DOI:
10.1039/D3RA06179E
(Review Article)
RSC Adv., 2023,
13, 33318-33335
Recent advances in biopolymers-based carbon materials for supercapacitors
Received
11th September 2023
, Accepted 27th October 2023
First published on 15th November 2023
Abstract
Supercapacitors as potential candidates for novel green energy storage devices demonstrate a promising future in promoting sustainable energy supply, but their development is impeded by limited energy density, which can be addressed by developing high-capacitance electrode materials with efforts. Carbon materials derived from biopolymers have received much attention for their abundant reserves and environmentally sustainable nature, rendering them ideal for supercapacitor electrodes. However, the limited capacitance has hindered their widespread application, resulting in the proposal of various strategies to enhance the capacity properties of carbon electrodes. This paper critically reviewed the recent research progress of biopolymers-based carbon electrodes. The advances in biopolymers-based carbon electrodes for supercapacitors are presented, followed by the strategies to improve the capacitance of carbon electrodes which include pore engineering, doping engineering and composite engineering. Furthermore, this review is summarized and the challenges of biopolymer-derived carbon electrodes are discussed. The purpose of this review is to promote the widespread application of biopolymers in the domain of supercapacitors.
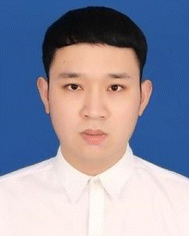 Hongjie Li | Mr Hongjie Li received his Bachelor degree in Materials Science and Engineering from Wuhan University of Technology in 2021. He is presently a postgraduate student at the School of Materials Science and Engineering in Shanghai Jiao Tong University. He is currently working on the research of biomass derived porous carbon and their applications in supercapacitors. |
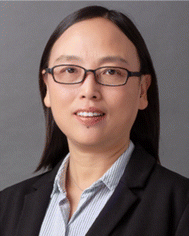 Shenmin Zhu | Prof. Shenmin Zhu received her PhD degree from Shanghai Jiao Tong University in 2001. She is presently a professor at the School of Materials Science and Engineering, State Key Lab of Metal Matrix Composites, Shanghai Jiao Tong University. Her current fields of interest are graphene-based functional materials, porous carbon, and bio-inspired photonic crystals with stimuli-responsive properties. |
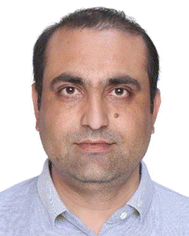 Imran Zada | Dr Imran Zada received his PhD degree in Materials Science and Engineering from Shanghai Jiao Tong University, China, in 2018. Currently, he is working as Post-doctor at the State Key Laboratory of Metal Matrix Composites, Shanghai Jiao Tong University. His research is mainly focused on Bio-inspired materials, Photothermal materials and Energy storage materials for supercapacitors. |
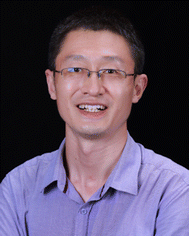 Yao Li | Asso. Prof. Yao Li received his PhD in Material Science from Shanghai Jiao Tong University, China in 2015. He is presently an associate professor at the School of Materials Science and Engineering, State Key Lab of Metal Matrix Composites, Shanghai Jiao Tong University. He is working on the research of bio-inspired material and carbon matrix material, as well as their application in environmental treatment and energy storage. |
1. Introduction
Energy plays a pivotal role in contemporary society, but excessive consumption of fossil fuels resulting from rapid global population growth and economic progress in the past few decades has caused a severe ecological crisis.1 The concern about the deterioration of the natural environment has led mankind to recognize the importance of developing clean energy sources such as hydrogen, wind and solar to replace non-renewable energy sources. Consequently, strategies like sustainable development, carbon neutrality and carbon peaking have been proposed to promote the utilization of clean energy sources.2,3 However, clean energy production is an intermittent and long-cycle process requiring stable energy storage technology for universal access to clean energy.4
Lithium-ion batteries (LIBs) stand as the foremost energy storage devices (ESDs) extensively employed in contemporary applications, whereas their development is constrained by issues such as shortage in lithium metal resources, limitations in overcharging and over-discharging, low output power and challenges in recycling waste batteries.5 Supercapacitors (SCs) have gained significant interest due to exceptional cycle life, excellent power density, affordability and superior safety in comparison to LIBs.6 Over the past few years, advancements in the sectors of flexible wearable electronic devices, hybrid vehicles and integrated power grids have given rise to novel iterations of SCs, such as metal ion hybrid SCs, micro-SCs and flow SCs.7 The design of new SCs relies on the innovation of materials. As the core of SCs, electrode materials are crucial for improving electrochemical properties.8 The main shortcoming of SCs is lower energy density (Fig. 1a),9 which is affected by the capacitance and voltage window (E = CV2/2).10 Therefore, there are three strategies to promote the energy density of SCs: (a) preparation of high-capacitance electrode materials, (b) development of electrolytes with wide operating voltage windows and (c) design of new devices.11,12 This review focuses on biopolymers-based carbon electrodes with high capacitance.
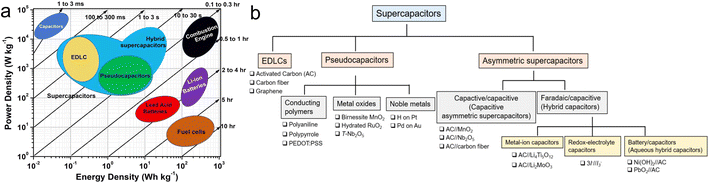 |
| Fig. 1 (a) Ragone diagram of ESDs;23 (b) classification of SCs and examples of corresponding electrode materials.5 | |
According to the electrode materials employed, SCs can be classified into three main kinds: electric double-layer capacitors (EDLCs), pseudocapacitors (PCs) and asymmetric supercapacitors (ASCs) in Fig. 1b.5 EDLCs store energy through ion adsorption–desorption at the electrode–electrolyte interface,13 wherein the electrode predominantly comprises carbon-based materials, encompassing carbon quantum dots, carbon fibers, graphene and activated carbon.12,14,15 The major advantage of EDLCs is the decent cycle stability, but the poor capacitance leads to the lower energy density of EDLCs (<10 W h kg−1) compared to LIBs (50–1000 W h kg−1).16 PCs store energy based on rapid and reversible oxidation–redox reactions,17 and electrode materials for PCs mainly include noble metals (e.g., Pt, Au, etc.), transition metal compounds (e.g., Nb2O5, RuO2, NiCo2S4, NixPy, etc.), alongside conductive polymers such as polyaniline (PANI), polypyrrole (PPy), and polythiophene (PTh).18–22 The capacitance of pseudocapacitors is generally better than EDLCs, but their limited cycling stability poses challenges for long-term operation. The ASCs consist of two types: capacitor/capacitor and battery/capacitor (hybrid capacitor) whose greatest advantage is to utilize the potential difference between anodes and cathodes to extend the voltage window of ASCs, while taking into account the high capacitance, thus further enhancing the energy density to satisfy the practical requirements.
It is clear from the above that carbon materials are widely applied in SCs. However, traditional carbon electrode materials derived from petroleum-based polymers are difficult to degrade and the resulting waste is a burden to the environment,24 while the high cost hinders the promotion of SCs, so the identification of cheap and inexpensive carbon precursors is an urgent task. As biologically originated macromolecules, biopolymers have unrivalled advantages owing to their abundant reserves, degradability and renewability. Biopolymers (e.g., cellulose, chitin, lignin, agar, gelatin, keratin, etc.) have been reported in works of literature as carbon electrode precursors for SCs.25 However, the existing articles are more of a review of single biopolymers for SCs and lack overall analysis. Therefore, this paper reviews research advances in biopolymers-based carbon electrodes for SCs. It is divided into three general parts: (a) review of the recent progress of several types of biopolymers popularly deployed for carbon electrodes in SCs; (b) summary of the approaches to improve the capacitance from three aspects: porous structure design of carbon electrodes, heteroatom doping and multi-component composite;26 (c) discussion about the challenges and future perspective of biopolymers-based carbon electrode materials Scheme 1.
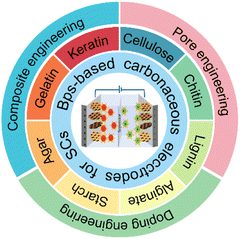 |
| Scheme 1 Illustration of biopolymers-based carbon materials for SCs. | |
2. Biopolymers-based electrodes for SCs
Biopolymers have gained significant interest as the precursor of electrode materials for SCs thanks to their advantages of renewable nature, abundant reserves, affordability and non-pollution.27 In addition, biopolymers can be synthetically transformed into diverse manifestations of carbon-based materials, encompassing carbon microspheres, carbon nanofibers, carbon nanosheets, and carbon aerogels.28 Meanwhile, biopolymers are rich in heteroatoms, which can contribute to additional pseudocapacitance.29 Moreover, they carry multiple functional groups (e.g., –OH, –NH3, –COOH, etc.) which can be compounded with other substances through chemical reactions and physical interactions.30 Considering the diversity of biopolymers, this part mainly focuses on biopolymers derived from biological resources for SCs. Table 1 summarizes the recent progress for biopolymers-based carbonaceous electrode materials for SCs.
Table 1 Overview of biopolymers-based carbon electrodes for SCsa
Precursors |
Electrode materials |
SSA (m2 g−1) |
Cs (F g−1) |
Ed (W h kg−1) |
Pd (W kg−1) |
Cycle stability |
Ref. |
Note: SSA: specific surface area; Cs: specific capacitance; Ed: energy density; Pd: power density; CNFs: cellulose nanofibers; BCs: bacterial nanocelluloses; CNCs: cellulose nanocrystals; SLS: sodium lignosulfonate; CA: cellulose acetate; SA: sodium alginate; CD: cyclodextrin. |
Cellulose fibers |
CS@CF-KFe |
1515.6 |
313@1 A g−1 |
21.5 |
456.6 |
100.2% (10 000 cycles) |
33 |
BCs |
u-MPC |
1554 |
430@0.5 A g−1 |
0.77 mW h cm−2 |
17.9 W h L−1 |
100% (10 000 cycles) |
35 |
BCs |
CBC-N@NiCo2S4 |
85.2 |
1078@1 A g−1 |
42.6 |
1500 |
96.8% (5000 cycles) |
155 |
BCs |
PANI@CNF/CNS-2 |
421.4 |
810@1 A g−1 |
65.3 |
800 |
98% (5000 cycles) |
160 |
CNFs |
CNFAs-17% |
514.7 |
440.29@1 A g−1 |
0.081 mW h cm−2 |
1.19 mW cm−2 |
100% (7000 cycles) |
36 |
CNCs |
CU-3 |
366.5 |
570.6@1 A g-1 |
— |
— |
91.2% (1000 cycles) |
139 |
Cellulose |
CDC |
1381 |
357@0.5 A g−1 |
243 |
492 |
85% (20 000 cycles) |
104 |
Cellulose |
Ccel-LE |
1893 |
253@0.1 A g−1 |
8.77 |
— |
96.5% (10 000 cycles) |
110 |
Cellulose |
WC-E-100-48 |
1418 |
384 (8.41 F cm−2)@1 mA cm−2 |
10.97 |
26.33 |
86.58% (15 000 cycles) |
114 |
Cellulose |
Cell@PPy |
139.8 |
387.6@0.5 A g−1 |
— |
— |
92.6% (10 000 cycles) |
159 |
Chitin |
HPCNs-800 |
855 |
316@5 mV s−1 |
23.8 |
215 |
100% (7000 cycles) |
40 |
Chitin |
NSCA-1000 |
2540 |
249.4@1 A g−1 |
26.15 |
950 |
98.44% (15 000 cycles) |
105 |
Chitin |
HPC-700 |
1488.3 |
412.5@0.5A g−1 |
9.67 |
— |
99.6% (10 000 cycles) |
111 |
Chitosan |
C-HPC |
3532 |
455@0.5 A g−1 |
20.6 |
226.8 |
99% (7000 cycles) |
43 |
Chitosan |
CuO/Cu@C-700 |
313.2 |
2479@0.5 A g−1 |
76.87 |
374.5 |
82.43% (10 000 cycles) |
44 |
Chitosan, SLS |
CHPC-800 |
2700.65 |
332@1 A g−1 |
17.7 |
166.4 |
97% (10 000 cycles) |
46 |
Chitosan, gelatin |
CHPC-0.5 |
927.17 |
331@1 A g−1 |
34 |
900 |
97% (10 000 cycles) |
47 |
Chitosan |
HPC-1 |
2787.47 |
253@0.5A g−1 |
5.83 |
4997.1 |
94.3% (3000 cycles) |
99 |
Chitosan |
PBE |
1011 |
250.5@0.5 A g−1 |
28.3 |
150.2 |
107% (5000 cycles) |
121 |
Chitosan |
NCSIL-900 |
301 |
355@0.2 A g−1 |
5.83 |
100 |
91% (10 000 cycles) |
127 |
Chitosan |
APC-2 |
1650 |
320@1 A−1 |
15.82 |
850 |
97% (10 000 cycles) |
146 |
Chitosan |
BNPC-Fe |
806.8 |
393@0.5 A g−1 |
19.1 |
400 |
103% (8000 cycles) |
147 |
Chitosan |
N, S-GHPCF |
2279.2 |
405@1 A g−1 |
18.4 |
300 |
98.8% (10 000 cycles) |
149 |
Chitosan |
NiCo-LDH/HPCA-30 |
1480.47 |
1504@1 A g−1 |
33.33 |
800 |
90.76% (3000 cycles) |
154 |
Enzymatic lignin |
LHC-3K |
1660 |
420@0.1 A g−1 |
46.8 |
— |
99% (10 000 cycles) |
52 |
Lignin |
ACS-600 |
2237.9 |
254.2@ 0.2 A g−1 |
22.4 |
646 |
80% (10 000 cycles) |
53 |
Lignin fibers |
CF-I-2 |
712 |
333@1 A g−1 |
— |
— |
100% (2000 cycles) |
55 |
Industrial lignin |
C-LRGO41 |
444.29 |
330@1 A g−1 |
11.3 |
254 |
100% (2000 cycles) |
57 |
Lignin, CA |
CFs-5 |
837 |
346.6@ 0.1 A g−1 |
31.5 |
400 |
— |
102 |
Lignin |
LDMCN-700-2 |
1012.5 |
245@0.5 A g−1 |
— |
— |
95.7% (5000 cycles) |
109 |
Lignin |
CSH-P.S.-PC-800 |
3439 |
— |
263.9 |
700 |
75.2% (10 000 cycles) |
113 |
SLS |
HPCSLS-700-1 |
903 |
247@0.05 A g−1 |
8.4 W h L−1 |
13.9 W L−1 |
92% (20 000 cycles) |
131 |
SLS |
LSC-ZnC2O4/PANI |
178 |
643@1 A g−1 |
36.3 |
850.2 |
88% (5000 cycles) |
161 |
Cobalt alginate |
N-PCNFs |
283 |
197@1 A g−1 |
— |
— |
91.7% (5000 cycles) |
60 |
Potassium alginate |
IPC-800 |
1145.8 |
279@1 A g−1 |
16.9 |
— |
96.6% (10 000 cycles) |
61 |
SA |
DSPCs-1 |
872.6 |
390.5@0.5 A g−1 |
10.17 |
150 |
100% (10 000 cycles) |
62 |
SA |
SAM-700-4 |
2577.62 |
441.8@0.5A g−1 |
20.87 |
4000 |
75.11% (5000 cycles) |
140 |
SA |
NSC |
387 |
309@0.5 A g−1 |
15.9 W h L−1 |
426 W L−1 |
90% (3000 cycles) |
145 |
SA |
CeCoSx-SA/GF aerogels |
10.35 |
873.3@1 A g−1 |
29.58 |
801 |
87.1% (5000 cycles) |
59 |
CA |
MXene/CA film |
27.3 |
1244.6 F cm−3@1 A g−1 |
27.2 W h L−1 |
— |
93.5% (30 000 cycles) |
150 |
Tapioca starch |
HPCMS-31 |
1668 |
286@0.5 A g−1 |
8.64 |
24.7 |
98% (20 000 cycles) |
64 |
α-starch |
SAC-700-50 |
1863 |
335.6@0.5 A g−1 |
7.4 |
5679.6 |
96% (20 000 cycles) |
65 |
Starch |
I-PCs-0.14 |
2989 |
1216@2 A g−1 |
65.4 |
787.3 |
110.2% (10 000 cycles) |
66 |
Starch |
st06-900C-HCl |
2300 |
229@ 1 A g−1 |
— |
— |
94% (10 000 cycles) |
119 |
β-CD |
PMnCD(β) |
499 |
228@1 mA cm−2 |
25.3 |
400 |
>94% (10 000 cycles) |
67 |
β-CD |
CDC-MB |
1580 |
291.5@0.5 A g−1 |
19.7 |
— |
96.3% (10 000 cycles) |
68 |
β-CD |
PCD-PC |
3710 |
416@0.5A g−1 |
23.4 |
224.9 |
100% (10 000 cycles) |
69 |
γ-CD |
HPC-NS |
777 |
405@1 A g−1 |
24.3 |
151 |
95% (10 000 cycles) |
126 |
Agar |
NKAC |
2185.5 |
366.9@0.5A g−1 |
5.9 |
103.2 |
96.4% (10 000 cycles) |
71 |
Agar |
BN-PCS |
2827.7 |
361.1@0.5 A g−1 |
43.5 |
375 |
91.1% (10 000 cycles) |
72 |
Collagen |
CSGC-700 |
2419.2 |
138.8 mA h g−1@ 0.1 A g−1 |
111.1 |
165 000 |
87.2% (10 000 cycles) |
75 |
Collagen |
C-G-collagen |
1087 |
365@1 mV s−1 |
50.69 |
21.59 |
97% (10 000 cycles) |
76 |
Gelatin |
HPC-3.5 |
2473 |
216.5 @1 A g−1 |
108.6 |
961.1 |
84.4% (10 000 cycles) |
79 |
Gelatin |
1G-30SC-750 |
350 |
215@0.1 A g−1 |
— |
— |
97.4% (10 000 cycles) |
81 |
Gelatin |
Ni2P-CNFs-700 |
12.9 |
145 mA h−1@0.5 A g−1 |
42 |
413 |
88% (6000 cycles) |
156 |
Fibroin |
NPC-750 |
80.4 |
565.3@1 A g−1 |
26.2 |
263.9 |
93.3% (10 000 cycles) |
83 |
Fibroin, CNFs |
NPCN-50 |
1882 |
329.9@0.25 A g−1 |
37.5 |
186.3 |
99.5% (5000 cycles) |
84 |
Keratin |
H2SO4-KK-3 |
2864 |
270@1 A g−1 |
11.84 |
8525 |
98% (10 000 cycles) |
87 |
Keratin |
HHC9K4 |
1548 |
999@1 A g−1 |
32 |
325 |
98% (10 000 cycles) |
88 |
2.1 Polysaccharide
2.1.1 Cellulose. Cellulose, primarily derived from the walls of plant cells and microbial tissues, is the most abundant and widely utilized biopolymer, where D-glucose units are connected through β-(1–4) glycosidic bonds.31 Cellulose is an ideal precursor for carbon electrodes, benefiting from the high carbon content as well as abundant pore structure after a high-temperature reaction.32 Zhang et al. grew glucose-derived porous carbon flakes on cellulose fibers based on the dual effect of K3[Fe(C2O4)3]-catalyzed graphitization and activation, to obtain “mushroom branch”-like porous carbon (CS@CF-KFe, Fig. 2a and b).33 The CS@CF-KFe exhibited a favorable rate performance (76.8% retention from 1 to 30 A g−1) and outstanding cycle life (100.2% over 10
000 cycles at 100 mV s−1), which are attributed to its lamellar architecture, extended specific surface area (SSA), and abundant micropores facilitating the passage of aqueous ions.
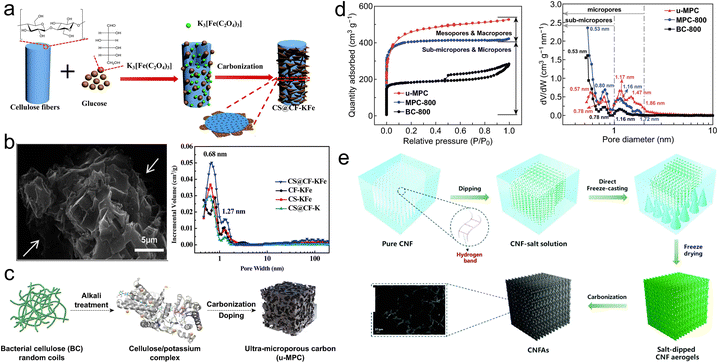 |
| Fig. 2 (a) Synthetic route for the synthesis of CS@CF-KFe; (b) SEM and pore size distribution (PSD) plots of CS@CF-KFe;33 (c) schematic for the synthesis of u-MPC; (d) nitrogen adsorption–desorption and PSD curves of samples;35 (e) preparation process of CNFAs.36 | |
After acid or enzymatic treatment, cellulose has the potential to be transformed into nanocelluloses, which consist of cellulose nanofibers (CNFs), cellulose nanocrystals (CNCs) and bacterial nanocelluloses (BCs).34 Ding's group developed highly porous carbon (uMPC) with one-step carbonization and activation utilizing compressed BCs as the precursor and thiourea as the doping agent (Fig. 2c).35 The uMPC possessed ultra-small micropores (−2 nm) and sub-micropores (<1 nm) in Fig. 2d, which improved ion storage and ion/electron diffusion, resulting in the superior capacitance (430 F g−1 at 0.5 A g−1) coupled with decent rate capability (76% retention to 10 A g−1) and almost no capacity loss upon undergoing 10
000 cycles.
Moreover, cellulose molecules can be assembled into aerogels with interlinked porous structures because of physical effects, which can effectively accelerate the transport of electrolyte ions, resulting in excellent electrochemical performance.37 A facile inorganic salt-assisted CNF pyrolysis approach for preparing carbon aerogels (CNFAs) was introduced by Chen's group (Fig. 2e).36 The large SSA and three-dimensional (3D) porous network provide rich channels of ion transport. The CNFAs realized an improved gravimetric capacitance (440.29 F g−1 at 1 A g−1). Furthermore, the corresponding symmetrical supercapacitors (SSCs) delivered a desirable areal energy density (0.081 mW h cm−2 at 1.19 mW cm−2), as well as a nearly 100% retention over 7000 cycles.
2.1.2 Chitin and chitosan. Chitin exists in the exoskeletons of arthropods as well as cell walls of fungi, green algae, yeasts and microorganisms, rendering it the second-largest biopolymer after cellulose.38 Chitin is a decent precursor for nitrogen-doping and its layered structure facilitates the formation of carbon nanosheets for the formation of connected conductive networks, enabling outstanding electrochemical performance.39 Gao and coworkers synthesized 2D hierarchical porous carbon nanosheets (HPCNs) by hydrothermally treating bulk chitin with phytate assistance followed by carbonization.40 The HPCNs exhibited ultrathin thickness (3.6 nm), moderate SSA, hierarchical porous architecture and abundant self-doped heteroatoms, resulting in HPCNs-based SSCs achieving a considerable energy density of 23.8 W h kg−1 at 215 W kg−1.Chitosan, the deacetylated derivative of chitin as shown in Fig. 3a, exhibits solubility in acidic solutions to form gels, while it possesses numerous functional groups capable of chelating with metal ions.41,42 Huang et al. reported that chitosan-based hierarchically porous carbon (C-HPC) with exceptional SSA of 3532 m2 g−1 was prepared by dissolving chitosan in acetic acid via hydrothermal carbonization and KOH activation (Fig. 3b).43 The C-HPC demonstrated a superior capacity (455 F g−1), and the assembled SSCs exhibited a maximum energy density of 20.6 W h kg−1 at 226.8 W kg−1 in 1 M Na2SO4. Xi's group employed a facile approach to prepare a composite of CuO/Cu@C, achieved through the chelation of Cu2+ with chitosan.44 Chitosan was transformed into the N-doped carbon framework and copper precursors into CuO/Cu nanoflowers. Remarkably, CuO/Cu@C-700 carbonized at 700 °C developed a capacity of 2479 F g−1 at 0.5 A g−1, and corresponding ASCs exhibited an impressive energy density (76.87 W h kg−1 at 374.5 W kg−1) on account of 3D interconnected porous structure and favorable SSA.
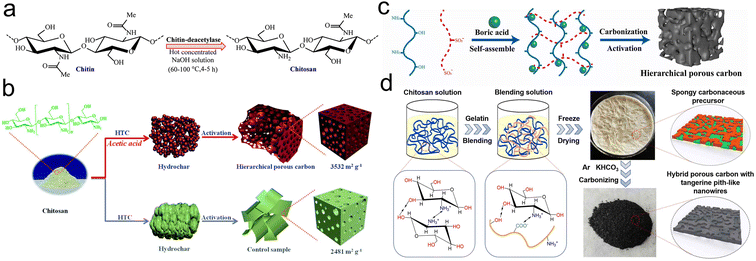 |
| Fig. 3 (a) Process of deacetylation of chitin for the fabrication of chitosan;42 (b) diagram for the construction of CHPC;43 (c) preparation mechanism diagram of CHPC-800;46 (d) scheme for the synthesis procedure of CHPC-0.5.48 | |
Moreover, chitosan is a polycationic polymer that can self-assemble with polyanionic polymers under acidic conditions, leading to form co-doped porous carbon.45 Sun and coworkers constructed the 3D porous carbon (CHPC) doped N, B and S by self-assembling sodium lignosulfonate (SLS) with chitosan at the aid of boric acid (Fig. 3c).46 The CHPC-800 activated at 800 °C a suitable capacity of 332 F g−1 at 1 A g−1, still remaining 267 F g−1 at 20 A g−1. Yuan et al. synthesized hierarchical porous carbon (CHPC) by combining chitosan with gelatin (Fig. 3d).47 Benefiting from high heteroatom content, SSA and appropriate average pore size, the optimal sample yielded a remarkable capacitance (331 F g−1 at 1 A g−1) with decent rate capability and mechanical stability.
2.1.3 Lignin. Lignin is an abundant class of aromatic polymers whose structure is forged by phenyl-propane structural units, specifically guaiacol (G), syringyl (S) and p-phenyl hydroxyl (H) via carbon–carbon and ether bonds (Fig. 4a).49 Lignin interacts with cellulose and hemicellulose to ensure the toughness of cell wall.50
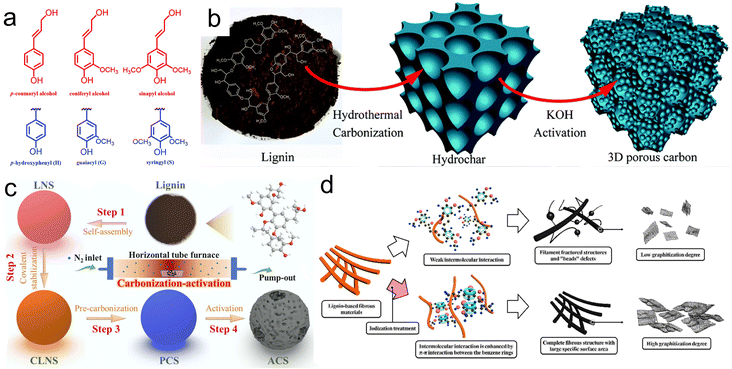 |
| Fig. 4 (a) Monomer units and precursors of lignin;49 (b) illustration for the fabrication of LHC;52 (c) diagram for the synthesis of ACS-600;53 (d) structure comparison between carbon fibers by iodization and original carbon fibers.55 | |
Lignin is ideal for preparing carbon electrodes with large carbon yields and active functional groups.51 Guo and coworkers transformed enzymatic lignin into 3D porous carbon (LHC) possessing a generous SSA (1660 m2 g−1) by hydrothermal carbonization and KOH activation (Fig. 4b), realizing a desirable capacity of 420 F g−1. The corresponding SSCs delivered an energy density of 46.8 W h kg−1 in ionic liquid.52 Wang et al. obtained monodisperse lignin-derived blueberry-like porous carbon nanospheres (ACS) through a four-step process as shown in Fig. 4c.53 The ACS-600 carbonized at 600 °C achieved an impressive capacitance (254.2 F g−1 at 0.2 A g−1) in 6 M KOH. The SSCs assembled with ACS-600 delivered a voltage range from 0 to 2 V and energy density was up to 22.4 W h kg−1 in 1 M Na2SO4. However, the amorphous structure of lignin after carbonization seriously hinders the migration and diffusion of electrolyte ions, so it is necessary to modify lignin.54 Han et al. demonstrated a simple method of iodinating lignin fibers (Fig. 4d), where a π–π conjugated structure was formed, enhancing intermolecular interactions and allowing the precursors to maintain original morphology.55 The carbon fibers maintained exceptional graphitization and proper SSA, leading to an enhancement in capacitance with a value of 333 F g−1 at 1 A g−1.
Furthermore, compounding lignin to 2D materials can optimize the structure of lignin while also helping to alleviate the stacking problem of 2D materials.56 Jiang et al. chose industrial lignin as the carbon precursor and reducing agent to achieve an ordered modification of lignin on the rGO surface through hydrothermal reaction followed by carbonization, which not only suppressed the stacking of rGO nanosheets but also avoided self-aggregation of lignin after carbonization.57 The lignin/rGO generated porous structures during no-activator carbonization, exhibiting an impressive capacitance of 330 F g−1 at 1 A g−1 and durable cyclability as evidenced by retaining 100% of initial capacity after enduring 10
000 cycles.
2.1.4 Alginate. Alginate, derived from brown algae or Sargassum, is a class of linear anionic biopolymers. The alginate molecular chain is composed of the homopolymerized region (G) of α-L-glucuronic acid residue, the homopolymerization region (M) of β-D-mannuronic acid residue, and the hetero-polymerization region (GM) connected by (1 → 4) glycosidic bond (Fig. 5a).58,59
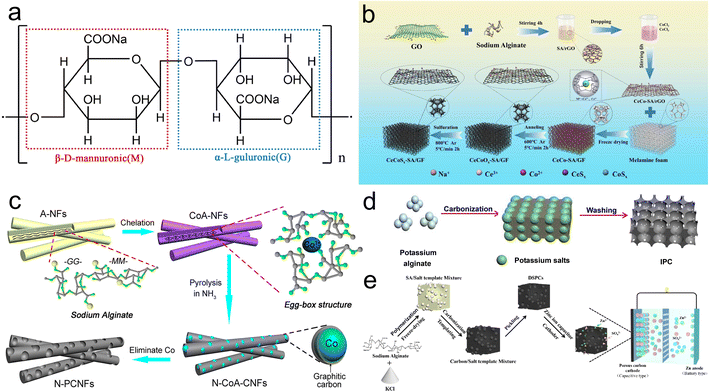 |
| Fig. 5 (a) Chemical formula of alginate; (b) diagram for the stepwise preparation of CeCoSx-SA/GF;59 (c) illustration for the synthesis of N-PCNFs;60 (d) schematic for the construction of IPC-800;61 (e) schematic diagram for the synthesis of DSPCs.62 | |
The functional groups in the G region of alginate enable cross-linking with metal ions to realize the “egg-shell” structure, which can be employed to achieve effective loading of metal compounds on carbon substrates, alleviating the problems of low multiplicity and poor electrical conductivity of pseudocapacitive materials. Guo et al. put forward a facile in situ synthesis strategy to construct N, S doped porous CeCoSx-SA/GF aerogels based on the pairing principle of sodium alginate (SA) with Ce3+ and Co2+ and the dispersion effect of melamine foam on graphene (Fig. 5b).59 The CeCoSx-SA/GF exhibited an outstanding capacity (873.3 F g−1 at 1 A g−1), complemented by the capacity retention of 87.1% after 5000 cycles, and the ASCs where CeCoSx-SA/GF was applied as the positive electrodes exhibited a remarkable energy density (29.58 W h kg−1 at 801 W kg−1). Furthermore, the characteristic for cross-linking alginate with metal ions is also frequently applied to pore engineering. Li's group prepared nitrogen-doped porous graphitic carbon nanofibers (N-PCNFs) with large-size mesopores (10–40 nm) utilizing the cross-linking of SA with Co2+ (Fig. 5c).60 The N-PCNFs realized a moderate capacitance (197 F g−1 at 1 A g−1) and retained 91.7% of initial capacity over 5000 cycles in the two-electrode system.
Furthermore, alginate also is the self-template and self-activator for pore engineering. Sun's group prepared 3D interlinked porous carbon (IPC) using one-step carbonization with potassium alginate as the precursor and self-activator (Fig. 5d).61 The IPC-800 carbonized at 800 °C showed a favorable capacitance (279 F g−1 at 1 A g−1), together with exceptional rate performance and outstanding cycling stability. In another work, Hu et al. prepared microporous-dominated porous carbons (DSPCs) derived from SA using Na+ and KCl for etching the carbon skeleton to increase SSA and modulate the structure (Fig. 5e).62 The corresponding SSCs and aqueous zinc ion capacitors (ZIHCs) assembled with DSPCs gave the energy storage of 10.17 W h kg−1 (150 W kg−1) and 99.22 W h kg−1 (200 W kg−1).
2.1.5 Starch and cyclodextrin. Starch, the product of photosynthesis in plants, is a natural polysaccharide formed by the polymerization of α-D-glucans. Starch has a high yield after carbonization and is a preferable choice to produce oxygen-rich porous carbon materials63 Yuan et al. obtained hierarchical porous carbon microspheres (HPCMSs) exhibiting large SSA (1668 m2 g−1), nano-sphericity (4–20 nm) and high carbon content (95%) using starch as the precursor and K2C2O4 with CaCl2 as the green activators (Fig. 6a).64 The HPCMSs achieved a high capacitance (286 F g−1/17.1 μF cm−2 at 0.5 A g−1). Furthermore, an outstanding retention of 98% was developed over 20
000 cycles.
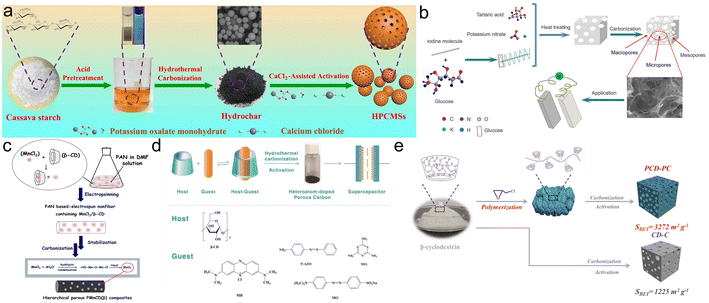 |
| Fig. 6 (a) Illustration for the synthesis of HPCMSs;64 (b) scheme for the preparation of I-PCs-X;66 (c) diagram for the construction of PMnCD(β);67 (d) schematic for the preparation mechanism of porous CMs;68 (e) mechanism diagram for the synthesis of the PCD-PC.69 | |
What's more, the electrochemical properties of starch-based hierarchical porous carbon (HPC) can be optimized after the pretreatment of starch. Zhao et al. obtained HPC with moderate SSA (1863 m2 g−1) using α-starch from gelatinized starch as the precursor, resulting in a higher capacitance of 335.6 F g−1 in comparison with untreated starch.65 Inspired by the phenomenon of starch turning blue when exposed to iodine, Luo's group prepared a porous iodine-doped carbon skeleton (I-PCs-X) by utilizing the reaction of starch with tartaric acid, potassium nitrate (KNO3) and iodine to generate the hierarchical porous structure (Fig. 6b).66 The assembled SSCs with BiBr3 as the electrolyte achieved a superior capacity of 1216 F g−1 at 2 A g−1 with remarkable energy density (65.4 W h kg−1 at 787.3 W kg−1).
Cyclodextrins (CDs), derived from starch hydrolysis, have also been reported as precursors for carbon electrodes. The structure of CDs is a hollow ring, and the three most studied types are α, β and γ, containing 6–8 glucose units respectively. Nowadays, the research on the application of CDs in SCs mainly focuses on its host–guest combination properties.67–69 Jeong et al. combined β-CD with Mn2+ and obtained carbon nanofiber (CNF)/MnO2 composites (PMnCD(β)) by electrostatic spinning and carbonization (Fig. 6c).67 The PMnCD(β) displayed a moderate capacity of 228 F g−1 at 1 mA cm−2 with considerable cyclability, thanks to the fast diffusion channels provided by the mesopores of PMnCD(β) and additional pseudocapacitance from N-doping. Chen's group fabricated N, S co-doped carbon materials (CMs) using hydrothermal carbonization followed by KOH activation owing to the coordination of β-CD with guest molecules (Fig. 6d).68 The CMs delivered a gravimetric capacity of 291.5 F g−1 at 0.5 A g−1 while achieving well mechanical stability of 94% retention over 10
000 cycles. Meanwhile, cyclodextrin polymers have also been reported as precursors. Lin’ group polymerized β-CD and then obtained HPC with ultrahigh SSA of 3710 m2 g−1 (PCD-PC) using the carbonization-activation process (Fig. 6e),69 which achieved excellent capacity (416 F g−1 at 0.5 A g−1).
2.1.6 Agar. Agar, the mixture of agarose and agaropectin derived from red algae, is famous for its room-temperature gelation properties.70 Zhang's group synthesized N-doped porous carbon aerogels (NKAC) possessing high SSA and small mesoporous structure by pyrolysis with urea as a nitrogen dopant and KOH as an activator based on the self-gelling of agar (Fig. 7a).71 The NKAC delivered a high capacitance (366.9 F g−1 at 0.5 A g−1) with a retention rate of 61.7% at 50 A g−1 and favorable cycle stability (96.4% over 10
000 cycles). Liu and coworkers successfully constructed B, N co-doped porous carbon sheets (BN-PCS) derived from agar in the KCl/KHCO3 molten salt system (Fig. 7b).72 Urea was not only the dopant but also the guiding agent for the two-dimensional (2D) sheet structure during carbonization, while the decomposition of KHCO3 and H3BO4 contributed to forming porous structures. The BN-PCS achieved a capacity of 361.1 F g−1 at 0.5 A g−1 in 6 M KOH, and the corresponding SSC reached a favorable energy density of 43.5 W h kg−1 at 375 W kg−1 in 1 M TEABF4 in Acetonitrile.
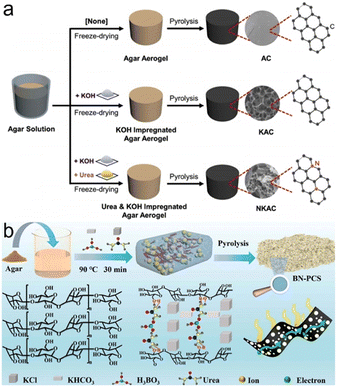 |
| Fig. 7 (a) Diagram for the fabrication of NKAC;71 (b) schematic for the preparation of BN-PCS.72 | |
2.2 Protein
2.2.1 Collagen. Collagen is a type of protein with a helical structure, mainly consisting of glycine, proline and hydroxyproline, which exists in bones, skin and carp scales.73 Collagen serves as a promising precursor for heteroatom doping. Furthermore, collagen aids in the formation of the extracellular matrix, resulting in increased surface area.74 These properties make it show potential as carbon electrodes. The graphene-based porous carbon (CSGC) doped with N and O atoms was synthesized by Lin and colleagues, who used carp scales as the precursor (Fig. 8a).75 The CSGC-700 activated at 700 °C exhibited a hybrid structure of graphene layers and amorphous carbon, coordinated with N, O doping, making the ZIHCs assembled with CSGC-700 realize a superior capacity of 138.8 mA h g−1, as well as durable cyclability and outstanding energy density. Subhani et al. fabricated graphene-integrated porous carbon aerogel (C-G-collagen) using collagen extracted from chicken feet as the precursor.76 Benefiting from the porous structure, moderate SSA (1087 m2 g−1) and interaction of porous carbon and graphene, C-G-collagen demonstrated excellent properties, achieving a remarkable capacitance (365 F g−1 at 1 mV s−1) and retention rate of 97% over 10
000 cycles.
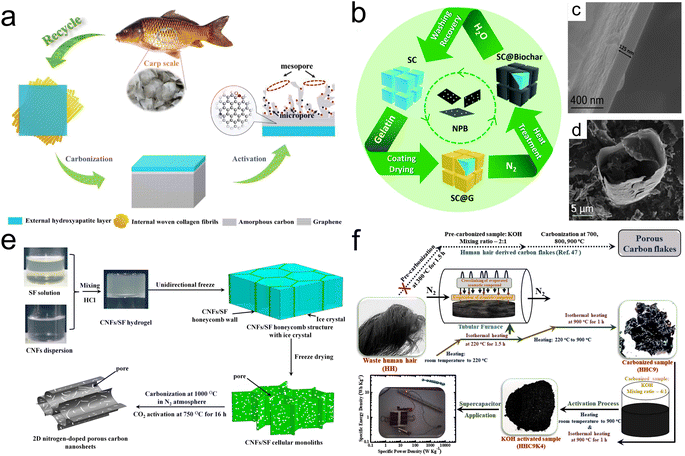 |
| Fig. 8 (a) Scheme for the fabrication of CSGC;75 (b–d) diagram for the synthesis and SEM images for NPB.81 (e) diagrams for the fabrication of NPCN;84 (f) synthetic route for the synthesis of HHC9K4.88 | |
2.2.2 Gelatin. Gelatin is the hydrolysis product of collagen. As a mixture of proteins and peptides, gelatin with a high nitrogen content (−16%) can be converted to nitrogen-doped carbon.77 Gelatin is a kind of hydrophilic colloid with gelation properties forming honeycomb porous carbon.78 Du et al. formed hydrogels by self-assembling the hydrophilic polymer polyacrylamide/gelatin/F127 and prepared 3D layered porous carbon (HPC) by freeze-drying and one-step activation.79 The mesoporous/microporous ratio and SSA of HPC varied with the amount of KOH. The HPC-3.5 based SSCs (the amount of KOH was 3.5 g) delivered the best electrochemical performance in ionic liquids (EMIMBF4) with an extensive voltage of 3.8 V, outstanding capacity of 216.5 F g−1 and superior energy density of 108.6 W h kg−1.Additionally, gelatin can form carbon nanosheets after carbonization with the assistance of the template.80 Zhang's group put forward a scalable approach for fabricating N-doped carbon nanosheets, choosing gelatin as the precursor with NaCl as the pyrogenic agent and 2D structure guide (Fig. 8b–d).81 The optimal sample showed a rich pore structure, highly graphitic and abundant nitrogen content, so beneficial rate performance of 70% retention rate from 0.1 to 20 A g−1 and considerable cycle performance (97.4% over 10
000 cycles) were developed.
2.2.3 Fibroin. Fibroin, extracted from silkworm silk, is mainly composed of glycine and alanine with serine, which are ideal nitrogen-rich doping precursors.82 Sun et al. introduced a simple approach to augment the ionic conductivity of N-doped porous carbon (NPC) obtained from silk via organic liquid treatment.83 With the cooperation of organic liquid, the NPC realized an increased capacity (565.3 F g−1 at 1 A g−1), and assembled SSCs showcased favorable stability (93.3% over 10
000 cycles) while maintaining an impressive energy density (26.2 W h kg−1 at 263.9 W kg−1). Fibroin can transform into different kinds of carbon material with high-temperature treatment thanks to the easy processing. Gao and coworkers developed nitrogen-doped porous carbon nanosheets (NPCN) from CNF/fibroin hydrogel via freeze-drying, carbonization and CO2 activation (Fig. 8e).84 The NPCN-50 (the mass ratio of fibroin to CNF was 50
:
50) showed a high capacity (329.9 F g−1 at 0.25 A g−1) with an excellent retention rate of 99.5% over 5000 cycles owing to 2D nanostructure, abundant pore distribution, high SSA and heteroatom doping.
2.2.4 Keratin. Keratin, consisting of dead cells produced by biological systems, is the main protein that makes up the outer layer of hair, feathers, horns, claws, and human skin.85 Keratin consists of various amino acids such as threonine, cysteine, histidine and methionine, and is rich in C, O, N and S, which is a promising precursor for heteroatom doping.86 Wu and coworkers developed N, O and S co-doped HPC, choosing keratin derived from chicken feathers.87 The optimal sample exhibited a total porosity volume of 1.461 m3 g−1 and elevated SSA of 2864 m2 g−1, thus culminating in a nice capacity (270 F g−1 at 1 A g−1) with favorable stability (98% over 10
000 cycles). Sinha and coworkers used keratin extracted from waste hair as a carbon source and introduced a low-temperature section (220 °C, 1.5 h) into the carbonization to prevent the evaporation of volatile molecules and to facilitate the rearrangement of heteroatoms (Fig. 8f).88 Due to the interlinked porous nanosheet structure and rich heteroatom content, the electrodes of KOH-activated carbon material (HHC9K4) manifested an ultrahigh capacity (999 F g−1 at 1 A g−1), and corresponding SSCs attained a remarkable energy density of 32 W h kg−1 at 324 W kg−1.
3. Strategies for boosting the capacitance of biopolymers-based electrodes
As the most prevalent electrode materials utilized in SCs, carbon materials derived from biopolymers show favorable cycling stability and high power density, but poor capacity limits their further applications.89 Various methods have been proposed to solve this problem, which can be summarized in the following three directions: (a) pore engineering, (b) doping engineering and (c) composite engineering. These strategies will be discussed in this part.
3.1 Pore engineering
It is well known that a reasonable pore size distribution (PSD) is in favor of carbon materials exhibiting promising capacitance and rate properties.90 Due to the dissolution of electrolyte ions, micropores (<2 nm) can increase the SSA, thus improving the capacitance,91 but excessive micropores result in slow ion transport kinetics and high resistance leading to poor rate performance.92 Mesopores (2–50 nm) can offer diffusion pathways for ions, improve electrolyte wetting, promote ion diffusion and ensure well-rate performance and power density.93 Macropores (>50 nm), as the ion buffers, can store electrolytes and shorten the diffusion distance of ions.90,94
Generally, biopolymers require a pyrolysis-activation process to transform into carbon-based electrodes. Carbonization can be carried out in two routes: (a) pyrolysis, which is a high-temperature reaction (500–1000 °C) in an inert atmosphere; (b) hydrothermal carbonization (HTC) is a high-pressure thermal reaction at low temperatures (<250 °C). However, biopolymer carbonization products exhibit a low SSA and underdeveloped pores, requiring further activation.95
3.1.1 Activation. Based on the different reaction mechanisms, the activation method can be categorized into physical, chemical and biological activation. Physical activation, also known as “thermal activation”, is a reaction of high-temperature gases (e.g. CO2, air, steam, etc.) with biopolymers to obtain pore formation.96,97 Physical activation is more beneficial to the environment, but the resulting activated carbon has a low yield, narrow PSD and low SSA, making its specific capacitance difficult to meet realistic conditions.12,98 So it is less studied and usually used in conjunction with chemical activation.Chemical activation utilizes the chemical reaction between the activator and carbonization product or biopolymers to achieve pore formation.99 Depending on the type of activator, chemical activation is distinguished by alkali, acid and salt activation.100 KOH is the most popular alkali activator for obtaining carbon materials with large SSA and relatively uniform PSD, and the reaction mechanism of KOH is shown in eqn (1)–(5). Meng et al. combined chitosan aerogels with KOH to obtain mesoporous-dominated N, O co-doped porous carbon (HPC) using freeze-drying and one-step activation (Fig. 9a).99 The HPC exhibited the maximum SSA of 2787.47 m2 g−1, thus delivering a favorable capacity of 253 F g−1 at 0.5 A g−1.
|
2C + 6KOH → 2K + 2K2CO3 + 3H2
| (1) |
|
2C + K2CO3 → 3CO + 2K
| (2) |
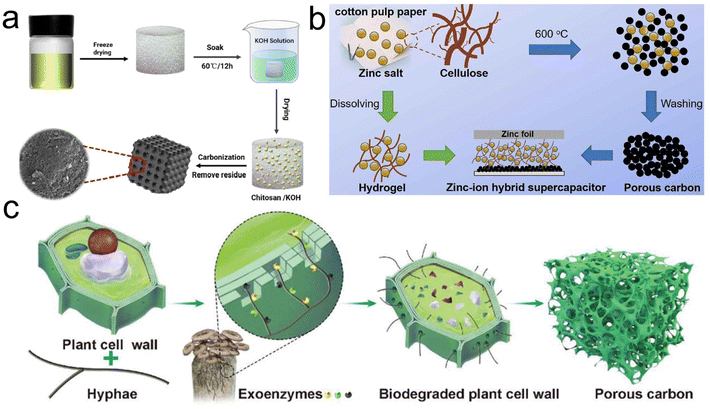 |
| Fig. 9 (a) Fabrication schematic for the HPC-X;99 (b) scheme of design for the ZIHS by using CDC as the cathode and cellulose hydrogel containing ZnCl2 as the electrolyte;104 (c) schematic diagram of fungi-enabled degradation of the plant cell wall to obtain porous carbon with ultrahigh SSA.113 | |
As a typical acid activator, phosphoric acid (H3PO4) activation consists of five steps: hydrolyzation, dehydration, aromatization, cross-linking and pore creation.101 Cao et al. used H3PO4 to dehydrate lignin and alleviate the hydrogen bonding between lignin molecules to obtain phosphorylated lignin, which subsequently reacted with cellulose acetate (CA) hydroxyl groups to form phospholipid bonds, reducing the phase separation of CA from lignin and enhancing the thermal stability of the precursor fiber.102 After a simple pre-oxidation, the obtained carbon fibers (CFs) developed a remarkable capacitance of 346.6 F g−1.
Zinc chloride (ZnCl2) is a commonly used salt activator offering both dehydration and deoxygenation during the activation process.103 Yang et al. utilized cellulose-rich cotton pulp paper as the precursor and prepared cellulose-derived carbon (CDC) possessing enriched meso- and micro-pores by a one-step ZnCl2 activation (Fig. 9b).104 The solid-state ZIHCs with CDC as the cathode yielded an excellent capacity of 247 mA h g−1 and energy density of 243 W h kg−1 while upholding a decent retention rate of 85% over 20
000 cycles. Zhai's group used chitin as the precursor and ZnCl2 as the dehydrator and activator to deliver N-doped carbon aerogels (NSCA) with a maximum SSA of 2540 m2 g−1.105 The NSCA-1000 carbonized at 1000 °C exhibited a favorable capacity of 249.4 F g−1 at 1 A g−1. Furthermore, even after undergoing 15
000 cycles, a retention rate of 98.44% was obtained.
Considering the environmental hazards of conventional activators and the cumbersome synthesis process of activated carbon, alternative salt activators have been tried with success. Depending on the activation mechanism, they are classified into three categories: molten salts (NaCl, KCl, LiCl, etc.), decomposition salts (KHCO3, NaNO3, Zn(Ac)2, etc.), and oxidation salts (HNO3, KMnO4, K2FeO4, etc.).106–108 Being a green activator, the molten salt can be easily removed after the carbonization without the need for acid washing. Wang and colleagues developed a lignin-based nitrogen-doped hierarchically porous carbon (LDMCN-700-2) by one-step activation using KCl as the activator and hard template, exhibiting a moderate SSA (1012.5 m2 g−1) with notable nitrogen content (4.5 at%). So favorable properties, such as high capacitance (245 F g−1 at 0.5 A g−1) and favorable mechanical stability (95.7% upon undergoing 5000 cycles) were achieved.109 The gas generated by the reaction of decomposing salts can etch the carbon matrix to form pores. Deng et al. were inspired by bread fermentation and proposed a strategy of KHCO3-assisted pyrolysis to obtain micro- and mesopores, while the CO2 produced by KHCO3 decomposition expanded and produced macropores, resulting in an HPC with high SSA (1893 m2 g−1). Consequently, it exhibited remarkable capacity (253 F g−1), along with low resistance and durable stability.110 In addition, oxidation salts can act as both activators and templates. Wang et al. chose chitin as the precursor and KMnO4 as the activator for generating micropores and small mesopores, while the generated K2MnO4 and MnO2 could be acted as templates to generate meso- and macropores.111 The obtained carbon material of HPC-700 could reach a substantial pore volume (1.286 cm3 g−1) with high SSA (1488.3 m2 g−1), demonstrating a significant capacity (412.5 F g−1 at 0.5 A g−1).
Biological activation is the use of microorganisms to degrade biopolymers, thereby achieving pore creation.112–114 Wang et al. first introduced the strategy for preparing porous carbon via fungal degradation of lignin (Fig. 9c).113 The structure of cotton seed hulls was embrittled by exoenzymes after inoculation with Pleurotus ostreatus. A 3D loose precursor of the honeycomb-like structure was formed, which could facilitate matrix carbonization and KOH activation to form abundant pores. The assembled lithium-ion capacitors demonstrated an ultrahigh energy density of 263.9 W h kg−1 at 0.7 kW kg−1. Samely, Wang's group exploited cellulase to degrade cellulose in wood, followed by high-temperature carbonization to obtain self-supported thick carbon electrodes possessing high SSA and hierarchically arranged porous structures, thus realizing the gravimetric capacitance of 384 F g−1 and volume capacitance of 8.41 F cm−2 at 1 mA cm−2.114
3.1.2 Template. The template method primarily employs three kinds of templates: hard templates, soft templates and self-templates. As for the synthesis of HPC with hard templates, biopolymers need to combine with the hard template, and then porous carbon is obtained after a high-temperature reaction and template removal.115 In addition to the molten salts, commonly employed hard templates include silica-based templates (e.g., mesoporous SiO2, tetraethyl silicate, etc.), metal oxides (e.g., ZnO, MgO, CaO, etc.) and ice templates.116–120 Cao et al. synthesized HPC with high SSA and controlled porosity using exothermic pyrolysis of starch with magnesium nitrate and subsequent heat treatment and acid washing (Fig. 10a).119 The optimized sample showed a hierarchical porous network with an SSA of 2200 m2 g−1 that offered accessible pathways for electrolyte transport, demonstrating the well electrochemical properties with moderate specific capacity (229 F g−1 at 1 A g−1), outstanding rate capability (92.13% retention to 10 A g−1) and decent cyclability (94% over 10
000 cycles). Liu's group obtained silicate/chitosan microspheres (PBE) by spray drying using SiO2 as the mesoporous template.121 The regular honeycomb-like HPC was obtained by one-pot carbonization using polytetrafluoroethylene as an etching agent and macroporous guide. The SSCs assembled with PBE exhibited a beneficial capacitance (250.5 F g−1 at 0.5 A g−1) and an excellent retention rate of up to 107% over 5000 cycles.
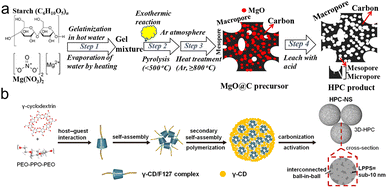 |
| Fig. 10 (a) Diagram for the fabrication of HPC;119 (b) scheme for the formation mechanism of HPC-NS.126 | |
Organic molecules or block copolymers with functional groups often act as soft templates.122–125 In a suitable solvent, the soft templates self-assemble into micelles to bond with the biopolymer through interactions to form a coating of encapsulated carbon precursors. Finally, the micelles decompose to obtain porous carbon during carbonization. Yao and coworkers developed hierarchically porous carbon nanospheres (HPC-NS) with interlinked ball-in-ball structures using pyrolysis of γ-CD/F127 (Fig. 10b).126 The connectivity of the pores facilitated ion transport, enabling excellent electrochemical properties, allowing for 405 F g−1 specific capacity at 1 A g−1 with a retention of 71% to 200 A g−1. Moreover, an impressive energy density of 24.3 W h kg−1 was achieved at 151 W kg−1. Ionic liquid (IL) as soft templates have also been reported. Using chitosan as the precursor and IL (2-butyl-1-methylimidazolium chloride) as the soft template, Wu et al. synthesized 2D layered graphitized carbon (NCSIL-900) with micro- and mesoporous structures by a one-pot hydrothermal, thus achieving the capacity of 355 F g−1 in 1 M H2SO4 and 275 F g−1 in 6 M KOH.127
Anionic polymers (e.g., lignosulfonates, alginates, etc.) can act as self-templates by generating metal compounds through pyrolysis without the introduction of additional templates, resulting in pores.128–130 Pang et al. chose SLS as the carbon source to fabricate SLS-derived HPC by carbonization without adding an extra template.131 The porous carbon (HPCSLS-700-1) showed the maximum SSA of 903 m2 g−1 and notable heteroatom contents (O 8.11 at%, N 1.76 at%). The SSCs assembled with HPCSLS-700-1 in 7 M KOH demonstrated a decent capacity of 247 F g−1 with a remarkable retention of 92% over 20
000 cycles.
3.2 Doping engineering
As another strategy for improving the capacity for carbon electrodes, heteroatom doping can be classified into two kinds: in situ and ex situ doping, where the former involves the calcination of precursors containing heteroatoms and the latter involves the introduction of heteroatoms through dopants.132,133 Moreover, depending on the kinds of dopant atoms, heteroatom doping can be classified as single and multiple heteroatom co-doping.134 Introducing heteroatoms not only augments the conductivity of carbon-based electrodes but also enhances the wettability in the electrolyte. More importantly, heteroatom doping provides pseudocapacitance and promotes hybrid capacitance.135
3.2.1 Single heteroatom doping. Nitrogen atoms are one of the most common dopant atoms, which easily bind to the carbon framework because their radius is comparable to the carbon atom.136 Nitrogen-doped carbon structures contain four types of functional groups: pyridine nitrogen (N-6), pyrroline nitrogen (N-5), quaternary nitrogen (N-Q) and oxidized nitrogen (N–O), where N-5 and N-6 offer active sites for Faraday reactions, while N-Q and N–O lead to electron transport.137,138 Wang and colleagues fabricated N-doped porous carbon (NPC) possessing moderate SSA (366.5 m2 g−1) with rich nitrogen content (7.4 at%), who used CNCs as the precursor with urea as the dopant (Fig. 11a).139 So the NPC achieved ultrahigh capacitance (570.6 F g−1 at 1 A g−1). Sun's group delivered N-doped carbon aerogels from SA/melamine composites (SAM) in Fig. 11b.140 Benefiting from its high heteroatom content, large SSA and unique directional channel structure, the SAM-700-4, synthesized at an optimal carbonization temperature of 700 °C and with a KOH/SAM ratio of 4, demonstrated an excellent capacity (441.80 F g−1 at 0.5 A g−1).
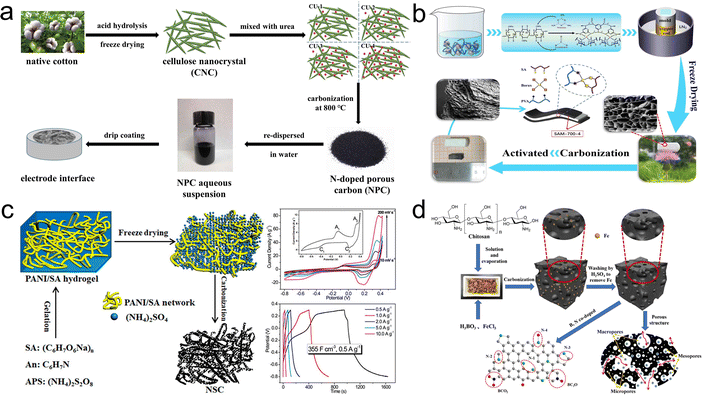 |
| Fig. 11 (a) Scheme for preparation of the NPC based on CNC and urea;139 (b) schematic for the synthesis of SAM-700-4;140 (c) illustration for fabrication procedure of NSC;145 (d) schematic diagram of the synthesis of BNPC-Fe.147 | |
Doping of phosphorus and sulfur atoms with larger radii and higher electrochemical activities introduces greater structural distortions and defects to the carbon skeleton compared with nitrogen doping.141,142 Boron and nitrogen atoms have a comparable radius to carbon atoms, making boron atoms easier to incorporate into carbon compounds. Boron doping increases the concentration of carrier holes, resulting in p-type doping and increased electrical conductivity.143 However, single phosphorus, sulfur, and boron atom doping are seldom reported, which is attributed to the low doping content making it difficult to effectively enhance the electrochemical properties, and hence co-doping tends to be done in collaboration with the nitrogen atom. Furthermore, it is a controversial topic whether oxygen is the doping atom or not. The functional groups containing oxygen, such as carboxy, carbonyl and hydroxy, can participate in Faraday reactions and improve the capacitance of aqueous SCs.134 However, it is undeniable that the majority of carbon electrodes contain oxygen and the content is not low, so it will not be discussed here.
3.2.2 Multiple heteroatom doping. Recently, more studies have proved that the synergistic effect of heteroatom co-doping contributes to boosting the performance of SCs. The surface condition and electronic property of carbon materials are more active thanks to introducing more heteroatoms, which facilitates exposure to more active sites for charge storage.144 Considering a large amount of co-doping types, this part will focus on the more frequently used “N + X” doping (X = B, P, S, etc.).As for N, S co-doping, introducing nitrogen and sulfur atoms enhances the hybrid capacitance while increasing the conductivity and carbon layer spacing.137 Huang's group fabricated micropore-dominated N, S co-doped carbon (NSC) based on the interaction between PANI and SA followed by one-step carbonization (Fig. 11c).145 The authors used ammonium sulfate, which was the by-product of aniline polymerization, as the nitrogen, sulfur activator to introduce N, S doping while optimizing the carbon structure. Thanks to the N, S co-doping with hierarchical porous structure, the NSC exhibited pseudocapacitive properties with high bulk capacity (355 F cm−3 at 0.5 A g−1), and the assembled SSC achieved excellent energy density (15.9 W h L−1 at 426 W L−1). Particularly, N, P co-doping helps to extend the voltage window in aqueous electrolytes while generating pseudocapacitance. Fan's group developed the porous carbon doped with N, P atoms (APC) from hydrogels formed by the interaction of chitosan with phytic acid.146 The optimized APC-2 showed a hierarchically porous framework, high SSA and an abundance of heteroatom. Thus, the voltages of corresponding SSCs were up to 1.3 V (6 M KOH) and 1.7 V (1 M Na2SO4). Nitrogen and boron atoms are electron-rich and electron-deficient, respectively. The B, N co-doping can produce special electronic structures to improve the electrochemical performance. Qiu's group used chitosan as a precursor, boric acid as a template and boron source and ferric chloride as a multifunctional reagent (solvent, template and activator) to prepare B, N co-doped porous carbon (BNPC-Fe) in Fig. 11d.147 The BNPC-Fe delivered an increased capacitance (348 F g−1 at 1 A g−1) compared to NPC-Fe without boric acid added.
3.3 Composite engineering
In addition to pore and doping engineering, combining biopolymers-based carbon materials with other carbon materials, transition metal compounds and conductive polymers utilizes the synergistic interplay of these constituents to form composites with multi-component, hierarchical structures and abundant active sites to achieve optimum electrochemical performance.
3.3.1 Carbon/carbon composite. Biopolymers-based porous carbon typically has an amorphous structure, resulting in poor conductivity and restricting rate performance. Carbon nanomaterials (e.g. graphene, carbon nanotubes and Mxene) generally deliver excellent conductivity and relatively high capacity, but the stacking of carbon nanomaterials limits ion dynamics and active site exposure.148 Combining porous carbon with carbon nanomaterials can help to solve the above problems and thus enhance the performance of the composite. Ma's group constructed the nitrogen, sulfur co-doped porous carbon foam reinforced by graphene (N, S-GHPCF) using sol–gel and one-step carbonization.149 The samples showed an amplified SSA (2279.2 m2 g−1), well conductivity (438 S m−1) and rich heteroatom content, realizing ultrahigh capacitance (405 F g−1 at 1 A g−1), along with impressive rate capability (72.8% retention to 100 A g−1) and cycle stability (98.8% over 10
000 cycles). To solve the problem with the stacking of MXene, Zhang and coworkers introduced a strategy of carbon dots intercalation to prepare flexible MXene thin film electrodes of high ion-accessible surface and large density via gelatin of calcium alginate with MXene and carbonization (Fig. 12a and b).150 The electrodes demonstrated superior capacitance (372.6 F g−1 and 1244.6 F cm−3 at 1 A g−1) coupled with outstanding rate performance (198.3 F g−1 and 662.5 F cm−3 to 1000 A g−1) and cycle stability (93.5% retention over 30
000 times).
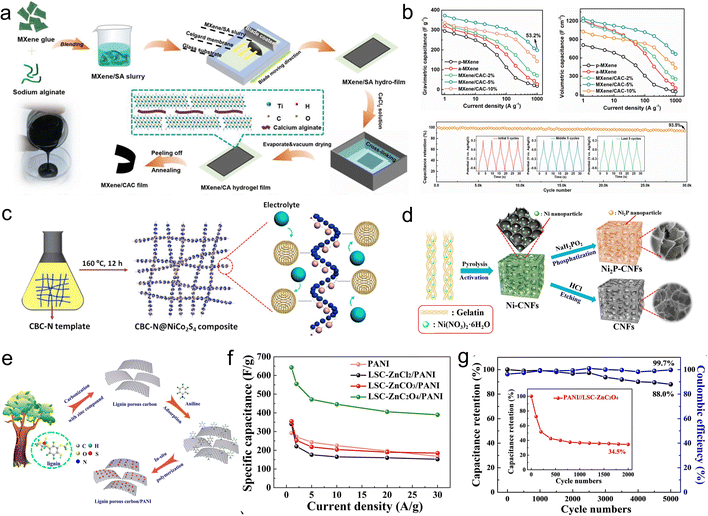 |
| Fig. 12 (a) Scheme for the synthesis of MXene/CAC films; (b) capacity and cycling stability test of MXene/CAC;150 (c) scheme for the space-confined growth of CBC-N@NiCo2S4 composite;155 (d) diagrams for the preparation of Ni-CNFs, Ni2P-CNFs and CNFs;156 (e) schematic for the fabrication of lignin porous carbon/PANI composites; (f) specific capacitance of the samples; (g) cycling test of LSC-ZnC2O4/PANI//LSC-ZnC2O4 ASCs.161 | |
3.3.2 Carbon/transition metal compounds. As promising pseudocapacitive materials, transition metal compounds (TMCs) can provide high capacitance and store much energy through reversible faradaic reactions.151 However, the volume variation induced by the phase change during the reaction leads to undesirable reaction kinetics and cycling stability.152 The integration of TMCs with biopolymers-derived porous carbon composites serves to optimize the conductivity of TMCs, alleviate volume fluctuations and prevent aggregation. Furthermore, it enhances the capacitance of carbon-based electrodes, thereby yielding increased energy density.153 Zhao's group fabricated chitosan-based hierarchical porous carbon aerogel (HPCA) via carbonization and activation followed by anchoring NiCo-LDH nanosheets upon the HPCA using hydrothermal reaction.154 Thanks to the interaction of HPCA and NiCo-LDHs, the optimized sample exhibited a superior specific capacity (1504 F g−1 at 1 A g−1), still retaining the value of 1219.7 F g−1 at 10 A g−1. After 5000 cycles, a capacity retention of 86% was identified. Ning and coworkers anchored NiCo2S4 nanoparticles on the N-doped carbon nanofibers (CBC-N) through the hydrothermal method (Fig. 12c).155 The CBC-N@NiCo2S4 composites exhibited a 3D conductive network, realizing an ultrahigh capacity (1078 F g−1 at 1 A g−1) and excellent stability (94.6% over 5000 cycling times) than NiCo2S4. Peng et al. achieved Ni2P nanoparticles dispersing in carbon nanosheet framework (Ni2P-CNFs) through Ni(NO3)2-assisted gelatin carbonization with a low-temperature phosphating process (Fig. 12d).156 The CNFs provided conductive accesses and inhibited the aggregation of Ni2P nanoparticles, so Ni2P-CNFs showed a decent capacity (145 mA h g−1 at 0.5 A g−1), and assembled Ni2P-CNFs//CNFs ASCs gave the voltage window up to 1.65 V and maximum energy density of 42 W h kg−1 at 413 W kg−1. Additionally, a remarkable capacity retention of 88% upon undergoing 6000 cycling times was realized.
3.3.3 Carbon/conductive polymers. As another kind of PCs' material, conductive polymers (CPs) conduct electricity through conjugated π bonds in polymer chains.22 The CPs are difficult to achieve excellent electrochemical performance owing to the limitations of self-aggregation, high transport resistance and volume change.157 So it is necessary to combine CPs with biopolymers-based porous carbon to improve the spatial structure and conductivity of CPs.158 Zhuo et al. loaded PPy uniformly on the cellulose-derived carbon aerogel (Cell@PPy), which achieved an increased capacitance (387.6 F g−1 at 0.5 A g−1).159 Meanwhile, the cell's porous structure effectively promotes the cycling stability of PPy, so the retention of 92.6% over 10
000 cycles was obtained. Liu's group constructed the network of carbon nanofiber/carbon nanosheet (CNF/CNS) through the pyrolysis process of BCs and exploited it as the substrate to modify the nanorod array of PANI.160 The PANI@CNF/CNS exhibited good hydrophilicity and rapid ion diffusion. Based on these advantages, the ASCs which utilized PANI@CNF/CNS as the positive electrodes and CNF/CNS as the negative electrodes delivered a remarkable energy density (65.3 W h kg−1 at 800 W kg−1) with outstanding stability (98% upon undergoing 5000 cycles). Fu and coworkers used SLS as the precursor and selected different activators (ZnCl2, ZnCO3 and ZnC2O4) to obtain porous carbons with various structures, and continued to prepare PANI/porous carbon composites by in situ polymerization (Fig. 12e).161 The results showed that the lamellar porous carbon offered a bigger contact area to penetrate and diffuse the aniline molecules, achieving an excellent capacity (643 F g−1 at 1 A g−1). The capacity retention of ASCs was as high as 88% after 5000 cycles (Fig. 12f and g).
4. Conclusion and perspective
As an alternative to synthetic polymers, biopolymers have great advantages, such as green environmental protection, abundant reserves and low budget, which contribute to the popularization of SCs as green energy storage devices and achieve sustainable development.25 This paper has reviewed the recent advances in biopolymers-based carbon electrodes for SCs and summarized the directions to promote the capacitance of carbon electrodes. Although great progress has been made, there are still many challenges that need to be resolved.
4.1 Raw material optimization
The diversity of types and structures of biopolymers makes them less effectively utilized. Moreover, the separation and purification of biopolymer components is also extremely challenging to achieve.
4.2 Tailored optimization of pore and composition
Although several strategies for optimizing the pore structure have been reported, most of the processes are indeterminate and do not allow for tailored pore size distribution. At the same time, activator etching will reduce the heteroatom content, which makes it hard to optimize capacitance. Therefore, optimizing the structure and heteroatom content of carbon-based electrodes will be the major investigation direction for future research.
4.3 Scaleup and green production
Biopolymers-based carbon electrodes with excellent performance reported in the literature are limited to the laboratory level, and the complicated synthesis methods are difficult to achieve popularization, so it is imperative to introduce facile and scalable strategies for production.24 In addition, the gases from high-temperature reactions may be harmful to the environment and require further treatment to achieve green production.
4.4 Energy density enhancement
The development of SCs is limited by inadequate energy density, which can be optimized through an increased capacitance and wider voltage window.162 Combining biopolymers-based carbon materials with pseudocapacitive materials is effective in boosting capacitance, but pseudocapacitive materials tend to fall off during repetitive charging and discharging cycles.163 The utilization of non-aqueous electrolytes contributes to a wider voltage window, but the electrolyte ions need to be compatible with the pore structure to reach their full potential. Hence, exploring the correlation between the structure and electrochemical characteristics of biopolymers-based carbon electrodes holds immense potential as a burgeoning area of research interest in the realm of supercapacitors (SCs).
4.5 Application expansion
Flexible and wearable electronics provide opportunities for supercapacitor development. Biopolymers can be applied as electrodes for flexible and stretchable SCs.164 However, achieving electrochemical performance comparable to conventional SCs is an urgent issue.
Conflicts of interest
There are no conflicts to declare.
Acknowledgements
The authors gratefully acknowledge the financial support from the National Key Research Development Program of China (2021YFB3800300), and the Open Project of State Key Laboratory of Metal Matrix Composites (2021SKLMMC-8).
References
- R. P. Rastogi, A. Pandey, C. Larroche and D. Madamwar, Renewable Sustainable Energy Rev., 2018, 82, 2946–2969 CrossRef CAS
. - Z. Liu, D. B. Guan, S. Moore, H. Lee, J. Su and Q. Zhang, Nature, 2015, 522, 279–281 CrossRef CAS PubMed
. - F. Biermann, T. Hickmann, C. A. Senit, M. Beisheim, S. Bernstein, P. Chasek, L. Grob, R. E. Kim, L. J. Kotze, M. Nilsson, A. O. Llanos, C. Okereke, P. Pradhan, R. Raven, Y. X. Sun, M. J. Vijge, D. van Vuuren and B. Wicke, Nat. Sustain., 2022, 5, 795–800 CrossRef
. - H. Jin, J. Li, Y. Yuan, J. Wang, J. Lu and S. Wang, Adv. Energy Mater., 2018, 8, 1801007 CrossRef
. - Y. L. Shao, M. F. El-Kady, J. Y. Sun, Y. G. Li, Q. H. Zhang, M. F. Zhu, H. Z. Wang, B. Dunn and R. B. Kaner, Chem. Rev., 2018, 118, 9233–9280 CrossRef CAS PubMed
. - E. S. Appiah, P. Dzikunu, N. Mahadeen, D. N. Ampong, K. Mensah-Darkwa, A. Kumar, R. K. Gupta and M. Adom-Asamoah, Molecules, 2022, 27, 6556 CrossRef CAS PubMed
. - F. X. Wang, X. W. Wu, X. H. Yuan, Z. C. Liu, Y. Zhang, L. J. Fu, Y. S. Zhu, Q. M. Zhou, Y. P. Wu and W. Huang, Chem. Soc. Rev., 2017, 46, 6816–6854 RSC
. - K. F. Chen and D. F. Xue, J. Mater. Chem. A, 2016, 4, 7522–7537 RSC
. - V. Aravindan, J. Gnanaraj, Y. S. Lee and S. Madhavi, Chem. Rev., 2014, 114, 11619–11635 CrossRef CAS PubMed
. - K. L. Van Aken, M. Beidaghi and Y. Gogotsi, Angew. Chem. Int. Ed., 2015, 54, 4806–4809 CrossRef CAS PubMed
. - Z. N. Yu, L. Tetard, L. Zhai and J. Thomas, Energy Environ. Sci., 2015, 8, 702–730 RSC
. - H. Lu and X. S. Zhao, Sustain. Energy Fuels, 2017, 1, 1265–1281 RSC
. - R. Vinodh, Y. Sasikumar, H. J. Kim, R. Atchudan and M. Yi, J. Ind. Eng. Chem., 2021, 104, 155–171 CrossRef CAS
. - S. W. Bokhari, A. H. Siddique, H. Pan, Y. Li, M. Imtiaz, Z. Chen, S. M. Zhu and D. Zhang, RSC Adv., 2017, 7, 18926–18936 RSC
. - M. Shaker, A. A. S. Ghazvini, W. Cao, R. Riahifar and Q. Ge, New Carbon Mater., 2021, 36, 546–572 CrossRef CAS
. - C. Choi, D. S. Ashby, D. M. Butts, R. H. DeBlock, Q. L. Wei, J. Lau and B. Dunn, Nat. Rev. Mater., 2020, 5, 5–19 CrossRef
. - M. Zenasni, H. Belhadj, M. Kiari, M. Alelyani, A. B. Alhailiy, A. Benyoucef and Y. Bakkour, Front. Energy Res., 2023, 11, 1244699 CrossRef
. - Y. Yan, T. Y. Wang, X. R. Li, H. Pang and H. G. Xue, Inorg. Chem. Front., 2017, 4, 33–51 RSC
. - D. Majumdar, T. Maiyalagan and Z. Q. Jiang, Chemelectrochem, 2019, 6, 4343–4372 CrossRef CAS
. - S. S. Patil and P. S. Patil, Nanoscale, 2022, 14, 16731–16748 RSC
. - G. F. Xue, T. Bai, W. G. Wang, S. J. Wang and M. D. Ye, J. Mater. Chem. A, 2022, 10, 8087–8106 RSC
. - G. A. Snook, P. Kao and A. S. Best, J. Power Sources, 2011, 196, 1–12 CrossRef CAS
. - R. Y. N, K. Sharma and P. M. Shafi, J. Energy Storage, 2022, 55, 105727 CrossRef
. - S. Ahmed, P. Sharma, S. Bairagi, N. P. Rumjit, S. Garg, A. Ali, C. W. Lai, S. M. Mousavi, S. A. Hashemi and C. M. Hussain, J. Energy Storage, 2023, 66, 107391 CrossRef
. - Y. X. Wang, T. Xu, K. Liu, M. Zhang, X. M. Cai and C. L. Si, Aggregate, 2023, e248 Search PubMed
. - N. Boutaleb, F. Z. Dahou, H. Djelad, L. Sabantina, I. Moulefera and A. Benyoucef, Polymers, 2022, 14, 4562 CrossRef CAS PubMed
. - G. Gopinath, S. Ayyasamy, P. Shanmugaraj, R. Swaminathan, K. Subbiah and S. Kandasamy, J. Energy Storage, 2023, 70, 108065 CrossRef
. - Z. H. Bi, Q. Q. Kong, Y. F. Cao, G. H. Sun, F. Y. Su, X. X. Wei, X. M. Li, A. Ahmad, L. J. Xie and C. M. Chen, J. Mater. Chem. A, 2019, 7, 16028–16045 RSC
. - Y. Zheng, K. Chen, K. Jiang, F. Zhang, G. Zhu and H. Xu, J. Energy Storage, 2022, 56, 105995 CrossRef
. - M. Darder, P. Aranda and E. Ruiz-Hitzky, Adv. Mater., 2007, 19, 1309–1319 CrossRef CAS
. - W. S. Chen, H. P. Yu, S. Y. Lee, T. Wei, J. Li and Z. J. Fan, Chem. Soc. Rev., 2018, 47, 2837–2872 RSC
. - S. H. Yang, Y. W. Cui, G. X. Yang, S. F. Zhao, J. Q. Wang, D. G. Zhao, C. Yang, X. T. Wang and B. Q. Cao, J. Power Sources, 2023, 554, 232347 CrossRef CAS
. - X. Zhang, H. Li, B. Qin, Q. Wang, X. Xing, D. Yang, L. e. Jin and Q. Cao, J. Mater. Chem. A, 2019, 7, 3298–3306 RSC
. - A. K. Rana, E. Frollini and V. K. Thakur, Int. J. Biol. Macromol., 2021, 182, 1554–1581 CrossRef CAS PubMed
. - C. F. Ding, T. Y. Liu, X. D. Yan, L. B. Huang, S. O. Ryu, J. L. Lan, Y. H. Yu, W. H. Zhong and X. P. Yang, Nano-Micro Lett., 2020, 12, 63 CrossRef CAS PubMed
. - L. M. Chen, H. Y. Yu, Z. H. Li, X. Chen and W. L. Zhou, Nanoscale, 2021, 13, 17837–17845 RSC
. - M. Yu, J. Li and L. J. Wang, Chem. Eng. J., 2017, 310, 300–306 CrossRef CAS
. - B. Duan, Y. Huang, A. Lu and L. N. Zhang, Prog. Polym. Sci., 2018, 82, 1–33 CrossRef CAS
. - M. A. Meyers, J. McKittrick and P. Y. Chen, Science, 2013, 339, 773–779 CrossRef CAS PubMed
. - L. Gao, G. Zhang, J. Cai, L. Huang, J. Zhou and L. Zhang, Nano Res., 2020, 13, 1604–1613 CrossRef CAS
. - M. Rinaudo, Prog. Polym. Sci., 2006, 31, 603–632 CrossRef CAS
. - M. Nasrollahzadeh, M. Sajjadi, S. Iravani and R. S. Varma, Carbohydr. Polym., 2021, 251, 116986 CrossRef CAS PubMed
. - J. Y. Huang, Y. R. Liang, H. Hu, S. M. Liu, Y. J. Cai, H. W. Dong, M. T. Zheng, Y. Xiao and Y. L. Liu, J. Mater. Chem. A, 2017, 5, 24775–24781 RSC
. - Y. Xi, Z. Xiao, H. Lv, H. Sun, S. Zhai and Q. An, J. Colloid Interface Sci., 2023, 630, 525–534 CrossRef CAS PubMed
. - T. Lyu, S. Lin, L. Mo, F. Wang and Z. Shao, Int. J. Energy Res., 2022, 46, 17056–17067 CrossRef
. - Y. Sun, D. Xu and S. Wang, Carbon, 2022, 199, 258–267 CrossRef CAS
. - M. Y. Yuan, Y. Q. Zhang, B. Niu, F. Jiang, X. N. Yang and M. Li, J. Mater. Sci., 2019, 54, 14456–14468 CrossRef CAS
. - M. Yuan, Y. Zhang, B. Niu, F. Jiang, X. Yang and M. Li, J. Mater. Sci., 2019, 54, 14456–14468 CrossRef CAS
. - Y. Tong, J. Y. Yang, J. J. Li, Z. Y. Cong, L. Wei, M. M. Liu, S. R. Zhai, K. Wang and Q. D. An, J. Mater. Chem. A, 2023, 11, 1061–1082 RSC
. - Q. N. Sun, R. Khunsupat, K. Akato, J. M. Tao, N. Labbe, N. C. Gallego, J. J. Bozell, T. G. Rials, G. A. Tuskan, T. J. Tschaplinski, A. K. Naskar, Y. Q. Pu and A. J. Ragauskas, Green Chem., 2016, 18, 5015–5024 RSC
. - C. Jiang, Z. H. Wang, J. X. Li, Z. J. Sun, Y. F. Zhang, L. Li, K. S. Moon and C. P. Wong, Electrochim. Acta, 2020, 353 Search PubMed
. - N. N. Guo, M. Li, X. K. Sun, F. Wang and R. Yang, Green Chem., 2017, 19, 2595–2602 RSC
. - H. Wang, F. Xiong, F. Guo, Y. Han, F. Chen, B. Ma, J. Yang, M. Wen, Y. Qing, F. Chu and Y. Wu, Colloids Surf., A, 2022, 655, 130237 CrossRef CAS
. - Y. Y. Long, X. Y. An, H. Zhang, J. Yang, L. Q. Liu, Z. J. Tian, G. H. Yang, Z. B. Cheng, H. B. Cao, H. B. Liu and Y. H. Ni, Chem. Eng. J., 2023, 451, 138877 CrossRef CAS
. - X. Han, Q. Wei, Y. Su, G. Che, J. Zhou and Y. Li, ACS Appl. Mater. Interfaces, 2023, 15, 1969–1983 CrossRef CAS PubMed
. - F. Torres-Canas, A. Bentaleb, M. Follmer, J. Roman, W. Neri, I. Ly, A. Derre and P. Poulin, Carbon, 2020, 163, 120–127 CrossRef CAS
. - C. Jiang, Z. H. Wang, J. X. Li, Z. J. Sun, Y. F. Zhang, L. Li, K. S. Moon and C. P. Wong, Electrochim. Acta, 2020, 353, 136482 CrossRef CAS
. - M. Hassan, M. A. Gondal, E. Cevik and A. Bozkurt, ACS Appl. Energy Mater., 2022, 5, 6833–6846 CrossRef CAS
. - H. W. Guo, A. T. Zhang, H. C. Fu, H. W. Zong, F. H. Jin, K. Zhao and J. Q. Liu, Chem. Eng. J., 2023, 453, 139633 CrossRef CAS
. - D. Li, C. Lv, L. Liu, Y. Xia, X. She, S. Guo and D. Yang, ACS Cent. Sci., 2015, 1, 261–269 CrossRef CAS PubMed
. - S. Sun, B. Ding, R. Liu and X. Wu, J. Alloys Compd., 2019, 803, 401–406 CrossRef CAS
. - Y. P. Lu, L. T. Liu, R. Zhang, Z. J. Jiang, Y. M. Li, Z. Y. Sun, X. H. Chen and H. H. Song, Appl. Surf. Sci., 2022, 604, 154631 CrossRef CAS
. - M. Nasrollahzadeh, M. Sajjadi, S. Iravani and R. S. Varma, Carbohydr. Polym., 2021, 251 Search PubMed
. - G. Yuan, K. X. Guan, H. Hu, B. F. Lei, Y. Xiao, H. W. Dong, Y. R. Liang, Y. L. Liu and M. T. Zheng, J. Colloid Interface Sci., 2021, 582, 159–166 CrossRef CAS PubMed
. - C. H. Zhao, Y. X. Wang, J. X. Zheng, S. J. Xu, P. F. Rui and C. Zhao, J. Power Sources, 2022, 521, 230942 CrossRef CAS
. - X. D. Luo, Y. Wang, Z. F. Shen, L. F. Cui, Y. G. Wang and X. Li, J. Colloid Interface Sci., 2021, 599, 351–359 CrossRef CAS PubMed
. - J. H. Jeong, Y. A. Kim and B. H. Kim, Carbon, 2020, 164, 296–304 CrossRef CAS
. - J. Chen, Y. Huo, S. Li, Y. Huang and S. Lv, Compos. Commun., 2019, 16, 117–123 CrossRef
. - H. Lin, Z. Tan, J. Yang, R. Mo, Y. Liang, M. Zheng, H. Hu, H. Dong, X. Liu, Y. Liu and Y. Xiao, J. Energy Storage, 2022, 53, 105036 CrossRef
. - X. T. Fu and S. M. Kim, Mar. Drugs, 2010, 8, 200–218 CrossRef CAS PubMed
. - F. Zhang, T. Y. Liu, J. H. Zhang, E. T. Cui, L. Yue, R. Y. Jiang and G. H. Hou, Carbon, 2019, 147, 451–459 CrossRef CAS
. - H. Liu, S. Zhu, Y. Zhang, H. Song, Y. Zhang, Y. Chang, W. Hou and G. Han, Small, 2023, 2204119 CrossRef CAS PubMed
. - J. Niu, R. Shao, M. Liu, Y. Zan, M. Dou, J. Liu, Z. Zhang, Y. Huang and F. Wang, Adv. Funct. Mater., 2019, 29, 201905095 Search PubMed
. - K. Gelse, E. Poschl and T. Aigner, Adv. Drug Delivery Rev., 2003, 55, 1531–1546 CrossRef CAS PubMed
. - H. Liu, W. Chen, H. Peng, X. Huang, S. Li, L. Jiang, M. Zheng, M. Xu and J. Zhu, Electrochim. Acta, 2022, 434, 141312 CrossRef CAS
. - K. Subhani, X. Jin, N. Hameed, A. K. Lau, J. A. M. Ramshaw, V. Glattauer and N. V. Salim, Mater. Today Sustain., 2022, 100152 CrossRef
. - N. Yang, R. Shao, Z. P. Zhang, M. L. Dou, J. Niu and F. Wang, Carbon, 2021, 178, 775–782 CrossRef CAS
. - G. J. Wang, Z. H. Lin, S. H. Jin, M. Li and L. Y. Jing, J. Energy Storage, 2022, 45, 103525 CrossRef
. - Q. Z. Du, Y. H. Zhao, K. L. Zhuo, Y. J. Chen, L. F. Yang, C. F. Wang and J. J. Wang, Nanoscale, 2021, 13, 13285–13293 RSC
. - X. M. Fan, C. Yu, J. Yang, Z. Ling, C. Hu, M. D. Zhang and J. S. Qiu, Adv. Energy Mater., 2015, 5, 201401761 Search PubMed
. - M. D. Zhang, C. Yu, Z. Ling, J. H. Yu, S. F. Li, C. T. Zhao, H. L. Huang and J. S. Qiu, Green Chem., 2019, 21, 2095–2103 RSC
. - S. Y. Cho, H. J. Yoon, N. R. Kim, Y. S. Yun and H. J. Jin, J. Power Sources, 2016, 329, 536–545 CrossRef CAS
. - Y. Sun, S. Xue, J. H. Sun, X. X. Li, Y. C. Ou, B. H. Zhu and M. Demir, J. Colloid Interface Sci., 2023, 645, 297–305 CrossRef CAS PubMed
. - K. Z. Gao, S. Y. Zhao, Q. Y. Niu and L. Z. Wang, Cellulose, 2019, 26, 9241–9254 CrossRef CAS
. - M. A. Meyers, P. Y. Chen, A. Y. M. Lin and Y. Seki, Prog. Mater. Sci., 2008, 53, 1–206 CrossRef CAS
. - S. Wu, H. Zhou, Y. Zhou, H. Wang, Y. Li, X. Liu and Y. Zhou, J. Alloys Compd., 2021, 859, 157814 CrossRef CAS
. - S. M. Wu, H. Zhou, Y. H. Zhou, H. Wang, Y. H. Li, X. Q. Liu and Y. M. Zhou, J. Alloys Compd., 2021, 859, 157814 CrossRef CAS
. - P. Sinha, A. Yadav, A. Tyagi, P. Paik, H. Yokoi, A. K. Naskar, T. Kuila and K. K. Kar, Carbon, 2020, 168, 419–438 CrossRef CAS
. - Y. N. Zhang, C. Y. Su, J. L. Chen, W. H. Huang and R. Lou, Rare Met., 2022, 42, 769–796 CrossRef
. - L. Borchardt, M. Oschatz and S. Kaskel, Mater. Horiz., 2014, 1, 157–168 RSC
. - B. Yan, J. Zheng, L. Feng, Q. Zhang, C. Zhang, Y. Ding, J. Han, S. Jiang and S. He, Mater. Des., 2023, 229, 111904 CrossRef CAS
. - S. Rawat, C. T. Wang, C. H. Lay, S. Hotha and T. Bhaskar, J. Energy Storage, 2023, 63, 107115 CrossRef
. - X. P. Li, J. U. Zhang, B. Liu, Z. P. Su and J. J. Klemes, J. Cleaner Prod., 2021, 310, 127428 CrossRef CAS
. - C. Young, T. Park, J. W. Yi, J. Kim, M. S. A. Hossain, Y. V. Kaneti and Y. Yamauchi, ChemSusChem, 2018, 11, 3546–3558 CrossRef CAS PubMed
. - Y. F. Yin, Q. J. Liu, J. Wang and Y. T. Zhao, Int. J. Hydrogen Energy, 2022, 47, 39338–39363 CrossRef CAS
. - Y. Li, Y. Sun, H. Li, M. Sun, J. Shen and S. Wang, Energy, 2023, 270, 126942 CrossRef CAS
. - S. A. Bhat, V. Kumar, S. Kumar, A. E. Atabani, I. Anjum Badruddin and K. J. Chae, Fuel, 2023, 337, 127125 CrossRef CAS
. - J. Yin, W. L. Zhang, N. A. Alhebshi, N. Salah and H. N. Alshareef, Small Methods, 2020, 4, 1900853 CrossRef CAS
. - D. Meng, Y. Hu, Y. Jing, X. Zhang, S. Mahmud, S. Su and J. Zhu, Fuel, 2022, 320, 124002 CrossRef CAS
. - Y. Gao, Q. Yue, B. Gao and A. Li, Sci. Total Environ., 2020, 746, 141094 CrossRef CAS PubMed
. - G. S. Jiang, R. A. Senthil, Y. Z. Sun, T. R. Kumar and J. Q. Pan, J. Power Sources, 2022, 520, 230886 CrossRef CAS
. - Q. Cao, M. Zhu, J. Chen, Y. Song, Y. Li and J. Zhou, ACS Appl. Mater. Interfaces, 2020, 12, 1210–1221 CrossRef CAS PubMed
. - Z. L. Yu, G. C. Li, N. Fechler, N. Yang, Z. Y. Ma, X. Wang, M. Antonietti and S. H. Yu, Angew. Chem. Int. Ed., 2016, 55, 14623–14627 CrossRef CAS PubMed
. - L. Y. Yang, J. Q. Li, Y. C. Zhou and J. F. Yao, J. Energy Storage, 2022, 50, 104252 CrossRef
. - Z. Zhai, B. Ren, Y. Xu, S. Wang, L. Zhang and Z. Liu, J. Power Sources, 2021, 481, 228976 CrossRef CAS
. - X. Tong, Z. Chen, H. Zhuo, Y. Hu, S. Jing, J. Liu and L. Zhong, Carbohydr. Polym., 2019, 207, 764–774 CrossRef CAS PubMed
. - J. Yin, W. Zhang, N. A. Alhebshi, N. Salah and H. N. Alshareef, Small Methods, 2020, 4, 1900853 CrossRef CAS
. - N. Díez, G. A. Ferrero, M. Sevilla and A. B. Fuertes, J. Mater. Chem. A, 2019, 7, 14280–14290 RSC
. - S. Wang, J. F. Feng and H. Pan, Colloids Surf., A, 2022, 651, 129622 CrossRef CAS
. - J. Deng, T. Y. Xiong, F. Xu, M. M. Li, C. L. Han, Y. T. Gong, H. Y. Wang and Y. Wang, Green Chem., 2015, 17, 4053–4060 RSC
. - Y. H. Wang, R. N. Liu, Y. D. Tian, Z. Sun, Z. H. Huang, X. L. Wu and B. Li, Chem. Eng. J., 2020, 384, 123263 CrossRef CAS
. - K. J. Zhang, M. R. Liu, T. Z. Zhang, X. Y. Min, Z. R. Wang, L. Y. Chai and Y. Shi, J. Mater. Chem. A, 2019, 7, 26838–26848 RSC
. - P. Wang, H. Ye, Y. X. Yin, H. Chen, Y. B. Bian, Z. R. Wang, F. F. Cao and Y. G. Guo, Adv. Mater., 2019, 31, 1805134 CrossRef PubMed
. - F. Wang, J. Y. Cheong, J. Lee, J. Ahn, G. G. Duan, H. L. Chen, Q. Zhang, I. D. Kim and S. H. Jiang, Adv. Funct. Mater., 2021, 31, 2101077 CrossRef CAS
. - C. D. Liang, Z. J. Li and S. Dai, Angew. Chem. Int. Ed., 2008, 47, 3696–3717 CrossRef CAS PubMed
. - Q. Wang, W. Ma, E. Yin, S. Yu, S. Wang, H. Xiang, D. Li and M. Zhu, ACS Appl. Energy Mater., 2020, 3, 9360–9368 CrossRef CAS
. - Y. D. Zhong, T. Wang, M. Yan, C. Miao, X. F. Zhou and G. L. Tong, Int. J. Biol. Macromol., 2022, 217, 66–76 CrossRef CAS PubMed
. - C. Ma, L. Q. Wu, M. Dirican, H. Cheng, J. J. Li, Y. Song, J. L. Shi and X. W. Zhang, J. Colloid Interface Sci., 2021, 586, 412–422 CrossRef CAS PubMed
. - J. Cao, C. Zhu, Y. Aoki and H. Habazaki, ACS Sustain. Chem. Eng., 2018, 6, 7292–7303 CrossRef CAS
. - E. K. Kim, H. S. Chang, B. M. Lee, J. J. Park, J. M. Yun and J. H. Choi, Sustainable Mater. Technol., 2022, 34, e00520 CrossRef CAS
. - X. W. Liu, X. H. Liu, B. F. Sun, H. L. Zhou, A. P. Fu, Y. Q. Wang, Y. G. Guo, P. Z. Guo and H. L. Li, Carbon, 2018, 130, 680–691 CrossRef CAS
. - G. J. Liang, L. G. Zhu, J. Xu, D. Fang, Z. K. Bai and W. L. Xu, Electrochim. Acta, 2013, 103, 9–14 CrossRef CAS
. - Y. T. Qiu, M. Z. Hou, J. C. Gao, H. L. Zhai, H. M. Liu, M. M. Jin, X. Liu and L. F. Lai, Small, 2019, 15, 1903836 CrossRef CAS PubMed
. - J. Lin, L. Yao, Z. Li, P. Zhang, W. Zhong, Q. Yuan and L. Deng, Nanoscale, 2019, 11, 3281–3291 RSC
. - H. Li, Y. H. Zhao, S. Q. Liu, P. C. Li, D. Yuan and C. B. He, Microporous Mesoporous Mater., 2020, 297, 109960 CrossRef CAS
. - L. Yao, J. Lin, Y. Chen, X. Li, D. Wang, H. Yang, L. Deng and Z. Zheng, InfoMat, 2022, 4, e12278 CrossRef CAS
. - Q. Wu, M. M. Gao, S. S. Cao, J. Q. Hu, L. Huang, S. T. Yu and A. J. Ragauskas, J. Taiwan Inst. Chem. Eng., 2019, 101, 231–243 CrossRef CAS
. - X. Hou, H. Dang, M. Liu, X. Shang, Y. Fu and D. He, J. Alloys Compd., 2019, 810, 151736 CrossRef CAS
. - X. S. Zhang, W. B. Jian, L. Zhao, F. W. Wen, J. L. Chen, J. Yin, Y. L. Qin, K. Lu, W. L. Zhang and X. Q. Qiu, Colloids Surf., A, 2022, 636, 128191 CrossRef CAS
. - L. Zhao, W. B. Jian, X. S. Zhang, F. W. Wen, J. H. Zhu, S. Huang, J. Yin, K. Lu, M. S. Zhou, W. L. Zhang and X. Q. Qiu, J. Energy Storage, 2022, 53, 105095 CrossRef
. - J. Pang, W. F. Zhang, J. L. Zhang, G. P. Cao, M. F. Han and Y. S. Yang, Green Chem., 2017, 19, 3916–3926 RSC
. - J. W. Li, X. F. Li, D. B. Xiong, L. Z. Wang and D. J. Li, Appl. Surf. Sci., 2019, 475, 285–293 CrossRef CAS
. - Y. K. Fan, F. B. Fu, D. J. Yang, W. F. Liu, Z. X. Li and X. Q. Qiu, J. Energy Storage, 2023, 63, 106947 CrossRef
. - Y. F. Zheng, K. M. Chen, K. P. Jiang, F. R. Zhang, G. S. Zhu and H. R. Xu, J. Energy Storage, 2022, 56, 105995 CrossRef
. - Z. Bian, H. Wang, X. Zhao, Z. Ni, G. Zhao, C. Chen, G. Hu and S. Komarneni, J. Colloid Interface Sci., 2023, 630, 115–126 CrossRef CAS PubMed
. - F. B. Fu, D. J. Yang, B. W. Zhao, Y. K. Fan, W. F. Liu, H. M. Lou and X. Q. Qiu, J. Colloid Interface Sci., 2023, 640, 698–709 CrossRef CAS PubMed
. - X. Feng, Y. Bai, M. Q. Liu, Y. Li, H. Y. Yang, X. R. Wang and C. Wu, Energy Environ. Sci., 2021, 14, 2036–2089 RSC
. - M. Seredych, D. Hulicova-Jurcakova, G. Q. Lu and T. J. Bandosz, Carbon, 2008, 46, 1475–1488 CrossRef CAS
. - S. A. Wang, L. N. Dong, Z. Y. Li, N. Lin, H. Xu and S. M. Gao, Int. J. Biol. Macromol., 2020, 164, 4095–4103 CrossRef CAS PubMed
. - J. Q. Sun, J. Zhang, M. G. Shang, M. N. Zhang, X. F. Zhao, S. J. Liu, X. C. Liu, S. Liu and X. B. Yi, Appl. Surf. Sci., 2023, 608, 155109 CrossRef CAS
. - Y. Zhou, S. L. Candelaria, Q. Liu, Y. X. Huang, E. Uchaker and G. Z. Cao, J. Mater. Chem. A, 2014, 2, 8472–8482 RSC
. - X. Wang, M. Hou, Z. Shi, X. Liu, I. Mizota, H. Lou, B. Wang and X. Hou, ACS Appl. Mater. Interfaces, 2021, 13, 12059–12068 CrossRef CAS PubMed
. - C. G. Hu and L. M. Dai, Adv. Mater., 2019, 31, 1804672 CrossRef PubMed
. - Q. Abbas, R. Raza, I. Shabbir and A. G. Olabi, J. Sci.: Adv. Mater. Devices, 2019, 4, 341–352 Search PubMed
. - J. Huang, W. Zhang, H. B. Huang, Y. L. Liu, Q. Y. Yang and L. Li, ACS Sustain. Chem. Eng., 2019, 7, 16710–16719 CrossRef CAS
. - B. B. Fan, S. M. Wu, H. Wang and Y. M. Zhou, J. Electrochem. Soc., 2021, 168, 100534 CrossRef CAS
. - S. Qiu, Z. Chen, H. Zhuo, Y. Hu, Q. Liu, X. Peng and L. Zhong, ACS Sustain. Chem. Eng., 2019, 7, 15983–15994 CrossRef CAS
. - Y. M. Wang, X. Wang, X. L. Li, Y. Bai, H. H. Xiao, Y. Liu, R. Liu and G. H. Yuan, Adv. Funct. Mater., 2019, 29, 1900326 CrossRef
. - L. Ma, J. Liu, S. Lv, Q. Zhou, X. Shen, S. Mo and H. Tong, J. Mater. Chem. A, 2019, 7, 7591–7603 RSC
. - P. Zhang, J. P. Li, D. Y. Yang, R. A. Soomro and B. Xu, Adv. Funct. Mater., 2022, 33, 2209918 CrossRef
. - R. Liu, A. Zhou, X. Zhang, J. Mu, H. Che, Y. Wang, T.-T. Wang, Z. Zhang and Z. Kou, Chem. Eng. J., 2021, 412, 128611 CrossRef CAS
. - K. Ren, Z. Liu, T. Wei and Z. J. Fan, Nano-Micro Lett., 2021, 13, 129 CrossRef CAS PubMed
. - S. Kumar, G. Saeed, L. Zhu, K. N. Hui, N. H. Kim and J. H. Lee, Chem. Eng. J., 2021, 403, 126352 CrossRef CAS
. - K. Zhao, X. Sun, Z. Wang, C. Huang, D. Li and J. Liu, J. Alloys Compd., 2022, 921, 166036 CrossRef CAS
. - X. Ning, F. Li, Y. Zhou, Y.-E. Miao, C. Wei and T. Liu, Chem. Eng. J., 2017, 328, 599–608 CrossRef CAS
. - H. Peng, J. Zhou, Z. Chen, R. Zhao, J. Liang, F. Wang, G. Ma and Z. Lei, J. Alloys Compd., 2019, 797, 1095–1105 CrossRef CAS
. - D. Wu and W. B. Zhong, J. Mater. Chem. A, 2019, 7, 5819–5830 RSC
. - N. Kumar, S. B. Kim, S. Y. Lee and S. J. Park, Nanomaterials, 2022, 12, 3708 CrossRef CAS PubMed
. - H. Zhuo, Y. J. Hu, Z. H. Chen and L. X. Zhong, Carbohydr. Polym., 2019, 215, 322–329 CrossRef CAS PubMed
. - S. Liu, K. Wan, C. Zhang and T. Liu, Compos. Commun., 2021, 24, 100610 CrossRef
. - F. B. Fu, H. Wang, D. J. Yang, X. Q. Qiu, Z. X. Li and Y. L. Qin, J. Colloid Interface Sci., 2022, 617, 694–703 CrossRef CAS PubMed
. - S. M. Mousavi, S. A. Hashemi, M. Y. Kalashgrani, A. Gholami, Y. Mazaheri, M. Riazi, D. Kurniawan, M. Arjmand, O. Madkhali, M. D. Aljabri, M. M. Rahman and W. H. Chiang, Chem. Rec., 2023, 202200266 CrossRef PubMed
. - J. L. Espinoza-Acosta, P. I. Torres-Chávez, J. L. Olmedo-Martínez, A. Vega-Rios, S. Flores-Gallardo and E. A. Zaragoza-Contreras, J. Energy Chem., 2018, 27, 1422–1438 CrossRef
. - M. S. Rostami and M. M. Khodaei, J. Energy Storage, 2023, 72, 108344 CrossRef
.
|
This journal is © The Royal Society of Chemistry 2023 |
Click here to see how this site uses Cookies. View our privacy policy here.