Low-temperature highly selective Kolbe electrolysis of acetic acid in bio-oil on a stable in situ grown RuO2/TiO2 at industrial-level current†
Received
1st March 2025
, Accepted 23rd May 2025
First published on 4th June 2025
Abstract
Acetic acid (AA) is abundant in biomass pyrolysis oil (bio-oil) but its presence can hinder the use and storage of bio-oil. In this study, we developed a highly stable in situ grown ruthenium dioxide (RuO2)/titanium dioxide (TiO2) catalyst for Kolbe electrolysis (KBE) at high current densities, converting AA to ethane (C2H6) with an 82% (±5%) selectivity. The RuO2/TiO2 catalyst sustained at least 150 hours of KBE at 100 mA cm−2, converting 3300 mmol of AA into 32.6 L of C2H6 with a faradaic efficiency of 74.1%. The selectivity for C2H6 remained high even in the presence of model bio-oil-relevant oxygenated phenolics and carbonyl compounds, and real bio-oil produced from corncob pyrolysis (88% selectivity for C2H6). In situ Raman spectroscopy was performed to examine catalytic events at the electrode interface and determine the unique selectivity toward AA during the KBE reaction.
Broader context
Pyrolysis of biomass for bio-oil production offers a scalable and efficient method to utilize biomass for carbon-neutral biofuel and chemical production. However, the transportation and storage of bio-oil are hindered by the high concentration of acetic acid (AA) in raw bio-oil, which diminishes its chemical and fuel value through uncontrolled polymerization in an acidic pH environment. Unlike other reactive bio-oil components, such as aldehydes, alkenes, and ketones, AA exhibits exceptional chemical stability. Consequently, current bio-oil upgrading strategies primarily target these more reactive compounds through hydrotreatment and reductive dimerization, leaving the persistent AA issue largely unaddressed. This study presents a novel approach for selectively converting problematic AA into energy-dense ethane via Kolbe electrolysis. Specifically, we developed an in situ growth method to directly deposit RuO2 onto titanium supports, enabling sustained high current density operation (e.g., 100–300 mA cm−2), which is essential for efficient Kolbe electrolysis of AA to ethane. This electrode system demonstrates remarkable performance under acidic conditions, achieving a faradaic efficiency of 74.1% for ethane production and maintaining high ethane selectivity even in complex real bio-oil matrices. This research establishes a new valorization pathway for AA and advances bio-oil upgrading.
|
1. Introduction
The pyrolytic conversion of biomass to bio-oil has garnered considerable attention in recent decades as a promising method for producing sustainable biofuels and renewable chemicals.1–3 This interest is driven by the urgent global need for renewable energy sources due to the dwindling supply of fossil fuels and the growing impact of climate change.4 If optimized, biomass pyrolysis can convert approximately 70 wt% of dried biomass into bio-oil, with the remaining 30 wt% forming biochar and biogas.5 However, freshly produced bio-oil is chemically unstable even at room temperature because of the presence of a high amount of acetic acid (AA), ranging from 1.5 to 30 wt%, as well as various reactive aldehydes, ketones, and aromatic phenols.6,7 Evidence suggests that AA plays a significant role in the acid-catalyzed condensation of oxygenated organics, leading to increased viscosity and tar formation, which impede the storage and downstream utilization of bio-oil.8,9 Therefore, to fully preserve the original components and valuable chemicals it contains, bio-oil is typically collected and stored at low temperatures.10,11 The chemical upgrading of AA present in bio-oil is challenging because of the inherent stability of carboxyl groups and the complex composition of fresh bio-oil. Various strategies have been used to upgrade bio-oil, including hydrotreatment,12 supercritical solvent extraction,13,14 catalytic cracking,15 esterification,16,17 emulsification,18 steam reforming,19 and electrochemical hydrogenation.20 These methods mitigate AA-catalyzed polymerizations by saturating or diluting the concentration of reactive species. Although many of these approaches have been reported to improve the stability of bio-oil, they have not thoroughly addressed the issue of inherent acidity caused by AA.21 Some studies have suggested solvent extraction to remove nonacidic components, such as aromatics and alcohols. However, solvent extraction often unpreventably leaves behind many of the oxygenated organics that compromise the overall carbon content of bio-oil, and thus may not be in line with the grand scheme of sustainability. Transforming AA into a pH-neutral product could represent a promising solution. This transformation would maximize the utilization of renewable carbon content in bio-oil for biofuel production while addressing the issue of bio-oil's chemical instability, and in our case, producing a self-separating and energy-rich product, ethane (C2H6).
In this context, Kolbe electrolysis (KBE) offers a uniquely suitable approach to converting carboxylic acids into pH-neutral alkane fuel.22–24 KBE involves the one-electron electrocatalytic oxidation of a carboxylate anion to produce a carboxyl radical. This radical then undergoes decarboxylation to yield an alkyl radical (Scheme 1). The alkyl radicals can either dimerize to form alkanes or be oxidized to a carbocation, which may react with local species, such as water or carboxylate ions, to produce alcohols, known as Hofer–Moest (HM) products, or an esterified product.25 If the R-hydrocarbon chain contains more than one carbon, beta-elimination may occur to yield an alkene. To date, KBE has been mainly studied on bulk platinum (Pt) surfaces due to the robust stability and high efficiency of Pt. However, the cost and scarcity of Pt limit its scalability. Emerging studies on non-Pt KBE catalysts have mainly focused on medium-chain carboxylic acids (C5–C8).26–28 In the case of non-Pt KBE for AA, boron-doped diamond has been explored as a catalyst for treating bio-oil-derived AA. However, this approach has shown limited success, achieving a faradaic efficiency (FE) of less than 10% for the KBE product C2H6.29 Fig. S1 and Table S1 (ESI†) provide a comparative summary of several state-of-the-art catalysts that have been applied in KBE as reported in recent years.
 |
| Scheme 1 General mechanistic pathways of Kolbe electrolysis of carboxylic acid to various products. *Non-Kolbe path is only possible when R contains more than one carbon. | |
In this study, we developed a ruthenium dioxide (RuO2)/titanium dioxide (TiO2) catalyst through in situ growth on conductive titanium (Ti) support via calcination. The in situ growth method eliminates the need for binders,30–32 ensuring a strong bond between the active catalytic materials and the support. This strong bond minimizes catalyst detachment during electrocatalytic reactions. The in situ grown RuO2/TiO2 demonstrated sustained high current electrolysis over long periods, which was not achievable with binder-adhered RuO2 catalysts painted on Ti or TiO2 supports. In addition, the catalyst effectively converted AA into energy-dense C2H6 at a low temperature (5 °C) and high current densities (100–300 mA cm−2).
Our findings revealed that when optimized, the in situ grown RuO2/TiO2 catalyst could sustain over 150 hours of high oxidative current density operation at 100 mA cm−2, producing C2H6 with 88% selectivity. Even in the presence of other oxygenated compounds relevant to bio-oil, including phenolics and aldehydes, the conversion of AA to C2H6 exhibited minimal compromise, achieving an average of 61% AA conversion with 87% selectivity for C2H6 with one oxidative equivalent delivered. In situ Raman spectroscopy was performed to investigate the selectivity toward AA in the presence of competing substrates, namely furfural (FF) and phenol. The results revealed that the interaction of AA on RuO2/TiO2 could be compromised by FF, which also interacted strongly on the electrode surface. This competitive adsorption could lead to a lower conversion rate of AA. These findings provide valuable insights into the strength and limitations of the catalytic system for the KBE reaction. With its ability to operate at high current densities and in mildly acidic conditions, our in situ grown RuO2/TiO2 catalyst shows significant promise for the development of green hydrocarbon biofuels, potentially reducing global dependence on fossil feedstocks. Herein, we applied KBE to real bio-oil samples prepared from corncob pyrolysis—our in situ grown RuO2/TiO2 displayed a superb catalytic performance with a 74.6% conversion of AA and an 88% selectivity for C2H6, enabling the conversion of the problematic bio-oil-derived AA into energy-rich biofuel.
2. Results and discussion
2.1. Structure and morphology characterization of RuO2/TiO2
The RuO2/TiO2 electrode was prepared using a two-step process. First, 0.5 M Ru3+ droplets were drop-coated onto a polished Ti sheet and then subjected to annealing treatment in a static air atmosphere in a muffle furnace at a high temperature of 450 °C (Fig. 1a). The Ti support provides inherent stability and conductivity, and the inclusion of TiO2 in RuO2 enhances the catalyst's activity and chemical stability.33 The morphology of the catalyst was examined using scanning electron microscopy (SEM) and transmission electron microscopy (TEM). The RuO2/TiO2 electrode displayed a well-ordered nanorod-like structure with lengths ranging from 100 to 150 nm (Fig. 1b). The catalyst uniformly covered the Ti sheet, but exhibited a cracked appearance resembling separated continents, presumably formed during the calcination process (Fig. 1b inset). SEM–energy-dispersive X-ray spectroscopic (EDS) elemental mapping showed that Ru, Ti, and oxygen (O) were homogeneously distributed within the microparticles (Fig. 1c and Fig. S2, ESI†). The average size of grown RuO2 particles was determined using TEM (Fig. 1d inset). High-resolution TEM revealed clear lattice spacings in the RuO2 planes of 0.308 nm (110) and 0.248 nm (101) (Fig. 1e and f). These values are slightly smaller than those of pristine rutile RuO2 (p-RuO2), where the (110) and (101) planes have lattice spacings of 0.318 and 0.255 nm, respectively.34 This discrepancy might be attributable to the Ti heteroatoms doped into the RuO2 lattice. In addition, the X-ray diffraction (XRD) pattern of RuO2/TiO2 (Fig. 1g and Fig. S4, ESI†) displayed clear reflection peaks corresponding to rutile RuO2 (JCPDS 01-071-4825) and TiOx, in contrast to the pattern of the RuO2-free calcinated Ti control (JCPDS 65-9622) annealed under the same conditions. Moreover, the diffraction peaks of the in situ grown RuO2 were in high accordance with p-rutile RuO2 (Fig. S4, ESI†) as they share the same space group of P42/mnm.35 The presence of TiOx reflection peaks indicates the synchronous oxidation of Ti during the growth of RuO2. Rietveld structure refinement analysis (Table S2, ESI†) of RuO2/TiO2 indicated the presence of three species, namely RuO2, Ti2O, and Ti, which was consistent with our expectations. Moreover, the in situ grown RuO2 was highly consistent in phase with rutile RuO2 despite the presence of Ti dopant. These analyses confirmed the co-formation of RuO2 and TiO2, demonstrating the existence of a RuO2/TiO2 interface, which was further corroborated by subsequent Raman analysis. The Raman bands at 396 cm−1 (B1g), 513 cm−1 (A1g + B1g), and 636 cm−1 (Eg) corresponded to anatase-type TiO2 (Fig. S5, ESI†).36 The RuO2 Raman bands (Fig. 1h) of the RuO2/TiO2 catalyst were observed at approximately 498 cm−1 (Eg), 613 cm−1 (A1g + B2g), and 678 cm−1 (B2g),37 which exhibited blue shifts and signal enhancement compared with the p-RuO2 reference peaks, either alone or after annealing on a TiO2 surface. The red shift of the RuO2 Eg band from 509 cm−1 to 498 cm−1 indicated the presence of compressive stress, resulting from a difference in mechanical strain between the RuO2/TiO2 interface and the in situ grown RuO2 layer, providing supportive evidence for the formation of Ru–O–Ti linkages.38
 |
| Fig. 1 (a) Schematic illustration of the synthesis of RuO2/TiO2 using coating–thermolysis methods for the KBE of AA to produce C2H6 in an electrolysis cell with Pt cathode. (b) SEM image of RuO2/TiO2. (c) SEM and SEM-EDS elemental mapping images of particles dispersed on the surface of RuO2/TiO2. (d) TEM image and (e) HR-TEM image of RuO2/TiO2. (f) Lattice spacing profile measured from (e) fast Fourier transform. (g) XRD patterns of RuO2/TiO2, calcinated Ti, and the refined pattern of RuO2/TiO2. (h) Raman spectra of RuO2/TiO2, p-RuO2-TiO2, and p-RuO2. p-RuO2-TiO2 was prepared by coating RuO2 powder on Ti with a binder, followed by the same calcination step as used in the synthesis of RuO2/TiO2. (i) High-resolution XPS spectra of Ti 2p in TiO2 and RuO2/TiO2. (j) XPS analysis of O 1s in TiO2 and RuO2/TiO2. | |
The interaction between the in situ grown RuO2 and Ti support was confirmed using high-resolution X-ray photoelectron spectroscopy (XPS). Based on the calibrated C 1s peak at approximately 284.8 eV, attributed to adventitious carbon contamination, the binding energy values of Ru, Ti, and O were determined and are listed in Table S2 (ESI†). The presence of Ru4+ in RuO2/TiO2 was confirmed by the Ru 3p peaks observed at 462.0 eV (3p3/2) and 484.4 eV (3p1/2)39 as well as the Ru 3d peaks at 280.5 eV (3d5/2) and 284.7 eV (3d3/2),26 accompanied by their respective satellite peaks (Fig. S6, ESI†), suggesting the oxidation of RuCl3 to RuO2 according to the equation 2RuCl3 + 2O2 → 2RuO2 + 3Cl2. Trace Cl signal observation in the RuO2/TiO2 sample confirmed the thorough transformation of Ru3+ to Ru4+ (Fig. S7, ESI†). The Ti 2p spectrum of loading-free TiO2 showed two peaks at 458.6 eV (2p3/2) and 464.3 eV (2p1/2) with a 5.7-eV separation (Fig. 1i), confirming the presence of the Ti4+ state on the surface.40 Furthermore, the Ti 2p3/2 peak almost disappeared in RuO2/TiO2 due to the replacement of Ti–O bonds with Ru–O bonds.37 In addition, the Ti 2p1/2 and Ti 2p3/2 peaks in RuO2/TiO2 shifted to lower binding energies by 0.5 eV and 0.4 eV, respectively, when compared with RuO2-free TiO2. This shift indicated that the grown Ru4+ partially altered the chemical environment of Ti4+ sites, due to the metal–support interaction. Similar electronic characteristics of Ru and O in RuO2/TiO2 and p-RuO2 confirmed the rutile structure of the grown RuO2; the slight shift (0.2–0.3 eV) to lower binding energy in RuO2/TiO2 was due to the introduction of Ti through bridging oxygen (Fig. S6, ESI†).41 Furthermore, the significant decrease in the lattice O content in TiO2 (Table S3, ESI†) and the 0.7 eV energy shift (Fig. 1j) indicated the replacement of Ti–O bonds with Ru–O bonds on the RuO2/TiO2 interface.37 Thus, the combined evidence from XRD, Raman spectroscopy, and XPS illustrated that the metal–support interaction between the grown RuO2 and Ti led to the formation of a RuO2/TiO2 interface through bridging oxygen in the in situ grown RuO2/TiO2 catalyst.
2.2. Electrochemical characterization
2.2.1. Linear sweep voltammetry of electrocatalytic oxidation of AA.
The KBE performance of the in situ grown RuO2/TiO2 anode was evaluated and compared with those of a p-RuO2-coated Ti sheet (RuO2–Ti) and TiO2 (RuO2–TiO2). As shown in Fig. 2a, the plain Ti sheet and TiO2 barely converted any AA, indicating that RuO2 served as the active catalyst layer for the KBE. However, the unstable adhesion of p-RuO2 painted on Ti (RuO2–Ti) and TiO2 (RuO2–TiO2) resulted in poor durability, failing to sustain the reaction even at a moderate current density of 50 mA cm−2. Thus, these catalysts exhibited considerably lower AA conversion than the in situ grown RuO2/TiO2. According to the linear sweep voltammetry (LSV) curves shown in Fig. 2b, the RuO2/TiO2 could sustain a substantially higher current flow than the p-RuO2-coated RuO2–Ti and RuO2–TiO2, demonstrating superior performance over a wide range of current densities from 10 to 300 mA cm−2. Both the bare Ti sheet and TiO2 surfaces showed minimal current flow in the presence of AA, indicating their poor catalytic activity for the oxygen evolution reaction (OER) or KBE performance. The onset potential for the RuO2-deposited electrodes, whether by paint or in situ growth, was observed at approximately +1.2 V vs. Ag/AgCl. A distinctive feature of the RuO2/TiO2 is its sustained activity throughout the tested potential range up to at least 10 V vs. Ag/AgCl, reaching a current density of more than 300 mA cm−2. In addition, the effect of temperature on catalytic performance was investigated at 5, 10, 20, and 30 °C, with a focus on bio-oil upgrading (Fig. S8, ESI†).
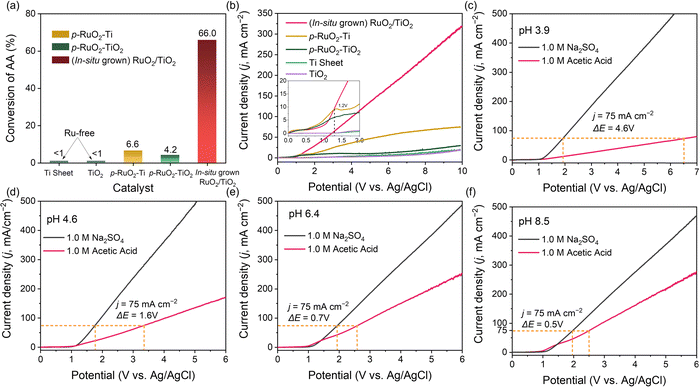 |
| Fig. 2 (a) Electrochemical performance of different RuO2-deposited electrodes in a 1.0 M AA solution at pH 4.6. (b) LSV curves of RuO2/TiO2, p-RuO2–Ti (coated on a Ti sheet), RuO2–TiO2 (coated on TiO2), Ti sheet, and TiO2 sheet in the presence of AA. (c–f) LSV curves of blank (1.0 M Na2SO4) and 1.0 M AA at pH 3.9, 4.6, 6.4, and 8.5. These LSV curves were recorded at a scan rate of 50 mV s−1 and a stirring speed of 900 rpm in a three-electrode system with Ag/AgCl serving as the reference electrode. | |
The LSV analysis revealed that the current response improved with increasing temperature, which is expected due to enhanced mass transfer.42,43 Regardless of the temperature, RuO2/TiO2 maintained its electrochemical activities without showing any signs of reaching a plateau. Although it has been reported that increasing temperature can improve the current efficiency, it also increases the energy expenditure,44 which is not consistent with the aims of sustainable development. Moreover, the ability to upgrade bio-oil-derived AA at low temperatures is advantageous because it minimizes the undesired polymerization commonly observed in bio-oil during room temperature storage. Fig. 2c–f displays the LSV findings for RuO2/TiO2 at different pH levels. All LSV data indicated that the presence of AA reduced the current response, which is consistent with the general understanding that an adsorptive layer of AA suppresses anodic activity.45 As shown in Fig. 2c–f, an increase in pH enhanced the current responses, indicating a weakening of the AA adsorptive inhibition layer. The current responses were significantly higher in the sodium sulfate AA-free electrolyte than in the AA trials across all pH environments, indicating that the OER was highly active in the absence of AA surface inhibition. The working potential differences at 75 mA cm−2 between the presence of AA (j75AA) and its absence (j75) at pH 3.9, 4.6, 6.4, and 8.5 were 4.6, 1.6, 0.7, and 0.5 V vs. Ag/AgCl, respectively. These decreasing differences in working potentials confirmed that RuO2/TiO2 became increasingly active for the OER as the pH increased.45
2.3. Systematic investigation and optimization of reaction conditions
The electrocatalytic performance of the in situ grown RuO2/TiO2 was systematically evaluated at different current densities, pH levels, temperatures, and AA concentrations. These factors affect the conversion rate and productivity of the catalytic process.46
2.3.1. Current density.
The KBE performance of the grown RuO2/TiO2 was investigated at different current densities in 1.0 M AA (pH 4.6). As shown in Fig. 3a, the conversion of AA increased from 32.8% to 66.0% as the current density rose from 10 to 150 mA cm−2 and plateaued thereafter. At low current densities below 50 mA cm−2, the conversion of AA was low, and product selectivity favored the production of HM products (Scheme 1), namely methanol (CH3OH) and formaldehyde (HCHO; Fig. 3e), rather than the Kolbe product C2H6. At 50 mA cm−2 and above, the conversion of AA increased and stabilized thereafter, and the selectivity for the Kolbe product (C2H6) reached higher than 80%. The increased yield of the Kolbe product can be attributed to the enhanced adsorption of acetate anions on the anode surface at a high working potential generated by a high current flow. The increased coverage promoted the formation of more methyl radicals (˙CH3) on the surface, facilitating their dimerization into C2H6. Conversely, low ˙CH3 coverage at low current densities (<50 mA cm−2) resulted in a lower conversion rate, with product selectivity shifting toward HM products due to insufficient ˙CH3 to promote dimerization, leading to the formation of CH3OH instead. When operating at 150 mA cm−2 or above, the selectivity for C2H6 remained consistently between 81% and 86%, which is comparable to the performance of Pt foil (92%) under similar conditions.46
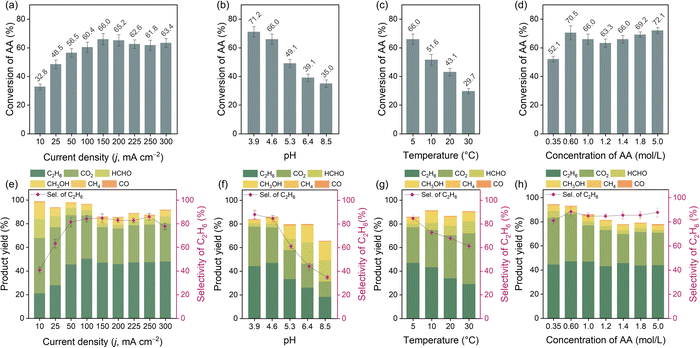 |
| Fig. 3 (a) KBE of 1.0 M AA under different current densities at 5 °C and pH 4.6. (b) KBE of 1.0 M AA at different pH levels at 5 °C and a current density of 150 mA cm−2. (c) KBE of 1.0 M AA at different temperatures at pH 4.6 with a current density of 150 mA cm−2. (d) KBE of different concentrations of AA at 5 °C and pH 4.6 with a current density of 150 mA cm−2. (e–h) Yield of products, including CH3OH, HCHO, CH4, CO2, CO, and C2H6, and selectivity for C2H6 at different current densities (e), pH values (f), temperatures (g), and concentrations (h) under controlled conditions. Error bars represent the standard error based on the combined standard deviation of the triplicate experiments. | |
2.3.2. pH.
A systematic investigation of the effects of pH revealed that both the conversion of AA and the selectivity for C2H6 were favored under acidic conditions. At pH 3.9, 71.2% of AA was converted, producing C2H6 with approximately 90% selectivity over CH3OH and HCHO (Fig. 3b and f). As the pH became more alkaline, both the conversion rate and yield of C2H6 declined considerably. The AA conversion rates at pH 4.6, 5.3, 6.4, and 8.5 were 66.0%, 49.1%, 39.1%, and 35.0%, respectively. This decreasing conversion is consistent with the LSV observations, which revealed that the OER was favored under alkaline conditions (Fig. 2). Furthermore, the selectivity for HM products increased with rising pH at the expense of C2H6. This trend can be explained by the increased coverage of hydroxy groups (−OH) on the anode surface at high pH levels, which promotes the formation of CH3OH from surface-bound ˙CH3. The CH3OH was subsequently oxidized to HCHO. To rule out the leaching of Ru species during the KBE, ICP (Inductively Coupled Plasma) was conducted to analyze the post-reaction electrolyte. There was only a trace amount (0.06 mg) of Ru detected when operating at 300 mA cm−2, while the leached amounts detected at other current densities (25–250 mA cm−2) and pH values (3.9–8.5) were negligible (Fig. S8, ESI†). The amount of Ti was below the detection limit. Overall, the results confirmed that the grown RuO2/TiO2 interface had high stability under various pH values and high current densities.
2.3.3. Temperature.
Low temperatures are beneficial for the stability of bio-oil and highly advantageous in industrial applications for bio-oil upgrading.47 However, most KBE studies have been conducted at room or elevated temperatures. For example, Klerk et al.44 performed the KBE of AA with a carbon electrode at various temperatures (10–30 °C) and observed the highest conversion of AA at 30 °C. In this study, we examined the effects of temperatures of 5, 10, 20, and 30 °C and found that AA conversion incrementally improved as the temperature decreased (Fig. 3c). The LSV curves recorded at different temperatures (Fig. S9a, ESI†) demonstrated that higher temperatures favored the OER, as indicated by a lower onset potential, which shifted from approximately 1.5 V at 5 °C to 1.0 V at 30 °C. The product distribution revealed that high temperatures shifted the product selectivity toward HM products, indicating that the increased surface coverage of –OH resulting from the OER was responsible for this shift.
2.3.4. Concentration of AA.
The effect of AA concentration on its conversion was less pronounced than those of the other experimental factors examined (Fig. 3d). A wide range of AA concentrations, from 0.35 to 5.0 M, was examined for C2H6 formation. The lower bound concentration of 0.35 M was set because it contained the minimal amount of acetate anions sufficient to sustain the reaction at 150 mA cm−2 (Table S4, ESI†). The impact of AA concentration was investigated through LSV (Fig. S8b, ESI†). The results revealed that the current response increased with the AA concentration, as expected, and the slope of each LSV curve exhibited strong linearity. At 0.35 M AA, the conversion was only 52.1% with an 80% selectivity for C2H6 (Fig. 3h). The selectivity values for CH3OH and HCHO were slightly higher than those at other concentrations. Starting at 0.6 M, the AA conversion and selectivity for C2H6 gradually improved. This improvement is consistent with the understanding that a high concentration of AA promotes the surface population of ˙CH3 radicals, thereby improving their dimerization rate for C2H6 formation. At 5 M, the conversion reached 72.1%, with a slight increase in C2H6 selectivity to 88%. These results indicated that the conversion of AA and the selectivity for C2H6 production were favorable at an AA concentration of 1.0 M and above. Furthermore, only marginal improvements were observed beyond these concentrations, presumably due to the saturation of the surface with adsorbed AA and its intermediates.
In summary, the RuO2/TiO2 anode demonstrated high efficiency in selectively converting AA under acidic conditions at a low temperature of 5 °C; both criteria are favorable to bio-oil treatment because bio-oil is naturally acidic and treatment should be conducted at low temperature to minimize the condensation reactions commonly observed at room temperature.5,9,11 Coincidentally, the low-temperature condition also suppressed the OER, which steered the reaction pathway toward the KBE of AA. Under alkaline conditions, LSV analysis revealed that the increased coverage of OH− adsorption competed with the acetate anions, diverting AA conversion toward the OER and shifting product selectivity from C2H6 to HM products. At pH 3.9, the C2H6 selectivity increased to 88% (Fig. 3f), which is comparable to the selectivity achieved with bulk Pt foil (92%) under optimized conditions.46 The RuO2/TiO2-catalyzed KBE requires a high current density of 150 mA cm−2 or above to maintain high C2H6 selectivity, due to the enhanced acetate anion coverage on the electrode surface. At the end of each KBE experiment, an increase in pH was observed (Table S4, ESI†). This finding confirmed the conversion of AA, which is essential for the bio-oil pH-neutralization scheme described in this work.
2.3.5. Stability and scaled-up investigation of KBE of AA.
The stability of the RuO2/TiO2 electrode was evaluated by performing 13 consecutive KBE trials at 150 mA cm−2. As shown in Fig. 4a and b, approximately 80% of the catalytic capacity of RuO2/TiO2 was retained even after 13 applications, and C2H6 selectivity was maintained at 80–83% throughout these trials. The used RuO2/TiO2 electrode was subjected to simple surface cleaning with deionized (DI) water and acetone, followed by oven drying for 10 minutes, before the 5th, 8th, and 11th experiments. This treatment effectively restored the catalytic performance of the used RuO2/TiO2 electrode.
 |
| Fig. 4 (a) KBE conversion of AA over 13 recycling tests using the RuO2/TiO2 electrode. (b) Product yield and selectivity of C2H6 during the recycling tests of the RuO2/TiO2 electrode. (c) Conversion of AA, product yield, and selectivity for C2H6 (d) when applying different charges during the electrooxidation of 40 mL, 28.6 wt% (5.0 M) AA using the RuO2/TiO2 catalyst in an undivided cell at pH 4.6 with a current density of 150 mA cm−2. (e) Comparison of the electrocatalytic performance between 2 cm × 2 cm Pt sheet and RuO2/TiO2 electrodes at 150 mA cm−2 in 1.0 M AA solution at pH 4.6 and 5 °C. (f) Large-scale application of the RuO2/TiO2 electrode for KBE of AA (pH 4.6) at 5 °C with 100 mA cm−2. The potential change was recorded using a three-electrode system with Ag/AgCl as the reference electrode. | |
Considering that AA accounts for 10–30 wt% of the organic content in various biomass-derived bio-oils,7,47 we conducted the KBE in an aqueous solution of 28.6 wt% (5 M) AA to evaluate the longevity of RuO2/TiO2. As displayed in Fig. 4c, the conversion of one oxidation equivalent (F × 0.2 mol, F = 96
485 C mol−1), with each C2H6 formation requiring two electrons, successfully converted 72.1% of AA with 88% selectivity for C2H6 and an FE of 63.4%. However, the continuous passage of charge did not proportionally increase the AA conversion, likely due to the depletion of available AA. Nonetheless, the C2H6 product selectivity remained above 80%.
To explore the practical application and stability of the RuO2/TiO2 anode, we conducted a scaled-up KBE test using 0.81 L of 4450 mmol AA solution. As shown in Fig. 4f, a repeating hill-shaped curve was observed throughout the trial. The initial rise in voltage was attributable to the adsorption and accumulation of acetate anions on the electrode surface, leading to the formation of a Kolbe layer at high current (100 mA cm−2, 0.8 A).48,49 This finding is consistent with that of our LSV analysis (Fig. 2), which indicated that the presence of AA shifted the onset overpotential to a more positive potential. Once most of the AA was consumed, the OER became the dominant reaction, and the potential decreased as the OER occurred at a lower onset potential than the KBE. During the scaled-up application, 3300 mmol of the 4450 mmol AA was selectively converted into 32.6 L of C2H6 with a selectivity of 88% and a total FE of 74.1%. This corresponded to each gram of RuO2 converting at least 330 moles of AA and producing 3260 L of C2H6, reaching a high turnover number (TON) of approximately 3600 (Fig. 4f). Furthermore, the working potential only increased by 0.4 V even after 150 hours at 100 mA cm−2, confirming the excellent stability of the RuO2/TiO2 anode. This stable performance is attributable to the RuO2/TiO2 interface formed by the bridging O, which was absent in the painted p-RuO2 catalyst. In addition, we benchmarked the KBE performance of the RuO2/TiO2 anode against that of a Pt plate anode under the same conditions (Fig. 4e). The two catalysts showed less than a 5% difference in AA conversion, and the product distributions were nearly identical. These findings indicate that our in situ grown RuO2/TiO2 catalyst with low Ru loading provides a cost-effective and stable alternative to commercial Pt.
To confirm the stability of the in situ grown RuO2/TiO2, post-reaction characterizations of the RuO2/TiO2 electrode were conducted. The surface of the electrodes was visibly affected after 150 hours of high-current-density electrolysis. Macroscopically, the surface of these electrodes showed some detachment. Microscopically, the catalyst appearance altered slightly from a nanorod morphology to a more flake-like morphology (Fig. S10, ESI†). In the XRD results, there was no obvious difference between the diffraction peaks before and after the reaction. This indicates that the lattice structure of RuO2/TiO2 was maintained, even after 150 hours, despite the fact that the electrode surface had undergone visible detachment during the reaction (Fig. S11, ESI†). The Raman spectra also indicated that the Ru–O–Ti structure of the RuO2/TiO2 was sustained after the reaction (Fig. S12, ESI†). Additionally, XPS analysis revealed that there was no further oxidation of the Ru to higher oxidation states (Fig. S13, ESI†). There was a moderate decrease in the content of lattice oxygen and an energy shift in the Ru 3d spectra (Table S5, ESI†) after 150 hours of reaction, indicating that part of the RuO2 species was lost during the reaction. Additionally, inductively coupled plasma–mass spectrometry (ICP-MS) analysis of the post-reaction electrolyte revealed that dissolved Ru species accounted for less than 1% of the total loaded RuO2, further corroborating its minimal dissolution under operational conditions. Moreover, we additionally performed an XPS analysis of the dropped powder of RuO2/TiO2 after the reaction (Fig. S14, ESI†). The results indicated that no over-oxidized Ru species were present. Overall, these post-reaction characterizations confirmed the stability of the RuO2/TiO2.
2.4. The mechanism of KBE on RuO2/TiO2 and its selective KBE of AA in bio-oil or bio-oil-derived oxygenated compounds
First, the reaction mechanism for KBE of AA was investigated by in situ attenuated total reflectance Fourier-transform infrared spectroscopy (ATR-FTIR). As shown in Fig. S15 (ESI†), we detected the change in the kinetics of the adsorption and consumption of the AA and acetate species (Fig. S15b, c, e and f, ESI†) with increasing potential from 0 to 10 V vs. Ag/AgCl, indicating the progress of the KBE reaction. Additionally, based on differential spectrum analysis (Fig. S15d, ESI†), the presence of C2H6 was monitored. A radical trapping agent, TEMPO, was applied during KBE to confirm the production of ˙CH3. As shown in Fig. S16 (ESI†), the addition of TEMPO did not significantly affect the conversion of AA. However, the decline in the yield of C2H6 caused by trapping of the produced ˙CH3, as observed by gas chromatography–mass spectrometry (GC–MS) analysis of ˙CH3, confirmed the production of ˙CH3 during the KBE reaction and also demonstrated that the yield of C2H6 was influenced by the presence of ˙CH3.
2.4.1. Effect of individual bio-oil-relevant oxygenated organics.
Bio-oil contains a diverse range of oxygenated organic compounds, including aldehydes, ketones, and (hetero) phenolics.20 In this study, we prepared a crude bio-oil from corncobs using fast pyrolysis at 300 °C, followed by condensation at −5 °C. The chemical composition of the resulting bio-oil was analyzed using GC–MS. The solvent extraction of the raw bio-oil using dichloromethane and ethyl acetate yielded consistent results, confirming the predominance of furans and phenolic constituents, consistent with the literature.50 The GC–MS chromatogram (Fig. S17, ESI†) and the components listed in Table S6 (ESI†) provide detailed information on the composition. Fifteen compounds, selected based on their abundance in bio-oil, were individually examined in a 1.0 M AA electrolyte for the KBE valorization of AA. We strategically used an undivided electrolyzer to minimize the resistivity caused by a membrane. A control experiment confirmed that the counter electrode cathode had a negligible effect on the product outcome. This membrane-free setup could be highly advantageous for future scale-up of electrolysis systems because it would reduce material costs and energy consumption.
As shown in Fig. 5a and b, the presence of organic additives had a negligible impact on the conversion of AA to C2H6. The conversion rate and C2H6 selectivity remained around the organic-free control level at 66.0% and 85%, respectively. FF had the strongest impact, reducing the AA conversion by 11.5% compared with the organic-free reference trial. Some organic additives produced trace amounts of discernible redox products. For example, the phenol trial (compound 1) yielded a small amount of benzoquinones, whereas FF produced some furfuryl alcohol originating from the electrochemical hydrogenation of its carbonyl group, which is consistent with our electrochemical understanding (Fig. S18 and Table S7, ESI†).43 In addition, some methylated aromatic products were observed (Fig. S19: GC chromatogram; Table S8: product identification, ESI†), presumably formed by the ˙CH3 intermediate during the KBE of AA. However, the amount of ˙CH3 involved in methylation was trivial, as indicated by the C2H6 product yield and selectivity compared with the reference control trial.
 |
| Fig. 5 (a) Conversion and (b) product yield and selectivity of C2H6 during KBE with the addition of various hydrocarbons (50 mM) in 40 mL of 1.0 M AA at a current density of 150 mA cm−2. (c–h) Raman spectra were recorded based on current variation because all KBE experiments in this study were conducted under constant current conditions. (c) Raman spectrum of 1.0 M AA and (d) FF for reference, (e) phenol for reference. (f) In situ Raman signal variation of AA with different currents. (g) In situ Raman band signal variation of FF (100 mM) in 1.0 M AA (mole ratio FF : AA = 1 : 10) at different currents. (h) In situ Raman band signal variation of phenol (100 mM) in 1.0 M AA (mole ratio phenol/AA = 1 : 10) at different currents. Open-circuit potential indicates no current applied. These in situ experiments were conducted at approximately 5 °C by cooling the solvent. ν: stretching vibration; δ: bending vibration; γ: rocking vibration; d: deformation. | |
Overall, the organic additive control experiments demonstrated that the in situ grown RuO2/TiO2 anode selectively converted AA even in the presence of a wide range of bio-oil-relevant aromatic compounds. FF reduced AA conversion by 11.5% compared with the organic-free reference trial. Considering that the impact of FF was more substantial than that of other organics, we performed an in-depth surface examination to understand how FF competes with AA for electrochemical oxidation using in situ Raman spectroscopy. Phenol was selected as a negative control because its influence on KBE was not apparent. The Raman spectra of AA, FF, and phenol were first obtained as references (Fig. 5c–e and Fig. S20, ESI†), and their vibration band assignments were obtained from previous studies.51–53
In the electrolyte containing only AA (Fig. 5f), the stretching vibration ν(C–C) bands of AA and acetate anions were observed at 892 and 926 cm−1, respectively. In addition, the CH3 deformation (d(CH3)) at 1413 cm−1 and C–O stretching vibrations (ν(C–O)) at 1554 and 1710 cm−1 were clearly visible at the open-circuit potential. When current was applied, the intensities of the 892 cm−1 (ν(C–C)), 1413 cm−1 (d(CH3)), and 1710 cm−1 (ν(C–O)) bands decreased with increasing current. In addition, two new bands appeared at 1286 and 1387 cm−1, corresponding to the bending (δ(CO2)) and stretching vibrations (ν(CO2)) of CO2, respectively, indicating the occurrence of decarboxylation at the electrode surface.54 Similar observations were made under other pH conditions, but the emergence of CO2 bands was the most pronounced at pH 8.2, likely due to the increased solubility of CO2 (Fig. S21, ESI†).
When FF was added to the AA electrolyte, the intensity of the AA peaks markedly weakened (Fig. 5g). In particular, the distinct 1554 cm−1 AA ν(C–O) band observed in the AA-only control (Fig. 5f) became barely visible in the presence of FF. Simultaneously, nearly all the Raman bands relevant to FF were observed, indicating the strong competitive adsorption of FF on the electrode surface against AA. A similar competition was observed in the constant current mode, where the spectrum mainly displayed FF peaks but not the 1554 cm−1 AA ν(C–O) band at all tested currents (Fig. S22, ESI†). The appearance of the 890 cm−1 band could correspond to either the AA 892 cm−1 (ν(C–C)) or the FF 888 cm−1 (ν(Ring
C–C)). Given its height relative to other peaks and its unchanged intensity throughout the experiment, it is more likely to have been the FF ν(Ring
C–C). Conversely, the intensity of the AA 892 cm−1 (ν(C–C)) would have decreased with increasing current, as observed in the AA-only (Fig. 5f) and AA-phenol (Fig. 5h) trials.
When phenol was added to the AA electrolyte, the 892 cm−1 (ν(C–C)) and 1554 cm−1ν(C–O) bands from AA remained visible, but the phenol peaks were not. Even the strong phenol peaks δ(C–C) at 1000 cm−1, ν(C
C) at 1606 cm−1, δ(C–H) at 1163 cm−1, and δ(C–H) 1371 cm−1 were not observed under potential (Fig. S20, ESI†). This result contrasts with the earlier observation when FF was added and indicates that the electrode surface was mainly occupied by AA (Fig. 5h). Furthermore, the 1286 cm−1 (δ(CO2)) and 1387 cm−1 (ν(CO2)) bands emerged as the current increased, resembling the scenario observed in the AA-only electrolyte (Fig. 5f). These results, including the δ(CO2) and ν(CO2) bands, were also observed under constant current mode, demonstrating their reproducibility (Fig. S23, ESI†). In summary, phenol was not as competitive as FF in adsorbing onto the electrode surface, allowing AA to be converted efficiently; this supports the results of the individual organic substrate study.
2.5. Application of RuO2/TiO2 in crude aqueous phase bio-oil
As illustrated in Fig. 6a, the KBE process was investigated in relation to AA within crude bio-oil that was pyrolyzed following a reported procedure using corncob as a feedstock.55 High-performance liquid chromatography (HPLC) analysis showed that the as-synthesized crude bio-oil contained 8.6 wt% (∼1.5 M) AA with a pH of 2.3 to 2.4 and negligible electrical conductivity (Table S4, ESI†). To prepare aqueous bio-oil for electrolysis, a pretreatment procedure (Fig. 6a) was used to remove any insoluble residues.56 Subsequently, sodium hydroxide was added to adjust the pH value to 4.4–4.5, which is favorable for the KBE conversion of AA and to provide sufficient conductivity (Table S4, ESI†). The compositional analysis of the aqueous phase revealed no significant deviations in chemical constituents when compared with crude bio-oil (Fig. S24, ESI†). The KBE conversion of AA derived from aqueous bio-oil was quantified at 74.6%, which closely approached the efficiency observed in the AA-only control electrolyte solution, with an 84.5% conversion (Fig. 6b). For C2H6, the AA control achieved 91.5% selectivity, whereas the aqueous bio-oil showed 88% selectivity (Fig. 6c). The similarity in product selectivity indicated that the presence of organic constituents in aqueous bio-oil did not significantly disrupt the C2H6 formation pathway, which is consistent with the results of the individual organic additive trials (Fig. 5b). The marginal reduction of 10% in the AA conversion rate in aqueous bio-oil compared with the AA control suggests limited interference from oxidizable organic species in the oil. LSV analysis showed a variation in the onset potential between the aqueous bio-oil and pure AA solution, with an increase in onset potential, indicating some adsorptive impedance from oxidizable components on the electrode surface (Fig. 6d). In summary, the as-prepared RuO2/TiO2 electrode demonstrated a high capability of selectively converting AA at a low temperature of 5 °C to C2H6, and the general organic components found in bio-oil did not considerably affect the reaction.
 |
| Fig. 6 (a) Illustration of the application of crude bio-oil from pyrolysis of corncobs for the selective synthesis of C2H6 through KBE. (b) Conversion of AA and (c) selectivity of C2H6 in prepared AA solution and aqueous-extracted bio-oil. (d) LSV curves for the prepared AA solution and aqueous-extracted bio-oil with the same concentration of AA. | |
3. Conclusion
We successfully fabricated a RuO2/TiO2 electrode using a facile coating–thermal deposition method that exhibited exceptionally high catalytic performance in the KBE of AA at 5 °C. The in situ grown RuO2/TiO2 interface provided enhanced stability to the electrode, allowing it to sustain high current density operation for 150 hours, outperforming the same RuO2 catalyst that was deposited by a conventional painting method. The performance is comparable to that of a conventional Pt sheet anode but only requires a mg-level loading, ∼2 mg per cm2 in our case, of the precious metal Ru for the reaction. The as-prepared RuO2/TiO2 catalyst demonstrated both high activity and stability: about 10 mg of RuO2 loading could convert at least 3300 mmol of AA and produce 32.6 L of C2H6 in a 150-hour experiment, achieving a total FE of 74.1% and an excellent TON of approximately 3600. The RuO2/TiO2 electrode could be recycled and operated at an industrial-level current density of 150 mA cm−2 (1.2 A) without apparent loss in activity. Our investigation into the application of RuO2/TiO2 for the KBE of AA under different conditions, including pH, temperature, current density, and AA concentration, revealed that low temperatures favor the conversion of AA and the production of C2H6. The reaction can be highly susceptible to alkaline pH, which promotes the OER. Under optimized conditions, AA could be selectively upgraded to C2H6, even in the presence of oxidizable organics commonly found in real bio-oil. Furthermore, we examined selectivity using individual organic components and real bio-oil prepared from corncob pyrolysis. Moreover, we conducted in situ Raman spectroscopy to examine the selective KBE of AA using FF and phenol as model competitor adsorbents. The results revealed that high concentrations of surface adsorptive species could impede the KBE conversion of AA.
The results presented in this study highlight a promising approach for upgrading bio-oil using a sustainable strategy based on the following points: (1) low-temperature operation maintains the stability of bio-oil and preserves the efficiency of KBE while suppressing water oxidation. (2) The development of a robust catalyst capable of sustaining industrial-level current densities reduces the dependence on Pt. (3) The mechanistic insights into the selective conversion of AA in complex bio-oil provide valuable guidance for the future development of bio-energy exploitation.
4. Methods
4.1. Synthesis of RuO2/TiO2 electrodes
The in situ grown RuO2/TiO2 electrode was synthesized using a thermochemical transformation method with Ru3+/Ti as the starting material based on iterative coating–thermolysis procedures. Prior to the synthesis of the RuO2/TiO2 catalyst, a 2 cm × 2 cm Ti sheet with a thickness of 0.2 mm was polished using 1000 mesh sandpaper and sonicated for 1 hour in 3 M sulfuric acid. The pretreated Ti sheet was then stored in acetone for later use. To prepare the ruthenium precursor solution, ruthenium(III) chloride hydrate (RuCl3·xH2O) was dissolved in a mixture of DI water and isopropanol in a 1
:
1 volume ratio, resulting in a 0.5 M RuCl3 solution. A total of 400 μL of the Ru3+ ink was drop-coated on both sides of the Ti sheet, and applied in 50 μL batches under a 200 °C drying lamp in an ambient environment to ensure an even distribution of the Ru3+ ink. After each coating, the sheet was calcined at 450 °C in a muffle furnace for 45 minutes. The RuO2/TiO2 electrode was obtained after calcining in air at 450 °C for an additional 3 hours. The resulting RuO2/TiO2 electrode was then used for further characterization and electrocatalysis. The loading weight of RuO2 on the Ti sheet was approximately 5 mg per cm2. Commercial RuO2-loaded Ti and TiO2 (RuO2–Ti, RuO2–TiO2) electrodes were prepared using a coating method with polytetrafluoroethylene (PTFE, 60 wt%) as a binder. The loading weight of commercial RuO2 was controlled to match that of the in situ grown RuO2/TiO2.
4.2. Corncob pyrolysis to prepare bio-oil
Pyrolysis of corncobs was conducted in an auger reactor at 300 °C. The auger reactor had a diameter of 100 mm and a length of 0.6 m, and it was heated in a 3.5-kW electrical furnace. The temperature was controlled using a temperature control unit. Nitrogen gas was used to maintain an inert atmosphere and remove volatile products from the reactor. These volatile products were cooled and condensed to collect the liquid product in two condensers at −5 °C. The quantification of AA in the fresh bio-oil revealed that there was 8.6 wt% of (∼1.5 M) AA in the sample.
4.3. Material characterization
The morphologies of the synthesized RuO2/TiO2 were characterized using SEM (ESCAN MIRA LMS, Czech Republic). TEM images were obtained using a JEOL JEM-2100F (Japan) transmission electron microscope with an accelerating voltage of 200 kV. The structure of the prepared RuO2/TiO2 catalysts was examined using XRD performed on a PANalytical X’Pert3 powder diffractometer (Netherlands) with monochromatic Cu Kα radiation (λ = 1.54 Å, 40 mA, 40 kV). Data were recorded in the 2θ range of 10°–80° in 0.02° steps with a continuous scanning rate of 10° min−1. The chemical states of Ru, Ti, and O species were characterized using XPS performed on a Thermo Scientific NEXSA (Thermo-Fisher, USA) K-Alpha spectrometer with a standard monochromatic aluminum Kα source (1486.6 eV) operating at 15 kV and 15 mA in the constant analyzer energy scanning mode. All binding energies were calibrated using the C 1s line at 284.8 eV. The XPS spectra were fitted using XPS Peak 4.1 software based on Shirley-type background subtraction. Raman spectra of the samples were recorded using a Raman spectrometer (Inspectors R532, EnSpectr) with a 20 mW λ = 532 nm laser. The in situ Raman measurements (Fig. S25, ESI†) were conducted using a DC power source to provide a constant current, wherein the synthesized RuO2/TiO2 was used as the anode and a Pt wire as the counter electrode. The content of the Ru loading in the RuO2/TiO2 samples, and after reaction, was determined by ICP–MS.
4.4. Reaction system and gaseous product collection
The KBE reaction system mainly consists of a circulating water bath device and an electrochemical reaction device. As illustrated in Scheme 2, the circulating water bath maintains a low temperature, while the DC power supply provides a constant current ranging from 10 to 300 mA cm−2.
 |
| Scheme 2 The established reaction system and gaseous product collection. | |
The gas collection system was composed of two tandem digital flowmeters. The first (top right corner in Scheme 1) was used to record the argon flow, which was used to push the gaseous products generated from the KBE of AA in the cell. A gas drying device was included to prevent water vapor from the aqueous AA solution from entering the second flowmeter. Here, the 3A-type (3 Å diameter) molecular sieve was applied, as it would not adsorb the alkanes, CO2, and other products of electrolysis. The mixture of gases was quantified by the second flowmeter and collected using collection bags, then injected into the gas chromatography (GC)–flame ionization detector (FID)/thermal conductivity detector (TCD) for further quantification.
4.5. Product identification and quantification
A GC (Shimadzu) instrument equipped with an FID and TCD was used for the offline analysis of gas products (CH4, C2H6, H2, CO2, O2, and others). These gas products were quantified using an external standard method with four calibrated gas mixtures, where the concentration of CH4 was one-hundredth of that of C2H6 (2500, 5000, 7500, and 10
000 ppm CH4 and 2.5%, 5%, 7.5%, and 10% C2H6, respectively). Typically, a 100-μL gas sample was injected with a 20
:
1 split at 50 °C into a GS-GASPRO (Agilent Technologies, Inc.) column (30.0 m × 250 μm × 0.25 μm). Argon, flowing at 4.0 mL min−1, was used as the carrier gas. As the TCD part, a Molecular Sieve 5A (MS-5A)-packed column was applied, and the gas sample was injected with a 20
:
1 split at 120 °C.
An HPLC instrument equipped with a Waters 2414 refractive index detector was used to quantify CH3OH, AA, and HCHO. A Bio-Rad Aminex HPX-87H ion exclusion column (300 mm × 7.8 mm) was used for analyte separation at 60 °C. Sulfuric acid (5 mM) flowing at 0.6 mL min−1 was used as the mobile phase.
Qualitative analysis of the components of bio-oil and reaction products was conducted using GC–MS (Shimadzu 2010, Japan). The GC system was equipped with a DB-5-HT column (30 m × 0.25 mm × 0.25 μm) with helium as the carrier gas and a split ratio of 1
:
10. The injection temperature was set at 260 °C. The GC oven program began at 40 °C, followed by a heating rate of 5 °C minute−1 to 200 °C, held for 2 minutes, and then increased at 25 °C minute−1 to 250 °C. The chromatographic peaks obtained were identified by comparing the mass spectra with the National Institute of Standards and Technology library.
4.6. Mechanistic analysis
In situ ATR-FTIR was used to identify the reaction mechanism of the KBE of AA. Herein, in situ ATR-FTIR was performed on a Thermo-Fisher Nicolet iS20 equipped with a liquid-nitrogen-cooled HgCdTe detector and VeeMax III ATR accessory. RuO2/TiO2 was used as the working electrode. The Ag/AgCl electrode and Pt wire were used as the reference and counter electrodes, respectively. ATR-FTIR was recorded by stepwise switching the potential from 0 V to −10 V (vs. Ag/AgCl). The spectra collected at open-circuit voltage were used for the background subtraction. All measurements were acquired by averaging 64 scans at a spectral resolution of 4 cm−1.
4.7. Calculation
The conversion (%) of AA, the selectivity (%), and the FE of the products were calculated using the following equations:
where F is the Faraday constant (96
485 C mol−1), I is the current (A), and t is time (s).
The TON of RuO2/TiO2 was estimated using the following equation:
where mol
converted
AA refers to the number of moles of AA converted during the reaction process, and mol
RuO2 refers to the number of moles of RuO
2 (the active sites), which can be calculated by the following equation:
where ECSA (electrochemical active surface area) is calculated by cyclic voltammetry as shown in Fig. S26 (ESI
†),
M is the mass loading of RuO
2 on the electrode,
N0 is the constant RuO
2 surface (here we use the (110) facet) concentration, which is 1.51 × 10
19 atoms cm
−2 as calculated based on the parameters in Table S2 (ESI
†), and
NA is Avogadro's constant.
Data availability
The data supporting this article have been included as part of the ESI.†
Conflicts of interest
No conflict to declare.
Acknowledgements
The author acknowledges the generous financial support from the National Natural Science Foundation of China (22109133) and Research Grants Council (CityU 11302623).
References
- J. Lehto, A. Oasmaa, Y. Solantausta, M. Kytö and D. Chiaramonti, Appl. Energy, 2014, 116, 178–190 CrossRef CAS.
- Y.-K. Chen, C.-H. Lin and W.-C. Wang, Energy, 2020, 201, 117655 CrossRef CAS.
- P. Lahijani, M. Mohammadi, A. R. Mohamed, F. Ismail, K. T. Lee and G. Amini, Energy Convers. Manage., 2022, 268, 115956 CrossRef CAS.
- Q. Tu, A. Parvatker, M. Garedew, C. Harris, M. Eckelman, J. B. Zimmerman, P. T. Anastas and C. H. Lam, Environ. Sci. Technol., 2021, 55, 3240–3249 CrossRef CAS.
- L. M. Terry, C. Li, J. J. Chew, A. Aqsha, B. S. How, A. C. M. Loy, B. L. F. Chin, D. S. Khaerudini, N. Hameed and G. Guan, Carbon Resour. Convers., 2021, 4, 239–250 CrossRef CAS.
- T. Sarchami, N. Batta and F. Berruti, Biofuels, Bioprod. Biorefin., 2021, 15, 1912–1937 CrossRef CAS.
- J.-Y. Jeong, U.-D. Lee, W.-S. Chang and S.-H. Jeong, Bioresource Technol., 2016, 219, 357–364 CrossRef CAS PubMed.
- R. W. Snell, E. Combs and B. H. Shanks, Top. Catal., 2010, 53, 1248–1253 CrossRef CAS.
- M. R. Haverly, K. V. Okoren and R. C. Brown, Energy Fuel, 2016, 30, 9419–9426 CrossRef CAS.
- D. Chen, J. Zhou, Q. Zhang and X. Zhu, Renewable Sustainable Energy Rev., 2014, 40, 69–79 CrossRef CAS.
- J. Meng, A. Moore, D. C. Tilotta, S. S. Kelley, S. Adhikari and S. Park, Energy Fuel, 2015, 29, 5117–5126 CrossRef CAS.
- S. Hansen, A. Mirkouei and L. A. Diaz, Renewable Sustainable Energy Rev., 2020, 118, 109548 CrossRef CAS.
- D. Wen, H. Jiang and K. Zhang, Prog. Nat. Sci., 2009, 19, 273–284 CrossRef CAS.
- S. Omar, S. Alsamaq, Y. Yang and J. Wang, Front. Chem. Sci. Eng., 2019, 13, 702–717 CrossRef CAS.
- A. H. Zacher, M. V. Olarte, D. M. Santosa, D. C. Elliott and S. B. Jones, Green Chem., 2014, 16, 491–515 RSC.
- X. Hu, R. Gunawan, D. Mourant, M. M. Hasan, L. Wu, Y. Song, C. Lievens and C.-Z. Li, Fuel Process. Technol., 2017, 155, 2–19 CrossRef CAS.
- L. Ciddor, J. A. Bennett, J. A. Hunns, K. Wilson and A. F. Lee, J. Chem. Technol. Biot., 2015, 90, 780–795 CrossRef CAS.
- L. Leng, H. Li, X. Yuan, W. Zhou and H. Huang, Energy, 2018, 161, 214–232 CrossRef CAS.
- R. Trane, S. Dahl, M. S. Skjøth-Rasmussen and A. D. Jensen, Int. J. Hydrogen Energy, 2012, 37, 6447–6472 CrossRef CAS.
- C. H. Lam, W. Deng, L. Lang, X. Jin, X. Hu and Y. Wang, Energy Fuel, 2020, 34, 7915–7928 CrossRef CAS.
- A. P. Fraise, M. Wilkinson, C. Bradley, B. Oppenheim and N. Moiemen, J. Hosp. Infect., 2013, 84, 329–331 CrossRef CAS.
- B. Kraeutler and A. J. Bard, J. Am. Chem. Soc., 1978, 100, 2239–2240 CrossRef CAS.
- H. Salzberg and M. Leung, J. Org. Chem., 1965, 30, 2873–2875 CrossRef CAS.
- M. T. Hicks and P. S. Fedkiw, J. Electrochem. Soc., 1998, 145, 3728 CrossRef CAS.
-
I. Markó and F. Chellé, in Encyclopedia of Applied Electrochemistry, ed. G. Kreysa, K.-I. Ota and R. F. Savinell, Springer New York, New York, NY, 2014, DOI:10.1007/978-1-4419-6996-5_369, pp. 1151–1159.
- Y. Qiu, J. A. Lopez-Ruiz, G. Zhu, M. H. Engelhard, O. Y. Gutiérrez and J. D. Holladay, Appl. Catal., B, 2022, 305, 121060 CrossRef CAS.
- Y. Qiu, J. A. Lopez-Ruiz, U. Sanyal, E. Andrews, O. Y. Gutiérrez and J. D. Holladay, Appl. Catal., B, 2020, 277, 119277 CrossRef CAS.
- C. Wang, K. Liu, Y. Jin, S. Huang and J. Chun-Ho Lam, ChemSusChem, 2023, 16, e202300222 CrossRef CAS PubMed.
- T. Ashraf, A. P. Rodriguez, B. T. Mei and G. Mul, Faraday Discuss., 2023, 247, 252–267 RSC.
- N. Yang, H. Li, J. Hao, X. Lin, S. Kondrat, C. Hardacre and W.-F. Lin, Curr. Opin. Electrochem., 2024, 101566 CrossRef CAS.
- W. Chen, H. Wang, Y. Li, Y. Liu, J. Sun, S. Lee, J.-S. Lee and Y. Cui, ACS Cent. Sci., 2015, 1, 244–251 CrossRef CAS PubMed.
- G. Liu, M. Wang, Y. Wu, N. Li, F. Zhao, Q. Zhao and J. Li, Appl. Catal., B, 2020, 260, 118199 CrossRef CAS.
- G. Creusen, F. J. Holzhäuser, J. Artz, S. Palkovits and R. Palkovits, ACS Sustainable Chem. Eng., 2018, 6, 17108–17113 CrossRef CAS.
- Y. Huang, T. Zhou, Y. Hu, Y. Yang, F. Yang, W. Huang, L. He and W. Sun, Int. J. Hydrogen Energy, 2023, 448, 33411–33421 CrossRef.
- Z. Li, H. Sheng, Y. Lin, H. Hu, H. Sun, Y. Dong, X. Chen, L. Wei, Z. Tian and Q. Chen, Adv. Func. Mater., 2024, 34, 2409714 CrossRef CAS.
- S. K. Gupta, R. Desai, P. K. Jha, S. Sahoo and D. Kirin, J. Raman Spectrosc., 2010, 41, 350–355 CrossRef CAS.
- M. T. Uddin, Y. Nicolas, C. Olivier, T. Toupance, M. M. Müller, H.-J. Kleebe, K. Rachut, J. R. Ziegler, A. Klein and W. Jaegermann, J. Phys. Chem. C, 2013, 117, 22098–22110 CrossRef CAS.
- J. Shi, F. Hui, J. Yuan, Q. Yu, S. Mei, Q. Zhang, J. Li, W. Wang, J. Yang and J. Lu, Catalysts, 2019, 9, 108 CrossRef.
- S. Jia, J. Zhang, Q. Liu, C. Ma, Y. Tang and H. Sun, J. Mater. Chem. A, 2023, 11, 23489–23497 RSC.
- V. Natu, M. Benchakar, C. Canaff, A. Habrioux, S. Celerier and M. W. Barsoum, Matter, 2021, 4, 1224–1251 CrossRef CAS.
- W. Wei, Y. Dai, B. Huang, X. Li, F. Nägele, H. Over, M.-H. Whangbo and T. Jacob, J. Phys. Chem. C, 2015, 119, 12394–12399 CrossRef CAS.
- S. Huang, Y. Jin, M. Zhang, K. Yan, S.-P. Feng and J. C.-H. Lam, Green Chem., 2022, 24, 7974–7987 RSC.
- S. Huang, B. Gong, Y. Jin, P. H.-L. Sit and J. C.-H. Lam, ACS Catal., 2022, 12, 11340–11354 CrossRef CAS.
- N. Ahad and A. de Klerk, Fuel, 2018, 211, 415–419 CrossRef CAS.
-
A. J. Fry, Synthetic organic electrochemistry, John Wiley & Sons, 1989 Search PubMed.
- M. O. Nordkamp, B. Mei, R. Venderbosch and G. Mul, ChemCatChem, 2022, 14, e202200438 CrossRef CAS.
- W. Deng, X. Wang, S. S. A. Syed-Hassan, C. H. Lam, X. Hu, Z. Xiong, H. Han, J. Xu, L. Jiang and S. Su, Energy, 2022, 251, 123944 CrossRef CAS.
- S. Liu, N. Govindarajan, H. Prats and K. Chan, Chem. Catal., 2022, 2, 1100–1113 CrossRef CAS.
- B. M. Weckhuysen, Chem. Catal., 2022, 2, 920–922 CrossRef CAS.
- S. Ren, X. P. Ye and A. P. Borole, J. Anal. Appl. Pyrolysis, 2017, 123, 30–39 CrossRef CAS.
- J. Monni, P. Niemelä, L. Alvila and T. T. Pakkanen, Polymer, 2008, 49, 3865–3874 CrossRef CAS.
- F. Wan, H. Shi, W. Chen, Z. Gu, L. Du, P. Wang, J. Wang and Y. Huang, Nanomaterials, 2017, 7, 210 CrossRef CAS.
- R. Frost and J. Kloprogge, J. Mol. Struct., 2000, 526, 131–141 CrossRef CAS.
- H. Fan, J. Liu, J. Guo, K. Ye and B. J. C. S. B. Cong, Chin. Sci. Bull., 2002, 47, 1028–1032 CrossRef CAS.
- İ. Demiral, A. Eryazıcı and S. Şensöz, Biomass Bioenergy, 2012, 36, 43–49 CrossRef.
- K. Drugkar, W. Rathod, T. Sharma, A. Sharma, J. Joshi, V. K. Pareek, L. Ledwani and U. Diwekar, Sep. Purif. Technol., 2022, 283, 120149 CrossRef CAS.
|
This journal is © The Royal Society of Chemistry 2025 |
Click here to see how this site uses Cookies. View our privacy policy here.