chang, G. Sun, T. Zhang, Y. Xu, Y. Wang, C. Pei and J. Gong, Propane Dehydrogenation: Catalyst Development, New Chemistry, and Emerging Technologies, Chem. Soc. Rev., 2021, 50(5), 3315–3354, 10.1039/D0CS00814A
.
- F. Cavani, N. Ballarini and A. Cericola, Oxidative Dehydrogenation of Ethane and Propane: How Far from Commercial Implementation?, Catal. Today, 2007, 127(1–4), 113–131, DOI:10.1016/j.cattod.2007.05.009
.
- C. Batiot and B. K. Hodnett, The Role of Reactant and Product Bond Energies in Determining Limitations to Selective Catalytic Oxidations, Appl. Catal., A, 1996, 137(1), 179–191, DOI:10.1016/0926-860X(95)00322-3
.
- J. T. Grant, C. A. Carrero, F. Goeltl, J. Venegas, P. Mueller, S. P. Burt, S. E. Specht, W. P. McDermott, A. Chieregato and I. Hermans, Selective Oxidative Dehydrogenation of Propane to Propene Using Boron Nitride Catalysts, Science, 2016, 5 Search PubMed
.
- J. T. Grant, W. P. McDermott, J. M. Venegas, S. P. Burt, J. Micka, S. P. Phivilay, C. A. Carrero and I. Hermans, Boron and Boron-Containing Catalysts for the Oxidative Dehydrogenation of Propane, ChemCatChem, 2017, 9(19), 3623–3626, DOI:10.1002/cctc.201701140
.
- L. Shi, B. Yan, D. Shao, F. Jiang, D. Wang and A.-H. Lu, Selective Oxidative Dehydrogenation of Ethane to Ethylene over a Hydroxylated Boron Nitride Catalyst, Chin. J. Catal., 2017, 38(2), 389–395, DOI:10.1016/S1872-2067(17)62786-4
.
- J. A. Loiland, Z. Zhao, A. Patel and P. Hazin, Boron-Containing Catalysts for the Oxidative Dehydrogenation of Ethane/Propane Mixtures, Ind. Eng. Chem. Res., 2019, 58(6), 2170–2180, DOI:10.1021/acs.iecr.8b04906
.
- A. M. Love, M. C. Cendejas, B. Thomas, W. P. McDermott, P. Uchupalanun, C. Kruszynski, S. P. Burt, T. Agbi, A. J. Rossini and I. Hermans, Synthesis and Characterization of Silica-Supported Boron Oxide Catalysts for the Oxidative Dehydrogenation of Propane, J. Phys. Chem. C, 2019, 123(44), 27000–27011, DOI:10.1021/acs.jpcc.9b07429
.
- W.-D. Lu, D. Wang, Z. Zhao, W. Song, W.-C. Li and A.-H. Lu, Supported Boron Oxide Catalysts for Selective and Low-Temperature Oxidative Dehydrogenation of Propane, ACS Catal., 2019, 9(9), 8263–8270, DOI:10.1021/acscatal.9b02284
.
- M. C. Cendejas, R. W. Dorn, W. P. McDermott, E. A. Lebrón-Rodríguez, L. O. Mark, A. J. Rossini and I. Hermans, Controlled Grafting Synthesis of Silica-Supported Boron for Oxidative Dehydrogenation Catalysis, J. Phys. Chem. C, 2021, 125(23), 12636–12649, DOI:10.1021/acs.jpcc.1c01899
.
- L. O. Mark, R. W. Dorn, W. P. McDermott, T. O. Agbi, N. R. Altvater, J. Jansen, E. A. Lebrón-Rodríguez, M. C. Cendejas, A. J. Rossini and I. Hermans, Highly Selective Carbon-Supported Boron for Oxidative Dehydrogenation of Propane, ChemCatChem, 2021, 13(16), 3611–3618, DOI:10.1002/cctc.202100759
.
- G. Wang, Y. Yan, X. Zhang, X. Gao and Z. Xie, Three-Dimensional Porous Hexagonal Boron Nitride Fibers as Metal-Free Catalysts with Enhanced Catalytic Activity for Oxidative Dehydrogenation of Propane, Ind. Eng. Chem. Res., 2021, 60(49), 17949–17958, DOI:10.1021/acs.iecr.1c04011
.
- H. Zhou, X. Yi, Y. Hui, L. Wang, W. Chen, Y. Qin, M. Wang, J. Ma, X. Chu, Y. Wang, X. Hong, Z. Chen, X. Meng, H. Wang, Q. Zhu, L. Song, A. Zheng and F.-S. Xiao, Isolated Boron in Zeolite for Oxidative Dehydrogenation of Propane, Science, 2021, 372(6537), 76–80, DOI:10.1126/science.abe7935
.
- Q. Liu, J. Wang, Z. Liu, R. Zhao, A. Xu and M. Jia, Water-Tolerant Boron-Substituted MCM-41 for Oxidative Dehydrogenation of Propane, ACS Omega, 2022, 7(3), 3083–3092, DOI:10.1021/acsomega.1c06504
.
- Y. Zhou, J. Lin, L. Li, X. Pan, X. Sun and X. Wang, Enhanced Performance of Boron Nitride Catalysts with Induction Period for the Oxidative Dehydrogenation of Ethane to Ethylene, J. Catal., 2018, 365, 14–23, DOI:10.1016/j.jcat.2018.05.023
.
- J. M. Venegas and I. Hermans, The Influence of Reactor Parameters on the Boron Nitride-Catalyzed Oxidative Dehydrogenation of Propane, Org. Process Res. Dev., 2018, 22(12), 1644–1652, DOI:10.1021/acs.oprd.8b00301
.
- A. M. Love, B. Thomas, S. E. Specht, M. P. Hanrahan, J. M. Venegas, S. P. Burt, J. T. Grant, M. C. Cendejas, W. P. McDermott, A. J. Rossini and I. Hermans, Probing the Transformation of Boron Nitride Catalysts under Oxidative Dehydrogenation Conditions, J. Am. Chem. Soc., 2019, 141(1), 182–190, DOI:10.1021/jacs.8b08165
.
- J. M. Venegas, Z. Zhang, T. O. Agbi, W. P. McDermott, A. Alexandrova and I. Hermans, Why Boron Nitride Is Such a Selective Catalyst for the Oxidative Dehydrogenation of Propane, Angew. Chem., Int. Ed., 2020, 59(38), 16527–16535, DOI:10.1002/anie.202003695
.
- R. W. Dorn, L. O. Mark, I. Hung, M. C. Cendejas, Y. Xu, P. L. Gor'kov, W. Mao, F. Ibrahim, Z. Gan, I. Hermans and A. J. Rossini, An Atomistic Picture of Boron Oxide Catalysts for Oxidative Dehydrogenation Revealed by Ultrahigh Field 11 B– 17 O Solid-State NMR Spectroscopy, J. Am. Chem. Soc., 2022, 144(41), 18766–18771, DOI:10.1021/jacs.2c08237
.
- M. C. Cendejas, O. A. Paredes Mellone, U. Kurumbail, Z. Zhang, J. H. Jansen, F. Ibrahim, S. Dong, J. Vinson, A. N. Alexandrova, D. Sokaras, S. R. Bare and I. Hermans, Tracking Active Phase Behavior on Boron Nitride during the Oxidative Dehydrogenation of Propane Using Operando X-Ray Raman Spectroscopy, J. Am. Chem. Soc., 2023, 145(47), 25686–25694, DOI:10.1021/jacs.3c08679
.
- P. Kraus and R. P. Lindstedt, It's a Gas: Oxidative Dehydrogenation of Propane over Boron Nitride Catalysts, J. Phys. Chem. C, 2021, 125(10), 5623–5634, DOI:10.1021/acs.jpcc.1c00165
.
- P. Kube, J. Dong, N. S. Bastardo, H. Ruland, R. Schlögl, J. T. Margraf, K. Reuter and A. Trunschke, Green Synthesis of Propylene Oxide Directly from Propane, Nat. Commun., 2022, 13(1), 7504, DOI:10.1038/s41467-022-34967-2
.
- L. Annamalai, Y. Liu and P. Deshlahra, Selective C–H Bond Activation via NOx-Mediated Generation of Strong H-Abstractors, ACS Catal., 2019, 9(11), 10324–10338, DOI:10.1021/acscatal.9b03862
.
- P. Yu, Y. Liu, P. Deshlahra and H.-W. Wong, Detailed Kinetic Modeling of NOx-Mediated Oxidative Dehydrogenation of Propane, Ind. Eng. Chem. Res., 2021, 60(37), 13553–13561, DOI:10.1021/acs.iecr.1c02635
.
- J. Tian, G. Collinge, S. F. Yuk, J. Lin, V.-A. Glezakou, M.-S. Lee, Y. Wang and R. Rousseau, Dynamically Formed Active Sites on Liquid Boron Oxide for Selective Oxidative Dehydrogenation of Propane, ACS Catal., 2023, 13(12), 8219–8236, DOI:10.1021/acscatal.3c01759
.
- H. Tian, Y. Liu and B. Xu, Kinetic Investigations of Oxidative Dehydrogenation of Propane on Boron Oxide in Confined Spaces, Catal. Today, 2023, 420, 114048, DOI:10.1016/j.cattod.2023.114048
.
-
D. G. Goodwin, H. K. Moffat, I. Schoegl, R. L. Speth and B. W. Weber, Cantera: An Object-Oriented Software Toolkit for Chemical Kinetics, Thermodynamics, and Transport Processes, 2023, DOI:10.5281/ZENODO.8137090.
- W. Liao, Z. Chu, Y. Wang and B. Yang, A Kinetic Investigation on Low-Temperature Ignition of Propane with Ozone Addition in an RCM, Proc. Combust. Inst., 2023, 39(1), 395–403, DOI:10.1016/j.proci.2022.07.261
.
-
H. F. Coward and G. W. Jones, Limits of Flammability of Gases and Vapors, United States Government Printing Office, Washington D.C., 1952 Search PubMed
.
- T. Batakliev, V. Georgiev, M. Anachkov, S. Rakovsky and S. Rakovsky, Ozone Decomposition, Interdiscip. Toxicol., 2014, 7(2), 47–59, DOI:10.2478/intox-2014-0008
.
- Y. Liu, L. Annamalai and P. Deshlahra, Effects of Lattice O Atom Coordination and Pore Confinement on Selectivity Limitations for Ethane Oxidative Dehydrogenation Catalyzed by Vanadium-Oxo Species, J. Phys. Chem. C, 2019, 123(46), 28168–28191, DOI:10.1021/acs.jpcc.9b07778
.
- Z. Liu, Z. Liu, J. Fan, W.-D. Lu, F. Wu, B. Gao, J. Sheng, B. Qiu, D. Wang and A.-H. Lu, Auto-Accelerated Dehydrogenation of Alkane Assisted by in-Situ Formed Olefins over Boron Nitride under Aerobic Conditions, Nat. Commun., 2023, 14(1), 73, DOI:10.1038/s41467-022-35776-3
.
- F. Wu, Z. Liu, J. Sheng, L. Zhu, W.-D. Lu, B. Qiu, D. Wang and A.-H. Lu, Effect of Non-Boron Element with the Different Electronegativity of Binary Boride on Oxidative Dehydrogenation of Propane, J. Catal., 2023, 424, 121–129, DOI:10.1016/j.jcat.2023.05.017
.
- Z. Zhang, I. Hermans and A. N. Alexandrova, Off-Stoichiometric Restructuring and Sliding Dynamics of Hexagonal Boron Nitride Edges in Conditions of Oxidative Dehydrogenation of Propane, J. Am. Chem. Soc., 2023, 145(31), 17265–17273, DOI:10.1021/jacs.3c04613
.
Footnotes |
† Electronic supplementary information (ESI) available: Figures, table of some reactor data, and code. See DOI: https://doi.org/10.1039/d3re00600j |
‡ Current address: Fabric & Home Care Strategic Innovation & Technology, Proctor & Gamble, Cincinnati. |
|
This journal is © The Royal Society of Chemistry 2024 |