DOI:
10.1039/D4QM00182F
(Research Article)
Mater. Chem. Front., 2024,
8, 2428-2438
Synergistically enhancing interface stability with soft gel and garnet-type Li6.4La3Zr1.4Ta0.6O12 bi-functional composite electrolyte of lithium metal batteries†
Received
6th March 2024
, Accepted 26th April 2024
First published on 15th May 2024
Abstract
Solid electrolytes are expected to fundamentally replace liquid electrolytes due to their high safety and energy density. Solid inorganic electrolytes have excellent ionic conductivity and ion mobility; however, they easily induce lithium dendrites without the modification of the soft interface layer. Although they have excellent interfacial properties, they have low ionic conductivity at room temperature and poor mechanical strength. Therefore, a composite electrolyte was prepared by combining a polymer electrolyte with an inorganic electrolyte, and then asymmetric composite electrolytes were designed based on the selective adsorption of glass fibers to further improve the long cycle performance of a battery. In particular, SEI rich in inorganic components can be formed on the surface of lithium metal through the synergistic effect of lithium metal pretreatment and asymmetric structural design. The assembled lithium symmetrical cell was stably cycled for 500 h at a current density of 0.5 mA cm−2. Matched with the LFP cathode electrode, it showed outstanding rate performance at 25 °C, and the initial discharge capacity of LFP‖As-THCE-10%LLZTO‖Li-FEC was 111.6 mA h g−1 at 2C and 25 °C, while the capacity retention rate was 84.73% after 500 cycles. This work provides a new idea for the preparation of lithium metal solid-state batteries with high safety and stability through the rational structural design of composite electrolytes.
1. Introduction
Solid electrolytes are expected to replace liquid electrolytes to further improve the safety and energy density of lithium batteries.1,2 These can be classified as solid inorganic electrolytes (SIE), solid polymer electrolytes (SPE), and organic–inorganic solid composite electrolytes (SCE).3–5 Solid inorganic electrolytes have excellent ionic conductivity and ion mobility number, show good chemical stability to air and moisture, and have high shear modulus (40–60 GPa).6 According to Monroe and Newman's theory, when the shear modulus of a solid electrolyte is twice as much as that of lithium metal, the growth of lithium dendrites can be effectively restrained.7–9 However, due to the existence of cracks, pores, and holes in SIEs and the low nucleation potential of Li+, it will preferentially deposit at the defects and cause local stress, thus accelerating the growth of lithium dendrites and the fracture of brittle oxide solid electrolytes.10,11 When the SIE and the electrode material form “point-to-point” contact without soft interface modification, it is easy to promote the growth of lithium dendrites due to Li+ conduction discontinuity and uneven local current distribution.2,12 Solid polymer electrolytes have the advantages of high flexibility, lightweight, low cost, and can be compatible with the existing large-scale manufacturing process of liquid lithium batteries.13–15 The common polymer systems are PEO-based and polyester-based.16–18 The oxygen atoms on PEO have strong electron-donating characteristics, which easily causes the complexation of Li+ and oxygen atoms on PEO in the system, thus promoting the dissociation of lithium salt; therefore, it has become the most widely studied polymer electrolyte.19,20 However, PEO has high crystallinity, and it is difficult for PEO chain segments to move in high crystallinity, resulting in low ionic conductivity at room temperature and poor mechanical strength of molten PEO, which hardly inhibit lithium dendrites.14 The oxidation voltage of PEO itself is lower than 3.9 V, which limits its application in high-voltage cathode materials. Polyester-based electrolyte has also been widely studied because of its flexibility, easy processing, soft chain, and low cost.21,22 In addition, –COO– has a good affinity for organic carbonate liquid electrolytes and can be blended with other systems to form a gel system. However, there are still some problems such as low ionic conductivity and poor mechanical strength at room temperature.23–25 The solid composite electrolyte, combined with the high mechanical strength of solid inorganic electrolytes and the flexibility of the solid polymer electrolyte, will improve the comprehensive performance of the electrolyte and has broad application prospect.
A balanced proportion of inorganic components and polymer components in the composite electrolyte is difficult to achieve; small amounts of inorganic components hardly inhibit lithium dendrite, but many inorganic components will increase the fragility of the electrolyte, and the contact between the electrolyte and electrode will deteriorate.26 In recent years, researchers have further improved the comprehensive performance of solid electrolytes by designing electrolyte structures. Wang et al. designed an MOF layer with high porosity (≈5 μm) near the cathodic side through in situ polymerization.17 The prepared electrolyte with an asymmetric cross-linked network structure not only has high mechanical strength to inhibit lithium dendrites but also modulates uniform Li+ flux during charging and discharging. Lin et al. developed an asymmetric Li1.3Al0.3Ti1.7(PO4)3 (LATP) ceramic framework with a novel bilayer structure, which was embedded into the PEO/LiTFSI matrix to form a composite solid electrolyte with ionic conductivity up to 0.101 mS cm−1 and effectively inhibited the formation of lithium dendrites.27 Huo et al. prepared two electrolytes, namely, ceramic in polymer (CIP) and polymer in ceramic (PIC), by adjusting the size of ceramic particles and prepared a sandwich composite electrolyte with external flexibility and internal rigidity using CIP and PIC, which achieved excellent contact between the lithium anode and electrolyte interface and effectively mitigated lithium dendrites, showing excellent cycling stability at room temperature.28 Huang et al. used LiF, Li3N, and ionic liquid on the cathodic side to form a flexible electronic insulation layer and ion reinforcement layer and introduced ether-based liquid electrolyte and ionic liquid layer on the anodic side to evenly distribute the electric potential by constructing a gradient interface; thus, the interfacial impedance is reduced and the transmission capacity of lithium ion is enhanced.29 By combining a polymer electrolyte and an inorganic electrolyte to prepare a composite electrolyte and then rationally designing the structure of the electrolyte, the electrochemical performance and cycle stability of the electrolyte can be improved and can effectively mitigate the growth of lithium dendrites.30,31
In this paper, a polymer gel layer was constructed by choosing a polyester-based monomer and an imidazole-based ionic liquid; the composite electrolyte was prepared by compounding inorganic ceramic particles Li6.4La3Zr1.4Ta0.6O12 (LLZTO), and then the asymmetric composite electrolytes (ACE) were designed based on the selective adsorption of glass fibers. The cathodic side is a gel-rich layer with high wettability to promote charge transfer, and the anodic side is ceramic-rich layer with high mechanical strength to effectively mitigate the growth of lithium dendrites. Also, the lithium anode is modified with fluoroethylene carbonate (FEC), which not only improves the wettability of the anode interface and eases the interfacial contact but the Li-FEC electrode and electrolyte also coordinate with each other to generate a fluorine-rich SEI layer, which further enhances the cell performance. The assembled lithium symmetric cell cycles stably for 200 h at a current density of 0.5 mA cm−2. The assembled LFP‖As-THCE-10%LLZTO‖Li-FEC has excellent rate performance at room temperature. The initial discharge capacity of LFP‖As-THCE-10%LLZTO‖Li-FEC is 111.6 mA h g−1 at 2C and 25 °C, the capacity retention rate is 84.73% after 500 cycles, while the initial discharge capacity is 128.2 mA h g−1 at 0.2C and 25 °C and the capacity retention is 93.22% after 120 cycles. Thus, the composite electrolyte with an asymmetric structure provides a new idea to enhance the cycle stability and effectively suppresses lithium dendrites in lithium batteries.
2. Experimental section
2.1. Materials
Trimethylolpropane trimethacrylate (TMPTMA, C18H26O6), 1,6-hexanediol diacrylate (HDDA, C12H16O4), tributylmethylammonium bis(trifluoromethanesulfonyl) imide (N1,4,4,4TFSI), lithium bis(trifluoromethane)sulfonimide (LiTFSI), dimethyl carbonate (DMC), fluoroethylene carbonate (FEC, China National Pharmaceutical Corporation), 2,2′-azobis-(2,4-dimethylvaleronitrile) (ABVN, C14H24N4), LiFePO4 and LLZTO were purchased from Xiamen Tungsten.
2.2. Preparation
Firstly, different mass fractions of monomers (5 wt%, 7.5 wt%, 10 wt%, 12.5 wt%, 15 wt%) were dissolved in DMC to obtain a clear solution, and then LiTFSI and N1,4,4,4TFSI were added sequentially and ultrasonicated for 2 h to obtain a homogeneous and clear precursor solution (where m(TMPTMA)
:
m(HDDA) = 1
:
1). In the precursor solution, m(DMC)
:
m(LiTFSI)
:
m(N1,4,4,4TFSI) = 7
:
2
:
1. Then, LLZTO was uniformly dissolved in the precursor solution in varying amounts (5 wt%, 10 wt%, 15 wt%, 20 wt%) and stirred by a magnetic mixer for 2 h to obtain TMPTMA-HDDA-based composite electrolyte solution. Finally, ABVN was added to the composite electrolyte solution, and the monomer was polymerized by thermal initiation to obtain the solid electrolyte, where the content of ABVN was 0.5–1 wt% of the monomer. The prepared electrolyte was added to the glass fiber, and the asymmetric composite electrolyte was prepared based on the selective adsorption of glass fiber (Fig. 1a and b). The gel polymer electrolytes containing different proportions of monomers were denoted as As-THGE-5%TH, As-THGE-7.5%TH, As-THGE-10%TH, As-THGE-12.5%TH and As-THGE-15%TH, respectively. The asymmetric composite electrolytes containing different proportions of LLZTO were denoted as As-THCE-X% LLZTO (X = 5, 10, 15, 20). In addition, the lithium anode was modified with fluoroethylene carbonate (FEC). The treated lithium metal (FEC-Li) has good wettability and can improve the compatibility with the electrolyte interface (Fig. 1c).
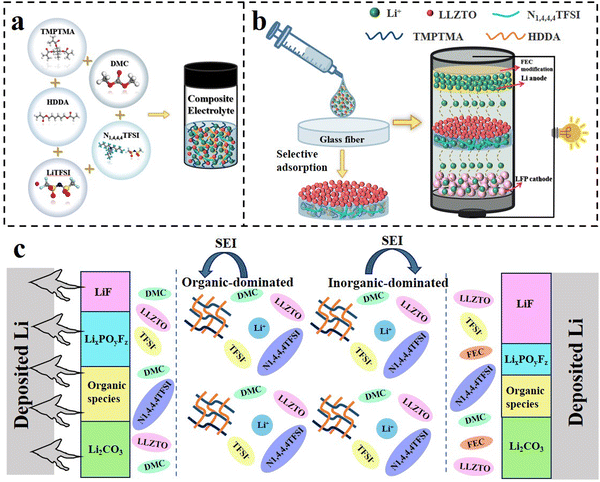 |
| Fig. 1 (a) Preparation diagram of the composite electrolyte; (b) selective adsorption mechanism of glass fiber. (c) Action mechanism diagram of As-THCE-10%LLZTO. | |
2.3. Material characterization
Scanning electron microscopy (SEM) was employed to analyze the morphology of the gel-rich layers, ceramic-rich layers and lithium metal. The elemental distribution and intensity in ceramic particles were characterized by energy dispersive spectroscopy (EDS). The tensile properties were recorded with an SUST CMT1104 universal tester. X-ray diffraction (XRD) was performed to study the crystallinity and phase structure of LiTFSI, As-THCE-10%LLZTO and LLZTO. X-ray photoelectron spectroscopy (XPS) was performed to observe the surface chemical compositions of lithium metal and the LiFePO4 surface.
2.4. Electrochemical measurements
The asymmetric composite electrolytes were assembled in stainless steel symmetric cells, which were tested at 5 mV AC amplitude in the frequency range from 0.01 to 106 Hz by a Princeton Electrochemical Workstation. The ionic conductivity (σ) was calculated by the following equation.where L denotes the thickness of the CPEs, S represents contact area, and Rb is the bulk impedance.
The interfacial stability of the Li|As-THCE-X% LLZTO|Li cell was measured by the Princeton Electrochemical Workstation with an AC amplitude of 5 mV in the frequency range of 0.01–106 Hz.
The CR2032 button battery was assembled with lithium metal as the counter electrode and LFP as the working electrode. A LAND-CT2001A test system was used for the electrochemical testing of LFP‖Li cells.
3. Results and discussion
Based on the characteristics of the selective adsorption of glass fibers, an asymmetric structure of the composite electrolyte with a ceramic-rich layer on the anodic side and a gel-rich layer on the cathodic side was prepared, and its structural features are shown in Fig. 2. Fig. 2a and Fig. S1a (ESI†) show the SEM image of the original glass fibers, from which it can be seen that the glass fiber separator consists of irregular large fibers, and the fiber skeleton provides the possibility to enhance the mechanical strength of the electrolyte as well as the infiltration of the gel electrolyte.31,32Fig. 2b and Fig. S1b (ESI†) show the SEM image of the anodic side of the asymmetric composite electrolyte, and by comparing with the SEM image of the original glass fiber, it can be seen that LLZTO is uniformly covered on the glass fiber. The optical photograph of the anodic side of the ACE is shown in Fig. S2a and b (ESI†), further confirming the ceramic-rich layer on the anodic side. The ceramic-rich layer on the anodic side of the ACE has high mechanical strength, which provides a strong guarantee of effectively mitigating lithium dendrite growth.30Fig. 2c and Fig. S1c (ESI†) show the SEM image of the surface of the cathodic side of the ACE, from which it can be seen that the gel polymer electrolyte is uniformly filled in the pores of the glass fibers, forming a dense gel layer, and the LLZTO is not observed. The optical photograph of the cathodic side of the ACE is shown in Fig. S2c (ESI†), comparing with the original glass fiber (Fig. S2a, ESI†), it can be seen that the cathodic side of the ACE is infiltrated by the gel polymer electrolyte. The modification of the cathode interface using polymers with elastic chain segments to accommodate the volume change of the cathode material during cycling and ensure close contact between the electrode and electrolyte leads to a continuous ion-conducting pathway9,33 and enhances the compatibility of the electrolyte–cathode interface. Fig. 2d and Fig. S3 (ESI†) show the cross-section of the ACE, which also demonstrates that a uniform and dense ceramic-rich layer is formed on one side of the glass fibers. The elemental distribution and intensity of the cross-section of the ACE were characterized, as shown in Fig. 2e. The elements C, O, La, Z and Ta show a decreasing concentration gradient, which is due to the selective adsorption of the glass fibers, and the ceramic particles form a ceramic-rich layer on one side of the glass fibers. The ceramic-rich layer formed by inorganic ceramic particles has a high shear modulus and can significantly improve the mechanical strength of the ACE, which can effectively mitigate the growth of lithium dendrites when the mechanical strength of the ceramic layer is twice as much as that of lithium metal.34 The three-dimensional skeleton of the glass fibers provides the possibility for the gel polymer electrolyte to fully penetrate, allowing the gel polymer electrolyte to fill the pores of the glass fibers, forming a gel-rich layer on the cathodic side. The excellent infiltration of the gel-rich layer achieves a soft contact between the electrolyte and the cathode material, effectively stabilizing the cathode interface and reducing the interfacial impedance.17
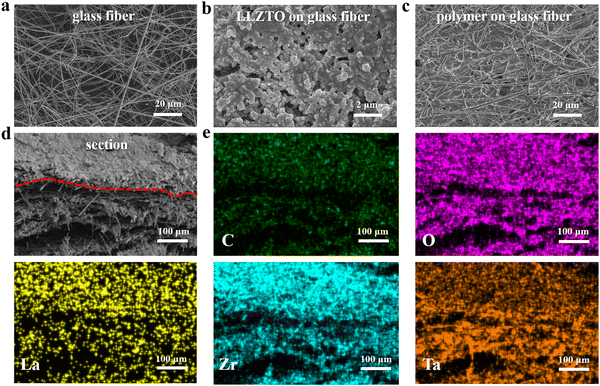 |
| Fig. 2 SEM images of (a) glass fiber; (b) ceramic-rich layer; (c) gel-rich layer; (d) cross-section of ACE; (e) EDS mapping of the cross-section. | |
The C
O functional groups on TMPTMA and HDDA have strong electronegativity and can form a large number of C
O⋯Li+ organic components, promoting Li+ transport. To analyze the effects of monomer ratio and inorganic filler ratio on the cell performance, Li/Li and SS/SS cells were assembled for electrochemical performance testing. As shown in Fig. 3a, the interfacial impedances of the gel electrolytes As-THGE-5%TH, As-THGE-7.5%TH, As-THGE-10%TH, As-THGE-12.5%TH and As-THGE-15%TH were 48.13 Ω, 48.55 Ω, 50.18 Ω, 54.16 Ω and 48.96 Ω, respectively. The interfacial impedances of the gel electrolytes containing different proportions of monomers were all stable at about 50 Ω. Fig. 3b shows the ionic conductivity of the gel electrolytes with different ratios of monomers, from which it can be seen that the ionic conductivity of As-THGE-5%TH is the highest. With the continued addition of monomers, the ionic conductivity will decrease. This may be due to the chain folding as a result of the excessive length of the chain segments,22,35 which inhibits the transport of lithium ions and reduces the ionic conductivity. As shown in Fig. 3c, the bulk impedance of As-THGE-5%TH decreases with increasing temperature, which is due to the high temperature environment promoting the transport of lithium ions. As shown in Fig. 3d, the interfacial impedances of the composite electrolytes As-THCE-5%LLZTO, As-THCE-10%LLZTO, As-THCE-15%LLZTO and As-THCE-20%LLZTO were 131.96 Ω, 220.86 Ω, 316.18 Ω and 551.51 Ω, respectively. The interfacial impedance of the electrolytes gradually increased with the addition of ceramic particles, which is due to the slight agglomeration of the ceramic-rich layer. The ionic conductivity of the composite electrolyte containing different proportions of LLZTO is shown in Fig. 3e. The introduction of LLZTO as an active filler can effectively reduce the crystallinity of the polymer, thereby enhancing the resistance to lithium dendrites and improving the mechanical properties of the electrolyte.36,37 In addition, the nanometer level of the LLZTO filler can provide a larger specific surface area and more active centers, which is conducive to promoting the chain segment movement of the polymer, which will inevitably affect the ionic conductivity of the electrolyte. It can be seen that As-THCE-10%LLZTO has the highest ionic conductivity, while the continued addition of LLZTO decreases it instead. This phenomenon may be due to the aggregation of LLZTO fillers at higher concentrations, which inhibits the transport of lithium ions, resulting in the enhancement of the dilution effect of the polymer and a decrease in the ionic conductivity of the As-THCE-15%LLZTO electrolyte. The activation energy (Ea) of the electrolyte was calculated by the Arrhenius equation
|  | (2) |
where
σ is the ionic conductivity,
σ0 is the proportionality coefficient, and
R is the gas constant. The
Ea fitting results of different electrolytes according to
eqn (2) are shown in Table S1 (ESI
†). The
Ea of As-THCE-5%LLZTO, As-THCE-10%LLZTO, As-THCE-15%LLZTO and As-THCE-20%LLZTO is 7.8, 6.978, 7.976 and 8.239 kJ mol
−1, respectively. It can be seen that As-THCE-10%LLZTO has the smallest
Ea, which is conducive to the transfer of Li
+ and further confirms that the As-THCE-10%LLZTO electrolyte has excellent Li
+ diffusion ability. The bulk impedance of the composite electrolyte As-THCE-10%LLZTO decreases from 5.8 Ω to 3.9 Ω with the increase in temperature, as shown in
Fig. 3f. The migration and transport of lithium ions are faster in a high-temperature environment, which is the same pattern as that in
Fig. 3c. The XRD patterns of LLZTO, As-THCE-10%LLZTO and LiTFSI are shown in
Fig. 3g. The prepared As-THCE-10%LLZTO has an amorphous structure and strong chain mobility, which is conducive to ion migration. In addition, the diffraction peak of LiTFSI was not observed in As-THCE-10%LLZTO, whose absence indicates the complete dissolution of LiTFSI. Moreover, the peak of the electrolyte corresponds to the LLZTO peak, the crystal structure does not change, and the introduction of this one-dimensional structure of LLZTO contributes to the further conduction of ions. The tensile strength of the electrolyte after adding ceramics was tested, as shown in
Fig. 3h. The shear modulus of LLZTO ceramics is as high as 55 GPa, far exceeding the minimum (8.5 GPa) required to inhibit the growth of lithium dendrites.
38 The addition of LLZTO as a filler is expected to enhance the mechanical strength of the composite electrolyte, thereby inhibiting the lithium dendrites to act as a physical barrier. The TG curves of As-THCE-10%LLZTO were tested in the range from 25 to 800 °C to study its thermal stability, as shown in
Fig. 3i. In the initial stage, there is a slight weight loss, which is related to the rapid evaporation of DMC (the boiling point of DMC is about 90 °C). After 319 °C, significant weight loss occurred, which was mainly caused by the decomposition of LiTFSI, TMPTMA and HDDA. After 497 °C, LLZTO and the glass fiber partition remained, and the weight loss phenomenon tended to stabilize. As a result, As-THCE-10% LLZTO has good thermal stability, a property that may enable it to have a wider range of applications.
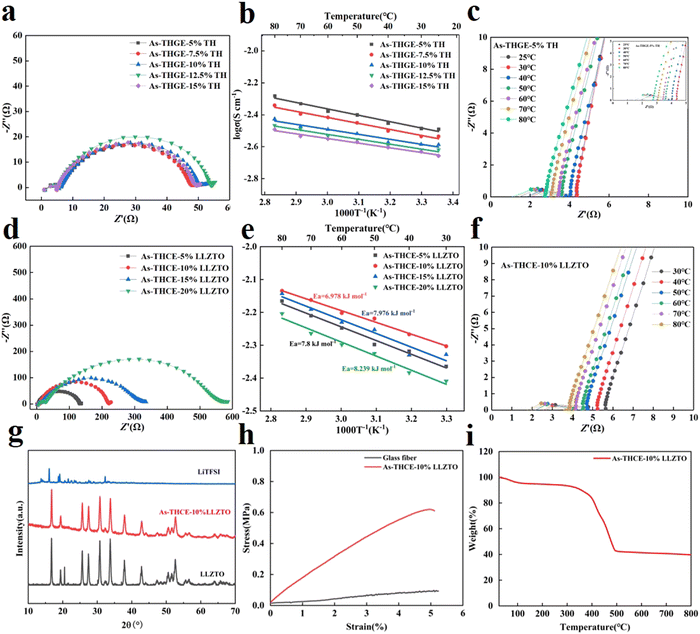 |
| Fig. 3 The interfacial impedance of (a) gel electrolytes and (d) composite electrolytes; the Arrhenius plot of (b) gel electrolytes and (d) composite electrolytes; the bulk impedance of (c) SS‖As-THGE-5%TH‖SS and (f) SS‖As-THCE-10%LLZTO‖SS cell. | |
The high interfacial impedance of ACE can be seen in Fig. 3d, which is due to the deposition of a dense ceramic layer on the anodic side, resulting in poor interfacial contact and ion transport discontinuity. In this regard, Li-FEC electrodes were formed by pretreating the lithium cathode with fluoroethylene carbonate (FEC), and the symmetric cell (Li-FEC‖As-THCE-10%LLZTO‖Li-FEC) was assembled by matching As-THCE-10%LLZTO with the Li-FEC electrode for the further analysis of the anode interface. As shown in Fig. 4a and b, compared with the unmodified Li/Li cell, the interfacial impedance of the Li-FEC‖As-THCE-10%LLZTO‖Li-FEC cell decreased from 220.86 Ω to 156.08 Ω. The stability of the anode interface was further tested by assembling the lithium symmetric cells, as shown in Fig. 4c. The assembled Li/Li cells were charged/discharged at a current density of 0.5 mA cm−2 for 200 h. The initial voltage of the Li‖As-THCE-10%LLZTO‖Li cell was 0.16 V. The fluctuation range of the polarization voltage suddenly increased after 116 h, which can be attributed to uncontrolled lithium dendrite growth and serious side effects between interfaces. In sharp contrast, the lithium symmetric cell with FEC exhibits relatively stable lower polarization voltage and a more stable plating/stripping process.39 The initial voltage of the Li-FEC‖As-THCE-10%LLZTO‖Li-FEC cell was 0.11 V, and the polarization voltage was stabilized at 0.09 V after 58 h. The Li/Li cells are also stable during plating/stripping at higher current densities. On the one hand, this is attributed to the high mechanical strength of the ceramic-rich layer of the ACE, which effectively mitigates the growth of lithium dendrites. On the other hand, the Li-FEC electrode improved the wettability of the anode interface and effectively alleviated interfacial contact at the anode, and the Li-FEC electrode and electrolyte coordinated with each other to generate a fluorine-rich SEI layer, which enhanced the cell performance.
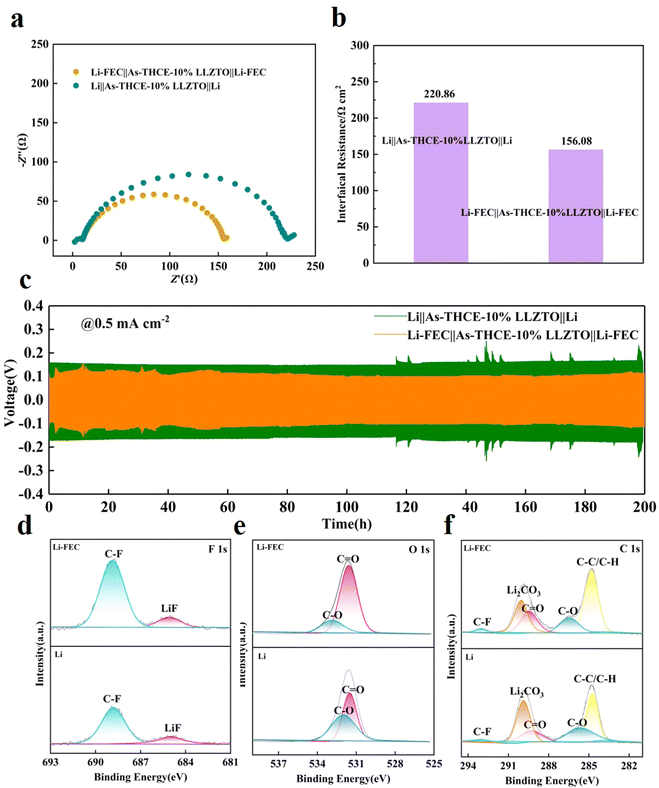 |
| Fig. 4 (a) and (b) The interfacial impedance; (c) the voltage profiles of Li plating/stripping at 0.5 mA cm−2. XPS profiles of (d) F 1s, (e) O 1s, and (f) C 1s of the SEI formed on the lithium surface in the LFP‖As-THCE-10%LLZTO‖Li and LFP‖As-THCE-10%LLZTO‖Li-FEC cells. | |
To further understand the important role of FEC on Li dendrite growth, Li-FEC‖As-THCE-10%LLZTO‖LFP and Li‖As-THCE-10%LLZTO‖LFP cells were disassembled after 100 cycles. The SEM images were obtained for the Li anodes with and without FEC (Fig. S4a and b, ESI†). A large number of rough states were formed on the surface of bare Li anode, which further led to the uneven deposition of lithium, while the surface of the Li-FEC anode showed a smooth state. XPS was used to analyze the composition of As-THCE-10%LLZTO in Li-FEC and bare Li anodes. In the F 1s spectra of the bare Li anode, a weak LiF peak at 685.1 eV was observed after cycling (Fig. 4d). In contrast, strong LiF peaks can be observed in Li-FEC anodes, indicating that FEC decomposes to form a large number of inorganic components at the Li-FEC interface, effectively inhibiting the growth of lithium dendrites.40 At the same time, bare Li showed stronger C–O (532.12 eV) (Fig. 4e), which was mainly due to the increase in organic products, and the rough surface causes the carbonate solvent to react more vigorously with the highly reactive Li. The C 1s spectrum in Fig. 4f also demonstrates the presence of C–O (285.7 eV) and C
O (289.4 eV) signals, which may be derived from the breakdown products of carbonate plasticizers such as ROCO2– and ROC–.41 The SEI of the asymmetric electrolyte has a high affinity for Li+, forming the negatively charged center, which contributes to the formation of uniform Li+ flux in the SEI so as to realize the rapid passage and uniform deposition of Li+. In addition, the SEI rich in Li2CO3 and LiF has fast Li+ transport, which can isolate electrons at the SEI interface and inhibit side reactions by enhancing lithium-ion migration.
LFP cathode has excellent long cycle life and wide operating temperature range. Therefore, THCE-10%LLZTO and THCE-10%LLZTO were matched with LiFeO4 (LFP) to further analyze the cell performance.42Fig. 5 shows the cycling performance of the LFP‖THCE-10%LLZTO‖Li and LFP‖As-THCE-10%LLZTO‖Li-FEC cell at 50 °C. At 2C rate, the initial discharge capacity of LFP‖As-THCE-10%LLZTO‖Li-FEC is 139 mA h g−1 (1C = 170 mA h g−1), as shown in Fig. 5a, and the retention capacity is 78.98% after 500 cycles. The LFP‖THCE-10%LLZTO‖Li has only 51.6% remaining capacity after 50 cycles, which shows that the asymmetric electrolyte can achieve excellent cycle stability. The charge/discharge curves for different cycles at 2C are shown in Fig. 5b; the polarization voltage slightly increases and the capacity gradually decreases as the reaction proceeds. The change in the impedance during cycling is shown in Fig. 5c; the initial impedance is 157.06 Ω, while it is 1213.84 Ω after 100 cycles and 974.53 Ω after 500 cycles. The impedance increases and then decreases during cycling. On the one hand, this is due to the reaction between the electrolyte and LFP to generate a CEI film during the charging–discharging process,43 and on the other hand, the crystal structure of the cathode material undergoes stress–strain during the cycling, which results in poor contact between the electrolyte/electrode and leads to higher impedance;44,45 thus, the impedance increases. As the reaction proceeds, the surface of the electrode material exposes more active sites and has more contact with the electrolyte;32,46 thus, the impedance decreases after cycling.47 As shown in Fig. S5a (ESI†), at 0.2C rate, the initial discharge capacity of LFP‖As-THCE-10%LLZTO‖Li-FEC is 122 mA h g−1, and the capacity retention is 72.17% after 280 cycles. The charge/discharge curves at 0.2C are shown in Fig. S5b (ESI†). The capacity gradually decays as the reaction proceeds, which is related to the consumption of active lithium and the change in the electrode material structure during the cycling.40,48,49 As shown in Fig. S6 (ESI†), the initial impedance of LFP‖As-THCE-10%LLZTO‖Li-FEC is 415.06 Ω, 1358.73 Ω after 100 cycles, and 804.87 Ω after 280 cycles; the trend of the impedance is the same as the 2C rate. On the other hand, the impedance at 0.2C is larger than that at the 2C rate at the beginning, which is due to the more adequate reaction between the electrolyte and electrode material at a small rate, generating a thicker CEI film.50–52 As shown in Fig. 5d, the discharge capacities of the LFP‖As-THCE-10%LLZTO‖Li-FEC cell at 0.1C, 0.2C, 0.5C, 1C and 2C rates (1C = 170 mA h g−1) are 141.7, 131.8, 114.5, 103.9 and 88.9 mA h g−1 at 50 °C, respectively. When the cell returns to the 0.1C rate, the discharge capacity is 137.3 mA h g−1, which is comparable to the capacity at the initial rate of 0.1C, indicating the excellent rate performance of the cell. Fig. 5e shows the charging and discharging curves at different rates, and it can be seen that the polarization voltage of the cell is higher for larger rates.49
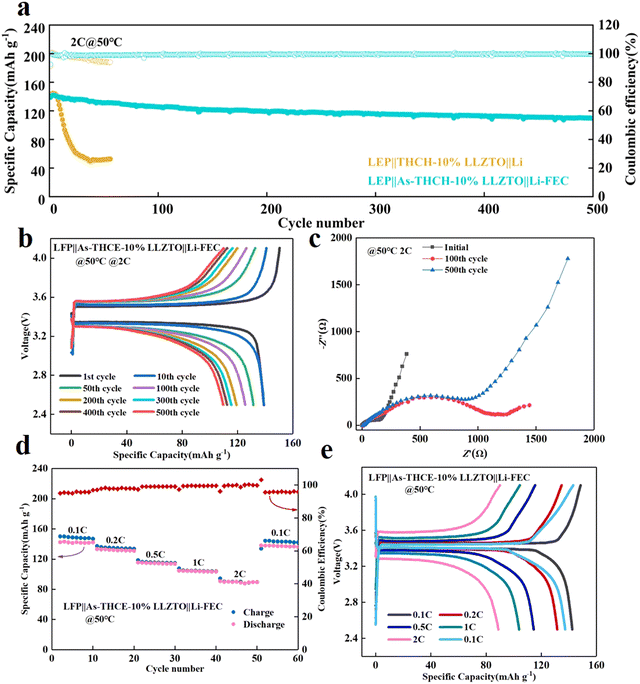 |
| Fig. 5 (a) The cycle performance of the LFP‖As-THCE-10%LLZTO‖Li-FEC cell at 2C at 50 °C; (b) charge–discharge curves at 2C of the LFP‖As-THCE-10%LLZTO‖Li-FEC cell at 50 °C; change of impedance during cycling at (c) 2C at 50 °C. (d) The rate performance and (e) charge–discharge curves of the LFP‖As-THCE-10%LLZTO‖Li-FEC cell at 50 °C. | |
To further study the cell performance at room temperature (25 °C), the LFP‖As-THCE-10%LLZTO‖Li-FEC cell was assembled for rate performance testing at 25 °C. As shown in Fig. 6a, the discharge capacities of the LFP‖As-THCE-10%LLZTO‖Li-FEC cell at 0.1C, 0.2C, 0.5C, 1C and 2C rates (1C = 170 mA h g−1) are 141.4, 133.1, 121.1, 112.0 and 89.3 mA h g−1, respectively, and the charge–discharge curves at different rates are shown in Fig. 6b. The cell's rate performance is also excellent at 25 °C. As shown in Fig. 6c, the initial discharge capacity of the LFP‖As-THCE-10%LLZTO‖Li-FEC cell at 2C is 111.6 mA h g−1, and the capacity retention rate is 84.73% after 500 cycles. Fig. 6d shows the charge/discharge curves of the LFP‖As-THCE-10%LLZTO‖Li-FEC cell with different number of cycles. As shown in Fig. 6e, the initial discharge capacity of the LFP‖As-THCE-10%LLZTO‖Li-FEC cell is 128.2 mA h g−1 at 0.2C and 25 °C, and the capacity retention is 93.22% after 120 cycles; the charge/discharge curves are shown in Fig. 6f. The high coulombic efficiency at room temperature is attributed to the asymmetric structure of the composite electrolyte. The gel-rich layer enhances the wettability of the cathode interface and achieves a soft contact at the interfaces,45 which promotes charge transfer at the interface. The ceramic-rich layer has high mechanical strength to mitigate the growth of lithium dendrites,53 and the Li-FEC electrode not only eases the interfacial contact but also coordinates with lithium anode to generate a fluorine-rich SEI layer, which further enhances the battery performance.51,54,55 The LFP‖As-THCE-10%LLZTO‖Li-FEC cell also exhibits excellent rate performance, high coulombic efficiency, and capacity retention at room temperature. It is indicated that the asymmetric structure of the composite electrolyte contributes to the enhancement of the cell performance. The interfacial composition of the solid electrolyte and LFP cathode was further confirmed by XPS testing (Fig. S7, ESI†). It can be clearly observed that the F 1s spectrum of LFP‖As-THCE-10%LLZTO‖Li-FEC has a stronger LiF signal and a lower C–O signal than that of the LFP‖As-THCE-10%LLZTO‖Li cell. This indicates that the cathode of LFP‖As-THCE-10%LLZTO‖Li-FEC contains a large number of inorganic components after cycling, which is conducive to the construction of a dense interface between the electrolyte and the electrode and enhance the oxidation resistance of the cathodic side.56
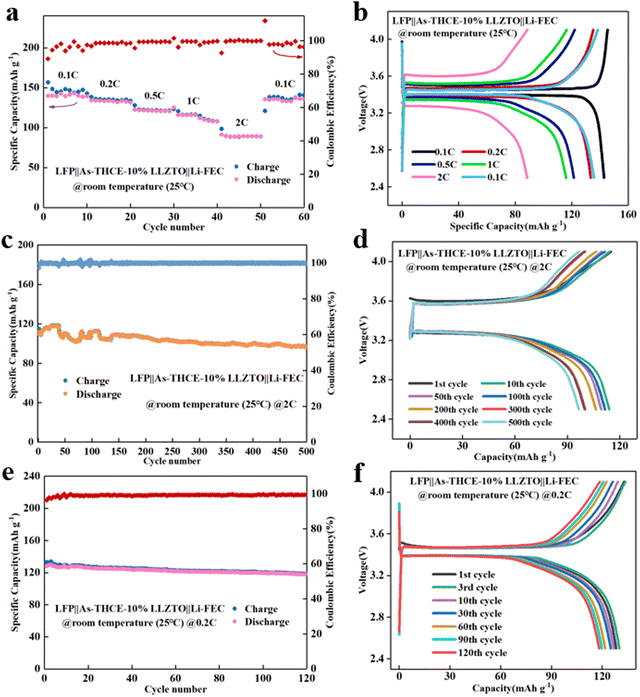 |
| Fig. 6 (a) The rate capability and (b) charge–discharge curves of the LFP‖As-THCE-10%LLZTO‖Li-FEC cell at 25 °C; the cycle performance of the LFP‖As-THCE-10%LLZTO‖Li-FEC cell at (c) 2C and (e) 0.2C at 25 °C; charge–discharge curves at (d) 2C and (f) 0.2C of LFP‖As-THCE-10%LLZTO‖Li-FEC cell at 25 °C. | |
4. Conclusion
In this work, asymmetric composite electrolytes were designed based on the selective adsorption of glass fibers. The cathodic side is a gel-rich layer with high wettability to promote charge transfer, and the anodic side is a ceramic-rich layer with high mechanical strength to effectively inhibit lithium dendrites. Also, the Li-FEC electrode not only improves the wettability of the anode interface and eases the interfacial contact but also coordinates with the electrolyte to generate a fluorine-rich SEI layer, which further enhances the battery performance. The assembled symmetric cell Li‖As-THCE-10%LLZTO‖Li was stably cycled for 200 h at a current density of 0.5 mA cm−2 and has excellent rate performance at 25 °C. The initial discharge capacity of the LFP‖As-THCE-10%LLZTO‖Li-FEC cell was 111.6 mA h g−1 at 2C and 25 °C, and the capacity retention rate was 84.73% after 500 cycles, while the initial discharge capacity was 128.2 mA h g−1 at 0.2C and 25 °C, and the capacity retention was 93.22% after 120 cycles. This work provides a new idea for improving the cycling stability and suppressing lithium dendrites in lithium metal batteries.
Conflicts of interest
The authors declare no conflict of interest.
Acknowledgements
This work was supported by the National Natural Science Foundation of China (22008053, 52002111), the Natural Science Foundation of Hebei Province (B2021208061, B2022208006, B2023208014), Beijing Natural Science Foundation (Z200011).
References
- L. Chen, W. Li, L. Z. Fan, C. W. Nan and Q. Zhang, Intercalated electrolyte with high transference number for dendrite-free solid-state lithium batteries, Adv. Funct. Mater., 2019, 29, 1901047 CrossRef
.
- Q. Wang, W. Zhu, Y. Su, D. Zhang, Z. Li, H. Wang, H. Sun, B. Wang, D. Zhou and L. Z. Fan, Synergistically enabling the interface stability of lithium metal batteries with soft ionic gel and garnet-type Li6.4La3Zr1.4Ta0.6O12 ceramic filler, J. Mater., 2022, 9, 568–576 Search PubMed
.
- H. Huo, Y. Chen, R. Li, N. Zhao, J. Luo, J. G. Pereira Da Silva, R. Mücke, P. Kaghazchi, X. Guo and X. Sun, Design of a mixed conductive garnet/Li interface for dendrite-free solid lithium metal batteries, Energy Environ. Sci., 2020, 13, 127–134 RSC
.
- J. Li, Y. Cai, Y. Cui, H. Wu, H. Da, Y. Yang, H. Zhang and S. Zhang, Fabrication of asymmetric bilayer solid-state electrolyte with boosted ion transport enabled by charge-rich space charge layer for −20∼70 °C lithium metal battery, Nano Energy, 2022, 95, 107027 CrossRef CAS
.
- N. Zhao, R. Fang, M. H. He, C. Chen, Y. Q. Li, Z. J. Bi and X. X. Guo, Cycle stability of lithium/garnet/lithium cells with different intermediate layers, Rare Met., 2018, 37, 473–479 CrossRef CAS
.
- L. Z. Fan, H. He and C. W. Nan, Tailoring inorganic–polymer composites for the mass production of solid-state batteries, Nat. Rev. Mater., 2021, 6, 1003–1019 CrossRef CAS
.
- H. Sun, W. Zhu, F. Yuan, D. Zhang, Z. Li, Q. Wang, W. Li, H. Wang and B. Wang, Hierarchical porous carbon nanofibers with enhanced capacitive behavior as a flexible self-supporting anode for boosting potassium storage, J. Power Sources, 2022, 523, 231043 CrossRef CAS
.
- Q. J. Wang, P. Zhang, B. Wang and L. Z. Fan, A novel gel polymer electrolyte based on trimethylolpropane trimethylacrylate/ionic liquid via in situ thermal polymerization for lithium-ion batteries, Electrochim. Acta, 2021, 370, 137706 CrossRef CAS
.
- H. Wang, Y. Sun, Q. Liu, Z. Mei, L. Yang, L. Duan and H. Guo, An asymmetric bilayer polymer-ceramic solid electrolyte for high-performance sodium metal batteries, J. Energy Chem., 2022, 74, 18–25 CrossRef CAS
.
- S. J. Tan, J. Yue, Y. F. Tian, Q. Ma, J. Wan, Y. Xiao, J. Zhang, Y. X. Yin, R. Wen, S. Xin and Y. G. Guo,
In situ encapsulating flame-retardant phosphate into robust polymer matrix for safe and stable quasi-solid-state lithium metal batteries, Energy Storage Mater., 2021, 39, 186–193 CrossRef
.
- D. Zhou, M. Zhang, F. Sun, T. Arlt, J. E. Frerichs, K. Dong, J. Wang, A. Hilger, F. Wilde, M. Kolek, M. R. Hansen, P. Bieker, I. Manke, M. C. Stan and M. Winter, Performance and behavior of LLZO-based composite polymer electrolyte for lithium metal electrode with high capacity utilization, Nano Energy, 2020, 77, 105196 CrossRef CAS
.
- L. Chen, Y. Li, S. P. Li, L. Z. Fan, C. W. Nan and J. B. Goodenough, PEO/garnet composite electrolytes for solid-state lithium batteries: From “ceramic-in-polymer” to “polymer-in-ceramic”, Nano Energy, 2018, 46, 176–184 CrossRef CAS
.
- S. Sen Chi, Y. Liu, N. Zhao, X. Guo, C. W. Nan and L. Z. Fan, Solid polymer electrolyte soft interface layer
with 3D lithium anode for all-solid-state lithium batteries, Energy Storage Mater., 2019, 17, 309–316 CrossRef
.
- Q. Wang, P. Zhang, W. Zhu, Z. Li, D. Zhang, H. Wang, H. Sun, B. Wang and S. S. Chi, Enabling good interfacial stability by dual-salt composite electrolyte for long cycle lithium metal batteries, J. Power Sources, 2023, 564, 232898 CrossRef CAS
.
- Q. Wang, P. Zhang, W. Zhu, D. Zhang, Z. Li, H. Wang, H. Sun, B. Wang and L. Z. Fan, A two-step strategy for constructing stable gel polymer electrolyte interfaces for long-life cycle lithium metal batteries, J. Mater., 2022, 8, 1048–1057 Search PubMed
.
- B. Wang, L. Gu, F. Yuan, D. Zhang, H. Sun, J. Wang, Q. Wang, H. Wang and Z. Li, Edge-enrich N-doped graphitic carbon: Boosting rate capability and cyclability for potassium ion battery, Chem. Eng. J., 2022, 432, 134321 CrossRef CAS
.
- G. Wang, P. He and L. Z. Fan, Asymmetric polymer electrolyte constructed by metal–organic framework for solid-sstate, dendrite-free lithium metal battery, Adv. Funct. Mater., 2021, 31, 2007198 CrossRef CAS
.
- F. Fu, Y. Liu, C. Sun, L. Cong, Y. Liu, L. Sun and H. Xie, Unveiling and alleviating chemical “Crosstalk” of succinonitrile molecules in hierarchical electrolyte for high-voltage solid-state lithium metal batteries, Energy Environ. Mater., 2022, 6, e12367 CrossRef
.
- F. Yuan, Z. Li, D. Zhang, Q. Wang, H. Wang, H. Sun, Q. Yu, W. Wang and B. Wang, Fundamental understanding and research progress on the interfacial behaviors for potassium-ion battery anode, Adv. Sci., 2022, 9, 2200683 CrossRef
.
- B. Jiang, Y. Wei, J. Wu, H. Cheng, L. Yuan, Z. Li, H. Xu and Y. Huang, Recent progress of asymmetric solid-state electrolytes for lithium/sodium-metal batteries, EnergyChem, 2021, 3, 100058 CrossRef CAS
.
- Y. Wang, S. Chen, Z. Li, C. Peng, Y. Li and W. Feng,
In situ generation of fluorinated polycarbonate copolymer solid electrolytes for high-voltage Li-metal batteries, Energy Storage Mater., 2022, 45, 474–483 CrossRef
.
- Y. Li, L. Yang, R. Dong, T. Zhang, J. Yuan, Y. Liu, Y. Liu, Y. Sun, B. Zhong, Y. Chen, Z. Wu and X. Guo, A high strength asymmetric polymer–inorganic composite solid electrolyte for solid-state Li-ion batteries, Electrochim. Acta, 2022, 404, 139701 CrossRef CAS
.
- F. Yuan, C. Shi, Q. Li, J. Wang, D. Zhang, Q. Wang, H. Wang, Z. Li, W. Wang and B. Wang, Unraveling the effect of intrinsic carbon defects on potassium storage performance, Adv. Funct. Mater., 2022, 32, 2208966 CrossRef CAS
.
- W. L. Huang, N. Zhao, Z. J. Bi, C. Shi, X. X. Guo, L. Z. Fan and C. W. Nan, Can we find solution to eliminate Li penetration through solid garnet electrolytes?, Mater. Today Nano, 2020, 10, 100075 CrossRef
.
- D. Cai, X. Qi, J. Xiang, X. Wu, Z. Li, X. Luo, X. Wang, X. Xia, C. Gu and J. Tu, A cleverly designed asymmetrical composite electrolyte via in situ polymerization for high-performance, dendrite-free solid state lithium metal battery, Chem. Eng. J., 2022, 435, 135030 CrossRef CAS
.
- R. Fan, C. Liu, K. He, S. Ho-Sum Cheng, D. Chen, C. Liao, R. K. Y. Li, J. Tang and Z. Lu, Versatile Strategy for Realizing Flexible Room-Temperature All-Solid-State Battery through a Synergistic Combination of Salt Affluent PEO and Li6.75La3Zr1.75Ta0.25O12 Nanofibers, ACS Appl. Mater. Interfaces, 2020, 12, 7222–7231 CrossRef CAS PubMed
.
- Y. Lin, K. Liu, C. Xiong, M. Wu and T. Zhao, A composite solid electrolyte with an asymmetric ceramic framework for dendrite-free all-solid-state Li metal batteries, J. Mater. Chem. A, 2021, 9, 9665–9674 RSC
.
- H. Huo, Y. Chen, J. Luo, X. Yang, X. Guo and X. Sun, Rational design of hierarchical “Ceramic-in-Polymer” and “Polymer-in-Ceramic” electrolytes for dendrite-free solid-state batteries, Adv. Energy Mater., 2019, 9, 1804004 CrossRef
.
- W. Huang, Z. Bi, N. Zhao, Q. Sun and X. Guo, Chemical interface engineering of solid garnet batteries for long-life and high-rate performance, Chem. Eng. J., 2021, 424, 130423 CrossRef CAS
.
- M. Jia, Z. Bi, C. Shi, N. Zhao and X. Guo, Air-stable dopamine-treated garnet ceramic particles for high-performance composite electrolytes, J. Power Sources, 2021, 486, 229363 CrossRef CAS
.
- S. A. Pervez, M. A. Cambaz, V. Thangadurai and M. Fichtner, Interface in solid-state lithium battery: Challenges, progress, and outlook, ACS Appl. Mater. Interfaces, 2019, 11, 22029–22050 CrossRef CAS PubMed
.
- L. Cong, Y. Li, W. Lu, J. Jie, Y. Liu, L. Sun and H. Xie, Unlocking the Poly(vinylidene fluoride-co-hexafluoropropylene)/Li10GeP2S12 composite solid-state Electrolytes for Dendrite-Free Li metal batteries assisting with perfluoropolyethers as bifunctional adjuvant, J. Power Sources, 2020, 446, 227365 CrossRef CAS
.
- Y. Gao, Z. Yan, J. L. Gray, X. He, D. Wang, T. Chen, Q. Huang, Y. C. Li, H. Wang, S. H. Kim, T. E. Mallouk and D. Wang, Polymer–inorganic solid–electrolyte interphase for stable lithium metal batteries under lean electrolyte conditions, Nat. Mater., 2019, 18, 384–389 CrossRef CAS PubMed
.
- M. Ebadi, C. Marchiori, J. Mindemark, D. Brandell and C. M. Araujo, Assessing structure and stability of polymer/lithium-metal interfaces from first-principles calculations, J. Mater. Chem. A, 2019, 7, 8394–8404 RSC
.
- J. Bao, X. Qu, G. Qi, Q. Huang, S. Wu, C. Tao, M. Gao and C. Chen, Solid electrolyte based on waterborne polyurethane and poly(ethylene oxide) blend polymer for all-solid-state lithium ion batteries, Solid State Ionics, 2018, 320, 55–63 CrossRef CAS
.
- Y. Guo, J. Cheng, Z. Zeng, Y. Li, H. Zhang, D. Li and L. Ci, Li2CO3: Insights into its blocking effect on Li-Ion transfer in garnet composite electrolytes, ACS Appl. Energy Mater., 2022, 5, 2853–2861 CrossRef CAS
.
- J. Cheng, Y. Guo, H. Zhang, F. Ji, X. Zhou, Z. Zeng, H. Liu, Q. Sun, D. Li and L. Ci, 2D flake-like garnet electrolytes for solid-state lithium metal batteries, Chem. Eng. J., 2024, 479, 147244 CrossRef CAS
.
- S. Yu, R. D. Schmidt, R. Garcia-Mendez, E. Herbert, N. J. Dudney, J. B. Wolfenstine, J. Sakamoto and D. J. Siegel, Elastic properties of the solid electrolyte Li7La3Zr2O12 (LLZO), Chem. Mater., 2016, 28, 197–206 CrossRef CAS
.
- B. Zhang, Y. Liu, X. Pan, J. Liu, K. Doyle-Davis, L. Sun, J. Liu, X. Jiao, J. Jie, H. Xie and X. Sun, Dendrite-free lithium metal solid battery with a novel polyester based triblock copolymer solid-state electrolyte, Nano Energy, 2020, 72, 104690 CrossRef CAS
.
- J. Chen, X. Fan, Q. Li, H. Yang, M. R. Khoshi, Y. Xu, S. Hwang, L. Chen, X. Ji, C. Yang, H. He, C. Wang, E. Garfunkel, D. Su, O. Borodin and C. Wang, Electrolyte design for LiF-rich solid–electrolyte interfaces to enable high-performance microsized alloy anodes for batteries, Nat. Energy, 2020, 5, 386–397 CrossRef CAS
.
- S. Liu, X. Xia, S. Deng, D. Xie, Z. Yao, L. Zhang, S. Zhang, X. Wang and J. Tu,
In situ solid electrolyte interphase from spray quenching on molten Li: A new way to construct high-performance lithium-metal anodes, Adv. Mater., 2019, 31, 1806470 CrossRef PubMed
.
- Y. Wei, J. Cheng, D. Li, Y. Li, Z. Zeng, H. Liu, H. Zhang, F. Ji, X. Geng, J. Lu and L. Ci, A structure self-healing Li-rich cathode achieved by lithium supplement of Li-rich LLZO coating, Adv. Funct. Mater., 2023, 33, 2214775 CrossRef CAS
.
- J. Gao, J. Zhu, X. Li, J. Li, X. Guo, H. Li and W. Zhou, Rational design of mixed electronic-ionic conducting Ti-doping Li7La3Zr2O12 for Lithium dendrites suppression, Adv. Funct. Mater., 2021, 31, 2001918 CrossRef CAS
.
- M. Nakayama, S. Wada, S. Kuroki and M. Nogami, Factors affecting cyclic durability of all-solid-state lithium polymer batteries using poly(ethylene oxide)-based solid polymer electrolytes, Energy Environ. Sci., 2010, 3, 1995–2002 RSC
.
- F. Du, N. Zhao, Y. Li, C. Chen, Z. Liu and X. Guo, All solid state lithium batteries based on lamellar garnet-type ceramic electrolytes, J. Power Sources, 2015, 300, 24–28 CrossRef CAS
.
- A. J. Bhattacharyya and J. Maier, Second phase effects on the conductivity of non-aqueous salt solutions: “Soggy sand electrolytes”, Adv. Mater., 2004, 16, 811–814 CrossRef CAS
.
- B. Zhang, Y. Zhang, N. Zhang, J. Liu, L. Cong, J. Liu, L. Sun, A. Mauger, C. M. Julien, H. Xie and X. Pan, Synthesis and interface stability of polystyrene-poly(ethylene glycol)-polystyrene triblock copolymer as solid-state electrolyte for lithium-metal batteries, J. Power Sources, 2019, 428, 93–104 CrossRef CAS
.
- F. Han, Y. Zhu, X. He, Y. Mo and C. Wang, Electrochemical stability of Li10GeP2S12 and Li7La3Zr2O12 solid electrolytes, Adv. Energy Mater., 2016, 6, 1501590 CrossRef
.
- C. Wang, H. Zhang, J. Li, J. Chai, S. Dong and G. Cui, The interfacial evolution between polycarbonate-based polymer electrolyte and Li-metal anode, J. Power Sources, 2018, 397, 157–161 CrossRef CAS
.
- J. T. Han, B. H. Jeong, S. H. Seo, K. C. Roh, S. Kim, S. Choi, J. S. Woo, H. Y. Kim, J. I. Jang, D. C. Shin, S. Jeong, H. J. Jeong, S. Y. Jeong and G. W. Lee, Dispersant-free conducting pastes for flexible and printed nanocarbon electrodes, Nat. Commun., 2013, 4, 1–8 Search PubMed
.
- J. Zheng, W. Zhou, J. Zhang, X. Liu, Q. Feng, X. An, B. Tang, X. Zhou, H. Wang and S. Peng, Cr depletion of the second phase particles in a Zr-Sn-Nb-Fe-Cr alloy: A TEM and SIMS study, J. Nucl. Mater., 2017, 491, 1–8 CrossRef CAS
.
- M. Arrese-Igor, M. Martinez-Ibañez, J. M. López del Amo, E. Sanchez-Diez, D. Shanmukaraj, E. Dumont, M. Armand, F. Aguesse and P. López-Aranguren, Enabling double layer polymer electrolyte batteries: Overcoming the Li-salt interdiffusion, Energy Storage Mater., 2022, 45, 578–585 CrossRef
.
- F. Li, J. He, J. Liu, M. Wu, Y. Hou, H. Wang, S. Qi, Q. Liu, J. Hu and J. Ma, Gradient solid electrolyte interphase and lithium-ion solvation regulated by bisfluoroacetamide for stable lithium metal batteries, Angew. Chem., Int. Ed., 2021, 60, 6600–6608 CrossRef CAS PubMed
.
- P. Jaumaux, Q. Liu, D. Zhou, X. Xu, T. Wang, Y. Wang, F. Kang, B. Li and G. Wang, Deep-eutectic-solvent-based self-healing polymer electrolyte for safe and long-life lithium-metal batteries, Angew. Chem., 2020, 132, 9219–9227 CrossRef
.
- N. Wu, P. H. Chien, Y. Qian, Y. Li, H. Xu, N. S. Grundish, B. Xu, H. Jin, Y. Y. Hu, G. Yu and J. B. Goodenough, Enhanced surface interactions enable fast Li+ conduction in oxide/polymer composite electrolyte, Angew. Chem., Int. Ed., 2020, 59, 4131–4137 CrossRef CAS PubMed
.
- J. Lu, C. Xu, W. Dose, S. Dey, X. Wang, Y. Wu, D. Li and L. Ci, Microstructures of layered Ni-rich cathodes for lithium-ion batteries, Chem. Soc. Rev., 2024, 53, 4707–4740 RSC
.
|
This journal is © the Partner Organisations 2024 |