DOI:
10.1039/D4RA02297A
(Paper)
RSC Adv., 2024,
14, 18073-18079
Green processing via surface diffuse atmospheric plasma to enhance the dyeing performance on polylactic acid fabric†
Received
26th March 2024
, Accepted 23rd May 2024
First published on 5th June 2024
Abstract
Poor dyeing performance has been a major defect of polylactic acid (PLA) fibers, which is caused by the lack of active chemical groups in PLA, and hinders the widespread use of this biodegradable material. Most of the existing chemical modification methods are not environmentally friendly and produce effluents. Herein, we report a green, efficient and continuous method to process PLA fibers via surface diffuse atmospheric plasma for the improvement of its hydrophilicity and dyeing performance. PLA fibers were processed via atmospheric plasma for grafting oxygen-containing functional groups, such as carboxyl, to achieve hydrophilicity and, meanwhile, strengthen the binding interactions with various dye molecules via covalent bonds, ionic bonds, or hydrogen bonds. In addition, different mechanisms of improving the dyeing performance on plasma-modified PLA fibers with different kinds of dyes have been discussed. This approach of material modification involves no chemical additives and has high processing efficiency, showing the potential applicability of green treatment to products in various fields.
1. Introduction
With the increasing interest in green ecology, degradable plastics and fibers have been widely regarded for research and usage.1,2 As one of the most promising materials, polylactic acid (PLA) is produced from renewable resources such as crop straws and is biodegradable, thus reducing the burden on the environment.3 Moreover, PLA can be processed into various forms of materials, such as films or fibers.4,5 Compared with common textiles, PLA fibers have the merits of a soft and smooth texture together with high value and sustainability.6–8 In the process of textile application, dyeing should meet practical needs, such as decoration and identification. However, compared with cellulose fibers with active groups such as hydroxyls, PLA fiber chains are composed of ester and methyl groups without hydrophilic and active functional groups.9,10 Therefore, PLA fibers are hydrophobic and difficult to bind with common dye molecules to achieve good dyeing performance.11
As a common pretreatment step for textiles, active groups can be grafted on fibers by adding chemicals, such as cationic reagents, to improve hydrophilicity and enhance the binding with dye molecules.12 However, the main chain of PLA molecules could be damaged by extreme conditions such as strong alkali or high temperatures, resulting in the reduction of mechanical properties and comfort.13,14 In addition, chemical pretreatment would produce a large amount of wastewater, which is not in agreement with green chemistry principles.15 In recent years, plasma, as a material processing technology, has been widely applied in the surface modification of various materials.16,17 Plasma is rich in high-energy species such as electrons, ions, and free radicals, which can graft functional groups onto the surface of materials without damaging their interior.18 There have been a variety of studies on using plasma to treat textile fibers, such as cotton, linen, and polyester, to enhance hydrophilicity or dyeing performance.19,20 However, few studies have reported on the enhanced dyeing performance of plasma-treated PLA fibers. Moreover, for the actual dyeing requirements of the continuous treating process, common plasma processing methods with closed chambers or small area jets are not feasible.21,22 As a new type of plasma, surface diffuse atmospheric plasma (SDAP) generated at atmospheric pressure can be applied to the surface hydrophilic treatment of various materials.23–25 With oxygen in the air as the source of active species, SDAP can graft oxygen-containing functional groups on the surface of materials, which makes it possible to apply this kind of plasma to the pretreatment of PLA fibers in order to achieve the modification grafted with active groups.
Herein, we propose a green, efficient, and continuous method to modify polylactic acid fibers by surface diffuse atmospheric plasma for the improvement of the hydrophilicity and dyeing performance. SDAP, with oxygen in air as the main source of active species, can graft oxygen-containing functional groups such as carboxyl onto the surface of PLA fibers. The plasma-modified PLA fibers can achieve hydrophilicity and strengthen the binding effect with various dye molecules such as cationic red, reactive blue and disperse red dyes, resulting in the improvement of the color intensity and fastness. This approach has the merits of fast response, no chemical addition and efficient continuity, exhibiting the potential applicability of the green treatment to materials in various fields.
2. Experimental
2.1 Materials
Polylactic acid (PLA) fabrics were obtained from Tongjieliang Biomaterials Co., Ltd, Anhui, China. Four kinds of dyes (Reactive Blue 21, Acid Orange 7, Astrazon Brilliant Red 4G, Disperse Red 3B) were obtained from Gutian Chemical Co., Ltd, Nanjing, China. Deionized water with a resistance of 18.2 MΩ was obtained from a Milli-Q instrument (Millipore 0.22 μm). Sodium sulfate, sodium carbonate and glacial acetic acid were obtained from InnoChem Chemical Reagents, China.
2.2 Plasma processing
The surface diffuse atmospheric plasma (SDAP) device was the same as that applied in the previous study.25 In brief, it contained two systems of parallel strip-like electrodes fixed in an alumina ceramic wafer with about 0.4 mm thickness. The device was powered by an AC power supply with about 10 kV and 20 kHz power. PLA fibers were attached to the surface of SDAP to be well modified.
2.3 Dyeing
Generally, about 1.5 g PLA fibers, treated or untreated by SDAP, were used during the dyeing process. For Reactive Blue 21, PLA fibers were stirred in a solution (100 g deionized water, 0.15 g dye, 0.2 g sodium carbonate and 0.5 g sodium carbonate) for 1 h at 60 °C. For Acid Orange 7 and Astrazon Brilliant Red 4G, PLA fibers were stirred in the solution (100 g deionized water, 0.15 g dye and 0.5 g sodium carbonate) for 1 h at 80 °C. For Disperse Red 3B, PLA fibers were stirred in the solution (100 g deionized water, 0.15 g dye and 0.1 g glacial acetic acid) for 1 h at 80 °C. After dyeing, PLA fibers were washed until the filtrate was colorless, then dried for later use.
2.4 Color fastness test
Washing and soaping color fastness were tested by a washing fastness tester. About 0.5 g dyed PLA fibers were stirred intensely in a solution (300 g deionized water, 1.5 g soap flake and 0.6 g sodium carbonate) for 0.5 h at 40 °C in the machine. The rubbing color fastness was tested by a rubbing fastness tester. The wet or dry dyed PLA fibers were rubbed back and forth 10 times by a white standard cloth in the machine.
2.5 Instrument and characterization
Contact angles were measured by a contact angle system (Data-Physics OCA20, Germany). The scanning electron microscopy (SEM) images were obtained by a field emission scanning electron microscope (HITACHI SU8010, Japan). Atomic force microscopy (AFM) images were obtained using an atomic force microscope (Dimension FastscanBio, USA). X-ray photoelectron spectra (XPS) were acquired with a K-Alpha spectrometer (Thermo Scientific). Fourier transform infrared (FTIR) spectra were collected by a FTIR instrument (Excalibur 3100). The color strength was tested by a spectrophotometer (X-Rite Ci4200). The washing color fastness was tested by a washing fastness tester (A104E-8, China). The rubbing color fastness was tested by a rubbing fastness tester (A101A, China). The microscopic images were obtained by a metallographic microscope (Nikon Eclipse LV100ND).
3. Results and discussion
3.1 Modification process by SDAP
Fig. 1 demonstrates that PLA fibers were treated by surface diffuse atmospheric plasma (SDAP) to improve the hydrophilicity with no burning of the material. The construction of the SDAP device is shown in Fig. 1a. Since SDAP generates in air, which is rich in oxygen, PLA fibers would be grafted with oxygen-containing functional groups to become hydrophilic when placed in the plasma discharging region. As shown in Fig. 1b and c, the state of a dyed water droplet placed on PLA fibers changed from non-wetting to wetting after plasma treatment. Meanwhile, there was no burning or any damage on the treated PLA fibers, according to the optical and microscopic images, because the discharge of SDAP was homogeneous and mild with a relatively low temperature. The working condition of SDAP is shown in Fig. 1d. Based on the mechanism of coplanar dielectric barrier discharge, SDAP is a thin layer of plasma on the ceramic surface, which has macro-uniformity and high energy density. Therefore, materials can be successfully treated and modified by SDAP in a short time. This method is environment-friendly so that no chemical is added and no waste water is produced during the process. As shown in Fig. 1e, PLA fibers became superhydrophilic after plasma treatment for 2 seconds, and water droplets could be completely absorbed within 0.6 seconds (Fig. S1†). Moreover, the superhydrophilicity of plasma-modified PLA fibers can be maintained for a week under room conditions, which reveals certain sustainability (Fig. S2†). Compared with other relevant reports on PLA fibers treatment, such as enzyme or alkali soaking, plasma treatment in vacuum or noble gas, this method has the merits of green, efficient, and continuous (Fig. 1f).11,26–28
 |
| Fig. 1 Improvement of the hydrophilicity on polylactic acid (PLA) fibers under SDAP treatment. (a) Schematic diagram of the SDAP treatment process on PLA fibers. (b) and (c) Optical and microscopic images of PLA fibers before and after SDAP treatment. (d) Discharging condition and advantages of the SDAP processing equipment. (e) Varieties of water contact angles on modified PLA fibers with plasma processing time. Insets are images of water contact angle. (f) The merits of SDAP treatment compared with the methods in relevant reports.11,26–28 | |
3.2 Surface morphology and chemical characterization
In order to explore the mechanism of SDAP treatment, scanning electron microscopy (SEM) and atomic force microscopy (AFM) characterizations were performed to analyze the surface morphology of PLA fibers. P0, P10, P30, and P60 refer to SDAP-modified PLA fibers for 0, 10, 30, and 60 seconds, respectively. As shown in Fig. 2a and b, the surface of original PLA fibers (marked as P0) was relatively smooth with few nanostructures, resulting from the manufacturing process. After plasma treatment for 10 s, micro/nano composite structures were generated on the surface of PLA fibers, and the roughness increased, which was in contrast to the untreated sample. The change in the surface morphology was attributed to the etching process by the high energy species in the plasma working region and grafting process on the surface. With the increase in the plasma processing time, the micro/nano composite structures and roughness of the PLA fiber surface further increased (marked as P10, P30, P60) due to the accumulation of plasma etching and grafting process.
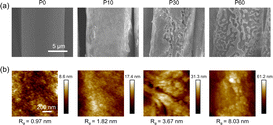 |
| Fig. 2 Surface characterization of PLA fibers after different time periods of plasma treatment. P0, P10, P30, and P60 refers to the plasma treatment for 0, 10, 30, and 60 seconds, respectively. (a) and (b) SEM and AFM images of PLA fibers after plasma treatment for different time. Micro-/nano-composite structures emerged and the roughness increased as the SDAP treatment proceeded. | |
Since SDAP is generated in the atmosphere rich in oxygen, the grafting of oxygen-rich species onto the PLA fiber surface is certain. X-ray photoelectron spectroscopy (XPS) was characterized to explore the surface chemical composition of the PLA fibers before and after plasma treatment. As shown in Fig. 3a–e and Table 1, high-resolution C 1s peaks fitting was carried out to study the change in the surface chemical functional groups. The C 1s peaks were deconvoluted into three peaks: C–C at 284.8 eV, C–O at 286.7 eV, and O–C
O at 288.8 eV.29 In Fig. 3a, the three peaks of untreated PLA were attributed to the chemical structure of polylactic acid itself. With the increase in the plasma processing time, the relative area of peaks referred to as C–O and C
O gradually increased (Fig. 3b–d and Table 1). XPS results demonstrated that oxygen-containing functional groups such as hydroxyl group and carboxyl group were formed on the surface of PLA fibers, which could be explained by the further progress of plasma modification and grafting process.
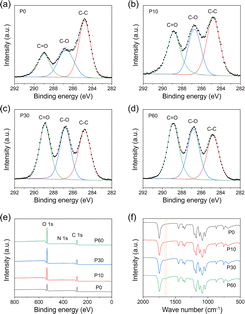 |
| Fig. 3 Surface elements analysis of PLA fibers before and after plasma treatment. (a–e) XPS spectra and peak-fitted high-resolution C 1s spectra of PLA fibers when the plasma processing time was 0, 10, 30, and 60 seconds (P0, P10, P30, and P60, respectively). The relative content of oxygen-containing species on PLA fibers surface increased after plasma treatment. (f) Infrared spectra of PLA fibers after different time periods of plasma treatment. | |
Table 1 Relative contents of the elements and deconvolution analysis of C 1s peaks of PLA fibers after different time points of plasma treatment
|
C 1s (%) |
O 1s (%) |
N 1s (%) |
O/C |
C–C |
C–O |
O–C O |
0 s |
68.79 |
31.21 |
0 |
0.454 |
48.46 |
29.94 |
21.60 |
10 s |
58.86 |
40.74 |
0.39 |
0.692 |
39.34 |
30.10 |
30.56 |
30 s |
56.53 |
42.55 |
0.92 |
0.753 |
33.73 |
32.59 |
33.68 |
60 s |
55.43 |
43.22 |
1.35 |
0.780 |
30.51 |
33.30 |
36.19 |
Besides the increasing relative content of oxygen, as shown in Fig. 3e and Table 1, a small amount of nitrogen was gradually grafted onto the surface of PLA fibers as the plasma treatment process progressed, which could be attributed to the large amount of nitrogen in the air that also served as a source of atmospheric plasma active species. High-resolution N 1s peak fitting was carried out in Fig. S3.† The XPS results showed that nitrate species at about 407.3 eV was detected when the plasma treatment time was 10 seconds.30 It could be explained by the oxidation of nitrogen and the formation of etching fragments under the effect of plasma. In addition, a weaker peak at about 400.5 eV, which belongs to amide, gradually appeared and became stronger (Fig. S3†), indicating the formation of amide bonds during the plasma treatment.31 This might be attributed to the insertion of nitrogen-containing species into the ester group of the PLA polymer. The formation of new groups was further characterized by Fourier transform infrared (FTIR) spectroscopy. Besides the characteristic peak of PLA molecule referred to the ester group (C
O) at about 1750 cm−1; with the increase in the plasma processing time, a small peak was found to gradually increase at around 1648 cm−1 (Fig. 3f),32 which corresponded to the gradual formation of amide bonds shown in the XPS data (Fig. 3e, S3† and Table 1).
As previously mentioned, SDAP, which uses air as the discharge medium, contains a large number of active species such as oxygen and nitrogen free radicals, ions, and electrons. When the plasma was applied to the surface of PLA fibers, many free radicals would be generated on the surface, which could be chosen as the sites for the reaction and grafting process. Meanwhile, the etching and fragment generated during the process could increase the roughness of the fiber surface and generate micro/nano composite structures. Compared with the original untreated PLA fibers, the formation of surface roughness and grafting of oxygen-containing functional groups could promote the diffusion and combination of dyes. In the next part, the dyeing performance enhancement of PLA fibers after plasma treatment would be described.
3.3 Enhanced dyeing performance
The dyeing performance of the PLA fibers before and after plasma treatment is demonstrated in Fig. 4. In this work, cationic dyes, reactive dyes, acid dyes and disperse dyes were selected for specific discussion. It is worth noting that for each type of dye, there might be a small number of dye molecules that do not meet the characteristics of the corresponding category of dyes. Therefore, the representative molecules of four kinds of dyes were selected for PLA fiber dyeing process: Astrazon Brilliant Red 4G (cationic red), Reactive Blue 21 (reactive blue), Acid Orange 7 (acid orange), and Disperse Red 3B (disperse red). Fig. 4a–d shows the dyeing results and the data of soaping color fastness of PLA fibers on the four dyes before and after plasma treatment. The color strength (K/S) is given by the following equation
where K is the absorption coefficient, S is the scattering coefficient, and R is the reflectance of the sample (Fig. S4†).
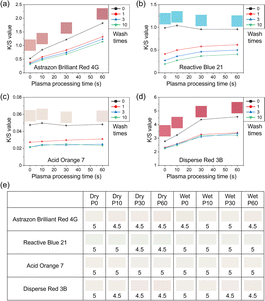 |
| Fig. 4 Dyeing performance and color fastness of PLA fibers before and after plasma treatment. (a–d) The color strength and soaping color fastness of plasma modified PLA fibers dyed by four kinds of dye. Astrazon Brilliant Red 4G for (a), Reactive Blue 21 for (b), Acid Orange 7 for (c) and Disperse Red 3B for (d). (e) The rubbing color fastness in dry and wet conditions of plasma modified PLA fibers dyed by four kinds of dye. | |
As shown in Fig. 4a, with the increase in the plasma processing time, the dyeing performance of cationic red increased significantly, and the color strength increased by more than three times at a processing time of 60 seconds. Even after soap washing for 10 times, the color fastness was still maintained with the color strength higher than that of the untreated PLA fibers. For reactive blue dye (Fig. 4b), there was no significant correlation between the dyeing performance and plasma processing time before soap washing. After the color on the surface was removed by soap washing, the color strength was slightly positively correlated with the plasma processing time, which indicated that the dyeing performance and soaping color fastness of reactive blue dye were improved after plasma treatment. However, for acid orange dye (Fig. 4c), there was no obvious dyeing enhancement performance after plasma treatment, and the dyeing color strength was low with a poor dyeing performance. In this work, the dyeing performance of disperse dye on PLA fibers before and after plasma treatment was also studied. As shown in Fig. 4d, with the increase in the plasma processing time, the color strength of disperse dye increased gradually. At the same time, after soap washing to remove color on the surface, PLA fibers still maintained a certain color strength, showing good soaping color fastness. Fig. S5† shows the actual effect images of PLA fibers dyed by four dyes at different plasma processing times. According to the color strength value mentioned in Fig. 4a–d, specific color block corresponding to each point is shown in Fig. S6,† in order to demonstrate more specific results of plasma treatment in the enhancement of the dyeing strength. Besides soaping color fastness, rubbing color fastness was also studied. For the four dyes after 10 friction cycles, no matter in the dry or wet state, the rubbing fastness of the plasma-modified PLA fibers did not decrease significantly compared with the untreated part (Fig. 4e). In summary, after SDAP modification, the dyeing performance of PLA fibers could be significantly improved for cationic red dye and disperse red dye and slightly improved for reactive blue dye, without a decrease in the rubbing color fastness.
To explain the difference in the dyeing results of plasma-modified PLA fibers to the four kinds of dyes, as described above, the possible mechanism is illustrated in Fig. 5. Since SDAP is rich in reactive oxygen species with high energy, the plasma-modified PLA fibers would be grafted with oxygen-containing functional groups such as carboxyl and hydroxyl groups (Fig. 5a). After plasma treatment, the large number of carboxyl groups grafted on the fibers surface would dissociate into negatively charged carboxyl ions in water, which would affect the subsequent dyeing process. The chemical structural formula of the four dyes studied in this work are shown in Fig. 5b.
 |
| Fig. 5 Mechanism of enhancing dyeing performance on PLA fibers by plasma treatment. (a) Negatively charged groups were grafted on PLA fibers after plasma treatment. (b) Chemical structural formula of the four kinds of dyes used in this work. (c–f) Binding mechanism between the plasma-modified PLA fibers and four kinds of dyes. Astrazon Brilliant Red 4G for (c), Reactive Blue 21 for (d), Acid Orange 7 for (e) and Disperse Red 3B for (f). | |
As for the dyeing process, the dye molecule of cationic red could generate positively charged chemical groups in water, which are attracted to negatively charged carboxylate group widely distributed on the plasma-modified PLA fibers and form a strong ionic bond, resulting in the enhancement of the dyeing strength and color fastness (Fig. 5c). Reactive dyes are often used for dyeing cellulose such as cotton because they can chemically bind to the hydroxyl group on the surface.33 Compared with the original PLA fibers with no chemical reaction site, a small number of hydroxyl groups grafted on the plasma-modified PLA fibers surface would act as the reaction sites to bind with reactive blue dye molecule and improve the color fastness. However, the negatively charged groups in reactive blue dye molecule repel the negatively charged carboxylate groups in the plasma-modified PLA fibers during the dyeing process, resulting in difficulty in dyeing and decrease in the dyeing strength (Fig. 5d). Similar to reactive blue dye, acid orange dye molecule would also generate negatively charged groups in water, leading to repulsive interaction with the plasma modified PLA fibers and difficulty in dyeing. Furthermore, acid orange dye molecule does not have chemical groups that could bind to the plasma-modified PLA fibers like reactive blue dye does, resulting in poor dyeing performance (Fig. 5e). Disperse dyes are often chosen to dye synthetic fibers such as polyester, which have no special active group sites. Interactions such as hydrogen bonds allow the dye molecules to bind with the fibers.34 Similarly, the PLA fibers contain a large number of ester groups that can connect with disperse red dye molecules in the form of hydrogen bonds. After plasma treatment, the grafted groups such as carboxyl and hydroxyl on PLA fibers allow the dye molecules to bind more strongly (Fig. 5f). To be specific, the hydroxyl group could form additional hydrogen bonds with disperse red dye molecule, while the carboxyl group could form covalent or ionic bonds with the amino group, which further improved the dyeing performance and color fastness. Fig. S7† shows the schematic diagram of binding between the four dyes and original PLA fibers, whose poor dyeing performance is attributed to the lack of active sites. In summary, after plasma treatment, the grafted active groups such as the carboxyl group enhanced the ionic bond with the cationic dyes, the covalent bond with the reactive dyes, and various interactions with disperse dyes such as covalent, ionic, and hydrogen bonding. Therefore, the dyeing performance and color fastness of the plasma-modified PLA fibers were improved. In addition, the method of modifying fibers with SDAP and the binding mechanism of the dye molecules proposed in this work should provide deep insights into the functionalization of various textiles in the future.
4. Conclusions
In conclusion, we reported a method of modifying PLA fibers by surface diffuse atmospheric plasma to improve the hydrophilicity and followed dyeing performance for various categories of dyes. The SEM and AFM results demonstrated that micro/nano composite structures appeared on the surface of PLA fibers after plasma treatment. The XPS results showed that oxygen-containing species such as carboxyl groups would be gradually grafted onto the surface of PLA fibers via plasma treatment, which would facilitate the subsequent dyeing process. By measuring the color strength, the plasma-modified PLA fibers showed obvious dyeing performance enhancement for cationic red and disperse red dyes and slight enhancement for reactive blue dye. This is attributed to the ionic bond between carboxyl groups grafted on plasma-modified PLA fibers and cationic red dye molecule; various interactions exist such as covalent, ionic and hydrogen bonding with disperse red dye molecule, and covalent bonding between a small amount of hydroxyl groups and reactive blue dye molecule. The SDAP modifying method mentioned in this work is green, efficient, and continuous. Further, the proposed mechanism may promote a new step for the large-scale modification and functionalization of PLA fibers and more cutting-edge materials in the future.
Conflicts of interest
There are no conflicts to declare.
Acknowledgements
The authors acknowledge project funding provided by the National Natural Science Foundation of China (21988102 and 22205247).
References
- D. Jayanth, P. S. Kumar, G. C. Nayak, J. S. Kumar, S. K. Pal and R. Rajasekar, J. Polym. Environ., 2018, 26, 838 CrossRef CAS.
- M. Naeimirad, B. Krins and G.-J. M. Gruter, Sustainability, 2023, 15, 14474 CrossRef CAS.
- L. Shao, Y.-C. Chang, C. Hao, M.-e. Fei, B. Zhao, B. J. Bliss and J. Zhang, Green Chem., 2022, 24, 8716 RSC.
- E. Castro-Aguirre, F. Iniguez-Franco, H. Samsudin, X. Fang and R. Auras, Adv. Drug Delivery Rev., 2016, 107, 333 CrossRef CAS PubMed.
- W. Shao, J. He, Q. Han, F. Sang, Q. Wang, L. Chen, S. Cui and B. Ding, Mater. Sci. Eng., C, 2016, 67, 599 CrossRef CAS PubMed.
- S. Farah, D. G. Anderson and R. Langer, Adv. Drug Delivery Rev., 2016, 107, 367 CrossRef CAS PubMed.
- R. A. Ilyas, M. Y. M. Zuhri, H. A. Aisyah, M. R. M. Asyraf, S. A. Hassan, E. S. Zainudin, S. M. Sapuan, S. Sharma, S. P. Bangar, R. Jumaidin, Y. Nawab, A. A. M. Faudzi, H. Abral, M. Asrofi, E. Syafri and N. H. Sari, Polymers, 2022, 14, 202 CrossRef CAS PubMed.
- R. A. Ilyas, S. M. Sapuan, M. M. Harussani, M. Hakimi, M. Z. M. Haziq, M. S. N. Atikah, M. R. M. Asyraf, M. R. Ishak, M. R. Razman, N. M. Nurazzi, M. N. F. Norrrahim, H. Abral and M. Asrofi, Polymers, 2021, 13, 1326 CrossRef CAS PubMed.
- Z. Li, B. H. Tan, T. Lin and C. He, Prog. Polym. Sci., 2016, 62, 22 CrossRef CAS.
- J. Gu, P. Xiao, P. Chen, L. Zhang, H. Wang, L. Dai, L. Song, Y. Huang, J. Zhang and T. Chen, ACS Appl. Mater. Interfaces, 2017, 9, 5968 CrossRef CAS PubMed.
- W. Li, Y. Yang, X. Xi and J. Feng, Langmuir, 2024, 40, 3859 CAS.
- J. Xia, C. Zhang, X. Liu, J. He and X. Dong, Green Chem., 2022, 24, 9180 RSC.
- L. Ying, H. Zhao, C. Li, H. Yang, C. Hu and Z. Wang, Macromolecules, 2022, 55, 6238 CrossRef CAS.
- N. Jayanth, K. Jaswanthraj, S. Sandeep, N. H. Mallaya and S. R. Siddharth, J. Mech. Behav. Biomed. Mater., 2021, 123, 104764 CrossRef CAS PubMed.
- T. Hussain, M. Tausif and M. Ashraf, J. Cleaner Prod., 2015, 108, 476 CrossRef CAS.
- A. Baltazar-Y-Jimenez and A. Bismarck, Green Chem., 2007, 9, 1057 RSC.
- A. Jordá-Vilaplana, V. Fombuena, D. García-García, M. D. Samper and L. Sánchez-Nácher, Eur. Polym. J., 2014, 58, 23 CrossRef.
- M. Wu, L. Jia, S. Lu, Z. Qin, S. Wei and R. Yan, Surf. Interfaces, 2021, 24, 101077 CrossRef CAS.
- A. Haji and M. Naebe, J. Cleaner Prod., 2020, 265, 121866 CrossRef CAS.
- R. A. Jelil, J. Mater. Sci., 2015, 50, 5913 CrossRef CAS.
- J. Lv, Q. Zhou, T. Zhi, D. Gao and C. Wang, J. Cleaner Prod., 2016, 118, 187 CrossRef CAS.
- F. Chen, J. Song, Z. Liu, J. Liu, H. Zheng, S. Huang, J. Sun, W. Xu and X. Liu, ACS Sustain. Chem. Eng., 2016, 4, 6828 CrossRef CAS.
- L. Yang, Y. Feng, Z. He, X. Jiang, X. Luo, H. Dai and L. Jiang, Nano Res., 2023, 16, 9625 CrossRef CAS.
- V. Štěpánová, P. Šrámková, S. Sihelník, M. Stupavská, J. Jurmanová and D. Kováčik, Vacuum, 2021, 183, 109887 CrossRef.
- L. Yang, D. Hao, Z. He, J. Sun, Y. Feng, H. Dai and L. Jiang, Adv. Funct. Mater., 2024, 34, 2310510 CrossRef CAS.
- Y. Ren, L. Xu, C. Wang, X. Wang, Z. Ding and Y. Chen, Appl. Surf. Sci., 2017, 426, 612 CrossRef CAS.
- H. Huang, Y. Qu, Z. Fu and Y. Sun, Adv. Mater. Res., 2013, 627, 233 Search PubMed.
- S. H. Lee and S. Y. Yeo, Fibers Polym., 2016, 17, 1154 CrossRef CAS.
- J. Wu, N. Wang, H. Zhang, L. Wang, H. Dong, Y. Zhao and L. Jiang, J. Mater. Chem. A, 2013, 1, 4642 RSC.
- J. Baltrusaitis, P. M. Jayaweera and V. H. Grassian, Phys. Chem. Chem. Phys., 2009, 11, 8295 RSC.
- N. Graf, E. Yegen, T. Gross, A. Lippitz, W. Weigel, S. Krakert, A. Terfort and W. E. S. Unger, Surf. Sci., 2009, 603, 2849 CrossRef CAS.
- L. G. Harris, W. C. E. Schofield and J. P. S. Badyal, Chem. Mater., 2007, 19, 1546 CrossRef CAS.
- A. Khatri, M. H. Peerzada, M. Mohsin and M. White, J. Cleaner Prod., 2015, 87, 50 CrossRef CAS.
- A. Ketema and A. Worku, J. Chem., 2020, 6628404 CAS.
|
This journal is © The Royal Society of Chemistry 2024 |
Click here to see how this site uses Cookies. View our privacy policy here.