Finding least-cost net-zero CO2e strategies for the European cement industry using geospatial techno-economic modelling†
Received
10th July 2024
, Accepted 13th September 2024
First published on 13th September 2024
Abstract
Cement production is responsible for approximately 7% of anthropogenic CO2-equivalent (CO2e) emissions, while characterised by low margins and the highest carbon intensity of any industry per unit of revenue. Hence, economically viable decarbonisation strategies must be found. The costs of many emission reduction strategies depend on geographical factors, such as plant location and proximity to feedstock or on synergies with other cement producers. The current literature lacks quantification of least-cost decarbonisation strategies of a country or region's total cement sector, while taking stock of these geospatial differences. Here, we quantify which intervention ensembles could lead to least-cost, full decarbonisation of the European cement industry, for multiple European regions. We show that least-cost strategies include the use of calcined clay cements coupled with carbon capture and storage (CCS) from existing cement plants and direct air capture with carbon storage (DACCS) in locations close to CO2 storage sites. We find that these strategies could cost €72–€75 per tonne of cement (tcement−1, up from €46–€51.5 tcement−1), which could be offset by future costs of cement production otherwise amounting to €105–€130 tcement−1 taking the cost of CO2e emission certificates into account. The analysis shows that for economically viable decarbonisation, collaborative and region-catered approaches become imperative, while supplementary cementitious materials including calcined clays have a key role.
Sustainability spotlight
Cement production, a major source of industrial emissions, urgently needs cost-effective emission reduction strategies. Decarbonising cement production is challenging, because it not only requires high temperatures but most of its CO2 emissions stem from releasing CO2 from limestone directly. While multiple different interventions for emission reduction have been suggested, many of them are going to work better in some locations than others. In this article we tackle the question, which mix of decarbonisation strategies are likely to be cheapest, taking multiple European regions as case studies and investigate how collaboration among cement producers can influence their costs to reach net-zero CO2e emission by 2050. This issue aligns with SDG 9 (Industry, Innovation, and Infrastructure) and SDG 13 (Climate action).
|
Introduction
CO2-equivalent (CO2e) emissions must reach net-zero by 2050 (also referred to as deep/full decarbonisation) to limit global warming to 1.5 °C.1 The cement industry alone is responsible for 7% of anthropogenic CO2e emissions.2,3 As the use of cement is essential for economic growth with a projected global market size of reaching 6.08 billion tonnes per year (a−1) in 2026,4 reducing cement's carbon intensity is vital. While alternative building materials (e.g., wood) could be used in some cases, it seems unlikely that cement can be replaced entirely, and therefore zero-carbon production practices need to be developed and implemented.5 Reducing CO2e emissions in the cement industry is particularly challenging: cementitious products are characterised by high emissions and low margins,6 leaving limited room for investments in decarbonisation methods, while the high process-inherent emissions reduce the technological options to produce “net-zero-CO2e” cement.
Cement production involves limestone mining followed by calcination to produce clinker, before it is ground and blended with other materials (e.g., gypsum) to reach specified cement properties. The calcination step is the main CO2 contributor, stemming from two sources. It requires high temperatures (1400–1500 °C
5), resulting in high energy-related emissions (from using fossil fuels such as coal), and causes CO2 to be released from limestone itself as process-inherent emissions (eqn (1)), accounting for approximately 60% of cement's total CO2e emissions.7
|  | (1) |
Hence, to significantly reduce CO2e emissions either the use of clinker must be reduced, or the produced CO2 needs to be abated, e.g., via CO2 capture and storage (CCS). A review of the academic literature and policy reports suggests a multitude of potential decarbonisation strategies (Fig. 1).6,8,10,16–18 As there are two major emissions sources (energy-related and process-inherent), it may be necessary to consider several complementary approaches for addressing each source.
 |
| Fig. 1 Map of suggested interventions for emission reduction in cement production. Compiled from academic literature and policy advise reports5,6,8–15 (Table S2†). Red-dotted interventions are investigated here. Classification of interventions based on Favier, et al.8 | |
Decreasing energy-related emissions can be accomplished by implementing energy efficiency measures and by fuel substitution. While substantial gains in efficiency have been made using these methods in recent years,8 to further decrease energy-related emissions alternative fuels6,8–11 or the adoption of process electrification13 have been suggested.
To reduce process-inherent emissions, the cement industry has used clinker substitutes known as supplementary cementitious materials (SCMs). These SCMs can be either industrial by-products (such as steel slag and fly ash) or natural minerals (like limestone and natural pozzolans).8,11,12,19,20 However, their use as a emission reduction measure is limited as they only substitute clinker partially and the availability of some industrial by-products is expected to decline in the future due to the implementation of more environmentally sustainable production processes in other industries.21 Moreover, the use of SCMs has limitations related to the overall strength and workability of the cement (including increased water requirements and altered curing time).12 Therefore, these measures alone will not suffice to mitigate all process-inherent emissions. Hence, the complementary use of emerging technologies such as alternative clinkers and novel SCMs (e.g., calcined clay cements), carbon capture, utilisation (CCU, e.g., CO2 mineralisation), and storage (CCS)10 as well as carbon dioxide removal (CDR, e.g., direct air capture and storage (DACCS)), is essential.
A critical remaining question is how countries' cement sectors and individual cement plants can reach net-zero-CO2e-emissions in a cost-effective manner? Cement plants are widely distributed across Europe (282 integrated cement plants located in Western Europe alone,22Fig. 2B), due to the low economic viability of transporting cement over long distances (90% of all cement is transported less than 281 km29). This also means that the economic viability of the aforementioned decarbonisation strategies depends heavily on plant location. For example, calcined clay cements require suitable kaolinite clays,30–32 CO2 mineralisation requires earth alkaline metal oxide containing minerals (such as olivine-bearing rocks which contain forsterite (Mg2SiO4
23,33)) and carbon capture and storage requires suitable underground CO2 storage sites (e.g., depleted oil and gas fields34), each of which are found in different locations in Europe (Fig. 2A). Therefore, policy and industry decision-makers face the challenge of selecting suitable decarbonisation strategies for a wide range of cement plant locations to decarbonise the sector as a whole.
 |
| Fig. 2 Available locations for production of olivine-bearing rocks23 and kaolinite clays24–26 and for offshore CO2 storage27,28 of relevance for the here analysed regions (i.e., Ireland, United Kingdom, Germany, Portugal and Spain) (A). Integrated cement plant locations in Europe22 (B). Regions analysed in this study are marked in red. | |
These strategies need to be based, among others, on comparative ex ante techno-economic assessments to evaluate the economic performance of each potential ensemble of decarbonisation interventions evaluated in a specific locational setting. However, techno-economic assessments that compare a suite of emission reduction technologies for the cement industry are sparse, while some generic analyses of individual technologies exist (e.g., carbon capture,35 calcined clay cements,31 CO2 mineralisation36). With CO2e neutrality goals only one or two investment cycles away, policy and industry decision-makers are in urgent need of detailed location-specific assessments, to help determine their technology and investment strategies.
To address this gap, we here present a techno-economic geospatial analysis for three selected case study regions (i.e., United Kingdom and Ireland (UK&IRE), Germany (GER) as well as Portugal and Spain (PT&ES)) to cover the heterogeneity of regions across Europe. By providing a geospatial assessment of these strategies across various cement plants in Europe, we offer a novel framework for optimising decarbonisation efforts in the cement industry tailored to local differences, resources, and constraints, filling a current gap in the literature. We developed a mixed-integer linear programming model to determine least-cost emission reduction strategies for the entire industry in one region considering several selected interventions which either aim to reduce the clinker content, store CO2 in cementitious products or capture CO2 from the atmosphere. The goal of this study is to shed light on emission reduction strategies in the cement industry while considering synergies between cement plants as well as avoiding path dependencies (i.e., earlier investment decisions affect, hinder future investments37). The key contributions of this study include:
• For the first time, least-cost, full cement decarbonisation strategies for selected European regions are presented, accounting for geospatial differences of individual cement plants.
• The value of collaboration between cement companies is quantified, showing the need for a concerted approach versus a single mover strategy.
• The value and effects of including selected abatement strategies is quantified, e.g., of using CCS or calcined clays.
• Optimal investment sequences for the cement sector are modelled to avoid technology lock-ins that may lead to higher final costs.
• We show that collaborative, full, decarbonisation of cement sectors can be cost effective viz-a-viz expected CO2 emissions taxes.
Methodology
To investigate net-zero CO2e emission strategies for the cement industry, considering transport costs for feedstocks and synergies between decisions of multiple cement plants, we first conducted a literature review (Methodology – Literature review) and selected suggested interventions (Methodology – Selected Interventions), before estimating their costs at maturity (Methodology – Iterative learning for CO2 emission reduction strategies). Second, we calculated the transport costs for feedstocks for different cement plant locations (Methodology – Transport of bulk materials) and fed both results (i.e., cost estimates for interventions and transport costs) into a mixed-integer programming model (Methodology – Model structure). To investigate least-cost emission reduction strategies while avoiding path dependencies which would only allow certain interventions to be selected at a specific time, a solver first finds the least-cost strategies for reaching net-zero CO2e emissions for an entire region (to be reached in the EU in 2050
38) by implementing interventions at cement plants (e.g., installing CO2 capture) and/or constructing infrastructure (e.g., CO2 pipelines, CO2 injection wells). After finding a least-cost solution for reaching net-zero, strategies for intermediary targets (e.g., 50% emission reduction) were selected by the solver via back-casting (Methodology – Optimisation Framework). Because the solver finds a least-cost strategy for the entire region, in a last step we allocated costs for shared infrastructure to individual cement plants (Methodology – Post-processing).
Literature review
There are a multitude of strategies suggested for emissions reduction in the cement industry (Fig. 1). A holistic review of technology options and their emission reduction potentials was performed by Favier, et al.8 Their review concluded that decarbonisation should be tackled in all stages of the value chain (from clinker, cement to concrete use). To reach deep decarbonisation multiple interventions might have to be implemented simultaneously, among them increasing energy efficiency and introducing alternative fuels, reducing clinker content in cement blends or the use of alternative clinkers as well as carbon capture, utilisation, and storage (CCUS). These suggestions were mostly in line with the roadmap by the European Cement Association,10 which estimates the biggest share of emission reductions could be implement through CCUS, alternative fuels and via clinker substitutions. To investigate the costs of carbon capture at cement plants, Voldsund, et al.35 provided a detailed techno-economic analysis showing that carbon capture not only can be costly (€42.4 € tCO2,avoided−1 to €83.5 tCO2,avoided−1), but also cannot be used to capture all emissions from a cement plant (e.g., due to energy penalties). Hence, residual downstream emission will have to be captured elsewhere using carbon dioxide removal techniques, like direct air capture and storage. To this end, Young, et al.39 provided a detailed assessment of different direct air capture technologies as well as their future costs. As clinker substitutes or alternative clinkers Favier, et al.8 reviewed multiple different options, many of which are in early stages of development or for niche markets (e.g., alkali activated systems,8 magnesia cements,8 CO2 concrete curing in precast concrete production20) while the use of calcined clays was suggested of having the highest potential, which was confirmed by other researchers.31,32,40 In Strunge et al.36 among other researchers,41,42 we previously showed that CO2 mineralisation to produce SCMs, which both stores CO2 permanently and replaces clinker can have similarly a large emission reduction potential. To investigate alternative fuels in the cement industry, Kusuma, et al.43 reviewed multiple bio-based feedstocks such as wood pallets and suggested that a combination of biofuels with CCS might lead to high emission reductions through synergetic effects.
Selected interventions
To select potential interventions for this study, we first reviewed potential emission reduction strategies for the cement industry (Fig. 1) and selected strategies (interventions) with high emission reduction potential. We chose alternative fuels (biomass), calcined clay cements, CO2 mineralisation, carbon capture and storage (CCS), and direct air capture and storage (DACCS). These interventions span the domain of decarbonisation options presented in Fig. 1, aside from recycling options.
The cement industry currently predominantly uses waste and industrial by-products44 as alternative fuels, which show limited effectiveness due to their fossil carbon content (i.e., fossil carbon is emitted during combustion of waste tyres, a common fuel replacement used).10 Therefore, we only considered biofuels as wood pellets from North America as means to decrease energy-related emissions as the availability of biomass from Europe is limited (Note S1 and Table S1†).
We considered calcined clay cements, particularly using kaolinite clays (Al4[(OH)8|Si4O10]), as a means of reducing emissions by blending clinker (50%) calcined clay (30%), limestone (15%) and gypsum (5%), forming LC3 (Limestone Calcined Clay Cement).31 This blend can significantly reduce emissions due to clinker replacement and lower calcination temperatures of clays, thus lower energy emissions per unit of cement produced31,40,45 (Note S4†).
We considered CO2 mineralisation as means of long-term CO2 storage in cementitious products, where captured CO2 reacts with minerals to create stable carbonates, producing supplementary cementitious materials as clinker replacements (we considered a substitution level of 30% clinker). As feedstock we here considered olivine-bearing rocks (i.e., peridotite which contain forsterite (Mg2SiO4)), due to their availability and low costs36 (Note S3†).
Due to its high emission reduction potential, we included CCS (i.e., capturing CO2 directly from cement plant flue gas and transporting it to geological storage sites). We only considered offshore CO2 storage due to lower risk perceptions of lay people compared to onshore storage46 (Note S2†).
To offset all residual emissions, thus allowing fully net-zero-CO2e supply chains, we included DACCS for carbon dioxide removal from the atmosphere47,48 (Note S5†).
As some combinations of interventions are possible (e.g., CCS and CO2 mineralisation), while others cannot be combined (e.g., CO2 mineralisation and calcined clay cements), we defined a set of interventions which can be considered by the solver. We here considered the following emission reduction interventions in the model:
(1) Conventional cement production + CCS.
(2) Conventional cement production + biofuels.
(3). Conventional cement production + biofuels + CCS.
(4) Conventional cement production + CO2 capture and mineralisation.
(5) Reduced conventional cement production + CO2 capture and mineralisation + biofuels.
(6) Reduced conventional cement production + CO2 capture and mineralisation + biofuels + CCS.
(7) Reduced conventional cement production + CO2 capture and mineralisation + CCS.
(8) Reduced conventional cement production + calcined clay.
(9) Reduced conventional cement production + calcined clay + biofuels.
(10) Reduced conventional cement production + calcined clay + CCS.
(11) Reduced conventional cement production + calcined clay + biofuels + CCS.
(12) Direct air capture and storage.
Iterative learning for CO2 emission reduction strategies
Most of the here considered interventions/technologies are not yet mature. As technologies can be expected to decrease in cost through iterative learning, from the first plant (first-of-a-kind) to when n plants have been built (Nth-of-a-kind), we used learning curves to estimate the cost of the interventions. Learning curves are essential tools in assessing the Nth-of-a-kind cost of new technologies, particularly in fields like CCUS.49 We followed the approach developed by Rubin et al.50,51 where we first estimated first-of-a-kind costs by applying accurate contingencies, according to technology maturity (Table S7†) and then used leaning curves to approximate costs of Nth-of-a-kind interventions (eqn (10) and (11). For CO2 mineralisation, CO2 capture and calcined clay production we followed Greig, et al.52 and considered 20 built plants as technological maturity. For these interventions we used a learning rate of 10.55%, the mean of suggested learning rates suitable for CO2 capture technologies Rubin, et al.53 For direct air capture we used estimates for Nth-of-a-kind plants from Young, et al.,54 which also followed the same methodology. But here, instead of a fixed number of plants, we considered a total cumulative capacity of 1 Gt a−1 which is likely to be reached by 2050
54 because many industries beside the cement industry will likely drive the investments and thus iterative learning of DAC technologies. For biofuel we did not consider any capital expenditures and hence do not consider technological learning. For CO2 infrastructure (i.e., pipelines, recompression stations between onshore and offshore pipelines) as well as CO2 injection sites, we did not consider technological learning.
Case study regions
Due to limitations in data availability or quality as well as computational time to solve the model, we selected case study regions in Europe. To cover a wide range of the heterogeneity of regions across Europe, we chose United Kingdom and Ireland, Germany, and Portugal and Spain as case study regions (Table 1, Fig. S5 and Note S6†).
Table 1 Case study descriptions
|
United Kingdom and Ireland |
Germany |
Portugal and Spain |
Current databases only consider onshore CO2 storage in Spain,27 which we do not consider in this study (Note S2).
|
Number of active integrated cement plants |
16 |
31 |
34 |
Region characteristics |
Much offshore CO2 storage capacity at close proximity27 |
Limited offshore CO2 storage capacity located only to the north27,28,55 |
Offshore CO2 storage in Portugal available27a |
No olivine-bearing rock deposits but kaolinite clays present in the south of England26 |
No olivine-bearing rock deposits available, but large amount of potential kaolinite clay deposits in Germany and surrounding countries (i.e., Hungary, Czech Republic)24 |
Olivine-bearing rock deposits23 and kaolinite clay deposits available in the north of Spain25 |
Transport of bulk materials
We evaluated the material transport for all case study regions (i.e., United Kingdom & Ireland, Germany, and Portugal and Spain). We calculated the transport costs of biofuel, minerals, and clay for each region. The results show that large regional differences can be expected (Table 2 and Fig. S6†). Note that end-to-end transport costs were calculated for each feedstock to each single cement plant (see Bulk transport modelling).
Table 2 Results of bulk transport calculations (see Bulk transport modelling for methods)
|
United Kingdom and Ireland |
Germany |
Portugal and Spain |
Biofuel |
6–20 € t−1 (transport emissions: 136–183 kgCO2e t−1) |
17–48 € t−1 (transport emissions: 186–327 kgCO2e t−1) |
14–31 € t−1 (transport emissions: 150–200 kgCO2e t−1) |
Olivine-bearing rocks |
5–13 € t−1 (transport emissions: 42–64 kgCO2e t−1) |
7–23 € t−1 (transport emissions: 16–85 kgCO2e t−1) |
3.3–22 € t−1 (transport emissions: 12–85 kgCO2e t−1) |
Clay |
11–18 € t−1 (transport emissions: 34–80 kgCO2e t−1) |
1–13 € t−1 (transport emissions: 1–16 kgCO2e t−1) |
9–28 € t−1 (transport emissions: 28–104 kgCO2e t−1) |
Model structure
The constructed model consists of three components: (1) international bulk transport model (INTERNAT-BT), a model that computes transportation costs for various feedstocks (such as olivine-bearing rocks for CO2 mineralisation), (2) industrial decarbonisation resource technology network model (INDiECAR-RTN), a mixed integer linear programming (MILP) model that allows us to build interventions using component models on existing cement plants and designs a CO2 storage network (if needed), with the objective to minimise the total system cost (TSC) for a given emission reduction target and (3) cost allocator (COSTALLO), a post-processing model to allocate costs to each cement plant (Fig. 3). The techno-economic model uses cost functions and mass and energy balances for each unique intervention as inputs.
 |
| Fig. 3 Schematic representation of developed model. Additional details in Fig. S1–S4.† | |
All models were developed using Python 3.9. To solve these complex problems, we used the commercially available solver CPLEX which uses a combination of algorithms (i.e., simplex algorithms, primal-dual logarithmic barrier algorithms, a sifting algorithm) on a high-performance computing cluster. The solver finds quasi-optimal solutions given a set mixed integer programming (MIP) gap (i.e., upper bound to solutions without constraints). The quasi-optimal solutions thus can slightly differ from run to run, given multiple solutions in a certain MIP gap exist.56 For the majority of the runs, we specified a mip gap of 0.02% or a maximum runtime of 4 hours per run. Fig. 3 gives a high-level representation of the models used and their interactions.
Bulk transport modelling
The transportation cost for bulk goods varies with transportation distance and (combination of) available modalities. To find least cost transport options, we developed a transport model INTERNAT-BT, based on work by Collis and Schomäcker57 and Benita, et al.58 This model allows comparison of various transport mode combinations, including shipping, rail, and road, to identify the most cost-effective options. For its input data, the model relies on shapefiles representing European railways, sourced from Mapcruzin,59 offshore shipping routes derived from automatic identification system data obtained from Halpern, et al.,60 and port information sourced from Novikov.61
To determine the shortest transportation routes, the model initially creates simplified networks based on the provided shapefiles to reduce computational demands. It then employs the Dijkstra algorithm to compute the shortest paths. However, due to the significantly larger scale of the European road network compared to the rail network, which can result in computationally intensive network analysis, we implemented an application programming interface (API) integration with openstreetmaps.org (http://openstreetmaps.org/) (Fig. S2†). The cost of transportation (Ctransport) for a specified mass flow of bulk material (ṁbulk) are subsequently calculated following eqn (2), considering multiple transport mode options represented by i choices and the calculated distances (dist) on each route as well as specific prices for transport (π).
| Cbulk transport = ṁbulk·MIN(i=1…n)[πtruck·∑disttruck + πtrain·∑disttrain + πship·∑distship] | (2) |
We calculated transport cost routes comparing 4 different possible combinations: (1) transport via ship, rail, and road, (2) transport via ship and road, (3) transport via rail and road, and (4) transport solely via road (Fig. S2†). To reduce the number of runs, we only calculated the least-cost transport routes for a given bulk material (e.g., olivine bearing rock) by first finding the n-closest feedstock locations based on the linear distance between resource and the cement plant, with n reaching from 2–4 depending on the feedstock (i.e., we limited finding the least-cost route for kaolinite clay for a given cement plant to the 4 closest clay sites and disregarded clay sites further away).
Depending on the selected modes of transport, the accuracy of the transport model differs due to variable data quality. The highest accuracy can be assumed for road transport as the route is calculated using an API integration to openstreetmaps.org (http://openstreetmaps.org/) (accuracy of 4–5m
62 reported). The used shapefiles for train and ship transport are shown in Fig. S10.† The least accurate transport cost calculation can be expected from ship transport as the shapefile uses existing transport data (with highest resolution in North America) and therefore some less-frequented routes may not be accurately captured. However, given the small costs of offshore shipping, it does not have a significant impact on results. For train transport the entire European railways network was considered. However, in reality freight trains may have to travel a longer distance as in some country's passenger trains may have priorities on certain routes.
Quantity of interest
As the quantity of interest for this geospatial-economic model, we here chose the change in levelised cost of product ΔLCOP (i.e., added costs per tonne of cement ṁcement) in [€ tcement−1], which combines capital costs, here, total capital requirements (TCR) and operational expenditures (OpEx) for each cement plant location g. Note that we only consider ordinary Portland cement with a clinker factor of 100%, which can be used as is, or to formulate other standard cement blends.
To calculate ΔLCOP, we applied the methodology described earlier in Strunge et al.36 which we developed in accordance to existing guidelines for techno-economic assessments in this field.50,63,64 We discounted the capital costs (i.e., TCR) using interest rate i and the plant's expected lifetime L.65 The interventions can be built at individual cement plants, while CO2 transport infrastructure, storage injection wells and direct air capture plants are investments shared by multiple plants. Therefore, they were allocated towards each cement plant location g that uses them (eqn (3) till eqn (8)).
| ΔLCOPtotal,g = ΔLCOPintervention,g + ΔLCOPCO2 transport,g + ΔLCOPCO2 storage,g + ΔLCOPNET,g | (3) |
|  | (4) |
|  | (5) |
|  | (6) |
|  | (7) |
|  | (8) |
Here,
ṁcement,g represents the cement plant's capacity in location
g,
yg represents the set of pipeline segments CO
2 is transported through from location
g to the storage site,
ṁCO2transported,pipeline,y describes the total amount of CO
2 transported in pipeline
y,
ṁCO2stored,g describes the amount of CO
2 captured and stored from the cement plant in location
g and
ṁCO2offset,g represents the amount of emitted CO
2 from a cement plant in location g that is offset using carbon dioxide removal technologies at location g or another location. OpEx
savings,g refers to operational expenditures that are saved compared to conventional production (
e.g., costs of energy, feedstock for clinker replacement by novel supplementary cementitious material).
We calculated the TCR for interventions using the total direct costs (TDC) as well as total overnight costs (TOC) for each technological intervention (eqn (9)).
|  | (9) |
The factors findirect, fprocess, fproject, fowner account for indirect costs, process contingencies, project contingences and owners' costs respectively. To calculate the TCR for an nth of a kind plant we used (eqn (10) and (11)).50,66
|  | (10) |
|  | (11) |
N characterizes the number of plants built, LR the learning rate, E the experience factor, i the interest during construction and tconstruction the estimated time for construction in years. The OpEx were derived using mass and energy balances as a basis to calculate the costs of utilities and feedstocks, the location specific costs of material transport and the costs of labour (eqn (12)). Here, the amount of feedstock or utility needed is represented bywi, πiis the price for feedstock or utility for resource i and location g.
| OpEx = ∑wiπi + OpExfixed + ∑Cbulk transport,i,g | (12) |
To scale the TCR for a given cement plant, we used a linear scaling approach, so it could be used in a linear programming formulation.
|  | (13) |
To evaluate the CO2e emissions offset by an intervention, we modified the approach used by Ostovari, et al.67 In line with their methodology, we calculated the climate change impacts following the Intergovernmental Panel on Climate Change by using the European Commission's recommendations in the International Reference Life Cycle Data Handbook.68
For assessing the climate change effects of an intervention, we used the carbon footprinting method. We limited this study's scope to climate change impacts measured in CO2e emissions, considering other impacts as beyond our study's techno-economic focus. In the emissions einterventions, we accounted for the emissions by the used feedstocks efeedstocks, their transport to the cement site etransport (containing emissions from each used mode of transport), emission for electricity eelectricity and heat eheat used in the process. From that burden we subtracted the emission reductions through CO2 that is bound in the product or stored offshore, estored, and emissions that are avoided by replacing clinker production ereplace (eqn (14)).
| eintervention = (efeedstocks + etransport + eel + eheat) − (estored + ereplace) | (14) |
Optimisation framework
The optimisation framework INDIeCAR-RTN used in this work was built on a resource technology network (RTN) formulation by Sunny, et al.69 based on Pantelides.70 We described our adapted framework in Küng, et al.71 In this RTN model we described a region using multiple grid cells, where each cell (g) represented a specific functional location (i.e., cement plant site, potential CO2 storage site, CO2 terminal site to connect offshore pipelines to the onshore grid or trunkline location where shared pipelines networks can be pre-defined, Table S3†). The optimisation model's objective function was to minimise the total added levelised costs for cement production (ΔLCOPtotal) as a sum over the set of all cement plant locations (Gc) (eqn (15)) for a given emission reduction target. | 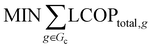 | (15) |
To solve this problem, we used a set of equations as constraints. The core element in the RTN formulation are sets of resources including cement, biofuel, olivine bearing rocks, emitted CO2, captured, and liquidised CO2 as well stored CO2. The model must solve these mass balances for each grid cell and each resource. Beside the resources, the model contains interventions that can be installed at grid cell locations (e.g., installing CO2 capture at a cement plant to reduce the emitted CO2 and convert it into captured CO2 or installing injection wells to convert captured CO2 into stored CO2). Additionally, the model contains a range of infrastructure interventions to transport resources between grid cells, such as onshore CO2 pipelines of different sizes. The general concept of the RTN formulation entails that all resources within each grid cell must be balanced, i.e., production within the cell, flows to the cell via transport, local demand and outflows (eqn (16))
|  | (16) |
Here, the term
εg,r,t denotes the emission rate of resource
r in grid cell
g at time
t, imp
r,g,t signifies the rate of importing resource
r (importable resources are for example electricity and olivine bearing rocks which are imported from outside of the grid cell). The summation

describes the conversion rate of the resource for all installed interventions with
μj,r being the conversion rate of resource
r (
e.g., biofuel usage) by intervention
j (
e.g., fuel switching to biofuel), while
pj,g,t is the production rate of the (installed) intervention
j (
e.g., output of cement plant) with a negative value indicating resource consumption and a positive value indicating resource production. The term

sums up all storage technologies in a grid cell where
λSj,r,g,t delineates the rates of storing resource CO
2 using storage technology
j,
i.e., injection wells. The term

sums up all carbon dioxide removal technologies, which can be installed at any grid cell and here consist of direct air capture technologies. Lastly, the final term considers the inflow and outflow of resources, denoted as
qĝ,g,r,d,t and
qg,ĝ,r,d,t respectively, between grid cell
g and its counterpart
ĝ through distribution installation
d (
e.g., 9 inch onshore CO
2 pipeline).
In the RTN model, all resources must be balanced meaning the overall sum must be zero, except for CO2. Excess CO2 is released to the environment. Eqn (17) establishes the total net CO2 emissions for the system over all grid cells (G) and major time frames (T).
|  | (17) |
To solve case studies, we hence set a CO2 reduction objective, which served as a constraint to the solver while the cement production of each plant needs to be fulfilled. Emissions can be reduced through either intervention, such as implementing carbon capture processes, or via installing CDR (here only direct air capture plants).
Each action, e.g., choosing to build an intervention in a grid cell, comes with associated costs as total added levelised costs for cement production (LCOPg). The solver's objective is to determine the optimal combination of technologies and infrastructure choices (integer decisions) that can meet the resource demands as constrained by eqn (16), comply with the CO2 reduction constraint, and simultaneously minimise a cost-based objective function (eqn (15)).
The outcomes generated by this optimisation framework represent economically and environmentally optimal clusters of configurations that fulfil a predefined CO2 or greenhouse gas (GHG) reduction target. To investigate optimal investment sequences while avoiding lock-in effects, we implemented a back-casting approach, where the solver starts with interventions selected for full decarbonisation and when given a decarbonisation goal (e.g., 50%), it selects the least-cost options among these interventions.
Post-processing
Given that INDiECAR-RTN finds a least-cost solution for the entire system, we developed a post-processing model COSTALLO to allocate the costs towards the individual cement plants. Here, interventions built at a cement plant were directly allocated to the cement plant located in this grid cell (eqn (4)) and costs for CO2 transport, storage and direct air capture (eqn (5)–(7)) were shared and only partially allocated towards each cement plant (Fig. S4†). While for CO2 storage and direct air capture installation the costs were allocated considering a plant's captured CO2 and offset CO2 respectively, we used the Dijkstra algorithm to determine the route of captured CO2 from each cement plant to a connected storage site. All pipeline investments were shared among all cement plants using a specific pipeline section on their route according to their amount of captured CO2 and length travelled on the pipeline section. This approach also allowed us to introduce shared infrastructure with other industries (i.e., trunk lines) and allocate the costs towards by the solver connected cement plants.
Results
We here present the results of the analysis across three case study regions (UK&IRE, GER and PT&ES), selected for their different levels of access to feedstocks and offshore CO2 storage.
Full decarbonisation of the cement industry will require large investments in CO2 transport and storage networks and carbon dioxide removal
The model results show that calcined clay cements coupled with CCS and DACCS are the least-cost ways to fully decarbonise the cement industry for all regions studied (Fig. 4), due to favourable economics for calcined clay cements (because of its low heat requirements, Note S4†) and comparably short transport distances onshore. High transport costs and emissions for both biofuels and CO2 mineralisation (Table 2) limit their economic viability compared to the use of low-cost clays as clinker replacements in the cement industry. Notably, for one plant in the UK (i.e., Wales), distant to the designed CO2 transport network and proximity to kaolinite clay sites in South England (Fig. 2A) no CCS was chosen by the solver. Showing that in case of large distances to shared infrastructure, it can be least-cost to divert from using CCS as connecting pipelines would fully have to covered by this individual cement plant (Methodology – Post-processing).
 |
| Fig. 4 Model results for reaching net-zero-CO2e-emissions in (A) United Kingdom and Ireland, (B) Germany and (C) Portugal and Spain. Each circle represents one integrated cement plant and each orange pentagon a direct air capture location. Circle colours represent interventions. Line colours indicate CO2 transport pipe thickness. Right panels show marginal CO2e abatement cost curves for each region, each bar represents a single cement plant. Total capital requirements (TCR) describe the capital expenditures (CAPEX) of an investment. Assumptions and used calculations shown in Tables S6–S12, S14–S24.†. | |
Our model predicts the full decarbonisation of the different case study regions could be achieved with added levelised costs of (cement) production (ΔLCOP) of €75 per tonne of ordinary Portland cement (tcement−1) (UK&IRE), €71 tcement−1 (GER), €74 tcement−1 (PT&ES) compared to European average levelised cement costs of €46–€51.5 tcement−1 (Fig. 4). This translates into annually added costs for the construction industry of €738M a−1 (UK&IRE), €2555M a−1 (GER) and €1529M a−1 (PT&ES) or 0.4% (UK&IRE), 0.7% (GER) and 0.9% (PT&ES) of the industry's annual production value.72,73 Assuming the case studies are representative of the entire European Union and United Kingdom, added costs of approximately €19 billion annually could be expected, approximately 0.1% of their gross domestic product.74,75 Most of the investment costs lie in direct air capture plants with €2322M (UK&IRE), €4820M (GER), €6933M (PT&ES) followed by CO2 transport and storage infrastructure with €1524M (UK&IRE), €3302M (GER), €5035M (PT&ES) (Fig. 4). Direct air capture and CO2 transport and storage accounted for 49–53% and 35–39% of total investment costs (which don't take place at cement production sites), while the interventions on the cement sites accounted for 12% of the total investment costs only. The high observed cost share for DACCS is commensurate with the observation that the other interventions are unable to fully decarbonise cement plants, even when implemented in tandem.
Collaboration between companies to design CO2 storage transport and storage networks significantly reduces costs for the majority of plants
The above results were generated assuming full collaboration and coordination between cement producers in a country/region (Fig. 4). This is a strong assumption and to test its effect we quantified the difference in total decarbonisation cost if coordination only happens within, but not between holdings (the European cement market consists of a few large parent companies owning multiple plants in a region as well as smaller producers owning only a single or few plant(s) (Table S26†)). To that end, we ran the simulation again for each parent company, where a decarbonisation strategy must be found only taking the plants of one company into account (e.g., when CO2 transport and storage was selected, a pipeline network was optimised for all plants in a parent company's portfolio). The difference in costs between a collaborative approach (Fig. 4) and a non-collaborative approach for each plant is shown in Fig. 5. The results show that this non-collaborative, uncoordinated approach could yield significantly higher costs to reach full decarbonisation: additional annual costs – on top of the previously determined costs for decarbonisation in a collaborative approach (Fig. 4) – were calculated as €94M a−1 (UK&IRE), €159M a−1 (GER) and €116.5M a−1(PT&ES) respectively. Per tonne of cement this translates into additional costs of 2.4€ tcement−1 (PT&ES) to 6.1€ tcement−1 (UK&IRE), Table S26.† While the presented costs can be seen as an upper bound as we assume an operation at full capacity with an average clinker factor of 0.737,76Fig. 5 illustrates that in this scenario these additional costs for decarbonisation will mostly have to be covered by a few companies, primarily by the companies that operate fewer plants. Additionally, in the case of central Spain the results illustrate that for some plants an uncoordinated approach could also lead to slightly lower costs for individual plants compared to a fully coordinated approach. This cost reduction was shown for some plants where the non-collaborative approach led to significantly smaller transport distances for CO2 (i.e., a direct pipeline was built to the shore where in the collaborative approach the pipeline had to be diverted to other cement plants).
 |
| Fig. 5 Additional costs for reaching full decarbonisation in a non-collaborative approach compared to the coordinated approach. (A) United Kingdom and Ireland, (B) Germany and (C) Portugal and Spain. Model optimisations were done for each parent company separately. Each circle represents one integrated cement plant. The size of the circle indicates additional annual costs in million € per year (M€ a−1) compared to the whole system optimisations in Fig. 4. The colour of each circle indicates the parent company taken from Tkachenko, et al.22 Note, colours between panels (e.g., A and B) may have been used multiple times for different parent companies. Detailed results shown in Table S26.† Note, to increase visibility pipelines are not shown here but individual pipeline networks were built by the solver for each parent company. | |
Elaborate CO2 transport networks are key to lower costs of reaching net-zero CO2e emissions. Absence leads to biomass use
Least-costs strategies for full decarbonisation will need CO2 transport and storage, and therefore elaborate CO2 transport networks. The absence of such infrastructure will increase the costs of reaching full decarbonisation by another €9 tcement−1 to €10 tcement−1 (Fig. 6) translating into additionally added costs of €99M a−1 (UK&IRE), €284M a−1 (GER) and €186M a−1 (PT&ES) respectively. In the absences of CO2 transport infrastructure, biofuel becomes a key strategy for many cement plants limited to transport costs (plants further inland do not select biofuel). While biofuel becomes a prevalent strategy in the absence of CO2 transport infrastructure, the results show comparably small differences between plants using biofuel and the ones which do not. Note that in this study we solely considered biomass as fuel from North America, due to the limited availability of this resource in Europe (Table S1†), leading to comparably high transport costs as well high emissions (Table 2).
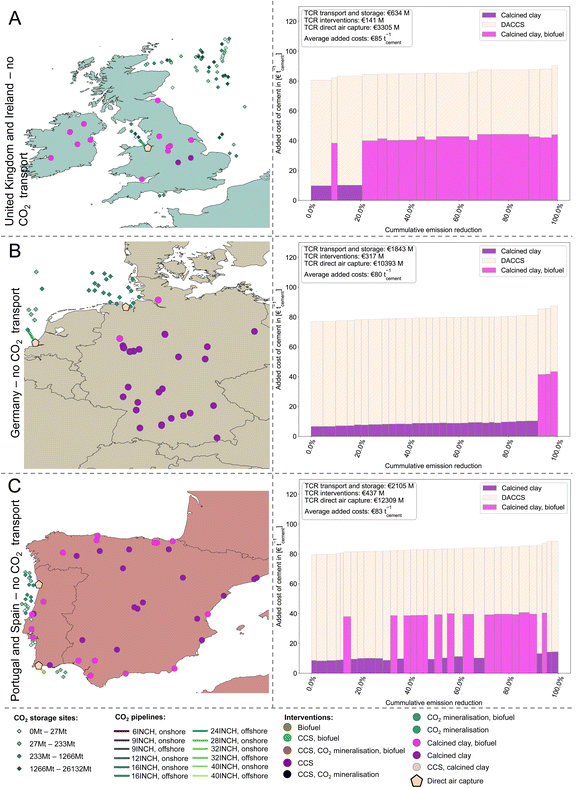 |
| Fig. 6 Model results for reaching full decarbonisation in the absence of onshore CO2 transport in (A) United Kingdom and Ireland, (B) Germany and (C) Portugal and Spain. Each circle represents one integrated cement plant and each orange pentagon a direct air capture location. Circle colours represent interventions. Line colours indicate CO2 transport pipe thickness. Right panels show marginal CO2e abatement cost curves for each region, each bar represents a single cement plant. Total capital requirements (TCR) describe the capital expenditures (CAPEX) of an investment Assumptions and used calculations shown in Tables S6–S12, S14–S24.† | |
Calcined clay cements could become a breakthrough technology overall lowering the costs of full decarbonisation by €9–€15 per tonne of cement
As shown in (Fig. 4), calcined clay cements coupled with CCS could become a breakthrough technology for deep decarbonisation due to their low heat requirements. Scenarios excluding the use of calcined clay cements increase the estimated added levelised costs by €9 tcement−1 to €15 tcement−1 (compare Fig. 4–7). For plants located further inland, bio-fuel was not a least-cost intervention. Notably, for plants not using biofuel, the majority of the decarbonisation costs lie in the costs for DACCS plants, which are not located at the cement plant itself. The results show that when CCS is combined with the use of biofuels, a significantly smaller share of the costs was used for DACCS because its high decarbonisation through storage of biogenic CO2 leading to carbon dioxide removal from the atmosphere5 (i.e., when excluding emissions from transport of CO2 and feedstocks CCS with biofuel leads to 91% emission from 850 kgCO2e tcement−1 to 77 kgCO2e tcement−1 or 93–94% emission reduction when coupled with CO2 mineralisation or calcined clay cements, Fig. S8†). Note that this scenario also requires a CO2 pipeline from Germany to Dutch offshore storage sites, resulting from increased CO2 transport volumes.
Local resources (e.g., olivine bearing rocks) can become key if widespread implementation of breakthrough technologies fail
In the absence of calcined clay cements (e.g., due to low acceptance by the cement market), the use of CO2 mineralisation or biofuels become key strategies contingent on low cost of transport (i.e., local availability of feedstock or access to offshore transport lead to significant differences in transport costs, Table 2). In Germany and Portugal and Spain, the use of CO2 mineralisation becomes the main strategy after CCS (Fig. 7). In Spain, it is mostly plants located close to the coast that select this option, limited by high onshore transportation costs. In Germany, both in the north (close to the shore) and in the south (proximity to olivine-bearing rock deposits in northern Italy, Fig. 2) this intervention was chosen. Generally, in the absence of calcined clay options, a variety of different strategies are chosen and local differences play a larger role in selecting cost-optimal interventions (e.g., proximity to feedstock or storage site).
 |
| Fig. 7 Model results for reaching full decarbonisation without calcined clay cements in (A) United Kingdom and Ireland, (B) Germany and (C) Portugal and Spain. Each circle represents one integrated cement plant and each orange pentagon a direct air capture location. Circle colours represent interventions. Line colours indicate CO2 transport pipe thickness. Right panels show marginal CO2e abatement cost curves for each region, each bar represents a single cement plant. Total capital requirements (TCR) describe the capital expenditures (CAPEX) of an investment. Assumptions and used calculations shown in Tables S6–S12, S14–S24.† | |
Designing CO2 transport networks should be coordinated with other industries which also plan to implement CCS
It is unlikely the cement industry will be responsible for constructing their own CO2 transport infrastructure, this may rather become a commodity shared with other industries (e.g., steel production, waste incineration). We investigated the use of predefined trunk lines which are only partially used by the cement industry. We modelled currently planned projects for the United Kingdom and Germany (Table S4†), to which the solver was allowed to build connections. The solutions obtained showed to be similar to those without trunk lines (compare Fig. 4–8), strengthening the robustness of the of the network designs obtained earlier. Note this analysis was only run for the British Isles and Ireland, and for Germany. To our knowledge there are no current offshore CO2 transport plans for the Iberian Peninsula. The costs of decarbonising the cement industry may be fully offset by expected costs for greenhouse gas emission certificates, but first-of-a-kind investments remain to be overcome.
 |
| Fig. 8 Model results for reaching full decarbonisation considering currently planned CO2 pipelines in (A) United Kingdom and Ireland, (B) Germany. Each circle represents one integrated cement plant and each orange pentagon direct air capture location. Circle colours represent interventions. Line colours indicate CO2 transport pipe thickness. Line fading indicates a trunk line. Right panels show marginal CO2e abatement cost curves for each region, each bar represents a single cement plant. Total capital requirements (TCR) describe the capital expenditures (CAPEX) of an investment. Assumptions and used calculations shown in Tables S4, S6–S12, S14–S24.† | |
While these presented costs might appear high compared to current costs for cement production, they must be compared to future costs of unabated production including the societal costs of emitting CO2e. Generally, future costs for cement production will significantly increase during the coming decades due to increasing costs of CO2 emission allowances (i.e., in the European Union the EU emission trading system (EU ETS) and in the United Kingdom the UK ETS), which aim to incentivise implementation of emission reduction strategies. In the EU and the UK as well in some other regions of the world (i.e., California), CO2 allowances use a “cap and trade” basis. Legislators establish a maximum limit (cap) on the total greenhouse gas emissions allowed for covered installations. This cap diminishes each year according to climate targets and the certificate prices are determined by the market.77 Therefore, future costs of emitting CO2 are likely to increase but depend on emission reduction of other plants (i.e., demand and supply of certificates). Price estimates differ but are expected to lie between €130 tCO2e−1 and €160 tCO2e−1 in 2030 (€56 tCO2e−1 and €111 tCO2e−1 in 2025),78 leading to added levelised costs for ordinary Portland cement production of €111 tcement−1 to €136 tcement−1, significantly higher than all calculated costs in this study (Fig. 9A). While costs of certificates are likely to depend on market fluctuations and do not reflect the actual costs of emitting greenhouse gas emissions into the atmosphere, some suggest the consideration of social cost of carbon dioxide, which reflect the damages to society of emitting a tonne of CO2e and is a key indicator for climate policy development.79 Estimates for social cost for CO2e vary from $44 tCO2e−1 to $413 tCO2e−1 (€40 tCO2e−1 to €371 tCO2e−1) with the mean being at $185 tCO2e−1 (€167 tCO2e−1).79 Considering the social costs for CO2e emissions, cement production (ordinary Portland cement) hence would increase by €142 tcement−1, significantly outweighing the here calculated costs for full decarbonisation.
 |
| Fig. 9 (A) Comparison of results from different scenarios compared to added costs of cement production by CO2e certificates (2030)78 and social costs of CO2e emissions,79 with current emissions for clinker 850 kgCO2e tclinker−1 35 for ordinary Portland cement and no free-allocation of allowances, assuming mature technologies. Results for first-of-a-kind (FOAK) installations for (B) United Kingdom and Ireland, (C) Germany and (D) Portugal and Spain compared to added costs of cement production by CO2e certificates in 2030 and current (2024). Note, FOAK installations were calculated using the interventions selected assuming technology maturity presented in Fig. 4. These strategies do not have to be least-cost for FOAK deployment. | |
To compare costs of different technologies long term, technology maturity of the interventions must be considered. To this end, up to this point we only considered interventions at mature stage based on learning curve estimates49 (Fig. 4–8). For interventions like carbon capture or CO2 mineralisation we considered 20 plants52 to be built with significantly higher costs to reach maturity, while for direct air capture a cumulative capacity of 1 GtCO2 must be installed to reach the costs used here54 (Methodology – Iterative learning for CO2 emission reduction strategies). We repeated the analysis shown in (Fig. 4), assuming each region would independently build first-of-a-kind (FOAK) plants, second-of-a-kind plants and so forth (Fig. 9B–D). This shows these first decarbonisation projects will be significantly more expensive. While ETS prices expected for 2030 will increase costs for cement production to a similar level as FOAK plants, the impact of current ETS prices at €70 tCO2e−1 lead to added levelised costs for ordinary Portland cement production of €59 tcement−1 in the model (excluding free allocation). Thus, current ETS prices may not incentivise cement plants to implement FOAK installations. This presents a timing mismatch between decarbonisation costs and credits, suggesting alternative support may be needed to kick-start cement's decarbonisation path. Additionally, the results show that even when multiple plants are built and maturity for interventions at the cement plant is reached, DAC costs remain high as the cement industry cannot bring down the costs alone (e.g., decarbonising the German cement industry led to a cumulative DAC capacity of 8 MtCO2).
First investments must be CO2 infrastructure. Direct air capture plants will be built last
After determining which mix of interventions would be cost-optimal endpoint for fully decarbonised cement industry, we used a back-casting approach to determine how to reach full decarbonisation in the most economically viable way (i.e., which investment is most economically viable to do first). The results show that first interventions at the cement plants themselves (i.e., mostly CCS and calcined clay) are implemented before direct air capture technologies are built (Fig. 10). For reaching 50% emission reduction in all regions only partial CO2 transport networks need to be built (but already sized to later accommodate the CO2 volumes at the endpoint). Plants farther away from plant agglomerations (e.g., those in Eastern Spain, East and Southeast Germany) are not connected to the pipeline network due to lack of synergies (e.g., connecting a single plant further away from the storage site increases costs, compared to connecting multiple ones close by). Reaching 50% emissions reduction comes with an added levelised cost of cement production of €46 tcement−1 (UK&IRE), €37 tcement−1 (GER) and €43 tcement−1 (PT&ES), accounting for 52% to 61% of the costs for full decarbonisation, again underlining the need for high upfront investments in times that ETS prices are at lower levels still. Reaching 75% emission reduction was achieved by connecting all plants to the CO2 transport and storage network and only partially implementing direct air capture accounting for added levelised cost of cement production of €40 tcement−1 to €50 tcement−1. Achieving 75% emission reduction only accounts for 56–68% of the total costs, compared to the 58–61% for 50% emission reduction, as most of the CO2 transport infrastructure at this point has already been constructed (and is already included in the levelised costs of the 50% emission reduction scenario). The last 25% to reach full decarbonisation is then entirely achieved by implementing direct air capture plants and establishing additional storage sites (i.e., CO2 injection wells). Note, direct air capture technologies were also added for lower emission targets, but mostly as the cheapest option to reach residual emission reductions to a set target (e.g., from 47 to 50%).
 |
| Fig. 10 Model results for reaching different decarbonisation goals (i.e., 50%, 75% and 100%) in (A) United Kingdom and Ireland, (B) Germany and (C) Portugal and Spain. Each circle represents one integrated cement plant or direct air capture location. Circle colours represent interventions. Line colours indicate CO2 transport pipe thickness. White circles are unabated cement plants further up the marginal cost curves. Total capital requirements (TCR) describe the capital expenditures (CAPEX) of an investment. | |
The obtained results are robust towards changes in feedstock and energy assumptions
As the outputs of ex ante modelling study, the results presented here contain significant uncertainties (i.e., all technologies assessed here have not yet reached maturity requiring the use of assumptions and future costs of feedstocks and energy cannot be known at this time). To verify the robustness of the generated results, we performed an uncertainty analysis in the form of a one-at-a-time sensitivity analysis which we showed earlier to be a sufficient method for a computational expensive model that does not allow global uncertainty analysis.80 We specified scenarios for feedstock prices with minimum and maximum estimates (i.e., prices for biofuel, prices for olivine-bearing rocks, prices for kaolinite clays as well as prices for energy, Table S5†). The results suggest that the model is robust to changes in assumptions, as mostly the same strategies are chosen as for the base case (Tables S27–S32†). When all interventions are included, CCS coupled with calcined clay cements is chosen for almost all cement plants. However, high kaolinite clay prices lead to a divergence from this strategy (such as changing to CCS alone, CCS with biofuel or CCS with CO2 mineralisation) (Tables S30 and S31†). Notably, when strategies are chosen using CCS or CO2 mineralisation in the base case, the model's outcomes become much more sensitive to energy prices, as these measures use considerable amounts of electricity and heat to compress CO2, facilitate reactions or separate products36,81,82(Fig. 11). For calcined clay interventions, which use less energy than conventional cement, high energy costs therefore have a smaller and sometimes even negative impact (Table S13† and Fig. 11).
 |
| Fig. 11 Results of one-at-a-time sensitivity analysis. Each point represents the change of one cement plant in (A) United Kingdom and Ireland, (B) Germany and (C) Portugal and Spain allowing all interventions (w/calcined clay) and allowing all interventions except the ones containing calcined clay (w/o calcined clay). Ranges for parameters shown in Table S5.† Note, due to the nature of the mixed integer linear programming model and finding quasi-optimal solutions, the runs can never fully be repeated, leading to small variations as “noise” in the sensitivity analysis. | |
Discussions
The here presented analysis of decarbonising the cement industry across three European case study regions (i.e., UK&IRE, GER, and PT&ES) showed multiple strategies toward achieving net-zero CO2e emissions. The results highlighted the essential role of CCS and DACCS technologies alongside novel cement replacements such as calcined clay cements as the most cost-effective strategies. However, we here want to also highlight the complexities in ex ante modelling with significant uncertainties due to simplifications and unknowns and put the major findings in context.
CO2 transport infrastructure planning
The results show that elaborate CO2 transport networks as well as their swift implementation will be necessary to reach full decarbonisation in an economically viable way. The absence of such infrastructure could significantly increase the costs of achieving decarbonisation, emphasising the necessity for coordinated efforts and investments in transport networks shared among industries, regions and countries, which will require further efforts from industry and policy (e.g., adapting legislation for transnational CO2 transport such as the ratification of the London Protocol83). Arguably the CO2 networks described here are unlikely to be realised in the presented form as many simplifications had to be made in the model (e.g., only cement plants are included as CO2 emitters, CO2 pipelines only connect two grid cells following a straight line between cement plants, terminals etcetera, no exclusion zones are implemented). But the results show that collaborative planning for CO2 transport networks with other cement plants and other industries intending to adopt CCS is imperative.
While others have modelled CO2 transport networks for European industries in varying resolutions,84–87 commonly based on emission datasets assuming a certain share of CO2 capture at each plant level,87 we here considered the cement industry as a whole while including a range of different interventions (i.e., biofuels, calcined clay cements) alongside CCS alone. This approach should be used in further research to model the interaction between decarbonisation strategies of multiple industries (e.g., including the steel industry with their options for decarbonisation).
We showed that the pathway, in particular timing of the implementation of an intervention, towards decarbonisation will depend on the location. This could give some companies a competitive advantage over others. E.g., a company owning multiple cement plants could leverage CO2 certificates among their plants (which is allowed in the EU ETS77), while other companies only owning few plants, will have to wait, e.g., until CO2 infrastructure is in place while being exposed to fluctuations in CO2 certificate prices. This might require actions from legislature or collaboration between competing companies to level market opportunities.
Additionally, our results highlight the importance of the selection of CO2 storage sites. Notably, all existing studies modelling CO2 transport and storage networks in Europe use different assumptions for determining suitable CO2 storage sites,84–87 while some include onshore storage and others do not. We excluded onshore CO2 storage due to higher risk perceptions by laypeople46 and used data from European Comission – Joint Research Centre27 to determine CO2 storage sites which were published a decade ago and to this day provides the most comprehensive survey of potential storage sites within Europe, but still required a significant amount of assumptions to be made (especially for Germany where storage locations and sizes were not fully investigated) (Note S6†). This highlights that suitable storage sites both from a technological as well as societal perspective must be determined to allow modellers, industry and policy makers to plan reliable strategies towards net-zero CO2e emissions. This is of particular importance for some countries such as Germany were the law must first be changed to allow CO2 storage,88 while in other countries the debate on CO2 storage is only beginning to develop now.
Calcined clay cements
Our results underscore the potential of calcined clay cements in substantially reducing decarbonisation costs. These cements, due to their low heat requirements when coupled with traditional cement production with CCS, present a promising avenue, albeit contingent on market acceptance and availability of local resources. Despite the great economic potential of calcined clay cements shown in this study, current prices for kaolinite clays are significantly above the prices necessary to be economically viable (i.e., in 2022 in the United States the average price for kaolinite clays sold was $160 tclay−1 (€150 tclay−1),89 while we here assume a price of €30 tclay−1 in the base case scenario (Table S5†)). Current markets for kaolinite clays include manufacturing ceramics, porcelain ware and floor or wall tiles due to its whitening properties90 leading to a high cost and small volume markets (e.g., in 2021 in Germany 864ktclay and in the United Kingdom 735 ktclay were produced91 while 35 Mtcement and 9 Mtcement were produced respectively92). But clays for the cement industry might not have to exhibit these whitening properties and could be of lower grades. Nevertheless, clay reserves for lower grade clays in Europe outside of existing quarries may be less accessible,20 where further investigations are needed (i.e., for locations, capacities, extraction costs, clay compositions). Beyond the sourcing of raw materials, further research for the product applications is needed. The use of calcined clay in cement mixtures might lead to challenges due to high surface area alongside high water demands as well as colour control20 which will have to be fully addressed before widespread market implementation, all the more reason to start investigating them now.
CO2 mineralisation and biofuels
The absence of calcined clay cements (e.g., due to lack of market adoption or lack of affordable feedstocks) could necessitate alternative strategies, such as CO2 mineralisation or biofuels, particularly influenced by local resource availability and transportation costs, highlighting that flexibility in technological choices might become key in the regional context.
For CO2 mineralisation, our results show that these strategies were chosen contingent to a plant's access to cheap transport or proximity to feedstock deposits. We solely considered olivine-bearing rocks as feedstocks used in a direct aqueous carbonation process, which we further developed to produce SCM for use in cement blends36 (Note S3†). While we chose this process due to its lowest levelised costs of production compared to other processes36 and the feedstock due to the large availability, there might be other processes and feedstocks to be considered. E.g., serpentine-bearing rocks which might be available e.g., in northern Europe as well as south England and south Spain,26,41 albeit with higher energetic penalties for the carbonation reaction due to necessary heat activation.33 Our results indicate that the main disadvantage of the considered CO2 mineralisation process is in addition to limitations of feedstock transport, its comparably high energy demands (the process requires grinding to particle sizes under 10 μm, increased pressure of 100 bar and 190 °C to facilitate mineralisation).36,93 Hence, other feedstocks like calcium oxide-rich industrial wastes (e.g., steel slag, red mud, concrete and demolition waste) might be feasible as they could carbonate with lower energy penalties (i.e., at lower temperatures, quicker residence times). But these calcium oxide-rich feedstocks are limited both by geographic availability of other industries (i.e., steel plants41) and volume (e.g., Germany produces 5.4 Mtsteel slag a−1
94 while producing 35 Mtcement a−1
92). Thus, further geospatial studies will be necessary beyond the question of feedstocks for CO2 mineralisation. The results show that CO2 utilisation concepts could become a part of decarbonisation for some locations, particularly in combination with CCS. When CO2 mineralisation concepts were chosen, it was due to their potential to permanently store CO2. Other CO2 utilisation options (e.g., production of fuels), would not have been chosen by the solver as costly direct air capture plants would have to be built to capture CO2 emissions created from the combustion at the end of their life cycles.
Similarly to CO2 mineralisation, biofuels were predominately selected for plants with access to cheap ship transport (i.e., Northern Germany) (Fig. 7). Although combining CCS with biofuels showed the highest emission reductions of all combinations through creating carbon dioxide removal from embodied biogenic CO2 (excluding transport 55 kgCO2e tcement−1 to 77 kgCO2e tcement−1, Fig. S8†), transport emissions (up to 327 kgCO2e tbiofuel−1 for south Germany, Table 2) and costs diminished the potential of using biofuels in many locations. Because none of the case study regions produces biofuels (i.e., wood pellets) in sufficient amounts for the energy demands of its cement industry (e.g., Germany, the Europe 3rd biggest producer of hardwood pellets could only satisfy 34% of its cement industries energy demand with hardwood pellets, Table S1†) we here only considered biofuels from North America, which has been suggested as a future potential source for biofuels in Europe.95 Even including significant transport emissions from North America some plants (in particular in the United Kingdom and Portugal & Spain) still chose biofuels as a strategy. This indicates that in some regions with high biofuel production (e.g., black forest in south Germany) the use of biofuels could become more attractive than shown here, contingent on low production costs to which the use of biofuel showed high sensitivity (Fig. 11). This should be addressed by future research. As biofuel production is limited in most countries (Table S1†) and might compete with other uses (e.g., material use or food resources), many countries might define strategies for biofuel use in their sustainability roadmaps. For example, the German government has already announced that their national biomass strategy (yet to be published) will likely prioritise material use for biomass over energy use96 and hence might limit the use of biofuels in the cement industry.
Direct air capture and carbon dioxide removal
Our results highlight the impact of direct air capture (as a model carbon dioxide removal technology) in deep decarbonisation strategies for the cement industry. We showed that if cement plants do not use biofuels, a significant share of their costs for deep decarbonisation will instead go to direct air capture and storage. While we showed that these strategies will be implemented last, due to their comparatively high costs (Fig. 10), in current industry roadmaps they play a minor role.5,10
Investment costs and first-of-a kind plants
While the cumulative investments calculated in our model appear substantial, the projected costs must be contextualised against potential future expenses incurred through greenhouse gas emission certificates. We acknowledge that all interventions have been considered with expected costs at technology maturity (Nth-of-a-kind) and first-of-a-kind plant costs will thus first have to be overcome, which will necessitate support from governments or environmentally conscious customers (e.g., green construction companies) as the ETS certificate market is not designed to reward companies carrying additional costs for first-of-a-kind investments.97 The here presented costs reflect estimated long-term costs and thus are lower than recently presented studies5 which estimate the cost based on current developments rather than at technology maturity.
Limitations
Inherently, the here developed model has limitations due to its ex ante nature (i.e., accessing technologies which are not fully developed yet) as well as simplifications necessary to overcome computational limitations. First, we only considered one type of cement (ordinary Portland cement with simplified clinker factor of 1), while a multitude of different cement types are currently produced,98 meaning this study neglected the use of clinker replacement in different cement types. But because all cement types contain ordinary Portland cement, most of the here derived conclusions are likely to hold true for other cement blends too. Similarly, we needed to limit the number of interventions studied due to computational constraints, while including interventions of different types (Fig. 1). While we acknowledge that other interventions may play an important role in decarbonisation for some cement plants or niche applications (such as alkali activated systems,8 magnesia cements,8 or CO2 concrete curing in precast concrete production20), many of the learnings from this paper are transferable, as these concepts either aim to reduce the clinker content, store CO2 in cementitious products or capture CO2 from the atmosphere.
A further limitation of the here shown results lies in the availability of feedstocks. We did not consider capacities of potential feedstock sites for mineralisation, biofuels, or clays. While estimations suggest that potential capacities might be sufficient for widespread implementation of these concepts24,33,41 detailed supply–demand matching would have to be done. Additionally, especially in the case of biofuels we did not consider environmental changes due to its harvest. The harvest of wood for wood pellet production can have significant impacts on the forest carbon and the environmental impact of biomass production is influenced by the tree's age when it is harvested, with break-even periods (until forest carbon is replaced) ranging up to multiple decades.99,100 Thus, further research should be conducted to investigate which wood sources might be suitable for biofuel production in the cement industry and detailed life cycle assessments should be conducted.
A major challenge currently lies in the uncertainty of the decarbonisation strategies of other industries. Integrated assessment modelling should be conducted including other energy-intensive industries in particular as they also might use similar feedstocks for their decarbonisation strategies and consequently impact regional demand and costs (e.g., other energy intensive industries might also consider biofuels).
Conclusions
For the first time, we presented a quantitative, spatially explicit analysis of cost-optimal strategies to transition the European cement industry towards net-zero CO2e emissions, focusing on three regions in Europe. Our results demonstrated the feasibility and economic viability of achieving net-zero emissions through strategic interventions and technological advancements (i.e., iterative learning), underpinning the notion that full decarbonisation of cement production is possible and economically sensible. However, our analysis underlined that these efforts require significant (upfront) investments that may need incentivising beyond CO2 credits or taxes, collaboration, and rational sequencing of interventions. The main conclusions for policy and decision makers can be summarised as follows.
Conclusions for policy and decision makers
• Prioritise investments in carbon capture, transport, and storage technologies as they play a vital role in the industry's decarbonisation strategy. Especially CO2 storage sites should be selected in conjunction with CO2 transport infrastructure and should be developed swiftly.
• Collaboration and coordination between cement producers and with other industries to plan and implement CO2 transport networks is essential for efficient and cost-effective decarbonisation. Moving alone will lead to substantially increased total costs of decarbonisation (added costs of up to €19 billion annually could be expected for the European Union and United Kingdom combined).
• Cement producers and governments must expedite the research into, and use of, calcined clay cements as a sustainable alternative, investigating local resource availability and market acceptance. Falling to include calcined clays may increase costs for deep decarbonisation by 12–21% or €9 to €15 tcement−1.
• Small cement producers or individual plant owners must explore options for synergies with other plants in their vicinity and develop strategies for emission reduction short to medium term (e.g., through use of biofuels, alternative clinkers) until CO2 transport infrastructure is built.
• Adapt decarbonisation strategies based on regional resources, transportation costs, and infrastructure availability (i.e., implementing CO2 mineralisation when CO2 transport infrastructure is yet to be built).
• Facilitate initial investments in new technologies through subsidies, incentives, or joint investments as high costs for first-of-a-kind technologies must be overcome for favourable economics of deep decarbonisation.
• Develop location-dependent decarbonisation strategies, which should only include technologies that can still be used when full decarbonisation is reached to avoid malinvestments (especially important for CO2 utilisation technologies without long-term CO2 storage).
• Include carbon dioxide removal strategies (using DACCS or biofuel CCS) into decarbonisation strategies for the cement industry. It is virtually impossible to reach net-zero CO2e cement production without this.
In summary, achieving net-zero CO2e emissions in the cement industry is complex but feasible. It requires a multi-faceted approach involving technological innovation, strategic planning, and collaborative efforts across cement producers and other industries. The long-term economic benefits make a compelling case for industry and policy makers to commit to a swift transition in this sector.
Data availability
Code generated during this study has been published as Strunge101 and can be accessed under: https://doi.org/10.5281/zenodo.13737709. The release also contains datasets of the all the results produced.
Author contributions
TS: conceptualisation, methodology, formal analysis, and writing—original draft. LK: methodology. NS: methodology of INDiECAR-RTN. NSh: conceptualisation and writing—review. PR: conceptualisation and writing—review. MV: conceptualisation, methodology, and writing—review.
Conflicts of interest
The authors declare that the research was conducted in the absence of any commercial or financial relationships that could be construed as a potential conflict of interest.
Acknowledgements
TS received a scholarship at Heriot-Watt University. PR, MV and NSh are funded through the UK's Industrial Decarbonisation Research and Innovation Centre (EP/V027050/1). NSh was also funded by the IDLES programme grant (EP/R045518/1). We want to thank the IDRIC project 12 partners at Imperial College London for their support and fruitful discussions.
References
-
M. Allen, O. Dube, W. Solecki, F. Aragón-Durand, W. Cramer, S. Humphreys and M. Kainuma, Special Report: Global warming of 1.5 °C, Intergovernmental Panel on Climate Change (IPCC), 2018 Search PubMed.
-
IEA, Cement, Paris, 2020 Search PubMed.
- C. Le Quéré, R. M. Andrew, P. Friedlingstein, S. Sitch, J. Hauck, J. Pongratz, P. A. Pickers, J. I. Korsbakken, G. P. Peters and J. G. Canadell, Earth Syst. Sci. Data, 2018, 10, 2141–2194 CrossRef.
-
Expert Market Research, Global Cement Market to Reach 6.08 Billion Tons by 2026, https://www.expertmarketresearch.com/pressrelease/global-cement-market#:%7E:text=Accordingtoanewreport,6.08BillionTonsby2026, accessed 22.03.2021, 2021.
- M. Schneider, V. Hoenig, J. Ruppert and J. Rickert, Cem. Concr. Res., 2023, 173, 107290 CrossRef CAS.
-
T. Czigler, S. Reiter, P. Schulze and K. Somers, Laying the Foundation for Zero-Carbon Cement, McKinsey & Company, 2020 Search PubMed.
- R. M. Andrew, Earth Syst. Sci. Data, 2018, 10, 195 CrossRef.
-
A. Favier, C. De Wolf, K. Scrivener and G. Habert, A Sustainable Future for the European Cement and Concrete Industry: Technology Assessment for Full Decarbonisation of the Industry by 2050, ETH Zurich, 2018 Search PubMed.
-
C. Bataille, Low and zero emissions in the steel and cement industries: Barriers, technologies and policies, 2020, DOI:10.1787/5ccf8e33-en.
-
The European Cement Association, Cementing the European Green Deal, The European Cement Association, Brussels, 2020 Search PubMed.
-
S. P. Deolalkar, in Designing Green Cement Plants, ed. S. P. Deolalkar, Butterworth-Heinemann, 2016, pp. 83–86, DOI:10.1016/B978-0-12-803420-0.00011-1.
- B. Lothenbach, K. Scrivener and R. Hooton, Cem. Concr. Res., 2011, 41, 1244–1256 CrossRef CAS.
-
L.-A. Tokheim, A. Mathisen, L. E. Øi, C. K. Jayarathna, N. H. Eldrup and T. Gautestad, Combined calcination and CO2 capture in cement clinker production by use of electrical energy, TCCS–10. CO2 Capture, Transport and Storage. Trondheim 17th–19th June 2019. Selected Papers from the 10th International Trondheim CCS Conference, 2019 Search PubMed.
- V. W. Y. Tam, M. Soomro and A. C. J. Evangelista, Constr. Build. Mater., 2018, 172, 272–292 CrossRef CAS.
-
E. Bellmann and P. Zimmermann, Climate Protection in the Concrete and Cement Industry – Background and Possible Courses of Action, Berlin, 2019 Search PubMed.
-
K. Koring, V. Hoenig, H. Hoppe, J. Horsh, C. Suchak, V. Llevenz and B. Emberger, IEA Report 2013, 2013, p. 19 Search PubMed.
-
R. K. Pachauri, M. R. Allen, V. R. Barros, J. Broome, W. Cramer, R. Christ, J. A. Church, L. Clarke, Q. Dahe and P. Dasgupta, Climate Change 2014: Synthesis Report. Contribution of Working Groups I, II and III to the Fifth Assessment Report of the Intergovernmental Panel on Climate Change, IPCC, 2014 Search PubMed.
-
IEA, Cement Technology Roadmap 2009–Carbon Emissions Reductions up to 2050, Paris, France, 2009, pp. 1–2 Search PubMed.
- E. Gartner and T. Sui, Cem. Concr. Res., 2018, 114, 27–39 CrossRef CAS.
- K. L. Scrivener, V. M. John and E. M. Gartner, Cem. Concr. Res., 2018, 114, 2–26 CrossRef CAS.
-
M. Wörtler, F. Schuler, N. Voigt, T. Schmidt, P. Dahlmann, H. B. Lüngen and J.-T. Ghenda, Steel’s Contribution to a Low-carbon Europe 2050: Technical and Economic Analysis of the Sector’s CO2 Abatement Potential, BCG, London, Retrieved April, 2013, vol. 20 Search PubMed.
- N. Tkachenko, K. Tang, M. McCarten, S. Reece, D. Kampmann, C. Hickey, M. Bayaraa, P. Foster, C. Layman, C. Rossi, K. Scott, D. Yoken, C. Christiaen and B. Caldecott, Sci. Data, 2023, 10, 696 CrossRef.
- D. Kremer, S. Etzold, J. Boldt, P. Blaum, K. M. Hahn, H. Wotruba and R. Telle, Minerals, 2019, 9, 485 CrossRef CAS.
- H. G. Dill, Ore Geol. Rev., 2020, 119, 103304 CrossRef.
- E. Galán, P. Aparicio, J. C. Fernández-Caliani, A. Miras, M. G. Márquez, A. E. Fallick and N. Clauer, Appl. Clay Sci., 2016, 131, 14–26 CrossRef.
-
British Geological Survey, 2022 Search PubMed.
-
European Comission – Joint Research Centre, European CO2 Storage Database (CO2Stop), 2013 Search PubMed.
- F. Neele, C. Hofstee, R. Arts, V. Vandeweijer, M. Nepveu, J. ten Veen and F. Wilschut, Energy Procedia, 2013, 37, 5220–5229 CrossRef CAS.
-
N. Miller and M. Osborne, Competition Among Spatially Differentiated Firms: An Empirical Model with an Application to Cement, Available at SSRN 1600746, 2010.
- A. A. Shubbar, M. Sadique, P. Kot and W. Atherton, Constr. Build. Mater., 2019, 210, 172–187 CrossRef CAS.
- S. Sánchez Berriel, A. Favier, E. Rosa Domínguez, I. R. Sánchez Machado, U. Heierli, K. Scrivener, F. Martirena Hernández and G. Habert, J. Cleaner Prod., 2016, 124, 361–369 CrossRef.
- R. Jaskulski, D. Jóźwiak-Niedźwiedzka and Y. Yakymechko, Materials, 2020, 13, 4734 CrossRef CAS PubMed.
- A. Sanna, M. Uibu, G. Caramanna, R. Kuusik and M. M. Maroto-Valer, Chem. Soc. Rev., 2014, 43, 8049–8080 RSC.
-
B. Metz, O. Davidson, H. De Coninck, M. Loos and L. Meyer, IPCC Special Report on Carbon Dioxide Capture and Storage, Cambridge University Press, Cambridge, 2005 Search PubMed.
-
M. Voldsund, R. Anantharaman, D. Berstad, C. Fu, S. Gardarsdottir, A. Jamali, J. Perez-Caivo, M. Romano, S. Roussanaly and J. Ruppert, H2020 Project: CO2 Capture from Cement Production, 2018 Search PubMed.
- T. Strunge, P. Renforth and M. Van der Spek, Commun. Earth Environ., 2022, 59, DOI:10.1038/s43247-022-00390-0.
-
M. Setterfield, in Routledge Handbook of Macroeconomic Methodology, Routledge, 2023, pp. 100–107 Search PubMed.
-
C. Fetting, ESDN Report, 2020, vol. 53 Search PubMed.
- J. Young, N. McQueen, C. Charalambous, S. Foteinis, O. Hawrot, M. Ojeda, H. Pilorgé, J. Andresen, P. Psarras, P. Renforth, S. Garcia and M. Van der Spek, One Earth, 2022, 6(7), 899–917 CrossRef.
- Y. Cancio Díaz, S. Sánchez Berriel, U. Heierli, A. R. Favier, I. R. Sánchez Machado, K. L. Scrivener, J. F. Martirena Hernández and G. Habert, Dev. Eng., 2017, 2, 82–91 CrossRef.
- H. Ostovari, L. Müller, F. Mayer and A. Bardow, J. Cleaner Prod., 2022, 360, 131750 CrossRef CAS.
- H. Ostovari, L. Müller, J. Skocek and A. Bardow, Environ. Sci. Technol., 2021, 55, 5212–5223 CrossRef CAS PubMed.
- R. T. Kusuma, R. B. Hiremath, P. Rajesh, B. Kumar and S. Renukappa, Renewable Sustainable Energy Rev., 2022, 163, 112503 CrossRef CAS.
-
J. Rowland, Cement Products, 2023 Search PubMed.
- S. C. Taylor-Lange, E. L. Lamon, K. A. Riding and M. C. G. Juenger, Appl. Clay Sci., 2015, 108, 84–93 CrossRef CAS.
- C. Merk, Å. D. Nordø, G. Andersen, O. M. Lægreid and E. Tvinnereim, Energy Res. Soc. Sci., 2022, 87, 102450 CrossRef.
-
A. Bergman and A. Rinberg, CDR Primer, 2021 Search PubMed.
- J. Fuhrman, H. McJeon, P. Patel, S. C. Doney, W. M. Shobe and A. F. Clarens, Nat. Clim. Change, 2020, 10, 920–927 CrossRef CAS.
- G. Faber, A. Ruttinger, T. Strunge, T. Langhorst, A. Zimmermann, M. van der Hulst, F. Bensebaa, S. Moni and L. Tao, Front. Clim., 2022, 4, 820261 CrossRef.
-
E. S. Rubin, N. Berghout, G. Booras, T. Fout, M. Garcia, M. S. Nazir, A. Ramirez, S. Roussanaly and M. van der Spek, in Towards Improved Guidelines for Cost Evaluation of Carbon Capture and Storage, ed. S. Roussanaly, E. S. Rubin and M. Van der Spek, 2021 Search PubMed.
- E. S. Rubin, Int. J. Greenhouse Gas Control, 2019, 88, 1–9 CrossRef.
-
C. Greig, A. Garnett, J. Oesch and S. Smart, Guidelines for Scoping and Estimating Early Mover CCS Projects, Univ. Queensl., Brisbane, 2014 Search PubMed.
- E. S. Rubin, I. M. Azevedo, P. Jaramillo and S. Yeh, Energy Policy, 2015, 86, 198–218 CrossRef.
- J. Young, N. McQueen, C. Charalambous, S. Foteinis, O. Hawrot, M. Ojeda, H. Pilorgé, J. Andresen, P. Psarras and P. Renforth, One Earth, 2023, 6, 899–917 CrossRef.
- S. Knopf and F. May, Energy Procedia, 2017, 114, 4710–4721 CrossRef CAS.
- R. Andreani, G. Haeser and J. M. Martínez, Optimization, 2011, 60, 627–641 CrossRef.
- J. Collis and R. Schomäcker, Front. Energy Res., 2022, 10, 909298 CrossRef.
-
F. Benita, G. Bansal, G. Piliouras and B. Tunçer, arXiv, 2019, preprint, arXiv:1902.08028, DOI:10.48550/arXiv.1902.08028.
-
Mapcruzin, OpenStreetMaps Shapefile European Railways, https://mapcruzin.com/free-europe-arcgis-maps-shapefiles.htm, 2022.
-
B. Halpern, M. Frazier, J. Potapenko, K. Casey, K. Koenig, C. Longo, J. Lowndes, C. Rockwood, E. Selig and K. Selkoe, Knowledge Network for Biocomplexity. 2015, vol. 10, p. F1S180F Search PubMed.
-
A. Novikov, Big Data and Environmental Impact of the Maritime Transportation, Towards Data Sci., 2019 Search PubMed.
-
Openstreetmap, Accuracy, https://wiki.openstreetmap.org/wiki/Accuracy#Naming_accuracy, accessed 10.07.2024, 2024.
-
A. Zimmermann, L. Müller, Y. Wang, T. Langhorst, J. Wunderlich, A. Marxen, K. Armstrong, G. Buchner, A. Kätelhön, M. Bachmann, A. Sternberg, S. Michailos, S. McCord, A. V. Zaragoza, H. Naims, L. Cremonese, T. Strunge, G. Faber, C. Mangin, B. Olfe-Kräutlein, P. Styring, R. Schomäcker, A. Bardow and V. Sick, Techno-Economic Assessment & Life Cycle Assessment Guidelines for CO2 Utilization (Version 1.1), 2020 Search PubMed.
-
IEAGHG, Towards Improved Guidelines for Cost Evaluation of Carbon Capture and Storage 2021-TR05, 2021 Search PubMed.
-
R. Smith, Chemical Process: Design and Integration, John Wiley & Sons, 2005 Search PubMed.
- E. S. Rubin, C. Short, G. Booras, J. Davison, C. Ekstrom, M. Matuszewski and S. McCoy, Int. J. Greenhouse Gas Control, 2013, 17, 488–503 CrossRef CAS.
- H. Ostovari, A. Sternberg and A. Bardow, Sustainable Energy Fuels, 2020, 4482, 10.1039/D0SE00190B.
-
European Commission, Joint Research Centre, Institute for Environment and Sustainability, ILCD Handbook, 2010 Search PubMed.
- N. Sunny, N. Mac Dowell and N. Shah, Energy Environ. Sci., 2020, 13, 4204–4224 RSC.
-
C. Pantelides, Proceedings on the Second Conference on Foundations of Computer Aided Operations, 1994, pp. 253–274 Search PubMed.
-
L. Küng, T. Strunge, N. Sunny, Z. Nie, N. Tariq, A. Korre, N. Shah and M. Van der Spek, An Open-Source Toolkit to Design and Evaluate Net-Zero Pathways for Industrial Clusters, Available at SSRN 4286330, 2022, DOI:10.2139/ssrn.4286330.
-
Eurostat, Annual Production Value of the Construction Industry in Selected European Countries 2020 (In Billion Euros), Statista, Statista, 2023 Search PubMed.
-
Office for National Statistics (ONS), ONS website, article, Construction statistics, Great Britain: 2022, 2023.
-
Eurostat, Gross domestic product of the European Union from 2011 to 2022 (in million euros at current market prices), https://www.statista.com/statistics/279447/gross-domestic-product-gdp-in-the-european-union-eu/, accessed December 15 2023, 2023.
-
Office for National Statistics (UK), Gross domestic product of the United Kingdom from 1948 to 2022 (in million GBP), https://www.statista.com/statistics/281744/gdp-of-the-united-kingdom/, accessed December 15 2023, 2023.
-
R. Anantharaman, D. Berstad, G. Cinti, E. De Lena, M. Gatti, H. Hoppe, I. Martinez, J. G. M.-S. Monterio, M. Romano, S. Roussanaly, E. Schols, M. Spinelli, S. O. Størset, P. van Os and M. Voldsund, CEMCAP Framework for Comparative Techno-Economic Analysis of CO2 Capture from Cement Plants-D3.2, Zenodo, 2018 Search PubMed.
-
European Comission, What is EU ETS?, https://climate.ec.europa.eu/eu-action/eu-emissions-trading-system-eu-ets/what-eu-ets, accessed 28.12.2023, 2023.
-
M. Pahle, J. Sitarz, S. Osorio and B. Görlach, Kopernikus-Projekt Ariadne Potsdam-Institut für Klimafolgenforschung (PIK) Telegrafenberg A, 2022, vol. 31, p. 14473 Search PubMed.
- K. Rennert, F. Errickson, B. C. Prest, L. Rennels, R. G. Newell, W. Pizer, C. Kingdon, J. Wingenroth, R. Cooke, B. Parthum, D. Smith, K. Cromar, D. Diaz, F. C. Moore, U. K. Müller, R. J. Plevin, A. E. Raftery, H. Ševčíková, H. Sheets, J. H. Stock, T. Tan, M. Watson, T. E. Wong and D. Anthoff, Nature, 2022, 610, 687–692 CrossRef CAS PubMed.
- T. Strunge, P. Renforth and M. Van der Spek, Front. Energy Res., 2023, 11 DOI:10.3389/fenrg.2023.1182969.
- D. Kremer, T. Strunge, J. Skocek, S. Schabel, M. Kostka, C. Hopmann and H. Wotruba, J. CO2 Util., 2022, 62, 102067 CrossRef CAS.
- A. M. Bremen, T. Strunge, H. Ostovari, H. Spütz, A. Mhamdi, P. Renforth, M. van der Spek, A. Bardow and A. Mitsos, Ind. Eng. Chem. Res., 2022, 13177, DOI:10.1021/acs.iecr.2c00984.
-
T. Dixon and A. Birchenough, Exporting CO2 for offshore storage – The London Protocol’s export amendment, in Proceedings of the 15th Greenhouse Gas Control Technologies Conference, 2021, pp. 15–18 Search PubMed.
- F. d'Amore, N. Sunny, D. Iruretagoyena, F. Bezzo and N. Shah, Comput. Chem. Eng., 2019, 129, 106521 CrossRef.
- J. Morbee, J. Serpa and E. Tzimas, Int. J. Greenhouse Gas Control, 2012, 7, 48–61 CrossRef.
- F. d’Amore and F. Bezzo, Front. Energy Res., 2020, 8 DOI:10.3389/fenrg.2020.00190.
- F. d'Amore, M. C. Romano and F. Bezzo, IFAC-PapersOnLine, 2021, 54, 609–614 CrossRef.
- R. Weber, Zeitschrift für Europäisches Umwelt- und Planungsrecht, 2023, 20(4), 422–427 Search PubMed.
-
US Geological Survey, Average Price of Kaolin in the U.S. From 2010 to 2022 (In U.S. Dollars Per Ton), Statista, 2023 Search PubMed.
-
Active Minerals, Properties and applications of kaolin, https://activeminerals.com/blog/kaolin-guide/, accessed 09.01.2024, 2024.
-
British Geological Survey, Production of Kaolin in Europe in 2021, by Country (In Metric Tons), 2023 Search PubMed.
-
British Geological Survey, Production Volume of Cement in Europe in 2021, by Country(in Metric Tons), 2023 Search PubMed.
- E. Eikeland, A. B. Blichfeld, C. Tyrsted, A. Jensen and B. B. Iversen, ACS Appl. Mater. Interfaces, 2015, 7, 5258–5264 CrossRef CAS PubMed.
-
T. Merkel, Institut für Baustoff-Forschung FehS: Duisburg, Germany, 2017 Search PubMed.
-
D. Thrän, D. Peetz, K. Schaubach, S. Backéus, L. Benedetti and L. Bruce, Global Wood Pellet Industry and Trade Study 2017, IEA Bioenergy Task 40, 2017 Search PubMed.
-
Federal Ministry for Economics and Climate Action, BMWK, 2022 Search PubMed.
- A. Patt and J. Lilliestam, Joule, 2018, 2, 2494–2498 CrossRef.
-
European Standard, EN 197-1:2000: Cement. Composition, Specifications and Conformity Criteria for Common Cements, British Standards Institute, 2000 Search PubMed.
- M. Ter-Mikaelian, J. McKechnie, S. Colombo, J. Chen and H. MacLean, For. Chron., 2011, 87, 644–652 CrossRef.
- J. McKechnie, S. Colombo, J. Chen, W. Mabee and H. L. MacLean, Environ. Sci. Technol., 2011, 45, 789–795 CrossRef CAS PubMed.
-
T. Strunge, INDiECAR Model, v1.0.1, DOI:10.5281/zenodo.13737709.
|
This journal is © The Royal Society of Chemistry 2024 |
Click here to see how this site uses Cookies. View our privacy policy here.