Retracted Article: Methane conversion for hydrogen production: technologies for a sustainable future
Received
27th July 2023
, Accepted 4th January 2024
First published on 24th January 2024
Abstract
Industrial and technological developments have resulted in a rapid increase in the rate of global energy consumption with the energy demand expected to increase by 33% by 2035. Fossil fuel resources are the dominant source of energy and due to the increased use of fossil fuels, the amount of carbon emissions have grown the highest in the past several years. This also led to an increase in the emission of greenhouse gases (GHGs) like CO2, NOx, and SOx, which contribute to climate change. Moreover, with the world's fossil reserves getting depleted, it is necessary to move towards a sustainable and environmentally genial source of energy. Various technologies are available for the production of hydrogen, among them catalytic decomposition of methane (CDM) to produce hydrogen as a COx free technology have gained the highest importance in recent years due to the CO free production of hydrogen. In this study we will analyze and discuss different carbon nano materials (CNMs) to be recycled as valuable byproduct for different purposes. Moreover, the financial and ecological assessment of CDM will be compared with methane steam reforming in terms of CO2 emission, coal gasification, productivity, and cost of hydrogen production. Catalytic decomposition of methane may be a reliable and convenient technology for on-site maximum production of hydrogen on a small or moderate industrial scale. Ni-based, Fe-based, carbonaceous catalyst and noble metals for the CDM process will be addressed. Prioritizing hydrogen/carbon yield and production costs, iron based catalysts are ideal for catalytic decomposition of methane. Though catalysts based on nickel exhibit a much higher hydrogen production with 0.39 mol H2 per g cat. per h compared to Fe-based ones with 0.22 mol H2 g cat. per h, hydrogen cost of the former is assumed to be 100-fold higher ($0.89/$0.009). Furthermore, CDM performances on various types of reactors will be addressed, the molten-metal catalyst/reactor may be a suitable path for the commercialization of CDM. Lastly, the synthesis mechanism, characterization, and application of carbon byproducts with diverse structures and morphologies will be described in this article. Unlike other studies, the current review will show that economical Fe-based catalysts (10 tons H2/1 ton iron ore) and novel molten-metal reactors (with 95% methane conversion) for CDM are the more suitable research directions for the basic understanding of CDM and moreover carbon nanomaterials synthesized by CDM could be also exploited for supercapacitors, as oil for lubrication and for wastewater purification.
1. Introduction
Global energy consumption (about 86%) is still ruled by fossil fuels; only 14% is coming from alternative renewable energy resources.1 Nevertheless, till now, the great increase in utilization of natural gas, petroleum and heavy oil in transportation and industry has generated huge environmental complications,1,2 and produces large quantity of greenhouse gases (GHGS) like COx, SOx, NOx and CxHy into the earth's atmosphere.3,4 The amount of CH4, another strong greenhouse gas, in earth's atmosphere increased from 722 ppb before 1750 to 1859 ppb in 2018.5 This increased release of CH4 and CO2 resulted in climate change, global warming, acid rain and air pollution,3,4,6 and may have a tragic impact on agriculture and natural ecosystem.7 Therefore, a hydrogen economy free of carbon is strongly needed.8–10 Solar, wind, geothermal, nuclear power and tidal (energy obtained from ocean tides) energy cannot fully meet the energy needs because of their safety concern, high prices, and less developed technology.4,8 These serious environmental issues may be addressed using hydrogen due to its environmentally friendly and sustainable nature. Hydrogen plays a role as an energy carrier both to deliver and store available energy. Hydrogen is significant as an industrial gas and raw material with extensive usages like in oil industry, methanol production, ammonia production and fuel cells etc.11,12 Hydrogen can be quickly transformed into energy by using fuel cells and can be used in vehicles directly. It is expected that in fuel cells powered cars, hydrogen usage could replace petroleum demand, with yearly hydrogen production estimated to be about 150 million tons in 2040.13
H2 is not a prime energy source as it should be produced from its compounds. Methane remains the prime source for H2 production.14 Nowadays, about 90% of the overall world's total hydrogen productivity is obtained from CH4.15 The steam reforming of methane (SRM) is considered the utmost popular method, and around 50% of the global need for hydrogen is achieved through this technology.16 Though, expecting a large quantity of carbon dioxide discharges because of SRM, the process of CDM may produce carbon dioxide free H2. In ref. 17 an ecological and economic study proved that CDM process may work at very low temperatures (600 °C), as compared to SRM. This would lead to a substantial savings of energy. Moreover, other researchers18 evaluate that the CDM-H2 economy might be a bridge for sustainable H2 production.6
Various research studies are investigating catalytic decomposition of methane and few are concentrating on hydrogen production, whereas others particularly on the production of carbon materials. Carbon catalyst and metals19–25 can significantly control carbon structure and hydrogen yield.26 Other researchers27 studied carbon materials as catalysts for methane decomposition by evaluating the role of carbon materials and by deliberating their textural properties, effect and O2 surface group and catalyst surface area. The early activity of catalytic methane decomposition was associated with the presence of oxygen surface group and catalyst surface area; however, the long-standing permanency of the catalyst was associated with the Braunauer Emmett Teller (BET) micro pore volume and surface area. Additionally, study demonstrated that activated carbon black and carbon catalyst were the ones with the best performances among carbon-based materials, thanks to their lower crystalline features.
The growth of carbonaceous and metal catalysts for catalytic methane decomposition with enhanced stability and conversion rate have been studied.28 The highly considered catalysts having carbonaceous nature are carbon black and activated carbon, whereas the most common catalysts made from metals are copper, iron and nickel. The speed of hydrogen production and the properties of carbon formed have been evaluated. The types of reactors, source of heating, methods of formation of the catalyst, regeneration operation and conditions have also been studied. In terms of industrialization, fluidize bed reactors are considered among the best ones for catalytic methane decomposition. The current developments in the reaction mechanism of CDM have been studied4 together with the kinetics on metal catalysts, particularly the function of metal particles during the reaction and inactivation mechanism of the catalysts.8,10 They proposed that the catalyst having the maximum metal loading can reduce more carbon monoxide produced from the support. Moreover, to the earlier stated topics, other groups3 studied entire progress in research or laboratory scale and conferred the effect of co-feeding with propylene, ethylene, ethanol, alkanes, CO2, H2O and catalyst generation for increasing the SDM production. The researchers encouraged additional investigations towards integrated membrane reactors to perform both decomposition renewal and separation processes for reliable, simple, clean and constant production of H2. On these bases, CDM is proven to be a capable exciting technology and its industrialization would be important for the future economy of H2. Though various researches have obtained good performances on CDM over reactor designation and preparation of catalyst, further steps and time are necessary to reach industrialization. Iron based catalysts are considered perfect for CDM, due to their environmental and economic benefits, high temperature resistance, stability, and the production of valuable carbon nano materials (CNMs). Hence, this study reviews iron based catalytic decomposition of methane. The commercial assessment of numerous technologies to produce hydrogen, followed by the function of iron based catalyst, laboratory or pilot reactors, reaction kinetics, particularly molten melt designing, and reaction mechanism are discussed. Moreover, the structures, mechanism of formation and uses of the CNMs byproduct is presented.
2. Economic assessment
Table 1 illustrates numerous types of H2 production methodologies comprising SRM,29 methanol reforming of steam (MSR),30 gasification of coal,31 splitting of water32 and CDM.33 While Table 2 illustrates a summary of basic hydrogen production cost, all-inclusive expenditure of hydrogen production on these methodologies and CO2 taxes. The hydrogen cost for the primary production consists of the material cost, maintenance, fixed assets, electricity, water, workers and steam. The CO2 tax is estimated according to $7.2 per ton CO2, whereas hydrogen production cost estimation is based on primary cost of hydrogen production and tax of CO2. In the case of catalytic CDM, complete H2 manufacturing expenditure is considered based on key production cost of H2, tax on CO2, and financial benefits of the CNMs byproduct.
Table 1 Reaction of some hydrogen production technologies
Technology |
Reaction |
Ref. |
Coal gasification |
C + H2O → CO + H2 |
29
|
CO + H2O → CO2 + H2 |
SRM |
CH4 + H2O → CO + 3H2O |
30
|
CH4 +2H2O → CO2 + 4H2O |
CO + H2O → CO2 + H2 |
MSR |
CH3OH + H2O → CO2 + 3H2O |
31
|
CDM |
CH4 → C + 2H2 |
32
|
Water splitting |
Cathode (−): 2H+ + 2e− → H2 |
33
|
Anode (+): 2H2O → overall reaction 2H2O → 2H2 + O2 |
Table 2 List of hydrogen production technologies and costsa
Production technology |
Productivity (N m3 h−1) |
Primary H2 production cost ($ per t H2) |
CO2 emission (t CO2 per t H2) |
CO2 tax ($) |
Total H2 production cost ($) |
Ref. |
The CO2 tax is calculated based on $7.2 per ton CO2. CDM is feasible with product carbon value $570.3 per ton (methane decomposition to produce one ton hydrogen, meanwhile produce three tons carbon material).
|
Coal gasification |
20 000 |
2020.8 |
29.01 |
208.8 |
2229.6 |
34 and 35 |
SRM |
20 000 |
1934 |
11.04 |
79.5 |
2013.5 |
36 and 37 |
|
1000 |
2693 |
12.49 |
89.9 |
2782.9 |
|
Reforming of methanol |
1200 |
3402.6 |
29.10 |
209.4 |
3612 |
38
|
Electricity-water splitting |
1000 |
6138.7 |
44.94 |
323.4 |
6462 |
39
|
Hydroelectric-water splitting |
1000 |
1977.6 |
14 |
100.8 |
2078.4 |
35
|
Wind power-water splitting |
1000 |
3490.4 |
23.6 |
170 |
3660 |
38 and 39 |
Photovoltaic-water splitting |
1000 |
4624.6 |
31.5 |
226.7 |
4851.2 |
40
|
CDM |
1000 |
2167–3764 |
6.6 |
47.5 |
503.6–2100.6 |
41
|
3. SRM vs. gasification of coal
For SRM process, clearly the entire cost of H2 production and CO2 discharge increases as the production reduces from 20
000 to 1000 N m3 h−1. Having a similar output target of 20
000 N m3 h−1, the cost of entire H2 formation of methane steam reforming ($2013.5 per t H2) is less compared to gasification of coal ($2229.6 per t H2), however the release of carbon dioxide of coal gasification is nearly three times as higher compared to steam reforming of methane.
3.1. SRM vs. MSR
Though the lesser operation temperature ≈ 300 °C makes steam reforming of methane a fascinating technology to produce H2 with lower energy consumption, the entire cost of hydrogen production ($3612 per t H2) and emission of carbon dioxide (29.10 t CO2 per t H2) of MSR remain high compared to SRM ($2013.5 per t H2, 11.04 t CO2 per t H2), at a productivity of H2 c. a. 1000 N m3 h−1.33,36
3.2. SRM vs. water splitting
Splitting of water is an ecofriendly procedure beside a further H2 refinement unit.37Table 2 illustrate that wind, photovoltaic and electricity using splitting of H2O can't contest with SRM at hydrogen production level of 1000 N m3 h−1. In addition, for photovoltaic splitting of H2O, the materials as a photocatalyst must have an appropriate band gap and be active, stable, cheap, abundant, and efficient.38 There are no substances today that can satisfy all these parameters.39 Water splitting through hydroelectric was an alternative mode for SRM to produce hydrogen at the similar expenditure (entire production cost of hydrogen: $2078.4 per t H2vs. $2782.9 per t H2; emissions of CO2: 14 t CO2/ t H2vs. 12.49 t CO2 per t H2). Though, because of the limitation of industrially present electrolyzers†40 (H2 production of polymer electrolyte membrane up to 100 N m h−3; alkaline electrolyzers up to 1000 N m3 h−1), hydroelectric-water splitting production is considered to have little chance of being scaled up to as large as that of SRM.
3.3 SRM vs. CDM
At the level of hydrogen productivity of 1000 N m3 h−1, the complete cost of H2 formation of SRM ($2782.9 per t H2) is high as compared to CDM ($503.6 to 2100.6 per t H2); the emissions of CO2 from CDM (6.6 t CO2 per t H2) are less compared to SRM (12.49 t CO2 per t H2) technology. Research studies41 compared catalytic decomposition of methane H2 formation expenses and showed that a breakeven worth for the byproduct of catalytic decomposition of methane carbon nanomaterials was found to be $503.6 to 2100.6 per t H2, above which catalytic decomposition of methane would be an inexpensive technology competing with steam reforming of methane.41 They additionally determined that the small or average hydrogen formation (1000 N m3 h−3) that happens on the spot on a commercial scale would be the main advantage for CDM process as online hydrogen formation by catalytic decomposition of methane can overcome the expenses of hydrogen transport. Few researchers and different industries are working for the commercialization of systems for CDM. Another group in ref. 42 has effectively produced hydrogen and graphite by methane catalytic decomposition on iron-ore catalyst.
Iron ore it's inexpensive compared to Ni. The energy required for the system was obtained from the produced H2 while the extra one was used as output. In the meantime, to maximize the economic viability, graphite powder byproduct can be wholesaled. Hazer group limited42 can manufacture hydrogen amount of 10 along with 1 ton of Fe ore catalyst. The procedure is combined with the processing of gas liquid to yield graphite and H2 by catalytic decomposition of methane. The researchers intended to manufacture 100 kg maximum pure hydrogen per day, which can be practically implemented by a tiny project of limited supply of hydrogen vehicle. The Karlsruhe Institut fur Technologie (KIT) and Institute of Advanced Sustainability (IASS)42 investigated the CDM process and produced a novel reactor that relies on the technology of liquid metal to eliminate the attached graphite in situ and confirmed the constant and effective reactor operation. This certainly proved the capacity of catalytic decomposition of methane for a huge hydrogen generation. Based on primary evaluation, the starting expenses has been estimated around $2.2 to 3.7 per kg H2, which did not consider the worth of the byproduct of graphite. Linde Engineering and ThyssenKrupp Steel combined with Badische Anilin-und-Soda-Fabrik (BASF) to establish a two-phase process to get the CO, syngas and H2. The very first step contained the production of H2 and C by an advanced technology of decomposition of methane at high temperatures without using a catalyst. H2 gas was then treated with large concentration of carbon dioxide, from additional commercial processes, to attain syngas. Because catalytic decomposition of methane without using a catalyst needs much more heat, BASF has built effective ways that, within the system, recycle the fuel, to significantly reduce the quantity of energy required.
4. Fe-based catalysts for CDM
A large variety of catalysts has been utilized for methane catalytic decomposition. Here, after introducing common Ni- and carbonaceous-based catalysts, CDM over Fe-based catalysts will be emphasized. The stability and catalytic activity of numerous catalysts have been analyzed and compared, comprising the operation conditions, type of reactors, activity, served stability, carbon yield, initial and final methane conversion, and amount of catalyst. The studies showed that hydrogen production with carbonaceous catalysts is less efficient compared to iron-oriented catalysts.43 Nickel and nobel metals may increase methane conversion but are comparatively more costly and less investigated. Some groups have reported iron as an economical catalyst, the cost of iron is about 1/140 with respect to that of nickel.43 Also, iron is considered much stable than nickel catalyst at elevated temperature. This may lead to a comparatively good thermodynamical conversion for a catalytic decomposition of methane (an endothermic process). Iron-based catalysts are an interesting option for catalytic decomposition of methane.
4.1 Supported Fe catalysts
Various researches confirmed a successful carbon decomposition of methane over iron catalysts.44,45 Inert oxides, which favor the catalytic activity of iron, have gained increasing interest46,47 as they showed good stability and high catalytic activity for CDM. Single-oxides (such as Al2O3, MgO, TiO2, CaO, CeO2, SiO2 and ZrO2) are used as catalytic supports for methane decomposition. Ref. 48 reports the use of various oxides supports (Al2O3, CaO, TeO2, TiO2 and MgO) with iron showing that Fe/Al2O3 is the most performing one. By a gas hourly space velocity (GHSV) of 1.875 L per g cat. per h, at 750 °C, 70% conversion of methane was achieved for 400 minutes for 65 wt% Fe/Al2O3. Moreover, infused 20 wt% iron catalysts were also produced with various additives (g-Al2O3, a-Al2O3, MCM41, SiO2/TiO2, SiO2, MgSiO3, zeolite and CeO2/ZrO2) finding that CH4 conversion varies from 2 to 23%. The 20 wt% Fe/g-Al2O3 ratio was considered the best one, with a 23% CH4 conversion. They suggested that Al2O3 support increases the Fe surface area for the selective deposition of carbon nanotubes (CNTs).
The influence of composition and structure of 59.5 wt% iron catalysts on TiO2, Al2O3, ZrO2 and SiO2 on the production and morphology of filamentous carbon formed by CDM was studied at 600–800 °C and GHSV of 48 L per g cat. per h.49 Fe/SiO2 showed the best performances: 45 gC/gFe was produced at 680 °C. Non uniform and random filaments were produced on Fe/TiO2, while thick-walled bamboo-like tubes over Fe/SiO2. The filaments formed over Fe/Al2O3 and Fe/ZrO2 were containing hollow tubes.
Furthermore, common supports of rare or binary inert oxides reinforced catalysts were also studied. Cunha et al.50 measured catalytic decomposition of methane on n wt% La2O3-promoted iron catalyst of Raney type (n ¼ 5, 10, 20, 50) at 600 °C (physical mixtures of La2O3 and Raney Fe). Fe/80Al2O3/20SiO2 catalyst shows a methane conversion profile that quickly inclined in 300 min from 44% to 5%; while the one of Fe/90Al2O3/10SiO2 reduced from 74% to 47%. The increase in SiO2 content decomposition of methane was reducing the pore volume and BET.
Murata et al.50,51 reported the performance of CDM in terms of catalytic stability over Fe/Al2O3 and Fe/MgO/Al2O3 at 800C in the presence of CH4/O2/CO2/N2 ¼ 80/10/5/5; W/F ¼ 41.9 g cat. per h per mol. Conversion for Fe/Al2O3 catalyst was reduced in 6 h from 95% to 79%. Meanwhile, for Fe/MgO/Al2O3 catalyst (Mg/Fe ¼ 1/1 wt. ratio) it remains stable at 95% for CDM for around 6 hours.
4.2 Non-supported iron catalysts
CDM has been presented as an environmentally friendly technology to produce hydrogen free from COx by various researchers nonetheless in opinion of Aparicio et al.52 generation of carbon monoxide in actual catalytic decomposition of methane cannot be ignored and should be taken into account for various reasons: (a) the impurities due to oxygen inside the reaction mixture; (b) the partial reduction of metal oxide (i.e., substantial quantity of CO may be produced by methane reaction with metal oxides in the early phases of the decomposition if the catalysts are not reduced during the deactivation or disintegration step); or (c) reaction of the carbonaceous adsorbed species originated by dissociative chemisorption of methane with surface OH groups (mostly from oxides supports)53,54via a redox mechanism. To eliminate the “O” from oxide supports, the non-supported or bulk Fe catalysts for CDM were investigated by many researchers,55,56 although the supports could help to improve CDM performance. There are several benefits in using non supported catalysts as reported in ref. 57. Firstly, the prevention of CO production due to the chemical reactions occurring between methane and/or deposited nano-carbon and lattice/surface oxygen. Moreover, carbon produced nanomaterials can be simply separated from the catalyst using magnetic field or acid treatments. Ashik et al.58 recently reported methane decomposition over iron NPs produced by co-precipitation treating FeNO3 solution with NH4 (calcination at 350 °C for the 3 hours). The catalyst was active at 595 °C and showed the highest H2 production of 9% which reduced to 2% in a few minutes.
Ref. 58 reported CDM performances of magnetite (Fe3O4) at an operating temperature ranging from 800 to 900 °C and GHSV of 7.5 L per g cat. per h. Fe3O4 was triggered by CH4 reducing at 900 °C for 2 h in comparison with H2O2. CH4 conversion of 98% was achieved, and remained constant for 75 h. Other researchers37 produced non-supported Fe oxides by solution combustion utilizing the fuel in the form of citric acid. After combining a specific quantity of citric acid with iron nitrate solution (corresponding molar ratio of 0.5
:
1.0), the obtained mixture was then slowly evaporated by continuous stirring at ∼80 °C till a paste was formed. Afterward, calcination was done in air at 600 °C for 3 hours to form an iron oxide catalyst. Then the catalyst was reduced in situ at 800 °C for 1 hour utilizing concentrated H2 with a 50 mL min−1 flow rate. Catalyst was assessed for catalytic decomposition of methane at 900 °C and a GHSV of 10.8 L per g cat. per h. The output showed that graphene nano-platelets of few layers were observed at 3.2 gC g cat−1. Zhang et al.59 through a reduction substitution methodology, prepared a non-supported Ni–Fe (with 1
:
1 molar ratio) bimetallic catalyst. After the pre-reduction by H2 at 400 °C, Fe–Ni modified from NiFe2O4 and α-Fe (Ni) to supplement of α-Fe (Ni) and γ-Fe-Ni (Fe0.64Ni0.36) alloy particles. No COx formation and larger catalytic decomposition of methane were observed. This may be a novel method for an iron-oriented catalyst of CDM with a way to eliminate oxygen from ordinary supports or attempt distinct supports with less oxygen like BN and SiC.
4.3 Wasted Fe-based catalysts
Lately, a group investigated a few iron rich wastes for the process of CDM. Iron wastes come from red mud (RM, Fe2O3-30–50 wt%),60 goethite (Fe2O3-51.28 ± 1.49 wt%),61 Fe ore tailings (Fe2O3-26.8 wt%),62 copper flotation waste (Fe2O3-67.68 wt%),63 hematite (Fe2O3-97.3 wt%)64 and residues of nickel-leaching (Fe2O3-38.57 wt%).65 Inside India, almost 18e20 million tons of tailings were generated per annum58 and 3 million tons of red mud66 were produced each year. Around 9 million tons of red mud was formed per year globally. Catalyst from red mud common RM composition was 30 wt%e50 wt% Fe2O3, SiO2 and Al2O3. It also has few other metallic elements like Zr, Mg, V and Cr. The main mineral constituents comprised sodalite, hematite, anatase goethite, quartz, and rutile. Obviously, red mud is a potential source of many valuable metals. Hence, red mud is among the best sources for the catalytic decomposition of methane due to environmental and economic reasons. Fang et al.67 studied the CDM for GHSV of 4.8 L per g cat. per h and over nano-mesoporous modified red mud catalyst at 800 °C. The distribution of modified red mud (MRM) pore size was 3 × 1012 nm, whereas the total pore volumes and surface area were 0.39 cm3 g−1 and 190.61 m2 g−1 correspondingly. A pore structure like a wormhole was also produced, which was positively affecting the performances of catalytic decomposition. The outcomes showed a conversion of methane of 25.99% that was reduced to 20% after 250 min of reaction time. Balakrishnan et al.68 studied carbon oxidation and deposition over RM catalyst in a novel two steps process, formed to transport, store, and utilize the associated petroleum gas (APG) lost in petroleum exploration in offshore platforms (Fig. 1). It was transformed catalytically to H2 and fuel in the form of carbon, with byproducts C deposited around 27 wt%. After the deposition of carbon in the platform, it can be securely transported and simply stored to the shore. Likewise, metal and carbon can be oxidized in controlled environments to produce CO/H2 in the form of steam. Hydrogen fuel produced can be preserved as a hydride or electricity in batteries, Balakrishnan et al.69 investigated the catalytic decomposition of methane over red mud at 800 °C, and GHSV of 7.2 L per g cat. per h with a supreme H2 production speed 3.80 10−5 mol H2 g−1 s−1 over a catalyst comprising 36.7 wt% Fe2O3. Researchers concluded that there is a crucial role of alkali metal content (alkaline metals are famous to be extremely active poisons in decomposition reaction).
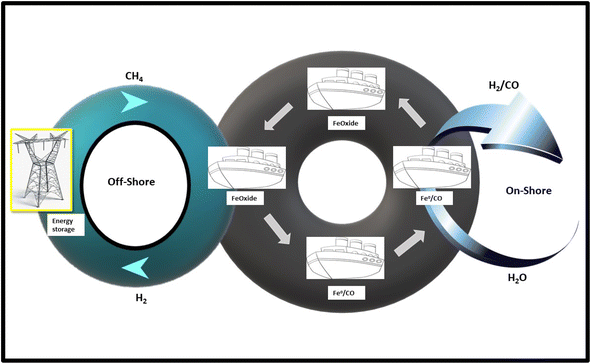 |
| Fig. 1 Flow chart of CDM for the conversion of offshore associated petroleum gas (APG) into hydrogen using the RM as a catalyst. | |
4.4. Iron ochre catalysts
Zhou et al.27 investigated ores of Fe (minerals and ores comprising sufficient amounts of iron oxides in term of hematite (Fe2O3) with some quantity of Al2O3, Na2O and SiO2 impurities) for CDM as a bulk catalyst. After the reduction with 100 mL min−1 H2 at 850 °C for 3.5 h, CH4 decomposition was performed with 100 mL min−1 pure methane (5 bar, 850 °C, and 3.75 L per g cat. per h) in a reactor. This led to a production of hydrogen of 3.2 mol g cat−1, free of COx impurities. The used catalyst sample was characterized as mixtures of Fe3C and graphite carbon with many defects. Alharthi et al.70 observed the catalytic decomposition of methane over Fe ochre achieved from a river in an automated temperature experimentation at a GHSV of 1.4 L per g cat. per h in between 600 and 800 °C. They explained the formation of two valuable products, magnetic and hydrogen carbon containing composites from the two wasted Fe ochre and CH4. Methane is observed as a leftover from the operation of refineries and from landfill dumping. Hydrogen productivity increased with temperature and carbon and graphite bound Fe and/or Fe3C were formed.
4.5. Catalyst regeneration
As great quantities of C are produced the catalysts decrease their reactivity. Various compounds (O2, H2O and CO2) can produce this deactivation.28,52 Wen et al.71 demonstrated that, by in situ injecting a minute quantity of O2 during the decomposition of methane, the growth of amorphous Fe/Mo/MgO catalyst can be observed. Another study52 effectively reused catalysts of 40 wt% Fe/Al2O3 for five cycles by CO2 oxidation. The activation time ranges from 20 to 5 min, and thanks to catalyst regeneration the methane conversion was enhanced from 70% to 75%.
5. Reactor
Designing a reactor plays an important part for the commercialization of CDM. For a methane deposition frequently, used reactors are plasma reactor (PLR), rotary bed reactor (RBR), fixed bed reactor (FBR) and molten melt reactor (MMR).
5.1 Fixed-bed reactorhn
Fixed bed reactor has been utilized widely for catalytic decomposition of methane over Ni, Fe, C and noble metal-based catalyst to evaluate the impact of different parameters such as GHSV, temperature, catalyst preparation, partial pressure and feed composition on conversion of methane and yield of carbon or hydrogen.72–74 FBR was extensively used in the research of carbonaceous catalysts. Lee et al.75 analyzed catalytic decomposition of methane over carbon black in a fixed bed vertical shape height of 45 cm, and 2.8 cm I. D (6.05 cm O. D) carbon flow steel reactor at 1020 and 1170 °C with cyclone and at the bottom a bag-filter. The reaction zone was heated through an electric tube furnace. Carbon steel plates with holes and crakes' wool were applied for supporting the carbon black catalyst. Approximately 100% conversion of methane was achieved at 1170 °C by76 using a fixed bed reactor of three-zone with outstanding temperature uniformity. Tube reactor was coupled with 120 cm height, 6.03 cm O. D, 8.74 cm thickness and stainless-steel tube. The apparent kinetics, catalyst deactivation was calculated with a simple model of catalyst activity for CDM. The deactivation and reaction order were 0.5 and 2 and the experimental data well fitted the simulations.
Few catalysts of metal were also applied to catalytic decomposition of methane. Konieczny et al.45 examined catalytic decomposition of methane in a FBR (length of 45.7 cm and 1.3 cm O. D) with a thermocouple of K-type. They observed 98% methane conversion that lasted for around 75 hours. Pinilla et al.46 investigated Fe-based catalysts in a fixed bed reactor, 1.8 cm I. D and 60 cm height, heated by using an electric furnace, with 93 vol% H2 achieved at 1 L gat−1 h−1 and 900 °C.
5.2. Fluidized bed reactor
Fluidized bed reactors are largely functional for petroleum, metallurgical and chemical industries. In recent years, experimental results77–80 demonstrated that it can be utilized as a quick reactor for CDM eliminating solid particles in the by-products.81 In ref. 82 a model consisting of catalyst and CDM activation and deactivation through the elimination of carbon for CDM in fluidized bed reactors is described. The outcomes of this unique model identify the key parameters for catalyst renewal (temperature, size, types of the catalyst and fluidizing gas velocity) and their optimal values. Łamacz et al.83 studied the catalyst of Ni/CeZrO2 for the very first time utilized in a FLBR (Fig. 2) for catalytic decomposition of methane to produce hydrogen and CNTs.
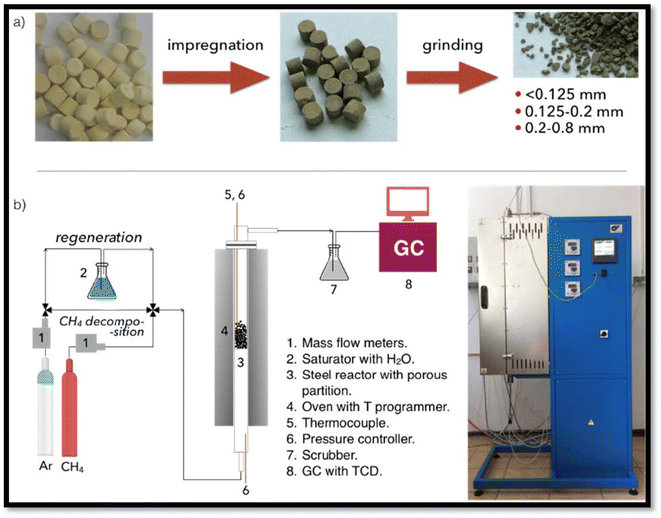 |
| Fig. 2 The scheme of the catalyst preparation (a), and installation used for experiments (b).83 | |
The deactivated catalyst was regenerated in a micro-reactor with 4.15H2O/Ar accompanied by hydrogen. A 93% conversion of methane was accomplished on Ni/CeZrO2 catalyst at 700 °C. Another study84 proved catalytic decomposition of methane in FLBR with Fe-based catalyst. The reactor system was coupled with a fluidized bed made of quartz (50 cm long, 1.85 cm I. D) and heated by a resistive heater. Numerous researches have examined the production of carbon materials in a fluidized bed reactor for hydrogen production in the catalytic decomposition of methane.84 Other researchers85 investigated the catalysts nature based on iron at a temperature between 700 °C and 900 °C in FLBR with height of 8 cm and 6.5 cm I. D. The FLBR was separated into two compartments by a perforated horizontal plate having the holes of 1 mm diameter. A variety of multiwall CNTs and carbon nanofibers (CNFs) with exciting properties related to structure was formed. Ref. 86 presented the capability of internal metal to graphitize CH4 decomposition-based carbon nanofibers, and the formation of carbon nanofibers with different proportions of nickel and silicon in the decomposition of methane over the Ni and Cu dependent catalyst in a fluidized bed reactor. The structural order of the prepared carbon materials gradually improved by increasing the Si/Ni weight ratio in CNFs. Hence, compared with FBR, FLBR is a more promising CDM reactor for large-scale production because it offers sufficient growing space, heat transfer, good mass, and it allows easy handling of solid particles and ongoing removal of carbon formed from the reactor.
5.3 Molten-metal reactor
To overcome the critical issues of catalytic decomposition such as catalyst deactivation or plugging of reactor through carbon deposition, few investigators87,88 studied a unique molten metal reactor for in situ separation of the carbon byproduct from the solid catalysts. In the molten system of this reactor, the insoluble carbon float to the surface where it can be skimmed off. Researchers also investigated molten-melt magnesium as a catalyst for CDM.89 CH4 was decomposed to carbon and hydrogen in a reactor system made of stainless steel. Into the reactor one or two stage reaction may happen due to the fluidity of the molten magnesium, the byproducts of carbon can be transferred away without covering the active part of the catalyst and hence its lifespan was greatly prolonged. Upham et al.89,90 produced a sequence of firm molten metal alloy catalytic for CDM. They also implemented the density functional theory to study different physical parameters of atoms introduced into melts together with their effect on the catalytic activity of the melt itself. The melts were used inside the reactor of molten metal bubble columns where carbon can be continuously removed (Fig. 3). Almost 95% methane transformation was achieved in a 1.1 m bubble column containing molten Ni0.27 Bi0.73 (27 mol% of Ni dissolved in molten Bi) at 1065 °C.
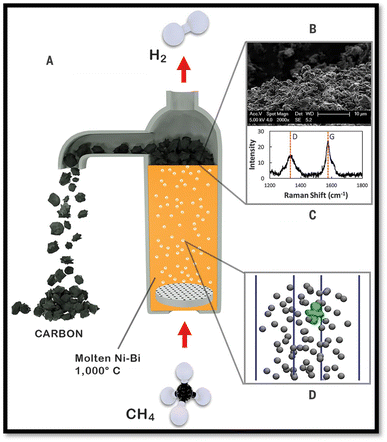 |
| Fig. 3 Hydrogen production with a NieBi molten catalyst. (A) Reactor, (B) SEM of the carbon produced, (C) Raman spectrum of surface carbon, and (D) ab initio molecular dynamics simulation.89 | |
Another research91 proved catalytic methane decomposition inside the reactor made from liquid tin at temperatures around 700 °C to 950 °C and measured the actual kinetic data confirming a kinetic equation for the methane conversion also using other experimental data.92 The outcomes showed that for all the investigated temperatures and the entire methane deposition process, liquid tin had no effect in the catalytic activity; though, the midway products were minimized by the existence of liquid tin. Additionally, most of the methane conversion observed in the bubble column reactor happened in the gas phase section above the liquid phase.
KIT and IASS86 found that conventional methods were inappropriate for large industrial scale uses for CDM as carbon byproducts accumulated in the walls of heated reactor and so blocked the reactors quickly. Hence, they utilized molten tin as a liquid medium and transfer of heat in a reactor of bubble column. Researchers92 looking at the financial side of SRM technology in the catalytic decomposition of methane for large scale manufacturing of CNMs and hydrogen. Zeng et al.92 proved that the conversion of methane with a furnace having electric arc was not in competition with steam reforming of methane without the presence of a carbon tax. Nonetheless, catalytic decomposition of methane could become a competitor with steam reforming of methane without the cost of CO2 in case that the molten metal is active catalytically and attained conversion to near-equilibrium at 1000 °C or lesser. Overall, providing a selective and functional molten metal catalyst in catalytic methane decomposition could be beneficial at skimming the byproduct of carbon from the top of the metal surface in the molten melt reactor.
6. Applications of carbon produced by CDM
The carbon obtained from catalytic decomposition of methane can be divided in CNFs, CNOs and CNTs, whereas the texture, morphology and structure of these C materials largely depend on reaction parameters28 like pressure, catalyst, gas phase composition and temperature. The CNMs chemical and physical properties (pore volume, surface chemistry, pore size and porosity) make them suitable for many applications.8,10,27
Although several carbon materials have been tested, activated carbon catalysts and carbon blacks are the most commonly used carbon supports.93–98 The typically large surface area and high porosity of activated carbon catalysts favor the dispersion of the active phase over the support and increase its resistance to sintering when the quantity of metal loaded is low. The pore size distribution can also be adjusted to suit the requirements of each reaction. The surface chemistry of carbon catalysts also influences their performance as catalyst supports, especially during the synthesis stage. Carbon materials are normally hydrophobic and they usually show a low affinity towards polar solvents, such as water, and a high affinity towards non-polar solvents, such as acetone. Although their hydrophobic nature may affect the dispersion of the active phase over the carbon support, the surface chemistry of carbon materials can easily be modified, for example by oxidation, to increase their hydrophilicity to favor ionic exchange. Apart from an easily tailorable porous structure and surface chemistry, carbon materials have other advantages:93 (i) metals on the support can be easily reduced; (ii) the carbon structure is resistant to acids and bases; (iii) the structure is stable to high temperatures (even above 750 °C); (iv) porous carbon catalysts can be prepared in different physical forms (as granules, cloth, fibers, pellets, etc.); (v) the active phase can be easily recovered; and, (vi) the cost of carbon supports is usually lower than that of conventional supports, such as alumina and silica. Nevertheless, carbon supports have some disadvantages, such as, they can be easily gasified, which makes them difficult to use in hydrogenation and oxidation reactions,96 and their reproducibility can be poor, esp. activated carbon catalysts, since different batches of the same material can have varying ash content. Carbon supported metal catalysts are employed in a number of applications including hydrodesulfurization of petroleum, hydrodenitrogenation, dehydrohalogenation, hydrogenation of CO, hydrogenation of halogenated nitroaromatics compounds and nitrocompounds, hydrogenation of unsaturated fatty acids, hydrogenation of alkenes and alkynes, oxidation of organic compounds and organic pollutants, and for fuel cells.95–97 As well as acting as catalyst supports, carbon materials themselves can be used as catalysts for different heterogeneous reactions.98 A large application of these CNMs would be significant for CDM process industrialization and business interest. Here, we will focus on CNTs, CNOs and CNFs.
6.1 Characteristics of CNTs
Carbon nanotubes show huge thermal99 and electronic conductivity100 and mechanical strength.101 Henceforth, it is not strange that they obtain a huge attraction for important applications like catalysts,130 electrodes,102 fuel cells103 and electrical devices.104 Many researchers105,106 investigated CDM to form carbon nanotubes over iron catalysts. Zhou et al.29 presented a model of carbon deposition (Fig. 4) over Fe catalysts based on DFT. Firstly, methane decomposes to amorphous carbon and hydrogen (Fig. 4a). Fe3C is then produced from the reorganization of iron atoms when the amount of deposited carbon surpasses the limitation of carbon solubility (Fig. 4b and c). The oversaturated deposition of Fe3C produces the amorphous carbon originating from decomposition of methane on graphite (Fig. 4d). Carbon accumulates on the catalyst and crystallizes in a cylindrical network and eventually grows into tubular structures (Fig. 4e). This group studied the morphology of the byproduct carbon nano materials from catalytic decomposition of methane over iron catalysts at 750 °C, finding bamboo-like CNTs.
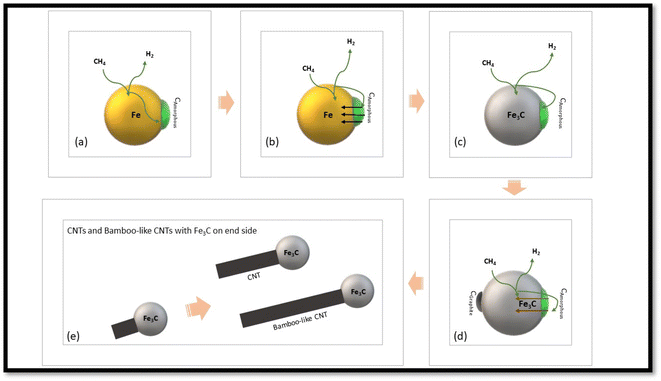 |
| Fig. 4 CNTs formation mechanism over Fe catalyst. Methane decomposition to hydrogen and amorphous carbon (a). Rearrangement of iron atoms (b and c). The supersaturated Fe3C decomposition deposited the amorphous carbon deriving from methane decomposition to graphitic one (d). Carbon deposited out to grew into tubular structures (e). | |
Others107 examined catalytic decomposition of methane to get CNTs and H2 over Al2O3 supporting iron catalysts. A research group57 showed a huge manufacturing of bamboo shaped multi-walled CNT on the nickel/cobalt/iron catalyst and produced carbon nanotubes with an average diameter of ∼20 nm. The results of thermal studies showed that the CNTs exhibited a very good oxidation stability. Avdeeva et al.59 studied the higher shelf-life iron-containing catalysts like Fe/Co/Al2O3 and FeAl2O3 for the decomposition of methane.
6.2 Characteristics of CNFs
Nanofiber technology is the division of nanotechnology that focuses on producing materials in the form of nanoscale fibers in order to obtain better functionalities. The unique combination flexibility, superior directional strength and high specific surface area of these fibers make them ideal materials for clothing and supports for aerospace structures. Decomposition of methane is a novel technology to form CNFs.36,137 CNFs over CNTs formation was selected by Simon et al.108 thanks to the correlation between reaction temperature and structural type of the carbon products on Pd/Al2O3. Herringbone CNFs were obtained at 700 °C, and the inclination angle of the graphene planes was 136°.109 Elevated reaction temperature (750 °C) produces bamboo shaped herringbone CNFs, and the inclination angle was 114. At 800 °C, bamboo-shaped CNFs were rarely achieved; the angle of graphene planes was less than the one at 700 °C and 750 °C. At 850 °C, the lowest number of CNTs/CNFs was obtained; additionally, the inclination angle of CNFs was 24 and CNTs was 0°. Kim et al.110,111 produced nanosheets and metal organic farmwork (MOF) through direct-carbonization for the advancement of batteries and supercapacitors for the diverse nanoarchitecture.
6.3 Characteristics of CNOs
Two different types of CNOs growth techniques were planned by He and co-workers.103 In the vapor-solid mechanism, Ni NPs are produced firstly, and after the graphitic layer carbon adsorption occurs on the surface of catalytic particles. Lastly, CNOs with an encapsulated nickel nanoparticle were found. In another vapor–liquid mechanism, nickel NPs was produced first and after that the entire liquid nickel particle was covered by a graphitic layer. Eventually, a very small liquid nickel particle was produced.
Fakeeha et al.112 showed that CNOs are produced at 700 °C on Fe/Al2O3 catalyst through decomposition of catalytic CH4. Ibrahim et al.113 mentioned that CNOS were obtained over 40% Fe/Al2O3 catalyst at 700 °C by CDM. Zhou et al.53 examined the CDM outcomes over iron ore catalysts.
6.4 Applications of CNMs prepared by the CDM process
Wang et al.114 used Ni/Fe/SiO2 and Fe/Al2O3 catalysts by nitric acid reflux to prepare isolated CNTs with 96% purity. Though most of the samples exhibited a decent dispersion instantly after sonication, in a few hours unprocessed CNTs settled down and in the solvent purified samples continued well-dispersed even after being stored for 60 days. This highlighted the acid purification effect on the dispersibility of CNTs.
Zhou et al.53 achieved CNMs from catalytic methane decomposition on iron ore catalysts at 750 °C, 850 °C, and 900 °C. They correlated the efficacy of formed carbon to commercial PACS on removal of pollutant from wastewater. The outcomes showed that though the CNMs did not show a better removal than commercial PACs, the average removal of three tested micro pollutants were higher than 98%.
Ge et al.115 produced CNMs from catalytic decomposition of methane on stainless steel wire at 800 °C. They concluded that the CNMs in purified form could be utilized as a conductive agent for supercapacitors, which had a maximum cycling stability and high specific capacity.
Utilizing the gas deposition process of the coal-bed, Shanxi Zhongxing Environmental and Energy Technology Co., Ltd116 measured the formation of CNOs. The manufactured CNOs have been effectively applied in supercapacitor and lubricating oil fields. The availability of CNMs from CDM may expand their limit and produce new market opportunities leading to a CNM industry.
7. Conclusion and perspectives
Catalytic decomposition of methane is a one-step procedure to produce COx-free hydrogen and CNMs like CNOs, CNFs and CNTs. This review article presented the cost of total hydrogen production and COx emissions for technologies like MSR, SRM, CDM, water splitting and coal gasification to evaluate their economic impacts and environmentally friendly nature. These evaluations are required to support and promote less greenhouse gasses emissions. The catalytic decomposition of methane would be financially inexpensive with SRM technology together with an extensive recycling of byproducts such as CNMs. Iron, nickel, carbon and noble metal-based catalysts have been broadly and carefully investigated and from the industrial costs point of view, iron-based catalysts, particularly bulk or wasted iron catalysts, were suggested as an effective material for catalytic methane decomposition as it is well studied and less costly compared to the other catalysts and these characteristics make it an ideal candidate.
The primary challenge faced during catalytic decomposition of methane is the separation of deactivated catalysts but to overcome this challenge this process was investigated in different reactors (specially MMR, FLBR and FBR). The MMR exhibited outstanding potentials for commercial applications, as carbon byproducts can be easily separated from the solid catalysts uninterruptedly and this avoids the reactor clogging and catalyst deactivation. Recently, huge cumulative effort has been made to go towards its commercialization, and the influence of different parameters like reactor, catalyst and mechanism has been studied. Yet, numerous challenges must be overcome, the most important are the following: (1) from an environmental and economic point of view, wasted iron-based catalysts for catalytic decomposition of methane would be a highly important challenge to overcome (2) the synthesis of molten-metal catalyst at low temperature would be a great challenge for CDM but researchers are working to use different type of nanocatalyst such as nanocomposites and some other encapsulated structures to tackle these challenges.
Although based on the initial studies, catalytic decomposition of methane is definitely a promising technology. For hydrogen economy its commercialization would be a positive aspect for the future. Many studies have been done on CDM over reactor designing and catalyst preparation, nevertheless further work is needed for its reliable commercialization. Additional research is needed on the catalytic decomposition of methane to make it more practical and scalable. Especially further work and development on molten-metal reactors is required to efficiently remove the byproduct avoiding any catalytic deactivation (Fig. 4). Hopefully, according to the economical evaluation, CDM will become an economical technology on a small or medium industrial scale such as demand-driven onsite H2 and byproduct formation. This in turn will generate new marketing opportunities leading to the foundation of new CNM-based industries and a new era for the emerging sustainable energies.
Conflicts of interest
There is no conflict to declare.
Acknowledgements
We are thankful to MUR PON DM 1061 for funding this study.
References
- N. Abas, A. Kalair and N. Khan, Review of fossil fuels and future energy technologies, Futures, 2015, 69, 31–49 CrossRef.
- G. Nicoletti, N. Arcuri, G. Nicoletti and R. Bruno, A technical and environmental comparison between hydrogen and some fossil fuels, Energy Convers. Manage., 2015, 89, 205–213 CrossRef.
- U. P. M. Ashik, W. M. A. Wan Daud and H. F. Abbas, Production of greenhouse gas free hydrogen by thermocatalytic decomposition of methane-a review, Renew. Sustainable Energy Rev., 2015, 44, 221–256 CrossRef CAS.
- Y. Li, D. Li and G. Wang, Methane decomposition to COx-free hydrogen and nano-carbon material on group 8–10 base metal catalysts: a review, Catal. Today, 2011, 162, 1–48 CrossRef CAS.
- R. Richter and S. Caillol, Fighting global warming: the potential of photocatalysis against CO2, CH4, N2O, CFCs, tropospheric O3, BC and other major contributors to climate change, J. Photochem. Photobiol., C, 2011, 12, 1–19 CrossRef.
- S. Singh, S. Jain, V. Ps, A. K. Tiwari, M. R. Nouni, J. K. Pandey and S. Goel, Hydrogen: a sustainable fuel for future of the transport sector, Renew. Sustainable Energy Rev., 2015, 51, 623–633 CrossRef CAS.
- M. Ball and M. Wietschel, The future of hydrogeneopportunities and challenges, Int. J. Hydrogen Energy, 2009, 34, 615–627 CrossRef CAS.
- A. Rehman and S. J. Park, Tunable nitrogen-doped microporous carbons: delineating the role of optimum pore size for enhanced CO2 adsorption, Chem. Eng. J., 2019, 362, 731–742 CrossRef CAS.
- A. Rehman and S. J. Park, From chitosan to urea-modified carbons: tailoring the ultra-microporosity for enhanced CO2 adsorption, Carbon, 2020, 159, 625–637 CrossRef CAS.
- A. Rehman and S. J. Park, Facile synthesis of nitrogen-enriched microporous carbons derived from imine and benzimidazole-linked polymeric framework for efficient CO2 adsorption, J. CO2 Util., 2017, 21, 503–512 CrossRef CAS.
- F. H. Abbas and W. M. A. W. Daud, Hydrogen production by methane decomposition: a review, Int. J. Hydrogen Energy, 2010, 35, 1160–1190 CrossRef.
- A. Zuttel, Hydrogen storage method, Naturwissenschaften, 2004, 91, 157–172 CrossRef PubMed.
-
T. K. Ghosh and M. A. Prelas, Energy Resources and Systems, Springer, Dordrecht Heidelberg London New York, New York, 2009, vol. 2 Search PubMed.
- A. Settar, S. Abboudi and N. Lebaal, Effect of inert metal foam matrices on hydrogen production intensification of methane steam reforming process in wall-coated reformer, Int. J. Hydrogen Energy, 2018, 43, 12386–12397 CrossRef CAS.
- A. Simpson and A. Lutz, Exergy analysis of hydrogen production via steam methane reforming, Int. J. Hydrogen Energy, 2007, 32, 4811–4820 CrossRef CAS.
- M. Voldsund, K. Jordal and R. Anantharaman, Hydrogen production with CO2 capture, Int. J. Hydrogen Energy, 2016, 41, 4969–4992 CrossRef CAS.
- K. C. Mondal and S. R. Chandran, Evaluation of the economic impact of hydrogen production by methane decomposition with steam reforming of methane process, Int. J. Hydrogen Energy, 2014, 39, 9670–9674 CrossRef CAS.
- L. Weger, A. Abanades and T. Butler, Methane cracking as a bridge technology to the hydrogen economy, Int. J. Hydrogen Energy, 2017, 42, 720–731 CrossRef CAS.
- Y. V. Kaneti, S. Dutta, M. S. A. Hossain, M. J. A. Shiddiky, K. L. Tung, F. K. Shieh, C. K. Tsung, K. C. W. Wu and Y. Yamauchi, Strategies for improving the functionality of zeolitic imidazolate rameworks: tailoring nanoarchitectures for functional applications, Adv. Mater., 2017, 29(38), 1700213 CrossRef PubMed.
- J. Tang, R. R. Salunkhe, H. Zhang, V. Malgras, T. Ahamad, S. M. Alshehri, N. Kobayashi, S. Tominaka, Y. Ide and J. H. Kim, Bimetallic metal–organic frameworks for controlled catalytic graphitization of nanoporous
carbons, Sci. Rep., 2016, 6, 30295 CrossRef CAS PubMed.
- Y. V. Kaneti, J. Zhang, Y. B. He, Z. Wang, S. Tanaka, M. S. A. Hossain, Z. Z. Pan, B. Xiang, Q. H. Yang and Y. Yamauchi, Fabrication of an MOF-derived heteroatom-doped Co/CoO/carbon hybrid with superior sodium storage performance for sodium-ion batteries, J. Mater. Chem., 2017, 5, 15356–15366 RSC.
- A. Azhar, Y. Li, Z. Cai, M. B. Zakaria, M. K. Masud, M. S. A. Hossain, J. Kim, W. Zhang, J. Na and Y. Yamauchi, Nanoarchitectonics: a new materials horizon for prussian blue and its analogues, Bull. Chem. Soc. Jpn., 2019, 92, 875–904 CrossRef CAS.
- H. Tan, J. Tang, J. Henzie, Y. Li, X. Xu, T. Chen, Y. Ide and Y. Bando, Assembly of hollow carbon nanospheres on graphene nanosheets and creation of iron-nitrogen-doped porous carbon for oxygen reduction, ACS Nano, 2018, 12, 5674–5683 CrossRef CAS PubMed.
- M. B. Zakaria, C. Li, Q. Ji, B. Jiang, S. Tominaka, Y. Ide, J. P. Hill, K. Ariga and Y. Yamauchi, Self-construction from 2D to 3D: one pot layer-by-layer assembly of graphene oxide sheets held together by coordination polymers, Angew. Chem., Int. Ed., 2016, 55, 8426–8430 CrossRef CAS PubMed.
- G. Darabdhara, M. A. Amin, G. A. M. Mersal, E. M. Ahmed, M. R. Das, M. Zakaria, V. Malgras, S. M. Alshehri, Y. Yamauchi and S. Szunerits, Reduced graphene oxide nanosheets decorated with Au, Pd and AuePd bimetallic nanoparticles as highly efficient catalysts for electrochemical hydrogen generation, J. Mater. Chem., 2015, 3, 20254–20266 RSC.
- J. X. Qian, T. W. Chen, L. R. Enakonda, D. B. Liu, G. Mignani, J. M. Basset and L. Zhou, Methane decomposition to produce COx-free hydrogen and nano-carbon over metal catalysts: a review, Int. J. Hydrogen Energy, 2020, 45, 7981–8081 CrossRef CAS.
- B. Fidalgo, Carbon materials as catalysts for decomposition and CO2 reforming of methane: a review, Chin. J. Catal., 2011, 32, 207–216 CrossRef CAS.
- H. F. Abbas and W. M. A. W. Daud, Hydrogen production by methane decomposition: a revie, Int. J. Hydrogen Energy, 2010, 35, 1160–1190 CrossRef CAS.
- A. M. Dehkordi, S. Chiya and G. Mohammad, Steam reforming of methane in a tapered membraneeAssisted fluidized-Bed reactor: modeling and simulation, Int. J. Hydrogen Energy, 2011, 36, 490 CrossRef CAS.
- W. Zhou, Y. Ke, P. Pei, W. Yu, X. Chu, S. Lia and K. Yang, Hydrogen production from cylindrical methanol steam reforming microreactor with porous Cu-Al fiber sintered felt, Int. J. Hydrogen Energy, 2018, 43, 3643–3654 CrossRef CAS.
- B. Lee, H. Chae, N. H. Choi, C. Moon and H. Lim, Economic evaluation with sensitivity and profitability analysis for hydrogen production from water electrolysis in Korea, Int. J. Hydrogen Energy, 2017, 42, 6462–6471 CrossRef CAS.
- S. S Seyitoglu, I. Dincer and A. Kilicarslan, Energy and exergy analyses of hydrogen production by coal gasification, Int. J. Hydrogen Energy, 2017, 42, 2592–2600 CrossRef.
- M. Pudukudy, Z. Yaakob, A. Kadier, M. S. Takriff and N. S. M. Hassan, One-pot solegel synthesis of Ni/TiO2 catalysts for methane decomposition into COx free hydrogen and multiwalled carbon nanotubes, Int. J. Hydrogen Energy, 2017, 42, 16495–16513 CrossRef CAS.
- Q. X. Li, X. T. Liu, K. F. Liu, T. F. Zhang and F. H. Kong, Technical and economic analysis for large-scale industrial hydrogen production, Nat. Gas Chem. Ind., 2015, 40, 78–82 CAS.
- W. Zhou, Discussion on economic comparison of hydrogen production by natural gas, methanol and water electrolysis, Nat. Gas Technol. Econ., 2016, 10, 47–49 Search PubMed.
-
China Natinal Institute of Standardization, National Technical Committee for the Standardization of Hydrogen Energy, China Hydrogen Industry Infrastructure Development Blue Book (2018)-implementation Path of Low Carbon and Low-Cost Hydrogen Sources, Beijing, China Quality and Standards Publishing & Media Co.,Ltd, Chinese Specification Press, 2018 Search PubMed.
- R. Bhandari, C. A. Trudewind and P. Zapp, Life cycle assessment of hydrogen production via electrolysise a review, J. Clean Prod., 2014, 85, 151–163 CrossRef CAS.
- C. Acar, I. Dincer and G. F. Naterer, Review of photocatalytic watersplitting methods for sustainable hydrogen production: review: photocatalysis for sustainable hydrogen, Int. J. Energy Res., 2016, 40, 1449–1473 CrossRef CAS.
-
U. P. M. Ashik, W. M. A. W. Daud and H. F. Abbas, Production of Greenhouse Gas Free Hydrogen by Thermocatalytic Decomposition of Methanee A Review, Social Science Electronic Publishing, 2015, vol. 44, pp. 221–256 Search PubMed.
- T. Keipi, H. Tolvanen and J. Konttinen, Economic analysis of hydrogen production by methane thermal decomposition: comparison to competing technologies, Energy Convers. Manage., 2018, 159, 264–273 CrossRef CAS.
-
C. Raston, H. T. Chua, A. Cornejo and L. Gao, Process for Producing Hydrogen from Hydrocarbons, US Pat, US20120258374A1, 2012 Search PubMed.
- B. Qian, Proof the concept of methane decomposition to produce hydrogen free-CO2 in Germany, Nat. Gas Chem. Ind., 2015, 6–45 Search PubMed.
- L. Zhou, L. R. Enakonda, M. Harb, Y. Saih, T. A. Aguilar, C. S. Ould, J. l. Hazemann, J. Li, N. Wei, D. Gary, P. Del-Gallo and J. M. Basset, Fe catalysts for methane decomposition to produce hydrogen and carbon nano materials, Appl. Catal., B, 2017, 208, 44–59 CrossRef CAS.
- D. P. Serrano, J. A. Botas and R. Lopez, H2 production from methane pyrolysis over commercial carbon catalysts: kinetic and deactivation study, Int. J. Hydrogen Energy, 2009, 34, 4488e–4494e CrossRef.
- L. Jin, H. Si, . Zhang, P. Lin, Z. Hu, B. Qiu and H. Hu, Preparation of activated carbon supported FeeAl2O3 catalyst and its application for hydrogen production by catalytic methane decomposition, Int. J. Hydrogen Energy, 2013, 38, 10373–10380 CrossRef CAS.
- J. X. Qian, L. R. Enakonda, W. J. Wang, D. Gary, P. Del-Gallo, J. M. Basset, D. B. Liu and L. Zhou, Optimization of a fluidized bed reactor for methane decomposition over Fe/Al2O3 catalysts: activity and regeneration studies, Int. J. Hydrogen Energy, 2019, 44, 31700–31711 CrossRef CAS.
- D. Torres, J. L. Pinilla, M. J. Ldzaro, R. Moliner and I. Suelues, Hydrogen and multiwall carbon nanotubes production by catalytic decomposition of methane: thermogravimetric analysis and scaling-up of Fe-Mo catalysts, Int. J. Hydrogen Energy, 2014, 39, 3698–3709 CrossRef CAS.
- A. F. Cunha, N. Mahata, J. J. M. Rfao and J. L. Figueiredo, Methane ∼ decomposition on La2O3-promoted raney-type Fe catalysts, Energy Fuels, 2009, 23, 4047–4050 CrossRef CAS.
- A. S. Al-Fatesh, A. A. Ibrahim, A. A. M. Alsharekh, F. S. Alqahtani, S. O. Kasim and A. H. Fakeeha, Iron catalyst for decomposition of methane: influence of Al/Si ratio support, Egpt. J. Petrol., 2018, 27, 1221–1225 CrossRef.
- K. Murata, M. Inaba, M. Saito, I. Takahara and N. Mimura, Improvement of stability of a Fe/Mg/Al2O3 catalyst for the decomposition of methane in the presence of O2/CO2, React. Kinet. Catal. Lett., 2003, 80, 39–44 CrossRef CAS.
- K. Murata, M. Inaba, M. Saito, I. Takahara and N. Mimura, Methane decomposition over iron-based catalysts in the presence of O2 and CO2, J. Jpn. Petrol. Inst., 2003, 46, 196–202 CrossRef CAS.
- P. Ferreira-Aparicio, I. Rodriguez-Ramos and A. Guerrero, Methane interaction with silica and alumina supported metal catalysts, Appl. Catal., A, 1997, 148, 343–356 CrossRef CAS.
- K. Otsuka, H. Ogihara and S. Takenaka, Decomposition of methane over Ni catalysts supported on carbon fibers formed from different hydrocarbons, Carbon, 2003, 41, 223–233 CrossRef CAS.
- M. A. Nieto, J. C. Lazo, A. Romero and J. L. Valverde, Growth of nitrogen-doped filamentous and spherical carbon over unsupported and Y zeolite supported nickel and cobalt catalysts, Chem. Eng. J., 2008, 144, 518–530 CrossRef.
- M. Pudukudy, A. Kadier, Z. Yaakob and M. S. Takriff, Non-oxidative thermocatalytic decomposition of methane into COx free hydrogen and nanocarbon over unsupported porous NiO and Fe2O3 catalysts, Int. J. Hydrogen Energy, 2016, 41, 18509–18521 CrossRef CAS.
- A. C. Lua and H. Y. Wang, Decomposition of methane over unsupported porous nickel and alloy catalyst, Appl. Catal., B, 2013, 132–133 Search PubMed.
- U. P. M. Ashik and W. M. A. W. Daud, Stabilization of Ni, Fe, and Co nanoparticles through modified Stober method to obtain € excellent catalytic performance: preparation, characterization, and catalytic activity for methane decomposition, J. Taiwan Inst. Chem. Eng., 2016, 61, 247–260 CrossRef CAS.
- C. Zhang, J. Li, C. Shi, E. Liu, X. Du, W. Feng and N. Zhao, The efficient synthesis of carbon nano-onions using chemical vapor deposition on an unsupported NiFe alloy catalyst, Carbon, 2011, 49, 1151–1158 CrossRef CAS.
- R. A. Pepper, S. J. Couperthwaite and G. J. Millar, Value adding red mud waste: high performance iron oxide adsorbent for removal of fluoride, J. Environ. Chem. Eng., 2017, 5, 2200–2206 CrossRef CAS.
- R. Kumar, R. Sakthivel, R. Behura, B. K. Mishra and D. Das, Synthesis of magnetite nanoparticles from mineral waste, J. Alloys Compd., 2015, 645, 398–404 CrossRef CAS.
- S. R. Prim, M. V. Folgueras, M. A. de Lima and D. Hotza, Synthesis and characterization of hematite pigment obtained from a steel waste industry, J. Hazard. Mater., 2011, 192, 1307–1313 CrossRef CAS PubMed.
- M. Romero and J. M. Rincon, Microstructural characterization of a goethite waste from zinc hydrometallurgical process, Mater. Lett., 1997, 31(1e2), 67–73 CrossRef CAS.
- S. Coruh, O. N. Ergun and T. W. Cheng, Treatment of copper industry waste and production of sintered glass-ceramic, Waste Manage. Res., 2006, 24, 234–241 CrossRef CAS PubMed.
- M. Romero, M. Kovacova and J. M. Rincon, Effect of particle size on kinetics crystallization of an iron-rich glass, J. Mater. Sci., 2008, 43, 4135–4142 CrossRef CAS.
- K. Jayasankar, P. K. Ray, A. K. Chaubey, A. Padhi, B. K. Satapathy and P. S. Mukherjee, Production of pig iron from red mud waste fines using thermal plasma technology, Int. J. Miner., Metall. Mater., 2012, 19, 679–684 CrossRef CAS.
- X. Fang, Q. Liu, P. Li, H. Li, F. Li and G. Huang, A nanomesoporous catalyst from modified red mud and its application for methane decomposition to hydrogen production, J. Nanomater., 2016, 2016, 1–8 Search PubMed.
- I. F. Teixeira, T. P. V. Medeiros, P. E. Freitas, M. G. Rosmaninho, J. D. Ardisson and R. M. Lago, Carbon deposition and oxidation using the waste red mud: a route to store, transport and use offshore gas lost in petroleum exploration, Fuel, 2014, 124, 7–13 CrossRef CAS.
- M. Balakrishnan, V. S. Batra, J. S. J. Hargreaves, A. Monaghan, I. D. Pulford, J. L. Rico and S. Sushil, Hydrogen production from methane in the presence of red mudemaking mud magnetic, Green Chem., 2009, 11, 42–47 RSC.
- A. Abdulrahman, R. A. Blackley, T. H. Flowers, J. S. Hargreaves, I. D. Pulford, J. Wigzell and W. Zhou, Iron ochre-a pre-catalyst for the cracking of methane, J. Chem. Technol. Biotechnol., 2014, 89, 1317e23 Search PubMed.
- Q. Wen, W. Qian, F. Wei and G. Ning, Oxygen-assisted synthesis of SWNTs from methane decomposition, Nanotechnology, 2007, 18, 1–7 Search PubMed.
- A. J. Carrillo, D. Sastre, L. Zazo, D. P. Serrano, J. M. Coronado and P. Pizarro, Hydrogen production by methane decomposition over MnOx/YSZ catalysts, Int. J. Hydrogen Energy, 2016, 41, 19382–19389 CrossRef CAS.
- S. Abanades, H. Kimura and H. Otsuka, Hydrogen production from thermo-catalytic decomposition of methane using carbon black catalysts in an indirectly-irradiated tubular packed-bed solar reactor, Int. J. Hydrogen Energy, 2014, 39, 18770–18783 CrossRef CAS.
- F. Frusteri, G. Italiano, C. Espro, C. Cannilla and G. Bonura, H2 production by methane decomposition: catalytic and technological aspects, Int. J. Hydrogen Energy, 2012, 37(21), 16367–16374 CrossRef CAS.
- S. C. Lee, H. J. Seo and G. Y. Han, Hydrogen production by catalytic decomposition of methane over carbon black catalyst at high temperatures, Korean J. Chem. Eng., 2013, 30, 1716–1721 CrossRef CAS.
- H. F. Abbas and W. M. A. W. Daud, Hydrogen production by thermocatalytic decomposition of methane using a fixed bed activated carbon in a pilot scale unit: apparent kinetic, deactivation and diffusional limitation studies, Int. J. Hydrogen Energy, 2010, 35, 12268–12276 CrossRef CAS.
- N. Shah, S. Ma, Y. Wang and G. P. Huffman, Semi-continuous hydrogen production from catalytic methane decomposition using a fluidized-bed reactor, Int. J. Hydrogen Energy, 2007, 32, 3315–3319 CrossRef CAS.
- J. L. Pinilla, I. Suelves, M. J. Lazaro, R. Moliner and J. M. Palacios, Parametric study of the decomposition of methane using a NiCu/Al2O3 catalyst in a fluidized bed reactor, Int. J. Hydrogen Energy, 2010, 35, 9801–9809 CrossRef CAS.
- J. Chen, H. Miao, G. Li, Y. Wang and Z. J. Zhu, Production of hydrogen from methane decomposition using nanosized carbon black as catalyst in a fluidized-bed reactor, Int. J. Hydrogen Energy, 2009, 34, 9730–9736 CrossRef CAS.
- A. M. Dunker, S. Kumar and P. A. Mulawa, Production of hydrogen by thermal decomposition of methane in a fluidized-bed reactordeffects of catalyst, temperature, and residence time, Int. J. Hydrogen Energy, 2006, 31, 473–484 CrossRef CAS.
- N. Muradov, F. Smith and M. Paster, Thermocatalytic CO2-free production of hydrogen from hydrocarbon fuels, Proc. Hydrogen Program Rev., 2000, 570, 1–29 Search PubMed.
- P. Ammendola, R. Chirone, G. Ruoppolo, G. Russo and R. Solimene, Some issues in modelling methane catalytic decomposition in fluidized bed reactors, Int. J. Hydrogen Energy, 2008, 33, 2679–2694 CrossRef CAS.
- A. Łamacz and G. Łabojko, CNT and H2 production during CH4 decomposition over Ni/CeZrO2. II. Catalyst performance and its regeneration in a fluidized bed, ChemEngineering, 2019, 3, 2–18 CrossRef.
- H. T. Jang and W. S. Cha, Hydrogen production by the thermocatalytic decomposition of methane in a fluidized bed reactor, Korea J. Chem. Eng., 2007, 24, 374–377 CrossRef CAS.
- G. Allaedini, P. Aminayi and S. M. Tasirin, Methane decomposition for carbon nanotube production: optimization of the reaction parameters using response surface methodology, Chem. Eng. Res. Des., 2016, 112, 163e–174e CrossRef.
- J. L. Pinilla, R. Moliner, I. Suelves, M. J. Lazaro, Y. Echegoyen and J. M. Palacios, Production of hydrogen and carbon nanofibers by thermal decomposition of methane using metal catalysts in a fluidized bed reactor, Int. J. Hydrogen Energy, 2007, 32, 4821–4829 CrossRef CAS.
- D. Torres, S. de Llobet, J. L. Pinilla, M. J. Lazaro, I. Suelves and R. Moliner, Hydrogen production by catalytic decomposition of methane using a Fe-based catalyst in a fluidized bed reactor, J. Nat. Gas Chem., 2012, 21, 367–373 CrossRef CAS.
- I. Camean, A. B. Garcĺa, I. Suelves, J. L. Pinilla, M. J. Lazaro, R. Moliner and J. N. Rouzaud, Influence of the inherent metal species on the graphitization of methane-based carbon nanofiber, Carbon, 2012, 50, 5387–5394 CrossRef CAS.
- K. Wang, W. S. Li and X. P. Zhou, Hydrogen generation by direct decomposition of hydrocarbons over molten magnesium, J. Mol. Catal. A: Chem., 2008, 283, 153–157 CrossRef CAS.
- D. C. Upham, V. Agarwal, A. Khechfe, Z. R. Snodgrass, M. J. Gordon, H. Metiu and E. W. McFarland, Catalytic molten metals for the direct conversion of methane to hydrogen and separable carbon, Science, 2017, 358, 917–921 CrossRef CAS PubMed.
- M. Plevan, T. Geißler, A. Abanades, K. Mehravaran, R. K. Rathnam, C. Rubbia, D. Salmieri, L. Stoppel, S. Stuckrad and T. Wetzel, Thermal cracking of methane in a liquid metal bubble column reactor: experiments and kinetic analysis, Int. J. Hydrogen Energy, 2015, 40, 8020–8033 CrossRef CAS.
- B. Parkinson, J. W. Matthews, T. B. McConnaughy, D. C. Upham and E. W. McFarland, Techno-economic analysis of methane pyrolysis in molten metals: decarbonizing Natural Gas, Chem. Eng. Technol., 2017, 40, 1022–1030 CrossRef CAS.
- X. Zeng, S. Yu, L. Ye, M. Li, Z. Pan, R. Sun and J. Xu, Encapsulating carbon nanotubes with SiO2: a strategy for applying them in polymer nanocomposites with high mechanical strength and electrical insulation, J. Mater. Chem. C, 2014, 3, 187–195 RSC.
-
L. R. Radovic and F. Rodríguez-Reinoso, Carbon Materials in Catalysis, Marcel Dekker, New York, 1997, vol. 25, p. 312 Search PubMed.
- N. Muradov, F. Smith and T. J. Ali, Catalytic activity of carbons for methane decomposition reaction, Catal. Today, 2005, 225–233 CrossRef.
- F. Rodriguez-Reinoso, The role of carbon materials in heterogeneous catalysis, Carbon, 1998, 159–175 CrossRef CAS.
- F. Stüber, J. Font, A. Fortuny, C. Bengoa, A. Eftaxias and A. Fabregat, Carbon materials and catalytic wet air oxidation of organic pollutants in wastewater, Top. Catal., 2005, 33, 3–50 CrossRef.
- E. Auer, A. Freund, J. Pietsch and T. Tacke, Carbons as supports for industrial precious metal catalysts, Appl. Catal., A, 1998, 173(2), 259–271 CrossRef CAS.
- F. Carrasco-Marín, A. Mueden and C. Moreno-Castilla, Surface-treated activated carbons as catalysts for the dehydration and dehydrogenation reactions of ethanol, J. Phys. Chem. B, 1998, 102(46), 9239–9244 CrossRef.
- S. N. Kim, J. F. Rusling and F. Papadimitrakopoulos, Carbon nanotubes for electronic and electrochemical detection of biomolecules, Adv. Mater., 2010, 19, 3214–3228 CrossRef PubMed.
- X. Zhang, R. Wen, Z. Huang, T. Chao, Y. Huang, Y. Liu, M. Fang, X. Wu, M. Xin and Y. Xu, Enhancement of thermal conductivity by the introduction of carbon nanotubes as a filler in paraffin/expanded perlite form-stable phase-change materials, Energy Build., 2017, 149, 463–470 CrossRef.
- A. N. Golikand, A. Mehdi and L. Elaheh, Study of oxygen reduction reaction kinetics on multi-walled carbon nano-tubes supported PtePd catalysts under various conditions, Int. J. Hydrogen Energy, 2011, 36, 13317–13324 CrossRef CAS.
- W. He, P. H. Xue, H. T. Du, L. P. Xu and M. L. Pang, A facile method prepared nitrogen and boron doped carbon nano-tube based catalysts for oxygen reduction, Int. J. Hydrogen Energy, 2017, 42, 4123–4132 CrossRef CAS.
- P. Yan, J. Xu, X. Zhang, C. Wu, Y. Gu and R. Zhang, Fabrication and enhanced supercapacitive performance of graphene/nanocarbide derived carbon composites, Int. J. Hydrogen Energy, 2016, 41, 14820–14829 CrossRef CAS.
- F. Kadirgan, A. M. Kannan, T. Atilan, S. Beyhan, S. S. Ozenler, S. Suzer and A. Yoeruer, Carbon supported nano-sized Pt-Pd and Pt-Co electrocatalysts for proton exchange membrane fuel cells, Int. J. Hydrogen Energy, 2010, 34, 9450–9460 CrossRef.
- A. H. Fakeeha, A. A. Ibrahim, M. A. Naeem, W. U. Khan, A. E. Abasaeed, R. L. Alotaibi and A. S. Al-Fatesh, Methane decomposition over Fe supported catalysts for hydrogen and nano carbon yield, Catal. Sustainable Energy, 2015, 2, 71–82 CAS.
- A. H. Fakeeha, A. A. Ibrahim, W. U. Khan, K. Seshan, R. L. Al Otaibi and A. S. Al-Fatesh, Hydrogen production via catalytic methane decomposition over alumina supported iron catalyst, Arabian J. Chem., 2018, 11, 405–414 CrossRef CAS.
- J. Sarada Prasad, V. Dhand, V. Himabindu and Y. Anjaneyulu, Production of hydrogen and carbon nanofibers through the decomposition of methane over activated carbon supported Ni catalysts, Int. J. Hydrogen Energy, 2011, 36, 11702–11711 CrossRef CAS.
- N. Bayat, M. Rezaei and F. Meshkani, Hydrogen and carbon nanofibers synthesis by methane decomposition over NiPd/Al2O3 catalyst, Int. J. Hydrogen Energy, 2016, 41(12), 5494–5503 CrossRef CAS.
- A. Simon, M. Seyring, S. Kamnitz, H. Richter and U. Ritter, Carbon nanotubes and carbon nanofibers fabricated on tubular porous Al2O3 substrates, Carbon, 2015, 90, 25–33 CrossRef CAS.
- M. Kim, R. Xin, J. Earnshaw, J. Tang, J. P. Hill, A. Ashok, A. K. Nanjundan, J. Kim and C. Young, MOF-derived nanoporous carbons with diverse tunable nanoarchitectures, Nat. Protoc., 2022, 2990–3027 CrossRef CAS PubMed.
- M. Kim, L. Ma, Z. Li, W. Mai, N. Amiralian, A. E. Rowan, Y. Yamauchi, A. Qin, R. A. Afzal, D. Martin and A. K. Nanjundan, N and S co-doped nanosheet-like porous carbon derived from sorghum biomass: mechanical nanoarchitecturing for upgraded potassium ion batteries, J. Mater. Chem. A, 2023, 11(31), 16626–16635 RSC.
- C. He, N. Zhao, C. Shi, X. Du and J. Li, Carbon nanotubes and onions from methane decomposition using Ni/Al catalysts, Mater. Chem. Phys., 2006, 97, 109–115 CrossRef CAS.
- A. A. Ibrahim, A. H. Fakeeha, A. S. Al-Fatesh, A. Abasaeed and W. U. Khan, Methane decomposition over iron catalyst for hydrogen production, Int. J. Hydrogen Energy, 2015, 40, 7593–7600 CrossRef CAS.
- I. W. Wang, D. A. Kutteri, B. Gao, H. Tian and J. Hu, Methane pyrolysis for carbon nanotubes and COx-free H2 over transition-metal catalysts, Energy Fuels, 2018, 33, 197–205 CrossRef.
- K. Ge, W. Z. Zhu, W. K. Zhang, C. Jiao and H. Y. Yang, Preparation of carbon nano onions and their application in supercapacitor, N. Chem. Mater., 2018, 46, 224–227 Search PubMed.
- B. Z. Qian, Shanxi has broken through the technology of catalytic cracking of coal bed methane to prepare nanocarbon materials, Aging Appl. Synth. Mater., 2015, 44, 129–130 Search PubMed.
Footnote |
† Hydrogen manufacturing of membrane produced from polymer electrolyte membrane up to 100 N m h−3; alkaline electrolyzers up to 1000 N m3 h−1. |
|
This journal is © The Royal Society of Chemistry 2024 |
Click here to see how this site uses Cookies. View our privacy policy here.