DOI:
10.1039/D2SC01180H
(Edge Article)
Chem. Sci., 2022,
13, 7172-7180
Tailoring a robust Al-MOF for trapping C2H6 and C2H2 towards efficient C2H4 purification from quaternary mixtures†
Received
25th February 2022
, Accepted 15th May 2022
First published on 20th May 2022
Abstract
Light hydrocarbon separation is considered one of the most industrially challenging and desired chemical separation processes and is highly essential in polymer and chemical industries. Among them, separating ethylene (C2H4) from C2 hydrocarbon mixtures such as ethane (C2H6), acetylene (C2H2), and other natural gas elements (CO2, CH4) is of paramount importance and poses significant difficulty. We demonstrate such separations using an Al-MOF synthesised earlier as a non-porous material, but herein endowed with hierarchical porosity created under microwave conditions in an equimolar water/ethanol solution. The material possessing a large surface area (793 m2 g−1) exhibits an excellent uptake capacity for major industrial hydrocarbons in the order of C2H2 > C2H6 > CO2 > C2H4 > CH4 under ambient conditions. It shows an outstanding dynamic breakthrough separation of ethylene (C2H4) not only for a binary mixture (C2H6/C2H4) but also for a quaternary combination (C2H4/C2H6/C2H2/CO2 and C2H4/C2H6/C2H2/CH4) of varying concentrations. The detailed separation/purification mechanism was unveiled by gas adsorption isotherms, mixed-gas adsorption calculations, selectivity estimations, advanced computer simulations such as density functional theory (DFT), grand canonical Monte Carlo (GCMC) and ab initio molecular dynamics (AIMD), and stepwise multicomponent dynamic breakthrough experiments.
Introduction
Purification and separation of chemical mixtures account for about 15% of total industrial energy consumption and are expected to increase nearly three times in the next twenty years as demand increases sharply in chemical industries.1,2 At present, industry performs separation by utilising two major classical techniques, either via cryogenic distillation or a solvent extraction process.3 However, these separation technologies are impaired by high energy penalties, while adsorptive separation using porous materials is environmentally friendly, effortless, and energetically inexpensive, which would save 80% of total energy expenditure.4 The separation of several bulk chemical commodities involving light hydrocarbons (ethane, C2H6; ethylene, C2H4; acetylene, C2H2; methane, CH4; etc.), which are the kernels of much industrial manufacturing, poses significant challenges due to their comparable shapes, volatilities and other physicochemical properties.5,6
C2H4 is the most commercially significant as it has exceeded an annual global production of 200 million tonnes.7,8 Conventionally, C2H4 is obtained through steam cracking, catalytic/oxidative dehydrogenation and thermal decomposition of naphtha or C2H6, in which a certain amount of C2H6 and C2H2 co-exists and needs to be removed to produce polymer grade C2H4, broadly utilised in polymer, fibre and chemical industries.9–11 In this process, C2H2 is primarily expelled through catalytic hydrogenation by using noble metal catalysts with the requirement of high pressure and temperature.12,13 This C2H2 can act as a spoiler by reacting with catalytic metals to form acetylides, which have been known to engender explosion by blocking the gas flow. Within the same process, C2H6 is later separated from C2H4 by an energy-intensive high-pressure cryogenic distillation, typically at 5–28 bar and 183–258 K, which accounts for a notable hike in C2H4 price.14–16 The separation of C2H6/C2H4 is presently considered the most challenging industrial separation, owing to similar molecular shapes (C2H4: 3.28 × 4.18 × 4.84 Å3; C2H6: 3.81 × 4.08 × 4.82 Å3) and boiling points (169.42 K for C2H4 and 184.55 for C2H6).6,17,18 Concomitantly, the simultaneous removal of C2H6 and C2H2 through a more energy-efficient route with a single-step and reduced energy footprint for C2H4 production would be of industrial relevance.
At the same time, C2H2 is also considered a major feedstock for polymer, polyester, plastic and chemical industries in the synthesis of essential organic compounds, including acrylic acid derivatives, α-ethynyl alcohols and vinyl compounds.19,20 C2H2 is mainly produced by thermal cracking or partial combustion of hydrocarbons including naphtha or natural gas, co-existing with spin-offs such as C2H4, CO2 and CH4.19,21,22 Purification of C2H2 from CO2 is enormously challenging due to similarities in shape (C2H2: 3.32 × 3.34 × 5.7 Å3; CO2: 3.18 × 3.33 × 5.36 Å3), boiling point (189.3 K for C2H2 and 194.7 K for CO2) and other physical properties (polarizabilities of C2H2 and CO2 are 19.5 and 33.3–39.3, respectively).23 As an alternative, being acquired as a by-product in petroleum refining, C2H4 is also refined on an industrial scale from natural gas (CH4 ∼ 70–90%, CO2 ∼ 0–10%, C2H6 and C2H4 ∼ 1–15%).24 As an outcome of similar physicochemical properties, it is most desirable but extremely complex to purify C2H4 from its associated bi-components, in particular C2H6, C2H2, CO2 and CH4 (Table S1†), through a one-step purification technique.
In the last two decades, great efforts have been undertaken in designing metal–organic frameworks (MOFs) as promising sorbents for various gas separations ranging from the simple N2/CO2 or H2/CO2 to the most challenging one such as olefin/paraffin by modulating the surface area, pore geometry, supramolecular and adsorbate–adsorbent interactions dictated by thermodynamic and kinetic preferences. To avail the preferential selectivity in MOFs, a few strategies have been generally adopted: (i) tuning the pore size/shapes, (ii) introducing functional organic linkers to generate strong binding sites, (iii) decorating the pore environment for favoured polarity and (iv) enhancing the density of open-metal sites (OMSs) for stronger interaction with unsaturated hydrocarbons.25–29 MOFs with open-metal sites customarily adsorb C2H4 over C2H6 as a consequence of electrostatic interaction between the π–electrons of C2H4 and the positively charged metal centres.30–33 However, this process leads to the preferential adsorption of C2H4, and releases C2H6 first, while C2H4 has to be recovered through heating or purging with an inert gas. Alternatively, this problem can be solved by employing C2H6 selective MOFs, which not only improves the purity of the liberated C2H4 but also avoids the multistep separation process by reducing energy expenditure.5 To date, only a few hydrophobic or less polar MOFs have been reported with low separation performance as the hydrophobic space is hardly capable of distinguishing non-polar C2H6 and C2H4.15,34–39 Yet, MOFs exhibiting such reverse adsorption phenomena of preferential C2H6 and C2H2 selectivity over C2H4 are still rare as of now.40–42
The Al-NDC ([Al(OH)(1,4-NDC)]·2H2O) MOF has high thermal and chemical stability with a robust 3D structure containing naphthalene moieties through the channel walls with distinct pore channels with sizes 3 × 3 Å2 (small pore channel) and 7.7 × 7.7 Å2 (large pore channel), respectively (Scheme 1).43 Here, we report the exclusive, unrivalled performance of an Al-MOF, an adsorbent displaying strong preferential adsorption of C2H2 and C2H6 over C2H4. The microwave heating enables faster nucleation that helps the formation of smaller particle sizes with an increased surface-to-volume ratio.44 Additionally, the mixed solvent duo, water–ethanol clusters act as templates for additional mesopore formation and corresponding hierarchical porosity in the framework.45 This investigation unfolds the impact of reaction time, ranging from 5 to 220 minutes, wherein the MOF produced with 15 minutes (Al-MOFM15) of reaction time showed the maximum surface area (BET; 793 m2 g−1) with the highest micro–mesopore volume ratio. Al-MOFM15 turned out to be an efficient adsorbent for the purification of C2H4 from the binary C2H6/C2H4 and quaternary C2H4/C2H6/C2H2/CO2 and C2H4/C2H6/C2H2/CH4 mixtures based on dynamic breakthrough studies. The C2H2/CO2, C2H6/CH4 and CO2/CH4 separation performances were also examined under ambient conditions. The key separations were performed through a stepwise dynamic breakthrough technique to obtain each component with high purity; the MOF retained its performance over multiple cycles, without any temperature swing desorption, and promises to be an efficient, major C2 hydrocarbon sorting tool in future industrial separation processes.
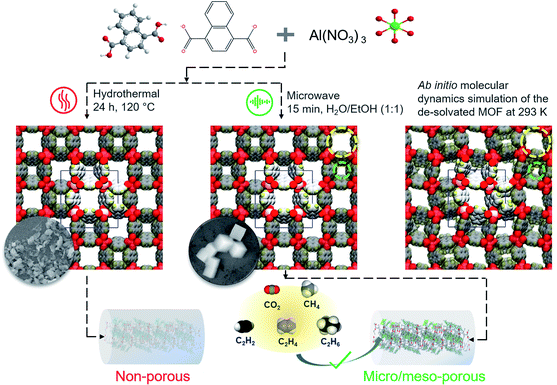 |
| Scheme 1 Schematic representation of the hydrothermal (left) and microwave heating (right) synthesis strategy for Al-MOF and Al-MOFM15, respectively. The corresponding insets are the FESEM images showing the morphologies of Al-MOF and Al-MOF15, respectively (see Fig. S2†). A small and a large pore channel are identified in green and yellow dashed circles, respectively. Ab initio molecular dynamics simulation of the de-solvated MOF at 293 K shows spontaneous closure of the small pore channels (extreme right). | |
Results and discussion
Synthesis and characterisation
The non-porous Al-NDC ([Al(OH)(1,4-NDC)]·2H2O) MOF was selected and synthesised by the hydrothermal reaction of 1,4-naphthalenedicarboxylate and Al(NO3)3·9H2O, according to the previously reported method.43 Al-NDC MOF was also synthesised under microwave heating conditions by tailoring the reaction times (5, 15, 30, 60, 120 and 220 minutes) with the assistance of the water/ethanol (1
:
1) solvent duo and six different products, namely Al-MOFM5, Al-MOFM15, Al-MOFM30, Al-MOFM60, Al-MOFM120, and Al-MOFM220, respectively (‘M’ stands for microwave and the subscript represents the reaction time in minutes) were isolated (see the ESI†).45 The similarity in powder X-ray diffraction (PXRD) patterns with that of the simulated pattern revealed the formation of a similar three-dimensional framework with two square-shaped cross-sectional channels (Fig. S1†). As reported by us previously, the microwave heating enables faster nucleation that improves the structural porosity by enhancing the surface-to-volume ratio based on particle downsizing.44–46 N2 adsorption experiments were performed at 77 K (Fig. S3†) to establish permanent porosity and Al-MOFM5, Al-MOFM15, Al-MOFM30, Al-MOFM60, Al-MOFM120, Al-MOFM220 with BET surface areas estimated to be 759, 793, 731, 694, 682 and 664 m2 g−1, respectively (Fig. S4†). The N2 adsorption isotherms for Al-MOFM5 and Al-MOF15 exhibited a characteristic type-I profile corresponding to a microporous nature, whereas Al-MOFM30,60,120,220 showed additional mesopore formation with the combination of type-I and type-IV isotherms (Fig. S3a†). The NLDFT (non-local density functional theory) model-based pore-size distribution analysis reveals the presence of mesopores with a size of about 3.6 nm with a gradual decrease in surface area and the corresponding micro-to-mesopore volume ratios for post-30 min reaction times (Fig. S3b and S4†). There are a few reports of low polarity or hydrophobic MOFs39,47,48 with high surface areas including structural rigidity, desirable pore aperture, and fascinating thermal and chemical stabilities with excellent moisture robustness.49–52 Thus, the remarkable surface area with exclusive microporosity (centred at 1.2 nm) of Al-MOFM15 prompted us to investigate its light hydrocarbon adsorption and separation properties.
Single-component hydrocarbon adsorption and mixed-gas selectivity calculation
Single component adsorption–desorption isotherms for CO2, CH4, C2H2, C2H4, and C2H6 were studied using activated Al-MOFM15 at 293 and 273 K. As shown in Fig. 1a and 2a, the saturation uptake amounts for C2H2, C2H6, CO2, C2H4, and CH4 are 64 (2.85 mmol g−1), 50 (2.23 mmol g−1), 40 (1.785 mmol g−1), 29 (1.29 mmol g−1) and 14 (0.625 mmol g−1) mL g−1 (or cm3 g−1) at 293 K, respectively. The isosteric heats of adsorption (Qst) were estimated with the Clausius–Clapeyron equation by fitting the isotherms using the virial expression and Freundlich–Langmuir (FL) isotherm models at 273, 283 and 293 K (Fig. S6–S12†).53Qst estimated by virial and FL-fitting are in qualitative agreement for the five gases; we use the ones obtained using virial fitting for the discussion that follows. The order of resultant Qst at near-zero coverage (Qst(0)) is C2H6 (−45.0 kJ mol−1) > C2H2 (−40.2 kJ mol−1) > C2H4 (−32.8 kJ mol−1) > CO2 (−24.6 kJ mol−1) > CH4 (−22.0 kJ mol−1). Notably, the adsorption enthalpies for CO2 and C2H2 do not vary substantially with loading suggesting uniformity in binding sites (Fig. 2b). On the other hand, high polarizability endorses a relatively greater affinity for C2H6 among C2 hydrocarbons (Table S4†). For C2H4, as shown in Fig. 1b, the adsorption enthalpy rapidly increases with the loading amount because of probable π⋯π and C–H⋯π interactions among guests. Most importantly, under dilute conditions, C2H6 has higher binding affinity compared to that of C2H4 by about 12 kJ mol−1, greater than in any other benchmark porous materials reported so far (Fig. S13 and Table S6†). As documented in Table S1,† C2H6–C2H4 separation is extremely challenging because of comparable physical properties. C2H4 (1.5 × 10−26 esu cm2) has a higher quadrupole moment over C2H6 (0.65 × 10−26 esu cm2), making the process of fabricating C2H4-selective MOFs relatively straightforward, for example, by incorporating unsaturated metal sites or a hydrogen-bonding acceptor to stimulate the selectivity.31,54 Achieving the reverse, i.e., enabling the preferential sorption of C2H6 over C2H4 is non-trivial, which can simplify the separation process by selectively releasing pure C2H4 from the downstream outlet.5,55 On a similar note, separating C2H2/CO2 is equally complex as a consequence of cognate molecular dimensions (C2H2: 3.32 × 3.34 × 5.7 Å3 and CO2: 3.18 × 3.33 × 5.36 Å3) and boiling points (C2H2, 189.3 K; CO2, 194.7 K). The higher uptake ratio of C2H6 over C2H4 and C2H2 over CO2 in Al-MOFM15 motivated us to study the nature of hydrocarbon binding interaction in its pore channels. In addition, the adsorption kinetics of CO2 and CH4 are analysed by fitting it into the LDF (linear driving force) model at the first adsorption point (P ∼ 4 kPa). CO2 shows a faster rate of adsorption with a rate constant value of 0.184 compared to CH4 (k = 2.25 × 10−3; Fig. S14†).
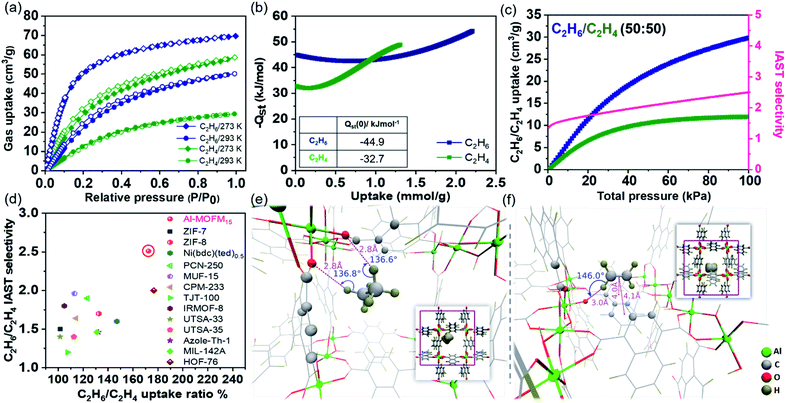 |
| Fig. 1 (a) Single-component adsorption–desorption isotherms of C2H6 and C2H4 in Al-MOFM15 measured at 273 and 293 K for pressures 0–690 torr. (b) Isosteric heats of adsorption (Qst) of C2H6 and C2H4 at various loading amounts (near-zero coverage Qst values are provided in the inset). (c) Mixed adsorption isotherms and selectivity calculated using IAST for C2H6/C2H4 (50 : 50) in Al-MOFM15 at 293 K. (d) C2H6/C2H4 separation performance in some benchmark porous materials. (e and f) Locations of the highest binding affinity sites determined by DFT optimization for C2H6 (−39.9 kJ mol−1) and C2H4 (−38.7 kJ mol−1). Insets: Corresponding molecule locations, zoomed out, within the large channel. C2H6 participates in two hydrogen-bonding interactions with carboxylate oxygens while C2H4 participates in π–π and hydrogen-bonding interactions with the naphthalene ring and carboxylate oxygen, respectively. Binding sites with lower affinities for C2H4 and C2H6 are shown in Fig. S23 and S24,† respectively. | |
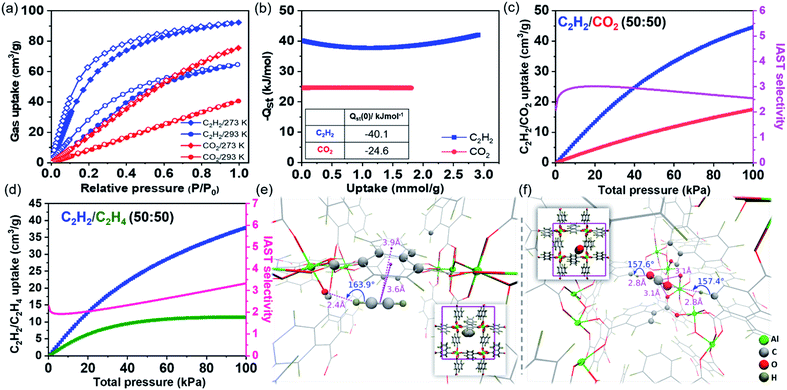 |
| Fig. 2 (a) Single-component adsorption–desorption isotherms of C2H2 and CO2 in Al-MOFM15 measured at 273 and 293 K for pressures 0–690 torr. (b) Isosteric heats of adsorption (Qst) of C2H2 and CO2 at various loading amounts (Qst values at near-zero coverage area are provided in the inset). (c and d) Mixed adsorption isotherms and selectivity calculated using IAST for (c) C2H2/CO2 (50 : 50) and (d) C2H2/C2H4 (50 : 50) in Al-MOFM15 at 293 K. (e and f) Locations of the highest binding affinity sites determined by DFT optimization for C2H2 (−37.3 kJ mol−1) and CO2 (−36.0 kJ mol−1), respectively. Insets show the positions of the guest molecules within the square cross-section of a large pore, while the corresponding main panels show their neighbourhood. C2H2 participates in π–π and hydrogen-bonding interactions with a naphthalene ring and a carboxylate oxygen, respectively, while CO2 interacts with two naphthalene hydrogens and a carboxylate oxygen via hydrogen-bonding and Lewis acid–base interactions, respectively. Binding sites with lower affinities for CO2 and C2H2 are shown in Fig. S21 and S22,† respectively. | |
Next, to estimate the adsorption isotherm and adsorption selectivity for the equimolar composition of gases under ambient (293 K, 1 bar) and near ambient conditions (273 K, 1 bar; Fig. S17–S20†), ideal adsorption solution theory (IAST)56 was employed. The Freundlich–Langmuir model was used to fit single-component experimental adsorption isotherms (at 273 and 293 K). The calculated bi-component equimolar C2H6/C2H4 adsorption isotherms are shown in Fig. 1c. The mixed adsorption amounts at 100 kPa for C2H6 and C2H4 are 41 and 29 mL g−1, respectively, whereas, for the C2H2/CO2 combination, the individual saturation uptakes are 44 and 17 mL g−1 (Fig. 1c, 2c and Table S3†). The selectivity value rises with increasing gas pressure for C2H6/C2H4, confirming the real separation ability of Al-MOFM15 under practical conditions. The selectivity of C2H6 over C2H4 exceeds most reported top-performing porous materials (Fig. 1d; Tables S3 and S6†). For C2H2/CO2, the selectivity factor reaches a maximum (3.018) at 20 kPa, and further drops with an increase in pressure (Fig. 2c).57,58 In contrast, C2H2/C2H4 selectivity drops to a minimum before exhibiting a monotonically increasing behaviour (Fig. 2d).59 As shown in Fig. 1c, 2c and d, the adsorption selectivities for C2H6/C2H4, C2H2/CO2 and C2H2/C2H4 at a pressure of 100 kPa were calculated to be 2.51, 2.54 and 3.32, respectively. For other equimolar mixtures, the selectivities of C2H2/C2H4, C2H6/CH4, CO2/CH4 and C2H2/CH4 are 6.15, 2.9, 3.32 and 7.12, respectively at 100 kPa at ambient temperature (293 K). To the best of our knowledge, Al-MOFM15 is one of those rare porous materials that show such a high selectivity in the range of 2 to 8 for all light hydrocarbon mixtures under ambient conditions (100 kPa and 293 K; Tables S3, S6 and S7†).60,61 In addition, Grand Canonical Monte Carlo (GCMC) simulations were also performed to theoretically calculate single-component adsorption isotherms. As shown in Fig S41,† the isotherms were obtained by performing the simulations after blocking the small pore channels of Al-MOF. Although these isotherms showed lower uptake than those obtained by not imposing any such restriction on where the molecules were adsorbed, they continued to overpredict the uptake amounts compared to the experimental observations; disregarding the flexibility of the naphthalene rings in the GCMC simulations could be a plausible reason for the overprediction.
Insights from molecular simulations
To understand the interactions governing single component adsorption, a combination of advanced molecular simulation tools was employed to (a) gain better insights into the binding sites and adsorption affinities of a diverse set of guest molecules—CO2, C2H2, C2H4, C2H6, and CH4 inside Al-MOF and (b) elucidate the underlying microscopic reasons for the crossover in Qstvs. uptake between C2H4 and C2H6 (Fig. 1b). We set out to identify binding sites only in the large pore channels (Fig. S16†) because of the following factors: (i) 129Xe NMR studies by Comotti et al.43 showed that xenon adsorption into the small pore channels (3 × 3 Å2) was negligible. However, the smallest dimension of any of the guests considered in the present work is well over 3 Å. (ii) To gain additional insights, a five pico-second ab initio molecular dynamics (AIMD) trajectory of the de-solvated MOF at 293 K was generated (Fig. S40 and ESI Movie†). The AIMD trajectory shows that the small pore channels are closed spontaneously, hence, cannot accommodate guest molecules (Scheme 1).
To identify preferred binding sites of the adsorbate molecule in the large pore channels, we adopted the following procedure. We first obtain a set of coarsely determined binding sites for each guest and their corresponding orientations in a 1 × 1 × 2 supercell of Al-MOF. Several such Al-MOF simulation boxes loaded with a guest molecule each are further optimised individually. Density functional theory (DFT) is employed for geometry optimisations. The corresponding binding energies (BEs) were calculated for each optimised configuration. The range of binding energies (BEs) for guest molecules show good agreement with the experimentally measured isosteric heats of adsorption at near-zero coverage [Qst(0)] (Fig. S26 and Table S4†)—CO2 (BE = −19.1 to −36.0 kJ mol−1; Qst(0) = −24.6 kJ mol−1), C2H2 (BE = −34.5 to −37.3 kJ mol−1; Qst(0) = −40.2 kJ mol−1), C2H4 (BE = −33.2 to −38.7 kJ mol−1; Qst(0) = −32.8 kJ mol−1), C2H6 (BE = −34.8 to −39.9 kJ mol−1; Qst(0) = −45.0 kJ mol−1), CH4 (BE = −25.2 to −25.4 kJ mol−1; Qst(0) = −22.0 kJ mol−1). In Fig. 1e, f and 2e, f, specific interactions such as hydrogen bonding, π-interactions, and Lewis acid–base pairs are depicted with relevant distances and/or angles. While these interactions aid in the adsorption of a guest molecule onto the surface of the pore channel, the affinity is predominantly due to dispersion interactions. To demonstrate the same, heavy (non-hydrogen) atoms that lie within 4 Å to any heavy atom of the guest molecule are represented as spheres in prominent figures (Fig. 1e, f and 2e, f).
The primary binding sites of CO2, CH4, and C2H6 are the corners of a pore channel. Corners allow a CO2 molecule to participate in two weak hydrogen bonds and interact with two other carboxylate oxygen atoms of the framework (Fig. 2f) while enabling a C2H6 molecule to interact via hydrogen bonding with two framework carboxylate oxygen atoms (Fig. 1e). In contrast, C2H2 and C2H4 primarily bind to an edge. The π-clouds on these guests favour π-interactions with those of the naphthalene rings of the framework; however, additionally, they allow the guests to participate in one weak hydrogen bond each (Fig. 1f and 2e). Furthermore, binding sites close to an edge of a pore channel for CO2/C2H6 and near the corner for C2H2/C2H4 exist, as shown in Fig. S21–S24.†
The isosteric heats of adsorption (Qst) for CO2 and C2H2 are nearly coverage-independent. In contrast, Qst values for both C2H4 and C2H6 show a nearly monotonic increase with loading (Fig. 1b and S12†). Despite having a much smaller Qst at near-zero coverage, the former increases rapidly with loading, thus surpassing the latter at a coverage of 0.92 mmol g−1 or about two molecules per unit cell of Al-MOF. To delineate this phenomenon, we followed the same protocol as that of single-molecule binding energy calculations, but now with simulation boxes consisting of more guest molecules.
Since we have considered two-unit cells of Al-MOF for our calculations, we generated initial configurations with four and six (2 and 3 molecules per unit cell, respectively) C2H4 and C2H6 guest molecules. Now, as the simulation cell includes two large pore channels, the configurations were further classified as 2/0, 1.5/0.5, and 1/1 configurations for two guest molecules per unit cell and likewise, 3/0, 2.5/0.5, 2/1, and 1.5/1.5 for three guest molecules per unit cell, depending on the number of guest molecules per pore channel per unit cell (Fig. S27–S39†). Following optimisation, in addition to binding energies (BE), we calculated the cooperative interaction energy (Ec) or the adsorbate–adsorbate interaction energies (see the ESI†). The average binding energies of molecules showed a steady increase with coverage for both C2H4 and C2H6 and to a greater extent when the molecules were concentrated in one of the channels. For 2/0 configurations, the binding energy for C2H6 and C2H4 was −43.1 and −41.1 kJ mol−1 (Table S5†), respectively, which are higher than their one molecule equivalents (Fig. S27, S30 and Table S4†). Three molecules per pore channel per unit cell (3/0) configuration were not obtained for C2H6, due to their large size.
In contrast, the binding energies ranged between −40.2 and −41.1 kJ mol−1 (Fig. S33†) for C2H4-3/0 configurations. Adsorbate–adsorbate interactions contribute significantly to the binding affinity, ranging between −5.6 and −6.9 kJ mol−1 (Table S5†). We speculate that the effect of cooperativity and hence the Qst increase with higher coverage might be much more prominent in actual samples than in a small simulation box we considered in our calculations. However, the cross-over in Qstvs. coverage between C2H4 and C2H6 does not affect the order of selectivity in equimolar mixture adsorption under ambient conditions. IAST calculations revealed that even at the highest pressure (P/P0 ∼ 1), the uptake amount of C2H4 is ∼0.5 mmol g−1, much less than ∼0.92 mmol g−1 where the cross-over occurs (Fig. 1b and S12†).
Stepwise multicomponent dynamic breakthrough separation
Along with high thermal (∼450 °C) and moisture stability (Fig. S15†), the estimated mixed gas adsorption isotherm with excellent selectivity prompted us to explore the performance of the material under real-time conditions. A series of practical breakthrough experiments were carried out on Al-MOFM15 for bi-component and quaternary-component gas mixtures. As shown in Fig. 3a, the C2H6/C2H4 mixture (0.5
:
0.5, v/v) was streamed through a packed column of activated adsorbent at the rate of 2.2–2.9 mL min−1 at 298 K. C2H4 can be detected first from the outlet gas runoff during the initial purges, resulting in a desirable high purity for more than 40 minutes, while no C2H6 was found. At approximately 45 minutes, as the adsorbent became saturated in the dynamic flow, C2H6 reached its breakthrough point as detected in the outlet downstream. Perceptibly, the C2H6 selective Al-MOFM15 allows early release of pure C2H4, significantly simplifying the purification of this major petrochemical feedstock. However, as soon as the outlet stream reaches equal proportion, by closing the feed flow and only allowing the carrier gas, the absorbed C2H6 could be removed by regenerating the column for subsequent separations. To confirm the regeneration of Al-MOFM15, we conducted a stepwise dynamic breakthrough for three consecutive cycles, and breakthrough times of the maximum release of each component are presented in Fig. 3b. Thereafter, a similar process was followed for the 0.5
:
0.5 mixture of C2H2/CO2, CO2/CH4 and C2H6/CH4. For C2H2/CO2, CO2 appears in the outlet flow as early as 10 minutes, while it took almost 6.5 times longer for C2H2 to reach its breakthrough point, revealing excellent separation performance for C2H2 from CO2 (Fig. 3c and d). In contrast, for C2H6/CH4 and CO2/CH4, C2H6 broke through the bed at 40 min, while it was 16 min for CO2, as both C2H6 and CO2 showed efficient adsorption over the weakly interacting CH4 (Fig. S43 and S44†). It is worth noting that all breakthrough time intervals were tested multiple times through subsequent regeneration by flowing helium gas and were comparable, thus, showing the excellent reusability of the material (Fig. 3b and d).
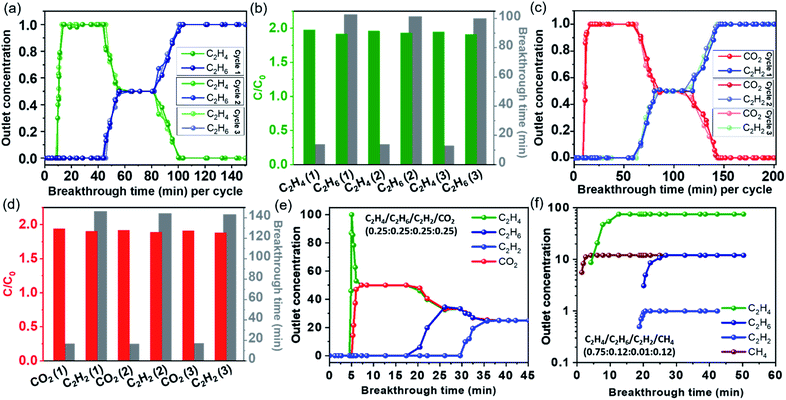 |
| Fig. 3 (a) Experimental stepwise dynamic column breakthrough curves for 0.5 : 0.5 (v/v) C2H6/C2H4 gas mixture and (b) the corresponding maximum release concentration (outlet/feed; C/C0) in the outlet of each component with time for three consecutive cycles. (c) Experimental stepwise dynamic column breakthrough curves for 0.5 : 0.5 (v/v) C2H2/CO2 gas mixture and (d) the corresponding maximum release concentration (outlet/feed; C/C0) in the outlet of each component with time for three consecutive cycles. Quaternary mixture separations of (e) C2H4/C2H6/C2H2/CO2 (0.25 : 0.25 : 0.25 : 0.25) and (f) C2H4/C2H6/C2H2/CH4 (0.75 : 0.12 : 0.01 : 0.12). The continuous flow was regulated by a mass flow controller using helium as the carrier gas with a total flow rate of 2.2–2.9 and 3.2–3.5 mL min−1 for binary and quaternary separations, respectively. The breakthrough experiments were studied in an adsorbed bed packed with ∼1.048 g of Al-MOFM15 at 298 K and 1.05 bar. The packed column dimensions are 16.5 cm in length and 0.3 cm in diameter. | |
The separation capacity of Al-MOFM15 was further tested using a quaternary C2H4/C2H6/C2H2/CO2 mixture. A sharp and pure separation of all four gases was observed with an early release of C2H4, with no evidence of CO2, C2H2, or C2H6 in the first 5 minutes (Fig. 3e). Such a flawless separation of C2H4 with a high purity only through a single breakthrough separation is rarely found in the literature. Moreover, the traditional C2H4 production also co-exists with other by-products, mainly C2H6 with trace amounts of CH4 and C2H2. So, this material was further investigated for the separation from a quaternary mixture of C2H4/C2H6/C2H2/CH4 by mimicking its available industrial concentration (0.75
:
0.12
:
0.01
:
0.12, v/v). As shown in Fig. 3f, C2H4 appeared just after CH4 within 5 minutes of gas flow, while highly efficient separation for even a trace amount (1%) of C2H2 was achieved by passing the mixture over a packed column of activated Al-MOFM15. All the practical separation measurements are consistent with the experimental and simulated adsorption isotherm, selectivity and binding interactions.
Conclusions
In conclusion, we have developed a robust Al-based metal–organic framework by optimising the reaction time under microwave heating to achieve exclusive microporosity with high surface area. The foregoing results showed that the material ([Al(OH)(1,4-NDC)]·2H2O) possesses not only extraordinary chemical and thermal stability but also exhibits exceptional sorption and selectivity performance of a tailor-made Al-MOF (Al-MOFM15). It unveiled remarkable preferential interactions for C2H6 and C2H2 over C2H4 and C2H2 over CO2, considered the most delicate combinations for separation in petroleum industries. The key to selectivity, as found, is a combination of multiple van der Waals interactions and suitable channel-like pores to match with different light hydrocarbons. At one end, single and mixed-gas adsorption, selectivity estimation, stepwise dynamic breakthrough separation from bi- and quaternary-component mixtures unfold extraordinary separation potency of such materials. On the other hand, the study also reveals the specific affinity of each hydrocarbon because of thermodynamic and kinetic predilections to the adsorbent as supported by binding energy estimation and molecular level visualisation through advanced molecular simulations.
Data availability
The data that support the findings of this study are available in the ESI of this article.†
Author contributions
TKM and SL designed the concept. SL and DR performed major experiments. ND and AS carried out the computational study under the guidance of SB. SL, ND, SB and TKM analysed the experimental and computational data and wrote the manuscript with inputs from all the co-authors.
Conflicts of interest
There are no conflicts to declare.
Acknowledgements
SL acknowledges DST-INSPIRE for the fellowship. ND thanks CSIR, India, for the fellowship. SB acknowledges the support and facility provided by ‘PARAM Yukti Faculty’ under the National Supercomputing Mission, Government of India, at the Jawaharlal Nehru Centre for Advanced Scientific Research, Bangalore, India. TKM is grateful to the Department of Science and Technology (DST, project no. CRG/2019/005951) for financial support.
Notes and references
- D. S. Sholl and R. P. Lively, Nature, 2016, 532, 435–437 CrossRef PubMed.
- K.-J. Chen, D. G. Madden, S. Mukherjee, T. Pham, K. A. Forrest, A. Kumar, B. Space, J. Kong, Q.-Y. Zhang and M. J. Zaworotko, Science, 2019, 366, 241 CrossRef CAS PubMed.
- N. A. Khan, Z. Hasan and S. H. Jhung, Chem.–Eur. J., 2014, 20, 376–380 CrossRef CAS PubMed.
- U. Wagner and H. M. Weitz, Ind. Eng. Chem., 1970, 62, 43–48 CrossRef CAS.
- R. Krishna, ACS Omega, 2020, 5, 16987–17004 CrossRef CAS PubMed.
- L. Yang, S. Qian, X. Wang, X. Cui, B. Chen and H. Xing, Chem. Soc. Rev., 2020, 49, 5359–5406 RSC.
- I. Amghizar, L. A. Vandewalle, K. M. Van Geem and G. B. Marin, Engineering, 2017, 3, 171–178 CrossRef CAS.
-
Handbook of Industrial Hydrocarbon Processes, ed. J. G. Speight, Gulf Professional Publishing, Boston, 2011, p. iii, DOI: DOI:10.1016/B978-0-7506-8632-7.10020-9.
- A. van Miltenburg, J. Gascon, W. Zhu, F. Kapteijn and J. A. Moulijn, Adsorption, 2008, 14, 309–321 CrossRef CAS.
- L. Li, R.-B. Lin, R. Krishna, H. Li, S. Xiang, H. Wu, J. Li, W. Zhou and B. Chen, Science, 2018, 362, 443 CrossRef CAS PubMed.
- Y. S. Ai-Zegbayer, S. I. Ai- Mayman and T. A. Ai-Smarei, J. King Saud Univ., Eng. Sci., 2010, 22, 21–27 CrossRef.
- B. Zhu, J.-W. Cao, S. Mukherjee, T. Pham, T. Zhang, T. Wang, X. Jiang, K. A. Forrest, M. J. Zaworotko and K.-J. Chen, J. Am. Chem. Soc., 2021, 143, 1485–1492 CrossRef CAS PubMed.
- Z. Bao, D. Xie, G. Chang, H. Wu, L. Li, W. Zhou, H. Wang, Z. Zhang, H. Xing, Q. Yang, M. J. Zaworotko, Q. Ren and B. Chen, J. Am. Chem. Soc., 2018, 140, 4596–4603 CrossRef CAS PubMed.
- T. Ren, M. Patel and K. Blok, Energy, 2006, 31, 425–451 CrossRef CAS.
- O. T. Qazvini, R. Babarao, Z.-L. Shi, Y.-B. Zhang and S. G. Telfer, J. Am. Chem. Soc., 2019, 141, 5014–5020 CrossRef CAS PubMed.
- H. Bux, C. Chmelik, R. Krishna and J. Caro, J. Membr. Sci., 2011, 369, 284–289 CrossRef CAS.
- J.-R. Li, R. J. Kuppler and H.-C. Zhou, Chem. Soc. Rev., 2009, 38, 1477–1504 RSC.
- J.-R. Li, J. Sculley and H.-C. Zhou, Chem. Rev., 2012, 112, 869–932 CrossRef CAS PubMed.
- A. Granada, S. B. Karra and S. M. Senkan, Ind. Eng. Chem. Res., 1987, 26, 1901–1905 CrossRef CAS.
-
D. A. Plattner, Y. Li and K. N. Houk, Modern Computational and Theoretical Aspects of Acetylene Chemistry, in Modern Acetylene Chemistry, ed. P. J. Stang and F. Diederich, 1995, DOI:10.1002/9783527615278.ch01.
- A. Hazra, S. Jana, S. Bonakala, S. Balasubramanian and T. K. Maji, Chem. Commun., 2017, 53, 4907–4910 RSC.
- S. Bhattacharyya, A. Chakraborty, A. Hazra and T. K. Maji, ACS Omega, 2018, 3, 2018–2026 CrossRef CAS PubMed.
- R. Matsuda, R. Kitaura, S. Kitagawa, Y. Kubota, R. V. Belosludov, T. C. Kobayashi, H. Sakamoto, T. Chiba, M. Takata, Y. Kawazoe and Y. Mita, Nature, 2005, 436, 238–241 CrossRef CAS PubMed.
- R. W. Baker, Ind. Eng. Chem. Res., 2002, 41, 1393–1411 CrossRef CAS.
- V. Guillerm, Ł. J. Weseliński, Y. Belmabkhout, A. J. Cairns, V. D'Elia, Ł. Wojtas, K. Adil and M. Eddaoudi, Nat. Chem., 2014, 6, 673–680 CrossRef CAS PubMed.
- B. R. Barnett, S. T. Parker, M. V. Paley, M. I. Gonzalez, N. Biggins, J. Oktawiec and J. R. Long, J. Am. Chem. Soc., 2019, 141, 18325–18333 CrossRef CAS PubMed.
- R.-B. Lin, L. Li, H.-L. Zhou, H. Wu, C. He, S. Li, R. Krishna, J. Li, W. Zhou and B. Chen, Nat. Mater., 2018, 17, 1128–1133 CrossRef CAS PubMed.
- S. Laha, R. Haldar, N. Dwarkanath, S. Bonakala, A. Sharma, A. Hazra, S. Balasubramanian and T. K. Maji, Angew. Chem., Int. Ed., 2021, 60, 19921–19927 CrossRef CAS PubMed.
- R. Haldar, N. Sikdar and T. K. Maji, Mater. Today, 2015, 18, 97–116 CrossRef CAS.
- D. Bloch Eric, L. Queen Wendy, R. Krishna, M. Zadrozny Joseph, M. Brown Craig and R. Long Jeffrey, Science, 2012, 335, 1606–1610 CrossRef CAS PubMed.
- S. Yang, A. J. Ramirez-Cuesta, R. Newby, V. Garcia-Sakai, P. Manuel, S. K. Callear, S. I. Campbell, C. C. Tang and M. Schröder, Nat. Chem., 2015, 7, 121–129 CrossRef CAS PubMed.
- J. W. Yoon, Y.-K. Seo, Y. K. Hwang, J.-S. Chang, H. Leclerc, S. Wuttke, P. Bazin, A. Vimont, M. Daturi, E. Bloch, P. L. Llewellyn, C. Serre, P. Horcajada, J.-M. Grenèche, A. E. Rodrigues and G. Férey, Angew. Chem., Int. Ed., 2010, 49, 5949–5952 CrossRef CAS PubMed.
- J. E. Bachman, M. T. Kapelewski, D. A. Reed, M. I. Gonzalez and J. R. Long, J. Am. Chem. Soc., 2017, 139, 15363–15370 CrossRef CAS PubMed.
- L. Li, R.-B. Lin, R. Krishna, H. Li, S. Xiang, H. Wu, J. Li, W. Zhou and B. Chen, Science, 2018, 362, 443–446 CrossRef CAS PubMed.
- D.-L. Chen, N. Wang, C. Xu, G. Tu, W. Zhu and R. Krishna, Microporous Mesoporous Mater., 2015, 208, 55–65 CrossRef CAS.
- Y. Chen, Z. Qiao, H. Wu, D. Lv, R. Shi, Q. Xia, J. Zhou and Z. Li, Chem. Eng. Sci., 2018, 175, 110–117 CrossRef CAS.
- Y. Chen, H. Wu, D. Lv, R. Shi, Y. Chen, Q. Xia and Z. Li, Ind. Eng. Chem. Res., 2018, 57, 4063–4069 CrossRef CAS.
- W. Liang, F. Xu, X. Zhou, J. Xiao, Q. Xia, Y. Li and Z. Li, Chem. Eng. Sci., 2016, 148, 275–281 CrossRef CAS.
- P.-Q. Liao, W.-X. Zhang, J.-P. Zhang and X.-M. Chen, Nat. Commun., 2015, 6, 8697 CrossRef PubMed.
- H.-G. Hao, Y.-F. Zhao, D.-M. Chen, J.-M. Yu, K. Tan, S. Ma, Y. Chabal, Z.-M. Zhang, J.-M. Dou, Z.-H. Xiao, G. Day, H.-C. Zhou and T.-B. Lu, Angew. Chem., Int. Ed., 2018, 57, 16067–16071 CrossRef CAS PubMed.
- K.-J. Chen, G. Madden David, S. Mukherjee, T. Pham, A. Forrest Katherine, A. Kumar, B. Space, J. Kong, Q.-Y. Zhang and J. Zaworotko Michael, Science, 2019, 366, 241–246 CrossRef CAS PubMed.
- Z. Xu, X. Xiong, J. Xiong, R. Krishna, L. Li, Y. Fan, F. Luo and B. Chen, Nat. Commun., 2020, 11, 3163 CrossRef CAS PubMed.
- A. Comotti, S. Bracco, P. Sozzani, S. Horike, R. Matsuda, J. Chen, M. Takata, Y. Kubota and S. Kitagawa, J. Am. Chem. Soc., 2008, 130, 13664–13672 CrossRef CAS PubMed.
- S. Głowniak, B. Szczęśniak, J. Choma and M. Jaroniec, Adv. Mater., 2021, 33, 2103477 CrossRef PubMed.
- S. Laha, D. Rambabu, S. Bhattacharyya and T. K. Maji, Chem.–Eur. J., 2020, 26, 14671–14678 CrossRef CAS PubMed.
- S. Laha, A. Chakraborty and T. K. Maji, Inorg. Chem., 2020, 59, 3775–3782 CrossRef CAS PubMed.
- C. Gücüyener, J. van den Bergh, J. Gascon and F. Kapteijn, J. Am. Chem. Soc., 2010, 132, 17704–17706 CrossRef PubMed.
- X. Zhang, J.-X. Wang, L. Li, J. Pei, R. Krishna, H. Wu, W. Zhou, G. Qian, B. Chen and B. Li, Angew. Chem., Int. Ed., 2021, 60, 10304–10310 CrossRef CAS PubMed.
- M. Sarker, H. J. An, D. K. Yoo and S. H. Jhung, Chem. Eng. J., 2018, 338, 107–116 CrossRef CAS.
- E. V. Alexandrov, A. V. Goltsev, R. A. Eremin and V. A. Blatov, J. Phys. Chem. C, 2019, 123, 24651–24658 CrossRef CAS.
- X. Liu, X. Wang and F. Kapteijn, Chem. Rev., 2020, 120, 8303–8377 CrossRef CAS PubMed.
- Y. Hu, Y. Chen, Y. Liu, W. Li, M. Zhu, P. Hu, H. Jin and Y. Li, Microporous Mesoporous Mater., 2018, 270, 67–74 CrossRef CAS.
- A. Nuhnen and C. Janiak, Dalton Trans., 2020, 49, 10295–10307 RSC.
- B. Li, Y. Zhang, R. Krishna, K. Yao, Y. Han, Z. Wu, D. Ma, Z. Shi, T. Pham, B. Space, J. Liu, P. K. Thallapally, J. Liu, M. Chrzanowski and S. Ma, J. Am. Chem. Soc., 2014, 136, 8654–8660 CrossRef CAS PubMed.
- J. Pires, M. L. Pinto and V. K. Saini, ACS Appl. Mater. Interfaces, 2014, 6, 12093–12099 CrossRef CAS PubMed.
- A. L. Myers and J. M. Prausnitz, AIChE J., 1965, 11, 121–127 CrossRef CAS.
- D. Ma, Z. Li, J. Zhu, Y. Zhou, L. Chen, X. Mai, M. Liufu, Y. Wu and Y. Li, J. Mater. Chem. A, 2020, 8, 11933–11937 RSC.
- W. Gong, H. Cui, Y. Xie, Y. Li, X. Tang, Y. Liu, Y. Cui and B. Chen, J. Am. Chem. Soc., 2021, 143, 14869–14876 CrossRef CAS PubMed.
- T.-L. Hu, H. Wang, B. Li, R. Krishna, H. Wu, W. Zhou, Y. Zhao, Y. Han, X. Wang, W. Zhu, Z. Yao, S. Xiang and B. Chen, Nat. Commun., 2015, 6, 7328 CrossRef CAS PubMed.
- H. Yang, Y. Wang, R. Krishna, X. Jia, Y. Wang, A. N. Hong, C. Dang, H. E. Castillo, X. Bu and P. Feng, J. Am. Chem. Soc., 2020, 142, 2222–2227 CrossRef CAS PubMed.
- R.-B. Lin, H. Wu, L. Li, X.-L. Tang, Z. Li, J. Gao, H. Cui, W. Zhou and B. Chen, J. Am. Chem. Soc., 2018, 140, 12940–12946 CrossRef CAS PubMed.
|
This journal is © The Royal Society of Chemistry 2022 |