DOI:
10.1039/C5RA14824C
(Paper)
RSC Adv., 2015,
5, 74907-74915
Facile and surfactant-free synthesis of supported Pd nanoparticles on hydrotalcite for oxidation of benzyl alcohol
Received
26th July 2015
, Accepted 26th August 2015
First published on 26th August 2015
Abstract
We report a facile modified deposition–precipitation method that permits reproducible preparation of a supported Pd catalyst with small particle size and narrow size distribution but without the protection of a surfactant and any additional treatment. The pH value in this technique plays a key role in controlling the size of the Pd nanoparticles as well as the electronic environment of the surface Pd atoms. With the increasing pH (4.0–12.0), the average size of the Pd nanoparticles decreases gradually, meanwhile, the peak area ratio for CO adsorbed on bridge-bonded Pd to that adsorbed on threefold-coordinate Pd increases. Stronger support–metal interaction (electron transfer from Pd0 to support) is observed at pH values of 7.0 and 10.0. Both the small particle size and the electron-deficient surface metallic Pd contribute to enhancement in the activity for the solvent-free oxidation of benzyl alcohol. Therefore, compared with supported Pd catalysts prepared by sol immobilization, impregnation and deposition–precipitation methods, Pd/hydrotalcite synthesized by this modified deposition–precipitation approach shows a higher TOF value (5330 h−1). This enhanced catalytic performance can also be maintained in five cycles. Under the considerations of green chemistry, a number of Pd catalysts were then prepared on alternative supports using this method without the addition of alkali in the preparation process.
1. Introduction
Supported Pd nanoparticles have been found to be effective for a number of applications, including energy processing,1,2 aerobic oxidation,3,4 hydrogenation,5,6 carbon–carbon coupling,7,8 and oxygen reduction reactions,9,10 as well as environmental catalysis.11–13 To achieve the highest activity and selectivity, it is desirable to have uniformly dispersed nanoparticles (NPs) that have identical properties and distribution. Many methods for preparing highly active heterogeneous Pd catalysts have been reported to date such as impregnation,14 deposition–precipitation,15 sol immobilization or colloidal deposition,16 ligand-assisted synthesis,17 and chemical vapor deposition.18 Conventional synthesis approaches do not provide the requisite degree of control, since they start from Pd salts that are first deposited on a support by precipitation or impregnation. Reduction in these methods is achieved by high-temperature treatment involving calcination and H2 reduction, leading to the aggregation of the resulting particles. The obtained Pd catalysts then display only a moderate level of activity in, for example, the direct synthesis of hydrogen peroxide or the solvent-free oxidation of alcohols.19,20 Hence there has been considerable interest in developing colloidal routes to synthesize highly dispersed heterogeneous catalysts. In the process of colloidal methods, polymer protecting agents such as polyvinyl pyrrolidone (PVP) and polyvinyl alcohol (PVA) are generally employed to stabilize the size as well as the shape of metal colloids.21–23 These polymer-capped NPs have shown preferred activity in a variety of liquid-phase reactions.24,25 However, the capping agent must be removed to achieve high catalytic activity, and the high-temperature treatments used for the removal of the capping agent would lead to particle aggregation and loss of monodispersity.26,27 Therefore, considerable effort is still being expended to discover a facile and effective method for the reproducible preparation of highly active and stable supported Pd NP catalysts.
Recent work by Hutchings’ group28 has shown a modification and post-reduction step in the impregnation method to prepare a supported AuPd/TiO2 catalyst possessing a tight Au particle size distribution of 2–5 nm, but without the ligands adsorbed on the particle surface. Similarly, by precise control of the precipitation conditions, Pd nanoparticles with narrow size distribution (2–4 nm) were synthesized,29 even on low-surface-area inorganic powders.30 Moreover, Datye et al.31 reported a Pd/C catalyst with 1.5 nm NPs by the reduction of palladium acetate in methanol under anhydrous conditions. Additionally, Gatica and coworkers32 prepared Au supported on ceria–zirconia mixed oxides using a speciation-controlled incipient wetness impregnation approach, and the resulting NPs featured both high gold loading and excellent metal dispersion. Thus it can be seen that well-dispersed NPs can be synthesized by the precise tuning of preparation conditions based on the existing approaches.
In previous study, hydrotalcite (HT), a type of two-dimensional (2D) layered inorganic material, has exhibited an increased catalytic performance in oxidation reactions, owing to the tunable acidity–basicity of the surface.33,34 HT has the general formula [M2+1−xM3+x(OH)2]x+(An−)x/n·mH2O, where M2+ and M3+ indicate metallic cations, x is the molar ratio of M3+/(M2+ + M3+), An− represents the interlayer anion and m indicates the amount of water.35,36 Besides the acidity–basicity, HT also offers cation tunability of the brucite-like layers as well as a high adsorption capacity, which mean it has been extensively investigated in the fields of both fundamental research and practical processes.37,38 For example, a green preparation of Pt NPs has been developed using soluble starch as a reducing and stabilizing agent, and the Pt NPs were then immobilized on an MgAl–LDH surface.39 These Pt/HT catalysts were employed in the oxidation of glycerol in water and showed 41% yield and 75% selectivity for glyceric acid with a turnover number of 357. In addition, our group reported a series of LDH-supported Pd catalysts for the partial hydrogenation of acetylene, which showed enhanced catalytic performances.40–42 Therefore, synthesis of HT-supported Pd catalysts with small particle size and narrow size distribution is of great importance to gain insight into HT-supported catalysts as well as to broaden their range of potential industrial applications.
In this work, we describe a facile route for synthesizing highly dispersed Pd/HT catalysts that involves the reduction of Pd(II) by NaBH4. The pH value is vital to obtain well-dispersed Pd NPs on the HT support. It is worth noting that the preparation is conducted at room temperature and no capping agent or thermal treatment is required in this process. High-resolution transmission electron microscopy and CO pulse chemisorption are used to determine the size and dispersion of the resulting Pd NPs. The status and electronic environment of surface Pd atoms are revealed by CO-IR and X-ray photoelectron spectroscopy analysis. Additionally, this technique is extended to other powder supports (HT with different Mg/Al ratios, MgO and hydroxyapatite (HAP)). These catalysts are also found to be active, very selective to benzaldehyde and stable for solvent-free aerobic oxidation of benzyl alcohol (BA).
2. Experimental
2.1 Support preparation
The Mg2Al–HT compound was prepared by co-precipitation at pH 10.0 (±0.1) of suitable amounts of Mg(NO3)2·6H2O (7.38 g) and Al(NO3)3·6H2O (5.40 g) with solutions of NaOH (1 M) and Na2CO3 (0.4 M). The addition of the alkaline solution and pH were controlled by pH meter (Mettler-Toledo FE20). The suspension was stirred at 353 K for 6 h, and the precipitate was then centrifuged and thoroughly washed with deionized water until the pH reached 7.0. After drying for 12 h at 383 K, the Mg2Al–HT support was obtained. Other MgAl–HT materials with different Mg/Al molar ratios (Mg3Al–HT, Mg4Al–HT and Mg5Al–HT) were prepared by the same method by adjusting the amounts of Mg(NO3)2·6H2O and NaOH([Mg2+] + [Al3+]/[OH−] = 1.6).
2.2 Catalyst preparation
2.2.1 Pd catalysts supported on HT prepared by a modified deposition–precipitation (MDP) method. 1.00 g Mg2Al–HT support was first suspended in 50 ml aqueous solution. The pH value of the suspension was controlled by the addition of NaOH (0.1 M). Until the pH reached 10.0, 2 ml Na2PdCl4 (0.046 M) was poured into the suspension. After that, more NaOH solution was added to maintain the overall pH at 10.0. A freshly prepared solution of NaBH4 (0.1 M, NaBH4/Pd (mol mol−1) = 5) was then added and the solution turned dark brown. After another 1 h stirring, the precipitate was centrifuged and thoroughly washed with deionized water until it reached ∼ pH 7.0. The washed solid was dried (383 K for 12 h) and the obtained catalyst was denoted as Pd/HTMDP-10. A variation in the MDP procedure was also investigated. The preparation process was kept the same except for the control of the pH value. When the pH was set at 12.0, the obtained catalyst was denoted as Pd/HTMDP-12. The catalyst was also prepared under acidic conditions (denoted as Pd/HTMDP-4), in which the pH was adjusted by the addition of HCl (0.1 M) to 4.0. Moreover, the Pd/HT catalyst without the adjustment of pH was denoted as Pd/HTMDP-7.Using the same method, Pd/Mg3Al–HT, Pd/Mg4Al–HT, Pd/Mg5Al–HT, Pd/MgO and Pd/hydroxyapatite were also prepared.
2.2.2 Pd catalysts supported on HT prepared by other methods. As a comparison, Pd catalysts supported on HT were prepared using three other preparation methods: impregnation (denoted as Im), deposition–precipitation (DP) and sol immobilisation (SIm). The detailed procedures for the three preparation methods have been described in detail elsewhere.14–16 Briefly, the synthesis of Pd/HT prepared by impregnation was carried out as follows: 1.4 ml Na2PdCl4 (0.046 M) was added to a stirred and heated aqueous solution (10 ml). The resultant solution was then added to the Mg2Al–HT (1.00 g) and the resulting slurry was dried at 383 K for 12 h. The resulting powder was ground and calcined in static air (673 K, 4 h) followed by reduction in 10% H2/Ar (473 K, 2 h). This material was denoted as Pd/HTIm. In the case of the DP method, a stirred slurry of Mg2Al–HT (1.00 g) in water (50 ml) was adjusted to pH 10 by the dropwise addition of (0.1 M) NaOH. 1.4 ml Na2PdCl4 (0.046 M) was added to the suspension and NaOH was added dropwise to maintain the overall pH at 10 for 1 h. The slurry was then filtered and washed with deionized water. The washed solid was dried (383 K for 12 h), calcined in air (673 K, 4 h) and reduced in H2/Ar (473 K, 2 h). This material was denoted as Pd/HTDP. As for the sol immobilization method, to an aqueous fresh Na2PdCl4 solution, the required amount of a PVA solution (1 wt%) was added (PVA/Pd (w/w) = 1.2). A freshly prepared solution of NaBH4 (0.1 M, NaBH4/Pd (mol mol−1) = 5) was then added to form a dark brown sol. After 1 h of sol generation, the colloid was immobilized by adding Mg2Al–HT (1.00 g) under vigorous stirring conditions. After another 1 h the slurry was filtered, the catalyst washed thoroughly with deionized water and dried at 383 K for 12 h. The obtained catalyst was denoted as Pd/HTSIm.
2.3 Catalyst characterization
The specific surface area was calculated according to the Brunauer–Emmett–Teller (BET) method based on the adsorption isotherm. Elemental analysis for Pd was recorded using a Shimadzu ICPS-75000 inductively coupled plasma atomic emission spectrometer (ICP-AES). The morphology and size of the samples were examined using a JEOL JEM-2100F high-resolution transmission electron microscope (HRTEM). CO pulse chemisorption was conducted at 110 °C on a Micrometrics ChemiSorb 2920 equipped with 50 μl loop. XRD analysis of supported Pd catalysts were performed on a Shimadzu XRD-6000 diffractometer using Cu Kα radiation (λ = 0.154 nm) in the 2θ range of 3–70° with a scan speed of 10° min−1. X-ray photoelectron spectra (XPS) of the samples were collected using a Thermo VG ESCALAB 250 spectrometer equipped with a Mg Kα anode. The C 1s peak at 284.6 eV was used for calibration. In situ diffuse reflectance infrared Fourier transform spectroscopy (DRIFTS) was performed on a Bruker Tensor 27 instrument. The sample was pressed into a self-supporting pellet and pretreated in the same cell used for the measurement. After hydrogen reduction and nitrogen pretreatment at 373 K for 30 min, the DRIFTS spectrum of the catalyst was recorded at 3 mbar with a resolution of 4 cm−1 in order to obtain a background spectrum. Then the catalyst was exposed to a CO flow for 30 min. DRIFTS measurements of CO chemisorbed on catalysts were conducted after the pressure was reduced to 3 mbar.
2.4 Alcohol oxidation
The catalytic performance was evaluated by the solvent-free aerobic oxidation of benzyl alcohol, which was carried out in a 50 ml glass reactor under O2 pressure at 1 bar. In a typical reaction, 3 ml benzyl alcohol and the requisite amount of catalyst (alcohol/active metal molar ratio was 10
000) were added. The reactor was purged with ultrahigh purity O2 for about 1 min and the O2 was continuously delivered to keep the pressure at 1 bar during the reaction. The reactor was then kept in a heating block that was preheated to 373 K, and the mixture was stirred at a speed of 1000 rpm. After a specific time, the samples were rapidly cooled in a cold water bath and centrifuged to remove the solid catalyst.
An aliquot of the clear supernatant reaction mixture (0.5 ml) was diluted with mesitylene (0.5 ml, external standard for GC analysis). For the analysis of the products an Agilent J&W GC-FID (DB-Wax, 30 m × 0.320 mm, df = 0.25 μm) was used. The products were identified by comparison with known authentic standards. For the quantification of the amounts of reactants consumed and products generated, an external standard method was used. The selectivity was calculated as number of moles of product formed per mole of reacted benzyl alcohol, and the carbon balance was within ±2%.
3. Results and discussion
3.1 Characterization of catalysts
Pd/HT catalysts prepared by the modified deposition–precipitation method were successfully synthesized under the different pH values of 4.0, 10.0, 12.0 (Pd/HTMDP-4, Pd/HTMDP-10 and Pd/HTMDP-12, respectively) as well as without pH adjustment (Pd/HTMDP-7). BET specific surface areas of Pd catalysts prepared by MDP method are given in Table 1. The values for supported Pd catalysts under different pH conditions are similar and reproducible within experimental error. Detailed HRTEM studies were carried out to compare the morphologies of 1 wt% Pd/HTMDP catalysts under different pH conditions. As shown in Fig. 1, the Pd NPs are evenly dispersed over the surface of HT and no obvious aggregation is observed for the four catalysts. More than 200 particles in different regions were randomly selected to measure the distribution and mean size of the Pd nanoparticles.
Table 1 The properties of Pd/HT catalysts prepared by modified deposition–precipitation using different pH conditions
Sample |
Surface areaa (m2 g−1) |
Pd loadingb (%) |
Particle size (nm) |
Theoretical dispersionc (%) |
CO uptaked (μmol g−1) |
Dispersione (%) |
Determined by BET analysis. Determined by ICP analysis. Estimated from average particle size. Determined by CO pulse. Determined by CO uptake assuming a Pd : CO stoichiometry of 2 : 1. |
Pd/HTMDP-4 |
107 |
1.08 |
3.7 |
23.8 |
12.3 |
24.2 |
Pd/HTMDP-7 |
110 |
1.02 |
2.5 |
35.2 |
22.9 |
47.8 |
Pd/HTMDP-10 |
98 |
0.98 |
2.3 |
38.3 |
25.0 |
51.4 |
Pd/HTMDP-12 |
103 |
1.02 |
2.2 |
40.0 |
12.4 |
26.9 |
 |
| Fig. 1 HRTEM images and the size distribution of Pd/HTMDP-4 (A and B), Pd/HTMDP-7 (C and D), Pd/HTMDP-10 (E and F) and Pd/HTMDP-12 (G and H). | |
It can be clearly seen that the mean size of the Pd NPs decreases (from 3.7 nm to 2.2 nm) with increasing pH value (from 4.0 to 12.0). Significantly, the Pd NPs larger than 6.0 nm disappear gradually and the size distribution becomes narrow with the addition of NaOH (0.5–9.0 nm for Pd/HTMDP-4, 0.5–8.0 nm for Pd/HTMDP-7, 0.5–6.0 nm for Pd/HTMDP-10 and 0.5–6.0 nm for Pd/HTMDP-12). Moreover, the percentage of Pd NPs between 1.0 and 3.0 nm apparently goes up with the increasing pH (33.0%, 73.2%, 82.7% and 85.4%). The narrow size distribution and large percentage of small NPs would contribute to the increase in activity. Interestingly, Pd NPs embedded on the edge of the HT support are observed in Fig. 1B, D and E, which are regarded to not only effectively prevent the NPs from migration and aggregation during use but also to induce strong metal–support interaction.43,44
Based on the average NP diameter determined from HRTEM, the theoretical dispersion is calculated by a formula described elsewhere.45,46 As listed in Table 1, the dispersion of Pd catalysts increases with decreasing NP size. To acquire more precise values, CO pulse chemisorption was also performed. Distinct from the theoretical values, a “volcano” curve is present for the CO uptake of the four catalysts. The dispersion was then calculated from the CO uptake assuming a Pd
:
CO stoichiometry of 2
:
1. The results show that the Pd/HTMDP-10 has the highest dispersion (51.4%), followed by the Pd/HTMDP-7 (47.8%), which is almost double that for the two other catalysts. The superior dispersion of Pd/HTMDP-7 and Pd/HTMDP-10 could be ascribed to the small Pd NPs as well as the tight size distribution. As for Pd/HTMDP-12, even though small Pd NPs are obtained, the low dispersion may be ascribed to the different status and electronic environment of the surface Pd atoms.
The extensive literature regarding the adsorption of CO on Pd makes this molecule well suited as an infrared radiation probe of adsorption sites present on the Pd particles. Therefore, in situ DRIFTS of samples exposed to CO at room temperature was performed. As seen in Fig. 2, two main vibrational features at ca. 1910 and 1818 cm−1, which are reasonably ascribed to bridge-bonded CO and threefold hollow site CO, are observed over the four catalysts.47 In addition, a weak peak at ca. 1995 cm−1 is seen in Pd/HTMDP-4 and Pd/HTMDP-7, meanwhile, a feature at ca. 2060 cm−1 appears in Pd/HTMDP-10 and Pd/HTMDP-12. The latter could be assigned to the CO linear adsorption.48 Comparison of the peak area ratio for CO adsorbed on bridge-bonded Pd (Ab) to that adsorbed on threefold-coordinate Pd (Am) shows that the Ab/Am ratio increases with rising pH value (from 0.1 to 31.9). Moreover, the shift in the CO band position is often interpreted as evidence of changes in the electronic properties of supported metals.48,49
 |
| Fig. 2 In situ CO-IR spectra of (A) Pd/HTMDP4, (B) Pd/HTMDP-7, (C) Pd/HTMDP-10 and (D) Pd/HTMDP-12. | |
In order to investigate the electronic structure of the Pd/HT catalysts under different preparation conditions, XPS analysis was carried out and the results are shown in Fig. 3. In the Pd/HTMDP-10 catalyst, the Pd 3d spectrum shows two main peaks, and the binding energy (BE) values at around 335.6 and 341.2 eV are ascribed to Pd 3d5/2 and Pd 3d3/2 of Pd0.42,49 Additionally, peaks attributed to Pd2+ are also observed in the spectra. As for Pd/HTMDP-7, similar BE values of Pd0 and Pd2+ are exhibited. Interestingly, peaks shift to lower BE by approximately 0.4 eV and 0.2 eV for Pd/HTMDP-4 and Pd/HTMDP-12 with respect to the Pd/HTMDP-10 catalyst, suggesting that distinct interaction between Pd and the HT support is induced by the MDP method. As reported, the size of Pd could also affect the BE value,50,51 however, the average size of Pd NPs in Pd/HTMDP-10 (2.3 nm) is similar to that in Pd/HTMDP-12 (2.2 nm). This shift of Pd 3d is thus reasonably ascribed to electron transfer from Pd to the HT support, resulting in electron-deficient surface metallic Pd, which may result in the enhancement in the catalytic performance.
 |
| Fig. 3 XPS spectra of (A) Pd/HTMDP-4, (B) Pd/HTMDP-7, (C) Pd/HTMDP-10 and (D) Pd/HTMDP-12. | |
3.2 Solvent-free oxidation of benzyl alcohol over Pd/HTMDP catalysts
The catalytic oxidation of benzyl alcohol over Pd catalysts prepared by the modified deposition–precipitation method under solvent- and base-free conditions was investigated at 373 K using a glass reactor. The results are shown in Fig. 4. The Pd/HTMDP-7 and Pd/HTMDP-10 catalysts exhibit comparable conversion of BA that is higher than that of Pd/HTMDP-4 and Pd/HTMDP-12. The inset in Fig. 4A shows the BA conversion at 1 h and 2 h for the four catalysts. It can be clearly seen that the BA conversions of Pd/HTMDP-7 and Pd/HTMDP-10 are 36.9% and 19.5% higher than those of Pd/HTMDP-4 and Pd/HTMDP-12, respectively, at the initial period (1 h). A similar trend was also found with a reaction time of 2 h. When the reaction was extended to 6 h, the BA conversion increased to 96.8%, 94.6%, 87.3% and 83.5% for Pd/HTMDP-10, Pd/HTMDP-7, Pd/HTMDP-12 and Pd/HTMDP-4, respectively. In the case of the selectivity, benzaldehyde was detected as the main product. All four catalysts displayed high selectivity towards benzaldehyde, more than 94.5%. At a BA conversion of 80% a slightly higher selectivity (97.0%) was observed for Pd/HTMDP-10.
 |
| Fig. 4 Selective oxidation of benzyl alcohol with Pd/HT catalysts prepared by the modified deposition–precipitation method under different pH conditions: (A) alcohol conversion as a function of reaction time and (B) selectivity towards benzaldehyde as a function of alcohol conversion for Pd/HTMDP-4, Pd/HTMDP-7, Pd/HTMDP-10 and Pd/HTMDP-12. Inset in (A) shows the alcohol conversion at 1 h and 2 h for the four catalysts. The oxidation of benzyl alcohol (3 ml) was carried out at 373 K, 1 bar pO2, 1000 rpm stirrer speed and 10 000 substrate/metal ratio. | |
Based on our previous findings,16 a three-step mechanism may be involved in the oxidation of benzyl alcohol over supported metal catalysts on HT, that is, an abstraction of the proton by the hydroxyl group on the support, a β-hydride elimination on the metal surface and the recovery of the metallic site from metal hydride. It is speculated that the first step may determine the selectivity, meanwhile the second step is related to the activity. The elimination of β-hydride is also regarded as the rate-determining step. In our system, the use of the same HT support with basic sites that could facilitate the abstraction of protons from benzyl alcohol leads to the high and similar selectivity towards benzaldehyde over the four catalysts. As for the activity, it is generally thought that small particles with a large number of coordinatively unsaturated metal atoms are more active for the cleavage of β-hydride. However, the highest conversion is observed for Pd/HTMDP-10, and the conversion with Pd/HTMDP-12 with the smallest mean size is much lower than that for Pd/HTMDP-10, indicating that the activity is not only related to the particle size but also to the electronic density of Pd NPs. Based on the XPS results, we speculate that an electron-deficient surface metallic Pd can contribute to β-hydride cleavage, and as a result Pd/HTMDP-7 and Pd/HTMDP-10 with relatively small Pd NPs as well as reduced electronic density of active component exhibit the highest activity.
3.3 Stability of the Pd/HTMDP-10 catalyst
Considering both the activity and selectivity, the Pd/HTMDP-10 catalyst has the highest catalytic performance for the oxidation of benzyl alcohol under our conditions. To determine the efficiency of this catalyst, five consecutive reuse experiments were performed. After 4 h of reaction, the catalyst was centrifuged, washed with acetone, and dried at 383 K. Then it was employed for another BA oxidation reaction under the same reaction conditions. As shown in Fig. 5, the catalyst could be reused at least five times. Only a slight decrease in BA conversion (8.3%) is seen in the fifth run and no remarkable change in the selectivity is observed (i.e., 95.9, 96.6, 95.9, 96.2 and 96.8% for five cycles). The Pd loading of the catalyst after the fifth use was also detected; the value is 0.98%, which is the same as that of the fresh catalyst.
 |
| Fig. 5 Recycling of Pd/HTMDP-10. The oxidation of benzyl alcohol (3 ml) was carried out at 373 K, 1 bar pO2, 4 h, 1000 rpm stirrer speed and 10 000 substrate/metal ratio. | |
To further determine the stability of the Pd/HT catalyst prepared by the modified deposition–precipitation method, the morphology of the catalyst after five runs was investigated by HRTEM. As shown in Fig. 6, Pd NPs are well dispersed on the surface of the HT support, and no obvious aggregation is found in the HRTEM image. The result of statistics from 200 randomly selected NPs shows that the average particle size is 3.0 nm. Moreover, the size distribution of the used catalyst is similar to that of fresh catalyst, and no larger particles (>6.0 nm) are seen. Therefore, we conclude that the modified deposition–precipitation method is a facile approach to synthesize Pd/HT catalysts with small particle size and narrow distribution, as well as high activity, selectivity and efficiency for the solvent-free oxidation of benzyl alcohol.
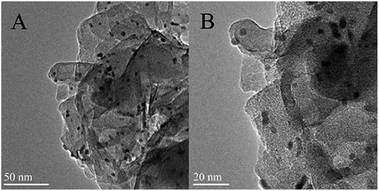 |
| Fig. 6 HRTEM images of used Pd/HTMDP-10. | |
3.4 Comparison with other preparation methods
As a comparison, the Pd catalysts supported on HT were prepared by sol immobilization, impregnation and deposition–precipitation methods. The HRTEM images of Pd/HT catalysts prepared by the three approaches are shown in Fig. 7. It can be seen that the Pd NPs are well dispersed on the HT support for all the catalysts. From the statistics of 200 randomly selected NPs, the average size and distribution were calculated. The particle sizes of Pd/HTSIm, Pd/HTIm and Pd/HTDP are 3.6, 3.2 and 2.6 nm, respectively. Moreover, all the catalysts possess a narrow size distribution from 0.5 to 7.0 nm. However, the percentage of Pd NPs between 1.0 and 3.0 nm in these catalysts is lower than that in the Pd/HTMDP-10 catalyst. Other information about the properties of the Pd/HT catalysts prepared by the three methods is listed in Table 2. It is highlighted that both the CO uptakes and corresponding dispersions of the catalysts prepared by the other methods are lower than the catalysts prepared by the modified deposition–precipitation method. The increase in the particle size as well as the drop in dispersion may result in different catalytic performances.
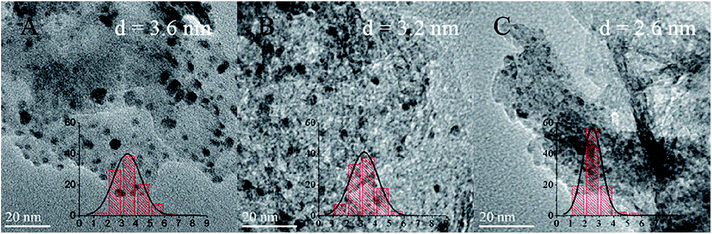 |
| Fig. 7 HRTEM images and the size distributions of (A) Pd/HTSIm, (B) Pd/HTIm, and (C) Pd/HTDP. | |
Table 2 The properties of Pd/HT catalysts prepared by different methods
Sample |
Surface areaa (m2 g−1) |
Pd loadingb (%) |
Particle size (nm) |
CO uptakec (μmol g−1) |
Dispersiond (%) |
TOFe (h−1) |
Determined by BET analysis. Determined by ICP analysis. Determined by CO pulse. Determined by CO uptake assuming a Pd : CO stoichiometry of 2 : 1. Calculated as the ratio of number of moles of benzyl alcohol converted per mole of total Pd per hour, measured at a time-on-stream of 1 h. |
Pd/HTSol |
99 |
1.17 |
3.6 |
10.0 |
21.1 |
4400 |
Pd/HTIm |
94 |
1.11 |
3.2 |
20.6 |
39.6 |
3000 |
Pd/HTDP |
104 |
0.95 |
2.6 |
6.8 |
15.8 |
4360 |
Pd/HTMDP-10 |
98 |
0.98 |
2.3 |
25.0 |
51.4 |
5330 |
The oxidation of benzyl alcohol was then carried out with the Pd catalysts prepared by the different methods for 1 h. The results are shown in Fig. 8. Pd/HTSIm and Pd/HTDP possess similar BA conversions after 1 h of reaction, higher than that for Pd/HTIm. It is also seen that Pd/HTMDP-10 is slightly more active than the catalysts prepared by SIm and DP methods, and it is significantly more active than that prepared by the Im method. This enhanced activity can be ascribed to the small particle size and high dispersion. The selectivity for benzaldehyde is compared at the iso-conversion of BA (80%). All the Pd catalysts show a superior selectivity (more than 95%) owing to the nature of the HT support. Moreover, the Pd/HTDP exhibits a slightly higher selectivity.
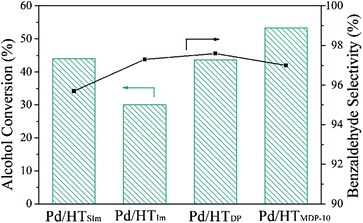 |
| Fig. 8 Selective oxidation of benzyl alcohol over supported Pd catalysts prepared by different methods. The oxidation of benzyl alcohol (3 ml) was carried out at 373 K, 1 bar pO2, 1000 rpm stirrer speed and 10 000 substrate/metal ratio. | |
3.5 Pd NPs on different supports
Pd catalysts were prepared on alternative supports (e.g. HT with different Mg/Al ratios, MgO and hydroxyapatite) by this modified deposition–precipitation method. As shown in Fig. 4, the Pd/HTMDP-7 catalyst exhibits comparable activity and a slightly lower selectivity than the best performing Pd/HTMDP-10 catalyst. Taking into consideration the requirements of green chemistry, these Pd catalysts on different supports were prepared without the adjustment of pH value, which avoids the addition of alkali in the preparation process. The powder XRD analyses of the obtained Pd catalysts were carried out (Fig. 9). The patterns of the samples are similar to those reported previously,16,52 suggesting that the structure of the pristine support is maintained under our conditions. The diffraction peaks of Pd are not seen for all the catalysts due to the relatively low Pd loading and small particle size. The basicity determined from a suspension of catalyst (1 g) in distilled water (50 ml) and Pd loadings are listed in Table 3. Evidently, an increase in the Mg/Al atomic ratio of the HT from 2 to 5 led to an increase in the support basicity (from pH 8.4 to 9.4), and to a decrease in Pd loading (from 1.02% to 0.96%). Moreover, Pd NPs were also successfully loaded onto the surface of MgO and hydroxyapatite. The low Pd loading (0.70%) in MgO can be attributed to the formation of Mg(OH)2 (as seen in Fig. 9), which increased the weight of the support by interaction with water in the preparation process. These data show that Pd NPs can be immobilized on the support with pH values between 6.9 and 10.6 by this facile approach, and meanwhile the texture and nature of the support also influence the preparation process.
 |
| Fig. 9 XRD patterns of supported Pd catalysts prepared by the modified DP method. | |
Table 3 Properties of Pd/HT catalysts prepared by the modified DP method
Support |
Loadinga (%) |
Basicityb (pH) |
Determined by ICP analysis. By suspension of catalyst (1 g) in distilled water (50 ml). |
Mg2Al1-LDHs |
1.02 |
8.4 |
Mg3Al1-LDHs |
1.01 |
8.6 |
Mg4Al1-LDHs |
0.97 |
9.0 |
Mg5Al1-LDHs |
0.96 |
9.4 |
MgO |
0.70 |
10.6 |
HAP |
1.04 |
6.9 |
The obtained catalysts were tested for the oxidation of benzyl alcohol for 1 h (Fig. 10). The highest activity was observed for the Pd/HAP catalyst, however, an obvious decrease in selectivity for this catalyst was also seen (from 98.0% to 91.4%). It is highlighted that the selectivity is calculated at a BA conversion of 57.6%, and this is even lower than that obtained at conversion of 80% for Pd/HTMDP-7 (96.4%). Moreover, the activity of the catalysts drops with increasing support basicity, indicating that the performance of the catalysts is truly affected by the nature of the support.
 |
| Fig. 10 The benzyl alcohol conversion and selectivity towards benzaldehyde of Pd catalysts on different supports prepared by the MDP method with a reaction time of 1 h. The oxidation of benzyl alcohol (3 ml) was carried out at 373 K, 1 bar pO2, 1000 rpm stirrer speed and a 10 000 substrate/metal ratio. | |
4. Conclusions
A surfactant-free modified deposition–precipitation methodology has been developed for the preparation of supported Pd/HT catalysts. The support was first suspended in an aqueous solution, followed by adjustment of the pH. After the addition of active precursor to the suspension, extra NaOH or HCl was added dropwise to maintain the overall pH value. A freshly prepared NaBH4 solution was then added quickly. The supported Pd catalysts were obtained by centrifugation and thorough washing. This synthesis method resulted in the reproducible variation of particle size and control of particle size distribution. At pH 10, the resulting Pd NPs had an average size of 2.3 nm and 82.7% of the NPs were in the range of 1.0–3.0 nm. The results of CO pulse chemisorption showed that this catalyst has a dispersion as high as 51.4%. The distinct status and electronic environment of the surface Pd atoms under controllable pH were also revealed by CO-IR and XPS analysis. CO-IR results showed that the Ab/Am ratio increased from 0.1 to 31.9 with rising pH value (from 4.0 to 12.0). Meanwhile, XPS results indicated stronger support–metal interaction at pH values of 7.0 and 10.0, and thus an electron-deficient surface metallic Pd was obtained in Pd/HTMDP-10 and Pd/HTMDP-7. In the solvent-free oxidation of benzyl alcohol, catalysts prepared by the MDP method were found to be 17%, 18% and 44% more active than those made by SIm, DP and Im methods. In recycling experiments, the Pd/HTMDP-10 catalyst retained its high activity and no Pd loss or obvious aggregation was detected in the used catalyst. Under the considerations of green chemistry, a number of different Pd catalysts were also prepared on alternative supports without the addition of alkali in the preparation process. It was highlighted that this technique alleviates the need to pretreat the catalyst and provides a new approach to synthesize well-dispersed supported Pd catalysts.
Acknowledgements
This work was supported by the National Natural Science Foundation of China, Beijing Natural Science Foundation (2132032), the 973 Project (2011CBA00506), the Beijing Engineering Center for Hierarchical Catalysts and the Fundamental Research Funds for the Central Universities (YS1406).
References
- B. Adams and A. Chen, Mater. Today, 2011, 14, 282 CrossRef CAS.
- D. M. Alonso, S. G. Wettstein and J. A. Dumesic, Chem. Soc. Rev., 2012, 41, 8075 RSC.
- D. I. Enache, J. K. Edwards, P. Landon, B. Solsona-Espriu, A. F. Carley, A. A. Herzing, M. Watanabe, C. J. Kiely, D. W. Knight and G. J. Hutchings, Science, 2006, 311, 362 CrossRef CAS PubMed.
- P. F. Zhang, Y. T. Gong, H. R. Li, Z. R. Chen and Y. Wang, Nat. Commun., 2013, 4, 1593 CrossRef PubMed.
- C. Q. Hu, D. Creaser, S. Siahrostami, H. Grönbeck, H. Ojagh and M. Skoglundh, Catal. Sci. Technol., 2014, 4, 2427 CAS.
- Y. N. Liu, J. T. Feng, Y. F. He, J. H. Sun and D. Q. Li, Catal. Sci. Technol., 2015, 5, 1231 CAS.
- L. X. Yin and J. Liebscher, Chem. Rev., 2007, 107, 133 CrossRef CAS PubMed.
- P. Sharma and A. P. Singh, Catal. Sci. Technol., 2014, 4, 2978 CAS.
- G. F. Alvarez, M. Mamlouk, S. M. S. Kumar and K. Scott, J. Appl. Electrochem., 2011, 41, 925 CrossRef CAS.
- E. Antolini, S. C. Zignani, S. F. Santos and E. R. Gonzalez, Electrochim. Acta, 2011, 56, 2299 CrossRef CAS PubMed.
- Y. Z. Li, Y. Yu, J. G. Wang, J. Song, Q. Li, M. D. Dong and C. J. Liu, Appl. Catal., B, 2012, 125, 189 CrossRef CAS PubMed.
- R. Wang, H. He, L. C. Liu, H. X. Dai and Z. Zhao, Catal. Sci. Technol., 2012, 2, 575 CAS.
- S. Iqbal, X. Liu, O. F. Aldosari, P. J. Miedziak, J. K. Edwards, G. L. Brett, A. Akram, G. M. King, T. E. Davies, D. J. Morgan, D. K. Knight and G. J. Hutchings, Catal. Sci. Technol., 2014, 4, 2280 CAS.
- L. H. Xiao, K. P. Sun, X. L. Xu and X. N. Li, Catal. Commun., 2005, 6, 796 CrossRef CAS PubMed.
- P. J. Miedziak, Q. He, J. K. Edwards, S. H. Taylor, D. W. Knight, B. Tarbit, C. J. Kiely and G. J. Hutchings, Catal. Today, 2011, 163, 47 CrossRef CAS PubMed.
- J. T. Feng, C. Ma, P. J. Miedziak, J. K. Edwards, G. L. Brett, D. Q. Li, Y. Y. Du, D. J. Morgan and G. J. Hutchings, Dalton Trans., 2013, 42, 14498 RSC.
- F.-M. McKenna, L. Mantarosie, R. P. K. Wells, C. Hardacreb and J. A. Anderson, Catal. Sci. Technol., 2012, 2, 632 CAS.
- M. Okumura, S. Nakamura, S. Tsubota, T. Nakamura, M. Azum and M. Haruta, Catal. Lett., 1998, 51, 53 CrossRef CAS.
- J. K. Edwards, B. Solsona, A. F. Carley, A. A. Herzing, C. J. Kiely and G. J. Hutchings, Science, 2009, 323, 1037 CrossRef CAS PubMed.
- P. Miedziak, M. Sankar, N. Dimitratos, J. A. Lopez-Sanchez, A. F. Carley, D. W. Knight, S. H. Taylor, C. J. Kiely and G. J. Hutchings, Catal. Today, 2011, 164, 315 CrossRef CAS PubMed.
- T. Teranishi and M. Miyake, Chem. Mater., 1998, 10, 594 CrossRef CAS.
- J. S. Bradley, E. W. Hill, B. Chaudret and A. Duteil, Langmuir, 1995, 11, 693 CrossRef CAS.
- L. Kesavan, R. Tiruvalam, M. H. A. Rahim, M. I. Bin Saiman, D. I. Enache, R. L. Jenkins, N. Dimitratos, J. A. Lopez-Sanchez, S. H. Taylor, D. W. Knight, C. J. Kiely and G. J. Hutchings, Science, 2011, 331, 195 CrossRef CAS PubMed.
- H. Hirai, J. Macromol. Sci., Chem., 1979, 13, 633 CrossRef PubMed.
- M. Mifsud, K. V. Parkhomenko, I. W. Arends and R. A. Sheldon, Tetrahedron, 2010, 66, 1040 CrossRef CAS PubMed.
- J. Park, C. Aliaga, J. Renzas, H. Lee and G. Somorjai, Catal. Lett., 2009, 129, 1 CrossRef CAS.
- A. Gniewek, J. J. ZiÓlkowski, A. M. Trzeciak, M. Zawadzki, H. Grabowska and J. Wrzyszcz, J. Catal., 2008, 254, 121 CrossRef CAS PubMed.
- M. Sankar, Q. He, M. Morad, J. Pritchard, S. J. Freakley, J. K. Edwards, S. H. Taylor, D. J. Morgan, A. F. Carley, D. W. Knight, C. J. Kiely and G. J. Hutchings, ACS Nano, 2012, 6, 6600 CrossRef CAS PubMed.
- G. Agostini, R. Pellegrini, G. Leofanti, L. Bertinetti, S. Bertarione, E. Groppo, A. Zecchina and C. Lamberti, J. Phys. Chem. C, 2009, 113, 10485 CAS.
- M. A. Kulagina, E. Y. Gerasimov, T. Y. Kardash, P. A. Simonov and A. V. Romanenko, Catal. Today, 2015, 246, 72 CrossRef CAS PubMed.
- P. D. Burton, T. J. Boyle and A. K. Datye, J. Catal., 2011, 280, 145 CrossRef CAS PubMed.
- E. Río, D. Gaona, J. C. Hernández-Garrido, J. J. Calvino, M. G. Basallote, M. J. Fernández-Trujillo, J. A. Pérez-Omil and J. M. Gatica, J. Catal., 2014, 318, 119 CrossRef PubMed.
- K. Nagashima, T. Mitsudome, T. Mizugaki, K. Jitsukawa and K. Kaneda, Green Chem., 2010, 12, 2142 RSC.
- S. Nishimura, A. Takagaki and K. Ebitani, Green Chem., 2013, 15, 2026 RSC.
- Y. Kuroda, Y. Miyamoto, M. Hibino, K. Yamaguchi and N. Mizuno, Chem. Mater., 2013, 25, 2291 CrossRef CAS.
- P. J. Sideris, U. G. Nielsen, Z. Gan and C. P. Grey, Science, 2008, 321, 113 CrossRef CAS PubMed.
- J. T. Feng, Y. F. He, Y. N. Liu, Y. Y. Du and D. Q. Li, Chem. Soc. Rev., 2015, 44, 5291 RSC.
- G. L. Fan, F. Li, D. G. Evans and X. Duan, Chem. Soc. Rev., 2014, 43, 7040 RSC.
- D. Tongsakul, S. Nishimura, C. Thammacharoen, S. Ekgasit and K. Ebitani, Ind. Eng. Chem. Res., 2012, 51, 16182 CrossRef CAS.
- X. Y. Ma, Y. Y. Chai, D. G. Evans, D. Q. Li and J. T. Feng, J. Phys. Chem. C, 2011, 115, 8693 CAS.
- J. T. Feng, X. Y. Ma, D. G. Evans and D. Q. Li, Ind. Eng. Chem. Res., 2011, 50, 1947 CrossRef CAS.
- Y. F. He, L. L. Liang, Y. N. Liu, J. T. Feng, C. Ma and D. Q. Li, J. Catal., 2014, 309, 166 CrossRef CAS PubMed.
- L. Guo, W. J. Jiang, Y. Zhang, J. S. Hu, Z. D. Wei and L. J. Wan, ACS Catal., 2015, 5, 2903 CrossRef CAS.
- A. H. Lu, W. C. Li, Z. S. Hou and F. Schuth, Chem. Commun., 2007, 1038–1040 RSC.
- J. R. Anderson, Structure of Metallic Catalysts, Academic Press, London, 1975 Search PubMed.
- Z. M. Ren, F. Zhang, L. W. Yue, X. Li, Y. Tao, G. Zhang, K. Wu, C. Wang and B. S. Li, RSC Adv., 2015, 5, 52658 RSC.
- J. B. Giorgi, T. Schroeder, M. Bäumer and H.-J. Freund, Surf. Sci., 2002, 498, L71 CrossRef CAS.
- F.-M. McKenna and J. A. Anderson, J. Catal., 2011, 281, 231 CrossRef CAS PubMed.
- F. Cárdenas-Lizana, Y. Hao, M. Crespo-Quesada, I. Yuranov, X. Wang, M. A. Keane and L. Kiwi-Minsker, ACS Catal., 2013, 3, 1386 CrossRef.
- Z. J. Zhao, F. Liu, L. M. Qiu, L. Z. Zhao and S. K. Yan, Acta Phys.-Chim. Sin., 2008, 24, 1685 CAS.
- W. P. Zhou, A. Lewera, R. Larsen, R. I. Masel, P. S. Bagus and A. Wieckowski, J. Phys. Chem. B, 2006, 110, 13393 CrossRef CAS PubMed.
- A. Ślósarczyk, Z. Paszkiewicz and C. Paluszkiewicz, J. Mol. Struct., 2005, 744–747, 657 CrossRef PubMed.
|
This journal is © The Royal Society of Chemistry 2015 |
Click here to see how this site uses Cookies. View our privacy policy here.