DOI:
10.1039/D3MH01587D
(Communication)
Mater. Horiz., 2024,
11, 238-250
Preparation of tough and stiff ionogels via phase separation†
Received
30th September 2023
, Accepted 13th October 2023
First published on 16th October 2023
Abstract
Ionogels have the advantages of thermal stability, non-volatility, ionic conductivity and environmental friendliness, and they can be used in the field of flexible electronics and soft robotics. However, their poor mechanical strength and complex preparation methods limit their practical application. Herein, we propose a simple strategy to improve the performance of ionogels by adjusting their phase separation behavior. In a polymer-ionic liquid (IL) binary system with an upper critical solution temperature (UCST) and Berghmans' point, the phase separation behavior will be frozen below the temperature corresponding to the Berghmans' point, and thus, the degree of phase separation can be adjusted by controlling the cooling rate. We found that a polyacrylamide (PAM)-IL binary system possessed a UCST and Berghmans' point and the resulting ionogels had excellent mechanical properties. Their tensile strength, tensile modulus, compressive strength and compressive modulus reached 31.1 MPa, 319.8 MPa, 122 MPa and 1.7 GPa, respectively, while these properties of the other ionogels were generally less than 10 MPa. Furthermore, they were highly transparent, stretchable, stable and multifunctional.
New concepts
We found that a polyacrylamide (PAM)-IL binary system exhibits a UCST and Berghmans' point and report a simple and general method for the synthesis of tough ionogels by adjusting the degree of phase separation through a ‘heating and rapid-cooling’ post-process. Due to the partial compatibility between the PAM and IL, a phase separation behavior occurs during cooling. Once the temperature drops below TB, the phase separation behavior of the ionogel is frozen, causing the gel to be in a phase-locked state. In this case, the phase separation behavior can be adjusted by controlling the cooling rate. Compared with the existing gel materials, the resulting PAM-IL ionogels exhibit excellent mechanical properties, including a tensile strength of 31.1 MPa, tensile modulus of 319.8 MPa, compressive strength of 122 MPa and compressive modulus of 1.7 GPa.
|
Introduction
Ionogels are a type of gel formed with ILs as the dispersion medium,1 which exhibit ionic conductivity, thermal stability and non-volatility.2 Consequently, they have broad application prospects in the field of flexible electronics,2–5 energy6,7 and intelligent monitoring.3,8,9 Furthermore, compared with water, ILs have the advantages of a wide liquid range and non-volatility.10–12 At present, the main methods for the preparation of polymer ionogels are direct polymerization and solvent exchange.11 However, the direct polymerization method is usually only applicable to small molecule monomers that can directly dissolve in ILs. Alternatively, the solvent exchange method is more versatile, but it is more complex and time-consuming. Compared with hydrogels, the development of ionogels is relatively sluggish and the mechanical properties of ionogels are generally poor.2 Simultaneously, they also have some drawbacks, such as complex and time-consuming preparation process, that seriously limit the development and practical application of ionogels.13,14 Accordingly, efforts have been made to solve the above-mentioned problems.14 For example, Yan and co-workers15 successfully prepared PVA/halometallate ionogels through the solvent exchange method. Due to the presence of supramolecular interactions and crystalline domains, the ionogels exhibited remarkable mechanical properties, including a tensile strength of up to 63.1 MPa and fracture elongation of 5248%. Dickey and co-workers13 polymerized acrylic acid (AA) and acrylamide (AM) in hydrophilic ILs, such as 1-ethyl-3-methylimidazolium ethyl sulfate, and realized the toughening of ionogels utilizing the phase separation behavior of the co-polymer. The ionogel exhibited a tensile strength of 12.6 MPa and elongation at break of more than 600%. In terms of the research on the phase separation behavior of ionogels, Liu and co-workers16 found that the phase separation behavior of polyisopropylacrylamide (PNIPAM) in ILs is common. The binary phase diagram of PNIPAM-IL has a UCST and Berghmans' point (the intersection points of the curves corresponding to the UCST and the glass transition temperature (Tg) of PNIPAM). They realized the transformation of the Young's modulus of the ionogels by adjusting the phase separation behavior of PNIPAM. According to these studies, it can be found that the phase separation behavior of ionogels may have a significant impact on their properties.17 However, although these works have greatly improved the performance of ionogels, they still have shortcomings, which need to be overcome. For example, simpler and faster methods for the preparation of high-performance ionogels still need to be further explored.
Herein, we realized the preparation of an ionogel with high strength and modulus through a simple strategy. In a polymer-IL system with a UCST and Berghmans' point, the degree of phase separation can be adjusted by a ‘heating and rapid-cooling’ process to obtain an ideal ionogel. Through research, we found that polyacrylamide (PAM) has a UCST in ILs, and the phase diagram of the binary system composed of PAM and IL also has a Berghmans' point. The obtained PAM-IL ionogels exhibited a tensile strength of 31.1 MPa, tensile modulus of 319.8 MPa, compressive yield strength of 112.2 MPa and compressive modulus of 1.77 GPa. To the best of our knowledge, this fantastic performance exceeds the mechanical properties of most of the reported ionogels and hydrogels, and even some general-purpose plastics. In addition, the ionogel has the advantages of a simple preparation process (two steps), rapid preparation (<30 min), low cost (using bromine-based IL), high transparency (90–96%), easy shaping (3D printing), good stability (vacuum and heat stability) and multi-functionality.
Results and discussion
Design and preparation of PAM-IL ionogels
Physically crosslinked PAM-IL ionogels were obtained via the photopolymerization of AM monomer dissolved in ILs consisting of imidazole cations and several types of anions. The synthetic route is shown in Fig. 1a. The prepared precursor solution was poured into a glass mould and exposed to 365 nm ultraviolet light. The PAM molecular chains underwent rapid growth, and within a few minutes, a translucent primary ionogel was obtained. Then, post-processing was performed by heating the ionogel to a high temperature and rapidly cooling it back to room temperature (RT), resulting in the formation of the final PAM-IL ionogels. Five ILs, including three types of cations and three types of anions, were used in this work, and the structure of the cations and anions is shown in Fig. S1 (ESI†). The details of the 1H-NMR, FT-IR and viscosity characterisation of the ILs are listed in ESI,† Fig. S2–S4. According to the difference in the mass fraction of PAM and the type of ionic liquid, the ionogels were denotes as PAMx-IL(Y), where ‘x’ represents the mass fraction of polymer and ‘Y’ represents the type of ionic liquid. For example, the PAM30-IL([EBIM]Br) ionogel possess 30 wt% PAM and [EBIM]Br as the ionic liquid. In addition, the translucent primary ionogel that was not subjected to the ‘heating and rapid-cooling’ post-processing is denoted as the WPAMx-IL (Y) ionogel, and the precursor solution for its preparation is referred to as pre-PAMx-IL(Y). The ionic liquids containing different cation–anion pairs had a significant impact on the performance of the ionogels. As shown in Fig. S5 (ESI†), the PAMx-IL([EBIM]Br) ionogels exhibited the best transparency. Furthermore, we found that the transparent ionogels tended to have better toughness, while the milky white ionogels were quite brittle.13 Therefore, we discuss the structure and performance of the PAMx-IL([EBIM]Br) ionogels in detail. Fig. 1b shows the chemical structures of each component in the precursor solution, as well as the linear molecular structure of PAM after photopolymerization. No chemical crosslinking agent was added to the precursor solution and the XRD tests revealed the absence of PAM crystallization in the ionogels (Fig. S6, ESI†). The ionogels formed a polymer network through physical crosslinking, primarily through non-covalent interactions (Fig. 1c) and phase separation structures (Fig. 1d). In the ionogels, the PAM polymer chains formed hydrogen bonds with the other PAM chains and underwent non-covalent interactions with the ionic liquid. Generally, it is believed that these interactions compete with each other, ultimately resulting in phase separation.18 The polymer chains aggregate into microdomains, acting as physical cross-linking points. Fig. 1e shows a model of the internal structure of the PAM40-IL([EBIM]Br) ionogel obtained through molecular dynamics (MD) simulation. It can be clearly seen that the polymer chains exhibit a coiled and folded conformation, with a tendency to aggregate. This indicates the presence of phase separation structures between the polymer and ionic liquid within the ionogel. As shown in Fig. 1g and Fig. S5 and S7 (ESI†), the ionogels obtained directly by photoinduced polymerization (WPAMx-IL([EBIM]Br) ionogels) were translucent. The degree of phase separation and morphology of the WPAMx-IL([EBIM]Br) ionogels were adjusted through the process of ‘heating and rapid-cooling’ in the post-process, which significantly improved their transparency and mechanical properties. Subsequently, the PAMx-IL([EBIM]Br) ionogels were obtained, which were thermo-sensitive and exhibited a UCST. Among them, the PAM50-IL([EBIM]Br) ionogel exhibited impressive transparency of up to 96% in the visible light range. Additionally, all the PAMx-IL([EBIM]Br) ionogels possessed adequate transparency for a clear view of the background image (Fig. 1f).
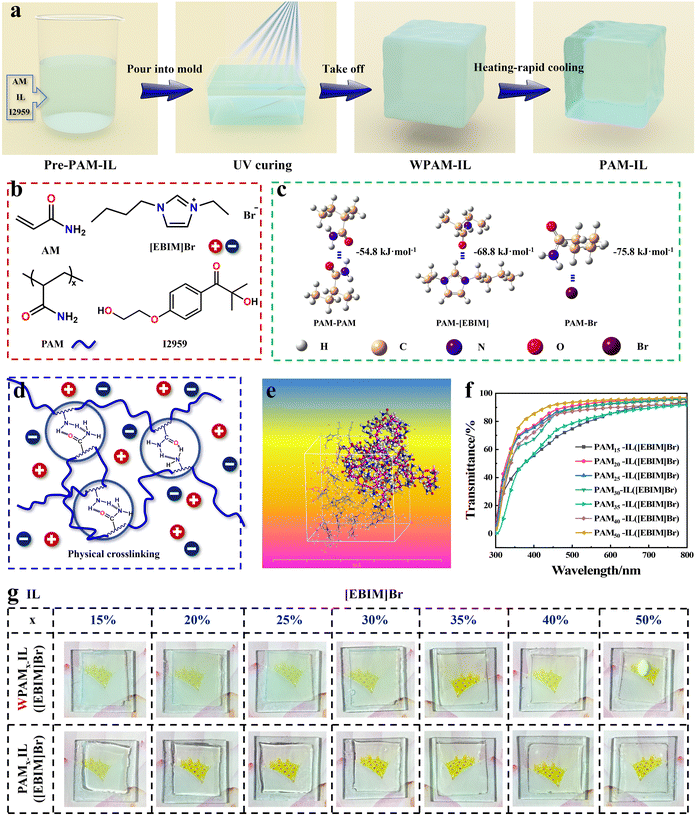 |
| Fig. 1 PAM-IL ionogels. (a) Procedure for the preparation of PAM-IL ionogels. (b) Chemical structures of each component in the precursor solution and ionogels. (c) Energy-optimized geometry between PAM and [EBIM]Br based on DFT calculation. (d) Schematic diagram of physically cross-linked structures within the ionogels. (e) Representative structure model of PAM40-IL([EBIM]Br) ionogel with annealing and dynamics optimized based on MD calculation. (f) Visible light transmittance spectra of PAMx-IL([EBIM]Br) ionogels. (g) Optical photos of WPAMx-IL([EBIM]Br) and PAMx-IL([EBIM]Br) ionogels prepared with [EMIM]Br, where ‘x’ represents the mass fraction of polymer (x = 15, 20, 25, 30, 35, 40 or 50). | |
Phase separation and structure of PAMx-IL([EBIM]Br) ionogels
Many acrylamide-based polymer hydrogels such as PNIPAM show thermo-sensitive characteristics.19,20 Generally, these polymers contain hydrophilic functional groups and hydrophobic carbon skeletons, which separate from water at a certain temperature, resulting in a transparent to opaque transition and volume mutation.21 However, both the AM monomer and its homopolymer have excellent hydrophilicity due to the presence of a significant number of amide groups. The amide groups can form hydrogen bonds with water, allowing PAM to be readily soluble in water at any proportion. Alternatively, neat PAM hydrogels are not thermo-sensitive.
However, we observed a UCST in the binary system of PAM-imidazolium-based ILs, and the corresponding PAMx-IL([EBIM]Br) ionogels also exhibited thermo-sensitivity. This phenomenon can be attributed to the presence of alkyl chains in the imidazolium-based ionic liquids, which diminish the compatibility between PAM and the ionic liquids compared to water. At lower temperatures, the amide groups present on the PAM chains are more prone to forming hydrogen bonds with the amide groups within or between the chains, leading to phase separation. Conversely, at higher temperatures, the hydrogen bonds break, causing PAM and the ionic liquids to mix spontaneously in a manner that maximizes entropy. Consequently, a homogeneous mixture is formed and phase separation is eliminated. Therefore, the phase separation of the PAMx-IL([EBIM]Br) ionogels occurred during cooling from a temperature above their UCST to a temperature below their UCST. Besides, different phenomena were observed during the process of cooling at a slow and fast rate, and the performance of the final ionogels was also different. For convenience, we named the two different post-processes as ‘heating and slow-cooling’ and ‘heating and rapid-cooling’, respectively.
Taking the PAM40-IL([EBIM]Br) ionogel as an example, during heating, the WPAM40-IL([EBIM]Br) ionogels underwent a gradual transition from an initial translucent state to an opaque state. As heating continued, they eventually reached a fully transparent state (Movie S1, ESI†). Subsequently, during the slow-cooling process, the gel gradually became an opaque milky white colour (Movie S2, ESI†). Furthermore, during the rapid-cooling process (from 140 °C to room temperature at a rate exceeding 70 °C min−1), the ionogel remained transparent throughout the process, as observed in Movie S1 (ESI†). Specifically, this particular gel was denoted as the PAM40-IL([EBIM]Br) ionogel. This phenomenon occurred because the two-phase structure in the PAMx-IL([EBIM]Br) ionogels underwent changes during heating and cooling.
According to Fig. 2a, we can gain a more intuitive understanding of the phase separation behavior of the PAMx-IL([EBIM]Br) ionogels during the heating and cooling processes. The phase diagram exhibits the binodal line of the PAM-[EBIM]Br binary system and the corresponding glass transition temperature curve of the ionogels, which were obtained through the cloud point test and DSC test (Fig. S9, ESI†). The point of intersection of the two curves represents Berghmans' point of the PAM-[EBIM]Br binary system, with the corresponding temperature denoted as TB. In the systems with Berghmans' point, when the temperature is below TB, the molecular chains are unable to move, and the phase structure remains unchanged. The phase diagram is divided into four regions by two curves. The pink region represents the ‘homogeneous region’ where no phase separation occurs. The yellow region represents the ‘phase separation region’ where phase separation can occur. The cyan region represents the ‘phase-locked’ region where phase separation cannot change. In the binary system of PAM-IL, liquid–liquid phase separation leads to the formation of a polymer-rich phase and a liquid-rich phase.16 For a certain state of the PAM-IL binary system characterized by a specific temperature and degree of phase separation, the corresponding points on the phase diagram for the polymer-rich phase and liquid-rich phase are labelled as ‘P’ point and ‘L’ point, respectively. This state is denoted as state ‘A’. Taking the WPAM40-IL([EBIM]Br) ionogel as an example, at room temperature and with a PAM content of 40 wt%, its state corresponds to point A0 on the diagram. Assuming that the polymer-rich phase corresponds to point P0 and the liquid-rich phase corresponds to point L0, we define the distance |L0, P0| between points L0 and P0 as the degree of phase separation. The smaller the distance, the lower the degree of phase separation, whereas a larger distance indicates a higher degree of phase separation. A higher degree of phase separation results in a larger size of the polymer-rich phase, increased system inhomogeneity, and reduced translucency. In state A0, the degree of phase separation ∣L0, P0∣ occurs due to the enhanced repulsion between the PAM molecular chains and the [EBIM]Br ionic liquid during the polymerization process. This enhanced repulsion leads to spontaneous phase separation from a thermodynamic perspective. Additionally, the limited mobility of the molecular chains at low temperatures contributes to a relatively low degree of phase separation. It is worth emphasizing that polymer phase separation is a dynamic process influenced by both thermodynamics and kinetics. Thermodynamics governs the equilibrium behavior of the system, determining whether phase separation will occur based on factors such as temperature, composition, and intermolecular interactions. Alternatively, kinetics is related to the time-dependent aspects of phase separation, including the rate at which it occurs and the evolution of the phase-separated structures with time.22 The interplay between thermodynamics and kinetics plays a crucial role in the phase separation process. Thermodynamic factors drive the system towards a more stable state, favouring phase separation when the conditions are suitable. Kinetic factors, such as molecular mobility and diffusion, determine the speed at which phase separation occurs and influence the resulting morphology and size of the separated phases. In most cases, due to the long relaxation time of the polymer chains, phase separation remains in a non-equilibrium state. Under A0 conditions, the macroscopic appearance of the WPAM40-IL([EBIM]Br) ionogel was translucent, as shown in Fig. 1g and 2b(I). When the system was heated, as the temperature increased to near TB, the state of the WPAM40-IL([EBIM]Br) ionogel changed from A0 to A1 (indicated by the black dashed line). At the A1 state, the corresponding points of the polymer-rich phase and liquid-rich phase are L1 and P1, respectively, as molecular chains are difficult to move when the temperature is below TB, and thus the degree of phase separation does not change. After the temperature exceeds TB, the molecular chains become active and phase separation begins slowly, gradually accelerating with an increase in temperature. The point corresponding to the polymer-rich phase changes from P1 to P2 (P1 → P2), and the point corresponding to the liquid-rich phase changes from L1 to L2 (L1 → L2). The degree of phase separation |L1, P1| gradually increases during this process and reaches the maximum at |L2, P2|. As the temperature continues to increase, both the polymer-rich phase and the liquid-rich phase surpass the binodal line, leading to a thermodynamic tendency of spontaneous mixing between the two phases (L2 → L3 and P2 → P3). During the TB < t < UCST process, the degree of phase separation initially increases, and then decreases. Consequently, the WPAM40-IL([EBIM]Br) ionogel become opaque initially, and then transparent (Movie S1 and S2, ESI†), corresponding to process I → II → III depicted in Fig. 2b. Once the temperature surpasses the UCST, the two phases mix uniformly, leading to a homogeneous state, which is denoted as A3 in the PAM-[EBIM]Br binary system. In this state, there is no phase separation and points L3 and P3 overlap at point A3, indicating |L3, P3| = 0, consistent with state III in Fig. 2b. Next, upon cooling the system below the UCST, phase separation occurs. The extent of phase separation, denoted as |L4, P4|, was influenced by the molecular chain activity and time scale. When considering the same time scale, higher molecular chain activity (corresponding to a higher temperature) leads to a greater |L4, P4|. Alternatively, when the molecular chain activity remains constant, a longer duration of phase separation results in a larger |L4, P4|. For both the ‘rapid-cooling’ and ‘slow-cooling’ processes, assuming that the WPAM40-IL([EBIM]Br) ionogel exhibits the same molecular chain activity at the same temperature, the degree of phase separation from the UCST to TB is solely dependent on the length of the phase separation time scale. In the case of the ‘slow-cooling’ process, the phase separation occurs for a long time, and the L and P points of the WPAM40-IL([EBIM]Br) ionogel reach points L4s and P4s along the L3 → L4s and P3 → P4s paths starting from point A3, respectively. At this time, ∣L4s, P4s∣ > ∣L0, P0∣, with a high degree of phase separation, resulting in an opaque ionogel macroscopically, corresponding to state IV in Fig. 2b. In the ‘rapid-cooling’ process, the phase separation occurs for a short time, and the L and P points of the WPAM40-IL([EBIM]Br) ionogel reach points L4f and P4f along the L3 → L4f and P3 → P4f paths starting from point A3, respectively. At this time, ∣L4f, P4f∣ < ∣L0, P0∣, with a low degree of phase separation, which has less obstruction to light transmission, resulting in a transparent gel macroscopically, corresponding to state V in Fig. 2b. When the temperature further decreases (t < TB), the PAM molecular chains exhibit less activity, the phase separation process stops, and the polymer-rich phase and liquid-rich phase of the WPAM40-IL([EBIM]Br) ionogel change from points P4 and L4 to the corresponding P5 and L5 points, respectively. Based on the above analysis, for the WPAMx-IL([EBIM]Br) ionogel, phase separation behavior occurs in the temperature range from UCST to TB due to the presence of UCST and Berghmans' points, and the degree of phase separation ∣L, P∣ is determined by
the time scale of this process, which is affected by the cooling rate.
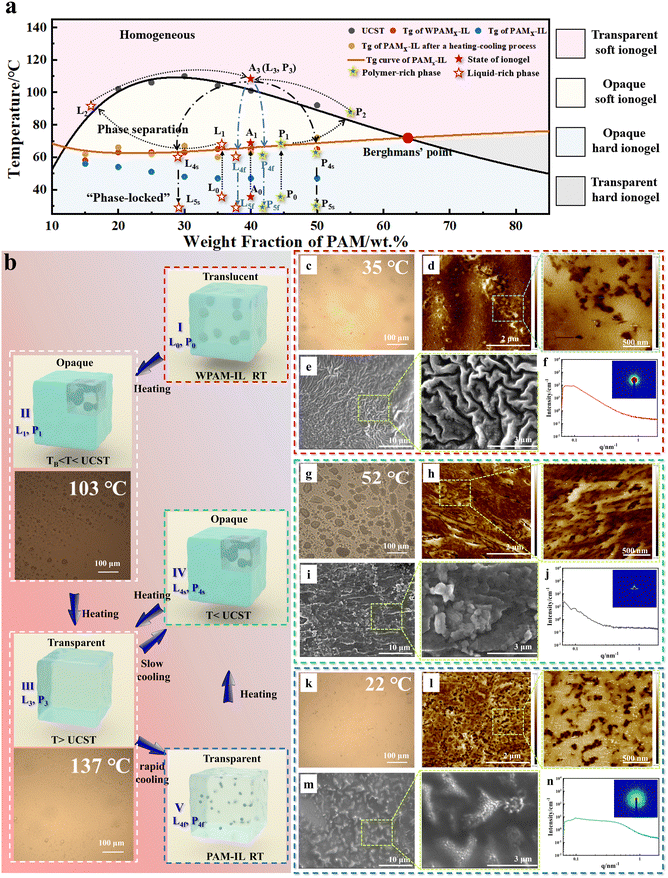 |
| Fig. 2 Characterization of the phase separation of PAMx-IL([EBIM]Br) ionogels. (a) Phase diagram of PAM-[EBIM]Br binary system, where the black dashed lines represent the trajectory of the points corresponding to the polymer-rich phase and liquid-rich phase in the phase diagram. (b) Proposed mechanism of PAM-IL phase separation behaviors during heating and cooling, where (I), (II), (III), (IV) and (V) correspond to the five states of the ionogel in (a). (c)–(f) Phase separation structure of WPAM40-IL([EBIM]Br) ionogel, (c) optical microscopy image, (d) AFM images, (e) SEM images and (f) SAXS data. (g)–(j) Phase separation structure of the ionogel obtained by slow cooling of the WPAM40-IL([EBIM]Br) ionogel, (g) optical microscopy image, (h) AFM images, (i) SEM images and (j) SAXS data. (k)–(n) Phase separation structure of the PAM40-IL([EBIM]Br) ionogel, (k) optical microscopy image, (l) AFM images, (m) SEM images and (n) SAXS data. In (d), (e), (h), (i), (l) and (m), the images on the right side are enlargements of the corresponding regions in the left-side images. | |
To validate our proposed phase separation mechanism, we conducted a comprehensive characterization of the microstructure of the PAMx-IL([EBIM]Br) ionogels using various techniques such as optical microscopy, AFM, SEM, and SAXS. The aim of this investigation was to examine the changes in microscopic morphology during phase separation and the impact of the gel composition on the phase separation structure. Taking the PAM40-IL([EBIM]Br) ionogel as an example, Fig. 2c, g and k show the phase separation structures observed under an optical microscope. As evident in these figures, the WPAM40-IL([EBIM]Br) ionogel exhibited a certain degree of phase separation. The ionic liquid was extruded and converged into droplets, and then absorbed by the ionogel during heating, while the liquid was extruded and converged again into droplets during slow-cooling. When phase separation occurred, the IL separated from the polymer, and the IL squeezed out from the ionogel. As the temperature increased, the phase separation structure disappeared, and the IL and polymer re-mixed.23 After heating and slow-cooling, the degree of phase separation intensified, resulting in a more pronounced structure. Conversely, the PAM40-IL([EBIM]Br) ionogel obtained through rapid-cooling displayed almost no visible phase separation structure under an optical microscope. AFM provided a clearer view of the phase separation structure, where both the WPAM40-IL([EBIM]Br) ionogel and PAM40-IL([EBIM]Br) ionogel exhibited the typical ‘sea-island’ structures. These islands represent the microdomains formed by polymer aggregation (Fig. 2d and l). The microdomains in the PAM40-IL([EBIM]Br) ionogel were uniformly distributed with a consistent size of around 50–100 nm, which is smaller than that of the WPAM40-IL([EBIM]Br) ionogel (approximately 125–175 nm). However, after slow-cooling, the resulting ionogel exhibited noticeably larger microdomains, with a size of approximately 150–200 nm, and a higher quantity compared to the PAM40-IL([EBIM]Br) ionogel (Fig. 2h). The phase separation morphology observed in the SEM images slightly differs. Both the PAM40-IL([EBIM]Br) ionogel and WPAM40-IL([EBIM]Br) ionogel featured randomly folded structures with particle-like protrusions on the fold surfaces, having similar diameters as the microdomains observed under AFM (around 100 nm). The gel obtained after slow-cooling exhibited larger particle-like protrusions in SEM, approximately 200 nm in diameter, which aggregated to form larger cluster structures. The phase separation structure of the three ionogels was further studied using SAXS. Fig. 2f, j and n show the one-dimensional and two-dimensional SAXS patterns of the three ionogels. It can be observed that the phase-separated microdomain size of the WPAM40-IL([EBIM]Br) ionogel and ionogel obtained through slow-heating was too large to be clearly displayed in SAXS. However, the PAM40-IL([EBIM]Br) ionogel exhibited a broad characteristic peak corresponding to a q value of 0.25–0.73, with calculated microdomain sizes in the range of 8.6 to 25 nm. This further indicates that the PAM40-IL([EBIM]Br) ionogel obtained through rapid-cooling has smaller phase separation structures. When subjected to high temperatures (above 120 °C), the phase separation structure in the ionogel disappeared, as confirmed by the optical microscope images and the high transparency exhibited at elevated temperatures. These observations are consistent with the proposed mechanism, indicating that the cooling rate can control the extent of phase separation.
Similar structural changes during heating and cooling, which are related to phase separation, were observed in the other PAMx-IL([EBIM]Br) ionogel compositions, suggesting that these changes are not isolated instances. Fig. S8 (ESI†) shows the phase separation structure changes under an optical microscope for the WPAM30-IL([EBIM]Br), WPAM35-IL([EBIM]Br), and WPAM50-IL([EBIM]Br) ionogels. These ionogels also exhibited the characteristic ‘translucent to opaque to transparent to opaque’ changes during the heating and slow-cooling process, with distinct ‘sea-island’ phase separation structures in the resulting ionogels. The internal structural model of the equilibrium ionogels obtained through MD also shows that PAM tends to aggregate mutually in the gels with different chemical compositions, and this trend becomes more pronounced with a higher polymer content (Fig. S10, ESI†). Fig. S11 (ESI†) displays the SEM images of the PAMx-IL([EBIM]Br) ionogels. All the PAMx-IL([EBIM]Br) ionogels exhibited phase separation except the PAM15-IL([EBIM]Br) ionogel, which showed similar folded and protrusion structures. Furthermore, the ionogels obtained after heating and slow-cooling demonstrated a significantly higher degree of phase separation compared to the corresponding PAMx-IL([EBIM]Br) ionogels.
Mechanical properties of PAMx-IL([EBIM]Br) ionogels
The WPAMx-IL([EBIM]Br) ionogels exhibited poor mechanical properties, while the PAMx-IL([EBIM]Br) ionogels possessed excellent mechanical properties after ‘heating and rapid-cooling’. Fig. 3a and Movie S3 (ESI†) show the mechanical properties of the PAMx-IL([EBIM]Br) ionogels intuitively. A strip of the PAM30-IL([EBIM]Br) ionogel (30 × 10 × 1 mm) could easily lift a 13.4 kg weight after folding in half without breaking. It could also be stretched to 4 times its original length or compressed into a round cake. These test photos indicate that the PAMx-IL([EBIM]Br) ionogels have high strength, extensibility and plasticity.
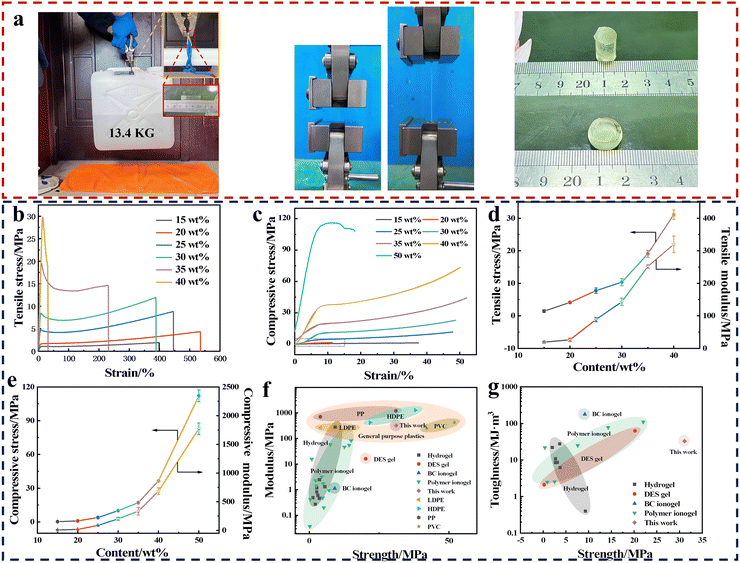 |
| Fig. 3 Mechanical properties of PAMx-IL([EBIM]Br) ionogels. (a) Optical photos of the mechanical test of PAMx-IL([EBIM]Br) ionogels. (b) Tensile and (c) compressive stress–strain curves of PAMx-IL([EBIM]Br) ionogels. (d) and (e) Relationship between the PAM content and (d) tensile strength and tensile modulus and (e) compressive yield strength and compressive modulus. (f) and (g) Comparison between this work and polymer ionogels, hydrogels, deep eutectic solvent (DES) gels, bacterial cellulose (BC) ionogels and general-purpose plastics in terms of (f) tensile modulus and (g) toughness in relation to tensile strength.3,4,6,8,13,26–43 The details are listed in ESI,† Table S3. Error bars show the standard deviation from three independent samples. | |
The mechanical properties of the PAMx-IL([EBIM]Br) ionogels were further characterized by uniaxial tensile and compression tests. Movie S4 (ESI†) recorded the change in the PAM30-IL([EBIM]Br) ionogel during the stretching process, where an obvious stress whitening phenomenon was observed. Fig. 3b shows the tensile stress–strain curves of the PAMx-IL([EBIM]Br) ionogels. The PAMx-IL([EBIM]Br) ionogels have the typical ‘strong and tough’ tensile stress–strain curves. Among them, the PAM20-IL([EBIM]Br) ionogel has the highest tensile elongation at break, reaching 535%, but with a continuous increase in the PAM content, the elongation at break decreased rapidly. When the PAM content reached 40 wt%, the PAM40-IL([EBIM]Br) ionogel still had tensile deformation capacity, and its elongation at break was 30.2%, while the elongation of most rigid gel materials is usually less than 5%.24 It can be seen in Fig. 3d that the tensile strength and tensile modulus of the PAMx-IL([EBIM]Br) ionogels gradually increased with an increase in PAM content. The PAM40-IL([EBIM]Br) ionogel had a tensile strength of 31.1 MPa and Young's modulus of 319.80 MPa, exceeding that of the majority of gel materials reported to date (Fig. 3f and g), respectively. In addition to excellent tensile properties, the compression properties of the PAMx-IL([EBIM]Br) ionogels are also fantastic. The PAMx-IL([EBIM]Br) ionogels show the compression stress–strain curves of typical plastic materials, as shown in Fig. 3c and Fig. S12 (ESI†). There was an apparent yield phenomenon in the compression stress–strain curves. Compared with the obvious failure phenomenon of brittle materials in the compression process, plastic materials will continue to deform after compression yield, and thus do not have compression strength. The compressive yield strength is the upper limit for plastic materials in practice. The compressive yield strength and compressive modulus of the PAMx-IL([EBIM]Br) ionogels also increased with an increase in PAM content (Fig. 3e). When the content of PAM reached 50 wt%, the compressive yield strength of the PAM50-IL([EBIM]Br) ionogel was 112.2 MPa and its compressive modulus was 1.77 GPa. In the case of gel materials, this compression performance is excellent. Similarly, we tested the mechanical properties of the WPAMx-IL([EBIM]Br) ionogels without ‘heating and rapid-cooling’. As shown in Fig. S13 and Table S2 (ESI†), the strength and toughness of the untreated WPAMx-IL([EBIM]Br) ionogels were inferior to the corresponding post-processed PAMx-IL([EBIM]Br) ionogels.
The toughening of gels often involves an enhancement in their energy dissipation capability under applied stress. This is achieved by promoting the interactions between polymer chains, such as hydrogen bonding, ionic bonding, and chain entanglement. Phase separation can also contribute to the enhancement of energy dissipation in gels, and this phenomenon is generally attributed to two main factors. Firstly, phase separation provides physical crosslinking points within the gel network, increasing the degree of network crosslinking and facilitating energy dissipation during deformation under stress (Fig. 1d). These physical crosslinks act as sacrificial bonds, which can break and reform, absorbing and dissipating energy. Secondly, the interface regions formed between the two phases as a result of phase separation are more susceptible to transitioning between ‘compatible’ and ‘separated’ states.18,25 This transition at the interface can further dissipate energy during mechanical deformation. In gels with high solvation, the presence of a solvent keeps the polymer chains separated, hindering the formation of strong interchain interactions such as hydrogen bonding. Consequently, the gel exhibits softness and stretchability. Conversely, in gels with low solvation, the absence of solvent restricts the chain mobility, leading to stiff and brittle behavior.13 Therefore, the degree of phase separation plays a crucial role in determining the toughness of gels. Moderate phase separation can enhance the strength and toughness of gels, while excessive phase separation can make gels brittle. When the WPAMx-IL([EBIM]Br) ionogels were obtained from pre-PAM-IL through UV curing, they were translucent and fragile with a high degree of phase separation (Fig. 1g and Fig. S5, ESI†). To improve the toughness of the ionogels, we needed to regulate the phase separation process and maintain it at a more ideal degree. As mentioned earlier, the degree of phase separation in gels can be adjusted by controlling the cooling rate. When the temperature dropped rapidly from the UCST to a temperature below TB, the system was locked in the metastable state because the WPAMx-IL([EBIM]Br) ionogel did not have sufficient time to realise a high degree of phase separation. Therefore, the PAMx-IL([EBIM]Br) ionogels maintained transparent and obtain excellent toughness. Thus, the result of the tensile test proves that the strategy we proposed to control the phase separation structure through ‘heating and rapid-cooling’ to improve the mechanical properties is feasible and effective.
Stability of PAMx-IL([EBIM]Br) ionogels
The stability of an ionogel is of great significance for its practical application.5,44 As shown in Fig. 4a, pre-PAM40-IL([EBIM]Br) exhibited excellent stability. After 30 days of storage at room temperature (in the dark), there was no delamination, discoloration, or gel in pre-PAM40-IL([EBIM]Br). The viscosity of pre-PAM40-IL([EBIM]Br) basically remained unchanged at 150 °C for 5 min, indicating that the precursor solution was stable and did not gel at high temperature (Fig. 4b). In the practical application of hydrogels, the water easily volatilizes, which leads to a decline in their performance.8 However, the non-volatility of ILs can prevent this problem.36 The quality of the PAM40-IL([EBIM]Br) ionogel did not change significantly when it was placed under vacuum for 220 h, indicating its excellent vacuum stability (Fig. 4c). Besides, the PAMx-IL([EBIM]Br) ionogels also possessed excellent thermal stability. As shown in Fig. 4d and Fig. S14 (ESI†), the PAMx-IL([EBIM]Br) ionogels began to decompose at 257 °C, which is attributed to the decomposition of the brominated ILs, and reached the fastest at 326 °C, while PAM began to decompose at 426 °C.
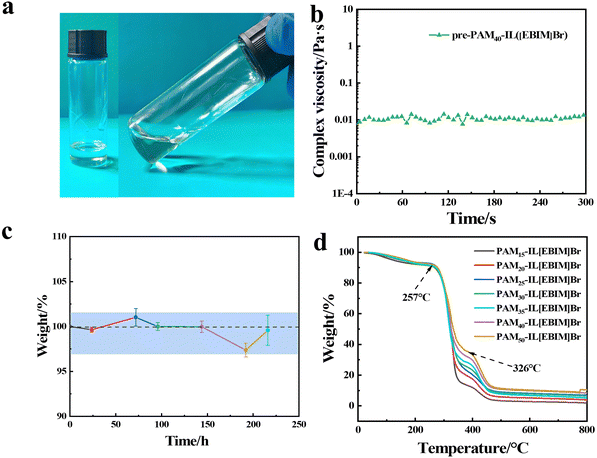 |
| Fig. 4 Stability of the pre-PAM-IL and PAMx-IL([EBIM]Br) ionogels. (a) Precursor solution pre-PAM40-IL([EBIM]Br) after being stored in the dark at room temperature for 30 days. (b) Viscosity-time curve of pre-PAM40-IL([EBIM]Br) at 120 °C. (c) Mass change in the PAM50-IL([EBIM]Br) ionogel in a vacuum environment. (d) TGA curves of PAMx-IL([EBIM]Br) ionogels. Error bars show the standard deviation from three independent samples. | |
Multi-functionality of PAMx-IL([EBIM]Br) ionogels
Shape-memory performance of PAMx-IL([EBIM]Br) ionogels.
In addition to excellent mechanical properties and stability, the PAMx-IL([EBIM]Br) ionogels exhibited excellent multi-functionality. Due to the phase separation during cooling, the PAMx-IL([EBIM]Br) ionogels showed shape-memory performance. As shown in Fig. 5a, after changing the flat PAM40-IL([EBIM]Br) ionogels into different shapes at high temperature, such as a ‘flower’, ‘thread’, ‘snail’ and ‘box’, they could recover to their original shape during heating. The illustration shows the corresponding photos under an infrared camera, and the shape recovery process was recorded in Fig. S15 and Movie S5 (ESI†). The PAMx-IL([EBIM]Br) ionogels were flexible at 120–140 °C, and their shapes could be easily controlled programmatically, and then fixed during cooling. When the temperature increased again, the PAM40-IL([EBIM]Br) ionogels could trigger the shape-memory ability to recover from the temporary shape to the original shape.
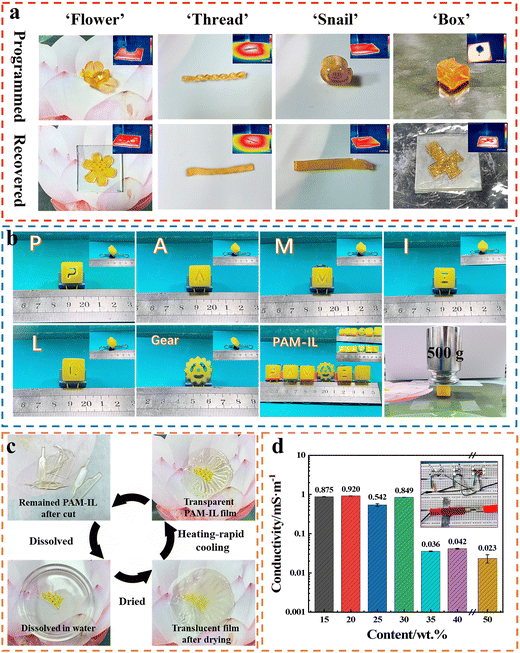 |
| Fig. 5 Multi-functionality of PAMx-IL([EBIM]Br) ionogels. (a) Heating-induced shape-memory behaviors of PAMx-IL([EBIM]Br) ionogels, which were dyed yellow. (b) Optical photos of the PAMx-IL([EBIM]Br) ionogel sample formed by 3D printing and its load-bearing display. The pre-PAM-IL used in 3D printing contained 0.3 wt% TPO photo-initiator, and it was coloured yellow. (c) Recycling process of PAMx-IL([EBIM]Br) ionogels in water. (d) Conductivity of PAMx-IL([EBIM]Br) ionogels, and the inset is a photo of the diode lit by the PAM15-IL([EBIM]Br) ionogel. Error bars show the standard deviation from three independent samples. | |
The driving force for the shape memory during the heating process is the internal stress generated in the gel during deformation and cooling.13 At high temperatures, the gel was shaped into a specific form through the application of external force. During the subsequent cooling process, the formation of phase-separated structures triggered crosslinking within the gel network, leading to the accumulation of internal stress. However, at lower temperatures (t < TB), the PAM polymer chains became immobilized, impeding the release of internal stress. Upon reheating, the internal stress gradually relaxed, enabling the gel to revert to its original shape.
3D printing PAMx-IL([EBIM]Br) ionogels.
When using the more efficient photo-initiator TPO to replace I2959, the PAMx-IL([EBIM]Br) ionogels could achieve rapid curing in 3 s (Movie S6, ESI†), and thus have the possibility to be shaped through 3D printing. Therefore, we configured a pre-PAM-IL containing TPO and used it as a raw material for 3D printing verification. The 3D-printed PAMx-IL([EBIM]Br) ionogel samples are shown in Fig. 5b, where pre-PAM-IL could be easily shaped by 3D printing. The 3D-printed PAMx-IL([EBIM]Br) ionogel samples exhibited good mechanical properties, which could withstand a load of 500 g without deformation and damage.
Recoverability of PAMx-IL([EBIM]Br) ionogels.
There is no chemical cross-linking in the PAMx-IL([EBIM]Br) ionogels. The polymer-rich phase and reversible intermolecular interactions in the PAMx-IL([EBIM]Br) ionogels act as the physical cross-links. When the PAMx-IL([EBIM]Br) ionogels were broken due to structural damage, aging or other stress, they could be easily recycled, avoiding environmental pollution. The recovery process of the PAMx-IL([EBIM]Br) ionogels is also environmentally friendly without pollution, which can be recovered by dissolving in water, and then volatilizing the water to avoid the secondary damage of volatile organic recovery solvents to the environment. As shown in Fig. 5c, the translucent PAM40-IL([EBIM]Br) ionogel film could be obtained again after the dissolution and drying. Then, through a ‘heating and rapid-cooling’ process, the PAM40-IL([EBIM]Br) ionogel film changed from translucent to transparent. The changes in the mechanical properties of the PAM40-IL([EBIM]Br) ionogel before and after recycling were further investigated through tensile testing (Fig. S16, ESI†). The recycled PAM40-IL([EBIM]Br) ionogel demonstrated a tensile strength of 23.5 MPa and elongation at break of 23.0%, accounting for 75.6% and 76.1% of that of the initial ionogel, respectively. Furthermore, the stress–strain curves indicated a minimal variation in the tensile modulus of the ionogel before and after recycling.
Conductivity of PAMx-IL([EBIM]Br) ionogels.
Ionogels have great application prospects in the field of flexible electronics due to their ionic conductivity. Movie S7 (ESI†) and the illustration in Fig. 5d show that the PAMx-IL([EBIM]Br) ionogels could make a diode glow, indicating their appropriate conductivity. Their conductivity also was tested using the two-electrode method, and the results are shown in Fig. 5d. The content of PAM had a significant impact on the conductivity of the PAMx-IL([EBIM]Br) ionogels. When the content of PAM was less than 30 wt%, the conductivity of the ionogels was in the range of 0.54–0.92 mS m−1. Whereas, when the content of PAM exceeded 30 wt%, the conductivity of the ionogels dropped suddenly by about an order of magnitude. This may be because the increase in polymer content reduces the path of IL formation in the PAMx-IL([EBIM]Br) ionogels. With its exceptional mechanical properties, high transparency, and conductivity, PAM-IL has potential applications in the field of flexible electronic devices. In this study, we constructed a straightforward PDMS/PAM-IL/PDMS ultra-thin keyboard to demonstrate its potential usability, as depicted in Fig. S17 and Movie S8 (ESI†). Leveraging the remarkable mechanical properties of the PAM40-IL([EBIM]Br) ionogel, even a 150 μm-thick film of PAM40-IL([EBIM]Br) ionogel exhibited commendable mechanical strength and elasticity. By combining it with two layers of PDMS film each measuring 100 μm in thickness, we were able to create a PDMS/PAM-IL/PDMS ultra-thin keyboard with a total thickness of merely 350 μm. An LCR digital bridge was utilized to evaluate the responsiveness of the PDMS/PAM-IL/PDMS ultra-thin keyboard across different clicking modes. The findings demonstrate that the signals generated by the PDMS/PAM-IL/PDMS ultra-thin keyboard exhibited strong discernibility under three clicking modes, namely, normal click, long press, and quick click (Fig. S17C, ESI†). Beyond ultra-thin keyboards, PAM-IL ionogels also hold substantial prospect for application in the field of flexible electronic touch screens.
Conclusions
In summary, we reported a simple method for the synthesis of tough ionogels by adjusting the degree of phase separation through a ‘heating and rapid-cooling’ post-process. Due to the partial compatibility between PAM and IL, phase separation behavior occurred during cooling. Once the temperature dropped below TB, the phase separation behavior of the ionogel was frozen, causing the gel to be in a phase-locked state. In this case, the phase separation behavior could be adjusted by controlling the cooling rate. Compared with the existing gel materials, the resulting PAMx-IL([EBIM]Br) ionogels exhibited excellent mechanical properties including a tensile strength of 31.1 MPa, tensile modulus of 319.8 MPa, compressive strength of 122 MPa and compressive modulus of 1.7 GPa. The PAMx-IL([EBIM]Br) ionogels were very transparent, stretchable and stable. Moreover, they exhibited multifunction of shape-memory, recyclability, and ionic conductivity, and could be shaped by 3D printing. Because of the excellent mechanical properties and multifunction, this kind of ionogel is expected to promote the development of flexible electronic devices in practical applications.
Experimental
Materials
1-Butylimidazole, bromoethane, 1-bromobutane, 1-bromoheptane, silver trifluoroacetate, 2-hydroxy-4′-(2-hydroxyethoxy)-2-methylpropiophenone (I2959), sodium tetrafluoroborate, and diphenyl (2,4,6-trimethylbenzoyl) phosphine oxide (TPO) were obtained from Shanghai Macklin Biochemical Co., Ltd. Ethyl acetate was purchased from Guangdong Guanghua Sci-Tech Co., Ltd. All reagents were used as received without further purification. Deionized water (DI) was self-made in the laboratory.
Preparation of ILs
Synthesis of 1-ethyl-3-butylimidazolium bromide [EBIM]Br.
1-Butylimidazole (41 g, 0.5 mol) and bromoethane (55 g, 0.5 mol) were mixed in ethyl acetate solution (80 mL) and stirred at 60 °C for 24 h. The product was separated after standing, the lower liquid was collected, washed 3–5 times with a small amount of ethyl acetate, and then the solvent was removed by rotary evaporation. 1H-NMR (400 MHz, CDCl3, δ): 10.34 (s, 1H), 7.60 (t, J = 1.6 Hz, 1H), 7.48 (t, J = 1.6 Hz, 1H), 4.43–4.23 (m, 4H), 1.91–1.75 (m, 2H), 1.53 (t, J = 7.4 Hz, 3H), 1.31 (dq, J = 14.8, 7.4 Hz, 2H), 0.87 (q, J = 7.4 Hz, 3H).
Synthesis of 1-butyl-3-butylimidazolium bromide [BBIM]Br.
1-Butylimidazole (41 g, 0.5 mol) and 1-bromobutane (68.5 g, 0.5 mol) were mixed in ethyl acetate solution (80 mL) and stirred at 60 °C for 24 h. The product was separated after standing, the lower liquid was collected, washed 3–5 times with a small amount of ethyl acetate, and then the solvent was removed by rotary evaporation. 1H-NMR (400 MHz, CDCl3, δ): 10.29 (s, 1H), 7.52 (d, J = 1.5 Hz, 2H), 4.26 (t, J = 7.4 Hz, 4H), 1.88–1.72 (m, 4H), 1.36–1.17 (m, 4H), 0.84 (t, J = 7.4 Hz, 6H).
Synthesis of 1-heptyl-3-butylimidazolium bromide [HBIM]Br.
1-Butylimidazole (41 g, 0.5 mol) and 1-bromoheptane (89.5 g, 0.5 mol) were mixed in ethyl acetate solution (80 mL) and stirred at 60 °C for 24 h. The product was separated after standing, the lower liquid was collected, washed 3–5 times with a small amount of ethyl acetate, and then the solvent was removed by rotary evaporation. 1H-NMR (400 MHz, CDCl3, δ): 10.36 (s, 1H), 7.51 (dd, J = 20.6, 1.5 Hz, 2H), 4.29 (dt, J = 9.7, 7.5 Hz, 4H), 1.93–1.55 (m, 4H), 1.41–1.00 (m, 10H), 0.93–0.65 (m, 6H).
Synthesis of 1-ethyl-3-butylimidazolium trifluoroacetate [EBIM]TFA.
Equimolar [EBIM]Br and silver trifluoroacetate were mixed in DI and stirred at RT for 24 h. The product was vacuum filtered 2–3 times to remove any insoluble matter. The product was obtained after removing the solvent from the filtrate by rotary evaporation. 1H-NMR (400 MHz, CDCl3, δ): 10.09 (s, 1H), 7.43 (s, 1H), 7.36 (s, 1H), 4.37–4.12 (m, 4H), 1.81 (td, J = 15.1, 7.6 Hz, 2H), 1.50 (t, J = 7.4 Hz, 3H), 1.30 (td, J = 15.1, 7.6 Hz, 2H), 0.89 (t, J = 7.4 Hz, 3H).
Synthesis of 1-ethyl-3-butylimidazolium tetrafluoroborate [EBIM]BF4.
Equimolar [EBIM]Br and sodium tetrafluoroborate were mixed in DI and stirred at RT for 24 h. The product was vacuum filtered 2–3 times to remove insoluble matter. The product was obtained after removing the solvent from the filtrate by rotary evaporation. 1H-NMR (400 MHz, CDCl3, δ): 9.52 (s, 1H), 7.51 (s, 1H), 7.43 (s, 1H), 4.36–4.14 (m, 4H), 1.90–1.70 (m, 2H), 1.50 (t, J = 7.4 Hz, 3H), 1.41–1.07 (m, 2H), 0.87 (t, J = 7.4 Hz, 3H).
Preparation of PAM-IL ionogels without post-processing (WPAM-IL ionogels)
Generally, AM (15 wt%, 20 wt%, 25 wt%,30 wt%, 35 wt%, 40 wt%, and 50 wt%) was prepared, and I2959 (photo-initiator, 0.05% molar ratio to monomer) was added to the ionic liquids. The mixture was ultrasonicated at 40 °C for 60 min until a homogeneous and fully transparent solution was obtained. The precursor solution was named pre-PAM-IL. Then, the transparent solution was poured into a mould made of clear glass. Polymerization was initiated by UV irradiation using a 365 nm UV lamp (6 W) for 10 min. The hard and translucent solid obtained could be easily detached from the mould, which was named as WPAM-IL ionogels.
Preparation of PAM-IL ionogels
In the case of the ionogels prepared with [EBIM]Br, the UV-light cured WPAM-IL ionogels were fragile and needed to be post-processed to improve their transparency and mechanical properties. The WPAM-IL ionogels were placed in an oven at 120 °C–140 °C for 15–20 min (when making the sample transparent, there should be no obvious bubbles between the sample and the glass base plate, not affecting subsequent experiments). Then they were placed at room temperature (about 18 °C) for rapid cooling (above 70 °C min−1) to obtain transparent and tough PAM-IL ionogels. In the case of the ionogels prepared with other ILs ([BBIM]Br, [HBIM]Br, [EBIM]TFA, and [EBIM]BF4), the temperature and post-process were the same (120–140 °C for 15–20 min), but these samples did not become transparent during heating and after cooling. When it was necessary to accurately specify the composition of a particular ionogel, according to the difference in the mass fraction of PAM and the type of ionic liquids, the ionogels were recorded as PAMx-IL(Y), where ‘x’ represents the mass fraction of polymer and ‘Y’ represents the type of ionic liquid. For example, the PAM30-IL([EBIM]Br) ionogel possesses 30 wt% PAM and it contains is [EBIM]Br as the ionic liquid. In addition, the translucent primary ionogel that did not undergo the ‘heating and rapid-cooling’ post-processing was denoted as WPAMx-IL (Y) ionogel, and the precursor solution for its preparation is pre-PAMx-IL(Y).
Measurement
The transparency of the ionogel films was measured using a UV-vis spectrophotometer (UNICO UA-2600A). FT-IR spectra were recorded using a Bruker Tensor II spectrometer in the wavenumber range of 4000 to 500 cm−1. 1H-NMR spectroscopic experiments were performed on a Bruker Avance 400 MHz spectrometer. The crystal performance of the samples was analysed using a Shimadzu XRD-7000 X-ray diffractometer with Cu Kα radiation (λ = 1.5406 Å) in the range of 5°–80° (2θ) at 30 kV. Differential scanning calorimetry (DSC) experiments were carried out on a Mettler-Toledo DSC-1 at a heating or cooling rate of 10 K min−1 under an N2 atmosphere. The viscoelasticity behavior was observed using a rheometer (AR2000EX). Atomic force microscopy (AFM) phase images were observed using a Bruker Dimension Icon microscope in tapping mode. Infrared thermal imaging photos were obtained through an infrared camera (Fotric 225 s). The morphologies of the hydrogels were characterized via scanning electron microscopy (FEI Verios G4). The phase-separated domains in the gel networks were analysed using an SAXS instrument with Cu X-ray radiation and wavelength of 0.154 nm (SAXS2, SAXSLab Ganesha). The 3D printing test was carried out with a AUTOCERA-M DLP 3D printer (Beijing TenDimensions Technology Co., Ltd), and the printing accuracy was 10 μm. The resistance of the PAM-IL ionogels was tested utilizing a two-probe measurement system (KEYSIGHT 34972A). Thermogravimetric analysis (TGA) was investigated with a linear heating rate of 10 °C min−1 from room temperature to 800 °C under an N2 atmosphere using a TGAQ50 instrument. The specimen mass ranged from 6 to 10 mg, and every sample was measured three times on average.
Simulation calculation
To analyse the formation of hydrogen bonds and weak interaction formed by PAM in the ionogels, theoretical calculations were performed using the Gaussian 09w software.45 Density functional theory (DFT) was employed, and the binding energies of hydrogen bonds formed by PAM and [EBIM]Br were calculated using a model compound instead of polymer chains. The B3LYP functional was used, and the structure optimization was conducted using the 6-31+g(d) basis set.2 Additionally, energy calculations were carried out using the 6-31++g(d,p) basis set, considering the basis set superposition error (BSSE).
To further analyse the structure of the PAMx-IL([EBIM]Br) ionogels, molecular structure simulation was conducted using the Materials Studio 8.0 software. Instead of using real random copolymer chains, a model compound consisting of 20 segments was utilized.46 Four model chains were placed in each box, and the appropriate amount of ionic liquid was added to maintain the polymer mass at 35% of the total mass. The simulation process involved geometric optimization, followed by annealing for 25 cycles at 500 K. Lastly, a dynamic simulation was conducted for 1 ps to obtain the final equilibrium structure of the ionogels.47
Cloud point test
The phase separation behavior of the ionogels in the process of ‘heating and slow-cooling’ was observed using an optical microscope (Nikon ECLIPSE LV150N). Firstly, the temperature was increased to make the WPAMx-IL([EBIM]Br) ionogels transparent at the rate of 5 °C min−1, and then reduced to room temperature at the rate of 3 °C min−1 and the temperature recorded when the phase separation phenomenon occurred or the brightness obviously darkened in the field of vision, which was the cloud point.
Mechanical test
The tensile properties of the ionogels were tested using a SANS CMT-8505 universal testing machine loaded with a 500 N load cell. Dumbbell specimens according to GB/T528-2009 Type 4 (thickness: 1 mm, length and width of the narrow parallel portion: 12 mm and 2 mm, respectively) were cut for testing. In the cyclic tensile tests, the sample was stretched at a rate of 100 mm min−1 to a specific axial strain, and then returned to zero stress at the same crosshead speed. The compressive properties were tested using a SANS CMT-7404 universal testing machine fitted with a 10 kN load cell. In the compressive test, a cylindrical sample with a diameter of 10 mm and height of 15 mm was employed.
Author contributions
The manuscript was written through the contributions of all authors. All authors have given approval to the final version of the manuscript. Jinliang Xie, conceptualization, methodology, investigation, visualization, software, writing – original draft, and writing – review & editing. Xiaoqian Li, investigation, writing – review & editing. Ling Fan, writing – review & editing. Zhongjie He, writing-review & editing. Dongdong Yao, writing – review & editing, resources, and funding acquisition. Yaping Zheng, supervision, resources, and funding acquisition.
Conflicts of interest
There are no conflicts to declare.
Acknowledgements
This work is supported by the Aeronautical Science Foundation of China (No. 2018ZF53065), the Key project of Shaanxi Provincial Natural Science Foundation (No. 2021JZ-09), and the National Natural Science Foundation of China (No. 21905228).
Notes and references
- L. Xu, Z. Huang, Z. Deng, Z. Du, T. L. Sun, Z.-H. Guo and K. Yue, Adv. Mater., 2021, 33, 2105306 CrossRef CAS.
- L. Li, W. Li, X. Wang, X. Zou, S. Zheng, Z. Liu, Q. Li, Q. Xia and F. Yan, Angew. Chem., Int. Ed., 2022, 61, 202212512 CrossRef.
- M. W. Zhang, R. Yu, X. L. Tao, Y. Y. He, X. P. Li, F. Tian, X. Y. Chen and W. Huang, Adv. Funct. Mater., 2022, 33, 2208083 CrossRef.
- Y. Zhao, D. L. Gan, L. C. Wang, S. Y. Wang, W. J. Wang, Q. Wang, J. J. Shao and X. C. Dong, Adv. Mater. Technol., 2023, 8, 2201566 CrossRef.
- Z. Q. Cao, H. L. Liu and L. Jiang, Mater. Horiz., 2020, 7, 912 RSC.
- L. Yu, S. Guo, Y. Lu, Y. Li, X. Lan, D. Wu, R. Li, S. Wu and X. Hu, Adv. Energy Mater., 2019, 9, 1900257 CrossRef.
- Z. Li, S. Gadipelli, H. Li, C. A. Howard, D. J. L. Brett, P. R. Shearing, Z. Guo, I. P. Parkin and F. Li, Nat. Energy, 2020, 5, 160 CrossRef CAS.
- B. Yiming, Y. Han, Z. Han, X. Zhang, Y. Li, W. Lian, M. Zhang, J. Yin, T. Sun, Z. Wu, T. Li, J. Fu, Z. Jia and S. Qu, Adv. Mater., 2021, 33, 2006111 CrossRef CAS PubMed.
- K. G. Cho, S. An, D. H. Cho, J. H. Kim, J. Nam, M. Kim and K. H. Lee, Adv. Funct. Mater., 2021, 31, 2102386 CrossRef CAS.
- Y. H. Ye, H. Oguzlu, J. Y. Zhu, P. H. Zhu, P. Yang, Y. L. Zhu, Z. M. Wan, O. J. Rojas and F. Jiang, Adv. Funct. Mater., 2023, 33, 2209787 CrossRef CAS.
- Z. Luo, W. Li, J. Yan and J. Sun, Adv. Funct. Mater., 2022, 32, 2203988 CrossRef CAS.
- Y. Wang, S. Kalytchuk, Y. Zhang, H. Shi, S. V. Kershaw and A. L. Rogach, J. Phys. Chem. Lett., 2014, 5, 1412 CrossRef CAS PubMed.
- M. Wang, P. Zhang, M. Shamsi, J. L. Thelen, W. Qian, V. K. Truong, J. Ma, J. Hu and M. D. Dickey, Nat. Mater., 2022, 21, 359 CrossRef CAS PubMed.
- M. Wang, J. Hu and M. D. Dickey, JACS Au, 2022, 2, 2645 CrossRef CAS.
- W. Li, L. Li, Z. Liu, S. Zheng, Q. Li and F. Yan, Adv. Mater., 2023, 35, 2301383 CrossRef CAS PubMed.
- L. Chen, C. Zhao, J. Huang, J. Zhou and M. Liu, Nat. Commun., 2022, 13, 6821 CrossRef CAS.
- T. P. Lodge, Science, 2008, 321, 50 CrossRef CAS.
- D. Wang, J. Xu, J. Chen, P. Hu, Y. Wang, W. Jiang and J. Fu, Adv. Funct. Mater., 2019, 30, 1907109 CrossRef.
- X. Du, P. P. He, C. Wang, X. Wang, Y. Mu and W. Guo, Adv. Mater., 2023, 35, 2206302 CrossRef CAS PubMed.
- T. Ueki and M. Watanabe, Chem. Lett., 2006, 35, 964 CrossRef CAS.
- S. So and R. C. Hayward, ACS Appl. Mater. Interfaces, 2017, 9, 15785 CrossRef CAS.
- S. Kasapis, Crit. Rev. Food Sci. Nutr., 2008, 48, 341 CrossRef CAS.
- C. Zhao, L. Chen, Y. Ru, L. Zhang and M. Liu, Soft Matter, 2022, 18, 5934 RSC.
- B. A. Sun and W. H. Wang, Prog. Mater. Sci., 2015, 74, 211 CrossRef CAS.
- Y. Yang, D. Davydovich, C. C. Hornat, X. L. Liu and M. W. Urban, Chem, 2018, 4, 1928 CAS.
- N. Yuan, L. Xu, H. Wang, Y. Fu, Z. Zhang, L. Liu, C. Wang, J. Zhao and J. Rong, ACS Appl. Mater. Interfaces, 2016, 8, 34034 CrossRef CAS PubMed.
- Y. Yang, X. Wang, F. Yang, L. Wang and D. Wu, Adv. Mater., 2018, 30, 1707071 CrossRef PubMed.
- S. X. Pan, M. Xia, H. H. Li, X. L. Jiang, P. X. He, Z. G. Sun and Y. H. Zhang, J. Mater. Chem. C, 2020, 8, 2827 RSC.
- S. H. Li, H. Y. Pan, Y. T. Wang and J. Q. Sun, J. Mater. Chem. A, 2020, 8, 3667 RSC.
- T. Nakajima, Y. Fukuda, T. Kurokawa, T. Sakai, U. I. Chung and J. P. Gong, ACS Macro Lett., 2013, 2, 518 CrossRef CAS PubMed.
- L. J. Zhou, X. J. Pei, K. Fang, R. Zhang and J. Fu, Polymer, 2020, 192, 122319 CrossRef CAS.
- J. Wen, X. Zhang, M. Pan, J. Yuan, Z. Jia and L. Zhu, Polymers, 2020, 12, 239 CrossRef CAS PubMed.
- Y. Zhang, M. Y. Li, X. Han, Z. W. Fan, H. H. Zhang and Q. L. Li, Chem. Phys. Lett., 2021, 769, 138437 CrossRef CAS.
- H. P. Yu and Y. J. Zhu, Nano Res., 2021, 14, 3643 CrossRef CAS.
- H. Zhang, N. Tang, X. Yu, M. H. Li and J. Hu, Adv. Funct. Mater., 2022, 32, 2206305 CrossRef CAS.
- T. Li, Y. Wang, S. Li, X. Liu and J. Sun, Adv. Mater., 2020, 32, 2002706 CrossRef PubMed.
- P. Liu, D. F. Pei, Y. P. Wu, M. J. Li, X. H. Zhao and C. X. Li, J. Mater. Chem. A, 2022, 10, 25602 RSC.
- H. Wang, J. Xu, K. Li, Y. Dong, Z. Du and S. Wang, J. Mater. Chem. B, 2022, 10, 1301 RSC.
- G. D. Fan, K. K. Liu, H. Su, Y. Q. Luo, Y. Geng, L. Y. Chen, B. J. Wang, Z. P. Mao, X. F. Sui and X. L. Feng, Chem. Eng. J., 2022, 434, 134702 CrossRef CAS.
- W. Choi, A. Abraham, J. Ko, J. G. Son, J. Cho, B. I. Sang and B. Yeom, ACS Appl. Mater. Interfaces, 2022, 14, 30056 CrossRef CAS PubMed.
- Y. Ren, J. Guo, Z. Liu, Z. Sun, Y. Wu, L. Liu and F. Yan, Sci. Adv., 2019, 5, 0648 Search PubMed.
- Z. Yu and P. Wu, Adv. Mater., 2021, 33, 2008479 CrossRef CAS.
- Q. Xia, W. Li, X. Zou, S. Zheng, Z. Liu, L. Li and F. Yan, Mater. Horiz., 2022, 9, 2881 RSC.
- Y. Ren, Z. Liu, G. Jin, M. Yang, Y. Shao, W. Li, Y. Wu, L. Liu and F. Yan, Adv. Mater., 2021, 33, 2008486 CrossRef CAS.
-
M. J. Frisch, G. W. Trucks, H. B. Schlegel, G. E. Scuseria, M. A. Robb, J. R. Cheeseman, G. Scalmani, V. Barone, B. Mennucci, G. A. Petersson, H. Nakatsuji, M. Caricato, X. Li, H. P. Hratchian, A. F. Izmaylov, J. Bloino, G. Zheng, J. L. Sonnenberg, M. Hada, M. Ehara, K. Toyota, R. Fukuda, J. Hasegawa, M. Ishida, T. Nakajima, Y. Honda, O. Kitao, H. Nakai, T. Vreven, J. A. Montgomery, Jr., J. E. Peralta, F. Ogliaro, M. Bearpark, J. J. Heyd, E. Brothers, K. N. Kudin, V. N. Staroverov, T. Keith, R. Kobayashi, J. Normand, K. Raghavachari, A. Rendell, J. C. Burant, S. S. Iyengar, J. Tomasi, M. Cossi, N. Rega, J. M. Millam, M. Klene, J. E. Knox, J. B. Cross, V. Bakken, C. Adamo, J. Jaramillo, R. Gomperts, R. E. Stratmann, O. Yazyev, A. J. Austin, R. Cammi, C. Pomelli, J. W. Ochterski, R. L. Martin, K. Morokuma, V. G. Zakrzewski, G. A. Voth, P. Salvador, J. J. Dannenberg, S. Dapprich, A. D. Daniels, O. Farkas, J. B. Foresman, J. V. Ortiz, J. Cioslowski and D. J. Fox, Gaussian, Inc., Wallingford CT, 2013.
- J. Xie, L. Fan, D. Yao, F. Su, Z. Mu and Y. Zheng, Mater. Today Chem., 2022, 23, 100708 CrossRef CAS.
- Z. J. He, M. L. Qin, C. Y. Han, X. Bai, Y. D. Wu, D. D. Yao and Y. P. Zheng, Colloids Surf., A, 2022, 652, 129837 CrossRef CAS.
|
This journal is © The Royal Society of Chemistry 2024 |
Click here to see how this site uses Cookies. View our privacy policy here.