DOI:
10.1039/D3NA00318C
(Paper)
Nanoscale Adv., 2024,
6, 2431-2446
Fe3O4@SiO2@SBA-3@CPTMS@Arg-Cu: preparation, characterization, and catalytic performance in the conversion of nitriles to amides and the synthesis of 5-substituted 1H-tetrazoles†
Received
10th May 2023
, Accepted 15th October 2023
First published on 26th March 2024
Abstract
A novel, efficient, and recyclable mesoporous Fe3O4@SiO2@SBA-3@CPTMS@Arg-Cu nanocatalyst was synthesized by grafting L-arginine (with the ability to coordinate with Cu) onto a mixed phase of a magnetic mesoporous SBA-3 support. The catalyst was characterized using several techniques, including Fourier-transform infrared (FT-IR) spectroscopy, thermogravimetric analysis (TGA), vibrating sample magnetometry (VSM), X-ray diffraction (XRD) analysis, N2 adsorption–desorption analysis, scanning electron microscopy (SEM), X-ray photoelectron spectroscopy (XPS), energy dispersive X-ray (EDX) analysis, and atomic absorption spectroscopy (AAS). The resulting solid material possessed a surface area of 145 m2 g−1 and a total pore volume of 34 cm3 g−1. The prepared mesoporous material was studied as a practical, recyclable, and chemoselective catalyst in some organic functional group transformations such as the conversion of nitriles to amides and synthesis of 5-substituted 1H-tetrazoles. This novel magnetic nanocatalyst proved to be effective and provided the products in high to excellent yields under green solvent conditions. Meanwhile, the as-prepared Fe3O4@SiO2@SBA-3@CPTMS@Arg-Cu demonstrated excellent reusability and stability under reaction conditions, and its catalytic activity shown only a slight decrease after seven consecutive runs. Therefore, the as-synthesized magnetic Fe3O4@SiO2@SBA-3@CPTMS@Arg-Cu has broad prospects for practical applications, and offers various benefits such as simplicity, nontoxicity, low cost, simple work-up, and an environmentally benign nature.
1. Introduction
The existence of larger mesopores plays a key role in enhancing activity efficiency, as it leads to the formation of metals with larger sizes, resulting in less metal–support interaction, which is more favorable for reaction. In recent years, various types of mesoporous materials such as mobile crystalline materials (MCM-48, MCM 41, and MCM-50)1 and SBA-type materials (SBA-15, SBA-3)2 have been developed. These materials have found critical applications in various fields3–9 due to their unique properties such as high surface areas and well-ordered large pore systems. Among the SBA-type materials, several catalytic reactions using SBA-15 as a support for metal active phases have been investigated and showed promising results.9–13 Moreover, due to the contribution of some micropores connecting the mesopores, SBA-15 silica mesoporous materials with a more regular structure and thicker walls were shown to have much higher stability than MCM-41.14 SBA-3 (pore diameter > 3 nm) and SBA-1 (pore diameter > 2 nm) can contain some micropores too.15 However, the microporosity of SBA-3 is higher than that of SBA-15 (ref. 15) but with similar thermal and hydrothermal resistances.15 In the literature, applications of SBA-3 as a catalyst support are rare.16,17 However, special attention has been focused on the preparation of various magnetic nanostructures owing to their unique characteristics and potential applications in various fields.18–23 The immobilization of magnetic nanoparticles coated with mesoporous materials is of considerable technological importance from both economic and the environmental point of views. The separation of magnetic catalysts via magnetic separation is an attractive alternative to filtration or centrifugation for separating solid catalysts. Tetrazoles are a class of synthetic organic heterocyclic compounds that have numerous applications, especially in the fields of medicine,24 biochemistry,25 pharmacology,26 and in industry as materials,27e.g., in photography,28 imaging chemicals,29 and the military.30 Various methods have been reported in the literature for the preparation of tetrazoles.31 A general and versatile procedure for the preparation of tetrazole is based on [3 + 2] cycloaddition of an azide ion and organic nitriles in the presence of a catalyst.32–35 However, the disadvantages of this method compared with other methods include the typically long reaction times, use of expensive and toxic reagents and high boiling solvents, harsh reaction conditions, low yield, and tedious work-up, which lead to unavoidable environmental and safety problems. In contrast, amides are an important key intermediate in many organic transformations that are widely applied in medicine,36,37 biochemistry,38 and materials science.39 Various approaches have been used to synthesize amides, such as condensation of carboxylic acid and esters with amines,40 reaction between alcohols/aldehydes with amines,41 and hydroamination of unsaturated hydrocarbons.42 Besides these methods, a practical method to form amides is the hydration of nitriles.43 Moreover, nitrile hydration reactions are atom-efficient and allow avoiding the generation of environmental waste. Based on these advantages, the hydration of nitriles to amides is a well-established method in the pharmaceutical industry for the synthesis of various amides for large-scale production. Various catalysts have been explored, including the commonly used strong acids and bases.44,45 However, the use of these acidic reagents in many cases may not be appropriate, particularly for compounds possessing acid-sensitive substrates. Herein, we introduce a facile synthesis approach for the preparation of Fe3O4@SiO2@SBA-3@CPTMS@Arg-Cu by grafting L-arginine (with the ability to coordinate with Cu) onto a mixed phase of a magnetic mesoporous SBA-3 support as a novel and magnetically recoverable heterogeneous catalyst. The green and environmentally sustainable nature of the prepared catalyst is a suitable factor for developing this composite material. One of the major advantages of the present study is that it demonstrates an eco-friendly and cost-effective method for the conversion of nitriles to amides and for the synthesis of 5-substituted 1H-tetrazoles. Furthermore, using a high surface area material has a synergistic effect that significantly enhances the catalyst performance. Moreover, the catalyst could be easily recovered by a facile separation process via magnetic forces and recycled several times without significant loss of its catalytic activity. Synthetic steps for the preparation of the catalyst are shown in Scheme 1.
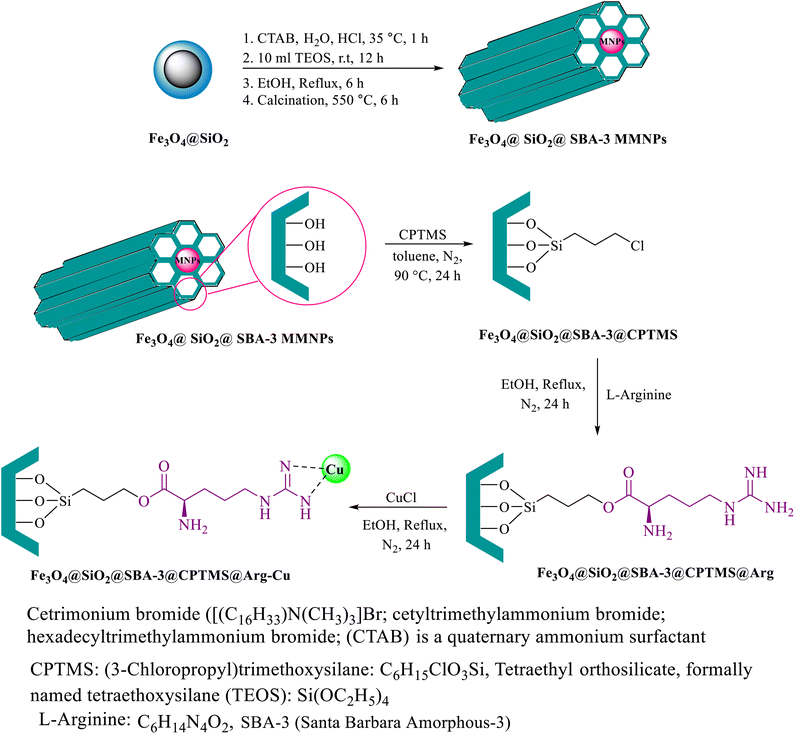 |
| Scheme 1 Preparation of Fe3O4@SiO2@SBA-3@CPTMS@Arg-Cu. | |
2. Experimental
2.1. Preparation of Fe3O4@SiO2@SBA-3@CPTMS@Arg-Cu
Fe3O4@SiO2@SBA-3 was readily synthesized in a similar way to a previously reported work.17 Briefly, 1.00 g of the obtained Fe3O4@SiO2@SBA-3 powder was dispersed in a mixture of 25 mL of toluene using sonication for 30 min, and 1.5 mL of (3-chloropropyl)triethoxysilane (CPTES) was then added to the mixture. The reaction mixture was stirred at 90 °C for 24 h. Then, the prepared Fe3O4@SiO2@SBA-3@CPTMS was filtered, washed with ethanol (70% v/v), and dried at room temperature. The obtained Fe3O4@SiO2@SBA-3@CPTMS (1 g) was dispersed in ethanol (25 mL in 20 min), and then L-arginine (2 mmol) was added to the reaction mixture and stirred (24 h at 80 °C). Then, the resulting nanoparticles (Fe3O4@SiO2@SBA-3@CPTMS@Arg) were filtered, washed with ethanol (70% v/v), and dried at room temperature. The obtained Fe3O4@SiO2@SBA-3@CPTMS@Arg (0.5 g) was dispersed in 25 mL of ethanol (70% v/v) by sonication for 20 min, and then copper(I) chloride (2 mmol) was added to the reaction mixture. The reaction mixture was stirred at 80 °C for 24 h. Finally, a brown-colored product [Fe3O4@SiO2@SBA-3@CPTMS@Arg-Cu] was obtained after filtering, washing using ethanol (70% v/v), and drying at room temperature.
2.2. General procedure for the conversion of nitriles to amides
A mixture of nitrile (1 mmol), potassium hydroxide (2 mmol), and Fe3O4@SiO2@SBA-3@CPTMS@Arg-Cu (40 mg) in water was heated at 75 °C for an appropriate period. The reaction progress was monitored through TLC. After the completion of the reaction, the precipitate was extracted with ethyl acetate, washed with double-distilled water, dried over Na2SO4, concentrated under reduced pressure, and finally purified by column chromatography on silica gel using hexane
:
ethylacetate (4
:
1) to afford the desired product.
2.3. General procedure for the synthesis of 5-substituted 1H-tetrazoles
A mixture of nitrile (1 mmol), sodium azide (1.1 mmol), and Fe3O4@SiO2@SBA-3@CPTMS@Arg-Cu (40 mg) in polyethylene glycol was heated at 120 °C for an appropriate period. The reaction progress was monitored through TLC. After the completion of the reaction (monitored by TLC), the precipitate was extracted with ethyl acetate, washed with double-distilled water, dried over Na2SO4, concentrated under reduced pressure, and purified by column chromatography on silica gel using hexane
:
ethylacetate (4
:
1) to afford the desired product.
3. Results and discussion
After the preparation of the catalyst, the structure of Fe3O4@SBA-3@CPTMS@Arg-Cu was extensively studied using various techniques such as FT-IR spectroscopy, TGA, VSM, XRD, BET, SEM, XPS, EDX, and AAS analysis. Fig. 1 shows the FT-IR spectra of Fe3O4 (a), Fe3O4@SiO2 (b), Fe3O4@SiO2@SBA (c), Fe3O4@SiO2@SBA-3@CPTMS (d), Fe3O4@SiO2@SBA-3@CPTMS@Arg (e), and Fe3O4@SiO2@SBA-3@CPTMS@Arg-Cu (f). As can be seen from Fig. 1a, there was a peak at 3438 cm−1 belonging to the O–H bond of nanomagnetic mesoporous materials and bands at 560 and 641 cm−1 could be assigned to the Fe–O stretching absorption. For all the samples, the absorption bands at around 1081–1066 cm−1 and 800–806 cm−1 could be attributed to asymmetric and symmetric stretching vibrations of Si–O–Si, stretching vibration of Si–O–H, and bending vibration of Si–O–Si. FTIR spectra for Fe3O4@SiO2@SBA-3@CPTMS showed an absorption peak at 2926–2959 cm−1, which was assigned to the C–H stretching vibration modes of the methylene group (Fig. 1d). The FT-IR analysis of Fe3O4@SiO2@SBA-3@CPTMS@Arg showed a stretching vibration for the C
O bond at 1632 cm−1 (Fig. 1e). This verified that the L-arginine was anchored on the surface of the magnetite. The C
N stretching vibration could be identified in the FT-IR spectrum of the Fe3O4@SiO2@SBA-3@CPTMS@Arg-Cu, which appeared at a higher frequency compared to that of Fe3O4@SiO2@SBA-3@CPTMS@Arg (Fig. 1f).
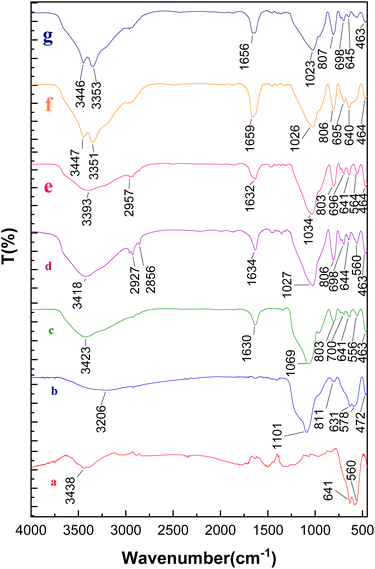 |
| Fig. 1 FT-IR spectra of (a) Fe3O4, (b) Fe3O4@SiO2, (c) Fe3O4@SiO2@SBA, (d) Fe3O4@SiO2@SBA-3@CPTMS, (e) Fe3O4@SiO2@SBA-3@CPTMS@Arg, (f) Fe3O4@SiO2@SBA-3@CPTMS@Arg-Cu (before recovery), and (g) Fe3O4@SiO2@SBA-3@CPTMS@Arg-Cu (after recovery). | |
The structure and phase purity of Fe3O4@SiO2@SBA-3@CPTMS@Arg-Cu and SBA-3 were studied using X-ray diffraction (XRD) analysis (Fig. 2 and 3). Fig. 2 shows typical peaks of a well-organized porous structured material with the main reflection in 2θ at 0.89° and other low-intensity reflections at 1.6° and 1.7°. In the low-angle XRD analysis, three diffraction planes were found, (100), (110), and (200), indicating a well-ordered hexagonal lattice.46
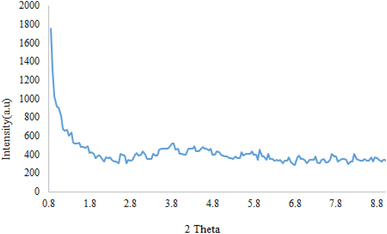 |
| Fig. 2 Low-angle XRD pattern of SBA-3. | |
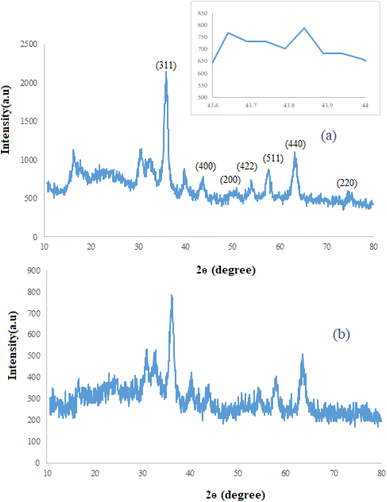 |
| Fig. 3 (a) XRD patterns of Fe3O4@SiO2@SBA-3@CPTMS@Arg-Cu (fresh catalyst) and (b) Fe3O4@SiO2@SBA-3@CPTMS@Arg-Cu after recovery. | |
The wide-angle X-ray powder diffraction patterns of Fe3O4@SiO2@SBA-3@CPTMS@Arg-Cu are shown in Fig. 3. The XRD results showed diffraction peaks at 2θ of 35.7°, 43.6°, 53.85°, 57.31°, and 62.97°, which could be attributed to the (311), (400), (422), (511), and (440) reflections, respectively (JCPDS card no. 25–0283), which have been previously reported in the literature.47 This means that the multiple steps followed in the catalyst preparation did not change the crystal structure of the Fe3O4 cores. Besides, diffraction peaks of copper located at 43.7°, 50.7°, and 74.3° were observed, corresponding to the (111), (200), and (220) planes of the fcc structure, respectively (JCPDS 04-0836) (Fig. 3).48,49 In addition, the broad peak around 2θ = 15°–30° was attributed to the amorphous SiO2 layer around Fe3O4 as a shell of the core and proved the formation of the Fe3O4@SiO2 magnetic nanocomposite.50,51
XPS analysis was performed to determine the oxidation states of Cu in the prepared nanocomposite (Fig. 4). The binding energy values of 935.6 and 955.8 eV, corresponding to the spin orbit splitting components of Cu 2p3/2 and Cu 2p1/2 in the +2 oxidation state of copper, agreed well with the reported literature values.52 Similarly, the peaks located at 932.8 eV and 953.1 eV corresponded to Cu 2p3/2 and Cu 2p1/2, respectively, indicating the presence of Cu compounds containing Cu+ ions.53 Besides, in Fig. 4, the Fe 2p3/2 spectrum displayed two minor peaks at 711.4 eV and 710.0 eV, which could be ascribed to Fe3+ and Fe2+, respectively.54 The deconvoluted XPS spectrum of Si displayed two sub-peaks for Si 2p (at 102 eV and 104 eV), which could be assigned to Si–C and Si–O.55 The deconvoluted high-resolution C 1s spectrum of the film yielded peaks at 284 eV, 285 eV, 286 eV, and 289.4 eV, which were attributed to the sp3 bulk bonded carbon C–C, C–N, C–O, and O–C
O bonds.56–58 The presence of the amino group in the catalyst led to the presence of an N1s peak, which was deconvoluted into three contributions, assigned to the amino group (C
N–C, 397 eV), (C
N, 399.4 eV), and (C–NH, 401 eV).59,60 The O 1s spectrum of the catalyst in Fig. 4 could be deconvoluted into four peaks for O–C
O at 531 eV, C–O at 533 eV, C
O at 532 eV, and H2O at 534 eV.61–63
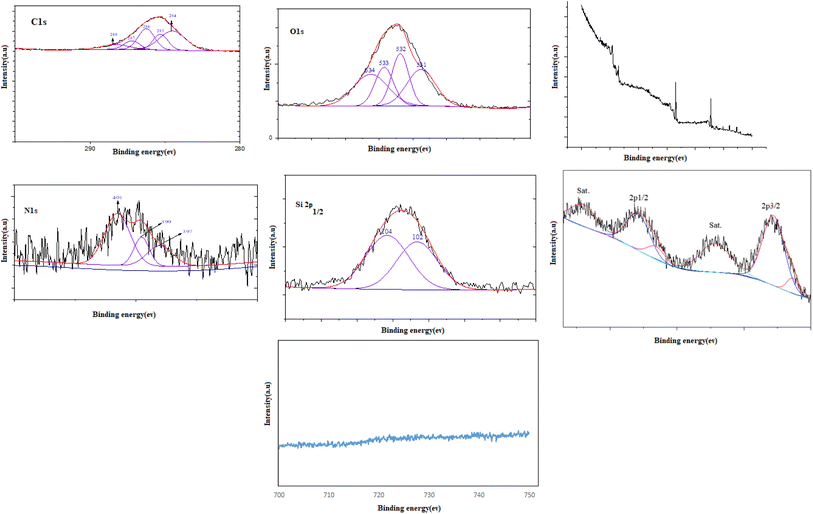 |
| Fig. 4 XPS spectra of the as-prepared Fe3O4@SiO2@SBA-3@CPTMS@Arg-Cu. | |
Vibrating sample magnetometry curves for Fe3O4@SiO2@SBA-3 nanoparticles and Fe3O4@SBA-3@CPTMS@Arg-Cu at room temperature are shown in Fig. 5. The Ms value for Fe3O4@SiO2@SBA-3@CPTMS@Arg-Cu was found to be 18 emu g−1. The Ms value for the catalyst was lower than that of the naked one (23 emu g−1). This result seems to confirm that the Fe3O4@SiO2@SBA-3 surface was surrounded by CPTMS@Arg-Cu, which quenched the magnetic properties.64
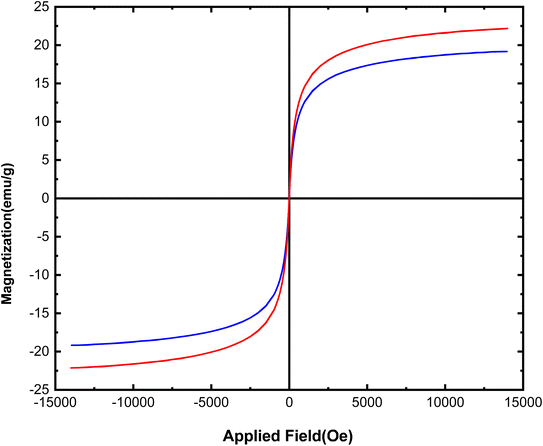 |
| Fig. 5 VSM patterns of Fe3O4@SiO2@SBA-3 (red) and Fe3O4@SiO2@SBA-3@CPTMS@Arg-Cu (blue). | |
Atomic absorption spectroscopy (AAS) was used to determine the exact amount of copper in Fe3O4@SiO2@SBA-3@CPTMS@Arg-Cu. Based on this experiment, the amount of copper in 1 g of Fe3O4@SiO2@SBA-3@CPTMS@Arg-Cu was found to be 2.9 × 10−4 mol.
SEM was performed to observe the morphology of the formed Fe3O4@SiO2@SBA-3@CPTMS@Arg-Cu. The SEM images of Fe3O4@SiO2@SBA-3@CPTMS@Arg-Cu are presented in one scale: 500 nm. The retainment of the shape and regularity of the parent mesopores in the newly designated hybrid materials were confirmed in the SEM images (Fig. 6).
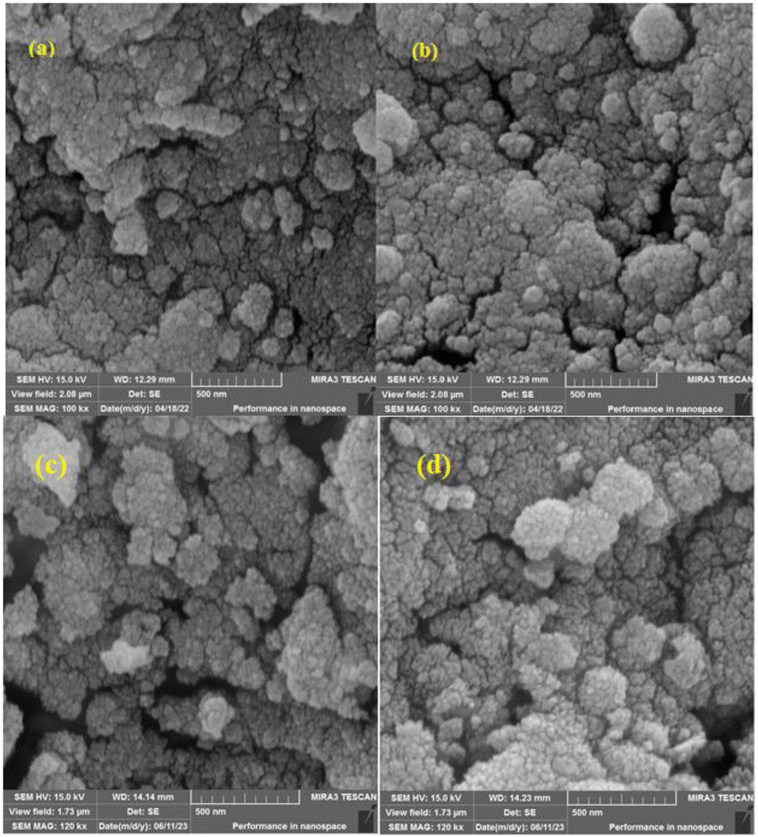 |
| Fig. 6 SEM images of Fe3O4@SiO2@SBA-3@CPTMS@Arg-Cu before recovery (a and b) and after recovery (c and d). | |
Thermogravimetric analysis (TGA) can be used to study the behavior of materials versus temperature (Fig. 7). As shown, there was a weight loss below 250 °C corresponding to the removal of the adsorbed water and organic solvents (about 7 wt%). The second weight loss region was mainly related to the thermal decomposition of organic compounds in the temperature range between 250 °C and 700 °C (about 11 wt%). Moreover, the continuation of weight loss with increasing temperatures up to 1000 °C was ascribed to the condensation of the silanol groups of Fe3O4@SiO2@SBA-3.
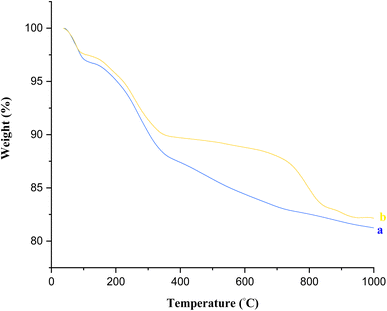 |
| Fig. 7 TGA curves of Fe3O4@SiO2@SBA-3@CPTMS@Arg-Cu before recovery (a) and after recovery (b). | |
Energy dispersive X-ray (EDX) was used to determine the presence and distribution of the components in the prepared nanocatalyst (Fig. 8). EDX analysis confirmed the presence of all elements (C = 16.22%, N = 7.56%, O = 47.56%, Cu = 4.54%, Si = 12.24%, and Fe = 8.59%) that had been used in the synthesis of the nanocatalyst.
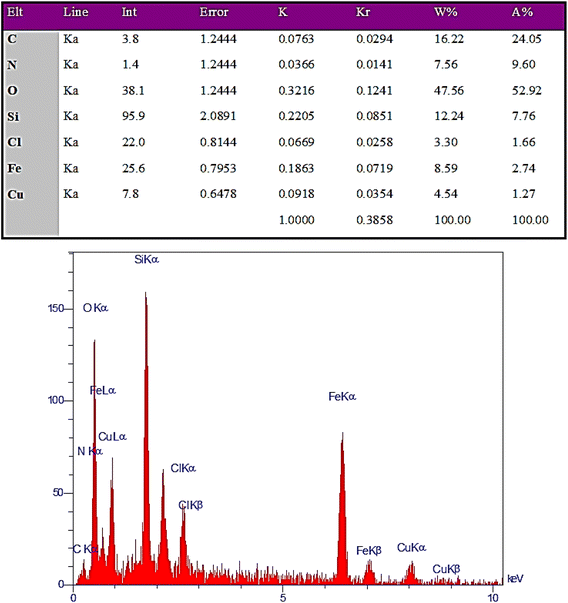 |
| Fig. 8 EDX spectrum of Fe3O4@SiO2@SBA-3@CPTMS@Arg-Cu. | |
The N2 adsorption–desorption isotherm and BJH pore size distribution curve of the Fe3O4@SiO2@SBA-3@CPTMS@Arg-Cu are shown in Fig. 9. The nitrogen adsorption–desorption isotherm of the catalyst after modification exhibited isotherms of type IV(a) characteristic of porous materials, with the hysteresis loop classified according to the IUPAC convention as H2(b).65 The BET surface area was found to be 145 m2 g−1. The average pore diameter of the catalyst pores was 2.68 nm. The total pore volume of the catalyst was approximately 0.1 cm3 g−1, which was estimated at a relative pressure of 0.99 (Table 1). The average pore size obtained by the BJH method using the adsorption branch was 1.22 nm (Table 2).
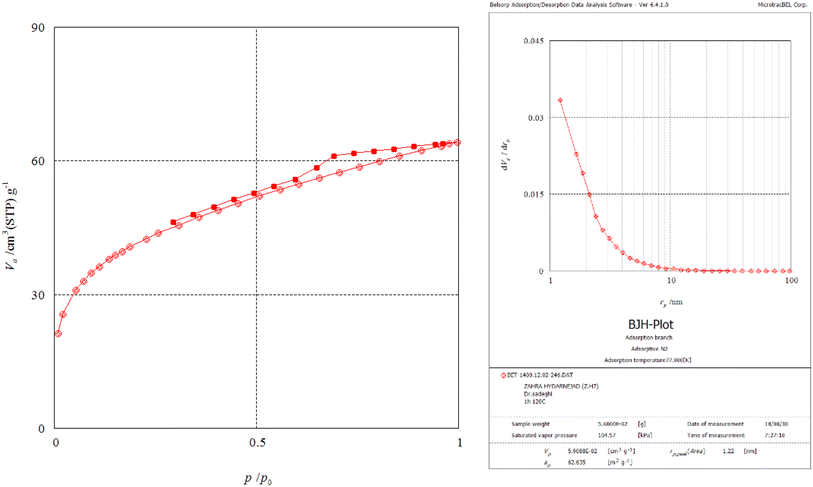 |
| Fig. 9 N2-adsorption isotherms of Fe3O4@SiO2@SBA-3@CPTMS@Arg-Cu. | |
Table 1 Nitrogen adsorption–desorption data for Fe3O4@SiO2@SBA-3@CPTMS@Arg-Cu (from BET calculation)
Entry |
BET plot |
V
m
|
34 cm3 g−1 |
a
s,BET
|
145 m2 g−1 |
Total pore volume (p/p0 = 0.990) |
0.099 cm3 g−1 |
Mean pore diameter |
2.68 nm |
Table 2 BJH-plot data for Fe3O4@SiO2@SBA-3@CPTMS@Arg-Cu
Plot data |
Adsorption branch |
V
p
|
0.05 cm3 g−1 |
r
p, peak (area) |
1.22 nm |
a
p
|
62.635 m2 g−1 |
3.1 Catalytic studies
After the preparation and characterization of the designed magnetic mesoporous material, the catalytic activity of this compound was investigated in the hydrolysis of nitriles to amides. Initially, benzonitrile was chosen as the model substrate to optimize the reaction parameters such as the amount of catalysts and the types of base and solvent, and the temperature (Table 3). The effect of the solvent was examined, and it was observed that the reaction was highly effective in water. The control experiment confirmed that the reaction did not occur in the presence of CuCl, Fe3O4, Fe3O4@SiO2, Fe3O4@SiO2@SBA-3, Fe3O4@SiO2@SBA-3@Arg, or Arg. Furthermore, the progress of the reaction depended on the amount of catalyst; whereby the reaction could be completed in the presence of 40 mg of this catalyst. The ideal temperature for the reaction was found to be 75 °C.
Table 3 Optimization of the reaction conditions for the hydrolysis of nitriles to amides in the presence of Fe3O4@SiO2@SBA-3@CPTMS@Arg-Cu

|
Entrya |
Solvent |
Catalyst (mg) |
Amount of KOH (mmol) |
Temperature (°C) |
Time (min) |
Yieldb (%) |
Reaction conditions: benzonitrile (1 mmol), base (mmol), solvent (2 mL), and temperature.
Isolated yield.
CuCl.
Fe3O4.
Fe3O4@SiO2.
Fe3O4@SiO2@SBA-3.
Fe3O4@SiO2@SBA-3@Arg.
Arg alone.
|
1 |
Propanol |
60 |
3 |
75 |
180 |
68 |
2 |
H2O |
60 |
3 |
75 |
180 |
97 |
3 |
EtOH |
60 |
3 |
75 |
180 |
75 |
4 |
MeOH |
60 |
3 |
Reflux |
180 |
40 |
5 |
THF |
60 |
3 |
Reflux |
180 |
N. R |
6 |
H2O |
60 |
4 |
75 |
180 |
98 |
7 |
H2O |
60 |
2 |
75 |
150 |
97 |
8 |
H2O |
50 |
2 |
75 |
150 |
98 |
9 |
H2O |
40 |
2 |
75 |
150 |
97 |
10 |
H2O |
40 |
2 |
95 |
150 |
94 |
11 |
H2O |
40 |
2 |
55 |
150 |
83 |
12c |
H2O |
60 |
3 |
75 |
180 |
57 |
13d |
H2O |
60 |
3 |
75 |
180 |
N.R |
14e |
H2O |
60 |
3 |
75 |
180 |
N.R |
15f |
H2O |
60 |
3 |
75 |
180 |
N.R |
16g |
H2O |
60 |
3 |
75 |
180 |
N.R |
17h |
H2O |
60 |
3 |
75 |
180 |
N.R |
After optimization of the reaction conditions, the limitations and generality of this work were investigated. Therefore, various benzonitrile-containing electron-withdrawing substituents were examined. The experimental results showed that the desired product was obtained with good yields (Table 4).
Table 4 Catalytic hydrolysis of nitriles to amides in the presence of Fe3O4@SiO2@SBA-3@CPTMS@Arg-Cu
The proposed mechanism of the reaction is shown in Scheme 2. The first step involves the coordination of the nitrile nitrogen atoms with copper to form complex 1 and its nucleophilic attack by KOH.
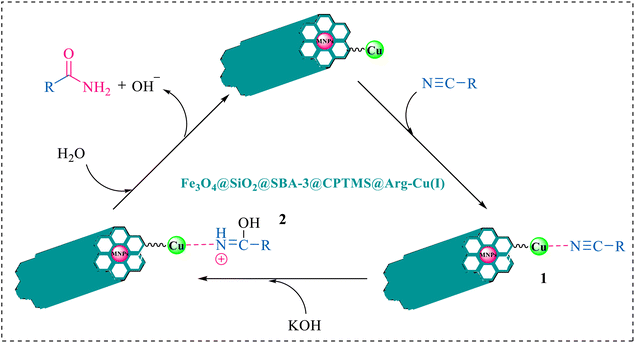 |
| Scheme 2 Proposed mechanism for the hydrolysis of nitriles to amides. | |
In the second part, the catalytic activity of this catalyst and the synthesis of 5-substituted 1H-tetrazole were studied as well. Initially, the reaction of benzonitrile with sodium azide was selected as a model reaction, and different parameters including the solvent type and temperature were studied. The results are summarized in Table 5. First, the effects of different solvents and various temperatures on the model reaction were investigated. According to the data given in (Table 5), PEG was the most efficient solvent for this reaction. When the reaction was conducted at 80 °C and 100 °C, the observed yields were very low (Table 5). The ideal temperature for the reaction was found to be 120 °C.
Table 5 Optimization of the reaction conditions for the synthesis of 5-substituted 1H-tetrazoles in the presence of Fe3O4@SiO2@SBA-3@CPTMS@Arg-Cu

|
Entrya |
Solvent |
Catalyst (mg) |
Temperature (°C) |
Time (min) |
Yieldb (%) |
Reaction conditions: benzonitrile (1 mmol), sodium azide (1.2 mmol), solvent (2 mL), and temperature.
Isolated yield.
|
1 |
PEG |
50 |
120 |
100 |
95 |
2 |
DMF |
50 |
120 |
100 |
59 |
3 |
DMSO |
50 |
120 |
100 |
68 |
4 |
H2O |
50 |
Reflux |
100 |
Trace |
5 |
PEG |
30 |
120 |
100 |
78 |
6 |
PEG |
40 |
120 |
100 |
84 |
7 |
PEG |
50 |
100 |
100 |
83 |
8 |
PEG |
50 |
80 |
100 |
68 |
To understand the scope and effectiveness of the catalyst, different substituted benzonitriles (Table 6) were selected to participate in the described cycloaddition reaction. The results showed that a wide range of nitrile compounds could produce the corresponding tetrazoles in excellent isolated yields.
Table 6 Catalytic synthesis of 5-substituted 1H-tetrazoles in the presence of Fe3O4@SiO2@SBA-3@CPTMS@Arg-Cu
The proposed mechanism of the reaction is shown in Scheme 3. The first step involves the coordination of the nitrile nitrogen atoms with copper to form complex I, which accelerates the cyclization step. Next, the [3 + 2] cycloaddition occurs between the two metal-coordinated CN bonds of the nitrile compound and azide ion to form intermediate II. Finally, the acidic work-up affords the desired product III.
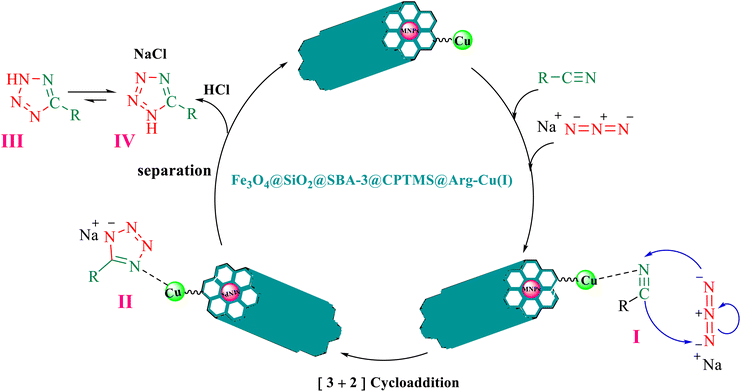 |
| Scheme 3 Proposed mechanism for the synthesis of 5-substituted 1H-tetrazoles. | |
3.2 Catalytic stability and reusability
The rapid separation and efficient recycling of catalysts after a catalytic reaction are considered to be important requirements, along with high catalytic performances. For this purpose, the recovery and recyclability of the employed Fe3O4@SiO2@SBA-3@CPTMS@Arg-Cu NPs were considered for the hydrolysis of benzonitrile to benzamide. Upon completion of the reaction, the catalyst was recovered via an external magnet, and then washed thoroughly with ethyl acetate, and dried under vacuum conditions. The metal leaching of the catalyst was studied by a hot filtration test. To examine the leaching of the copper in the reaction mixture and the heterogeneity of the described catalyst, we performed a hot filtration experiment for the synthesis of 5-substituted 1H-tetrazoles. In this study, we found that the yield of the product at half the reaction time was 55%. Then, the reaction was repeated, and at half the reaction time, the catalyst was separated and the filtrate was allowed to react further. The yield of the reaction after this test was 55%, which confirmed that leaching of copper had not occurred. The recovered catalyst was then applied in the next cycle. The results indicated that this catalyst could be successfully reused seven times without any significant loss of activity (Fig. 10). To demonstrate the structural stability of the catalyst after recycling, the recovered catalyst was characterized using FT-IR, TGA, SEM, and XRD techniques. The recovered catalyst was investigated using XRD (Fig. 9), and FT-IR (Fig. 10). To confirm the stability of the catalytic system, the recovered catalyst was characterized using FT-IR, TGA, SEM, and XRD techniques (Fig. 1, 3, 6, and 7, respectively). TGA data showed the weight change in the recovered catalyst compared to the fresh catalyst. The characterization also showed that the catalytic system could be reused for several runs without any change in its structure. Moreover, the XRD pattern for the Cu-based catalyst shows a decrease in intensity due to the destroyed crystal structure and the size distribution of copper nanoparticles in the reactivated catalyst.73
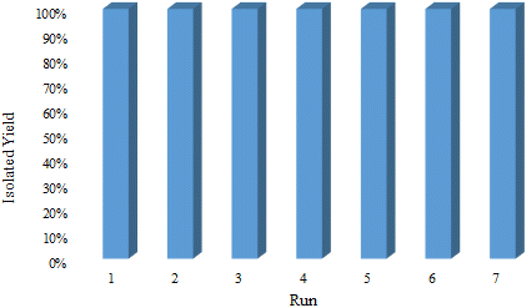 |
| Fig. 10 Recyclability of Fe3O4@SiO2@SBA-3@CPTMS@Arg-Cu NPs for the hydrolysis of benzonitrile to benzamide. | |
3.3 Comparison of the catalyst behavior with previously reported procedures
We evaluated the efficiency of the described catalytic system for comparison with previously reported procedures in the literature. A comparison of the results showed a better catalytic activity of the Fe3O4@SiO2@SBA-3@CPTMS@Arg-Cu NPs for the hydrolysis of benzonitrile to benzamide (Table 7). The comparison indicated that the prepared magnetite mesoporous material as a versatile nanocatalyst was comparable to or maybe better in some aspects than the other reported catalysts.
Table 7 Comparison of the performance of the Fe3O4@SiO2@SBA-3@CPTMS@Arg-Cu NP catalyst and other catalysts for the hydrolysis of benzonitrile to benzamide
Entry |
Catalyst |
Conditions |
Time (h) |
Yielda (%) |
Ref. |
Isolated yield.
|
1 |
TBANa-SrPd12(pent)3 |
DMF, H2O, 90 °C |
600 |
88 |
74
|
2 |
Fe3O4@SiO2-NHC-Cu |
H2O, 110 °C |
360 |
92 |
68
|
3 |
Ru@imine-nanoSiO2 |
KOH, i-PrOH, 40 °C, air |
300 |
75 |
75
|
4 |
Au NPs |
KOH, i-PrOH : H2O (1 : 1), 80 °C |
180 |
99 |
76
|
5 |
Complex [OsCl2(η6-p-cymene){PPh2(NMe2)}] |
H2O, 100 °C |
180 |
97 |
77
|
6 |
Fe3O4@SiO2@SBA-3@CPTMS@Arg-Cu |
KOH, H2O, 75 °C |
150 |
97 |
This work |
4. Conclusions
In conclusion, we developed a simple, efficient, and environmentally benign method for the hydrolysis of nitriles to amides and the synthesis of 5-substituted 1H-tetrazoles, employing Fe3O4@SiO2@SBA-3@CPTMS@Arg-Cu as a recyclable heterogeneous catalyst with a magnetic and mesoporous nature. The advantages of the present protocol are the reusability of the catalyst for up to four cycles, excellent product yield, shorter reaction time, and green reaction conditions.
Conflicts of interest
The authors declare that they have no known competing financial interests or personal relationships that could have influenced the work reported in this study.
Acknowledgements
The authors would like to thank the research facilities of Ilam University and Bu-Ali Sina University for their financial support.
References
- J. A. Cecilia, R. Moreno Tost and M. Retuerto Millán, Int. J. Mol. Sci., 2019, 20, 3213 CrossRef CAS PubMed.
- A. Kiderys, M. Kot, E. Janiszewska, M. Pietrowski, C.-M. Yang and M. Zieliński, Catal. Today, 2020, 356, 178–186 CrossRef CAS.
- H. Ebrahimzadeh, N. Tavassoli, O. Sadeghi, M. M. Amini and M. Jamali, Microchim. Acta, 2011, 172, 479–487 CrossRef CAS.
- C. Cai, H. Zhang, X. Zhong and L. Hou, Water Res., 2014, 66, 473–485 CrossRef CAS PubMed.
- X. Wang, L. Zhu, Y. Liu and S. Wang, Sci. Total Environ., 2018, 625, 686–695 CrossRef CAS PubMed.
- M. Shaban, M. R. Abukhadra and A. Hamd, Clean Technol. Environ. Policy, 2018, 20, 13–28 CrossRef CAS.
- A. Ghorbani-Choghamarani, B. Tahmasbi, R. H. E. Hudson and A. Heidari, Microporous Mesoporous Mater., 2019, 284, 366–377 CrossRef CAS.
- S. Molaei, T. Tamoradi, M. Ghadermazi and A. Ghorbani-Choghamarani, Microporous Mesoporous Mater., 2018, 272, 241–250 CrossRef CAS.
- O. Y. Gutiérrez, G. A. Fuentes, C. Salcedo and T. Klimova, Catal. Today, 2006, 116, 485–497 CrossRef.
- J. Wisniewska, I. Sobczak and M. Ziolek, Chem. Eng. J., 2021, 413, 127548 CrossRef CAS.
- K. Soni, P. E. Boahene and A. K. Dalai, ACS Symp. Ser., 2011, 1088, 15–29 CrossRef CAS.
- L. Y. Lizama and T. E. Klimova, J. Mater. Sci., 2009, 44, 6617–6628 CrossRef CAS.
- C. Ochoa-Hernández, Y. Yang, P. Pizarro, V. A. De La Peña O'Shea, J. M. Coronado and D. P. Serrano, Catal. Today, 2013, 210, 81–88 CrossRef.
- A. Galarneau, M. Nader, F. Guenneau, F. Di Renzo and A. Gedeon, J. Phys. Chem. C, 2007, 111, 8268–8277 CrossRef CAS.
- E. Janiszewska, M. Zieliński, M. Kot, E. Kowalewski and A. Śrębowata, ChemCatChem, 2018, 10, 4109–4118 CrossRef CAS.
- Z. Heidarnezhad, A. Ghorbani-Choghamarani and Z. Taherinia, Catal. Lett., 2022, 152, 3178–3191 CrossRef CAS.
- M. Khabazipour, S. Shariati and F. Safa, Synth. React. Inorg., Met.-Org., Nano-Met. Chem., 2016, 46, 759–765 CrossRef CAS.
- S. Molaei, M. Ghadermazi and N. Moeini, Res. Chem. Intermed., 2022, 48, 771–793 CrossRef CAS.
- N. Moeini, S. Molaei and M. Ghadermazi, J. Mol. Struct., 2021, 1246, 131071 CrossRef CAS.
- I. D. Inaloo and S. Majnooni, Eur. J. Org. Chem., 2019, 2019, 6359–6368 CrossRef CAS.
- I. Dindarloo Inaloo, S. Majnooni, H. Eslahi and M. Esmaeilpour, Mol. Catal., 2020, 492, 110915 CrossRef CAS.
- A. R. Sardarian, M. Zangiabadi and I. D. Inaloo, RSC Adv., 2016, 6, 92057–92064 RSC.
-
(a) I. D. Inaloo, S. Majnooni, H. Eslahi and M. Esmaeilpour, New J. Chem., 2020, 44, 13266–13278 RSC;
(b) F. Hakimi, A. Sharifi-Zarchi and E. Golrasan, Chem. Methodol., 2023, 7, 489–498 CAS;
(c) R. Khazaei, A. Khazaei and M. Nasrollahzadeh, J. Appl. Organomet. Chem., 2023, 3, 123 Search PubMed;
(d) F. Hakimi, M. Taghvaee and E. Golrasan, Adv. J. Chem., Sect. A, 2023, 6, 188–197 CAS;
(e) F. Hakimi, A. Sharifi-Zarchi and E. Golrasan, Chem. Methodol., 2023, 7, 489–498 CAS.
- C. X. Wei, M. Bian and G. H. Gong, Molecules, 2015, 20, 5528–5553 CrossRef CAS PubMed.
- R. K. Uppadhayay, A. Kumar, J. Teotia and A. Singh, Russ. J. Org. Chem., 2022, 58, 1801–1811 CrossRef CAS.
- P. B. Mohite and V. H. Bhaskar, Int. J. PharmTech Res., 2011, 3, 1557–1566 CAS.
- M. Nasrollahzadeh, Z. Nezafat, N. S. S. Bidgoli and N. Shafiei, Mol. Catal., 2021, 513, 111788 CrossRef CAS.
- I. Zanoni, M. Blosi, V. Fiorini, M. Crosera, S. Ortelli, S. Stagni, A. Stefan, S. Psilodimitrakopoulos, E. Stratakis, F. L. Filon and A. L. Costa, Nanomaterials, 2020, 10, 1020 CrossRef CAS PubMed.
- P. An, Z. Yu and Q. Lin, Chem. Commun., 2013, 49, 9920–9922 RSC.
- R. Ahmadi and L. Shemshaki, Int. J. Bio-Inorg. Hybrid Nanomater., 2016, 5, 141–146 Search PubMed.
- A. Ghorbani-Choghamarani and Z. Taherinia, Aust. J. Chem., 2017, 70, 1127–1137 CrossRef CAS.
- S. Molaei, N. Moeini and M. Ghadermazi, J. Organomet. Chem., 2022, 977, 122459 CrossRef CAS.
- N. Moeini, S. Molaei and M. Ghadermazi, Res. Chem. Intermed., 2022, 48, 3109–3128 CrossRef CAS.
- N. Moeini, M. Ghadermazi and S. Molaei, J. Mol. Struct., 2022, 1251, 131982 CrossRef CAS.
- S. Molaei, M. Ghadermazi and N. Moeini, Appl. Surf. Sci. Adv., 2022, 7, 100192 CrossRef.
- Y. Guo, R. Y. Wang, J. X. Kang, Y. N. Ma, C. Q. Xu, J. Li and X. Chen, Nat. Commun., 2021, 12, 1–9 CrossRef PubMed.
- L. C. Wang, B. Chen, Y. Zhang and X. F. Wu, Angew. Chem., Int. Ed., 2022, 61, e202207970 CrossRef CAS PubMed.
- C. J. Fowler, K. O. Jonsson and G. Tiger, Biochem. Pharmacol., 2001, 62, 517–526 CrossRef CAS PubMed.
- N. Aslankoohi and K. Mequanint, Mater. Sci. Eng., C, 2021, 128, 112288 CrossRef CAS PubMed.
- T. Krause, S. Baader, B. Erb and L. J. Gooßen, Nat. Commun., 2016, 7, 1–7 Search PubMed.
- A. Drageset and H. R. Bjørsvik, Eur. J. Org. Chem., 2018, 2018, 4436–4445 CrossRef CAS.
- T. N. Reddy and D. P. de Lima, Asian J. Org. Chem., 2019, 8, 1227–1262 CrossRef CAS.
- X. Bin Jiang, A. J. Minnaard, B. L. Feringa and J. G. De Vries, J. Org. Chem., 2004, 69, 2327–2331 CrossRef PubMed.
- S. Zhang, H. Xu, C. Lou, A. M. Senan, Z. Chen and G. Yin, Eur. J. Org. Chem., 2017, 2017, 1870–1875 CrossRef CAS.
- D. B. Bagal and B. M. Bhanage, Adv. Synth. Catal., 2015, 357, 883–900 CrossRef CAS.
- K. C. Souza, J. D. Ardisson and E. M. B. Sousa, J. Mater. Sci.: Mater. Med., 2019, 20, 507–512 CrossRef PubMed.
- K. S. Loh, Y. H. Lee, A. Musa, A. A. Salmah and I. Zamri, Sensors, 2008, 8, 5775–5791 CrossRef CAS PubMed.
- L. Wang, S. C. Gopinath, P. Anbu, R. D. A. A. Rajapaksha, P. Velusamy, K. Pandian and C. G. Lee, Biochem. Eng. J., 2019, 142, 97–104 CrossRef CAS.
- R. Betancourt-Galindo, P. Y. Reyes-Rodriguez, B. A. Puente-Urbina, C. A. Avila-Orta, O. S. Rodríguez-Fernández, G. Cadenas-Pliego and L. A. García-Cerda, J. Nanomater., 2014, 2014, 10 Search PubMed.
- F. Ghorbani and S. Kamari, Environ. Technol. Innovation, 2019, 14, 100333 CrossRef.
- N.-N. Song, H.-T. Yang, H.-L. Liu, X. Ren, H.-F. Ding, X.-Q. Zhang and Z.-H. Cheng, Sci. Rep., 2013, 3, 3161 CrossRef PubMed.
- S. Roy, T. Chatterjee, B. Banerjee, N. Salam, A. Bhaumik and S. M. Islam, RSC Adv., 2014, 4, 46075–46083 RSC.
-
S. Mokhtari and A. W. Wren, Copper Containing Glass-Based Bone Adhesives for Orthopaedic Applications: Glass Characterization and Advanced Mechanical Evaluation, bioRxiv, 2020, DOI:10.1101/2020.11.19.390138.
- F. Han, L. Ma, Q. Sun, C. Lei and A. Lu, Nano Res., 2014, 7, 1706–1717 CrossRef CAS.
- H. Wang, H. Zhou, A. Gestos, J. Fang, H. Niu, J. Ding and T. Lin, Soft Matter, 2013, 9, 277–282 RSC.
- V. Chen, X. Wang and D. Fang, Fullerenes, Nanotubes Carbon Nanostruct., 2020, 28, 1048–1058 CrossRef.
- J. Li, X. Hou, Y. Mao, C. Lai and X. Yuan, Energy Fuels, 2020, 34, 14995–15003 CrossRef CAS.
- R. R. Solís, A. Gómez-Avilés, C. Belver, J. J. Rodriguez and J. Bedia, J. Environ. Chem. Eng., 2021, 9, 106230 CrossRef.
- R. Nazir, P. Fageria, M. Basu, S. Gangopadhyay and S. Pande, New J. Chem., 2017, 41, 9658–9667 RSC.
- J. S. Stevens, A. C. De Luca, M. Pelendritis, G. Terenghi, S. Downes and S. L. Schroeder, Surf. Interface Anal., 2013, 45, 1238–1246 CrossRef CAS.
- A. Shakeri, N. A. Jarad, J. Terryberry, S. Khan, A. Leung, S. Chen and T. F. Didar, Small, 2020, 16, 2003844 CrossRef CAS PubMed.
- J. Fusy, M. Alnot, J. Jupille, P. Pareja and J. J. Ehrhardt, Appl. Surf. Sci., 1984, 17, 415–428 CrossRef CAS.
- H. Idriss, Surf. Sci., 2021, 712, 121894 CrossRef CAS.
- K. NR, Asian J. Biomed. Pharm. Sci., 2015, 5, 13–19 Search PubMed.
- L. Wolski, K. Sobańska, A. Walkowiak, K. Akhmetova, J. Gryboś, M. Frankowski, M. Ziolek and P. Pietrzyk, J. Hazard. Mater., 2021, 415, 125665 CrossRef CAS PubMed.
- M. H. Bahreininejad and F. Moeinpour, J. Chin. Chem. Soc., 2021, 68, 893–901 CrossRef CAS.
- S. K. Das, P. Bhattacharjee, M. Sarmah, M. Kakati and U. Bora, Curr. Res. Green Sustainable Chem., 2021, 4, 100071 CrossRef CAS.
- M. Kazemi Miraki, M. Arefi, A. Salamatmanesh, E. Yazdani and A. Heydari, Catal. Lett., 2018, 148, 3378–3388 CrossRef CAS.
- M. A. Jani and K. Bahrami, Appl. Organomet. Chem., 2020, 34, e6014 CrossRef CAS.
- E. Aali, M. Gholizadeh and N. Noroozi-Shad, J. Mol. Struct., 2022, 1247, 131289 CrossRef CAS.
- P. Movaheditabar, M. Javaherian and V. Nobakht, J. Iran. Chem. Soc., 2022, 19, 1805–1816 CrossRef CAS.
- M. Nikoorazm, B. Tahmasbi, S. Gholami and P. Moradi, Appl. Organomet. Chem., 2020, 34(11), e5919 CrossRef CAS.
- A. R. Hajipour, S. M. Hosseini and F. Mohammadsaleh, New J. Chem., 2016, 40, 6939–6945 RSC.
- T. Wang, D. Liu and J. Dong, IOP Conf. Ser. Earth Environ. Sci., 2019, 310, 042040 CrossRef.
- S. Sultana, G. Borah and P. K. Gogoi, Appl. Organomet. Chem., 2019, 33, e4595 CrossRef.
- M. Hazarika, G. D. Kalita, S. Pramanik, D. Borah and P. Das, Curr. Res. Green Sustainable Chem., 2020, 3, 100018 CrossRef.
- R. González-Fernández, P. Crochet and V. Cadierno, ChemistrySelect, 2018, 3, 4324–4329 CrossRef.
|
This journal is © The Royal Society of Chemistry 2024 |
Click here to see how this site uses Cookies. View our privacy policy here.