DOI:
10.1039/D3SU90060F
(Editorial)
RSC Sustainability, 2024,
2, 261-264
Introduction to sustainable composites
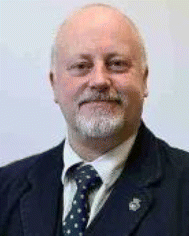 Ian Hamerton | Ian Hamerton has been the NCC Professor of Polymers and Sustainable Composites in the Bristol Composites Institute (BCI) since 2021, a joint appointment between the University of Bristol and the National Composites Centre, Bristol, UK. He is the Deputy Director/Research Coordinator of the two EPSRC Centres for Doctoral Training (ACCIS, (EP/L016028/1) and Composites Science, Engineering and Manufacturing (EP/S021728/1) within the BCI. He completed his PhD in high performance polymers (University of Surrey, 1987-1990) with support from the US Navy and the Ministry of Defence (under the supervision of Prof. Mike Abraham, John B. Rose, John M. Barton, and John R Jones), before undertaking postdoctoral research in high temperature composites with the Defence Research Agency, Farnborough (formerly the Royal Aircraft Establishment) with Profs. John M. Barton, Bill Wright, and Mike Bader before joining the academic staff of the Department of Chemistry (University of Surrey). Ian was invited to serve on the Top UK Younger Chemists’ Group (1992-1999) at request of Professor Sir William Stewart, then Chief Scientific Officer/Head of the Office of Science & Technology and his successor, Sir Robert May. Ian has been an Editorial Board member for Polymer International (John Wiley) since 1996 and an EPSRC Peer Review College Member (Materials Chemistry) since 2007. During his career (first at Surrey then at the University of Bristol), he has been associated with research and research training income of £22.2M (£17.9M Since 2015) and has co-supervised 55 PhD and EngD doctoral students to completion (25 as primary supervisor). A co-author of the first report of a molecular simulation of a crosslinked polymer in 1996 (now an established field of research), his edited work, Chemistry and Technology of Cyanate Ester Resins, is the standard reference work for this family of materials (and still in print after 30 years), while his review of non-halogenated flame retardants, published in Progress in Polymer Science in 2002 has been cited on 1953 occasions. Ian has been actively developing nanocomposite materials for increasingly hostile and demanding environments throughout his career and in 2020 his team was selected to participate in the £3.5M Euro Materials Ageing 1 campaign (with composite samples being flown in an 18-month ESA mission on the International Space Station). As the PI on the High Performance Discontinuous Fibre Composites grant (EP/P027393/1, £1M), he was a founder member of Lineat Composites (formed to commercialise the HiPerDiF technology to manufacture composites more sustainably using reclaimed carbon fibres). |
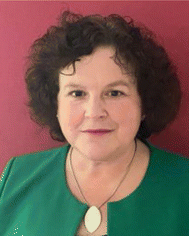 Lois Jane Hobson | Lois Hobson is a Senior Manager at the Centre for Process Innovation (CPI), a Research Technology Organisation and part of the UK High Value Manufacturing Catapult. Lois completed her PhD in organometallics (University of Wales, 1991–94) before undertaking postdoctoral positions with Professor Jim Feast (IRC in Polymer Science and Technology, Durham University, ROPA 1995–98) and Professor Shiro Kobayashi (JSPS Fellowship, Kyoto University, Japan, 1998–99) focussing on the synthesis and characterisation of hyperbranched polymer systems and artificial cellulosic structures, respectively. Continuing her interests in structure–property–performance relationships, she was the first female to hold the Toshiba Fellowship, joining Toshiba Japan’s fuel cell research group (Kawasaki, Japan) in 1999 and establishing patented technology for direct methanol systems. Joining the ICI Group in 2001, Lois worked with the National Starch & Chemical Company (Vinamul Polymers BV, 2001) and ICI Group companies (Ablestik Laboratories, Emerson & Cumming, ICI Paints, Quest International) in the UK, Europe, Asia and North America, in research, product development, programme management and techno-commercial roles, latterly establishing large-scale, cross-business collaborative programmes to create underpinning patented research, technology translation and future product innovation. In 2008, she moved to the UK public sector as Programme Manager for an £11M Local Enterprise Growth Initiative funded regeneration programme, before joining the Centre for Process Innovation (CPI) in 2009. Over the past 15 years, Lois has held various roles across the CPI business, focusing on enabling more effective translation of fundamental science and technology to market, including a 15 month secondment to PPX Medical as their European Operations Manager. She has established a portfolio of large collaborative programmes and supporting infrastructure on behalf of the CPI, accessing regional, national, and European programmes to build its translational capabilities. She led development of CPI's new Sustainable Materials Strategy and currently holds the title of Principal Strategic Programmes Manager. |
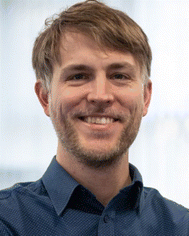 Jonathan Wagner | Jon Wagner is Reader in Circular Economy Engineering at Loughborough University. He is the Programme Lead for the Undergraduate Chemical Engineering Programme and Co-Director for the Interdisciplinary Centre for Circular Chemical Economy (CircularChem). He completed his PhD in 2016 on the hydrothermal liquefaction of microalgae under the supervision of Prof. Valeska Ting and Chris Chuck within the Centre for Sustainable Chemical Technologies at the University of Bath. Until his appointment at Loughborough, he joined the Horizon 2020 Photofuel project as a research associate at Imperial College London, focusing on algae system scale-up and system analysis. Before his PhD, he worked in industry, completing the BP upstream process engineering graduate scheme, with placements in Aberdeen (Schiehallion FPSO) and the CATS terminal in Teeside. Since 2012, Jon Wagner has secured more than £6m in research funding as PI or Co-I from the UKRI and Royal Society. He is co-founder of Loughborough’s Mini-CDT in low-dimensional catalysis. |
Introduction
Composites are a broad and versatile group of materials consisting of multiple components with desirable individual characteristics to yield enhanced, and often multifunctional, material properties. Fibre-reinforced polymer matrix composites combine excellent strength and low-weight with high thermal stability and corrosion resistance, leading to extended lifetime of components. They are already extensively used within high-performance sectors, ranging from aviation or automotive, to wind and marine. The glass fibre reinforced polyester market has been valued1 at £14.9bn in 2023, and the global carbon fibre epoxy composite market similarly valued2 at £22.1bn in 2020 and expected to grow at a compound annual growth rate of 8.3% from 2021 to 2028. Although the global market was severely affected due to the global SARS-CoV-2 (COVID-19) pandemic in 2020, rapid replacement of conventional materials in automotive and aerospace applications is expected to drive the market in the near future. With around 1500 British companies involved, the UK composite product market, which was estimated at £2.3bn in 2015, could grow to £12bn by 2030.3 Of perhaps even greater importance is the key and enabling role that composites may play in driving the transition to Net Zero, with key applications in the wind and hydrogen sectors, and lightweighting transport.
Despite this, the composites industry still largely follows a historical linear ‘take–make–dispose’ model, with 95% of fibre-reinforced composites currently made from virgin fossil feedstocks. Although composite design has moved beyond their use as ‘black metal’, to date it has mainly focused on maximising their material performance within a single lifetime with less consideration for their material recovery post use, or even a cascade of uses. A particular challenge is the effective removal and/or recovery of the polymer matrix without damaging the valuable composite fibres, to enable the reuse of one or both components in high-performance applications.
Most composites employ thermoset matrices, which display enhanced high-temperature properties compared to their thermoplastic alternatives but cannot be remoulded after use, rendering their use in a second life problematic. Current recycling approaches are mostly focused on the controlled thermal decomposition of the composite matrix, through pyrolysis, to enable recovery of the fibre, while the bulk of the material is lost through degradation of the matrix. There is increasing interest in the use of superheated steam, which has been used for this purpose of reclaiming fibres for around a decade. The technique was originally investigated to prevent or substantially reduce the degradation of reclaimed fibres, which occurs during the oxidative char removal step of most pyrolysis-based reclamation techniques. As yet, this is still comparatively developmental at commercial scales, but is clearly growing apace. Alternative mechanical recycling methods crush or grind the composites into fillers for lower performance applications, losing the inherent strength of the fibre component. As a result, only 15% of composites are currently sent for recycling, with just 6% reused, yielding increasing quantities of landfill as many first-generation composites start to reach the end of their useable life. While the production of second-life higher-performance composites manufactured from reclaimed components is still in its infancy (notable remanufacturing techniques including HiPerDiF/AFFT from the University of Bristol and TUFF from the University of Delaware), these rely for their success on the reclaimed discontinuous fibres retaining their strength and modulus following recovery and high degrees of alignment during the remanufacturing process.
In the context of significant pressures to reduce fossil-fuel use and increasing competition for resources, the composites industry needs to adapt to a more sustainable approach by improving composite lifetime and material recovery, and embracing a switch from fossil to renewable resources. To this end, the whole composite lifecycle needs to be considered at the design stage to minimise manufacturing losses and facilitate the repair, repurposing, and recycling of composites at the end of their working life. There is undoubtedly a role for life cycle assessment (LCA) in quantifying these impacts and the databases on which the various LCA software packages depend are becoming more accurate and representative all the time. Inevitable carbon losses throughout the composite value chain need to be compensated with renewable organic carbon, derived from biomass or direct CO2 reduction. Development of new materials should also build on the properties of these renewable feedstocks, rather than simply attempting to replicate existing fossil-based chemistries.
At the same time, as outlined in Meegan’s perspective on the sustainability challenges faced by the Composites Industry (https://doi.org/10.1039/D3SU00200D), development of a more circular composites industry should be considered within the context of the wider chemical industry to take advantage of existing supply chains and relationships, economies of scale, and increased flexibility to reuse/repurpose or recycle more materials. Therefore, the sustainable composites challenge is closely related to other ongoing initiatives focused on improving the resource efficiency of the chemical industry, including The Royal Society’s ‘Green carbon for the chemical industry of the future’ initiative, or the joint study by the UK Department for Energy Security and Net Zero (DESNZ) and the Department for Environment, Agriculture and Rural Affairs (Defra) on the potential benefits from increased resource efficiency across UK industry.4
The present collection showcases developments in a range of complementary approaches to address composite sustainability challenges.
• Although the existence of vitrimers/covalent adaptive networks (CANs) has been known for over a couple of decades, the existence of several commercial offerings has now stimulated the examination of their inclusion into blends to improve the self-healing and repair of composites (e.g., https://doi.org/10.1039/D3TA04351G, https://doi.org/10.1039/D2RA05103F).
• The chemical modification of the surfaces of reinforcing fibres is receiving significantly more attention to improve the matrix/fibre interface or the recyclability of composites, e.g. coating of aramid fibres (https://doi.org/10.1039/D3SU00258F).
• There are opportunities to improve the intrinsic properties of a composite, e.g. for super capacitive energy storage (https://doi.org/10.1039/D3TA02741D), or addition of functional groups to add flame-retardant properties and otherwise prevent the use of additives that would further complicate composite stability and polymer recycling (https://doi.org/10.1039/D2GC01405J).
• The need to deal with legacy materials is still a challenging task and superheated steam has already been mentioned. Other approaches to break down the thermoset matrix range from solvolysis to electrochemical methods (https://doi.org/10.1039/D3GC01765F).
• Renewable feedstocks for composite manufacture include cellulose, chitosan, and bio-based captodative ligands (https://doi.org/10.1039/D3SU00302G, https://doi.org/10.1039/D3GC03001F).
Whether targeting composite repair/rework, extending the ‘as-manufactured’ lifetime, or improving recovery and recyclability of component materials, the requirement for new materials solutions to align with current polymer processing techniques and embedded manufacturing routes cannot be ignored if exploitation is to be achieved in the short to medium-term. However, the fundamental question of incremental improvement versus the radical change driven by ‘demand-led innovation’ remains.
Whilst the challenge of bridging between materials capability and application requirements is not new, it is recognised that the concept of ‘sustainability’ has many dimensions. The European Chemical Council (CEFIC) has adopted the guiding principles of ‘Safe and Sustainable-by-Design’ as a mechanism to drive transformative change5 whilst recognising the need for “…enabling policy measures to ensure predictability of goals, within timelines that are ambitious yet realistic…”.
Recognising the value of this approach, the UK High Value Manufacturing (HVM) Catapult has recently launched its own cross-sector ‘Design for Sustainability and Circularity’ initiative6 to drive whole-system thinking, from raw material selection to product end-of-life fate.
Concluding remarks
The composites industry is well placed to meet the monumental and crucial challenge of the transition to Net Zero, with a high-performance product that can be integrated across a number of engineering sectors and may lead to reductions in fuel use and extensions in lifetime. However, as this collection makes clear, the change cannot be made using the same trajectory. The entire design and manufacturing chain must be reappraised holistically, approaching the development of new materials, manufacturing processes, and composites design and reuse from a fresh perspective, unfettered by historical reliance on fossil fuels. It is indeed an exciting time to be working in this vibrant and influential sector.
References
- Glass Fiber Reinforced Plastic (GFRP) Composites Market. Market Survey on Glass Fiber Reinforced Plastic (GFRP) Composites Market Covering Sales Outlook, Up-to-date Key Trends, Market Size and Forecast, Production Capacity, Export and Import Analysis, Regulations, Trade Analysis and Company Analysis (https://www.futuremarketinsights.com/reports/global-glass-fiber-reinforced-plastic-composites-market).
- Epoxy Composite Market Size, Share & Trends Analysis Report By Fiber Type (Glass, Carbon), By End-use (Automotive & Transportation, Wind Energy), By Region (APAC, North America), And Segment Forecasts, 2021–2028 (https://www.grandviewresearch.com/industry-analysis/epoxy-composites-market).
- Lightening the Load: Delivering UK Growth through the multi-sector application of composites, The 2016 UK Composites Strategy, Composites Leadership Forum, 2016, https://compositesuk.co.uk/wp-content/uploads/2021/09/Strategy-final-version_1.pdf.
- DESNZ, Defra, 2023, Unlocking resource efficiency, https://www.gov.uk/government/publications/unlocking-resource-efficiency, accessed January 2024.
- Safe and Sustainable-By-Design: A Transformative Power, https://cefic.org/app/uploads/2022/04/Safe-and-Sustainable-by-Design-Guidance-A-transformative-power.pdf, accessed December 2023.
- Sustainable, by design – HVMC, https://hvm.catapult.org.uk/news/sustainable-by-design/, accessed December 2023.
|
This journal is © The Royal Society of Chemistry 2024 |
Click here to see how this site uses Cookies. View our privacy policy here.