Direct flue gas capture for algae cultivation and subsequent valorization: evaluating life cycle emissions and costs†
Received
4th March 2025
, Accepted 24th June 2025
First published on 25th June 2025
Abstract
Algae cultivation and processing is an important pathway under discussion within the broader CO2 capture and utilization umbrella. Here, we discuss the results of a life-cycle analysis and techno-economic analysis of a pilot-scale photobioreactor that uses flue gas directly from natural gas or biogas combustion at 3–5% CO2 concentration. The system requires minimal freshwater use as it has been successfully run with industrial wastewater and has a much smaller areal footprint compared with open pond cultivation. Introducing the flue gas directly to the photobioreactor avoids the need for CO2 separation and pressurization, which is undertaken in many other algae cultivation systems. For the end-use of the biomass, the default case assumes conversion of algae to liquid fuels via hydrothermal liquefaction. The results indicate that the pilot-scale system has a higher cost, and comparable greenhouse gas emissions compared to pond-based systems, especially as the grid is anticipated to evolve to a lower carbon intensity. The costs of algae biofuel production range from $12–16 per GGE at the current pilot scale. Depending on whether the source of the carbon is fossil or biogenic, the net emissions are 68 g CO2e per MJ and −4 g CO2e per MJ respectively. If the marine algae species is used instead of the freshwater species, it offers an additional 16 g CO2e per MJ carbon fixation in the form of calcium carbonate. The findings point to broadly desirable trends in GHG emissions and costs, while the discussion aims to shed light on areas that could further improve the scalability of the system.
1. Introduction
CO2 capture and utilization (CCU) is considered an important suite of approaches to produce fuels, high-value products and chemicals from flue gases. Past analyses suggest that CCU could help in the reduction of 0.5 Gt-CO2 annually with the present-day technology.1 However, this could rapidly scale up with the emergence of new technological pathways. One such pathway is the conversion of microalgae into fuels and products of high value. The key advantage of an algal CCU platform is its relatively high carbon fixation efficiency, compared to other biomass types. Particularly, the biomass yield of algae biomass in closed bioreactors is estimated at 60–120 t ha−1, which is well above that for terrestrial biomass (20–40 t ha−1).2 Past work has shown that algal CO2 utilization could increase to 200–900 MtCO2 per year by 2050 under favorable conditions, which could represent 5% of all CCU globally.1 Another study has estimated this number to be as high as 4.1–7.5 Gt-CO2.3 Additionally, algae biomass is useful because it can deliver a variety of gaseous and liquid fuels, along with a number of valuable chemicals.4 That said, there are several gaps in the scalability of algal biofuels. Notably, the current cost of CO2 mitigation through such platforms is subject to very wide uncertainty (with estimates ranging from $220–1000 per t-CO2).4 This wide variance is primarily attributable to differences in experimental and modeled yields, although other reasons include differences in financial assumptions (e.g., capital costs, discount rates, etc.). Similarly, the energy burdens associated with algae remain uncertain and depend on the type of configuration used. We aim to address this by directly incorporating pilot-scale data directly into our systems analysis.
While the literature on algal fuels is large and diversified,5–7 their efficacy strongly depends on the context. Technological development and feedstock availability tend to strongly affect the supply chain. The present analysis looks at a novel microalgal technology platform, and its economic and life-cycle environmental evaluation to produce algal biofuels. As mentioned earlier, life-cycle analyses (LCAs) and techno-economic analyses (TEAs) of algal systems have been subject to wide uncertainty in energy investment for CO2 provision. Meta-analyses have shown that this often arose because of differences in energy inputs that were assumed in the various analyses.8 As such, the energy return on investment has varied from 0.46 to 2.6 The platform being evaluated in this study makes use of flue gas from power plants directly, which avoids the additional energy investments and associated uncertainties related to flue gas transport and distribution.
Instead of algal ponds, which are land-intensive, this approach uses a novel, tall-column, LED-lit photobioreactor (PBR) to cultivate the algal strains. Open-pond algal systems may entail considerable loss in CO2.9 The land and water requirements for such systems also continue to be deterrents to scalability.10 The two microalgal strains selected for this study were Scenedesmus obliquus HTB1 (a freshwater strain) and Nannochloropsis oceanica IMET1 (a saltwater strain), that could tolerate CO2 containing flue gases (6–12% CO2 and 104–112 ppm NOx from a power plant) and maintain a high-pH and high-alkalinity culture for removal of CO2 during their biomass production.11 As noted above, CCU approaches are being widely discussed to meet the decarbonization targets. It has been reported that the red plastid-bearing marine microalgal species can photosynthesize in highly alkaline cultures (>pH 10),12 while continuing their carbon concentrating mechanism.13 Hence, in the current study, Nannochloropsis oceanica, a marine microalgal species was also selected to study its potential to precipitate the calcium carbonate at high pH, facilitating additional CO2 storage. The feasibility of the algal system strongly depends on its design considerations and product end use. This study looks at specific sensitivities which affect the multiple pathways explored in this algal system.
The key question of interest in this analysis is whether this system, and PBRs in general, can offer a cost-effective algal production pathway with comparable greenhouse gas (GHG) emissions as open raceway ponds. We also wanted to understand the impact of key design sensitivities affecting costs and greenhouse gas metrics. From a systems analysis perspective, it is important to emphasize that prior LCA/TEA of PBR systems were limited to algae cultivation, where the system boundary typically included cultivation, harvesting and dewatering but not co-product valorization.14,15 This study further considers the conversion of algae into biofuel and the cited co-products in the system boundaries which represents the primary novelty of this study.
There are also additional novel features attributable to the setup itself. First, flue gas is directly used for the cultivation of algae, which is hypothesized to reduce the energy penalty for CO2 capture. Second, a non-potable industrial wastewater source is used in place of freshwater to cultivate algae. Third, it incorporates recycling of the dewatering loop that reduces nutrient input requirements, and thus, the use of expensive synthetic media. Fourth, two different algal strains are cultivated in PBRs: (1) S. obliquus, to study its potential in achieving high biomass productivity and carbon utilization or storage via a biochar end product, and (2) N. oceanica, to study its potential in precipitating calcium carbonate (an inorganic biocementitious material) as a valuable co-product.
2. Material and methods
2.1. Pilot setup summary
The pilot PBR is made up of cylindrical polyvinyl chloride bags and is supported by a Kevlar structure. The laminated Mylar/Kevlar bond minimizes the cost of bioreactor construction. The PBR uses a high-intensity, light-emitting diode (LED) system comprising three external lights (ca. 200 μmol m−2 s−1 measured at the reactor mid-point). The facility is co-located with a medium-size gas boiler (3 MW) and the Back River Wastewater Treatment plant in Columbia, MD. The current scale of the PBR is 500 L with a depth of 2.9 m and it uses 0.04 kg CO2 per h using a gas sparger. Ongoing work is targeting scale-up to a 6800 L PBR with a depth of 5.9 m with a CO2 input of 12–40 0.04 kg CO2 per h. Slipstream testing was conducted at the 500 L facility over a period of 28 days, during which the algae dry weight was observed to plateau; further details have been discussed by Jonas et al.16
We used non-axenic, monocultures of S. obliquus and N. oceanica because we aimed to establish one freshwater (S. obliquus) and one seawater (N. oceanica) microalgae-driven carbon capture platform. Among the strains we tested, S. obliquus and N. oceanica are top candidates for freshwater and seawater microalgae, respectively. Moreover, our previous work has shown that non-axenic, monocultures of N. oceanica12 and S. obliquus17 are highly effective in mitigating carbon emission from power plant flue gas while also rapidly consuming NOx emissions.
2.2. Goal and scope definition
This analysis focuses on the novel algae production process to produce algal biofuels and deliver CO2 fixation benefits. Fig. 1 shows the detailed configuration incorporating the baseline and sensitivity cases. For the baseline configuration (shown via colored boxes), the algae capture the CO2 present (6–12%) in the power plant flue gases coming from the combustion of natural gas or biogas for its cultivation. The system boundaries include the cultivation of the algal biomass – S. obliquus, for the baseline configuration pathway – in a single PBR. Provision of light, nutrients and water is accounted for in this analysis. The cultivated algal biomass is dewatered and then converted to biocrude via hydrothermal liquefaction (HTL), followed by its upgrading to renewable diesel. This baseline pathway is primarily aimed at liquid fuel production (Fig. 1). Waste heat recovery produces electricity in the baseline configuration pathway to offset the power demand of the LED lights and induced motor loads. The primary functionality of the system described in Fig. 1 is transportation fuel. The functional unit (FU) is 1 MJ of algae biofuel for the baseline configuration's GHG results and 1 GGE of fuel for the economic costs. Alternative functional units are also described for individual biofuel and biochar pathways.
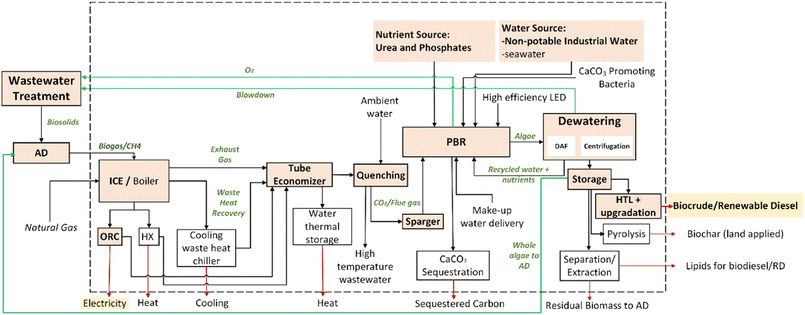 |
| Fig. 1 System boundary for the LCA and TEA baseline and sensitivity configurations evaluated in the study. The baseline configuration is shown via colored boxes with bold text, while the sensitivity cases are shown in monochromatic boxes. Green arrows pertain to the reuse/recycle of resources. AD – Anaerobic Digestion, ICE – Internal Combustion Engine, ORC – Organic Rankine Cycle, PBR – photobioreactor, HTL – hydrothermal liquefaction, HX – heat exchanger, LED – Light Emitting Diode, DAF – Dissolved Air Flotation, CaCO3 – calcium carbonate, O2 – oxygen gas, and RD – Renewable Diesel. | |
In addition, we evaluated several sensitivities. For instance, biogas or renewable natural gas combustion produces biogenic CO2, which is considered as an alternative CO2 source. Another sensitivity is the cultivation of N. oceanica in PBR, which precipitates calcium carbonate (a form of permanent carbon sink) as a co-product. The third alternative configuration involves converting algae to biochar to prioritize carbon storage where the functional unit is 1 kg CO2 stored.
2.3. Process parameters
2.3.1. PBR for algal cultivation.
The initial CO2 loading for the PBR is calculated to be 1.83 kg CO2 stored per kg of algal biomass (dry basis).18 The CO2 provision from the flue gas involves no additional energy consumption for the separation process as the algae use flue gas directly. Algae have the potential to fix CO2 (directly) using the Calvin–Benson–Bassham pathway, even when the CO2 concentration is as low as 5–6%.19 This low level of CO2 purity is sufficient for an optimum algal growth, thus preventing the need for additional CO2 purification and pressurization steps. Some marine strains of algae use this CO2 fixation pathway for the calcification (biomineralization) process, resulting in the formation of a protective calcium carbonate layer.20 This is a substantial advantage of this process compared to several other CCU processes that require a much higher level of purity and pressurization.19 The flue gas is assumed to be transported with an additional energy penalty of 0.0116 kW h per kg CO2.
Once the CO2 feedstock is accounted for, we made several assumptions based on the algal growth pilot data from the UMCES facility. The current biomass density achieved in the reactor is 4.5 g L−1 or 32 g per m2 per day, but experimental trials have shown productivities as high as 7.1 g L−1 after adding BG11 medium on day-25. Thus, the analysis considers both these configurations in the costing study. The nutrient requirements for the algal growth were also incorporated from the pilot studies with N-nutrients equivalent to 0.42 kg HNO3 per kg algae (dry) and P-nutrients equivalent to 0.041 kg H3PO4 per kg algae (dry). The GHG emission intensity for HNO3 and H3PO4 are 0.66 kg CO2e per kg and 0.96 kg CO2e per kg based on the Greenhouse Gases, Regulated Emissions, and Energy Use in Technologies (GREET) model.
This algae cultivation setup requires 0.93 kW h of electricity consumption per dry kg of algae for the reactors, compressors and LED lights (excluding facility heating, ventilation and air conditioning). This is sourced from the U.S. grid average electricity using a CO2 emission factor of 0.43 kg CO2e per kW h.21,22 Several sensitivities are also considered later, to assess the impact of shifting to an electricity grid with lower carbon intensity. The PBR facility has been operated thus far with negligible freshwater consumption because non-potable water (plant service water) is used for make-up water needs. As such, a nominal freshwater consumption of zero is assigned.
2.3.2. Harvesting/dewatering of the algal biomass.
The second key design consideration comprises the dewatering stage following the PBR. This is carried out with a series of dissolved air floatation (DAF) and centrifugation processes. The solids capture efficiency of the DAF and centrifugation processes is assumed to be 97% and 93%, respectively. This increases to 30% solids after DAF treatment, and further to 50% solids after centrifugation of the DAF float material. Furthermore, the energy requirements for DAF and centrifugation are assumed to be 1.33 × 10−4 kW h per dry g and (3.3 kW h m−3), based on past GREET work.23 The initial algae density is assumed to be 4.5 g L−1 (or 0.45% solids), although the peak concentration from the UMCES pilot tests achieved was 7.1 g L−1. The increased productivity is depicted as a sensitivity case. The daily input for dewatering is assumed to equal the total volume of algal culture in a pilot-scale PBR of 500 L.
As noted, the immediate step following the PBR is dewatering via a two-stage process (i.e. DAF and centrifugation). Such a dewatering loop is schematically shown in Fig. 2. While these systems are efficient with solids capture rates of 97% and 93% respectively, considerable amounts of aqueous effluents are generated with low-to-moderate nutrient concentrations. This approach reuses these aqueous streams from the dewatering stage to make up the volume of the PBR to maintain 100% capacity and use the nutrients available in these effluents. The objective here is to evaluate the benefits of nutrient recycling from the dewatering loop in terms of the reduced need of nutrient inputs and carbon utilization. Assuming a 5 g per L algal density, the density of the algal biomass leaving the centrifuge is 50% solids (1 kg L−1). The recycled water loops are added to result in a return volume of 6767 L and 3.33 kg of solids (0.04% solids as residual algal biomass).
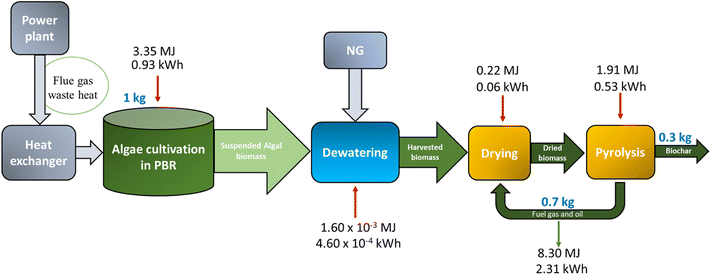 |
| Fig. 2 Schematic of slow pyrolysis of algal biomass. Energy calculations are on a per kg dry algal biomass basis. PBR: photobioreactor, NG: natural gas, and DAF: dissolved air flotation. | |
2.3.3. HTL of the algal biomass.
After the harvesting of cultivated algae, they were subjected to HTL. At high temperature and pressure, this process converts the wet algal biomass into three/four products: biocrude (hydrocarbons-rich), biochar/solids (carbon-rich) and aqueous fraction (nutrients-rich) and gases.24Table 1 shows the key process parameters for the HTL pathway. In this pathway, energy products are produced in the form of biocrude and naptha (roughly in a 65–35% proportion). For the production of 1 MJ of energy products, 0.028 kg of algae (dry biomass basis) is utilized, with a higher heating value (HHV) of 23.3 MJ kg−1.25 The biocrude is further converted to renewable diesel after upgrading with hydrogen. Hydrogen is derived from steam methane reforming of natural gas in the baseline configuration with CO2 capture (blue hydrogen). Because of the high concentration of CO2 in the SMR flue gas (40–50%), the incremental cost of capture is not considered significant.4 The aqueous co-product is recycled into the PBR.
Table 1 Process parameters for hydrothermal liquefaction (HTL)
Biomass input |
Algae biomass (kg afdw per MJ) |
2.79 × 10−2 |
Fuel products |
Renewable diesel (MJ per MJ biocrude) |
6.52 × 10−1 |
Naphtha (MJ per MJ biocrude) |
3.48 × 10−1 |
Total (MJ fuels) |
1.00 × 100 |
Energy inputs |
Electricity demand (kW h MJ−1) |
1.07 × 10−2 |
Natural gas (utility) (MJ per MJ) |
1.58 × 10−1 |
Natural gas (H2 production) (MJ per MJ) |
2.06 × 10−1 |
Other inputs |
HT catalyst (HTL) (kg MJ−1) |
1.09 × 10−5 |
Hydrocracking catalyst (HTL) (kg MJ−1) |
8.11 × 10−8 |
Na2CO3 (kg MJ−1) |
1.08 × 10−2 |
Boiler chemicals (kg MJ−1) |
1.02 × 10−7 |
Cooling tower chemicals (kg MJ−1) |
3.71 × 10−7 |
Water (process demands) (gal per MJ) |
5.80 × 10−3 |
2.3.4. Slow pyrolysis of the algal biomass.
Slow pyrolysis prioritizes carbon storage in place of liquid fuel production and may play an important role in delivering a dual effect i.e., carbon dioxide removal from the atmosphere and transfer of this carbon into soil for improved soil health. The literature on algae pyrolysis shows that the primary product from slow pyrolysis is biochar. Roughly 20–35% of the dry biomass gets converted into biochar, with the rest converted into fuel oil and gas.26 Accordingly, the key process parameters for slow pyrolysis are summarized in Table 2. We nominally assume a 30% biochar yield in line with the literature. It is further assumed that 80% of the carbon in the biochar gets permanently stored, while the rest is emitted over a period of 30 years.27 Based on regression estimates from Cheng et al.26 about 40% of the carbon from the algae and 50% of energy content are fractionated in the form of biochar. Algal biomass has an energy content of 16.5 MJ kg−1 (dry biomass basis). Assuming the product ratios mentioned above, 8.2 MJ per kg of algae (dry biomass basis) is fractionated into the biochar and the rest is fractionated into fuel oil and gas. Algae have high moisture content (80–92%)24 and require considerably high drying energy as compared to other feedstocks assumed in GREET (e.g., corn stover or forest residue). Cheng et al.26 provides an empirical relationship which results in an energy requirement of 7.8 MJ per kg algae (dry biomass basis) for reducing the moisture content from 80% to 10%.26 In addition, the pyrolysis step itself requires an additional 1.9 MJ per kg algae (dry biomass basis). With dryer feedstock, it is observed that the heat from the residual oil and gas is adequate to provide heat for drying and pyrolysis.
Table 2 Process parameters for slow pyrolysis
Biomass input |
Algae biomass (kg, dry) |
1 |
Products |
Char (kg per kg algae, dry) |
0.3 |
Fuel oil and gas (kg per kg algae, dry) |
0.7 |
Heating value of fuel oil and gas (MJ) |
8.3 |
Energy inputs |
Natural gas (pyrolysis) (MJ per kg algae, dry) |
1.9 |
Natural gas (drying) (MJ per kg algae, dry) |
0.2 |
Other inputs |
Carbon fractionated in biochar (%) |
40 |
Permanent carbon stored from biochar over 100 years (%) |
80 |
2.3.5. Waste heat recovery units.
The power plant flue gas exhaust temperature for natural gas is higher than that of coal-fired plants, estimated at 121 °C. Low to medium quality heat in the range of 60–350 °C can be reliably converted into electricity for small-scale applications.28 As such, this system utilizes an organic Rankine cycle (ORC) to convert waste heat from the flue gas into supplemental electricity. This electricity displaces U.S. grid average electricity, which has a carbon intensity of 0.43 kg CO2e per kW h. In the alternative configuration involving slow pyrolysis for biochar, the heat is reused via a heat exchanger to supplement these heating requirements.
2.4. LCA-specific assumptions
The principal output metric for the LCA pertains to the GHG emissions reported in terms of kg-CO2e per functional unit. As noted before, LCA is carried out using the GREET model developed at the Argonne National Laboratory.29 In addition to the process parameters mentioned above, GREET also allows for tuning key LCA-related parameters. Particularly, all greenhouse gas emissions for the output metrics are converted to CO2 equivalents using the global warming potential of the 5th Assessment Report of the Intergovernmental Panel on Climate Change (IPCC). The default electricity consumption is selected as the U.S.-grid average, but sensitivities are also studied to reflect the changes in the fuel mix. System expansion is used in accordance with the guidance from the National Energy Technology Laboratory.30 As such, the algal biofuel is identified as the primary product and the energy obtained from natural gas or biogas combustion is considered as the secondary product. Accordingly, the electricity from the CO2-providing process (e.g., NGCC power plant) is assumed to displace GHG emissions and other environmental burdens. The CO2 equivalent content of the calcium carbonate (0.2 kg CaCO3 per kg of dried algae) is assumed to be stored for 100 years. Notably, past studies have found that GHG emissions attributable to energy inputs and nutrients in a PBR vastly outweigh construction burdens.14,31 Therefore, environmental burdens pertaining to reactor construction and assembly are not included within the study scope.
2.5. TEA-specific assumptions
The principal output metric for the TEA is the minimum fuel selling price required to achieve a net-present value of zero. The TEA was carried out using an in-house spreadsheet based on the discounted cash flow rate of the return method. The analysis was carried out for 33 years (from year -2 to year 30). The capacity factor was zero for years -2, -1 and 0, and 75% for year 2. Year 2 is the year when the facility becomes fully operational and starts generating revenue from the sale of biofuels.
2.5.1. PBR.
The costs are reported here for a 500 L facility. The overall fixed capital investment for the facility (i.e., a 20-reactor module) is $3.73 million dollars, 70% of which is invested in year -1 and 30% in year 0. The capital investment is subject to an interest rate of 8% over 10 years of operation of the plant. Additional working capital is also invested, that is assumed to be 5% of the fixed capital investment (additional details are included in Table S1 of the ESI†). The internal rate of return is assumed to be 10%. The major operation and maintenance (O & M) expenses are the nutrients, electricity supply, and provision of CO2. CO2 is assumed to be free of cost, when the supply is from flue gas. The cost of P-nutrients is $726 per ton-P and that of the N-nutrients is $900 per t-N.
2.5.2. HTL.
The cost parameters for the HTL pathway are derived from the detailed cost report (assuming the 2022 configuration) of the Pacific Northwest National Laboratory. According to their work, the biocrude production entailed an expenditure of $1.04 per GGE while upgrading required a further $0.50 per GGE. Further details can be found in ref. 32.
2.5.3. Slow pyrolysis.
The cost of pyrolysis is highly variable based on the scale and feedstock conditions.33,34 However, assuming a scale equivalent to the algae biomass above, the capital costs of biochar production without the feedstock costs are $39 per t-dry feedstock after accounting for inflation and considering currency exchange from the stated value of GBP 22.8 per t-dry (in 2007).35,36 The feedstock costs are the same as the baseline configuration. The supplemental natural gas price for heating requirement is assumed to be $4 per MMBTU. As discussed in the future work section, these costs may be subject to uncertainty.
2.5.4. Other system costs.
The capital cost of dewatering via DAF and centrifuge is $5000 per MGD and $12600 per MGD as per the Algae Harmonization Report.37 Energy costs for the process are based on the electricity price of $69 per MW h. The costs for the ORC system are not directly available for the flue gas system. That said, the NREL Annual Technology Baseline indicates that the cost for a medium-grade heat system would be $67–74 per MW h. We have assumed a nominal value of $70 per MW h.38
3. Results and discussion
We have started the presentation of the findings with a discussion of liquid fuel production pathway (functional unit = 1 MJ renewable diesel). This begins with an evaluation of the baseline HTL configuration, followed by sensitivity considerations. Subsequently, the carbon storage pathway via biochar (functional unit = 1 g CO2 stored) is evaluated. LCA and TEA results are presented in parallel for these pathways.
3.1. GHG emissions for liquid fuel production pathways
While it is known that the algal system takes up 1.83 kg CO2e per kg-dry algae, it is imperative to evaluate the net emissions after accounting for the other life cycle emissions and displacement credits. For instance, a past analysis by Wilson et al. showed a similar gross uptake (1.76 kg CO2e per kg dry algae), of which 26% was stored from a life cycle perspective.15Fig. 3 shows the net GHG emissions from the baseline HTL configuration for freshwater algae assuming that the flue gas is sourced from fossil CO2 and electricity is supplied from the current U.S. average grid.
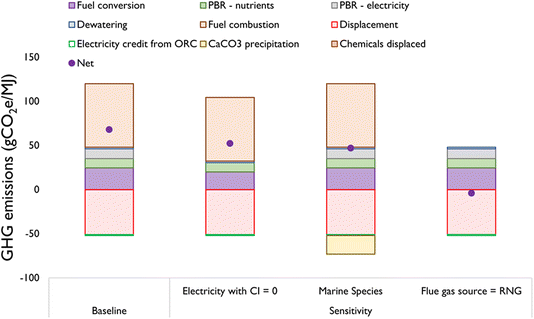 |
| Fig. 3 Net greenhouse emissions for algae biofuels in functional units of 1 MJ liquid biofuel. Here, the positive bars depict emissions throughout the life cycle while the negative bars represent displacement credits. These are added to compute net greenhouse gas emissions. The baseline corresponds to the freshwater species, fossil source of CO2 and current U.S. grid and impact of individual changes are shown as sensitivities. PBR: photobioreactor; CI: carbon intensity; RNG: renewable natural gas. | |
The net emissions for the baseline configuration, microalgae to HTL, are 68 g CO2e per MJ, which is represented by the dot within the “Baseline” bar chart. This amounts to a 31% reduction compared to the fossil diesel baseline of 98 g CO2e per MJ. The key source of emissions result from the eventual combustion of renewable diesel (72 g CO2e per MJ). The PBR inputs result in a total of 11 g CO2e per MJ out of which 51% is due to electricity requirements for running the compressors and PBRs, while the rest is for nutrient supply (after accounting for recycle from the dewatering loop). Energy requirements for HTL (with upgrading) and dewatering (from DAF and centrifugation) result in additional emissions of 25 g CO2e per MJ and 2 g CO2e per MJ algae respectively. The CO2 is sourced from natural gas combustion (6% CO2), which has a similar emissions intensity to the current U.S. grid average. As such, 51 g CO2e per MJ is credited towards the net emissions. In this way, the system expansion approach reveals nearly identical results to the so-called ‘incremental approach’.30 Additionally, the ORC system produces additional electricity which is credited with 1 g CO2e per MJ algae.
This baseline, and all algal product pathways described hereafter, also generate pure O2, a by-product of photosynthesis, and recycle N- and P- nutrients within the dewatering recycle loop along with algal biomass residuals. The former is vented during all of the experimental test runs; thus the O2 impacts on TEA or LCA of the wastewater treatment plant are not included in this evaluation. The latter leads to a reduction in the nutrient requirement per kg-dry algae since the recycled nutrients are accounted for as nutrient credits.
The second bar pertains to a sensitivity configuration where the electricity assumed to have a end-of-pipe carbon intensity of zero (i.e., derived from nuclear, geothermal, solar or wind). Here, we remain technologically agnostic regarding the exact grid configuration. Both the PBR and HTL processes require considerable electricity input. When these are decarbonized, the net emissions reduce to 52 g CO2e per MJ from 68 g CO2 per MJ. This is achieved through a reduction at the PBR stage by 11 g CO2e per MJ and at the HTL stage by 4 g CO2e per MJ, compared to the baseline configuration.
The third bar represents the cultivation of marine algal species, Nannochloropsis oceanica (IMET1). Here, the key benefit compared to the baseline configuration is the additional carbon storage in the form of CaCO3 precipitation. Pilot data show that 1600 g CaCO3 is precipitated per kg algae (dry). This corresponds to 24 g CO2 per FU, resulting in net emissions of 44 g CO2e per MJ. The CaCO3 yield in the presence of 0.02 M sodium bicarbonate has been demonstrated in previous work by our group.16
The fourth bar in Fig. 3 represents the HTL baseline configuration emissions when the flue gas is sourced from biogas or RNG. Here, most of the emission components are the same. That said, the combustion emissions that are considered zero are biogenically derived. Moreover, the CO2 providing process results in slightly higher emissions due to higher fugitive methane emissions in RNG as compared to fossil natural gas. Lastly, assuming RNG pipeline quality of 97% methane, the algal growth rates are reduced proportionally. As such, the net emissions here are −4 g CO2e per MJ algae. This configuration, accordingly shows that, decoupling of fossil carbon is necessary for achieving carbon-neutral algae biofuels, as also evidenced by our past work.39
Comparing the life cycle efficacy of this system with that from Wilson et al.15 reveals some similarities. While Wilson et al. did not consider any conversion of the algal biomass or the subsequent combustion of its derivatives, the highest emissions in their case resulted from nutrient requirements followed by electricity needs for compressors. This is similar to our analysis. That said, the overall nutrient and electricity requirements are lesser for this system. Moreover, one of the sensitivity approaches in Fig. 1 involves additional CO2 fixation via CaCO3 precipitation as well as electricity credits from the ORC. As such, the net CO2 fixation from a life cycle perspective (without accounting for fuel conversion and combustion to maintain parity with Wilson et al.'s system boundary) is 54% of the gross CO2 uptake, which is more than double the rate reported by Wilson et al. (26%).15 When additional CaCO3 storage is accounted for in the case of the marine strain, the net uptake increases to 62%.
These results for liquid fuel are important from the point of view of incentivizing these technologies. For instance, the California Low Carbon Fuel Standard (LCFS) requires a 60% reduction in GHG emissions from current gasoline emissions to be eligible for reduction certifications.40 In this vein, the sensitivity pertaining to biogenic CO2 shows the greatest influence. Thus, we may conclude that long-term pathways compatible with the LCFS would need to use biogenic carbon preferably from RNG exhaust or alternatively, CHP exhaust from biomass combustion.
3.2. Costs for liquid fuel production pathways
For discussion of the costs, we have focused more on the PBR stage because it relies on engineering design data from our pilot setup. Other costs, which are obtained from the secondary literature, are not sub-categorized as their discussion has been carried out elsewhere. As with the LCA, we evaluate the baseline configuration followed by other sensitivities (Fig. 4). These sensitivities are slightly different from those in Fig. 3 as some factors affect that GHG emissions may not affect the TEA (e.g., fossil NG versus RNG flue gas).
 |
| Fig. 4 Cost results for algae biofuels in functional units of 1 MJ liquid biofuel. The baseline here corresponds to productivity of 32 g per m2 per day and assumes freshwater algal species. Individual sensitivities then show the influence of increased productivity (to 49 g per m2 per day) and marine species. RD: renewable diesel; PBR: photobioreactor; ORC: organic Rankine cycle; O & M: operations & maintenance; GGE: gallon of gasoline equivalent. | |
The cost of renewable diesel production in the baseline configuration is $16.6 per GGE. Out of these costs, $13.9 per GGE originates from the PBR system while the remaining comes from upstream and downstream processes. The capital cost for the PBR contributes $6.7 per GGE, while fixed operating costs add $4.6 per GGE. Electricity and nutrient costs are $1.4 per GGE and $1.2 per GGE respectively, assuming an electricity price of $69 per MW h and nutrient costs of $412 per t-dry.
As the majority of the costs are concentrated on the PBR end, increased algal concentration from 4.5 g L−1 to 7.1 g L−1 can facilitate lower costs for the liquid fuels. Here, the reduced capital, fixed and electricity costs for the more productive PBR results in a reduction of the liquid fuels costs to $12.1 per GGE. At baseline productivity, the marine species add more logistical costs to the PBR, with total liquid fuel costs being $16.8 per GGE. This is, however, offset by the large carbon storage by the calcium carbonate precipitation.
These costs are substantially higher than the current diesel price (US average: $3.7 per GGE). However, it may not be a fully apples-to-apples comparison for multiple reasons. Primarily, the scale at which the results are reported here correspond to a pilot or demonstration scale. The market price of diesel is projected to grow at a compounded annual growth rate of 3% while the price of algae biofuels would nominally decrease with increased commercialization. With higher commercialization, economies of scale are anticipated to set in. On the other hand, the market price of fossil diesel comprises taxes, royalties and other margins not included in the estimates for algae biofuels.
For comparison with the past study by Wilson et al.15 it is also important to discuss the cost of production of 1 t-dry algae. It is seen that the baseline productivity leads to costs of $4555 per t-dry algae (not including fuel conversion and combustion for parity with Wilson et al.'s system boundaries) while improved productivity can result in algae production at $3092 per t-dry algae. Wilson et al. showed that their lowest cost converged to $2322 per t-dry. This shows that the system studied in this paper is comparable in costs to the current state-of-the-art. PBR-based algal systems are currently substantially more expensive than open pond algae cultivation, which ranges from $400–110 per t-dry.41 However, such processes often require higher-purity CO2, as well as extensive land and freshwater requirements – which are correspondingly reflected in the GHG emissions.
3.3. Pathway prioritizing carbon storage via biochar
The baseline configuration assumes that HTL will be used to convert the algae into liquid fuels. That said, there may be alternative uses of algal biomass. Patrizio et al. showed the tradeoffs between using biomass for energy production versus carbon storage.42 Indeed, future modeling scenarios differ in the projected share of liquid fuels in the energy mix, based on the extent to which various categories of transport may be electrified or shifted to other energy carriers.43 In case the demand for liquid fuel can be adequately addressed using waste biomass resources or e-fuels, algal biomass may also supplement carbon storage. In such a configuration, microalgae biomass is converted to biochar using slow pyrolysis. Pyrolysis is a heat-intensive process. Thus, the waste heat available from the flue gas is used for the drying and pyrolysis processes, instead of being converted to electricity. As this pathway prioritizes carbon storage, the functional unit is chosen as 1 g CO2 stored by algae using photosynthesis.
Fig. 5A shows the life cycle GHG emissions for the pyrolysis configuration which prioritizes carbon storage for the two flue gas sources evaluated. When fossil natural gas is treated as the CO2 source, each unit of CO2 fixed by the algae corresponds to GHG emissions of 1.2 g CO2e. This is comparable to post-combustion CO2 capture via solvents. However, when the CO2 is captured from a biogenic source, the additional emissions are 0.49 g CO2e per FU.
 |
| Fig. 5 A) Net GHG emissions and B) system costs for algal-derived biochar in functional units of 1 g CO2 fixed via slow pyrolysis. Here, the baseline system consists of freshwater algae with a productivity of 32 g per m2 per day using fossil CO2. Key sensitivity in panel (A) is the use of biogenic CO2, while that in panel (B) is the increased productivity. PBR: photobioreactor; NG: natural gas; RNG: renewable natural gas; O & M: operation and maintenance. | |
The costs of carbon mitigation via this pathway are estimated at $5410 per t-CO2 as shown in Fig. 5B. These are substantially higher than the costs of carbon removal through most other pathways, including pyrolysis with other feedstocks. Again, these costs of storage should not be directly compared to other systems for which costs are reported at a commercial scale. For instance, Shackley et al.36 reported that the average cost of feedstock provision is $180 per t. Given the current scale of the PBR, the feedstock production costs are >$4500 per t-dry algae (corresponding to $4928 per t-CO2). In addition, dewatering adds another $426 per t-CO2 to the system. The capital costs of slow pyrolysis and supplemental natural gas are comparable at an estimated $57 per t-CO2. Bio-oil and fuel gas revenues are not shown in the figure since they are consumed internally.
Even at an increased productivity of 49 g per m2 per day, the costs of carbon mitigation decline only marginally to $4016 per t-CO2. Based on past work on pyrolysis, we conclude that cost reductions in the PBR setup alongside accounting for the holistic benefits of biochar, e.g., soil organic carbon, fertility and nutrient retention may aid in reducing these costs. This is, however, outside the scope of this paper.
3.4. Comparison with prior work
As noted in the introduction, the key aim of this study was to elicit system-level insights for the PBR and fuel conversion. To do so, we have compared the findings from the present system with four prior studies (Table 3). Systems analysis of PBRs is not new but has evolved with the emergence of more pilot data. For instance, Davis et al.46 compared PBR operation with open raceway ponds. They found that the costs of green diesel production (using the extraction/separation pathway) was more than double that of open raceway ponds. Their work, however, acknowledged the need for improved process data to refine these results. Similar assumptions – and stated limitations – formed the basis for the work by Richardson et al., wherein the costs of biofuel production were even higher (>$30 per GGE) when considering inflation.47 Some degree of operational experience, from expert elicitation, was then incorporated by Zhu et al.45 who estimated the costs of algal biomass production at $1137 per tonne (dry). This work also acknowledged the need for pilot-scale data for PBR cost estimation. Notably, this work relies upon previous work from the Algae Farm Model for CO2 and nutrients provisioning, which indicates that the process requires medium-to-high purity CO2. More recent studies by Gurreri et al.44 and Wilson et al.15 are at a comparable scale with this study. Gurreri et al. found low productivity and in turn, high GHG emissions (153 g CO2e per g [dry]). Furthermore, the study comprised of a LCA only without costing results. As such, Wilson et al. provided the closest analog to our work as evidenced by a near-identical baseline productivity of 32 g per m2 per day. The costs for their system are comparable, although slightly lower costs could be partially attributable to the larger scale. That said, the net GHG emissions for the present system are notably lower. This is due to the lower fertilizer consumption (owing to the discharge loop) and the use of LED lighting. It may be noted that these comparisons are based on the reported results and are not completely harmonized.
Table 3 Comparison of this study's findings with prior LCAs/TEAs on PBRs
Study |
Unit |
This study |
Gurreri et al.44 |
Wilson et al.15 |
Zhu et al.45 |
Davis et al.46 |
System boundary |
|
Flue gas to renewable diesel (and biochar as an additional pathway) |
PBR plant only |
Flue gas to algal biomass |
PBR only |
Flue gas to renewable diesel |
Scale per reactor |
L |
500 |
1440 (per tube) |
1700 (per tube) |
50 (per bag) |
|
Productivity |
g per m2 per day |
32–49 |
0.15 |
32.1 |
25 |
25 |
Reactor type |
|
Column airlift |
Tubular horizontal |
Tubular vertical |
Vertical flat-bag |
Tubular |
Biomass production cost |
$ per tonne (dry) |
3100–4500 |
LCA only |
2322 |
1137 |
|
Biofuel production cost |
$ per GGE |
12.1–16.9 |
LCA only |
N.A. |
N.A. |
18.1 |
GHG emissions for PBR only, excluding carbon uptake |
g CO2e per g (dry) |
1.07 |
153 |
1.46 |
TEA only |
TEA only |
4. Conclusions and future work
In this paper, we discussed the GHG implications and the costs of a novel PBR system for algae production and illustrated two potential end uses. The key advantage of this system is that it is directly able to utilize flue gas. Based on experimental findings and updated LCA methodology from NETL, we find that the costs of this system are comparable to other PBRs studied in the literature, coupled with lower GHG emissions. The costs of algae biofuel production range from $12–16 per GGE at the current pilot scale. Depending on whether the source of the carbon is fossil or biogenic, the net emissions are 68 g CO2e per MJ and −4 g CO2e per MJ respectively. If the marine algae species is used instead of the freshwater species, it offers an additional 16 g CO2e per MJ carbon fixation in the form of calcium carbonate. The slow pyrolysis pathway offers near-zero or negative emissions depending on whether the flue gas source is fossil or biogenic. As such, it may be treated as a form of carbon dioxide removal. However, the costs of this pathway exceed $5000 per t-CO2 and would need to decline to be competitive with other biochar systems.
We anticipate substantial cost reductions for the system. While early system productivity was 32 g per m2 per day, system optimization resulted in a productivity of 49 g per m2 per day, resulting in a cost reduction of nearly 25%. It is also notable that the current system is at a pilot scale, en route to a commercial scale system of 6800 L. While cost estimates for such a system are not readily available with us, a back-of-the-envelope calculation suggests that biofuel costs could fall below $10 per GGE. At such a stage, these costs would be comparable to the estimates for open-raceway ponds. Even assuming a conservative sixth-tenth rule for capital costs and a 30% reduction in fixed O & M costs,48 the system costs would be reduced by $6 per GGE. For the pyrolysis pathway, a holistic accounting of benefits via soil organic carbon, fertility and nutrient retention, is imperative to arrive at more realistic system costs.
We have also identified three areas for future work. First, this system can be used to directly capture flue gas from low-to-moderate purity CO2 sources. Thus, it is an analogue to post-combustion CO2 capture from power plants. Future work can also compare the life-cycle efficacy of this system with solvent-based or membrane-based capture. Second, life cycle inventory for construction and assembly related emissions have been excluded. This was done because past studies have shown that emissions attributable to energy inputs and nutrients in a PBR vastly outweigh construction burdens.14,31 Monari et al. concluded that contributions from construction materials in a PBR are negligible.49 This is particularly the case as the share of energy inputs in a PBR to the overall life cycle inventory is much higher than in the case of open raceway ponds.50 That said, future studies could incorporate these factors depending on regional contexts. Third, while this study considers monocultures, mixed cultures could have competitive advantages over monocultures in some cases, and future work will test different combinations of monocultures.
Data availability
Process parameters were derived directly from experimental findings of co-authors from the University of Maryland Center for Environmental Science and HY-TEK Bio, LLC (https://doi.org/10.1016/j.jcou.2024.102669). Inventory and costing data are provided within the manuscript (Tables 1, 2 and Fig. 2) and the ESI material (Table S1).† Life cycle emission factors for electricity, nutrients and biomass conversion can be found in the open-access GREET model developed at the Argonne National Laboratory (https://greet.anl.gov).
Conflicts of interest
There are no conflicts to declare.
Acknowledgements
The research effort was supported by the Office of Fossil Energy and Carbon Management of the U.S. Department of Energy (DOE) under contracts DE-FE0031914 and DE-FE0032188. The authors thank Dr Lei Hong, Project Manager, Carbon Utilization & Storage Team, Carbon Management Program, DOE. The views and opinions of the authors expressed herein do not necessarily state or reflect those of the U.S. Government or any agency thereof. Neither the U.S. Government nor any agency thereof, nor any of their employees, makes any warranty, expressed or implied, or assumes any legal liability or responsibility for the accuracy, completeness, or usefulness of any information, apparatus, product, or process disclosed, or represents that its use would not infringe privately owned rights. Thanks are also due to Dr Fangwei Cheng and Dr Hongxi Luo for suggestions pertaining to pyrolysis heat calculations.
References
- C. Hepburn, E. Adlen, J. Beddington, E. A. Carter, S. Fuss, N. Mac Dowell, J. C. Minx, P. Smith and C. K. Williams, The Technological and Economic Prospects for CO2 Utilization and Removal, Nature, 2019, 575(7781), 87–97 CrossRef CAS PubMed.
- C. Posten and G. Schaub, Microalgae and Terrestrial Biomass as Source for Fuels—a Process View, J. Biotechnol., 2009, 142(1), 64–69 CrossRef CAS PubMed.
- M. J. Walsh, L. G. Van Doren, D. L. Sills, I. Archibald, C. M. Beal, X. G. Lei, M. E. Huntley, Z. Johnson and C. H. Greene, Algal Food and Fuel Coproduction Can Mitigate Greenhouse Gas Emissions While Improving Land and Water-Use Efficiency, Environ. Res. Lett., 2016, 11(11), 114006 CrossRef.
- L. Ou, S. Banerjee, H. Xu, A. M. Coleman, H. Cai, U. Lee, M. S. Wigmosta and T. R. Hawkins, Utilizing High-Purity Carbon Dioxide Sources for Algae Cultivation and Biofuel Production in the United States: Opportunities and Challenges, J. Clean. Prod., 2021, 321, 128779 CrossRef CAS.
- X. Wang, Y. Zhang, C. Xia, A. Alqahtani, A. Sharma and A. Pugazhendhi, A Review on Optimistic Biorefinery Products: Biofuel and Bioproducts from Algae Biomass, Fuel, 2023, 338, 127378, DOI:10.1016/j.fuel.2022.127378.
- J. R. Cruce, A. Beattie, P. Chen, D. Quiroz, M. Somers, S. Compton, K. DeRose, B. Beckstrom and J. C. Quinn, Driving toward Sustainable Algal Fuels: A Harmonization of Techno-Economic and Life Cycle Assessments, Algal Res., 2021, 54, 102169 CrossRef.
- S. Thanigaivel, S. Vickram, N. Dey, G. Gulothungan, R. Subbaiya, M. Govarthanan, N. Karmegam and W. Kim, The Urge of Algal Biomass-Based Fuels for Environmental Sustainability against a Steady Tide of Biofuel Conflict Analysis: Is Third-Generation Algal Biorefinery a Boon?, Fuel, 2022, 317, 123494, DOI:10.1016/j.fuel.2022.123494.
- M. D. Somers and J. C. Quinn, Sustainability of Carbon Delivery to an Algal Biorefinery: A Techno-Economic and Life-Cycle Assessment, J. CO2 Util., 2019, 30, 193–204 CrossRef CAS.
-
L. Qin, Md. A. Alam and Z. Wang, Open Pond Culture Systems and Photobioreactors for Microalgal Biofuel Production, in Microalgae Biotechnology for Development of Biofuel and Wastewater Treatment, ed. Md. A. Alam and Z. Wang, Springer Singapore, Singapore, 2019, pp. 45–74, DOI:10.1007/978-981-13-2264-8_3.
- A. F. Clarens, H. Nassau, E. P. Resurreccion, M. A. White and L. M. Colosi, Environmental Impacts of Algae-Derived Biodiesel and Bioelectricity for Transportation, Environ. Sci. Technol., 2011, 45(17), 7554–7560 CrossRef CAS PubMed.
- R. J. Powell and R. T. Hill, Rapid Aggregation of Biofuel-Producing Algae by the Bacterium Bacillus Sp. Strain RP1137, Appl. Environ. Microbiol., 2013, 79(19), 6093–6101 CrossRef CAS PubMed.
- Y.-Y. Lee, L. Jonas, R. Hill, A. Place, G. Silsbe, S. Hunsicker, E. North and Y. Li, Engineering Whiting Events in Culture: A Microalgae-Driven Calcium Carbonate and Biomass Production Process at High pH and Alkalinity with the Marine Microalga Nannochloropsis Oceanica IMET1, J. CO2 Util., 2024, 80, 102669 CrossRef CAS.
- C. W. Gee and K. K. Niyogi, The Carbonic Anhydrase CAH1 Is an Essential Component of the Carbon-Concentrating Mechanism in Nannochloropsis Oceanica, Proc. Natl. Acad. Sci. U. S. A., 2017, 114(17), 4537–4542 CrossRef CAS PubMed.
- T. M. Mata, M. Cameira, F. Marques, E. Santos, S. Badenes, L. Costa, V. V. Vieira, N. S. Caetano and A. A. Martins, Carbon Footprint of Microalgae Production in Photobioreactor, Energy Procedia, 2018, 153, 432–437 CrossRef CAS.
- M. H. Wilson, A. Shea, J. Groppo, C. Crofcheck, D. Quiroz, J. C. Quinn and M. Crocker, Algae-Based Beneficial Re-Use of Carbon Emissions Using a Novel Photobioreactor: A Techno-Economic and Life Cycle Analysis, BioEnergy Res., 2021, 14, 292–302 CrossRef CAS.
- L. Jonas, Y.-Y. Lee, R. Mroz, R. T. Hill and Y. Li,
Nannochloropsis Oceanica IMET1 and Its Bacterial Symbionts for Carbon Capture, Utilization, and Storage: Biomass and Calcium Carbonate Production under High pH and High Alkalinity, Appl. Environ. Microbiol., 2025, 91(5), e00133–25, DOI:10.1128/aem.00133-25.
- F. Jiao, K. Ramarui, C. He, E. W. North, Y. Li and F. Chen, Impact of Salinity on Morphology, Growth, and Pigment Profiles of Scenedesmus Obliquus HTB1 under Ambient Air and Elevated CO2 (10%) Conditions, Algal Res., 2025, 104027 CrossRef.
- S. P. Singh and P. Singh, Effect of CO2 Concentration on Algal Growth: A Review, Renew. Sustain. Energy Rev., 2014, 38, 172–179 CrossRef CAS.
- H.-J. Ho, A. Iizuka and E. Shibata, Carbon Capture and Utilization Technology without Carbon Dioxide Purification and Pressurization: A Review on Its Necessity and Available Technologies, Ind. Eng. Chem. Res., 2019, 58(21), 8941–8954, DOI:10.1021/acs.iecr.9b01213.
- M. Blondeau, M. Sachse, C. Boulogne, C. Gillet, J.-M. Guigner, F. Skouri-Panet, M. Poinsot, C. Ferard, J. Miot and K. Benzerara, Amorphous Calcium Carbonate Granules Form Within an Intracellular Compartment in Calcifying Cyanobacteria, Front. Microbiol., 2018, 9, 1768, DOI:10.3389/fmicb.2018.01768.
- T. Ghosh, W. W. Ingwersen, M. Jamieson, T. R. Hawkins, S. Cashman, T. Hottle, A. Carpenter and K. Richa, Derivation and Assessment of Regional Electricity Generation Emission Factors in the USA, Int. J. Life Cycle Assess., 2023, 28(2), 156–171 CrossRef PubMed.
- S. Koebrich, J. Cofield, G. McCormick, I. Saraswat, N. Steinsultz and P. Christian, Towards Objective Evaluation of the Accuracy of Marginal Emissions Factors, Renew. Sustain. Energy Rev., 2025, 215, 115508 CrossRef CAS.
- E. D. Frank, A. Elgowainy, J. Han and Z. Wang, Life Cycle Comparison of Hydrothermal Liquefaction and Lipid Extraction Pathways to Renewable Diesel from Algae, Mitig. Adapt. Strategies Glob. Change, 2013, 18, 137–158 CrossRef.
- F. Naaz, A. Bhattacharya, K. K. Pant and A. Malik, Investigations on Energy Efficiency of Biomethane/Biocrude Production from Pilot Scale Wastewater Grown Algal Biomass, Appl. Energy, 2019, 254, 113656, DOI:10.1016/j.apenergy.2019.113656.
- J. Zhang, Y. Zhu, T. Hawkins, B. Klein, A. Coleman, U. Singh, R. Davis, L. Ou, Y. Xu and S. Kar, Saline Microalgae Cultivation for the Coproduction of Biofuel and Protein in the United States: An Integrated Assessment of Costs, Carbon, Water, and Land Impacts, Sustain. Energy Fuels, 2025, 9, 1859–1870, 10.1039/D4SE01423E.
- F. Cheng, H. Luo and L. M. Colosi, Slow Pyrolysis as a Platform for Negative Emissions Technology: An Integration of Machine Learning Models, Life Cycle Assessment, and Economic Analysis, Energy Convers. Manage., 2020, 223, 113258 CrossRef CAS.
- Z. Wang, J. B. Dunn, J. Han and M. Q. Wang, Effects of Co-Produced Biochar on Life Cycle Greenhouse Gas Emissions of Pyrolysis-Derived Renewable Fuels, Biofuel Bioprod. Biorefining, 2014, 8(2), 189–204 CrossRef CAS.
- K. Rahbar, S. Mahmoud, R. K. Al-Dadah, N. Moazami and S. A. Mirhadizadeh, Review of Organic Rankine Cycle for Small-Scale Applications, Energy Convers. Manag., 2017, 134, 135–155 CrossRef CAS.
-
M. Wang, A. Elgowainy, U. Lee, A. Bafana, S. Banerjee, P. T. Benavides, P. Bobba, A. Burnham, H. Cai and U. R. Gracida-Alvarez, Summary of Expansions and Updates
in GREET® 2021, Argonne National Lab.(ANL), Argonne, IL (United States), 2021 Search PubMed.
-
G. Cooney, J. Benitez, U. Lee and M. Wang, Clarification to Recent Publication – Incremental Approach for the Life-Cycle Greenhouse Gas Analysis of Carbon Capture and Utilization, Technical Publications, Argonne National Laboratory, Lemont, IL, 2022, https://greet.es.anl.gov/files/ccu_lca_memo, accessed 2023-04-07 Search PubMed.
- L. B. Brentner, M. J. Eckelman and J. B. Zimmerman, Combinatorial Life Cycle Assessment to Inform Process Design of Industrial Production of Algal Biodiesel, Environ. Sci. Technol., 2011, 45(16), 7060–7067, DOI:10.1021/es2006995.
-
Y. Xu, S. J. Edmundson, Y. Zhu, T. R. Hart, D. J. Cronin, S. P. Fox, A. J. Schmidt and P. J. Valdez, 2023 Business Case Study: Hydrothermal Liquefaction of Algal Bloom Biomass, Pacific Northwest National Laboratory (PNNL), Richland, WA (United States), 2024, https://www.osti.gov/biblio/2482043, accessed 2025-05-24 Search PubMed.
- S. Shabangu, D. Woolf, E. M. Fisher, L. T. Angenent and J. Lehmann, Techno-Economic Assessment of Biomass Slow Pyrolysis into Different Biochar and Methanol Concepts, Fuel, 2014, 117, 742–748 CrossRef CAS.
- T. R. Brown, M. M. Wright and R. C. Brown, Estimating Profitability of Two Biochar Production Scenarios: Slow Pyrolysis vs. Fast Pyrolysis, Biofuels, Bioprod. Biorefin., 2011, 5(1), 54–68, DOI:10.1002/bbb.254.
-
S. H. Vetter, M. Abdalla, M. Kuhnert and P. Smith, Soil Carbon Sequestration and Biochar, in Greenhouse Gas Removal Technologies, ed. M. Bui and N. Mac Dowell, The Royal Society of Chemistry, London, 2022, pp. 194–243, 10.1039/9781839165245-00194.
- S. Shackley, J. Hammond, J. Gaunt and R. Ibarrola, The Feasibility and Costs of Biochar Deployment in the UK, Carbon Manag., 2011, 2(3), 335–356, DOI:10.4155/cmt.11.22.
-
R. E. Davis, J. N. Markham, C. M. Kinchin, C. Canter, J. Han, Q. Li, A. Coleman, S. Jones, M. Wigmosta and Y. Zhu, 2017 Algae Harmonization Study: Evaluating the Potential for Future Algal Biofuel Costs, Sustainability, and Resource Assessment from Harmonized Modeling, National Renewable Energy Lab.(NREL), Golden, CO (United States), 2018, https://www.osti.gov/biblio/1468333, accessed 2025-03-04 Search PubMed.
-
NREL, Geothermal. 2019 Annual Technology Baseline, https://atb-archive.nrel.gov/electricity/2019/index.html?t=gt#ae7xijry, accessed 2025-03-04.
- U. Singh, S. Banerjee and T. R. Hawkins, Implications of CO 2 Sourcing on the Life-Cycle Greenhouse Gas Emissions and Costs of Algae Biofuels, ACS Sustainable Chem. Eng., 2023, 11(39), 14435–14444, DOI:10.1021/acssuschemeng.3c02082.
- W. A. Scott, Cost and carbon-intensity reducing innovation in biofuels for road transportation, Energy Policy, 2025, 197, 114416, DOI:10.1016/j.enpol.2024.114416.
- S. Banerjee and S. Ramaswamy, Comparison of Productivity and Economic Analysis of Microalgae Cultivation in Open Raceways and Flat Panel Photobioreactor, Bioresour. Technol. Rep., 2019, 8, 100328, DOI:10.1016/j.biteb.2019.100328.
- P. Patrizio, M. Fajardy, M. Bui and N. Mac Dowell, CO2 Mitigation or Removal: The Optimal Uses of Biomass in Energy System Decarbonization, iScience, 2021, 24(7), 102765 CrossRef CAS PubMed.
- M. Contestabile, G. J. Offer, R. Slade, F. Jaeger and M. Thoennes, Battery Electric Vehicles, Hydrogen Fuel Cells and Biofuels. Which Will Be the Winner?, Energy Environ. Sci., 2011, 4(10), 3754–3772 RSC.
- L. Gurreri, M. C. Rindina, A. Luciano, L. Falqui, D. Fino and G. Mancini, Microalgae Production in an Industrial-Scale Photobioreactors Plant: A Comprehensive Life Cycle Assessment, Sustain. Chem. Pharm., 2024, 39, 101598 CrossRef CAS.
-
Y. Zhu, S. B. Jones and D. B. Anderson, Algae Farm Cost Model: Considerations for Photobioreactors, Pacific Northwest National Laboratory (PNNL), Richland, WA (United States), 2018, https://www.osti.gov/biblio/<?ccdc_no 1485133?>1485133<?ccdc END?>, accessed 2025-05-25 Search PubMed.
- R. Davis, A. Aden and P. T. Pienkos, Techno-Economic Analysis of Autotrophic Microalgae for Fuel Production, Appl. Energy, 2011, 88(10), 3524–3531 CrossRef.
- J. W. Richardson, M. D. Johnson and J. L. Outlaw, Economic Comparison of Open Pond Raceways to Photo Bio-Reactors for Profitable Production of Algae for Transportation Fuels in the Southwest, Algal Res., 2012, 1(1), 93–100 CrossRef.
- L. Bruni, Internal Economies of Scale with a Given Technique, J. Ind. Econ., 1964, 12(3), 175–190, DOI:10.2307/2097656.
- C. Monari, S. Righi and S. I. Olsen, Greenhouse Gas Emissions and Energy Balance of Biodiesel Production from Microalgae Cultivated in Photobioreactors in Denmark: A Life-Cycle Modeling, J. Clean. Prod., 2016, 112, 4084–4092 CrossRef CAS.
- T. Sarat Chandra, M. Maneesh Kumar, S. Mukherji, V. S. Chauhan, R. Sarada and S. N. Mudliar, Comparative Life Cycle Assessment of Microalgae-Mediated CO 2 Capture in Open Raceway Pond and Airlift Photobioreactor System, Clean Technol. Environ. Policy, 2018, 20, 2357–2364 CrossRef CAS.
|
This journal is © The Royal Society of Chemistry 2025 |
Click here to see how this site uses Cookies. View our privacy policy here.