DOI:
10.1039/D4CP01077A
(Review Article)
Phys. Chem. Chem. Phys., 2024,
26, 14476-14504
The magnetocaloric effect properties for potential applications of magnetic refrigerator technology: a review
Received
12th March 2024
, Accepted 18th April 2024
First published on 29th April 2024
Abstract
In the pursuit of a clean and environmentally friendly future, magnetic refrigerator technology based on the magnetocaloric effect has been proposed as a replacement for conventional refrigeration technologies characterized by inefficient energy use, greenhouse gas emissions, and ozone depletion. This paper presents an in-depth exploration of the current state of research on magnetocaloric effect (MCE) materials by, examining various types of MCE materials and their respective potentials. The focus is particularly directed towards perovskite manganite materials because of their numerous advantages over other materials. These advantages include a wide working temperature range, easily adjustable Curie temperature around room temperature, excellent chemical stability, cost-effective production processes, negligible magnetic and thermal hysteresis properties, as well as competitive values for −ΔSM and ΔTad compared to other materials. Additionally, crucial parameters defining the MCE properties of perovskite manganite materials are comprehensively discussed, both at a fundamental level and in detail.
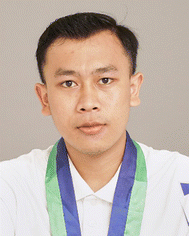
Phahul Zhemas Zul Nehan
| Phahul Zhemas Zul Nehan obtained Bachelor's degree in Physics, from Institut Teknologi Sepuluh Nopember (2023). Currently, He continues to study Master's degree in the Study Program of Materials Science at the Department of Physics from Universitas Indonesia under the supervision of Dr Budhy Kurniawan, Dr Maykel T. E. Manawan, and Prof. Dr Darminto. In his study, he received a Pendidikan Magister menuju Doktor untuk Sarjana Unggul (PMDSU) scholarship program from the Indonesian Ministry of Education, Culture, Research and Technology. His research interests are the materials science mainly in the characterization of magnetic, composite, and energy storage materials. |
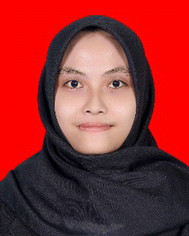
Okvarahireka Vitayaya
| Okvarahireka Vitayaya is currently a joint materials science MS student at Universitas Indonesia under the supervision of Dr Budhy Kurniawan R. and Dr Maykel T. E. Manawan in 2023. She obtained a Bachelor's degree in Physics from Universitas Riau in 2022. In her study, he received a Pendidikan Magister menuju Doktor untuk Sarjana Unggul (PMDSU) scholarship program from the Indonesian Ministry of Education, Culture, Research and Technology. Her research interest is in magnetic material properties such as colossal magnetoresistance and magnetocaloric effect of magnetic material, mainly Lanthanum manganite-based materials. |
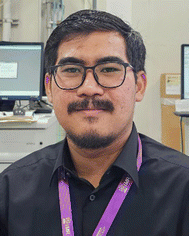
Dicky Rezky Munazat
| Dicky Rezky Munazat obtained his Bachelor's in Physics (2018) and Master's degrees in Materials Science from Universitas Indonesia (2020). He is a research assistant and support staff at Department of Physics, Universitas Indonesia. He is currently pursuing a Doctoral degree in Materials Science at the Department of Physics, Universitas Indonesia, under the guidance of Dr Budhy Kurniawan and Dr Maykel T. E. Manawan. His research interests are synthesized and characterized ceramic magnetic materials by X-ray/Neutron diffraction crystallography analysis, and the properties of magnetic materials, including colossal magnetoresistance and the magnetocaloric effect. |
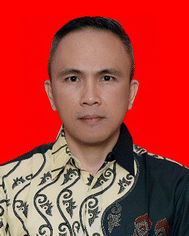
Maykel T. E. Manawan
| Maykel T. E. Manawan obtained his Bachelor's, Master's, and PhD degrees in Physics (2005, 2009, 2014) from Universitas Indonesia. Currently, he is a lecturer at Universitas Pertahanan Indonesia (since 2018) and a researcher at the National Research and Innovation Agency (since 2022). In other experiences, he joins and works in the International Center for Diffraction Data (ICDD since 2020) and Bruker-AXS Indonesia (since 2017). His research interests are the application of crystallography, quantum crystallography, X-ray/Neutron diffraction analysis, batteries, magnetic materials, and materials science. |
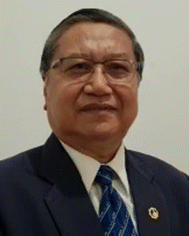
Darminto Darminto
| Darminto Darminto graduated from PhD program in Physics, at Institut Teknologi Bandung, Indonesia (2000) and continued the post-doctoral research program at Twente University, The Netherlands (2001–2003). Returned then as a lecturer at the Physics Department, Institut Teknologi Sepuluh Nopember, Surabaya, Indonesia, he was appointed as a professor of condensed matter physics in 2011. Apart from collaborating with RIKEN Nishina Center since 2009, Federal Institute for Materials Research and Testing (BAM), Germany (since 2013) and Synchrotron Light Research Institute, Thailand (since 2016). His current research interest focuses on superconductivity, magneto-electronics, nano- and 2D-materials. |
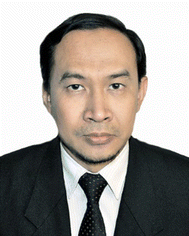
Budhy Kurniawan
| Budhy Kurniawan obtained his Bachelor's and Master's degrees in Physics (1992 & 1995) from Universitas Indonesia and he received his PhD in the Field of Condensed Matter Physics from Tokyo Institute of Technology, Japan (2000). Currently, he is an Associate Professor at the Department of Physics, Universitas Indonesia. His research interests are the characterization and properties of quantum spin systems and magnetic materials such as static and dynamic magnetic properties of NH4CuCl3, magnetoresistance, magnetocaloric effect, microwave absorber materials, multiferroics materials and also thermoelectric phenomena. |
1. Introduction
Modern technology and massive improvements in industrial technology have exposed several problems for society, such as issues related to global warming and excessive energy consumption. These issues are believed to arise in modern technology, particularly conventional gas compression-based refrigeration technology (CRT), which is increasingly prevalent in wider communities and areas.1 This is supported by the world energy consumption data for CRT, which reportedly reached 17% in 2015,2 and increased to 20% in 2018.3 This condition demonstrates the extensive use of CRTs worldwide. Furthermore, conventional refrigerators have disadvantages, including high and inefficient energy consumption, low cooling efficiency cycles ranging from 5–10%, requiring ample space, and the presence of harmful gases still in use.1,4,5 Hazardous gases utilized such as chlorofluorocarbons (CFC), hydrochlorofluorocarbons (HCFC), and hydrofluorocarbons (HFC) contribute to ozone layer depletion and greenhouse gas emissions. Fortunately, according to the Montreal Protocol, CFC gas has been banned since 2010, but the use of others continues, with HCFC estimated to be phased out by 2040 and an 80% reduction in HFC usage by 2047.3,6
Looking towards the future, CRT is based on liquid and gas-phase cooling which is being considered for replacement by other technologies. Currently, researchers are developing solid-state based technologies with utilizing the electric and magnetic properties of materials to replace them as they are deemed more efficient in terms of energy usage and size. The most used application based on electric properties is the thermoelectric system, which exploits the Seebeck effect.7 Thermoelectric technology has several advantages such as not having a moving parts, different operating temperature ranges, and flexibility which allows it to be used as a cooling alternative. However, after more than 20 years of development, it still suffers from low energy conversion efficiency.7 This has led researchers to seek alternative options by leveraging the properties of the magnetocaloric effect, namely magnetic refrigeration technology (MRT).4,8,9 MRT possesses superior properties compared to CRT, including energy efficiency, compact and portable size, cooling efficiency cycles of 30–60%, and the absence of harmful gases due to its environmentally friendly solid-based composition.4,10 However, the assembly cost of MRT is estimated to be nearly two-thirds of the total cost, posing a significant obstacle to its widespread adoption. Despite that looking at other benefits this assembly cost can be offset by its higher thermodynamic cycles, which are 1 to 2 times greater than CRT, thereby impacting economic competition.11
Research on MRT materials is often associated with their magnetism. Their presence has a significant appeal to researchers and technicians, prompting them to do depth studies. Some intriguing phenomena can be explored, such as microwave absorber properties, magnetostriction, magnetoresistance,12–15 magnetocaloric effect,1,4,16,17 multiferroic properties,7 and others. One of the phenomena that has been intensively developed for the application of MRT is the magnetocaloric effect (MCE). The MCE is an intrinsic property of magnetic materials that, when subjected to a magnetic field, induces changes in magnetic entropy (−ΔSM) and adiabatic temperature changes (ΔTad), which can assist in controlling environmental temperature by increasing or decreasing it.18,19
The phenomenon of MCE was discovered by Weiss and Piccard, who studied nickel samples reported in 1917 and 1918 regarding the discovery of heat around the Curie temperature (TC). This temperature marks the transition from ferromagnetic to paramagnetic material when subjected to a magnetic field.7 Furthermore, they also distinguished between reversible effects and heating caused by hysteresis. In 1926, Debye and Giauque discovered the MCE phenomenon in paramagnetic salt materials. After a long time of undeveloped research related to an MCE, brown investigated pure gadolinium (Gd), in 1976 year, as a potential material for magnetic refrigeration applications. Gadolinium stood out due to its favorable properties, such as a Curie temperature (TC) of 294 K around room temperature, magnetic entropy change of 10.2 J kg−1 K−1, and relative cooling power of 410 J kg−1 under a magnetic field of 5 T.20,21 This remarkable discovery of MCE materials has potential applications in magnetic refrigeration and cancer treatment using hyperthermia methods.22 Therefore, Gd has become the standard reference for ideal MCE materials.16,23–27 However, satisfactory results have not been yet achieved in practical applications. The main challenge in the expensive development of MRT is the use of Gd as a material, which has a high ($4000 per kg), and limited availability.17 Therefore, there is a need for alternative materials that are more affordable and abundantly available in nature.
Several alternative MCE materials have been developed by researchers to address these challenges. Fig. 1(A) illustrates the progress of MCE material research from 2010 to 2023. Research on MCE materials has progressed rapidly, resulting in various potential MCE materials, as shown in Fig. 1(B). To date, innovative types of materials include Heusler alloys,28,29 LaFe13−xSix alloys,30–33 Fe-based alloys,34 MnAs,35 spinnel ferrites,36–38 perovskite magnanites,9,15–17,27,39–41 double perovskites,19 and composite.42–44 This was aimed at obtaining MCE materials with ideal criteria for magnetic refrigeration applications. Based on the criteria proposed by Phan et al., perovskite manganites have the potential as a permanent magnetic refrigeration applications.4 Therefore, in this study, we will discuss the MCE phenomenon in general, the development of various types of materials, and a detailed discussion on perovskite manganites.
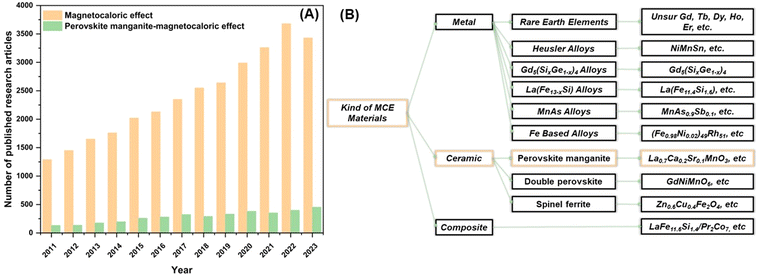 |
| Fig. 1 (A) The number of published research articles on magnetocaloric effect based on magnetic materials using search keywords “magnetocaloric effect” and “perovskite manganite magnetocaloric effect” from Google Scholar accessed on January 4, 2024, and (B) a classification diagram of various magnetocaloric effect materials. | |
2. Fundamental aspects
2.1 Theory of magnetocaloric effect
The MCE properties represented by the two expressions consist of a change in the magnetic entropy (−ΔSM) and the adiabatic temperature change (ΔTad). In the concept of entropy (S), a measure of the degree of disorder in thermodynamics, a system can be adjusted by changing its magnetic field, temperature, or other thermodynamic parameters.1 Thus, in an adiabatic state, the total entropy in the system has three entropy component values, as shown in eqn (1):45 | ST(H, T) = SM(H, T) + Sl(T) + Se(T) | (1) |
where ST is the total entropy of the system, SM is the magnetic entropy, Sl is the lattice entropy, and Se is the electronic entropy. It is known that SM depends on the temperature and magnetic field, while Sl and Se only depend on temperature.1 That makes the value of MCE associated with SM and −ΔSM, with the latter being one of the crucial parameters influencing environmental temperature changes.
Fig. 2 depicts a simple mechanism of the magnetocaloric effect phenomenon. When the magnetic material is without a magnetic field (H1 = 0 T), the magnetic spin moments appear randomly resulting in a significant value of SM. If the magnetic field is applied (H2 > 0 T), an adiabatic magnetization process occurs that causes rotating magnetic spin moments of atoms reducing the value of SM.4 This has adiabatically occurred with a constant S value, so the decrease in SM increases the values in Sl value, influencing the rise in material temperature due to lattice vibrations or phonons and the value of −ΔSM ≪ 0.46 the excess heat in the system quickly dissipates into the environment through a medium such as air, water, water–alcohol, etc. when a magnetic field is applied to materials. This condition increases the ΔTad value. After the magnetic field is removed (H3 = 0 T), an adiabatic demagnetization process and the direction of the random magnetic spin moments occur. This causes an increase in SM and a decrease in Sl, resulting in a decrease in the temperature of the system with the value of −ΔSM ≫ 0. Therefore, the system absorbed heat from the environment to return to equilibrium, causing a decrease in the environmental temperature accompanied by a decrease in ΔTad value.46 If this process is repeated, then a reversible cycle is created.
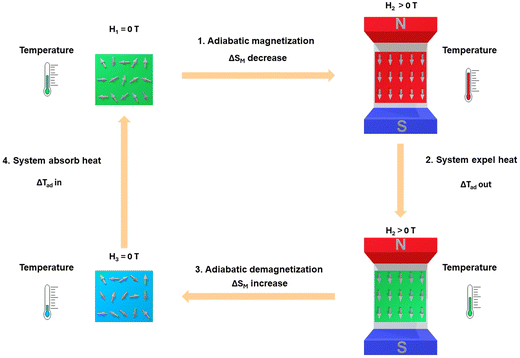 |
| Fig. 2 Schematic diagram of the mechanism of magnetocaloric effect properties. | |
2.2 Relation between magnetic entropy and adiabatic temperature change
Based on the mentioned definition, the MCE properties can be expressed using parameters −ΔSM and ΔTad with thermodynamic aspects. In general, the value of −ΔSM isothermal under a magnetic field change, ΔH = H2 − H1, can be defined as follows: | ΔSM(T, ΔH) = SM(T, H2) − SM(T, H1) | (2) |
| ΔSM(T, ΔH) = dSM(T, ΔH) | (3) |
| 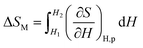 | (4) |
By utilizing the Maxwell relationship equation expressed in eqn (5) as a function of magnetization (M), magnetic field (H), and temperature (T) under constant pressure (p). | 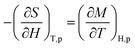 | (5) |
Therefore, if eqn (5) is substituted into eqn (4), the formula for −ΔSM can be obtained by utilizing indirect measurements as follows eqn (6): | 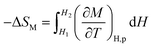 | (6) |
Indirect measurements such as measuring magnetization at discrete magnetic fields and temperature intervals, where −ΔSM can be expressed by the following equation: |  | (7) |
where (−ΔSM)i is the magnetic entropy change at temperature Ti, Mi and Mi+1 are the magnetizations at Ti and Ti+1, Hj is the magnetic field.
On the other hand, there is another parameter, ΔTad, to know the performance of the MCE properties from direct measurements such as measuring the capacity against the magnetic field. Using the second law of thermodynamics equation regarding entropy and specific heat capacity (CP), eqn (8) is obtained:
|  | (8) |
To obtain the equation for Δ
Tad,
eqn (8) is substituted into
eqn (3), resulting in
| 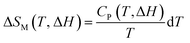 | (9) |
Based on
eqn (9), it can be evaluated to obtain the equation for Δ
Tad, given as follows:
|  | (10) |
From eqn (6), (8) and (10), it can be concluded that every magnetic material exhibiting MCE will perform well if it has high values of −ΔSM and ΔTad. Both of these values will be high when the value of
, the magnetic entropy change with temperature at a constant magnetic field and pressure, is large and Cp, the heat required to increase the temperature by 1 °C for 1 kg of mass, is small at the same temperature.1,4,39 The value of
increases the maximum at around TC, which may be associated with enhancing the maximum MCE value.
2.3 Determination of magnetic cooling capability
In addition to measuring ΔTad, −ΔSM and Cp, other important parameters characterizing the MCE properties are related to the magnetic cooling capability of the MCE material.1 These parameters divided into two definitions are relative cooling power (RCP) and refrigerant capacity (RC). Both represent the amount of heat available for transfer between the hot and cold sides in one ideal Carnot cycle.39,47,48
The calculation of RCP is related to the value of −ΔSM and can be defined as follows:9,41,44
| RCP = |−ΔSmaxM| × δTFWHM | (11) |
where, −Δ
SmaxM is the maximum magnetic entropy change from −Δ
SM and δ
TFWHM is the full width at half maximum (FWHM) of −Δ
SM curve. This approach presents some problems, such as certain samples having wide −Δ
SM(
T) curves with very small −Δ
SM values or narrow −Δ
SM(
T) curves with very high −Δ
SM values. It may yield acceptable RCP values. However, in such cases, it may not be suitable for practical applications.
1 Furthermore, many researchers have assumed that δ
TFWHM =
T2 −
T1, where
T2 and
T1 are the normalizations of the value

.
47,49
The calculation of RC has a relationship with the value of −ΔSM and can be defined as follows:41,50,51
| 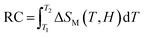 | (12) |
where,
T2 is the temperature of the hot reservoir state, and
T1 is the temperature of the cold reservoir state. It is worth noting that if the measured material exhibits hysteresis, steps are required to eliminate losses due to hysteresis to obtain a clean RC value.
1,35
2.4 Relation between magnetic behavior and types of magnetic phase transition
It is known that determining the order of the magnetic phase transition between the ferromagnetic and paramagnetic states is usually carried out through a thermodynamic sense, such as utilizing the first derivatives of Gibbs free-energy with parameters such as temperature, pressure, magnetic field, etc., which can be observed from the resulting curves. Many researchers have reported two types of magnetic phase transition orders based on the results of these curves.1,4,7,16,17,41,47,48,52–57 If the first derivative results in a discontinuous curve marked by a magnetic phase transition at critical points within a very narrow temperature range, such as changes in entropy, volume, and magnetization values, it is known as the behavior of a first-order magnetic phase transition (FOMT).54,55,57 This phenomenon often occurs when the magnetic transition (dis)order–order occurs parallel to changes in the underlying crystal lattice, which is associated with magnetostructural transformations accompanied by the emergence of hysteresis.1,34,54 The advantage of FOMT is its significant value of −ΔSM for applications in magnetic refrigeration technology (MRT). However, FOMT exhibits significant magnetic and thermal hysteresis, leading to losses in the performance of the MCE properties and a very narrow operating temperature range.52,54 Examples of materials that exhibit FOMT include La(Fe,Si)13,58 Gd5Si2Ge2,59 MnAs1−xSbx,35 Ni65Mn20Ga15,28 and (Fe0.98Ni0.02)51Rh49 alloys.34 On the other hand, if the first derivative presents a continuous curve marked by a magnetic phase transition at critical points with a broad temperature range, this behavior is known as a second-order magnetic phase transition.53,56 The advantage of materials exhibiting SOMT behavior is that SOMT materials have a broad operating temperature range and small magnetic and thermal hysteresis, although the value of −ΔSM is slightly lower than FOMT.1 Small magnetic and thermal hysteresis can disregard the presence of losses in the performance and cycle reversibility of the MCE properties in MRT. Examples of materials exhibiting SOMT behavior include La0.55Ca0.05Sr0.40MnO3,60 La0.05Pr0.1Sr0.35MnO3,61 Zn0.6Cu0.4Fe2O4,62 CoGa1.2Fe0.8O4,36 and others.
2.5 Ideal criterion of MCE materials
The remarkable discovery of MCE properties in pure Gd by Brown has been used as the standard reference for ideal MCE materials until now.16,23,26,27,63,64 According to a summary by Phan and Yu, the ideal criteria for MCE materials for magnetic refrigerator applications include several aspects listed as follows:4
a. Large values of −ΔSM and ΔTad.
b. Small lattice entropy (high Debye temperature).
c. Curie temperature around room temperature, i.e., 300 K.
d. The MCE properties have a broad working temperature range, such as 10–80 or >250 K.
e. Magnetic hysteresis approaching zero, associated with the reversibility of MCE in magnetic refrigerators.
f. Small thermal hysteresis linked to the reversibility of MCE in magnetic refrigerators.
g. Small specific heat capacity and high thermal conductivity, ensuring remarkable temperature changes and heat exchange rates.
h. Large electrical resistance associated with low eddy current heating or minimal losses.
i. High chemical stability, easy sample synthesis, and cost-effective materials for magnetic refrigerator applications.
2.6. Types of MCE measurements
2.6.1 Direct measurement method.
The direct method involves placing a thermometer on the experimental material, and the value of ΔTad can be directly determined additionally, direct measurement methods can be employed to obtain Cp data. Direct measurement methods show an accuracy in the range of 5–10% and depend on errors in thermometry, errors in field settings, the quality of thermal insulation on the sample, and the quality of the compensation scheme to eliminate the effects of changes in magnetic fields in temperature sensor readings.1,4,52 However, it should be noted that the tools used for direct measurement methods are sensitive and require careful to collect data.
2.6.2 Indirect measurement method.
Indirect measurements were carried out to obtain magnetization data for calculating the change in magnetic entropy. The accuracy of magnetization data measurements has a relatively high error (20–30%), whereas calculating MCE from heat capacity data shows better accuracy than other techniques at low temperatures.4 Indirect methods can be performed using two approach calculations. The first method involves utilizing data measuring the temperature dependence on magnetization under varying magnetic fields or data measuring the dependence of magnetic fields on isothermal magnetization.1,4,52
3. Challenges and various types of MCE materials for future application
A brief explanation of the characterization and main properties of the MCE material based on its classification is provided in this section. The aim was to categorize MCE materials based on the compositions from previous studies. However, this concise discussion focuses on MCE materials for MRT applications near room temperature. According to previous studies, MCE materials can be classified into three categories consist of metals, ceramics, and composites.1,4,5,19,22,31,35,59,64 For more details, the classifications of metals and ceramics are summarized in Table 1. However, in this section, we will also explain the development of challenges and efforts to achieve MRT applications in the future in general for all existing alternative materials.
Table 1 Comparison of ideal MCE parameters for types of MCE materials in the classification of metals and ceramics
No. |
Materials |
Ideal MCE parameters |
A* |
B* |
C* |
D* |
E* |
F* |
G* |
H* |
Note: * (A) inexpensive and easily obtainable material, (B) large and easily controllable −ΔSM and RCP values, (C) Curie temperature close to or easily adjustable to room temperature (300 K), (D) wide MCE working temperature range such as 10–80 K, (E) low thermal and magnetic hysteresis, (F) easy production or synthesis processes, (G) good chemical stability, (H) non-toxic and environmentally friendly. |
Metals |
1 |
Pure of rare earth elements |
|
√ |
√ |
√ |
√ |
√ |
√ |
√ |
2 |
Heusler alloys |
√ |
√ |
√ |
|
|
|
|
√ |
3 |
Gd5(Si4−xGex) alloys |
|
√ |
√ |
|
|
|
|
√ |
4 |
La(Fe13−xSix) alloys |
√ |
√ |
√ |
|
|
|
|
√ |
5 |
Fe-based alloys |
√ |
√ |
|
|
|
|
|
√ |
6 |
MnAs alloys |
√ |
√ |
√ |
√ |
√ |
√ |
|
|
|
Ceramics |
1 |
Perovskite manganite |
√ |
√ |
√ |
√ |
√ |
√ |
√ |
√ |
2 |
Double perovskite |
√ |
√ |
|
√ |
√ |
√ |
√ |
√ |
3 |
Spinel ferrite |
√ |
|
|
√ |
√ |
√ |
√ |
√ |
3.1 Challenges and strategies for future MRT application
Based on the background mentioned, homework still needs to be completed to achieve future MRT applications. In addition to the challenges in the economic aspect, prototype development, and sustainability optimization are expected to be the next challenges. These challenges include reducing the heat exchange time between the materials and heat exchangers,65 integrating thermal change controls,65,66 minimizing losses due to magnetic hysteresis,58 enhancing mechanical stability and thermodynamic cycle sustainability,11 and achieving good MCE performance at low magnetic field strengths and over a wide temperature range.4,52 Efforts to solve these challenges have been undertaken by researchers, primarily using strategies such as (i) selecting alternative materials, (ii) adjusting chemical stoichiometry, (iii) modifying external parameters (pressure, magnetic field, and temperature), (iv) utilizing fluid mediums, and (v) reducing the size.4,65 Further discussions on strategies (i), (ii), and (iii) will be addressed in the following sections.
Principally, the magnetocaloric effect can induce local heating and cooling associated with the transfer of heat from the system to the environment. This gap has been exploited by researchers to explore fluid mediums to enhance their magnetocaloric effect properties. The development of fluid mediums in heat transfer extends beyond air alone but also includes water, alcohol, water–alcohol mixtures, liquid mercury, liquid sodium–potassium, and GaInSn liquid alloys.4,11 The use of GaInSn alloy-based heat transfer fluids has attracted attention for further study because of their non-toxic nature at room temperature,11 thermal conductivity 27 times greater than that of water enabling faster heat transfer,67 and a specific heat value of 1/14 that of water allowing for higher temperatures to be achieved in MRT.68 Moreover, it is estimated that using this medium can reduce the size of system components and costs for MRT production, promising for the future. Furthermore, at high frequencies, the GaInSn liquid alloy is estimated to be more than 2.5 times cheaper than water–alcohol mixtures.11 For example, Rajamani et al. investigated the use of GaInSn as a heat transfer medium with La(Fe,Mn,Si)13Hz, presenting the stability of the magnetocaloric material for 1.5 years and the compatibility of the GaInSn liquid alloy heat transfer medium as a cheaper, more effective, and sustainable medium in MRT systems.11
In addition, size reduction strategies are expected that will play a significant role in their magnetic properties.69–74 Furthermore, the interest in reducing the size from micro to nanoscale can provide opportunities for other developments such as hyperthermia or drug delivery,75 thermal switchers,65,66 energy harvesting devices,76etc. However, this review will focus on MRT applications. Generally, size reduction strategies from micro to nanoscale in MCE materials can affect the broadening of the magnetic phase transition, resulting in a broader working temperature range, a decrease in saturation magnetization, and −ΔSM value.51,65,77–80 These changes are associated with disturbances such as strain fields, atomic disorder, uncompensated surface spins, chemical inhomogeneity, grain size distribution, etc.65 For example, Zeng et al. reduced the size of Gd material to as small as 15 nm, resulting in a reported decrease in the −ΔSM value by up to 50% compared with micro-sized samples.81 However, this size reduction can alter the characteristics of the magnetic phase transition from the first order to the second order, characterized by a broadening of the working temperature range.65 Similar results were also obtained with other materials such as Gd5.09Ge2.03Si1.88,82 La–Fe–Si,83 and La0.7Ca0.3MnO3,84 where larger particle sizes could maintain significant MCE values.81–84 Therefore, future strategies need to be developed not only for the base material but also for fluid media and grain size considerations to obtain more effective MCE materials ready to replace CRT.
3.2 Metal materials
3.2.1 Pure of rare earth elements.
The discovery of remarkable MCE properties in the Gd element makes it one of the best MCE materials in this group. The Gd material has a −ΔSM value of 10.2 J kg−1 K−1 with a TC value of 294 K and an RCP value of 410 J kg−1 under a magnetic field of 5 T.4 The emergence of MCE properties in Gd is due to its placement in the 4f group and having the largest magnetic spin moment. Additionally, rare earth metals exhibit different magnetic structures due to indirect oscillations in the localized 4f magnetic moment through electron conduction.85 Furthermore, Ayas et al. reported that rare earth metals have larger crystal field interactions than exchange interactions in light rare earth pure elements. On the other hand, the opposite condition occurs in heavy rare earth pure elements.1 In addition to Gd, other materials have also been investigated, such as terbium (Tb), dysprosium (Dy), holmium (Ho), erbium (Er), and thulium (Tm), as listed in Table 2.45 Unfortunately, the high cost and limited availability restrict the use of pure rare earth metals for MRT applications.
Table 2 List MCE performance from previous researches
Material |
Sample form, heat treatment (T(K)/t) |
Grain size (nm) |
T
C (K) |
|−ΔSM| (J kg−1 K−1) |
ΔH (T) |
RCP (J kg−1) |
Transition order |
Ref. |
Note: SG (sol–gel), SSR (solid-state reaction), wet-mixing (WM), PW (pore wetting), ST (solvothermal), MM (mechanical milling), SGP (sol–gel pechini), MSGP (microwave sol–gel Pechini), SSRPR (solid-state reaction planetary Mill), SSRAM (solid-state reaction attrition mill), Arc-M (arc melting), MS-R (melt spinning-ribbons), polyol-spark plasma sintering (P-SPS), sol–gel-spark plasma sintering (SG-SPS), polyol (P), high energy ball milling (HEBM), high pressure resistive furnace (HPRF), microwave assisted solid state (MW), solid-vapor reaction (SVR), CP (coprecipitation process). |
Metals |
Pure rare-earth elements5 |
Gd |
— |
— |
294 |
11.2 |
|
— |
— |
45
|
Tb |
— |
— |
230 |
15.7 |
6 |
— |
— |
45
|
Dy |
— |
— |
180 |
13.5 |
6 |
— |
— |
45
|
Ho |
— |
— |
134 |
1.8 |
6 |
— |
— |
45
|
Er |
— |
— |
85 |
1.2 |
6 |
— |
— |
45
|
Tm |
— |
— |
56 |
— |
— |
— |
— |
45
|
|
Heusler alloys |
Ni50Mn27Ga23 |
Arc-M, (1173/24 h) |
— |
350 |
1.98 |
3 |
235.8 |
2 |
95
|
Ni54Mn21Ga25 |
Arc-M, (1173/24 h) |
— |
322 |
1.90 |
3 |
161.5 |
2 |
95
|
Ni54Mn25Ga21 |
Arc-M, (1173/24 h) |
— |
345 |
3.53 |
3 |
144.7 |
1 |
95
|
Ni2.16Mn0.84Ga |
Arc-M, (1073/48 h) |
— |
339 |
7.3 |
14 |
— |
1 |
93
|
Ni42Mn43Cr4Sn11 |
Arc-M, (1173/24 h) |
— |
168.2 |
8.7 |
6 |
284.2 |
1 |
88
|
Ni42Mn43Cr4Sn11 |
Arc-M, (1173/24 h) |
— |
291.1 |
5.04 |
6 |
234.1 |
2 |
88
|
Ni50Mn25Sn25 |
MW, (−) |
— |
— |
1.4 |
2 |
— |
2 |
89
|
Ni65Mn20Ga15 |
Nanowire (−) |
— |
∼350 |
2.5 |
2 |
— |
1 |
28
|
Ni2MnGa |
Arc-M, (−) |
— |
375 |
0.35 |
0.27 |
— |
— |
195
|
Ni44Mn45Sn11 |
Arc-M, (1173/24 h) |
— |
237 |
7.2 |
5 |
122 |
1 |
196
|
Ni44Mn44Fe1Sn11 |
Arc-M, (1173/24 h) |
— |
262.5 |
21.3 |
5 |
172 |
1 |
196
|
Ni44Mn43Fe2Sn11 |
Arc-M, (1173/24 h) |
— |
288.5 |
21.2 |
5 |
90 |
1 |
196
|
Ni44Co6Mn37In13 |
Arc-M, (1173/48 h) |
— |
419.5 |
9.8 |
5 |
221.7 |
— |
29
|
Mn49Ni42Sn9 |
Arc-M, (1173/72 h) |
— |
315.1 |
— |
5 |
— |
1 |
197
|
Mn49Ni41Co1Sn9 |
Arc-M, (1173/72 h) |
— |
304.8 |
34.5 |
5 |
— |
1 |
197
|
Mn49Ni39Co3Sn9 |
Arc-M, (1173/72 h) |
— |
266.3 |
36.5 |
5 |
— |
1 |
197
|
Mn49Ni37Co5Sn9 |
Arc-M, (1173/72 h) |
— |
217.5 |
39.9 |
5 |
— |
1 |
197
|
Mn0.97Zr0.03CoGe |
Arc-M, (−) |
— |
290 |
6.93 |
5 |
195 |
— |
87
|
Mn0.95Zr0.05CoGe |
Arc-M, (−) |
— |
285 |
13.42 |
5 |
425 |
— |
87
|
Mn0.93Zr0.07CoGe |
Arc-M, (−) |
— |
283 |
3.96 |
5 |
246 |
— |
87
|
Mn0.90Zr0.10CoGe |
Arc-M, (−) |
— |
278 |
2.94 |
5 |
219 |
— |
87
|
|
Gd5(SixGe1−x)4 alloys |
Gd5Si2Ge2 |
—, (−) |
— |
276 |
18.4 |
5 |
535 |
— |
59
|
Gd5Si2Ge2 (0 kbar) |
Arc-M, (1300/1 h) |
— |
∼275 |
∼28.5 |
5 |
— |
1 |
99
|
Gd5Si2Ge2 (0.7 kbar) |
Arc-M, (1300/1 h) |
— |
∼273 |
∼21.5 |
5 |
— |
1 |
99
|
Gd5Si2Ge2 (1.5 kbar) |
Arc-M, (1300/1 h) |
— |
∼278 |
∼19.6 |
5 |
— |
1 |
99
|
Gd5Si2Ge2 (2.7 kbar) |
Arc-M, (1300/1 h) |
— |
∼284 |
∼15.8 |
5 |
— |
1 |
99
|
Gd5Si2Ge2 (3.4 kbar) |
Arc-M, (1300/1 h) |
— |
∼292 |
∼13.4 |
5 |
— |
1 |
99
|
Gd5Si2Ge2 (4.2 kbar) |
Arc-M, (1300/1 h) |
— |
∼294 |
∼12.1 |
5 |
— |
1 |
99
|
Gd5Si2Ge2 (5.9 kbar) |
Arc-M, (1300/1 h) |
— |
∼303 |
∼7.3 |
5 |
— |
1 |
99
|
Gd5Si2Ge2 (9.2 kbar) |
Arc-M, (1300/1 h) |
— |
∼307 |
∼7.1 |
5 |
— |
1 |
99
|
Gd5Si2Ge2 |
Arc-M, (1573/1 h) |
— |
294 |
7.0 |
2 |
— |
1 |
198
|
Gd5Si2Ge1.98Ga0.02 |
Arc-M, (1573/1 h) |
— |
295 |
∼4.0 |
2 |
— |
2 |
198
|
Gd5Si2Ge1.96Ga0.04 |
Arc-M, (1573/1 h) |
— |
298 |
∼4.0 |
2 |
— |
2 |
198
|
Gd5Si2Ge1.984Ga0.06 |
Arc-M, (1573/1 h) |
— |
298 |
∼3.2 |
2 |
— |
2 |
198
|
Gd5Si1.72Ge2.28 |
Arc-M, (−) |
— |
247 |
13.73 |
2 |
— |
1 |
199
|
(Gd0.98Tb0.02)5Si1.72Ge2.28 |
Arc-M, (−) |
— |
241 |
12.73 |
2 |
— |
1 |
199
|
(Gd0.96Tb0.02)5Si1.72Ge2.28 |
Arc-M, (−) |
— |
237 |
18.85 |
2 |
— |
1 |
199
|
(Gd0.94Tb0.02)5Si1.72Ge2.28 |
Arc-M, (−) |
— |
231 |
25.13 |
2 |
— |
1 |
199
|
(Gd0.92Tb0.02)5Si1.72Ge2.28 |
Arc-M, (−) |
— |
230 |
16.90 |
2 |
— |
1 |
199
|
(Gd0.90Tb0.10)5Si1.72Ge2.28 |
Arc-M, (−) |
— |
230 |
14.50 |
2 |
— |
1 |
199
|
Gd5Ge2.04Si1.94Mn0.02 |
Arc-M, (1173/7 d) |
— |
293 |
19.8 |
5 |
357 |
1 |
98
|
Gd5Ge2.035Si1.935Mn0.06 |
Arc-M, (1173/7 d) |
— |
295 |
14.7 |
5 |
378 |
1 |
98
|
Gd5Si2.035Ge1.935Mn0.03 |
Arc-M, (1173/7 d) |
— |
295 |
11.6 |
5 |
220.1 |
1 |
200
|
Gd5Si2.01Ge1.91Mn0.08 |
Arc-M, (1173/7 d) |
— |
299 |
7.0 |
5 |
175.3 |
1 |
200
|
Gd5Si2Ge2 |
— |
— |
262 |
8.1 |
1 |
— |
— |
100
|
Gd4.5Dy0.5Si2Ge2 |
— |
— |
252 |
7.7 |
1 |
— |
— |
100
|
Gd4Dy1Si2Ge2 |
— |
— |
243 |
7.5 |
1 |
— |
— |
100
|
Gd3.5Dy1.5Si2Ge2 |
— |
— |
231 |
7.6 |
1 |
— |
— |
100
|
Gd3Dy2Si2Ge2 |
— |
— |
220 |
7.5 |
1 |
— |
— |
100
|
DyAl2Ge2 |
SF, (1323/10 h) |
— |
8 |
12.0 |
7 |
275 |
— |
201
|
Dy0.5Gd4.5Si2Ge2 |
Arc-M, (−) |
— |
— |
∼8.8 |
5.5 |
— |
1 |
202
|
Dy3Gd2Si2Ge2 |
Arc-M, (−) |
— |
— |
∼13.9 |
5.5 |
— |
1 |
202
|
Dy5Si2Ge2 |
Arc-M, (−) |
— |
— |
∼6.9 |
5.5 |
— |
1 |
202
|
|
La(Fe13−xSix) alloys |
LaFe11.2Si1.8 |
SC, (1373/10 h) |
— |
∼182 |
16.8 |
2 |
— |
1 |
30
|
LaFe11.2Si1.8 |
SC-powder <100 μm, (1373/10 h) |
— |
∼182 |
10.6 |
2 |
— |
1 |
30
|
LaFe11.2Si1.8 |
SC-powder <100–200 μm, (1373/10 h) |
— |
∼182 |
12.5 |
2 |
— |
1 |
30
|
LaFe11.2Si1.8 |
SC-powder <200–300 μm, (1373/10 h) |
— |
∼182 |
12.8 |
2 |
— |
1 |
30
|
LaFe11.2Si1.8 |
HPS-powder <100 μm, (753/25 m) |
— |
191 |
10.3 |
2 |
— |
1 |
30
|
LaFe11.2Si1.8 |
HPS-powder <100–200 μm, (753/25 m) |
— |
187 |
11.1 |
2 |
— |
1 |
30
|
LaFe11.2Si1.8 |
HPS-powder <200–300 μm, (753/25 m) |
— |
186 |
12.1 |
2 |
— |
1 |
30
|
LaFe11.2Si1.8 |
SPS-powder <100 μm, (1223/5 m) |
— |
193 |
7.2 |
2 |
— |
1 |
30
|
LaFe11.2Si1.8 |
SPS-powder <100–200 μm, (1223/5 m) |
— |
185 |
12.8 |
2 |
— |
1 |
30
|
LaFe11.2Si1.8 |
SPS-powder <200–300 μm, (1223/5 m) |
— |
185 |
12.5 |
2 |
— |
1 |
30
|
La1.2Fe11.6Si1.4 |
Arc-M, (1273/30 m) |
— |
190 |
6.1 |
2 |
— |
2 |
58
|
La1.2Fe11.6Si1.4B0.75 |
MS-R 5 m s−1, (1273/30 m) |
— |
191 |
20.2 |
2 |
— |
1 |
58
|
La1.2Fe11.6Si1.4B0.75 |
MS-R 10 m s−1, (1273/30 m) |
— |
188 |
13.5 |
2 |
— |
1 |
58
|
La(Fe0.94Co0.6)Si1.6B0.25 |
Arc-M, (1325/48 h) |
— |
285 |
6.70 |
3 |
174.2 |
2 |
203
|
La(Fe0.92Ni0.02Co0.6)Si1.6B0.25 |
Arc-M, (1325/48 h) |
— |
293 |
4.63 |
3 |
166.7 |
2 |
203
|
La(Fe0.90Ni0.04Co0.6)Si1.6B0.25 |
Arc-M, (1325/48 h) |
— |
303 |
3.77 |
3 |
154.1 |
2 |
203
|
La(Fe0.88Ni0.06Co0.6)Si1.6B0.25 |
Arc-M, (1325/48 h) |
— |
311 |
3.12 |
3 |
136.8 |
2 |
203
|
La(Fe0.86Ni0.08Co0.6)Si1.6B0.25 |
Arc-M, (1325/48 h) |
— |
319 |
2.97 |
3 |
— |
2 |
203
|
La(Fe0.84Ni0.10Co0.6)Si1.6B0.25 |
Arc-M, (1325/48 h) |
— |
329 |
1.99 |
3 |
— |
2 |
203
|
LaFe11.6Si1.4(<100 μm) |
Arc-M-SPS, (for SPS 1273/5 m forwad to 1323/24 h) |
— |
230 |
3.08 |
5 |
84 |
2 |
31
|
La(Fe12.4Si1.6) |
Arc-M, (1273/30 d) |
— |
208 |
10.5 |
1 |
— |
— |
102
|
La(Fe12.4Si1.6) |
Arc-M, (1273/30 d) |
— |
208 |
14.3 |
2 |
— |
— |
102
|
La(Fe12.4Si1.6) |
Arc-M, (1273/30 d) |
— |
208 |
19.4 |
5 |
— |
— |
102
|
La0.7Ce0.3(Fe0.92Co0.08)11.4Si1.6 |
Arc-M, (1273/3 h) |
— |
— |
4.1 |
2 |
— |
2 |
204
|
La0.7Ce0.3(Fe0.92Co0.08)11.4Si1.6 |
Arc-M, (1273/3 h) |
— |
— |
8.3 |
5 |
— |
2 |
204
|
La0.7Ce0.3(Fe0.92Co0.08)11.4Si1.6 |
MS-R, (1273/3 h) |
— |
— |
5.4 |
2 |
— |
2 |
204
|
La0.7Ce0.3(Fe0.92Co0.08)11.4Si1.6 |
MS-R, (1273/3 h) |
— |
— |
10.4 |
5 |
— |
2 |
204
|
La1.4Fe10.92Co0.88Si1.2 |
HEBM, (1323/12 d) |
— |
292 |
3.74 |
2 |
129.4 |
2 |
205
|
La1.4Fe10.86Co0.94Si1.2 |
HEBM, (1323/12 d) |
— |
298 |
3.63 |
2 |
130.7 |
2 |
205
|
La1.4Fe10.82Co0.98Si1.2 |
HEBM, (1323/12 d) |
— |
301 |
4.00 |
2 |
138.0 |
2 |
205
|
La1.4Fe10.78Co1.02Si1.2 |
HEBM, (1323/12 d) |
— |
307 |
3.69 |
2 |
132.1 |
2 |
205
|
La1.4Fe10.72Co1.06Si1.2 |
HEBM, (1323/12 d) |
— |
310 |
3.65 |
2 |
136.1 |
2 |
205
|
La1.4Fe10.82Co0.98Si1.2 |
Arc-M, (1323/12 d) |
— |
296 |
5.35 |
2 |
130.5 |
2 |
205
|
La0.9Ce0.1Fe11.5Si1.5 |
Arc-M, (1373/15 d) |
— |
191 |
21.2 |
3 |
— |
1 |
206
|
La0.8Ce0.2Fe11.5Si1.5 |
Arc-M, (1373/15 d) |
— |
∼186 |
27.4 |
3 |
— |
1 |
206
|
La0.7Ce0.3Fe11.5Si1.5 |
Arc-M, (1373/15 d) |
— |
181 |
51.6 |
3 |
— |
1 |
206
|
LaFe11.5Si1.5 |
Arc-M, (1373/9 d) |
— |
195 |
16.5 |
2 |
154.3 |
1 |
207
|
La0.95Gd0.05Fe11.5Si1.5 |
Arc-M, (1373/9 d) |
— |
196 |
15.3 |
2 |
140.2 |
1 |
207
|
La0.9Gd0.1Fe11.5Si1.5 |
Arc-M, (1373/9 d) |
— |
196 |
12.6 |
2 |
117.6 |
1 |
207
|
La0.85Gd0.15Fe11.5Si1.5 |
Arc-M, (1373/9 d) |
— |
198 |
9.5 |
2 |
110.2 |
2 |
207
|
La0.8Gd0.2Fe11.5Si1.5 |
Arc-M, (1373/9 d) |
— |
200 |
7.9 |
2 |
86.1 |
2 |
207
|
La0.75Gd0.25Fe11.5Si1.5 |
Arc-M, (1373/9 d) |
— |
204 |
6.8 |
2 |
90.9 |
2 |
207
|
La1.0Fe10.2Co1.0Si1.8 |
Arc-M, (1423/100 h) |
— |
312 |
2.0 |
1 |
68 |
2 |
32
|
La1.0Fe10.2Co1.0Si1.8 |
Arc-M, (1423/100 h) |
— |
312 |
3.6 |
2 |
162 |
2 |
32
|
La1.0Fe10.2Co1.0Si1.8 |
Arc-M, (1423/100 h) |
— |
312 |
4.9 |
3 |
255 |
2 |
32
|
|
MnAs alloys |
MnAs |
HPRF, (1647/8 h) |
— |
311 |
47 |
5 |
— |
1 |
109
|
MnAs |
HPRF, (1647/8 h) |
— |
318 |
44 |
2 |
— |
1 |
109
|
MnAs0.9Sb0.1 |
SVR, (1073/7 d) |
— |
280 |
30 |
5 |
— |
1 |
110
|
MnAs0.95Sb0.05 |
SSR, (1073/7 h) |
— |
300 |
∼23.00 |
5 |
∼240 |
1 |
35
|
MnAs0.90Sb0.10 |
SSR, (1073/7 h) |
— |
288 |
∼22.50 |
5 |
∼260 |
1 |
35
|
MnAs0.85Sb0.15 |
SSR, (1073/7 h) |
— |
282 |
∼22.45 |
5 |
∼220 |
1 |
35
|
MnAs0.80Sb0.20 |
SSR, (1073/7 h) |
— |
276 |
∼22.43 |
5 |
∼240 |
1 |
35
|
MnAs0.75Sb0.25 |
SSR, (1073/7 h) |
— |
262 |
∼21.40 |
5 |
∼225 |
1 |
35
|
MnAs0.70Sb0.30 |
SSR, (1073/7 h) |
— |
242 |
∼20.30 |
5 |
∼245 |
1 |
35
|
Fe-based alloys |
(Fe0.98Ni0.02)49Rh51 |
Arc-M, (1273/10 d) |
— |
266 |
10.3 |
2 |
— |
1 |
34
|
(Fe70Ni30)89B11 |
Arc-M, (973, 2 h) |
— |
381 |
0.31 |
1 |
100 |
2 |
208
|
(Fe70Ni30)89B11 |
Arc-M, (973, 2 h) |
— |
381 |
1.46 |
5 |
641 |
2 |
208
|
(Fe70Ni30)99Cr1 |
HEBM, (973, 2 h) |
— |
398 |
1.58 |
5 |
548 |
2 |
209
|
(Fe70Ni30)96Cr3 |
HEBM, (973, 2 h) |
— |
323 |
1.49 |
5 |
436 |
2 |
209
|
(Fe70Ni30)95Cr5 |
HEBM, (973, 2 h) |
— |
258 |
1.45 |
5 |
406 |
2 |
209
|
(Fe70Ni30)94Cr6 |
HEBM, (973, 2 h) |
— |
245 |
1.22 |
5 |
366 |
2 |
209
|
(Fe70Ni30)92Cr7 |
HEBM, (973, 2 h) |
— |
215 |
1.11 |
5 |
306 |
2 |
209
|
Fe17Pr2 |
HEBM, (−) |
— |
292 |
2.1 |
1.5 |
107 |
— |
210
|
Fe17Pr2 |
HEBM, (−) |
— |
292 |
4.5 |
5 |
573 |
— |
210
|
|
Ceramics |
Spinel ferrites |
Zn0.6Cu0.4Fe2O4 |
SG, (1373/24 h) |
460 |
305 |
1.16 |
5 |
289 |
2 |
62
|
Zn0.4Ni0.2Cu0.4Fe2O4 |
SG, (1373/24 h) |
— |
565 |
1.41 |
5 |
141 |
2 |
62
|
Zn0.2Ni0.4Cu0.4Fe2O4 |
SG, (1373/24 h) |
810 |
705 |
1.61 |
5 |
233 |
2 |
62
|
Zn0.7Ni0.3Fe2O4 |
SG, (1273/24 h) |
— |
327 |
0.67 |
2 |
112 |
2 |
38
|
Zn0.7Ni0.2Cu0.1Fe2O4 |
SG, (1273/24 h) |
— |
296 |
0.64 |
2 |
117 |
2 |
38
|
Zn0.7Ni0.1Cu0.2Fe2O4 |
SG, (1273/24 h) |
— |
282 |
0.62 |
2 |
124 |
2 |
38
|
CoGa1.2Fe0.8O4 |
SSR, (1273/10 h) |
— |
210 |
1.51 |
5 |
27 |
2 |
36
|
CoGa1.2Fe0.8O4 |
SSR, (1273/10 h) |
— |
210 |
1.23 |
4 |
18 |
2 |
36
|
CoGa1.2Fe0.8O4 |
SSR, (1273/10 h) |
— |
210 |
1.00 |
3 |
12 |
2 |
36
|
CoGa1.2Fe0.8O4 |
SSR, (1273/10 h) |
— |
210 |
0.7 |
2 |
7 |
2 |
36
|
CoGa1.2Fe0.8O4 |
SSR, (1273/10 h) |
— |
210 |
0.4 |
1 |
3 |
2 |
36
|
CoFe2O4 |
SSR, (1473/6 h) |
— |
675 |
0.66 |
5 |
335.7 |
2 |
211
|
Co8.875Cr0.125 Fe2O4 |
SSR, (1473/6 h) |
— |
740 |
1.98 |
5 |
128 |
2 |
211
|
Co8.705Cr0.250 Fe2O4 |
SSR, (1473/6 h) |
— |
735 |
1.8 |
5 |
137 |
2 |
211
|
Co8.675Cr0.325 Fe2O4 |
SSR, (1473/6 h) |
— |
731 |
1.76 |
5 |
145 |
2 |
211
|
Co8.500Cr0.500 Fe2O4 |
SSR, (1473/6 h) |
— |
687 |
1.02 |
5 |
52 |
2 |
211
|
Ni0.4Cd0.3Zn0.3Fe3O4 |
SG, (1173/24 h) |
— |
510 |
0.68 |
3 |
81.07 |
2 |
212
|
Ni0.4Cd0.3Zn0.3Fe3O4 |
SG, (1373/24 h) |
— |
545 |
0.98 |
3 |
145.18 |
2 |
212
|
Ni0.4Cd0.3Zn0.3Fe3O4 |
SG, (1173/24 h) |
— |
510 |
1.11 |
5 |
152.09 |
2 |
212
|
Ni0.4Cd0.3Zn0.3Fe3O4 |
SG, (1373/24 h) |
— |
545 |
1.62 |
5 |
253.65 |
2 |
212
|
Mg0.35Zn0.65Fe2O4 |
SSR, (1573/12 h) |
— |
295 |
1.026 |
3 |
114.5 |
2 |
37
|
Mg0.35Zn0.65Fe2O4 |
SSR, (1573/12 h) |
— |
295 |
1.337 |
4 |
150.17 |
2 |
37
|
Mg0.35Zn0.65Fe2O4 |
SSR, (1573/12 h) |
— |
295 |
1.642 |
5 |
185.2 |
2 |
37
|
|
Double perovskites |
Gd2NiMnO6 |
SSR, (1623/−) |
— |
130 |
35 |
7 |
— |
— |
213
|
Gd2NiMnO6 |
SG, (1573/48 h) |
— |
130 |
3.7 |
5 |
— |
2 |
127
|
Pr2NiMnO6 |
SSR, (1423/24 h) |
— |
215 |
4.9 |
5 |
— |
— |
214
|
Nd2NiMnO6 |
SSR, (1423/24 h) |
— |
191 |
2.3 |
5 |
— |
— |
214
|
Tb2NiMnO6 |
SSR, (1423/24 h) |
— |
110 |
5.2 |
5 |
— |
— |
214
|
Tb2NiMnO6 |
SG, (1573/48 h) |
— |
112 |
3.5 |
5 |
— |
2 |
127
|
Ho2NiMnO6 |
SG, (1273/100 h) |
— |
86 |
6.4 |
5 |
— |
— |
214
|
Ho2NiMnO6 |
SG, (1473/48 h) |
— |
81.2 |
1.7 |
5 |
— |
2 |
128
|
Ho2NiMnO6 |
SG, (1473/48 h) |
— |
101 |
3.4 |
5 |
175 |
2 |
215
|
Dy2NiMnO6 |
SSR, (1473/24 h) |
— |
97 |
5.2 |
7 |
— |
— |
216
|
Dy2NiMnO6 |
SG, (1473/48 h) |
— |
93 |
3.7 |
5 |
194 |
2 |
215
|
Er2NiMnO6 |
SG, (1473/48 h) |
— |
84 |
3.4 |
5 |
169 |
2 |
215
|
Eu2NiMnO6 |
SSR, (1473/24 h) |
— |
145 |
4.0 |
7 |
— |
— |
216
|
Eu2NiMnO6 |
SG, (1573/48 h) |
— |
143 |
3.2 |
|
— |
— |
127
|
Gd2CoMnO6 |
SSR, (1623/–) |
— |
112 |
24 |
7 |
— |
— |
213
|
Dy2CoMnO6 |
SG, (1373/48 h) |
— |
96 |
4.2 |
7 |
216 |
2 |
217
|
Ho2CoMnO6 |
SG, (1373/48 h) |
— |
85 |
4.6 |
7 |
275 |
2 |
217
|
Ho2CoMnO6 |
SG, (1473/48 h) |
— |
73.5 |
2.2 |
5 |
— |
2 |
127
|
Er2CoMnO6 |
SG, (1373/48 h) |
— |
71 |
4.5 |
7 |
253 |
2 |
217
|
Er2FeCrO6 |
SG, (1500/32 h) |
— |
11.7 |
11.95 |
5 |
215.8 |
2 |
218
|
Tm2FeCrO6 |
SG, (1500/32 h) |
— |
10.5 |
4.76 |
5 |
123.5 |
2 |
218
|
|
Perovskite manganites |
Pr0.7Sr0.3MnO3 |
SG, (973/5 h) |
44 |
275 |
2.92 |
5 |
350 |
2 |
47
|
Pr0.5La0.2Sr0.3MnO3 |
SSR, (1623/24 h) |
— |
229 |
6.65 |
5 |
302.17 |
2 |
219
|
Pr0.4La0.3Sr0.3MnO3 |
SSR, (1623/24 h) |
— |
319 |
5.21 |
5 |
216.13 |
2 |
219
|
Pr0.7Sr0.3MnO3 |
SSR, (1623/24 h) |
— |
263 |
3.38 |
1.8 |
50.00 |
— |
169
|
Pr0.7Sr0.2Ba0.1MnO3 |
SSR, (1523/24 h) |
— |
231 |
∼3.15 |
1.8 |
∼62.00 |
— |
169
|
Pr0.7Sr0.1Ba0.2MnO3 |
SSR, (1523/24 h) |
— |
200 |
∼2.55 |
1.8 |
∼70.00 |
— |
169
|
Pr0.7Ba0.3MnO3 |
SSR, (1523/24 h) |
— |
184 |
1.58 |
1.8 |
74.02 |
— |
169
|
Pr0.5Eu0.1Sr0.4Mn |
SSR, (1623/60 h) |
42.38 |
279.9 |
4.47 |
5 |
264.88 |
2 |
48
|
Pr0.5Er0.1Sr0.4Mn |
SSR, (1623/60 h) |
51.68 |
188.5 |
4.86 |
5 |
270.00 |
2 |
48
|
EuTi0.8625Nb0.0625Mn0.075O3 |
SSR, (1473/18 h) |
— |
5.5 |
34.7 |
5 |
364.9 |
2 |
49
|
EuTi0.8375Nb0.0625Mn0.100O3 |
SSR, (1473/18 h) |
— |
5.5 |
27.8 |
5 |
367.6 |
2 |
49
|
EuTi0.8125Nb0.0625Mn0.125O3 |
SSR, (1473/18 h) |
— |
6.5 |
23.2 |
5 |
369.2 |
2 |
49
|
EuTi0.7875Nb0.0625Mn0.150O3 |
SSR, (1473/18 h) |
— |
9.0 |
17.1 |
5 |
357.6 |
2 |
49
|
(Nd0.5Sm0.5)0.5Sr0.5MnO3 |
SSR (1573/36 h) |
— |
188 |
∼2.85 |
5 |
∼183 |
2 |
171
|
LaMnO3 bulk |
SG, (1673/36 h) |
— |
124 |
2.69 |
5 |
250 |
2 |
142
|
LaMnO3 |
SG, (1673/36 h) |
200 |
135 |
2.67 |
5 |
355 |
2 |
142
|
LaMnO3 |
SG, (1673/36 h) |
40 |
150 |
2.4 |
5 |
369 |
2 |
142
|
La0.7Sr0.3MnO3 |
SG, (973/5 h) |
21 |
358 |
2.81 |
5 |
232 |
2 |
47
|
La0.56Pr0.14Sr0.3MnO3 |
SG, (973/5 h) |
30 |
343 |
2.96 |
5 |
271 |
2 |
47
|
La0.42Pr0.28Sr0.3MnO3 |
SG, (973/5 h) |
34 |
329 |
2.70 |
5 |
267 |
2 |
47
|
La0.28Pr0.42Sr0.3MnO3 |
SG, (973/5 h) |
24 |
311 |
2.17 |
5 |
283 |
2 |
47
|
La0.14Pr0.56Sr0.3MnO3 |
SG, (973/5 h) |
27 |
290 |
2.44 |
5 |
289 |
2 |
47
|
La0.05Pr0.1Sr0.35MnO3 |
SGP, (1373/24 h) |
— |
310 |
3.58 |
3 |
161.11 |
2 |
61
|
La0.05Pr0.1Sr0.35Mn0.95Ti0.05O3 |
SGP, (1373/24 h) |
— |
288 |
2.78 |
3 |
118.85 |
2 |
61
|
La0.6Ca0.4MnO3 |
SG, (973/10 h) |
45 |
258 |
2.3 |
5 |
228 |
2 |
23
|
La0.7Ca0.3MnO3 |
P, (1273/48 h) |
190 |
254 |
5.98 |
5 |
252 |
1 |
119
|
La0.7Ca0.3MnO3 |
SG, (1273/48 h) |
265 |
251 |
6.88 |
5 |
259 |
1 |
119
|
La0.7Ca0.3MnO3 |
SSR, (1573/48 h) |
11 000 |
253 |
7.06 |
5 |
263 |
1 |
119
|
La0.7Ca0.3MnO3 |
P-SPS, (1073/10 m) |
95 |
243 |
2.60 |
5 |
288 |
2 |
119
|
La0.7Ca0.3MnO3 |
SG-SPS, (1073/10 m) |
75 |
235 |
2.81 |
5 |
272 |
2 |
119
|
La0.7Ca0.3MnO3 |
R-SPS, (1073/10 m) |
40 |
160 |
1.65 |
5 |
249 |
2 |
119
|
La0.66Ca0.33MnO3 |
ST, (1023/6 h) |
22.60 |
258 |
3.76 |
5 |
226.61 |
2 |
24
|
La0.61Ca0.33Mn1.05O3 |
ST, (1023/6 h) |
21.20 |
272 |
3.61 |
5 |
210.51 |
2 |
24
|
La0.56Ca0.33Mn1.10O3 |
ST, (1023/6 h) |
21.90 |
262 |
3.08 |
5 |
183.57 |
2 |
24
|
La0.66Ca0.28Mn1.05O3 |
ST, (1023/6 h) |
24.00 |
266 |
3.67 |
5 |
233.45 |
2 |
24
|
La0.66Ca0.23Mn1.10O3 |
ST, (1023/6 h) |
20.30 |
278 |
2.99 |
5 |
195.71 |
2 |
24
|
La0.7Ca0.3MnO3 |
MM, (−) |
15 |
139 |
0.89 |
1.5 |
— |
2 |
172
|
La0.7Ca0.3Mn0.98Ni0.02O3 |
MM, (−) |
15 |
134 |
0.77 |
1.5 |
— |
2 |
172
|
La0.7Ca0.3Mn0.93Ni0.07O3 |
MM, (−) |
15 |
139 |
0.70 |
1.5 |
— |
2 |
172
|
La0.7Ca0.3Mn0.90Ni0.10O3 |
MM, (−) |
15 |
154 |
0.95 |
1.5 |
— |
2 |
172
|
La0.7Ca0.24Sr0.06MnO3 |
SGP, (1473/6 h) |
40 |
292 |
5.3 × 10−4 |
5 |
∼276 |
2 |
220
|
La0.7Ca0.24Sr0.06MnO3 |
SGP-SPS, (1473/6 h) |
400 |
292 |
5.16 × 10−4 |
5 |
— |
2 |
220
|
La0.7Ca0.26Sr0.04MnO3 |
MSGP, (1473/3 h) |
1440 |
280 |
1.9 × 10−4 |
5 |
— |
2 |
220
|
La0.7Ca0.23Sr0.07MnO3 |
SSRPR, (1573/24 h) |
1680 |
292 |
5.5 × 10−4 |
5 |
∼210 |
2 |
220
|
La0.7Ca0.23Sr0.07MnO3 |
SSRAM, (1573/24 h) |
1120 |
301 |
4.2 × 10−4 |
5 |
∼160 |
2 |
220
|
La0.7Ca0.3MnO3 |
HEBM, (1373/2 h) |
568.86 |
243 |
7.43 |
1.8 |
93.29 |
1 |
117
|
La0.7Sr0.05Ca0.25MnO3 |
HEBM, (1373/2 h) |
586.33 |
271 |
6.29 |
1.8 |
65.51 |
2 |
117
|
La0.7Sr0.10Ca0.20MnO3 |
HEBM, (1373/2 h) |
599.18 |
312 |
4.05 |
1.8 |
60.80 |
2 |
117
|
La0.7Sr0.15Ca0.15MnO3 |
HEBM, (1373/2 h) |
608.49 |
325 |
3.78 |
1.8 |
70.39 |
2 |
117
|
La0.7Sr0.20Ca0.10MnO3 |
HEBM, (1373/2 h) |
416.99 |
342 |
3.47 |
1.8 |
74.63 |
2 |
117
|
La0.55Sr0.45MnO3 |
SSR, (1373/12 h) |
480 |
354 |
3.088 |
5 |
213 |
2 |
60
|
La0.55Ca0.05Sr0.40MnO3 |
SSR, (1373/12 h) |
410 |
342 |
2.830 |
5 |
196 |
2 |
60
|
La0.55Ca0.10Sr0.35MnO3 |
SSR, (1373/12 h) |
420 |
336 |
2.710 |
5 |
177 |
2 |
60
|
La0.55Ca0.25Sr0.20MnO3 |
SSR, (1373/12 h) |
430 |
311 |
2.550 |
5 |
165 |
2 |
60
|
La0.67Ca0.23Sr0.1Mn0.98Ni0.02O3 |
SG, (1273/24 h) |
860 |
296 |
4.92 |
5 |
193 |
2 |
26
|
La0.63Ca0.20Sr0.13MnO3 |
SG, (−) |
40 |
267 |
0.83 |
3 |
48 |
2 |
33
|
La0.63Ca0.20Sr0.13MnO3 |
SG-SPS, (1073/15 m) |
— |
272 |
1.1 |
3 |
65 |
2 |
33
|
La0.63Ca0.20Sr0.13MnO3 |
SG-SPS, (1173/15 m) |
— |
285 |
1.8 |
3 |
88 |
2 |
33
|
La0.63Ca0.18Sr0.15Mn0.98Fe0.02O3 |
SG, (1273/24 h) |
410 |
329 |
4.889 |
5 |
181 |
2 |
27
|
La0.63Ca0.13Sr0.20Mn0.98Fe0.02O3 |
SG, (1273/24 h) |
680 |
330 |
4.712 |
5 |
204 |
2 |
27
|
La0.63Ca0.03Sr0.30Mn0.98Fe0.02O3 |
SG, (1273/24 h) |
790 |
350 |
3.355 |
5 |
179 |
2 |
27
|
La0.63Ca0.29Sr0.04MnO3 |
SGP, (1373/1 h) |
— |
264.43 |
0.56 |
0.5 |
16 |
2 |
167
|
La0.63Ca0.29Sr0.04MnO3 |
SGP, (1373/1 h) |
— |
266.87 |
1.02 |
1 |
34.8 |
2 |
167
|
La0.63Ca0.29Sr0.04MnO3 |
SGP, (1373/1 h) |
— |
269.29 |
1.43 |
2 |
54.1 |
2 |
167
|
La0.63Ca0.29Sr0.04MnO3 |
SGP, (1373/1 h) |
— |
276.31 |
2.44 |
3 |
114.9 |
2 |
167
|
La0.70Ca0.20Sr0.10MnO3 |
SSR, (1473/24 h) |
— |
308 |
1.97 |
2 |
— |
2 |
123
|
La0.7Ca0.15Sr0.15MnO3 |
SSR, (1473/24 h) |
— |
338 |
0.344 |
1 |
12.272 |
2 |
124
|
La0.7Ca0.15Sr0.15Mn0.98Gd0.02O3 |
SSR, (1473/24 h) |
— |
211 |
0.629 |
1 |
48.951 |
2 |
124
|
La0.7Ca0.15Sr0.15Mn0.94Gd0.06O3 |
SSR, (1473/24 h) |
— |
203 |
0.509 |
1 |
51.964 |
2 |
124
|
La0.7Ca0.15Sr0.15MnO3 |
SSR, (1473/24 h) |
— |
338 |
0.925 |
2 |
37.568 |
2 |
124
|
La0.7Ca0.15Sr0.15Mn0.98Gd0.02O3 |
SSR, (1473/24 h) |
— |
211 |
1.198 |
2 |
108.698 |
2 |
124
|
La0.7Ca0.15Sr0.15Mn0.94Gd0.06O3 |
SSR, (1473/24 h) |
— |
203 |
1.004 |
2 |
111.63 |
2 |
124
|
La0.75Eu0.05Ca0.1Sr0.1MnO3 |
SG, (1173/10 h) |
171 |
264 |
5.39 |
2 |
110.38 |
2 |
144
|
La0.70Eu0.10Ca0.1Sr0.1MnO3 |
SG, (1173/10 h) |
98.34 |
226 |
4.52 |
2 |
119.81 |
2 |
144
|
La0.65Eu0.15Ca0.1Sr0.1MnO3 |
SG, (1173/10 h) |
84.34 |
194 |
4.35 |
2 |
124.38 |
2 |
144
|
La0.75Eu0.05Ca0.1Sr0.1MnO3 |
SG, (1173/10 h) |
171 |
264 |
5.39 |
5 |
282.20 |
2 |
144
|
La0.70Eu0.10Ca0.1Sr0.1MnO3 |
SG, (1173/10 h) |
98.34 |
226 |
4.52 |
5 |
305.20 |
2 |
144
|
La0.65Eu0.15Ca0.1Sr0.1MnO3 |
SG, (1173/10 h) |
84.34 |
194 |
4.35 |
5 |
323.15 |
2 |
144
|
La0.7Sr0.15Ca0.15MnO3 |
SG, (1223/10 h) |
114.37 |
341 |
3.74 |
5 |
— |
2 |
115
|
La0.65Bi0.05Sr0.15Ca0.15MnO3 |
SG, (1223/10 h) |
275.55 |
321 |
4.13 |
5 |
—- |
2 |
115
|
La0.60Bi0.10Sr0.15Ca0.15MnO3 |
SG, (1223/10 h) |
325.5 |
291 |
4.28 |
5 |
257 |
2 |
115
|
La0.55Bi0.15Sr0.15Ca0.15MnO3 |
SG, (1223/10 h) |
433.83 |
251 |
4.18 |
5 |
248 |
2 |
115
|
La0.7Sr0.3Mn0.9Cu0.1O3 |
SG, (1273/24 h) |
27 |
320 |
3.07 |
5 |
198 |
2 |
20
|
La0.6Bi0.1Sr0.2Ca0.1Mn0.9Cu0.1O3 |
SG, (1273/24 h) |
29 |
275 |
3.66 |
5 |
162 |
2 |
20
|
La0.6Bi0.1Sr0.15Ca0.15Mn0.9Cu0.1O3 |
SG, (1273/24 h) |
32 |
235 |
3.74 |
5 |
159 |
2 |
20
|
La0.7Sr0.3Mn0.9Cu0.1O3 |
SG, (1273/24 h) |
27 |
320 |
3.07 |
5 |
198 |
2 |
20
|
La0.6Bi0.1Sr0.3Mn0.9Cu0.1O3 |
SG, (1273/24 h) |
23 |
300 |
3.4 |
5 |
161 |
2 |
20
|
La0.6Bi0.1Sr0.25Ca0.05Mn0.9Cu0.1O3 |
SG, (1273/24 h) |
24 |
290 |
3.65 |
5 |
184 |
2 |
20
|
La0.7Ba0.1Ca0.1Sr0.1MnO3 |
WM, (1473/6 h) |
40 |
316.17 |
3.16 |
5 |
284.53 |
2 |
16
|
La0.7Ba0.1Ca0.1Sr0.1MnO3 |
WM, (1473/6 h) |
40 |
316.17 |
2.6 |
4 |
221.16 |
2 |
16
|
La0.7Ba0.1Ca0.1Sr0.1MnO3 |
WM, (1473/6 h) |
40 |
316.17 |
2 |
3 |
162.66 |
2 |
16
|
La0.7Ba0.1Ca0.1Sr0.1MnO3 |
WM, (1473/6 h) |
40 |
316.17 |
1.34 |
2 |
102.51 |
2 |
16
|
La0.7Ba0.1Ca0.1Sr0.1MnO3 |
WM, (1473/6 h) |
40 |
316.17 |
0.61 |
1 |
48.59 |
2 |
16
|
La0.7Ba0.1Ca0.1Sr0.1MnO3 |
SG, (1473/6 h) |
62 |
337.81 |
4.89 |
5 |
229.29 |
2 |
16
|
La0.7Ba0.1Ca0.1Sr0.1MnO3 |
SG, (1473/6 h) |
62 |
337.81 |
4.27 |
4 |
173.66 |
2 |
16
|
La0.7Ba0.1Ca0.1Sr0.1MnO3 |
SG, (1473/6 h) |
62 |
337.81 |
3.51 |
3 |
123.80 |
2 |
16
|
La0.7Ba0.1Ca0.1Sr0.1MnO3 |
SG, (1473/6 h) |
62 |
337.81 |
2.58 |
2 |
74.923 |
2 |
16
|
La0.7Ba0.1Ca0.1Sr0.1MnO3 |
SG, (1473/6 h) |
62 |
337.81 |
1.31 |
1 |
32.619 |
2 |
16
|
La0.7Ba0.15Ca0.15MnO3 |
SSR, (1623/30 h) |
91.18 |
308 |
4.37 |
4 |
140.43 |
2 |
77
|
La0.7Ba0.10Ca0.20MnO3 |
SSR, (1623/30 h) |
89.99 |
279 |
5.43 |
4 |
184.69 |
2 |
77
|
La0.7Ba0.05Ca025MnO3 |
SSR, (1623/30 h) |
132.45 |
261 |
7.01 |
4 |
182.37 |
2 |
77
|
La0.7Ba0.15Ca0.15MnO3 |
SG, (1273/10 h) |
16.41 |
210 |
1.31 |
4 |
144.1 |
2 |
77
|
La0.7Ba0.10Ca0.20MnO3 |
SG, (1273/10 h) |
17.65 |
185 |
1.28 |
4 |
153.6 |
2 |
77
|
La0.7Ba0.05Ca0.25MnO3 |
SG, (1273/10 h) |
54.6 |
130 |
0.27 |
4 |
40.5 |
2 |
77
|
La0.6Ca0.2Ba0.2MnO3 |
SSR, (1473/48 h) |
120 |
300 |
2.4 |
2 |
190 |
2 |
40
|
La0.6Ca0.2Ba0.2MnO3 |
P-SPS, (973/12 m) |
60 |
245 |
4.7 |
2 |
244 |
2 |
40
|
La0.7Ca0.3MnO3 |
SG-SPS, (973/10 m) |
63 |
205 |
2.62 |
5 |
267.2 |
— |
118
|
La0.7Ca0.2Ba0.1MnO3 |
SG-SPS, (973/10 m) |
52 |
225 |
2.51 |
5 |
268.5 |
— |
118
|
La0.7Ca0.1Ba0.2MnO3 |
SG-SPS, (973/10 m) |
44 |
245 |
2.33 |
5 |
270.3 |
— |
118
|
La0.7Ca0.3MnO3 |
SSR, (1573/48 h) |
11 000 |
243 |
7.1 |
5 |
263 |
1 |
120
|
La0.7Ca0.2Ba0.1MnO3 |
SSR, (1573/48 h) |
5000 |
260 |
4.3 |
5 |
258 |
1 |
120
|
La0.7Ca0.1Ba0.2MnO3 |
SSR, (1573/48 h) |
4000 |
302 |
3.5 |
5 |
207 |
1 |
120
|
La0.7Ca0.3MnO3 |
P-SPS, (1073/10 m) |
95 |
253 |
2.6 |
5 |
288 |
2 |
120
|
La0.7Ca0.2Ba0.1MnO3 |
P-SPS, (1073/10 m) |
140 |
280 |
2.3 |
5 |
301 |
2 |
120
|
La0.7Ca0.1Ba0.2MnO3 |
P-SPS, (1073/10 m) |
125 |
311 |
1.7 |
5 |
306 |
2 |
120
|
La0.8Ba0.05Sr0.15MnO3 |
SG, (1373/10 h) |
38.57 |
320 |
4.21 |
5 |
254 |
2 |
17
|
La0.75K0.05Ba0.05Sr0.15MnO3 |
SG, (1373/10 h) |
61.75 |
335 |
4.99 |
5 |
219 |
2 |
17
|
La0.70K0.10Ba0.05Sr0.15MnO3 |
SG, (1373/10 h) |
58.66 |
345 |
5.19 |
5 |
249 |
2 |
17
|
La0.65K0.15Ba0.05Sr0.15MnO3 |
SG, (1373/10 h) |
58.37 |
355 |
4.83 |
5 |
301 |
2 |
17
|
La0.50K0.20Ba0.05Sr0.15MnO3 |
SG, (1373/10 h) |
58.86 |
360 |
3.90 |
5 |
173 |
2 |
17
|
La0.67Sr0.33MnO3 |
SG, (873/12 h) |
48 |
275 |
1092 |
5 |
133.13 |
2 |
221
|
La0.67Sr0.33MnO3 |
SG, (1073/12 h) |
65 |
315 |
1.615 |
5 |
138.82 |
2 |
221
|
La0.67Sr0.33MnO3 |
SG, (1273/12 h) |
85 |
350 |
1.791 |
5 |
229.16 |
2 |
221
|
La0.67Sr0.33MnO3 |
SG, (1473/12 h) |
96 |
370 |
2.394 |
5 |
248.05 |
2 |
221
|
La0.67Sr0.33MnO3 |
SG, (1273/24 h) |
163.8 |
368.2 |
1.5 |
1 |
— |
2 |
25
|
La0.67Sr0.33CoO3 |
SG, (1273/24 h) |
71.8 |
244.1 |
0.145 |
1 |
— |
2 |
25
|
La0.67Sr0.33CrO3 |
SG, (1273/24 h) |
205.7 |
276.1 |
0.023 |
1 |
— |
2 |
25
|
La0.67Sr0.33FeO3 |
SG, (1273/24 h) |
144.7 |
369.9 |
0.002 |
1 |
— |
2 |
25
|
La0.7Sr0.3MnO3 |
SG, (1073/5 h) |
70 |
370 |
1.83 |
2 |
101 |
2 |
137
|
La0.7Sr0.3Mn0.96Fe0.04O3 |
SG, (1073/5 h) |
48 |
335 |
1.26 |
2 |
101 |
2 |
137
|
La0.7Sr0.3Mn0.92Fe0.08O3 |
SG, (1073/5 h) |
43 |
297 |
1.09 |
2 |
108 |
2 |
137
|
La0.7Sr0.3Mn0.88Fe0.12O3 |
SG, (1073/5 h) |
51 |
258 |
0.82 |
2 |
87 |
2 |
137
|
La0.7Sr0.3Mn0.84Fe0.16O3 |
SG, (1073/5 h) |
61 |
197 |
0.60 |
2 |
74 |
2 |
137
|
La0.7Sr0.3Mn0.80Fe0.20O3 |
SG, (1073/5 h) |
58 |
150 |
0.42 |
2 |
46 |
2 |
137
|
La0.7Sr0.3Mn0.76Fe0.24O3 |
SG, (1073/5 h) |
60 |
116 |
0.25 |
2 |
27 |
2 |
137
|
La0.7Sr0.3Mn0.70Fe0.30O3 |
SG, (1073/5 h) |
67 |
98 |
0.13 |
2 |
13 |
2 |
137
|
La0.9Sr0.1MnO3 |
SSR, (1173/96 h) |
— |
172.8 |
2.64 |
5 |
306 |
2 |
222
|
La0.9Sr0.1Mn0.85Fe0.15O3 |
SSR, (1173/96 h) |
— |
168 |
2.79 |
5 |
213 |
2 |
222
|
La0.9Sr0.1Mn0.90Fe0.10O3 |
SSR, (1173/96 h) |
— |
155 |
2.44 |
5 |
197 |
2 |
222
|
La0.8Sr0.2MnO3 |
SG, (1173/10 h) |
41.88 |
332 |
1.94 |
2 |
120.59 |
2 |
164
|
La0.775Gd0.050Sr0.2MnO3 |
SG, (1173/10 h) |
41.28 |
315 |
2.13 |
2 |
108.84 |
2 |
164
|
La0.725Gd0.075Sr0.2MnO3 |
SG, (1173/10 h) |
53.30 |
295 |
2.03 |
2 |
116.40 |
2 |
164
|
La0.700Gd0.010Sr0.2MnO3 |
SG, (1173/10 h) |
58.96 |
292 |
1.71 |
2 |
102.91 |
2 |
164
|
La0.8Sr0.2MnO3 |
SG, (1173/10 h) |
41.88 |
332 |
4.06 |
5 |
— |
2 |
164
|
La0.7Sr0.3Si0.05Mn0.95O3 |
SSR, (1523/6 h) |
— |
365.2 |
0.83 |
1.5 |
71.3 |
2 |
179
|
La0.7Sr0.3Ti0.05Mn0.95O3 |
SSR, (1523/6 h) |
— |
314.7 |
1.08 |
1.5 |
53.4 |
2 |
179
|
La0.7Sr0.3MnO3 |
MM, (1373/2 h) |
— |
376 |
2.7 |
1.8 |
156 |
2 |
116
|
La0.65Gd0.05Sr0.3MnO3 |
MM, (1373/2 h) |
— |
356 |
2.6 |
1.8 |
155 |
2 |
116
|
La0.60Gd0.10Sr0.3MnO3 |
MM, (1373/2 h) |
— |
335 |
2.4 |
1.8 |
166 |
2 |
116
|
La0.55Gd0.15Sr0.3MnO3 |
MM, (1373/2 h) |
— |
311 |
3.7 |
1.8 |
183 |
2 |
116
|
La0.50Gd0.20Sr0.3MnO3 |
MM, (1373/2 h) |
— |
238 |
3.2 |
1.8 |
131 |
2 |
116
|
La0.775Gd0.050Sr0.2MnO3 |
SG, (1173/10 h) |
41.28 |
315 |
4.26 |
5 |
— |
2 |
164
|
La0.725Gd0.075Sr0.2MnO3 |
SG, (1173/10 h) |
53.30 |
295 |
4.23 |
5 |
304.12 |
2 |
164
|
La0.700Gd0.010Sr0.2MnO3 |
SG, (1173/10 h) |
58.96 |
292 |
3.59 |
5 |
281.80 |
2 |
164
|
La0.4Gd0.2Sr0.4MnO3 |
SG, (1173/10 h) |
∼25 |
331 |
0.067 |
6 |
12.196 |
2 |
78
|
La0.4Gd0.2Sr0.4MnO3 |
SG, (1173/10 h) |
∼25 |
318 |
2.486 |
6 |
404.085 |
2 |
78
|
La0.7Sr0.3MnO3 |
SG, (1173/24 h) |
20.09 |
319 |
1.63 |
5 |
178 |
2 |
122
|
La0.69Dy0.01Sr0.3MnO3 |
SG, (1173/24 h) |
23.88 |
315 |
1.21 |
5 |
114 |
2 |
122
|
La0.67Dy0.03Sr0.3MnO3 |
SG, (1173/24 h) |
23.88 |
264 |
1.05 |
5 |
204 |
2 |
122
|
La0.7Sr0.3MnO3 |
SSR, (1753/12 h) |
— |
357 |
3.43 |
5 |
170 |
2 |
126
|
La0.6Eu0.1Sr0.3MnO3 |
SSR, (1753/12 h) |
— |
342 |
4.35 |
5 |
201 |
2 |
126
|
La0.5Eu0.2Sr0.3MnO3 |
SSR, (1753/12 h) |
— |
292 |
4.46 |
5 |
203 |
2 |
126
|
La0.4Eu0.3Sr0.3MnO3 |
SSR, (1753/12 h) |
— |
228 |
4.55 |
5 |
203 |
2 |
126
|
La0.75Eu0.05Sr0.2MnO3 |
SG, (1073/20 h) |
56 |
298 |
0.70 |
2 |
90.11 |
2 |
223
|
La0.75Eu0.05Sr0.2MnO3 |
SG, (1273,20 h) |
97 |
305 |
1.33 |
2 |
85.14 |
2 |
223
|
La0.75Eu0.05Sr0.2MnO3 |
SG, (1473/20 h) |
484 |
305 |
1.76 |
2 |
78.24 |
2 |
223
|
La0.67Ca0.33MnO3 |
SG, (1273/24 h) |
257.76 |
270.5 |
1.8 |
1 |
— |
— |
64
|
La0.67Sr0.33MnO3 |
SG, (1273/24 h) |
223.19 |
301.2 |
1.0 |
1 |
— |
— |
64
|
La0.8□0.2MnO2.8 |
SG, (1173/24 h) |
1059 |
232 |
2.39 |
2 |
126.83 |
2 |
224
|
La0.8□0.2MnO2.9 |
SG, (1173/24 h) |
143 |
302 |
3.04 |
2 |
89.95 |
2 |
224
|
La0.8□0.2MnO3 |
SG, (1173/24 h) |
141 |
300 |
2.88 |
2 |
87.53 |
2 |
224
|
La0.5□0.1Ca0.4MnO3 |
SSR, (1623/12 h) |
— |
251 |
0.78 |
1 |
24.33 |
2 |
39
|
La0.5□0.1Ca0.4MnO3 |
SSR, (1623/12 h) |
— |
251 |
2.18 |
2 |
71.64 |
2 |
39
|
La0.5□0.1Ca0.4MnO3 |
SSR, (1623/12 h) |
— |
251 |
3.24 |
3 |
124.42 |
2 |
39
|
La0.5□0.1Ca0.4MnO3 |
SSR, (1623/12 h) |
— |
251 |
4.08 |
4 |
180.69 |
2 |
39
|
La0.5□0.1Ca0.4MnO3 |
SSR, (1623/12 h) |
— |
251 |
4.80 |
5 |
232.20 |
2 |
39
|
La0.8Ca0.2MnO3 |
SSR, (1473/24 h) |
— |
187 |
∼4.110 |
5 |
∼269 |
— |
114
|
La0.8Ca0.15□0.05MnO3 |
SSR, (1473/24 h) |
— |
183 |
∼4.050 |
5 |
∼267 |
— |
114
|
La0.8Ca0.10□0.10MnO3 |
SSR, (1473/24 h) |
— |
183 |
∼4.014 |
5 |
∼284 |
— |
114
|
La0.8Ca0.05□0.15MnO3 |
SSR, (1473/24 h) |
— |
182 |
∼3.681 |
5 |
∼293 |
— |
114
|
La0.8□0.2MnO3 |
SSR, (1473/24 h) |
— |
182 |
∼3.497 |
5 |
∼260 |
— |
114
|
La0.8Ca0.2MnO3 |
SSR, (1473/24 h) |
— |
241 |
∼7.70 |
5 |
∼255 |
— |
121
|
La0.8Ca0.10□0.10MnO3 |
SSR, (1473/24 h) |
— |
264 |
∼7.25 |
5 |
∼275 |
— |
121
|
La0.8□0.20MnO3 |
SSR, (1473/24 h) |
— |
259 |
∼7.60 |
5 |
∼230 |
— |
121
|
La0.8Ca0.2MnO3 |
SSR, (1473/24 h) |
— |
241 |
∼5.50 |
2 |
∼95 |
— |
121
|
La0.8Ca0.10□0.10MnO3 |
SSR, (1473/24 h) |
— |
264 |
∼4.30 |
2 |
∼105 |
— |
121
|
La0.8□0.20MnO3 |
SSR, (1473/24 h) |
— |
259 |
∼5.00 |
2 |
∼92 |
— |
121
|
La0.8Ca0.2MnO3 |
SSR, (1473/24 h) |
— |
241 |
∼2.00 |
0.5 |
∼25 |
— |
121
|
La0.8Ca0.10□0.10MnO3 |
SSR, (1473/24 h) |
— |
264 |
∼1.10 |
0.5 |
∼40 |
— |
121
|
La0.8□0.20MnO3 |
SSR, (1473/24 h) |
— |
259 |
∼1.15 |
0.5 |
∼26 |
— |
121
|
La0.55□0.1Ca0.35MnO3 |
SG, (1173/24 h) |
— |
274.7 |
1.97 |
2 |
71.88 |
2 |
43
|
La0.65Ba0.35MnO3 |
SSR, (1473/24 h) |
— |
325 |
1.83 |
5 |
186 |
2 |
168
|
La0.65Ba0.30□0.05MnO3 |
SSR, (1473/24 h) |
— |
345 |
3.75 |
5 |
180 |
2 |
168
|
La0.65Ba0.25□0.10MnO3 |
SSR, (1473/24 h) |
— |
332 |
3.91 |
5 |
213 |
2 |
168
|
La0.65Ba0.15□0.20MnO3 |
SSR, (1473/24 h) |
— |
288 |
4.12 |
5 |
231 |
2 |
168
|
La0.67Sr0.33MnO3 |
SSR, (1623/12 h) |
— |
365 |
1,62 |
1 |
— |
2 |
146
|
La0.58Sr0.33□0.09MnO3−δ |
SSR, (1623/12 h) |
— |
367 |
1.41 |
1 |
— |
2 |
146
|
La0.63Sr0.24□0.09MnO3−δ |
SSR, (1623/24 h) |
— |
355 |
1.78 |
1 |
— |
2 |
146
|
La0.67Sr0.33MnO3 |
SSR, (1623/12 h) |
— |
365 |
4.78 |
5 |
120 |
2 |
146
|
La0.58Sr0.33□0.09MnO3−δ |
SSR, (1623/12 h) |
— |
367 |
4.12 |
5 |
103 |
2 |
146
|
La0.67Sr0.24□0.09MnO3−δ |
SSR, (1623/12 h) |
— |
355 |
5.08 |
5 |
142 |
2 |
146
|
La0.67Sr0.15□0.18MnO3−δ |
SSR, (1623/12 h) |
— |
310 |
4.61 |
5 |
— |
2 |
135
|
La0.67Sr0.06□0.27MnO3−δ |
SSR, (1623/12 h) |
— |
276 |
4.11 |
5 |
— |
2 |
135
|
|
Composite |
0.75La0.67Ca0.33MnO3/0.25La0.67Sr0.33MnO3 |
SG, (1273/24 h) |
342.09 |
370 |
>1.0 |
1 |
— |
— |
64
|
0.50La0.67Ca0.33MnO3/0.50La0.67Sr0.33MnO3 |
SG, (1273/24 h) |
326.7 |
335 |
1.1 |
1 |
— |
— |
64
|
0.25La0.67Ca0.33MnO3/0.75La0.67Sr0.33MnO3 |
SG, (1273/24 h) |
237.88 |
340 |
0.8 |
1 |
— |
— |
64
|
0.75La0.62Nd0.05Ba0.33MnO3/0.25Ni0.5Zn0.5Fe2O4 |
CP, (1273/10 h) |
— |
290 |
3.03 |
5 |
242 |
2 |
44
|
0.75La0.62Nd0.05Ba0.33MnO3/0.25Ni0.4Zn0.6Fe2O4 |
CP, (1273/10 h) |
— |
281 |
2.40 |
5 |
252.72 |
2 |
44
|
0.75La0.62Nd0.05Ba0.33MnO3/0.25Ni0.4Zn0.7Fe2O4 |
CP, (1273/10 h) |
— |
255 |
2.30 |
5 |
300.60 |
2 |
44
|
LaFe11.6Si1.4 (<100 μm)/5 wt% Pr2Co7 |
Arc-M-SPS, (for SPS 1273/5 m forwad to (1323/24 h)) |
— |
270 |
2.29 |
5 |
115 |
2 |
31
|
LaFe11.6Si1.4 (<100 μm)/10 wt% Pr2Co7 |
Arc-M-SPS, (for SPS 1273/5 m forwad to (1323/24 h)) |
— |
297 |
2.22 |
5 |
133 |
2 |
31
|
LaFe11.6Si1.4 (100–200 μm)/10 wt% Pr2Co7 |
Arc-M-SPS, (for SPS 1273/5 m forwad to (1323/24 h)) |
— |
280 |
3.64 |
5 |
149 |
2 |
31
|
LaFe11.6Si1.4 (200–300 μm)/10 wt% Pr2Co7 |
Arc-M-SPS, (for SPS 1273/5 m forwad to (1323/24 h)) |
— |
275 |
1.92 |
5 |
138 |
2 |
31
|
3.2.2 Heusler alloys.
Heusler alloys, also commonly known as shape memory alloys, were discovered in the late 19th century and have been extensively researched to this day. Since their initial discovery, Heusler alloys have grown to include more than 1500 members. The structural characteristic of these materials include face-centered cubic (FCC) and body-centered cubic (BCC) unit cells. Heusler alloys have two general formulas both A2BC (full Heusler) and ABC (half Heusler), where A and B are filled with transition metal elements, and C is filled with elements from groups III–IV A.86,87Fig. 3(A) illustrates the structure of full Heusler (a) and half Heusler (b).
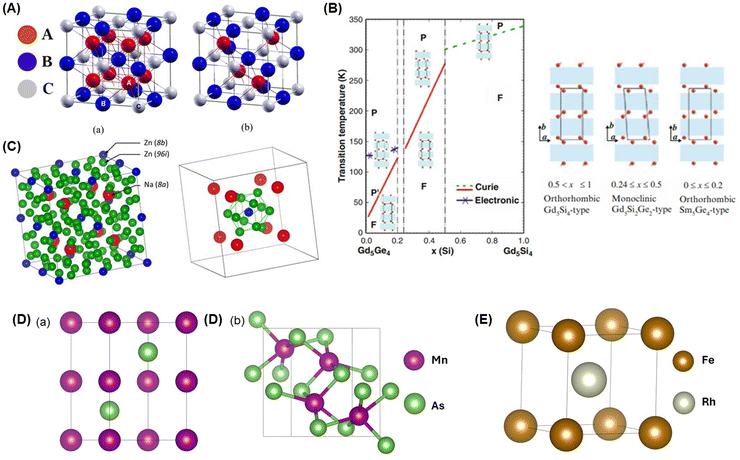 |
| Fig. 3 (A) Illustration of crystal structure for (a) full Heusler and (b) half Heusler reprinted from ref. 87 with open acess from MDPI,87 (B) phase diagram of magnetic and crystal structure of Gd5(SixGe1−x)4 reprinted from ref. 96 with permission, copyright 2001, Wiley,96 (C) crystal structure of NaZn13-type in La(FexSi1−x)13 reprinted from ref. 101 with open access from MDPI,101 (D) crystal structure of MnAs (a) NiAs-hexagonal type and (b) MnP-orthorhombic type obtained by MaterialProjects,108 (E) crystal structure of FeRh obtained by crystallography open database,192 where (D) and (E) are illustrated by VESTA.193 | |
Heusler alloys, such as Ni–Mn–Ga, have been extensively developed due to their exceptional MCE properties resulting from the FOMT behavior and the transformation from ferromagnetic austenite to weakly magnetic martensite.29,88–94 Zheng et al. reported Ni44Co6Mn37In13 alloy, and described the martensitic phase transition under a magnetic field. The results showed values of −ΔSM = 9.8 J kg−1 K−1 and RCP = 221.7 J kg−1 occurring around TC = 419.5 K under a magnetic field 6 T. However, the Ni44Co6Mn37In13 alloy exhibited thermal and magnetic hysteresis, resulting in losses in MCE properties.29 Furthermore, Datta et al. conducted research on Ni–Mn–Ga-based materials with varying compositions, including Ni50Mn27Ga23 (NMG-1), Ni54Mn21Ga25 (NMG-2), and Ni54Mn25Ga21 (NMG-3). Different types of magnetic phase transitions were observed, with SOMT behavior for NMG-1, NMG-2, and FOMT behavior for NMG-3. Although the −ΔSM values were lower than those reported by Zheng et al., it is crucial to note that differences in the composition can influence the type of magnetic phase transition.95 Additionally, Ni–Mn–X alloys with X = In, Sn, and Sb have been found to exhibit −ΔSM values in the range of 11.85 to 20.00 J kg−1 K−1.94 Kutynia and Gebara reported on Mn1−xZrxCoGe materials with x = 0.03, 0.05, 0.07, and 0.1, showing −ΔSmaxM values with a range 2.94 to 13.42 J kg−1 K−1.87 In summary, the investigations mentioned above indicate that composition, structure, and doping determination play crucial roles in determining the magnetocaloric properties of Heusler alloys. The comprehensive performance summary of MCE in Heusler alloys is provided in Table 2.
3.2.3 Gd5(SixGe1−x)4 alloys.
The development of Gd-based materials, such as Gd5(SixGe1−x)4, has attracted attention due to their excellent magnetic properties.59Fig. 3(B) illustrates the crystal structure transformation at specific temperatures, categorized into three regions. For the range 0.5 < x ≤ 1, an orthorhombic crystal structure of the Gd5Si4 type is presented in both the paramagnetic and ferromagnetic phases. This condition arises from the covalent bonding of Si(Ge)–Si(Ge) between layers. The transition occurring in this range was SOMT without a change in the crystal structure. In the concentration range 0.24 ≤ x ≤ 0.5, a FOMT is observed along with a change in the orthorhombic crystal structure (ferromagnetic state) of Gd5Si4 below TC to the monoclinic structure of Gd5Si2Ge2 (paramagnetic state) above TC. This is caused by the disruption of half of the Si(Ge)–Si(Ge) bonding between the layers. Finally, in the range 0 ≤ x ≤ 0.24, FOMT and a change in the crystal structure from orthorhombic Gd5Ge4 above TC to orthorhombic Gd5Si4 below TC were observed, accompanied by the absence of Si(Ge)–Si(Ge) bonding between layers.96,97
Based on the report by Pecharsky and Gschneider a Gd5(Si2Ge2) material indicates −ΔSM = 18.4 J kg−1 K−1 and RCP = 535 J kg−1 with TC = 276 K under a magnetic field of 5 T, suggesting the occurrence of a FOMT. Additionally, researchers have explored doping at Gd sites or (Si1−xGex)4 and have applied hydrostatic pressure treatments to achieve excellent MCE properties with TC around room temperature.1,98–100 Despite the high MCE performance and potential for application in magnetic refrigerators, there are still factors to consider, such as hysteresis losses due to FOMT properties, a narrow working temperature range, difficulty in fabricating methods, limited and expensive materials.
3.2.4 La(Fe13−xSix) alloys.
La(Fe13−xSix) alloys are one the most promising for magnetic refrigeration applications at room temperature. In the concentration x ≤ 2.5, the crystal structure of the LaFe13−xSix alloys is NaZn13 type cubic with the Fm
c space group, as illustrated in Fig. 3(C). The addition of Si to LaFe13 shows a negative lattice expansion at TC and a transition known as the itinerant electron metamagnetic (IEM) transition above TC.101 The IEM transition occurs due to changes in the density of states at the Fermi level when a magnetic field is applied, which occurs with a slight increase in Si concentration.1 This led to a sharp decrease in the magnetization change, enhancing the MCE properties of the alloy, accompanied by FOMT. Hu et al. reported an investigation of La(Fe11.4Si1.6), which showed sharper magnetization change and larger −ΔSM than La(Fe10.4Si2.6). They calculated −ΔSM of 19.4 J kg−1 K−1 under a magnetic field of 5 T.102 Therefore, this research shows the importance of negative lattice expansion as a key parameter influencing the MCE properties of La(Fe13−xSix) alloys.
The La(Fe13−xSix) alloys are not limited to investigate in the IEM transition. Other developments have been carried out, such as modifying synthesis methods, heat treatments, and compound compositions, to achieve ideal MCE properties. Zhang et al. reported La1.2Fe11.2Si1.4B0.75 which is produced using different synthesis methods both Arc-melting (solid) and melt-spinning at 10 m s−1 and 50 m s−1. All three samples indicated the presence of the IEM transition, marked by a very sharp magnetization change. This led to presenting FOMT state and high −ΔSM values of 6.1, 20.2, and 13.5 J kg−1 K−1 under a magnetic field of 2 T. Additionally, the TC value increased with the addition of B concentration (188–191 K), associated with the presence of Fe–Fe exchange interactions with a broadening of the Fe–Fe distance and cell volume.58 Another study compared the heating behavior of La(Fe13−xSix) alloy-based materials using hot pressing sintering (HPS) and spark plasma sintering (SPS).30 As observed from the porosity, density, and compressive strength analysis, the SPS method provided better mechanical properties than the HPS method. The value of −ΔSM from the SPS and HPS methods reached 12.8 and 12.1 J kg−1 K−1, respectively. Thus, it was concluded that the use of the SPS method presents high MCE properties along with good mechanical properties, making it potentially suitable for application as a magnetic refrigerator.30 More detailed information on La(Fe13−xSix) alloys MCE properties from previous studies is tabulated in Table 2.
3.2.5 MnAs alloys.
MnAs alloys are promising candidates for magnetic refrigeration applications, because of their significantly high MCE properties. This is attributed to the magneto-structural transition of MnAs from the hexagonal NiAs structure to the orthorhombic MnP structure as it approaches TC = 313 K.103,104Fig. 3(D) illustrates the hexagonal NiAs structure with space group P63/mmc (a) below TC and the orthorhombic MnP structure with space group Pnma (b) above TC.105–108 The MnAs alloy is known for its high −ΔSM value, reaching 47 J kg−1 K−1 under a magnetic field of 5 T at TC = 318 K.109 Additionally, Wada et al. experimented by doping MnAs with Sb, and one of the results, Mn(As0.9Sb0.1), is reported −ΔSM of 32 J kg−1 K−1 and TC of 283 K under a magnetic field of 5 T. Furthermore, this sample exhibited the loss of hysteresis behavior at high temperatures.110 Sathyanarayana and Mani investigated the MCE properties of Mn(As1−xSbx) with x = 0.05–0.30. The results revealed a range of −ΔSM values ranging from 20.30 to 23.00 J kg−1 K−1 and RCP values from 220 to 260 J kg−1 under a magnetic field of 5 T, accompanied by the FOMT state. All samples exhibited a ferromagnetic to paramagnetic phase transition with a decrease in TC from 300.5 to 242 K as the concentration x increased.35
The high MCE properties of MnAs are also manifested under hydrostatic pressure. The presence of hydrostatic pressure effects on MnAs leads to the conclusion that there is a decrease in TC with an increase in pressure and an exponential increase in MCE properties proportional to the pressure increment.111 The anticipated increase −ΔSM value was estimated to reach 267 J kg−1 K−1 under a pressure of 2.23 kbar in a 5 T magnetic field. However, this effect diminishes and becomes detrimental when pressed beyond 2.64 kbar.105 However, behind this promising potential, there are critical issues such as the challenging process of obtaining arsenic (As), which is environmentally toxic and limits its practical applications.112
3.2.6 Fe-Based alloys.
Iron-based alloys have been extensively investigated due to their high −ΔSM values and comparable with other materials. These materials typically exhibit FOMT behavior and magneto-structural transformations which are associated with good MCE properties and high −ΔSM values.34 Various types of materials have been developed from Fe-based alloys, such as Fe17R2 (R = rare earth element), Fe–Ni–M (M = B, Mn, Cr, Mo), Fe–M (M = Rh, Ni, Zr), Fex(M1−x)3Al (M = Cr and Mn), Fe–B–Cr–R (R = La, Ce, Gd, Nd), Fe–Zr–B–M (M = Mn, Cr, Ni, Al, Ti, Mo, Co, Er, Sm), Fe–B–X (X = Mn, Nb, Cr, Cu), and Fe–Zr–M (M = Mn, Dy).1,34,85
Two of the Fe-based alloys mentioned above are particularly interesting because of differences in their MCE properties such as FeNi and FeRh. Research on FeNi alloys has focused on reducing the TC values, which are still above room temperature. The addition of Mn to FeNi alloys resulted in a decrease in TC to 338 and 317 K for (Fe70Ni30)95Mn5 and (Fe70Ni30)92Mn8, respectively.85 On the other hand, FeRh alloys, with a cubic crystal structure as shown in Fig. 3(E), have been extensively studied due to their spectacular giant MCE properties, such as Fe50Rh50 and Fe49Rh51.22 Fe50Rh50 has a TC of 400 K, above room temperature, and requires an applied magnetic field of up to 40 T to obtain TC at around room temperature. Meanwhile, Fe49Rh51 had a TC of 315.6 K. It is noteworthy that FeRh alloys are highly sensitive to thermal treatment and composition.34 Chirkova et al. investigated Fe49Rh51 with slight Ni doping, revealing a significant decrease in TC to 266 K and obtaining a −ΔSM value of 10.3 J kg−1 K−1 under a magnetic field of 2 T. The emergence of high −ΔSM values is associated with FOMT behavior.34 The FOMT behavior shows hysteresis losses due to thermal and magnetic hysteresis. Therefore, although these materials exhibit excellent MCE values, other factors must be considered before their application in magnetic refrigerators.
3.3 Ceramic materials
3.3.1 Perovskite manganite materials.
Perovskite manganites (PM) are ceramic materials with the general formula R1−xAxMnO3, where R represents rare earth metals, trivalent elements such as La, Pr, Nd, Sm, Eu, Gd, Ho, Tb, Y and A represents elements such as monovalent elements (Li, Na, K, Ag, etc)4,15 and divalent elements (Mg, Ca, Sr, Ba, etc)41,44,113 which have been extensively combined. The mixed element combinations of PM will create a mixed valence at site A or B. For example, if monovalent and divalent elements are substituted in PM, it will provide a new chemistry stability state as R1−x3+Ax1+Mn1−2x3+Mn2x4+O2− and R1−x3+Ax2+Mn1−x3+Mnx4+O2− respectively.15,114 The existence of Mn3+ and Mn4+ ions in PM can be attracted by exchange interactions, which can influence the magnetic properties of PM. This fact has led researchers to investigate it as an alternative material for MRT. PM has several advantages, including cost-effectiveness, shorter production processes, relative ease of production, chemical stability, good structure, environmental friendliness, resistance to corrosive environments, SOMT behavior, excellent MCE properties, and easily adjustable TC within the room-temperature range.40,42,43,114–124
The basic crystal structure of perovskite ABO3 is cubic, where cation A occupies the A sites with twelve coordination sites (AO12), and a small portion of cations occupy the B sites with six octahedral coordination (BO6).19 However, PM are substituted with specific atoms and experience structural distortions due to changes in the cation size and the Jahn–Teller effect. In a cubic crystal, Jahn–Teller distortion is observed with a reduction in the symmetry and the splitting of eg levels. This event is influenced by the doping and energetic positions, which strongly affect the hybridization between the Mn3+ and O states in the 2p orbital. According to previous studies, the crystal field is determined by ligand states based on the 3d shell structure of ions: three electrons in the low t2g state (t32g) and one electron in the high eg state (e1g) for Mn3+ ions and a configuration of (t32g) for Mn4+ ions.45,52 As a result, the cubic structure transforms into a rhombohedral or orthorhombic structure, as illustrated in Fig. 4(A).
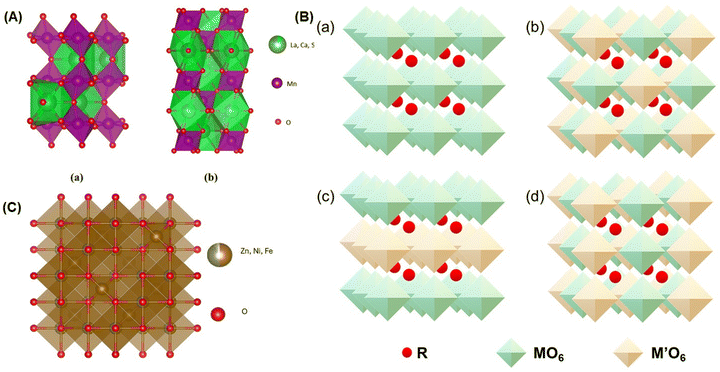 |
| Fig. 4 Illustration of crystal structure (A) perovskite manganites (a) orthorhombic-La0.6Ca0.3Sr0.1MnO3 and (b) rhombohedral-La0.6Ca0.2Sr0.2MnO3 obtained by crystallography open database,194 (B) crystal structure of double perovskite-R2MM′O6 for (a) similar M and M′, (b) rock-salt, (c) layered and (d) columnar order redrawn from ref. 19, (C) crystal structure of spinel ferrite cubic-Zn0.9Ni0.1Fe2O4 obtained by crystallography open database,130 where (A) and (C) are illustrated by VESTA.193 | |
The MCE properties of PM materials have been studied by several researchers. Banik et al. reported that Pr0.8Sr0.2MnO3 exhibits a decrease in magnetization around TC = 150 K with −ΔSM = 3.54 J kg−1 K−1 and RCP = 289 J kg−1 under a magnetic field of 5 T.125 Meanwhile, Khlifi et al. investigated La0.8Ca0.2−x□xMnO3 (0 ≤ x ≤ 0.2) with annealing treatment at 1073 K, showing a transition from ferromagnetic to paramagnetic phase around TC, with values of 269, 273, and 276 K, and a decrease in magnetization due to Ca2+ ion substitution. The presence of Ca2+ ions can convert Mn3+ ions to Mn4+, which is linked to double-exchange and super-exchange interactions in the system. Both, the −ΔSM values and RCP values for the samples appear in the ranges of 7.25–7.70 J kg−1 K−1 and 230–275 J kg−1, respectively in under a magnetic field of 5 T, respectively.121 Furthermore, Vadnala et al. studied La0.7−xEuxSr0.3MnO3 compounds with x = 0.0, 0.1, 0.2, 0.3 to adjust the TC value around room temperature, accompanied by an enhancement in the MCE properties. The TC values for all the samples were 357, 342, 292, and 228 K, respectively. The decrease in TC is due to the substitution of Eu2+ ions, which have a smaller ionic radius. The −ΔSM values increased from 3.43 to 4.55 J kg−1 K−1, accompanied by an increase in the RCP values from 170 to 203 J kg−1. The analysis of the magnetic phase transition in La0.7−xEuxSr0.3MnO3 compounds exhibits a SOMT behavior, which is associated with the absence of hysteresis losses due to thermal and magnetic hysteresis.126 A summary of these examples is presented in Table 2.
3.3.2 Double perovskite materials.
Double perovskites (DP) based on rare-earth and transition metals have been extensively studied due to their fascinating physical properties, such as MCE properties under cryogenic conditions. Additionally, this material has been well-researched for its easy synthesis, chemical stability, and high physical stability. The structure of DP materials is essentially similar to that of perovskite structure, but in a double version. Therefore, the general formula for DP is (ABO3)2, which can have crystal structures as depicted in Fig. 4(B) when connected with rare-earth and transition metals, forming R2MM′O6 (R represents a rare-earth metal, M and M′ are transition metals).19 Several examples of MCE materials based on DP structures (R2MM′O6) are listed in Table 2.19,127–129 An example is R2NiMnO6, which has a monoclinic crystal structure and is known as a B-sites rock-salt type ordered structure where magnetic ions Ni2+ and Mn4+ alternate along the c-axis. Furthermore, the SE interaction between Ni2+–O–Mn4+ associated with the distribution of Mn4+ and Ni2+ ions gives rise a high-temperature ferromagnetic ordering. If the rare-earth metal elements (R) of R2MM′O6 changed from La to Lu, it would decrease in TC, ranging from 40 to 275 K, which is attributed to decreased ionic radius. Meanwhile, the −ΔSM value is 35.5 under magnetic field 7 T, and 4.9, 2.3, 5.2, 6.4 under magnetic field 5 T for R = Gd, Dy, Eu, Pr, Nd, Tb, and Ho.19
3.3.3 Spinel ferrite materials.
Spinel ferrites have the general formula AFe2O4, where A is a transition metal from the 3d group (Mn, Fe, Co, Ni, Cu, Zn, etc.).5 The AFe2O4 type has a cubic spinel crystal structure with the Fd
m space group, as depicted in Fig. 4(C).130 The potential applications of spinel ferrites are broad, such as high-density information storage, electromagnetic wave absorption, biomedical applications, and MRT. However, based on the literature review, there are not many reports on the MCE properties of spinel ferrite. One reason why this material has not been extensively investigated for MCE properties is its relatively small −ΔSM values, even when applied to high magnetic fields. Additionally, the highly sensitive TC values pose a consideration, as MCE applications, especially for magnetic refrigeration, require a working temperature range around room temperature.
Oumezzine et al. reported on Zn0.6−xNixCu0.4Fe2O4 (0 ≤ x ≤ 0.6) compounds which were synthesized using the Pechini sol–gel method. They observed a transition from ferromagnetic to paramagnetic phases around TC values of 305, 565, 705, and > 750 K for x from 0 to 0.6. The significant increase in TC was associated with the enhanced interactions between A and B in the AB2O4 structure. Analysis of the transition type using Arrot plots confirmed the occurrence of SOMT behavior. Furthermore, they calculated −ΔSM values of 1.16, 1.41, 1.61 J kg−1 K−1, and RCP values of 289, 141, 233 J kg−1 for x = 0.0, 0.2, 0.4 under a magnetic field of 5 T.62 Jiyu Hu et al. also conducted research on spinel ferrite materials with the chemical formula CoGa1.2Fe0.8O4, which exhibited TC = 210 K and −ΔSM = 1.5 J kg−1 K−1 under a magnetic field of 5 T.36 A summary of the MCE performance from various previous studies is provided in Table 2.
3.4 Composite materials
In the case of composite material research, there are studies on their magnetic properties including the MCE. Zhong et al. reported a composite material LaFe11.6Si1.4/Pr2Co7, which showed variations in particle size and Pr2Co7 content. The −ΔSM values for the different samples ranged from 1.92 to 3.64 J kg−1 K−1, with RCP values in the range of 84 to 149 J kg−1 under a magnetic field of 2 T. Meanwhile, the TC values of the samples increased from 230 to 297 K with variations in particle size.31 Additionally, Ezaami et al. also reported (1 − x)La0.7Ca0.2Sr0.1MnO3/xLa0.7Ca0.15MnO3 based on the rule of mixture estimation. In the investigation of the material (1 − x)La0.7Ca0.2Sr0.1MnO3/xLa0.7Ca0.15MnO3, the optimum MCE properties were found at x = 0.45, and more details can be found in their report.42 In addition, Tillaoui et al. reported the magnetocaloric effect properties in (0.75)La0.62Nd0.05Ba0.33MnO3/(0.25)Ni1−xZnxFe2O4 composites (x = 0.5, 0.6, 0.7) where it revealed TC around room temperature ∼290 K and provided −ΔSM with ranges of 3.03, 2.40, 2.30 J kg−1 K−1 for x = 0.5, 0.6, 0.7 respectively. They also reported the value of the RCP which had a good value with ranges of 242, 252.72, 300.60 for x = x = 0.5, 0.6, 0.7.44
4. Phenomena and parameters influencing the behavior of MCE in perovskite manganites
As mentioned, a lot of PM exhibit SOMT behavior. Materials with SOMT behavior show reversible magnetic cooling cycles due to their small magnetic and thermal hysteresis.1 Despite the high values of −ΔSM in Table 1, but the −ΔSM values of PM are relatively lower than those of the alloys. On the positive side, the valuable aspects of the PM are that −ΔSM and TC can be easily tuned at room temperature, making researchers extensively explore materials for obtaining better MCE properties with ideal criteria. Several important parameters in PM will be discussed in the following section.
4.1 Types of substitution in perovskite manganites
The effect of substitution in PM materials is on the exchange interactions that occur. There are two possible interactions, namely the double-exchange (DE) interaction between Mn3+–O2−–Mn4+ and the super-exchange (SE) interaction between Mn3+–O2−–Mn3+.18Fig. 5 shows the principles of exchange interactions. It is believed that if part of the trivalent ion, A-sites, in the perovskite material is replaced by a lower valence material and part of Mn3+ is replaced by Mn4+. As a result, the spin in the eg orbit becomes vacant, and O2− acts as a bridge between two manganese states in the DE interaction.131 For example, if A-sites are substituted with divalent ions, the equation becomes R1−x3+Ax2+Mn1−x3+Mnx4+O32−. Substitution in PM materials is categorized into three groups: substitution at site-A, site-B, and vacancy.18,132–141 The determination of these three substitution methods in PM materials is based on considerations of ion valence, ion size, and crystal structure.
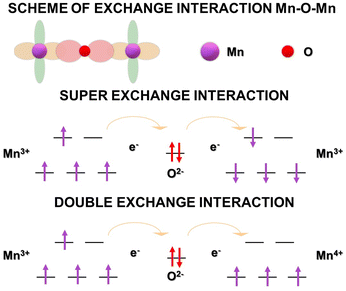 |
| Fig. 5 Schematic of exchange interactions in PM systems. | |
4.1.1 Substitution in A-sites of perovskite manganite systems.
Substitution at the A-site has numerous variations that result in different magnetic moments, valence states, and ionic radii to generate a mixed valence of Mn3+ and Mn4+. This mixed valence allows the generation of DE at low temperatures, leading to ferromagnetic materials, accompanied by changes in the average ion radii on the A-site, crystal structure, and magnetic moments. The effects of DE and MCE on the material will result in various magnetic order phenomena such as charge order, orbit order, and coupling together. These conditions will influence the values of TC and −ΔSM.18 The substitution at the A-site can consist of two types: single-ion substitution (Na, K, Ag, Li, etc.) and double-ion substitution (Sr, Ca, Mg, Ba, etc.). It is known that different valence conditions and ionic radius due to substitution have different effects on the structure, TC, and MCE in LaMnO3.142 For instance, substitution at the A-site includes La0.7Ca0.3MnO3,117 and La0.7Ba0.05Ca0.25MnO3.77 which exhibit higher −ΔSM values than LaMnO3. Based on several studies, it can be concluded that A-site substitution with low-valence ions significantly influences changes in magnetic entropy and TC, often exhibiting extreme values that need to be considered for the effects of substitution in Mn3+/Mn4+ in the material system.18,77,117,119,121,143
4.1.2 Substitution in B-sites of perovskite manganite systems.
Substitution at the B-site involves replacing Mn ions with specific ions to tailor TC and increase the magnetic moment, which can enhance the value of −ΔSM.18,137,144 The elements substituted at the B-site are transition metals (Ni, V, Fe, Co, Cr, and Cu). Al-Shahumi et al. reported an investigation on La0.7Sr0.3Mn1−xFexO3 (x = 0.0–0.30) compounds, where the TC values decreased from 370 to 98 K, accompanied by a decrease in the −ΔSM values from 1.83 to 0.13 J kg−1 K−1. The linear decrease in the TC and −ΔSM values are due to the weakening of the DE interaction, which affects the reduction in the magnetic interaction between the Mn magnetic moments. Additionally, the saturation magnetization decreased with increasing Fe concentration. The addition of Fe resulted in competition between SE and DE interactions. This is because the eg and t2g electrons in Fe3+ ions participate in the SE interaction with neighboring Mn and Fe ions in the lattice.137 Researchers Riahi et al. also reported on La0.7Ca0.15Sr0.15Mn1−xGdxO3 (x = 0.00–0.06), which exhibited decreasing TC values from 338 to 203 K and −ΔSM values from 0.344 to 0.629 J kg−1 K−1 under a magnetic field of 1 T.124 It can be concluded that substitution at the B-site results in the value of lower TC and −ΔSM values than doping at the A-site. This is because the natural magnetism of perovskite manganese oxide and MCE is caused by DE based on Mn3+–O2−–Mn4+. Another reason for doping at the B-site being weaker than the A-site is attributed to: 1. The change in TC is directly dependent on the exchange interactions that occur. 2. After doping, the dopant ions replace one of the Mn3+–O2−–Mn4+ ions in the DE.18,124,137
4.1.3 Vacancy substitution in perovskite manganite systems.
The last type is the vacancy substitution (□), which reduces the composition either at the A-site or B-site. Vacancy substitutions are divided into two categories: vacancy substitution in oxygen or elements.18 Vacancy substitution in PM materials oxygen sites tends to reduce the TC and −ΔSM values because the decreased DE interactions occur. The reduction in DE interactions can be associated with oxygen ions playing a crucial role as a bridge between two Mn3+ and Mn4+ ions. Therefore, if the oxygen ions are reduced, and the Mn3+–O2−–Mn4+ interactions are not optimal. On the other hand, if vacancy substitution occurs at element sites, it will affect the composition of Mn3+ and Mn4+ ions.145–152 The appearance of Mn4+ ions can be linked to the ability of the system to maintain its chemical stability by converting Mn3+ ions to Mn4+, allowing the chemical equation to become La(1−x)3+□xMn(1−y)3+Mn2y4+O32−.114
Patra et al. examined a vacancy substitution in La0.9MnO3 samples, presenting a −ΔSM value of 4.9 J kg−1 K−1 with TC = 254 K under a magnetic field of 2 T, which was larger than the parent compound LaMnO3. Additionally, Sankar and Joy investigated the magnetic properties of La1−xMnO3, and reported an increasing trend in TC and magnetization with the increasing x content. The TC value increased from 116 to 240 K with x from 0.03 to 0.13.153 The increase in the TC value in the system is associated with the increased amount of Mn4+ ions, strengthening the occurrence of DE interactions. Moreover, it is known that vacancy substitution also significantly influences lattice distortion and decreases the ionic radius at the A-site, which is another factor in controlling the TC value.18
4.2 Composition of perovskite manganite systems
The determination of the system's composition can estimate the amounts of Mn3+ and Mn4+ ions. Known Mn3+/Mn4+ ion ratio close to 2/1 or 7/3 will present excellent MCE properties because the strong DE interactions occur in the ferromagnetic state.16 On the other hand, the composition also influences the occurrence of Jahn–Teller distortion.18 Schiffer et al. studied the magnetic property behavior of La1−xCaxMnO3 with increasing x, presenting three magnetic phase regions: paramagnetic, ferromagnetic, and antiferromagnetic.154 Another example is the investigation by Szewczyk et al. into La1−xSrxMnO3, where the addition of x shows regions of ferromagnetic, paramagnetic, and antiferromagnetic phases.155–157 Ju et al. also investigated the magnetic phase behavior of La1−xBaxMnO3, which exhibits a ferromagnetic phase.158 The phase diagrams for these three examples are clearly illustrated in Fig. 6(A). In this case, the substitution with divalent ion and composition with x = 0.3 show ferromagnetic behavior. This demonstrates the correlation between strong DE interactions and the ferromagnetic behavior of the PM system. Therefore, considering the composition or amount of doping used is one of the considerations for predicting the material's properties.
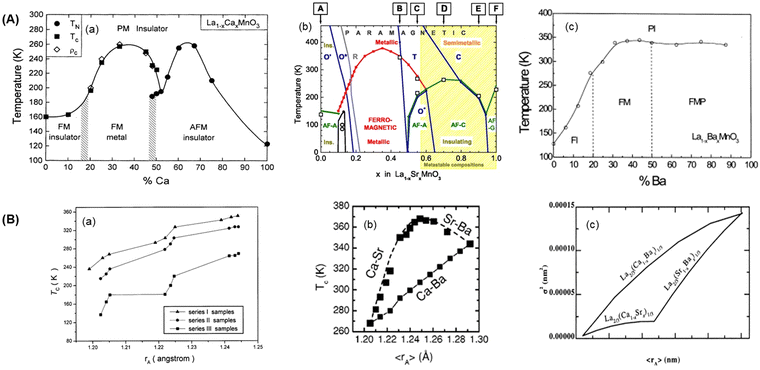 |
| Fig. 6 Phase diagram of substituted PM materials in (A) (a) La1−xCaxMnO3 reprinted with permission, copyright 1995, American Physics Society,154 (b) La1−xSrMnO3 reprinted with permission, copyright 2005, American Physical Society,157 (c) La1−xBaxMnO3 reprinted with permisson, copyright 2000, Elsevier,158 (B) graph of influencing 〈rA〉 to TC reprinted with permision (a), copyright 2001, Elsevier,159 (b), copyright 2002, American Institute of Physics161 and (c) the influence 〈rA〉 to cation mismatch effect reprinted with permission, copyright 2002, Elsevier.165 | |
4.3 Crystal structures
The substitution in PM materials can influence the crystal structure due to changes in the substituted ionic radius. The discussion on the crystal structure of PM materials will be related to several factors such as the average ionic radius at site-A, mismatch effect (σ2), Goldsmith tolerance (t), and Jahn–Teller distortion. These four factors will aid in predicting the characteristics of the samples, particularly PM materials. The factors mentioned above will be discussed in more detail below.
4.3.1 Average ionic radius size factor at site-A.
Substitution at site-A in the PM system will alter the average radius size of the ions at site-A. To estimate its size, a formulation has been proposed as defined below.17where, 〈rA〉 is the average ion radius size, xi is the ion content in the system, and ri is the ion radius size in the system. Fig. 6(B)(a) displays the experimental results of the influence of 〈rA〉 on the TC of the PM materials. Wang et al. reported Ln1−xTxMnO3 (series I), Ln1−xTxMn0.9Cr0.1O3 (series II), and Ln1−xTxMn0.9Fe0.1O3 (series III) where Ln is La, (La, Nd), and (La, Y), while T is Ca, CaSr, and Sr.159 The results demonstrated that an increase in the average ionic radius size leads to an increase in the TC value. Abdelmoula et al., also investigated the differences in the size of 〈rA〉 in La0.7Sr0.3−xCaxMnO3 and La0.7−xPrxSr0.3MnO3 materials, yielding similar results to Wang et al.160 On the other hand, Ulyanov et al. conducted experiments to prove this in different compound compositions. These were divided into three groups: La0.7Ca0.3−xSrxMnO3 (X), La0.7Ca0.3−xBaxMnO3 (Y), and La0.7Sr0.3−xBaxMnO3 (Z). Fig. 6(B)(b) presents groups X and Y with increased TC with an increase in 〈rA〉, while the opposite phenomenon occurs in compound Z.161 Some researchers believe that there are other influencing factors, namely the mismatch effect, which will be discussed in the next section. Therefore, it was concluded that the influence of 〈rA〉 on TC can increase or decrease depending on the material.
4.3.2 Goldscmith tolerance factor (t).
Substitution in the PM system will alter the crystal structure, originally cubic, into orthorhombic or rhombohedral due to decreasing its symmetry level. This is associated with decreasing in the Mn–O–Mn bond angle and shifting in the MnO6 octahedral structure to another crystal structure. Previous researchers concluded a relationship between changes in crystal structure and goldsmith tolerance factor (t).1,48,113,115,162 This factor is defined by eqn (14). | 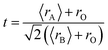 | (14) |
where, 〈rA〉 dan 〈rB〉 are the average ionic radii sizes of sites A and B, respectively, and rO is the radius of the oxygen ion. There are three ranges of t values, each corresponding to a crystal structure. For t = 1, a perfect cubic crystal structure was observed.1 In the range 0.96 < t < 1, it indicates the occurrence of a rhombohedral symmetrical crystal structure. Meanwhile, in the range t < 0.96 or 0.75 < t < 0.96 an orthorhombic crystal structure is formed.48 Sakka et al. demonstrated that Pr0.5Eu0.1Sr0.4MnO3 and Pr0.5Eu0.1Sr0.4MnO3 with t values of 0.9287 and 0.9266, respectively, have an orthorhombic crystal structure.48 Additionally, Razaq et al. reported that La0.8K0.1Ba0.05Sr0.15MnO3 has a t value of 0.965, displaying a rhombohedral structures.17
4.3.3 Mismatch effect (σ2).
The determination of the system's composition can estimate the amounts of Mn3+ and Mn4+ ions. Known Mn3+/Mn4+ ion ratio close to 2/1 or 7/3 will present excellent MCE properties because the strong DE interactions occur in the ferromagnetic state.16 On the other hand, the composition also influences the occurrence of Jahn–Teller distortion.18 Schiffer et al. studied the magnetic property behavior of La1−xCaxMnO3 with increasing x, presenting three magnetic phase regions: paramagnetic, ferromagnetic, and antiferromagnetic.154 Another example is the investigation by Szewczyk et al. into La1−xSrxMnO3, where the addition of x exhibited regions of ferromagnetic, paramagnetic, and antiferromagnetic phases.155–157 Ju et al. also investigated the magnetic phase behavior of La1−xBaxMnO3, which exhibits a ferromagnetic phase.158 The phase diagrams for these three examples are clearly illustrated in Fig. 6(A). In this case, the substitution with divalent ion and composition with x = 0.3 show ferromagnetic behavior. This demonstrates the correlation between strong DE interactions and the ferromagnetic behavior of the PM system. Therefore, considering the composition or amount of doping used is one of the considerations for predicting the material's properties.
Other parameters related to magnetic properties such as TC, −ΔSM, and magnetic phase transition are the mismatch effect (σ2).1 In perovskite manganite (PM) materials, a large value of σ2 is defined as the difference in the ion radius values for each ion at site-A compared to 〈rA〉, and it can be formulated as follows:8,162–164
where, 〈
rA〉 is the average ion radii size,
xi is the ion content in the system, and
ri is the ion radii size in the system. For example, Razaq
et al. calculated the
σ2 values for La
0.8K
xBa
0.05Sr
0.15−xMnO
3 (
x = 0.00–0.20) with results from 3.833 × 10
−3 to 18.101 × 10
−3.
17 Additionally, Bangrong He
et al. reported La
0.8−xGd
xSr
0.2MnO
3 (
x = 0.00–0.10) with
σ2 values from 1.024 × 10
−3 to 7.594 × 10
−3.
164 Both studies reported changes in their physical and magnetic properties which are connected to local lattice distortion with a random placement of oxygen. Moreover, mismatch effect plays a role in controlling the type of magnetic phase transition and
TC values.
1,17,18,164 Yuan
et al. revealed a correlation between the mismatch effect values and 〈
rA〉, producing a pattern similar to the
TC pattern in the cases of compounds X, Y, and Z.
165 This correlation is depicted in
Fig. 6(B) point (
d). Furthermore, it has been widely reported that an increase in the mismatch effect on the size of site-A leads to slightly less magnetic and MCE properties.
1
4.3.4 Jahn–Teller distortion.
The last parameter influencing crystal structure is Jahn–Teller distortion. This phenomenon is associated with structural changes in materials, where in the case of PM, a cubic structure becomes distorted into an orthorhombic or rhombohedral structure. For example, in PM materials, Mn ions, due to the difference in energy levels in the 3d orbitals, especially in the t2g and eg orbitals, lead to sample-specific compositions and average ion radius sizes.1,166
4.4 Materials production methods
The performance of materials is determined by several crucial factors, one of which is the production method. Previous studies on the production of PM materials have employed various methods. The choice of production method plays a crucial role in investigating MCE properties as it is highly sensitive to the material's characteristics. Some of the methods used by researchers consist of solid-state reaction (SSR),167–171 sol–gel (SG),16,17,164 polyol (P), solvothermal (ST),24 ball milling (BM) or high energy ball milling (HEBM),116,117,172 pore-wetting (PW),23 wet-mixing (WM),16 hydrothermal (HT) methods,1etc. It is known that each method has its own targeted advantages.
The most commonly used production methods are SSR, SG, and BM. The SSR method is widely employed because it is easy to make. The SSR method is advantageous for MCE materials since it enhances crystallinity and reduces crystal boundaries, which are magnetically dead areas.1 However, it should be noted that the mixing process can impact to get desired compounds, since it may lead to non-homogeneous particle sizes. To address this, the BM method was developed by utilizing milling machines to achieve homogenous particle sizes. In general, the process involves combining all precursors, breaking them down, and reuniting them to reduce the particle size, modify the shape and structure, and combine all precursors.52,117 However, both SSR and BM methods have drawbacks, such as higher sintering temperatures (>1273 K) and longer holding times (>24 hours) to obtain the compounds.52 Some materials produced using SSR and BM methods include La0.7SrxCa0.3−xMnO3,117 La0.65Ba0.30−x□xMnO3,168 and La0.63Ca0.29Sr0.04MnO3.167
The SG method is preparation to obtain ceramic materials from solids transformed into a gel. This method is often associated with the use of citric acid and ethylene glycol in the manufacturing process. Citric acid is used as a complexing agent and combustion aid, while ethylene glycol is used as a polymerization agent. Many researchers use the SG method due to its advantages such as the manufacturing process, short experimental cycles, production of more homogenous particle sizes, adjustable sintering temperatures, and shorter sintering treatment times compared to SSR and BM methods.16,164 However, materials produced using the SG method tend to have lower crystallinity than those produced using the SSR method.1 Some materials produced using the SG method include La0.7Ca0.1Sr0.1Ba0.1MnO3,16 La0.8−xKxBa0.05Sr0.15MnO3,17 and La0.7GdxSr0.3−xMnO3.164
4.5 Effect of heat treatment
The heat treatment process plays a crucial role in PM materials production. The most frequently used methods are dehydration, calcination, annealing, and sintering. The dehydration process involves heating to evaporate water content from the compound at low temperatures ranging from 373 to 473 K over a specific duration. Calcination is a heat treatment process with a specific temperature without melting the compound, using or not using a specific gas, aiming to remove impurities and cause thermal decomposition.16 Meanwhile, annealing is a heating process for compounds with purposing to alter the physical and chemical properties of samples, such as reducing stress to facilitate subsequent manufacturing processes. The last, sintering process involves heating the material at high temperatures but below its melting point for a specific duration, aiming to promote crystal growth (nucleation) accompanied by atomic diffusion.1
One of the methods to determine the sintering temperature is differential thermal analysis (DTA) and thermogravimetric analysis (TGA) measurements. DTA measurements are used to determine the temperature difference between the reference and the sample during heating. Commonly, DTA measurements display two types of peaks such as exothermic and endothermic below the melting point detected in TGA. On the other hand, TGA measurements show the weight change of the material with increasing applied temperature. The results of the measurements allowed for the detection of mass reduction caused by the loss of solvent, impurities, and sample material.1 For example the DTA–TGA curve results from Kumar et al., recommended a sintering temperature above 1023 K for the LaMnO3 sample.173
It is known that the sintering and compaction processes have several methods such as conventional sintering, hot pressing sintering, and spark plasma sintering.9,30,31,33,40,118,120,174,175 Most researchers use the conventional method to obtain PM materials. However, the development of sintering processes using SPS and HPS methods has become popular because of faster cycles. The SPS method is an advanced technology used to produce high-density bulk, where the sintering and compaction processes occur simultaneously. SPS has a thickness change sensor component that can monitor during the sintering process by adjusting the heating rate and holding time, offering the advantage of a shorter processing time.33,40,118,120 On the other hand, HPS is a sintering method combined with sample compression at a specific temperature, but its heating rate is not as fast as SPS. Moreover, it has been reported that the mechanical properties of SPS are superior to conventional sintering and HPS methods, demonstrated by lower porosity, higher density, and other mechanical properties.30,31 The popularity of the SPS method is also used for investigating MCE properties. Khlifi et al. reported an investigation on La0.6Ca0.2Ba0.2MnO3 by comparing synthesis and sintering methods in their research. The synthesis method used was SSR followed by conventional sintering, and the P method followed by SPS. They reported that the MCE properties of the P method followed by SPS had values of −ΔSM = 4.5 J kg−1 K−1 and RCP = 244 J kg−1, which were larger than the SSR method followed by conventional sintering.40
4.6 Effect of morphology and grain size
Most of the PM materials produced are polycrystalline materials because they are easier to synthesize than single-crystal materials, which are identified through X-ray diffraction (XRD) measurements. Both polycrystalline and single-crystal materials can be morphologically characterized through scanning electron microscope (SEM) and energy dispersive spectroscopy (EDS) measurements. SEM measurements were conducted to determine morphology, size, and grain arrangement. Meanwhile, EDS measurements serve as elemental analyses of the material.
Fig. 7 presents the SEM results of La0.7Ba0.1Ca0.1Sr0.1MnO3 with variations in synthesis methods, SG, and WM, where the morphological shape appears as spheres with specific grain sizes and clear grain boundaries in both samples.16 It can be observed that the grain size of the SG sample is larger than that of the WM sample. The presented differences in grain size affect the MCE properties and TC, where larger grain sizes can enhance the values of −ΔSM and TC.176 Andrade et al. also reported La0.6Ca0.4MnO3 with the smallest grain size of 23 nm and the largest grain size of 223 nm, showing an increase in −ΔSM values from 0.3 J kg−1 K−1 to 8.3 J kg−1 K−1 and RCP values from 40 J kg−1 to 508 J kg−1.23 Additionally, Yadav et al. studied the magnetic properties of La0.7Sr0.3MnO3, indicating that larger grain sizes can influence magnetization values and increased coercivity fields related to non-magnetic layers on the surface of each grain.73
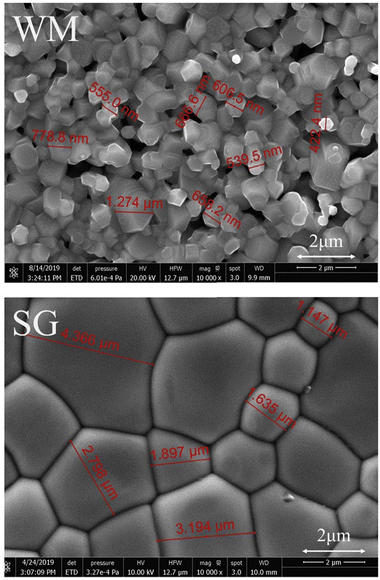 |
| Fig. 7 The morphology of SEM results sample La0.7Ba0.1Ca0.1Sr0.1MnO3 compound with production method SG dan WM reproduced from ref. 16 with permission from Elsevier, copyright 2020.16 | |
5. Analysis of magnetic properties and magnetocaloric data of perovskite manganite materials
After understanding the parameters that influence the magnetic properties and MCE of PM materials, a deeper understanding is needed for an analysis of the data. Based on several previous studies discussing MCE, the data usually presented in reports include temperature dependence curves on magnetic fields (M–T), temperature inverse susceptibility (χ−1 − T), magnetic field–isothermal magnetization (M–H), arrow plot (H/M − M2), universal curve
and MCE parameters. When presenting data, don't just show it as it is. Instead, calculations and analysis are required to understand their behavior. A more detailed discussion will be presented in the following section.
5.1 Analysis and measurement of temperature dependence on magnetization (M − T)
It is known that temperature dependence on magnetization measurements for magnetic and MCE properties investigations of materials. M–T measurements are conducted with different modes such as zero field cooled (ZFC), field cooled (FC), and field heated (FH). Generally, these measurements are conducted to determine the point of the ferromagnetic to paramagnetic phase transition and the TC value of the PM material, which is related to the appearance of the highest magnetic entropy change. Thus, it can be concluded that M–T measurements are crucial for investigations in determining the working temperature range of magnetic refrigeration materials.
Fig. 8(A) exhibits M–T curve analysis results from Munazat et al. report, showing that both samples undergo a phase transition from ferromagnetic to paramagnetic states with increasing temperature. This is marked by a significant decrease in magnetization around TC as many research results.20,60,115 To determine TC value more accurately, an analysis of the phase transition temperature is needed, where the determination is done by deriving M–T to temperature (dM/dT). The analysis for determining the TC value was also conducted by Munazat et al., stating that the TC values for La0.7Ba0.1Ca0.1Sr0.1MnO3 samples are 330.81 K and 316.17 K for SG and WM samples, respectively.16
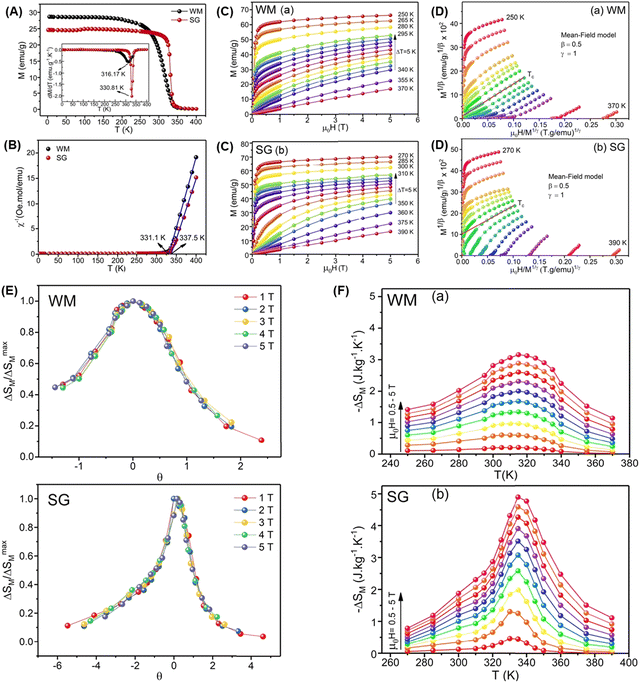 |
| Fig. 8 The results of the magnetic properties and MCE analysis of the La0.7Ba0.1Ca0.1Sr0.1MnO3 compound with different production methods, (a) WM (wet-mixing), and (b) SG (sol–gel), are presented. The figures include (A) temperature dependence on a magnetic field of 0.05 T, (B) inverse susceptibility versus temperature, (C) isothermal magnetization, (D) Arrot plot, (E) universal curve analysis, and (F) curve of magnetic entropy change versus temperature where all of the pictures reproduced from ref. 16 with permission from Elsevier, copyright 2020.16 | |
5.2 Analysis and measurement of temperature dependence on inverse susceptibility (χ−1 − T)
Futhermore, analysis of the χ−1 − T curve data was carried out to determine TC value as another alternative approach to the M–T curve and effective magnetic moment value associated with the Curie–Weiss Law. The Curie–Weiss Law equation for ferromagnetic materials can be described by the following expression:16 |  | (16) |
| 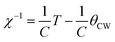 | (17) |
where χ is the material susceptibility, θCW is the Curie–Weiss temperature, and C is the Curie constant. In determining the Curie–Weiss temperature, a transformation of the function into the χ−1 − T curve is needed, and the Curie constant is defined as follow:16 | 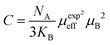 | (18) |
where, NA is Avogadro's number, KB is the Boltzmann constant, μexpeff is the experimental effective magnetic moment, and μB is the Bohr magneton.
Fig. 8(B) presents the analysis of inverse susceptibility versus temperature for La0.7Ba0.1Ca0.1Sr0.1MnO3. In their report, Munazat et al. state that the presented data suits Curie–Weiss Law due to the linear behavior of the graph in the paramagnetic region.16 The estimated lines of paramagnetic behavior intersect x-axis at the Curie paramagnetic temperature (TC or θCW) values of 331.1 K and 337.5 K for the WM and SG samples, respectively. If the sample does not have good magnetic homogeneity, the TC values from the χ−1 − T analysis may differ from the M–T analysis. Additionally, the dominance of ferromagnetic conditions in the paramagnetic region may lead to the presence of Griffith phases and anomalies.113,128,177,178 These anomalies are characterized by the absence of a straight-line behavior in the paramagnetic region.128,177–179
In addition, the Curie constants obtained from the analysis of the slopes of the straight lines above provide μexpeff values for the Munazat et al. samples of 5.36μB and 5.80μB for the WM and SG samples, respectively.16 These results do not align with an effective magnetic moment value calculated as μcaleff (4.61μB). According to them, the discrepancy is attributed to the presence of non-homogeneous magnetic states, particularly in the temperature transition region of the samples. Additionally, this difference is also linked to the presence of short-range ferromagnetic interactions above TC.16
5.3 Analysis and measurement of isothermal magnetization (M–H)
These measurements are conducted to obtain the isothermal M–H curve, which is used as data for indirectly calculating the −ΔSM value from the PM sample. Additionally, this data serves as a tool for analysing the type of phase transition in PM samples by utilizing the Arrot plot. It is noteworthy that previous research suggests the need for special treatment in the isothermal M–H measurements of FOMT-type materials to reduce errors in −ΔSM. Therefore, FOMT-type materials are recommended to be measured using direct methods.35 Meanwhile, for SOMT-type samples, no special treatment is required.1Fig. 8(C) provides a general illustration of isothermal M–H measurements conducted around TC with constant temperature changes.16 Isothermal M–H curves in MCE materials typically exhibit a sharp increase in magnetization with a slight change in magnetic field (ferromagnetic phase behavior below TC) and almost become a straight line approaching saturation when reaching high magnetic fields (paramagnetic phase behavior above TC).1,180–182
5.4 Analysis of phase transition types utilizing Arrot plot
To determine magnetic phase transition types, many researchers utilize the Arrot plot (H/M − M2). As mentioned earlier, the data used for the Arrot plot comes from isothermal M–H data. According to the Banerjee criteria, the type of transition can be illustrated by the slope of the graph. FOMT transitions have a negative slope, while SOMT transitions have a positive slope.1,183–186 This determination is crucial because MCE materials depend on the type of magnetic transition, as explained earlier. Certainly, Banerjee's criteria and the formulation of the Arrot plot can be defined quantitatively from Landau theory. This theory is considered to originate from the Gibbs free energy (G(M, T)) as a function of the magnetic field, which can be expressed as a power series expansion:187 |  | (19) |
In thermal equilibrium conditions
the magnetic state equation is obtained as:
| 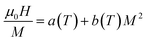 | (20) |
eqn (20), known as the Arrot plot formula, presents two Landau coefficients namely
a(
T), and
b(
T). Generally, the minimum value of
a(
T) represents the
TC value according to the Landau expansion characteristics. On the other hand,
b(
T) in the Landau expansion indicates the type of phase transition that occurs at a specific temperature. At
b(
TC), it will confirm the type of magnetic phase transition that occurs; if
b(
TC) < 0, it indicates FOMT, and if
b(
TC) ≥ 0, it indicates SOMT.
48 For example, experimental results can be seen in
Fig. 8(D), which presents the Arrot plot of La
0.7Ba
0.1Ca
0.1Sr
0.1MnO
3 synthesized using the WM and SG methods.
16 Munazat
et al. revealed that their sample exhibited SOMT transition type, characterized by its positive slope as indicated at
TC.
16
5.5 Analysis of phase transition types utilizing universal curve
Not only is the analysis carried out using the Arrot plot, but also Franco et al. proposed an analysis of magnetic phase transitions using the universal curve.188,189 They revealed that a material exhibiting FOMT transitions would not have its universal curve merging, while for SOMT transitions, the universal curve would merge into a single line, regardless of the applied magnetic field magnitude. In the analysis of the universal curve, normalization of the axis
is performed, and rescaling is applied to the θ axis, defined as follows:16,190 | 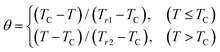 | (21) |
Where, Tr1 and Tr2 are the temperature values of two reference points chosen based on
. Munazat et al. demonstrated the analysis of SOMT transition type with the merging of −ΔSM values into a single line in their sample, as shown in Fig. 8(E).16 Additionally, Bonilla et al. conducted an investigation of the universal curve for RECo2 (RE = Tb, Pr, Nd, Ho, Dy), showing universal curve results for both FOMT and SOMT transition types, as proposed by Franco et al.191
5.6 Parameter of MCE properties measurements corellated by Landau theory
As discussed in the subsection on fundamental aspects of MCE property parameters, −ΔSM and RCP are crucial. However, when processing experimental −ΔSM data, most researchers use the discrete version of eqn (7).64 Additionally, it can also be calculated using the equation derived from Landau theory, which is obtained from the relationship between entropy and the Landau theory derivative to temperature, as follows: |  | (22) |
Fig. 8(F) presents the results of the calculation of magnetic entropy change from the study by Munazat et al.16 Thus, all the MCE materials discussed here will be summarized in Table 2, which contains important parameters for the MCE properties of the material.
6. Conclusion
The research progress on magnetocaloric effect (MCE) for application of magnetic refrigeration technology operating at room temperature has been intensifying. This development aims to envision a better future in terms of energy efficiency and environmental conservation, particularly by avoiding greenhouse gas effects and ozone layer depletion. Numerous types of MCE materials have been developed as alternatives to expensive and limited Gd-based materials ($4000 per kg). Among the various proposed alternative materials, one stands out as an ideal MCE material – perovskite manganite. The emergence of MCE properties in perovskite manganite materials is linked to crucial parameters such as production methods, heat treatment, crystal structure, atom substitution (doping), compound composition, morphology and grain size, temperature dependence, and magnetic field dependence on magnetization. These parameters significantly influence MCE properties, represented by values like −ΔSM, ΔTad, and RCP. Considering all these crucial parameters and the increasing intensity of research on perovskite manganite-based MCE materials, they hold the potential to be permanently applied in magnetic refrigeration, replacing conventional refrigerator technologies.
Conflicts of interest
There are no conflicts to declare.
Acknowledgements
The authors gratefully acknowledge the PMDSU Scholarship for Phahul Zhemas Zul Nehan and the financial support under grant “Penelitian Dasar Unggulan Perguruan Tinggi 2021” NKB-160/UN2.RST/HKP.05.00/2021.
References
- A. O. Ayaş, S. K. Çetin, G. Akça, M. Akyol and A. Ekicibil, Magnetic refrigeration, Mater. Today Commun., 2023, 35, 105988 CrossRef.
-
D. Coulomb, J. L. Dupont and A. Pichard, The Role of Refrigeration in the Global Economy, 2015 Search PubMed.
-
I. energy Agency, The Future of Cooling: Opportunities for energy efficient air conditioning, OECD, 2018 Search PubMed.
- M. H. Phan and S. C. Yu, J. Magn. Magn. Mater., 2007, 308, 325–340 CrossRef CAS.
- N. R. Ram, M. Prakash, U. Naresh, N. S. Kumar, T. S. Sarmash, T. Subbarao, R. J. Kumar, G. R. Kumar and K. C. B. Naidu, J. Supercond. Nov. Magn., 2018, 31, 1971–1979 CrossRef CAS.
- Y. Dong, M. Coleman and S. A. Miller, Ann. Rev. Environ. Resources, 2021, 46, 59–83 CrossRef.
- A. Kitanovski, Adv. Energy Mater., 2020, 10, 1903741 CrossRef CAS.
- W. Zhang, Z. Xie, Z. Zou, X. Jiang, C. Xu and M. Feng, Ceram. Int., 2024, 50, 4921–4935 CrossRef CAS.
- M. Z. Kurt, S. Kılıç Çetin, A. Kandemir, G. Akça, F. Karadağ and A. Ekicibil, J. Mater. Sci.: Mater. Electron., 2024, 35, 565 CrossRef CAS.
- O. Sari and M. Balli, Int. J. Refrig., 2014, 37, 8–15 CrossRef.
- K. Rajamani, M. S. Toprak, F. Zhang, A. I. Dugulan, E. Brück, T. van der Meer and M. Shahi, ACS Omega, 2023, 8, 49027–49036 CrossRef CAS PubMed.
- H. Gu, X. Zhang, H. Wei, Y. Huang, S. Wei and Z. Guo, Chem. Soc. Rev., 2013, 42, 5907–5943 RSC.
- S. Solanki, D. Dhruv, H. Boricha, A. Zankat, K. N. Rathod, B. Rajyaguru, R. K. Trivedi, A. D. Joshi, S. Mukherjee, P. S. Solanki and N. A. Shah, J. Solid State Chem., 2020, 288, 121446 CrossRef CAS.
- L. Yin, C. Wang and Q. Shen, Ceram. Int., 2023, 49, 33392–33400 CrossRef CAS.
- W. Hizi, H. Rahmouni, K. Khirouni and E. Dhahri, Phys. B, 2024, 673, 415423 CrossRef CAS.
- D. R. Munazat, B. Kurniawan, D. S. Razaq, K. Watanabe and H. Tanaka, Phys. B, 2020, 592, 412227 CrossRef CAS.
- D. S. Razaq, B. Kurniawan, D. R. Munazat, K. Watanabe and H. Tanaka, Crystals, 2020, 10(5), 407 CrossRef CAS.
- Z. Xie, Z. Zou, B. He, L. Liu and Z. Mao, Front. Mater., 2021, 8, 771941 CrossRef.
- L. Li and M. Yan, J. Mater. Sci. Technol., 2023, 136, 1–12 CrossRef CAS.
- E. Bouzaiene, A. H. Dhahri, J. Dhahri and E. K. Hlil, Inorg. Chem. Commun., 2021, 132, 108824 CrossRef CAS.
- T. Gottschall, M. D. Kuz’Min, K. P. Skokov, Y. Skourski, M. Fries, O. Gutfleisch, M. G. Zavareh, D. L. Schlagel, Y. Mudryk, V. Pecharsky and J. Wosnitza, Phys. Rev. B, 2019, 99, 134429 CrossRef CAS.
- A. M. Tishin, Y. I. Spichkin, V. I. Zverev and P. W. Egolf, Int. J. Refrig., 2016, 68, 177–186 CrossRef CAS.
- V. M. Andrade, R. J. C. Vivas, S. S. Pedro, J. C. G. Tedesco, A. L. Rossi, A. A. Coelho, D. L. Rocco and M. S. Reis, Acta Mater., 2016, 102, 49–55 CrossRef CAS.
- W. Chen, B. Hong, Y. Zeng, X. Wang, X. Peng, J. Li and J. Xu, J. Alloys Compd., 2023, 933(13), 22281–22293 Search PubMed.
- A. T. Coşkun, Y. S. Ak, N. Güleç, G. Akça, S. K. Çetin, A. Ekicibil and A. Coşkun, J. Mater. Sci.: Mater. Electron., 2023, 34, 1257 CrossRef.
- K. Laajimi, M. Khlifi, E. K. Hlil, K. Taibi, M. H. Gazzah and J. Dhahri, J. Mater. Sci.: Mater. Electron., 2019, 30, 11868–11877 CrossRef CAS.
- K. Laajimi, F. Ayadi, M. Kchaw, I. Fourati, M. Khlifi, M. H. Gazzah, J. Dhahri and J. Juraszek, Solid State Sci., 2019, 30, 11868–11877 CAS.
- M. Varga, L. Galdun, P. Diko, K. Saksl and R. Varga, J. Alloys Compd., 2023, 944, 169196 CrossRef CAS.
- T. Zheng, K. Liu, H. Chen and C. Wang, J. Magn. Magn. Mater., 2022, 563, 170034 CrossRef CAS.
- Y. C. Wu, Y. X. Li, X. C. Zhong, C. L. Liu, J. H. Huang, H. Y. Yu, Z. W. Liu, M. L. Zhong, Z. C. Zhong and R. V. Ramanujan, Mater. Res. Bull., 2022, 156, 111974 CrossRef.
- X. C. Zhong, Y. C. Wu, S. M. Wu, Y. X. Li, J. H. Huang, C. L. Liu, H. Zhang, Z. W. Liu, M. L. Zhong, Z. C. Zhong and R. V. Ramanujan, J. Alloys Compd., 2022, 902, 163780 CrossRef CAS.
- H. Wang, G. F. Wang, Y. Bo and Y. Y. Ma, J. Magn. Magn. Mater., 2024, 591, 171727 CrossRef CAS.
- Z. R. Zhao, T. Jing, G. F. Wang, Y. F. Li, Q. Ma and X. F. Zhang, J. Supercond. Nov. Magn., 2019, 32, 993–999 CrossRef CAS.
- A. M. Chirkova, K. P. Skokov, Y. Skourski, F. Scheibel, A. Y. Karpenkov, A. S. Volegov, N. V. Baranov, K. Nielsch, L. Schultz, K. H. Müller, T. G. Woodcock and O. Gutfleisch, Phys. Rev. Mater., 2021, 5, 064412 CrossRef CAS.
- A. T. Sathyanarayana and A. Mani, J. Alloys Compd., 2021, 862, 158322 CrossRef CAS.
- J. Hu, C. Liu, M. Wang, M. Wang, S. Wang, G. Zheng and Y. Ma, J. Solid State Chem., 2022, 314, 123369 CrossRef CAS.
- J. Zhao, X. Liu, X. Kan, C. Liu, W. Wang, J. Hu, Q. Lv, J. Huang and M. Shazeda, Ceram. Int., 2021, 47, 7906–7917 CrossRef CAS.
- R. Felhi, H. Omrani, M. Koubaa, W. C. Koubaa and A. Cheikhrouhou, J. Alloys Compd., 2018, 758, 237–246 CrossRef CAS.
- N. Assoudi, I. Walha, E. Dhahri, S. Alleg and E. K. Hlil, Solid State Commun., 2018, 277, 13–18 CrossRef CAS.
- H. Ben Khlifa, F. Ayadi, R. M’nassri, W. Cheikhrouhou-Koubaa, G. Schmerber and A. Cheikhrouhou, J. Alloys Compd., 2017, 712, 451–459 CrossRef CAS.
- H. Ma, X. Jin, L. Gao, J. Zhao and J. Zhao, J. Low Temp. Phys., 2024, 215, 93–108 CrossRef CAS.
- A. Ezaami, N. Ouled Nasser, W. Cheikhrouhou-Koubaa and A. Cheikhrouhou, Mater. Res. Bull., 2017, 95, 211–215 CrossRef CAS.
- A. Ezaami, E. Sellami-Jmal, W. Cheikhrouhou-Koubaa and A. Cheikhrouhou, J. Mater. Sci.: Mater. Electron., 2017, 28, 16741–16746 CrossRef CAS.
- S. Tillaoui, B. Rabi, M. Sajieddine, A. Essoumhi, M. Emo, A. El Boubekri, M. Lassri, E. K. Hlil, M. Sahlaoui and A. Razouk, Ceram. Int., 2024, 50, 16375–16381 CrossRef CAS.
-
A. M. Tishin and Y. I. Spichkin, The Magnetocaloric Effect and its Applications, Institute of Physics Publishing, Bristol and Philadelphia, 2003 Search PubMed.
- J. Y. Law and V. Franco, Encycl. Mater.: Composites, 2021, 2, 461–472 Search PubMed.
- T. M. Al-Shahumi, I. A. Al-Omari, S. H. Al-Harthi and M. T. Z. Myint, SN Appl. Sci., 2023, 5, 121 CrossRef CAS.
- A. Sakka, R. M’nassri, M. M. Nofal, S. Mahjoub, W. Cheikhrouhou-Koubaa, N. Chniba-Boudjada, M. Oumezzine and A. Cheikhrouhou, J. Magn. Magn. Mater., 2020, 514, 167158 CrossRef CAS.
- J. Wang, H. Xie, Q. Liu, Z. Hao, Z. Mo, Q. Fu, X. Gao and J. Shen, J. Rare Earths, 2023 DOI:10.1016/j.jre.2023.06.015.
- X. Wang, L. Wang, N. L. Gulay, L. Li and R. Pöttgen, J. Magn. Magn. Mater., 2024, 589, 171406 CrossRef CAS.
- D. H. Manh, T. D. Thanh, D. H. Kim and T. L. Phan, Curr. Appl. Phys., 2024, 60, 70–78 CrossRef.
- V. E. Salazar-Muñoz, A. Lobo Guerrero and S. A. Palomares-Sánchez, J. Magn. Magn. Mater., 2022, 562, 169787 CrossRef.
- F. Zhang, K. Westra, Q. Shen, I. Batashev, A. Kiecana, N. van Dijk and E. Brück, J. Alloys Compd., 2022, 968, 164337 CrossRef.
- A. Biswas, N. A. Zarkevich, A. K. Pathak, O. Dolotko, I. Z. Hlova, A. V. Smirnov, Y. Mudryk, D. D. Johnson and V. K. Pecharsky, Phys. Rev. B, 2020, 101, 224402 CrossRef CAS.
- W. Lu, N. T. Nam and T. Suzuki, J. Appl. Phys., 2009, 105, 07A904 CrossRef.
- S. N. Kaul and M. Rosenberg, Philosophical Magazine B: Physics of Condensed Matter; Statistical Mechanics, Electronic, Optical and Magnetic Properties, 1981, 44, 357–368 CrossRef CAS.
- E. Rauwel Buzin, W. Prellier, C. Simon, S. Mercone, B. Mercey, B. Raveau, J. Sebek and J. Hejtmanek, Appl. Phys. Lett., 2001, 79, 647–649 CrossRef CAS.
- H. Zhang, X. Zhang, J. Tan, J. Yan, H. Shi, J. Zhang, H. Wei, H. Li, W. Li and A. Xia, J. Alloys Compd., 2023, 953, 170114 CrossRef CAS.
- V. K. Pecharsky and K. A. Gschneidner, Phys. Rev. Lett., 1997, 78, 4494–4497 CrossRef CAS.
- M. A. A. Bally, M. A. Islam, M. Z. Ahasan and F. A. Khan, J. Magn. Magn. Mater., 2022, 557, 169462 CrossRef CAS.
- A. Guedri, S. Mnefgui, S. Hcini, E. K. Hlil and A. Dhahri, J. Solid State Chem., 2021, 297, 122046 CrossRef CAS.
- E. Oumezzine, S. Hcini, M. Baazaoui, E. K. Hlil and M. Oumezzine, Powder Technol., 2015, 278, 189–195 CrossRef CAS.
- W. Chen, J. Xu, Y. Zeng, X. Wang, X. Peng, J. Li and B. Hong, Ceram. Int., 2023, 49, 22281–22293 CrossRef CAS.
- A. Coşkun, A. E. Irmak, B. Altan, Y. S. Ak and A. T. Coşkun, J. Magn. Magn. Mater., 2023, 584, 171104 CrossRef.
- J. H. Belo, A. L. Pires, J. P. Araújo and A. M. Pereira, J. Mater. Res., 2019, 34, 134–157 CrossRef CAS.
- J. B. Puga, B. D. Bordalo, D. J. Silva, M. M. Dias, J. H. Belo, J. P. Araújo, J. C. R. E. Oliveira, A. M. Pereira and J. Ventura, Nano Energy, 2017, 31, 278–285 CrossRef CAS.
- T. Yang, B. Kwon, P. B. Weisensee, J. G. Kang, X. Li, P. Braun, N. Miljkovic and W. P. King, Appl. Phys. Lett., 2018, 112, 063505 CrossRef.
- M. Hodes, R. Zhang, L. S. Lam, R. Wilcoxon and N. Lower, IEEE Trans. Compon. Packag. Manuf. Technol., 2014, 4, 46–56 Search PubMed.
- J. Bornacelli, C. Torres-Torres, J. Arenas-Alatorre, M. M. Martínez-Mondragón, L. Rodríguez-Fernández and A. Oliver, Nanotechnology, 2020, 31(35), 355705 CrossRef CAS PubMed.
- D. R. Munazat, B. Kurniawan and D. S. Razaq, IOP Conf. Ser.: Mater. Sci. Eng., 2019, 546, 042026 CAS.
- A. D. Souza, P. D. Babu, S. Rayaprol, M. S. Murari, L. D. Mendonca and M. Daivajna, J. Alloys Compd., 2019, 797, 874–882 CrossRef.
- H. Baaziz, A. Tozri, E. Dhahri and E. K. Hlil, J. Magn. Magn. Mater., 2018, 449, 207–213 CrossRef CAS.
- P. A. Yadav, A. V. Deshmukh, K. P. Adhi, B. B. Kale, N. Basavaih and S. I. Patil, J. Magn. Magn. Mater., 2013, 328, 86–90 CrossRef CAS.
- A. D. Souza, S. Rayaprol, M. S. Murari and M. D. Daivajna, J. Supercond. Nov. Magn., 2021, 34, 3319–3331 CrossRef CAS.
- A. O. Ayaş, E. Seçilmiş and A. Ekicibil, J. Mol. Struct., 2021, 1231, 130010 CrossRef.
- S. Koner, S. Satapathy, P. Deshmukh, R. K. Sharma, P. K. Sahoo and S. K. Majumder, J. Alloys Compd., 2023, 986, 172249 CrossRef.
- R. Atanasov, E. Brinza, R. Bortnic, R. Hirian, G. Souca, L. Barbu-Tudoran and I. G. Deac, Magnetic Magnetochem., 2023, 9(7), 170 CrossRef CAS.
- R. Hamdi, D. Ramotar, S. S. Hayek, A. Samara, S. A. Mansour and Y. Haik, Inorg. Chem. Commun., 2023, 150, 110551 CrossRef CAS.
- R. Hamdi, S. S. Hayek, A. Samara, Y. Tong, S. A. Mansour and Y. Haik, Solid State Sci., 2023, 142, 107223 CrossRef CAS.
- A. B. Tewari, R. Sharma and D. Sharma, Results Eng., 2023, 20, 101537 CrossRef CAS.
- H. Zeng, J. Zhang, C. Kuang and M. Yue, Appl. Nanosci., 2011, 1, 51–57 CrossRef CAS.
- P. V. Trevizoli, C. S. Alves, M. A. B. Mendes, A. M. G. Carvalho and S. Gama, J. Magn. Magn. Mater., 2008, 320, 1582–1585 CrossRef CAS.
- J. Lyubina, R. Schäfer, N. Martin, L. Schultz and O. Gutfleisch, Adv. Mater., 2010, 22, 3735–3739 CrossRef CAS PubMed.
- P. Lampen, N. S. Bingham, M. H. Phan, H. Kim, M. Osofsky, A. Piqué, T. L. Phan, S. C. Yu and H. Srikanth, Appl. Phys. Lett., 2013, 102, 062414 CrossRef.
- V. Chaudhary, X. Chen and R. V. Ramanujan, Prog. Mater. Sci., 2019, 100, 64–98 CrossRef CAS.
- S. Tavares, K. Yang and M. A. Meyers, Prog. Mater. Sci., 2023, 132, 101017 CrossRef CAS.
- K. Kutynia and P. Gębara, Materials, 2012, 14, 3129 CrossRef PubMed.
- S. Mandal and T. K. Nath, Intermetallics, 2023, 162, 108019 CrossRef CAS.
- L. Trombi, F. Cugini, R. Rosa, N. S. Amadè, S. Chicco, M. Solzi and P. Veronesi, Rapid microwave synthesis of magnetocaloric Ni–Mn–Sn Heusler compounds, Scr. Mater., 2020, 176, 63–66 CrossRef CAS.
- T. Bachaga, J. Zhang, M. Khitouni and J. J. Sunol, Int. J. Adv. Manuf. Technol., 2019, 103, 2761–2772 CrossRef.
- S. Ghosh and S. Ghosh, Phys. Rev. B, 2021, 103, 054101 CrossRef CAS.
- J. Liu, T. Gottschall, K. P. Skokov, J. D. Moore and O. Gutfleisch, Nat. Mater., 2012, 11, 620–626 CrossRef CAS PubMed.
- M. Chmielus, X. X. Zhang, C. Witherspoon, D. C. Dunand and P. Müllner, Nat. Mater., 2009, 8, 863–866 CrossRef CAS PubMed.
- Y. S. Koshkid’ko, E. T. Dilmieva, A. P. Kamantsev, J. Cwik, K. Rogacki, A. V. Mashirov, V. V. Khovaylo, C. S. Mejia, M. A. Zagrebin, V. V. Sokolovskiy, V. D. Buchelnikov, P. Ari-Gur, P. Bhale, V. G. Shavrov and V. V. Koledov, J. Alloys Compd., 2022, 904, 164051 CrossRef.
- S. Datta, S. S. Dheke, S. K. Panda, S. N. Rout, T. Das and M. Kar, J. Alloys Compd., 2023, 968, 172251 CrossRef CAS.
- V. K. Pecharsky and K. A. Gschneidner, Adv. Mater., 2001, 13, 683–686 CrossRef CAS.
- E. Brück, J. Phys. D: Appl. Phys., 2005, 38, R381–R391 CrossRef.
- E. Yüzüak, I. Dincer and Y. Elerman, J. Rare Earths, 2012, 30, 217–221 CrossRef.
- A. Magnus, G. Carvalho, C. S. Alves, A. De Campos, A. A. Coelho, S. Gama, F. C. G. Gandra, P. J. Von Ranke and N. A. Oliveira, J. Appl. Phys., 2005, 97, 10M320 CrossRef.
- E. V. Aghababyan and N. P. Harutyunyan, J. Contemp. Phys., 2012, 47, 142–144 CrossRef CAS.
- V. Paul-Boncour and L. Bessais, Magnetochemistry, 2021, 7, 1–18 CrossRef.
- F. X. Hu, B. G. Shen, J. R. Sun, Z. H. Cheng, G. H. Rao and X. X. Zhang, Appl. Phys. Lett., 2001, 78, 3675–3677 CrossRef CAS.
- L. Pytlik and A. Zieba, J. Magn. Magn. Mater., 1985, 51, 199–210 CrossRef CAS.
- L. Däweritz, Rep. Prog. Phys., 2006, 69, 2581–2629 CrossRef.
- S. Gama, A. A. Coelho, A. De Campos, A. Magnus, G. Carvalho, F. C. G. Gandra, P. J. Von Ranke and N. A. De Oliveira, Phys. Rev. Lett., 2004, 93, 237202 CrossRef PubMed.
- N. Menyuk, J. A. Kafalas, K. Dwight and J. B. Goodenough, Phys. Rev., 1969, 177(2), 942–951 CrossRef CAS.
- V. Z. C. Paes, I. L. Graff, J. Varalda, V. H. Etgens and D. H. Mosca, J. Phys.: Condens. Matter, 2013, 25, 046003 CrossRef CAS PubMed.
- A. Jain, S. P. Ong, G. Hautier, W. Chen, W. D. Richards, S. Dacek, S. Cholia, D. Gunter, D. Skinner, G. Ceder and K. A. Persson, APL Mater., 2013, 1, 011002 CrossRef.
- F. Cristina Nascimento, A. Oliveira dos Santos, A. de Campos, S. Gama and L. Pavie Cardoso, Mater. Res., 2006, 9(1), 111–114 CrossRef.
- H. Wada and Y. Tanabe, Appl. Phys. Lett., 2001, 79, 3302–3304 CrossRef CAS.
- U. E. Habiba, K. S. Khattak, S. Ali and Z. H. Khan, Mater. Res. Express, 2020, 7, 046106 CrossRef CAS.
- N. A. Zarkevich and V. I. Zverev, Crystals, 2020, 10, 1–28 CrossRef.
- G. Singh, A. Gaur, P. Bisht and R. N. Mahato, J. Magn. Magn. Mater., 2024, 591, 171731 CrossRef CAS.
- M. Khlifi, M. Bejar, O. El Sadek, E. Dhahri, M. A. Ahmed and E. K. Hlil, J. Alloys Compd., 2011, 509, 7410–7415 CrossRef CAS.
- L. Liu, Z. Zou, B. He, Z. Mao and Z. Xie, J. Magn. Magn. Mater., 2022, 549, 169006 CrossRef CAS.
- C. A. Taboada-Moreno, A. M. Bolarín-Miró, F. Pedro-García, C. A. Cortés-Escobedo and F. Sánchez-De Jesús, J. Magn. Magn. Mater., 2023, 570, 170542 CrossRef CAS.
- C. A. Taboada-Moreno, F. Sánchez-De Jesús, F. Pedro-García, C. A. Cortés-Escobedo, J. A. Betancourt-Cantera, M. Ramírez-Cardona and A. M. Bolarín-Miró, J. Magn. Magn. Mater., 2020, 496, 165887 CrossRef CAS.
- F. Ayadi, Y. Regaieg, W. Cheikhrouhou-Koubaa, M. Koubaa, A. Cheikhrouhou, H. Lecoq, S. Nowak, S. Ammar and L. Sicard, J. Magn. Magn. Mater., 2015, 381, 215–219 CrossRef CAS.
- F. Ayadi, S. Ammar, S. Nowak, W. Cheikhrouhou-Koubaa, Y. Regaieg, M. Koubaa, J. Monnier and L. Sicard, J. Alloys Compd., 2018, 759, 52–59 CrossRef CAS.
- F. Ayadi, S. Ammar, W. Cheikhrouhou-Koubaa, A. Cheikhrouhou, T. Gaudisson, S. Reguer, S. Nowak, J. Monnier and L. Sicard, J. Alloys Compd., 2017, 691, 474–481 CrossRef CAS.
- M. Khlifi, E. Dhahri and E. K. Hlil, J. Alloys Compd., 2014, 587, 771–777 CrossRef CAS.
- I. Sfifir, A. Ezaami, W. Cheikhrouhou-Koubaa and A. Cheikhrouhou, J. Alloys Compd., 2017, 696, 760–767 CrossRef CAS.
- A. Ezaami, I. Sfifir, W. Cheikhrouhou-Koubaa, M. Koubaa and A. Cheikhrouhou, J. Alloys Compd., 2017, 693, 658–666 CrossRef CAS.
- K. Riahi, A. Ezaami, I. Messaoui, M. Solzi, W. Cheikhrouhou-Koubaa, F. Cugini, G. Allodi, F. Rossi and A. Cheikhrouhou, J. Magn. Magn. Mater., 2017, 441, 776–786 CrossRef CAS.
- S. Banik, K. Das and I. Das, J. Magn. Magn. Mater., 2019, 490, 165443 CrossRef CAS.
- S. Vadnala and S. Asthana, J. Magn. Magn. Mater., 2018, 446, 68–79 CrossRef CAS.
- K. P. Shinde, E. J. Lee, M. Manawan, A. Lee, S. Y. Park, Y. Jo, K. Ku, J. M. Kim and J. S. Park, Sci. Rep., 2021, 11, 20206 CrossRef CAS PubMed.
- K. P. Shinde, C. Hwang, M. Manawan, Y. S. Choi, S. Y. Park, Y. Jo, S. Lee, D. H. Kim and J. S. Park, RSC Adv., 2023, 13, 9099–9108 RSC.
- Y. Zhang, Y. Tian, Z. Zhang, Y. Jia, B. Zhang, M. Jiang, J. Wang and Z. Ren, Acta Mater., 2022, 226, 117669 CrossRef CAS.
- S. B. Madake, A. R. Patil, R. S. Pedanekar, N. A. Narewadikar, J. B. Thorat and K. Y. Rajpure, J. Mater. Sci.: Mater. Electron., 2022, 33, 6273–6282 CrossRef CAS.
- C. Zener, Phys. Rev., 1951, 82, 403–405 CrossRef CAS.
- R. Dhahri and F. Halouni, J. Alloys Compd., 2004, 381, 21–25 CrossRef CAS.
- E. Sellami-Jmal, A. Ezaami, W. Cheikhrouhou-Koubaa, M. Koubaa and A. Cheikhrouhou, J. Supercond. Nov. Magn., 2017, 30, 489–496 CrossRef CAS.
- W. C. Koubaa, M. Koubaa and A. Cheikhrouhou, J. Alloys Compd., 2011, 509, 4363–4366 CrossRef.
- B. Arun, V. R. Akshay and M. Vasundhara, RSC Adv., 2019, 9, 23598–23606 RSC.
- I. S. Debbebi, H. Omrani, W. Cheikhrouhou-Koubaa and A. Cheikhrouhou, J. Phys. Chem. Solids, 2018, 113, 67–73 CrossRef CAS.
- T. M. Al-Shahumi, I. A. Al-Omari, S. H. Al-Harthi, M. T. Z. Myint, P. Kharel, S. Lamichhane and S. H. Liou, J. Alloys Compd., 2023, 958, 170454 CrossRef CAS.
- N. T. Dang, D. P. Kozlenko, G. Kim, W. Shon, J. S. Rhyee, D. N. Petrov, T. V. Manh and P. T. Long, Curr. Appl. Phys., 2020, 20, 794–801 CrossRef.
- A. M. Bolarín-Miró, C. A. Taboada-Moreno, C. A. Cortés-Escobedo, O. Rosales-González, G. Torres-Villaseñor and F. Sánchez-De Jesús, Appl. Phys. A: Mater. Sci. Process., 2020, 126, 369 CrossRef.
- N. Zaidi, M. Elabassi, M. Selmi and E. K. Hlil, J. Supercond. Nov. Magn., 2019, 33, 2257–2267 CrossRef.
- M. Elabassi, N. Zaidi and M. O. Khair, J. Supercond. Nov. Magn., 2019, 32, 3019–3027 CrossRef CAS.
- A. Biswas, S. Chandra, M. H. Phan and H. Srikanth, J. Alloys Compd., 2012, 545, 157–161 CrossRef CAS.
- A. Mabrouki, H. Chadha, O. Messaoudi, A. Benali, T. Mnasri, E. Dhahri, M. A. Valente, S. Elgharbi, A. Dhahri and L. Manai, Inorg. Chem. Commun., 2022, 139, 109310 CrossRef CAS.
- Z. Xie, X. Jiang, W. Zhang and Z. Zou, J. Mater. Sci.: Mater. Electron., 2023, 34, 1514 CrossRef CAS.
- S. Naas, N. Abassi and C. Boudaya, J. Mater. Sci.: Mater. Electron., 2017, 28, 17985–17992 CrossRef CAS.
- B. Arun, V. R. Akshay and M. Vasundhara, Dalton Trans., 2018, 47, 15512–15522 RSC.
- E. Sellami-Jmal, A. Marzouki, W. Cheikhrouhou-Koubaa, A. Cheikhrouhou and N. Njah, J. Supercond. Nov. Magn., 2015, 28, 831–838 CrossRef CAS.
- R. Dhahri, M. Bejar, M. Hajlaoui, N. Sdiri, M. A. Valente and E. Dhahri, J. Magn. Magn. Mater., 2009, 321, 1735–1738 CrossRef CAS.
- R. Selmi, W. Cherif and N. M. Ferreira, J. Supercond. Nov. Magn., 2022, 35, 3585–3601 CrossRef CAS.
- J. Makni-Chakroun, R. M’nassri, W. Cheikhrouhou-Koubaa, M. Koubaa, N. Chniba-Boudjada and A. Cheikhrouhou, Chem. Phys. Lett., 2018, 707, 61–70 CrossRef CAS.
- N. Ameur, F. Elleuch, M. Triki, E. Dhahri, L. Bessais and E. K. Hlil, Solid State Commun., 2019, 289, 30–37 CrossRef CAS.
- R. Skini, A. Omri, M. Khlifi, E. Dhahri and E. K. Hlil, J. Magn. Magn. Mater., 2014, 364, 5–10 CrossRef CAS.
- C. R. Sankar and P. A. Joy, Phys. Rev. B: Condens. Matter Mater. Phys., 2005, 72, 024405 CrossRef.
- P. Schiffer, A. P. Ramirez, W. Bao and S.-W. Cheong, Phys. Rev. Lett., 1995, 75(16), 3336–3339 CrossRef CAS PubMed.
- S. Majumdar and S. Van Dijken, J. Phys. D: Appl. Phys., 2014, 47, 034010 CrossRef CAS.
- H. Fujishiro, T. Fukase and M. Ikebe, J. Phys. Soc. Jpn., 1998, 67, 2582–2585 CrossRef CAS.
- A. Szewczyk, M. Gutowska and B. Dabrowski, Phys. Rev. B: Condens. Matter Mater. Phys., 2005, 72, 224429 CrossRef.
- H. L. Ju, Y. S. Nam, J. E. Lee and H. S. Shin, J. Magn. Magn. Mater., 2000, 219, 1–8 CrossRef CAS.
- Z. M. Wang, G. Ni, H. Sang and Y. W. Du, J. Magn. Magn. Mater., 2001, 234, 213–217 CrossRef CAS.
- N. Abdelmoula, J. Dhahri, K. Guidara, E. Dhahri and J. C. Joubert, Phase Trans., 1999, 70, 197–210 CrossRef CAS.
- A. N. Ulyanov, S. C. Yu, N. Y. Starostyuk, N. E. Pismenova, Y. M. Moon and K. W. Lee, J. Appl. Phys., 2002, 91, 8900–8902 CrossRef CAS.
- W. Abdelhedi, A. Krichene, N. Chniba Boudjada and W. Boujelben, Ceram. Int., 2024, 50, 11528–11538 CrossRef CAS.
- Y. Li, H. Zhang, Q. Chen, D. Li, Z. Li and Y. Zhang, Ceram. Int., 2018, 44, 5378–5384 CrossRef CAS.
- B. He, Z. Zou, W. Zhang, X. Jiang and Z. Mao, J. Electron. Mater., 2023, 52, 2665–2675 CrossRef CAS.
- S. L. Yuan, G. Peng, Z. C. Xia, J. Liu, S. Liu, Z. Y. Li, Y. P. Yang, L. Liu, J. Tang, G. H. Zhang, L. J. Zhang, W. Feng, C. S. Xiong and Y. H. Xiong, Solid State Commun., 2002, 121, 501–504 CrossRef CAS.
-
S. Blundell, Magnetism in Condensed Matter, Oxford University Press, Oxford, New York, 2001 Search PubMed.
- V. E. Salazar-Muñoz, S. A. Palomares-Sánchez, I. Betancourt, T. J. Pérez-Juache, V. D. Compeán-García and A. L. Guerrero, J. Sol-gel Sci. Technol., 2019, 90, 241–249 CrossRef.
- A. Marzouki-Ajmi, H. Omrani, W. Cheikhrouhou-Koubaa, M. Koubaa and A. Cheikhrouhou, J. Alloys Compd., 2017, 690, 403–411 CrossRef CAS.
- A. G. Gamzatov, A. B. Batdalov, N. Z. Abdulkadirova, A. M. Aliev, V. V. Khovaylo, T. D. Thanh, N. T. Dung and S. C. Yu, J. Alloys Compd., 2023, 964, 171330 CrossRef CAS.
- T. D. Thanh, N. T. Dung, N. T. V. Chinh, D. S. Lam, D. A. Tuan and A. G. Gamzatov, J. Alloys Compd., 2021, 884, 161046 CrossRef CAS.
- S. Chatterjee and I. Das, J. Alloys Compd., 2023, 935, 167957 CrossRef CAS.
- A. F. Manchón-Gordón, A. Gómez, J. J. Ipus, J. S. Blázquez, C. F. Conde and A. Conde, J. Alloys Compd., 2020, 848, 156566 CrossRef.
- R. Dhinesh Kumar, R. Thangappan and R. Jayavel, Res. Chem. Intermed., 2018, 44, 4323–4337 CrossRef CAS.
- K. Zmorayová, P. Diko and J. G. Noudem, Mater. Sci. Forum, 2017, 891, 468–472 Search PubMed.
- J. Cheng, C. You, N. Tian, Y. Deng, L. Gao, P. Wang, Y. Guo and Z. Li, J. Magn. Magn. Mater., 2024, 596, 171935 CrossRef CAS.
- A. Ezaami, N. O. Nasser, W. Cheikhrouhou-Koubaa, M. Koubaa, A. Cheikhrouhou and E. K. Hlil, J. Mater. Sci.: Mater. Electron., 2017, 28, 3648–3658 CrossRef CAS.
- H. Baaziz, A. Tozri, E. Dhahri and E. K. Hlil, J. Magn. Magn. Mater., 2016, 403, 181–187 CrossRef CAS.
- P. T. Phong, D. H. Manh, L. C. Hoan, T. V. Ngai, N. X. Phuc and I. J. Lee, J. Alloys Compd., 2016, 662, 557–565 CrossRef CAS.
- G. Jagadish Kumar, A. Jose, E. P. Jinu, T. T. Saravanan, E. Senthil Kumar, M. Navaneethan, H. Sreemoolanadhan and K. Kamala Bharathi, Mater. Res. Bull., 2023, 160, 112140 CrossRef CAS.
- T. L. Phan, N. T. Dang, T. A. Ho, T. V. Manh, T. D. Thanh, C. U. Jung, B. W. Lee, A. T. Le, A. D. Phan and S. C. Yu, J. Alloys Compd., 2016, 657, 818–834 CrossRef CAS.
- I. Othmani, Y. Regaieg, F. Ayadi, W. Cheikhrouhou-Koubaa, M. Koubaa, V. Nachbaur, M. Abdelhedi and A. Cheikhrouhou, J. Supercond. Nov. Magn., 2023, 36, 1143–1152 CrossRef CAS.
- S. Choura-Maatar, R. M’Nassri, W. Cheikhrouhou-Koubaa, M. Koubaa, A. Cheikhrouhou and E. K. Hlil, RSC Adv., 2017, 7, 50347–50357 RSC.
- S. Banerjee, Phys. Lett., 1964, 12, 16–17 CrossRef.
- C. Henchiri, R. Hamdi, T. Mnasri, M. A. Valente, P. R. Prezas and E. Dhahri, Appl. Phys. A: Mater. Sci. Process., 2019, 125, 725 CrossRef.
- J. Dhahri, R. Lefi, S. Bouzidi, M. Essid, F. Abdulaziz, A. H. Alsehli and M. M. Alsowayigh, Appl. Phys. A: Mater. Sci. Process., 2023, 129, 726 CrossRef CAS.
- S. Ghorai, R. Skini, D. Hedlund, P. Ström and P. Svedlindh, Sci. Rep., 2020, 491, 19485 CrossRef PubMed.
- E. Bouzaiene, A. H. Dhahri, J. Dhahri, E. K. Hlil and A. Bajahzar, J. Magn. Magn. Mater., 2019, 491, 165540 CrossRef CAS.
- V. Franco, A. Conde, J. M. Romero-Enrique and J. S. Blázquez, J. Phys.: Condens. Matter, 2008, 20, 285207 CrossRef.
- V. Franco, J. S. Blázquez and A. Conde, Appl. Phys. Lett., 2006, 89, 222512 CrossRef.
- Z. Xie, Z. Zou, X. Jiang, W. Zhang, B. He, X. Han and Z. Mao, Phys. B, 2022, 639, 413985 CrossRef CAS.
- C. M. Bonilla, J. Herrero-Albillos, F. Bartolomé, L. M. García, M. Parra-Borderías and V. Franco, Phys. Rev. B: Condens. Matter Mater. Phys., 2010, 81, 224424 CrossRef.
- S. A. Makhlouf, T. Nakamura and M. Shinga, J. Magn. Magn. Mater., 1994, 135, 257–264 CrossRef CAS.
- K. Momma and F. Izumi, J. Appl. Crystallogr., 2011, 44, 1272–1276 CrossRef CAS.
- R. S. Liu, C. H. Shen and S. F. Hu, Int. J. Inorg. Mater., 2001, 3, 1063–1072 CrossRef CAS.
- M. Hennel, L. Galdun, A. Džubinská, M. Reiffers and R. Varga, J. Alloys Compd., 2023, 960, 170621 CrossRef CAS.
- J. Ouyang, Y. Tian, H. Xiao and Y. Zhang, Mater. Chem. Phys., 2021, 273, 125150 CrossRef CAS.
- M. Ye, C. Jing, C. Liu, Y. Zhang, X. Sun, B. Kang, D. Deng, Z. Li and K. Xu, J. Magn. Magn. Mater., 2018, 462, 178–184 CrossRef CAS.
- D. M. R. Kumar, M. M. Raja, R. Gopalan, R. Balamuralikrishnan, A. K. Singh and V. Chandrasekaran, J. Alloys Compd., 2008, 461, 14–20 CrossRef CAS.
- J. Q. Deng, Y. H. Zhuang, J. Q. Li and K. W. Zhou, J. Alloys Compd., 2007, 428, 28–33 CrossRef CAS.
- E. Yüzüak, I. Dincer and Y. Elerman, J. Rare Earths, 2010, 28, 477–480 CrossRef.
- F. Gao, W. Ren, H. Wu, M. An, X. Zhao, B. Li and Z. Zhang, J. Solid State Chem., 2023, 328, 124347 CrossRef CAS.
- R. Nirmala, D. C. Kundaliya, S. R. Shinde, A. G. Joshi, A. V. Morozkin and S. K. Malik, J. Appl. Phys., 2007, 101, 123901 CrossRef.
- Z. Wang, Y. Zhang, C. Chen, H. G. Piao, L. Ding, L. Pan, J. Huang, H. R. Park, D. S. Kim and S. C. Yu, J. Magn. Magn. Mater., 2023, 565, 170147 CrossRef CAS.
- X. C. Zhong, X. L. Feng, X. W. Huang, X. Y. Shen and Z. W. Liu, J. Alloys Compd., 2016, 685, 913–916 CrossRef CAS.
- L. Xian, J. Yu, W. Lin, S. Ke, C. Liu, X. Nie, W. Zhu, P. Wei, D. He, W. Zhao and Q. Zhang, Intermetallics, 2023, 153, 107827 CrossRef.
- J. I. E. Hu, H. A. O. T. I. A. N. Liu, X. I. N. Y. A. O. Zhang, Z. H. I. Wang, Z. H. I. G. A. N. G. Yang, M. E. N. G. N. A. N. Feng and X. U. E. P. E. N. G. Shi, Heliyon, 2024, 10(3), e25169 CrossRef CAS PubMed.
- Y. Yan, C. Liu, W. Lu, Y. Sun, W. Zhu, X. Nie, X. Sang, W. Zhao and Q. Zhang, J. Alloys Compd., 2022, 910, 164858 CrossRef CAS.
- V. Chaudhary and R. V. Ramanujan, IEEE Magn Lett., 2015, 6, 6700104 Search PubMed.
- V. Chaudhary and R. V. Ramanujan, Sci. Rep., 2016, 6, 35156 CrossRef CAS PubMed.
- P. Gorria, J. L. Sánchez Llamazares, P. Álvarez, M. J. Pérez, J. Sánchez Marcos and J. A. Blanco, J. Phys. D: Appl. Phys., 2008, 41, 192003 CrossRef.
- M. A. Islam and A. K. M. A. Hossain, RSC Adv., 2022, 12, 17362–17378 RSC.
- S. Hcini, N. Kouki, A. Omri, A. Dhahri and M. L. Bouazizi, J. Magn. Magn. Mater., 2018, 464, 91–102 CrossRef CAS.
- J. K. Murthy, K. Devi Chandrasekhar, S. Mahana, D. Topwal and A. Venimadhav, J. Phys. D: Appl. Phys., 2015, 48, 355001 CrossRef.
- T. Chakraborty, H. Nhalil, R. Yadav, A. A. Wagh and S. Elizabeth, J. Magn. Magn. Mater., 2017, 428, 59–63 CrossRef CAS.
- Y. Jia, Q. Wang, Y. Qi and L. Li, J. Alloys Compd., 2017, 726, 1132–1137 CrossRef CAS.
- L. Su, X. Q. Zhang, Q. Y. Dong, Y. J. Ke, K. Y. Hou, C. S. Liu and Z. H. Cheng, J. Alloys Compd., 2018, 746, 594–600 CrossRef CAS.
- Y. Jia, Q. Wang, P. Wang and L. Li, Ceram. Int., 2017, 43, 15856–15861 CrossRef CAS.
- Z. Dong, Z. Wang and S. Yin, Ceram. Int., 2020, 46, 26632–26636 CrossRef CAS.
- D. Chi Linh, N. Thi Viet Chinh, N. Thi Dung, L. Viet Bau, N. Huu Duc, D. Hung Manh and T. Dang Thanh, Phys. B, 2023, 661, 414945 CrossRef.
- M. E. Botello-Zubiate, M. C. Grijalva-Castillo, D. Soto-Parra, R. J. Sáenz-Hernández, C. R. Santillán-Rodríguez and J. A. Matutes-Aquino, Materials, 2019, 12, 309 CrossRef CAS PubMed.
- H. Baaziz, A. Tozri, E. Dhahri and E. K. Hlil, Chem. Phys. Lett., 2018, 691, 355–359 CrossRef CAS.
- S. K. Estemirova, V. Y. Mitrofanov, S. A. Uporov and G. A. Kozhina, Solid State Sci., 2022, 124, 106806 CrossRef CAS.
- A. Bouzayen, A. Elghoul, A. Krichene, N. Chniba Boudjada and W. Boujelben, J. Alloys Compd., 2023, 952, 169986 CrossRef CAS.
- A. Mabrouki, A. Benali, T. Mnasri, E. Dhahri, M. A. Valente and M. Jemmali, J. Mater. Sci.: Mater. Electron., 2020, 31, 22749–22767 CrossRef CAS.
|
This journal is © the Owner Societies 2024 |