DOI:
10.1039/D2SU00099G
(Tutorial Review)
RSC Sustain., 2023,
1, 213-223
Ginger waste as a potential feedstock for a zero-waste ginger biorefinery: a review
Received
10th November 2022
, Accepted 14th December 2022
First published on 16th December 2022
Abstract
Ginger consumption and its use in industrial applications such as essential oil and oleoresin extraction are growing globally. There will be increased volumes of ginger waste (rhizomes, stems and leaves) in the coming years. However, the valorisation of ginger waste is limited in the literature beyond its use as a ginger meal for animal feed. Herein, this review consolidates the literature on ginger waste within the context of developing a zero-waste ginger biorefinery that yields chemicals, materials and (bio)energy for emerging bio-based markets and applications. Green extraction technologies are reported; some are at an industrial scale for processing fresh ginger which could be re-used to obtain a second crop of oil or oleoresin. The application of ginger waste to produce potential value-added products such as anti-microbial materials, environmental remediation agents, supercapacitors, bioenergy and heterogeneous catalysts is presented. Limitations based on logistics, feedstock, processing technology and final output are discussed.
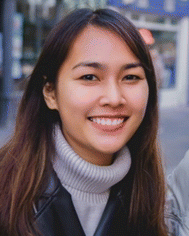 Natthamon Inthalaeng | Ms Natthamon Inthalaeng is a PhD student under the supervision of Prof. Avtar S. Matharu and Dr Tom Dugmore. She is a recipient of the highly prestigious DPST scholarship from the Royal Thai Government which allowed her to study for a bachelor's degree in chemistry at Mahidol University, Thailand, and then to continue her MSc (2021) and PhD in green chemistry at the Green Chemistry Centre of Excellence, University of York, England. She is currently in her second year of PhD study and her research studies involve the valorization of unavoidable food supply wastes leading to the development of zero-waste biorefineries. She is an emerging talent in green and sustainable chemistry. |
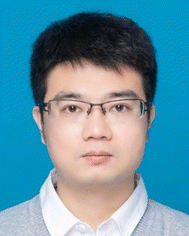 Yang Gao | Dr Yang Gao is currently at the State Key Laboratory of Separation Membrane and Membrane Process, School of Chemistry, Tiangong University, China after having completed his PhD under the supervision of Prof. Avtar S. Matharu at the Green Chemistry Centre of Excellence, University of York, United Kingdom in 2021. His research involves conversion of agricultural residues and unavoidable food supply chain wastes into high value-added chemicals, bio-based materials and (bio)energy via green chemical technologies. Yang Gao is an outstanding researcher aspiring to be a permanent academic. |
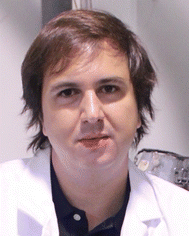 Javier Remón | Dr Javier Remón specialises in valorising biomass and waste to produce biofuels, energy carriers and chemicals. He holds a BSc, MSc and PhD in chemical engineering from the University of Zaragoza (Spain), with 8 months of PhD at Imperial College London (UK). Then, he worked at the Green Chemistry Centre of Excellence, University of York (UK) as a senior research associate for 2 years (2016–2018). Afterwards, he joined the Instituto de Carboquímica (ICB-CSIC) as a Juan de la Cierva Researcher (2018–2022). He has now been awarded a Ramon y Cajal Fellowship to join the University of Zaragoza (2023–). |
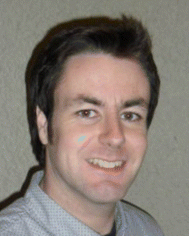 Thomas I. J. Dugmore | Dr Tom Dugmore is a lecturer in the Green Chemistry Centre of Excellence, University of York, UK. His background is in waste management and valorisation, specialising in food waste valorisation and wastewater remediation. He has worked with over 60 businesses locally and internationally on deriving value from food waste and has authored over 15 papers and book chapters on the subject. |
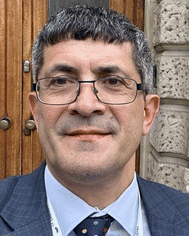 Mustafa Ozel | Dr Mustafa Zafer Ozel obtained his PhD in Chemistry (1993) from Leeds University (UK) under the supervision of Professor Keith Bartle and Professor Tony Clifford. He is currently a lecturer at the School of Life and Medical Sciences at Hertfordshire University in the UK. His research interests have been within the fields of environmental analytical, bioanalytical, atmospheric, green, flavour, and pharmaceutical chemistry. He is specifically interested in green extraction/processes from sustainable resources. He has published 4 book chapters and 53 papers. |
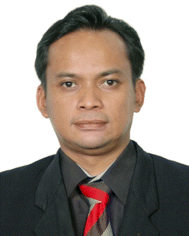 Allyn Sulaeman | Dr Allyn Pramudya Sulaeman earned a BSc in chemistry from Universitas Padjadjaran in Indonesia. In 2020, he completed his PhD in Chemistry from the Green Chemistry Centre of Excellence, University of York, United Kingdom under the supervision of Prof. Avtar S. Matharu. He is now a lecturer and researcher at the University Padjadjaran, focusing on microwave processing of biomass waste and photocatalysis for hydrogen production. |
Sustainability spotlight
The review focuses on key recent developments in ginger waste valorisation providing an in-depth analysis of current literature, identifiies knowledge, and gives future perspectives. The sustainability spotlight covers UN SDGs (SDG 12: responsible consumption and production), green chemistry principles and the ‘‘benign-by-design concept’’ (the design of efficient, economically viable and environmentally benign chemical processes). Ginger waste is a renewable resource and its fractionation into high value chemicals, materials and (bio)energy follows the use of benign solvents and energy efficient processes as well as reducing waste.
|
Introduction
Ginger (Zingiber officinale) is a flowering plant native to Southeast Asia whose root is commonly used as a spice or flavouring in foods and in fragrances as well as in traditional and modern medicine due to its distinctive pharmacological and nutritional values.1,2 Ginger extractives are rich in high-value oleoresins, which exhibit unique antioxidant, antimicrobial, anti-inflammatory and anticoagulant properties.3 Thus, the global popularity of ginger and its extractives is increasing.
As shown in Fig. 1, according to the statistics database of the Food and Agriculture Organization (FAOSTAT), 3.5 million tons of raw ginger (excluding leaves and stalks) were produced globally in 2017, and it rose to 4.3 million tons in 2020, with the majority (77%) still being cultivated across Asia.4 The global ginger market is forecast to continue to grow for both fresh and dried ginger. The Centre for the Promotion of Imports from developing countries, in 2020, reported over 152
000 tons of dried ginger were imported from developing countries into the European market with an import value of €310 million.5 As ginger is rich in oleoresin and used as a spice for culinary purposes, the market size of oleoresins and organic spices is chosen to demonstrate the demand for ginger globally. According to the Market Data Forecast in 2018, the global market size of oleoresins was valued at $1.4 billion in 2018 and is estimated to grow at an annual rate of 4.7% from 2018 to 2025.6 Moreover, in 2021 the global market size of organic spices was valued at $20 billion and is estimated to grow with an annual growth rate of 7.5% from 2021 to 2026.7 Ginger oil itself is a value product (around 100$ per kg). The global ginger oil market is expected to grow at 9.41% over the period to reach a total market size of US$189.431 million by 2025.8
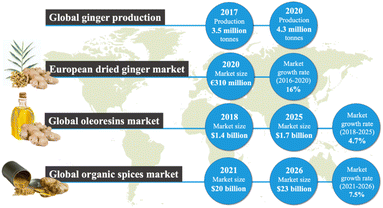 |
| Fig. 1 The global scope and potential of ginger, its markets and potential applications. | |
With the significant increase in ginger and its extractives, there is a commensurate increase in ginger oleoresin industries. Typically, fresh ginger rhizome contains 83–94% of moisture content on a wet basis9 and ginger oleoresins comprise approximately 20–30% of volatile oil, 10% of fixed oil, and 50–70% of pungent resinous matter. However, compared to the total dry weight of the rhizome, these high-value oils only account for 4–10% by weight, and, thus, there is a significant amount of spent ginger waste (by weight) produced from these.10 Traditionally, ginger waste, which also can include stalks and leaves, is directly sent to landfills, incinerated and/or used as low-value animal feed (ginger waste meal).11,12
Due to the adverse environmental effects of producing such a large volume of ginger waste, including, but not limited to, decomposition to greenhouse gases, there is a strong incentive to find alternatives to disposal. Fortunately, due to some of the unique compounds present in ginger oils, ginger waste also represents an excellent opportunity for valorisation. In fact, our own group recently reported the isolation of residual ginger oils from spent ginger waste followed by sequential conversion of oil-free residues into defibrillated celluloses as a part of a partial biorefinery concept.13 During our investigation, it became apparent that research into the re-utilisation of spent ginger wastes for high-value chemicals, materials and bioenergy beyond simple biomass burning or composting, was beginning to increase (see Fig. 2) but is still very much limited.
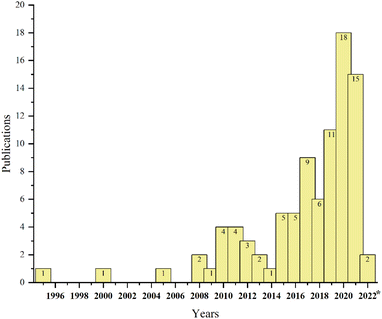 |
| Fig. 2 Number of papers published annually in the Web of Science (https://www.webofscience.com/) based on the keyword “ginger waste”. | |
Herein, this review summarises green extraction technologies for the valorisation of ginger waste into chemicals and materials, lending themselves to downstream products and applications such as anti-microbial materials, adsorbents and catalysts within the context of a zero-waste ginger biorefinery (Fig. 3). The most relevant publications from 2015 to date are reviewed with ginger meal waste deemed out of scope.
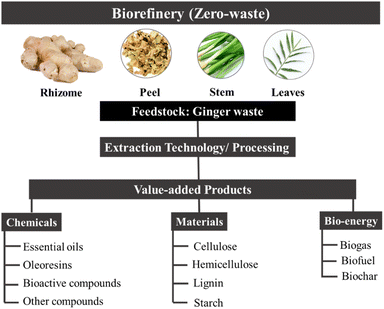 |
| Fig. 3 A conceptual zero-waste ginger biorefinery. | |
Composition and components of ginger waste
Depending on where the ginger is sourced, within an industrial processing context, ginger peel, ginger stem and leaves may also constitute ‘ginger waste’. However, normally ginger stems and leaves (GSL) are wastes generated after harvesting and have little or no commercial value but do comprise proteins and polysaccharides, e.g., sugar, starch, cellulose, hemicellulose and lignin.14,15Table 1 summarises the composition of ginger waste produced at the farm gate (stem and leaves) and during secondary processing, for example, oleoresin extraction.
Table 1 Type and composition (%) of ginger waste
Waste type |
Ash |
Protein |
Fat |
Starch |
Pectin |
Cellulose |
Sugar |
Hemicellulose and lignin |
References |
Spent ginger |
9.37 |
11.74 |
1.67 |
50.79 |
2.09 |
3.84 |
4.52 |
— |
11
|
Stem and leaves |
7.04 |
6.02 |
— |
— |
— |
48.48 |
52.14 |
31.50 |
14 and 15 |
Spent ginger waste (SGW) is the primary solid by-product of the ginger oleoresin industry. Approximately 90% of SGW is obtained from post extraction of ginger oleoresin. SGW comprises carbohydrates (starch, pectin, and cellulose), fats, proteins, free sugars and residual essential oils and oleoresins.11 The latter comprised approximately 4% by dry basis containing a mixture of zingiberene 1, zingerone 2, gingerols 3, shogaols 4, α-curcumene 5, β-bisabolene 6, β-sesquiphellandrene 7, and other oil compounds (Fig. 4).13
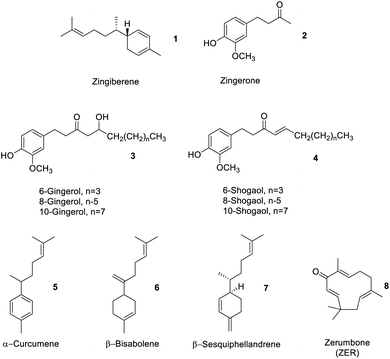 |
| Fig. 4 Examples of chemicals found in essential oils and oleoresins from ginger. | |
Strategies and methodologies for ginger waste utilisation
Extraction processes for recovery of oils and high value chemicals
Historical and/or traditional extraction technologies for the extraction of essential oils have been reliant on cold pressing or the use of hot solvents such as water (steam distillation), ethanol and hexane (either reflux or Soxhlet). The latter are energy-intensive processes and, in the case of hexane, under regulatory watch as it is a suspected reprotoxic chemical. Thus, there is a significant interest in finding effective green extraction methods for ginger oil, such as supercritical carbon dioxide (SC-CO2), subcritical water extraction (SWE), microwave-assisted extraction (MAE), and ultrasound-assisted extraction (UAE). Table 2 summarises a variety of green extraction methods for ginger waste and their resultant extractives.
Table 2 Summary of green extraction technologies for ginger oil recovery
Feedstock |
Extraction techniques |
Solvent |
Essential oil yield |
References |
Percentage of each component is calculated as the peak area of the analyte divided by the peak area of total ion chromatogram times 100.
The highest yield of 6-gingerol and 6-shogaol.
Yield on dry basis.
Yield on fresh basis.
The highest yield of zingiberene.
|
Spent ginger waste |
Soxhlet extraction |
Heptane |
4% W,a |
13
|
SC-CO2 extraction |
CO2 |
2.51% W,a |
|
CO2 – ethanol |
4.12% W,a |
Ginger pulp |
Subcritical water extraction |
Water |
0.50 mg g−1,b,d |
59
|
Ginger rhizome peel |
Subcritical water extraction |
Water |
1.06 mg g−1,b,d |
Fresh rhizome ginger |
Solvent-free microwave extraction |
— |
1.12% W,c |
18
|
Fresh ginger |
Microwave assisted hydro-distillation |
Water |
1.71% W,c |
19
|
Fresh ginger |
Microwave-assisted extraction |
1-Decyl-3-methylimidazolium bromide |
0.72% W,c |
24
|
Red ginger rhizome pulp |
Enzymatic extraction |
Isolated cow rumen enzymes |
26.28%,d,e |
16
|
Gao et al. recently compared the conventional Soxhlet extraction of spent industrial ginger waste using hot heptane (Soxhlet) with respect to supercritical carbon dioxide (SC-CO2) and SC-CO2-EtOH as a greener methodology. Heptane was used in preference to hexane due to its reprotoxic concerns but also because the polarity of carbon dioxide mimics that of heptane. Carbon dioxide is widely used in industry as a green solvent because it leaves no residual trace solvent in the products or post-extraction residues, has high diffusivity and solvation capacity, can be recycled and is food grade approved – notably already in use in the industry for decaffeination of coffee. The addition of up to 10% by weight of ethanol increases polarity such that more polar compounds can be extracted. Interestingly, the yield of ginger oil from Soxhlet extraction and SC-CO2-EtOH extraction were similar (approximately 4% wt), but the SC-CO2 and SC-CO2-EtOH techniques extracted more compounds beyond zingiberene 1, gingerols 3, shogaols 4, α-curcumene 5, β-bisabolene 6 and β-sesquiphellandrene 7.13 The high diffusivity and solvation power of SC-CO2 and SC-CO2-EtOH compared to those of hot heptane extraction enabled a richer fraction of products to be isolated. Biocatalysis or enzymes have also been used to isolate essential oils. For example, Handayani et al. utilized enzymes from cow rumen to isolate oils rich in zingiberene 1 from red ginger rhizomes. Time was the key factor affecting yield in the enzymatic extraction. The optimal time (5 days) allowed cow rumen enzymes to hydrolyze polysaccharides in the cell wall, resulting in more isolated ginger oil (26.28%).16
In another work, Das et al. compared and contrasted the effect of UAE with respect to MAE of ginger rhizome peel on the total phenolic content (TPC, see Table 3) and antioxidant activity (2,2-diphenyl-1-picrylhydrazyl, DPPH). The MAE methodology resulted in higher TPC and antioxidant activity compared to UAE and cold maceration of ginger rhizome peel and rhizome.3 Polar solvents such as acetone, ethyl acetate and ethanol–water showed higher extraction capabilities. However, a range of non-green and undesirable solvents, such as chloroform and petroleum ether, have also been reported for such applications. These, therefore, should not be taken further within green biorefinery scenarios.
Table 3 Summary of extraction techniques with respect to total phenolic, total terpenoid and total flavonoid content
Extraction technique |
Solvent |
Total phenolics (mg GAE per g) |
Total terpenoids (mg g−1) |
Total flavonoids (mg Q g−1) |
Cold maceration |
Petroleum ether |
0.30 |
13.40 |
0.31 |
Chloroform |
2.00 |
12.63 |
2.63 |
Ethyl acetate |
23.92 |
7.17 |
4.17 |
Acetone |
15.92 |
2.63 |
3.63 |
Ethanol–water |
21.92 |
2.53 |
4.17 |
MAE |
Petroleum ether |
1.18 |
12.86 |
1.86 |
Chloroform |
4.58 |
12.82 |
2.82 |
Ethyl acetate |
25.25 |
7.10 |
6.10 |
Acetone |
20.25 |
2.82 |
5.82 |
Ethanol–water |
35.81 |
3.10 |
7.45 |
UAE |
Methanol–water |
0.72 |
15.18 |
1.84 |
Chloroform |
3.81 |
13.02 |
3.01 |
Ethyl acetate |
24.44 |
9.91 |
5.91 |
Acetone |
21.44 |
3.01 |
4.01 |
Ethanol–water |
30.44 |
3.91 |
6.91 |
Interestingly, the ginger essential oils obtained from MAE and solvent-free MAE were richer in oxygenated and monoterpene compounds, which resulted in enhanced antibacterial activities.17,18 Argo et al. showed that the microwave power and material-solvent (w/w) ratio significantly affected the ginger essential oil yield. The highest yield of essential oil (1.71%) was obtained at 600 W with 1
:
8 (w/w) material-solvent ratio,19 bettering that of Yingnham and Brantner, who reported a yield of 1.12% wt (microwave power, 700 W; irradiation time, 70 minutes).18
Although 6-gingerol 3 and 6-shogaol 4 are structurally similar molecules, and both have beneficial bioactive properties, 6-shogaol 4 has stronger bioactivity. Thus, processes that isolate or enrich the concentration of shogaols 4 from ginger may represent interesting medicinal applications. Yulianto et al. reported the hydrothermal extraction of ginger rhizome powder using subcritical water (SWE), which increased the content of shogaols 4, compared to that using conventional extraction processes such as Soxhlet extraction, percolation, supercritical fluid extraction, MAE, and UAE.20 Subcritical water behaves as a less polar solvent with increasing temperature, whose acidity also increases. Gingerols 3 can be converted into shogaols 4 at high temperatures and low pH. Dalasso et al. recently reported on the effect of production processes, including extraction and drying processes, on bioactive compounds from ginger. Low-temperature processes tend to give extracts rich in phenolics 2 and gingerols 3. These also produce liquids with stronger antioxidant activities compared to high temperature, acidic, processes in which gingerols 3 are converted to shogaols 4, as previously described, thus enhancing the concentration of the latter.21 In contrast, Švarc-Gajić et al. successfully extracted sugars, diols, phenolic acids, phenolic compounds, peptides, terpenoids, and other organic compounds as extracts using SWE at 150 °C. The antimicrobial and cytotoxic activities of subcritical water extracts showed higher anti-inflammatory, anti-carcinogenic, chemo-protective and antifungal activities with respect to those of conventional water extraction (steam distillation or reflux).22
Kalantari et al. have reviewed the isolation of zerumbone (ZER) 8 from ginger rhizomes using a variety of green extraction methods (solvent extraction, hydrodistillation, supercritical fluid extraction, Soxhlet extraction and pressurized liquid extraction). ZER 8 has antioxidant, anti-inflammatory anti-proliferative activity showing selective toxicity to various cancer lines.23
Guo et al. reported probably the first use of water-miscible ionic liquids (IL) (1-hexyl-3-methylimidazolium bromide ([C6MIM]Br), 1-octyl-3-methylimidazolium bromide ([C8MIM]Br), 1-decyl-3-methylimidazolium bromide ([C10MIM]Br), 1-decyl-3-methylimidazolium chloride ([C10MIM]Cl), and 1-decyl-3-methylimidazolium toluene sulfonate ([C10MIM]ToS)) coupled with microwave-assisted extraction (ILMAE) for the rapid extraction of gingerols 3 and shogaols 4 from ginger. The ionic liquid [C10MIM]Cl gave the maximum essential oil yield (0.72%).24 Similarly, Kou et al. extracted polysaccharides and gingerols 3 (1.22%) from dried ginger using ionic liquids but this time coupled with UAE. Compared to conventional extraction methodologies, ionic liquid-UAE process reduced the extraction time considerably without compromising the yields of ginger polysaccharides and oils.25
Nasti et al. recently reported the extraction of gingerols 3 and shogaols 4 using dichloromethane from ginger lees obtained from the alcoholic fermentation of ginger. The fermentation process did not affect the isolation of such compounds. The extracted compounds from ginger lees waste were stereoselectively reduced using enzymes to afford ginger alcohols with high enantiomeric purity for use in flavours and fragrances.26 However, the use of dichloromethane is discouraged, and greener solvents and processes, as discussed earlier, should be considered.
Extraction of other molecules
In addition to essential oils, oleoresins and some phenolic compounds described earlier, Table 4 summarizes the extraction of potentially high-value compounds from ginger waste, such as sugars, uronic acid, proteins, phenolics and starch. Gao et al. reported the hydrothermal microwave-assisted extraction of starch, sugars, and small molecules (e.g., levoglucosan 9, 5-hydroxymethylfurfural (5-HMF) 10, furfural 11, formic acid 12, acetic acid 13 and lactic acid 14, Fig. 5) from spent industrial ginger waste. Hydrothermal microwave treatment between 120 °C and 200 °C for 30 min afforded a starch yield of approximately 50% by wt. The yield of small molecules increased with temperature, whilst the yield of sugar (e.g., glucose and xylose) decreased with increasing temperature due to thermal degradation, converting into 5-HMF 10 and furfural 11.13
Table 4 Summary of potential high value chemicals derived from ginger waste valorisation
Feedstock |
Extraction technique |
Yield (%) |
Chemical composition (%) |
References |
Sugars |
Uronic acid |
Proteins |
Total phenols |
Starch yield.
|
Ginger pomace |
Hot water extraction |
12.13 |
76.42 |
4.42 |
8.33 |
— |
27
|
Ultrasound-assisted extraction |
16.62 |
82.53 |
6.09 |
5.65 |
— |
Ginger stem and leaves |
Hot water extraction |
6.83 |
37.85 |
3.29 |
3.25 |
0.82 |
60
|
Ultrasound-assisted extraction |
8.29 |
44.65 |
3.85 |
1.94 |
0.95 |
Alkaline extraction |
11.38 |
48.43 |
5.64 |
3.59 |
0.99 |
Enzyme-assisted extraction |
8.13 |
41.89 |
3.99 |
2.95 |
1.53 |
High-pressure ultrasonic extraction |
9.82 |
58.69 |
5.32 |
4.87 |
1.28 |
28
|
Ultrasound extraction (no pressure) |
8.22 |
42.28 |
4.33 |
5.55 |
1.16 |
Spent ginger waste |
Hydrothermal microwave hydrolysis |
48.6a |
— |
— |
— |
— |
13
|
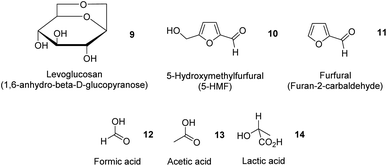 |
| Fig. 5 Exemplar chemicals isolated from hydrothermal MAE of spent industrial ginger waste. | |
Chen et al. have explored the hot water ultrasonic-assisted extraction (UAE) of polysaccharides from ginger pomace. The combination of hot water and ultrasounds afforded a higher polysaccharide yield compared to individual processes. However, hot water alone provided larger molecular weight saccharides and higher protein content in the extracts. The UAE extracts resulted in more potent antioxidant activity (DPPH, hydroxyl and superoxide radical scavenging).27 Recently, Chen et al. reported the high-pressure ultrasonic extraction (HUE) and pressure-free ultrasonic extraction (UAE) of ginger stems and leaves. The HUE and UAE were performed at 62 °C for 44 min and 71 °C for 53 min, providing optimal yields of polysaccharides of 9.82% and 8.22%, respectively. The main extracts of HUE and UE from ginger stems and leaves were neutral sugars. The HUE provided extracts with lower molecular weights, higher sugar contents, higher uronic acid, higher sulfate radical, and stronger antioxidant activities than UAE.26 The dual and triple-ultrasonic extraction (UAE) of ginger stems and leaves to obtain polysaccharides were also studied. The yield of polysaccharides obtained from triple UAE was 10.50%, which is higher than that of dual UAE (9.74%). The triple UAE provided liquids with higher sugar, uronic acid, and sulfate radical contents, stronger antioxidant activities, and better functional properties. On the contrary, the dual UE provided extracts containing polysaccharides with larger molecular weights.14
Future perspectives: applications
Potential and emerging applications beyond the isolation of essential oils and oleoresins for existing global markets (see Fig. 1) are considered in this section. Opportunities range, for example, from exploiting cellulose itself, to carbonaceous materials to packaging. Although some examples may not use ginger waste per se, they provide an opportunity to horizontally scan potential applications.
Defibrillated and nanocelluloses
The structure of cellulose is well-known, comprised of repeating β-D-glucose moieties covalently linked via 1,4-glycosidic bonds as shown in Fig. 6. Cellulose contains both crystalline and amorphous regions dependent upon the packing arrangement of individual strands, which are held together via extensive intra- and inter-molecular hydrogen bonding rendering it insoluble in cold water. Cellulose in this form is often regarded as passive, but through chemical and physical manipulation, the structure of cellulose can be altered, making it an active material (defibrillated and nanocelluloses) with functional properties. Currently, there is a significant interest in producing nanocelluloses from pulp and paper wastes for applications in sensors, lightweight and high strength materials, packaging, cosmetics and pharmaceuticals. A complete discussion on nanocellulose is out of scope within this review and the reader is alerted to recent studies in the literature.29–31
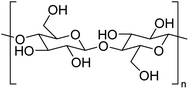 |
| Fig. 6 The chemical structure of cellulose. | |
Defibrillation of celluloses and production of nanocelluloses from ginger waste are still in their infancy, with very few recent publications (Table 5). However, this is an essential niche area of research to consider, given the emerging importance of nanocellulose as a biomaterial. Jacob et al. reported on the production of nanofibres from spent ginger waste via acid hydrolysis and high-pressure homogenisation,32 with these materials then being used for remediation of Cu(II) from wastewater (see later). Zhou et al. isolated cellulose from ginger stalks using potassium hydroxide (KOH) and nitric acid–ethanol (NAE) treatments. The resultant cellulose yielded a crystallinity index of >50%.33 However, both Jacob et al. and Zhou et al. used harsh chemical conditions, generating considerable amounts of acidic and basic aqueous waste streams. Alternatively, Gao et al. reported on the production of porous microfibrillated cellulose (MFC) in the absence of any harsh chemical or extensive mechanical processing. They used acid-free hydrothermal microwave processing (120–200 °C, 30 min) to afford MFCs with pore diameters between 16–20 nm. The MFC yield decreased from 21.6% to 7.8% when the extraction temperature was increased. Conversely, the crystallinity index of the MFCs increased by up to 20% due to the leaching of amorphous cellulose and degradation of hemicellulose on increasing the processing temperature. The resultant materials were able to form hydrogels and thus can foresee applications as rheology modifiers.13
Table 5 Summary of a recent review of ginger cellulose extraction form ginger waste
Feedstock |
Valorisation technique |
Highlights |
References |
Spent ginger waste |
NaOH pre-treatment, NaCl bleaching, acid hydrolysis, ad high-pressure homogenisation |
• First time report of ginger nanofibre extraction from spent ginger waste using acid hydrolysis and high-pressure homogenisation |
32
|
• Ginger nanofibres width ranged between 130 and 200 nm |
|
Hydrothermal microwave hydrolysis |
• First time report of ginger microfibrillated cellulose via hydrothermal microwave processing without any pre-treatment |
13
|
• Microfibrillated cellulose and nanocellulose were produced with short time microwave processing (only 30 min) and the temperature ranged between 120 and 200 °C |
Ginger stalk |
KOH treatment and nitric acid–ethanol treatment |
• Ginger cellulose extracted from these two treatments have low lignin and hemicellulose content |
33
|
• Ginger cellulose with a high crystallinity index (more than 50%) was produced |
Anti-bacterial and anti-fungal materials
From a resource efficiency perspective and end of life point of view, the use of natural oils and materials derived from wastes as antibacterial and antifungal agents is more favourable than using metals and/or synthetically derived bactericides. Lei et al. reported on the production of anti-bacterial ginger essential oil-palygorskite (GEO-PGS) composites. These authors found that the inclusion of approximately 19% ginger essential oil in the GEO-PGS composite boosted the thermal and chemical (acid and base) resistances in addition to enhanced antibacterial activities compared to those of a palygorskite (PGS) alone composite.34 Noshirvani et al. showed that the inclusion of ginger essential oil into chitosan-carboxymethyl cellulose films improved their antifungal properties. Ginger essential oils gave much better fungal control than cinnamon oil infused films.35 Similarly, Fahrina et al. showed that adding ginger essential oils to polyvinylidene fluoride (PVDF) membranes enhanced their biofouling resistance.36 Jacob et al. discovered that the direct incorporation of 5% by wt ginger cellulosic fibres (100–200 nm width) into chitosan-PVA composites improved their mechanical strength and antibacterial activity against Bacillus cereus, Escherichia coli, Staphylococcus aureus and Salmonella typhimurium.37
Oluba et al. recently reported the inclusion of a 5% w/v ginger starch solution in the production of keratin (obtained from waste chicken feathers) to produce a keratin-starch biocomposite film. The film was plasticised with glycerol and the mechanical properties were dependent on the starch
:
keratin ratio. Such an improvement in antimicrobial activity was linked to reduced moisture ingress, but whether this is due to keratin, starch, or both is still unclear.38
Environmental remediation agents
Suitably modified ginger wastes have significant potential for use as environmental remediation agents, especially in wastewater treatment. There is a global need for readily available drinking water. As stated earlier, Jacob et al. defibrillated waste ginger cellulose to afford fibres (100–200 nm width), which were then blended into magnetic ginger nanofibre composites. The resultant composite exhibited enhanced adsorption of Cu(II) ions from the contaminated water supply in comparison to their nonmagnetic counterpart composites.39
Both Zhang et al. and Kaur et al. have reported on the production of carbonaceous materials from ginger waste for wastewater remediation. Zhang et al. carbonised ginger straw waste at 400 °C into a porous material with a high adsorption capacity (98.5 mg g−1) and high adsorption rate (63.4 mg g−1 min−1), capable of removing methylene blue. The material could be reused more than five times with minimal loss in adsorption capacity (from 97.0 to 83.7 mg g−1) for methylene blue.40 Kaur et al. produced activated carbon from ginger peel waste to remediate calcium ions in wastewater with an adsorption capacity of 77.21 mg g−1.41 In another work, Liu et al. produced activated carbon from ginger stems. The optimal processing conditions for carbonisation were 700 °C for 6 h, while the optimal activation took place at 800 °C for 1 h with KOH (1
:
4 KOH
:
hydrochar). Under such conditions, the activated carbon had high adsorption capabilities and a BET surface area of 660 m2 g−1.42
Supercapacitors
Energy storage continues to be a global grand challenge. Carbonaceous materials have been considered for use as supercapacitors for some time. There is significant recent interest in using ginger waste for such purposes. Li et al. reported the chemical-free pyrolytic synthesis (700 °C, 2 h) of porous carbon from ginger straw. The resultant activated carbon possessed a specific capacitance as high as 88% after 6000 cycles and good electric double-layer performance and relatively high energy density.43 Furthermore, Zheng et al. showed that such materials could be used for high-performance supercapacitors and Li-ion capacitors with high-performance capacity (82.7%) still present after 10
000 cycles.44 Similarly, Liangshuo et al. produced porous activated carbon derived from waste ginger slices. The material showed a capacitance retention of 98.95% after 5000 cycles.45 Gopalakrishnan et al. reported unique hierarchical worm-like porous carbon nanosheets from ginger waste, with the nanosheets exhibiting excellent rate capability and high cycling stability (95%) after 10
000 cycles.46
Films and packaging
Non-biodegradable petroleum-based polymers used in packaging, coatings and films are a modern-day environmental problem. Materials derived from renewable feedstocks, for example, ginger waste, offer a potential solution to this dilemma. Driven by this challenge, Abral et al. recently reported synthesising transparent films derived from ginger nanofibres obtained via a chemical treatment combined with ultrasonication. The resultant films possessed outstanding optical clarity with a light transmittance of 83% (650 nm) and high thermal resistance to heat degradation (353 °C). However, the films possessed mediocre water resistance and antimicrobial properties at higher processing temperatures.47,48 Sariningsih et al. reported the production of a ginger starch
:
chitosan (9
:
1) edible film with high mechanical strength, elasticity, antibacterial properties and good (43%) water resistance when a ginger starch: chitosan (optimum) ratio of 9
:
1 was used.49
Microencapsulation is a new approach for maintaining the freshness of food during packaging. In this regard, Ban et al. microencapsulated ginger essential oil with chitosan and sodium carboxymethyl cellulose (CMC) to produce potential packaging materials with excellent thermal stability.50 Similarly, Maulidina et al., exploited the antioxidant properties of ginger essential oil to produce materials comprising chitosan, ginger essential oil and oil palm trunk waste fibres.51
Use of ginger waste in catalysis
Catalysis plays an important role in industrial chemistry, and there are many reports addressing the use of renewable feedstocks as catalytic supports. As for many other biomasses, ginger waste has been used as a porous support in the production of heterogeneous catalysts. Yu et al. first carbonised ginger straw (350 °C, 60 min) and then sulfonated (concentrated H2SO4, 105 °C) the hydrochar produced to afford a heterogeneous acid catalyst. In comparison with Amberlyst-15, the ginger straw-derived acid catalyst was able to esterify oleic acid more efficiently (up to 93% conversion) with excellent re-usability (up to 5 cycles, achieving 66% yield in the 5th cycle).12 In another work, John et al. used carbonised or activated ginger leaves as a transesterification base-catalyst for the production of biodiesel from sunflower and methanol. Ginger leaves were either calcined or activated with KOH or with NaOH. The KOH-activated ginger hydrochar proved the best material, giving a 93.83% yield (1.6 wt%, 90 min) of biodiesel from one step transesterification of sunflower oil, using a methanol to oil ratio of 6
:
1.52
Miscellaneous applications
Antioxidants in fuels and lubricants.
As discussed previously, ginger extract is very well known for having high antioxidant activity. This can be attributed to the presence of phenolic compounds, notably zingerone 2, gingerols 3 and shogaols 4. Phenolics are noted for their antioxidant activity via the mechanism of the O–H bond being radically cleaved by peroxyl and alkoxyl radicals with the subsequent radical being resonance stabilised across the aromatic ring. A second radical can then subsequently attack at the para-position to form a stabilised quinone (see Fig. 7).53
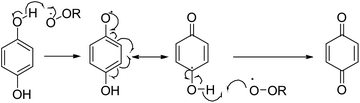 |
| Fig. 7 The radical scavenging mechanism for phenolic antioxidants. | |
In fuels and lubricants for the automotive industry, synthetic antioxidants, such as Irganox L107 (Fig. 8) are typically further stabilised by the addition of electron-donating groups at the ortho-position (typically tert-butyl) with an alkyl group at the para-position to both act as a leaving group and to improve oil solubility. The structure of the gingerols 3 and shogaols 4 mimic this structure well, with the –OMe groups acting as the electron donors in place of the tert-butyl groups. Devi et al. exploited this property to improve the resistance to oxidation of biodiesel derived from Indian beech (Pongamia pinnata). At a minimum concentration of 250 ppm, the ginger extract proved effective as an antioxidant for biodiesel, meeting the standard specifications for biodiesel oxidation stability in both American (ASTM D-6751) and European (ENE14214) test standards.3
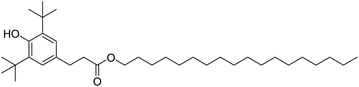 |
| Fig. 8 The structure of Irganox L107, a typical synthetic phenolic antioxidant. | |
Production of biofuels.
There are limited publications exploring the conversion of ginger waste into biofuels (solid, liquid and gaseous). One of the earliest reports on the conversion of ginger into bioethanol was provided by Konar et al., who exploited the high carbohydrate (sugar and starch) content of ginger. Acid hydrolysis followed by enzymatic fermentation gave a fermentation efficiency of 81.53% and a bioethanol yield as high as 43.4 g L−1.11 However, as many researchers have carbonised or have produced hydrochars from ginger waste, these could also be considered solid biofuels. In pioneering research, Gao et al. extracted biogas, bio-oil, and biochar from oil-free ginger waste via conventional microwave pyrolysis at a temperature ranging from 220 °C to 280 °C for 9 min. The biogas, bio-oil and biochar were 15%, 33%, and 77%, respectively.13 A comparison between the higher heating values (HHV) of ginger and ginger char with that of other biomass-derived chars is shown in Fig. 9. The microwave pyrolysis of ginger (HHV, 16–17 MJ kg−1) afforded an energy densified ginger biochar (23–24 MJ kg−1), with this material being reasonably comparable to other biomass biochar types, including low quality hard black coal (approx. 24 MJ kg−1).
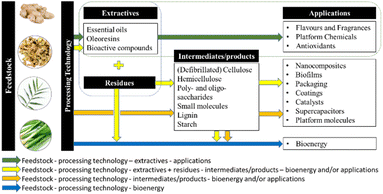 |
| Fig. 9 Summary of valorisation strategies for a zero-waste ginger biorefinery. | |
Future fuel: green hydrogen from sugars.
This decade is transitioning from fossil fuels to renewable and sustainable energy sources, with hydrogen energy expected to contribute to 10% of worldwide energy consumption by 2050.54 However, the green hydrogen production from overall renewable sources is only 5% (e.g., photocatalytic water splitting), where the rest (∼95%), the grey hydrogen, comes from fossil fuels.55
In the case of spent ginger, soluble sugars (e.g. from starch, hemicellulose, and pectin) make up a relatively large proportion of the composition of up to 50% by weight. These compounds have a high potential for green hydrogen by photocatalytic sugar reforming. Unfortunately, research on starch or soluble sugars from ginger waste via photocatalytic hydrogen production could not been found at the time of writing. Theoretically, photocatalytic soluble sugar reforming (E° = 0.001 V) to H2 and CO2 is less energy-intensive and faster than water splitting (E° = 1.23 V) that is possible under visible light.56
Taylor et al. reported that starch photo-reforming by CdS/CdOx QDs, with a band gap of 2.4 eV under alkaline conditions, obtained a hydrogen yield of 462 μmol g−1.57 Kurenkova et al. also reported that Cd0.7Zn0.3S (2.55 eV) photocatalytic starch conversion yielded the highest rate of 730 μmol h−1 g−1 hydrogen.58
Conclusions
This review has highlighted the growth of ginger and its extractives, primarily essential oils and oleoresins, in a variety of established, global, and high-value markets, such as flavours, fragrances and medicines. With the current and future expansion and development of such industries, it is clear that more ginger waste will be produced worldwide. As a result, ginger waste should stop being considered waste but a renewable feedstock with potential applications beyond just those well-established, instead. Inspired by sustainability and green practices, we picture ginger waste as a promising feedstock for developing a zero-waste biorefinery with multiple outputs and applications as outlined in Fig. 9.
However, there are several considerations to establishing such a biorefinery scenario for sustainable ginger waste utilisation.
Geographical availability and location
As Asia is the major grower of ginger, any major or large-scale biorefinery operating on several thousand tons of feedstock should be based in this region to avoid transport costs and embedded carbon. However, smaller agile ginger waste semi-biorefineries could be envisaged alongside large-scale ginger essential oil or oleoresin extraction industries in the context of industrial symbiosis.
Type of feedstock
Ginger rhizomes or stem and leaves. Ginger rhizomes, in preference to stems and leaves, appear to be the best choice of feedstock both in terms of tonnage and logistics. At present, there is no centralised collection of leaves and stems. Their economic value as a standalone feedstock is limited, and the best recommendation would be to co-mix ginger rhizomes with leaves and stems, where necessary.
Processing technology
Essential oil and oleoresin extraction industries are well-established, including those using green methodologies, for example, supercritical carbon dioxide. The process technology should avoid the use of restricted solvents or substances of very high concern. Newer, greener technologies such as microwaves, will require infrastructure investment, and thus the output has to be of higher value. The scale and logistics of the technology need to be considered, i.e., one single processor, continuous or batch and/or multiple processors.
Outputs and applications
Beyond existing markets, outputs and applications that promote a bio-based economy need to be envisioned. Our review has shown several potential applications and opportunities. Final outputs will be dictated by a full techno-economic, as well as a full life cycle assessment. A zero-waste biorefinery must be both green and sustainable with transparent evidence of resource utilisation, energy and water needs and any impact on biodiversity.
As closing remarks, this review shows that ginger waste valorisation is an emerging area. However, there are areas for unique opportunities yet to be explored. For example, (bio)hydrogen production is a global grand challenge. Ginger waste could be considered a direct feedstock for (bio)hydrogen production via dark fermentation or microbial strategies. Ginger waste gasification and/or the catalytic steam reforming of pyrolysis ginger bio-oil might be interesting research areas to produce bio(hydrogen) and syngas from ginger waste. The circularity of ginger waste products also needs to be considered, especially when they are ‘trapped’ in the form of challenging to recycle composites. There are no publications in the area of full life cycle assessment for any product emanating from ginger waste. This publication is the first to consolidate the opportunities of utilising ginger waste as a renewable feedstock within the context of a biorefinery for a sustainable 21st century.
Conflicts of interest
There are no conflicts to declare.
Acknowledgements
Natthamon Inthalaeng would like to express her sincere thanks to the Development and Promotion of Science and Technology Talents Project (DPST) scholarship (DPST582042), Royal Thai Government for the award to study for a PhD at University of York under the supervision of Professor Avtar S Matharu and Dr Thomas Dugmore. Javier Remón is grateful to the Spanish Ministry of Science, Innovation and Universities for his Juan de la Cierva (JdC) fellowship (IJC2018-037110-I).
Notes and references
- F. R. Procopio, M. C. Ferraz, B. N. Paulino, P. J. do Amaral Sobral and M. D. Hubinger, Trends Food Sci. Technol., 2022, 122, 123–139 CrossRef CAS
.
- A. Shukla, S. N. Naik, V. V. Goud and C. Das, Ind. Crops Prod., 2019, 130, 352–362 CrossRef CAS
.
- A. Devi, V. K. Das and D. Deka, Fuel, 2017, 187, 306–314 CrossRef CAS
.
-
FAO Database, https://www.fao.org/faostat/, accessed 16 March 2022 Search PubMed.
-
Ginger market in Europe, https://www.cbi.eu/market-information/spices-herbs/dried-ginger/market-potential, accessed 16 March 2022 Search PubMed.
-
World oleoresins market, https://www.marketdataforecast.com/market-reports/oleoresins-market, accessed 16 March 2022 Search PubMed.
-
World organic spices market, https://www.marketdataforecast.com/market-reports/organic-spices-market, accessed 16 March 2022 Search PubMed.
-
Ginger oil market, https://www.researchandmarkets.com/reports/5215214/ginger-oil-market-forecasts-from-2020-to-2025, accessed 1 June 2022 Search PubMed.
- H. Gan, E. Charters, R. Driscoll and G. Srzednicki, Horticulturae., 2017, 3(1), 13 CrossRef
.
- T. Wiastuti, L. U. Khasanah, W. A. Kawiji, G. J. Manuhara and R. Utami, IOP Conf. Ser.: Mater. Sci. Eng., 2016, 107, 012057 Search PubMed
.
- E. M. Konar, S. M. Harde, L. D. Kagliwal and R. S. Singhal, Ind. Crops Prod., 2013, 42, 299–307 CrossRef CAS
.
- H. Yu, Y. Cao, H. Li, G. Zhao, X. Zhang, S. Cheng and W. Wei, Renewable Energy, 2021, 176, 533–542 CrossRef CAS
.
- Y. Gao, M. Z. Ozel, T. Dugmore, A. Sulaeman and A. S. Matharu, J. Hazard. Mater., 2021, 401, 123400 CrossRef CAS PubMed
.
- X. Chen, Z. Wang and J. Kan, Food Biosci., 2021, 42, 101166 CrossRef CAS
.
- H. M. Zendrato, Y. S. Devi, N. Masruchin and N. J. Wistara, J. Korean Wood Sci. Technol., 2021, 49, 287–298 CrossRef
.
- D. Handayani, R. Amalia, M. Yulianto, I. Hartati and Murni, Int. J. Technol., 2018, 9, 455–463 CrossRef
.
- P. H. D. Nguyen, K. T. Le Nguyen, T. T. N. Nguyen, N. L. Duong, T. C. Hoang, T. T. P. Pham and D. V. N. Vo, J. Food Process Eng., 2019, 42, 1–10 Search PubMed
.
- B. Yingngam and A. Brantner, J. Essent. Oil Res., 2018, 30, 409–420 CrossRef CAS
.
- B. D. Argo, M. B. Hermanto, D. W. Andriani and J. S. Rosadhani, IOP Conf. Ser.: Earth Environ. Sci., 2020, 542, 012002 CrossRef
.
- M. E. Yulianto, R. Amalia, V. Paramita, I. Hartati and Q. A. K. Nisa, IOP Conf. Ser.: Mater. Sci. Eng., 2020, 771, 012039 CrossRef CAS
.
- R. R. Dalsasso, G. A. Valencia and A. R. Monteiro, Int. Food Res. J., 2022, 154, 111043 CrossRef CAS PubMed
.
- J. Švarc-Gajić, A. Cvetanović, A. Segura-Carretero, I. B. Linares and P. Mašković, J. Supercrit. Fluids, 2017, 123, 92–100 CrossRef
.
- K. Kalantari, M. Moniri, A. B. Moghaddam, R. A. Rahim, A. Bin Ariff, Z. Izadiyan and R. Mohamad, Molecules, 2017, 22, 1645 CrossRef PubMed
.
- J. B. Guo, Y. Fan, W. J. Zhang, H. Wu, L. M. Du and Y. X. Chang, J. Food Compos. Anal., 2017, 62, 35–42 CrossRef CAS
.
- X. Kou, Y. Ke, X. Wang, M. R. T. Rahman, Y. Xie, S. Chen and H. Wang, Food Chem., 2018, 257, 223–229 CrossRef CAS PubMed
.
- R. Nasti, I. Bassanini, E. E. Ferrandi, F. Linguardo, S. Bertuletti, M. Vanoni, S. Riva, L. Verotta and D. Monti, ChemBioChem, 2022, 23(8), e202200105, DOI:10.1002/cbic.202200105
.
- G. Tang Chen, B. Yuan, H. Xiang Wang, G. Hong Qi and S. Jie Cheng, Int. J. Biol. Macromol., 2019, 139, 801–809 CrossRef PubMed
.
- X. Chen, Z. Wang, Q. Yang and J. Kan, J. Food Meas. Charact., 2022, 16, 85–101 CrossRef
.
- R. M. Cherian, A. Tharayil, R. T. Varghese, T. Antony, H. Kargarzadeh, C. J. Chirayil and S. Thomas, Carbohydr. Polym., 2022, 282, 119123 CrossRef CAS PubMed
.
- M. B. Noremylia, M. Z. Hassan and Z. Ismail, Int. J. Biol. Macromol., 2022, 206, 954–976 CrossRef CAS PubMed
.
- D. Pradhan, A. K. Jaiswal and S. Jaiswal, Carbohydr. Polym., 2022, 285, 119258 CrossRef CAS PubMed
.
- J. Jacob, J. T. Haponiuk, S. Thomas, G. Peter and S. Gopi, Fibers, 2018, 6, 79 CrossRef CAS
.
- C. Zhou, X. Song, S. Wang and F. Chen, PBM Ser., 2017, 2(2), 1–7 Search PubMed
.
- H. Lei, Q. Wei, Q. Wang, A. Su, M. Xue, Q. Liu and Q. Hu, Mater. Sci. Eng., C, 2017, 73, 381–387 CrossRef CAS PubMed
.
- N. Noshirvani, B. Ghanbarzadeh, C. Gardrat, M. R. Rezaei, M. Hashemi, C. Le Coz and V. Coma, Food Hydrocolloids, 2017, 70, 36–45 CrossRef CAS
.
- A. Fahrina, N. Arahman, S. Mulyati, S. Aprilia, N. I. M. Nawi, A. Aqsha, M. R. Bilad, R. Takagi and H. Matsuyama, Polymers, 2020, 12, 1–11 CrossRef PubMed
.
- J. Jacob, G. Peter, S. Thomas, J. T. Haponiuk and S. Gopi, Int. J. Biol. Macromol., 2019, 129, 370–376 CrossRef CAS PubMed
.
- O. M. Oluba, C. F. Obi, O. B. Akpor, S. I. Ojeaburu, F. D. Ogunrotimi, A. A. Adediran and M. Oki, Sci. Rep., 2021, 11, 1–11 CrossRef PubMed
.
- J. Jacob, G. Peter, S. Thomas, J. T. Haponiuk and S. Gopi, Mater. Today Commun., 2019, 21, 100690 CrossRef CAS
.
- W. Zhang, H. Li, J. Tang, H. Lu and Y. Liu, Molecules, 2019, 24, 1–8 Search PubMed
.
- C. Kaur, T. Roy, S. Das, R. Gupta and T. Pramanik, Biomass Convers. Biorefin., 2021 DOI:10.1007/s13399-021-01806-1
.
- J. Liu, X. Song, S. Gao and F. Chen, Pap. Biomater., 2019, 4, 45–50 CAS
.
- J. Li, J. Wang, K. Han, J. Qi, M. Li, Z. Teng and M. Wang, Int. J. Electrochem. Sci., 2019, 14, 10289–10305 CrossRef CAS
.
- Y. Zheng, H. Wang, S. Sun, G. Lu, H. Liu, M. Huang, J. Shi, W. Liu and H. Li, Sustainable Energy Fuels, 2020, 4, 1789–1800 RSC
.
- L. Liangshuo, Q. Lin, L. Xinyu, D. Ming and F. Xin, Optoelectron. Adv. Mater., Rapid Commun., 2020, 14, 548–555 Search PubMed
.
- A. Gopalakrishnan, T. D. Raju and S. Badhulika, Carbon, 2020, 168, 209–219 CrossRef CAS
.
- H. Abral, J. Ariksa, M. Mahardika, D. Handayani, I. Aminah, N. Sandrawati, A. B. Pratama, N. Fajri, S. M. Sapuan and R. A. Ilyas, Food Hydrocolloids, 2020, 98, 105266 CrossRef CAS
.
- H. Abral, J. Ariksa, M. Mahardika, D. Handayani, I. Aminah, N. Sandrawati, S. M. Sapuan and R. A. Ilyas, Polym. Test., 2020, 81, 106186 CrossRef CAS
.
- N. Sariningsih, Y. P. Putra, W. P. Pamungkas and T. Kusumaningsih, IOP Conf. Ser.: Mater. Sci. Eng., 2018, 333, 012083 CrossRef
.
- Z. Ban, J. Zhang, L. Li, Z. Luo, Y. Wang, Q. Yuan, B. Zhou and H. Liu, Food Chem., 2020, 306, 125628 CrossRef CAS PubMed
.
- B. Maulidna, T. Wirjosentono and L. Marpaung, Case Stud. Therm. Eng., 2020, 18, 100606 CrossRef
.
- M. John, M. O. Abdullah, T. Y. Hua and C. Nolasco-Hipólito, Renewable Energy, 2021, 168, 815–828 CrossRef CAS
.
-
E. T. Denisov and I. B. Afanas'Ev, Oxidation and Antioxidants in Organic Chemistry and Biology, CRC Press, 1st edn, 2005, DOI:10.1201/9781420030853
.
-
IEA, Global Hydrogen Review 2021, Paris, 2021, https://www.iea.org/reports/global-hydrogen-review-2021 Search PubMed
.
-
H. Phoumin, The Role of Hydrogen in ASEAN's Clean Energy Future, 2021, https://www.nbr.org/wp-content/uploads/pdfs/publications/asia_edge_phoumin_aug21.pdf Search PubMed
.
- M. F. Kuehnel and E. Reisner, Angew. Chem., Int. Ed., 2018, 57, 3290–3296 CrossRef CAS PubMed
.
- T. Uekert, F. Dorchies, C. M. Pichler and E. Reisner, Green Chem., 2020, 22, 3262–3271 RSC
.
- A. Y. Kurenkova, T. B. Medvedeva, N. V. Gromov, A. V. Bukhtiyarov, E. Y. Gerasimov, S. V. Cherepanova and E. A. Kozlova, Catalysts, 2021, 11(7), 870 CrossRef CAS
.
- M. J. Ko, H. H. Nam and M. S. Chung, Food Chem., 2019, 270, 149–155 CrossRef CAS PubMed
.
- X. Chen, G. Chen, Z. Wang and J. Kan, Int. J. Biol. Macromol., 2020, 151, 635–649 CrossRef CAS PubMed
.
|
This journal is © The Royal Society of Chemistry 2023 |
Click here to see how this site uses Cookies. View our privacy policy here.