Honeycomb-like hollow carbon loaded with ruthenium nanoparticles as high-performance HER electrocatalysts†
Received
18th October 2023
, Accepted 14th November 2023
First published on 14th November 2023
Abstract
Electrolysis of water to produce hydrogen is an effective way to prepare green hydrogen, and hydrogen evolution reaction (HER) catalysts play a very important role in the reaction. We obtained a honeycomb-like hollow carbon material through simple etching of ZIF8, which can uniformly load a low content of ruthenium nanoparticles, fully expose active sites and react with electrolytes, thereby improving its catalytic performance. ICP-OES shows that the ruthenium content is only 0.73 wt%. The HER catalytic performance of Ru/HNC is excellent, and it also has good acid-base adaptability. For Ru/HNC, in 1 M KOH, the overpotential is only 44 mV at 10 mA cm−2, almost equivalent to that of Pt/C (31 mV). At higher current densities, its performance even exceeds that of Pt/C; the overpotential is 194 mV and 286 mV at 100 mA cm−2 and 200 mA cm−2, respectively. Under the same conditions, for Pt/C, the overpotential is 197 mV and 330 mV at 100 mA cm−2 and 200 mA cm−2, respectively. Under acidic conditions, Ru/HNC also exhibits excellent HER catalytic performance. The overpotential is 71 mV, 148 mV and 194 mV at 10 mA cm−2, 100 mA cm−2 and 200 mA cm−2, respectively. In the water-splitting test, the decomposition voltage only needs 1.51 V at 10 mA cm−2 (1.64 V, 100 mA cm−2).
Introduction
Due to the rapid development of the economy, energy demand is becoming increasingly urgent, and the increasingly depleted fossil energy cannot meet people's needs and will cause serious environmental pollution. Hydrogen energy has advantages such as high combustion heat value, sustainability, abundant reserves, and zero pollution.1,2 Developing hydrogen energy can achieve green, clean, and sustainable development. Among various hydrogen production methods, electrolysis of water for hydrogen production has a very broad application prospect.3,4 The purity of hydrogen produced by this method is very high, making it suitable for application in fuel cells. The hydrogen evolution reaction (HER) is one of the important semi-reactions, usually requiring highly active catalysts to reduce reaction energy barriers, improve reaction activity, and reduce energy loss.5–7 Currently, the best HER catalyst is Pt/C, but it has important drawbacks such as high price and scarce reserves. In recent years, low-platinum and non-platinum catalysts have attracted widespread attention, and many new catalysts have also been developed.8–12
In terms of reducing the amount of platinum, a lot of research work focused on two aspects. On the one hand, the amount of platinum was reduced by modifying the structure of the catalyst to obtain catalysts with better performance, such as core–shell structures, nanostructures, and alloy catalysts.13,14 On the other hand, catalyst support materials were modified to prepare high-performance catalysts with highly dispersed active components, such as using new supports such as carbon nanotubes, carbon nanofibers, and graphene.15,16 Dispersing catalysts on the surface of support materials can yield excellent catalytic materials, and this method has been widely used. Carbon materials are one of the most commonly used supports, and their catalytic activity can be further improved by doping, such as N, S, B, P and other elements.17–20 When carbon materials are combined with heteroatoms, due to the difference in bond length and atomic size, defect sites will be generated near the carbon materials, which will lead to uneven charge distribution around them, thus creating new active sites to improve catalytic performance.21–23 The loaded metal catalyst can also further improve its catalytic performance by regulating its morphology, particle size, dispersibility, and alloying degree.24–27Metal–organic frameworks (MOFs) are a typical representative of such electrocatalysts and have been widely developed and applied.28–30 After pyrolysis of MOFs, not only carbon support materials with rich doping sites can be obtained, but also highly dispersed metal active sites or other active atomic sites can be obtained. At the same time, MOFs have the advantages of high specific surface area and porous structure.31–33 For example, Xu et al. reviewed the application of single/dual-atom or cluster metal catalysts prepared from MOFs in energy storage.34 Wang et al. obtained a high-performance HER catalyst Co1.5W0.5-py-500@NF through heat treatment of CoW-MOF@NF, with an overpotential of only 55 mV at 25 mA cm−2.35
Herein, we use the easily available ZIF8 (2-methylimidazole zinc salt) as the base material and can obtain the honeycomb shape by controlling the etching conditions, which can further increase the probability of the active site contacting the electrolyte. After pyrolysis, we can obtain a nitrogen-doped carbon material with rich open pores. If this material is used as a support to composite with other high-performance metal catalysts, the performance of the material will be greatly improved.36,37 Based on this, we designed to load ruthenium nanoparticles on its surface to improve the HER catalytic performance. Although ruthenium is also one of the platinum-group precious metal elements, its price is relatively cheap and it has excellent catalytic performance, which has attracted widespread research attention. A large amount of work has been carried out around ruthenium-based catalysts.38–43 Ru/HNC loaded with an extremely low content of ruthenium nanoparticles exhibits superior HER catalytic performance, and its catalytic performance is comparable to that of commercial Pt/C under both alkaline and acidic conditions.
Experimental
Chemicals
2-Methylimidazole, Zn(NO3)2·6H2O, tannic acid and RuCl3·3H2O were purchased from J & K CHEMICAL Co., Ltd. The commercial Pt/C catalyst was purchased from Shanghai Macklin Biochemical Co., Ltd.
Synthesis of ZIF8
Typically, 2-methylimidazole (2-MI) (4.86 g) and Zn(NO3)2·6H2O (4.41 g) were dissolved in 150 mL methanol under vigorous stirring to form a clear solution, respectively. Then, the former solution was added to the latter solution under stirring. The obtained mixture was stirred at room temperature for 12 h to form ZIF8. The solid product (ZIF8) was collected by centrifugation, washed with methanol three times, and dried at 60 °C in a vacuum overnight.
Synthesis of H-ZIF8
In a typical synthesis, ZIF8 was dissolved in deionized water first, then ethanol was slowly added to precipitate, and then it was collected by centrifugation, and dried at 60 °C in a vacuum overnight. Then, 180 mg of this ZIF8 is dissolved in 30 mL of methanol solution containing 200 mg of tannic acid. After stirring for 15 min, the product is collected by centrifugation, washed with ethanol 3 times, and dried at 60 °C in a vacuum overnight.
Synthesis of NC
ZIF8 was sealed in a quartz tube and heated at 900 °C for 2 h under a high-purity N2 atmosphere, and the heating rate was 5 °C min−1. The resulting black powder was named NC.
Synthesis of HNC
H-ZIF8 was sealed in a quartz tube and heated at 900 °C for 2 h under a high-purity N2 atmosphere, and the heating rate was 5 °C min−1. The resulting black powder was named HNC.
Synthesis of Ru/HNC
H-ZIF8 (100 mg) and RuCl3·3H2O (5 mg) were added to deionized water (20 mL), and then the mixture was stirred at room temperature for 4 h. After that, the mixture was centrifuged and dried. Then, the residue was sealed in a quartz tube and heated at 900 °C for 2 h under a high-purity N2 atmosphere, and the heating rate was 5 °C min−1. The resulting black powder was named Ru/HNC.
Synthesis of Ru/NC
ZIF8 (100 mg) and RuCl3·3H2O (5 mg) were added to deionized water (20 mL), and then the mixture was stirred at room temperature for 4 h. After that, the mixture was centrifuged and dried. Then, the residue was sealed in a quartz tube and heated at 900 °C for 2 h under a high-purity N2 atmosphere, and the heating rate was 5 °C min−1. The resulting black powder was named Ru/HNC.
Materials characterization
The material morphology was examined using a field emission scanning electron microscope (Sigma 500) with an accelerating voltage of 30 kV and a transmission electron microscope (TEM) (JEM-2100, JEOL, Japan) operating at 200 kV. X-ray diffraction (XRD) patterns were acquired on a PANalytical X’Pert powder diffractometer with Cu-Kα radiation. The X-ray photoelectron spectroscopy (XPS) with an Al-Kα X-ray source (Thermo Escalab 250Xi) was performed to determine the surface composition. The content of Ru was determined by inductively coupled plasma optical emission spectrometry (Agilent, ICP-OES 720). N2 adsorption–desorption data were collected using a physisorption analyzer (Tristar II 3020).
Electrochemical measurements
A conventional three-electrode system was employed to evaluate the electro-catalytic performance of the obtained catalyst on a CHI 760E electrochemical workstation. HER measurements were carried out in 0.5 M H2SO4 and 1.0 M KOH aqueous solutions at a scan rate of 5 mV s−1. A rotating disk electrode (RDE) with a glassy carbon (GC) disk loaded with catalysts was used as the working electrode, Ag/AgCl was used as the reference electrode, and graphite was used as the counter electrode. All potentials were iR compensated and converted to a reversible hydrogen electrode (RHE) scale via calibration. All the polarization curves are the ones reaching steady states after several cycles. The electrolyte solution was saturated with N2 for 30 min before each test. The TOF (H2 s−1) was calculated with the following equation: TOF = I/(2Fn), where I is the current (A) during linear sweep voltammetry (LSV), F is the Faraday constant (96485.3C mol−1), and n is the number of active sites (mol). The factor 1/2 is based on the assumption that two electrons are necessary to form hydrogen molecules.
Results and discussion
The synthesis of Ru/HNC is schematically illustrated in Fig. 1. We chose ZIF8 as the basic support, and its preparation method is very simple, and a lot of research work has been carried out around it. Through optimization of conditions, we can obtain honeycomb-like materials after etching. Tannic acid is easily soluble in water and ethanol and can disrupt the metal zinc nodes in ZIF8, degrade metal organic bonds, and thus destroy the polyhedral structure of ZIF8. It can also effectively connect ZIF8 together, resulting in a honeycomb-like structure. Such structural features are conducive to full contact between the active site and electrolyte and can improve catalytic activity. In addition, this structure is also beneficial for reducing the amount of ruthenium nanoparticles used and can exhibit excellent catalytic performance even when loaded with an extremely low content of ruthenium nanoparticles. We first use a scanning electron microscope (SEM) to observe and analyze the morphology of the material. As shown in Fig. 2a and S1,† ZIF8 with a standard polyhedral structure can be easily prepared. In order to obtain honeycomb-like materials, we use tannic acid for etching. However, it is interesting that if ZIF8 is directly etched, honeycomb-like materials cannot be obtained. We have tried several times and found that under the same conditions, only a few ZIF8 particles are etched, while the majority of ZIF8 particles remain unchanged (Fig. S2†). As shown in Fig. 2b and S3,† we first dissolve ZIF8 in deionized water, then precipitate it with ethanol, and then use tannic acid etching to obtain honeycomb-like material H-ZIF8. In order to further improve the HER catalytic performance, we designed and utilized H-ZIF8 to naturally adsorb RuCl3·3H2O. After pyrolysis, a carbon-based material uniformly loaded with ruthenium nanoparticles (Ru/HNC) can be obtained. As shown in Fig. 2c and S4,† Ru/HNC still maintains the honeycomb shape. This material has very rich open pores, which is conducive to creating more active sites. In order to further observe and analyze the morphology of the material and the distribution of ruthenium nanoparticles, we conducted transmission electron microscope (TEM) related tests. As shown in Fig. 2d, e and S5,† it can be clearly seen that Ru/HNC presents a honeycomb shape, and each nanoparticle is a hollow structure with open pores. In addition, ruthenium nanoparticles are uniformly loaded on the inner and outer surfaces of the material, and the nanoparticles are also very small. The surface of the material is uniformly dispersed with a type of small nanoparticles. High-resolution transmission electron microscopy (HR-TEM) can further confirm these ruthenium nanoparticles. In addition, we can clearly see three types of lattice spacing, which are measured to be 0.205 nm, 0.234 nm and 0.214 nm, which should be attributed to (101), (100) and (002) facets (Fig. S6†). We conducted statistical analysis on the particle size distribution of ruthenium nanoparticles, and the results showed that the particle size was about 3–4 nm (Fig. S7†). In addition, we also recorded the N2 adsorption–desorption isotherms of Ru/HNC (Fig. S8†). It is obvious that the isotherm with a sharp increase in the relatively low pressure region indicates the presence of micropores. Under relatively high pressure, a significant hysteresis loop appears, indicating the presence of mesopores. The specific surface area is 316.8 m2 g−1. From the pore size distribution, it can be seen that there are mainly mesopores around 4 nm and some larger mesopores around 20 nm. This structural characteristic is beneficial for exposing more active sites and allowing for full contact with electrolytes, thereby improving the catalytic performance of the material. In order to further analyze the distribution of elements, we recorded the TEM-EDS mapping spectrum (energy dispersive spectrometer) of the material. Obviously, the distribution of C, O, N, and Ru is very uniform. Due to the large amount of N element in the precursor ZIF8, N-doped hollow carbon materials can be easily obtained after pyrolysis. From the distribution of the ruthenium element, it can be seen that its distribution is very uniform, and it is inferred that its content is also very low. The ICP-OES (inductively coupled plasma optical emission spectrometer) test results show that the ruthenium content is only 0.73 wt%. Such a low content of ruthenium can be uniformly loaded on nitrogen-doped hollow carbon materials and exhibit excellent HER catalytic performance, surpassing many similar materials (Tables S1 and S2†).
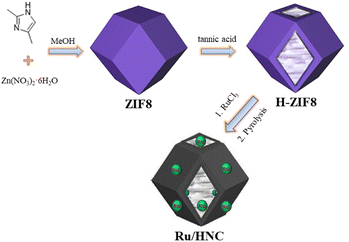 |
| Fig. 1 Fabrication process of Ru/HNC. | |
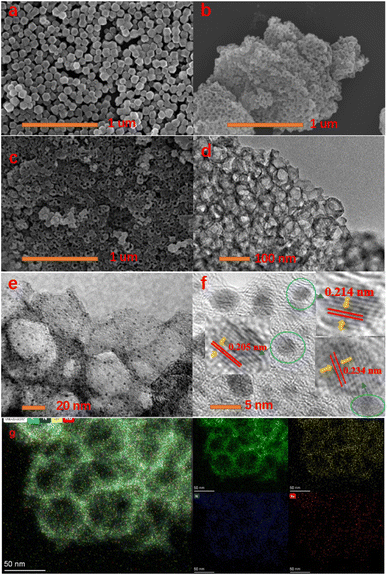 |
| Fig. 2 (a) SEM of ZIF8, (b) SEM of H-ZIF8, (c) SEM of Ru/HNC, (d and e) TEM of Ru/HNC, (f) HR-TEM of Ru/HNC, and (g) TEM-EDS mapping of Ru/HNC. | |
The X-ray diffraction (XRD) patterns of ZIF8 and H-ZIF8 are shown in Fig. S9.† It can be seen that the crystallinity of the ZIF8 we prepared is very good, and its diffraction peaks show a narrow and pointed distribution, corresponding to the standard spectral peaks one by one. From the previous morphology analysis, it can also be seen that ZIF8 exhibits a standard octahedral structure, indicating good crystallinity. After etching with tannic acid, it still maintains the standard diffraction peak, indicating that its basic structure has not been damaged. After carbonization, these materials also exhibit wider diffraction peaks near 23° and 43°, indicating that they are amorphous carbon materials (Fig. S10†). For Ru/HNC and Ru/NC, no diffraction peaks of ruthenium nanoparticles were observed, which should be due to the low content of ruthenium and the excessively small particles.
In order to analyze the elemental composition and chemical valence state of the material and determine the presence of elements such as N and Ru, we further performed X-ray photoemission spectroscopy (XPS). As shown in Fig. 3a, the C, O, N and Ru elements can be readily resolved. The raw material dimethyl imidazole contains a large amount of nitrogen element, so the N-doping effect can be achieved after pyrolysis. N-doping of materials has a positive significance in the field of electrocatalysis. When carbon materials combine with heteroatoms, due to differences in bond length and atomic size, defect sites will be generated near the carbon material, which can lead to uneven distribution of charges around it and improve its catalytic performance. In addition, it can also be easily seen that ruthenium element exists in the material. As shown in Fig. 3b, there are four characteristic peaks in the high-resolution C1s + Ru3d spectrum, which are C
C, C–N, C
O and Ru0 at 284.8 eV, 285.4 eV, 288.6 eV and 280.2 eV respectively. Due to the low content of ruthenium, in order to further analyze the valence state of ruthenium, we also analyzed the high-resolution spectra of Ru3P. From Fig. 3d, we can see two distinct peaks. The peaks with binding energy of 461.6 eV and 483.7 eV are assigned to Ru0. The peaks with binding energy of 465.2 eV and 487.1 eV are assigned to Run+. It can be seen from the N1s spectrum that there are three forms of nitrogen distribution in the material, namely pyridinic-N, pyrrolic-N and N-oxide, respectively, and their binding energy is 398.4 eV, 400.1 eV and 404.5 eV, respectively. It is evident that this material is a nitrogen-doped hollow carbon material loaded with an extremely low content of ruthenium nanoparticles.
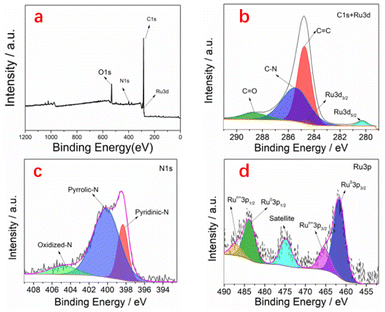 |
| Fig. 3 (a) XPS survey spectrum of Ru/HNC and (b–d) high-resolution XPS spectra of C1s + Ru3d, N1s, and Ru3p. | |
We used a three-electrode system to test the HER catalytic performance and conducted tests under both alkaline and acidic conditions. In 1 M KOH, these materials exhibit significantly different catalytic effects, indicating that NC has the worst catalytic performance. As shown in Fig. 4b, for NC, the overpotential is 637 mV at 10 mA cm−2. At 100 mA cm−2, the overpotential is as high as 834 mV. After etching, the material forms a hollow structure with an overall appearance like a honeycomb, which can greatly increase the contact probability between the active site and the electrolyte, so the catalytic activity has been significantly improved. For HNC, the overpotential is 513 mV at 10 mA cm−2; although the catalytic performance is still poor, the overpotential loss has been reduced by 124 mV. When the current density reaches 100 mA cm−2, the overpotential has decreased to 660 mV. Ruthenium has been extensively studied in recent years for its efficient HER catalytic activity and relatively inexpensive price. In order to further improve the catalytic performance of the material, we designed to uniformly load ruthenium nanoparticles on its surface. As expected, the performance of the material was greatly improved after loading ruthenium nanoparticles. For Ru/NC, the overpotential is only 112 mV at 10 mA cm−2. Obviously, there has been a significant improvement in potential loss. At 100 mA cm−2, the overpotential is 295 mV. At 200 mA cm−2, the overpotential is 381 mV. We can clearly see that Ru/HNC has the best HER catalytic performance. The open and hollow structures formed after etching can better support ruthenium nanoparticles, which can improve the contact probability between the active site and the electrolyte, so the catalytic performance has been further improved. Even compared to Pt/C, it exhibits better catalytic performance. At 10 mA cm−2, the overpotential is only 44 mV. When the current density reaches 100 mA cm−2, the overpotential has decreased to 194 mV. Even at a high current density of 200 mA cm−2, its overpotential is only 286 mV. Under the same conditions, the overpotentials of Pt/C are 31 mV (10 mA cm−2), 197 mV (100 mA cm−2), and 330 mV (200 mA cm−2), respectively. As shown in Fig. 4b, we further analyzed their Tafel slope; the value of Ru/HNC (72 mV dec−1) is almost the same as that of Pt/C (62 mV dec−1), which shows very fast reaction kinetics. The value of Ru/NC is 140 mV dec−1, this is consistent with its relatively poor catalytic performance. The smaller the Tafel slope, the faster the reaction kinetics. Based on previous research, for Ru/HNC, the reaction should follow the Volmer–Heyrovsky mechanism, which is the electrochemical–desorption reaction path.44,45 The HER catalytic performance in 0.5 M H2SO4 was also tested. The catalytic performance of these materials is consistent with the situation under alkaline conditions. NC still exhibits the worst catalytic performance. At 10 mA cm−2, the overpotential reaches up to 687 mV. After etching, the catalytic performance is significantly improved. The overpotential of HNC has been reduced to 487 mV, and the working current density has also significantly increased. When the current density reaches 100 mA cm−2, the overpotential has decreased to 703 mV. After compounding these carbon materials with ruthenium nanoparticles, their catalytic performance has greatly improved. For Ru/NC, at 10 mA cm−2, the overpotential is 75 mV. When the current density reaches 100 mA cm−2, the overpotential has decreased to 215 mV. Even at a high current density of 200 mA cm−2, its overpotential is only 280 mV. Ru/HNC shows the best HER catalytic performance. At 10 mA cm−2, the overpotential is only 71 mV, its performance is almost identical to that of Pt/C (77 mV, 10 mA cm−2). Even at high current densities, its performance surpasses that of most reported similar materials. The overpotentials are 148 mV (100 mA cm−2) and 194 mV (200 mA cm−2), respectively. As shown in Fig. 4d, their Tafel slope was further analyzed; the value for Ru/HNC is 52 mV dec−1 and the value for Ru/NC is 77 mV dec−1. Ru/HNC exhibits very fast reaction kinetics, which is consistent with its excellent HER catalytic performance. The intrinsic HER catalytic activities of Ru/HNC were calculated by using their turnover frequencies (TOFs). Through ICP-OES analysis, it can be known that the ruthenium content is extremely low, only 0.73% wt%. As shown in Fig. 4f, in 1 M KOH, the TOF values of Ru/HNC at the overpotentials of 50 mV, 100 mV and 150 mV were 1.69, 4.66 and 9.16 H2 s−1, respectively. In 0.5 M H2SO4, the TOF values at the overpotentials of 50 mV, 100 mV and 150 mV were 0.36, 4.40 and 15.13 H2 s−1, respectively.
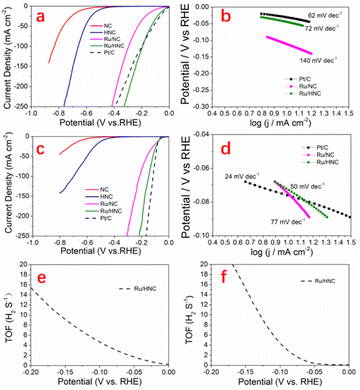 |
| Fig. 4 (a) Linear sweep voltammetry (LSV) curves of the NC, HNC, Ru/NC, Ru/HNC and commercial Pt/C catalyzed HER in 1 M KOH, (b) Tafel plots of the Ru/NC, Ru/HNC and commercial Pt/C catalyzed HER in 1 M KOH, (c) LSVs of the NC, HNC, Ru/NC, Ru/HNC and commercial Pt/C catalyzed HER in 0.5 M H2SO4, (d) Tafel plots of the Ru/NC, Ru/HNC and commercial Pt/C catalyzed HER in 0.5 M H2SO4, (e) TOF of Ru/HNC in 1 M KOH, and (f) TOF of Ru/HNC in 0.5 M H2SO4. | |
The quality of charge transfer performance is crucial for the performance of catalysts, and their electrochemical impedance spectrum (EIS) and charge transfer impedance (Rct) were measured. The bias voltage is −50 mV, and the scanning frequency ranges from 105 to 0.1 Hz. As shown in Fig. 5a, in 1 M KOH, both NC and HNC have very large charge transfer impedances, therefore their catalytic performance is not ideal. After etching, there is a certain degree of improvement in charge transfer performance. After loading ruthenium, the charge transfer impedance of the material decreases sharply. We can see that the impedance of Ru/NC is much smaller than that of NC and HNC. And Ru/HNC has the smallest impedance, even exceeding that of Pt/C, which is consistent with its most excellent HER catalytic performance. In 0.5 M H2SO4, the situation of charge transfer impedance is consistent with that under alkaline conditions. Ru/HNC also has the smallest impedance, indicating its excellent catalytic performance (Fig. S11†). The electrochemical active area (ECSA) can truly reflect the catalytic activity of the material, which can be indirectly obtained through double-layer capacitance (Cdl) testing. Fig. 5b and S12–S14† show that the Cdl of Ru/HNC is 86 mF cm−2 and 81 mF cm−2 in 0.5 M H2SO4 and 1 M KOH, respectively. In contrast, the Cdl of Ru/NC is 71 mF cm−2 and 70 mF cm−2 in 0.5 M H2SO4 and 1 M KOH, respectively. The results show that Ru/HNC has a large electrochemical active area, which means that it has more active sites and more chances to come in contact with electrolytes, so it has better catalytic performance. We analyzed the stability of the material through 5000 cycles of CV testing. The same cycle tests were conducted in both alkaline and acidic electrolytes, and the results showed that this material has good stability, with overpotential loss not exceeding 2 mV (Fig. 5c and S15†). We also further observed the morphology of the material, and the results showed that there was basically no change. The small ruthenium nanoparticles were still uniformly dispersed on the carbon support, and there was no obvious aggregation phenomenon (Fig. S16†). In addition, we use Ru/HNC as a cathode catalyst and commercial RuO2 as an anode for overall water-splitting in 1.0 M KOH. It can be seen that the decomposition voltage is very low, only 1.51 V (10 mA cm−2). At 100 mA cm−2, the decomposition voltage is 1.64 V. For Pt/C, the decomposition voltage is 1.54 V and 1.75 V at 10 mA cm−2 and 100 mA cm−2, respectively. It can be seen that this catalyst can significantly reduce the loss of overpotential and effectively reduce energy consumption in the process of electrolyzing water to produce hydrogen gas.
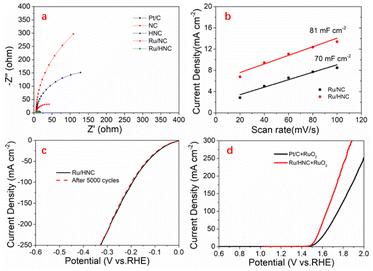 |
| Fig. 5 (a) EIS of the NC, HNC, Ru/NC, Ru/HNC and commercial Pt/C in 1 M KOH, (b) the linear slope of Ru/NC and Ru/HNC, equivalent to twice the double-layer capacitance, Cdl was used to represent the rECSA in 1 M KOH, (c) LSVs of Ru/HNC catalysts before and after 5000 CV cycles in 1 M KOH, and (d) the (LSV) curve of the Ru/HNC and Pt/C as the cathode catalysts for overall water-splitting in 1 M KOH. | |
Conclusions
In summary, the high-performance HER catalyst Ru/HNC exhibits excellent catalytic performance under both alkaline and acidic conditions. We can obtain a honeycomb-like ZIF8 by adjusting the etching conditions, and then use it as a support to load ruthenium nanoparticles with extremely low content (0.73 wt%). The honeycomb-like and hollow carbon material is very suitable as a support for ruthenium nanoparticle catalysts, which can fully expose active sites and have sufficient contact and reaction with electrolytes. Even when loaded with an extremely low content of ruthenium nanoparticles, it can display excellent HER catalytic performance, which can also reduce the cost of the catalyst and provide theoretical guidance for the development of inexpensive non-platinum catalysts. Ru/HNC exhibits excellent HER catalytic performance; in 1 M KOH, the overpotential is only 44 mV (10 mA cm−2). More importantly, at high current density, it exhibits more excellent catalytic performance, even surpassing Pt/C. The overpotential is 194 mV and 286 mV at 100 mA cm−2 and 200 mA cm−2, respectively. The HER catalytic performance is also very excellent in 0.5 M H2SO4, almost identical to that of Pt/C. Ru/HNC has very high turnover frequencies; in 1 M KOH, the TOF values at the overpotentials of 50 mV, 100 mV and 150 mV were 1.69, 4.66 and 9.16 H2 s−1, respectively. When Ru/HNC is used as a cathode catalyst for water-splitting, the required bias voltage is only 1.51 V at 10 mA cm−2 (1.64 V, 100 mA cm−2).
Conflicts of interest
There are no conflicts to declare.
Acknowledgements
This work was supported by grants from the Postgraduate Research & Practice Innovation Program of Jiangsu Province (No. SJCX23-1641) of China, College Students' Training Program of Innovation and Entrepreneurship of Jiangsu Province (No. 202311463012Z) of China, Zhongwu Youth Innovative Talent Support Program of Jiangsu University of Technology, Qing Lan Project of Jiangsu Province, Key Research and Development Program of Jiangsu Province (No. BE2021640) and Changzhou Science and Technology Bureau (No. CM20223017).
Notes and references
- M. Chatenet, B. G. Pollet, D. R. Dekel, F. Dionigi, J. Deseure, P. Millet, R. D. Braatz, M. Z. Bazant, M. Eikerling, I. Staffell, P. Balcombe, Y. Shao-Horn and H. Schäfer, Water electrolysis: from textbook knowledge to the latest scientific strategies and industrial developments, Chem. Soc. Rev., 2022, 51, 4583–4762 RSC.
- A. Devendran and A. Nagai, Recent advancements in 3D porous graphene-based electrode materials for electrochemical energy storage applications, Adv. Mater., 2023, 4, 2524–2543 RSC.
- S. Zhu, Z. Xu, H. Tao, D. Yang, X. Tang and Y. Wan, Planar micro-supercapacitors toward high performance energy storage devices: design, application and prospects, Energy Adv., 2023, 2, 765–783 RSC.
- S. Palchoudhury, K. Ramasamy, J. Han, P. Chen and A. Gupta, Transition metal chalcogenides for next-generation energy storage, Nanoscale Adv., 2023, 5, 2724–2742 RSC.
- V. Jose, V.-H. Do, P. Prabhu, C.-K. Peng, S.-Y. Chen, Y. Zhou, Y.-G. Lin and J.-M. Lee, Activating Amorphous Ru Metallenes Through CoIntegration for Enhanced Water Electrolysis, Adv. Energy Mater., 2023, 2301119 CrossRef CAS.
- L. Yang, R. Grzeschik, P. Jiang, L. Yu, C. Hu, A. Du, S. Schlücker and W. Xie, Tuning the Electronic Properties of Platinum in Hybrid-Nanoparticle Assemblies for use in Hydrogen Evolution Reaction, Angew. Chem., 2023, 135, e2023010 Search PubMed.
- Q. Du, R. Zhao, X. Chen, L. Liu, S. Zhang, T. Guo, J. Du and J. Li, Synthesis of Ultrathin and Grid-Structural Carbon Nanosheets Coupled with Mo2C for Electrocatalytic Hydrogen Production, Chem.–Asian J., 2021, 16, 2107–2112 CrossRef CAS PubMed.
- Z. Zhang, C. Jiang, P. Li, Q. Feng, Z. l. Zhao, K. Yao, J. Fan, H. Li and H. Wang, Pt atoms on doped carbon nanosheets with ultrahigh N content as a superior bifunctional catalyst for hydrogen evolution/oxidation, Sustainable Energy Fuels, 2021, 5, 532–539 RSC.
- H. Chen, C. Guan and H. Feng, Pt-Based High-Entropy Alloy Nanoparticles as Bifunctional Electrocatalysts for Hydrogen and Oxygen Evolution, ACS Appl. Nano Mater., 2022, 5, 9810–9817 CrossRef CAS.
- S. Jaiswal, R. Mondal, V. Kushwaha, A. Gupta and P. Singh, Tuning of Redox Energy of Transition-Metal Ions through the Utilization of Interlayer Potentials in Layered Perovskites: Development of a Titanium-Based Superior HER Catalyst in an Acidic Medium, ACS Appl. Energy Mater., 2023, 6, 7323–7334 CrossRef CAS.
- D. Maarisetty, D.-R. Hang, M. M. C. Chou and S. Parida, Tuning the Ni/Co Ratios and Surface Concentration of Reduced Molybdenum States for Enhanced Electrocatalytic Performance in Trimetallic Molybdates: OER, HER, and MOR Activity, ACS Appl. Energy Mater., 2022, 5, 14059–14070 CrossRef CAS.
- S. L. Zhang, X. F. Lu, Z.-P. Wu, D. Luan and X. W. Lou (David), Engineering Platinum–Cobalt Nano-alloys in Porous Nitrogen-Doped Carbon Nanotubes for Highly Efficient Electrocatalytic Hydrogen Evolution, Angew. Chem., Int. Ed., 2021, 60, 19068–19073 CrossRef CAS.
- R. Zhang, A. Xie, L. Cheng, Z. Bai, Y. Tang and P. Wan, Hydrogen production by traditional and novel alkaline water electrolysis on nickel or iron based electrocatalysts, Chem. Commun., 2023, 59, 8205–8221 RSC.
- S. Sk, S. P. Shelake, D. Dolui, S. Karim, R. Ghosh, M. V. Jyothirmai, A. V. S. Sainath, U. Pal and A. Dutta, Post-synthetic modulation of UiO-66-NH2 with a cobaloxime catalyst for efficient hydrogen production, Energy Adv., 2023, 2, 1116–1121 RSC.
- Y. Luo, Y. Yan, S. Zheng, H. Xue and H. Pang, Graphitic carbon nitride based materials for electrochemical energy storage, J. Mater. Chem. A, 2019, 7, 901–924 RSC.
- M. Khalid, P. A. Bhardwaj, A. M. B. Honorato and H. Varela, Metallic single-atoms confined in carbon nanomaterials for the electrocatalysis of oxygen reduction, oxygen evolution, and hydrogen evolution reactions, Catal. Sci. Technol., 2020, 10, 6420–6448 RSC.
- P. Kuang, M. Sayed, J. Fan, B. Cheng and J. Yu, 3D Graphene-Based H2-Production Photocatalyst and Electrocatalyst, Adv. Energy Mater., 2020, 10, 1903802 CrossRef CAS.
- I. Ahmed, R. Biswas, R. A. Patil, K. K. Halder, H. Singh, B. Banerjee, B. Kumar, Y.-R. Ma and K. K. Haldar, Graphitic Carbon Nitride Composites with MoO3-Decorated Co3O4Nanorods as Catalysts for Oxygen and Hydrogen Evolution, ACS Appl. Nano Mater., 2021, 4, 12672–12681 CrossRef CAS.
- S. S. Kumar and H. Lim, Recent advances in hydrogen production through proton exchange membrane water electrolysis-a review, Sustainable Energy Fuels, 2023, 7, 3560–3583 RSC.
- H. Liu, Y. Li, Y. Pan, J. Xie, B. Li, Z. Guo and T.-C. Lau, Roles of Co Dopants in Electrocatalytic Hydrogen Evolution by N-Rich Carbon Nanotubes Grafted on Carbon Layers, ACS Appl. Nano Mater., 2021, 4, 11830–11840 CrossRef CAS.
- T. Liu, B. Feng, X. Wu, Y. Niu, W. Hu and C. M. Li, Ru2P Nanoparticle Decorated P/N-Doped Carbon Nanofibers on CarbonCloth as a Robust Hierarchical Electrocatalyst with Platinum-Comparable Activity toward Hydrogen Evolution, ACS Appl. Energy Mater., 2018, 1, 3143–3150 CrossRef CAS.
- S. Sharma, S. Basu, N. P. Shetti, K. Mondal, A. Sharma and T. M. Aminabhavi, Versatile Graphitized Carbon Nanofibers in Energy Applications, ACS Sustain. Chem. Eng., 2022, 10, 1334–1360 CrossRef CAS.
- M. Yadav, D. K. Singh and V. Ganesan, Template-free hydrothermal synthesis of nickel sulfide nanocrystals on MWCNTs: efficient and stable bifunctional electroactive material for oxygen electrocatalysis, Sustainable Energy Fuels, 2023, 7, 3077–3087 RSC.
- X. Wang, Y. Wang, X. Ma, L. Xu, S. Liu, W. Wang, H. Lu and L. Wu, Carbon layer-protected self-supporting CoSe2 nanowire arrays for durable hydrogen evolution reaction catalysts, Sustainable Energy Fuels, 2023, 7, 3116–3121 RSC.
- H. Zhang, W. Wang, Z. Dai, Y. Zhu, M. Cheng, B. Zhang, Y. Feng, Y. Zhang and G. Zhang, Boosting hydrazine oxidation and hydrogen evolution catalysis with anchored Ru clusters by electronically tunable Ru–S–C bonds, J. Mater. Chem. A, 2023, 11, 14674–14681 RSC.
- Z. Wang, J. Huang, J. Mao, Q. Guo, Z. Chen and Y. Lai, Metal–organic frameworks and their derivatives with graphene composites: preparation and applications in electrocatalysis and photocatalysis, J. Mater. Chem. A, 2020, 8, 2934–2961 RSC.
- C. Hu, R. Paul, Q. Daib and L. Dai, Carbon-based metal-free electrocatalysts: from oxygen reduction to multifunctional electrocatalysis, Chem. Soc. Rev., 2021, 50, 11785–11843 RSC.
- D. Guan, H. Xu, Q. Zhang, Y.-C. Huang, C. Shi, Y.-C. Chang, X. Xu, J. Tang, Y. Gu, C.-W. Pao, S.-C. Haw, J.-M. Chen, Z. Hu, M. Ni and Z. Shao, Identifying a universal activity descriptor and a unifying mechanism concept on perovskite oxides for green hydrogen production, Adv. Mater., 2023, 2305074 CrossRef CAS.
- F. Abdelghafar, X. Xu, S. P. Jiang and Z. Shao, Designing single-atom catalysts toward improved alkaline hydrogen evolution reaction, Mater. Rep.: Energy, 2022, 2, 100144 CAS.
- X. Xu, H. Sun, S. P. Jiang and Z. Shao, Modulating metal-organic frameworks for catalyzing acidic oxygen evolution for proton exchange membrane water electrolysis, SusMat, 2021, 1, 460–481 CrossRef CAS.
- H. J. Kim, H. Y. Kim, J. Joo, S. H. Joo, J. S. Lim, J. Lee, H. Huang, M. Shao, J. Hu, J. Y. Kim, B. J. Min, S. W. Lee, M. Kang, K. Lee, S. Choi, Y. Park, Y. Wang, J. Li, Z. Zhang, J. Ma and S.-I. Choi, Recent advances in non-precious group metal based catalysts for water electrolysis and beyond, J. Mater. Chem. A, 2022, 10, 50–88 RSC.
- H. Xu, Y. Li, Q. Li, D. Yang, T. Li, S. Jin, L. Zhou, Q. Zhang and J. H. Clark, Reactive oxygen species induced by plant essential oil for effective degradation of p-phenylenediamine, Green Chem., 2023, 25, 5647–5653 RSC.
- W. Cheng, H. Zhang, D. Luan and X. W. Lou (David), Exposing unsaturated Cu1-O2 sites in nanoscale Cu-MOF for efficient electrocatalytic hydrogen evolution, Sci. Adv., 2021, 7, eabg2580 CrossRef CAS.
- A. S. A. Ahmed, M. M. S. Sanad, A. Kotb, A. N. R. M. Negm and M. H. Abdallah, Removal of methyl red from wastewater using a NiO@Hyphaene thebaica seed-derived porous carbon adsorbent: kinetics and isotherm studies, Adv. Mater., 2023, 4, 2981–2990 RSC.
- P. Zhou, L. Wang, J. Lv, R. Li, F. Gao, X. Huang, Y. Lu and G. Wang, Tuning the electronic structure of Co@N–C hybrids via metal-doping for efficient electrocatalytic hydrogen evolution reaction, J. Mater. Chem. A, 2022, 10, 4981–4991 RSC.
- H. Qi, X. Guan, G. Lei, M. Zhao, H. He, K. Li, G. Zhang, F. Zhang, X. Fan, W. Peng and Y. Li, Bimetallic ZIF-Derived Co/N-Codoped Porous Carbon Supported Ruthenium Catalysts for Highly Efficient Hydrogen Evolution Reaction, Nanomaterials, 2021, 11, 1228 CrossRef CAS.
- I. Rabani, J.-W. Lee, S. R. Choi, J.-Y. Park, S. A. Patil, G. R. Turpu, M. Kim and Y. Soo-Seo, Structural engineering of ruthenium decorated zeolitic imidazole framework nanocomposite for hydrogen evolution reactions and supercapacitors, J. Energy Storage, 2023, 62, 106885 CrossRef.
- S. Zhao, Y. Zhang, H. Li, S. Zeng, R. Li, Q. Yao, H. Chen, Y. Zheng and K. Qu, Regulating Ru active sites by Pd alloying to significantly enhance hydrazine oxidation for energy-saving hydrogen production, J. Mater. Chem. A, 2023, 11, 13783–13792 RSC.
- Y. Cao, S. Liang, Y. Yan, W. Dong, C. Dong, W. Zheng, S. Nong and F. Huang, Unique sandwich structure of Ru@TiO2: salicylic acid micro-etching from K2Ti2O5 and high-performance electrocatalytic hydrogen evolution, Inorg. Chem. Front., 2023, 10, 3852–3859 RSC.
- Q. Liang, Q. Li, L. Xie, H. Zeng, S. Zhou, Y. Huang, M. Yan, X. Zhang, T. Liu, J. Zeng, K. Liang, O. Terasaki, D. Zhao, L. Jiang and B. Kong, Superassembly of Surface-Enriched Ru Nanoclusters from Trapping-Bonding Strategy for Efficient Hydrogen Evolution, ACS Nano, 2022, 16, 7993–8004 CrossRef CAS PubMed.
- S. Zhou, H. Jang, Q. Qin, L. Hou, M. G. Kim, S. Liu, X. Liu and J. Cho, Boosting Hydrogen Evolution Reaction by Phase Engineering and Phosphorus Doping on Ru/P-TiO2, Angew. Chem., Int. Ed., 2022, 61, e202212196 CrossRef CAS PubMed.
- T. Luo, J. Huang, Y. Hu, C. Yuan, J. Chen, L. Cao, K. Kajiyoshi, Y. Liu, Y. Zhao, Z. Li and Y. Feng, Fullerene Lattice-Confined Ru Nanoparticles and Single Atoms Synergistically Boost Electrocatalytic Hydrogen Evolution Reaction, Adv. Funct. Mater., 2023, 33, 2213058 CrossRef CAS.
- S. Liu, H. Li, J. Zhong, K. Xu, G. Wu, C. Liu, B. Zhou, Y. Yan, L. Li, W. Cha, K. Chang, Y. Y. Li and J. Lu, A crystal glass-nanostructured Al-based electrocatalyst for hydrogen evolution reaction, Sci. Adv., 2022, 8, eadd6421 CrossRef CAS PubMed.
- K. Chi, Z. Wu, X. Tian, Z. Wang, F. Xiao, J. Xiao and S. Wang, Boosting hydrogen evolution via integrated construction and synergistic cooperation of confined graphene/CoSe2 active interfaces and 3D graphene nanomesh arrays, Appl. Catal., B, 2023, 324, 122256 CrossRef CAS.
- J. Xie, H. Zhang, S. Li, R. Wang, X. Sun, M. Zhou, J. Zhou, X. W. Lou (David) and Y. Xie, Defect-Rich MoS2 Ultrathin Nanosheets with Additional Active Edge Sites for Enhanced Electrocatalytic Hydrogen Evolution, Adv. Mater., 2013, 25, 5807–5813 CrossRef CAS PubMed.
Footnote |
† Electronic supplementary information (ESI) available: Synthesis details and characterization data; details for all physical characterization experiments. See DOI: https://doi.org/10.1039/d3se01343j |
|
This journal is © The Royal Society of Chemistry 2024 |
Click here to see how this site uses Cookies. View our privacy policy here.