DOI:
10.1039/D5CC00262A
(Feature Article)
Chem. Commun., 2025,
61, 4897-4903
Two-step thermochemical cycle for solar fuel production from H2O and CO2: technological challenges and potential solutions
Received
15th January 2025
, Accepted 25th February 2025
First published on 4th March 2025
Abstract
A two-step thermochemical cycle for solar fuel production technology is considered a promising path for alternative energy of fossil fuels, because it employs solar energy as a high-temperature heat supply to directly convert H2O or/and CO2 into H2 or/and CO, which is well in line with the requirements of carbon neutrality. A large amount of effort has been put into this research, but there are still several bottleneck issues that need to be addressed. In this review, we present the working principles of a two-step thermochemical cycle for solar fuel production and discuss the current technological challenges hindering such technology's further development towards large-scale application, such as severe operating conditions and low solar-to-fuel efficiency. Finally, we explore the potential solutions from the perspectives of materials and reactors based on current status and demand, which can serve as guidance for future innovations in this field.
1. Introduction
The energy crisis and environmental pollution pose serious challenges to social sustainability, which means it is urgent to prioritize the development of renewable energy sources, such as solar, wind, water, and biomass energies, to gradually eliminate fossil fuels. Among these, solar energy is considered the most promising renewable energy source, as the sun provides enormous amounts of clean radiant energy for earth, far exceeding humanity's needs.1,2 Lots of scholars and experts have devoted themselves to effectively converting sunlight into other forms of energy, so called light-to-X3 (heat, electricity and chemicals), and proposed a series of innovative approaches which span the physical and chemical sciences to engineering to achieve an effective utilization of solar energy, such as photothermal,4 photovoltaic,5 photochemical6 and thermochemical7 technologies. These technologies have the potential to make solar energy serve as an alternative to fossil fuels, offering a sustainable energy solution for global development.
Existing paths employed to realize light-to-X energy conversion mainly include solar photovoltaic, photochemical, photothermal and thermochemical technologies. At present, the most mature and widely used technologies are photovoltaic and photothermal conversion. However, solar photovoltaics only utilizes a portion of the solar spectral radiation energy (focused on ultraviolet and visible light range) due to the limitation of semiconductor materials, which causes the potential solar conversion efficiency to be limited to a relatively low level. Although photothermal conversion can use the entire solar spectrum energy, thermal energy is hard to store and transport for a long time and its energy level is also lower than electricity and fuels. Solar photochemical technology is similar to photovoltaics and only uses a small portion of solar spectral energy. Moreover, a series of technical problems have not been resolved yet. In contrast, solar thermochemical technology simultaneously possesses the advantages of the above three technologies. It can not only utilize the entire solar spectrum, but also the generated fuel has high energy level and is convenient to store and transport. Therefore, solar thermochemical fuel production technology is regarded as one of the most promising paths to replace fossil fuels to achieve social sustainability and global carbon neutrality.8 At present, the solar thermochemical splitting of H2O or/and CO2via a two-step redox cycle for sustainable fuel production is becoming one of the currently popular research hotspots,9 as it can directly convert solar into chemical energy stored in energy-dense chemicals H2 or/and CO without subsequent gas product separation in time and space. Moreover, it can also co-split H2O and CO2 simultaneously to achieve a tailored mixture of H2 and CO suitable for subsequent liquid fuel synthesis, which successfully eliminates the energy penalty associated with additional refinement steps for adjusting the syngas mixture.10 In addition, such technology only adopts H2O or/and CO2 as the initial feedstock, which leads to the low cost of raw materials and zero carbon emissions during the production process.11 These advantages make it become an ideal choice for humanity, as it well meets the requirements of social sustainability.
However, this technology is still in the stage of theoretical research on a laboratory scale and has a long way to go before commercialization,12 because there are several challenges that have not yet been resolved, such as severe operating conditions and low solar-to-fuel efficiency.13 For example, during ceria-based thermochemical redox cycles, the high temperature (typically ∼1500 °C)14 and low oxygen partial pressure atmosphere (typically ∼10−5 bar)15 are required for the reduction reaction. Such operating conditions not only impose strict requirements on the materials and devices, but also make the sealing of moving parts become extremely difficult, and even cause extra energy penalties.16 Another issue of concern is the low solar-to-fuel efficiency, whose value is still in the single digits, and its current maximum experimental result is only 5.25%,17 which is far from meeting the requirements of commercialization. These challenges are urgent to be solved before scale up of such technology. In this perspective, we discuss the current technological challenges faced by two-step thermochemical redox cycling for solar fuel production, and point out several potential solutions from the perspectives of materials and reactors. The contents of this article can be employed to serve as guidance for future innovations in this field.
2. Principle of two-step solar thermochemical fuel production
The essence of solar thermochemical fuel production is to convert solar energy into chemical energy, which is stored in sustainable fuel carriers, such as H2 and CO. The sunlight is firstly tracked and concentrated into dense solar radiation power, which serves as a high-temperature heat supply to drive the thermochemical reaction. Due to the requirement for high temperature, solar dish and tower concentrators with a high concentration ratio (generally >2000 suns) can provide sufficient dense solar radiation to obtain such elevated temperatures. The solar dish concentrator is considered to be one of the most perfect solar concentrators for use as a high-temperature heat source due to the high concentration ratio and optical efficiency, but its size limits its large-scale application in practical production. Solar tower concentrators can serve as solar high-temperature heat sources on an industrial scale. Considering the complexity of the heliostat field, environmental factors and optical loss during sunlight delivery and concentration, its solar-to-thermal conversion efficiency is usually around 60%. High-concentration solar energy directly enters the reactor and is absorbed by the redox material. Once the temperature meets the requirement of reaction, redox cycle starts and converts solar to chemical energy. A complete two-step thermochemical cycle based on metal oxides consists of two-step reactions,18 which involves – step 1: endothermic reduction reaction driven by concentrated solar radiation, discharging oxygen atoms and achieving a reduced oxygen carrier material alongside oxygen; and step 2: an exothermic oxidation reaction in the presence of H2O or/and CO2, regenerating the initial redox material and harvesting the products of H2 or/and CO. The detailed thermochemical cyclic operation is shown in Fig. 1,11 and the reduction and oxidation reactions can be generically described as19 | 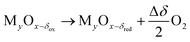 | (1) |
| MyOx−δred + ΔδH2O(CO2) → MyOx−δox + ΔδH2(CO) | (2) |
where MyOx−δox and MyOx−δred represent a generic nonstoichiometric redox material in the oxidized state and reduced state, respectively, such as metal oxide; Δδ denotes the reduction extent of the redox material under specific conditions and can be expressed as Δδ = Δδred − Δδox. It should be noted that the splitting of H2O and CO2 obeys the same thermochemical principle, which is why H2O and CO2 can be co-split simultaneously in the same reactor. On a microscopic level, the reduction reaction depends on the concentration of removable oxygen, and the oxidation reaction depends on the concentration of vacancies and the concentration of oxygen gas.20 While on a macroscopic level, the swing of reduction and oxidation steps depends on temperature and oxygen partial pressure. Namely, the reduction reaction usually requires a relatively high temperature and low oxygen partial pressure, and the oxidation reaction needs to proceed under a relatively low temperature and in the presence of H2O or/and CO2.21 A two-step reaction strategy can not only decrease the temperature required for direct thermolysis, but also can generate O2 and H2/CO in separate stages (reduction and oxidation steps) in the thermochemical cycling process, which eliminates gas product separation and successfully avoids the risk of explosive recombination of O2 and H2/CO.22 Therefore, the two-step thermochemical cycle for solar fuel production technology can be regarded as a significant potential method for efficient utilization of solar energy.
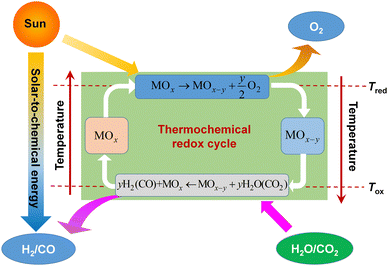 |
| Fig. 1 Principle of two-step thermochemical cycling for solar fuel production based on ceria-based redox materials. Reproduced with permission11 Copyright 2023, Elsevier. | |
3. Challenges of two-step solar thermochemical fuel production
The principle of two-step thermochemical cycling indicates that such technology has theoretical feasibility, but there are still a series of issues that need to be solved before practical production on a large scale. In this section, technological challenges are summarized based on current status and demand for further development.
3.1 The high temperature required for the reduction reaction
The first challenge is the high temperature required for the reduction reaction during thermochemical conversion.23 Such high temperature (usually > 1000 °C) not only places constraints on the selection of redox materials and devices, but also increases the energy penalties due to serious heat losses, which would inevitably limit their practicality on a large scale. Moreover, it also causes extreme difficulty in temperature monitoring, equipment maintenance, and operational safety. In addition, high-flux solar energy with high concentration ratio (generally >2000 suns) is required to provide heat supply. At present, only solar dish and tower concentrators can provide such high-temperature heat sources for the thermochemical conversion process,24 because they both provide 3D point-focus concentration. The dish concentrator is only suitable for experimental research on a laboratory scale, due to the limitation of size.25 A solar tower system with a heliostat field concentrator is a unique choice for scale-up of such technology.26 However, up to now, no solar tower plants for thermochemical fuel production have been employed on a commercial scale, because there are still a lot of scientific and technical issues, including efficiency, cost, intermittent solar energy, weather and seasons, which all need to be resolved in the future.11 Furthermore, the operation and maintenance costs of solar tower systems are also very high, which is also an additional issue that needs to be considered in practice.
3.2 The low oxygen partial pressure required for the reduction reaction
The low oxygen partial pressure required for the reduction reaction is another challenge.27 Because an acceptable high temperature alone is not enough to drive or ensure normal reduction reaction. If the temperature continues to increase, the materials and devices would be damaged and even could not work well. To control the temperature within a reasonable range, the specific low oxygen partial pressure atmosphere must be required based on the thermodynamic principle that Gibbs free energy is less than zero. To achieve a low oxygen partial pressure (usually ∼10−5 bar) during the reduction step, extra technologies or devices need to be integrated into the thermochemical system, such as the inert gas sweeping and vacuum pumping,28,29 which would introduce additional energy consumption. For example, the inert gas sweeping method usually uses a large amount of inert gas to sweep oxygen away from the reactor to create a low oxygen partial pressure atmosphere, which leads to consumption of inert gas and electricity as well as significant additional energy demand for sweep gas heating due to the fact that the inert gas is heated from ambient temperature to the reduction temperature within the reactor.30 The vacuum pumping method, although can eliminate the heat loss caused by the inert gas, would consume a lot of electricity due to the low electrical pumping efficiency (<1%) for low absolute pressures (<10−5 atm).28 The additional mechanical pumping requirement and extra energy consumption for oxygen scrubbing cause increased complexity of the system, which not only becomes the limiting factor for its practical deployment, but also further decreases the overall energy efficiency of solar thermochemical systems.13 Therefore, how to improve the operating conditions including, a high temperature and low oxygen partial pressure environment during the reduction step of two-step thermochemical cycling, should be regarded as one key in future research.
3.3 The low solar-to-fuel efficiency of thermochemical cycling
Except for severe operating conditions, the low solar-to-fuel efficiency of solar thermochemical fuel production technology is the most concerning issue,31 because it is a key indicator to determine whether such technology has commercial value. The current optimal experimental result from the laboratory is only 5.25%, which is far from meeting the requirements of commercialization.17 One major reason is that the temperature/pressure swing mode commonly applied between reduction and oxidation steps incurs serious irreversible energy losses. Namely, there is a large amount of sensible heat that has to leave the reactor when the reduction reaction switches to the oxidation reaction. Taking a 4 kW ceria-based solar reactor as an example, under a solar flux irradiation with a 3000 concentration ratio, the sensible heat of the redox material accounts for over 60% of the total energy in the reactor.32 This is because a several hundred temperature difference between the reduction and oxidation steps is hard to avoid due to the specific reaction conditions required for the reduction and oxidation reactions.33 Moreover, under the high-temperature condition, an amount of energy is taken away from the reactor by unreacted gases and products, as well as an amount of energy in the form of radiation escaping from the reactor through an aperture, which is designed to receive concentrated solar radiation. In addition, solar energy loss during the concentrating process is not ignored, because the optical losses in the delivery of solar energy can account for nearly 20% of the total solar energy incident onto solar concentrators.34 These energy losses cause the solar energy conversion efficiency of the thermochemical process to be extremely low, and there are still no effective technical methods that can well solve this issue. In summary, the high reduction temperature, low oxygen partial pressure and low solar-to-fuel efficiency are three main challenges, which hinder further development of two-step solar thermochemical fuel production technology.
4. Potential solutions for two-step thermochemical fuel production
4.1 Redox material modification
The redox material is the core of the thermochemical redox cycle, because it simultaneously serves as a solar energy absorber and participates in reduction and oxidation reactions, which directly determine the performance of solar thermochemical conversion. Therefore, an excellent redox material plays a vital role in two-step thermochemical fuel production. At present, ceria-based materials are regarded as state-of-the-art redox materials for thermochemical cycling with temperature/pressure swing mode due to their good crystallographic stability, favorable re-oxidation thermodynamics and fast splitting kinetics.35 However, high temperature and low oxygen partial pressure conditions are still required for achieving a relatively good reduction extent due to its limited amount of available oxygen vacancies at low and moderate temperatures.36 One potential method to improve the reaction conditions of ceria-based redox materials during the reduction step is the cationic-dopant scheme, which substitutes transition or rare earth metals into the crystal structure of ceria to introduce lattice defects and create additional oxygen vacancies, as shown in Fig. 2(a)–(l).37,38 Such doping treatment generally can change the thermodynamic properties and redox performance of ceria. In recent years, a series of doping schemes for ceria have been proposed and tested, which witness the improvement of performance in repeated redox cycling processes. Among the investigated doping compositions, the Ce0.75Zr0.25O2 shows the best cyclability and performance during CO2 thermochemical catalytic splitting.39 But it should be noted that not all doping schemes can be expected to reduce the reduction temperature and improve the reduction extent. If not treated reasonably, results opposite to expectations would occur. Even though for good doping schemes, the reaction conditions have not yet been satisfactorily improved. Therefore, this doping method still needs to be further explored. Fortunately, the development of artificial intelligence (AI) technology can assist in accelerating the development of new doped redox materials. In other words, the AI-assisted doped scheme will contribute to redox material modification to achieve a milder reaction condition to push the development of two-step thermochemical fuel production towards commercialization.
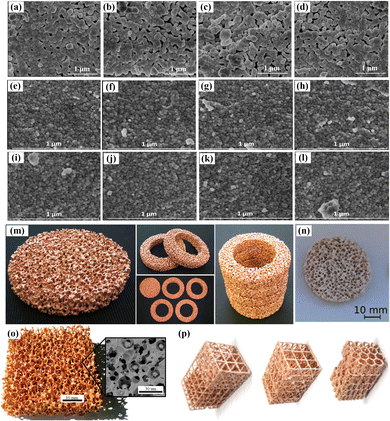 |
| Fig. 2 Redox material modification including doping schemes and porous structures. (a) Sr-doped, reproduced with permission37 Copyright 2020, Springer Nature; (b) Ba-doped, reproduced with permission37 Copyright 2020, Springer Nature; (c) Ca-doped, reproduced with permission37 Copyright 2020, Springer Nature; (d) Sn-doped, reproduced with permission37 Copyright 2020, Springer Nature; (e) La-doped, reproduced with permission38 Copyright 2018, Elsevier; (f) Pr-doped, reproduced with permission38 Copyright 2018, Elsevier; (g) Sm-doped, reproduced with permission38 Copyright 2018, Elsevier; (h) Nd-doped, reproduced with permission38 Copyright 2018, Elsevier; (i) Gd-doped, reproduced with permission38 Copyright 2018, Elsevier; (j) Dy-doped, reproduced with permission38 Copyright 2018, Elsevier; (k) Er-doped, reproduced with permission38 Copyright 2018, Elsevier; (l) Tb-doped, reproduced with permission38 Copyright 2018, Elsevier; (m) reticulated porous ceramic structure, reproduced with permission40 Copyright 2012, American Chemical Society; (n) microstructured porous structure, reproduced with permission41 Copyright 2020, Elsevier; (o) dual-scale reticulated porous ceramic structure, reproduced with permission14 Copyright 2014, Royal Society of Chemistry; (p) ordered porous structures, reproduced with permission42 Copyright 2019, John Wiley and Sons. | |
In addition to the compositions of the redox material themselves, the material morphology and microstructure can also govern the reaction kinetics and heat transfer process, which means that the optimal design of morphology and microstructure is another potential method to improve the redox performance of thermochemical conversion. Current designs of redox materials are mainly particle-based structure43 and porous-based structure.44 When the redox material is prepared into a small particle structure, its specific surface area (SSA) would be increased to enhance solid/gas reactions, and if it is employed in the circulating fluidized bed reactor, a good heat transfer behavior and continuous fuel production can be achieved. Moreover, the particle-based fluidized bed reactor is easier to realize solid phase sensible heat recovery,45 which is beneficial for improving solar-to-fuel efficiency. But, such design makes the thermochemical system become extremely complex, which faces a series of technical issues.
In contrast, the porous-based structure design of redox materials is more popular, as shown in Fig. 2(m)–(p),14,40–42 because it not only can increase the SSA but also make the reactor structure simpler. One current successful design is the reticulated porous ceramic structure made of ceria with dual-scale interconnected porosity in the millimeter and micrometer ranges.14 The macro-porous structures with millimeter-size facilitate radiation infiltration and proper gas dynamics, which can enable volumetric absorption of concentrated solar radiation for efficient heat transfer to the reaction site during endothermic reduction. And the micrometer-size microstructures within the struts of porous materials can further maximize the SSA for enhanced reaction kinetics during reduction and oxidation reactions. Furthermore, the concept of hierarchically ordered structures with a porosity gradient is introduced to optimize the design of redox materials.46 Namely, the sizes of porosity voids decrease continuously from top (exposed to solar radiation) to bottom (far from solar radiation), which facilitates more radiation absorption and better heat and mass transfer. These physical measures improve the thermochemical redox performance by enhancing external factors and help achieve a current optimal experimental solar-to-fuel efficiency 5.25%, which indicates that physical design measures in addition to chemical doping schemes are also a promising technological method for improving the thermochemical redox performance.
Besides, more effort should also be devoted to exploring novel redox materials with higher oxygen exchange capacity at lower temperatures, such as perovskite materials.47 Perovskites as a type of crystal structure with a general formula ABO3 can be considered as a promising candidate of redox materials. Up to now, perovskites have been proposed to be applied in thermochemical fuel production for over 10 years, and research has indicated that perovskite materials have superior redox performance but have not yet proven to be as stable as ceria.9 Fortunately, it is easy to tune the material properties by varying A and B sites and therefore there is large probability to find a composition that can outperform the well-established redox materials,48 as long as enough efforts are devoted to this study. Therefore, exploring novel perovskites suitable to serve as redox materials that work well under more mild operating conditions is another potential pathway.
4.2 Novel reactor designs
The reactor is the most important device which finishes the thermochemical conversion from solar to chemical energy via redox cycling for splitting of H2O or/and CO2. Conventional thermochemical reactors can be classified into two categories: fluidized-bed reactor and fixed-bed reactor. The major difference between the two types of reactors is the structure of the redox materials. In general, a particle-based structure is employed in the fluidized-bed reactor, while a porous-based structure is applied in the fixed-bed reactor. At present, existing conventional reactors all face common issues: severe operating conditions and low solar-to-fuel efficiency. In addition, the fluidized-bed reactor system is extremely complex to realize thermochemical conversion processes, which leads to there being relatively few publications on its research. Meanwhile, the fixed-bed reactor system attracts large interest due to the relatively simple composition. But it has to withstand significant temperature fluctuations during repeated cycling, which poses challenges to the long-term stable operation of the reactor. Therefore, reactor design is important research content in future works.
The energy loss during the entire solar two-step thermochemical production process includes sunlight loss during solar concentration and heat loss during redox cycling in the reactor. The sunlight loss during solar radiation delivery and concentration accounts for nearly 20% of the total solar energy incident onto solar concentrators.11 The heat losses during the reduction and oxidation steps are re-radiation loss, which depends on the size of the aperture which is designed to receive concentrated solar energy, and this loss is relatively small due to the aperture being small. The maximum energy loss occurs at a two-step thermochemical redox cycle process in the reactor, mainly due to the sensible heat rejected during the temperature-swing cycling mode, which accounts for over 60% of the absorbed solar energy according to the energy balance analysis. Research has indicated that if most sensible heat of the reactor can be recovered, the potential solar-to-fuel efficiency would rise above 20%, which meets the requirements of commercialization.49 The energy required for product separation and collection is not avoided in practical production, which depends on the performance of auxiliary devices. Thus, heat recovery technology is a significantly powerful driving force pushing solar thermochemical fuel production towards the commercial scale. Heat recovery includes the solid phase sensible heat recovery and gas phase sensible heat recovery. Solid phase sensible heat recovery refers to the recovery of heat from high-temperature redox materials that finishes the reduction reaction and needs to be cooled to the oxidation temperature. Gas phase sensible heat recovery mainly recovers heat from high-temperature gas leaving the reactor during the reduction and oxidation steps to heat ambient-temperature gas, which would enter the reactor. Sensible heat recovery not only can reduce the energy consumption, but also can relieve temperature fluctuations inside the reactor, which are beneficial for thermochemical cycling processes. At present, a series of heat recovery designs including solid and gas phase sensible heat recovery have been proposed for application in the two-step thermochemical cycle, as shown in Fig. 3(a)–(e).50–54 Theoretical calculation and analysis indicate that the integrated thermochemical reactor/heat exchanger design is the current most effective method to significantly improve solar-to-fuel efficiency of thermochemical conversion, although the ideas of heat recovery of the reactor are almost still stuck in the concept and design stage due to a large number of detailed techniques yet to be resolved. Here, we strongly recommend that heat recovery should be currently the first choice to push development of two-step thermochemical fuel production towards practical application, due to its contribution far exceeding redox materials and the reactors themselves in terms of solar conversion efficiency.
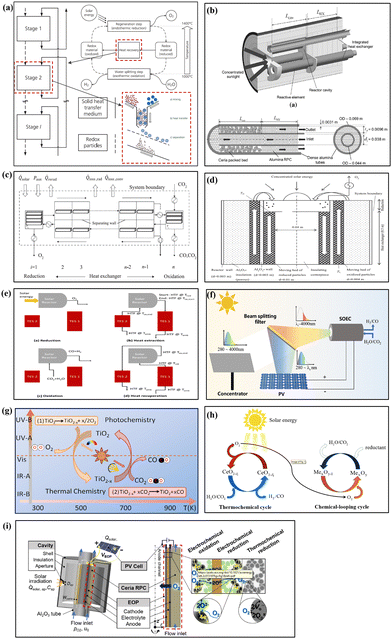 |
| Fig. 3 Reactor design. (a) Particle solid phase heat recovery, reproduced with permission50 Copyright 2014, Elsevier; (b) particle fluidized bed heat recovery, reproduced with permission51 Copyright 2018, Elsevier; (c) brick counter-flow solid heat recovery, reproduced with permission52 Copyright 2017, Elsevier; (d) gas phase heat recovery, reproduced with permission53 Copyright 2015, Elsevier; (e) high temperature heat recovery reactor system, reproduced with permission54 Copyright 2023, Elsevier; (f) electro-assisted thermochemical system based on solar spectral splitting, reproduced with permission55 Copyright 2024, Elsevier; (g) integrating photochemistry and thermochemistry scheme, reproduced with permission56 Copyright 2015, Elsevier; (h) integrating chemical-looping and thermochemical cycle, reproduced with permission57 Copyright 2023, Elsevier; (i) integrating thermochemical cycle and electrochemical oxygen pumping, reproduced with permission13 Copyright 2022, American Chemical Society. | |
In addition to heat recovery, some experts proposed the concept of isothermal thermochemical cycling, namely, the reduction and oxidation reactions proceed under the same temperature conditions. This idea successfully eliminates the temperature difference between two steps and doesn’t require heat recuperation from solids.58 In fact, “isothermal” is just an ideal condition, because the absolute isothermal thermochemical cycle is hard to achieve. In the reported studies, near-isothermal thermochemical cycles with a relatively small temperature variation, such as ΔT < 150 °C,59 are adopted. Such treatment not only minimizes solid phase sensible heat loss to the greatest extent possible, but also preserves the original intention of simple reactor design. However, the pros and cons of isothermal versus two-temperature thermochemical cycling are still under debate. This is because the temperature swing design is just for enhancing redox reactions based on the reaction kinetics and thermodynamic properties of redox materials. It is well-known that materials with lower reduction enthalpy and higher reduction entropy are easier to reduce but more difficult to re-oxidize. Taking ceria as an example, if the temperature is too high, the oxidation kinetics would be decreased, which is not conducive to the oxidation reaction; if the temperature is too low, a lower oxygen partial pressure is required to drive the reduction reaction, which means higher energy consumption associated with the vacuum pump or inert gas sweeping. Whether final isothermal operation can improve the solar conversion efficiency needs further verification. Therefore, isothermal thermochemical cycle design can be regarded as a new idea that can be further explored in the future.
Reactor modifications alone are insufficient to improve the thermochemical efficiency based on existing research works. Hybrid cycle technologies might help overcome the challenges of severe operating conditions and low solar conversion efficiency shown in Fig. 3(f)–(i).13,55–57 For example, a two-step electro-assisted thermochemical cycle system based on solar spectral splitting uses solar long-wavelength energy to drive thermochemical conversion, and solar short-wavelength energy is used to generate electricity, which is employed to assist in reduction reactions to reduce the requirement of high temperature and low oxygen partial pressure.55 Integrating the photochemistry and thermochemistry scheme for splitting of H2O can eliminate the requirement for high temperature due to the high-temperature reduction reaction being replaced by photochemical reaction.56 A chemical-looping cycle is employed to integrate into the thermochemical cycle to realize oxygen removal to reduce the energy consumption for creating low oxygen partial pressure in the reduction step.57 Integrating thermochemical cycling and electrochemical oxygen pumping can achieve a low oxygen partial pressure via in situ oxygen removal,13 which can avoid additional energy consumption by inert gas sweeping or vacuum pumping. In summary, novel ideas, whether material, reactor or integrating scheme, are all potential methods to face the challenges of two-step thermochemical cycling for solar fuel production. Any idea that can be transformed into practical applications will push such technology forward.
5. Conclusions
Two-step thermochemical cycling for solar fuel production based on the redox cycle can be regarded as one of the most promising clean energy solutions for social sustainability, due to the fact that only solar energy, water and carbon dioxide are employed as input, which means the low cost of raw materials and zero carbon emissions during the production process. This perspective summarizes the current technological challenges faced by such technology, which focuses on severe operating conditions and low solar-to-fuel efficiency, and lists several potential solutions from the perspectives of materials and reactors via analysing existing research. These potential solutions can assist in overcoming these bottleneck issues to achieve a better performance of thermochemical conversion, which can serve as guidance for future innovations in this field.
Author contributions
Conceptualization: Linyang Wei and Liang An; methodology: Zhefei Pan; writing – original draft: Linyang Wei and Zhefei Pan; writing – review & editing: Linyang Wei and Liang An; supervision: Liang An; funding acquisition: Zhefei Pan and Liang An.
Data availability
No primary research results, software or code have been included and no new data were generated or analysed as part of this invited paper.
Conflicts of interest
There are no conflicts to declare.
Acknowledgements
The work described in this paper was supported by a grant from the Research Grants Council of the Hong Kong Special Administrative Region, China (No. N_PolyU559/21) and Chongqing Talents (CSTB2024YCJH-KYXM0082).
Notes and references
- N. S. Lewis and D. G. Nocera, Proc. Natl. Acad. Sci. U. S. A., 2006, 103, 15729–15735 CrossRef CAS PubMed.
- M. Perez and R. Perez, Sol. Energy Adv., 2022, 2, 100014 CrossRef.
- F. V. Vázquez, J. Koponen, V. Ruuskanen, C. Bajamundi, A. Kosonen, P. Simell, J. Ahola, C. Frilund, J. Elfving and M. Reinikainen, J. CO2 Util., 2018, 28, 235–246 CrossRef.
- J. Li, Y. Long, X. Cao, H. Sun, R. Jiao, Z. Zhu, W. Liang and A. Li, Adv. Colloid Interface Sci., 2024, 325, 103118 CrossRef CAS PubMed.
- A. Machín and F. Márquez, Materials, 2024, 17, 1165 CrossRef PubMed.
- X. X. Zou and Y. Zhang, Chem. Soc. Rev., 2015, 44, 5148–5180 RSC.
- W. C. Chueh, C. Falter, M. Abbott, D. Scipio, P. Furler, S. M. Haile and A. Steinfeld, Science, 2010, 330, 1797–1801 CrossRef CAS PubMed.
- A. Le Gal, S. Abanades and G. Flamant, Energy Fuels, 2011, 25, 4836–4845 CrossRef CAS.
- R. Schäppi, D. Rutz, F. Dähler, A. Muroyama, P. Haueter, J. Lilliestam, A. Patt, P. Furler and A. Steinfeld, Nature, 2022, 601, 63–68 CrossRef PubMed.
- S. Zoller, E. Koepf, D. Nizamian, M. Stephan, A. Patané, P. Haueter, M. Romero, J. González-Aguilar, D. Lieftink and E. De Wit, Joule, 2022, 6, 1606–1616 CrossRef CAS PubMed.
- L. Wei, Z. Pan, X. Shi, O. C. Esan, G. Li, H. Qi, Q. Wu and L. An, iScience, 2023, 26, 108127 CrossRef CAS PubMed.
- Y. P. Guo, J. Chen, H. L. Song, K. Zheng, J. Wang, H. S. Wang and H. Kong, Appl. Energy, 2024, 357, 122499 CrossRef CAS.
- W. Bai, H. Huang, C. Suter, S. Haussener and M. Lin, ACS Energy Lett., 2022, 7, 2711–2716 CrossRef CAS.
- P. Furler, J. Scheffe, D. Marxer, M. Gorbar, A. Bonk, U. Vogt and A. Steinfeld, Phys. Chem. Chem. Phys., 2014, 16, 10503–10511 RSC.
- S. Abanades, A. Haeussler and A. Julbe, Chem. Eng. J., 2021, 422, 130026 CrossRef CAS.
- M. Tou, R. Michalsky and A. Steinfeld, Joule, 2017, 1, 146–154 CrossRef CAS PubMed.
- D. Marxer, P. Furler, M. Takacs and A. Steinfeld, Energy Environ. Sci., 2017, 10, 1142–1149 RSC.
- Y. Lu, L. Zhu, C. Agrafiotis, J. Vieten, M. Roeb and C. Sattler, Prog. Energy Combust. Sci., 2019, 75, 100785 CrossRef.
- B. D. Ehrhart, C. L. Muhich, I. Al-Shankiti and A. W. Weimer, Int. J. Hydrogen Energy, 2016, 41, 19881–19893 CrossRef CAS.
- P. Wang, R. Wei and K. Vafai, Energy Convers. Manage., 2022, 272, 116363 CrossRef CAS.
- D. Arifin and A. W. Weimer, Sol. Energy, 2018, 160, 178–185 CrossRef CAS.
- S. Abanades, Energies, 2022, 15, 7061 CrossRef CAS.
- H. Pan, Y. Li, L. Zhu and Y. Lu, Energy Convers. Manage., 2022, 259, 115578 CrossRef CAS.
- A. Boretti, J. Nayfeh and A. Al-Maaitah, Front. Energy Res., 2021, 9, 666191 CrossRef.
- J. Lilliestam, M. Labordena, A. Patt and S. Pfenninger, Nat. Energy, 2017, 2, 17094 CrossRef.
- H. Villafán-Vidales, C. Arancibia-Bulnes, D. Riveros-Rosas, H. Romero-Paredes and C. Estrada, Renewable Sustainable Energy Rev., 2017, 75, 894–908 CrossRef.
- B. D. Ehrhart, C. L. Muhich, I. Al-Shankiti and A. W. Weimer, Int. J. Hydrogen Energy, 2016, 41, 19904–19914 CrossRef CAS.
- S. Brendelberger, H. von Storch, B. Bulfin and C. Sattler, Sol. Energy, 2017, 141, 91–102 CrossRef CAS.
- P. T. Krenzke and J. H. Davidson, Energy Fuels, 2015, 29, 1045–1054 CrossRef CAS.
- M. Lin and S. Haussener, Energy, 2015, 88, 667–679 CrossRef CAS.
- L. Wei, Z. Li, Z. Pan, Z. Yi, G. Li and L. An, Energy Convers. Manage., 2024, 310, 118484 CrossRef CAS.
- S. Siegrist, H. von Storch, M. Roeb and C. Sattler, J. Sol. Energy Eng., 2019, 141, 021009 CrossRef CAS.
- L. Y. Wei, Z. F. Pan, S. C. Sun, Z. Yi, G. J. Li and L. An, Int. J. Heat Mass Transfer, 2024, 229, 125742 CrossRef CAS.
- N. P. Siegel, J. E. Miller, I. Ermanoski, R. B. Diver and E. B. Stechel, Ind. Eng. Chem. Res., 2013, 52, 3276–3286 CrossRef CAS.
- R. R. Bhosale, G. Takalkar, P. Sutar, A. Kumar, F. AlMomani and M. Khraisheh, Int. J. Hydrogen Energy, 2019, 44, 34–60 CrossRef CAS.
- Y. P. Mao, Y. B. Gao, W. Dong, H. Wu, Z. L. Song, X. Q. Zhao, J. Sun and W. L. Wang, Appl. Energy, 2020, 267, 114860 CrossRef CAS.
- G. Takalkar, R. R. Bhosale, S. Rashid, F. AlMomani, R. A. Shakoor and A. Al Ashraf, J. Mater. Sci., 2020, 55, 11797–11807 CrossRef CAS.
- R. Bhosale and G. Takalkar, Ceram. Int., 2018, 44, 16688–16697 CrossRef CAS.
- M. Portarapillo, D. Russo, G. Landi, G. Luciani and A. Di Benedetto, RSC Adv., 2021, 11, 39420–39427 RSC.
- P. Furler, J. Scheffe, M. Gorbar, L. Moes, U. Vogt and A. Steinfeld, Energy Fuels, 2012, 26, 7051–7059 CrossRef CAS.
- A. Haeussler, S. Abanades, A. Julbe, J. Jouannaux, M. Drobek, A. Ayral and B. Cartoixa, Chem. Eng. Res. Des., 2020, 156, 311–323 CrossRef CAS.
- M. Hoes, S. Ackermann, D. Theiler, P. Furler and A. Steinfeld, Energy Technol., 2019, 7, 1900484 CrossRef.
- I. Ermanoski, N. P. Siegel and E. B. Stechel, J. Sol. Energy Eng., 2013, 135, 031002 CrossRef.
- M. Orfila, D. Sanz, M. Linares, R. Molina, R. Sanz, J. Marugán and J. Á. Botas, Int. J. Hydrogen Energy, 2021, 46, 17458–17471 CrossRef CAS.
- C. P. Falter and R. Pitz-Paal, Appl. Therm. Eng., 2018, 132, 613–623 CrossRef CAS.
- S. Wijewardane, Solar Compass, 2022, 2, 100024 CrossRef.
- J. R. Scheffe, D. Weibel and A. Steinfeld, Energy Fuels, 2013, 27, 4250–4257 CrossRef CAS.
- S. Li, V. M. Wheeler, A. Kumar, M. B. Venkataraman, C. L. Muhich, Y. Hao and W. Lipiński, Energy Technol., 2022, 10, 2000925 CrossRef CAS.
- J. Lapp, J. H. Davidson and W. Lipiński, Energy, 2012, 37, 591–600 CrossRef CAS.
- J. Felinks, S. Brendelberger, M. Roeb, C. Sattler and R. Pitz-Paal, Appl. Therm. Eng., 2014, 73, 1006–1013 CrossRef.
- R. B. Chandran, R. M. De Smith and J. H. Davidson, Int. J. Heat Mass Transfer, 2015, 81, 404–414 CrossRef.
- C. P. Falter and R. Pitz-Paal, Sol. Energy, 2017, 144, 569–579 CrossRef CAS.
- C. P. Falter and R. Pitz-Paal, Appl. Therm. Eng., 2018, 132, 613–623 CrossRef CAS.
- A. Lidor, Y. Aschwanden, J. Häseli, P. Reckinger, P. Haueter and A. Steinfeld, Appl. Energy, 2023, 329, 120211 CrossRef CAS.
- W. X. Yang, H. Pan, G. Z. Yang, F. S. Han, Z. M. Dang, Y. J. Lu, Z. P. Shao and L. Y. Zhu, Int. J. Hydrogen Energy, 2024, 49, 1615–1624 CrossRef CAS.
- Y. Zhang, C. Xu, J. Chen, X. Zhang, Z. Wang, J. Zhou and K. Cen, Appl. Energy, 2015, 156, 223–229 CrossRef CAS.
- J. Chen, H. Kong and H. Wang, Appl. Energy, 2023, 343, 121161 CrossRef CAS.
- M. Roeb and C. Sattler, Science, 2013, 341, 470–471 CrossRef CAS PubMed.
- H. Kong, Y. Hao and H. Jin, Appl. Energy, 2018, 228, 301–308 CrossRef CAS.
|
This journal is © The Royal Society of Chemistry 2025 |
Click here to see how this site uses Cookies. View our privacy policy here.