DOI:
10.1039/D3RA06758K
(Paper)
RSC Adv., 2024,
14, 29-45
Enhanced microwave assisted pyrolysis of waste rice straw through lipid extraction with supercritical carbon dioxide†
Received
5th October 2023
, Accepted 24th November 2023
First published on 2nd January 2024
Abstract
A combination of supercritical carbon dioxide (scCO2) extraction and microwave-assisted pyrolysis (MAP) have been investigated for the valorisation of waste rice straw. ScCO2 extraction of rice straw led to a 0.7% dry weight yield of lipophilic molecules, at elevated temperatures of 65 °C and pressures of 400 bar. Lipid compositions (fatty acids, fatty alcohol, fatty aldehydes, steroid ketones, phytosterols, n-alkanes and wax esters) of the waxes obtained by scCO2 were comparable to those obtained Soxhlet extraction using the potentially toxic solvent n-hexane. ScCO2 extraction positively influenced the pyrolysis heating rate, with a rate of 420 K min−1 for particles of 500–2000 μm, compared to 240 K min−1 for the same particle size of untreated straw. Particle size significantly affected cellulose decomposition and the distribution of pyrolysis products (gaseous, liquid and char), highlighting the importance of selecting an adequate physical pre-treatment. TG and DTG of the original rice straw and resulting biochar produced indicated that cellulose was completely decomposed during the MAP. While a rapid pressure change occurred at ∼120 °C (size > 2000 μm) and ∼130 °C (size 500–2000 μm) during MAP and was associated with the production of incondensable gas during cellulose decomposition, this takes place at significantly lower temperatures than those observed with conventional pyrolysis, 320 °C. Wax removal by scCO2 influences the dielectric properties of the straw, enhancing microwave absorption with rapid heating rates and elevated final pyrolysis temperatures, illustrating the benefits of combining these sustainable technologies within a holistic rice straw biorefinery.
1 Introduction
Rice straw is a major agricultural residue globally, especially in south and south-east Asia, where cultivation of rice is prevalent. Each year approximately 550 million tons of rice straw waste are generated globally.1 Since the cost of collection and transportation is significant, the straw is either left in paddy fields to rot post-harvest or subjected to open field burning to prepare the land for subsequent cropping.1 However, incorporation of rice straw into soil may be a significant source of CH4 greenhouse emission, due to anaerobic degradation.2 In field burning of rice straw leads to a range of emissions including carbon dioxide (CO2), carbon monoxide (CO), hydrocarbons (including methane (CH4)), nitrogen oxides (NOx) and sulfur dioxide (SO2).3 In addition, some contaminants such as polycyclic aromatic hydrocarbon (PAHs) and polychlorinated dibenzofurans (PCDFs), which are environmentally toxic and potentially carcinogenic, are usually emitted during the combustion.4,5 Unburnt carbon and particulate matter from rice burning can have adverse effects on human health and can have negative implications with respect to climate change caused by regional atmospheric phenomena.6 These releases from in field burning of rice straw led to direct visible signs of pollution, which include problems relating to human health and the environment; what cannot be observed are the indirect effects on a country's economy.4 It is therefore crucial to find a sustainable, environmentally friendly, and economically beneficial solution for this issue. Rice straw has the potential to be a feedstock of great significance for fuel and high value chemical production as part of a biorefinery located within areas of extensive rice cultivation such as the USA and Asia.
Natural waxes have been utilized for various applications particularly in cosmetics, food, personal care products, coatings, polishes, and household products.7–9 There is a high demand for natural waxes, with approximately three thousand kilotons of wax being commercially available each year in the world market.10 Rice straw has been reported to contain about 1% by dry weight of wax, which consists of a mixture of different groups of compounds including long chain fatty acids and fatty alcohols, sterols and wax esters.11 Due to the significant volumes of rice straw, it makes it attractive to exploit this waste resource. Extraction of lipophilic compounds are traditionally achieved using an organic solvent such as hexane. There are environmental hazards and health concerns associated with the use of hexane as it is recognized as a hazardous air pollutant, while this solvent is also reported to potentially cause nervous system damage.12,13 Hexane solvent extraction is non-selective, resulting in the necessity to further purify or extract undesirable co-extractives from the waxes. Soxhlet extraction of lipids from rice straw has been extensively investigated and the composition has been thoroughly characterised.11,14 However, unselective, unsustainable, and potentially toxic organic solvents have been used in such extraction systems. Thus, it is important to consider the use of alternative greener solvents for wax extraction.15–17 Supercritical fluid extraction (SFE), which is environmentally friendly, efficient, and often more selective,18 could be an alternative path towards wax extraction and a potential first step in an integrated rice straw biorefinery. In addition, scCO2 extraction has demonstrated a positive effect on the downstream processing of biomass via pyrolysis, and hydrolysis for sugar release.19,20
Several studies have focussed on the use of scCO2 for the extraction of rice bran,21,22 but fewer studies have focussed on rice straw. The recalcitrant nature of rice straw makes processing this biomass in a biorefinery context challenging. Importantly, scCO2 extraction has been demonstrated to have a positive effect on the downstream processing of biomass including rice straw.20,23 Recent studies have also demonstrated that the combination of SFE and thermochemical treatment can have a profound effect on product distribution.19
Thermochemical treatment such as pyrolysis can be a cost-effective way to decompose the crystalline structure of lignocellulose and produce a variety of chemicals or fuels.24 Significant attention has been given to biomass pyrolysis as it leads to a wide product variety of solids (char), liquids (bio-oil), or gases (including syngas), which could potentially be used as fuels or used to make energy products. Recently, it was demonstrated that bio-oil and biochar could be produced from macroalgae Sargassum sp. via slow pyrolysis.25 However, conventional pyrolysis often operates in the absence of oxygen, at high temperatures (>500 °C), and for extended periods of time, making such processes more energy intensive. Recently, scCO2 extraction was combined with pyrolysis or gasification of Scots pine or spruce.19,26 This research demonstrates that scCO2 extraction of the biomass prior to pyrolysis can have a significant influence on Scots pine tree fractions, changing the surface concentration of water, lipids and metals simultaneously.19 Surface composition of the biomass and the modification of this through scCO2 extraction has a considerable impact on the fast pyrolysis, leading changes in the volatile composition and the solid char structure.26 ScCO2 was able to extract surface metals in the form of fatty acid salts thereby controlling the pyrolysis products.19 In addition, it has also been demonstrated that the extractives have a significant catalytic effect on the yields and morphology of solid chars.
Microwave heating is used in various applications due to its uniform heating, selectivity, and energy efficiency. Microwave-assisted pyrolysis (MAP) has been studied with different raw materials including wheat straw,27 coffee hulls,28 corn stalk bale,29 oil palm biomass,30 rice husk,31 and rice straw.32–35 It was previously observed that increasing the power of MAP of rice straw has led to higher temperatures and rates of heating.32,34,35 The product distribution was gas (49.37%), char (28.07%) and liquid (22.56%) and this was comparable to conventional pyrolysis. The solid char could potentially be used to remove metallic contaminants and the gas product is a H2 rich fuel gas.32,34,35 A recent study demonstrated that scCO2 extraction coupled with microwave activated gasification of spruce forestry residues led to enhanced production of fullerene-like soot nanoparticles and increased syngas yield.36 Low temperature microwave activation of scCO2 extracted spruce produced bio-oils and the resulting biochar was an excellent feedstock for gasification. Lipid content and composition of biomass can have a significant effect on microwave pyrolysis. scCO2 was able to successfully extract the resin acids, aromatics, and steroids from the woody biomass.36 Such compounds are typically less reactive than the many volatile components, leading to enhanced syngas production during gasification with limited effect on the yields of solid product. Importantly, woody biomass such as spruce has a significantly higher fatty and resin acid content to cereal crops such as rice straw. To date no studies have focused on the effects of scCO2 extraction being coupled with microwave pyrolysis of rice straw. As such, the investigation of scCO2 extraction for the removal of the surface lipids prior to MAP is warranted.
Herein, this work reports the first optimization of scCO2 extraction of waxes from rice straw, combined with MAP for the generation of valuable chemicals and fuels as part of a sustainable holistic biorefinery. A 2 × 2 factorial experimental design investigating the variation of temperature and pressure in the scCO2 extraction has been used to optimise the total recovery of wax from rice straw. Various high value compounds including n-policosanols, wax esters, fatty aldehydes, and steroid ketones were quantified in the rice straw wax. These compounds have potential use in industrial applications such as lubricants, surface coating and pharmaceutical uses. The effects of scCO2 extraction on the rate of heating and reaction time of microwave assisted pyrolysis were studied and compared with non-scCO2 extracted rice straw. The effect of particle size on the microwave pyrolysis of rice straw was studied, something which has previously had limited investigation for microwave assisted pyrolysis processes.
2 Experimental section
2.1 Materials
Rice straw (Oryza sativa L.), harvested in July 2013, was obtained from the Faculty of Agriculture, Khon Kaen University (Thailand). The biomass was then sundried and cut into pieces for further storage. Prior to experiments (Scheme 1), the biomass was ground to 0.5 mm particles with a Glen Creston Ltd. hammer mill.
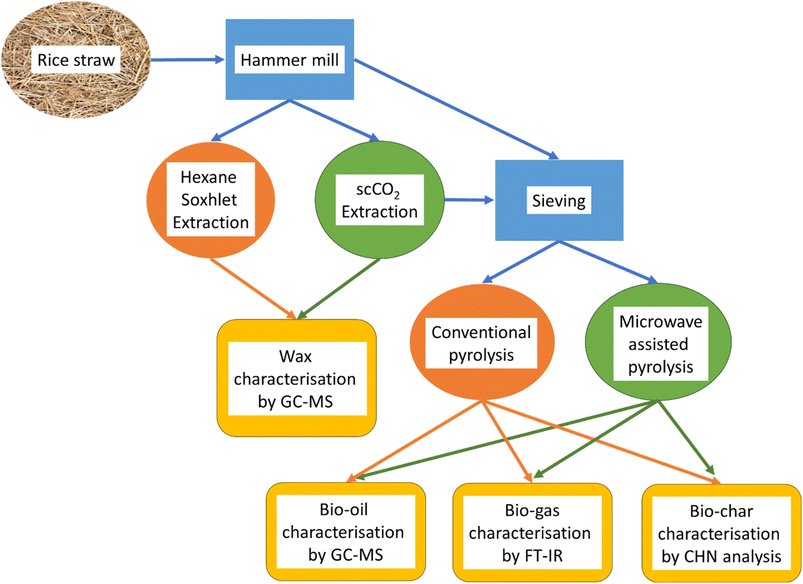 |
| Scheme 1 Schematic of the experimental process of supercritical extraction and microwave assisted pyrolysis. | |
2.2 Conventional Soxhlet extraction
Approximately 10 g of milled rice straw was placed in a cellulose thimble and extracted with 200 ml of hexane for 4 hours in a Soxhlet apparatus. The resulting solution was filtered, and the solvent was removed in vacuo. Extractions were carried out in triplicate.
2.3 Supercritical fluid extraction (SFE)
Approximately 90 g of milled rice straw was extracted using a SFE 500 provided by Thar technologies. CO2 (99.99%), supercritical grade, was used for all extractions. The biomass was loaded into the extractor and connected to the system. The selected temperatures (35, 50 and 65 °C) and pressures (75, 237.5 and 400 bar) were set up, an internal pump was used to reach the required pressure and the pressure of the system was maintained by means of an ABPR. The system was run in dynamic mode, in which the CO2, containing the epicuticular lipids, was allowed to flow into the collection vessel. A flow rate of 40 g min−1 of liquid CO2 was applied for rice straw, and the extraction was carried out for 4 hours. When the extraction was terminated, depressurisation of the system was carried out over a period of 75 min. The % yield of crude extracted was recorded for each sample collected and extractions were carried out in triplicate. For optimisation of time the system was stopped at specific time intervals; whereby rice straw wax was collected at 30, 60, 120, 180, 300 and 360 minutes.
2.4 Wax analysis procedure
Wax analysis methods and sample preparation including derivatisation and HT-GC also HT-GC-MS) procedures were performed using methodology published in previous literature.17 A typical HT-GC analysis was performed on an Agilent Technologies 6890N Network GC System as follow: a ZB-5HT capillary column (30 m × 250 μm × 0.25 μm nominal) was fitted at constant pressure of 22.35 psi. The carrier gas used was helium. The injector temperature and the flame ionisation detector temperature were maintained at 300 °C. The samples were injected by automated injection (1 μl injection volume) with a split 281 ratio of 5
:
1. An initial oven temperature of 60 °C was maintained for 1 minute. The temperature was increased at a ramp rate of 8 °C min−1 until 360 °C and held at this temperature for 30 minutes. Quantification of the lipid components was carried out by means of internal standard calibration and response factors (Rf). Linear calibration graphs were produced using external standards for the quantification of hydrophobic compounds (fatty acids, alcohols, aldehydes, alkanes, wax esters, sterols, monoglycerides, diglycerides, 1-O-alkylglycerol, fatty aldehydes and wax esters). Three sequential injections were applied to calculate the standard deviations.
2.5 Microwave pyrolysis of rice straw and residue after scCO2 extraction
Prior to the microwave pyrolysis, the untreated and scCO2 extracted rice straw was sieved to obtain six different particle sizes, <125 μm, 125–180 μm, 180–300 μm, calculate, 500–2000 μm and >2000 μm. Microwave pyrolysis was subsequently conducted in a CEM-Discover microwave reactor model. The experiments were carried out under fixed power mode with a maximum power of 300 W and in a microwave pressure vial (10 mL CEM Discover SP, CEM Corp., USA). The samples temperature was measured by an IR detector. The microwave pyrolysis of the sample was stopped upon reaching the target pressure (19.305 Bar). 300 mg of milled rice straw and rice straw residue after scCO2 extraction were used without further pre-treatment. Pyrolyzed biomass was extracted with ethanol; the char (insoluble) and bio-oil (ethanol soluble) were then filtrated. The solvent was removed, and the solid was dried in an oven until constant weight. The produced gases were analysed by FTIR. HT-GC-MS was used for liquid product analysis and solid chars were analysed by thermogravimetric analysis (TG), CHN elemental analysis and bomb calorimetry.
2.6 Characterisation of gas fraction
The apparatus for thermal decomposition of rice straw consisted of a microwave connected to IR gas cell for monitoring of gases, with the IR cell and transfer pipe heated at 200 °C. 0.9 g of rice straw was placed inside the microwave reactor and 300 W of microwave as described in 2.5. Fourier transform infrared spectroscopy (FT-IR), a Bruker VERTEX 70 infrared spectroscope was used to perform this analysis. Samples spectra were collected between 500 and 4000 cm−1 at a resolution of 4 cm−1 and a scan number of 64, scanning over a wavelength range of 4000–500 cm−1 at a resolution of 4 cm−1. The spectra were subsequently analysed to determine possible bond types and functional group of the gas. The spectra were collected using a rapid scan software running under OPUS 5.5 and the spectrum of each sample was calculated from an average of 16 scans.
2.7 SEM analysis
SEM micrographs were recorded with JEOL JSM-6490LV scanning electron microscope. The samples, mounted on an aluminium plate, were coated with Au–Pd prior to analysis. The acceleration voltage beam energy was 5 kV.
2.8 CHN elemental analysis
Elemental analysis based on carbon, hydrogen and nitrogen content was carried out using an Exeter Analytical (Warwick, UK) CE440 Elemental Analyser, calibrated against acetanilide with an S-benzyl-thiouronium chloride as internal standard. Analyses were carried out in triplicate.
2.9 Characterisation of liquid fraction
HT-GC-MS was used to examine the oils produced from pyrolysis experiments to tentatively determine their composition. Samples were prepared at a concentration of 20 mg mL−1 of pyrolysis oil in ethanol. A sample of 0.5 μL was injected on to a Perkin ElmerClarus 500 Gas chromatography and Clarus 560S Mass spectrometer at an injector temperature of 350 °C and a column flow rate of 1.0 ml min−1 with a 1
:
10 split ratio applied. The oils were passed onto a DB5-HT column (30 m × 0.25 m × 0.25 μm) at a temperature of 60 °C. The column was held for 1 minute at this temperature and then ramped to 360 °C at 8 °C min−1. It was then held for further 10 minutes. During the GC run the mass spectrometer with Ei+ source of 70 eV was scanning between 40 to 1200 Da at a scan duration of 0.39 s and cycle time of 0.400 s, with an inter scan delay of 0.050 s. The subsequent m/z spectra recorded were compared against the NIST 2005 spectral database and possible chemical matches identified. Analyses were carried out in triplicate.
2.10 Simultaneous thermal analysis
Thermogravimetric analysis (TGA) analysis was carried out simultaneously on a PL Thermal Sciences STA 625. Milled rice straw or biochar (10 mg) was accurately weighed into an aluminium cup and analysed against an empty aluminium reference pan from 20 °C to 625 °C at a heating rate of 10 K min−1 under a 60 ml min−1 flow of nitrogen. All biochars were washed and dried prior to analysis. Analyses were carried out in duplicate.
3 Results and discussion
3.1 Supercritical carbon dioxide extraction of rice straw
3.1.1 Extraction yields. Temperature and pressure were systematically investigated to optimise the scCO2 extraction of total wax recovery from rice straw; hence a two-level factorial design was applied.37 The runs were conducted at a constant flow rate of 40 g min−1 of CO2 for 4 hours. The temperature and pressure ranges selected were between 35 to 65 °C and 75 to 400 bar, respectively. This parameter influences the solubility of compounds in CO2 leading to different extraction yields and chemical composition of the extracts.38 The extracts obtained were analysed without further purification. The rice straw waxes yield under the aforementioned conditions varied from 0.01 to 0.70% of dry biomass (Fig. 1). Isothermally increasing the pressure significantly improved the extraction yield, 0.01% at 35 °C, 75 bar compared to 0.41% at 35 °C, 400 bar. However, the temperature also plays an essential role in the extraction and the highest yield, 0.70%, was obtained at 65 °C, 400 bar. These yields are consistent with those previously reported by Sun et al. by hexane extraction (0.65% of dry plant).11,14 The waxes obtained from the scCO2 extractions were compared to those obtained by conventional solvent extraction to evaluate the scCO2 process. The wax yield obtained for hexane was found to be close to 1%. Due to their internal semi-crystalline structure, the plant cuticular waxes require high thermal energy to enhance solubility. The solubility of selected lipid molecules increases with elevated pressure; however, the effect of pressure on solubility differs with the nature of solutes and operating temperature. The temperature of the system at constant pressure had two contradictory influences on the solubility of lipids. Increasing temperature led to more significant vapour pressure of lipids in CO2 thus enhancing solubility, while the decrease in solvent density caused by a temperature increase resulted in a reduction in solubility.39 A crossover pressure value exists between these two opposing factors, below which the solubility decreases with temperature (where the density is more critical). This phenomenon of increased yield due to density is observed for low pressure and temperature (0.05% at 75 bar, 35 °C) compared to a higher temperature (0.01% at 75 bar, 65 °C). Once this crossover pressure value has been overcome, there is an increase in solubility with temperature due to the greater vapour pressure of lipids.15 In this study at high pressures, an outstanding increase of yield was achieved with elevated temperature (0.70% at 400 bar, 65 °C), whereas at lower temperatures of 35 °C, only 0.41% was yielded.
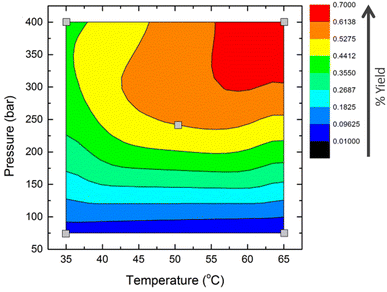 |
| Fig. 1 Two-dimensional plot demonstrating % yield of extractives from rice straw at varying temperature (°C) and pressure (Bar). | |
3.1.2 Quantification of lipophilic compounds. Characterization and quantification of lipophilic compounds at different temperatures and pressures were demonstrated in Fig. 2 and 3 (ESI, Tables S1–S7†). The scCO2 extraction process demonstrated that waxes, consisting of long-chain fatty acids, n-policosanols, n-hydrocarbons, fatty aldehydes, sterols, steroid ketones, and wax esters, can be effectively obtained.
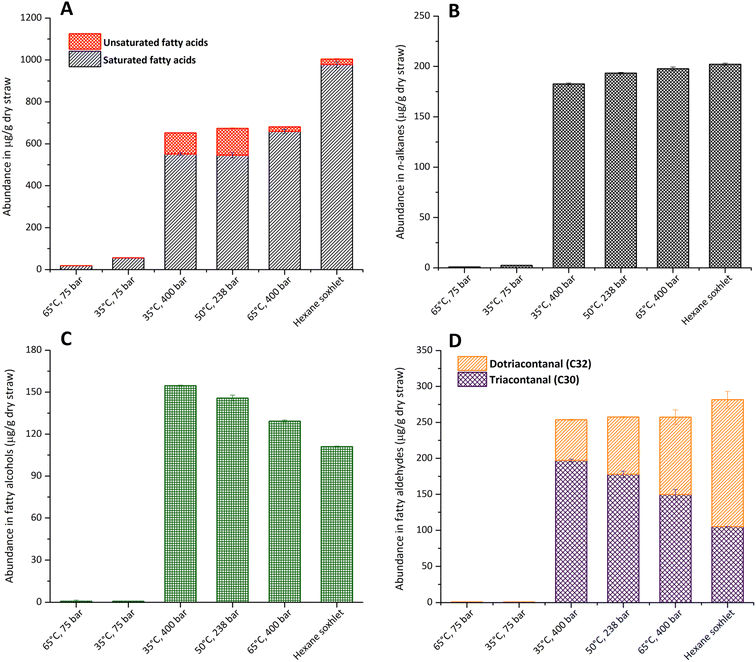 |
| Fig. 2 Extract compositions of (A) free fatty alcohols, (B) n-alkanes, (C) free fatty alcohols and (D) free fatty aldehydes from rice straw waxes using scCO2 and hexane Soxhlet extraction for 4 hours. | |
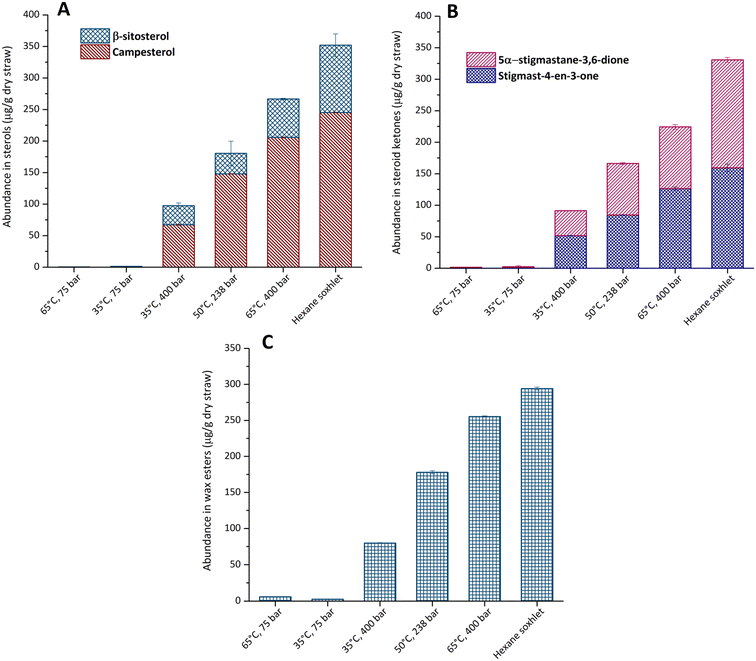 |
| Fig. 3 Extract composition of (A) sterols, (B) sterol ketones, and (C) wax esters from rice straw waxes using scCO2 and hexane Soxhlet extraction for 4 hours. | |
Free fatty acids were the most abundant lipophilic compounds in rice straw waxes, with chain lengths ranging from C12 to C32. Saturated fatty acids represented most of this class of compounds, with hexadecanoic acid (C16:0) being the most predominant in hexane Soxhlet extraction. This is consistent with previous studies on the lipid composition of rice straw.11,14 The highest yield of fatty acids (681 ± 10.3 μg g−1 of dry plant) was found at 65 °C, 400 bar. On reducing the temperature to 35 °C only slightly decreases this yield to 652 ± 8.4 μg g−1 of dry plant (Fig. 2A). Unsaturated fatty acids were obtained in greater amounts (100 μg g−1 of dry plant), at 35 °C, (400 bar), compared to 22 μg g−1 at 65 °C (400 bar) while the highest amount of unsaturated fatty acids was obtained at 50 °C, 238.5 bar. These results are in good correlation with the extraction of lipids from sorghum distillers grains with scCO2.39 Saturated fatty acids were selectively extracted with increased temperature; this contrasts with the trend of unsaturated fatty acids that decreased with increasing temperature. This is consistent with previous studies showing that the extraction efficiency of saturated fatty acids increases as higher temperatures and pressures are applied.15 The greatest concentration of oleic acid (C18:1), was obtained at 50 °C, 238 bar and that of linoleic acid (C18:2) were obtained by scCO2 extraction at 50 °C and 238 bar 96.6 ± 0.9 and 31.2 ± 1.2. The extraction of unsaturated fatty acids by scCO2 was significantly higher than that of hexane Soxhlet (24.6 ± 1.6 and 2.3 ± 0.4 μg g−1 of dry straw for oleic and linoleic acids respectively). Traditional solvent extraction with hexane was a more effective method in terms of total free fatty acid recovery as it was able to extract 1004.5 ± 15.7 μg g−1 of dry straw, whereas the maximum concentration obtained by scCO2 at 65 °C and 400 bar was 681.5 ± 10.37 μg g−1 of dry straw. However, scCO2 was seen to be the more selective method towards unsaturated fatty acids, 127.8 ± 2.1 and 26.9 ± 2.0 μg g−1 of dry straw obtained by scCO2 at 50 °C and 238 bar and hexane Soxhlet, respectively. Such a difference might be due to the ability of scCO2 to reduce the potential for further reactions, including oxidation.
Four n-alkanes were detected in the extracts, heptacosane (C27), nonacosane (C29), hentriacontane (C31) and tritriacontane (C33), which were also identified in the hexane extract. ScCO2 extraction at low pressures was not effective for the recovery of n-alkanes, as only 1–2 μg g−1 of dry straw were detected in the 75 bar, 35 °C or 65 °C extracts, both of which were low density (ESI, Table S8†). Higher concentrations of hydrocarbons were identified in the other three conditions investigated (Fig. 2B). There was no significant difference among them in terms of concentration; however, the greatest concentration of n-alkanes was obtained at 65 °C, 400 bar with 197.8 ± 1.8 μg g−1 of dry biomass, followed by scCO2 extraction at 50 °C, 238 bar with 193.3 ± 0.7 μg g−1 of dry biomass and then 35 °C, 400 bar with 182.6 ± 1.0 μg g−1 of dry biomass. Not only CO2 density played an important role in the amount of hydrocarbon extracted, but the temperature was also another key factor, which agreed with the study of extraction efficiency of aromatic hydrocarbons in scCO2.40 The extraction efficiency towards n-alkanes using scCO2 and hexane Soxhlet were comparable, 197.8 ± 1.8 μg g−1 of dry straw and 202.2 ± 1.1 μg g−1 of dry straw, respectively.
n-Policosanols (fatty alcohols) demonstrate a small decrease in yield at elevated extraction temperatures, but only represent a minor fraction of the wax extracted from rice straw. The total concentration of fatty alcohols in the lipid extract of rice straw from hexane Soxhlet was 111.0 ± 0.4 μg g−1, this concentration was lower compared to the scCO2 extract at 35 °C, 400 bar, 50 °C, 238 bar and 65 °C, 400 bar with 154.6 ± 0.4, 145.8 ± 2.1 and 129.3 ± 0.8 μg g−1 of rice straw respectively (Fig. 2C). The results in this study were in line with the comparative study, where the yield of alcohols in the scCO2 extract was higher than that of hexane.41,42 The dominant fatty alcohol in scCO2 extracts was 1-triacontanol, while the greatest amount of total fatty alcohol was recovered at high pressure (400 bar) and low temperature (35 °C). It was also reported that long chain fatty alcohols were effectively obtained when applying high pressure to a supercritical system.42
Long chain fatty alcohols, triacontanal (C30) and dotriacontanal (C32), were identified in rice straw extract in both hexane and scCO2 extracts (Fig. 2D). In scCO2 extraction, these two compounds were barely extractable at low pressure. However, in high pressure experiments, 35 °C, 400 bar and 50 °C, 238 bar and 65 °C, 400 bar, the total concentration obtained were comparable, 253.7 ± 2.7, 257.5 ± 5.0 and 257.4 ± 16.7 in μg g−1 of dry rice straw respectively. In contrast with hexane extract, as shown in Fig. 2D, there was no significant difference in terms of total fatty aldehydes presented in both extraction methods. Hexane extraction yielded a little higher concentration in fatty aldehydes. However, it was interesting to analyse each fatty aldehyde separately, as each condition yielded different concentrations of these compounds. In all extracts from hexane and scCO2, triacontanal (C30) was predominant. However, at 65 °C and 400 bar, a higher concentration of dotriacontanal (C32) was detected. Therefore, it was advantageous to selectively extract a component only by changing the temperature. The solubility of fatty aldehyde increased with temperature and pressure, as was observed in the scCO2 of sawdust.43
A great abundance of sterols, steroid ketones and wax esters was observed at the highest extraction temperature and pressure, consistent with previous scCO2 extractions of waxes (Fig. 3).15–17 The research demonstrated that the most abundant phytosterol obtained from rice straw was campesterol (Fig. 3A). This differs from other agricultural straw residues, such as those from wheat and triticale, which have β-sitosterol as the dominant phytosterol.15,44 Previous studies on rice straw extraction also indicated that β-sitosterol and stigmasterol accounted for 90% of the total sterols.11,14 Sterols were not extractable at low pressure; only 1 μg g−1 of dry straw was detected at 35 °C and 65 °C at 75 bar. The highest concentration identified among all the scCO2 extracts, was obtained at 65 °C, 400 bar, with 205.8 ± 0.7 μg g−1 of dry straw, followed by the extract recovered at 50 °C, 238 bar with 148.0 ± 0.4 μg g−1 of dry straw. This result was in good agreement with optimisation of scCO2 of triticale straw and wheat straw.15,44 As seen in Fig. 3B, hexane extraction demonstrated greater efficiency towards sterol extraction from rice straw. Steroid ketones including stigmast-4-en-3-one and 5α-stigmastane-3,6-dione, were identified and obtained in high concentrations, 330.7 ± 9.9 μg g−1 of dry straw with hexane Soxhlet extraction (Fig. 3B). With scCO2 extraction, the greatest yield for steroid ketones was 65 °C, 400 bar was 224.4 ± 6.1 μg g−1 of dry straw.
The predominant wax ester molecule in the rice straw extract was C46, consistent with the composition from the stem extract of maize.17 Wax esters were detected in low concentration in rice straw, with the greatest concentration from scCO2 being extracted at 65 °C and 400 bar, 255.3 ± 0.8 μg g−1 of dry straw (Fig. 3C). The conditions at low pressure were reconfirmed to be unsuitable to extract lipophilic compounds from rice straw, including wax esters.
The rice straw wax extracts could be utilised in various applications. In fact, scCO2 wax extracts of rice straw demonstrated a melting point range of between 66 to 81 °C (ESI, Fig. S1†). The elevated melting point range observed for scCO2 extracted wax may make it a suitable replacement for candelilla or carnauba waxes. Individual components of the extracts, including wax esters, have beneficial industrial applications as high-temperature lubricants, surface coatings and emulsifiers.45 n-Policosanols such as hexacosanol (C26), octacosanol (C28) and triacontanol (C30) found in rice straw wax have been promising for cardiovascular disease prevention and therapy as lowering-cholesterol and increasing low-density lipoprotein (LDL) levels.46,47
3.1.3 SEM analysis of scCO2 extracted rice straw. The SEM micrograms demonstrated changes in the surface morphology of rice straw before and after scCO2 extraction at 65 °C and 400 bar (Fig. 4). The surface of the untreated rice straw (a) was coated with the epicuticular wax. However, the scCO2 extracted one was clearly smooth (b), which confirmed that the wax was efficiently removed from the straw during the extraction. ScCO2 extraction has been reported as an alternative method of pre-treatment prior to enzymatic or thermochemical processes, as it increased the permeability of the biomass surface and influences the surface composition of elements, which leads to improved downstream processing.19,48 Previous studies have demonstrated a decrease in surface metal ion concentrations for K+ and Na+, in addition to Ca+, Mg+, Al+, and Si+ post scCO2 extraction of Scots pine tree fractions.19
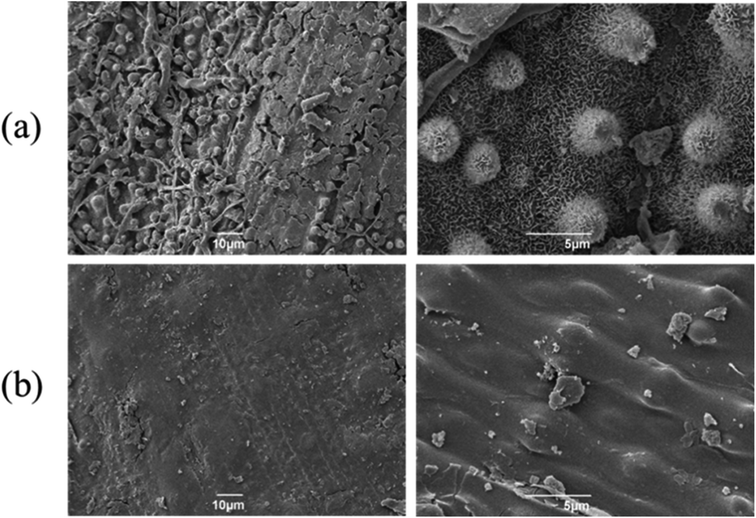 |
| Fig. 4 SEM micrograms of rice straw (a) before scCO2 extraction (b) after scCO2 extraction at 65 °C, 400 bar for 4 hours. | |
SEM results indicated that ScCO2 extraction demonstrated a high efficiency and selectivity to remove valuable phytochemicals without leaving any solvent residue in the rice straw. Therefore, the extracted straw is suitable for further uses in various applications. A combination of scCO2 extraction with a thermochemical process, such as microwave pyrolysis of the scCO2 extracted rice straw, could offer other high-value outcomes as it results in liquid, solid and gaseous products.31
3.2 A comparison of the microwave-assisted pyrolysis of untreated and scCO2 extracted rice straw
To study the effect of scCO2 extraction on the resulting products and thermal behaviour by microwave pyrolysis, both untreated and scCO2 extracted rice straw were investigated using fixed power mode at 300 W in a closed vessel microwave system. It was previously demonstrated that 300 W power provided the optimal MAP conditions for the highest energy densification ratio of solid residues.31 Other factors that influence the pyrolysis process including the effect of particle size were investigated. The products, including char, bio-oil, and gas, were analysed.
3.2.1 Temperature and pressure profiles. Fig. 5A illustrates the temperature profile of microwave pyrolysis of untreated and scCO2 extracted rice straw with six different particle sizes, <125 μm, 125–180 μm, 180–300 μm, 300–500 μm, 500–2000 μm and >2000 μm. The patterns of reaction temperature were identical in the two raw materials. Interestingly, there was a difference in the temperature profiles among the different particle sizes. In the case of the smaller particle sizes (particle sizes smaller than 500 μm), there was a sharp temperature increase in the first 100 seconds which plateaued at around 125–140 seconds, where final temperatures of above 250 °C were obtained. In contrast, the pyrolysis temperatures of the larger particle sizes (of the two materials, ≥500 μm) were terminated at the early heating stage (around 125 °C) due to a rapid increase in pressure (surpassing the safety pressure limit of 19.305 Bar) (Fig. 5B). This spontaneous increase in pressure was attributed to the generation of incondensable gases during the microwave pyrolysis process. Consequently, it can be concluded that particle size played an important role not only in reaction temperature, but also in the end products of the microwave pyrolysis of rice straw.
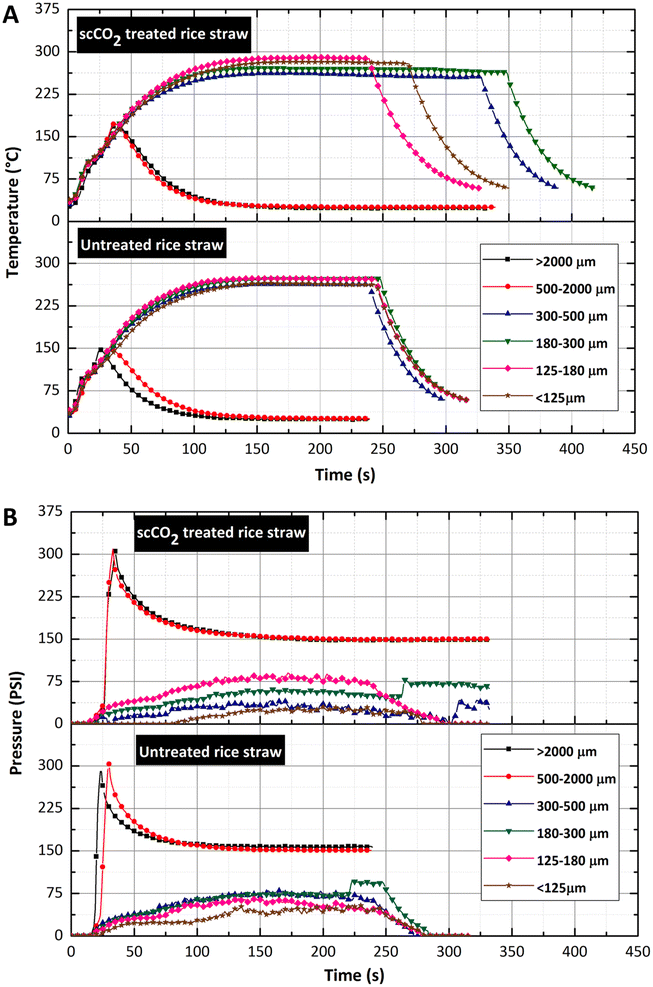 |
| Fig. 5 (A) Temperature and (B) pressure profiles of microwave pyrolysis of untreated and scCO2 extract rice straw with different particle sizes. (Sample mass 0.3 g, closed vessel, 300 W, fixed power mode). | |
3.2.2 Heating rates and maximal temperatures. The full comparison including the evolution of the heating rates and pressure change rates are illustrated in the ESI for all particle sizes (ESI, Fig. S2†). A summary of the heating rate and maximal temperature of microwave pyrolysis for untreated and scCO2 extracted rice straw is listed in Table 1. It was observed that the highest temperatures were reached with the particle size of <125 μm scCO2 extracted rice straw, followed by 125–180 μm and 180–300 μm with the highest temperature attained at 272–273 °C for both untreated and scCO2 extracted rice straw. For the particle size smaller than 500 μm, there was no significant difference in heating behaviours for both untreated and scCO2 extracted rice straw during microwave irradiation. In addition, samples having the particle size smaller than 500 μm also resulted in relatively low pressure change rates due to the absence of incondensable gas production during the process. The rate of pressure change indicated the level of biomass decomposition at a specific temperature. The untreated and scCO2 extracted rice straw with the particle size larger than 500 μm, including 500–200 and >2000 μm, possessed unique thermal behaviour towards the microwave irradiation resulting in not only high heating rates, but also the most significant pressure change rates. The rates of pressure change and their corresponding temperatures are summarised in Table 2.
Table 1 Heating rates and maximum temperatures reached in the microwave pyrolysis of untreated and scCO2 extracted rice straw
Particle size (μm) |
Heating rate (K min−1) |
Maximum temperature (°C) |
Untreated |
scCO2 extracted |
Untreated |
scCO2 extracted |
<125 |
180 |
180 |
265 |
282 |
125–180 |
180 |
180 |
273 |
272 |
180–300 |
210 |
210 |
272 |
273 |
300–500 |
210 |
240 |
262 |
263 |
500–2000 |
240 |
420 |
137 |
158 |
>2000 |
420 |
480 |
128 |
154 |
Table 2 Maximum rate of pressure change, and temperature reacted at maximum rate of pressure change in the microwave pyrolysis of untreated and scCO2 extracted rice straw
Particle size (μm) |
Maximum rate of pressure change (bar min−1) |
Temperature at maximum rate of pressure change (°C) |
Untreated |
scCO2 extracted |
Untreated |
scCO2 extracted |
<125 |
12.41 |
12.41 |
255 |
245 |
125–180 |
12.41 |
12.41 |
272 |
272 |
180–300 |
10.34 |
10.34 |
263 |
263 |
300–500 |
14.48 |
14.48 |
224 |
232 |
500–2000 |
219.25 |
256.49 |
126 |
137 |
>2000 |
364.04 |
287.51 |
116 |
119 |
The overall trend of heating rate increased with larger particle sizes. For the feed sizes of <125 μm, 125–180 μm, 180–300 μm, 300–500 μm, 500–2000 μm and >2000 μm, the rates of heating were 180, 180, 210, 210, 240 and 420 K min−1 respectively for untreated rice straw and 180, 180, 210, 240, 420 and 480 K min−1 respectively for scCO2 extracted rice straw. Importantly, the rate of heating in the microwave pyrolysis of rice straw was found to be exceptionally high, with a heating rate of 480 K min−1 in the largest feed size (>2000 μm). In contrast, the heating performances (150–240 K.min−1) were lower for the smaller particle size <500 μm than those of the larger sizes. Interestingly, the scCO2 extracted biomass with a size of 500–2000 μm, could retain high rates of heating at 420 K min−1, while the untreated straw exhibited a substantially lower heating rate at 270 K min−1 for the same microwave power 300 W. Thus, demonstrating that the extraction of waxes has a significant effect on the rate of heating and the efficiency of the microwave pyrolysis process. It can be concluded that scCO2 extraction of lipids from the rice straw surface enhances microwave pyrolysis. Such an effect could be explained by the inhibition of the pyrolysis by wax fractions and its influence on the dielectric properties of the feedstock. Therefore, wax removal by scCO2 extraction results high heating rates and greater maximum temperatures of pyrolysis. These results are significant in terms of large-scale microwave processing of scCO2 extracted biomass such as rice straw. Firstly, rapid heating rates lead to a switch from biochar and oil production to include extensive gas creation, leading to a rise in pressure that reaches the allowable limit and terminates the experiment. A large-scale microwave system for the microwave pyrolysis of scCO2 extracted rice straw particles >500 μm, would need to be carefully designed, operated, and monitored to control such processes for both safety and product distribution.
Previous studies demonstrated that the final temperature and the heating rate of microwave pyrolysis increased with decreasing particle size, due to the increase of bulk density and the contact area, which enhance heat transfer.33,49 This is in contrast with this current study, where the observed heating rate followed an opposite trend, and the maximal temperature was irrespective of size. scCO2 extracted biomass reached higher temperatures when a size-by-size comparison is made with untreated rice straw. In addition, greater heating rates were recorded for scCO2 extracted rice straw, demonstrating that the wax removal by scCO2 has an influence on the dielectric property of the rice straw, as the scCO2 extracted rice straw became a better microwave absorber with a constant high heating rate and in most cases a higher final temperature. This demonstrates that scCO2 extraction has a positive effect on the microwave pyrolysis process, further illustrating the benefits of introducing this technology within a holistic biorefinery.
3.2.3 Conventional vs. microwave pyrolysis. Thermogravimetric analysis (TG) of untreated and scCO2 extracted rice straw having different particle sizes were conducted to investigate the conventional heating pyrolysis processes compared to microwave pyrolysis. Generally, there are three main stages of decomposition in biomass pyrolysis: moisture evaporation, main devolatilization and continuous devolatilization.50,51 Rice straw is a lignocellulosic biomass consisting mainly of three types of biopolymers: hemicellulose, cellulose and lignin. The composition of cellulose, hemicellulose, and lignin of the rice straw in this study was 34%, 19% and 13% respectively. The hemicellulose of rice straw is generally the first to decompose up to a temperature of 250 °C, followed by the breakdown of cellulose at about 250–350 °C, both with significant mass loss rates. The lignin decomposition is the most complex as it occurs slowly from initial heating to 900 °C with a very low mass loss rate.52–54 The TG and DTG curves of untreated and scCO2 extracted rice straw, Fig. 6, showed a similar pattern. The first mass loss is a result of water evaporation. The decomposition of hemicellulose occurred at approximately 180 °C followed by cellulose decomposition to approximately 350 °C. The hemicellulose decomposition could not be clearly observed as it overlapped with the cellulose decomposition peak as seen in previous studies.53,54 The TG and DTG curves for all particle sizes (for both the untreated and scCO2 extracted rice straw) were similar. A maximum decomposition rate at 320–330 °C was observed (for all feed sizes), attributed to the decomposition of cellulose (the main component of the rice straw). This indicates that the particle size does not influence on the pyrolysis temperature in conventional heating and was consistent with the microwave process.
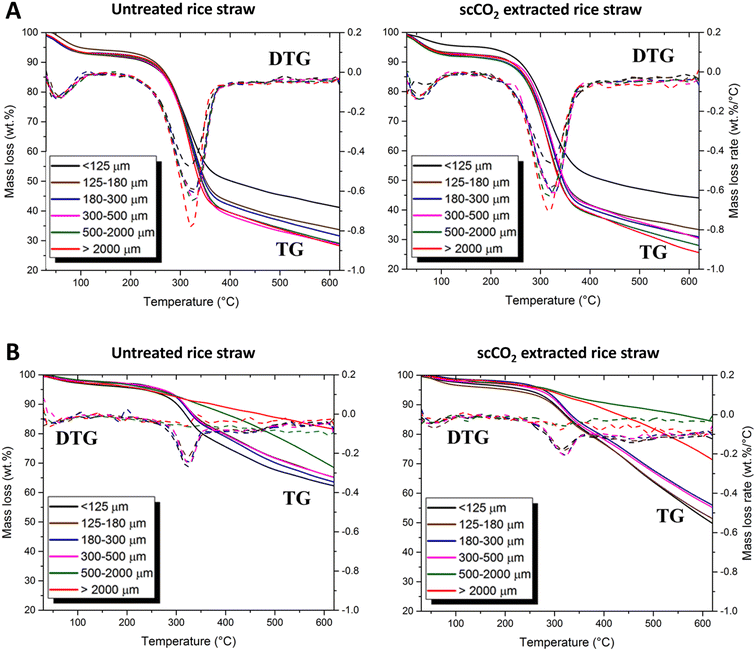 |
| Fig. 6 TG and DTG curves of (A) untreated and scCO2 extracted rice straw and (B) resulting bio-chars from microwave pyrolysis of untreated and scCO2 extracted rice straw. | |
Cellulose decomposition within the untreated and scCO2 extracted rice straw occurred at relatively low temperatures during the microwave pyrolysis, indicated by the production of incondensable gas (ESI Fig. S2†). This decomposition occurred at ∼120 °C (size > 2000 μm) and ∼130 °C (size 500–2000 μm), which were significantly lower than the 320 °C observed with conventional pyrolysis. To confirm that microwave heating is a promising alternative thermal method to conventional heating in a rice straw biorefinery, the solid chars were also analysed by TG to compare the thermal behaviour of the biomass before and after microwave pyrolysis. In the case of feed size >500 μm, the TG of the solid char showed that the peak of cellulose decomposition, ∼320 °C was no longer present. In contrast, in the case of particle size <500 μm, it was clearly visible even though the intensity sharply decreased. Importantly, this indicates that the complete decomposition of cellulose with microwave pyrolysis at a 120–130 °C (∼200 °C lower than conventional heating) for particle sizes larger than 500 μm. However, further investigation is needed for to better understand this from a mechanistic point of view.
3.2.4 Products distribution. Microwave pyrolysis of untreated and scCO2 extracted rice straw demonstrated that particle size significantly affected the product yields of bio-oil, char, and gas (Fig. 7). In the case of particles <500 μm, biochar was predominantly produced during microwave pyrolysis, yielding 50–60% dry weight, for both the untreated and scCO2 extracted biomass. The bio-oil yields were low, 6–9% dry weight and there was no incondensable gas generated during this thermal process. In contrast, the main product obtained for the microwave pyrolysis of the large rice straw particles sizes (≥500 μm) was the gas, with yields of 56–59% dry weight. This was coupled with significant decreases in solid char (approximately 25–32%) and a slight increase in bio-oil production (10–12%) (for both untreated and scCO2 extracted rice straw sized 500–2000 μm and >2000 μm). Huang et al. investigated the MAP of rice straw, in which a maximum of 50 wt% bio-oil was observed at 300 W power and significantly differs from the yields in this current study.31 It has also been reported that scCO2 extraction coupled with microwave activated gasification of spruce forestry residues demonstrated the enhanced production of fullerene-like soot nanoparticles and increased syngas yield.35 In contrast, the current study demonstrated no significant change in gas yield following scCO2 extraction, a slight increase in gas production was observed for 500–2000 μm, while the gas yield of the >2000 μm rice straw presented a small reduction. All particle sizes demonstrate an increase in bio-oil after extraction and in most cases a reduction in char yields were observed following scCO2. It was previously demonstrated that metals with the biomass could be extracted by scCO2 as fatty acid salts, thus enabling greater control over the product distribution by pyrolysis. According to ICP analysis, the rice straw investigated in this study demonstrated a high concentration of potassium (5108.0 μg g−1 of biomass) before extraction, reducing its surface concentration via scCO2 extraction in the form of fatty acid salts could lead to changes observed in product distribution.
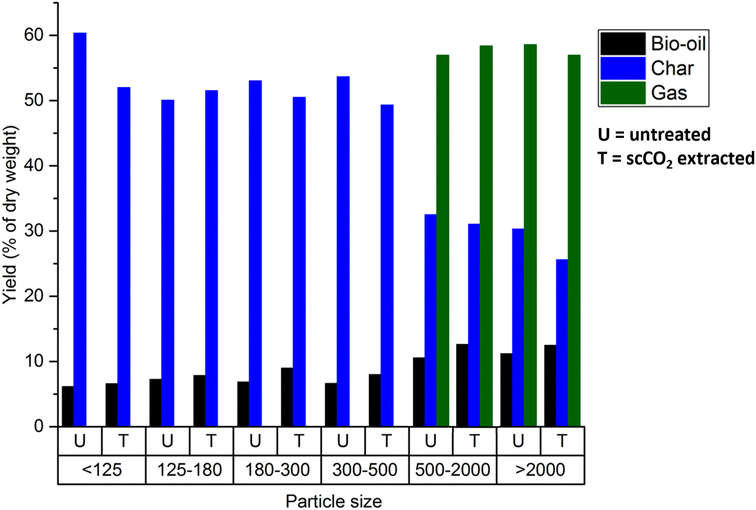 |
| Fig. 7 Pyrolytic Product distribution of untreated (U) and scCO2 extracted (T) rice straw. | |
As particle of 500–2000 μm demonstrated the production of bio-oil, biochar and bio-gas in the for both untreated and scCO2 extracted rice straw, this fraction was selected for qualitative analysis. The incondensable gaseous products generated were collected in a syringe and then analysed by FTIR. The composition of gas products from microwave pyrolysis of biomass such as wheat straw,55 coffee hulls,56 rice husk,30 and rice straw,34 are primarily composed of H2, CH4, CO, CO2, and some short chain hydrocarbons. Fig. 8 shows the FTIR spectra of the gas phases of the two feedstocks, the major components of product gases from rice straw microwave pyrolysis were CO, CO2, CH4, C1–C2 hydrocarbons, and some carbonyl-containing gases. The result obtained were consistent with previous studies with conventional heating,53,54 and with microwave heating.34 The gas composition of the untreated and scCO2 extracted rice straw was identical, confirming that this extraction method has no adverse effect on the biomass and can be used as a pre-treatment step in a holistic biorefinery of rice straw. Interestingly, certain gases such as CH4 and some light hydrocarbons were previously reported to be obtained at temperatures >400 °C, in contrast their formation was achieved at a lower temperature within the microwave pyrolysis system.33,52–54
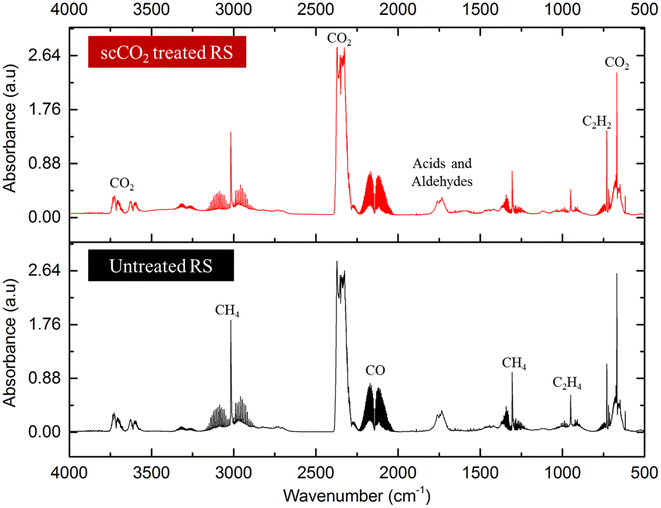 |
| Fig. 8 FT-IR gas product from microwave pyrolysis of scCO2 extracted (above) and untreated rice straw (below). | |
Two liquid fractions were obtained from the rice straw microwave pyrolysis and organic soluble fraction was analysed by HT-GC-MS without further purification (Fig. 9). A range of phenolic lignin breakdown products were identified including 2-methoxy-phenol, 2- and 3-methyl-phenol, 2,6-dimethyl-phenol, and 4-vinyl-2-methoxy-phenol. It has been confirmed that some aromatic and polycyclic aromatic compounds included naphthalene, anthracene and phenanthrene were identified in the microwave pyrolysis oil. The presence of these molecules was in good agreement with the results of previous studies.54,57,58 The aqueous fraction contained a range of anhydrase sugars and cellulose breakdown products.
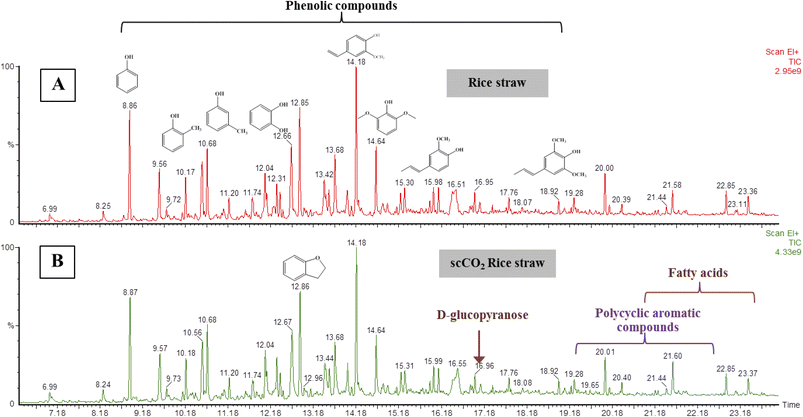 |
| Fig. 9 HT-GC-MS chromatograms of bio-oil of liquid fractions of (A) untreated and (B) scCO2 extracted rice straw. | |
The elemental analysis of the biomass showed a significant increase in the percentage of C and a decrease in H (Table 3). However, there was no significant difference between the untreated and scCO2 extracted rice straw. The gross caloric value of the solid residues was 18.7 and 18.5 MJ kg−1 in untreated and scCO2 extracted rice straw respectively, which were notably higher when compared to the starting biomasses (typically 15 MJ kg−1) making them useful for large scale energy production. These gross caloric value are consistent with those previously published for microwave assisted pyrolysis of rice straw.31 This demonstrates that microwave pyrolysis could be a viable technology to produce chemicals and fuels within a rice straw biorefinery.
Table 3 Characteristics of untreated and scCO2 extracted rice straw pre and post microwave pyrolysis
Elemental analysis (wt%) |
Before pyrolysis |
After pyrolysis |
Untreated rice straw |
scCO2 extracted rice straw |
Untreated rice straw |
scCO2 extracted rice straw |
C |
38.9 |
40.5 |
48.5 |
51.1 |
H |
5.2 |
5.3 |
1.9 |
1.6 |
N |
0.3 |
0.3 |
0.2 |
0.3 |
Calorific value (MJ kg−1) |
15.8 |
15.5 |
18.7 |
18.5 |
ScCO2 extraction serves as an effective pre-treatment step to provide enhanced interactions between microwaves and the resulting extracted biomass. In addition, greater heating rates were recorded in experiments in the case of scCO2 treated rice straw. These results indicate that the wax removal by scCO2 has an influence on the dielectric property of the rice straw, as the scCO2 treated rice straw became a better microwave absorber with a constant high heating rate and higher final temperature. This therefore shows that scCO2 extraction has a positive effect on the microwave pyrolysis process, further illustrating the benefits of introducing this technology within a holistic biorefinery. However, for such processes to be commercially viable carefully design, and operation of microwave pyrolysis in flow would be needed. In addition, steps must be taken to control rapid heating and gas evolution from both a safety viewpoint and for the tuning of product distribution. Microwave pyrolysis of particle greater than 500 μm demonstrated almost complete decomposition of cellulose at low temperatures, 120–130 °C. Importantly, this is ∼200 °C lower than conventional heating, which could lead to significant reduction in energy usage for the decomposition of cellulose in rice straw. However, better mechanistic understanding of this process is warranted to enable the full exploitation at a commercial scale.
4 Conclusions
The optimisation of scCO2 extraction of wax from rice straw was successfully achieved whereby the highest yields were obtained at 65 °C and 400 bar, 0.7% dry weight. This is comparable to Soxhlet extractions with hexane (1% dry weight). Various high value compounds including n-policosanols, wax esters, fatty aldehydes, and steroid ketones were present in high concentrations in the rice straw wax. These compounds have potential use in industrial applications such as lubricants, surface coating and pharmaceutical uses. The waxes obtained from scCO2, and hexane demonstrated similar compositions and quantities of the major lipophilic groups of compounds. The microwave pyrolysis of untreated and scCO2 extracted rice straws were investigated. The effect of particle size on the microwave pyrolysis process was also investigated. It was found that scCO2 extraction had a positive effect on the microwave pyrolysis of the rice straw, having a significant beneficial effect on the rate of heating with increased particle size (420 K min−1 for particle sizes of 500–2000 μm) when compared to untreated rice straw (270 K min−1 for particle sizes of 500–2000 μm). There was no significant difference between the untreated and scCO2 extracted rice straw in the product distribution of char, gas, and bio-oil, thus highlighting that, importantly, scCO2 extraction has no adverse effects on products obtained from the pyrolysis. Particle size had a significant effect on the decomposition of cellulose and the distribution of products (gaseous, liquid and char) for both the untreated and scCO2 extracted rice straw. For particle sizes >500 μm there was no cellulose decomposition peak in the DTG of the solid char obtained from microwave pyrolysis while a cellulose decomposition peak is present in the solid char for particle sizes <500 μm. This indicates that for particles sizes >500 μm, cellulose decomposition occurs at 120–130 °C, which is around ∼200 °C lower than conventional heating. Such results demonstrate that the application of both scCO2 extraction and microwave assisted pyrolysis in combination, offer exciting opportunities for sustainable and energy efficient processes for the valorisation of rice straw within a holistic biorefinery.
Conflicts of interest
There are no conflicts to declare.
Acknowledgements
Chanettee Sikhom gratefully acknowledges funding through The Oil Refinery Contract Contribution Fund and the Ministry of Energy, Thailand. This research was supported by the Fundamental Fund of Khon Kaen University. The research on “Valorisation of low value sugarcane residues through a development of sustainable advanced materials and biofuels” by Khon Kaen University, Department of Chemistry, has received funding support from the National Science, Research, and Innovation Fund. This project is funded by National Research Council of Thailand (NRCT) (Grant number: No. 42A650240). The Center of Excellence for Innovation in Chemistry (PERCH-CIC), Ministry of Higher Education, Science, Research, and Innovation is also gratefully acknowledged.
References
- International Rice Research Institution, Rice Straw Energy Project, https://irri.org/networks/rice-straw-project, accessed 10/05/2023 Search PubMed.
- D. A. Bossio, W. R. Horwath, R. G. Mutters and C. Van Kessel, Methane pool and flux dynamics in a rice field following straw incorporation, Soil Biol. Biochem., 1999, 31(9), 1313–1322, DOI:10.1016/S0038-0717(99)00050-4.
- S. Tripathi, R. N. Singh and S. Sharm, Emissions from Crop/Biomass Residue Burning Risk to Atmospheric Quality, Int. Res. Earth Sci., 2013, 1, 24–30 Search PubMed.
- B. Gadde, S. Bonnet, C. Menke and S. Garivait, Air pollutant emissions from rice straw open field burning in India, Thailand and the Philippines, Environ. Pollut., 2009, 157(5), 1554–1558, DOI:10.1016/j.envpol.2009.01.004.
- Y. Miura and T. Kanno, Emission of trace gases (CO2, CO, CH4, and N2O) resulting from rice straw burning, Soil Sci. Plant Nutr., 1997, 43(4), 849–854, DOI:10.1080/00380768.1997.10414651.
- N. T. Kim Oanh, B. T. Ly, D. Tipayarom, B. R. Manandhar, P. Prapat, C. D. Simpson and L. J. Sally Liu, Characterization of particulate matter emission from open burning of rice straw, Atmos. Environ., 2011, 45(2), 493–502, DOI:10.1016/j.atmosenv.2010.09.023.
- T. M. Attard, N. Bukhanko, D. Eriksson, M. Arshadi, P. Geladi, U. Bergsten, V. L. Budarin, J. H. Clark and A. J. Hunt, Supercritical extraction of waxes and lipids from biomass: A valuable first step towards an integrated biorefinery, J. Clean. Prod., 2018, 177, 684–698, DOI:10.1016/j.jclepro.2017.12.155.
- B. Ritter, J. Schulte, E. Schulte and H. P. Thier, Detection of coating waxes on apples by differential scanning calorimetry, Eur. Food Res. Technol., 2001, 212(5), 603–607, DOI:10.1007/s002170100290.
- J. L. Hargrove, P. Greenspan and D. K. Hartle, Nutritional significance and metabolism of very long chain fatty alcohols and acids from dietary waxes, Exp. Biol. Med., 2004, 229(3), 215–226, DOI:10.1177/153537020422900301.
- H. Wei, An overview of wax production, requirement and supply in the world market, Eur. Chem. Bull., 2012, 1(7), 266–268, DOI:10.17628/ECB.2012.1.266.
- R. Sun, X. F. Sun and B. Xiao, Extraction and Characterization of Lipophilic Extractives From Rice Straw. Ii. Spectroscopic and Thermal Analysis, J. Wood Chem. Technol., 2002, 22(1), 1–9, DOI:10.1081/WCT-120004430.
- J. M. DeSimone, Practical approaches to green solvents, Science, 2002, 297(5582), 799–803, DOI:10.1126/science.1069622.
- P. S. Spencer and H. H. Schaumburg, Neurotoxic Properties of Certain Aliphatic Hexacarbons, Proc. R. Soc. Med., 1977, 70, 37–39 CAS.
- B. Xiao, X. F. Sun and R. Sun, Extraction and characterization of lipophilic extractives from rice straw. i. chemical composition, J. Wood Chem. Technol., 2001, 21(4), 397–411, DOI:10.1081/WCT-100108334.
- E. H. K. Sin, R. Marriott, A. J. Hunt and J. H. Clark, Identification, quantification and Chrastil modelling of wheat straw wax extraction using supercritical carbon dioxide, Compt. Rendus Chem., 2014, 17(3), 293–300, DOI:10.1016/j.crci.2013.12.001.
- T. M. Attard, C. R. McElroy, R. J. Gammons, J. M. Slattery, N. Supanchaiyamat, C. L. A. Kamei, O. Dolstra, L. M. Trindade, N. C. Bruce and S. J. McQueen-Mason, et al., Supercritical CO2 Extraction as an Effective Pretreatment Step for Wax Extraction in a Miscanthus Biorefinery, ACS Sustain. Chem. Eng., 2016, 4(11), 5979–5988, DOI:10.1021/acssuschemeng.6b01220.
- T. M. Attard, E. Theeuwes, L. D. Gomez, E. Johansson, I. Dimitriou, P. C. Wright, J. H. Clark, S. J. McQueen-Mason and A. J. Hunt, Supercritical
extraction as an effective first-step in a maize stover biorefinery, RSC Adv., 2015, 5(54), 43831–43838, 10.1039/C5RA07485A.
- M. Herrero, J. A. Mendiola, A. Cifuentes and E. Ibanez, Supercritical fluid extraction: Recent advances and applications, J. Chromatogr. A, 2010, 1217(16), 2495–2511, DOI:10.1016/j.chroma.2009.12.019.
- A. Trubetskaya, T. M. Attard, V. L. Budarin, A. J. Hunt, M. Arshadi and J. Grams, Supercritical Extraction of Biomass - A Green and Sustainable Method to Control the Pyrolysis Product Distribution, ACS Sustain. Chem. Eng., 2021, 9(15), 5278–5287, DOI:10.1021/acssuschemeng.0c08599.
- Y. Liu, P. E. N. G. Luo, Q. Q. Xu, E. J. Wang and J. Z. Yin, Investigation of the effect of supercritical carbon dioxide pretreatment on reducing sugar yield of lignocellulose hydrolysis, Cellul. Chem. Technol., 2014, 48(1–2), 89–95 CAS.
- S. Fraterrigo Garofalo, N. Cavallini, R. Destefano, M. Micera, C. Cavagnero, A. Botto, F. Savorani, T. Tommasi and D. Fino, Optimization of Supercritical Carbon Dioxide Extraction of Rice Bran Oil and γ-Oryzanol Using Multi-Factorial Design of Experiment, Waste Biomass Valor, 2023, DOI:10.1007/s12649-023-02111-w.
- A. Kayathi, P. P. Chakrabarti, L. Bonfim-Rocha, L. Cardozo-Filho, A. Bollampalli and V. Jegatheesan, Extraction of γ-Oryzanol from defatted rice bran using supercritical carbon dioxide (SC-CO2): process optimisation of extract yield, scale-up and economic analysis, Process Saf. Environ. Prot., 2021, 148, 179–188, DOI:10.1016/j.psep.2020.09.067.
- M. Gao, F. Xu, S. Li, X. Ji, S. Chen and D. Zhang, Effect of SC-CO2 pretreatment in increasing rice straw biomass conversion, Biosyst. Eng., 2010, 106(4), 470–475, DOI:10.1016/j.biosystemseng.2010.05.011.
- K. N. Yogalakshmi, P. T. Devi, P. Sivashanmugam, S. Kavitha, Y. R. Kannah, S. Varjani, S. AdishKumar, K. Gopalakrishnan and R. J. Banu, Lignocellulosic biomass-based pyrolysis: a comprehensive review, Chemosphere, 2022, 286, 131824, DOI:10.1016/j.chemosphere.2021.131824.
- O. Farobie, A. Amrullah, A. Bayu, N. Syaftika, L. A. Anisb and E. Hartulistiyoso, In-depth study of bio-oil and biochar production from macroalgae Sargassum sp. via slow pyrolysis, RSC Adv., 2022, 12, 9567, 10.1039/D2RA00702A.
- A. Trubetskaya, V. Budarin, M. Arshadi, D. Magalhaes, F. Kazanç and A. J. Hunt, Supercritical extraction of biomass as an effective pretreatment step for the char yield control in pyrolysis, Renewable Energy, 2021, 170, 107–117, DOI:10.1016/j.renene.2021.01.116.
- X. Zhao, W. Wang, H. Liu, C. Ma and Z. Song, Microwave pyrolysis of wheat straw: product distribution and generation mechanism, Bioresour. Technol., 2014, 158, 278–285, DOI:10.1016/j.biortech.2014.01.094.
- A. Domínguez, J. A. Menéndez, Y. Fernández, J. J. Pis, J. M. V. Nabais, P. J. M. Carrott and M. M. L. R. Carrott, Conventional and microwave induced pyrolysis of coffee hulls for the production of a hydrogen rich fuel gas, J. Anal. Appl. Pyrolysis, 2007, 79(1–2), 128–135, DOI:10.1016/j.jaap.2006.08.003.
- X. Zhao, Z. Song, H. Liu, Z. Li, L. Li and C. Ma, Microwave pyrolysis of corn stalk bale: apromising method for direct utilization of large-sized biomass and syngas production, J. Anal. Appl. Pyrolysis, 2010, 89(1), 87–94, DOI:10.1016/j.jaap.2010.06.001.
- A. A. Salema and F. N. Ani, Microwave induced pyrolysis of oil palm biomass, Bioresour. Technol., 2011, 102(3), 3388–3395 CrossRef CAS PubMed.
- S. Zhang, Q. Dong, L. Zhang and Y. Xiong, High quality syngas production from microwave pyrolysis of rice husk with char-supported metallic catalysts, Bioresour. Technol., 2015, 191, 17–23 CrossRef CAS PubMed.
- Y. F. Huang, P. Te Chiueh, W. H. Kuan and S. L. Lo, Microwave pyrolysis of rice straw: products, mechanism, and kinetics, Bioresour. Technol., 2013, 142, 620–624 CrossRef CAS PubMed.
- A. E. Pütün, E. Apaydm and E. Pütün, Rice straw as a bio-oil source via pyrolysis and steam pyrolysis, Energy, 2004, 29(12–15), 2171–2180 CrossRef.
- Y. F. Huang, W. H. Kuan, S. L. Lo and C. F. Lin, Total recovery of resources and energy from rice straw using microwave-induced pyrolysis, Bioresour. Technol., 2008, 99(17), 8252–8258 CrossRef CAS PubMed.
- Y. F. Huang, W. H. Kuan, S. L. Lo and C. F. Lin, Hydrogen-rich fuel gas from rice straw via microwave-induced pyrolysis, Bioresour. Technol., 2010, 101(6), 1968–1973 CrossRef CAS PubMed.
- A. Trubetskaya, A. J. Hunt, V. L. Budarin, T. M. Attard, J. Kling, G. R. Surup, M. Arshadi and K. Umeki, Supercritical extraction and microwave activation of wood wastes for enhanced syngas production and generation of fullerene-like soot particles, Fuel Process. Technol., 2021, 212, 106633, DOI:10.1016/j.fuproc.2020.106633.
- M. Kane, J. R. Dean, S. M. Hitchen, C. J. Dowle and R. L. Tranter, Experimental design approach for supercritical fluid extraction, Anal. Chim. Acta, 1993, 271(1), 83–90 CrossRef.
- J. a. Hyatt, Liquid and supercritical carbon dioxide as organic solvents, J. Org. Chem., 1984, 49(26), 5097–5101 CrossRef CAS.
- L. Wang, C. L. Weller, V. L. Schlegel, T. P. Carr and S. L. Cuppett, Comparison of supercritical CO2 and hexane extraction of lipids from sorghum distillers grains, Eur. J. Lipid Sci. Technol., 2007, 109(6), 567–574 CrossRef CAS.
- J. J. Langenfeld, S. B. Hawthorne, D. J. Miller and J. Pawliszyn, Summarizing the Effectiveness of Supercritical Fluid Extraction of Polycyclic Aromatic Hydrocarbons from Natural Matrix Environmental Samples, Anal. Chem., 1993, 65, 338–344, DOI:10.1021/ac980618f.
- A. de Lucas, A. García, A. Alvarez and I. Gracia, Supercritical extraction of long chain n-alcohols from sugar cane crude wax, J. Supercrit. Fluids, 2007, 41, 267–271, DOI:10.1016/j.supflu.2006.09.013.
- Y. Athukorala and G. Mazza, Optimization of extraction of wax from flax straw by supercritical carbon dioxide, Sep. Sci. Technol., 2011, 46, 247–253, DOI:10.1080/01496395.2010.514014.
- T. M. Attard, M. Arshadi, C. Nilsson, V. L. Budarin, E. Valencia-Reyes, J. H. Clark and A. J. Hunt, Impact of supercritical extraction on solid fuel wood pellet properties and off-gassing during storage, Green Chem., 2016, 2682–2690, 10.1039/C5GC02479J.
- Y. Athukorala and G. Mazza, Supercritical carbon dioxide and hexane extraction of wax from triticale straw: Content, composition and thermal properties, Ind. Crops Prod., 2010, 31(3), 550–556, DOI:10.1016/j.indcrop.2010.02.011.
- S. Reiser and C. Somerville, Isolation of mutants of Acinetobacter calcoaceticus deficient in wax ester synthesis and complementation of one mutation with a gene encoding a fatty acyl coenzyme A reductas, J. Bacteriol., 1997, 179(9), 2969–2975 CrossRef CAS PubMed.
- K. A. Varady, Y. Wang and P. J. H. Jones, Role of policosanols in the prevention and treatment of cardiovascular disease, Nutr. Rev., 2003, 61(11), 376–383 CrossRef PubMed.
- C. P. F. Marinangeli, P. J. H. Jones, A. N. Kassis and M. N. Eskin, Policosanols as nutraceuticals: fact or fiction, Crit. Rev. Food Sci. Nutr., 2010, 50(3), 259–267 CrossRef CAS PubMed.
- G. Qi, F. Peng, L. Xiong, X. Lin, C. Huang, H. Li, X. Chen and X. Chen, Extraction and characterization of wax from sugarcane bagasse and the enzymatic hydrolysis of dewaxed
sugarcane bagasse, Prep. Biochem. Biotechnol., 2017, 47(3), 276–281, DOI:10.1080/10826068.2016.1224246.
- M. J. Wang, Y. F. Huang, P. T. Chiueh, W. H. Kuan and S. L. Lo, Microwave-induced torrefaction of rice husk and sugarcane residues, Energy, 2012, 37(1), 177–184 CrossRef CAS.
- S. Munir, S. S. Daood, W. Nimmo, A. M. Cunliffe and B. M. Gibbs, Thermal analysis and devolatilization kinetics of cotton stalk, sugar cane bagasse and shea meal under nitrogen and air atmospheres, Bioresour. Technol., 2009, 100(3), 1413–1418 CrossRef CAS PubMed.
- S. S. Idris, N. A. Rahman, K. Ismail, A. B. Alias, Z. A. Rashid and M. J. Aris, Investigation on thermochemical behaviour of low rank Malaysian coal, oil palm biomass and their blends during pyrolysis via thermogravimetric analysis (TGA), Bioresour. Technol., 2010, 101(12), 4584–4592 CrossRef CAS PubMed.
- H. Yang, R. Yan, H. Chen, D. H. Lee and C. Zheng, Characteristics of hemicellulose, cellulose and lignin pyrolysis, Fuel, 2007, 86(12–13), 1781–1788 CrossRef CAS.
- C. Song, A. Pawłowski, A. Ji, S. Shan and Y. Cao, Catalytic pyrolysis of rice straw and product analysis, Environ. Prot. Eng., 2014, 40(1), 35–43 CAS.
- S. H. Jung, B. S. Kang and J. S. Kim, Production of bio-oil from rice straw and bamboo sawdust under various reaction conditions in a fast pyrolysis plant equipped with a fluidized bed and a char separation system, J. Anal. Appl. Pyrolysis, 2008, 82(2), 240–247 CrossRef CAS.
- X. Zhao, M. Wang, H. Liu, L. Li, C. Ma and Z. Song, A microwave reactor for characterization of pyrolyzed biomass, Bioresour. Technol., 2012, 104, 673–678 CrossRef CAS PubMed.
- J. A. Menéndez, A. Domínguez, Y. Fernández and J. J. Pis, Evidence of Self-Gasification during the Microwave-Induced Pyrolysis of Coffee Hulls, Energy Fuels, 2007, 21(1), 373–378 CrossRef.
- C. A. Mullen, A. A. Boateng, N. M. Goldberg, I. M. Lima, D. A. Laird and K. B. Hicks, Bio-oil and bio-char production from corn cobs and stover by fast pyrolysis, Biomass Bioenergy, 2010, 34(1), 67–74 CrossRef CAS.
- D. Mohan, C. U. Pittman and P. H. Steele, Pyrolysis of wood/biomass for bio-oil: a critical review, Energy Fuel., 2006, 20(3), 848–889 CrossRef CAS.
|
This journal is © The Royal Society of Chemistry 2024 |
Click here to see how this site uses Cookies. View our privacy policy here.