DOI:
10.1039/D3RA08590B
(Paper)
RSC Adv., 2024,
14, 9656-9667
Click chemistry modifications for the selective crosslinking of wood pulp fibers – effect on the physical and mechanical properties of paper
Received
15th December 2023
, Accepted 8th March 2024
First published on 22nd March 2024
Abstract
The Cu(I)-catalyzed Huisgen cycloaddition click chemistry reaction is of particular interest in the production of paper sheets or natural fiber composites since it leads to the formation of chemically stable bonds between two fibers. This study focuses on the click chemistry modification of kraft pulp fibers. We based our approach on prior research that treated kraft fibers using click chemistry, including propargylation and tosylation reactions. Our focus was on enhancing these treatments to achieve better final sheet properties. After the azidation of tosylated fibers, the crosslinking is carried out with and without a catalyst using water as a solvent to form enhanced kraft fiber sheets. The chemical characterization and the mechanical properties of fibers obtained at intermediate stages confirmed the presence of various functions on the surface of the modified fibers, with a very high degree of substitution and the inter-fiber cross-linking by click chemistry. The presence of inter-fibers covalent bonds led to significant improvements in the mechanical strength and tensile stiffness of the sheets.
Introduction
Natural fibers have shown their potential in a wide range of applications such as construction materials, furniture making, automobiles and aerospace.1 They have rapidly gained popularity as composite reinforcements and alternatives to synthetic fibers due to their economic and environmental advantages.2–5 Most paper properties, depend strongly on interactions between the functional groups or molecules adsorbed at the fiber surface. It is widely known that the interfiber interface can be modified, either chemically or physically,6–17 to improve sheet properties. These surface treatments are performed either to clean the surface of the fiber and eliminate non-cellulosic compounds, to add chemical functions, to modify the surface energy of fibers, or to perform additional reactions, such as the formation of covalent bonds between the fibers. In this latter case, the chemical treatment substitutes polar hydroxyl groups found on the surface of cellulosic substrates with chemical functions capable of reinforcing inter-fiber bonds.18 Currently, amino-based chemicals are commonly used for cross-linking lignocellulosic substrates but pose stability and toxicity issues. Citric acid and 1,2,3,4-butanetetracarboxylic acid (BTCA) are preferred as safer alternatives.19 The Copper Catalyzed Alkyne–Azide Cycloaddition (CuAAC) reaction offers a novel approach by forming a three-dimensional network between propargylated and azidated polysaccharide chains, eliminating the need for conventional cross-linkers.20,21 This method also allows for controlled network formation and covalent bonding between specific fiber types, enhancing the properties of lignocellulosic materials like paper sheets and composites.22,23
According to Koschella et al., the copper-mediated 1,3-dipolar cycloaddition of water-soluble cellulose derivatives grafted with azide and alkyne functions yields novel cellulose hydrogels.24 It was shown that the limiting factor for eventual application of this process is the low mechanical stability of the material, which is related to the low yield of the cross-linking reaction.24 In an attempt to increase the reaction yield, kraft pulp fibers were used as a model substrate to identify the conditions necessary for the synthesis of reaction intermediates: tosyl,25,26 propargyl,25,27 and azido cellulose. Elchinger et al. described a direct cross-linking of azidated starch and propargylated kraft pulp in the presence of a Cu(I) catalyst. The mechanical properties of the final material are significantly higher than those of kraft pulp fibers by approximately 71% and 44% for tear and breakage indices respectively, up to 173% for elongation, and 136% for the burst index.28
Lszló Szabó et al.23 functionalized carbon fibers with a cellulose propionate coating using a click chemistry approach. The functionalization resulted in an increase in interfacial shear strength (IFSS) of approximately 32% compared to the control sample. Additionally, they found that a small molecule with a highly lipophilic and compact CF3 substituent on a rigid aromatic structure resulted in a slightly higher interfacial adhesion, an increase of about 45% compared to the control sample.23 Jun Chen et al. succeeded in increasing the tensile strength, Young's modulus and elongation at break of polar glycidyl azide polymer-based nanocomposites and propargyl-terminated non-polar polybutadiene, via the introduction of alkenyl cellulose nanocrystals as filler, which acted as a crosslinking agent based on CuAAC for the composite network, to improve the interfacial adhesion, in view of the high crystallinity and high stiffness of these nanofillers.29
The primary objective of this study is to improve the low mechanical properties obtained by Faugeras et al.22 by modifying the reaction conditions. Specifically, in the case of azidated and crosslinked kraft fibers, the tensile index was decreased in both cases by about 46% compared to unmodified kraft pulp fibers. Our objective is to increase the reaction yield, which in turn will improve inter-fiber bonding inside the sheet and the final quality of the paper sheet. In contrast with Elchinger et al.28 and Faugeras et al.,22 we studied more thoroughly the impact of the fiber pretreatment on the accessibility of fiber surface to reactants. This could positively affect the yield of the various preliminary reactions and lead to a higher crosslinking level in the final sheet. Propargyl and azide groups were attached to fibers in various fiber dispersions. The CuAAC reaction was then used to combine and crosslink the two modified pulps, creating a material with improved mechanical characteristics (Fig. 1). As a secondary objective, the results of the mechanical characteristics obtained with kraft pulp fibers will allow for the choice of the optimal reaction conditions that will be applied to other types of natural fibers, such as flax fibers, in order to generate new reinforcements for use in natural fiber composites.
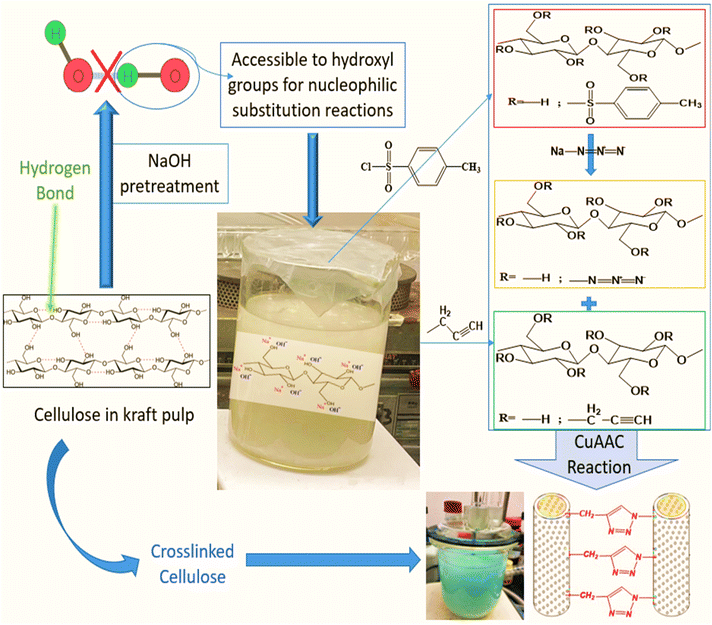 |
| Fig. 1 Cross-linking of cellulosic fibers in the paper pulp. | |
Materials and methods
Materials
A commercial bleached softwood kraft pulp was provided by Fraser Paper (Thurso, Canada). Chemical reagents were purchased from suppliers: propargyl bromide (80% in toluene), p-toluenesulfonyl chloride and sodium azide (Alfa Aesar), sodium hydroxide and copper sulfate pentahydrate (CuSO4·5H2O) (Acros Organics), dimethylformamide, sodium ascorbate, and triethylamine (Sigma-Aldrich). All materials were used as received without any further purification.
Fiber activation: alkaline pretreatment
25 g of dry pulp (KFT-RAW) were dispersed in 2 L of deionized water for a minimum of four hours. The pulp, well soaked in water, was then put in a standard pulp disintegrator for ten minutes at 1000 rpm to prepare a homogeneous fiber dispersion.
In order to improve the accessibility of cellulose hydroxyl groups, an alkaline pretreatment was performed to remove unwanted surface contaminants such as pectin, lignin, and hemicelluloses. The fibers were soaked in a 5% w/w NaOH solution for 24 hours at room temperature. Then, the fibers were washed thoroughly with water, followed by acidified water (20 drops of HCl 0.1 M in 1 L of water) to neutralize residual NaOH. Then again, the fibers were washed with water. According to a protocol adapted from Faugeras et al.,22 the pretreated kraft pulp fibers were dispersed in an alkaline medium (2.5% w/v) for 30 min under stirring before initiating the propargylation and tosylation reactions.
Fiber modification
Activated kraft pulp fibers were submitted to different chemical treatments to prepare the following materials: propargylated kraft pulp (KFT-Pr), tosylated kraft pulp (KFT-Ts), azidated kraft pulp (KFT-Az), crosslinked kraft pulp without catalyst (KFT-CLICK), crosslinked kraft pulp with catalyst (KFT-CLICK-CUAAC), and NaOH treated kraft pulp for 7 days (KFT-NaOH).
Preparation of propargylated fibers
The procedure for the preparation of propargylated kraft pulp fibers (KFT-Pr), was based on Faugeras et al.,22 with some modifications to reaction conditions. The reaction time and the volume of propargyl bromide were increased. 76 mL (0.640 mol) of propargyl bromide was added to 1 L of an alkaline suspension of fibers (20 g, 124 mmol). The reaction medium was placed under mechanical stirring at room temperature. After 96 h, the mixture was diluted with 2 L of deionized water, let to rest for 4 h, filtered and washed with 2 × 1 L of hot water and 1 L of hot ethanol.
Preparation of tosylated fibers
In contrast to the previous work of Elchinger et al.,26 the tosylation reaction was performed in an alkaline medium (2.5% w/v NaOH) after a 24 h pretreatment in 5% w/v NaOH. 104 mL (0.744 mol) of triethylamine was added to 1 L (20 g, 124 mmol) of a pretreated kraft fiber dispersion to which 142.2 g (0.744 mol, 6 eq.) of tosyl chloride was added. After 120 h under mechanical stirring at room temperature, the mixture was diluted in 2 L of deionized water and the fibers were filtered and washed with 3 × 1 L of hot water and 1 L of hot ethanol. The obtained white fibrous product (KFT-Ts) was stored in a desiccator.
Preparation of azidated fibers
Azidation of tosylated fibers was also performed using a modified version of the procedure described by Faugeras et al.22 32.108 g (0.492 mol, 10 eq. per Ts) of sodium azide were added to 20 g of tosylated kraft pulp dispersed in 0.8 L of dimethylformamide. The reaction medium was placed under magnetic stirring at 75 °C for 7 days. After cooling, the mixture was diluted in 2 L of deionized water. The fibers were filtered and washed with 2 L of hot water and 2 L of hot ethanol. The light beige fibrous product (KFT-Az) was stored in a desiccator.
Preparation of crosslinked fibers
15 g (DS N3 1.086, 76.5 mmol) of KFT-Az and 15 g (DS 1.52, 64.1 mmol) of KFT-Pr were dispersed in 2 L of distilled water. In the case of crosslinking with catalyst, 1.48 g (5.9 mmol) copper sulfate pentahydrate and 2.34 g (11.8 mmol) sodium ascorbate were added. The reaction was placed under mechanical stirring at room temperature for 7 days. The reaction medium was filtered and washed with 2 × 1 L of hot water and 1 L of hot ethanol. The product obtained in the form of yellow fibers was stored in a desiccator.
Characterization of modified fibers
Chemical characterization. Infrared spectroscopy was carried out using a Thermo Scientific Nicolet iS10 FT-IR spectrometer, 32 acquisitions were performed at room temperature at a resolution of ±4 cm−1.Scanning electron microscopy (SEM) was used to evaluate the effect of click chemistry and chemical treatments on fiber morphology. SEM images were obtained using a Hitachi SU1510 microscope operating in secondary electron mode with a beam current of 100 mA and an accelerating voltage of 15 kV. The SEM is equipped with an Energy Dispersive X-Ray Spectroscopy (EDX, Oxford instrument X-Max 20 mm2) which was used for the chemical characterization of the surface of fiber pellets composed of homogeneously ground samples. We are more interested in the external surface of fibers since interfiber interactions occur only at the external surface of fibers. The propargyl, tosyl and azide groups present on the functionalized surface of KFT are mainly composed of carbon, sulfur, nitrogen, and oxygen. Three trials were completed for each sample.
The calculation of the surface degree of substitution (DS) for each intermediate was calculated using EDX data. Specific hypotheses tailored to each reaction guided DS calculations. Table 1 presents the hypotheses and corresponding formulas used for DS calculation in each reaction.
Table 1 Hypotheses and formulas for surface degree of substitution (DS) calculation in different reactions
Reaction |
Hypotheses for DS calculation |
Formula for DS calculation |
Propargylation |
The total amount of carbon found in a sample (CTOT) is expressed in terms of anhydroglucose units' carbon (CAGU) and propargyl carbon (CPRO). CAGU is determined by multiplying the oxygen content of the sample (OAGU) by 6/5 since there are 5 oxygen and 6 carbon atoms in each AGU. Then, CPRO is obtained by the difference between CTOT and CAGU |
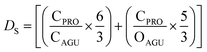 |
Tosylation |
A tosyl unit contains 7 times more carbon than sulfur: % Ctosyl = % S × 7, the percentage of carbon atoms in the anhydroglucose unit (AGU) is: % CAGU = % Ctotal − % Ctosyl. Each AGU contains 6 carbon atoms. The percentage of carbon found in an AGU is given by: % ConeAGU = (%CAGU)/6 |
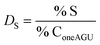 |
Azidation |
An azide unit does not contain any carbon: % Cazide = % N × 0, the percentage of carbon atoms in the AGU is: % CAGU = % Ctotal − % Cazide. Each AGU contains 6 carbon atoms. The percentage of carbon found in an AGU is given by: % ConeAGU = (% CAGU)/6 |
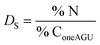 |
Mechanical properties of sheets. Handsheets (60 g m−2) containing NaOH pretreated, azide, propargyl and crosslinked fibers were prepared according to Tappi T205 sp02 standard method.
Burst strength. The burst strength is the maximum pressure that a paper can resist without breaking when a pressure perpendicular to the plane is applied to the sample. It is reported as an index expressed in kPa m2 g−1. Measurements were made at two different locations on each half of a sheet using a Mullen-type burst tester according to the TAPPI T 403 om-97 method.
Tear test. This test is performed according to the TAPPI T 414 om-98 method using the Elmendorf Tearing Tester Thwing-Albert. The tear index is expressed in mN m2 g−1.
Tensile test. This test measures the tensile strength of the paper. It is carried out with an Instron 4201 device according to the TAPPI T 494 om-01 method. The traction (or tensile) index is expressed in N m g−1. The tensile stiffness St (kN m−1) was calculated from the force per unit width versus strain curves according to:
here, Δf (kN) is the difference between two force levels, L (m) is the initial specimen length, w (m) is the initial specimen width and ΔL (m) is the change in length corresponding induces by Δf.
Results and discussions
Characterization of modified fibers
The analysis of paper sheet shows peaks characterizing propargyl, tosyl as well as azido groups. EDX analyses put in evidence an increase in the surface degree of substitution of the fiber. Finally, through mechanical testing, the positive impacts of click chemistry treatment on the strength properties of the final sheet is significantly improved compared to those reported by Faugeras et al.22
First, we investigated the individual impact of the three chemical treatments (propargylation, tosylation, and azidation) on kraft pulp fibers. In order to determine changes that occurred in each case, FTIR spectroscopy was used to obtain spectra for each of the four samples, including the untreated kraft pulp serving as a control sample. Key absorption peaks were labeled and annotated in Fig. 2, allowing for the identification and comparison of the characteristic absorption peaks of the untreated and treated samples. KFT-RAW is characterized by C–H stretching vibrations at 2900–3000 cm−1 and C–O vibrations at 1050–1100 cm−1. Changes in the positions and intensities of certain absorption peaks is observed in treated samples. The successful propargylation was confirmed by the apparition of a new peak at around 2100–2200 cm−1 associated with the triple bond of the propargyl group, as well as changes in the intensity of the C–H stretching peaks. Tosylation resulted in the apparition of two peaks corresponding to the S
O group at 1359 and 1160 cm−1, indicating the presence of the tosyl group. Azidation resulted in the apparition of a new band at 2112 cm−1, confirming the presence of azide groups, as well as changes in the intensity of the C–O stretching bands.
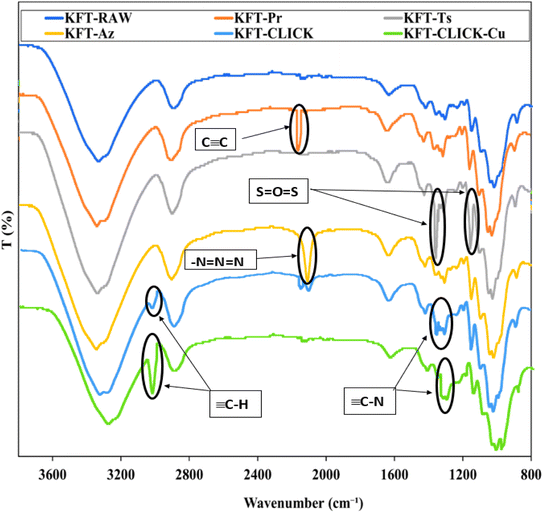 |
| Fig. 2 FTIR spectra of unmodified, modified (propargylated, tosylated, and azidated), and clicked (with and without Cu) fibers. | |
The EDX analysis complements infrared spectroscopy and provides further insights into the chemical modifications made to KFT-Raw (Table 2 and Fig. 3, 4). The surface DS for each of the treated samples was determined using EDX analysis. We are obviously more interested in the external surface of fibers (instead of the interior) considering the interfacial interaction is formed at the exterior surface of fibers.
Table 2 Chemical composition of modified fibers
|
Element (EDX atomic%) |
O/C |
Surface DS |
C |
O |
S |
N |
This study |
Faugeras et al.22 |
KFT-Raw |
59.7 |
40.2 |
— |
— |
0.67 |
— |
— |
KFT-NaOH |
57.5 |
41.4 |
— |
— |
0.72 |
— |
— |
KFT-Pr |
74.0 |
25.9 |
— |
— |
0.35 |
1.52 |
1.32 |
KFT-Ts |
75.8 |
19.2 |
4.8 |
— |
0.25 |
1.68 |
0.60 |
KFT-Az |
63.5 |
24.7 |
0.2 |
11.5 |
0.39 |
1.09 |
0.22 |
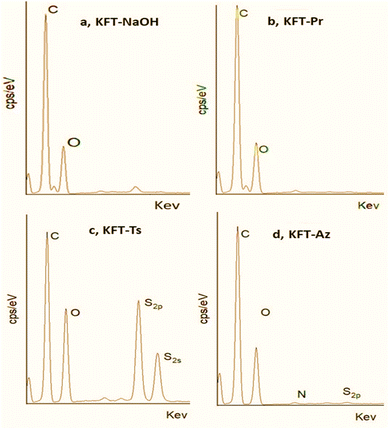 |
| Fig. 3 EDX spectra of (a) NaOH pretreatment, (b) propargylated, (c) tosylated, and (d) azidated fibers. | |
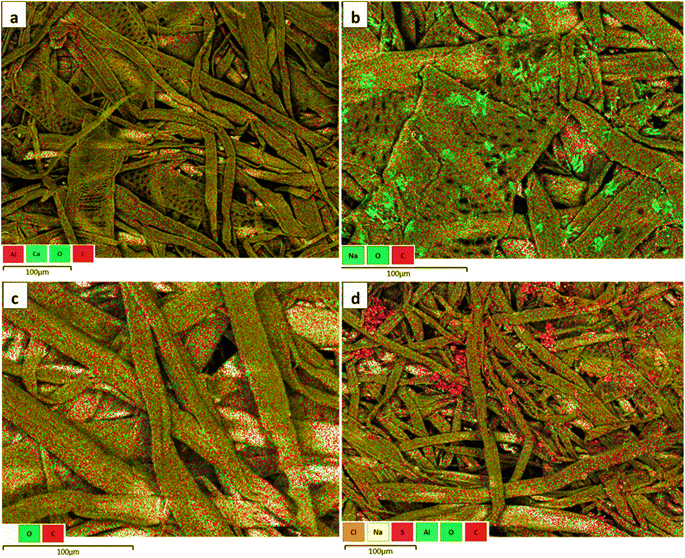 |
| Fig. 4 Elemental mapping analysis of (a) KFT-Raw, (b) KFT-NaOH, (c) KFT-Pr, and (d) KFT-Ts. | |
The EDX spectrum of KFT-Pr (Fig. 3b) shows only carbon and oxygen signals at 270 KeV (C1s) and 524 KeV (O1s), with a much lower O/C ratio than KFT-Raw. This is confirmed by EDX mapping (Fig. 4c) detecting the main elements C and O at the surface of fibers after KFT-Pr treatment, with a lower O/C ratio compared to KFT-Raw (Table 2). This indicates a decrease in the number of hydroxyl groups in the fiber caused by the propargylation.
For KFT-Ts, the EDX spectrum (Fig. 3c) revealed the presence of sulfur, with two peaks at 1750 keV (S2s) and 1490 keV (S2p), and a decrease in the O/C ratio compared to KFT-Raw (Table 2). The significant increase in sulfur content observed in tosylated samples (Fig. 4d) confirmed the successful introduction of tosyl groups onto fiber surfaces with a relatively uniform substitution. This differs significantly with EDX mapping of fibers untreated and treated only with NaOH, where only carbon and oxygen were detected (Fig. 4a and b). This comparison demonstrates the efficiency of the tosylation process, demonstrating the specific incorporation of sulfur-containing tosyl groups on the fiber surface. Again, this suggests a decrease in the number of hydroxyl groups, which is also consistent with the FTIR results showing changes in the intensity of the C–H stretching bands. Additionally, the EDX spectrum for azide-treated fibers show the presence of about 11.5% nitrogen atoms (Table 2), confirming the presence of azide groups, with a DS (N3) of 1.086 and a conversion rate of 97.5%. Notably, the presence of sulfur in the EDX spectrum for KFT-Az (Fig. 3d) suggests that some tosyl groups did not react.
Comparing the DS values obtained in this study to those found by Faugeras et al.22 (Table 2), we can observe a notable improvement in reaction yields. For KFT-Pr, the DS value found in this study was 1.52 compared to 1.32 for Faugeras et al.22 For tosyl-treated fibers, the DS value found is 1.68 compared to 0.60 in the study by Faugeras et al.22 These results indicate that the alkaline pre-treatment step allowed to improve the efficiency of the reactions of the click chemistry, leading to a higher degree of surface substitution.
SEM images shown in Fig. 5 provide detailed observations and comparison of the morphological changes resulting from the different chemical modifications carried out on kraft pulp fibers. The morphology and surface characteristics of the fibers could impact the mechanical properties of the final material. For composites, fibers with a more irregular surface may lead to materials with better mechanical properties, due to improved interfacial bonding with the polymer matrix. On the other hand, fibers with a smoother and more homogeneous surface may lead to weaker interfacial bonding and lower mechanical properties. The general appearance of KFT-RAW, long flat fibers with a smooth surface, is typical for a kraft pulp (Fig. 5a). Kraft pulp pretreated with NaOH (Fig. 5b) have a similar aspect to KFT-RAW, but with the fiber surface smoothed out, most likely as a result of the alkaline pretreatment used to clean fiber surface.
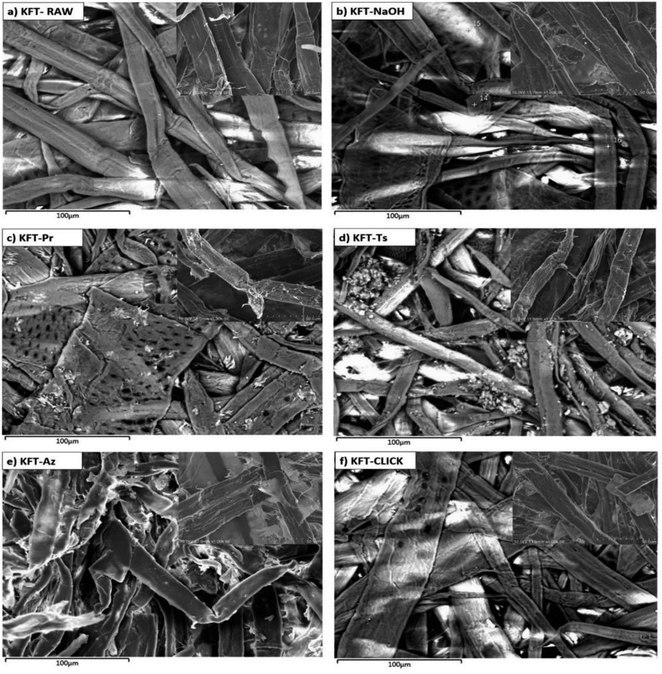 |
| Fig. 5 SEM images of untreated (a) and modified kraft pulp fibers; (b) pretreated fibers; (c) propargylated fibers; (d) tosylated fibers; (e) azidated fibers; and (f) crosslinked fibers. | |
After propargylation (KFT-Pr, Fig. 5c), the fiber surface becomes irregular, with a rough texture. This is likely due to the effect of reaction conditions, such as agitation for 96 h. Similarly, after tosylation (KFT-Ts, Fig. 5d), the fibers underwent a morphological modification resulting in more irregularities on the surface such as deposited residues resulting by slightly fibrillated from the agitation time. The EDX mapping in (Fig. 4c) showed a non-uniform and random distribution of the sulfur molecules, which could explain the roughness in some zones on the tosylated fibers.
SEM analysis of the azide-treated fibers (KFT-Az) (Fig. 5e) still shows a clear morphological difference compared to the untreated fibers, suggesting that the azide modification has an effect on the fiber surface. However, unlike the propargylated and tosylated fibers, the azide-treated fibers displayed significantly reduced surface roughness. This is probably because an organic solvent (DMF) is used rather than water for azidation. The effect of mechanical agitation on the fibers is not the same in an organic medium.
Finally, in the case of the crosslinking by click chemistry between propargyl and azide fibers, the surface of the crosslinked fibers (KFT-CLICK) in Fig. 5f exhibited a distinct roughness, differing from both KFT-Pr and KFT-Az, with a mixture of propargyl and azide fibers. However, only the determination of the mechanical properties of modified fibers will allow the confirmation of any crosslinking.
Influence of treatments on the mechanical properties
Mechanical tests were performed on dry sheets made of fibers without treatment (KFT-Raw) and on those obtained after each intermediate chemical modifications: alkaline pretreatment with NaOH (KFT-NaOH), propargylation (KFT-Pr), tosylation (KFT-Ts), azidation (KFT-Az), and crosslinking without and with a catalyst (KFT-CLICK and KFT-CLICK-Cu). The results of the mechanical tests, including traction, burst, tear indexes along with the elongation at break and tensile stiffness are all summarized in Table 3. Typical tensile test curves of sheets made from different fiber samples are shown in Fig. 6. A nonlinear behavior is clearly shown, so the tensile stiffness was measured using the linear initial portion of the curve. To appreciate these results and their evolution, Fig. 7 to 11 present histograms of the mechanical property results. Each figure reports the actual value of each property (the same of those in Table 3) along with the percent variation of the property, using the KFT-Raw reinforcement as a reference. The properties can be grouped in two categories, those related to the strength, i.e. the traction, burst and tear indexes (Fig. 7 to 9) and those related to the stiffness of the sheet, i.e. the elongation at break and the tensile stiffness (Fig. 10 and 11). They can also be grouped in terms of three treatment levels, the initial cleaning treatment (the NaOH pretreatment), the intermediate treatments (propargylation, tosylation and azidation) and finally the click chemistry treatment.
Table 3 Mechanical properties of sheets made from the different fiber samples
|
KFT-RAW |
KFT-NaOH |
KFT-Pr |
KFT-TS |
KFT-Az |
KFT-CLICK |
KFT-CLICK-Cu |
Elongation at break (%) |
0.85 ± 0.07 |
1.07 ± 0.15 |
1.27 ± 0.19 |
1.09 ± 0.06 |
1.86 ± 0.22 |
1.59 ± 0.32 |
1.79 ± 0.36 |
Traction index (N m g−1) |
19.51 ± 1.43 |
21.76 ± 2.66 |
22.40 ± 2.72 |
21.38 ± 1.09 |
24.11 ± 1.06 |
34.16 ± 2.84 |
33.54 ± 3.46 |
Tensile stiffness (kN m−1) |
1.98 ± 0.08 |
1.75 ± 0.26 |
1.79 ± 0.27 |
1.65 ± 0.13 |
1.88 ± 0.12 |
2.85 ± 0.35 |
2.71 ± 0.16 |
Burst index (kPa m2 g−1) |
0.77 ± 0.11 |
0.84 ± 0.09 |
1.25 ± 0.17 |
1.06 ± 0.14 |
1.14 ± 0.16 |
2.02 ± 0.16 |
2.26 ± 0.30 |
Tear index (mN m2 g−1) |
19.03 ± 2.16 |
22.91 ± 3.8 |
33.02 ± 4.64 |
23.53 ± 3.52 |
26.72 ± 3.20 |
37.10 ± 5.72 |
32.90 ± 2.62 |
Tensile strength (MPa) |
9.57 ± 0.63 |
10.91 ± 1.2 |
12.06 ± 1.43 |
10.6 ± 0.47 |
12.16 ± 0.54 |
14.43 ± 1.22 |
18.8 ± 1.94 |
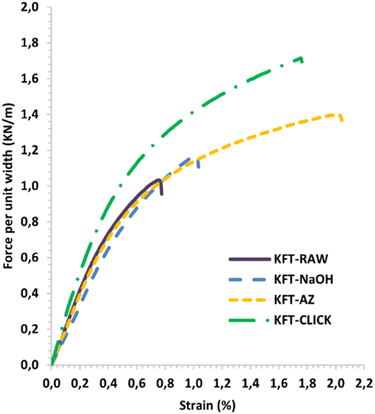 |
| Fig. 6 Typical force per unit width versus strain curves for treated and untreated kraft pulp sheets. | |
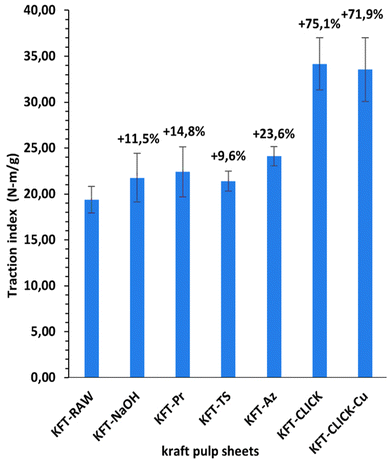 |
| Fig. 7 Traction index (N m g−1) of sheets made from different fiber types. | |
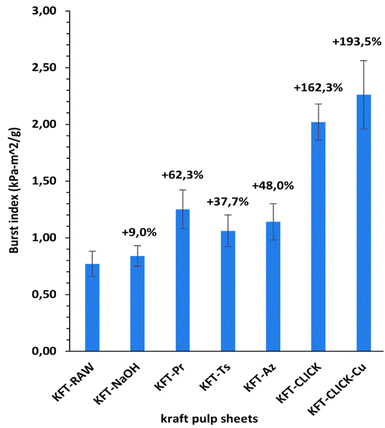 |
| Fig. 8 Burst index (kPa m2 g−1) of sheets made from different fiber types. | |
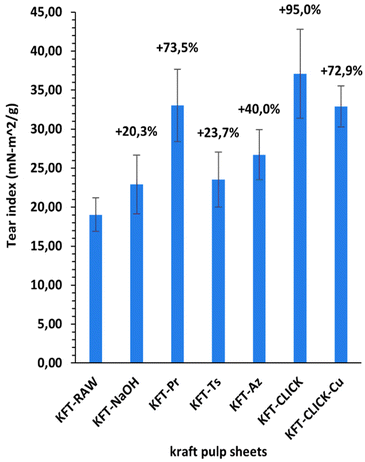 |
| Fig. 9 Tear index (mN m2 g−1) of sheets made from different fiber types. | |
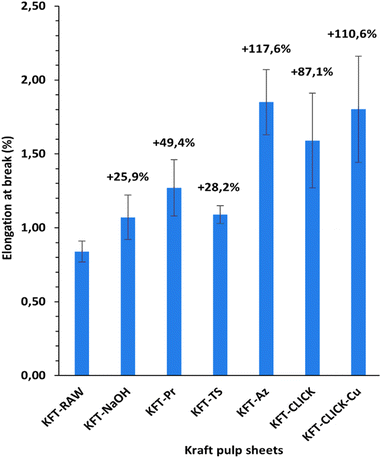 |
| Fig. 10 Elongation at break (%) of sheets made from different fiber types. | |
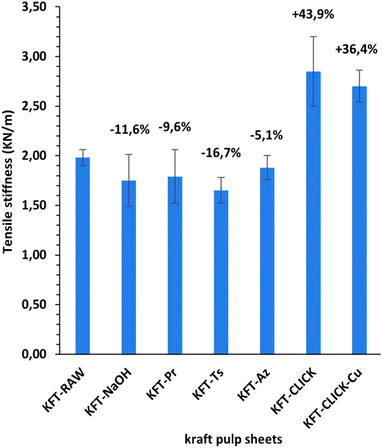 |
| Fig. 11 Tensile stiffness (kN m−1) of sheets made from different fiber types. | |
Influence of treatments on strength
Fig. 7 to 9 show the properties related to the strength of sheets, i.e. the traction, burst and tear indexes respectively. Considering the standard deviations, papers processed by click chemistry show large increases in tensile and burst indexes. There is also a certain gradation in the measured properties when comparing the different treatment levels. First, the NaOH pretreatment (KFT-NaOH) generally has the lowest influence on the strength properties compare to other treatments. The best improvement was for the tear index at 20.3%, while for burst and traction indexes, the effect was negligible. The cleaning effect of the NaOH pretreatment was efficient to prepare the fibers for the other treatments, but as such it has a much lower influence on strength. The intermediate treatments (i.e. KFT-Pr, KFT-Ts and KFT-Az) show modest increases in the traction index but important ones for the burst and tear indexes, ranging from 37.7% for the burst index up to 73.5% for the tear index. Tosylation shows the lowest increases while propargylation led to significant improvements in the mechanical properties, especially for the burst and tear indexes with increases of 62.3% and 73.5%. This is partly attributed to the formation of covalent bonds between the propargyl groups and the fibers, leading to a rougher fiber surface thus producing a stronger fiber-matrix adhesion.
Moreover, it is known that propargyl and polar azide groups act as plasticizers in materials.30–35 This could promote the compaction of fiber bed during sheet making by increasing the contact surface between fibers, thus contributing to higher strength compare to the non-treated fibers.
Clearly, the best strength results were obtained after the creation of covalent bonds with the click chemistry reaction. This is especially evident for the traction and burst indexes, with increases of 75.1% and 193.5% respectively, as shown in Fig. 7 and 8. These increases represent huge improvements over intermediate treatments of respectively 51.5% and 131.2% when compared to KFT-Az (at 23.6%) for the traction index and KFT-Pr (at 62.3%) for burst index. The largest improvement is obtained for the burst index. This suggests the click reaction is particularly effective at increasing the inter-fiber bonding strength considering the burst test induces two-dimensional in-plane tensile stresses in the sheet compare to the unidirectional tensile test. This is a clear indication of the direct and positive influence of the covalent bonds created with the click chemistry treatment to increase the strength of paper sheets. Fig. 12 shows SEM images of the tensile fracture zones for the KFT-Raw and KFT-CLICK samples. Surprisingly, except a slightly rougher fiber surface for the KFT-CLICK, there is no evident differences in the damage mechanisms after fracture, i.e. there is no evidence of severe alteration of the fiber surface due to the presence of strong covalent bonds in the KFT-CLICK sample. This can be explained by the fact that the paper sheet breaks at its weakest locations, which are located in weakly bonded zones away from the cross-linked zones. In consequence SEM images taken at the fiber scale cannot clearly show the influence of cross-linking on the fiber fracture.
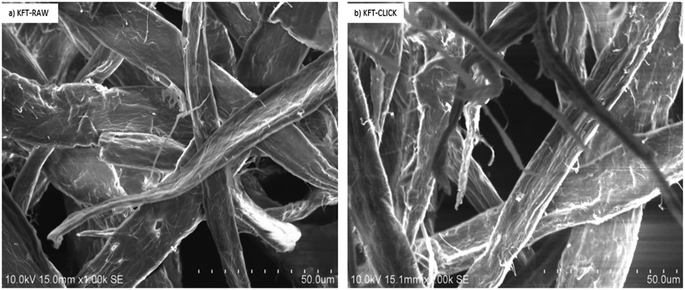 |
| Fig. 12 SEM images of the tensile fracture zones for the two types of sheets: (a) KFT-RAW and (b) KFT-CLICK. | |
It is worth mentioning that the lowest CLICK treatment improvement over the intermediate (precursor) treatments is obtained for the tear index (Fig. 9) with an improvement of only 21.5%. This is observed by comparing KFT-CLICK (95%) and KFT-Pr (73.5%) in Fig. 9. This could be attributed to the shear loading mode in the tear index test, combined to the presence of the Pr group acting as plasticizer in both cases (KFT-Pr precursor and CLICK papers). Indeed, the presence of plasticizers in shear loading could lead to less involved and efficient inter-fiber covalent bonds compared to the more direct tensile and membrane loads obtained in the traction and burst index tests. Comparing the influence of treatments on strength obtained in this study to those found by Elchinger et al. and Faugeras et al., we can observe a notably increased after the click-chemistry reaction, with enhancements of 75%, 1934%, and 95% in traction, burst, and tear indexes, respectively, compared to 43.9%, 136.7% and 71.9% for Elchinger et al., and −45.78%, −58.1% and −45.9% for Faugeras et al.
Finally, comparing the click-chemistry reactions obtained with and without the Cu catalyst (KFT-Click-Cu and KFT-Click), some improvements in the properties are better without the use of catalyst (traction and tear indexes for instance) while some other are better with the presence of Cu catalyst (burst and elongation at break indexes). The regioselectivity of the Cu catalyzed reaction do not appear to have a significant impact on mechanical properties. Globally the differences are relatively small so it can be said that the use of a Cu catalyst (detrimental for the environment) can be avoided which is another very interesting aspect of this work. Ultimately and in view of Fig. 6 to 11, potentially other effects could be related to the specific chemical modifications used. A more detailed analysis should be performed to provide a deeper understanding of any observed improvements.
Influence of treatments on stiffness
Fig. 10 and 11 show properties related to the stiffness behavior of the sheets of paper, i.e. the elongation at break and tensile stiffness. For the NaOH and intermediate treatments, to the increases in elongations at break (Fig. 10) corresponds a decrease in stiffness (Fig. 11). This is consistent with the definition of the tensile stiffness, i.e. a lower tensile stiffness is obtained for more deformable sheets. But this behavior was unexpected considering that usually, the formation of stronger bonds increases stiffness and reduces the deformation at break by precluding fiber movements. Especially, very high and unexpected increases in the elongation at break were obtained for the KFT-Az (117.6%) and the KFT-CLICK treatments (of 110.6% and 87.1% with and without Cu catalyst). To these elongations at break correspond however a decrease in stiffness for the KFT-Az treatment compared to a stiffness increase for the KFT-CLICK treatments. This is also observed in Fig. 6. Globally, the CLICK and CLICK-Cu treatments produce the highest increases in elongation at break (110.6%) and tensile stiffness (43.9%) compared to the non-treated KFT-Raw sheet of paper. While maintaining a high deformability as for KFT-Az, the covalent bonds obtained by click chemistry also produced the desired effect of a much higher stiffness.
Conclusions
This study successfully demonstrated the modification of kraft pulp fibers through various chemical treatments and click chemistry. A crucial aspect of this work was the implementation of a NaOH pretreatment (cleaning) step before initiating the click chemistry reaction. This pretreatment helps to remove unwanted surface contaminants, making the hydroxyl groups of the cellulose accessible for further chemical modifications. It also enhances the reactivity of the fibers and improves their compatibility with the chemical reactants, thus leading to an important improvement in the degree of substitution for most of the intermediate treatments.
The click chemistry reaction significantly improved the mechanical properties of the kraft pulp fiber sheets. Increases in tensile, burst, and tear indexes were observed for sheets made from the NaOH and intermediate treated fibers. Notably, the burst and tear indexes of propargylated paper sheets increased by up to 62% and 74%, respectively. However, even more substantial improvements were achieved after the click-chemistry reaction, with enhancements of 75%, 1934%, and 95% in tensile, burst, and tear indexes, respectively, following the formation of covalent bonds. Additionally, the click-chemistry reaction led to a significant increase in stiffness (44%) compared to the precursor treatments, along with one of the highest elongation at break values (111%). Most importantly, the use of the Cu catalyst was found to be unnecessary to achieve these high levels of mechanical properties, simplifying the treatment process while avoiding environmentally harmful chemicals.
Overall, this work provides valuable insights into the potential of click chemistry to modify kraft pulp fibers for the creation of paper sheets with enhanced properties, paving the way for further research and development in the field of advanced materials and green chemistry.
Conflicts of interest
There are no conflicts of interest to declare.
Acknowledgements
The authors thank the Natural Sciences and Engineering Research Council of Canada (NSERC) for its financial support.
References
- M. R. Sanjay, G. R. Arpitha, L. Laxmana Naik, K. Gopalakrishna and B. Yogesha, Applications of Natural Fibers and Its Composites: An Overview, Nat. Resour., 2016, 7, 108–114 CAS.
- Y. G. Thyavihalli Girijappa, S. Mavinkere Rangappa, J. Parameswaranpillai and S. Siengchin, Natural Fibers as Sustainable and Renewable Resource for Development of Eco-Friendly Composites: A Comprehensive Review, Front. Mater., 2019, 6, 226 CrossRef.
- C. E. Njoku, K. K. Alaneme, J. A. Omotoyinbo and M. O. Daramola, Natural Fibers as Viable Sources for the Development of Structural, Semi-Structural, and Technological Materials – A Review, Adv. Mater. Lett., 2019, 10, 682–694 CrossRef CAS.
- R. S. Mbakop, G. Lebrun and F. Brouillette, Experimental analysis of the planar compaction and preforming of unidirectional flax reinforcements using a thin paper or flax mat as binder for the UD fibers, Composites, Part A, 2018, 109, 604–614 CrossRef CAS.
- A. Couture, G. Lebrun and L. Laperrière, Mechanical properties of polylactic acid (PLA) composites reinforced with unidirectional flax and flax-paper layers, Compos. Struct., 2016, 154, 286–295 CrossRef.
- A. More, Flax fiber-based polymer composites: a review, Adv. Compos. Hybrid Mater., 2021, 5(3), 1–20 Search PubMed.
- I. Van de Weyenberga, J. Ivensa, A. De Costerb, B. Kinob, E. Baetensb and I. Verpoesta, Influence of processing and chemical treatment of flax fibers on their composites, Compos. Sci. Technol., 2003, 63, 1241–1246 CrossRef.
- Y. Xie, C. A. S. Hill, Z. Xiao, H. Militz and C. Mai, Silane coupling agents used for natural fiber/polymer composites: a review, Composites, Part A, 2010, 41, 806–819 CrossRef.
- A. Atiqah, et al., Effect of Alkali and Silane Treatments on Mechanical and Interfacial Bonding Strength of Sugar Palm Fibers with Thermoplastic Polyurethane, J. Nat. Fibers, 2018, 15, 251–261 CrossRef CAS.
- S. Y. Nayak, Effect of chemical treatment on the physical and mechanical properties of flax fibers: a comparative assessment, Mater. Today: Proc., 2021, 38, 2406–2410 CAS.
- S. Adil, A. Maazouz, E. Fleury, H. Sautereau and H. Kaddami, Short date palm tree fibers/polyepoxy composites prepared using RTM process: effect of TEMPO mediated oxidation of the fibers, BioResources, 2010, 5(2), 672–689 Search PubMed.
- M. Sood, D. Deepak and V. K. Gupta, Effect of Fiber Chemical Treatment on Mechanical Properties of Sisal Fiber/Recycled HDPE Composite, Mater. Today: Proc., 2015, 2, 3149–3155 CAS.
- M. Wanga, L. Maa, L. Shia, P. Fenga, X. Wanga, Y. Zhua, G. Wub and G. Song, Chemical grafting of nano-SiO2 onto graphene oxide via thiolene click chemistry and its effect on the interfacial and mechanical properties of GO/epoxy composites, Compos. Sci. Technol., 2019, 182, 107751 CrossRef.
- S. Shinoj, R. Visvanathan, S. Panigrahic and M. Kochubabu, Oil palm fiber (OPF) and its composites: a review, Ind. Crops Prod., 2010, 33(1), 7–22 CrossRef.
- S. O. Han and H. Y. Choi, Morphology and surface properties of natural fiber treated with electron beam, Microscopy: Science, Technology, Applications and Education, 2010, 3, 1880–1887 Search PubMed.
- M. Isik, H. Sardon and D. Mecerreyes, Ionic Liquids and Cellulose: Dissolution, Chemical Modification and Preparation of New Cellulosic Materials, Int. J. Mol. Sci., 2014, 15(7), 11922–11940 CrossRef CAS PubMed.
- C. Lorraine, V. Wielen and A. J. Ragauskas, Grafting of acrylamide onto cellulosic fibers via dielectric-barrier discharge, Eur. Polym. J., 2003, 40(3), 477–482 Search PubMed.
- G. Siqueira, J. Bras and A. Dufresne, New process of chemical grafting of cellulose nanoparticles with a long chain isocyanate, Langmuir, 2009, 26(1), 402–411 CrossRef PubMed.
- Y. Ma, X. You, M. Rissanen, I. Schlapp-Hackl and H. Sixta, Sustainable
Cross-Linking of Man-Made Cellulosic Fibers with Poly(carboxylic acids) for Fibrillation Control, ACS Sustain. Chem. Eng., 2021, 9(49), 16749–16756 CrossRef CAS.
- H. C. Kolb, M. G. Finn and K. B. Sharpless, Click Chemistry: Diverse Chemical Function from a Few Good Reactions, Angew. Chem., Int. Ed., 2001, 40, 2004–2021 CrossRef CAS PubMed.
- P.-H. Elchinger, P.-A. Faugeras, B. Boën, F. Brouillette, D. Montplaisir, R. Zerrouki and R. Lucas, Polysaccharides: The “Click” Chemistry Impact, Polymers, 2001, 3, 1607–1651 CrossRef.
- P.-A. Faugeras, R. Zerrouki and F. Brouillette, Selective crosslinking of kraft pulp fibres by click chemistry – characterisation of the properties of reaction intermediates and final product, Nord. Pulp Pap. Res. J., 2014, 29(4), 673–678 CrossRef CAS.
- L. Szabó, S. Imanishi, N. Kawashima, R. Hoshino, D. Hirose, T. Tsukegi, K. Ninomiya and K. Takahashi, Interphase Engineering of a Cellulose-Based Carbon Fiber Reinforced Composite by Applying Click Chemistry, ChemistryOpen, 2018, 7(9), 720–729 CrossRef PubMed.
- A. Koschella, M. Hartlieb and T. Heinze, A “clickchemistry” approach to cellulose-based hydrogels, Carbohydr. Polym., 2011, 86, 154–161 CrossRef CAS.
- P.-A. Faugeras, F. Brouillette and R. Zerrouki, Crosslinked cellulose developed by CuAAC, a route to new materials, Carbohydr. Res., 2012, 356, 247–251 CrossRef PubMed.
- P.-H. Elchinger, P.-A. Faugeras, C. Zerrouki, D. Montplaisir, F. Brouillette and R. Zerrouki, Tosylcellulose synthesis in aqueous medium, Green Chem., 2012, 14, 3126–3131 RSC.
- P.-A. Faugeras, P.-H. Elchinger, F. Brouillette, D. Montplaisir and R. Zerrouki, Advances in cellulose chemistry - microwave-assisted synthesis of propargylcellulose in aqueous medium, Green Chem., 2012, 14, 598–600 RSC.
- P.-H. Elchinger, H. Awada, C. Zerrouki, D. Montplaisir and R. Zerrouki, Kraft pulp-starch covalent linking: a promising route to a new material, Ind. Eng. Chem. Res., 2014, 53(18), 7604–7610 CrossRef CAS.
- J. Chen, N. Lin, J. Huang and A. Dufresne, Highly alkynyl-functionalization of cellulose nanocrystals and advanced nanocomposites thereof via click chemistry, Polym. Chem., 2015, 6, 4385 RSC.
- P. Jia, et al., Internally plasticized PVC materials via covalent attachment of aminated tung oil methyl ester, RSC Adv., 2017, 7, 30101 RSC.
- R. Hunter Cooke III, J. Wu, H. A. Livingston, G. L. Parker, B. C. Peoples, A. Ekin, A. Bushmire and R. F. Storey, Polyurethane polymers cured via azide-alkyne cycloaddition, Prog. Org. Coat., 2021, 151, 106047 CrossRef.
- T. Zeng, D. Li, Y. Lan, W. Gao, J. Li and R. Yang, Study on Interaction between Propargyl-Terminated Polybutadiene and Plasticizers Based on Simulation and Experiments, J. Phys. Chem. A, 2019, 123(29), 6370–6377 CrossRef CAS PubMed.
- Z. Geng, J. J. Shin, Y. Xi and C. J. Hawker, Click chemistry strategies for the accelerated synthesis of functional macromolecules, J. Polym. Sci., 2021, 59, 963–1042 CrossRef CAS.
- M. Ma and Y. Kwon, Reactive Energetic Plasticizers Utilizing Cu-Free Azide-Alkyne 1,3-Dipolar Cycloaddition for In-Situ Preparation of Poly(THF-co-GAP)-Based Polyurethane Energetic Binders, Polymers, 2018, 10, 516 CrossRef PubMed.
- T. Jarosz, A. Stolarczyk, A. Wawrzkiewicz-Jalowiecka, K. Pawlus and K. Miszczyszyn, Glycidyl Azide Polymer and Its Derivatives-Versatile Binders for Explosives and Pyrotechnics: Tutorial Review of Recent Progress, Molecules, 2019, 24, 4475 CrossRef CAS PubMed.
|
This journal is © The Royal Society of Chemistry 2024 |
Click here to see how this site uses Cookies. View our privacy policy here.