DOI:
10.1039/D3QI01522J
(Review Article)
Inorg. Chem. Front., 2023,
10, 7095-7108
Recent advances in electrocatalytic reduction of ambient CO2 toward high-value feedstock
Received
3rd August 2023
, Accepted 10th October 2023
First published on 17th October 2023
Abstract
The effects of climate change have arisen due to greenhouse gases emitted into the atmosphere, and the finite supply of fossil fuels will eventually be unable to support the needs of the petrochemical industry. Solutions to these two complex problems will have to be multipronged, but the industrial implementation of the electrocatalytic reduction of CO2 can help with both issues. Importantly, the demand for multi-carbon feedstock offers immediate financial incentives, accelerating the search for solutions to the climate problem. However, the technology for the electrocatalytic reduction of CO2 is still in the process of being commercialised, and the use of ambient CO2 is a prerequisite for widescale adoption. Here we discuss the progress in this area and the remaining barriers to realizing its potential.
1. Introduction
Nature has a rich history of converting CO2 into valuable resources driven by the abundant renewable energy from the sun. Carbon monoxide dehydrogenase/acetyl–CoA synthase, the main enzymatic complex in thousands of types of bacteria, has been remarkably effective in microorganisms for more than 3.5 billion years, fixing CO2 as a carbon resource.1 In contrast, human beings have only enjoyed highly energy-intensive modern life since the industrial revolution, powered by oxidising energetically compressed fossil fuels. This process results in the reverse carbon flow from underground to the atmosphere. This anthropogenic oxidative carbon consumption accounts for the rise of atmospheric CO2 levels, as illustrated by the Keeling Curve.2 Consequently, the United Nations has declared “a code red for humanity”, warning that the concentration of atmospheric greenhouse gases poses a threat to lives, economies, health and food security.
A desired pathway is to aggressively implement renewable energies, which would consequently lead to a dramatic shift in the material production scheme from the fossil-fuel dependent supply chain to one that relies on more sustainable resources. The CO2 reduction reaction (CO2RR) has the potential to play a pivotal role in accelerating such a material evolution due to its attractive natural features: it occurs under atmospheric reaction conditions, does not require any side reactants such as hydrogen, is compatible with renewable energy resources, and offers a wide range of potential products.
A literature search shows that the CO2RR study dates back as far as the 1950s as a way to produce chemicals.3,4 In the 1980s and 90s, comprehensive research was conducted on a variety of metal or molecular catalysts and electrolytes to discuss the selectivity of CO2RR.5–7 As predicted by Hori,7 there has been a significant resurgence in the use of CO2RR within the research community in recent years, resulting in an increasing number of publications equivalent to Moore's law (Fig. 1). Despite its long history and the renewed focus on developing efficient and selective electrocatalysts, CO2RR has not been adopted by conventional chemical industries as a replacement for fossil fuels. This is in contrast to lithium-ion battery technology, which was discovered later but has been widely commercialised with an even steeper rise in the publication rate.
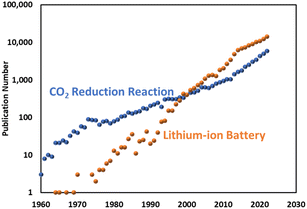 |
| Fig. 1 Annual publications for an electrocatalytic CO2 reduction reaction and lithium-ion battery research. | |
Why has nature successfully implemented ambient CO2 reduction, while the same achievement has thus far eluded human ingenuity? With this question in mind, we will discuss several important aspects of CO2RR. However, given the breadth of research in this field, this review does not seek to be exhaustive; rather, it aims to provide insight into the economic viability and future of CO2RR. First, we introduce the potential products of CO2RR, followed by a techno-economic analysis to shed light on the current barriers towards the successful commercialization of CO2RR. Finally, we will review a few studies dealing with the less-discussed but significant properties for successful CO2RR implementation.
2. Basic principles and catalyst science for CO2RR
One of the attractive but complicating features of CO2RR is that it has a variety of possible products along with competing hydrogen evolution reaction (HER), all of which have similar standard redox potentials vs. reversible hydrogen electrode derived from the Gibbs energy and physicochemical constant.8 Due to the close thermodynamic characteristics of CO2RR, the selectivity of the expected CO2RR is dependent on both the modulation of electrochemical activation energy toward a specific route and the availability of the corresponding reactants. An electrochemical catalyst is needed to lower the activation energy of a specific target by stabilising an intermediate for the reaction. CO2RR is an inner-sphere reaction involving multiple electron- and proton-transfer processes. In contrast to an outer-sphere reaction, in which the electron transfer occurs through tunnelling across a monolayer of solvents, the heterogeneous inner-sphere reaction is based on the interaction of a reactant, a product, or an intermediate with the catalyst surface. These interactions enable a critical intermediate species more likely to be structurally changed in subsequent steps.
As a principle, the rate of the multi-step reaction is determined by the slowest step, i.e., the rate-determining step (RDS). It has been proposed that two-electron transfer reactions of CO2RR into CO or HCOOH may possess different types of RDS.9–11
As for CO2RR into CO and HCOOH (Fig. 2), steps 1 and 5 represent the CO2 adsorption process which triggers the CO2RR pathway. A recent study indicates that this process can be dependent on the applied potential because of the interaction between the dipoles of the participating reaction intermediates with the interfacial field.10,11 Both field-dependent density functional theory and pH-dependent activity measurements concluded that the ideal catalyst should possess large adsorbate dipoles on CO2*.10 Steps 2 and 6 are concerted proton–electron transfer steps, and the configuration of CO2* seems to determine the selectivity with transition metal surfaces.12 One computational study13 suggests that the C-atom bonding structure leads to the CO production pathway while an O-atom mediated bond is more likely to induce formate/formic acid production. Experimental studies such as in situ surface Raman scattering confirm that such a configurational change determines the selectivity of the CO2RR product.14,15 Steps 1′ and 5′ are proton-decoupled electron-transfer steps whose kinetics are independent of the number of local protons in the vicinity of the catalytic site, followed by the protonation to form COOH or OCOH [steps 2′ and 6′]. The final step of CO2RR is the desorption of a product from the catalytic site [steps 4 and 8]. Since the electrochemical activation energy expectedly correlates with the adsorption energy between the intermediate species of the rate determining step and the catalytic sites, the free energy of the adsorption of the intermediate is usually discussed to elucidate the catalyst selectivity.
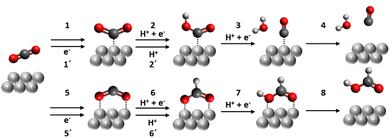 |
| Fig. 2 Reaction schemes for the CO2 reduction reaction into CO or HCOO. | |
3. Techno-economic analysis of CO2RR in the context of performance matrices
Since CO2RR is an alternative way to produce existing fossil fuel-derived catalysts, the electro-synthesized product needs to compete economically with the widely-established market products. In this context, a techno-economic analysis (TEA) should be considered and included in the discussion of studies which investigate the application of CO2RR. One of the simplest ways to approximate the economic validity of CO2RR products is to plot the relationship between the minimum energy requirement for the targeted product and the corresponding market price. Here the minimum energy consumption per unit mass Emin is defined by |  | (1) |
where n is the electron number for a specific reaction,
is the standard redox potential for CO2RR,
is the standard redox potential for the counter reaction, F is the faradaic constant, and MW is the molar mass of the product.
The thermodynamic cell potential serves as an indicator of the minimum energy requirement for a given product and thus, given the energy costs, provides a means to estimate the economic viability of a product. Fig. 3 shows the possible CO2RR products plotted as a function of Emin and market price as of 2023. One notices that CO and formic acid are well positioned in this proximity of economic analysis due to its two-electron transfer characteristics. Some oxygenates such as acetic acid and acetaldehyde also possess a relatively high market value compared to the required minimum cost. Alcohol derivatives and graphite materials are in the middle group because of the moderate minimum costs and current economic value. As the carbon number in the alcohol increases, the minimum cost and current market price increase concomitantly, indicating that the market price reflects the energy required for the chemical supply. The graph also highlights the challenges of synthesizing hydrocarbon products such as ethylene, methane, and ethane. The discrepancy between the low market price and the high-cost characteristics of these derivatives is attributed to the fundamental differences between the processes in the existing petrochemical infrastructure and in a future CO2-based electrochemical supply. Specifically, hydrocarbons can be extracted from fossil fuels without additional energy to convert chemical structures since nature has already converted CO2 into hydrocarbons over a long period of time. By contrast, CO2RR needs additional energy to convert CO2 into hydrocarbons, which inevitably adds costs relative to fossil-fuel-derived hydrocarbons. Since hydrocarbons are a fundamental commodity for the chemical industry, subsidies are likely needed for the timely implementation of CO2RR to support the hydrocarbon chemical chain.
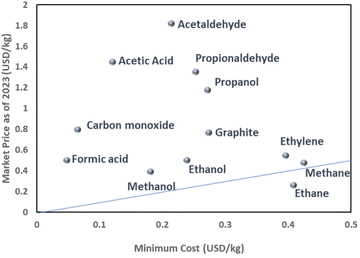 |
| Fig. 3 Possible electrocatalytic CO2 reduction reaction products plotted as a function of minimum energy consumption per unit mass and market price as of 2023. The line represents the break-even point assuming no additional financial incentives. | |
Note that recent electrocatalyst and photocatalyst studies have demonstrated the combination of CO2RR and an unconventional anode reaction to either reduce the cell voltage16 or directly synthesize more complex chemicals,17,18 which may pave the way toward an efficient CO2RR production system.
While the minimum cost approximation is helpful to identify the economic potential of CO2RR targets, the actual TEA should be more in-depth. There are three basic process steps for CO2RR: CO2 purification, CO2 conversion, and product purification (Fig. 4). The TEA of the overall chemical process reminds us of what we need to rapidly scale up the CO2RR and, in turn, provides key insights for essential future studies.
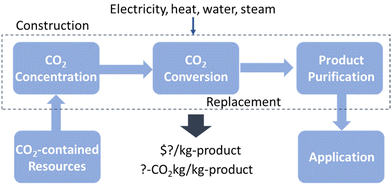 |
| Fig. 4 Basic processes for a scaled-up electrocatalytic CO2 reduction reaction: CO2 purification, CO2 conversion, and product purification. | |
The cost associated with CO2 purification depends on the CO2 ratio of the initial gas mixture and a capture method. CO2 captured from concentrated CO2 sources, such as power and chemical plants or from amine technology, has the lowest price of $50–70 t−1 with a US Department of Energy target of $40 t−1.19 On the contrary, capturing CO2 from the air is more expensive than from flue gas because of its low concentration: one study estimated that the cost for CO2 capture from the air could potentially reach ≈$100–200 t−1 in the future.20 The cost of CO2 purification in a typical carbon conversion unit provides an opportunity to pursue new technology to simplify or eliminate CO2 purification. If effluent gas is converted in the CO2 conversion unit on site in places such as fired power plants or incineration plants, the cost for the CO2 purification step decreases. In addition, the degree of required CO2 purification depends on how sensitive the CO2 conversion is to the impurities in the gas stream entering the CO2 conversion. For instance, NOx and SOx are usually present in exhaust gas and the effects of these oxide impurities on the selectivity and durability of the CO2RR catalyst are still largely unexplored.
The CO2RR product purification process includes gas and/or liquid separation, depending on the physicochemical properties of the production. Gas separation is usually required because of the presence of unconverted CO2 and unintended side products such as H2 in the product effluent. Liquid product separation is often required to extract products in the liquid catholyte. Pressure swing adsorption (PSA) and membrane technologies are currently used in other industrial processes with similar gas compositions.21 It appears that PSA is generally preferred because of its relatively low operating costs and high efficiency with an estimated cost of around $10 t−1 based on CO2RR TEA22 and the Sherwood plot for the separation of dilute streams.23 Liquid product separation can be executed through distillation, extraction, precipitation, and pervaporation.21 Among these, distillation is widely used but it is expected to have a much higher operational cost than gas separation with PSA.
The operational cost of the CO2RR product depends on the purity of the target and chemical composition in the product stream from the electrochemical conversion unit. Thus, both the selectivity and conversion ratio of CO2RR are imperative to determine the energy required for the purification process. In addition, the additives for the electrochemical reaction, such as electrolyte salts and co-catalysts, should be considered in the cost analysis for the product separation process.
The CO2 conversion unit operates predominantly with electricity as input energy and CO2 as feedstock. Therefore, the energy efficiency in converting CO2 into target chemicals, defined as the ratio of thermodynamic energy to input energy, affects the operational cost of CO2RR. Energy efficiency is a function of the sum of the overpotential of cathodic and anodic reactions along with other voltage drops in an electrolyser and FE for the specific product. CO2RR into hydrocarbon such as ethylene usually requires prominent overpotential to kinetically drive the reaction, which may push up the operational costs. As for the CO2 feedstock, the conversion ratio of CO2 as a system affects the operational cost as the unconverted CO2 is either wasted or requires more energy to be recycled. The CO2RR cell is preferably designed to minimize CO2 loss. For instance, when an alkaline electrolyte is used on the cathode side, CO2 loss likely occurs as a dissolved carbonate, preventing the efficient utilization of CO2. One strategy is to utilize a fully carbonated system with an anion exchange membrane, which leads to the consumption of CO2 at the cathode and the re-emission of CO2 with oxygen at a locally acidic anode. However, an additional separation step is required to recover CO2 from the anode vapours.
As for the capital cost, the partial current density, the observed current for the relevant reaction per geometric area, is important to determine the total electrode size of the electrolyser for the CO2RR. Given that the number of electrons to be transferred varies depending on the CO2RR reaction, a more practical manner to evaluate the productivity of CO2RR may be to convert current density into the production rate of the targeted product per geometric area.
The durability of the CO2 converting unit or electrochemical cell is also an important factor in affecting the frequency of cell replacement and the operational cost. TEA studies often use a lifecycle of 5–30 years.22,24,25 However, conventional CO2RR studies usually report durability results for times of 10–100 h, and there is a gap between the current testing period and the prolonged durability test required before building the actual plant. Moreover, an accelerated testing protocol needs to be designed to speed up the durability development, which is also currently not well addressed. The definition of the reduction in performance at which the CO2RR cell should be replaced will remain an open question until key stability/durability relationships are experimentally established.
One should note that the CO2RR process can reduce or increase CO2 emissions depending on the energy required for the total production process and the carbon intensity of the electricity and utilization. The carbon intensity of renewable energy is significantly lower than that of fossil fuel-derived electricity, suggesting the combination of the CO2RR process and such renewable energy can be a more carbon-neutral scheme. In this case, integrating the CO2RR process into the off-grid renewable energy should be discussed since the plant system requires additional electric equipment, such as energy storage systems and converters. A hydrogen production electrolyser plant powered by renewable energy can be a good model for estimating the cost impact of electricity management in a CO2RR plant.
The source of CO2 and electricity significantly affects the cost of the CO2RR process and the benefit of CO2 emission reduction. The CO2RR process prefers more concentrated CO2 sources in the fluent gas. However, we should envision the long-term viability of CO2 emitters since the social system will require a change toward more carbon–neutral structures. The electricity price changes significantly depending on the region, the electricity resources, and geopolitical environments. Since the CO2RR plant is an electricity-demanding process, one needs to choose the place to develop the plant carefully. Usually, TEA applies an electricity cost of 0.02–0.03 USD per kW per h,22,24,25 which still limits the actual short-term option to scale up the CO2RR process, which can reflect the cost simulation of the TEA.
After providing an overview of TEA, we propose emphasizing the following domains in the plant flow (CO2 concentration, conversion, and the production purification step) for scaling up CO2RR deployment (Fig. 5): (1) the effect of chemical composition of the feed gas, (2) the industrially relevant productivity and durability of CO2RR, and (3) maximizing the CO2 conversion ratio and optimizing selectivity to minimize the need for purification processes.
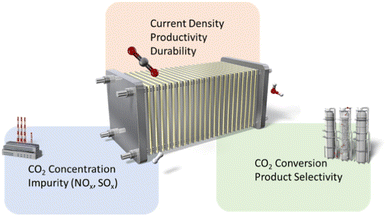 |
| Fig. 5 The highlighted research domain in the process flow of the electrocatalytic CO2 reduction reaction. | |
4. Noteworthy CO2RR research toward economically valuable feedstock
4.1. Effect of the chemical composition of feed gas
Most CO2RR research has been carried out with concentrated CO2, which helps increase the reaction rate and selectivity of CO2RR due to the high availability of CO2 at catalytic sites and avoids undesirable side reactions stemming from impurities. As mentioned in section 3, the CO2 concentration process, while relatively mature, introduces additional energy consumption and costs to implement CO2RR, which may induce unfavourable CO2 emissions. Therefore, it is desirable that the CO2RR is compatible with direct effluents from CO2 sources. The CO2 concentration of fired power plants is around 15% (v/v), depending on the type of fossil fuels and combustion system. Also, industry exhaust streams often contain other gaseous species such as N2, O2, H2O, NOx, SOx, and volatile organic compounds. The oxidized components of flue gas, such as SOx and NOx, may influence CO2RR catalysts, although their concentrations are low (typically in the order of hundreds of ppm). Therefore, deviating from pure CO2 gas could impact the CO2RR catalytic activity and durability.
The decrease in CO2 partial pressure is expected to decrease the reaction rate of CO2RR when CO2 diffusion is a rate-limiting step. This is the case for electrolysis under the practical conditions of operating close to the maximum partial current density regardless of the structure of the electrolyser cell. Additionally, the decreased CO2 partial pressure creates a reaction environment preferable to the competing HER since the number of protons for the reaction is independent of the gas component. Moreover, the adverse effect of limited CO2 in the incoming gas may become more severe as the size of the electrolyser increases because the consumption of CO2 in the gas or electrolyte occurs along with the plane of the electrode, and the gas/liquid stream close to the outlet of the flow cell has the lowest amount of CO2. Therefore, the influence of CO2 partial pressure is a vital factor in determining the compatibility of CO2RR with the exhaust gas.
There have been some studies on the effect of CO2 partial pressure and presenting engineering-based strategies to tackle limitations. Among the pioneering studies in the 1990s,26,27 Komatsu observed that the current density and FE for CO2RR decreased as CO2 concentration decreased from 100 to 14% with the copper composite electrode for the gas-phase CO2RR.28 Consistent with that work, Kenis et al.29 reported that the partial current density noticeably decreased with the decrease in the CO2 concentration with Ag nanoparticle catalysts on the gas diffusion electrode in the CO2/N2 mixture feed in 1 M KCl electrolyte media. The authors also observed the decrease in the FE for CO2RR to CO by using phosphate buffer as the electrolyte to distinguish between the effect of CO2 partial pressure and pH in the electrolyte. The pH dependency study showed that the FE for CO2RR to CO decreased more severely with the decrease in pH, suggesting that the number of local protons initiates the HER, diminishing CO2RR more easily as either the CO2 concentration in the feed or the pH in the electrolyte decreased.
A straightforward way to address the diluted CO2 concentration is to elevate the pressure of the electrolyser system, which increases CO2 availability at the catalyst. Xu et al.30 demonstrated that the pressurization of the feed gas at 15 bar successfully maintained a 91% FE for CO2RR to CO with 15% (v/v) CO2, which is similar to or higher than that of the performance with pure CO2 at 1 bar, depending on the applied potential. While pressurization requires some additional energy input, they calculated that the energy required to pressurize to 10 bar represents only ∼3% of the energy required to perform efficient CO2RR to C2 products. These results indicate that pressurization helps enable the direct conversion of streams with CO2 concentrations characteristic of major flue gas sources at industrially relevant current densities.
O2 is the highest concentration reactive impurity in flue gas and is challenging to remove. The oxygen reduction reaction has a more favourable thermodynamic potential and kinetics compared to CO2RR, which significantly impedes the target selectivity. As an initial study, Morikawa et al.31 confirmed that the inclusion of O2 significantly reduces the FE for CO2RR to formate with a porous ruthenium complex polymer catalyst on a photocathode from 93% (at 0% O2) to 6% (at 7% O2) due to the selective O2 reduction competing with CO2 reduction. They demonstrated that the combination of the catalyst with carbon papers mitigated the drop of FE to 75% at 7% O2, which is attributed to the affinity of the carbon materials to gaseous CO2 in aqueous solution, resulting in the relatively concentrated CO2 in the vicinity of the catalytic sites. However, the measurement of local CO2 should be carried out for further discussion.
Exploiting the difference in solubility between CO2 and O2 in the electrolyte media is one way of mitigating the parasitic effect of O2. Sinton et al.30 exploited an ionomer and TiO2 coating to create a hydrophilic environment around the Cu catalysts so that CO2 can predominantly dissolve and reach the catalytic sites over O2. They observed a FE towards C2 products of 68% and energy efficiency of 26% over 10 h of stable operation (at 10 bar), a performance competitive with some of the best results previously reported on reactors using pure CO2.
Another methodology to circumvent the oxygen reduction reaction is to implement an additional layer to selectively transport or adsorb CO2 over O2. Wang et al.32 demonstrated that a polymer of intrinsic microporosity serves a role in selectively permitting CO2 to permeate while preventing O2 from reaching the catalytic sites. They coated the gas separation polymer on the opposite side of the carbon paper of the cobalt phthalocyanine catalyst and observed FE for CO of 75.9% in a gas with 5% O2 in contrast to the catalyst without the gas separation layer performing no observable FE with the same O2 concentration. Subsequently,33 the authors applied aniline molecules to enhance the ability of the permeable ionic membrane (PIM) to separate CO2 from O2 using chemical interactions between the acidic CO2 and the basic amino group of aniline. In an electrolytic flow cell with a cobalt phthalocyanine/carbon nanotube catalyst, they observed a FE for CO of 71% in the presence of 10% O2 in CO2 using the PIM/aniline membrane, therefore outperforming the pure PIM with a FE for CO of 63% under the same conditions. While these studies highlight the effectiveness of structurally or chemically engineering the microstructure, further research regarding the physicochemical properties of CO2 and O combined with kinetic modelling will lead to clearer design principles for selective CO2 supply in a microenvironment.
NOx is among the major contaminants present in industrial CO2 point sources with a typical concentration of 10–500 ppm depending on the regional regulation and combustion system.34 NOx usually consists of 90–95% NO and 5–10% NO2, N2O being a common by-product formed in the NOx removal process. All of these NOx gases can compete with CO2 for electrons through the corresponding reduction reaction, which has a more favourable standard redox potential than CO2RR. Therefore, the kinetics of the NOx reduction reaction, along with the concentration of NOx, could be crucial factors to be investigated. Moreover, NO2 can also react with water to produce various acidic products, including nitric and nitrous acids.
Komatsu et al.28 found no effect of 200 ppm NO on the catalytic activity of gas-phase CO2RR with a copper-deposited electrode. The author argued that the amount of NO was about two times higher than that of the exhaust gas from a typical coal-fired power plant. Jiao et al.35 demonstrated that the presence of much higher amounts of NO, NO2, and N2O (8300 ppm) in the CO2 feed leads to a considerable FE loss in CO2RR with Cu, Ag, and Sn catalyst-loaded gas diffusion electrodes. Notably, they observed the recovery of the FE for CO2RR after switching the feed gas without NOx, suggesting that NOx is involved in the electroreduction process but does not affect the structure of the catalysts in these conditions. In addition, they evaluated the effect of 830 ppm and 83 ppm NO, showing less severe (less than 5%) and negligible losses in FE, respectively, highlighting that CO2RR can be compatible with typical concentrations of NOx in flue gases. Note that the parasitic effect of NOx is dependent on the nature of the catalyst and an electrochemical setup. Oh et al.36 reported a decrease in FE for HCOO– from 69.4% to 37.7% using SnSx as the catalyst in the presence of 90 ppm NO. Sridhar et al.37 observed a loss in FE for ethylene of 22.9% after exposing the copper catalyst to 1% NO2 and a change in the surface colour of the copper catalyst, showing that excessive NO2 may contribute to the oxidation of the catalysts.
SOx is another possible chemical component in the gas feed. Typical power plants emit exhaust containing 10–300 ppm SO2. Komatsu et al.28 found that 170 ppm SO2 in the feed noticeably changed the distribution of the products with a copper catalyst. Jiao et al. observed a general decrease in the FE for total CO2 reduction after copper, silver, and tin catalysts were exposed to a gas stream of 1% SO2 in CO2, which is attributed to the preferential reduction of SO2. Silver and tin catalysts showed less change in the product distribution and the recovery of FE for each product was attained after stopping the feed of SO2. However, the catalyst characterization shows the sulfurization and desulfurization reaction of Ag and Sn after the SO2 and pure CO2 feed, respectively, inferring that these materials are relatively durable against the sulfur-derived structural change. On the contrary, the exposure of SO2 causes the product distribution with Cu catalysts toward formate, which is irreversible even after switching back to a pure CO2 stream. The authors attributed the change to residual Cu2S formed on the surface.
One finds that there is a sizeable difference between the amount of impurities used for the CO2RR studies mentioned above and the actual content found in the exhaust from specific CO2 sources. This is because the emitters have often already modified the fraction of impurities to prevent air pollution. Therefore, in more practical scenarios, the tested chemical composition for CO2RR needs to match the actual composition for a true feasibility study. Investigations into the effects of impurities on the durability of the CO2RR catalyst should also be conducted. Since the existing CO2 purification process, such as the amine adsorption method, already works to reduce the impurities, the total design of combining the CO2 purification and conversion relies on the efficiency and durability of the CO2RR process.
Current CO2RR demands a high CO2 partial pressure compared to nature, which converts 440 ppm CO2 with highly diluted solar energy. While direct air capture is in the pilot phase of plant testing, the general cost for concentrating CO2 from a level of a few hundred ppm to nearly 100% is unacceptably high due to the intensive energy required for the process. One option would be combining the CO2 concentrator and a converter compatible with significantly diluted CO2 sources, but resolving the issues surrounding gas impurities needs to be addressed first.
4.2. Industrially relevant productivity and durability of CO2RR
While the FE and energy efficiency for a specific product affect the operational cost of electrolysis, the current density or productivity per geometric surface area of the electrode is essential in determining the capital cost since as the productivity increases, the size of the electrolyser decreases. The current density is typically one of the matrices used to evaluate CO2RR research. A practical measure is the productivity of the specific product per specific time and the electrode geometric area.
Fig. 6a shows the reported partial current density and expected production rate per day for various products.33–126 HCOOH/HOO− has the highest value of production rate per partial current density due to its 2-electron transfer characteristics and relatively high molecular weight, followed by CO production. CO2 to ethanol or ethylene has a lower production rate per partial current density because these products require 12 electrons to be transferred to the reactant but have a similar molecular weight.
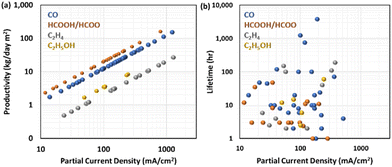 |
| Fig. 6 (a) The expected production rate per day as a function of the partial current density for each CO2RR product with the experimental data according to the literature survey. (b) Reported lifetime of CO2RR as a function of the partial current density for each CO2RR product with the experimental data according to the literature survey. | |
Significant efforts to improve the partial current density have been made in the last few years, mainly focusing on the catalyst design to increase the catalytic site density and electrochemical cell engineering to achieve gas-phase reactions to circumvent the limitations of CO2 solubility in the electrolyte. The flow or membrane electrode assembly (MEA) cell configuration with a gas diffusion electrode especially has played a central role in creating a three-phase boundary environment where CO2 can encounter the catalytic sites and ions as a counterpart for the CO2RR reaction. In addition, recent studies127 have introduced micropores or a hydrophobic environment in the catalytic layer to accumulate CO2 near the catalytic sites.
Sun et al.128 demonstrated a hierarchical nanoporous catalyst by retaining the micropores of a metal–organic framework precursor to enhance CO2 concentration in the gas-diffusion electrode, achieving 645 mA cm−2 CO partial current density at −0.53 V vs. RHE with 86% FE for CO under ambient conditions, which is equivalent to a production rate of 80 kg d−1 m−2. Chen et al.78 developed a cell with 450 mA cm−2 partial current density with 90% FE for formate with a SnO2 electrocatalyst. This corresponds to an impressive production rate of 88 kg d−1 m−2. Liao et al.129 implemented a Ni–N5–C single atom catalyst in a flow cell configuration, achieving industrial-scale performance for CO2RR to CO a FE of 97% at a current density reaching a maximum of 1.23 A cm−2 with an FE of 99.6%, the highest production rate of CO2RR to CO of 154 kg d−1 m−2 to date. The authors attributed the high performance to the Ni–N5 catalytic site, which is superior in activating CO2 molecules and reducing the energy barriers for the intermediate binding energy for boosting the kinetic activation process and catalytic activity. Endrödi et al. employed a PiperION membrane for electrocatalytic CO2 reduction to CO in a tailored zero-gap electrolyser.130 This membrane possesses high carbonate-ion conductivity, leading to a high CO current density (over 1 A cm−2) with commercial Ag nanoparticles while maintaining a high FE for CO (up to 90%).
In contrast to the recent rapid advancement of the productivity of CO2RR, industrially relevant durability has not been achieved yet. Many durability tests (Fig. 6b), including the aforementioned industrially viable production rates, are in the range of 10–100 h. There are only a few studies on CO2RR to CO that report durability test results over 1000 h long. Notably, one case44 involves a commercially available anion–exchange membrane (Sustainion) incorporated in MEAs, which illustrated at least 3800 hours of activity at 190 mA cm−2 with FE for CO2RR to CO of 95% with a silver nanoparticle cathode and an IrOx anode. The authors implemented two strategies to keep the membrane hydrated: (1) humidifying CO2 and (2) circulating deionized water or diluted KHCO3 solution in the anode.
In general, more thorough durability testing is required. So far, only ex situ and after-use characterization has been carried out for the CO2RR electrolyser. There is an urgent need to develop conditions for accelerated testing and then correlating the results between accelerated aging and actual performance.
4.3. Minimizing the purification process
Here we suggest distinguishing between two performance metrics regarding the CO2RR conversion. One is the CO2 conversion efficiency (CECO2) defined as the ratio of the amount of CO2 converted into a target to the amount of CO2 fed into the system. Another important but less discussed factor is product selectivity, defined as the fractional amount of the target product within the total stream. The former is relevant to the cost of CO2 consumption and recovery if necessary, and there are some recent studies focused on CECO2. The latter is important to determine how much energy is needed to purify the product in the following chemical process. The electrochemical cell can be divided into the cathode and anode compartments, and a path for the product stream is not always the same as the CO2 flow pathway since the CO2 can cross the membrane; CECO2 is often independent of the product selectivity.
Most CO2RR studies have been carried out in neutral and alkaline electrolytes to impede HER, in which the high current density often creates a strongly alkaline microenvironment at the cathodic interface. This consumes some CO2 in the feed through sequential chemical reactions of CO2 driven by the pH gradient in the cell.66,132,133 Specifically, an unfavourable reaction between CO2 and OH− produces carbonate or bicarbonate, which subsequently crosses the anion exchange membrane to the anode, reacts with H+ from the oxygen evolution reaction, and is converted to CO2 in the anode tail gas, giving rise to a low theoretical single pass conversion rate of 50%. Moreover, bicarbonates precipitate with alkaline metals at the cathode once their local solubility hits the limit, which closes microchannels for CO2 and ion for the CO2RR and causes a degradation mode.134 It is expected that regenerating lost CO2 demands additional energy and operating costs.
One adopted strategy for overcoming the CO2 carbonation problem is to provide CO2 regeneration space between the catalytic layer and an ion exchange membrane while maintaining the anionic micro-environment in the vicinity of the catalytic site. This methodology has been implemented by including additives in the catalyst layer or inserting an additional buffer layer.124,135,136
O'Brien et al.135 developed a permeable CO2 regeneration layer, which provides an alkaline environment at the CO2RR catalyst surface and enables local CO2 regeneration concomitantly. They coated the copper cathode layer with the functional groups of the anion exchange polymer (Aemion AP1-CNN5-00-X) to create a positive space charge, enabling the transport of anions and impeding the cations. The polymer coating on the cathode allows for CO2 transport to the catalyst via diffusion through the water-filled hydrated ionic domains in the polymer matrix. With the careful tuning of the thickness of the regeneration layer of ∼10 μm to minimize impedance to CO2 and water, they attained 85% CECO2 with a cation exchange membrane (Nafion 117) and deionized water. The authors proposed that the positively charged functional groups in the polymer structure act as a positive charge as an alternative to alkali metal cations, which can stabilize CO2RR intermediates to promote C–C coupling on copper catalysts.
Li et al.136 demonstrated that an acid-fed MEA for CO2 electroreduction to CO with an H+ to Cs+ satisfies both the FE and conversion efficiency of CO2. Essentially, an anion–exchange ionomer with quaternary ammonium side chains was incorporated into the Ag catalyst layer to shield the Ag surface from a high proton flux and provide diffusion pathways for dissolved CO2 and water. After optimizing ion concentrations and operation parameters, they observed a single-pass conversion efficiency of ∼90% and long-term stability of 50 h.
While such device and process engineering is an attractive approach, the carbonation of CO2 at a microscopic level, which seems inevitable as long as the local environment is basic, and the subsequent regeneration process across the two components raise concerns about the long-term durability of the cycle. Moreover, the use of alkaline metals raises another issue of metal precipitation.137,138 Therefore, designing a catalyst to accomplish acidic CO2RR without alkaline metals is an imperative subject for tackling both the CO2 conversion ratio and precipitation problem. One alternative is a metal-heteroatom-involved polymer catalyst, which is compatible with zero-gap CEM cells with deionized water.131 Such a configuration may contribute to increasing the CO2 conversion efficiency.
The product selectivity of CO2RR is less discussed in most CO2RR studies, though the plant process design requires the specification of the product component from the conversion unit to access the cost of the following purification. Krause et al.139 reported the product gas composition in an effort to scale up the CO2RR to CO. The ratio of CO2 in the product gas was 10–50% which significantly depends on the CO2 flow rate and current density. Since product selectivity is closely linked to operation and structural parameters, it is important to clarify both CO2 conversion efficiency and product concentration, especially when the CO2RR is scaled up.
There have been several recent approaches to engineer selectivity. Rather than a constant potential for electrosynthesis, Timoshenko and colleagues140 have used electrical pulses to tune the products. This presumably protects the catalyst from poisoning. Liu et al.141 developed pyramidal catalysts, the shape of which presumably controlled the selectivity. While such effects, such as confinement, have long been known, Zhu et al.142 used multilayer pyramids to optimize selectivity by combining geometrical effects with layer sequencing to accelerate the reaction. To reach the requisite selectivity, such synergies in the catalyst (and even electrolyser) design must be exploited.
5. Conclusions
For CO2RR to be rapidly implemented, it must be scalable and profitable, providing the means and incentive for the procedure. Scalability requires readily available catalysts, electrolytes, and devices that can safely operate with ambient CO2. On the other hand, profitability necessitates affordable and durable electrolysers that synthesize value-added products with energy efficient processes at a sufficiently high rate and purity. While nature has had billions of years to perfect photosynthesis, our first intentional use of catalysts for any type of synthesis can be traced back to just over a century ago, and our efforts on CO2RR are even more recent. Nevertheless, our knowledge has grown rapidly. This acceleration can be attributed to continued progress in experimental techniques with the advent of in operando measurements to verify the reaction mechanisms, the understanding and development of quantum chemistry to provide the theoretical framework, and now the use of artificial intelligence to examine trends to fill the gaps between experimental results and computational predictions in this multi-dimensional space. Discovery has been advanced by high throughput investigations, yet the promise of CO2RR has yet to be realized on an industrial scale especially with perhaps the most important outstanding issues – purity and durability. Given the progress that humanity has made in the exceedingly short time spent investigating viable CO2RR, in comparison to the eons nature has had to perfect the process, it is not a question of if we succeed in its realization but when.
Author contributions
Naohiro Fujinuma: Writing – original draft, writing – review & editing; Samuel Lofland: Conceptualization, writing – review & editing, funding acquisition.
Conflicts of interest
There are no conflicts to declare.
Acknowledgements
SEL acknowledges support from Sekisui Chemical Ltd.
References
- P. S. Adam, G. Borrel and S. Gribaldo, Evolutionary history of carbon monoxide dehydrogenase/acetyl-CoA synthase, one of the oldest enzymatic complexes, Proc. Natl. Acad. Sci. U. S. A., 2018, 115, E1166–E1173 CrossRef CAS PubMed.
- D. C. Harris, Charles David keeling and the story of atmospheric CO2 measurements, Anal. Chem., 2010, 82, 7865–7870 CrossRef CAS PubMed.
- J. Giner, Electrochemical reduction of CO2 on platinum electrodes in acid solutions, Electrochim. Acta, 1963, 8, 857–865 CrossRef CAS.
- T. E. Teeter and P. Van Rysselberghe, Reduction of Carbon Dioxide on Mercury Cathodes, J. Chem. Phys., 1954, 22, 759–760 CrossRef CAS.
- H. Noda, S. Ikeda, Y. Oda, K. Imai, M. Maeda and K. Ito, Electrochemical Reduction of Carbon Dioxide at Various Metal Electrodes in Aqueous Potassium Hydrogen Carbonate Solution, Bull. Chem. Soc. Jpn., 1990, 63, 2459–2462 CrossRef CAS.
- N. Furuya and K. Matsui, Electroreduction of carbon dioxide on gas-diffusion electrodes modified by metal phthalocyanines, J. Electroanal. Chem. Interfacial Electrochem., 1989, 271, 181–191 CrossRef CAS.
- Y. Hori, Electrochemical CO2 Reduction on Metal Electrodes, Mod. Aspects Electrochem., 2008, 89–189 CAS.
- S. Nitopi, E. Bertheussen, S. B. Scott, X. Liu, A. K. Engstfeld, S. Horch, B. Seger, I. E. L. Stephens and K. Chan,
et al., Progress and Perspectives of Electrochemical CO2 Reduction on Copper in Aqueous Electrolyte, Chem. Rev., 2019, 119, 7610–7672 CrossRef CAS PubMed.
- M. Dunwell, W. Luc, Y. Yan, F. Jiao and B. Xu, Understanding Surface-Mediated Electrochemical Reactions: CO2 Reduction and beyond, ACS Catal., 2018, 8, 8121–8129 CrossRef CAS.
- S. Vijay, W. Ju, S. Brückner, S. C. Tsang, P. Strasser and K. Chan, Unified mechanistic understanding of CO2 reduction to CO on transition metal and single atom catalysts, Nat. Catal., 2021, 4, 1024–1031 CrossRef CAS.
- J. A. Gauthier, M. Fields, M. Bajdich, L. D. Chen, R. B. Sandberg, K. Chan and J. K. Nørskov, Facile Electron Transfer to CO2 during Adsorption at the Metal|Solution Interface, J. Phys. Chem. C, 2019, 123, 29278–29283 CrossRef CAS.
- Y. Y. Birdja, E. Pérez-Gallent, M. C. Figueiredo, A. J. Göttle, F. Calle-Vallejo and M. T. M. Koper, Advances and challenges in understanding the electrocatalytic conversion of carbon dioxide to fuels, Nat. Energy, 2019, 4, 732–745 CrossRef CAS.
- J. S. Yoo, R. Christensen, T. Vegge, J. K. Nørskov and F. Studt, Theoretical Insight into the Trends that Guide the Electrochemical Reduction of Carbon Dioxide to Formic Acid, ChemSusChem, 2016, 9, 358–363 CrossRef CAS PubMed.
- B. Zhang, Y. Chang, Y. Wu, Z. Fan, P. Zhai, C. Wang, J. Gao, L. Sun and J. Hou, Regulating *OCHO Intermediate as Rate-Determining Step of Defective Oxynitride Nanosheets Enabling Robust CO2 Electroreduction, Adv. Energy Mater., 2022, 12, 2200321 CrossRef CAS.
- J. Chen, B. Ma, Z. Xie, W. Li, Y. Yang, M. Mu, X. Zou, B. Zhao and W. Song, Bifunctional porous SnO2/Ag nanofibers for efficient electroreduction of carbon dioxide to formate and its mechanism elucidation by in situ surface-enhanced Raman scattering, Appl. Catal., B, 2023, 325, 122350 CrossRef CAS.
- S. Verma, S. Lu and P. J. A. Kenis, Co-electrolysis of CO2 and glycerol as a pathway to carbon chemicals with improved technoeconomics due to low electricity consumption, Nat. Energy, 2019, 4, 466–474 CrossRef CAS.
- C. Han, Y. H. Li, J. Y. Li, M. Y. Qi, Z. R. Tang and Y. J. Xu, Cooperative Syngas Production and C–N Bond Formation in One Photoredox Cycle, Angew.
Chem., Int. Ed., 2021, 60, 7962–7970 CrossRef CAS PubMed.
- L. Yuan, M. Y. Qi, Z. R. Tang and Y. J. Xu, Coupling Strategy for CO2 Valorization Integrated with Organic Synthesis by Heterogeneous Photocatalysis, Angew. Chem., Int. Ed., 2021, 60, 21150–21172 CrossRef CAS PubMed.
- SunShot 2030 | Department of Energy, < https://www.energy.gov/eere/solar/sunshot-2030> (31 July 2023).
- A. Raksajati, M. T. Ho and D. E. Wiley, Reducing the cost of CO2 capture from flue gases using aqueous chemical absorption, Ind. Eng. Chem. Res., 2013, 52, 16887–16901 CrossRef CAS.
- J. B. Greenblatt, D. J. Miller, J. W. Ager, F. A. Houle and I. D. Sharp, The Technical and Energetic Challenges of Separating (Photo)Electrochemical Carbon Dioxide Reduction Products, Joule, 2018, 2, 381–420 CrossRef CAS.
- M. Jouny, W. Luc and F. Jiao, General Techno-Economic Analysis of CO2 Electrolysis Systems, Ind. Eng. Chem. Res., 2018, 57, 2165–2177 CrossRef CAS.
- S. Verma, B. Kim, H. R. M. Jhong, S. Ma and P. J. A. Kenis, A Gross-Margin Model for Defining Technoeconomic Benchmarks in the Electroreduction of CO2, ChemSusChem, 2016, 9, 1972–1979 CrossRef CAS PubMed.
- P. De Luna, C. Hahn, D. Higgins, S. A. Jaffer, T. F. Jaramillo and E. H. Sargent, What would it take for renewably powered electrosynthesis to displace petrochemical processes?, Science, 2019, 364, eaav3506 CrossRef CAS PubMed.
- J. M. Spurgeon and B. Kumar, A comparative technoeconomic analysis of pathways for commercial electrochemical CO2 reduction to liquid products, Energy Environ. Sci., 2018, 11, 1536–1551 RSC.
- G. Z. Kyriacou and A. K. Anagnostopoulos, Influence CO2 partial pressure and the supporting electrolyte cation on the product distribution in CO2 electroreduction, J. Appl. Electrochem., 1993, 23, 483–486 CrossRef CAS.
- N. Hidetomo, I. Shoichiro, Y. Akio, E. Hisahiko and I. Kaname, Kinetics of Electrochemical Reduction of Carbon Dioxide on a Gold Electrode in Phosphate Buffer Solutions, Bull. Chem. Soc. Jpn., 2006, 68, 1889–1895 Search PubMed.
- S. Komatsu, M. Tanaka, A. Okumura and A. Kungi, Preparation of cu-solid polymer electrolyte composite electrodes and application to gas-phase electrochemical reduction of CO2, Electrochim. Acta, 1995, 40, 745–753 CrossRef CAS.
- B. Kim, S. Ma, H. R. Molly Jhong and P. J. A. Kenis, Influence of dilute feed and pH on electrochemical reduction of CO2 to CO on Ag in a continuous flow electrolyzer, Electrochim. Acta, 2015, 166, 271–276 CrossRef CAS.
- Y. Xu, J. P. Edwards, J. Zhong, C. P. O'Brien, C. M. Gabardo, C. McCallum, J. Li, C. T. Dinh and E. H. Sargent,
et al., Oxygen-tolerant electroproduction of C2 products from simulated flue gas, Energy Environ. Sci., 2020, 13, 554–561 RSC.
- T. Arai, S. Sato and T. Morikawa, A monolithic device for CO2 photoreduction to generate liquid organic substances in a single-compartment reactor, Energy Environ. Sci., 2015, 8, 1998–2002 RSC.
- X. Lu, Z. Jiang, X. Yuan, Y. Wu, R. Malpass-Evans, Y. Zhong, Y. Liang, N. B. McKeown and H. Wang, A bio-inspired O2-tolerant catalytic CO2 reduction electrode, Sci. Bull., 2019, 64, 1890–1895 CrossRef CAS PubMed.
- L. Liao, R. An, H. Li, Y. Xu, J. J. Wu and X. Zhao, Catalytic Access to Functionalized Allylic gem-Difluorides via Fluorinative Meyer–Schuster-Like Rearrangement, Angew. Chem., Int. Ed., 2020, 59, 11010–11019 CrossRef CAS PubMed.
- 8.7. Nitrogen Oxides (NOx) Emissions | netl.doe.gov, < https://www.netl.doe.gov/research/Coal/energy-systems/gasification/gasifipedia/nitrogen-oxides> (31 July 2023).
- B. H. Ko, B. Hasa, H. Shin, E. Jeng, S. Overa, W. Chen and F. Jiao, The impact of nitrogen oxides on electrochemical carbon dioxide reduction, Nat. Commun., 2020, 11, 1–9 CrossRef PubMed.
- B. U. Choi, Y. C. Tan, H. Song, K. B. Lee and J. Oh, System Design Considerations for Enhancing Electroproduction of Formate from Simulated Flue Gas, ACS Sustainable Chem. Eng., 2021, 9, 2348–2357 CrossRef CAS.
- Y. Zhai, L. Chiachiarelli and N. Sridhar, Effect of Gaseous Impurities on the Electrochemical Reduction of CO2 on Copper Electrodes, ECS Trans., 2009, 19, 1–13 CrossRef CAS.
- D. Kopljar, N. Wagner and E. Klemm, Transferring Electrochemical CO2 Reduction from Semi-Batch into Continuous Operation Mode Using Gas Diffusion Electrodes, Chem. Eng. Technol., 2016, 39, 2042–2050 CrossRef CAS.
- H. Yang, J. J. Kaczur, S. D. Sajjad and R. I. Masel, Electrochemical conversion of CO2 to formic acid utilizing Sustainion™ membranes, J. CO2 Util., 2017, 20, 208–217 CrossRef CAS.
- X. Lu, D. Y. C. Leung, H. Wang and J. Xuan, A high performance dual electrolyte microfluidic reactor for the utilization of CO2, Appl. Energy, 2017, 194, 549–559 CrossRef CAS.
- S. Ma, M. Sadakiyo, R. Luo, M. Heima, M. Yamauchi and P. J. A. Kenis, One-step electrosynthesis of ethylene and ethanol from CO2 in an alkaline electrolyzer, J. Power Sources, 2016, 301, 219–228 CrossRef CAS.
- C. Reller, R. Krause, E. Volkova, B. Schmid, S. Neubauer, A. Rucki, M. Schuster and G. Schmid, Selective Electroreduction of CO2 toward Ethylene on Nano Dendritic Copper Catalysts at High Current Density, Adv. Energy Mater., 2017, 7, 1602114 CrossRef.
- C. T. Dinh, T. Burdyny, G. Kibria, A. Seifitokaldani, C. M. Gabardo, F. Pelayo García De Arquer, A. Kiani, J. P. Edwards and P. De Luna,
et al., CO2 electroreduction to ethylene via hydroxide-mediated copper catalysis at an abrupt interface, Science, 2018, 360, 783–787 CrossRef CAS PubMed.
- Z. Liu, H. Yang, R. Kutz and R. I. Masel, CO2 Electrolysis to CO and O2 at High Selectivity, Stability and Efficiency Using Sustainion Membranes, J. Electrochem. Soc., 2018, 165, J3371–J3377 CrossRef CAS.
- J. J. Kaczur, H. Yang, Z. Liu, S. D. Sajjad and R. I. Masel, Carbon dioxide and water electrolysis using new alkaline stable anion membranes, Front. Chem., 2018, 6, 377597 Search PubMed.
- T. Haas, R. Krause, R. Weber, M. Demler and G. Schmid, Technical photosynthesis involving CO2 electrolysis and fermentation, Nat. Catal., 2018, 1, 32–39 CrossRef CAS.
- S. Verma, Y. Hamasaki, C. Kim, W. Huang, S. Lu, H. R. M. Jhong, A. A. Gewirth, T. Fujigaya and N. Nakashima,
et al., Insights into the Low Overpotential Electroreduction of CO2 to CO on a Supported Gold Catalyst in an Alkaline Flow Electrolyzer, ACS Energy Lett., 2018, 3, 193–198 CrossRef CAS.
- C. M. Gabardo, A. Seifitokaldani, J. P. Edwards, C. T. Dinh, T. Burdyny, M. G. Kibria, C. P. O'Brien, E. H. Sargent and D. Sinton, Combined high alkalinity and pressurization enable efficient CO2 electroreduction to CO, Energy Environ. Sci., 2018, 11, 2531–2539 RSC.
- K. Jiang, S. Siahrostami, T. Zheng, Y. Hu, S. Hwang, E. Stavitski, Y. Peng, J. Dynes and M. Gangisetty,
et al., Isolated Ni single atoms in graphene nanosheets for high-performance CO2 reduction, Energy Environ. Sci., 2018, 11, 893–903 RSC.
- X. Lu, Y. Wu, X. Yuan, L. Huang, Z. Wu, J. Xuan, Y. Wang and H. Wang, High-Performance Electrochemical CO2 Reduction Cells Based on Non-noble Metal Catalysts, ACS Energy Lett., 2018, 3, 2527–2532 CrossRef CAS.
- B. Endrödi, E. Kecsenovity, A. Samu, F. Darvas, R. V. Jones, V. Török, A. Danyi and C. Janáky, Multilayer Electrolyzer Stack Converts Carbon Dioxide to Gas Products at High Pressure with High Efficiency, ACS Energy Lett., 2019, 4, 1770–1777 CrossRef PubMed.
- D. A. Salvatore, D. M. Weekes, J. He, K. E. Dettelbach, Y. C. Li, T. E. Mallouk and C. P. Berlinguette, Electrolysis of Gaseous CO2 to CO in a Flow Cell with a Bipolar Membrane, ACS Energy Lett., 2018, 3, 149–154 CrossRef CAS.
- P. Jeanty, C. Scherer, E. Magori, K. Wiesner-Fleischer, O. Hinrichsen and M. Fleischer, Upscaling and continuous operation of electrochemical CO2 to CO conversion in aqueous solutions on silver gas diffusion electrodes, J. CO2 Util., 2018, 24, 454–462 CrossRef CAS.
- P. De Luna, R. Quintero-Bermudez, C. T. DInh, M. B. Ross, O. S. Bushuyev, P. Todorović, T. Regier, S. O. Kelley and P. Yang,
et al., Catalyst electro-redeposition controls morphology and oxidation state for selective carbon dioxide reduction, Nat. Catal., 2018, 1, 103–110 CrossRef CAS.
- T. T. Zhuang, Z. Q. Liang, A. Seifitokaldani, Y. Li, P. De Luna, T. Burdyny, F. Che, F. Meng and Y. Min,
et al., Steering post-C–C coupling selectivity enables high efficiency electroreduction of carbon dioxide to multi-carbon alcohols, Nat. Catal., 2018, 1, 421–428 CrossRef CAS.
- M. Luo, Z. Wang, Y. C. Li, J. Li, F. Li, Y. Lum, D. H. Nam, B. Chen and J. Wicks,
et al., Hydroxide promotes carbon dioxide electroreduction to ethanol on copper via tuning of adsorbed hydrogen, Nat. Commun., 2019, 10, 1–7 CrossRef PubMed.
- F. Li, Y. C. Li, Z. Wang, J. Li, D. H. Nam, Y. Lum, M. Luo, X. Wang and A. Ozden,
et al., Cooperative CO2-to-ethanol conversion via enriched intermediates at molecule–metal catalyst interfaces, Nat. Catal., 2019, 3, 75–82 CrossRef.
- F. P. García de Arquer, C. T. Dinh, A. Ozden, J. Wicks, C. McCallum, A. R. Kirmani, D. H. Nam, C. Gabardo and A. Seifitokaldani,
et al., CO2 electrolysis to multicarbon products at activities greater than 1 A cm−2, Science, 2020, 367, 661–666 CrossRef PubMed.
- X. Wang, Z. Wang, F. P. García de Arquer, C. T. Dinh, A. Ozden, Y. C. Li, D. H. Nam, J. Li and Y. S. Liu,
et al., Efficient electrically powered CO2-to-ethanol via suppression of deoxygenation, Nat. Energy, 2020, 5, 478–486 CrossRef CAS.
- X. Wang, A. Xu, F. Li, S. F. Hung, D. H. Nam, C. M. Gabardo, Z. Wang, Y. Xu and A. Ozden,
et al., Efficient Methane Electrosynthesis Enabled by Tuning Local CO2 Availability, J. Am. Chem. Soc., 2020, 142, 3525–3531 CrossRef CAS PubMed.
- Z. Yin, H. Peng, X. Wei, H. Zhou, J. Gong, M. Huai, L. Xiao, G. Wang and J. Lu,
et al., An alkaline polymer electrolyte CO2 electrolyzer operated with pure water, Energy Environ. Sci., 2019, 12, 2455–2462 RSC.
- W. Lee, Y. E. Kim, M. H. Youn, S. K. Jeong and K. T. Park, Catholyte-Free Electrocatalytic CO2 Reduction to Formate, Angew. Chem., Int. Ed., 2018, 57, 6883–6887 CrossRef CAS PubMed.
- J. Lee, J. Lim, C. W. Roh, H. S. Whang and H. Lee, Electrochemical CO2 reduction using alkaline membrane electrode assembly on various metal electrodes, J. CO2 Util., 2019, 31, 244–250 CrossRef CAS.
- R. Xia, S. Zhang, X. Ma and F. Jiao, Surface-functionalized palladium catalysts for electrochemical CO2 reduction, J. Mater. Chem. A, 2020, 8, 15884–15890 RSC.
- Q. Gong, P. Ding, M. Xu, X. Zhu, M. Wang, J. Deng, Q. Ma, N. Han and Y. Zhu,
et al., Structural defects on converted bismuth oxide nanotubes enable highly active electrocatalysis of carbon dioxide reduction, Nat. Commun., 2019, 10, 1–10 CrossRef CAS PubMed.
- G. O. Larrazábal, P. Strøm-Hansen, J. P. Heli, K. Zeiter, K. T. Therkildsen, I. Chorkendorff and B. Seger, Analysis of Mass Flows and Membrane Cross-over in CO2 Reduction at High Current Densities in an MEA-Type Electrolyzer, ACS Appl. Mater. Interfaces, 2019, 11, 41281–41288 CrossRef PubMed.
- T. Möller, W. Ju, A. Bagger, X. Wang, F. Luo, T. Ngo Thanh, A. S. Varela, J. Rossmeisl and P. Strasser, Efficient CO2 to CO electrolysis on solid Ni–N–C catalysts at industrial current densities, Energy Environ. Sci., 2019, 12, 640–647 RSC.
- T. Zheng, K. Jiang, N. Ta, Y. Hu, J. Zeng, J. Liu and H. Wang, Large-Scale and Highly Selective CO2 Electrocatalytic Reduction on Nickel Single-Atom Catalyst, Joule, 2019, 3, 265–278 CrossRef CAS.
- S. Ren, D. Joulié, D. Salvatore, K. Torbensen, M. Wang, M. Robert and C. P. Berlinguette, Molecular electrocatalysts can mediate fast, selective CO2 reduction in a flow cell, Science, 2019, 365, 367–369 CrossRef CAS PubMed.
- W. H. Cheng, M. H. Richter, I. Sullivan, D. M. Larson, C. Xiang, B. S. Brunschwig and H. A. Atwater, CO2 Reduction to CO with 19% Efficiency in a Solar-Driven Gas Diffusion Electrode Flow Cell under Outdoor Solar Illumination, ACS Energy Lett., 2020, 470–476 CrossRef CAS.
- J. P. Edwards, Y. Xu, C. M. Gabardo, C. T. Dinh, J. Li, Z. B. Qi, A. Ozden, E. H. Sargent and D. Sinton, Efficient electrocatalytic conversion of carbon dioxide in a low-resistance pressurized alkaline electrolyzer, Appl. Energy, 2020, 261, 114305 CrossRef CAS.
- J. Chen, Z. Wang, H. Lee, J. Mao, C. A. Grimes, C. Liu, M. Zhang, Z. Lu and Y. Chen,
et al., Efficient electroreduction of CO2 to CO by Ag-decorated S-doped g-C3N4/CNT nanocomposites at industrial scale current density, Mater. Today Phys., 2020, 12, 100176 CrossRef.
- T. Li, E. W. Lees, M. Goldman, D. A. Salvatore, D. M. Weekes and C. P. Berlinguette, Electrolytic Conversion of Bicarbonate into CO in a Flow Cell, Joule, 2019, 3, 1487–1497 CrossRef CAS.
- Y. C. Li, G. Lee, T. Yuan, Y. Wang, D. H. Nam, Z. Wang, F. P. Garciá De Arquer, Y. Lum and C. T. Dinh,
et al., CO2 Electroreduction from Carbonate Electrolyte, ACS Energy Lett., 2019, 4, 1427–1431 CrossRef CAS.
- C. Xia, P. Zhu, Q. Jiang, Y. Pan, W. Liang, E. Stavitsk, H. N. Alshareef and H. Wang, Continuous production of pure liquid fuel solutions via electrocatalytic CO2 reduction using solid-electrolyte devices, Nat. Energy, 2019, 4, 776–785 CrossRef CAS.
- T. Shinagawa, G. O. Larrazábal, A. J. Martín, F. Krumeich and J. Pérez-Ramírez, Sulfur-Modified Copper Catalysts for the Electrochemical Reduction of Carbon Dioxide to Formate, ACS Catal., 2018, 8, 837–844 CrossRef CAS.
- S. Sen, S. M. Brown, M. L. Leonard and F. R. Brushett, Electroreduction of carbon dioxide to formate at high current densities using tin and tin oxide gas diffusion electrodes, J. Appl. Electrochem., 2019, 49, 917–928 CrossRef CAS.
- Y. Chen, A. Vise, W. E. Klein, F. C. Cetinbas, D. J. Myers, W. A. Smith, W. A. Smith, W. A. Smith and T. G. Deutsch,
et al., A Robust, Scalable Platform for the Electrochemical Conversion of CO2 to Formate: Identifying Pathways to Higher Energy Efficiencies, ACS Energy Lett., 2020, 5, 1825–1833 CrossRef CAS.
- J. J. Lv, M. Jouny, W. Luc, W. Zhu, J. J. Zhu and F. Jiao, A Highly Porous Copper Electrocatalyst for Carbon Dioxide Reduction, Adv. Mater., 2018, 30, 1803111 CrossRef PubMed.
- F. Li, A. Thevenon, A. Rosas-Hernández, Z. Wang, Y. Li, C. M. Gabardo, A. Ozden, C. T. Dinh and J. Li,
et al., Molecular tuning of CO2-to-ethylene conversion, Nature, 2020, 577, 509–513 CrossRef CAS PubMed.
- W. Ma, S. Xie, T. Liu, Q. Fan, J. Ye, F. Sun, Z. Jiang, Q. Zhang and J. Cheng,
et al., Electrocatalytic reduction of CO2 to ethylene and ethanol through hydrogen-assisted C–C coupling over fluorine-modified copper, Nat. Catal., 2020, 3, 478–487 CrossRef CAS.
- M. Zhong, K. Tran, Y. Min, C. Wang, Z. Wang, C. T. Dinh, P. De Luna, Z. Yu and A. S. Rasouli,
et al., Accelerated discovery of CO2 electrocatalysts using active machine learning, Nature, 2020, 581, 178–183 CrossRef CAS PubMed.
- C. M. Gabardo, C. P. O'Brien, J. P. Edwards, C. McCallum, Y. Xu, C. T. Dinh, J. Li, E. H. Sargent and D. Sinton, Continuous Carbon Dioxide Electroreduction to Concentrated Multi-carbon Products Using a Membrane Electrode Assembly, Joule, 2019, 3, 2777–2791 CrossRef CAS.
- N. Martić, C. Reller, C. Macauley, M. Löffler, B. Schmid, D. Reinisch, E. Volkova, A. Maltenberger and A. Rucki,
et al., Paramelaconite-Enriched Copper-Based Material as an Efficient and Robust Catalyst for Electrochemical Carbon Dioxide Reduction, Adv. Energy Mater., 2019, 9, 1901228 CrossRef.
- R. Wang, H. Haspel, A. Pustovarenko, A. Dikhtiarenko, A. Russkikh, G. Shterk, D. Osadchii, S. Ould-Chikh and M. Ma,
et al., Maximizing Ag Utilization in High-Rate CO2 Electrochemical Reduction with a Coordination Polymer-Mediated Gas Diffusion Electrode, ACS Energy Lett., 2019, 4, 2024–2031 CrossRef CAS.
- S. Ma, R. Luo, J. I. Gold, A. Z. Yu, B. Kim and P. J. A. Kenis, Carbon nanotube containing Ag catalyst layers for efficient and selective reduction of carbon dioxide, J. Mater. Chem. A, 2016, 4, 8573–8578 RSC.
- W. Zhu, S. Kattel, F. Jiao and J. G. Chen, Shape-Controlled CO2 Electrochemical Reduction on Nanosized Pd Hydride Cubes and Octahedra, Adv. Energy Mater., 2019, 9, 1802840 CrossRef.
- H. R. Molly Jhong, C. E. Tornow, C. Kim, S. Verma, J. L. Oberst, P. S. Anderson, A. A. Gewirth, T. Fujigaya and N. Nakashima,
et al., Gold Nanoparticles on Polymer-Wrapped Carbon Nanotubes: An Efficient and Selective Catalyst for the Electroreduction of CO2, ChemPhysChem, 2017, 18, 3274–3279 CrossRef PubMed.
- L. Ma, W. Hu, Q. Pan, L. Zou, Z. Zou, K. Wen and H. Yang, Polyvinyl alcohol-modified gold nanoparticles with record-high activity for electrochemical reduction of CO2 to CO, J. CO2 Util., 2019, 34, 108–114 CrossRef CAS.
- S. Ma, Y. Lan, G. M. J. Perez, S. Moniri and P. J. A. Kenis, Silver Supported on Titania as an Active Catalyst for Electrochemical Carbon Dioxide Reduction, ChemSusChem, 2014, 7, 866–874 CrossRef CAS PubMed.
- Q. Zhu, D. Yang, H. Liu, X. Sun, C. Chen, J. Bi, J. Liu, H. Wu and B. Han, Hollow Metal–Organic-Framework-Mediated In Situ Architecture of Copper Dendrites for Enhanced CO2 Electroreduction, Angew. Chem., Int. Ed., 2020, 59, 8896–8901 CrossRef CAS PubMed.
- F. Yang, P. L. Deng, Q. Wang, J. Zhu, Y. Yan, L. Zhou, K. Qi, H. Liu and H. S. Park,
et al., Metal–organic framework-derived cupric oxide polycrystalline nanowires for selective carbon dioxide electroreduction to C2 valuables, J. Mater. Chem. A, 2020, 8, 12418–12423 RSC.
- K. Yao, Y. Xia, J. Li, N. Wang, J. Han, C. Gao, M. Han, G. Shen and Y. Liu,
et al., Metal–organic framework derived copper catalysts for CO2 to ethylene conversion, J. Mater. Chem. A, 2020, 8, 11117–11123 RSC.
- Y. Wang, H. Shen, K. J. T. Livi, D. Raciti, H. Zong, J. Gregg, M. Onadeko, Y. Wan and A. Watson,
et al., Copper Nanocubes for CO2 Reduction in Gas Diffusion Electrodes, Nano Lett., 2019, 8461–8468 CrossRef CAS PubMed.
- W. Ju, F. Jiang, H. Ma, Z. Pan, Y. B. Zhao, F. Pagani, D. Rentsch, J. Wang and C. Battaglia, Electrocatalytic Reduction of Gaseous CO2 to CO on Sn/Cu-Nanofiber-Based Gas Diffusion Electrodes, Adv. Energy Mater., 2019, 9, 1901514 CrossRef.
- H. Xiang, S. Rasul, B. Hou, J. Portoles, P. Cumpson and E. H. Yu, Copper-Indium Binary Catalyst on a Gas Diffusion Electrode for High-Performance CO2 Electrochemical Reduction with Record CO Production Efficiency, ACS Appl. Mater. Interfaces, 2020, 12, 601–608 CrossRef CAS PubMed.
- K. Ye, Z. Zhou, J. Shao, L. Lin, D. Gao, N. Ta, R. Si, G. Wang and X. Bao, In Situ Reconstruction of a Hierarchical Sn-Cu/SnOx Core/Shell Catalyst for High-Performance CO2 Electroreduction, Angew. Chem., Int. Ed., 2020, 59, 4814–4821 CrossRef CAS PubMed.
- Y. C. Li, Z. Wang, T. Yuan, D. H. Nam, M. Luo, J. Wicks, B. Chen, J. Li and F. Li,
et al., Binding Site Diversity Promotes CO2 Electroreduction to Ethanol, J. Am. Chem. Soc., 2019, 141, 8584–8591 CrossRef CAS PubMed.
- J. C. Lee, J. Y. Kim, W. H. Joo, D. Hong, S. H. Oh, B. Kim, G. Do Lee, M. Kim and J. Oh,
et al., Thermodynamically driven self-formation of copper-embedded nitrogen-doped carbon nanofiber catalysts for a cascade electroreduction of carbon dioxide to ethylene, J. Mater. Chem. A, 2020, 8, 11632–11641 RSC.
- C. Chen, X. Yan, Y. Wu, S. Liu, X. Zhang, X. Sun, Q. Zhu, H. Wu and B. Han, Boosting the Productivity of Electrochemical CO2 Reduction to Multi-Carbon Products by Enhancing CO2 Diffusion through a Porous Organic Cage, Angew. Chem., Int. Ed., 2022, 61, e202202607 CrossRef CAS PubMed.
- C. Chen, X. Yan, S. Liu, Y. Wu, Q. Wan, X. Sun, Q. Zhu, H. Liu and J. Ma,
et al., Highly Efficient Electroreduction of CO2 to C2+ Alcohols on Heterogeneous Dual Active Sites, Angew. Chem., Int. Ed., 2020, 59, 16459–16464 CrossRef CAS PubMed.
- C. Yang, H. Shen, A. Guan, J. Liu, T. Li, Y. Ji, A. M. Al-Enizi, L. Zhang and L. Qian,
et al., Fast cooling induced grain-boundary-rich copper oxide for electrocatalytic carbon dioxide reduction to ethanol, J. Colloid Interface Sci., 2020, 570, 375–381 CrossRef CAS PubMed.
- W. Luo, J. Zhang, M. Li and A. Züttel, Boosting CO Production in Electrocatalytic CO2 Reduction on Highly Porous Zn Catalysts, ACS Catal., 2019, 9, 3783–3791 CrossRef CAS.
- F. Y. Gao, S. J. Hu, X. L. Zhang, Y. R. Zheng, H. J. Wang, Z. Z. Niu, P. P. Yang, R. C. Bao and T. Ma,
et al., High-Curvature Transition-Metal Chalcogenide Nanostructures with a Pronounced Proximity Effect Enable Fast and Selective CO2 Electroreduction, Angew. Chem., Int. Ed., 2020, 59, 8706–8712 CrossRef CAS PubMed.
- A. Löwe, C. Rieg, T. Hierlemann, N. Salas, D. Kopljar, N. Wagner and E. Klemm, Influence of Temperature on the Performance of Gas Diffusion Electrodes in the CO2 Reduction Reaction, ChemElectroChem, 2019, 6, 4497–4506 CrossRef.
- H. Xiang, H. A. Miller, M. Bellini, H. Christensen, K. Scott, S. Rasul and E. H. Yu, Production of formate by CO2 electrochemical reduction and its application in energy storage, Sustainable Energy Fuels, 2019, 4, 277–284 RSC.
- J. Wang, J. Zou, X. Hu, S. Ning, X. Wang, X. Kang and S. Chen, Heterostructured intermetallic CuSn catalysts: high performance towards the electrochemical reduction of CO2 to formate, J. Mater. Chem. A, 2019, 7, 27514–27521 RSC.
- G. Díaz-Sainz, M. Alvarez-Guerra, J. Solla-Gullón, L. García-Cruz, V. Montiel and A. Irabien, CO2 electroreduction to formate: Continuous single-pass operation in a filter-press reactor at high current densities using Bi gas diffusion electrodes, J. CO2 Util., 2019, 34, 12–19 CrossRef.
- P. Deng, F. Yang, Z. Wang, S. Chen, Y. Zhou, S. Zaman and B. Y. Xia, Metal–Organic Framework-Derived Carbon Nanorods Encapsulating Bismuth Oxides for Rapid and Selective CO2 Electroreduction to Formate, Angew. Chem., Int. Ed., 2020, 59, 10807–10813 CrossRef CAS PubMed.
- J. Yang, X. Wang, Y. Qu, X. Wang, H. Huo, Q. Fan, J. Wang, L. M. Yang and Y. Wu, Bi-Based Metal-Organic Framework Derived Leafy Bismuth Nanosheets for Carbon Dioxide Electroreduction, Adv. Energy Mater., 2020, 10, 2001709 CrossRef CAS.
- C. Cao, D. D. Ma, J. F. Gu, X. Xie, G. Zeng, X. Li, S. G. Han, Q. L. Zhu and X. T. Wu,
et al., Metal-Organic Layers Leading to Atomically Thin Bismuthene for Efficient Carbon Dioxide Electroreduction to Liquid Fuel, Angew. Chem., Int. Ed., 2020, 59, 15014–15020 CrossRef CAS PubMed.
- H. Yang, Y. Wu, Q. Lin, L. Fan, X. Chai, Q. Zhang, J. Liu, C. He and Z. Lin, Composition Tailoring via N and S Co-doping and Structure Tuning by Constructing Hierarchical Pores: Metal-Free Catalysts for High-Performance Electrochemical Reduction of CO2, Angew. Chem., Int. Ed., 2018, 57, 15476–15480 CrossRef CAS PubMed.
- C. Chen, X. Sun, X. Yan, Y. Wu, H. Liu, Q. Zhu, B. B. A. Bediako and B. Han, Boosting CO2 Electroreduction on N,P-Co-doped Carbon Aerogels, Angew. Chem., Int. Ed., 2020, 59, 11123–11129 CrossRef CAS PubMed.
- H. Yang, Q. Lin, C. Zhang, X. Yu, Z. Cheng, G. Li, Q. Hu, X. Ren and Q. Zhang,
et al., Carbon dioxide electroreduction on single-atom nickel decorated carbon membranes with industry compatible current densities, Nat. Commun., 2020, 11, 1–8 CrossRef PubMed.
- H. Yang, Q. Lin, Y. Wu, G. Li, Q. Hu, X. Chai, X. Ren, Q. Zhang and J. Liu,
et al., Highly efficient utilization of single atoms via constructing 3D and free-standing electrodes for CO2 reduction with ultrahigh current density, Nano Energy, 2020, 70, 104454 CrossRef CAS.
- J. Gu, C. S. Hsu, L. Bai, H. M. Chen and X. Hu, Atomically dispersed Fe3+ sites catalyze efficient CO2 electroreduction to CO, Science, 2019, 364, 1091–1094 CrossRef CAS PubMed.
- H. Y. Jeong, M. Balamurugan, V. S. K. Choutipalli, E. S. Jeong, V. Subramanian, U. Sim and K. T. Nam, Achieving highly efficient CO2 to CO electroreduction exceeding 300 mA cm−2 with single-atom nickel electrocatalysts, J. Mater. Chem. A, 2019, 7, 10651–10661 RSC.
- Y. Wang, Z. Jiang, X. Zhang, Z. Niu, Q. Zhou, X. Wang, H. Li, Z. Lin and H. Zheng,
et al., Metal Phthalocyanine-Derived Single-Atom Catalysts for Selective CO2 Electroreduction under High Current Densities, ACS Appl. Mater. Interfaces, 2020, 12, 33795–33802 CrossRef CAS PubMed.
- X. Zhang, Y. Wang, M. Gu, M. Wang, Z. Zhang, W. Pan, Z. Jiang, H. Zheng and M. Lucero,
et al., Molecular engineering of dispersed nickel phthalocyanines on carbon nanotubes for selective CO2 reduction, Nat. Energy, 2020, 5, 684–692 CrossRef CAS.
- C. F. Wen, F. Mao, Y. Liu, X. Y. Zhang, H. Q. Fu, L. R. Zheng, P. F. Liu and H. G. Yang, Nitrogen-Stabilized Low-Valent Ni Motifs for Efficient CO2 Electrocatalysis, ACS Catal., 2020, 10, 1086–1093 CrossRef CAS.
- M. Wang, K. Torbensen, D. Salvatore, S. Ren, D. Joulié, F. Dumoulin, D. Mendoza, B. Lassalle-Kaiser and U. Işci,
et al., CO2 electrochemical catalytic reduction with a highly active cobalt phthalocyanine, Nat. Commun., 2019, 10, 1–8 CrossRef PubMed.
- K. Chen, M. Cao, Y. Lin, J. Fu, H. Liao, Y. Zhou, H. Li, X. Qiu and J. Hu,
et al., Ligand Engineering in Nickel Phthalocyanine to Boost the Electrocatalytic Reduction of CO2, Adv. Funct. Mater., 2022, 32, 2111322 CrossRef CAS.
- K. Torbensen, C. Han, B. Boudy, N. von Wolff, C. Bertail, W. Braun and M. Robert, Iron Porphyrin Allows Fast and Selective Electrocatalytic Conversion of CO2 to CO in a Flow Cell, Chem. – Eur. J., 2020, 26, 3034–3038 CrossRef CAS PubMed.
- K. Xie, R. K. Miao, A. Ozden, S. Liu, Z. Chen, C. T. Dinh, J. E. Huang, Q. Xu and C. M. Gabardo,
et al., Bipolar membrane electrolyzers enable high single-pass CO2 electroreduction to multicarbon products, Nat. Commun., 2022, 13, 1–12 Search PubMed.
- S. Li, W. Chen, X. Dong, C. Zhu, A. Chen, Y. Song, G. Li, W. Wei and Y. Sun, Hierarchical
micro/nanostructured silver hollow fiber boosts electroreduction of carbon dioxide, Nat. Commun., 2022, 13, 1–9 CAS.
- Y. Wang, Z. Wang, C. T. Dinh, J. Li, A. Ozden, M. Golam Kibria, A. Seifitokaldani, C. S. Tan and C. M. Gabardo,
et al., Catalyst synthesis under CO2 electroreduction favours faceting and promotes renewable fuels electrosynthesis, Nat. Catal., 2019, 3, 98–106 CrossRef.
- T. Zhang, J. C. Bui, Z. Li, A. T. Bell, A. Z. Weber and J. Wu, Highly selective and productive reduction of carbon dioxide to multicarbon products via in situ CO management using segmented tandem electrodes, Nat. Catal., 2022, 5, 202–211 CrossRef CAS.
- J. H. Guo, X. Y. Zhang, X. Y. Dao and W. Y. Sun, Nanoporous Metal–Organic Framework-Based Ellipsoidal Nanoparticles for the Catalytic Electroreduction of CO2, ACS Appl. Nano Mater., 2020, 3, 2625–2635 CrossRef CAS.
- J. R. Huang, X. F. Qiu, Z. H. Zhao, H. L. Zhu, Y. C. Liu, W. Shi, P. Q. Liao and X. M. Chen, Single-Product Faradaic Efficiency for Electrocatalytic of CO2 to CO at Current Density Larger than 1.2 A cm−2 in Neutral Aqueous Solution by a Single-Atom Nanozyme, Angew. Chem., Int. Ed., 2022, 61, e202210985 CrossRef CAS PubMed.
- B. Endrdi, E. Kecsenovity, A. Samu, T. Halmágyi, S. Rojas-Carbonell, L. Wang, Y. Yan and C. Janáky, High carbonate ion conductance of a robust PiperION membrane allows industrial current density and conversion in a zero-gap carbon dioxide electrolyzer cell, Energy Environ. Sci., 2020, 13, 4098–4105 RSC.
- N. Fujinuma, A. Ikoma and S. E. Lofland, Highly Efficient Electrochemical CO2 Reduction Reaction to CO with One-Pot Synthesized Co-Pyridine-Derived Catalyst Incorporated in a Nafion-Based Membrane Electrode Assembly, Adv. Energy Mater., 2020, 10, 2001645 CrossRef CAS.
- J. A. Rabinowitz and M. W. Kanan, The future of low-temperature carbon dioxide electrolysis depends on solving one basic problem, Nat. Commun., 2020, 11, 1–3 CrossRef PubMed.
- M. Ma, E. L. Clark, K. T. Therkildsen, S. Dalsgaard, I. Chorkendorff and B. Seger, Insights into the carbon balance for CO2 electroreduction on Cu using gas diffusion electrode reactor designs, Energy Environ. Sci., 2020, 13, 977–985 RSC.
- E. R. Cofell, U. O. Nwabara, S. S. Bhargava, D. E. Henckel and P. J. A. Kenis, Investigation of Electrolyte-Dependent Carbonate Formation on Gas Diffusion Electrodes for CO2 Electrolysis, ACS Appl. Mater. Interfaces, 2021, 13, 15132–15142 CrossRef CAS PubMed.
- C. P. O'Brien, R. K. Miao, S. Liu, Y. Xu, G. Lee, A. Robb, J. E. Huang, K. Xie and K. Bertens,
et al., Single Pass CO2 Conversion Exceeding 85% in the Electrosynthesis of Multicarbon Products via Local CO2 Regeneration, ACS Energy Lett., 2021, 6, 2952–2959 CrossRef.
- B. Pan, J. Fan, J. Zhang, Y. Luo, C. Shen, C. Wang, Y. Wang and Y. Li, Close to 90% Single-Pass Conversion Efficiency for CO2 Electroreduction in an Acid-Fed Membrane Electrode Assembly, ACS Energy Lett., 2022, 7, 4224–4231 CrossRef CAS.
- J. Disch, L. Bohn, S. Koch, M. Schulz, Y. Han, A. Tengattini, L. Helfen, M. Breitwieser and S. Vierrath, High-resolution neutron imaging of salt precipitation and water transport in zero-gap CO2 electrolysis, Nat. Commun., 2022, 13, 1–9 Search PubMed.
- S. Garg, Q. Xu, A. B. Moss, M. Mirolo, W. Deng, I. Chorkendorff, J. Drnec and B. Seger, How alkali cations affect salt precipitation and CO2 electrolysis performance in membrane electrode assembly electrolyzers, Energy Environ. Sci., 2023, 16, 1631–1643 RSC.
- R. Krause, D. Reinisch, C. Reller, H. Eckert, D. Hartmann, D. Taroata, K. Wiesner-Fleischer, A. Bulan and A. Lueken,
et al., Industrial Application Aspects of the Electrochemical Reduction of CO2 to CO in Aqueous Electrolyte, Chem. Ing. Tech., 2020, 92, 53–61 CrossRef CAS.
- J. Timoshenko, A. Bergmann, C. Rettenmaier, A. Herzog, R. M. Arán-Ais, H. S. Jeon, F. T. Haase, U. Hejral and P. Grosse,
et al., Steering the structure and selectivity of CO2 electroreduction catalysts by potential pulses, Nat. Catal., 2022, 5, 259–267 CrossRef CAS.
- S. Liu, H. Tao, L. Zeng, Q. Liu, Z. Xu, Q. Liu and J. L. Luo, Shape-Dependent Electrocatalytic Reduction of CO2 to CO on Triangular Silver Nanoplates, J. Am. Chem. Soc., 2017, 139, 2160–2163 CrossRef CAS PubMed.
- Y. Zhu, Z. Gao, Z. Zhang, T. Lin, Q. Zhang, H. Liu, L. Gu and W. Hu, Selectivity regulation of CO2 electroreduction on asymmetric AuAgCu tandem heterostructures, Nano Res., 2022, 15, 7861–7867 CrossRef CAS.
|
This journal is © the Partner Organisations 2023 |