DOI:
10.1039/D4SU00696H
(Critical Review)
RSC Sustainability, 2025,
3, 2064-2078
Exploring mineral–organic interactions for eco-friendly concrete alternatives: a radical concept
Received
7th November 2024
, Accepted 6th April 2025
First published on 9th April 2025
Abstract
Concrete is central to the civil construction industry worldwide, which is facing increasing governmental, social, and economic pressure to alleviate its considerable environmental impact. This impact centres around Portland cement, the main binder of concrete. The production of a single tonne of Portland cement generates 0.9 tonne of CO2 gas along with other negative environmental impacts. In the quest for alternate construction materials, there is much focus on artificial geopolymers which use aluminosilicate-based binders, the production of which does not liberate large amounts of CO2. However, due to the use of dangerous alkaline chemicals and high curing temperatures, industry is reluctant to implement artificial geopolymers despite their superior material properties. The research into replicating natural geopolymers appears to be in its infancy, possibly due to the underappreciated interaction between organic and mineral fractions. However, mineral–organic interactions are well researched, and the materials produced have considerably favourable properties. This work proposes the application of free radical chemistry to enhance and accelerate mineral–organic interactions to produce analogues of natural rock. The use of free radicals greatly reduces the energy requirements for reactions. They also efficiently degrade organic intermediates and promote mineral polymerisation. The benefits of these rock analogues lie not only in their material properties but also the potential re-use of waste building materials such as iron, aluminium, and glass. Therefore, the environmental impact of these materials will be substantially lower than that of concrete, with superior material properties. The implications of this study is a shift in conventional thinking away from current Portland cement-based construction materials to considering analogues of natural geopolymers.
 Peter Spencer | Peter is currently completing his PhD in chemistry and engineering at the University of the Sunshine Coast (UniSC). His previous research includes designing a machine readable labelling system for the leather tanning industry, and investigating claims of structured water. He has a broad range of interests and enjoys seeking innovative solutions for difficult problems. |
 Hejie Li | Dr Hejie Li was awarded his PhD in Mechanical Engineering from the University of Wollongong in 2012. Now he currently is a research fellow of Degradable Medical Implants based on the University of the Sunshine Coast Moreton Bay campus. Hejie's research focuses include metal-based medical implants, antibacterial coatings, advanced manufacturing techniques, EM analysis of materials' characteristics, finite element simulation of metal forming processes. Hejie have published about 80 research papers in peer-reviewed international journals. |
 Scott Hocknull | Scott is a multiple award-winning vertebrate palaeoecologist, passionate science communicator, exhibitor, multimodal 3D scanning technologist, and leader in Australian palaeotourism. 31 years in palaeontology began with his first paper aged 16, at the time Australia's youngest scientific author. Realising that most museum collections are hidden from public view and centralised in major cities, Scott has spent decades pursuing better connections between museums, tourism, education, traditional owners and regional communities. He is passionate about decentralised custodianship and activation of fossil and geoheritage collections through multidisciplinary research and non-traditional interpretation techniques, all via regional community-led enterprise. |
 Gareth Chalmers | Dr Gareth Chalmers is a sedimentary geologist and academic at University of the Sunshine Coast, Queensland, Australia. Dr Chalmers obtained his PhD at University of British Columbia, Canada. His research includes environmental and applied geology in societal problems. Dr Chalmers uses geochemistry, petrophysics, Earth surface processes and sedimentology to investigate nature-based solutions to climate change that includes coastal wetland restoration and measuring peatland resilience. |
 Tianfang Wang | Dr Tianfang Wang is a leading researcher and educator specializing in biotechnology and sustainability. After earning a PhD in 2008 from the University of Science and Technology of China, Dr Wang completed postdoctoral research at the University of Adelaide, focusing on mass spectrometry, ion chemistry, computational chemistry, and peptide chemistry. His work addresses multidisciplinary challenges, including parasitic infections, aquaculture, antimicrobial resistance, cancer treatment, and medical implant technologies. At the University of the Sunshine Coast, Dr Wang leads research on bioactive peptides from Australian marine and terrestrial organisms. His work emphasises sustainability by harnessing natural resources to combat multi-drug-resistant bacteria and creating biodegradable, biocompatible coatings for magnesium implants. These innovations minimise reliance on synthetic materials and promote environmentally friendly medical technologies. Dr Wang's research on host-defence peptides has advanced sustainable cancer immunotherapies, improving therapeutic vaccines and immune checkpoint blockade treatments. He also led the first single-nucleus transcriptomic study of cervical cancer, paving the way for sustainable precision medicine. |
Sustainability spotlight
This article presents an advancement in sustainable construction materials through the application of free radical chemistry. Our innovative theory enables us to combine organic and inorganic compounds to create rock analogues, which can substitute for conventional concrete. This review aligns well with the UN's Sustainable Development Goals 13 and 15 by addressing the environmental challenges associated with concrete production, including high CO2 production and land degradation from limestone mining. The proposed new materials can be made from recycled construction waste, offer enhanced engineering properties, while significantly reducing the environmental impact of the construction industry. Our findings highlight the potential of these rock analogues to reshape the future of construction with a minimal ecological footprint.
|
Introduction
The urgent need to reduce greenhouse gas emissions from human activities has become a focal point in global environmental policy, with significant attention directed at the construction industry.1–3 A report by the United Nations Environment Programme and the International Energy Agency4 underscores the magnitude of this challenge, noting the building and construction sector is responsible for 36% of global final energy use and 39% of energy-related CO2 emissions. These emissions encompass the entire lifecycle of construction materials, including their production and transportation. Civil construction, a cornerstone of the industry, is a major part of the building and construction industry, and concrete is central to civil construction. Concrete is second only to water in terms of human production and consumption.5 The key component of concrete is Portland cement, a calcium carbonate (CaCO3)-based binder. However, the environmental cost of Portland cement is substantial; its production requires the calcination of limestone, a process that releases approximately 0.55 tonnes of CO2 per tonne of CaCO3 according to eqn (1):6 |  | (1) |
In addition to this, approximately 0.40 tonnes of CO2 are emitted per tonne of concrete due to the burning of fuel required to power the reaction, as well as the energy consumed by crushing and transportation machinery.7–11 These emissions, combined with other environmental concerns such as water extraction12 and wastewater generation, have intensified the search for sustainable alternatives to traditional concrete.
As global efforts to combat climate change intensify, the construction industry faces increasing pressure to adopt more sustainable practices. This has spurred interest in finding viable alternatives to traditional concrete, with a focus on reducing or eliminating the environmental impact associated with Portland cement. Emerging technologies, such as geopolymer cements, mineral–organic composites, and the incorporation of recycled materials, represent promising avenues for innovation.
The bulk of previous studies seeking to address the environmental impact of Portland cement appear to be limited to supplementing Portland cement with alternative binders. Such binders centre around fly ash which is an aluminium and silica oxide-rich by-product of coal-fired power generation. Problems posed by the use of this material include limited availability and the requirement of dangerous alkaline activators. Other industrial waste products such as granulated blast furnace slag, wood ash, waste glass, waste tire rubber, and recycled demolition waste are used as aggregates and bulking agents to reduce mining virgin materials.7 However, demolition waste aggregates poses problems such as stress concentration due to sharp edges,13 compensation for varying porosity and water absorption,14–16 and varying density of particulates.15–17
This review highlights several studies that explore the chemical interactions between organic and inorganic substances, producing materials with desirable properties for construction. Such properties include chemical stability, limited shrinkage, and high mechanical strength. Although the number of studies investigating the application of biomolecules to concrete is increasing18–22 there are very few that focus on the chemical mechanisms of the organic–inorganic interaction. The apparent limited interest in this area of research may be responsible for its under-explored potential to solve the environmental concerns of the civil construction industry. This study seeks to spark further interest in the application of organic–inorganic interactions and provide a practical application for the civil construction industry.
As far as the authors of this study are aware, this is the first to propose the incorporation of free radical-induced organic–inorganic interactions for the purpose of developing civil construction materials. This innovative and practical approach combines unrelated topics such as natural geopolymers, organic templating in silica and metal oxide deposition, and artificial fossilisation with the development of a new construction material that is unlike the current CaO-based cements. The success of this approach could eliminate the use of Portland cement and thereby significantly reduce the environmental impact of the civil construction industry.7,13,14,17–22
Geopolymers
One of the most popular alternatives to traditional concrete is use of geopolymers, which rely on polymerised alumina–silicates as the main binder.6,23 This binder, also known as alumina–silicate gel (or cement/binder) is formed by combining an alkaline reagent consisting of sodium or potassium soluble silicates with a molar ratio SiO2 to M2O (with M being Na or K) greater than 1.65 and water.6 Geopolymer cements differ significantly from Portland-based cements, particularly in their curing process. While Portland cement requires up to 28 days to achieve maximum strength, geopolymer cements cure much more rapidly gaining most of their strength within just 24 hours.24,25
One of the environmental advantages of geopolymers is that their ability to utilise fly ash, a finely powdered silica and aluminium oxide-rich waste product from coal-fired electrical power generation.6,7,9,11,26–28 However, the production of geopolymers often requires the use of hazardous chemicals, such as strong alkaline solutions (typically NaOH), to dissolve the [SiO4]4− and [AlO4]5− ions before reforming them into the desired cross-linked polymer matrix of Si–O–Al–O–Si.6,29 While geopolymers offer advantages like short setting times, they also have notable drawbacks. These include low flowability, high curing temperatures, and high shrinkage.7,29
It is worth noting that some natural geopolymers incorporate organic biopolymers such as humic materials, polysaccharides, and chitosan.18,30,31 It has been proposed that these natural geopolymer formations may resist degradation due to cross-linking between inorganic and organic components.18,19,30 Ancient civilisations, including the Egyptians, Romans, and inhabitants of South America, reportedly used organic substances such as plant- and animal-fibres, proteins, and even dried blood, to improve the durability of their concretes.31,32 This polymer combination may explain how such constructions have withstood the test of time for over a thousand years.31 In contrast, current Portland cement materials (without organic additives) are only expected to last a maximum of 100 years.25,33,34
Organic–inorganic interactions
Recent studies on organic–inorganic polymer interactions suggest that the partial degradation of biopolymers can lead to crosslinking, which enhances the overall strength and chemical stability of geopolymers.18,30 Nodules surrounding fossilised organisms are excellent examples of such interaction, as they tend to resist weathering better than the surrounding host matrix.35–38
The mechanisms by which organic and inorganic compounds interact are of great interest in material science, especially in organisms that use silicon dioxide as a structural material. Examples include sea sponges, diatom algae, and rice plants. Intriguingly, biogenic silica found in organisms such as diatom algae have a density (2.07 g cm−3) similar to that of amorphous quartz glass (2.18 g cm−3).39 This is significant because artificial analogues of such material can only be synthesised at temperatures above 1000 °C,40 demonstrating that biogenic silica synthesis is far more efficient than artificial processes.
In non-biogenic silica, condensation (or polymerisation) occurs through a relatively simple process, as depicted in Fig. 1. A neutral silicic acid monomer (Si(OH)4) reacts with a deprotonated silanol group of a Si(OH)3O−, forming a pentacoordinate transition state. A hydroxyl ion is expelled, resulting in the formation of a silicic acid dimer. This condensation process continues, creating larger polysilicic acid molecules (dimers, trimers, and larger particles).40 pH plays a significant role in this process,40 under acidic (∼pH 5) or very dilute conditions, Si(OH)4 remains stable, but as pH increases (becomes more alkaline), it ionises more readily into Si(OH)3O−. Larger polysilicic acid molecules, with more hydroxyl groups, are prone to polymerisation, even at neutral pH.40
 |
| Fig. 1 Condensation of silicic acid (left) to polysilicic acid (right) via a pentacoordinate intermediate (centre). Adapted from ref. 40. | |
In contrast, biogenic silica formation relies on specific biomolecules that bind to and stabilise silica precursors, facilitating and directing condensation. In diatoms, proteins such as silaffins and long-chain polyamines41 interact with silicic (or polysilicic) acid by hydrogen and/or ionic bonds depending on the basicity of the functional groups (Fig. 2).40–44 These biomolecules “trap” silicic acid, creating opportunities for it to polymerise and form silicic acid polymers, effectively acting as templates for silica deposition.45 Depending on the properties of the biopolymer (e.g. isoelectric point, length), the resulting silica can be rapidly precipitated as a solid or stabilised in solution.40,42,46
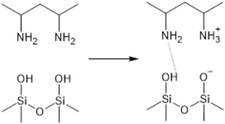 |
| Fig. 2 Polyamine molecule interacting with surface silanol groups of a silicic acid dimer (right) by hydrogen and ionic bonds. Adapted from ref. 42. | |
This concept of templating is utilised in the synthesis of zeolites, microporous crystalline aluminosilicate materials used as adsorbents, ion exchangers, catalysts, and fertilisers. Zeolites have the general formula (Mn+)x/n[(AlO2)x(SiO2)y]·mH2O, where M is a positively charged metal ion such as Na+, K+, Ca2+, and Mg2+.47 Organic compounds are key in the synthesis of zeolites due to their cationic and anionic regions. Thus, the mineral ions (i.e., SiO−, M+) can bind to the larger organic molecules where they are immobilised, allowing other mineral ions to bind to their stationary counterparts, and a mineral network is created around the organic molecules. Through this process, the organic compounds act as templates.48,49 Once the structure is stabilised, the organic template is often removed either via calcination or chemical degradation, leaving a porous solid with pore size and shape determined by the template and reaction conditions.50,51
Notable examples of detailed silica structuring via organic templates include studies by Townson et al. and Kaehr et al.43,52 Their experiments involved using 0.1 M silicic acid in an acidic saline solution (0.9% saline, pH 3) to stabilise monomers, reducing the likelihood of polymerisation without external influence. Thus, silica deposition is only governed by hydrogen bonding and other noncovalent silica/molecular interactions.43,44,52 In the presence of complex organic molecules, proteins capture and concentrate silica precursors, promoting their condensation and conversion into covalently bonded siloxanes.43 Removal of the templating organic components was then achieved by high temperature calcination (500–600 °C) under oxidising conditions. By this process, soft biological tissues were replicated by solid silica structures on the size range of subcellular to whole organism (e.g. chicken embryo).43,52 Organisms such as diatom algae and sea sponges use a specialised enzyme called silicatein to hydrolyse the C–Si bonds, releasing the newly formed silica structure from the organic template.53 This process is much more efficient than thermal calcination or reacting with acids or bases but is difficult to replicate on a practical scale.
In a similar experiment that investigated the fossilisation process of microorganisms, bacterial cells were silicified after reacting with an aqueous 10 mM FeCl3·6H2O solution. It was found that the biomaterial that bonded to the ferric iron preserved its morphology and structure during drying and calcination in the silicification process. This was not the case for biomaterials without ferric ion exposure, which exhibited significant shrinkage and structural degradation.45Table 1 provides a summary of studies highlighting enhanced material properties derived from organic–mineral interactions. It should be noted that the organic fractions mentioned in Table 1 cover a wide range of biomatter from simple organic acids (e.g. oxalic, citric, and malonic) to polysaccharide hydrogels (e.g. xanthan gum, guar gum) to the complex proteins of microorganisms and chicken embryos. With this in mind, and in keeping with the environmental focus of this study, it is not unreasonable to assume that industrial biowaste (e.g. biochar, sewage sludge, and straw husks etc.) could be utilized in the processes mentioned in this study. This in turn would further improve the environmental footprint of biowaste-generating industries.
Table 1 General organic–mineral interactions
Interaction |
Mineral fraction |
Organic fraction |
Description |
Operating conditions |
Findings |
Ref. |
Dissolution |
SiO2 |
Naphthalene, bitumen, kerogen. Organic acids (oxalic, stearic, humic, citric, malonic, succinic), BSA, amino acids, and sugars |
Simple, small molecule acids to long, complex amino chains (e.g. BSA) |
25 °C, pH ∼7 |
• Organic groups chelate surface hydroxyl groups by ligand exchange |
54–61
|
• The organic molecules weaken crystal bonds, facilitating dissolution |
• Only multi-protic or multi-functional mono-protic acids (e.g., citric, oxalic, pyruvic acids) interact with quartz |
• Dissolution rate is increased independently of other solubility constraints (i.e., temperature, pressure, molecule size, etc.) |
Metallosilicates (e.g., Al, Ca, K) |
Organic acids (oxalic, citric) |
Simple, small-molecule acids |
pH ∼4–9 |
• Organic molecules form complexing ligands with the metal sites (and silica, to a lesser degree), aiding in their release from the solid matrix |
56 and 62–68 |
• Ligand-promoted dissolution rates increase linearly with the concentration of absorbed ligands |
Metal oxides (e.g., Al2O3, BeO, Fe3O4) |
Organic acids (e.g., oxalic, malonic, succinic, salicylic) |
Simple, small-molecule acids |
|
• Organic groups chelate surface-bound hydrous metal oxides, forming detachable surface complexes |
69–74
|
• Bidentate ligands are the most effective chelators |
• Light accelerates metal oxide–organic interaction |
Metal–organic frameworks (MOF's) |
High valence metals (e.g., Mn, Co, Cr, Ni, Fe, Al, Cu, Ti, Zn), Zi, lanthanide metals, & SiO2 |
Various compounds (e.g., with –OH, –NH2, –N3−, carboxyl, and carbonyl groups) |
The functional groups allow organic molecules to interact with the mineral groups |
Temp.: 100–1000 °C, pressure: 1–10,000 atm. sometimes followed by calcination |
• Stable porous solids with high surface areas are formed by metal complexes within an organic framework |
75–85
|
• The metal's valence and the organic moieties (e.g. carboxylates, imidazolates, azolates) dictate pore size and shape |
• Pore characteristics and metal selection determine the material's effectiveness in targeting specific pollutants |
• Complexing metals enhance their catalytic ability |
• Uses include solid-state, and photo-catalysts, adsorbents, gas storage, separation, and pollution sensing |
Zeolites |
Silicates |
Organic surfactants, copolymers (e.g., glucose, fructose, dibenzoyl tartaric acid) |
Soap-like substances. Polymers with varying monomers |
pH varies, calcination |
• Similar results to that of MOF's except that silica forms the solid structure rather than metals |
86 and 87 |
Geopolymers (natural) |
Metals, calcium, crushed glass |
Biopolymers and hydrogels (e.g., xanthan and guar gum, chitosan) |
Fibrous, long-chained linear polysaccharides |
|
• Biopolymeric functional groups bind metals and form interpenetrating cross-linking networks with other polymers |
1, 18, 19, 30, 88 and 89 |
• Crosslinking can be chemical (e.g. covalent bonds) or physical (e.g. ionic, hydrogen, van der Waals bonds) |
• Biopolymers add to the strength of the mineral–organic composite material |
• Degradation of biopolymers interacting with metals can lead to geopolymers |
• Geopolymers (including organic components) are thermally, mechanically, and chemically stable in extreme conditions |
Biogeochemistry |
Ca2+, natural geopolymers |
Humic acids, micro-organisms |
Residual organic matter |
|
• Organic–inorganic interaction preserves organic structures in extreme temperatures (e.g., ∼250 °C) and pH ranges |
35, 37 and 90–98 |
• Biomatter degradation contributes to the physical properties of the concretion matrix |
Synthetic fossilisation |
Transition metals, uranium, aqueous silicates |
Microbial cell walls, chicken embryo |
Complex proteins |
Acidic metal salt bath (e.g., Fe3+, Al3+), acidic saline bath (pH 3, 0.9% NaCl), then silicate bath. Finally, calcination (500–600 °C) |
• Cell wall proteins trap and retain substantial amounts of metal ions |
43, 45, 52 and 99–101 |
• Uranium-loaded cell walls undergo crystallisation and structural degradation |
• Organic–metal complexes appear to preserve cell structure and resist further degradation |
• Silicate ions only interact with biomaterial under high concentrations of organic matter |
• Silicate ions interact more readily with pre-absorbed Fe and Al oxides in the organic matter |
Free radical chemistry
It is of particular interest that iron and other transition metals play multiple roles in the synthesis of new metallosilicate materials. That is, supporting the structure of organic scaffolding during silicification, integrating into the silica matrix, and catalysing the formation of molecular radical species.102,103 Molecular radicals are known to efficiently and rapidly degrade organic substances,79,104–107 accelerate the formation of metallosilicate matrixes,49,108–110 and initiate cross-linking between organic polymers.104 Radicals, which are highly energetic species with unpaired electrons (e.g. OH˙), are generated through homolytic fission. This process requires energy inputs such as heat, UV light, electrical fields, and/or ultrasonic irradiation.111–116 Unlike heterolytic cleavage, where the more electronegative atoms gains both bonding electrons, homolytic fission results in the even splitting of electrons between atoms. An example of heterolytic cleavage is the production of a methyl ion and a hydroxyl ion from methanol, as shown in eqn (2).
In this case, the more electronegative oxygen retained both the bonding electrons, creating the negatively charged hydroxyl ion (OH−) leaving the methyl ion with a positive charge (CH3+).
Conversely, homolytic cleavage of chlorine gas (Cl2), for example, causes each atom to retain one of the bonding electrons as depicted in eqn (3).
|  | (3) |
Radicals undergo three stages, initiation, propagation, and termination (see Fig. 3). Once created (initiated), the radical can react with another molecule, thereby transferring its unpaired electron to the second molecule (propagation). This then causes the second molecule to become radicalised as depicted in Fig. 3. Radical propagation can continue as long as there are organic molecules present.77,117
 |
| Fig. 3 Radical initiation, propagation, and termination. | |
By joining one radical species to another the electrons are now paired and stable. Therefore, the radicals are terminated. By this process larger molecules can be created. Polymerisation occurs when multiples of the same radical species are joined. Conversely, larger molecules can be oxidised to smaller, simpler molecules. Complete oxidation of organic molecules produces CO2 and H2O. These reactions and their products depend on reaction conditions such as pH, temperature, variety and concentration of other radical species and the nature of the reacting organic molecules.
As mentioned above, initiating radicals is energy intensive. This is often in the form of intense heat, UV light, electrical field, and ultrasonic irradiation (sonication).114,116,118–120 However, transition metals such as iron, copper, cobalt, and manganese have been found to play a catalytic role in the formation of radicals, particularly when bound to organic molecules.79,106,107
Of these metals, iron is often used as an efficient and cost-effective catalyst.77,102 Iron is commonly used in its oxidised (Fe2+, Fe3+) and unoxidized forms (Fe0).77,121–125 A classic example of an iron-catalysed radical reaction is the Fenton reaction.126 In the Fenton reaction, ferrous iron (Fe2+) catalyses the degradation of hydrogen peroxide (H2O2) to generate hydroxyl and hydroperoxyl radicals (˙OH,
) through eqn (4) and (5), with a secondary hydroxyl–peroxide reaction shown in eqn (6).127
| Fe2+ + H2O2 → Fe3+ + OH− + HO˙ | (4) |
|  | (5) |
|  | (6) |
It can be seen from eqn (4) and (5), the iron cycles between ferrous (Fe2+) and ferric (Fe3+) species. The reaction of H2O2 with Fe3+ is slower compared to Fe2+ (ref. 127 and 128) but can be accelerated by applying UV light by which Fe3+ is reduced back to Fe2+.103,111,129 This is known as the photo-Fenton reaction and an example of which is shown in eqn (7).103
| Fe(OH)2+ + hv → Fe2+ + HO˙ | (7) |
It should be noted that UV light required for the photo-Fenton reaction could be (and often is) sourced freely from sunlight. This factor alone greatly reduces the energy demands of free radical-based processes.130–134
Fenton reactions
Fenton and Fenton-like reactions (involving alternate or additional metals) are widely used in industrial wastewater treatment to oxidise organic compounds into smaller, less harmful molecules, ideally CO2 and H2O.127 While much focus is on hydroxyl radical (HO˙), a study by Varanasi et al.135 highlights the generation of other radicals by using UV/H2O2, such as atomic chlorine (Cl˙) and sulphate radicals (SO4˙−), each displaying unique selectivity. For instance, Cl˙ targets high electron-donating groups (double bonds, aromatic groups, phenolic groups, and carboxylate functional groups) via single electron transfer.136 HO˙ reacts with non-aromatics through hydrogen abstraction, and SO4˙− is more reactive towards aromatic and olefinic groups over aliphatic groups.135 To maximise organic degradation in Fenton-like systems, using a combination of metal salts is recommended.
In silica–organic composites, the degradation of organic components by various radicals facilitates condensation and polymerisation of silica precursors, which is further enhanced by radical interactions.49,108–110 Transition metals from Fenton-like reactions can then be incorporated into the developing silica matrix, forming rock-like metallosilicate structures.78,81 The final material's properties depend on the concentrations of metals and silica, the nature (size and complexity) of retained organic molecules, and presence of filler particles.
Low molecular weight organic acids, such as oxalic, glyoxylic, maleic, acetic, and formic acids, often accumulate due to incomplete oxidation, especially in dark Fenton reactions, while photo-assisted Fenton reactions offer more complete oxidation. Also, the mineralisation of organic substrates containing heteroatoms (e.g. Cl, N, S, and O) leads to the formation of inorganic acids.127 In both cases, the solution pH decreases. This is particularly important when the initial pH is high (≥7) as the optimal pH for the photo-Fenton reaction is ∼3.0.137,138 Therefore, the reaction is likely to be slow to start but will become more efficient as the pH decreases. Additionally, the presence of NaCl in the photo-Fenton reactions can contribute to the formation of Cl˙ radicals, which are effective oxidisers under neutral to high pH conditions.137
Mechanical activation
In addition to the above-mentioned means of generating radicals, there is also mechanochemical activation through various milling processes (i.e., ball, planetary ball, ring) or simply grinding with mortar and pestle. By fracturing silica particles, the mechanical separation of silicon ions from their neighbouring oxygen atoms does not allow the transfer of electrons to the more electronegative ion. Thus, solid-state siloxyl (SiO˙) and silicon (Si˙) radicals are formed as depicted in eqn (8).139–142 |  | (8) |
where ≡ = silicon valence bonds.
Eqn (9) shows how the surface-bound siloxyl radical can react with H2O to generate ˙OH.139,140,143
| ≡SiO˙ + H2O → SiOH + OH˙ | (9) |
Also possible is:
| ≡Si˙ + H2O → SiOH + H˙ | (10) |
It is important to note that without mechanochemical activation or extreme temperatures (>300 °C), the silica surfaces remain relatively inert.144
Free radicals
As demonstrated, free radicals play key roles in both oxidation of organic compounds and the polymerisation of minerals. They are key components of “advanced oxidation processes” (AOP), which are used to treat waste waters from domestic and industrial sources. The primary goal of AOP is to separate heavy metals from organic fractions (via precipitation) and oxidise organic matter into CO2 and water.145,146 In many cases, however, the AOP is optimised to reduce harmful organic compounds into less environmentally damaging substances, rather than achieving total mineralisation. In this research context, if organic matter acts as an intermediate between silicates and metals, free radical-based oxidation and polymerisation could be essential for developing metallosilicate rock analogues. The oxidation of organic intermediates allows mineral fractions to bond together.
Much of the literature on AOP focuses on the hydroxyl radical (OH˙) due to its high energy, low selectivity, and minimal environmental impact.145,147,148 OH˙ is particularly relevant in aqueous environments,149 and can be easily generated through various methods, such as UV light exposure,112,127,130,150 electrical fields,151 sonolysis,118,120,152 and ozone adsorption.145,146,153 In water bodies exposed to natural light (sunlight), especially UV, OH˙ can form naturally.111,129,149,154 Transition metal ions such as iron(II, and III),111,128,155 copper(II), cobalt(II) and manganese(II),148,156,157 act as catalysts to enhance the formation of these radicals.
Hydroxyl radicals primarily oxidise organic compounds by abstracting hydrogen from CH, NH, or OH bonds, or by adding to C
C bonds (shown in eqn (11) and (12) (ref. 127)), or adding to aromatic rings.127
| HO˙ + R − H → H2O + R˙ | (11) |
| HO˙ + C C → HO − C–C˙ | (12) |
where R = organic compound.
Through these reactions, the unpaired electron in radicals is transferred to organic molecules,127,158 initiating a chain reaction that often leads to the formation of various inorganic radicals. Each radical displays unique properties, such as redox potential, pH range stability, and selective reactivity.135,158
However, hydroxyl radicals are not always the ideal oxidiser in all conditions. For instance, a study by Anipsitakis and Dionysiou159 compared the effectiveness of HO˙ to the sulphate radical (SO4˙−). It was found that the HO˙ is effective near 3 but lose efficacy at pH values above 6. Cobalt-catalysed sulphate radicals were found to degrade 2,4-dichlorophenol and atrazine more efficiently than OH˙ under a wide range of conditions.159 In contrast, for the degradation of the contaminant naphthalene, HO˙ was more efficient in acidic conditions, while SO4˙− performed better at neutral pH.159 Additionally, both radicals react with atrazine at the same rate.159
Transition metals also vary in their ability to activate radicals. For example, when iron(II or III) concentrations are low and sulphate ions are high, HO˙ production may be limited. In such cases, Co(II) and Ru(III) are the ideal for activating peroxymonosulphate, while Ag(I) is effective in activating persulphate to generate SO4˙−.160
While the redox potential of sulphate radicals (2.6–3.1 V) is similar to that of hydroxl radicals (2.6 V), the reaction rate of hydroxyl radicals with organic compounds is generally higher (108–109 per mole, per second (M−1 s−1)) than sulphate radicals (106–107 M−1 s−1).148
From this, as well as the information in Table 2, it becomes evident that different radicals require specific conditions and/or activators (e.g., metal oxides and UV light) for optimal reactivity. For complex organic compounds, a combination of radical types may be necessary for effective mineralization.135
Table 2 A brief summary of some of the commonly utilised radicals in AOP's, their effective pH range, selectivity, and metal activators
Radical |
Redox potential (V)148 |
Optimum pH range |
Selectivity |
Metal activator |
Hydroxyl (HO˙) |
OH˙ + e− → OH− 1.8 V (ref. 147) |
∼3 (ref. 159 and 161) |
H atom abstraction135 |
TiO2 photocatalyst162,163 |
OH˙ + e− + H+ → 2.7 (ref. 147) |
Fe0 (ref. 121–124, 164 and 165) |
Fe3+/Fe2+, Co3+/Co2+, Cu2+/Cu+, Mn4+/Mn3+ (ref. 151) |
Sulphate (SO4˙−) |
2.5–3.1 (ref. 158) |
Neutral166 |
Aromatic and olefinic groups (C C)135,167 |
Cusolid2+ (ref. 168) |
Fe0, Fe2+, Cu2+, Co2+, Ag+ (ref. 166) |
Superoxide (O2˙−) |
2.4 (ref. 169) |
∼4.8 (ref. 170) |
C–C bonds171,172 |
From the breakdown of H2O2 (ref. 105 and 127) |
4.8–9.5 (ref. 173) |
Singlet oxygen (1O2) |
2.2 (ref. 169) |
3.8 (ref. 169) |
C C, and α-ethereal C–H bonds174 |
Mo0 (ref. 169) |
Hydroperoxyl (HO2˙) (the acid form of superoxide) |
1.7 (ref. 158) |
4 (ref. 175) |
Abstracts H+ to form H2O2 and peroxidises other compounds.176 |
From the breakdown of H2O2 (ref. 127, 138 and 177) |
Peroxymonosulphate (SO5˙−) |
1.1 (ref. 158) |
2–8 (ref. 159) |
Oxidises to form sulphate radicals148,159,160,166,168 |
Co3+/Co2+ (ref. 168) |
Chlorine (Cl˙) |
2.03 (ref. 178) |
<7 (ref. 131) |
H abstraction of C–H bonds, single electron transfer with OH– functional groups, and carbonyl (C O) groups135,179 |
Ni3+/Ni2+ (ref. 178) |
∼7 (ref. 179) |
Chlorine addition179 |
Organic intermediates
As shown in Fig. 3, the termination of radicals can result in the formation of larger molecules. Silica radicals, in particular, can covalently bond with organic molecules to form siloxane (Si–C) groups,141–143,180 and/or to metal oxides via a bridging oxygen atom (Si–O–Mn+). Organic acids such as oxalic, humic, fulvic, and citric acids are excellent metal chelators. They not only bond to (complex with) and solubilise silica particles but also form complexes with metal oxides.55–57,61,67,181 This process allows the combination of metal oxides and silicates in a water-based solution with an organic intermediate (e.g. Si–R–O–M+, where R = organic molecules). A critical feature of this organic intermediate is that the transition metal and silica fractions can coexist in solution at the same pH.46 While silicates are generally alkaline, the addition of acids can lead to the precipitation of solid silica particles. Transition metal salt solutions, which are typically acidic, also tend to precipitate solid particles when mixed with other solutions, unless significantly diluted. This bonding of metal and organic ions is the basis of chemical coagulation such as is commonly used in the wastewater treatment process.182,183 The precipitated sludge (metal–organic mixture) is easily removed from the water by filtration before further processing to remove the organic fractions (decontamination). A very common decontamination process in wastewater treatment is the Fenton reaction (or Fenton-like reactions).125,184 In this, and similar reactions, the metal ions present in the sludge (as inexpensive metal salts) play a crucial role in the decontamination process.77,79 Transition metal ions, such as iron and aluminium, can catalyse the formation of HO˙ and other radicals in water, especially when exposed to UV light (freely available as sunlight).77,129,130,134,154 These radicals are capable of degrading (oxidising) the organic intermediate to CO2 and H2O.127,128,184–186 This oxidation process not only removes the organic fractions, thereby enabling the bonding of metal and silica fractions to form metallosilicates, but also allows for the release of CO2 into the atmosphere or adjacent water bodies. The CO2 can also be reduced by the iron catalysts to form simple organic acids.187 The degradation of complex organic molecules into simpler by-products such as CO2 and esters is noteworthy as these products are used as setting agents for sodium silicate (water glass) in the metal foundries.188 Thus, these degradation by-products may contribute to the solidification of silica precursors.
Material development
The physical and chemical properties of the final metal–silicate composite may be tuned by altering the concentrations of its mineral and organic constituents. Factors such as the addition of fillers and aggregates, reaction temperatures, reaction times, and additional Fenton-like reactions (e.g. electro-, magneto-, and photo-Fenton) can further influence the material's properties. Simple methods such as high-speed ultrasonic irradiation (sonication), heating and UV–C irradiation (200–280 nm wavelength) are envisioned for the necessary reactions. Techniques like blending and sonication not only accelerate general chemical processes but also fracture the silica particles, generating solid-state radicals that contribute to the degradation of organic components.143,180,189,190 This approach has the added advantage of utilising recycled building materials like glass (silica), iron, and aluminium, which are abundant in most rocks. Challenges such as setting times, curing temperatures, and shrinkage are not fully understood for the proposed material. However, studies by Kaehr et al.43 and Townson et al.52 suggest that mildly acidic conditions might yield a material that is dimensionally preserved with no shrinkage, down to the nano scale. This research holds the potential to reduce environmental harm while maintaining compatibility with building methods.
Recycling construction and demolition waste
Generally, recycled construction and demolition (C&D) materials are used in the form of aggregates for new concrete.191,192 The reuse of C&D waste is considered to be a more environmentally sustainable approach as it seeks to conserve natural resources and reduce harmful environmental impacts associated with gravel and sand mining.15–17,192,193 In addition to this, extraction and processing of C&D aggregate consumes less energy compared to that of virgin aggregates, leading to lower carbon emissions during production.194,195 There is also the benefit of reduced landfill volume, and other disposal issues, generated from construction sites.195
However, the use of C&D waste-derived aggregates poses significant challenges. The recycled materials are often more porous than concrete and include cracks and fissures.15,16,194 These features can lead to reduced mechanical strength and weakened bonding between the aggregate and new concrete.15,16,194 The weakening of material strength is due to preexisting cracks in the aggregate which can initiate cracking in the new concrete matrix.15,16,194 Also, the variability in source materials makes it challenging to predict the behaviour of the recycled aggregate concrete (RAC).194 This is because different materials (wood, glass, metals, brick, plastic, etc.) have different mechanical properties, porosity, and densities, and their varying concentrations within the concrete mix will be reflected in the mechanical properties of the overall structure.15,16,192,194
A number of studies have investigated ways to improve the properties of RAC by filling the pores, cracks, and fissures with mineral admixtures such as fly ash, meta kaolin, silica fume, ground granulated blast furnace slag (GGBS), and nano silica.194 Although these methods show potential there remains the problem of variation within the sourced aggregate materials. Thus, precise characterisation and quality assurance would need to be implemented to reduce the amount of variation in aggregate material properties. This in itself may pose an economical and logistical challenge. Conversely, it may be efficient enough to compete with the natural resource mining industry. Further research is required to determine if such implementation is feasible.
The different approach proposed by this study focusses on recycling materials such as glass, iron, and aluminium in chemical form as opposed to aggregate form. That is, metal and glass waste can be chemically dissolved into solution form which allows for greater chemical bonding during the formation of the solid binder cement. This may seem to exclude concrete and ceramic waste as they are difficult to dissolve. However, it may be possible to pretreat C&D waste aggregate with rock analogue whilst in solution, thereby reducing stress points by filling unwanted micro-cavities, rounding sharp edges, as well as mineralising any organic components. The dissolution process is very simple, requiring inexpensive acids (for metals) and bases (for glass) and can be conducted in vats or a flow-through system. The energy requirements for dissolution are low as glass dissolves in NaOH at ∼130 °C, and the acid–metal reaction creates its own heat (exothermic). This is substantially simpler and less energy demanding than the calcination process required for converting CaCO3 to CaO as mentioned above.
Although not directly related to the construction industry, waste from the biological sectors also poses environmental concerns which can be somewhat alleviated by the processes mentioned in this study. For example, waste from biochar, meat processing, and recalcitrant plant fibres could be oxidized to simpler organic acids and humic substances that are able to interact with mineral ions (e.g. Fe3+, Al3+, and Si–O− ions). Indeed, this same process is employed by wastewater treatment plants, as mentioned above. Therefore, both the mineral and organic fractions could be sourced from readily available waste materials. It is granted that chemical preprocessing would be required in both fractions, but catalysts and catalytic processes (e.g. metal oxides and solar-Fenton reaction systems) could easily be applied to reduce energy requirements and reduce reaction times.129,133,134,155,196
Economic feasibility
Needless to say, the economic feasibility of recycled aggregate concrete is yet to be determined due to the number of unmet challenges. Likewise, the novelty of this study also makes it difficult to determine its economic feasibility. Also, early implementation of any materials and methods developed may also be economically risky on a large scale. Therefore, initial small scale implementation may be more prudent. However, since waste metals and glass (silica) can be easily dissolved by acids and bases, respectively, the conversion of these materials to useful solutes does not pose a daunting economic challenge. Also, due to the ease by which free radicals can be produced (e.g. solar irradiation and inexpensive iron oxide catalysts), processing of organic substances is equally financially attainable.112,129,137,149,151,154,197 Furthermore, the wide array of radicals that can be generated increases the range of organic substances that can be oxidised. Therefore, the complex substances produced by wastewater treatment systems could be employed in the production process. Again, this is an inexpensive and easily attainable option. With these things in mind, the exploration of the concepts proposed in this study is invitingly inexpensive.
A further consideration is that the product will be temporarily in the form of a mineral slurry of similar consistency to wet cement. Therefore, it is likely that no costly adaptation to existing pumps and transport vehicles will be required. Finally, in order for the product to be adopted commercially, it will undergo the same mechanical testing as conventional concrete. It is envisaged that by adjusting the chemistry of the process the material will meet, and possibly surpass, the mechanical properties of concrete at a substantially reduced cost.
Health and safety factors
Working silica-based materials has long been known to generate respitory problems associated with inhaled silica dust. Even simple sand grains pose health threats due to surface-bound silicon-centred radicals which can propagate to, and oxidise, organic matter.143,180,190,198 Most rock types (natural and synthesised) contain silica and are therefore prone to generating respirable crystalline silica (RCS) when cut, broken, or drilled. This is similar to other construction materials such as concrete, tiles, bricks, and clay. Therefore, dust control and exposure mitigation procedures are enforced by governments when working such materials.199 Such controls would also apply to applications of this study. However, this study focusses on use of metals and silicates in solute form. As such, particulates capable of generating respiratory problems cannot be created. On the other hand, such solutions are generally highly acidic or alkaline which do pose health risks. Therefore, during the dissolution of metals and silicas, protective systems and protocols should be applied. Such protections are already in place for wastewater treatment plants when applying metal salt coagulants and radical-based decontamination processes.
Similar to concrete, reinforcing iron bars may need to be applied to the final rock product to prevent sudden mechanical failure of the material. The oxidation of these bars could cause them to expand, causing destructive pressure within the material, similar to what is known as “concrete cancer”. Although such considerations may be outside the scope of this exploratory study, it may be possible to reduce the porosity of the material by altering its chemical composition and thereby prevent water penetration. This is something that can be explored during the initial experimentation. Similarly, environmental impacts could be mitigated by ensuring that leached salts and metal oxides are considered during the material preparation. These could also be identified during initial experimentation.
Conclusion
The persuit of concrete alterenatives is driven by the need to reduce CO2 and mitigate other environmental impacts caused by traditional construction materials. Artificial geopolymers have emerged as a promising solution, utilising industrial waste products like fly ash (rich in silicon and aluminium oxides) to form alumina–silicate gels, which serve as stronger binders than the calcium oxide-based binders found in Portland cement. Despite this, the widespread adoption of geopolymers has been hindered by challenges such as high temperature curing, material shrinkage, and the need for highly alkaline activators, which pose safety risks.
Research into replicating natural geopolymers is still in its early stage, though evidence of their long-time endurance abounds. Indeed, organic–mineral interactions are well researched showing strong evidence of structural templating and silica polymerisation. The product of such interactions are structures that resist weathering more than surrounding inorganic materials and maintain morphology even on the nanoscale. The complexity of organic molecules allows them to act as structural intermediaries between ionised silica and metals. The oxidation of these organic intermediaries will, in turn, allow the mineral fractions to bind, forming metallosilicates like natural rock.
This study aims to catalyse a paradigm shift in construction material science, moving away from the dominance of Portland cement-based systems and toward sustainable analogues inspired by natural rock. Our review highlights the undervalued potential of organic chemistry to address the environmental challenges currently facing the construction industry. We suggest that leveraging easily available free radical chemistry could significantly enhance organic–mineral interaction, organic oxidation, and mineral polymerisation, leading to the development of rock-like construction materials that surpass the performance of concrete. By integrating low-energy chemical processes with the recycling of waste materials such as aluminium, iron, and crushed glass (SiO2), as well as wastewater by-products, the civil construction industry could substantially reduce its environmental footprint while delivering durable and sustainable building materials. We acknowledge that implementing such transformative changes within the well-established civil construction industry presents considerable challenges. These include the restructuring of supply chains, modifications to equipment, and chemical processes, and potential adjustments in the application of final products. However, the escalating environment crisis may necessitate these expenses and investments. Also, utilising low-cost factors such as free radical chemistry and waste recycling could significantly reduce the initial financial outlay, thereby making the implementation of this study more inviting. Alternately, gradual adoption, beginning with small-scale applications, accompanied by proven performance and growing social acceptance, could drive incremental progress.
Data availability
No primary research results, software or code have been included and no new data were generated or analysed as part of this review.
Author contributions
Peter Spencer: conceptualisation (lead); writing – original draft (lead). Tianfang Wang: supervision (lead); writing – review and editing (lead); Hejie Li, Gareth Chalmers, Scott Hocknull: writing – review and editing (equal).
Conflicts of interest
There are no conflicts to declare.
Acknowledgements
Peter Spencer thanks the support from Australian Government Research Training Program Scholarship (RTP2022).
References
- K. A. Komnitsas, Procedia Eng., 2011, 21, 1023–1032 CrossRef.
- S. A. Miller, A. Horvath and P. J. M. Monteiro, Nat. Sustain., 2018, 1, 69–76 CrossRef.
- J. M. Allwood, J. M. Cullen and R. L. Milford, Environ. Sci. Technol., 2010, 44, 1888–1894 CrossRef CAS PubMed.
-
UN Environment and International Energy Agency, Towards a zero-emission, efficient, and resilient buildings and construction sector, Global Status Report 2017, 2017 Search PubMed.
-
H. Klee, Presented in Part at the P I Civil Eng-Eng Su, 2004 Search PubMed.
-
J. Davidovits, Geopolymer Science and Technics, 2013, vol. 21, pp. 1–11 Search PubMed.
- H. Afrin, N. Huda and R. Abbasi, IOP Conf. Ser. Mater. Sci. Eng., 2021, 1200, 012003 CrossRef CAS.
- B. C. McLellan, R. P. Williams, J. Lay, A. Van Riessen and G. D. Corder, J. Clean. Prod., 2011, 19, 1080–1090 CrossRef CAS.
- D. J. Flower and J. G. Sanjayan, Int. J. Life Cycle Assess., 2007, 12, 282–288 CrossRef CAS.
- J. Hong, G. Q. Shen, Y. Feng, W. S.-t. Lau and C. Mao, J. Clean. Prod., 2015, 103, 249–259 CrossRef CAS.
- A. M. Ö. Arıoğlu, D. G. Dhavale and J. Sarkis, J. Clean. Prod., 2017, 167, 1195–1207 CrossRef.
-
Commonwealth of Australia, Adequacy of the Regulatory Framework Governing Water Use by the Extractive Industry, Parliment of Australia, Australia, 2018 Search PubMed.
- R. Devaraj, J. Jordan, C. Gerber and A. Olofinjana, Appl. Sci., 2021, 11, 3318 CrossRef CAS.
- R. V. Silva, J. de Brito and R. K. Dhir, Constr. Build. Mater., 2018, 178, 19–31 CrossRef.
- R. Cardoso, R. V. Silva, J. d. Brito and R. Dhir, J. Waste Manage., 2016, 49, 131–145 CrossRef PubMed.
- F. de Andrade Salgado and F. de Andrade Silva, J. Build. Eng., 2022, 52, 104452 CrossRef.
- Y. R. Patil, V. A. Dakwale and R. V. Ralegaonkar, Adv. Civ. Eng., 2024, 2024, 6234010 CrossRef.
- D. Kim, H.-T. Lai, G. V. Chilingar and T. F. Yen, Environ. Geol., 2006, 51, 103–111 CrossRef CAS.
-
D. Kim, PhD, University of Southern California, 2004.
- H. Dehghan, A. Tabarsa, N. Latifi and Y. Bagheri, Clean Technol. Environ. Policy, 2019, 21, 155–165 CrossRef CAS.
- S. Yanez, C. Márquez, B. Valenzuela and C. Villamar-Ayala, Buildings, 2022, 12, 597 CrossRef.
-
K. Ouedraogo, J. Aubert, C. Tribout and G. Escadeillas, presented in part at the 3rd International Conference on Bio-Based Building Materials, 2019 Search PubMed.
- J. Davidovits, J. Therm. Anal. Calorim., 1991, 37, 1633–1656 CrossRef CAS.
- P. C. R. A. Abrão, F. A. Cardoso and V. M. John, Constr. Build. Mater., 2020, 247, 118546 CrossRef.
- H. S. Müller, M. Haist and M. Vogel, Constr. Build. Mater., 2014, 67, 321–337 CrossRef.
-
J. Aldred and J. Day, Presented in Part at the Proceedings of the 37th Conference on Our World in Concrete & Structures, Singapore, 2012 Search PubMed.
- D. Hardjito, S. E. Wallah, D. M. Sumajouw and B. V. Rangan, Materials, 2004, 101, 467–472 CAS.
- R. Kajaste and M. Hurme, J. Clean. Prod., 2016, 112, 4041–4052 CrossRef CAS.
-
A. D. Adesina, in SynerCrete'18: Interdisciplinary Approaches for Cement-Based Materials and Structural Concrete, RILEM Publications, 2018, vol. 1, pp. 389–394 Search PubMed.
- D. Kim, I. G. Petrisor and T. F. Yen, Carbohydr. Polym., 2004, 56, 213–217 CrossRef CAS.
- J. Davidovits, L. Huaman and R. Davidovits, Ceram. Int., 2019, 45, 7385–7389 CrossRef CAS.
-
J. Plank, in Biopolymers Online, ed. A. Steinbüchel, 2005, DOI:10.1002/3527600035.bpola002.
- J. W. Phair, Green Chem., 2006, 8, 763–780 RSC.
- F. M. Sabouni, J. Eng. Technol., 2013, 31, 723–728 CrossRef.
- H. Yoshida, A. Ujihara, M. Minami, Y. Asahara, N. Katsuta, K. Yamamoto, S.-i. Sirono, I. Maruyama, S. Nishimoto and R. Metcalfe, Sci. Rep., 2015, 5, 14123 CrossRef CAS PubMed.
- D. M. Martill, Geol. Today, 1989, 5, 201–205 CrossRef.
- M. J. Bojanowski and E. N. K. Clarkson, J. Sediment. Res., 2012, 82, 585–598 CrossRef CAS.
- D. M. MARTILL, Palaeontology, 1988, 31, 1–18 Search PubMed.
- M. A. Grachev, V. V. Annenkov and Y. V. Likhoshway, BioEssays, 2008, 30, 328–337 CrossRef CAS PubMed.
- V. V. Annenkov, E. N. Danilovtseva, V. A. Pal'shin, N. V. Ol'ga, S. N. Zelinskiy and U. M. Krishnan, RSC Adv., 2017, 7, 20995–21027 RSC.
- N. Kröger, R. Deutzmann and M. Sumper, Science, 1999, 286, 1129–1132 CrossRef PubMed.
- V. V. Annenkov, E. N. Danilovtseva, V. A. Pal'shin, V. O. Aseyev, A. K. Petrov, A. S. Kozlov, S. V. Patwardhan and C. C. Perry, Biomacromolecules, 2011, 12, 1772–1780 CrossRef CAS PubMed.
- B. Kaehr, J. L. Townson, R. M. Kalinich, Y. H. Awad, B. Swartzentruber, D. R. Dunphy and C. J. Brinker, Proc. Natl. Acad. Sci. U. S. A., 2012, 109, 17336–17341 CrossRef CAS PubMed.
- C. Y. Khripin, D. Pristinski, D. R. Dunphy, C. J. Brinker and B. Kaehr, ACS Nano, 2011, 5, 1401–1409 CrossRef CAS PubMed.
- F. G. Ferris, W. S. Fyfe and T. J. Beveridge, Geology, 1988, 16, 149–152 CrossRef CAS.
- V. V. Annenkov, E. N. Danilovtseva, Y. V. Likhoshway, S. V. Patwardhan and C. C. Perry, J. Mater. Chem., 2008, 18, 553–559 RSC.
- L. M. Jurkić, I. Cepanec, S. K. Pavelić and K. Pavelić, Nutr. Metab., 2013, 10, 2 CrossRef PubMed.
-
A. W. Burton and S. I. Zones, in Stud. Surf. Sci. Catal., ed. J. Čejka, H. van Bekkum, A. Corma and F. Schüth, Elsevier, 2007, vol. 168, pp. 137–179 Search PubMed.
- G. Feng, P. Cheng, W. Yan, M. Boronat, X. Li, J.-H. Su, J. Wang, Y. Li, A. Corma, R. Xu and J. Yu, Science, 2016, 351, 1188–1191 CrossRef CAS PubMed.
- P. M. Price, J. H. Clark and D. J. Macquarrie, J. Chem. Soc., Dalton Trans., 2000, 101–110 RSC.
- N. J. Sommerdijk, E. H. van Eck and J. Wright, Chem. Commun., 1997, 159–160 RSC.
- J. L. Townson, Y.-S. Lin, S. S. Chou, Y. H. Awad, E. N. Coker, C. J. Brinker and B. Kaehr, Nat. Commun., 2014, 5, 5665 CrossRef CAS PubMed.
-
K. Shimizu and D. E. Morse, in Methods Enzymol, ed. B. S. Moore, Academic Press, 2018, vol. 605, ch. 14, pp. 429–455 Search PubMed.
- N. W. Hinman, Geochim. Cosmochim. Acta, 1990, 54, 1563–1574 CrossRef CAS.
- P. C. Bennett, Geochim. Cosmochim. Acta, 1991, 55, 1781–1797 CrossRef CAS.
-
P. C. Bennett and W. Casey, in Organic Acids in Geological Processes, ed. E. D. Pittman and M. D. Lewan, Springer, Berlin, Heidelberg, 1994, pp. 162–200, DOI:10.1007/978-3-642-78356-2_7.
- P. C. Bennett, M. E. Melcer, D. I. Siegel and J. P. Hassett, Geochim. Cosmochim. Acta, 1988, 52, 1521–1530 CrossRef CAS.
- M. Kawano and J. Hwang, Clays Clay Miner., 2010, 58, 272–279 CrossRef CAS.
- M. Kawano and S. Obokata, Clays Clay Miner., 2007, 55, 361–368 CrossRef CAS.
- J. B. Lambert, G. Lu, S. R. Singer and V. M. Kolb, J. Am. Chem. Soc., 2004, 126, 9611–9625 CrossRef CAS PubMed.
- N. Marley, P. Bennett, D. Janecky and J. Gaffney, Org. Geochem., 1989, 14, 525–528 CrossRef CAS.
- C. Amrhein and D. L. Suarez, Geochim. Cosmochim. Acta, 1988, 52, 2785–2793 CrossRef CAS.
- R. E. Blake and L. M. Walter, Chem. Geol., 1996, 132, 91–102 CrossRef CAS.
- J. Cama and J. Ganor, Geochim. Cosmochim. Acta, 2006, 70, 2191–2209 CrossRef CAS.
- J. I. Drever and L. L. Stillings, Colloids Surf., A, 1997, 120, 167–181 CrossRef CAS.
- S. A. Welch and W. J. Ullman, Geochim. Cosmochim. Acta, 1993, 57, 2725–2736 CrossRef CAS.
- S.-M. Lin, Y.-L. Yu, Z.-J. Zhang, C.-Y. Zhang, M.-F. Zhong, L.-M. Wang, S.-X. Lu, W. Xu, N. Li and X. Huang, Appl. Clay Sci., 2020, 196, 105756 CrossRef CAS.
- G. d. O. Mendes, H. M. Murta, R. V. Valadares, W. B. d. Silveira, I. R. d. Silva and M. D. Costa, Miner. Eng., 2020, 155, 106458 CrossRef CAS.
- M. A. Blesa, H. A. Marinovich, E. C. Baumgartner and A. J. Maroto, Inorg. Chem., 1987, 26, 3713–3717 CrossRef CAS.
- G. Furrer and W. Stumm, Geochim. Cosmochim. Acta, 1986, 50, 1847–1860 CrossRef CAS.
- S. O. Lee, T. Tran, B. H. Jung, S. J. Kim and M. J. Kim, Hydrometallurgy, 2007, 87, 91–99 CrossRef CAS.
- D. Panias, M. Taxiarchou, I. Paspaliaris and A. Kontopoulos, Hydrometallurgy, 1996, 42, 257–265 CrossRef CAS.
- R. Salmimies, M. Huhtanen, J. Kallas and A. Häkkinen, J. Powder Technol., 2013, 2013, 164239 Search PubMed.
- B. Zinder, G. Furrer and W. Stumm, Geochim. Cosmochim. Acta, 1986, 50, 1861–1869 CrossRef CAS.
- A. Fdez-Sanromán, E. Rosales, M. Pazos and A. Sanroman, Appl. Sci., 2022, 12, 8240 CrossRef.
-
S. K. Ghosh, Metal–Organic Frameworks (MOFs) for Environmental Applications, Elsevier, 2019 Search PubMed.
- Z. Hu, J. Shi, H. Yang, J. Huang and F. Sheng, Sustainability, 2021, 13, 10993 CrossRef CAS.
- L. Jiao, Y. Wang, H. L. Jiang and Q. Xu, Adv. Mater., 2018, 30, 1703663 CrossRef PubMed.
- M. Kleber, I. C. Bourg, E. K. Coward, C. M. Hansel, S. C. Myneni and N. Nunan, Nat. Rev. Earth Environ., 2021, 2, 402–421 CrossRef.
- P.-Q. Liao, J.-Q. Shen and J.-P. Zhang, Coord. Chem. Rev., 2018, 373, 22–48 CrossRef CAS.
- M. Y. Masoomi, A. Morsali, A. Dhakshinamoorthy and H. Garcia, Angew. Chem., Int. Ed., 2019, 58, 15188–15205 CrossRef CAS PubMed.
- C. Pettinari, F. Marchetti, N. Mosca, G. Tosi and A. Drozdov, Polym. Int., 2017, 66, 731–744 CrossRef CAS.
- O. M. Yaghi, M. O'Keeffe, N. W. Ockwig, H. K. Chae, M. Eddaoudi and J. Kim, Nature, 2003, 423, 705–714 CrossRef CAS PubMed.
- S. Yuan, L. Feng, K. Wang, J. Pang, M. Bosch, C. Lollar, Y. Sun, J. Qin, X. Yang, P. Zhang, Q. Wang, L. Zou, Y. Zhang, L. Zhang, Y. Fang, J. Li and H.-C. Zhou, Adv. Mater., 2018, 30, 1704303 CrossRef PubMed.
-
P. Zhang, Q. Wang, Y. Fang, W. Chen, A. A. Kirchon, M. Baci, M. Feng, V. K. Sharma and H.-C. Zhou, in Metal–Organic Frameworks (MOFs) for Environmental Applications, Elsevier, 2019, pp. 203–229 Search PubMed.
- Z. A. Alothman, Materials, 2012, 5, 2874–2902 CrossRef CAS.
- C. S. Cundy and P. A. Cox, Microporous Mesoporous Mater., 2005, 82, 1–78 CrossRef CAS.
- I. C. Alupei, M. Popa, M. Hamcerencu and M. J. M. Abadie, Eur. Polym. J., 2002, 38, 2313–2320 CrossRef CAS.
- D. Kim, l. G. Petrisor and T. F. Yen, J. Air Waste Manag. Assoc., 2005, 55, 961–969 CrossRef CAS PubMed.
- J. Alleon, S. Bernard, C. Le Guillou, D. Daval, F. Skouri-Panet, M. Kuga and F. Robert, Sci. Rep., 2017, 7, 1508 CrossRef PubMed.
- C. Bravo, C. Millo, S. Covelli, M. Contin and M. De Nobili, J. Soils Sediments, 2020, 20, 1074–1086 CrossRef CAS.
- D. E. Briggs, R. P. Evershed and M. J. Lockheart, Paleobiology, 2000, 26, 169–193 CrossRef.
- V. G. Eder, V. O. Krasavchikov, Y. N. Zanin and A. G. Zamirailova, Lithol. Miner. Resour., 2001, 36, 236–242 CrossRef CAS.
- G. Eglinton, B. Simoneit and J. Zoro, Proc. R. Soc. London, Ser. B, 1975, 189, 415–442 CAS.
- P. F. Greenwood, J. J. Brocks, K. Grice, L. Schwark, C. M. B. Jaraula, J. M. Dick and K. A. Evans, Ore Geol. Rev., 2013, 50, 1–27 CrossRef.
- H. Ifansyah, J. Trop. Soils, 2014, 18, 203–208 Search PubMed.
-
M. Ivanić, N. Vdović, D. S. Škapin and I. Sondi, 2016.
-
B. P. Tissot, D. H. Welte, B. P. Tissot and D. H. Welte, Petroleum Formation and Occurrence, 1984, pp. 69–73 Search PubMed.
- T. J. Beveridge, Can. J. Microbiol., 1978, 24, 89–104 CrossRef CAS PubMed.
- T. J. Beveridge, J. D. Meloche, W. S. Fyfe and R. G. E. Murray, Appl. Environ. Microbiol., 1983, 45, 1094–1108 CrossRef CAS PubMed.
- J. B. Fein, S. Scott and N. Rivera, Chem. Geol., 2002, 182, 265–273 CrossRef CAS.
- W. P. Kwan and B. M. Voelker, Environ. Sci. Technol., 2003, 37, 1150–1158 CrossRef CAS PubMed.
-
R. Vasquez-Medrano, D. Prato-Garcia and M. Vedrenne, in Advanced Oxidation Processes for Waste Water Treatment, Elsevier, 2018, pp. 89–113 Search PubMed.
- K. J. Davies, S. W. Lin and R. E. Pacifici, J. Biol. Chem., 1987, 262, 9914–9920 CrossRef CAS PubMed.
- A. Kessler, J. Hedberg, E. Blomberg and I. Odnevall, Nanomaterials, 2022, 12, 1922 CrossRef CAS PubMed.
- S. D. Aust, L. A. Morehouse and C. E. Thomas, Free Radic. Biol. Med., 1985, 1, 3–25 CrossRef CAS PubMed.
- D. M. Miller, G. R. Buettner and S. D. Aust, Free Radic. Biol. Med., 1990, 8, 95–108 CrossRef CAS PubMed.
- G. Feng, J. Wang, M. Boronat, Y. Li, J.-H. Su, J. Huang, Y. Ma and J. Yu, J. Am. Chem. Soc., 2018, 140, 4770–4773 CrossRef CAS PubMed.
- P. Cheng, M. Song, H. Zhang, Y. Xuan and C. Wu, J. Mater. Sci., 2018, 54, 4573–4578 CrossRef.
- P. Cheng, G. Feng, C. Sun, W. Xu, J.-H. Su, W. Yan and J. Yu, Inorg. Chem. Front., 2018, 5, 2106–2110 RSC.
- N. López-Vinent, A. Cruz-Alcalde, L. E. Romero, M. E. Chávez, P. Marco, J. Giménez and S. Esplugas, J. Hazard. Mater., 2019, 380, 120882 CrossRef PubMed.
- R. Yin, L. Ling and C. Shang, Water Res., 2018, 142, 452–458 CrossRef CAS PubMed.
- V. V. Novikov and E. V. Yablokova, Appl. Sci., 2022, 12, 5185 CrossRef CAS.
-
G. Chatel, Sonochemistry: New Opportunities for Green Chemistry, World Scientific Publishing Company, 2016 Search PubMed.
-
M. Ashokkumar and T. J. Mason, in Kirk-Othmer Encyclopedia of Chemical Technology, John Wiley and Sons, Hoboken, NJ, USA, 2007, pp. 1–34, DOI:10.1002/0471238961.1915141519211912.a01.pub2..
- K. S. Suslick, Science, 1990, 247, 1439–1445 CrossRef CAS PubMed.
- F. Collin, Int. J. Mol. Sci., 2019, 20, 2407 CrossRef PubMed.
-
M. Ashokkumar and T. J. Mason, in Kirk-Othmer Encyclopedia of Chemical Technology, 2007, DOI:10.1002/0471238961.1915141519211912.a01.pub2.
-
K. Kerboua and O. Hamdaoui, in Nanotechnology in the Life Sciences, 2020, pp. 409–460, DOI:10.1007/978-3-030-42284-4_15.
- Y. G. Adewuyi, Ind. Eng. Chem. Res., 2001, 40, 4681–4715 CrossRef CAS.
- M. Suzuki, Y. Suzuki, K. Uzuka and Y. Kawase, Chemosphere, 2020, 259, 127470 CrossRef CAS PubMed.
- C.-S. He, R.-R. Ding, J.-Q. Chen, G.-N. Zhou and Y. Mu, Sci. Total Environ., 2022, 802, 149812 CrossRef CAS PubMed.
- S.-Y. Oh, P. C. Chiu, B. J. Kim and D. K. Cha, Water Res., 2003, 37, 4275–4283 CrossRef CAS PubMed.
- Y. Nakatsuji, Z. Salehi and Y. Kawase, J. Environ. Manage., 2015, 152, 183–191 CrossRef CAS PubMed.
- N. Ahmed, D. Vione, L. Rivoira, L. Carena, M. Castiglioni and M. C. Bruzzoniti, Molecules, 2021, 26, 4584 CrossRef CAS PubMed.
- H. J. H. Fenton, J. Chem. Soc., Trans., 1894, 65, 899–910 RSC.
- J. J. Pignatello, E. Oliveros and A. MacKay, Crit. Rev. Environ. Sci. Technol., 2006, 36, 1–84 CrossRef CAS.
-
R. Vasquez-Medrano, D. Prato-Garcia and M. Vedrenne, in Advanced Oxidation Processes for Waste Water Treatment, ed. S. C. Ameta and R. Ameta, Academic Press, 2018, pp. 89–113, DOI:10.1016/B978-0-12-810499-6.00004-8.
- Z. S. B. de Souza, M. P. Silva, T. J. M. Fraga and M. A. Motta Sobrinho, Environ. Sci. Pollut. Res., 2021, 28, 23912–23928 CrossRef CAS PubMed.
- M. A. Ali, I. M. Maafa and I. Y. Qudsieh, Water, 2024, 16, 453 CrossRef CAS.
- D. M. Bulman, S. P. Mezyk and C. K. Remucal, Environ. Sci. Technol., 2019, 53, 4450–4459 CrossRef CAS PubMed.
- B. C. Faust and R. G. Zepp, Environ. Sci. Technol., 1993, 27, 2517–2522 CrossRef CAS.
- D. Clematis and M. Panizza, Chemosphere, 2021, 270, 129480 CrossRef CAS PubMed.
- S. Garcia-Segura, E. Brillas, L. Cornejo-Ponce and R. Salazar, Sol. Energy, 2016, 124, 242–253 CrossRef CAS.
- L. Varanasi, E. Coscarelli, M. Khaksari, L. R. Mazzoleni and D. Minakata, Water Res., 2018, 135, 22–30 CrossRef CAS PubMed.
- W.-L. Wang, X. Zhang, Q.-Y. Wu, Y. Du and H.-Y. Hu, Water Res., 2017, 124, 251–258 CrossRef CAS PubMed.
- A. J. Luna, O. Chiavone-Filho, A. Machulek, J. E. F. de Moraes and C. A. O. Nascimento, J. Environ. Manage., 2012, 111, 10–17 CrossRef CAS PubMed.
- C. Jiang, S. Pang, F. Ouyang, J. Ma and J. Jiang, J. Hazard. Mater., 2010, 174, 813–817 CrossRef CAS PubMed.
- J. Narayanasamy and J. D. Kubicki, J. Phys. Chem. B, 2005, 109, 21796–21807 CrossRef CAS PubMed.
- X. Shi, N. S. Dalai and V. Vallyathan, J. Toxicol. Environ. Health, 1988, 25, 237–245 CrossRef CAS PubMed.
- I. Vorsina, T. Grigorieva, A. Barinova and N. Lyakhov, Chem. Sustain. Dev., 2011, 19, 447–455 Search PubMed.
- T. Watanabe, S. Hasegawa, N. Wakiyama, F. Usui, A. Kusai, T. Isobe and M. Senna, J. Solid State Chem., 2002, 164, 27–33 CrossRef CAS.
- V. Vallyathan, X. L. Shi, N. S. Dalal, W. Irr and V. Castranova, Am. Rev. Respir. Dis., 1988, 138, 1213–1219 CrossRef CAS PubMed.
- S. K. Parida, S. Dash, S. Patel and B. K. Mishra, Adv. Colloid Interface Sci., 2006, 121, 77–110 CrossRef CAS PubMed.
- N. C. Baird, J. Chem. Educ., 1997, 74, 817 CrossRef CAS.
- S. J. Masten and S. H. Davies, Environ. Sci. Technol., 1994, 28, 180A–185A CrossRef CAS PubMed.
- G. V. Buxton, C. L. Greenstock, W. P. Helman and A. B. Ross, J. Phys. Chem. Ref. Data, 1988, 17, 513–886 CrossRef CAS.
- J. Wang and S. Wang, Chem. Eng. J., 2020, 401, 126158 CrossRef CAS.
- C. Ruales-Lonfat, J. F. Barona, A. Sienkiewicz, M. Bensimon, J. Vélez-Colmenares, N. Benítez and C. Pulgarín, Appl. Catal., B, 2015, 166–167, 497–508 CrossRef CAS.
-
J. C. Mierzwa, R. Rodrigues and A. C. Teixeira, in Advanced Oxidation Processes for Waste Water Treatment, Elsevier, 2018, pp. 13–48 Search PubMed.
- Z. Heidari, R. Pelalak and M. Zhou, Chem. Eng. J., 2023, 474, 145741 CrossRef CAS.
- J. Jagannathanmadhavan, S. Dhandapanibalaji and M. Choi, Molecules, 2019, 24, 3341 CrossRef PubMed.
- D. B. Miklos, C. Remy, M. Jekel, K. G. Linden, J. E. Drewes and U. Hübner, Water Res., 2018, 139, 118–131 CrossRef CAS PubMed.
- L. M. Mayer, L. L. Schick, K. Skorko and E. Boss, Limnol. Oceanogr., 2006, 51, 1064–1071 CrossRef CAS.
- M. Minella, G. Marchetti, E. De Laurentiis, M. Malandrino, V. Maurino, C. Minero, D. Vione and K. Hanna, Appl. Catal., B, 2014, 154–155, 102–109 CrossRef CAS.
- N. Zhang, Y. Yi, J. Lian and Z. Fang, Chem. Eng. J., 2020, 395, 124897 CrossRef CAS.
- M. Strlic, J. Kolar, V.-S. Selih, D. Kocar and B. Pihlar, Acta Chim. Slov., 2003, 50, 619–632 CAS.
- P. Neta, R. E. Huie and A. B. Ross, J. Phys. Chem. Ref. Data, 1988, 17, 1027–1284 CrossRef CAS.
- G. P. Anipsitakis and D. D. Dionysiou, Environ. Sci. Technol., 2003, 37, 4790–4797 CrossRef CAS PubMed.
- G. P. Anipsitakis and D. D. Dionysiou, Environ. Sci. Technol., 2004, 38, 3705–3712 CrossRef CAS PubMed.
- C.-Y. Chang, Y.-H. Hsieh, K.-Y. Cheng, L.-L. Hsieh, T.-C. Cheng and K.-S. Yao, Water Sci. Technol., 2008, 58, 873–879 CrossRef CAS PubMed.
- C. Carlsson, B. Fégeant, E. Svensson, L. Wiklund and M. Jonsson, J. Phys. Chem. C, 2022, 126, 12435–12440 CrossRef CAS.
-
H. Hu and K. Xu, in High-risk Pollutants in Wastewater, Elsevier, 2020, pp. 169–207 Search PubMed.
- N. Ohta, M. Kobayashi and Y. Kawase, Environ. Sci. Pollut. Res., 2023, 30, 38819–38831 CrossRef CAS PubMed.
- X. Sun, T. Kurokawa, M. Suzuki, M. Takagi and Y. Kawase, J. Environ. Sci. Health, Part A: Toxic/Hazard. Subst. Environ. Eng., 2015, 50, 1057–1071 CrossRef CAS PubMed.
- J. Wang and S. Wang, Chem. Eng. J., 2018, 334, 1502–1517 CrossRef CAS.
- S. Luo, Z. Wei, D. D. Dionysiou, R. Spinney, W.-P. Hu, L. Chai, Z. Yang, T. Ye and R. Xiao, Chem. Eng. J., 2017, 327, 1056–1065 CrossRef CAS.
- T. Zhang, H. Zhu and J.-P. Croué, Environ. Sci. Technol., 2013, 47, 2784–2791 CrossRef CAS PubMed.
- Q. Yi, J. Ji, B. Shen, C. Dong, J. Liu, J. Zhang and M. Xing, Environ. Sci. Technol., 2019, 53, 9725–9733 CrossRef CAS PubMed.
- M. S. Baker and J. M. Gebicki, Arch. Biochem. Biophys., 1984, 234, 258–264 CrossRef CAS PubMed.
- M. Liu, H. Liu, N. Li, C. Zhang, J. Zhang and F. Wang, ChemSusChem, 2022, 15, e202201068 CrossRef CAS PubMed.
- J. Wang, H. Zhao, P. Liu, N. Yasri, N. Zhong, M. G. Kibria and J. Hu, J. Energy Chem., 2022, 74, 324–331 CrossRef CAS.
- D. Klug, J. Rabani and I. Fridovich, J. Biol. Chem., 1972, 247, 4839–4842 CrossRef CAS PubMed.
- A. Sagadevan, K. C. Hwang and M.-D. Su, Nat. Commun., 2017, 8, 1812 CrossRef PubMed.
- U. T. Twahir, C. N. Stedwell, C. T. Lee, N. G. J. Richards, N. C. Polfer and A. Angerhofer, Free Radic. Biol. Med., 2015, 80, 59–66 CrossRef CAS PubMed.
- A. C. Lloyd, Int. J. Chem. Kinet., 1974, 6, 169–228 CrossRef CAS.
- Y. Lin, J. Qiao, Y. Sun and H. Dong, J. Environ. Sci., 2025, 147, 114–130 CrossRef CAS PubMed.
- B. J. Shields and A. G. Doyle, J. Am. Chem. Soc., 2016, 138, 12719–12722 CrossRef CAS PubMed.
- Y. Lei, X. Lei, P. Westerhoff, X. Zhang and X. Yang, Environ. Sci. Technol., 2021, 55, 689–699 CrossRef CAS PubMed.
- F. Turci, C. Pavan, R. Leinardi, M. Tomatis, L. Pastero, D. Garry, S. Anguissola, D. Lison and B. Fubini, Part. Fibre Toxicol., 2016, 13, 32 CrossRef PubMed.
- G. Subramanian and G. Madras, Water Res., 2016, 104, 168–177 CrossRef CAS PubMed.
-
ChemREADY, Coagulation In Wastewater Treatment. What is the Purpose?, https://www.getchemready.com/water-facts/what-is-purpose-of-coagulation-in-wastewater-treatment/#:%7E:text=What-is-Coagulation-in-Wastewater,Certain-viruses-and-bacteria, accessed March 12, 2025.
-
J. Greaves, How are coagulants and flocculants used in water and wastewater treatment?, https://www.wcs-group.co.uk/wcs-blog/coagulants-flocculants-wastewater-treatment#:%7E:text=Conclusion-,What-is-coagulation-and-flocculation-in-water-treatment?,to-centuries-to-settle-out!, accessed March 12, 2025.
- P. Bautista, A. Mohedano, J. Casas, J. Zazo and J. Rodriguez, J. Chem. Technol. Biotechnol., 2008, 83, 1323–1338 CrossRef CAS.
- Y. Li, W. Zhang, J. Niu and Y. Chen, ACS Nano, 2012, 6, 5164–5173 CrossRef CAS PubMed.
- K. Barbusinski, Ecol. Chem. Eng. S, 2009, 16, 347–358 CAS.
- R. Bonetto, F. Crisanti and A. Sartorel, ACS Omega, 2020, 5, 21309–21319 CrossRef CAS PubMed.
-
J. R. Brown, in Foseco Ferrous Foundryman's Handbook, Butterworth-Heinemann, Oxford, 11 edn, 2000 Search PubMed.
- S. Gabor and Z. Anca, Int. Arch. Arbeitsmed., 1974, 32, 327–332 CrossRef CAS PubMed.
- X. Shi, N. S. Dalai, X. N. Hu and V. Vallyathan, J. Toxicol. Environ. Health, 1989, 27, 435–454 CrossRef CAS PubMed.
- P. Sormunen and T. Kärki, J. Build. Eng., 2019, 24, 100742 CrossRef.
- N. Kisku, H. Joshi, M. Ansari, S. Panda, S. Nayak and S. C. Dutta, Constr. Build. Mater., 2017, 131, 721–740 CrossRef CAS.
- R. V. Silva, J. de Brito and R. K. Dhir, J. Clean. Prod., 2019, 236, 117629 CrossRef.
- M. Behera, S. K. Bhattacharyya, A. K. Minocha, R. Deoliya and S. Maiti, Constr. Build. Mater., 2014, 68, 501–516 CrossRef.
-
A. Abbas, G. Fathifazl, O. B. Isgor, A. G. Razaqpur, B. Fournier and S. Foo, presented in part at the 2006 IEEE EIC Climate Change Conference, Ottawa, ON, Canada, 2006 Search PubMed.
- F. C. Moreira, S. Garcia-Segura, V. J. P. Vilar, R. A. R. Boaventura and E. Brillas, Appl. Catal., B, 2013, 142–143, 877–890 CrossRef CAS.
- L. Hernández, P. A. Augusto, T. Castelo-Grande and D. Barbosa, J. Environ. Manage., 2021, 285, 112155 CrossRef PubMed.
- M. Ding, X. Shi, Z. Dong, F. Chen, Y. Lu, V. Castranova and V. Vallyathan, J. Biol. Chem., 1999, 274, 30611–30616 CrossRef CAS PubMed.
-
worksafe.qld.gov.au, Construction dust: respirable crystalline silica, https://www.worksafe.qld.gov.au/safety-and-prevention/hazards/hazardous-exposures/respirable-crystalline-silica/silica-exposure-a-serious-risk-for-construction-workers, accessed October 9, 2024.
|
This journal is © The Royal Society of Chemistry 2025 |
Click here to see how this site uses Cookies. View our privacy policy here.