DOI:
10.1039/C7CE00517B
(Communication)
CrystEngComm, 2017,
19, 2830-2835
Inadvertent liquid assisted grinding: a key to “dry” organic mechano-co-crystallisation?
Received
16th March 2017
, Accepted 3rd May 2017
First published on 3rd May 2017
Abstract
Mechanical treatment of dry powder mixtures has often been reported to give new compounds. The assumption of neat mechanochemical conditions must, however, be made with caution even if the reactants are not crystal hydrates. The fluidised intermediate, which is often necessary for mechano-co-crystallisation of organic molecules, can readily form by interaction with atmospheric moisture. We illustrate this using “dry” mechanochemical synthesis of glycinium semi-malonate as an example. The α-glycine and malonic acid mixture is shown to be highly hygroscopic, which can be largely accredited to the hygroscopicity of malonic acid. Dissolution in atmospheric moisture is sufficient for the spontaneous crystallisation of the salt product. This is a prime example where liquid is both necessary for mechanosynthesis, while simultaneously hindering the reaction by affecting the rheology of the mixture: Liquid Hindered Grinding. These results shed new light on possible sources of regional, seasonal and temperature effects on mechanosynthesis, as well as a potential role for polymer additives.
Introduction
Elucidating the mechanisms through which solids are able to react has been at the forefront of solid state chemical research for many years.1–4 Mechanisms of reactions induced by mechanical action (mechanochemical reactions) are especially intriguing. To date, mechanochemistry of organic materials has found application in multi-component co-crystallisation,5–7 synthesis,8–16 and processing of biological materials,17,18 and has led to the discovery of numerous materials inaccessible through conventional solution-based approaches. With the expanding academic and industrial interest in organic mechanochemistry,5–21 the need to understand multi-phase reactions of molecular crystalline powders is of growing importance.
Models for multi-phase reactions in powders have been developed for inorganic reactions.2,22–24 Their applicability to molecular crystals remains uncertain. This uncertainty stems from the fact that these models are built on the diffusion of reacting species from one lattice into another, or in both directions. This process is greatly limited in molecular lattices, when whole molecules (as opposed to ions) must diffuse through a foreign structure. The situation is somewhat easier if the product is a host–guest compound, where one component can easily intercalate into the structure of another component. This has led to the development of models regarding organic mechano-cocrystallisation that invoke the need for some form of fluidized intermediate state.25–35 This state can be a solution, when true liquid is added to the reacting mixture on purpose – liquid assisted grinding (LAG) – or is released on dehydration of a solid reactant, taken as a crystal hydrate.36,37 When the grinding is performed dry, the formation of a fluidized state is often taken as being related to the formation of an amorphous intermediate, or eutectic melting. Examples when organic co-crystallisation occurs via gas-phase diffusion due to sublimation of one or several solid components are also known.8,30,34
Still, some reactions have been documented to occur on co-grinding of solid powders, where none of the components is a crystal hydrate and sublimation and eutectic melting are not feasible. The present work investigates one such reaction in detail, seeking to elucidate the potential existence, nature and role of a fluid phase intermediate.
Co-grinding of α-glycine (αGly) and β-malonic acid (Mal) has been selected as a model reaction for this study. It is known32,36,38 that co-grinding of a dry mixture of these two compounds gives a stoichiometric salt, glycinium semi-malonate (GSM), Fig. 1. Its rheology was observed to be particularly intriguing, requiring further investigation. On grinding, the system goes through a sequence of states with different rheological properties, starting from friable powder, passing through a viscous fluidized phase/paste, finally ending as a caked pellet. Caking of free-flowing powders during storage is a well-known deleterious phenomenon that is ubiquitous in the food, fertilizer and pharmaceutical industries. Caking is related to humidity,39–46 therefore in this study we focused on the possible interaction of the reactant mixture with atmospheric water and its possible role in the mechanochemical transformation.
 |
| Fig. 1 Reaction scheme for the mechano-cocrystallisation of αGly + Mal to form glycinium semi-malonate. | |
Experimental
Materials
Samples of α-glycine (ICN Biomedicals) and β-malonic acid (Sigma-Aldrich) were used as supplied, without further purification. Polyvinylpyrrolidone (PVP; Sigma-Aldrich) was used as supplied.
Hygroscopicity measurements
The samples were stored in 5 litre glass desiccators, quarter-filled with distilled water and aqueous solutions of inorganic salts of KCl, NaCl and NH4NO3. At 25 °C, these desiccators correspondingly adopted relative humidities of 100%, 85%, 75%, and 65%, respectively. The amount of sorbed water was measured with Ohaus precision scales. Humidity was monitored using a TFH 620 Ebro hygrometer with an extendable probe. Samples were removed from desiccators for weighting, and immediately returned. The average time of each sample spent in ambient atmosphere was no longer than 30 seconds, across which time no measureable change in mass was observed.
Thermal gravimetric analysis
TGA of hydrated samples was performed on a NETZSCH STA 449 F1 Jupiter instrument equipped with a mass-spectrometer. Samples were heated and subsequently cooled at a rate of 2 K min−1.
Mechanical treatment
Ball milling was performed in a Retsch cryo-mill. Milling jars (Retsch) with internal diameter 12 mm and internal length 44.6 mm (volume 5 mL) were used. All jars are commercially available stainless steel vessels, with screw closure (Teflon seal washers). A single milling ball (stainless steel, 0.7 g, 5.6 mm diameter) was used, and milling was performed at 24 Hz. Cryo-milling was performed at 77 K under a stream of liquid N2, using the same ball mill as for ambient temperature experiments. All grinding experiments were performed for 20 minutes at 24 Hz. A total of 0.5 g stoichiometric mixture was used in each.
Characterisation
All solid samples were characterised by X-ray powder diffraction (XRPD) using a STOE-MP diffractometer. The diffractometer was equipped with a Cu anode (Kα1 1.54056 Å) and a bent Ge(111) monochromator. XRPD patterns were collected in steps of 0.195°, with collection time 5 s per step.
Hot stage microscopy
Hot stage microscopy experiments were performed on a custom-built thermal stage with inbuilt thermal couple. The heat stage was mounted on a Nikon AZ100 microscope with an attached digital camera.
Results and discussion
As with many mechano-co-crystallisations, neat mechanical treatment of α-glycine (αGly) and β-malonic acid (Mal) leads to formation of a multi-component crystal. Here, a 1
:
1 salt, glycinium semi-malonate (GSM) is produced.32 In all mechanochemical experiments conducted on this system, the resulting powder was slightly wet, which suggested the presence of a fluid phase. No liquid was explicitly added to the mixture, nor were any of the reacting components hydrates or solvates. As such, two possible origins of a truly fluid intermediate can be suggested: contact melting or sorption of atmospheric moisture.
Hygroscopicity of the reacting system
The hygroscopicity of αGly and Mal, along with their mixture and reaction product (GSM), was studied at 100% relative humidity (RH). When stored under these conditions, the mass of powdered αGly was found to increase by 45%, reaching a maximum mass after 24 hours. This is consistent with an uptake of 1.9 mmol of water for 1 mmol of αGly. Interestingly, the same study with γ-glycine (γGly) showed considerably smaller quantities of water being sorbed (1 mmol of water for 1 mmol of γGly). This difference may suggest a rationale for the unique mechanochemical reactivity of the two Gly polymorphs, where grinding of different Gly polymorphs with oxalic acid dihydrate led to different co-crystal polymorphs.47 In contrast, the hygroscopicity of Mal was shown to be drastically higher than for either Gly polymorph. After storage at 100% RH for 24 h, a total uptake of 25.1 mmol water was found, corresponding to 5 mmol of Mal: a 5
:
1 ratio. At this stage the Mal sample was found to have completely dissolved due to sorption of atmospheric moisture at 100% RH. When subsequently left in ambient atmospheric conditions (ca. 50% RH), excess water evaporated and the resulting sample was highly viscous Mal. Stoichiometric mixtures of the reactants were subsequently investigated at 100% RH and room temperature (25 °C). Mass uptake under these conditions was seen to reach 3.2 mmol in the mixture containing 1 mmol αGly and 1 mmol Mal. This is consistent with a ca. 3
:
1 molar ratio of water to each reacting component. Interestingly, this is considerably less uptake than would be assumed for a sum of the individual components, and may suggest that particle–particle and particle–solution contacts result in reduced hygroscopicity of each component, possibly through coating with the co-crystal product. At its maximum wetness, the sample was found to consist of a mainly Mal solution, in which αGly particles were dispersed, Fig. 2, verified by the crystal habit and diffraction patterns of remaining particles. On drying, XRPD analysis of the mixture indicated that GSM was present as a nearly X-ray pure phase, Fig. 3. One can therefore suggest a rather straightforward mechanism to the mechanosynthesis of GSM based on the dissolution of reactant compounds.
 |
| Fig. 2 Mixture of αGly and Mal at high levels of relative humidity. Liquid solution of Mal (red circles) with remaining solid powder of αGly (blue rectangles). | |
 |
| Fig. 3 XRPD pattern of the Gly + Mal mixture following “dissolution” at 100% RH, and recrystallising under ambient atmosphere (ca. 20% RH). The experimental XRPD (black) is shown alongside the simulated patterns for GSM (red), αGly (blue) and Mal (pink). | |
In mechanochemical terminology, any “dry” mechanochemical processes performed in a location of elevated humidity will inadvertently be a liquid assisted grinding (LAG) reaction, with η ≈ 0.1 in the present example, in line with typical LAG experiments.48
Atmospheric conditions
All experiments described above were conducted at higher RH levels than might be expected in a typical neat mechanochemical process. Analysis of the hygroscopicity profiles at lower RH (65%, 75%, 85%) are therefore of interest. At 85% RH notable sorption of atmospheric water is still observed in both Mal and Mal + αGly samples. Interestingly, however, at 65% and 75% RH the mass of the mixture is observed to first increase, and subsequently decrease. At low levels of humidity, sufficient moisture is observed only to create a highly viscous layer on the surface of reactant particles, appearing even under ambient conditions (Fig. 4). This highly viscous layer dissolves a small amount of αGly, and the product phase crystallises at the surface. GSM does not display hygroscopic properties at less than 90% RH (Fig. 5) and thus, with all Mal particles coated, the sorbed water is released. At higher humidities, this layer becomes increasingly fluid, and does not remain restricted to the Mal surface; thus on dissolution, internal layers of the particles are exposed. The situation in a mechanoreactor can be considered as a combination of the two processes. The low RH in a typical laboratory can trigger the coating of reactant particles by product, which is subsequently removed by mechanical action. The refreshed surfaces can then interact with the atmospheric moisture and the process continues.
 |
| Fig. 4 Photos of αGly and Mal powder mix at ambient (60%) RH. Formation of a fluid layer at the contact point between particles of αGly and Mal is shown by a circle. | |
 |
| Fig. 5 Water sorption of Gly + Mal mixture and GSM at various RH levels. ▲ – Gly + Mal RH 85%, ● – Gly + Mal RH 75%, ■ – Gly + Mal RH 65%, ◀, ♦, ▼ – GSM at RH 85%, 75%, 65%, respectively. | |
Thermal analysis of a stoichiometric mixture exposed to the open atmosphere for 2 hours displays two endothermic events (Fig. 6). Mass loss begins immediately on heating, corresponding to the loss of sorbed water. There is no significant change in the gradient of mass loss associated with the first endotherm (85–95 °C), which can therefore be interpreted as fluidisation of the glycine–malonic acid–water complex, confirmed by hot stage microscopy (Fig. 7).
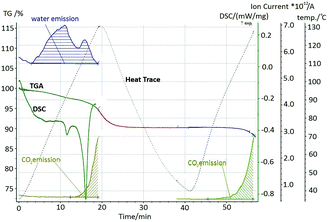 |
| Fig. 6 Combined TGA and DSC analysis of αGly + Mal mixture after 2 hours at room level of RH (60%). The DSC and TGA traces are shown, as labelled, alongside inset mass spectrometry analysis (CO2 and water emission; ion current) for the mass loss at each stage of heating. The heat trace (dotted line) is shown as an overlay. The initial stage shows two endothermic peaks and mass loss, water and CO2 emission, second stage shows only CO2 emission. | |
 |
| Fig. 7 Hot stage microscopy of 1 : 1 mixture of Mal + αGly at (left) room temperature and (right) ca. 80 °C. | |
Emission of carbon dioxide is associated with the second endotherm from 113 °C. This is consistent with decomposition of reactant compounds in the fluidised sample. The sample was cooled down and subsequent TGA revealed no water loss. Further, no melting was observed for this material up to 120 °C, and XRPD of an externally melted sample revealed the resulting solid to be GSM. Thus, on formation of GSM on time scales associated with mechanochemistry, GSM does not contain sorbed atmospheric water. We therefore find that an initial mixture of αGly + Mal, held under ambient conditions, is in fact a ternary system, Gly–Mal–H2O, which undergoes a thermally-induced reaction to form GSM. More precisely, this is likely a quaternary system of glycine–malonic acid–H2O–GSM, with only minute quantities of GSM existing at the particle contacts. The amount of water sorbed can be approximated as 30 mole%, taken as the mass loss up to the decomposition point. The GSM is not hygroscopic, and thus no water is released on subsequent heating.
We can suggest that mechanical treatment of the mixture of αGly + Mal results in a sequence of processes. First, malonic acid sorbs water from the air and forms a highly oversaturated viscous solution: a syrup. Gly subsequently dissolves in this oversaturated syrup of Mal. The solubility and hygroscopicity of GSM is lower than that of the Mal, and thus it precipitates. This releases water, which is firmly bound in the viscous syrup-like fluid, resembling hydrated cement. The crystallisation of the viscous fluid is difficult because it contains different components. The syrup therefore becomes easily oversaturated and is possibly structured. The released water dissolves more malonic acid, which again reacts with glycine to give the less soluble salt precipitate. This three-stage cycle repeats many times, so that a small amount of water enables a large amount of salt to be formed from the two starting powder components.
The results of hygroscopicity studies and TGA analysis are consistent with the model schematically presented in Fig. 8, where low RH permits reactivity at the particle–particle contacts.
 |
| Fig. 8 Model of stepwise interactions in αGly + Mal + H2O system. Water is first sorbed by Mal, fluidising its surface. Subsequent fluidisation of the αGly surface follows, and recrystallisation of GSM ensues. | |
“Dry” mechanochemistry: is atmospheric moisture the key?
It is evident that the neat mechanochemistry of αGly and Mal is unlikely to be as dry as previously believed. To further investigate the role of this atmospheric moisture in the direct mechanochemical process, milling was performed under two additional conditions: in the presence of a highly hygroscopic polymer additive (polyvinylpyrrolidone, PVP), and under a dry atmosphere.
The addition of PVP to the reaction mixture had a marked effect on both the rheology and reactivity of the sample. Unlike mixtures of αGly + Mal, the mixtures of αGly + Mal + PVP did not cake under mechanical treatment. Instead, the powder remained free flowing throughout. However, despite the flowability of the powder, no GSM product was found to be produced. This is a common occurrence of where liquid is both required for the reaction, but inhibits mixing and completion of a reaction: liquid hindered grinding (LHG).
To conduct “truly dry” mechano-cocrystallisation, dry particles were loaded into the reaction vessel under a dry atmosphere (<5% RH). The samples were milled for 20 minutes and compared to the same sample, loaded in open atmosphere (ca. 50% RH), Fig. 9.
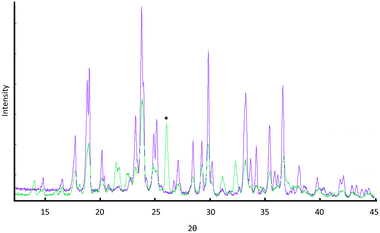 |
| Fig. 9 Powder patterns for 1 : 1 mixtures of Gly : Mal loaded in ambient (green) atmosphere and dry (purple) atmosphere. The peak at 26° (marked with *) is unique to the salt product, GSM, and it is clear that this product is formed only in the presence of a moist atmosphere. | |
The cryo-grinding of αGly + Mal was also observed to reduce the reactivity of the system. While one may immediately interpret these results as indicative of a thermally-induced reaction between the two components, the above evidence from ball milling in the presence of PVP suggests an alternative interpretation. On cooling to 77 K, any liquid water in the system solidifies and is thus no longer available to fluidise the Mal surfaces. We therefore suggest that the immediate association of cryo-grinding results with thermal mechanisms may lead to erroneous interpretation of mechanochemical processes.
General discussion
The neat mechano-cocrystallisation of αGly + Mal is in fact not dry at all. Instead, this reaction is an example of inadvertent liquid assisted grinding, and is surely not an isolated example in organic mechanochemistry. Elucidating the role of atmospheric moisture in mechanochemistry allows interpretation of mechanisms of LAG, which in many cases must act the same. That is, in most cases the liquid most likely fluidises the surface of reactant particles. Either the product displays considerably lower affinity for this liquid (as in the current example) and expels the liquid for use in further reaction, or the evaporation of the liquid leads to crystallisation of the product phase. We note that this must be distinctly different than processes which involve solvate molecules, where the existence of these solvent molecules is in insufficient quantity to act as solvent. In such cases the addition of hygroscopic media does not inhibit reactivity.34
In the current literature, it is often assumed that the intermediate state of dry grinding is necessarily an amorphous solid material. However, this may not always be the case. The “fluidised phase” is needed in order to enable mixing of components at the molecular level. However, this “fluidised state” need not be an amorphous solid, but may be a liquid crystal, a micellar liquid, a viscous supersaturated solution (syrup), or any other mobile phase.34 If present in sufficient quantity, these states may manifest themselves as amorphous humps in diffraction patterns, or may be responsible for the apparent loss of crystalline phases observed in milling experiments. A common mechanism associated with forming a “fluidised state” is local melting, which may occur on sufficiently small scale (at contacts, or “hot spots”) to be undetectable by real-time analysis on the macroscopic scale.37,49,50 The maximum temperature achievable at these contacts is dictated by the lowest melting temperature of the materials, and heat dissipation can be very rapid, particularly for low melting temperature organic materials.49 However, this is not the only possible process as the present study has shown.
The mechanochemical reaction studied in the present contribution appears to require atmospheric moisture as a mediator. In this way the reaction is observed on time scales typical of mechanochemical studies. It remains possible that such mechanochemical systems could be driven to completion in the absence of external moisture, given sufficient time and a different intermediate fluidised state. The study of reaction kinetics and equilibria for mechanochemical systems therefore requires considerably more detailed exploration of these phenomena. It is very possible that many mechanochemical studies are susceptible to this problem, where atmospheric moisture may inadvertently accelerate reactions.
Conclusions
Organic crystals are commonly hygroscopic, and the presence of moisture in a mechanochemical system cannot be neglected, although it often is. The mechano-cocrystallisation of αGly + Mal is driven by atmospheric moisture, which is present due to the high hygroscopicity of Mal. Atmospheric moisture is present in sufficient quantities, even at ambient relative humidities (ca. 60%), so as to permit this mechano-cocrystallisation. Removal of moisture through the addition of hygroscopic polymer (PVP) or by conducting the reaction under dry N2 atmosphere inhibits product formation, although it ensures the powder does not cake and remains free-flowing. This is a prime example of a system in which liquid is both required for the reaction, but simultaneously inhibits the reaction by inadvertently affecting the rheology: liquid hindered grinding (LHG). This is surely not an isolated example of organic mechano-cocrystallisation that is dependent on atmospheric moisture. It is imperative that detailed studies of mechanochemical processes account for atmospheric conditions, as it is clear that regional and seasonal variation in environmental conditions will have considerable influence on all “solid-state” reactions. In addition, complementary water vapor sorption measurements for reactants and products of co-grinding transformations must be carried out.
Acknowledgements
The authors thank RFBR grant 16-33-60086 (IT), project 1828 from the Russian Ministry of Education and Science (AM), an Edinburgh Global Research Scholarship (AM), EPSRC EP/I033459/1 (EPSRC CMAC) (AM), project 0301-2016-0014 from Siberian Branch of Russian Academy of Sciences (AP, EB, VB) for financial support. AM thanks Prof. CR Pulham for on-going support. We thank Dr. K. B. Gerasimov for performing TGA measurements.
Notes and references
-
Reactions in the Solid State, ed. M. Brown, D. Dollimore and A. K. Galwey, Elsevier, 1980 Search PubMed.
-
H. Schmalzried, Solid State Reactions, Chemie, Verlag, Weinheim, 1981 Search PubMed.
-
Reactivity of Molecular Solids, ed. E. V. Boldyreva and V. V. Boldyrev, Wiley & Sons, Ltd., 1999 Search PubMed.
- P. Naumov, S. Chizhik, M. K. Panda, N. K. Nath and E. Boldyreva, Chem. Rev., 2015, 115, 12440–12490 CrossRef CAS PubMed.
- A. V. Trask, D. A. Haynes, W. D. S. Motherwell and W. Jones, Chem. Commun., 2006, 51–53 RSC.
- D. R. Weyna, T. Shattock, P. Vishweshwar and M. J. Zaworotko, Cryst. Growth Des., 2009, 9, 1106–1123 CAS.
- D. Braga, L. Maini and F. Grepioni, Chem. Soc. Rev., 2013, 42, 7638–7648 RSC.
- M. A. Mikhailenko, T. P. Shakhtshneider and V. V. Boldyrev, J. Mater. Sci., 2004, 39, 5435–5439 CrossRef CAS.
- G. Kaupp, CrystEngComm, 2009, 11, 388–403 RSC.
- A. M. Belenguer, T. Friščić, G. M. Day and J. K. M. Sanders, Chem. Sci., 2011, 2, 696–700 RSC.
- S. L. James, C. J. Adams, C. Bolm, D. Braga, P. Collier, T. Friščić, F. Grepioni, K. D. M. Harris, G. Hyett, W. Jones, A. Krebs, J. Mack, L. Maini, A. G. Orpen, I. P. Parkin, W. C. Shearouse, J. W. Steed and D. C. Waddell, Chem. Soc. Rev., 2012, 41, 413–447 RSC.
- O. H. Qareaghaj, S. Mashkouri, M. R. Naimi-Jamal and G. Kaupp, RSC Adv., 2014, 4, 48191–48201 RSC.
- T. X. Metro, J. Bonnamour, T. Reidon, A. Duprez, J. Sarpoulet, J. Martinez and F. Lamaty, Chem. – Eur. J., 2015, 21, 12787–12796 CrossRef CAS PubMed.
- V. Porte, M. Thioloy, T. Pigoux, T. X. Metro, J. Martinez and F. Lamaty, Eur. J. Org. Chem., 2016, 21, 3505–3508 CrossRef.
- D. Tan, L. Loots and T. Friščić, Chem. Commun., 2016, 52, 7760–7781 RSC.
- D. Tan and T. Friščić, Chem. Commun., 2017, 53, 901–904 RSC.
- I. O. Lomovskii and A. A. Politov, Chem. Nat. Compd., 2014, 50, 247–250 CrossRef CAS.
- A. Politov and O. Golyazimova, Faraday Discuss., 2014, 170, 345–356 RSC.
- D. Braga and F. Grepioni, Angew. Chem., Int. Ed., 2004, 43, 4002–4011 CrossRef CAS PubMed.
- Y. X. Shi, K. Xu, J. K. Clegg, R. Ganguly, H. Hirao, T. Friščić and F. García, Angew. Chem., Int. Ed., 2016, 55, 12736–12740 CrossRef CAS PubMed.
- H. Kulla, S. Greiser, S. Benemann, K. Rademann and F. Emmerling, Cryst. Growth Des., 2017, 17, 1190–1196 CAS.
- Models of reactions in powder mixtures, In: Heterogeneous chemical reactions, ed. I. F. Kononyuk, Nauka & Technika, Minsk, 1975 Search PubMed.
- S. S. Tamhankar and L. K. Doraiswamy, AIChE J., 1979, 25, 561–582 CrossRef CAS.
- S. V. Kornienko and A. M. Gusak, J. Eng.
Phys. Thermophys., 1994, 66, 275–278 CrossRef.
- A. Jayasankar, A. Somwangthanaroj, Z. J. Shao and N. Rodríguez-Hornedo, Pharm. Res., 2006, 23, 2381–2392 CrossRef CAS PubMed.
- K. L. Nguyen, T. Friscić, G. M. Day, L. F. Gladden and W. Jones, Nat. Mater., 2007, 6, 206–209 CrossRef CAS PubMed.
- J. F. Willart and M. Descamps, Mol. Pharmaceutics, 2008, 5, 905–920 CrossRef CAS PubMed.
- T. Friscic and W. Jones, Cryst. Growth Des., 2009, 9, 1621–1637 CAS.
- O. Dolotko, J. W. Wiench, K. W. Dennis, V. K. Pecharsky and V. P. Balema, New J. Chem., 2010, 34, 25 RSC.
- E. Boldyreva, Chem. Soc. Rev., 2013, 42, 7719–7738 RSC.
- G. A. Bowmaker, Chem. Commun., 2013, 49, 334–348 RSC.
- A. A. L. Michalchuk, I. A. Tumanov, V. A. Drebushchak and E. V. Boldyreva, Faraday Discuss., 2014, 170, 311–335 RSC.
- E. A. Losev and E. V. Boldyreva, CrystEngComm, 2014, 16, 3857 RSC.
- E. V. Boldyreva, Curr. Pharm. Des., 2016, 22, 1–20 CrossRef.
- S. Y. Lin, Curr. Pharm. Des., 2016, 22, 5001 CrossRef CAS PubMed.
- I. A. Tumanov, A. F. Achkasov, E. V. Boldyreva and V. V. Boldyrev, CrystEngComm, 2011, 13, 2213 RSC.
- K. Užarević, V. Štrukil, C. Mottillo, P. A. Julien, A. Puškarić, T. Friščić and I. Halasz, Cryst. Growth Des., 2016, 16, 2342–2347 Search PubMed.
- A. A. L. Michalchuk, I. A. Tumanov and E. V. Boldyreva, CrystEngComm, 2013, 15, 6403 RSC.
- J. M. Aguilera, J. M. del Valle and M. Karel, Trends Food Sci. Technol., 1995, 6, 149–155 CrossRef CAS.
- A. G. Tereshchenko, J. Pharm. Sci., 2015, 104, 3639–3652 CrossRef CAS PubMed.
- M. Dupas-Langlet, M. Benali, I. Pezron, K. Saleh and L. Metlas-Komunjer, Powder Technol., 2015, 270, 502–509 CrossRef CAS.
- K. Brockbank, B. Armstrong, Y. Chandorkar and T. Freeman, Part. Sci. Technol., 2014, 33, 102–108 CrossRef.
- T. Freeman, K. Brockbank and B. Armstrong, Procedia Eng., 2015, 102, 35–44 CrossRef.
- T. Freeman, K. Brockbank and B. Armstrong, Curr. Pharm. Des., 2017, 23, 5766–5788 Search PubMed.
- M. Carpin, H. Bertelsen, J. K. Bech, R. Jeantet, J. Risbo and P. Schuck, Trends Food Sci. Technol., 2016, 53, 1–12 CrossRef CAS.
- Q. Chen, U. Zafar, M. Ghadiri and J. Bi, Int. J. Pharm., 2017, 521, 61–68 CrossRef CAS PubMed.
- E. A. Losev, M. A. Mikhailenko, A. F. Achkasov and E. V. Boldyreva, New J. Chem., 2013, 37, 1973–1981 RSC.
- V. Štrukil, M. D. Igrc, M. Eckert-Maksić and T. Friščić, Chem. – Eur. J., 2012, 18, 8464–8473 CrossRef PubMed.
-
G. Heinicke, Tribochemistry, Akademic-Verlag, Berlin, GDR, 1985, vol. 18 Search PubMed.
- H. Kulla, M. Wilke, F. Fischer, M. Röllig, C. Maierhofer and F. Emmerling, Chem. Commun., 2017, 53, 1664–1667 RSC.
|
This journal is © The Royal Society of Chemistry 2017 |
Click here to see how this site uses Cookies. View our privacy policy here.