DOI:
10.1039/D3RA08404C
(Paper)
RSC Adv., 2024,
14, 2293-2299
Methylation of softwood and hardwood kraft lignins with chloromethane†
Received
8th December 2023
, Accepted 19th December 2023
First published on 10th January 2024
Abstract
Methylation is a well-established means of enhancing the thermal stability, improving the compatibility in polymer blends, and lowering the glass-transition temperature of lignins. This process normally involves reagents that are costly, associated with poor atom economy and/or highly toxic. Herein, we report the methylation of softwood and hardwood kraft lignins using chloromethane in alkaline aqueous media. This reaction proceeds in high yields at 90–110 °C under moderate pressure (40 psi) while generating environmentally benign sodium chloride and water as by-products.
Introduction
Kraft lignins are heterogenous polyphenolic biopolymers produced at the 70 million metric ton scale in kraft pulp mills worldwide every year.1 Despite their abundance and renewable origins, they are seldom used in commercial applications, rather being virtually all burned as a low-value fuel in recovery boilers. This is in part due to the characteristic complex and reactive structure of kraft lignins which makes them susceptible to oxidation and thermally unstable above their glass-transition temperatures.2–4 Indeed, this instability greatly complicates their incorporation in polymers, composites, and other materials where thermal stability is critical. In addition, kraft lignins are hygroscopic and readily absorb a significant amount of moisture which further impedes their use in many applications.5,6 Methylation is a standard means of circumventing these issues. By masking the reactive phenols within lignins, improved thermal stability, reduced hygroscopicity, and lower glass-transition temperature can be achieved.2,3,7–10 Furthermore, the yields of aromatic compounds obtained by depolymerization of lignins can also be significantly improved by methylation of the phenols.11,12 However, classical methylation agents such as dimethyl sulfate and iodomethane are toxic, expensive, and lead to processes characterized by poor atom economy. In recent years, dimethyl carbonate13 and trimethyl phosphate14 were shown to be less toxic alternatives, but they remain expensive and do not improve atom economy. Furthermore, they require large excesses of reagents at elevated temperatures to achieve reasonable methylation rates. Chloromethane appeared to be an excellent alternative as it offers many advantages over other methylation agents: (1) it has relatively high reactivity, (2) it has relatively low toxicity, (3) it generates chloride and water as by-products, (4) it is less expensive and offers better atom economy than other lignin methylation agents, and (5) it can be used in aqueous media. While chloromethane is rarely encountered as a methylating agent in academic settings where iodomethane or dimethyl sulfate are usually preferred, its industrial use is exemplified in the manufacture of methylcellulose15 and quaternary ammonium salts.16 Herein we report that the combination of chloromethane and sodium hydroxide are effective reagents for the methylation of both softwood and hardwood kraft lignins under mild conditions (Scheme 1).
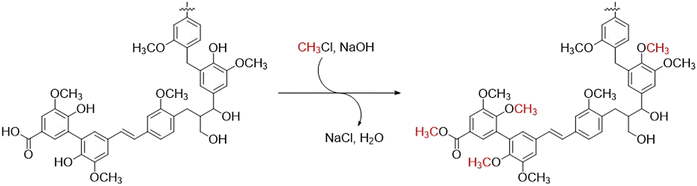 |
| Scheme 1 Methylation of a representative kraft lignin fragment with chloromethane and sodium hydroxide. | |
Materials and methods
Materials
LignoForce™ softwood kraft lignin (SKL) was obtained from a mill in Hinton, AB, Canada (West Fraser) and LignoForce™ hardwood kraft lignin (HKL) was obtained from a mill in Thunder Bay, ON, Canada (Resolute).17,18 Chloromethane, sodium hydroxide, dimethyl sulfoxide, pullulan standards, lithium bromide, deuterated chloroform, pyridine, 2-chloro-4,4,5,5-tetramethyl-1,3,2-dioxaphospholane, cyclohexanol, and chromium(III) acetylacetonate were purchased from commercial sources and used without further purification. Selected properties of the kraft lignins used in this study are provided in Table 1.
Table 1 Selected properties of kraft lignins used in this study
Lignin |
Mw (SEC-MALS) (g mol−1) |
Mw (SEC-RI) (g mol−1) |
Tg (°C) |
Hydroxyl group content (mmol g−1) |
Aliphatic OH |
Non-condensed phenolic OH |
Condensed phenolic OH |
Carboxylic OH |
SKL |
15 130 |
7800 |
166 |
1.94 |
2.09 |
2.02 |
0.58 |
HKL |
8100 |
4880 |
142 |
1.78 |
1.14 |
3.03 |
0.25 |
Optimization of the methylation reaction
SKL (0.50 g) and aqueous sodium hydroxide (10 mL, 0.25–0.35 M, 2.5–3.5 mmol) were charged into a 50 mL stainless steel reactor. The resulting mixture was magnetically stirred until the solids were fully dissolved, then the reactor was flushed with nitrogen, sealed, and pressurized with chloromethane (40 psi). The reactor was then heated to an internal temperature of 80–110 °C in an aluminium block and maintained at this temperature under magnetic stirring for 1–4 h. After cooling to room temperature and venting the reactor, the resulting mixture was transferred into ca. 30 mL of water, stirred, and acidified with diluted aqueous sulfuric acid (1.5 M) to pH = 2. The resulting suspension was vigorously stirred for 30 min at ambient temperature, then it was filtered on a glass-fritted funnel. The collected solid was washed with deionized water (3 × 20 mL) before being air-dried to afford methylated SKL. The extent of the methylation reaction was determined by quantitative 31P NMR spectroscopy (vide infra). Yields were calculated by considering the increase in mass caused by methylation according to eqn (1): |
 | (1) |
where mi is the initial mass of lignin (g), mf is the final mass of lignin (g) and [ArOH + COOH]d is the difference between the initial and final concentrations of phenolic and carboxylic hydroxyls groups (mol g−1). The 14.027 g mol−1 factor corresponds to the molar mass of a methylene unit.
Methylation of SKL with chloromethane
SKL (100 g), water (550 mL) and aqueous sodium hydroxide (350 mL, 2.0 M, 700 mmol) were charged into a 1.8 L stainless steel reactor. The resulting mixture was mechanically stirred until the solids were fully dissolved, then the reactor was sealed, flushed with nitrogen, and pressurized with chloromethane (40 psi). The pressure of chloromethane was maintained at 40 psi for the whole reaction time by means of a check valve. The reactor was then heated to an internal temperature of 90 °C for 4 h. After cooling to room temperature and flushing the reactor with nitrogen, the resulting suspension was drained from the reactor and kept aside. At this point, a copious amount of solid remained in the reactor. Water (1.0 L) was charged in the reactor. The resulting mixture was mechanically stirred, and the reactor was heated to an internal temperature of 90 °C for 1 h. After cooling to room temperature, the resulting suspension was drained from the reactor and combined with the suspension that was earlier kept aside. The combined suspensions were mechanically stirred and acidified with diluted aqueous sulfuric acid (1.5 M) to pH = 2. The resulting thick suspension was centrifuged (17
000×g, 30 min), and the supernatant was decanted. The precipitate was resuspended in ca. 1.0 L of water, and the resulting suspension was vigorously stirred for 30 min at ambient temperature before being centrifuged (17
000×g, 30 min). The supernatant was decanted, and the solid residue was finally air-dried to afford methylated SKL (98.9 g, 94.3% yield).
Methylation of HKL with chloromethane
The same procedure as for the methylation of SKL was followed but using HKL instead which afforded methylated HKL (96.0 g, 91.5% yield).
1H and 13C NMR spectroscopy
Approximately 70 mg of lignin sample was completely dissolved in 500 μL DMSO-d6. The spectra were recorded at room temperature on a Varian Inova 600 MHz spectrometer. A total of 1024–8192 scans were acquired for each 13C spectrum.
31P NMR spectroscopy
The concentration of hydroxyl groups in lignin samples was determined by 31P NMR spectroscopy.19,20
Sample preparation. Approximately 35 mg of lignin sample was completely dissolved in 900 μL of a 1.0
:
1.6 mixture of CDCl3 and pyridine. Afterwards, 200 μL of a CDCl3
:
pyridine stock solution containing 26.5 mg of cyclohexanol and 1.0 mg of Cr(acac)3 was added. Finally, 150 μL of 2-chloro-4,4,5,5-tetramethyl-1,3,2-dioxaphospholane was added, and the resulting solution was shaken for 1 h before being loaded in an NMR tube.
Hydroxyl content determination. 31P NMR spectra were recorded on a 500 MHz Bruker Avance NEO spectrometer. 1024 scans were acquired with 0.6 s acquisition time and 10 s relaxation delay. Integration was done after baseline correction. All spectra were calibrated to the anhydride formed by the reaction of the derivatization reagent with water at 132.2 ppm. The quantification ranges applied were 150.0–145.4 ppm for aliphatic hydroxyl groups, 144.5–140.2 ppm for condensed phenolic hydroxyl groups, 140.2–137.6 for non-condensed phenolic hydroxyl groups, and 136.0–133.6 ppm for carboxylic hydroxyl groups.
Size-exclusion chromatography (SEC)
The molar mass distribution of kraft lignins and of fractions of kraft lignins were determined by size-exclusion chromatography (SEC). The method described by Zinovyev et al. was used.21
Sample preparation. Kraft lignins, methylated kraft lignins and standards were stirred in LiBr/DMSO (0.5% w/v) at 50 °C for 2 h at a concentration of 5 mg mL−1. Once cooled to ambient temperature, the resulting solutions were filtered through 0.2 μm PTFE filters prior to analysis.
SEC analysis. SEC analysis was performed using an Agilent Model 1200 high performance liquid chromatography system (solvent tray, degasser, quaternary pump, autosampler, column heating module, UV diode-array detector) equipped with a Wyatt Dawn® multi-angle light scattering detector (MALS) with a laser operating at 785 nm and a Wyatt Optilab® differential refractive index (RI) detector (λ = 785 nm). The MALS detector comprises 18 photodiodes at different measuring angles, with narrow band pass filters (±10 nm installed on every second photodiode). The separation was performed with three columns in series: one Agilent PolarGel M column (7.8 mm × 300 mm, 8 μm) followed by two Agilent PolarGel L columns (7.8 mm × 300 mm, 8 μm). The columns were kept at 50 °C. The SEC system was operated under the following conditions: LiBr/DMSO (0.5% w/v) eluent, 0.5 mL min−1 flow rate; 50 μL injection volume; 65 min run time. A set of 10 pullulan polymers standards (Mp = 710, 343, 202, 116, 50.6, 23.0, 9.90, 6.00, 1.26 and 0.342 kg mol−1) was used to construct a conventional narrow standard calibration curve for relative molar mass determination. Data evaluation was done using ASTRA software, version 7.3.
Determination of (dn/dc)μ values. The determination of the specific refractive index increment at a constant chemical potential (dn/dc)μ of each lignin sample in LiBr/DMSO (0.5% w/v) was performed using the online approach by integration of the RI peak area after sample elution from the columns assuming 100% sample mass recovery.
Differential scanning calorimetry (DSC)
The glass transition temperature (Tg) of kraft lignins and of fractions of kraft lignins were measured by differential scanning calorimetry (DSC) using a TA Instruments DSC Q2500. The method outlined by Cui et al. was used.3 All samples were dried at 60 °C for 12 h prior to the DSC analysis. Approximately 5 mg of dried lignin sample was weighed directly in a DSC aluminum sample pan, which was then sealed by cold pressing. A pinhole was made in the lid of the pan. After the sample was loaded in the instrument, it was heated to 105 °C at a rate of 5 °C min−1 and then isothermally conditioned for 40 minutes prior to being quenched to 30 °C. Afterwards, the DSC thermograms were recorded by increasing the temperature to 200 °C at a rate of 10 °C min−1. The glass-transition temperature was determined at ½ΔCp for the transition.
Results and discussion
Optimization of the methylation
Chemical modifications of lignins are typically carried out in polar aprotic solvents such as pyridine or dimethyl sulfoxide since lignins have limited solubility in common organic solvents.22,23 Yet, for a lignin chemical modification process to be green and industrially sound, it must be viable from both environmental and economic standpoints. In this context, organic solvents often are an impediment to process development due to their associated high operational costs, considerable waste streams, and safety concerns.24 As our aim was to develop a chloromethane-based methylation procedure that would be both environmentally friendly and relatively cost-effective to implement at large scale, water was deemed an ideal solvent and was exclusively studied. While kraft lignins are insoluble in acidic or neutral aqueous media, they are highly soluble at pH 10 and above. However, one complication that arises from the use of aqueous alkali as solvent is that chloromethane readily reacts both with water (following pseudo-first order kinetics) and with hydroxide (following second order kinetics) to generate methanol (Table 2).25
Table 2 Kinetics of hydrolysis of chloromethane
Reaction |
k (100 °C) |
pH |
Half lifea (100 °C) |
Calculated from the data reported by Fells and Moelwyn-Hughes.25 |
CH3Cl + H2O |
1.49 × 10−4 s−1 |
— |
77.5 min |
CH3Cl + HO− |
2.42 × 10−2 L mol−1 s−1 |
11.0 |
477 min |
11.5 |
151 min |
12.0 |
47.7 min |
12.5 |
15.1 min |
13.0 |
4.77 min |
13.5 |
1.51 min |
Consequently, it is essential to determine conditions where the rate of lignin methylation exceeds that of chloromethane hydrolysis to avoid unproductive consumption of chloromethane. With these limitations in mind, it was deemed critical to carry the methylation at a pH of 13 or below.
As a starting point for the optimization, SKL was methylated in 50 mL stainless steel reactors using an initial static pressure of 40 psi of chloromethane (corresponding to ca. 9 mmol CH3Cl per g SKL as estimated from the remaining volume in the reactor), 5 mmol NaOH per g SKL (slightly above the sum of phenolic and of carboxylic acid groups in SKL) and 20 mL water per g SKL (Table 3). At 80 °C, methylation did occur, but the reaction was slow (Table 3, entry 1). Indeed, the pH of the reaction mixture after 4 h was still above 10 and only 42% of the phenolic groups were found to be methylated. At 90 °C and 100 °C the reaction proceeded much faster: the pH of the reaction mixture after 4 h was acidic and up to 66% of the phenolic groups were methylated (Table 3, entry 2–3). Increasing the temperature further to 110 °C did not lead to higher phenol methylation within these parameters (Table 3, entry 4). It is noteworthy that the pH at the end of the methylation reactions were found to be slightly higher for reactions done at 110 °C compared to those done at 100 °C. The significantly lower solubility of chloromethane in water at high temperatures might be the reason for this observed decrease in the overall chloromethane consumption rate (methylation and hydrolysis).26
Table 3 Optimization of the methylation of softwood kraft lignin using chloromethane and sodium hydroxide (0.5 g scale, 40 psi CH3Cl)
Entry |
Lignin |
NaOH (mmol g−1) |
Temperature (°C) |
Time (h) |
H2O (mL g−1) |
Initial pH |
Final pH |
Reduction in hydroxyl content (%) |
Yield (%) |
Aliphatic |
Non-condensed phenolic |
Condensed phenolic |
Total phenolic |
Carboxylic |
100 g scale. CH3I (6 mmol g−1) was used instead of CH3Cl. Control experiment without NaOH and CH3Cl. |
1 |
SKL |
5 |
80 |
4 |
20 |
12.4 |
10.3 |
5 |
55 |
28 |
42 |
9 |
98.9 |
2 |
SKL |
5 |
90 |
4 |
20 |
12.4 |
5.0 |
30 |
69 |
50 |
59 |
59 |
94.7 |
3 |
SKL |
5 |
100 |
4 |
20 |
12.4 |
2.0 |
44 |
74 |
58 |
66 |
64 |
96.8 |
4 |
SKL |
5 |
110 |
4 |
20 |
12.4 |
2.2 |
43 |
73 |
56 |
64 |
67 |
94.0 |
5 |
SKL |
6 |
90 |
4 |
20 |
12.6 |
6.6 |
13 |
73 |
50 |
62 |
41 |
95.9 |
6 |
SKL |
6 |
100 |
4 |
20 |
12.6 |
2.5 |
30 |
77 |
57 |
67 |
66 |
97.6 |
7 |
SKL |
6 |
110 |
4 |
20 |
12.6 |
3.0 |
49 |
80 |
64 |
72 |
67 |
97.9 |
8 |
SKL |
6 |
110 |
3 |
20 |
12.6 |
3.1 |
43 |
74 |
57 |
66 |
66 |
97.3 |
9 |
SKL |
7 |
90 |
4 |
20 |
12.8 |
7.6 |
12 |
74 |
50 |
62 |
38 |
95.5 |
10 |
SKL |
7 |
110 |
3 |
20 |
12.8 |
3.6 |
26 |
78 |
55 |
66 |
64 |
98.3 |
11 |
SKL |
6 |
90 |
4 |
10 |
12.9 |
6.3 |
25 |
82 |
61 |
72 |
52 |
95.3 |
12 |
SKL |
6 |
90 |
4 |
8 |
13.0 |
6.8 |
11 |
84 |
63 |
74 |
66 |
95.0 |
13 |
SKL |
7 |
90 |
4 |
10 |
13.0 |
6.6 |
25 |
85 |
66 |
76 |
62 |
98.0 |
14a |
SKL |
7 |
90 |
4 |
9 |
13.1 |
8.0 |
15 |
91 |
68 |
80 |
38 |
94.3 |
15a |
HKL |
7 |
90 |
4 |
9 |
13.1 |
7.2 |
11 |
84 |
83 |
83 |
8 |
91.5 |
16b |
SKL |
6 |
90 |
4 |
10 |
12.9 |
3.4 |
6 |
90 |
71 |
81 |
84 |
94.9 |
17c |
SKL |
— |
130 |
2 |
20 |
4.2 |
3.6 |
12 |
0 |
0 |
0 |
4 |
— |
18c |
SKL |
— |
100 |
1 |
20 |
1.5 |
1.5 |
35 |
0 |
0 |
0 |
2 |
— |
Increasing the sodium hydroxide charge led to up to 72% methylation of the phenolic groups (Table 3, entry 5–10). Increasing the concentration of lignin further improved the extent of phenol methylation to 74% (Table 3, entry 11–12). Increasing both the sodium hydroxide charge and the concentration of lignin only increased the extent of methylation to 76% (Table 3, entry 13). Scaling-up the optimized conditions to 100 g scale led to slightly higher methylation rate reaching 80% (Table 3, entry 14). When the same conditions were applied to HKL, 83% of the phenolic groups were found to be methylated (Table 3, entry 15).
Methylation extents of approximatively 80% of the phenols appeared to be an upper attainable limit in the hydroxide/chloromethane/water system. Using the more reactive iodomethane instead of chloromethane as a comparison led to practically identical phenolic hydroxyl methylation (Table 3, entry 16). This limit appears to stem from the use of water as solvent. Indeed, during the course of the methylation reaction, both the concentration of phenolates and the pH of the reaction mixture decrease, eventually leading to the precipitation of a partially methylated lignin. This ultimately restricts the maximum degree of methylation that can be achieved under these conditions as the precipitated lignin does not appear to further react with chloromethane. Instead, chloromethane then reacts with water faster than with lignin which can result in pH as low as 2 in the isolated reaction mixtures.
The extent of methylation of carboxylic acid groups loosely followed the same trend as that of phenolic groups but, in contrast, these were significantly more methylated at higher temperatures. At best, up to 67% of the carboxylic acids could be methylated.
The aliphatic hydroxyl groups were also found to be reduced in the methylated kraft lignins. Indeed, a reduction of anywhere from 10% to 50% of the aliphatic hydroxyls was measured. The most significant reductions were observed at relatively high temperature (100–110 °C) and in reactions where the pH of the isolated reaction mixture was 3 and below. Temperature alone cannot explain such a reduction as heating SKL to 130 °C for 2 h only led to 12% reduction in aliphatic hydroxyls (Table 3, entry 17). On the other hand, heating SKL to 100 °C for 1 h at pH 1.5 (Table 3, entry 18) led to a 35% reduction in aliphatic alcohols. As such, it is likely that the hydroxyls are eliminated via acid-catalyzed dehydration similarly to the well-known acidolysis of lignin (Scheme 2).27,28
 |
| Scheme 2 Acid-catalyzed dehydration of kraft lignins. | |
Effect on the molar mass distribution
The molar mass distributions of the initial and the methylated SKL were nearly identical in most cases, with an expected slight increase towards higher average molar mass. The average molar mass values are available in the ESI.† Nonetheless, prolonged reaction times at 100–110 °C led to gradual changes in the molar mass distributions. Specifically, a shift toward higher average molar mass when the reaction temperature and the reaction time were relatively high was observed (Fig. 1). A combined severity factor (R0) relating both temperature and time was used to model the increase in Mw (eqn (2)).29,30 |
 | (2) |
where t is the time of the reaction (min), T is the temperature of the reaction (°C) and ω is a fitting constant (14.75 °C).
 |
| Fig. 1 SEC-MALS profile of SKL (black), SKL methylated at 90 °C for 4 h using 6 mmol NaOH per g (blue), SKL methylated at 100 °C for 4 h using 6 mmol NaOH per g (green) and SKL methylated at 110 °C for 4 h using 6 mmol NaOH per g (red). | |
The relatively good correlation between the mass average molar mass (Mw) measured by SEC-MALS and the severity of the methylation conditions is a good indicator that the observed aggregation is primarily driven by temperature and time (Fig. 2).
 |
| Fig. 2 Mass average molar mass (Mw) as determined by SEC-MALS (785 nm) against the severity of the methylation conditions. | |
Effect on the glass-transition temperature
Comparing the DSC thermograms of the SKL starting material with the methylated SKL revealed that the glass-transition temperature decreased upon methylation in accordance with previous reports (Fig. 3).2,13,14 The best correlation found was that the glass-transition temperature increased linearly with the total hydroxyl content. This was anticipated since relatively high hydroxyl group content in kraft lignins is known to correlate with relatively high glass-transition temperatures.31 Methylation disrupts the intermolecular hydrogen bonding between lignin fragments leading to increased mobility.
 |
| Fig. 3 Glass-transition temperatures (Tg) of SKL and methylated SKL versus total hydroxyl content. | |
Comparison with other methylation agents
Interest in the methylation of lignin has been rekindled in recent years in view of the recent shift towards sustainable polymeric materials. Dimethyl sulfate is an excellent methylation agent for this purpose as complete methylation of phenolic hydroxyls in softwood kraft lignin can be achieved in water at 80 °C (Table 4). However, a relatively large excess of reagent and continuous addition of aqueous NaOH is essential to obtain this result, and the reagent is ineffective at methylating hardwood kraft lignin unless a very large excess of reagent is used in combination with a low concentration of lignin. Furthermore, the extreme toxicity and carcinogenicity of dimethyl sulfate make it an undesirable reagent for industrial use, as does its poor atom economy. Iodomethane certainly is a better alternative, but methylation in dimethylformamide was shown to methylate only 61% of phenolic groups in softwood kraft lignin despite a large excess of reagent. In water, we showed that iodomethane could methylate up to 81% of phenolic groups in softwood kraft lignin, but this reagent is plagued by its toxicity, its high cost, and its poor atom economy. Recently, dimethyl carbonate was shown to be effective at methylating the phenolic groups in softwood kraft lignin. This reagent has relatively low toxicity, but a very large excess is required (>45 mmol g−1) at a very high temperature (150 °C) to react at reasonable rates (15 h reaction time). It also requires the use of dimethyl sulfoxide as solvent, generates stochiometric amounts of methanol as byproduct and has a slightly improved atom economy compared to dimethyl sulfate and iodomethane. Lastly, trimethyl phosphate was also shown to be effective at methylating the phenolic groups in various lignins yet, as was the case for dimethyl carbonate, a very large excess of reagent is required (>45 mmol g−1) at high temperature (120 °C) to react at reasonable rates. It has the added benefits of not requiring a solvent but generates stochiometric amounts of dimethyl phosphate as byproduct and has a poor atom economy. The use of chloromethane as methylating agent allows the use of water as solvent, requires mild temperatures to be effective at methylating both softwood and hardwood kraft lignins, and offers the best atom economy compared to other reagents.
Table 4 Comparison of various methylating agents used for the methylation of kraft lignins
Lignin |
Methylating agent (MA) |
Amount of MA (mmol g−1) |
Base |
Solvent |
Conditions |
Reduction in hydroxyl content (%) |
Atom economyb |
Ref. |
Al–OH |
Ph–OH |
–COOH |
Estimated from the pH at the end of the methylation reaction considering each consumed chloromethane leads to the acidification of the reaction mixture. Calculated from lignin's C9 unit using the molecular weight of 185 g mol−1 with the model reaction: lignin-OH + NaOH + CH3X → lignin-OCH3 + NaX + H2O. |
SKL |
Dimethyl sulfate |
9.5 |
NaOH (10.5 mmol g−1) |
H2O (15 mL g−1) |
80 °C, 2.5 h |
4 |
99 |
n.d. |
57 |
2 |
HKL |
Dimethyl sulfate |
23.7 |
NaOH (30.0 mmol g−1) |
H2O (100 mL g−1) |
25 °C, 8 h |
0 |
88 |
n.d. |
57 |
2 |
SKL |
Iodomethane |
11.4 |
K2CO3 (excess) |
DMF (15 mL g−1) |
25 °C, 18 h |
38 |
61 |
n.d. |
54 |
2 |
SKL |
Iodomethane |
6.0 |
NaOH (6.0 mmol g−1) |
H2O (10 mL g−1) |
90 °C, 4 h |
6 |
81 |
84 |
54 |
This work |
SKL |
Dimethyl carbonate |
46.6 |
NaOH (9.3 mmol g−1) |
DMSO (19 mL g−1) |
150 °C, 15 h |
75 |
100 |
99 |
63 |
13 |
SKL |
Trimethyl phosphate |
45.4 |
K2CO3 (4.5 mmol g−1) |
— |
120 °C, 1 h |
22 |
100 |
100 |
55 |
14 |
SKL |
Chloromethane |
7.0a |
NaOH (7.0 mmol g−1) |
H2O (10 mL g−1) |
90 °C, 4 h |
15 |
80 |
38 |
72 |
This work |
HKL |
Chloromethane |
7.0a |
NaOH (7.0 mmol g−1) |
H2O (10 mL g−1) |
90 °C, 4 h |
11 |
83 |
8 |
72 |
This work |
Conclusions
In this work, we have developed an aqueous, environmentally friendly, and economically attractive process for methylating the phenolic hydroxyl groups in kraft lignins. The use of chloromethane as methylating agent in conjunction with sodium hydroxide as base yielded a process where the only byproducts are benign sodium chloride and water. In addition, chloromethane greatly improved the atom economy associated with lignin methylation compared to other reagents. The optimized condition led to the methylation of approximately 80% of the phenolic hydroxyl groups present in both softwood and hardwood kraft lignins. This could be achieved using only 6–7 mmol of sodium hydroxide and chloromethane per gram of kraft lignin which constitutes a notable improvement compared to known protocols using other reagents. The observed reduction in aliphatic hydroxyl groups in methylated kraft lignins was shown to be mostly caused by acid-catalyzed dehydration and this reduction remained minimal when the pH of the reaction was not allowed to drop below 3. As expected, the glass-transition temperature of the methylated kraft lignins was lowered proportionally to the methylation extent compared to the initial kraft lignins. Further improvements to the method described herein are being investigated to reach the complete methylation of phenolic hydroxyl groups and involve continuous addition of base and the use of surfactants to limit precipitation.
Conflicts of interest
There are no conflicts to declare.
Acknowledgements
The authors gratefully acknowledge Natural Resources Canada for funding this work.
Notes and references
- C. C. Xu, L. Dessbesell, Y. Zhang and Z. Yuan, Biofuels, Bioprod. Biorefin., 2021, 15, 32–36 CrossRef CAS.
- H. Sadeghifar, C. Cui and D. S. Argyropoulos, Ind. Eng. Chem. Res., 2012, 51, 16713–16720 CrossRef CAS.
- C. Cui, H. Sadeghifar, S. Sen and D. S. Argyropoulos, BioResources, 2013, 8, 864–886 Search PubMed.
- A. Ayoub, T. Treasure, L. Hansen, T. Nypelö, H. Jameel, S. Khan, H. Chang, M. A. Hubbe and R. A. Venditti, Cellulose, 2021, 28, 1039–1053 CrossRef CAS.
- O. Gordobil, R. Herrera, F. Poohphajai, J. Sandak and A. Sandak, J. Mater. Res. Technol., 2021, 12, 159–169 CrossRef CAS.
- V. Mimini, E. Sykacek, S. N. A. Syed Hashim, J. Holzweber, H. Hettegger, K. Fackler, A. Potthast, N. Mundigler and T. Rosenau, J. Wood Chem. Technol., 2019, 39, 14–30 CrossRef CAS.
- N. S. Alwadani and P. Fatehi, ChemistryOpen, 2019, 8, 1258–1266 CrossRef CAS PubMed.
- Y. Li and S. Sarkanen, Macromolecules, 2005, 38, 2296–2306 CrossRef CAS.
- Y. Li and S. Sarkanen, Macromolecules, 2002, 35, 9707–9715 CrossRef CAS.
- S.-J. Xiong, B. Pang, S.-J. Zhou, M.-K. Li, S. Yang, Y.-Y. Wang, Q. Shi, S.-F. Wang, T.-Q. Yuan and R.-C. Sun, ACS Sustainable Chem. Eng., 2020, 8, 5338–5346 CrossRef CAS.
- J. A. Barrett, Y. Gao, C. M. Bernt, M. Chui, A. T. Tran, M. B. Foston and P. C. Ford, ACS Sustainable Chem. Eng., 2016, 4, 6877–6886 CrossRef CAS.
- J.-Y. Kim, S. Heo and J. W. Choi, Fuel, 2018, 232, 81–89 CrossRef CAS.
- S. Sen, S. Patil and D. S. Argyropoulos, Green Chem., 2015, 17, 1077–1087 RSC.
- A. Duval and L. Avérous, Green Chem., 2020, 22, 1671–1680 RSC.
- J. A. Grover, in Industrial Gums, ed. R. L. Whistler and J. N. Bemiller, Academic Press, London, 3rd edn, 1993, pp. 475–504 Search PubMed.
- C. W. Weston, J. R. Papcun and M. Dery, Kirk-Othmer Encycl. Chem. Technol., 2003, 728–753 Search PubMed.
- L. Kouisni, P. Holt-Hindle, K. Maki and M. Paleologou, J. Sci. Technol. For. Prod. Processes, 2012, 2, 6–10 Search PubMed.
- L. Kouisni, A. Gagné, K. Maki, P. Holt-Hindle and M. Paleologou, ACS Sustain. Chem. Eng., 2016, 4, 5152–5159 CrossRef CAS.
- D. Argyropoulos, Res. Chem. Intermed., 1995, 21, 373–395 CrossRef CAS.
- P. Korntner, I. Sumerskii, M. Bacher, T. Rosenau and A. Potthast, Holzforschung, 2015, 69, 807–814 CrossRef CAS.
- G. Zinovyev, I. Sulaeva, S. Podzimek, D. Rössner, I. Kilpeläinen, I. Sumerskii, T. Rosenau and A. Potthast, ChemSusChem, 2018, 11, 3259–3268 CrossRef CAS PubMed.
- J. Sameni, S. Krigstin and M. Sain, BioResources, 2017, 12, 1548–1565 CrossRef CAS.
- A. E. Kazzaz, Z. H. Feizi and P. Fatehi, Green Chem., 2019, 21, 5714–5752 RSC.
- F. P. Byrne, S. Jin, G. Paggiola, T. H. M. Petchey, J. H. Clark, T. J. Farmer, A. J. Hunt, C. Robert McElroy and J. Sherwood, Sustainable Chem. Processes, 2016, 4, 7 CrossRef.
- I. Fells and E. A. Moelwyn-Hughes, J. Chem. Soc., 1959, 398–409 RSC.
- H. L. Clever, Monatsh. Chem., 2003, 134, 745–750 CrossRef.
- K. Lundquist and R. Lundgren, Acta Chem. Scand., 1972, 26, 2005–2023 CrossRef CAS.
- T. Yokoyama, J. Wood Chem. Technol., 2015, 35, 27–42 CrossRef.
- R. P. Overend, E. Chornet, J. A. Gascoigne, B. S. Hartley, P. M. A. Broda and P. J. Senior, Philos. Trans. R. Soc., A, 1987, 321, 523–536 CrossRef CAS.
- W. G. Glasser, V. Davé and C. E. Frazier, J. Wood Chem. Technol., 1993, 13, 545–559 CrossRef CAS.
- R. Ebrahimi Majdar, A. Ghasemian, H. Resalati, A. Saraeian, C. Crestini and H. Lange, ACS Sustainable Chem. Eng., 2020, 8, 16803–16813 CrossRef CAS.
|
This journal is © The Royal Society of Chemistry 2024 |
Click here to see how this site uses Cookies. View our privacy policy here.