DOI:
10.1039/D3GC04082H
(Tutorial Review)
Green Chem., 2024,
26, 202-243
Chemocatalytic production of sorbitol from cellulose via sustainable chemistry – a tutorial review
Received
24th October 2023
, Accepted 28th November 2023
First published on 29th November 2023
Abstract
Sorbitol, which is a six carbon polyol typically derived from glucose, is widely used in food, personal care and pharmaceutical products. Sorbitol production processes that use cellulose as feedstock are much less developed than those that use glucose and are important for future sustainability. Herein, we review the latest progress in chemocatalytic production of sorbitol from cellulose with emphasis on sustainable chemistry. Relevant feedstocks include isolated cellulose solids, pretreated biomass, and raw lignocellulosic biomass that use homogeneous multi-step, heterogeneous one-pot, or flow-chemistry catalytic approaches for sorbitol production. In the processes analyzed, we focus on state-of-the-art results achieved with supported metal catalysts, and explore their characteristics, active site functionalities, reaction kinetics and mechanisms for guiding the design of future sorbitol chemocatalytic production systems.
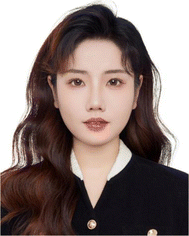 Yingqiao Zhou | Yingqiao Zhou is currently a master candidate in the group of Prof. Xinhua Qi, College of Environmental Science and Engineering at Nankai University. She is presently engaged in the design and synthesis of highly efficient catalysts for biomass catalytic upgrading. |
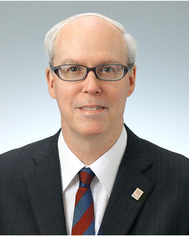 Richard L. Smith Jr | Richard Lee Smith, Jr. is a Professor in the Graduate School of Environmental Studies (GSES)/GP-RSS, Tohoku University, Japan. He obtained his PhD in Chemical Engineering from the Georgia Institute of Technology (USA) in 1985 (Supervisor: Amyn S. Teja). His research focuses on developing green chemical processes with solvothermal and hydrothermal methods. He has published more than 300 scientific papers and is an author of “Introduction to Supercritical Fluids” published by Elsevier in 2013 and Co-editor for the Book Series “Biofuels and Biorefineries” (Zhen Fang, Editor-In-Chief) published by Springer-Nature. Professor Smith is Asia Regional Editor for the Journal of Supercritical Fluids. |
 Xinhua Qi | Dr Xinhua Qi is a distinguished professor of College of Environmental Science and Engineering at Nankai University. Prof. Qi received his B.S. in environmental chemistry from Nankai University in 1998, and Ph.D. in environmental science from Nankai University in 2003. He worked as a JSPS Postdoctoral Fellow at Tohoku University (Sendai, Japan) from Oct. 2006 to Nov 2010. He was promoted to a full professor in 2011 at Nankai University. His research interest mainly focuses on green processes for biomass conversion into value-added materials and chemicals. He has published more than 150 peer reviewed scientific papers, and these papers have been cited over 5300 times with H index 40. He also has co-authored over 20 patents, 5 books and 3 book chapters on environmental engineering and biomass resources utilization. His research work has been awarded 2 items of first-class prizes and 1 item of second-class prizes of provincial and ministerial level. Prof. Qi has been selected as leading talent in the National Ten Thousand Talents Plan, Shennong Talent Plan from Ministry of Agriculture and Rural Affairs, New Century Excellent Talent Program from Ministry of Education, and was supported by the Outstanding Youth Science Foundation of Tianjin. |
1. Introduction
Societal demands are driving food and energy sources towards sustainability by supplementing traditional production methods that rely on petroleum resources with new processes that take advantage of renewable resources.1,2 Green and low-carbon transformation of energy has become preferred in countries across the globe.3,4 Unlike wind and solar energy sources that provide electrical energy and heat, biomass is a primary renewable resource for producing carbon-based fuels and chemicals.5 Cheap, readily available and carbon neutral bio-based substitutes for petroleum-based chemicals have become a hot topic in recent years.6 Due to the current worldwide trend of shifting from petroleum-based economies to bio-based economies,7 biomass-based chemicals have become essential for improving manufacturing sustainability and for improving living standards in accordance with the UN sustainable development goals (UN SDGs).8
Cellulose, which is the most abundant carbohydrate present in both land and water forms, can be converted into bio-based fuels or high-value chemicals through processes such as hydrolysis,9 gasification,10 and pyrolysis.11,12 From the perspective of atomic economy, conversion of cellulose into sorbitol has advantages such as retaining O and H atoms for conserving atom transfer that can lower overall energy requirements for chemical production. Cellulose can be depolymerized into glucose as shown by numerous research efforts that focus on upgrading cellulose into platform molecules such as 5-hydroxymethylfurfural, ethylene glycol, gluconic acid and sorbitol, in which the production of furfural and 5-hydroxymethylfurfural via glucose dehydration destroys the sugar-steric structure, whereas its conversion to hexitols can maintain some of the original steric structure without C–C bond dissociation.13,14 Hence, the hydrogenation of glucose to sorbitol has an important position in future biorefineries for industrial production of chemicals.
As one of the “top chemicals derived from carbohydrates,15 sorbitol is economical, environmentally friendly, readily available, and it can be produced from cellulosic biomass derived from agricultural and forestry waste.16 Sorbitol has good thermal stability, solvent resistance and mechanical properties and as a functional sugar alcohol, it has a large market with a wide variety of downstream products.17 In the context of consumer living standards, there is likely to be high demand for low calorie healthy food and daily chemical products that have health benefits, which will drive innovation and development of consumer goods, such that markets for functional sugar alcohols such as sorbitol will continue to broaden and thrive.
As a platform chemical, sorbitol can be used to produce vitamin C or ascorbic acid (ASC) by fermentation18 or isosorbide (ISB) by dehydration.19 Sorbitol can be further hydrolyzed to low carbon number alcohols such as glycerol (GLY), propylene glycol (PG) and ethylene glycol (EG)20,21 for replacing petroleum industry products, and can be converted into cyclic hydrocarbons for aerospace fuels by continuous isomerization aromatization.22 Sorbitol can be used to synthesize and modify polymers such as polylactic acid (PLA)23 that has a variety of uses such as biodegradable plastics, bio-composites and biomedicines (Fig. 1).
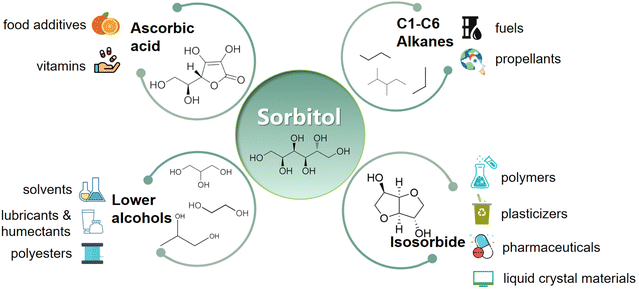 |
| Fig. 1 Transformation and applications of sorbitol as a platform chemical. | |
To produce sorbitol efficiently, many catalytic systems have been examined. Through kinetic control and process integration, efforts are being made to reduce energy consumption.24–26 Based on VOSviewer analysis of keywords (Fig. 2) in research papers related to the catalytic production of sorbitol, much attention is being paid to upstream and downstream bio-derived compounds and performance of the catalytic systems. Development of catalytic methods for lignocellulose as feedstock in sorbitol production could also reduce energy and separation costs. In this review, lignocellulosic biomass refers to non-food agriculture, agricultural waste and forestry waste. Development of lignocellulosic biomass for the chemical industry is of strategic importance in world food security and sustainable economies for fine chemical industry supply chains.27 In this review, the focus is on discussion relevant to chemo-catalytic systems of sorbitol production and the challenges of the proposed methods. Key aspects of reaction systems for sorbitol production are design of multifunctional catalysts, role of active sites in the catalysts and the theoretical basis for efficient catalysis with the goal being to achieve one-pot conversion with optimized process flows.
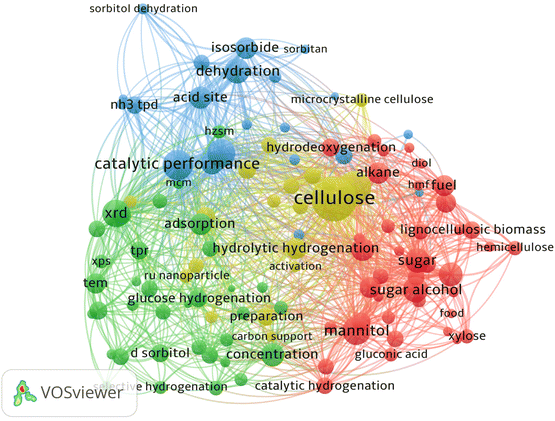 |
| Fig. 2 Keyword network visualization of “catalytic production of sorbitol” created by VOSviewer software using bibliographic data from Web of Science with correlation value of 60%. | |
Although several reviews28–30 have described catalytic synthesis and conversion of sorbitol with improved reaction systems, those works mainly analyze preparation of sorbitol from raw biomass and derived sugars by chemical catalysis and conversion of sorbitol to chemical products. This paper focuses on structure-reaction performance of catalysts proposed for sorbitol production, discusses the rationale of design of multifunctional catalysts in detail from the perspective of catalyst supports and active centers, and then analyzes the role of catalyst active sites in the reactions. Studies on the regulation of sorbitol synthesis pathways are summarized and the theoretical basis for efficient catalysis is explored through simulations. This review provides analysis of research progress on catalytic production and conversion of sorbitol and summarizes commonalities of catalyst exploration, especially bifunctional catalysts being applied to one-pot conversion of cellulose to sorbitol.
2. Catalytic systems for sorbitol production
Production of sorbitol (Table 1) can be via bio-catalytic,31,32 electro-catalytic33 or chemo-catalytic methods.34 Methods based on bio-catalysis (fermentation) offer high selectivity, but tend to have low reaction rates (Table 1) and they have inherent issues in the presence of inhibitors that can deactivate enzymes, enzyme cost and recycling that require intensive separation procedures. Methods based on electro-catalysis (electrochemical) offer high-selectivity and energy efficiency, but tend to require clean feedstocks of simple molecules (e.g. glucose) in electrolyte solutions and are not competitive economically for reduction compared with chemo-catalytic hydrogenation schemes.35 Photo-catalytic methods for cellulose conversion have been explored in recent years to make reaction conditions mild and sustainable.36 Of the methods shown in Table 1, chemo-catalysis offers both broad scope and scalability for the many kinds of lignocellulosic biomass substrates that need to be addressed. This review mainly examines production of sorbitol and its derivatives via chemo-catalysis methods.
Table 1 Characteristics and chief issues of methods for sorbitol production
Method |
Characteristics |
Chief issues |
Bio-catalysis |
• low reaction rate |
• enzyme compatibility |
• long reaction time (ca. days) |
• sensitive to pH and inhibitors |
• high selectivity |
• enzyme cost |
• large volume equipment |
• enzyme recycling |
• batch processing |
• product separation |
• low energy consumption |
• large equipment investment |
• low substrate concentrations |
• product uniformity |
• aqueous buffered solution |
• solution recycling |
• mature process control |
• environmental housing requirement |
|
|
|
Electro-catalysis |
• high reaction rate |
• electrode synthesis and activity |
• short reaction time (ca. minutes) |
• electrode robustness |
• high selectivity |
• electrode regeneration and recycling |
• small volume equipment |
• difficult to industrialize |
• batch or continuous processing |
• product separation |
• low energy consumption |
• Faraday efficiency and overpotential |
• low substrate concentrations |
• clean or model substrates |
• aqueous electrolyte (e.g. KOH) |
• electrolyte recycling |
• custom process control |
• scalability |
|
|
|
Chemo-catalysis |
• high reaction rate |
• catalyst synthesis and activity |
• short reaction time (ca. minutes) |
• catalyst robustness |
• moderate-to-high selectivity |
• catalyst regeneration and recycling |
• small volume equipment |
• temperature and pressure conditions |
• batch or continuous processing |
• product separation |
• moderate energy consumption |
• heat transfer and throughput |
• high substrate concentrations |
• byproduct formation |
• hydrothermal or solvothermal |
• solvent recycling |
• custom process control |
• flow stability |
Preparation and transformation routes for production of sorbitol from cellulose typically use acid catalysis to first break the hydrogen bond network in cellulose (or starch) and glycosidic bonds and hydrolysis to convert oligomers into C6 sugar molecules. Then, catalytic hydrogenation of the aldehyde groups in glucose molecules produces sorbitol (Fig. 3). In bifunctional catalytic systems, sorbitol can be produced in one-pot, improving efficiency, while avoiding the cost of product separation, which has been received much attention.37,38
 |
| Fig. 3 Conversion of cellulose to sorbitol via sequential catalytic hydrolysis and hydrogenation steps or via one-pot hydrolytic hydrogenation with bifunctional catalysts. | |
2.1 Catalytic conversion of glucose to sorbitol
Glucose is the monomer of cellulose and in solution, glucose molecules exist in an open-chain form or in cyclic forms that are subdivided into six-membered α- or β-pyranose structures.39 In aqueous solutions, glucose mostly exists in a stable ring conformation that has an energy barrier for the ring-opening process of about 105 kJ mol−1.40 Glucose in the aldose conformation can be adsorbed onto metal surfaces via the oxygen lone pair η1O or via the carbonyl group η2C
O to complete a subsequent ring-opening hydrogenation reaction (Fig. 4).41,42 In hydrogenation of the aldose (Fig. 4), hydrogen molecules first diffuse from the gas phase to the gas–liquid interface and then the dissolved hydrogen overflows in active metal sites of the catalyst to generate active H (H*), that is followed by H* transfer to the aldehyde group after which sorbitol is desorbed from the catalyst and diffuses into the liquid phase.43
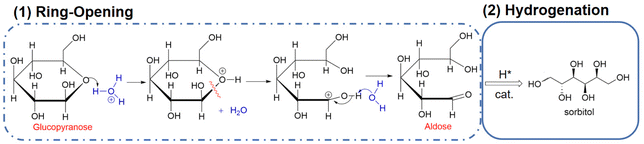 |
| Fig. 4 Ring opening and hydrogenation of glucose.41 Reproduced from ref. 41 with permission from American Chemical Society, copyright 2016. | |
2.1.1 Thermal catalytic systems.
Hydrogenation of glucose is by far the most studied chemical reaction among production methods for sorbitol due to its implementation on the industrial scale.44,45 Numerous researchers have explored a range of highly efficient nickel and ruthenium catalysts for glucose hydrogenation with yields above 95% at close to complete conversion (Table 2). Almost all current sorbitol preparation methods use heterogeneous catalysts for glucose hydrogenation reactions, so the selection of highly-active, reusable, environmentally-friendly and economical catalysts have been the focus of development.46,47 Noble metals such as Ru and Pd have attracted a lot of attention due to their high stability and activity. To reduce cost, ruthenium nanoparticles have been proposed, because when dispersed on solid supports, they increase the number of active sites and lower mass transfer resistances. Advanced catalytic systems have been explored to avoid the use of high temperature and high-pressure hydrogen as discussed in a section below.25,48–50
Table 2 Catalytic systems, reaction conditions, conversions, yields and by-products for glucose hydrogenation to sorbitol
Metal sites |
No. |
Catalyst (cat.) |
Conditions |
Catalyst performance |
|
Temp (°C) |
p
H2 (MPa) |
Time (min) |
Glucose(Glu) concentration (wt%) |
Glu/cat wt ratio |
Glucose conversion (%) |
Sorbitol yield (%) |
Byproducts (%) |
TOFa (h−1) |
Ref. |
n.r. not reported. TOF: molar sorbitol conversion (or glucose conversion) rate per mole of (active) metal per hour. System: 10 mL isopropyl alcohol + 15 mL water with microwave irradiation. Mg: to generate hydrogen in situ from water. Glucose weight/Ru weight. |
Non-noble metal |
1b |
RaNi-Cr/Fe |
120 |
4 |
120 |
10 |
n.r. |
100 |
>98 |
|
|
51
|
2 |
nano-Ni2P/HT |
100 |
2 |
120 |
10 |
0.45 |
99 |
99 |
mannitol (1) |
|
25
|
3 |
Ni–Co-1-1 |
100 |
3 |
240 |
25 |
25 |
97 |
96 |
|
|
48
|
4 |
Ni/NiO |
130 |
5 |
n.r. |
4.6 |
24 |
95 |
84 |
mannitol (11) |
720 |
52
|
5 |
nano-Ni2P/Al2O3 |
100 |
2 |
120 |
10 |
0.45 |
83 |
78 |
mannitol (1) |
|
25
|
6 |
Ni1.85Cu1Al1.15 hydrotalcite |
120 |
3 |
180 |
5 |
5 |
78 |
73 |
|
|
53
|
7 |
Fe–Ni/CB |
140 |
3 |
360 |
0.5 |
8.3 |
71 |
50 |
|
56 |
54
|
8 |
nano-Ni2P/ZrO2 |
100 |
2 |
120 |
10 |
0.45 |
65 |
43 |
mannitol (4) |
|
25
|
9c |
SiO2@Ni/NiO + Mg |
120 |
0 |
180 |
1 |
2 |
99 |
89 |
mannitol (5) |
|
49
|
fructose (0.2) |
|
Noble metal |
10 |
Pt-SBA-15 |
140 |
4 |
240 |
2.5 |
5 |
16 |
10 |
|
45 |
41
|
11 |
Pt/AC |
180 |
1.6 |
60–180 |
2.8 |
2.3 |
97–100 |
90–95 |
arabinitol (5) |
54 |
55
|
glycerol (1) |
propane-1,2-diol (0.5) |
12 |
Pt/γ-Al2O3 + HT |
90 |
1.6 |
360 |
0.4 |
1 |
98 |
53 |
Mannitol (12) |
613 |
50
|
Glycols (8) |
Gluconic acid (5) |
Xylitol(4) |
13 |
(RuO2)0.04·(SiO2)0.96 |
120 |
2 |
300 |
1.8 |
7.1 |
100 |
94 |
|
0.7 |
56
|
14 |
Ru/C |
120 |
4 |
120 |
10 |
n.r. |
100 |
>98 |
|
12 |
57
|
15 |
Ru/ZSM-5-TF |
120 |
4 |
120 |
25 |
n.r. |
100 |
99 |
|
32 |
58
|
16 |
Ru/AFPS |
100 |
5.5 |
120 |
4 |
20 |
100 |
98 |
|
235 |
59
|
17 |
Ru/HYZ |
120 |
5.5 |
20 |
25 |
40 |
100 |
99 |
|
1275 |
60
|
18 |
Ru/GLC |
140 |
2 |
140 |
5 |
12.5 |
100 |
97 |
|
1681 |
61
|
19 |
Ru@DEMOF |
120 |
5 |
150 |
25 |
50 |
>99 |
96 |
|
2151 |
62
|
20 |
Ru/Al2O3 |
100 |
3 |
150 |
10 |
20 |
100 |
97 |
|
|
63
|
21 |
Fe3O4@SiO2@L2-Ru(II) |
150 |
n.r. |
60 |
0.8 |
n.r. |
99 |
96 |
|
|
64
|
22 |
Ru2P/C |
200 |
3 |
120 |
1 |
2 |
>99 |
93 |
|
|
65
|
23d |
Ru/C |
120 |
2.5 |
10 |
0.7 |
42Ru |
95 |
95 |
|
|
66
|
24d |
Ru/TiO2 |
120 |
2.5 |
20 |
0.7 |
42Ru |
91 |
91 |
|
|
66
|
25d |
Ru/MCM-48 |
120 |
2.5 |
25 |
0.7 |
42Ru |
90 |
90 |
|
|
66
|
|
Bimetal |
26 |
Ni–Ru@PCS |
140 |
3 |
120 |
1 |
1 |
99 |
99 |
|
|
67
|
27 |
FeNi@OMC |
160 |
3 |
180 |
1 |
1 |
99 |
99 |
|
|
68
|
2.1.2 Hydrogen sources.
At present, commonly used hydrogen sources for sorbitol production include hydrogen-donor solvents such as isopropanol and ethanol or other inorganic and organic hydrogen sources, of which high-pressure H2 is the first and most widely used hydrogen source. External high hydrogen pressure can promote the production of sorbitol, because an increase in hydrogen partial pressure leads to an increase in hydrogen dissociation at the metal sites, resulting in an increase in the concentration of hydrogen available for hydrogenation, i.e. overflow hydrogen phenomenon.69 which facilitates hydrogenation reactions. For example, when hydrogen partial pressure is increased from 3 MPa to 6.5 MPa, initial TOF linearly increases from 117 h−1 to 263 h−1, while the sorbitol yield increases from 42% to 73% and sorbitol selectivity of (97% to 98%) are maintained (Table 2, entry 16).59 Increasing the partial pressure of hydrogen raises the concentration of dissolved hydrogen, which increases the rate of adsorption and desorption of hydrogen on the metal surface thus promoting the reaction. Zhang et al.41 reported that in the transformation of glucose, an increase in hydrogen partial pressure from 0.5 MPa to 2 MPa shifted the reaction product from mainly fructose to sorbitol, suggesting that the glucose isomerization pathway is inhibited by a hydrogen-saturated surface while the hydrogenation pathway is promoted (Table 2, entry 10). Stirring speed also has a certain influence on conversion rate and selectivity of glucose, with a higher stirring speed (>1000 rpm for 100 mL vessel) being preferred, because it can make H2 diffuse rapidly into the liquid and increase gas–liquid mass transfer rates.59
The conversion of cellulose or glucose into sugar alcohols via catalytic transfer hydrogenation (CTH) using small molecular alcohols (ethanol, propanol) instead of molecular hydrogen has been studied by researchers. Kobayashi et al.70 investigated direct hydrogen transfer from 2-propanol to glucose over Ru/activated carbon catalyst without the use of external molecular hydrogen, wherein the transfer hydrogenation of glucose and cellulose oligomers provided 85% C6 sugar alcohol in less than 1 h reaction time. Then, researchers probed the mechanism of hydrogen transfer hydrogenation by using deuterium instead of hydrogen and showed that the main source of hydrogen for hydrogenation was the direct transfer of adsorbed hydrogen species to glucose via 2-propanol on the Ru surface without the involvement of molecular hydrogen.71 García et al.72 explored the production of sorbitol from glucose by catalytic transfer hydrogenation (CTH) in the presence of short-chain sacrificial alcohols using RANEY® nickel as catalyst. As shown in Fig. 5, sugar alcohols can be derived via two hydrogen transfer pathways: (i) production from a sacrificial alcohol (ethanol) as hydrogen donor and (ii) production from glucose disproportionation. Alkyl diols, especially terminal diols with C4 and C5 alkyl chains (e.g. 1,4-butanediol and 1,5-pentanediol) have been identified as good hydrogen donors. García et al.73 used 1,4-butanediol as a hydrogen donor, and obtained sorbitol selectivity above 90% in a continuous fluidized bed reactor operated for 550 h with Mo-promoted RANEY® nickel catalyst.
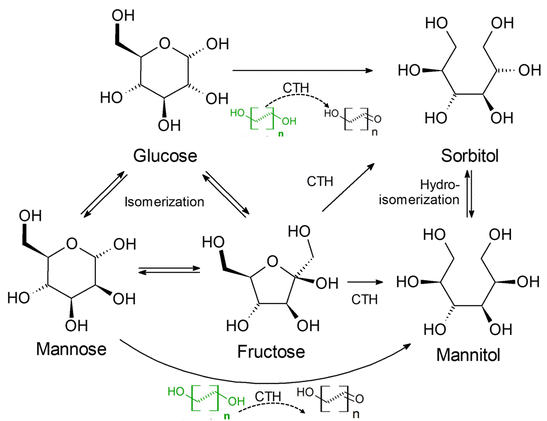 |
| Fig. 5 Proposed reaction scheme for catalytic transfer hydrogenation (CTH) reduction of glucose to sorbitol with short-chain alcohols over RANEY® nickel catalysts.73 Reproduced from ref. 73 with permission of American Chemical Society, Copyright, 2021. | |
In situ hydrogen generation via metal activation is another method besides CTH to reduce the dependence of hydrogenation reaction systems for external molecular hydrogen gas. Li et al.49 used Mg as a hydrogen generation activator for hydrogen production that occurs through hydrolysis. Glucose conversions and sorbitol selectivity as high as 99% and 90%, respectively, were achieved through coordination of SiO2@Ni/NiO catalyst having a core–shell structure with Mg hydrogen generation activator under mild conditions (Table 2, entry 9).49
2.1.3 Electro-catalytic systems.
Electro-catalytic systems have inherent advantages in environmental and energy aspects over chemo-catalytic systems (Table 1). Unlike conventional thermal catalysis that uses high-temperature or high-pressure reaction conditions, electro-catalysis systems typically use ambient conditions and avoid the addition of chemical reducing/oxidizing agents which makes regulation of reaction rates relatively simple. Electro-catalytic hydrogenation (ECH) has a long and rich history,74 and although the electrochemical oxidation of sugars, especially glucose has gained attention,75,76 electro-catalytic hydrogenation of glucose still remains a challenge.77 In this context, electrocatalytic production of sorbitol from glucose has been explored.
The reaction of electro-catalytic hydrogenation (ECH) of glucose to sorbitol occurring on the cathode competes with HER.
| ECH: glucose(C6H12O6) + 2H2O + 2e− → sorbitol(C6H14O6) + 2OH− | (2) |
Faraday efficiency (FE) is an assessment of the effectiveness and efficiency of charge transfer in electrochemical reactions and an indicator of the competition between the electrocatalytic conversion of glucose to sorbitol and HER. The Faraday efficiency is calculated as:
|  | (3) |
where
n is the number of electrons transferred for each product and
F is the Faraday constant (96
![[thin space (1/6-em)]](https://www.rsc.org/images/entities/char_2009.gif)
485 C mol
−1). Two electrons are exchanged for each glucose molecule converted to a sorbitol/mannitol molecule.
Current efficiency (CE) is calculated as:
| 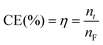 | (4) |
where
nt is the actual moles of glucose converted to sorbitol and
nF is the theoretical moles of sorbitol produced according to Faraday's law. The current efficiency is usually tested under constant current density conditions.
Glucose as substrate.
Early electrocatalytic production of sorbitol used glucose as substrate. The efficiency of the electrochemical reaction was assessed by current density, maintaining a constant current and testing the ratio of actual to theoretical production. Lessard et al.78 found that RANEY® nickel was active for ECH of glucose in both batch and flow reactors with high sorbitol selectivity (90% to 95%) and moderate current efficiencies (40% to 47%). Pintauro et al.79 used a packed-bed flow reactor that oxidized glucose to gluconic acid on the graphite anode and reduced glucose to sorbitol on a zinc cathode. For that case, the current efficiency at 0.25 F mol−1 for sorbitol and gluconic acid production was 26% and 68%, respectively, and at 0.4 F mol−1, the yields of sorbitol and gluconic acid were 34% and 47%, respectively. The choice of catalyst is important for obtaining high yields and selectivities of sorbitol, because the overpotential water reduction and adsorption energy of glucose depends greatly on its characteristics. Kwon et al.80 tested the electrocatalytic hydrogenation of glucose to sorbitol on different solid metal electrodes in neutral medium Na2SO4, which was classified into three groups based on the products formed (Fig. 6).
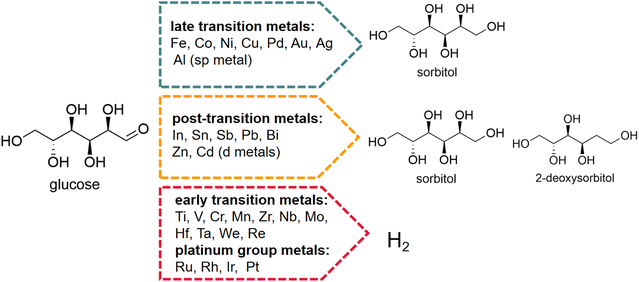 |
| Fig. 6 Electrocatalytic hydrogenation (ECH) of glucose to sorbitol and 2-deoxysorbitol and competitive hydrogen evolution reaction (HER). Conditions: 0.1 M glucose, 0.1 M Na2SO4, work electrode: various metal polycrystalline wires/rods/plates, counter electrode: platinum plate, reference electrode: reversible hydrogen electrode (RHE), scan rate: 1 mV s−1.81,82 Reproduced from ref. 82 with permission from American Chemical Society, copyright 2020. | |
Electrocatalysts which can provide both high sorbitol yield and current efficiency still have many avenues of development. Lessard et al.78 performed electro-hydrogenation of glucose under constant current conditions (J = 66 mA cm−2) at 60 °C and pH 3–6 using RANEY® nickel as an electrode and obtained 95% sorbitol yields with a current efficiency of 57%. When hydrogen-storage alloys were employed as electrodes (current density = 8 mA cm−2, pH = 8, 30 °C), current efficiency of sorbitol exceeded 90% with sorbitol yields of 80%.83 When zinc and zinc alloys were supported on carbon nanotubes (CNT) and employed as electrodes, a current efficiency of 58% was obtained (current density = 1 mA cm−2, pH = 11, 30 °C).84 Their current efficiency was obtained according to an iodimetric analysis method,84 but unfortunately, their Faraday efficiency was not reported. Most papers on glucose electroreduction published more than 10 years ago only report current efficiency. However, one disadvantage of using current efficiency to assess a reaction system is that it is only based on the conversion of the current in the experiment, and cannot effectively distinguish between side reactions and losses, and even a current efficiency of 100% can occur.85
Therefore, in recent years, electrocatalytic hydrogenation of glucose to sorbitol has been explored using Faraday efficiency for a more scientific assessment of electrocatalysis. Oña et al.86 investigated the electrocatalytic hydrogenation of glucose using gold nanoparticles (AuNP) on an activated carbon fiber (CF) carrier as a cathode, and a Faraday efficiency of 0.4 was obtained in 0.1 M Na2SO4 containing 0.1 M glucose for 6 h (−1.5 V vs. Ag/AgCl, current density = 7.4 mA cm−2). They also found that the particle size of gold nanoparticles affects the electrocatalytic activity and Faraday efficiency.
Fructose as substrate.
In addition to the reduction of glucose discussed above, the electrochemical reduction of fructose as a raw material to sorbitol has also been explored. Owobi-Andely et al.87 used Pt–Rh/electrodes as cathodes in an electrocatalytic membrane reactor to electrochemically reduce fructose to sorbitol and mannitol with 60% conversion and 40% selectivity of sorbitol. Furthermore, using fructose as a substrate in a weakly alkaline medium (pH = 11.3) with a copper wire as cathode, Creus et al. could achieve a Faraday efficiency of greater than 40% with fructose conversion of 77% to sorbitol and mannitol after 10 h of electrolysis.33
Cellobiose as substrate.
Notably, electrochemical methods for cellobiose hydrolysis and decomposition have been studied, such as electro-Fenton.88 The potential of the anode was controlled to generate enough H+ to hydrolyze cellulose into glucose.89 One ingenious reactor design allowed hydrolysis at the anode and electrocatalytic hydrogenation at the cathode to provide one-pot electrolysis of sorbitol from cellobiose or cellulose.89
Strong competition between the HER reaction and hydrogenation reaction along with low Faraday efficiency (<50%) have led to less exploration of sorbitol preparation by electroreduction, however, electrocatalysis avoids the use of strong acids and uses mild conditions and thus is an overlooked and promising green chemical technology that deserves further investigation.
2.1.4 Photocatalytic systems.
Photocatalysis is an innovative method for producing H2 and performing organic reactions under mild reaction conditions. Photocatalysis, mainly through the reduction of photogenerated electrons, has the potential to provide a sustainable method for converting glucose into sorbitol and other value-added chemicals. Highly selective conversion of glucose to sorbitol can be achieved at room temperature and pressure which significantly reduces energy consumption.90 Using typical photocatalyst, Ag/AgBr/g-C3N4 nanoparticles, glucose can be reduced to sorbitol in the presence of NaHSO3 under visible light irradiation (Fig. 7), facilitating in situ hydrogen production with sorbitol yields of more than 89% in 8 h.90 TiO2-based photocatalysts commonly used in photocatalysis can also be used for the reaction.91 For example, TiO2 pillared bentonite-Co catalyst Ni92 has been used to produce sorbitol, and the sorbitol produced by UV irradiation for 30 d reached 66.8%. Situmeang et al.91 used LaCrO3 catalysts to convert nanocellulose into 620 ppm glucose, 260 ppm xylitol, 150 ppm mannitol, and 210 ppm sorbitol in 45 min under UV irradiation, although in trace amounts, thus possibly opening a new window of opportunity. The chief disadvantage of photocatalysis at present is that reaction time is much longer than that of thermal catalysis. In addition, attention should be paid to the breakage of C–C bonds due to the oxidation of holes and hydroxyl groups generated by photocatalysis causing the sorbitol selectivity to become lower. Photocatalytic technology for the production of sorbitol has received little attention and it is hoped that it will receive more in the near future.
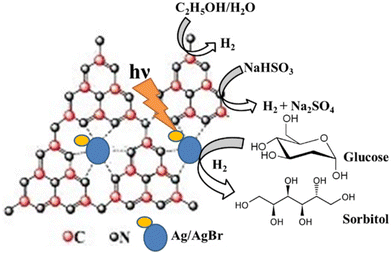 |
| Fig. 7 Postulated mechanism for photocatalytic production of sorbitol from glucose in absence of external hydrogen source.90 Reproduced from ref. 90 with permission from The Royal Society of Chemistry, copyright 2022. | |
2.2 One-pot catalytic conversion of cellulose to sorbitol
Glucose is usually produced by hydrolysis of starch or cellulose using either enzymes under atmospheric conditions or acid catalysts under high-temperatures and high-pressures. Pressurized hydrogenation of glucose to sorbitol can be integrated into the chemical production of glucose from cellulose or starch to avoid separation, concentration and purification steps. While direct catalytic hydrogenation of starch to produce sorbitol has been studied for many years,93 the cost of starch is high, so production of sorbitol from cheap and available cellulose as a starch substitute is a hot research topic. As non-edible biomass is available in substantial quantities, cellulose as a raw material for sorbitol production avoids competition between food and fuel and instead creates a “fuel to food” scenario. In direct synthesis schemes, there are two reaction steps: (i) hydrolysis of cellulose to glucose and (ii) hydrogenation of glucose to sorbitol, whereas the hydrolysis step is rate-limiting.94 Consecutive hydrolysis and hydrogenation processes for producing sorbitol from cellulose are simple in operation and avoid separation or purification steps which saves time and energy.
Conversion of cellulose to sorbitol by direct synthesis schemes has two challenges: (i) selection of suitable catalysts that are sufficiently selective for promoting glucose formation and (ii) selection of reaction system or pretreatment method that allows cellulose-catalyst contact because cellulose is insoluble in water.
2.2.1 Reaction pathways of cellulose conversion.
A reaction network for conversion of cellulose to hexitols and other oxygenated small molecule by-products is shown in Fig. 8. To produce hexitols, the ideal catalyst should promote hydrogenation of C
O bonds in aldehydes or polysaccharides and inhibit further hydrogenation and parallel reactions of hexitols. Glucose formed via cellulose hydrolysis can isomerize to fructose and mannose, dehydrate to 5-hydroxymethylfurfural (5-HMF), furfural, or oxidize to organic acids. Sorbitol can also be dehydrated to sorbitan, isosorbide or hydrolyzed to small molecule by-products such as ethylene glycol, propylene glycol and glycerol. Variation of the catalyst type and reaction system can change the reaction pathway to favor hydrolysis, isomerization, inverse hydroxyl aldol condensation or hydrogenation which strongly affects product selectivity. Deng et al.95 modified Pt/Al2O3 with SnOx, and found hydrogenation reaction products could be adjusted by controlling the Sn/Pt ratio. When the Sn/Pt ratio was relatively low, SnOx strongly interacted with Pt, transferring electrons to the Pt site that promoted hydrogenation to hexitols; when the Sn/Pt ratio was greater than 1.5, the formation of C2 and C3 products was favored, and possibly SnOx promoted the isomerization of glucose to fructose and subsequent trans-hydroxylated aldol condensation. The acidity or alkalinity of the reaction system can also affect the pathway. An alkaline environment promotes the isomerization pathway of glucose and the pathway that produces glyoxal (GA) erythrulose from the condensation of trans-hydroxylated aldehydes. Excessive acidity causes dehydration of glucose to 5-HMF, while hydrogenolysis of hexitols leads to breakage of C–C bonds and formation of small molecules EG and 1,2-PG.96 By fully understanding the reaction mechanism, formation of the target product can be maximized by adjusting reaction parameters and catalyst to provide a basis for selective hydrogenation of aldehydes and ketones.
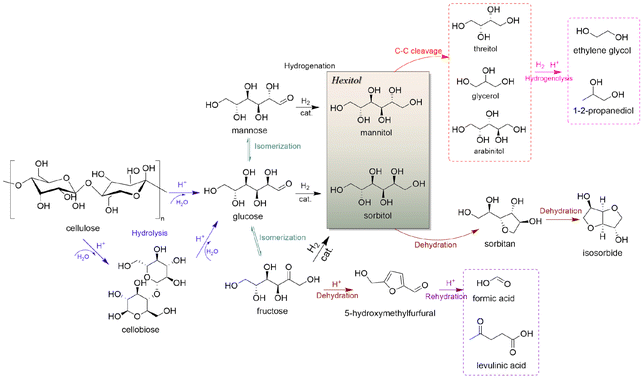 |
| Fig. 8 Reaction network in hydrolytic hydrogenation from cellulose to hexitols. | |
2.2.2 Historical development and recent advances.
Cellulose is a polymer of glucose linked by β-1,4-glycosidic bonds with high crystallinity,29 which makes it difficult to dissolve in water due to its hydrogen-bond network.97 Cellulose is hydrolyzed in water in the presence of homogeneous or heterogenous acids, wherein an appropriate acidity allows highly selective conversion to glucose. Coupling the hydrolysis and hydrogenation steps for cellulose-glucose-sorbitol conversion in one-pot has to address issues in cellulose solubility, substrate-catalyst adsorption and product-catalyst desorption kinetics, and reaction kinetics for limiting byproduct formation.
Since the pioneering work by Fukuoka and Dhepe,98 who demonstrated the feasibility of a one-pot reaction for polysaccharide or disaccharide hydrolysis and monosaccharide hydrogenation, many catalytic and pretreatment systems for synthesis of sorbitol from cellulose have been proposed (Table 3). Deng et al.99 reported the conversion of cellulose to sorbitol over Ru/CNT catalyst after pretreatment of cellulose with phosphoric acid to afford sorbitol yields as high as 69% at 5 MPa hydrogen partial pressure and 185 °C reaction temperature (Table 3, entry 2). Subsequent studies showed that proper heating and stirring pretreatment of cellulose samples in 0.06% H3PO4 could facilitate the hydrolysis–hydrogenation reaction.100 Mineral acids are usually used to depolymerize cellulose in high yields and at a lower cost than many present heterogeneous catalytic methods. However, there are issues with mineral acid hydrolysis, such as product separation, equipment corrosion and wastewater treatment. Therefore, solid acid-metallic bifunctional catalytic systems have been studied for developing one-pot conversion of cellulose to sorbitol.
Table 3 Catalytic systems, reaction conditions, conversions (Conv.), yields, and by-products for one-pot production of sorbitol
No. |
Substrate (sub) |
Catalyst (cat.) |
Sub/cat wt ratio |
Pretreatmenta |
Reaction conditions |
Conva (%) |
Sorbitol yield (%) |
By-productsa (yield%) |
Ref. |
T (°C) |
p
H2 (MPa) |
t (h) |
Solvent |
Entries marked with dashes denote no pretreatment; n.a. not available; n.r. not reported.
|
1 |
Cellulose |
4 wt% Ru/AC |
10 |
— |
245 |
6 |
0.5 |
H2O |
86 |
30 |
C2–C5 polyols (28) |
103
|
Mannitol (18) |
Sorbitan (13) |
2 |
Cellulose |
1 wt% Ru/CNT |
3.2 |
H3PO4 |
185 |
5 |
24 |
H2O |
|
69 |
Erythritol (5) |
99
|
Glycerol (5) |
Mannitol (4) |
3 |
Cellulose |
3 wt% Ni/CNF |
2 |
Ball-milled |
190 |
4 |
24 |
H2O |
92 |
50 |
Erythritol (13) |
105
|
Mannitol (6) |
Ethylene glycol (3) |
Glycerol (1) |
4 |
Cellulose |
2 wt% Ru/AC |
6.5 |
Ball-milled |
190 |
0 |
18 |
IPA-H2O |
85 |
36 |
Mannitol (11) |
70
|
C2–C6 polyols (7) |
Sorbitan (1) |
Glucose (1) |
5 |
Cellulose |
2 wt% Ru/AC |
6.5 |
Mix-milled w/cat |
190 |
0.9 |
3 |
H2O |
89 |
58 |
Mannitol (9) |
94
|
C2–C6 polyols (7) |
Glucose(1) |
6 |
Cellulose |
0.4 wt% Ru-3 wt%Ni/CNT |
2.5 |
Mix-milled w/cat |
205 |
5 |
1 |
H2O |
86 |
74 |
n.r. |
116
|
7 |
Cellulose |
0.4 wt% Ru-3 wt%Ni/AC |
2.5 |
Mix-milled w/cat |
245 |
6 |
5 |
H2O |
87 |
69 |
Mannitol (8) |
116
|
Glycerol (5) |
Erythritol (3) |
8 |
Cellulose |
0.4%wt Ru/CNT |
2.5 |
Mix-milled w/cat |
205 |
5 |
5 |
H2O |
84 |
51 |
Formic acid (12) |
117
|
Erythritol (7) |
Ethylene glycol (3) |
Mannitol (2) |
9 |
Cellulose |
5 wt%Ru-Tsu |
4 |
Cat treated w/H2SO4 |
190 |
5 |
3 |
H2O |
69 |
30 |
Mannitol (8) |
118
|
Glucose (0.7) |
10 |
Cellulose |
Nafion NR50 + Ru/AC |
1 |
Ball-milled |
150 5 1 [Amim]Cl-H2O |
n.a. |
34 |
|
|
|
Glucose (15) |
119
|
11 |
Cellulose |
4 wt% Ru/CCD-SO3H |
1.25 |
Ball-milled |
180 4 10 H2O |
100 |
64 |
|
|
|
Propylene glycol (2) |
107
|
12 |
Cellulose |
0.4 wt% Ru/AG-CNT1200 |
2.5 |
— |
205 |
5 |
5 |
H2O |
100 |
60 |
Formic acid (4) |
106
|
Glycerol (4) |
Propylene glycol (3) |
Ethylene glycol (0.6) |
13 |
Cellulose |
1 wt% Ru/Cs3HSiW12O40 |
1 |
Ball-milled |
180 |
5 |
3 |
H2O |
|
59 |
Mannitol (3) |
120
|
14 |
Cellulose |
ZrP-3 wt%Ru/MC |
0.5 |
Mix-milled w/ZrP |
170 |
5 |
1.5 |
H2O |
100 |
66 |
Mannitol (2) |
121
|
15 |
Cellulose |
5 wt% Ru/PBC |
3 |
H3PO4 |
150 |
5 |
8 |
H2O |
99 |
87 |
Mannitol (2) |
110
|
16 |
Cellulose |
3 wt% Ru-PW/ZrO2 |
1 |
— |
180 |
7 |
7 |
H2O |
95 |
66 |
Mannitol (12) |
122
|
17 |
Cellulose |
3 wt% Ru-PW/Nb2O5 |
1 |
— |
180 |
7 |
7 |
H2O |
92 |
41 |
Mannitol (9) |
122
|
18 |
Cellulose |
15 wt% Ni/ZrP2 |
1 |
— |
200 |
5 |
5 |
H2O |
n.a. |
50–60 |
1,4-Sorbitan (9) |
123
|
Isosorbide (5.8) |
Xylitol (3) |
19 |
Cellulose |
1 wt% Cu2(OH)PO4 + Ru/C |
|
Pre-treated w/H3PO4 |
180 |
4 |
1 |
H2O |
100 |
85 |
Mannitol (69) |
115
|
Sorbitan (39) |
|
Pentitols (29) |
|
20 |
Cellulose |
1 wt% Ru/PSBC |
6 |
Pre-treated w/H3PO4 |
150 |
3 |
6 |
H2O |
100 |
83 |
Mannitol (2) |
111
|
21 |
Cellulose |
2 wt% Ru2P/C-SO3H |
2 |
Mix-milled w/cat |
200 |
3 |
2 |
0.02% H2SO4 |
>99 |
64 |
n.r. |
65
|
22 |
Cellulose |
9.6 wt% Ni-0.4 wt% Ru@MC |
5 |
Mix-milled w/cat |
200 |
3 |
3 |
H2O |
100 |
75 |
n.r. |
113
|
23 |
Cellulose |
2 wt%Ru2P/OMCPL |
2 |
Ball-milled |
200 |
4 |
5 |
0.02% H2SO4 |
|
77 |
n.r. |
124
|
24 |
Cellobiose |
10 wt% Ni/SiC |
3.4 |
— |
185 |
5 |
3 |
H2O |
87 |
68 |
n.r. |
24
|
25 |
Cellobiose |
5 wt% Ni5%Ir/SiC |
3.4 |
— |
185 |
5 |
3 |
H2O |
88 |
Hexitols (76) |
n.r. |
24
|
26 |
Cellobiose |
(9 wt% Ni)SBA-10Ni4P |
1.25 |
— |
180 |
4 |
3 |
H2O |
94 |
81 |
Mannitol (7) |
125
|
27 |
Cellobiose |
4 wt% Ru/MCM48 |
1.75 |
— |
180 |
5 |
0.16 |
H2O |
86 |
55 |
Mannitol (4) |
126
|
Glucose (9) |
Fructose (2) |
28 |
Cellobiose |
0.75 wt% Ru/CTS-0.5 |
5 |
— |
185 |
5 |
3 |
H2O |
100 |
Hexitols (95) |
n.r. |
127
|
29 |
Cellobiose |
Ru/N-doped AC |
5 |
— |
160 |
3 |
6 |
H2O |
100 |
66 |
Cellobitol (31) |
109
|
Glucose (1) |
|
30 |
Cellobiose |
Ru/N-doped GNP |
5 |
— |
160 |
3 |
6 |
H2O |
100 |
61 |
Cellobitol (13) |
109
|
Bifunctional catalysts typically consist of a dispersion of metal-containing active sites on a functional support in which Ru or Ni are commonly used because these have been shown to be effective for hydrogenating glucose to sorbitol. The functional support may provide acidity, alkalinity or redox properties, and it can provide a balance between hydrogenation and hydrogenolysis activity to control the selectivity of the desired product.39,101 The catalyst should have a higher activation barrier than hexitol dehydrogenation and hydrogenolysis to facilitate the desorption of hexitol rather than conversion to by-products (Fig. 8).
Many studies have focused on tailoring bifunctional catalysts to achieve favorable depolymerization and hydrogenation of cellulose to sorbitol. Carbon materials having rich surface functional groups are one type of the candidate carriers.102 Carbon-supported Ru or Ni catalysts are effective catalysts for achieving one-pot conversion, such as Ru/AC,103 Ru/CNT,104 Ni/CNF105 and Ru/AG-CNT.106 It is also possible to introduce sulfonic acid groups to improve Ru/CCD-SO3H,107,108 or to dope heteroatoms like nitrogen109 and phosphorus.110,111 Combination of bimetallic catalysts can achieve simultaneous improvement in selectivity and stability.112 For example, the combination of precious metals and transition metals (Ru and Ni),67,113 and the formation of alloys from transition metals (Ni, Fe)54,68 all improve the stability of the metal sites. High yields have been obtained for carbon and silicon composite supported metal catalysts, such as Ni/SiC,24 Ru/CB@SiO2.114 Some hydrothermally stable solid acids are good supports for bifunctional heterogeneous catalysts, such as zeolites, metal oxides, heteropolyacids and modified carbon materials, which will be discussed in detail in the next section.
Liu et al.115 proposed recyclable mineral acids, insoluble copper salts Cu2(OH)PO4 and Cu3(OH)4SO4, which can be reduced by H2 and used to efficiently hydrolyze cellulose via the in situ generated H3PO4 and H2SO4, and after the reaction, the H3PO4 or H2SO4 can be reconverted to the insoluble salts by the addition of CuO. In combination with the hydrogenation catalyst Ru/C, it provided sorbitol in 93.7% yields from cellulose at conditions of 473 K, 4 MPa H2 partial pressure and 1 h reaction time (Table 3, entry 19).
In summary, efficient and economic coupling of catalytic cellulose hydrolysis and hydrogenation is the key bottleneck for production of sorbitol directly from cellulose. Progress achieved to date for one-pot production of sorbitol from cellulose via selected catalytic systems (Table 3) will be discussed next.
2.2.3 Pretreatment methods.
In heterogeneous catalytic reaction systems, contact between catalyst and cellulose is an inherent issue, so many methods have been proposed for pretreating cellulose to decrease its crystallinity and degree of polymerization. Pretreatment is broadly categorized into physical methods, namely, mechanical ball-milling, mix ball-milling (isothermal), ultrasound, microwave, supercritical CO2 assisted128 and chemical methods, namely, acids, bases, organic solvents and biological methods, namely, use of enzymes, enzymatic decomposition.129 The use of additives for promoting cellulose dissolution in solvents has long been explored, with acids (H2SO4, H3PO4),130 bases (NaOH, KOH),131 and ionic liquids132 being proposed. Moreover, solvent additives are commonly used in the preparation of cellulose-based materials and cellulose processing.133 However, with much emphasis on green chemistry and green engineering, safe and environmental (green) pretreatment methods for cellulose are being sought.
Pretreatment of cellulose using ball-milling has received attention because this method has zero waste and it can be universally applied.29,134 As a means of mechanical pulverization used in industry, ball milling can reduce cellulose crystallinity and improve cellulose solubility and reactivity through mechanical shear and thermal effects.135,136 Microcrystalline cellulose changes from needle to spherical shape after ball milling and its particle size is greatly decreased.137 Ball milling can promote contact and adsorption of cellulose molecules onto catalyst surfaces under solvent-free conditions. Control of cellulose crystallinity can be achieved by varying the parameters of ball milling, such as milling time, speed, ball-to-cellulose ratio, and milling media. Fig. 9 shows the effect of ball-milling on cellulose properties,138 where it can be seen that there are decreases in degree of polymerization (DP), crystallinity index (CrI) and particle size (d) with an increase in ball-milling time and frequency. Ball-milling cellulose weakens its hydrogen bond network and changes its physical properties. Li et al.107 applied XRD analyses to cellulose and found that after ball-milling, cellulose crystallinity decreased significantly and it had an amorphous character. Compared with microcrystalline cellulose, cellulose conversion of ball-milled cellulose increased from 48% to 100% and sorbitol yield increased from 30% to 64% over Ru/CCD-SO3H catalyst in water at 180 °C for 10 h reaction time (Table 3, entry 11). In the Ru–Ni/CNT catalytic system, 74% sorbitol yield could be achieved within 1 h at 205 °C and 5 MPa H2 after mix-milling (e.g. isothermal ball-milling) of cellulose and catalyst at 20 Hz for 4 h, which nearly doubled the yield of sorbitol compared with using untreated cellulose as substrate (Table 3, enty 6).116 Pretreatment of cellulose with ball-milling or mix ball-milling are waste-free and efficient methods that have industrial potential.
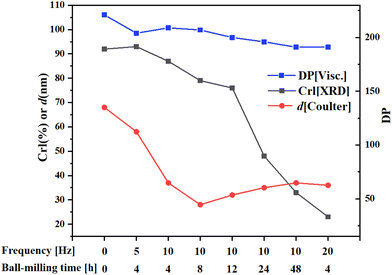 |
| Fig. 9 Changes in crystallinity index (CrI), degree of polymerization (DP) and average particle diameter (d) of microcrystalline cellulose after ball-milling.138 | |
Introduction of microwave and ultrasonic auxiliaries into a catalytic system have been shown to improve contact of cellulose with catalysts and to increase, for example, glucose yields. Zhang et al.139 introduced sonication into a hydrolysis reaction system containing microcrystalline cellulose that gave glucose yields of up to 42% in reaction times of less than 3 h. However, scalability and separability of systems that use microwave140,141 and ultrasonic auxiliaries142 still require further development.
2.2.4 Solvent effects.
Production of sorbitol from cellulose and glucose is usually carried out in aqueous solutions because water is an environmental solvent that readily promotes hydrolysis. The concentration of H3O+ and OH− generated by self-ionization in water as its temperature increases catalyzes the breakage of glycosidic bonds and promotes hydrolysis of cellulose to form oligomers and glucose, which can then be converted into sorbitol in the presence of a hydrogenation catalyst. However, the hydrolytic activity of water is generally weak at room temperature, and liquid or solid acids need to be added to improve its efficiency or the system temperature needs to be increased. If the acidity is too strong, it leads to an increase in side reactions, such as dehydration of glucose to 5-HMF and LA143 or dehydration of sorbitol to isosorbide.123 Although it has been reported that an appropriate alkalinity is beneficial for glucose ring opening that leads to an increase in conversion, alkaline sites promote isomerization of glucose and its hydrogenolysis into small molecule alcohols via retro-aldol condensation.144
Ionic liquids are considered as green solvents for cellulose hydrolysis and hydrogenation.145 Cellulose can be dissolved in ionic liquids, which improves the contact between the solid catalyst and cellulose.146,147 Yan et al. used Ru nanocluster catalysts in [bmim]Cl ionic liquids to convert cellulose into C6 alcohols, confirming the promotional effect of ionic liquids on cellulose conversion to hexitols, although only 15% conversion was observed.148 Zhu et al.149 produced hexitols from cellulose by hydrogenation in IL, where cellulose combined with boric acid to form a conjugate, which was reduced to sorbitol by loading hydrogen in a yield of about 89%, whereas a higher yield of 94% could be obtained if sodium formate was used as the hydrogen source. Gao et al.119 selected [Amim]Cl for cellulose dissolution, which effectively promoted hydrolysis to afford glucose yields up to 50%. With a Nafion NR50 and Ru/AC catalyst, the yield of sorbitol was 34.3% at 150 °C for 1 h reaction time.119 The low viscosity of [Amim]Cl makes it easier to enter the inner structure of cellulose and to disrupt its hydrogen-bond network which facilitates dissolution of cellulose in the solvent.
The compound ZnCl2·4H2O is a salt hydrate in the liquid state at room temperature and a cheap alternative to ionic liquids as a reaction solvent or additive for efficient hydrolysis. For example, for cellobiose, sorbitol yields higher than 95% have been reported.150 However, due to the interaction of hydroxyl groups with ZnCl2 salt hydrate ionic species, sorbitol in the medium is easily further dehydrated to isosorbide.151 A scheme for sequential hydrolysis, hydrogenation and dehydration of lignocellulose to isosorbide, in a molten hydrate medium (Fig. 10) shows that there is the possibility for one-pot conversion and when the salt hydrate medium is recovered, a continuous process can be developed.
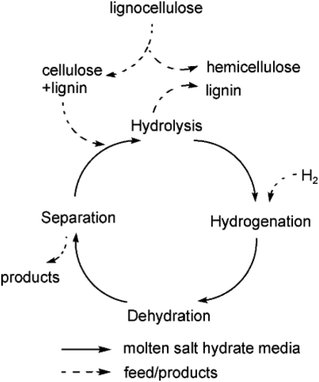 |
| Fig. 10 Scheme of hydrolysis, hydrogenation and dehydration of lignocellulose to isosorbide in molten hydrates.151 Reproduced from ref. 151 with permission from WILEY, copyright 2010. | |
Deep eutectic solvents (DES) have become an alternative to ionic liquids, because they are less expensive, more environmental and can be effective for dissolving cellulose.152 However, most studies that use DES to pretreat cellulose have been applied to enzymatic reactions rather than to catalytic conversion reactions for sorbitol production. The exploration of solubilization of cellulose has received attention in several fields, and the use of solvents such as ionic liquids, metal salts, deep eutectic solvents or alkaline ammoniated cellulose has been studied to increase the solubility of cellulose. Limitations in the field of cellulose catalysis are mainly due to the difficulty of separating hydrogenation catalysts and polyol products from ionic liquids and the ease of dehydration of intermediates into by-products such as 5-HMF. It can be expected that the range of options will be broadened, because reaction solvents and mixed-reaction solvents are active research topics.
In examining available literature on one-pot conversion of cellulose to sorbitol, it can be concluded that no papers address the separation and recycle of ionic liquids due to multifacets of the reaction. Research studies tend to focus on ionic liquids for hydrolysis of cellulose to glucose, while solvents are not demonstrated to promote hydrogenation of glucose to sorbitol with separation and recycle aspects being a future consideration. The effects of using non-aqueous solvents on cellulose hydrolysis have been explored far more than one-pot conversion to sorbitol.
2.3 Production of sorbitol from lignocellulose biomass waste
Lignocellulosic biomass has a multi-layered and multi-scale spatial structure with cellulose, hemicellulose and lignin constituents, with cellulose having the highest percentage of the skeleton.156 Conversion from raw biomass to sorbitol requires a strong pretreatment process to remove non-fiber components from the lignocellulose, e.g. strong acids or bases are commonly used to extract cellulose for further use. Conventional inorganic acids (sulfuric acid, phosphoric acid)157,158 and heteropolyacids159 have been used in the production of carbohydrates from lignocelluloses. To address pollution and corrosion issues caused by liquid acids, researchers have explored direct conversion of woody biomass into sugar alcohols by heterogeneous catalysis.160 Zhou et al.161 converted Jerusalem artichoke tuber, which is a crop, directly to hexitols in 93% yields (32% mannitol and 61% sorbitol) over a Ru/AC-SO3H catalyst. Yamaguchi et al.162 reported on the direct conversion of lignocellulosic biomass (Japanese cedar, eucalyptus, bagasse, empty fruit bundles and rice straw) to sugar alcohols using carbon black BP2000-supported Pt and Ru–Pt catalysts without the addition of acid, and obtained up to 0.551 g of sugar alcohols from 1 g of ground lignocellulosic biomass, with bagasse giving the highest amounts of sugar alcohols. Non-noble metal catalysts Ni/ZrP2 were used to obtain 40.2% sorbitol and 67.9% xylitol directly from untreated birch sawdust.123
Ribeiro et al.163 used a two-step thermal ramp-up method with Ru/CNT catalyst in presence of 5 MPa H2 under hydrothermal conditions to produce sorbitol and xylitol directly from a mixture of cellulose and hemicellulose (corncob xylan). Specifically, they163 used an initially used a reaction temperature of 170 °C, which favors xylitol formation, and then increased the reaction temperature to 205 °C, which favors the formation of sorbitol. The yield of sorbitol and xylitol was 73.9% and 75.6%, respectively, when Ru/CNT catalyst was added to react at 170 °C for 2 h and then at 205 °C for 4 h at 5 MPa H2, maximizing the yield of both two products. This group117 also used waste cellulose feedstocks such as cotton wool, cotton fabric, toilet paper and printing paper ball milled with Ru/CNT catalyst prepared by simple impregnation method to achieve 100% conversion and 50% sorbitol yield in 4 h reaction time.
3. Catalyst development for sorbitol production
The preparation of sorbitol and its derivatives from cellulose mainly involves hydrolysis and hydrogenation reactions, so bifunctional catalysts are necessary to achieve one-pot conversion of cellulose to sorbitol. There have been many studies on solid acid-promoted hydrolysis of cellulose to glucose,9,30,164 with glucose yields approaching 100%. Similarly, for glucose hydrogenation to sorbitol, there have been a number of studies reporting sorbitol yields close to 100%.53 However, highly selective production of sorbitol from cellulose has not been achieved by simple combination of the hydrolysis–hydrogenation reactions. Catalytic efficiencies of metal supported acidic supports are higher than those of physically-mixed solid acid and hydrogenation catalysts, whereas it has been noted that sorbitol yields can be increased by 10% to 30% when bifunctional catalysts are used.107,120 There may be a subtle link between hydrolysis and hydrogenation that requires deep probing into the mechanism to identify reaction intermediates. Bifunctional catalysts have been developed to promote hydrolysis and hydrogenation and to accelerate the transfer of intermediates of different reactions. Catalytic activity is mainly influenced by surface properties such as functional groups, acid centers, pore structure, specific surface area and metal active centers on the catalyst.165 Understanding the relationship between catalyst structure and performance is important for catalyst design and for suppressing side reactions and improving product yields (Fig. 11).
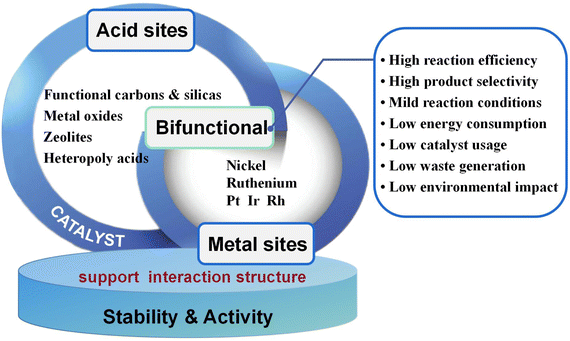 |
| Fig. 11 Bifunctional heterogeneous catalysts and optimization for one-pot conversion of cellulose to sorbitol. | |
3.1 Role of metal sites in hydrogenation
Both noble metals (Ru, Rh, Pd, In, Pt) and non-noble metals (Ni, Fe, Cu, Co) have been used as active sites for glucose hydrogenation reactions. This section focuses on the role and performance of active metal sites in hydrogenation and the structural properties and characteristics of the metals (particle size, dispersion).
3.1.1 Non-noble metal catalysts.
Nickel catalysts were introduced into glucose hydrogenation processes in the middle of the twentieth century because of their relatively high efficiency and low cost.166 RANEY® nickel, which is derived from a nickel-aluminum alloy, is a typical catalyst for industrial production of sorbitol from glucose, because it is inexpensive and highly active even though its stability and recyclability are generally unsatisfactory.167 In the hydrogenation of glucose, the loss of Ni and the poisoning of active sites by undesirable humin byproducts are the main reasons for inactivation of RANEY® nickel.73,168 Transition metal promoters, such as Mo and Cr, can be added to increase the activity and lower the leachability of RANEY® nickel, but the improvement is limited.169 Gallezot et al.170 explored the mechanism of high hydrogenation activity of promoted RANEY®-nickel catalysts through the use of promoters such as Fe, Sn in the low valence state on the nickel surface that act as Lewis adsorption points for the oxygen atom of the carbonyl group, which is then polarized by nucleophilic attack of hydride ions on the carbon atom, favoring hydrogenation.169 However, nickel catalysts are prone to poisoning, sintering, and leaching during the reaction which shortens catalyst life and interferes with product purity.171 Excessive Ni content occurs in sorbitol products that use nickel catalysts due to formation of chelate complexes with nickel in alkaline aqueous solutions.168 In practical applications of sorbitol for medicines, cosmetics and food in which the maximum allowable concentration of nickel is 2 mg kg−1, nickel must be completely removed from the product, resulting in additional production costs.172
Therefore, researchers have focused on improving performance and stability of nickel-based catalysts by selecting suitable supports or by adding promoters to reduce leaching of Ni.173 Hoffer et al.168 investigated the addition of Mo and Cr/Fe promoters for increasing BET surface area and stability of RANEY® nickel catalysts in which BET surface area increased from 56 m2 gcat−1 (RANEY® nickel) to 112 m2 gcat−1 (RANEY®-Ni–Cr/Fe) and activity increased from 0.35 kg−1 s−1 to 0.90 kg−1 s−1, respectively, while the loss of activity decreased from 48% to 16% after 3 runs. Appropriate concentrations of W, Mo, Cr and Fe act as promoters with RANEY®-Ni to improve catalyst activity and stability in glucose-sorbitol reaction systems, because of several reasons: (i) they can have synergistic effects with Ni, (ii) they can increase in the number of surface active sites and adsorption capacity that improves hydrogenation, (iii) they can modulate surface chemical structure and electron distribution, all of which can inhibit undesirable side reactions.
Porous supports such as SiO2, TiO2, Al2O3 and carbon can improve nickel dispersion and catalyst performance. Among the supports, SiO2 is commonly used with Ni for industrial catalysts. Schimpf et al.172 used ethylenediamine nickel nitrate impregnated on a silica support in which Ni2+ ions were attached to the strongly chelated ethylenediamine ligand giving small metallic nickel particles of ca. (2 to 3) nm that inhibited nickel migration and particle growth during heat treatment. Ni/ZSM-5 catalysts loaded with petal-like nickel are effective for converting cellulose to hexitols and for inhibiting further hydrogenolysis of sorbitol with 48.6% conversion and 91% selectivity at 230 °C being reported.174
Some carbon supports are also beneficial for the stability and dispersion of Ni metal particles, making them an alternative to specialized materials. Van de Vyver et al.105 loaded Ni crystals on the tips of carbon nanofibers (CNF), and the 3 wt% Ni/CNF catalyst showed high efficiency and durability with 92% cellulose conversion and 50% sorbitol yields, which was better than the performance of conventional Ni/Al2O3 and Ni/C catalysts. They proposed that the attachment of nickel particles to the tips of carbon nanofibers increased the accessibility of the active sites to cellulose. In addition, they confirmed by XRD characterization that the increase of the Ni(111) surface ratio and the reaction-induced remodeling of nickel nanocrystals explained the high catalytic activity.175 Later researchers confirmed by DFT calculations that the different crystalline forms of nickel do affect hydrogenation activity.176,177 Another way to improve the catalytic activity and stability of nickel is to strengthen the interaction between the metal and support. The doping of N in the carbon-loaded nickel catalyst to create Mott–Schottky heterojunctions promotes partial charge transfer from the metal to the supports. Fig. 12 shows an image of the strong metal–support interactions, where charge transfer between the Ni nanoparticles (δ+) and the carrier (δ−) leads to high reduction activity and stability of nickel.173,178
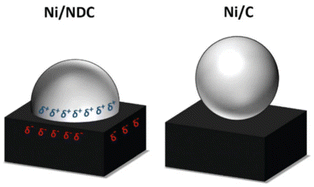 |
| Fig. 12 Proposed charge-transfer stabilization effect between Ni nanoparticles and NDC in comparison with pristine carbon support (Ni/C).173 Reproduced from ref. 173 with permission from The Royal Society of Chemistry, copyright 2020. | |
Conventional nickel catalysts use zero-valent Ni and NiO nanoparticles as active sites.52,179 Nickel phosphide nanoparticles have been found to have catalytic potential and to be constituents of amorphous metal catalysts that have high activity and stability.25 The development of new catalysts by appropriate addition of P to Ni produces new crystalline phases, which can improve activity, enhance metal dispersion and impart the materials to have good hydrogen transfer ability. Nickel metal phosphide bifunctional catalyst loaded onto activated carbon support as Ni2P/AC catalyst afforded a sorbitol yield of 48.4% from cellulose,180 whereas the conversion of cellobiose to sorbitol achieved yields of 80.8% over catalyst S-10Ni4P supported on SBA-15.125 Nano Ni2P activates H2 for hydrogenation and has good air stability, high activity and reusability.25 The acidic potential energy formed by excess P favors hydrolysis and different P–Ni ratios allow selectivities to be varied. Li et al.181 synthesized Ni–P–Al amorphous alloy catalysts (RANEY® Ni–P) in the molten state by an alkali immersion rapid quenching technique which when applied enhanced TOF by up to 4 times compared with the conventional RANEY® Ni catalyst of the same loading, thus phosphorus greatly enhanced the catalytic activity of the nickel active sites. Those authors also developed Ni–B/SiO2 amorphous catalyst (6.4 wt% Ni) for hydrogenation of 50 wt% glucose at 373 K, 4.0 MPa H2 and 6 h using a stainless steel autoclave containing 1 wt% catalyst.182 Amorphous catalysts exhibited much higher activity than other nickel-based catalysts due to their high dispersion, high concentration of ligand unsaturated sites and nickel-rich electrons, which favor hydrogen adsorption.183
Nano-catalysts have been prepared by chemical reduction, using hydrazine hydrate184 and sodium borohydride52 for deposition and reduction of metals that have high dispersion and good activity. The principle reaction equation for nano-catalyst synthesis by chemical reduction is as follows:
| M2+(aq) + N2H4(aq) + 2OH− → M0(s) + N2(g) + 2H2O(aq) | (5) |
with M = Ni or Cu.
Other transition metals such as Fe, Co and Cu can be used in the hydrogenation of carbohydrates to produce sugar alcohols, by forming alloys to improve catalytic activity and to lower metal leaching. When Fe alone is used as nano-catalyst, it promotes ring-opening isomerization of glucose to fructose,185,186 whereas Cu nano-catalysts show good catalytic activity for the hydrogenation of fructose to mannitol. Co nano-catalysts facilitate the conversion of xylose to xylitol, and promote glucose hydrogenation after the formation of an alloy with Ni.187
Ni/Cu/Al catalysts loaded onto hydrotalcite supports in different ratios can be adjusted to obtain 73.2% glucose conversions and 93.4% sorbitol selectivity.53 As the Ni/Cu molar ratio was increased from 0.9 to 2.8, the yield and selectivity of sorbitol both increased from 40% to 65% and from 60% to 90%,53 however, when the Ni content was further increased to 31 wt%, the yield of sorbitol decreased to 45%. Those authors53 did not discuss in depth the reason for the synergistic effect between Ni and Cu. An iron-nickel alloy supported on carbon gave higher glucose conversions (70.4%) and sorbitol yields (50%) than the respective metal catalyst.54 In the future, more in-depth research is needed to elucidate synergistic effects in metal alloys through advanced characterization techniques and theoretical calculations for developing clear mechanistic pictures.
3.1.2 Noble metal catalysts.
The noble metal catalyst Pt/γ-Al2O3 is commonly applied for hydrogenation and was initially used for the conversion of cellulose to sorbitol.188 Ruthenium catalysts exhibit the best performance,189 requiring less than 5 wt% loading to obtain similar hydrogenation performance as Pt/γ-Al2O3, and are compensated by their lower cost and extended lifetime that results in shorter downtimes which benefits industrial production. Michel and Gallezot190 proposed two mechanisms to explain the superior performance of ruthenium-based catalysts over other platinum group metals in the hydrogenation of carbonyl groups to the corresponding alcohols. One mechanism was based on the interaction between the C
O group adsorbed onto the Ru surface and the adjacent adsorbed water molecules through hydrogen bonding that lowers the activation energy barrier of hydrogenation, and the electron-rich Ru facilitating the dissociation of H2 leading to the carbonyl group of glucose being more easily hydrogenated. Another mechanism was based on the dissociation of water adsorbed on the ruthenium surface, which produces H+ and [Ru(H2O)5OH]2+ as Brønsted acid, increasing the concentration of hydrogen atoms on the surface and thus increasing the hydrogenation capacity. The energetic gain of water molecule chemisorption on the overall barrier is closely related to the pro-oxidative nature of the metal, i.e., the d-band center.190 Negoi et al.191 concluded that the metal d-bandwidth determines sorbitol selectivity, which follows in the order of Ir > Ru > Rh > Pd regardless of whether glucose or cellulose is used as substrate. Due to the special electronic structure and charge distribution properties, Ru can adsorb and activate hydrogen molecules, thus accelerating hydrogenation reactions.
Ruthenium-based catalysts are so active in aqueous phase hydrogenation reactions of carbonyl compounds that they have attracted a lot of attention in chemistry.190 Appropriate supports offer large surface areas, aid in dispersion of Ru species, and provide strong interactions with Ru, all of which contribute to enhancing the catalytic activity of Ru catalysts. One materials that is particularly suitable is carbon in which ruthenium is anchored by interacting with abundant active sites on the material, forming chemical bonds through covalent or ionic bonds.30 Carbon has good electron conduction and electron transfer occurs between Ru and carbon, thus promoting catalytic efficiency. Small crystals of metallic Ru nanoparticles coexist with amorphous Ru(O)xı+ species on supports in which the model proposed by Lazaridis et al. is based on the dissociative adsorption of molecular H2 on metallic Ru(0) nanoparticles and the subsequent formation of hydrogen atoms spilling over to neighboring Ru(O)1+ species, while electrons are transferred from H atoms to positively charged Ru(0) species, forming protonic acid sites Ru(O)xH+ and releasing protons into aqueous solution55 (Fig. 13). Direct hydrolysis from cellulose to sugar alcohols could be achieved with this type of catalyst,55 however, unfortunately, the high activity leads to undesirable dehydration and hydrolysis of sorbitol to byproducts such as arabinitol and glycerol.30,106
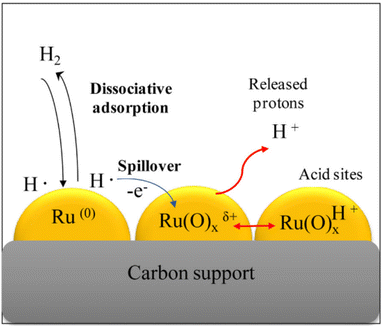 |
| Fig. 13 Model for formation of released protonic acid sites Ru(O)xH+ and H+ in aqueous solution proposed based on dissociative adsorption of hydrogen on metallic Ru(0) nanoparticles followed by spillover to neighboring Ru(O)1+ species and electron transfer of H atoms on these species.55 Reproduced from ref. 55 with permission from Elsevier, copyright 2015. | |
Although the cost of Ru is about half that of Pt, it is still considered to be expensive, and further research is needed to improve catalyst lifetime through effective supports and regeneration methods. The high activity and general stability of Ru catalysts can be attributed to the wide dispersion of Ru particles, the strong interactions between Ru and the support and suitable acid–base sites on the surface of the support.190 Mishra et al.60 prepared HY zeolite-loaded ruthenium nanoparticle catalysts by conventional impregnation–reduction method using an ethanol solution of NaBH4 as reducing agent. In the application of the HY zeolite-loaded Ru nanoparticle catalysts,60 glucose conversions reached 100% with 98.7% sorbitol selectivities at 393 K for 5.5 MPa H2 partial pressure and 2 h reaction time. Ru nanoparticles are more dispersed and crystalline on N-doped carbon supports than on unmodified carbon supports resulting in higher catalytic activity. Carlier et al.109 used N-doped carbon supported Ru catalyst to convert cellobiose into sorbitol with a yield of 66% for 3 MPa H2 partial pressure and 6 h reaction time. Some new strategies have been proposed, such as the introduction of transition metal phosphides to regulate Ru electron transfer and to improve sorbitol yield. Qiu et al.65 designed Ru2P/C-SO3H catalysts to convert cellulose into sorbitol and obtained yields of 64% at 200 °C for 2 h reaction time. Xu et al.62 used defect-engineered MOFs supported Ru catalysts for glucose hydrogenation and obtained TOF values of over 2150 h−1 with catalyst stability being maintained for more than 10 cycles. The activity of noble metals can be greatly enhanced by support materials, which provides many opportunities for research and development.
3.1.3 Multimetallic catalysts.
Compared with mono-metallic catalysts, multimetallic catalysts can exhibit synergy that improves catalytic performance. The addition of a second metal may alter the activity of the original metal by changing the d-band center present in the metal site.192 Interactions between different metals may also affect the metal particle size along with its activity and stability (Table 4).54,113
Table 4 Dissolution of cellulose and subsequent hydrogenation in solvents
Solvent |
Dissolution mechanism |
Solvent |
One pot conversion |
Catalyst |
Conversion (%) |
Yield (%) |
Conditions |
Ref. |
n.r.: not reported. |
Aqueous |
Hydrogen bond destruction, electrostatic interactions |
Acid/H2O |
Catalysts with hydrogenation sites and acid sites |
Cellulose (80–100) |
Sorbitol (30–75) |
(150 to 250) °C, (3 to 6) MPa, (1 to 6) h |
46, 98, 106, 116, 122, 153, 154 |
Molten inorganic salt hydrates |
Hydrogen bond destruction |
ZnCl2 hydrate medium |
Ru/C |
Cellobiose (100) |
Sorbitol (95) |
125 °C |
151
|
4 MPa |
1.25 h |
Ionic liquids |
Hydrogen bond destruction by anions and cations |
[BMIM]Cl |
Ru nanocluster |
Cellulose (15) |
n.r. |
n.r. |
148
|
[BMIM]Cl |
Ru nanoparticles |
Cellulose (100) |
Sorbitol (94) |
80 °C |
149
|
HCO2Na |
5 h |
[BMIM]Cl |
Rh/C, HRuCl(CO)(PPh3)3 |
Cellulose (100) |
Sorbitol (74) |
150 °C |
155
|
3.5 MPa |
48 h |
[AMIM]Cl |
Ru/AC, Nafion NR50 |
n.r. |
Sorbitol (34) |
150 °C |
119
|
5 MPa |
1 h |
Zhang et al.53 prepared Ni/Cu/Al catalysts using a co-precipitation-reduction method, and the glucose conversion and sorbitol selectivity reached 78.4% and 93.4%, respectively, while improving the performance of the catalyst and reducing its cost. Pang et al.153 investigated the synergistic effect of using Ni-doped Pt, Pd, Ru, Rh and Ir bimetallic catalysts for sorbitol production on mesoporous carbon (MC) supports and obtained up to 59.8% yields of sorbitol from cellulose by adjusting the type and ratio of doped noble metals. In that work,153 complete cellulose conversions and similar 50% sorbitol yields were obtained using 20% Ni/MC and 4% Ir-4% Ni/MC catalysts with ball-milled cellulose as the substrate, however, in recycling evaluations, the pure nickel catalyst activity decreased to afford 40% yields after three cycles, while the bimetallic catalyst maintained its level of activity. Doping of precious metals in nickel catalysts is beneficial for improving catalytic activity and stability. Ruthenium-nickel bimetallic catalysts loaded onto mesoporous silica MCM-48 exhibited higher selectivities (ca. 100%) for the hydrogenation of glucose to sorbitol, compared with 93% to 95% for catalysts using only Ni or Ru as the hydrogenation sites.193 In another work, Ru and Ni mono- and bimetallic catalysts were prepared by impregnation in either activated carbon or carbon nanotube as supports. After ball-milling with cellulose using Ru–Ni/CNT bimetallic catalyst and application in the reaction system, cellulose conversion reached 99% and sorbitol yield reached 71% (mass basis) after 1 h reaction time.116 Addition of Ir promoter increased the yield of hexitols over SiC-supported Ni catalyst to 75.7% from cellobiose and the formation of Ni–Ir alloy led to improved cyclic stability.24 As shown in Table 5, some combinations of noble and non-noble metals have synergistic interactions, namely, that the total catalytic activity of the combined-metals is greater than the sum of the individual metal activities.
Table 5 Metal combinations and effects
Multi-metal |
Support |
Interaction type |
Role |
Ni-noble metal (Ir, Ru, Pt) |
Silica/carbon |
Electron transfer |
• promotes hydrogenation |
Ni-transition metal (Cu, Al, Fe) |
Silica/carbon |
Alloy formation |
• promotes hydrogenation |
• improves stability |
Ni, Ru, Pt |
Al2O3, ZrO2, ZrP |
Support-metal Lewis/Brønsted acidity |
• provides acid sites via supports |
• promotes metal dispersion |
• prevents agglomeration |
The attractive cost advantage of non-precious metals over noble metals has prompted researchers to explore ways to improve the catalytic activity of transition metal alloys. Zhang et al.100 prepared an inexpensive paramagnetic catalyst Ni/Cu/Al/Fe on a hydrotalcite support that gave 68.1% sorbitol yields from cellulose by addition of 0.08 wt% phosphoric acid to the reaction system that was at conditions of 215 °C, 4 MPa H2 partial pressure and 3 h reaction time. Nickel-cobalt nanoalloy catalysts with a molar ratio of Co/Ni = 1 exhibited higher catalytic activity in hydrogenation reactions than the two respective metal catalysts.48 Electronic effects are observed for Fe–Ni alloys in catalysts that enhance catalyst activity and stability by inhibiting metal leaching.54
Some multi-metallic catalysts can be supported by a metallic element to allow the metal with the hydrogenation function to be uniformly dispersed and to prevent its agglomeration. Metallic element supports such as Al2O3 and ZrO2 can provide acid sites, which is one of the design strategies of hydrolysis–hydrogenation multifunctional catalysts.
3.1.4 Effect of structural properties.
In addition to metal type of a catalyst, structural properties such as metal particle size and metal dispersion in the material, affect catalytic activity.29 Through advanced characterization techniques, the relationship between structural properties and catalytic performance has been explored with more works beginning to focus on structure–activity relationships.165,194
Fukuoka's group195 showed that increasing Ni loading in a material increases particle size, but obtained good activity and durability with some formulations. When carbon black supported Ni catalyst loading was increased from 10 wt% to 70 wt%, average nickel particle radii increased from 4 nm to 16 nm, and the sorbitol yields from cellulose increased from 3.8% to 50% at 5 MPa H2 partial pressure, 483 K reaction temperature and 6 h reaction time, in which the catalyst could be reused for 7 times. Low nickel loadings tend to contain large amounts of nickel oxides, which deactivates quickly under hydrothermal conditions, while catalysts with high nickel loadings are more resistant to sintering and inhibit hydration of nickel oxide that forms Ni(OH)2 and covers active sites. Zhang et al.41 investigated the structure–activity relationship of Pt nanoparticles (3 to 17) nm in diameter on mesoporous SBA-15 supports for the hydrogenation of glucose to sorbitol and showed that larger Pt nanoparticles favor selective C
O hydrogenation to the corresponding alcohols. Aho et al.196 investigated the structural sensitivity of Ru-supported carbon nanotubes for the hydrogenation of glucose to sorbitol and found that the highest catalytic activity was obtained for ruthenium particles having a size of 3 nm.
The active site of a hydrogenation catalyst is usually a metal in its zero-valent state. Metal species, such as ruthenium, nickel and platinum are generally thermally-reduced by hydrogen or carbothermal reduction at high temperatures173 or chemically-reduced by strong reducing agents such as NaBH4,55 ascorbic acid or glycol.197 However, the pyrolysis temperature greatly affects the performance of carbon-based catalysts, with Ni nanoparticles agglomerating above 700 °C and possibly catalyzing the methanation of carbon, which then contributes to the collapse of porous structures in a carbon support.177 Small Ni metal particles on the catalyst surface are more easily oxidized to NiOx than large Ni metal particles, while Ru metal particles smaller than 2 nm are easily oxidized to RuO2·2H2O at room temperature.94 However, some studies have shown that proper oxidation to the ionic state or the formation of alloys can improve hydrogenation activity of metals. Partial oxidation of Ru/C to Ru/RuOx/C favors activity and selectivity over the metal phase alone in transfer hydrogenation processes.198 Furthermore, the formation of by-products depends on the crystalline/non-crystalline nature of Ru and Ru(O)xδ+ nanoparticles. It should also be noted that a suitable precursor should be selected for doping of the metal.55 Residual chloride ions on the catalyst may promote the occurrence of side reactions, inhibit selective hydrogenation sites or promote hydrogenolysis reactions leading to C–C and C–O cleavage reactions.188
Amorphous alloys are a new class of multi-component alloy materials that can improve the activity of conventional catalysts by modulating the electronic structure to obtain desirable catalytic activity centers.199 Ru–B amorphous alloy has been shown to be a potential substitute for commercial catalyst RANEY® nickel for hydrogenation of glucose to sorbitol.200 Similarly, amorphous metal phosphides have received wide attention, because the transfer of partial charge from metal atoms to P atoms is conducive to reducing the reaction energy barrier of hydrogen desorption which provides high hydrogenation activity.201 Amorphous alloys deposited on supports can further improve the activity and stability of a catalyst.202 Materials with large surface area and porous structures such as mesoporous molecular sieves125,203 or modified carbons65 can be used as supports to disperse and stabilize metals and can provide acidic sites as multi-functional catalysts. It was found that Ni2P combinations,180 and RuP combinations65 as catalytic sites could obtain glucose conversions greater than 95% and sorbitol yields of up to 50%, when acid sites were loaded onto different supports.180
3.2 Role of catalyst supports
Catalysts for one pot conversion of cellulose to sorbitol typically have acidic sites for promoting hydrolysis of cellulose and metal sites for promoting hydrogenation of glucose. The catalyst support provides acidity and supports the metal sites, while the interaction between the metal and the support promotes adsorption of the substrate and dissociation of H2, which largely affects the kinetics.154 Therefore, design of the support and targeting the layout of active centers can improve sorbitol yields. Supports with suitable proportions and distribution of mesopores and high specific surface area facilitate mass transfer, increase the exposure of active sites, increase the contact area for the substrate and promote the dispersion of the surface-active sites.106,204
Hydrogen ions generated by dissociation of water under hydrothermal conditions (T < 250 °C) are unable to effectively break glycosidic bonds in cellulose molecules, thus past investigations on the direct conversion of cellulose to sorbitol have focused on acid catalysis. Early studies on acid catalysis of cellulose hydrolysis employed mineral acids or heteropolyacids which have issues in recycle, corrosion and cost. Use of solid acids has become popular in the literature with materials being proposed ranging from acidic resin supports to niobium phosphate,205 alumina,206 zeolites, biochar, heteropolymers, or supports modified to contain acidic groups. Alkaline support materials are generally unsuitable for the synthesis of sugar alcohols, because the alkaline sites promote reverse aldol reactions that give ethylene glycol and propylene glycol as final products.207 Common approaches used by researchers is to design catalysts that have metal loadings on porous solid acid catalysts with application of the materials to one-pot hydrolytic hydrogenation.165 Porous supports can be classified according to the type of solid acid used as discussed in the following sections.9
3.2.1 Zeolites as supports.
Natural zeolites and synthetic molecular sieves such as HY,60,208 SBA-15,209 HZSM-5, β-zeolite,191 MCM-48126 have mesoporous structures, abundant acid sites and excellent diffusional properties, thus they are frequently chosen as supports in design of bifunctional catalysts. The differences in pore sizes and acid sites between different types of zeolites lead to large differences in catalyst activity and stability. Metals introduced into molecular sieves tend to uniformly disperse into the pore channels while stabilizing their skeletal structure and provide some resistance to pore collapse that can occur in hydrothermal reaction environments.
Defects on zeolite surfaces facilitate anchoring of the metal onto the support. Ru-BEA zeolite catalyst was prepared by a simple impregnation method, which afforded 72.8% yield of sorbitol from glucose, and it also facilitated the direct conversion of cellulose to sorbitol with conversions of 99% after 3 h reaction time with sorbitol selectivity of 72.5%.191 Both the acidic functional groups of zeolites and the concentration of hydrogen adsorbed on the surface play key roles in the formation of sorbitol. Compared with TiO2 and carbon support, zeolite supports have higher selectivity and activity for sorbitol due to their special structure and better dispersion of loaded metals. Mishra et al.60 confirmed that the TOF of HY zeolite-loaded Ru (1 wt%)/HYZ catalyst was 1.08, 1.19, and 5.4 times higher than that of Ru (1 wt%)/NiO–TiO2, Ru (1 wt%)/TiO2, and Ru (5 wt%)/C catalysts, respectively. The special sodalite cage and super cage structures of Y-type molecular sieves allow isolated Ptδ+ to be stabilized by the oxygen atoms of the surrounding six-membered ring, promoting dihydro-isomeric cleavage. Pt@Y shows good activity and remarkable selectivity in the hydrogenation of α,β-unsaturated aldehydes to alcohols.208 Zeolites have strongly acidity, well-developed pore structures and are commonly used for dehydration reactions.210 Brandi et al.211 developed a continuous flow process for direct production of isosorbide from aqueous glucose solutions using β-zeolite in conjunction with a N-doped carbon supported nickel catalyst. The β-zeolites had a three-dimensional pore structure, moderately-high specific surface area (520 m2 g−1) and abundant Brønsted acid sites (69 μmol g−1) with pore sizes (6.6 × 6.7 Å2) slightly larger than the cross section of sorbitol and isosorbide, thus allowing efficient diffusion of reactants and products through the pores, all of which led to high yields as high as 60% of isosorbide.
SBA-15, which has a mesoporous structure, was loaded with precious metals Pt41 and Ru212 for glucose hydrogenation and the metals became stabilized in the pore channels that facilitated dispersion to afford sorbitol selectivity of more than 85%. Although SBA-15 supports metal sites well and promotes mass transfer, it does not provide acidic sites and therefore needs to be modified with other functional groups. Many reports have modified zeolites with sulfonic acid-based dendrimers to introduce Brønsted acid sites.213 Hydrolytic hydrogenation of cellulose could be promoted by re-deposited metals (Ru nanoparticles) on sulfonic acid functionalized SBA-15,209 MCM-41214 and silica gel.154
3.2.2 Metal oxides/phosphides as supports.
Unlike metal sites for hydrogenation, some metal oxides or phosphides have acidic sites that can be used as supports in the design of multifunctional catalysts. There are many kinds of metallic elements or metal oxides, however, research on supports has mainly focused on solid acids with porous structures such as Al2O3, ZrO2,215 NbO2, TiO2216 and CeO2. Among these metallic elements, γ-Al2O3 is the most acidic and has long been used as a solid acid to catalyze cellulose conversion.98,217 Metal oxide supports typically have strong interactions with hydrogenation metal sites such as Ru and they promote metal dispersion and improve stability of the metals. Commercial Ru/Al2O3 catalyst has been used to obtain sorbitol yields of up to 97% from 10 wt% glucose solutions and showed good stability over 10 cycles, with little change in catalyst morphology and Ru particle size (ca. 2 nm) after recycling.63 The reaction rate constant for the hydrogenation of glucose to sorbitol over zirconia-coated catalyst Ru-ZrO2-SBA-15 was twice as high as that of a Ru/SiO2 catalyst with one reason speculated being that since ZrO2 is favorable for Ru dispersion, it remains stable after reaction compared with other supports.212 Several studies have used ZrO2, which is stable under hydrothermal conditions in combination with other materials, to balance Lewis and Brønsted acid sites and to catalyze cellulose one-pot hydrolysis and hydrogenation reactions with one example being Ru-PW/ZrO2 that afforded 66% sorbitol yields from cellulose.122
One-pot cellulose conversion of cellulose to sorbitol over Ni/ZrP2 catalysts with zirconium phosphate as support gave sorbitol yields as high as 60.8% (Table 6, entry 3).123 For a series of Ni/ZrPx catalysts with Ni particle sizes of about 20 nm, the sorbitol yields were found to be related to the P/Zr ratio.123 As the P/Zr ratio increased from 0.5 to 2 to 3, the yield of the catalyzed conversion of cellulose to sorbitol increased from 11% to 50% in which the number of acidic sites first increased and then decreased. The proper match between the acidity and hydrogenation activity of the catalyst is essential for the production of sorbitol from microcrystalline cellulose, as demonstrated by experiments with cellobiose and glucose as substrates. Zhang et al.121 constructed a binary catalyst ZrP-Ru/MC, by combining zirconium phosphate with a mesoporous carbon support loaded with ruthenium, and mix-milling (isothermal ball-milling technique) cellulose and catalysts to afford sorbitol yields of 66.4% in 1.5 h reaction time.
Table 6 Bifunctional heterogeneous catalysts for one-pot conversion from cellulose to sorbitol
No. |
Material |
Metal |
Support |
Specific surface area (m2g−1) |
Acid information |
Catalytic performance |
Ref. |
Conversion (%) |
Yield (%) |
Reaction conditions |
T (°C) |
p
H2 (MPa) |
t (h) |
Solvent |
Acid density was detected by NH3-TPD.
Brønsted and Lewis acidity was analyzed by IR-spectroscopy using pyridine as the probe molecule.
The oxygen-containing functionalities was analyzed by temperature programmed desorption experiments (TPD).
|
1 |
Ni/NCC-ZSM5 |
Ni |
Mesoporous ZSM-5 |
338 |
acid densitya: 3.3 mL g−1 |
Cellulose (80) |
Sorbitol (60) |
240 |
4 |
2.5 |
H2O |
245
|
2 |
Al-S-10Ni4P |
NiP(10 wt% Ni, 4 wt% P) |
Al-SBA-15 |
298 |
acid density: 0.324 mmol g−1 |
cellobiose (94) |
Sorbitol (81) |
180 |
4 |
3 |
H2O |
125
|
3 |
Ni/ZrPx |
Ni (15 wt%) |
ZrP2 |
140 |
P/Zr ≥ 2 showed a higher total acid |
Cellulose |
Sorbitol(53) |
200 |
4 |
5 |
H2O |
123
|
4 |
Ni/TaOPO4 |
Ni (5 wt%) |
TaOPO4 |
48 |
Acid density: 0.37 mmol g−1 |
Cellulose (100) |
Sorbitol (21) |
200 |
3 |
24 |
H2O |
244
|
Brønsted/Lewis acid sites ratio = 0.153 |
Isosorbide (13) |
5 |
Ru/CsHPA |
Ru (1 wt%) |
Cs3HSiW12O40 |
110 |
Brønsted acid sitesb: 46μmol g−1 |
Cellulose |
Sorbitol (58) |
180 |
5 |
3 |
H2O |
120
|
Lewis acid sites: 82μmol g−1 |
6 |
Ru-PW/Nb2O5 |
Ru (3 wt%) |
H3PW12O40 supported on Nb2O5 |
41 |
Brønsted acid sites: 32μmol g−1 |
Cellulose (92) |
Sorbitol (66) |
180 |
7 |
7 |
H2O |
222
|
Lewis acid sites: 64μmol g−1 |
7 |
Ru-PW/ZrO2 |
Ru (3 wt%) |
H3PW12O40 supported on ZrO2 |
93 |
Brønsted acid sites: 46μmol g−1 |
Cellulose (95) |
Sorbitol(41) |
180 |
7 |
7 |
H2O |
122
|
Lewis acid sites: 176μmol g−1 |
8 |
Ru/AG-CNT1200 |
Ru (0.4 wt%) |
Hydrothermal glucose-derived/CNT hybrids |
1151 |
mild acidic sites phenol/carbonyl-quinone ratioc: 0.49 |
Cellulose (100) |
Sorbitol(60) |
205 |
5 |
5 |
H2O |
106
|
9 |
Ru/CCD-SO3H |
Ru (4 wt%) |
Sulfonated carbon |
10 |
acid density: 0.64 mmol g−1, sulfonation time: 15h |
Cellulose (100) |
Sorbitol (64) |
180 |
4 |
10 |
H2O |
107
|
10 |
Ni-Ru@MC |
Ni(9.6 wt%) Ru(0.4 wt%) |
Porous carbon (SiO2 template) |
940 |
mild acidic sites(-OH, -COOH): 0.54 mmol−1g−1 |
Cellulose |
Sorbitol (68) |
200 |
4 |
3 |
H2O |
113
|
Metal phosphates, such as zirconium phosphate or niobium oxide phosphate, have received increasing attention due to their easy synthesis, adjustable acidity and good thermal stability and have been used as solid acids to catalyze the breakage of glycosidic bonds.218 NbOPO4, which has a layered structure, can be used as a support in the design of bifunctional catalysts for one-pot conversion of cellulose to sorbitol.219 Xi et al.220,221 synthesized a bifunctional Ru/NbOPO4-PH2 catalyst for sorbitol production by mix-milling cellulose and obtained yields of 69% under optimal conditions that was attributed to the strong acidity of the NbOPO4 support as well as to the mesoporous structure that facilitated active site contact with cellulose. Niobium oxide supports with abundant total acid sites and high B/L acid ratios have been found to promote one-pot conversion of cellulose to isosorbide in which 44% yields of isosorbide were obtained over Ni/NbOPO4 bifunctional catalyst.
The discovery of strong metal–support interactions (SMSI) phenomena and metal migration has led to the development of metal oxide support catalysts having both high hydrogenation capacity and stability that is leading to many new opportunities.222 For example (Fig. 14), SnOx has significant electronic and geometric effects on the catalytic properties of the Pt site, enhancing its Lewis acidity, extracting electrons from the oxygen atom of the glucose carbonyl group to promote polarization, thus promoting the hydrogenation of C
O by adsorption of H2 dissociation on Pt.95 The adsorption of the aldehyde group by the catalyst and further hydrogenation mechanisms are due to SMSI phenomena (Fig. 14).
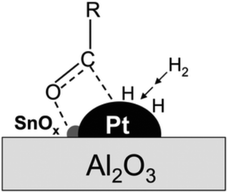 |
| Fig. 14 Schematic role of SnOx in strong metal–support interactions (SMSI) phenomena for glucose hydrogenation over Pt-SnOx/Al2O3 catalysts.95 Reproduced from ref. 95 with permission from The Royal Society of Chemistry, copyright 2013. | |
3.2.3 Polyoxometalates as supports.
Polyoxometalates (POMs) are combinations of oxygen and transition metals (e.g., M = V, Nb, Ta, Mo, W) at their highest oxidation state,223 that form a ligand polyhedral structure similar to zeolite molecular sieves with tunable acidic and oxidizing properties. POMs play an important role in catalysis as “green” or environmental acids,224 wherein Keggin-type heteropolyacids (HPAs) are used as catalysts for cellulose hydrolysis due to their strong Brønsted acidity. Geboers et al.225 used a mixture of Ru/AC and H4SiW12O40 with cellulose ball-milled for 1 h to obtain sugar alcohol yields of 85%. Ogasawara et al.226 used H5BW12O40 to promote the hydrolysis of cellulose, and HPA was separated from sugars and recovered from the aqueous reaction solutions by taking advantage of their different solubilities in alcohols.
Solid heteropolyacid (salts) catalysts have been widely used to hydrolyze cellulose and to avoid the corrosion of vessels by liquid acids. Metal-heteropolyacid (NP-POM) composites can be applied beneficially in at least two ways: (i) to immobilize the metal and HPA onto another support and (ii) to load a metal on HPA insoluble salts (Cs). The intimate contact between metals and POMs has the advantage of facilitating the migration of substrates/intermediates between the metal and acid sites at nanoscale distances compared with discrete mixtures. Gromov et al.122 deposited heteropolyacids and Ru on ZrO2 supports and activated the material at 550 °C to obtain a Ru-PW/ZrO2 catalyst, which afforded a maximum sorbitol yield of 66% at 180 °C and 7 MPa H2 partial pressure, and the catalyst was stable in its recycle for three times. Solid heteropoly salt Cs3PW12O40 supporting Ru catalyst (Ru/Cs3PW12O40) could convert cellulose to sorbitol in aqueous media with a maximum sorbitol yield of 59% at 180 °C and 5 MPa H2 partial pressure for 7 h reaction time (Table 6, entry 5).120 Liu et al.227 speculated (Fig. 15) that the strong activity of Cs3PW12O40 was due to the more H2-originated Brønsted acid and the overflow of H species from the surface of Cs3PW12O40 and obtained evidence through FT-IR studies of the adsorbed pyridine that the catalyst showed stronger acidity after the introduction of H2. Deng et al.228 similarly demonstrated this hypothesis that the Brønsted acid site originating from H2 over Ru/Cs3PW12O40 catalyst was reversible.
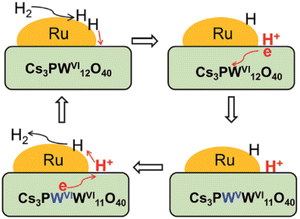 |
| Fig. 15 Schematic diagram of Brønsted acid sites generated in situ from H2.227,228 Reproduced from ref. 228 with permission from The Royal Society of Chemistry, copyright 2014. | |
Polyoxometalates have been shown to be effective supports for stabilizing a range of single-atom catalysts (SACs) that provide selective hydrogenation and they are indeed potential bifunctional catalyst supports that deserve further study.224 It should be noted that the introduction of W species may promote the retro-adol condensation (RAC) reaction, leading to the breakage of the C–C bond and the production of small molecule alcohols, with the selectivity of sorbitol being correspondingly lowered.229,230 It would be interesting to explore the precise regulation of tungsten compounds for glycosidic and C–C bond breaking and thus control the selectivity of hexitols and diols in one-pot conversion of cellulose.
3.2.4 Carbon materials as supports.
Carbon materials derived from biomass are versatile supports for reactions, because they can be easily modified to add sulfonic acid, carboxylic acid or other functional groups on their surfaces or pores.231 Carbon materials can be designed to have mesopore structures, high specific surface areas favorable for metal dispersion and bifunctional catalytic properties and they generally have good stability under hydrothermal conditions.232 Carbon materials, such as biochars and hydrochars, are popular for catalyst development due to their unique renewable characteristics.233 Carbon materials derived from biomass generally exhibit high affinity for cellulose molecules due to the presence of CH–π interactions with substrates, which tends to lower interactions of intermolecular hydrogen bonds and promote steric dissociation of cellulose (carbon solid acid hydrolysis mechanism).234 Typical carbon material supports loaded with metals have been shown to be effective for production of sugar alcohols, but activated carbon powder is not convenient for recycling, while carbon nanofibers CNF112 and carbon nanotubes CNT235 are limited in their application due to cost. The unique structure and spatial effects of carbon nanomaterials, as well as their superior heat and water resistance, has led to the development of many types of carbon-based catalysts.236
Textural properties of carbon materials greatly affect the dispersion and accessibility of substrates to active sites. In particular, mesoporous carbon (MC) materials offer advantages over conventional activated carbon (AC), because of their well-controlled pore structure in mesopores, which facilitates macromolecular transport. Pang et al.153 measured the uptake of cellobiose and glucose by MC that was found to be 0.149 g g−1 and 0.041 g g−1, respectively, which was almost twice as much as AC supports and strongly suggests that MC carriers have the ability to adsorb and activate the unique function of β-1,4-glycosidic bonds in cellulose.
Carbon supports can be easily functionalized and their functional groups and defective sites can also serve as active centers. Sulfonic acid group modified carbon supports such as Ru/AC-SO3H materials237 and Ru/CCD-SO3H materials107 have been employed to enhance acid catalyzed cellulose hydrolysis, whereas the introduction of sulfate into materials increases surface acidity and promotes cellulose hydrolysis. The total acidity of a Ru/CCD-SO3H material was 0.64 mmol g−1 after sulfonation and when it was applied as catalyst for cellulose one-pot conversion at 180 °C under 4 MPa H2 partial pressure for a 10 h reaction time, sorbitol yields of 64% were obtained compared with 20% yields from un-sulfonated material.107 Interactions of doped heteroatoms nitrogen109 and phosphorus110 with metal sites improves dispersion of the metal during synthesis and enhances the hydrothermal stability of metal species in the catalysts. In addition to external nitrogen sources, natural nitrogenous biomasses have been used. Xiao et al.127 selected chitosan as carbon and nitrogen source for synthesis of N-doped carbon materials that was used to promote transformation of cellulose to hexitols with yields of 95% for conversions of nearly 100%.
Besides dispersion and stabilization of metal particles, carbon supports play an important role in catalytic reactions as carriers for electron transfer. Carbon materials with electrical conductivity can effectively transfer electrons, modulate the energy levels of adsorbed states and reaction intermediates on the catalyst surface and facilitate reaction progress.30,238 Extensive investigations have confirmed that ruthenium carbon catalysts promote hydrogenation of cellulose to sorbitol and show high activity and yields due to hydrogen spillover and electron transfer effects caused by the unique surface contact between ruthenium nanoparticles and carbon-based supports.61,109,239 Carbon can absorb more hydrogen from Ru spillover and shows excellent adsorption capacity for glucose, thus providing additional catalytic active sites over those of Ru alone.102 The carbon-based ruthenium materials such as Ru/AC,103 Ru/CNT104 and Ru/AG-CNT106 are efficient catalysts for achieving one-pot conversion of cellulose to sorbitol, possibly due to the abundance of functional groups on the surface and strong Ru–C interactions as compared with other common supports (Fig. 16).235
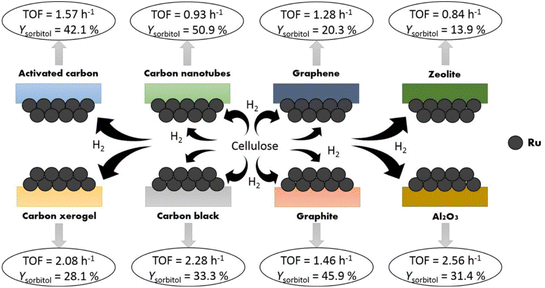 |
| Fig. 16 Catalytic effect of Ru materials on carbon supports for hydrolysis and hydrogenation of cellulose to sorbitol in one-pot. Reaction condition: ball-mixed cellulose, 478 K, 5 MPa H2 partial pressure, 5 h reaction time.235 Reproduced from ref. 235 with permission from Elsevier, copyright 2017. | |
Liu et al.198 prepared ruthenium nanoparticles dispersed in mesoporous carbon microfibers that had good hydrogenation activity via chemical vapor deposition (CVD) using alumina microfibers as template. Rey-Raap and Ribeiro106 prepared two different supports by hydrothermal carbonization (HTC): (i) glucose-based materials and (ii) glucose/carbon nanotube mixtures. Complete conversion of cellulose was achieved in 3 h reaction time at 205 °C and 5 MPa hydrogen partial pressure using Ru/AG-CNT1200 (specific surface area 1200 m2 g−1) hybrid catalyst with a maximum sorbitol yield of 64.1%, and four cyclic uses that showed good catalyst stability. The catalysts of glucose-CNT hybrid support were chemically stabilized with rich functional groups and the sorbitol yield increased from 50% to more than 60% compared to the catalysts of glucose-derived carbon (AG) or CNT as support alone. The high specific surface area and porosity of the synthetic carbon materials facilitated dispersion of the supported metal nanoparticles.173 Carbons have weakly acidic functional groups and the adjacent carboxyl and phenol groups can have a synergistic effect on hydrolysis reactions.240 Graphene oxide flakes provide good support and stabilization for dispersed platinum nanoparticles, preventing their aggregation and allowing recoverability to afford sorbitol yields of 58.9%.197
3.3 Interactions between metal and acid sites
By precisely controlling and modifying active sites, multifunctional catalysts can be synthesized to combine hydrolysis and hydrogenation functions required for direct conversion of cellulose to sorbitol, as well as dehydration functions required for conversion of sorbitol to isosorbide. Each active site of the catalyst has its own role, but also interacts with reactants and intermediates according to their proximity with substrates for eliminating separation steps and increasing catalytic efficiency.241
It is known that hydrolysis and dehydration reactions occur at acidic sites. On the other hand, basic sites promote opening of the glucose chain and make it easier to isomerize or convert intermediates into by-products.50 Precise control of the acid–base properties of a catalyst ensures that the reaction tends toward hydrolysis and hydrogenation, rather than retro-aldol condensation and isomerization. The intensity and distribution of acidic groups on the catalyst surface strongly affect sorbitol selectivity. Acidic sites directly affect the efficiency of cellulose hydrolysis to sugars, which further affect the yield of hydrogenation to sorbitol.
Functional groups can be introduced onto a support such as carbon nanotubes (CNTs) with nitric acid that is followed by vapor phase heat treatment to incorporate oxidation groups on the CNT surface. Modified CNT supported Ru catalyst with oxygenated groups on the surface have been found to promote cellulose conversion, but to lower sorbitol selectivities.242 Zhang et al.204 synthesized a series of nickel-loaded hierarchical carbon materials using a dual-template method, and used them as bifunctional catalysts to facilitate the conversion of cellulose to sorbitol, but of the polyols with a maximum yield of 45%, only 20% were hexitols.
One of the chief challenges in conversion schemes for cellulose to sorbitol is improving the accessibility of cellulose molecules to H+. Both the pore size distribution and specific surface area of a catalyst affects contact between the substrate and acidic sites. Table 6 shows some representative materials, where it can be seen that an appropriate increase in total acidity facilitates cellulose hydrolysis, while insufficient acidity in Lewis acid sites increases the concentration of the enol forms of glucose and results in isomerization of glucose to fructose, producing mannitol and by-products.50 However, excessive acidity can lead to further dehydration and cleavage of sorbitol to short-chain alcohols and lowering of hexitol selectivity.243,244 Preparation of metal/acid bifunctional catalysts generally involves studying the relationship between acid content and product yields via adjusting catalyst acid content. While many trends have been reported, detailed mechanisms of acid active sites in hydrolysis and dehydration reactions are still unclear. Furthermore, there is delicate balance between interactions of acid and hydrogenation sites of catalysts that is not well understood.
Accessibility of the substrate to acidic and hydrogenation sites of a catalyst is strongly affected by material structure. Zhang et al.245 prepared mesoporous ZSM-5-loaded Ni catalysts using untreated microcrystalline cellulose as the substrate and the Ni/NCC-ZSM5-3 catalyst gave close to 60% hexitol yields (Table 6, entry 1). Acid sites and mesoporous volume had maxima values that coincided with the trend of hexitol yields (Fig. 17). It is likely that understanding the structural features of these catalysts can be further advanced through characterization and calculation methods.
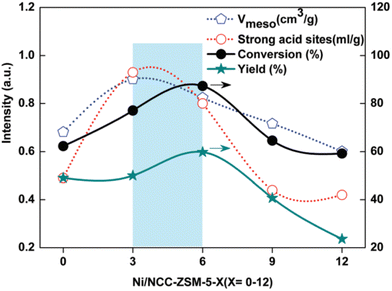 |
| Fig. 17 Relationship between structural characteristics (mesoporous and acidic sites) and catalytic performance over Ni/NCC-ZSM5-X catalysts in conversion of cellulose to sorbitol in one-pot,245 where X denotes quantities of nanocrystalline cellulose (NCC) used in catalyst preparation. Reproduced from ref. 245 with permission from The Royal Society of Chemistry, copyright 2016. | |
Acidity enhancement by grafting sulfonic acid groups onto carbon materials is effective for making catalysts that are effective for cellulose to sorbitol one-pot conversions. Carbon black supported Ru materials that are sulfonated by treatment with H2SO4 showed sorbitol selectivities of above 40%.118 In another study, one-pot conversion of cellulose with a sulfonic acid-functionalized silica-supported ruthenium catalyst (Ru/SiO2–SO3H) achieved 61.2% sorbitol yields for reaction conditions of 150 °C and 10 h reaction time.154 In that work, sulfonation was concluded to provide something more than acidity and through characterization by XPS and pyridine-adsorbed FT-IR, it was shown that interactions existed between the sulfonic acid groups and Ru nanoparticles that were responsible for the high yields of sorbitol observed. The Ruδ+ arising from the interaction between the metal and the sulfonic group could contribute to the generation of Lewis acid sites beneficial for hydrolysis. However, under conditions of high-temperature and high-pressure, the sulfonic acid group is readily lost, resulting in poor recyclability of the catalyst.246 Therefore, one key point in this method is the inhibition of sulfonic acid group leaching which requires attention in the future.161
Weakly acidic functional groups such as hydroxyl and carboxyl groups are able promote acidic breakage of glycosidic bonds and can have synergistic effects for adsorbing reactants, desorbing products and promoting mass transfer. Furthermore, weakly acidic functional groups tend to be hydrothermally stable. Komanoya et al.247 prepared a highly active and effective ordered mesoporous carbon (CMK-3) supported Ru catalyst, whose activity was attributed to favorable interactions between cellulose and carbon surfaces and to the presence of small amounts of weakly acidic groups such as carboxyl and phenolic groups (0.41 mmol g−1 in total). The carboxyl groups on the surface form hydrogen bonds with cellulose hydroxyl groups, thus increasing the probability that adjacent carboxyl groups attack the β-1,4-glycosidic bonds.
By tuning the relative number and distribution of metal and acidic sites, the rate of cellulose hydrolysis and hydrogenation can be controlled, which means that the concentration of intermediate product glucose can be regulated to maintain product selectivity, reduce the rate of side reactions such as isomerization and polymerization and to avoid deactivation of active sites by humins. Liang et al.248 prepared catalysts with different dispersions of Ni and oxygen groups on the surface by changing the reduction temperature and loading of nickel using different strong acid oxidants. A high hexitol yield (ca. 80%) was obtained when the ratio between the acidic sites (nA) and surface metal hydrogenation sites (nNi) was adjusted to be in the range of 0.7 < nA/nNi < 1.1. Van de Vyver et al.249 showed that 7.5 wt% Ni/CNF catalyst had a relatively high nickel surface atomic weight and a low density of Brønsted acid sites, which could catalyze cellulose to hexitols with a conversion of 93% and yield of 76%. Chen et al.250 designed catalysts by so-called “ship in bottle”, which effectively controlled H3PW12O40 (PTA) loading by its encapsulation in a metal–organic-framework (MOF) compound, MIL-100 (Cr), and this method allowed adjustment of the amount and strength of acid sites (Fig. 18a). They found that hexose alcohol yield was maximized when the ratio of acid sites (nA) to Ru sites (nRu) was between 8 and 13 (Fig. 18b). The ratio of acidity to metal content on the catalyst surface was proposed to allow a balance to be achieved between hydrolysis and hydrogenation reaction rates, thus they demonstrated a clear example for the role of acid sites – metal sites in a bifunctional catalyst.
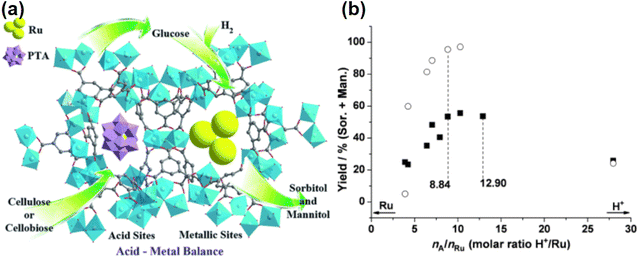 |
| Fig. 18 Encapsulation of a catalytic material in a metal organic framework MIL-100(Cr) material ("ship-in-a-bottle" method).250 (a) preparation scheme of metal-acid bifunctional catalyst Ru-PTA/MIL-100(Cr) via phosphotungstic acid (PTA) and (b) relationship between nA(H+)/nRu ratio and observed sorbitol and mannitol yields from (○) cellobiose and (■) cellulose substrates. Reproduced from ref. 250 with permission from WILEY, copyright 2013. | |
The type and number of functional groups on the surface of a support greatly affect catalyst efficiency and stability. For example, the size of ruthenium particles are positively correlated with the number of Lewis acid sites, and the conversion of cellulose to sorbitol decreases with increasing Ru particle size.122 N-doped materials significantly improve the catalytic performance due to the enhanced hydrogen adsorption capacity, increased wettability and changes in the electronic properties of ruthenium.198 The interaction between the metals and the supports can reduce the enthalpy of the transition state and thus kinetically facilitate reaction progress while improving catalytic efficiency. Fang's group62 designed a Ru impregnated MOF heterogeneous catalyst that exploited the synergistic effects of artificially implanted defects, the loaded ruthenium noble metal active component and the single active site of the pristine metal. The prepared Ru@DEMOF heterogeneous catalyst afforded simultaneous increase in activity, selectivity and cycling stability in glucose hydrogenation to sorbitol with a turnover frequency of about 10 times higher than that of other polymer-supported Ru catalysts (Fig. 19).
 |
| Fig. 19 Formation of defects (type A defect (doping with 3,5-pyridinedicarboxylate) and type B defect (doping with m-phthalate)) in metal–organic frameworks for Ru@DEMOF catalyst and corresponding catalytic mechanisms for conversion of glucose to sorbitol (L = total ligands, D = defective ligands).62 Reproduced from ref. 62 with permission from Springer Nature, copyright 2022. | |
4 Dynamic modeling and mechanism analysis
Efficient production of sorbitol can be achieved by controlling reaction conditions and adjusting reaction kinetics between glycosidic bond breakage and aldehyde hydrogenation, while preventing C–C bonds breakage, sugar isomerization, or retro-aldol condensation. Kinetic models have been developed to understand the effects of mass and heat transfer on sorbitol yield and to optimize processes for maximizing yields, while reducing energy consumption. Furthermore, machine learning can be used to predict reaction products, accelerate catalyst design and optimization, and to explore new catalysts and reaction systems.26 In the past several years, studies have analyzed the adsorption energy and hydrogen activation capacity of catalysts by density-functional theory (DFT) calculations to gain insight into the mechanisms of cellulose hydrolysis and glucose hydrogenation. With the development of microscopic and macroscopic characterization techniques, calculation methods have become powerful enough to propose insights into reaction mechanisms.
4.1 DFT simulations
Understanding the adsorption and binding of biomass-derived molecules on catalytic surfaces is essential for predicting and interpreting site activity and preferred reaction pathways. The adsorption of cellulose or its derived sugars on heterogeneous catalysts is the first and dominant step in their conversion into platform chemicals. Regarding cellulose hydrolysis, sufficient interaction between the solid acid and cellulose is required and pretreatment as well as adsorption of the catalyst can reduce energy barriers of transition states. Early studies have explored detailed mechanistic steps using density functional theory and transition state calculations to model the sequential solubilization of oligosaccharide intermediates and simulate reaction mechanisms involving protonation, conformational changes, glycosidic link breakage, and solvent effects.251,252
For sustainable hydrogenation of glucose formed from cellulose hydrolysis, comparison between the rate of hydrogen dissociation and substrate adsorption plays a decisive role. The aldehyde group of the aldose conformation can be adsorbed on the metal surface via the oxygen lone pair η1(O) or the carbonyl group η2(C
O), and the η1(O) configuration is beneficial to hydrogenation of glucose while η2(C
O) configuration promotes isomerization.41
With the continuous improvement of computing power and theoretical methods, the use of DFT calculations to describe hydrolysis–hydrogenation reactions has been improved. The modified Perdew–Burke–Enzerhof (PBE) function (Fig. 20) can be used to correctly predict the stable adsorption conformation of aldehydes on transition metals as η1(O).42 It is hypothesized that the metal-catalyzed deprotonation and the ring-opening process of glucose adsorbed in cyclic forms produce the open-chain conformation, thus explaining why there are more η1(O) conformations in the experiments.
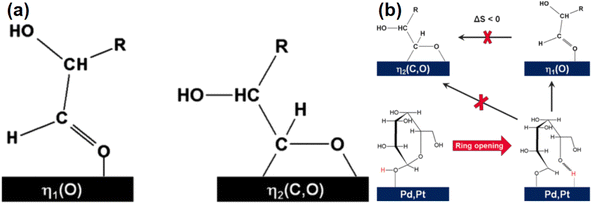 |
| Fig. 20 Modified Perdew–Burke–Enzerhof (PBE) function predictions: (a) two adsorption structures of glucose on transition metal surfaces and (b) possible transformations between η1(O) and η2(C,O) structures (right).42 Reproduced from ref. 42 with permission from American Chemical Society, copyright 2015. | |
DFT calculations combined with kinetic tests can explain the differences in activity between catalysts. Guo et al.24,253 used DFT simulations to theoretically explain the activity observed for catalysts. The adsorption dissociation energy of H2 was calculated using optimized Ni4 and Ni13 nickel clusters, demonstrating that Pt doping reduced the activation potential of H2 by 0.8 kcal mol−1 for Pt-capped Ni4 clusters compared with pure Ni4 clusters in accordance with experimentally observed high hexitol yields.253 The same group24 investigated the reason for the higher sorbitol yield by nickel loaded onto SiC supports and determined hydrogen activation capacity on different catalysts by DFT simulation.24 The H2 dissociation on Ni4/SiC (111) plates (−26.9 kcal mol−1) was found to have lower energy than that on Al2O3(100) plates (−34.1 kcal mol−1) and the graphene plate (−32.5 kcal mol−1, the local structure of the support CNT). The lower energy potential and H2 activation energy of the SiC-loaded nickel catalysts are consistent with the corresponding high hexitol yields. These simulations allow discussion of the hydrogenation effect of specific supports and dopant atoms. Liu et al.177 revealed the structure of the active center of (Ni–N4)⋯N by DFT calculations and K-edge X-ray absorption spectroscopy (Fig. 21). Significantly distorted octahedral ligands and pyridine nitrogen constituted a frustrated Lewis pair (FLP) for the heterogeneous dissociation of H2 molecules. The stability of the highly loaded Ni–N–C SAC catalyst was explained by strong covalent chemical bonds between nickel and nitrogen atoms.
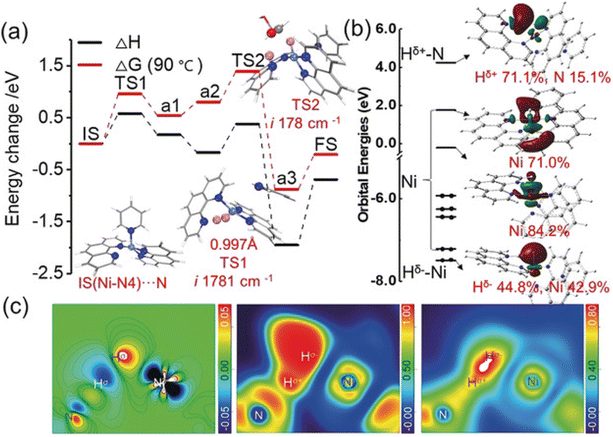 |
| Fig. 21 The DFT calculation of Ni–N–C single-atom catalyst and the proposed heterolytic dissociation manner of H2. (a) The proposed H2 activation and glycolaldehyde hydrogenation energy change profile on Ni–N–C-600 catalyst. (b) Localized molecular orbitals (LMOs) and localized orbital bonding analysis (LOBA) showing oxidation states of each split H atoms and Ni center. (c) Maps of electron density differences, electron localization function (ELF), and localized orbital locator (LOL) of transition state 1 (TS1).177 Reproduced from ref. 177 with permission from WILEY, copyright 2018. | |
Theoretical calculations can guide the design of catalysts.254 Advances in simulation and characterization have made it possible to gain insight into reaction mechanisms. With further multidisciplinary integration, the predictive interpretation of catalyst models will be possible.
4.2 Reaction kinetics
The kinetics of hydrogenation of sugars by different heterogeneous catalysts have been studied in early works,47 whereas analysis of kinetic data show first-order kinetics relative to glucose concentration.52,62,193 The calculated Ea values of different catalysts can provide a theoretical basis for comparing favored reaction pathways between catalysts.66
With the development of research on the conversion of cellulose feedstocks, oligosaccharides such as cellobiose are used as models to explore the hydrolysis mechanism of cellulose.255,256 There are two reaction pathways for conversion of cellobiose to sorbitol (Fig. 20): (i) cellobiose is hydrolyzed to glucose and then hydrogenated to sorbitol and (ii) cellobiose begins to be hydrogenated to cellobitol (sorbitol 3-β-D-glucopyranosyl-D-glucitol) and then hydrolyzed to one molecule of sorbitol and one molecule of glucose, which is further hydrogenated to sorbitol.255 In contrast to postulated hydrolysis followed by hydrogenation type of pathways, simultaneous hydrolysis and hydrogenation has higher kinetic selectivity, especially because the second pathway is preferred at lower reaction temperatures.109,112,219
Based on kinetic analyses, mathematical models have been proposed to explore reaction pathways and kinetic parameters of one-pot conversions of cellulose to sorbitol and to predict product yields. Kobayashi et al.188 used Pt(N)/BP2000 as catalyst to study the kinetics, wherein glucose was hydrogenated via the Langmuir–Hinshelwood mechanism and adsorption of glucose and dissociative H2 played key roles. With sufficiently low glucose concentration and excess H2 availability, the kinetic equation was found to be first-order with a rate constant of 2.8 h−1.188 Negahdar et al.255 explored the mechanism of hydrolytic hydrogenation from cellobiose to sorbitol using Ru/C catalyst and found that cellobitol could be produced in selectivities of up to 81%.
Selective conversion of cellobiose to sorbitol seems to occur via formation of a cellobitol intermediate (Fig. 22).256,257
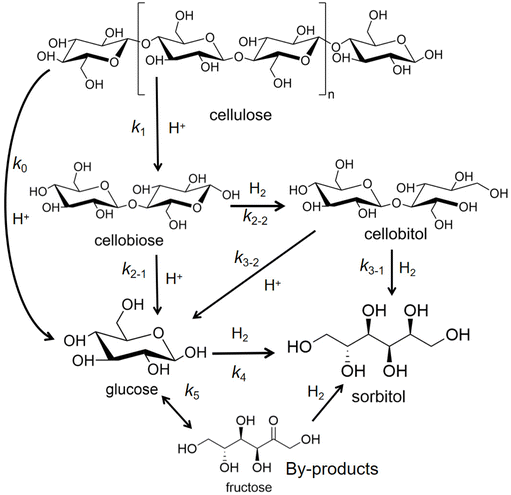 |
| Fig. 22 Hypothetical reaction pathways for cellulose hydrolysis and hydrogenation into sorbitol for kinetic study.94 Reproduced from ref. 94 with permission from WILEY, copyright 2014. | |
Study of reaction kinetics allows one to explore catalytic mechanisms and to estimate product yields. Gromov et al.120 developed a mathematical model to describe the yield of hexitol over Ru/Cs-HPA catalyst (Fig. 23). It can be seen that the developed kinetic model described the experimental data well for cellulose conversion and sorbitol yield in which the maximum sorbitol yield was estimated to be about 59%. The kinetic model focuses on the rate and mechanism of chemical reactions, providing information on reaction kinetics such as activation energy and reaction rate.258 In the context of biological refining, kinetic models can assist in predicting inputs, outputs, and by-products.259
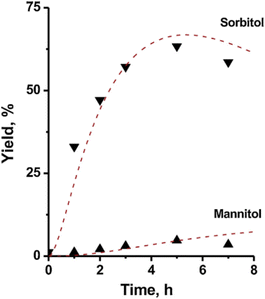 |
| Fig. 23 Experimental data (symbols) and theoretical calculations (dashed-line) for hydrolysis–hydrogenation of mechanically activated cellulose over 1% Ru/Cs-SiW in water,120 with assumption of first-order kinetics and negligible mass transfer limitations. Conditions: 10 g L−1 of cellulose, 10 g L−1 of catalyst, 5 MPa of H2, partial pressure at reaction temperature of 453 K. Reproduced from ref. 120 with permission from Elsevier, copyright 2020. | |
4.3 Machine learning
Interdisciplinary research with machine learning (ML) techniques on biomass molecules and reaction networks have constructed models for complex chemical systems that allow mechanisms and reactions to be predicted in depth.260 In the field of lignocellulosic biomass (LCB) biorefinery, the ML algorithm has many uses. There is an increasing use of supply chain261 and life cycle assessment (LCA).262 Machine learning also allows for the prediction of conversion and desired yields for pretreatment263 and biomass conversion processes.264 In addition, ML can also predict the properties and reactions of biomass molecules.265 Chang et al.265 used vector descriptions of Mol2Vec and LDA combinations as inputs to regression models to predict reaction energies with mean absolute errors as low as 0.59 eV. Consistent with chemical intuition, ML supports the use of model compounds to explore the complex reaction mechanism. The Euclidean distance between vectors can be used to evaluate the similarity between different biomass compounds.265 For example, the reaction of converting linear glucose to sorbitol was explored by using similarity between glyceraldehyde and glycerol, and provided support for exploring the homogeneous complex reaction mechanism with model compounds. However, ML-assisted prediction is still in its infancy and lacks explanatory power, and it needs to be improved in the future.26
5 Sorbitol applications
Sorbitol is used in the synthesis of isosorbide, 1,4-sorbitol, glycol, glycerol, lactic acid, vitamin C and many other chemicals. In this section, typical reactions such as dehydration, hydrolysis, oxidation (enol) and selective reduction are chosen to illustrate the preparation of chemical products from sorbitol by chemo-catalytic methods.
Isosorbide is an important downstream product, which is considered to be an important future bio-based chemical next to polylactic acid (PLA), and is widely used in food, cosmetics, plastics and pharmaceuticals.19 As shown in Fig. 24, isosorbide is usually obtained by double dehydration of sorbitol.19
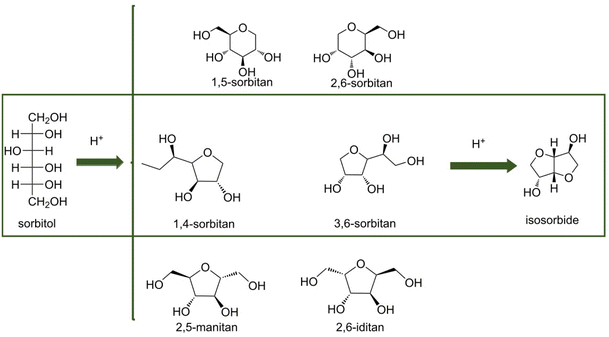 |
| Fig. 24 Reaction pathways of sorbitol dehydration to isosorbide.266 Reproduced from ref. 266 with permission from BEILSTEIN-INSTITUT, copyright 2020. | |
Homogeneous acids can be used to for the initial sorbitol dehydration.158,267 Using concentrated sulfuric acid commonly used in industry as a catalyst, yield of isosorbide can reach 70% to 80%. Hydrothermally stable solid acids with high surface area and strong acidity are drawing attention for sorbitol dehydration step to avoid equipment corrosion, solution recycle and product separation.158,266 Solid acids such as acid resins, zeolites, metal phosphides/oxides, and phosphotungstic acid PW-loaded catalysts, can be used for sorbitol dehydration to obtain more than 60% isosorbide yield.266 In addition, highly polar ionic liquid solvents are suitable for dissolving hydrophilic polyols like sorbitol. ZnCl2 molten salt hydrate effectively dissolves sorbitol or cellulose and transforms it into isosorbide.151 Kamimura et al.268 explored the dehydration of sorbitol in hydrophobic ionic liquids [TMPA][NTf2] in the presence of PTSA under microwave irradiation, and reported isosorbide yields of up to 60% at reaction conditions of 180 °C (Fig. 25). On account of isosorbide being soluble in water, the hydrophobic ionic liquid can be recovered and reused by dichloromethane extraction (2.5 g of ionic liquid in 100 ml dichloromethane).
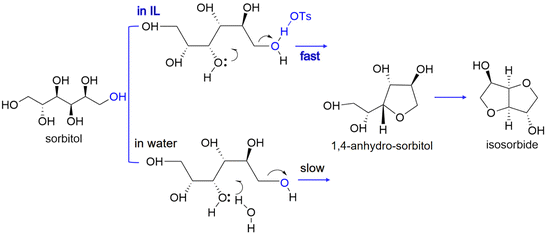 |
| Fig. 25 Mechanism of sorbitol dehydration in ionic liquids and aqueous systems.268 Reproduced from ref. 268 with permission from WILEY, copyright 2014. | |
Similar to one-pot production of sorbitol, the direct production of isosorbide from cellulose has been extensively studied for establishing a consecutive catalytic system of hydrolysis–hydrogenation-dehydration. Efficient one-pot conversion of cellulose to isosorbide can be achieved by using hydrogenation catalysts in homogeneous acid159 or ionic liquid systems,151 or by combination with solid acid catalysts. Therefore, heterogeneous catalysts with strong acidic sites still need to be developed.269 Sun et al.270 synthesized Ru catalyst supported on mesoporous niobium phosphate catalyst (Ru@mNbPO) to directly convert microcrystalline cellulose into isosorbide using only water as reaction medium and achieved nearly 100% cellulose conversion and 50% isosorbide yields in 1 h reaction time with the catalyst being demonstrated for recycle. Keskiväli et al.158 used sulphonated and oxidized Ru/C catalysts to produce isosorbide in 57% yields from cellulose substrates through two-step heating (i.e. step 1: reaction at 170 °C and 2 MPa partial pressure H2 for 2 h; step 2: reaction at 200 °C and 4 MPa partial pressure H2 for 6 h). The synthesis of isosorbide from sorbitol or even cellulose, however, remains as a technical challenge, because there are a large number of competing reactions that require precise control for obtaining product selectivity and avoiding side reactions such as degradation or polymerization.266,271 In the future, catalytic dehydration of sorbitol by solid acids in molten or solvent states is likely to have many opportunities. For example, fluidized beds have made it possible for industry to develop continuous processes for converting cellulose into sorbitol and into isosorbide.211
Sorbitol can be hydrocracked to prepare ethylene glycol, propylene glycol and other alcohols. Transition metal catalysts for the hydrogenation of sugars, such as copper and tungsten,272 will further hydrogenate sugar alcohols to give products such as glycerol, ethylene glycol and propylene glycol. The mechanism of sorbitol hydrocracking is that the hydroxyl group on the sorbitol molecule is dehydrogenated in the metal active part of the catalyst, then the anti-hydroxyl aldol condensation reaction is carried out in the presence of a basic center to break the C–C, and finally the hydrogenation reaction occurs in the metal active part to produce small molecules of polyol. The whole process requires synergistic catalysis of the metal active component and the basic center, so it is especially important to adjust the basicity of the catalysts. Currently, most of the active centers used in catalysts for sorbitol hydrocracking are nickel-based or ruthenium-based with supports La(OH)3, Al2O3, MgO and other oxides being used to obtain certain alkalinity or acid–base amphiphilicity.273 Clark et al.81 used nickel supported on diatomite to catalyze the hydrogenolysis of sorbitol and added Ca(OH)2 as an alkaline cofactor to obtain ethylene glycol, 1,2-propanediol and glycerol yields of 16%, 17% and 40%, respectively. Leo et al.274 investigated the preparation of ethylene glycol from the catalytic hydrolysis of sorbitol by Ru loaded onto different supports and found that Al2O3 as a support had the highest selectivity and ethylene glycol yield.
Sorbitol can also be converted to liquid alkanes (mainly C5–C6) by aqueous phase reforming (APR) to replace fossil fuels.275,276 The longer chain alkanes derived from sorbitol can be used directly as a substitute for petroleum, overcoming the limitations of bioethanol and methanol that are now considered as the second generation biofuels. Bifunctional catalysts containing metal sites (Pt, Pd, Ni, Ru and Ir) for hydrogenation and acid sites (Al2O3, ZrO2, Nb2O5, WOx, HZSM-5) for dehydration are preferred for the formation of hydrocarbons by catalytic hydrodeoxygenation (HDO). Some synthetic catalysts was developed, such as Ni/HZSM-5,277 Pt/Al2O3,278,279 Ru-MoO3−x/C,280 have showed good activity with C5–C6 alkane yields being higher than 80% in a continuous flow reactor.281 The products produced by HDO depend on the relative rates of C–C and C
O bond breakage.278
6 Summary and outlook
Catalytic production and sorbitol applications have been reviewed and strategies for constructing highly active and low-cost catalytic systems for efficient transformation of biomass resources have been analyzed. With process development, production feedstock has been gradually broadened from highly water-soluble glucose to cellulose and raw biomass materials. The difficulty of contacting heterogeneous catalysts with cellulose limits reaction rates and remains as one of the chief challenges in design of catalytic systems to convert cellulose into sorbitol. A great deal of research has been devoted to breaking down the barrier between cellulose and catalyst with the use of green and effective pretreatment methods instead of mineral acids. To achieve one-pot conversion of cellulose into sorbitol, development of many types of effective heterogeneous catalytic systems is needed.
Conformational relationships and active site functions of the heterogeneous catalysts prepared from sorbitol have been summarized. Adjustment of hydrolytic hydrogenation active sites in-depth analysis of reaction mechanisms is necessary for design of catalytic systems that still lack selectivity and necessary efficiency.
For catalytic reactions, it is important to identify descriptors for catalyst activity and to clarify activity trends of catalysts in terms of structure–reactivity relationships that can be related to theoretical calculations. Most research articles display the effectiveness of catalysts in terms of conversion and yields, however, the effectiveness of catalysts among research groups is difficult to compare due to differences in many reaction conditions. Therefore, turnover frequency (TOF) should be considered to express catalyst activity for reactions of interest as well as a set of standardized reactions and conditions could help to identify favorable catalytic systems.282 We believe that research papers should include universal TOF data for comparison. In addition, intrinsic reaction rate constants are some of the most meaningful parameters for comparing different catalytic systems and can better describe the design of catalysts for achieving high TOF, long life and low cost. In recent years, high-throughput (HT) experiments have been used for catalyst screening and for combining design of experiments (DoE) to synthesize, characterize and test new catalysts. In this way, the use of these techniques can significantly reduce time lag, energy and financial constraints of screening catalysts that can be effective for industrial applications and provide an inter-industry intermediaries for sustainable processes in biomass catalysis.184
The simultaneous improvement of catalyst activity and stability has been a technical challenge for proposed cellulose to sorbitol conversion schemes. Metals are often used as active sites for hydrogenation reaction in which noble metal Ru and transition metal Ni have been shown to be effective for hydrogenation of sugars to sorbitol. In view of the characteristics of different metals, many scholars have explored schemes that require fewer additives and achieve better metal dispersion and have longer service life to make up for the high cost of noble metal catalysts. The interactions between support and active components as well as bimetallic synergy have been explored to prevent the sintering and leaching of nickel.54 To achieve production of sorbitol by tandem hydrolysis and hydrogenation in one-pot, multifunctional catalysts with acid sites and hydrogenation sites have to be further developed and explored. In the future, development of innovative synthesis methods that allow simple adjustment of the type and distribution of active sites and precise control of the size and position of metal particles or single atoms on the support is needed.
Design of catalysts based on biological enzymes to achieve molecular recognition and regulation may provide new ideas and theoretical support for synthesis of multifunctional catalysts. To extend the life of catalysts, supports can be introduced that inhibit metal migration and formation of metallic element clusters. The composite use of multiple metals is another strategy to enhance the catalytic activity and reduce coking by enhancing the interaction between metals. Exploring the structure–activity relationship and summarizing the different reaction paths initiated by different active sites and interactions will provide new insight in the design and synthesis of multifunctional catalysts.
Many studies in the field of biomass thermal catalysis have focused on catalyst preparation and product distributions, whereas there is an urgent need to understand fundamental catalytic mechanisms and with this goal in mind, the authors offer some recommendations for future study:
(1) Development of advanced characterization methods: for example, in situ analyses that can detect changes in structure and composition of catalyst surface functional groups under actual reaction conditions as well as presence and transformation of reaction intermediates. Advanced characterization methods must be accompanied by theoretical support for mechanism exploration
(2) Modeling and DFT calculations: molecular characterization by means of machine learning has become very popular. However, most of the target molecules for biomass conversion are compounds with relatively high carbon numbers, so there are few studies on glucose and sorbitol models. Kinetic models and DFT calculations for sorbitol production reaction pathways need to be firmly established by using cutting-edge algorithms. Interpretability of models still needs to be explored and the prediction of catalyst efficiency by simulation is expected to be achieved in the near future.
Although direct conversion of cellulose to sorbitol has been studied in the laboratory, more efforts are needed to transfer laboratory concepts into scalable processes keeping in mind present industrial production needs. Current industrial production of sorbitol still mainly relies on hydrolysis of starch into glucose following with hydrogenation. Continuous flow reactor systems are suitable for large-scale production of hexitols from cellulose, which have advantages of high energy efficiency, safety and ease of process controlling, but reaction systems with cellulose face issues with cellulose solubility and product separation and refinement. There is still a long way to bridge the gap between direct conversion of cellulose into sorbitol and practical applications. Scholars have been working to develop green and effective pretreatment methods to improve the contact between catalyst and cellulose to increase reaction efficiency or to explore hydrogen transfer effects to reduce the use of high-pressure hydrogen. Practicality and feasibility of new catalytic systems for conversion of lignocellulosic biomass to sorbitol will have to show clear advantages in safety, health, environmental, sustainability and cost issues over conventional methods for acceptance by future society.
Conflicts of interest
There are no conflicts to declare.
Acknowledgements
This work was financially supported by the National Natural Science Foundation of China (No. 22178181 and 21876091), the Natural Science Fund of Tianjin (No. 21JCZDJC00180) and the Fundamental Research Funds for the Central Universities (Nankai University (No. 63231085)).
References
- Y. Nakagawa, M. Yabushita and K. Tomishige, A perspective on catalytic production of olefinic compounds from biomass, RSC Sustainability, 2023, 1(4), 814–837 RSC.
- R. Mori, Replacing all petroleum-based chemical products with natural biomass-based chemical products: a tutorial review, RSC Sustainability, 2023, 1(2), 179–212 RSC.
- P. Zhou, Y. Lv and W. Wen, The Low-Carbon Transition of Energy Systems: A Bibliometric Review from an Engineering Management Perspective, Engineering, 2023 DOI:10.1016/j.eng.2022.11.010.
- A. I. Osman, L. Chen, M. Yang, G. Msigwa, M. Farghali, S. Fawzy, D. W. Rooney and P.-S. Yap, Cost, environmental impact, and resilience of renewable energy under a changing climate: a review, Environ. Chem. Lett., 2023, 21(2), 741–764 CrossRef CAS.
- R. Zou, M. Qian, C. Wang, W. Mateo, Y. Wang, L. Dai, X. Lin, Y. Zhao, E. Huo, L. Wang, X. Zhang, X. Kong, R. Ruan and H. Lei, Biochar: From by-products of agro-industrial lignocellulosic waste to tailored carbon-based catalysts for biomass thermochemical conversions, Chem. Eng. J., 2022, 441, 135972 CrossRef CAS.
- Z. Zhou, D. Liu and X. Zhao, Conversion of lignocellulose to biofuels and chemicals via sugar platform: An updated review on chemistry and mechanisms of acid hydrolysis of lignocellulose, Renewable Sustainable Energy Rev., 2021, 146, 111169 CrossRef CAS.
- H. C. Erythropel, J. B. Zimmerman, T. M. de Winter, L. Petitjean, F. Melnikov, C. H. Lam, A. W. Lounsbury, K. E. Mellor, N. Z. Janković, Q. Tu, L. N. Pincus, M. M. Falinski, W. Shi, P. Coish, D. L. Plata and P. T. Anastas, The Green ChemisTREE: 20 years after taking root with the 12 principles, Green Chem., 2018, 20(9), 1929–1961 RSC.
- J. G. Segovia-Hernández, G. Contreras-Zarazúa and C. Ramírez-Márquez, Sustainable design of water–energy–food nexus: a literature review, RSC Sustainability, 2023, 1(6), 1332–1353 RSC.
- M. Zeng and X. Pan, Insights into solid acid catalysts for efficient cellulose hydrolysis to glucose: progress, challenges, and future opportunities, Catal. Rev., 2020,(1), 1–46 CAS.
- Ö. Tezer, N. Karabağ, A. Öngen, C.Ö Çolpan and A. Ayol, Biomass gasification for sustainable energy production: A review, Int. J. Hydrogen Energy, 2022, 47(34), 15419–15433 CrossRef.
- C. Zhang, L. Chao, Z. Zhang, L. Zhang, Q. Li, H. Fan, S. Zhang, Q. Liu, Y. Qiao, Y. Tian, Y. Wang and X. Hu, Pyrolysis of cellulose: Evolution of functionalities and structure of bio-char versus temperature, Renewable Sustainable Energy Rev., 2021, 135, 110416 CrossRef CAS.
- Y. Wu, H. Wang, H. Li, X. Han, M. Zhang, Y. Sun, X. Fan, R. Tu, Y. Zeng and C. C. Xu, Applications of catalysts in thermochemical conversion of biomass (pyrolysis, hydrothermal liquefaction and gasification): A critical review, Renewable Energy, 2022, 196, 462–481 CrossRef CAS.
-
S. Wang and Z. Luo, Pyrolysis of biomass, in Pyrolysis of Biomass, De Gruyter, 2016 Search PubMed.
- S. Wang, A. Cheng, F. Liu, J. Zhang, T. Xia, X. Zeng, W. Fan and Y. Zhang, Catalytic conversion network for lignocellulosic biomass valorization: a panoramic view, Ind. Chem. Mater., 2023, 1(2), 188–206 RSC.
- J. J. Bozell and G. R. Petersen, Technology development for the production of biobased products
from biorefinery carbohydrates—the US Department of Energy's “Top 10” revisited, Green Chem., 2010, 12(4), 539–554 RSC.
- J. Xiang, S. Yang, J. Zhang, J. Wu, Y. Shao, Z. Wang and M. Yang, The preparation of sorbitol and its application in polyurethane: a review, Polym. Bull., 2021, 1–18 Search PubMed.
- A. M. Erian and M. Sauer, Utilizing yeasts for the conversion of renewable feedstocks to sugar alcohols - a review, Bioresour. Technol., 2022, 346, 126296 CrossRef CAS.
- S. M. Lim, M. S. L. Lau, E. I. J. Tiong, M. M. Goon, R. J. C. Lau, W. S. Yeo, S. Y. Lau and N. M. Mubarak, Process design and economic studies of two-step fermentation for production of ascorbic acid, SN Appl. Sci., 2020, 2(5), 816 CrossRef CAS.
- C. Dussenne, T. Delaunay, V. Wiatz, H. Wyart, I. Suisse and M. Sauthier, Synthesis of isosorbide: an overview of challenging reactions, Green Chem., 2017, 19(22), 5332–5344 RSC.
- Y. Jia, Q. Sun and H. Liu, Selective hydrogenolysis of biomass-derived sorbitol to propylene glycol and ethylene glycol on in-situ formed PdZn alloy catalysts, Appl. Catal., A, 2020, 603, 117770 CrossRef CAS.
- N. Annuar, Z. Alexzman, A. Daud, A. Alias, H. Hairi and H. Setiabudi, A review on hydrogenolysis of sorbitol over heterogeneous catalysts, J. Environ. Chem. Eng., 2022, 107229 CrossRef CAS.
- Y. Weng, S. Qiu, L. Ma, Q. Liu, M. Ding, Q. Zhang, Q. Zhang and T. Wang, Jet-Fuel Range Hydrocarbons from Biomass-Derived Sorbitol over Ni-HZSM-5/SBA-15 Catalyst, Catalysts, 2015, 5(4), 2147–2160 CrossRef CAS.
- X. Zhang, B. Yang, B. Fan, H. Sun and H. Zhang, Enhanced Nonisothermal Crystallization and Heat Resistance of Poly(l-lactic acid) by d-Sorbitol as a Homogeneous Nucleating Agent, ACS Macro Lett., 2021, 10(1), 154–160 CrossRef CAS PubMed.
- Z. Guo, S. H. Lim, W. Chu, Y. Liu and A. Borgna, Highly Efficient SiC-Supported Ni-Based Catalysts with Enhanced Recycle Stability for One-Pot Cellobiose Hydrolytic Hydrogenation to Hexitols, ACS Sustainable Chem. Eng., 2020, 8(29), 10747–10755 CAS.
- S. Yamaguchi, S. Fujita, K. Nakajima, S. Yamazoe, J. Yamasaki, T. Mizugaki and T. Mitsudome, Air-stable and reusable nickel phosphide nanoparticle catalyst for the highly selective hydrogenation of d-glucose to d-sorbitol, Green Chem., 2021, 23(5), 2010–2016 RSC.
- A. Velidandi, P. Gandam, L. Chinta, M. Konakanchi, S. Bhavanam, A. Baadhe, R. Sharma, M. Gaffey, J. Nguyen and Q. D. Gupta, State-of-the-art and future directions of machine learning for biomass characterization and for sustainable biorefinery, J. Energy Chem., 2023, 81, 42–63 CrossRef CAS.
- Y. Liao, S.-F. Koelewijn, G. Van den Bossche, J. Van Aelst, S. Van den Bosch, T. Renders, K. Navare, T. Nicolaï, K. Van Aelst and M. Maesen, A sustainable wood biorefinery for low–carbon footprint chemicals production, Science, 2020, 367(6484), 1385–1390 CrossRef CAS.
- J. Zhang, J.-B. Li, S.-B. Wu and Y. Liu, Advances in the Catalytic Production and Utilization of Sorbitol, Ind. Eng. Chem. Res., 2013, 52(34), 11799–11815 CrossRef CAS.
- A. Shrotri, H. Kobayashi and A. Fukuoka, Cellulose Depolymerization over Heterogeneous Catalysts, Acc. Chem. Res., 2018, 51(3), 761–768 CrossRef CAS.
- L. S. Ribeiro, J. J. M. Órfão and M. F. R. Pereira, An overview of the hydrolytic hydrogenation of lignocellulosic biomass using carbon-supported metal catalysts, Mater.
Today Sustain., 2021, 11–12, 100058 CrossRef.
- R. Jonas and M. M. Silveira, Sorbitol can be produced not only chemically but also biotechnologically, Appl. Biochem. Biotechnol., 2004, 118(1), 321–336 CrossRef CAS PubMed.
- A. Inan, A. B. Sünbül, M. Caylar, S. Uruş, Z. Orhan, M. Köse and E. Ispir, Highly effective aldose reductase mimetics: Catalytic transfer hydrogenation of D-Glucose to D-Sorbitol with novel azo-azomethine based Ru(II) complexes, J. Mol. Struct., 2023, 1277, 134844 CrossRef CAS.
- J. Creus, M. Miola and P. P. Pescarmona, Unravelling and overcoming the challenges of the electrocatalytic reduction of fructose to sorbitol, Green Chem., 2023, 25, 1658 RSC.
-
J. R. Ochoa-Gómez and T. Roncal, Production of Sorbitol from Biomass, in Production of Platform Chemicals from Sustainable Resources, ed. Z. Fang, J. R. L. Smith and X. Qi, Springer Singapore, Singapore, 2017, pp. 265–309 Search PubMed.
- J. Lee, S. Jung, Y. T. Kim, H. J. Kim and K.-H. Kim, Catalytic and electrocatalytic conversion of glucose into value-added chemicals, Renewable Sustainable Energy Rev., 2023, 181, 113337 CrossRef CAS.
- G. Mafra, R. Brognoli, E. Carasek, Á.I López-Lorente, R. Luque, R. Lucena and S. Cárdenas, Photocatalytic Cellulose-Paper: Deepening in the Sustainable and Synergic Combination of Sorption and Photodegradation, ACS Omega, 2021, 6(14), 9577–9586 CrossRef CAS PubMed.
- H. Li, Z. Fang, R. L. Smith and S. Yang, Efficient valorization of biomass to biofuels with bifunctional solid catalytic materials, Prog. Energy Combust. Sci., 2016, 55, 98–194 CrossRef.
- W. Deng, Y. Feng, J. Fu, H. Guo, Y. Guo, B. Han, Z. Jiang, L. Kong, C. Li, H. Liu, P. T. T. Nguyen, P. Ren, F. Wang, S. Wang, Y. Wang, Y. Wang, S. S. Wong, K. Yan, N. Yan, X. Yang, Y. Zhang, Z. Zhang, X. Zeng and H. Zhou, Catalytic conversion of lignocellulosic biomass into chemicals and fuels, Green Energy Environ., 2023, 8(1), 10–114 CrossRef CAS.
- E. Redina, O. Tkachenko and T. Salmi, Recent Advances in C5 and C6 Sugar Alcohol Synthesis by Hydrogenation of Monosaccharides and Cellulose Hydrolytic Hydrogenation over Non-Noble Metal Catalysts, Molecules, 2022, 27(4), 1353 CrossRef CAS PubMed.
- X. Qian, Free Energy Surface for Brønsted Acid-Catalyzed Glucose Ring-Opening in Aqueous Solution, J. Phys. Chem. B, 2013, 117(39), 11460–11465 CrossRef CAS.
- X. Zhang, L. J. Durndell, M. A. Isaacs, C. M. A. Parlett, A. F. Lee and K. Wilson, Platinum-Catalyzed Aqueous-Phase Hydrogenation of d-Glucose to d-Sorbitol, ACS Catal., 2016, 6(11), 7409–7417 CrossRef CAS.
- Q. T. Trinh, B. K. Chethana and S. H. Mushrif, Adsorption and Reactivity of Cellulosic Aldoses on Transition Metals, J. Phys. Chem. C, 2015, 119(30), 17137–17145 CrossRef CAS.
- V. N. Sapunov, M. Y. Grigoryev, E. M. Sulman, M. B. Konyaeva and V. G. Matveeva, d-Glucose Hydrogenation over Ru Nanoparticles Embedded in Mesoporous Hypercrosslinked Polystyrene, J. Phys. Chem. A, 2013, 117(20), 4073–4083 CrossRef CAS PubMed.
- J. Moreno, J. Iglesias, J. Blanco, M. Montero, G. Morales and J. A. Melero, Life-cycle sustainability of biomass-derived sorbitol: Proposing technological alternatives for improving the environmental profile of a bio-refinery platform molecule, J. Cleaner Prod., 2020, 250, 119568 CrossRef CAS.
-
J. C. Chao and D. T. Huibers, Catalytic hydrogenation of glucose to produce sorbitol, Google Patents, 1982.
- Y. Wu, H. Wang, J. Peng and M. Ding, Advances in catalytic valorization of cellulose into value-added chemicals and fuels over heterogeneous catalysts, Catal. Today, 2023, 408, 92–110 CrossRef CAS.
- M. J. Ahmed and B. H. Hameed, Hydrogenation of glucose and fructose into hexitols over heterogeneous catalysts: A review, J. Taiwan Inst. Chem. Eng., 2019, 96, 341–352 CrossRef CAS.
- Q. Dong, Y. Huang, H. Yang, J. Pei, K. Li, M. Yuan, W. Xiao, W. Ni and Z. Hou, The Catalytic Hydrogenation of Biomass Platform Molecules by Ni–Co Nanoalloy Catalysts, Top. Catal., 2017, 60(9), 666–676 CrossRef CAS.
- L. Qin, S. Lee, K. Kim and O. Li, Selective hydrogenation of reducing sugars over SiO2@Ni/NiO hetero-structured nanoreactor in Mg-driven aqueous phase, Appl. Surf. Sci., 2022, 587, 152849 CrossRef CAS.
- A. Tathod, T. Kane, E. S. Sanil and P. L. Dhepe, Solid base supported metal catalysts for the oxidation and hydrogenation of sugars, J. Mol. Catal. A: Chem., 2014, 388–389, 90–99 CrossRef CAS.
- B. Hoffer, E. Crezee, P. Mooijman, A. Van Langeveld, F. Kapteijn and J. Moulijn, Carbon supported Ru catalysts as promising alternative for Raney-type Ni in the selective hydrogenation of D-glucose, Catal. Today, 2003, 79, 35–41 CrossRef.
- H. Singh, A. Rai, R. Yadav and A. K. Sinha, Glucose hydrogenation to sorbitol over unsupported mesoporous Ni/NiO catalyst, Mol. Catal., 2018, 451, 186–191 CrossRef CAS.
- J. Zhang, S. Wu, Y. Liu and B. Li, Hydrogenation of glucose over reduced Ni/Cu/Al hydrotalcite precursors, Catal. Commun., 2013, 35, 23–26 CrossRef CAS.
- Y. Fu, L. Ding, M. L. Singleton, H. Idrissi and S. Hermans, Synergistic effects altering reaction pathways: The case of glucose hydrogenation over Fe-Ni catalysts, Appl. Catal., B, 2021, 288, 119997 CrossRef CAS.
- P. A. Lazaridis, S. Karakoulia, A. Delimitis, S. M. Coman, V. I. Parvulescu and K. S. Triantafyllidis, d-Glucose hydrogenation/hydrogenolysis reactions on noble metal (Ru, Pt)/activated carbon supported catalysts, Catal. Today, 2015, 257, 281–290 CrossRef CAS.
- S. Esposito, B. Silvestri, V. Russo, B. Bonelli, M. Manzoli, F. A. Deorsola, A. Vergara, A. Aronne and M. Di Serio, Self-Activating Catalyst for Glucose Hydrogenation in the Aqueous Phase under Mild Conditions, ACS Catal., 2019, 9(4), 3426–3436 CrossRef CAS.
- E. Crezee, B. W. Hoffer, R. J. Berger, M. Makkee, F. Kapteijn and J. A. Moulijn, Three-phase hydrogenation of d-glucose over a carbon supported ruthenium catalyst-mass transfer and kinetics, Appl. Catal., A, 2003, 251(1), 1–17 CrossRef CAS.
- X. Guo, X. Wang, J. Guan, X. Chen, Z. Qin, X. Mu and M. Xian, Selective hydrogenation of D-glucose to D-sorbitol over Ru/ZSM-5 catalysts, Chin. J. Catal., 2014, 35(5), 733–740 CrossRef CAS.
- A. A. Dabbawala, D. K. Mishra and J.-S. Hwang, Selective hydrogenation of D-glucose using amine functionalized nanoporous polymer supported Ru nanoparticles based catalyst, Catal. Today, 2016, 265, 163–173 CrossRef CAS.
- D. K. Mishra, A. A. Dabbawala, J. J. Park, S. H. Jhung and J.-S. Hwang, Selective hydrogenation of d-glucose to d-sorbitol over HY zeolite supported ruthenium nanoparticles catalysts, Catal. Today, 2014, 232, 99–107 CrossRef CAS.
- Y. Zhou, Y. Liang, X. Liu and X. Qi, Efficient Glucose Hydrogenation to Sorbitol by Graphene-like Carbon-Encapsulated Ru Catalyst Synthesized by Evaporation-Induced Self-Assembly and Chemical Activation, ACS Sustainable Chem. Eng., 2023, 11(32), 12052–12064 CrossRef CAS.
- W. Xu, Y. Zhang, J. Wang, Y. Xu, L. Bian, Q. Ju, Y. Wang and Z. Fang, Defects engineering simultaneously enhances activity and recyclability of MOFs in selective hydrogenation of biomass, Nat. Commun., 2022, 13(1), 2068 CrossRef CAS PubMed.
- I. Bonnin, R. Méreau, T. Tassaing, F. Jérôme and K. De Oliveira, Hydrogenation of Sugars to Sugar Alcohols in the Presence of a Recyclable Ru/Al2O3 Catalyst Commercially Available, ACS Sustainable Chem. Eng., 2021, 9(28), 9240–9247 CrossRef CAS.
- S. Uruş, H. Eskalen, M. Çaylar and M. Akbulut, Highly effective aldose reductase mimetics: Microwave-assisted catalytic transfer hydrogenation of d-glucose to D-sorbitol with magnetically recoverable aminomethylphosphine-Ru(II) and Ni(II) complexes, J. Mol. Struct., 2021, 1237, 130313 CrossRef.
- M. Qiu, J. Zheng, Y. Yao, L. Liu, X. Zhou, H. Jiao, J. Aarons, K. Zhang, Q. Guan and W. Li, Directly converting cellulose into high yield sorbitol by tuning the electron structure of Ru2P anchored in agricultural straw biochar, J. Cleaner Prod., 2022, 362, 132364 CrossRef CAS.
- A. Romero, E. Alonso, Á. Sastre and A. Nieto-Márquez, Conversion of biomass into sorbitol: Cellulose hydrolysis on MCM-48 and d-Glucose hydrogenation on Ru/MCM-48, Microporous Mesoporous Mater., 2016, 224, 1–8 CrossRef CAS.
- R. Xi, Y. Tang, R. L. Smith Jr., X. Liu, L. Liu and X. Qi, Selective hydrogenation of glucose to sorbitol with tannic acid-based porous carbon sphere supported Ni–Ru bimetallic catalysts, Green Energy Environ., 2023, 8(6), 1719–1727 CrossRef CAS.
- J. Fu, C. Chen, R. L. Smith Jr. and X. Qi, General strategy for embedding metallic element, multi-metal or metal alloy nanoparticles into ordered mesoporous carbons via alcohol-soluble humins, Chem. Eng. J., 2023, 473, 145457 CrossRef CAS.
- W. Liu, W. You, W. Sun, W. Yang, A. Korde, Y. Gong and Y. Deng, Ambient-pressure and low-temperature upgrading of lignin bio-oil to hydrocarbons using a hydrogen buffer catalytic system, Nat. Energy, 2020, 5(10), 759–767 CrossRef CAS.
- H. Kobayashi, H. Matsuhashi, T. Komanoya, K. Hara and A. Fukuoka, Transfer hydrogenation of cellulose to sugar alcohols over supported ruthenium catalysts, Chem. Commun., 2011, 47(8), 2366–2368 RSC.
- A. Shrotri, H. Kobayashi, A. Tanksale, A. Fukuoka and J. Beltramini, Transfer Hydrogenation of Cellulose-based Oligomers over Carbon-supported Ruthenium Catalyst in a Fixed-bed Reactor, ChemCatChem, 2014, 6(5), 1349–1356 CrossRef CAS.
- B. García, J. Moreno, G. Morales, J. A. Melero and J. Iglesias, Production of Sorbitol via Catalytic Transfer Hydrogenation of Glucose, Appl. Sci., 2020, 10(5), 1843 CrossRef.
- B. García, A. Orozco-Saumell, M. López, J. Moreno and J. Iglesias, Catalytic Transfer Hydrogenation of Glucose to Sorbitol with Raney Ni Catalysts Using Biomass-Derived Diols as Hydrogen Donors, ACS Sustainable Chem. Eng., 2021, 9(44), 14857–14867 CrossRef.
- S. A. Akhade, N. Singh, O. Y. Gutiérrez, J. Lopez-Ruiz, H. Wang, J. D. Holladay, Y. Liu, A. Karkamkar, R. S. Weber, A. B. Padmaperuma, M.-S. Lee, G. A. Whyatt, M. Elliott, J. E. Holladay, J. L. Male, J. A. Lercher, R. Rousseau and V.-A. Glezakou, Electrocatalytic Hydrogenation of Biomass-Derived Organics: A Review, Chem. Rev., 2020, 120(20), 11370–11419 CrossRef CAS.
- A. Brouzgou, L. L. Yan, S. Q. Song and P. Tsiakaras, Glucose electrooxidation over PdxRh/C electrocatalysts in alkaline medium, Appl. Catal., B, 2014, 147, 481–489 CrossRef CAS.
- Y. Q. Zhu, H. Zhou, J. Dong, S. M. Xu, M. Xu, L. Zheng, Q. Xu, L. Ma, Z. Li and M. Shao, Identification of active sites formed on cobalt oxyhydroxide in glucose electrooxidation, Angew. Chem., 2023, 135(15), e202219048 CrossRef.
- K. Li and Y. Sun, Electrocatalytic Upgrading of Biomass-Derived Intermediate Compounds to Value-Added Products, Chem. – Eur. J., 2018, 24(69), 18258–18270 CrossRef CAS.
- J. Lessard, G. Belot, Y. Couture, S. Desjardins and C. Roy, The use of hydrogen generated at the electrode surface for electrohydrogenation of organic compounds, Int. J. Hydrogen Energy, 1993, 18(8), 681–684 CrossRef CAS.
- P. Pintauro, D. Johnson, K. Park, M. Baizer and K. Nobe, The paired electrochemical synthesis of sorbitol and gluconic acid in undivided flow cells, J. Appl. Electrochem., 1984, 14, 209–220 CrossRef CAS.
- Y. Kwon and M. T. M. Koper, Electrocatalytic Hydrogenation and Deoxygenation of Glucose on Solid Metal Electrodes, ChemSusChem, 2013, 6(3), 455–462 CrossRef CAS.
- I. T. Clark, Hydrogenolysis of sorbitol, Ind. Eng. Chem., 1958, 50(8), 1125–1126 CrossRef CAS.
- C. H. Lam, W. Deng, L. Lang, X. Jin, X. Hu and Y. Wang, Minireview on Bio-Oil Upgrading via Electrocatalytic Hydrogenation: Connecting Biofuel Production with Renewable Power, Energy Fuels, 2020, 34(7), 7915–7928 CrossRef CAS.
- Y. Tang, H. Chen, J. Jiang, Z. Tang, B. Huang and H. W. Roesky, Application of hydrogen-storage alloy electrode in electrochemical reduction of glucose, J. Power Sources, 2004, 130(1), 56–60 CrossRef CAS.
- S. Fei, J. Chen, S. Yao, G. Deng, L. Nie and Y. Kuang, Electroreduction of α-glucose on CNT/graphite electrode modified by Zn and Zn–Fe alloy, J. Solid State Electrochem., 2005, 9, 498–503 CrossRef CAS.
- K. Park, P. N. Pintauro, M. M. Baizer and K. Nobe, Flow Reactor Studies of the Paired Electro–Oxidation and Electroreduction of Glucose, J. Electrochem. Soc., 1985, 132(8), 1850 CrossRef CAS.
- J. P. Oña, R.-M. Latonen, N. Kumar, M. Peurla, I. Angervo and H. Grénman, Electrocatalytic hydrogenation of glucose and xylose using carbon fiber supported Au nanocatalysts, Electrochim. Acta, 2022, 426, 140754 CrossRef.
- Y. Owobi-Andely, K. Fiaty, P. Laurent and C. Bardot, Use of electrocatalytic membrane reactor for synthesis of sorbitol, Catal. Today, 2000, 56(1), 173–178 CrossRef CAS.
- R. G. Keller, J. Weyand, J. B. Vennekoetter, J. Kamp and M. Wessling, An electro-Fenton process coupled with nanofiltration for enhanced conversion of cellobiose to glucose, Catal. Today, 2021, 364, 230–241 CrossRef CAS.
- Y. Kwon, S. E. F. Kleijn, K. J. P. Schouten and M. T. M. Koper, Cellobiose Hydrolysis and Decomposition by Electrochemical Generation of Acid and Hydroxyl Radicals, ChemSusChem, 2012, 5(10), 1935–1943 CrossRef CAS PubMed.
- M. Taha, Y. M. A. Mohamed, S. S. Medany and Y. A. Attia, Nano Ag/AgBr/g-C3N4 catalyzed the production of hydrogen and reduction of d-glucose to sorbitol under visible light irradiation, New J. Chem., 2022, 46(37), 17746–17754 RSC.
- R. Situmeang, M. Tamba, E. Simarmata, T. Yuliarni, W. Simanjuntak, Z. Sembiring and S. Sembiring, LaCrO3 nano photocatalyst: the effect of calcination temperature on its cellulose conversion activity under UV-ray irradiation, Adv. Nat. Sci.: Nanosci. Nanotechnol., 2019, 10(1), 015009 CAS.
-
M. Supeno and R. Siburian, In: Role of TiO2 pillared bentonite-Co catalyst Ni to convert glucose hydrogenation to be sorbitol, 2018, IOP Publishing, 2018, pp. 042038 Search PubMed.
-
P. Jacobs and H. Hinnekens, EP0329923, 1989;
L. Hartstra and L. Bakker, H.A van Westen. Hydrogenation of carbohydrates, US Patent2518235, 1950 Search PubMed.
- T. Komanoya, H. Kobayashi, K. Hara, W.-J. Chun and A. Fukuoka, Kinetic Study of Catalytic Conversion of Cellulose to Sugar Alcohols under Low-Pressure Hydrogen, ChemCatChem, 2014, 6(1), 230–236 CrossRef CAS.
- T. Deng and H. Liu, Promoting effect of SnOx on selective conversion of cellulose to polyols over bimetallic Pt-SnOx/Al2O3 catalysts, Green Chem., 2013, 15(1), 116–124 RSC.
- K. Tajvidi, P. J. Hausoul and R. Palkovits, Hydrogenolysis of Cellulose over Cu–Based Catalysts—Analysis of the Reaction Network, ChemSusChem, 2014, 7(5), 1311–1317 CrossRef CAS PubMed.
- D. Klemm, B. Heublein, H.-P. Fink and A. Bohn, Cellulose: Fascinating Biopolymer and Sustainable Raw Material, Angew. Chem., Int. Ed., 2005, 44(22), 3358–3393 CrossRef CAS PubMed.
- A. Fukuoka and P. L. Dhepe, Catalytic Conversion of Cellulose into Sugar Alcohols, Angew. Chem., Int. Ed., 2006, 45(31), 5161–5163 CrossRef CAS PubMed.
- W. Deng, X. Tan, W. Fang, Q. Zhang and Y. Wang, Conversion of Cellulose into Sorbitol over Carbon Nanotube-Supported Ruthenium Catalyst, Catal. Lett., 2009, 133(1), 167 CrossRef CAS.
- J. Zhang, S.-b. Wu and Y. Liu, Direct Conversion of Cellulose into Sorbitol over a Magnetic Catalyst in an Extremely Low Concentration Acid System, Energy Fuels, 2014, 28(7), 4242–4246 CrossRef CAS.
- L. Alves de Souza, P. Magalhães de Souza, G. Tozzi Wurzler, V. Teixeira da Silva, D. A. Azevedo, R. Wojcieszak and F. Bellot Noronha, Reductive Catalytic Fractionation of Lignocellulosic Biomass: Unveiling of the Reaction Mechanism, ACS Sustainable Chem. Eng., 2023, 11(1), 67–77 CrossRef CAS.
- S. Yang, H. Kim and D. H. Kim, Improving the efficiency of Ru metal supported on SiO2 in liquid-phase hydrogenation of gluconic acid by adding activated carbon, Chem. Eng. J., 2022, 450, 138149 CrossRef CAS.
- C. Luo, S. Wang and H. Liu, Cellulose Conversion into Polyols Catalyzed by Reversibly Formed Acids and Supported Ruthenium Clusters in Hot Water, Angew. Chem., Int. Ed., 2007, 46(40), 7636–7639 CrossRef CAS.
- L. S. Ribeiro, J. J. Delgado, J. J. de Melo and M. F. Ribeiro, Influence of the Surface Chemistry of Multiwalled Carbon Nanotubes on the Selective Conversion of Cellulose into Sorbitol, ChemCatChem, 2017, 9(5), 888–896 CrossRef CAS.
- S. Van de Vyver, J. Geboers, M. Dusselier, H. Schepers, T. Vosch, L. Zhang, G. Van Tendeloo, P. A. Jacobs and B. F. Sels, Selective Bifunctional Catalytic Conversion of Cellulose over Reshaped Ni Particles at the Tip of Carbon Nanofibers, ChemSusChem, 2010, 3(6), 698–701 CrossRef CAS.
- N. Rey-Raap, L. S. Ribeiro, J. J. d. M. Órfão, J. L. Figueiredo and M. F. R. Pereira, Catalytic conversion of cellulose to sorbitol over Ru supported on biomass-derived carbon-based materials, Appl. Catal., B, 2019, 256, 117826 CrossRef CAS.
- Z. Li, Y. Liu, C. Liu, S. Wu and W. Wei, Direct conversion of cellulose into sorbitol catalyzed by a bifunctional catalyst, Bioresour. Technol., 2019, 274, 190–197 CrossRef CAS.
- Z. Li, W. Lan and C. Liu, Biomass derived bifunctional catalyst for the conversion of cassava dreg into sorbitol, Ind. Crops Prod., 2023, 197, 116493 CrossRef CAS.
- S. Carlier, J. Gripekoven, M. Philippo and S. Hermans, Ru on N-doped carbon supports for the direct hydrogenation of cellobiose into sorbitol, Appl. Catal., B, 2021, 282, 119515 CrossRef CAS.
- F. Mao, S. Chen, Q. Zhang, L. Yang, F. Wan, D. Jiang, M. Xiong, C. Zhang, Y. Liu and Z. Fu, Ru/P-Containing Porous Biochar-Efficiently Catalyzed Cascade Conversion of Cellulose to Sorbitol in Water under Medium-Pressure H2 Atmosphere, Bull. Chem. Soc. Jpn., 2020, 93(8), 1026–1035 CrossRef CAS.
- S. Chen, F. Mao, S. Tang, Z. Yi, H. Zhang, J. She, B. Yang, C. Zhang, Y. Liu and Z. Fu, One-pot hydrolytic hydrogenation of carbohydrates to hexitols catalyzed by Ru loaded P and Si-containing hierarchical porous biochars with excellent catalytic efficiency, Cellulose, 2022, 1–18 Search PubMed.
- E. Frecha, D. Torres, A. Pueyo, I. Suelves and J. L. Pinilla, Scanning different Ni-noble metal (Pt, Pd, Ru) bimetallic nanoparticles supported on carbon nanofibers for one-pot cellobiose conversion, Appl. Catal., A, 2019, 585, 117182 CrossRef.
- Y. Zhang, G. Zhang and T. Chen, Efficient one-pot conversion of cellulose to sorbitol over Ni-based carbon catalysts with embedment structure, Fuel, 2023, 339, 127447 CrossRef CAS.
- T. Haynes, S. Hubert, S. Carlier, V. Dubois and S. Hermans, Influence of Water-Miscible Organic Solvent on the Activity and Stability of Silica-Coated Ru Catalysts in the Selective Hydrolytic Hydrogenation of Cellobiose into Sorbitol, Catalysts, 2020, 10(2), 149 CrossRef CAS.
- Y. Liu, L. Chen, W. Zhang and H. Liu, Recyclable Cu Salt-Derived Brønsted Acids for Hydrolytic Hydrogenation of Cellulose on Ru Catalyst, CCS Chem., 2021, 3, 3419–3426 Search PubMed.
- L. S. Ribeiro, J. J. Delgado, J. J. M. Órfão and M. F. R. Pereira, Carbon supported Ru-Ni bimetallic catalysts for the enhanced one-pot conversion of cellulose to sorbitol, Appl. Catal., B, 2017, 217, 265–274 CrossRef CAS.
- L. S. Ribeiro, J. J. d. M. Órfão and M. F. R. Pereira, Direct catalytic production of sorbitol from waste cellulosic materials, Bioresour. Technol., 2017, 232, 152–158 CrossRef CAS PubMed.
- M. D. Adsuar-García, J. X. Flores-Lasluisa, F. Z. Azar and M. C. Román-Martínez, Carbon-Black-Supported Ru Catalysts for the Valorization of Cellulose through Hydrolytic Hydrogenation, Catalysts, 2018, 8(12), 572 CrossRef.
- K. Gao, J. Xin, D. Yan, H. Dong, Q. Zhou, X. Lu and S. Zhang, Direct conversion of cellulose to sorbitol via an enhanced pretreatment with ionic liquids, J. Chem. Technol. Biotechnol., 2018, 93(9), 2617–2624 CrossRef CAS.
- N. V. Gromov, T. B. Medvedeva, O. P. Taran, M. N. Timofeeva, O. Said-Aizpuru, V. N. Panchenko, E. Y. Gerasimov, I. V. Kozhevnikov and V. N. Parmon, The main factors affecting the catalytic properties of Ru/Cs-HPA systems in one-pot hydrolysis-hydrogenation of cellulose to sorbitol, Appl. Catal., A, 2020, 595, 117489 CrossRef CAS.
- G. Zhang, T. Chen, Y. Zhang, T. Liu and G. Wang, Effective Conversion of Cellulose to Sorbitol Catalyzed by Mesoporous Carbon Supported Ruthenium Combined with Zirconium Phosphate, Catal. Lett., 2020, 150(8), 2294–2303 CrossRef CAS.
- N. V. Gromov, T. B. Medvedeva, Y. A. Rodikova, M. N. Timofeeva, V. N. Panchenko, O. P. Taran, I. V. Kozhevnikov and V. N. Parmon, One-pot synthesis of sorbitol via hydrolysis-hydrogenation of cellulose in the presence of Ru-containing composites, Bioresour. Technol., 2021, 319, 124122 CrossRef CAS.
- X. Liu, X. Liu, N. Li, P. Ma and Y. Zhang, Direct synthesis of hexitols from microcrystalline cellulose and birch over zirconium(IV) phosphate supported nickel catalysts and the mechanism study, Green Chem., 2021, 23(3), 1353–1360 RSC.
- L. Liu, M. Qiu, H. Zhang, J. Yang, F. Shen, H. Guo, J. Yang, Q. Guan and W. Li, Green and efficient utilization of
beech sawdust waste for sorbitol production: Direct conversion residue via Ru2P/OMC derived from separated lignin, Chem. Eng. J., 2023, 477, 147093 CrossRef CAS.
- W. Anutrasakda and P. Pitakjakpipop, Performances of mesoporous silica-supported nickel phosphide nanocatalysts in the one-pot transformation of cellobiose to sorbitol, Catal. Today, 2021, 375, 216–224 CrossRef CAS.
- M. Andérez, Ó. Benito-Román, A. Romero and E. Alonso, Hydrolytic Hydrogenation of Cellobiose into Hexitols by Means of Ru/MCM48 Catalysts, Catal. Lett., 2021, 151(5), 1350–1360 CrossRef.
- X. Xiao, S. H. Lim, W. Chu and Y. Liu, Chitosan-Derived Porous N-Doped Carbon as a Promising Support for Ru Catalysts in One-Pot Conversion of Cellobiose to Hexitol, ACS Sustainable Chem. Eng., 2021, 9(37), 12655–12662 CrossRef CAS.
- D. Polidoro, G. Stamilla, M. Feltracco, A. Gambaro, A. Perosa and M. Selva, CO2-assisted hydrolytic hydrogenation of cellulose and cellulose-based waste into sorbitol over commercial Ru/C, Green Chem., 2023, 25(17), 6677–6685 RSC.
- Y. Liao, B. O. de Beeck, K. Thielemans, T. Ennaert, J. Snelders, M. Dusselier, C. M. Courtin and B. F. Sels, The role of pretreatment in the catalytic valorization of cellulose, Mol. Catal., 2020, 487, 110883 CrossRef CAS.
- R. Rinaldi and F. Schüth, Acid hydrolysis of cellulose as the entry point into biorefinery schemes, ChemSusChem, 2009, 2(12), 1096–1107 CrossRef CAS PubMed.
- Y. Liu, H. Fu, W. Zhang and H. Liu, Effect of Crystalline Structure on the Catalytic Hydrolysis of Cellulose in Subcritical Water, ACS Sustainable Chem. Eng., 2022, 10(18), 5859–5866 CrossRef CAS.
- P. Griffin, S. Ramer, M. Winfough and J. Kostal, Practical guide to designing safer ionic liquids for cellulose dissolution using a tiered computational framework, Green Chem., 2020, 22(11), 3626–3637 RSC.
- L. T. Mika, E. Cséfalvay and Á. Németh, Catalytic Conversion of Carbohydrates to Initial Platform Chemicals: Chemistry and Sustainability, Chem. Rev., 2018, 118(2), 505–613 CrossRef CAS PubMed.
- L. S. Ribeiro, J. J. M. Órfão and M. F. R. Pereira, Comparative study of different catalysts for the direct conversion of cellulose to sorbitol, Green Process. Synth., 2015, 4(2), 71–78 CAS.
- M. Yabushita, H. Kobayashi and A. Fukuoka, Catalytic transformation of cellulose into platform chemicals, Appl. Catal., B, 2014, 145, 1–9 CrossRef CAS.
- F. Shen, X. Xiong, J. Fu, J. Yang, M. Qiu, X. Qi and D. C. W. Tsang, Recent advances in mechanochemical production of chemicals and carbon materials from sustainable biomass resources, Renewable Sustainable Energy Rev., 2020, 130, 109944 CrossRef CAS.
- P. Lazaridis, S. Karakoulia, C. Teodorescu, N. Apostol, D. Macovei, A. Panteli, A. Delimitis, S. Coman, V. Parvulescu and K. Triantafyllidis, High hexitols selectivity in cellulose hydrolytic hydrogenation over platinum (Pt) vs. ruthenium (Ru) catalysts supported on micro/mesoporous carbon, Appl. Catal., B, 2017, 214, 1–14 CrossRef CAS.
- L. S. Ribeiro, J. J. M. Órfão and M. F. R. Pereira, Enhanced direct production of sorbitol by cellulose ball-milling, Green Chem., 2015, 17(5), 2973–2980 RSC.
- Q. Zhang, M. Benoit, K. De Oliveira, J. Barrault, G. Jégou, M. Philippe and F. Jérôme, Pretreatment of microcrystalline cellulose by ultrasounds: effect of particle size in the heterogeneously-catalyzed hydrolysis of cellulose to glucose, Green Chem., 2013, 15(4), 963–969 RSC.
- Z. M. A. Bundhoo, Microwave-assisted conversion of biomass and waste materials to biofuels, Renewable Sustainable Energy Rev., 2018, 82, 1149–1177 CrossRef CAS.
-
Z. Fang, X. Qi and R. L. Smith
Jr., Production of biofuels and chemicals with microwave, Springer, 2015 Search PubMed.
-
Z. Fang, X. Qi and R. L. Smith Jr., Production of biofuels and chemicals with ultrasound, Springer, 2015 Search PubMed.
- Y. Abdullayev, O. Ahmadov, G. Valadova, A. Karimli and J. Autschbach, Unveiling the catalytic effects of Brønsted acidic ionic liquid on quantitative α-glucose conversion to 5-HMF: Experimental and computational studies, Renewable Energy, 2021, 171, 383–390 CrossRef CAS.
- Y. Liu, W. Zhang, C. Hao, S. Wang and H. Liu, Unveiling the mechanism for selective cleavage of C-C bonds in sugar reactions on tungsten trioxide-based catalysts, Proc. Natl. Acad. Sci. U. S. A., 2022, 119(34), e2206399119 CrossRef CAS.
- R. P. Swatloski, S. K. Spear, J. D. Holbrey and R. D. Rogers, Dissolution of Cellose with Ionic Liquids, J. Am. Chem. Soc., 2002, 124(18), 4974–4975 CrossRef CAS.
- J. Baruah, B. K. Nath, R. Sharma, S. Kumar, R. C. Deka, D. C. Baruah and E. Kalita, Recent Trends in the Pretreatment of Lignocellulosic Biomass for Value-Added Products, Front. Energy Res., 2018, 6, 141 CrossRef.
- Z. Zhang, J. Song and B. Han, Catalytic transformation of lignocellulose into chemicals and fuel products in ionic liquids, Chem. Rev., 2017, 117(10), 6834–6880 CrossRef CAS.
- N. Yan, C. Zhao, C. Luo, P. J. Dyson, H. Liu and Y. Kou, One-step conversion of cellobiose to C6-alcohols using a ruthenium nanocluster catalyst, J. Am. Chem. Soc., 2006, 128(27), 8714–8715 CrossRef CAS.
- Y. Zhu, Z. N. Kong, L. P. Stubbs, H. Lin, S. Shen, E. V. Anslyn and J. A. Maguire, Conversion of Cellulose to Hexitols Catalyzed by Ionic Liquid-Stabilized Ruthenium Nanoparticles and a Reversible Binding Agent, ChemSusChem, 2010, 3(1), 67–70 CrossRef CAS PubMed.
- J. Li, H. S. M. P. Soares, J. A. Moulijn and M. Makkee, Simultaneous hydrolysis and hydrogenation of cellobiose to sorbitol in molten salt hydrate media, Catal. Sci. Technol., 2013, 3(6), 1565–1572 RSC.
- R. M. de Almeida, J. Li, C. Nederlof, P. O’Connor, M. Makkee and J. A. Moulijn, Cellulose Conversion to Isosorbide in Molten Salt hydrate Media, ChemSusChem, 2010, 3(3), 325–328 CrossRef.
- B. B. Hansen, S. Spittle, B. Chen, D. Poe, Y. Zhang, J. M. Klein, A. Horton, L. Adhikari, T. Zelovich, B. W. Doherty, B. Gurkan, E. J. Maginn, A. Ragauskas, M. Dadmun, T. A. Zawodzinski, G. A. Baker, M. E. Tuckerman, R. F. Savinell and J. R. Sangoro, Deep Eutectic Solvents: A Review of Fundamentals and Applications, Chem. Rev., 2021, 121(3), 1232–1285 CrossRef CAS.
- J. Pang, A. Wang, M. Zheng, Y. Zhang, Y. Huang, X. Chen and T. Zhang, Catalytic conversion of cellulose to hexitols with mesoporous carbon supported Ni-based bimetallic catalysts, Green Chem., 2012, 14(3), 614–617 RSC.
- W. Zhu, H. Yang, J. Chen, C. Chen, L. Guo, H. Gan, X. Zhao and Z. Hou, Efficient hydrogenolysis of cellulose into sorbitol catalyzed by a bifunctional catalyst, Green Chem., 2014, 16(3), 1534–1542 RSC.
- I. A. Ignatyev, C. Van Doorslaer, P. G. N. Mertens, K. Binnemans and D. E. De Vos, Reductive Splitting of Cellulose in the Ionic Liquid 1-Butyl-3-Methylimidazolium Chloride, ChemSusChem, 2010, 3(1), 91–96 CrossRef CAS PubMed.
- K. Wilson and A. F. Lee, Catalyst design for biorefining, Philos. Trans. R. Soc., A, 2016, 347(2061), 20150081 CrossRef PubMed.
- R. Palkovits, K. Tajvidi, J. Procelewska, R. Rinaldi and A. Ruppert, Hydrogenolysis of cellulose combining mineral acids and hydrogenation catalysts, Green Chem., 2010, 12(6), 972–978 RSC.
- J. Keskiväli, S. Rautiainen, M. Heikkilä, T. T. T. Myllymäki, J.-P. Karjalainen, K. Lagerblom, M. Kemell, M. Vehkamäki, K. Meinander and T. Repo, Isosorbide synthesis from cellulose with an efficient and recyclable ruthenium catalyst, Green Chem., 2017, 19(19), 4563–4570 RSC.
- B. Op de Beeck, J. Geboers, S. Van de Vyver, J. Van Lishout, J. Snelders, W. J. J. Huijgen, C. M. Courtin, P. A. Jacobs and B. F. Sels, Conversion of (Ligno)Cellulose Feeds to Isosorbide with Heteropoly Acids and Ru on Carbon, ChemSusChem, 2013, 6(1), 199–208 CrossRef CAS PubMed.
- E. Nzediegwu and M.-J. Dumont, Chemo-Catalytic Transformation of Cellulose and Cellulosic-Derived Waste Materials into Platform Chemicals, Waste Biomass Valorization, 2021, 12(6), 2825–2851 CrossRef CAS.
- L. Zhou, Z. Li, J. Pang, M. Zheng, A. Wang and T. Zhang, Catalytic conversion of Jerusalem artichoke tuber into hexitols using the bifunctional catalyst Ru/(AC-SO3H), Chin. J. Catal., 2015, 36(10), 1694–1700 CrossRef CAS.
- A. Yamaguchi, O. Sato, N. Mimura and M. Shirai, Catalytic production of sugar alcohols from lignocellulosic biomass, Catal. Today, 2016, 265, 199–202 CrossRef CAS.
- L. S. Ribeiro, J. J. d. M. Órfão and M. F. R. Pereira, Simultaneous catalytic conversion of cellulose and corncob xylan under temperature programming for enhanced sorbitol and xylitol production, Bioresour. Technol., 2017, 244, 1173–1177 CrossRef CAS PubMed.
- Y. Yang, S. Shao, F. Yang, D. L. Brewe, S. Guo, D. Ren and S. Hao, Conversion of cellulose to high-yield glucose in water over sulfonated mesoporous carbon fibers with optimized acidity, Green Chem., 2021, 23(12), 4477–4489 RSC.
- X. Wang, M. Arai, Q. Wu, C. Zhang and F. Zhao, Hydrodeoxygenation of lignin-derived phenolics – a review on the active sites of supported metal catalysts, Green Chem., 2020, 22(23), 8140–8168 RSC.
- D. Gericke, D. Ott, V. G. Matveeva, E. Sulman, A. Aho, D. Y. Murzin, S. Roggan, L. Danilova, V. Hessel and P. Loeb, Green catalysis by nanoparticulate catalysts developed for flow processing? Case study of glucose hydrogenation, RSC Adv., 2015, 5(21), 15898–15908 RSC.
- P. Gallezot, N. Nicolaus, G. Fleche, P. Fuertes and A. Perrard, Glucose hydrogenation on ruthenium catalysts in a trickle-bed reactor, J. Catal., 1998, 180(1), 51–55 CrossRef CAS.
- B. W. Hoffer, E. Crezee, F. Devred, P. R. M. Mooijman, W. G. Sloof, P. J. Kooyman, A. D. van Langeveld, F. Kapteijn and J. A. Moulijn, The role of the active phase of Raney-type Ni catalysts in the selective hydrogenation of d-glucose to d-sorbitol, Appl. Catal., A, 2003, 253(2), 437–452 CrossRef CAS.
- P. Gallezot, P. Cerino, B. Blanc, G. Fleche and P. Fuertes, Glucose hydrogenation on promoted raney-nickel catalysts, J. Catal., 1994, 146(1), 93–102 CrossRef CAS.
- P. Gallezot, Conversion of biomass to selected chemical products, Chem. Soc. Rev., 2012, 41(4), 1538–1558 RSC.
- B. Kusserow, S. Schimpf and P. Claus, Hydrogenation of glucose to sorbitol over nickel and ruthenium catalysts, Adv. Synth. Catal., 2003, 345(1–2), 289–299 CrossRef CAS.
- S. Schimpf, C. Louis and P. Claus, Ni/SiO2 catalysts prepared with ethylenediamine nickel precursors: Influence of the pretreatment on the catalytic properties in glucose hydrogenation, Appl. Catal., A, 2007, 318, 45–53 CrossRef CAS.
- F. Brandi, M. Bäumel, V. Molinari, I. Shekova, I. Lauermann, T. Heil, M. Antonietti and M. Al-Naji, Nickel on nitrogen-doped carbon pellets for continuous-flow hydrogenation of biomass-derived compounds in water, Green Chem., 2020, 22(9), 2755–2766 RSC.
- G. Liang, H. Cheng, W. Li, L. He, Y. Yu and F. Zhao, Selective conversion of microcrystalline cellulose into hexitols on nickel particles encapsulated within ZSM-5 zeolite, Green Chem., 2012, 14(8), 2146–2149 RSC.
- S. Helveg, C. López-Cartes, J. Sehested, P. L. Hansen, B. S. Clausen, J. R. Rostrup-Nielsen, F. Abild-Pedersen and J. K. Nørskov, Atomic-scale imaging of carbon nanofibre growth, Nature, 2004, 427(6973), 426–429 CrossRef CAS PubMed.
- M. Shirazi, A. Bogaerts and E. C. Neyts, A DFT study of H-dissolution into the bulk of a crystalline Ni (111) surface: a chemical identifier for the reaction kinetics, Phys. Chem. Chem. Phys., 2017, 19(29), 19150–19158 RSC.
- W. Liu, Y. Chen, H. Qi, L. Zhang, W. Yan, X. Liu, X. Yang, S. Miao, W. Wang, C. Liu, A. Wang, J. Li and T. Zhang, A Durable Nickel Single-Atom Catalyst for Hydrogenation Reactions and Cellulose Valorization under Harsh Conditions, Angew. Chem., Int. Ed., 2018, 57(24), 7071–7075 CrossRef CAS PubMed.
- S. M. G. Lama, J. Pampel, T.-P. Fellinger, V. P. Beškoski, L. Slavković-Beškoski, M. Antonietti and V. Molinari, Efficiency of Ni Nanoparticles Supported on Hierarchical Porous Nitrogen-Doped Carbon for Hydrogenolysis of Kraft Lignin in Flow and Batch Systems, ACS Sustainable Chem. Eng., 2017, 5(3), 2415–2420 CrossRef CAS.
- B. García, J. Moreno, J. Iglesias, J. A. Melero and G. Morales, Transformation of Glucose into Sorbitol on Raney® Nickel Catalysts in the Absence of Molecular Hydrogen: Sugar Disproportionation vs Catalytic Hydrogen Transfer, Top. Catal., 2019, 62(5), 570–578 CrossRef.
- L. Ding, A. Wang, M. Zheng and T. Zhang, Selective Transformation of Cellulose into Sorbitol by Using a Bifunctional Nickel Phosphide Catalyst, ChemSusChem, 2010, 3(7), 818–821 CrossRef CAS PubMed.
- H. Li, W. Wang and J. F. Deng, Glucose hydrogenation to sorbitol over a skeletal Ni-P amorphous alloy catalyst (Raney® Ni-P), J. Catal., 2000, 191(1), 257–260 CrossRef CAS.
- H. Li, H. Li and J. Deng, Glucose hydrogenation over Ni–B/SiO2 amorphous alloy catalyst and the promoting effect of metal dopants, Catal. Today, 2002, 74(1–2), 53–63 CrossRef CAS.
- J. Guo, Y. Hou, C. Yang, Y. Wang, H. He and W. Li, Preparation of Ni–B amorphous alloy catalyst from nickel hydrazine complex with ultrasonic assistance, Catal. Commun., 2011, 16(1), 86–89 CrossRef CAS.
- L. Silvester, F. Ramos, J. Thuriot-Roukos, S. Heyte, M. Araque, S. Paul and R. Wojcieszak, Fully integrated high-throughput methodology for the study of Ni- and Cu-supported catalysts for glucose hydrogenation, Catal. Today, 2019, 338, 72–80 CrossRef CAS.
- J. Zelin, S. A. Regenhardt, C. I. Meyer, H. A. Duarte, V. Sebastian and A. J. Marchi, Selective aqueous-phase hydrogenation of D-fructose into D-mannitol using a highly efficient and reusable Cu-Ni/SiO2 catalyst, Chem. Eng. Sci., 2019, 206, 315–326 CrossRef CAS.
- P.
P. Upare, Y. K. Hwang, J. C. Kim, J. H. Lee, S. K. Kwak and D. W. Hwang, A Robust and Highly Selective Catalytic System of Copper–Silica Nanocomposite and 1–Butanol in Fructose Hydrogenation to Mannitol, ChemSusChem, 2020, 13(18), 5050–5057 CrossRef CAS.
- M. Audemar, W. Ramdani, T. Junhui, A. Ifrim, A. Ungureanu, F. Jérôme, S. Royer and K. de Oliveira, Selective hydrogenation of xylose to xylitol over Co/SiO2 catalysts, ChemCatChem, 2020, 12(7), 1973–1978 CrossRef CAS.
- H. Kobayashi, Y. Ito, T. Komanoya, Y. Hosaka, P. L. Dhepe, K. Kasai, K. Hara and A. Fukuoka, Synthesis of sugar alcohols by hydrolytic hydrogenation of cellulose over supported metal catalysts, Green Chem., 2011, 13(2), 326–333 RSC.
- K. Van Gorp, E. Boerman, C. Cavenaghi and P. Berben, Catalytic hydrogenation of fine chemicals: sorbitol production, Catal. Today, 1999, 52(2–3), 349–361 CrossRef CAS.
- C. Michel and P. Gallezot, Why Is Ruthenium an Efficient Catalyst for the Aqueous-Phase Hydrogenation of Biosourced Carbonyl Compounds?, ACS Catal., 2015, 5(7), 4130–4132 CrossRef CAS.
- A. Negoi, K. Triantafyllidis, V. I. Parvulescu and S. M. Coman, The hydrolytic hydrogenation of cellulose to sorbitol over M (Ru, Ir, Pd, Rh)-BEA-zeolite catalysts, Catal. Today, 2014, 223, 122–128 CrossRef CAS.
- S. Wang, H. Li and M. Wu, Advances in metal/biochar catalysts for biomass hydro-upgrading: A review, J. Cleaner Prod., 2021, 303, 126825 CrossRef CAS.
- A. Romero, A. Nieto-Márquez and E. Alonso, Bimetallic Ru:Ni/MCM-48 catalysts for the effective hydrogenation of d-glucose into sorbitol, Appl. Catal., A, 2017, 529, 49–59 CrossRef CAS.
- Z. Dong, W. Chen, K. Xu, Y. Liu, J. Wu and F. Zhang, Understanding the Structure–Activity Relationships in Catalytic Conversion of Polyolefin Plastics by Zeolite-Based Catalysts: A Critical Review, ACS Catal., 2022, 12(24), 14882–14901 CrossRef CAS.
- H. Kobayashi, Y. Hosaka, K. Hara, F. Bo, Y. Hirosaki and A. Fukuoka, Control of selectivity, activity and durability of simple supported nickel catalysts for hydrolytic hydrogenation of cellulose, Green Chem., 2014, 16(2), 637–644 RSC.
- A. Aho, S. Roggan, O. A. Simakova, T. Salmi and D. Y. Murzin, Structure sensitivity in catalytic hydrogenation of glucose over ruthenium, Catal. Today, 2015, 241, 195–199 CrossRef CAS.
- D. Wang, W. Niu, M. Tan, M. Wu, X. Zheng, Y. Li and N. Tsubaki, Pt Nanocatalysts Supported on Reduced Graphene Oxide for Selective Conversion of Cellulose or Cellobiose to Sorbitol, ChemSusChem, 2014, 7(5), 1398–1406 CrossRef CAS PubMed.
- J. Liu, P. Bai and X. S. Zhao, Ruthenium nanoparticles embedded in mesoporous carbon microfibers: preparation, characterization and catalytic properties in the hydrogenation of d-glucose, Phys. Chem. Chem. Phys., 2011, 13(9), 3758–3763 RSC.
- Z. Wang, M. Li, J. Yu, X. Ge, Y. Liu and W. Wang, Low-Iridium-Content IrNiTa Metallic Glass Films as Intrinsically Active Catalysts for Hydrogen Evolution Reaction, Adv. Mater., 2020, 32(4), 1906384 CrossRef CAS PubMed.
- H. Guo, H. Li, J. Zhu, W. Ye, M. Qiao and W. Dai, Liquid phase glucose hydrogenation to d-glucitol over an ultrafine Ru-B amorphous alloy catalyst, J. Mol. Catal. A: Chem., 2003, 200(1–2), 213–221 CrossRef CAS.
- S.-H. Li, M.-Y. Qi, Z.-R. Tang and Y.-J. Xu, Nanostructured metal phosphides: from controllable synthesis to sustainable catalysis, Chem. Soc. Rev., 2021, 50(13), 7539–7586 RSC.
- S. Wang, W. Wei, Y. Zhao, H. Li and H. Li, Ru–B amorphous alloy deposited on mesoporous silica nanospheres: An efficient catalyst for d-glucose hydrogenation to d-sorbitol, Catal. Today, 2015, 258, 327–336 CrossRef CAS.
- W. Anutrasakda, K. Eiamsantipaisarn, D. Jiraroj, A. Phasuk, T. Tuntulani, H. Liu and D. N. Tungasmita, One-Pot Catalytic Conversion of Cellobiose to Sorbitol over Nickel Phosphides Supported on MCM-41 and Al-MCM-41, Catalysts, 2019, 9(1), 92 CrossRef.
- B. Zhang, B. Chen, M. Douthwaite, Q. Liu, C. Zhang, Q. Wu, R. Shi, P. Wu, F. Zhao and G. Hutchings, Macroporous–mesoporous carbon supported Ni catalysts for the conversion of cellulose to polyols, Green Chem., 2018, 20(15), 3634–3642 RSC.
- M. He, J. Guo, X. Wang, Y. Song, S. Liu, H. Wang and C. Li, Direct conversion of cellulose into isosorbide over Ni doped NbOPO4 catalysts in water, New J. Chem., 2020, 44(25), 10292–10299 RSC.
- E. Girel, A. Cabiac, A. Chaumonnot, M. Besson and A. Tuel, Selective Carbon Deposition on γ-Alumina Acid Sites: toward the Design of Catalyst Supports with Improved Hydrothermal Stability in Aqueous Media, ACS Appl. Mater. Interfaces, 2020, 12(11), 13558–13567 CrossRef CAS PubMed.
- M. Banu, S. Sivasanker, T. M. Sankaranarayanan and P. Venuvanalingam, Hydrogenolysis of sorbitol over Ni and Pt loaded on NaY, Catal. Commun., 2011, 12(7), 673–677 CrossRef CAS.
- X. Deng, B. Qin, R. Liu, X. Qin, W. Dai, G. Wu, N. Guan, D. Ma and L. Li, Zeolite-Encaged Isolated Platinum Ions Enable Heterolytic Dihydrogen Activation and Selective Hydrogenations, J. Am. Chem. Soc., 2021, 143(49), 20898–20906 CrossRef CAS PubMed.
- J. M. A. R. Almeida, L. Da Vià, P. Demma, Y. Carvalho, P. N. Romano, J. A. O. Peña, L. Smith, E. F. Sousa-Aguiar and J. A. Lopez-Sanchez, Screening of mono- and bi-functional catalysts for the one-pot conversion of cellobiose into sorbitol, Catal. Today, 2017, 279, 187–193 CrossRef CAS.
- P. Yan, H. Wang, Y. Liao and C. Wang, Zeolite catalysts for the valorization of biomass into platform compounds and biochemicals/biofuels: A review, Renewable Sustainable Energy Rev., 2023, 178, 113219 CrossRef CAS.
- F. Brandi, I. Khalil, M. Antonietti and M. Al-Naji, Continuous-Flow Production of Isosorbide from Aqueous-Cellulosic Derivable Feed over Sustainable Heterogeneous Catalysts, ACS Sustainable Chem. Eng., 2021, 9(2), 927–935 CrossRef CAS.
- J. A. Melero, J. Moreno, J. Iglesias, G. Morales, J. L. G. Fierro, R. Sánchez-Vázquez, A. Cubo and B. García, Ru-ZrO2-SBA-15 as efficient and robust catalyst for the aqueous phase hydrogenation of glucose to sorbitol, Mol. Catal., 2020, 484, 110802 CrossRef CAS.
- A. Galadima, A. Masudi and O. Muraza, Conversion of cellulose to glucose and further transformation into fuels over solid acid catalysts: A mini review, Microporous Mesoporous Mater., 2022, 336, 111846 CrossRef CAS.
- Z. Wu, S. Ge, C. Ren, M. Zhang, A. Yip and C. Xu, Selective conversion of cellulose into bulk chemicals over Brønsted acid-promoted ruthenium catalyst: one-pot vs. sequential process, Green Chem., 2012, 14(12), 3336–3343 RSC.
- X. Zhang, A. I. M. Rabee, M. Isaacs, A. F. Lee and K. Wilson, Sulfated Zirconia Catalysts for D-Sorbitol Cascade Cyclodehydration to Isosorbide: Impact of Zirconia Phase, ACS Sustainable Chem. Eng., 2018, 6(11), 14704–14712 CrossRef CAS.
- R. Geyer, P. Kraak, A. Pachulski and R. Schödel, New Catalysts for the Hydrogenation of Glucose to Sorbitol, Chem. Ing. Tech., 2012, 84(4), 513–516 CrossRef CAS.
- V. Jollet, F. Chambon, F. Rataboul, A. Cabiac, C. Pinel, E. Guillon and N. Essayem, Non-catalyzed and Pt/γ-Al2O3-catalyzed hydrothermal cellulose dissolution–conversion: influence of the reaction parameters and analysis of the unreacted cellulose, Green Chem., 2009, 11(12), 2052–2060 RSC.
- S. Zhu, J. Guo, X. Wang, J. Wang and W. Fan, Alcoholysis: a promising technology for conversion of lignocellulose and platform chemicals, ChemSusChem, 2017, 10(12), 2547–2559 CrossRef CAS PubMed.
- M. Mani and L. J. Konwar, Ru/N-doped activated carbon/NbOPO4 composites as an efficient bi-functional catalyst for direct hydrolytic hydrogenation of cellobiose to sorbitol, Biomass Convers. Biorefin., 2023, 1–13 Search PubMed.
- J. Xi, Y. Zhang, Q. Xia, X. Liu, J. Ren, G. Lu and Y. Wang, Direct conversion of cellulose into sorbitol with high yield by a novel mesoporous niobium phosphate supported Ruthenium bifunctional catalyst, Appl. Catal., A, 2013, 459, 52–58 CrossRef CAS.
- J. Xi, Y. Zhang, D. Ding, Q. Xia, J. Wang, X. Liu, G. Lu and Y. Wang, Catalytic production of isosorbide from cellulose over mesoporous niobium phosphate-based heterogeneous catalysts via a sequential process, Appl. Catal., A, 2014, 469, 108–115 CrossRef CAS.
- S. Li, Y. Xu, Y. Chen, W. Li, L. Lin, M. Li, Y. Deng, X. Wang, B. Ge and C. Yang, Tuning the selectivity of catalytic carbon dioxide hydrogenation over iridium/cerium oxide catalysts with a strong metal–support interaction, Angew. Chem., 2017, 129(36), 10901–10905 CrossRef.
- M. Ammam, Polyoxometalates: formation, structures, principal properties, main deposition methods and application in sensing, J. Mater. Chem. A, 2013, 1(21), 6291–6312 RSC.
- J. Zhong, J. Pérez-Ramírez and N. Yan, Biomass valorisation over polyoxometalate-based catalysts, Green Chem., 2021, 23(1), 18–36 RSC.
- J. Geboers, S. Van de Vyver, K. Carpentier, K. de Blochouse, P. Jacobs and B. Sels, Efficient catalytic conversion of concentrated cellulose feeds to hexitols with heteropoly acids and Ru on carbon, Chem. Commun., 2010, 46(20), 3577–3579 RSC.
- Y. Ogasawara, S. Itagaki, K. Yamaguchi and N. Mizuno, Saccharification of Natural Lignocellulose Biomass and Polysaccharides by Highly Negatively Charged Heteropolyacids in Concentrated Aqueous Solution, ChemSusChem, 2011, 4(4), 519–525 CrossRef CAS PubMed.
- M. Liu, W. Deng, Q. Zhang, Y. Wang and Y. Wang, Polyoxometalate-supported ruthenium nanoparticles as bifunctional heterogeneous catalysts for the conversions of cellobiose and cellulose into sorbitol under mild conditions, Chem. Commun., 2011, 47(34), 9717–9719 RSC.
- W. Deng, E. Zhu, M. Liu, Q. Zhang and Y. Wang, Cs-substituted tungstophosphate-supported ruthenium nanoparticles as efficient and robust bifunctional catalysts for the conversion of inulin and cellulose into hexitols in water in the presence of H2, RSC Adv., 2014, 4(81), 43131–43141 RSC.
- L. S. Ribeiro, A. L. F. Pires, J. J. d. M. Órfão and M. F. R. Pereira, Paving the way towards an eco- and budget-friendly one-pot catalytic conversion of cellulose and lignocellulosic residues into ethylene glycol over Ni–W/CNT catalysts, Renewable Energy, 2022, 200, 1008–1022 CrossRef CAS.
- S. Yu, X. Cao, S. Liu, L. Li and Q. Wu, Production of ethylene glycol from direct catalytic conversion of cellulose over a binary catalyst of metal-loaded modified SBA-15 and phosphotungstic acid, RSC Adv., 2018, 8(44), 24857–24865 RSC.
- P. Kashyap, S. Bhardwaj, V. P. Chodimella and A. K. Sinha, Carbon-based heterogeneous catalysts
for conversion of cellulose and cellulosic feedstock, Biomass Convers. Biorefin., 2022, 1–21 CAS.
- X. Wang, X. Liu, R. L. Smith Jr., Y. Liang and X. Qi, Direct one-pot synthesis of ordered mesoporous carbons from lignin with metal coordinated self-assembly, Green Chem., 2021, 23(21), 8632–8642 RSC.
- Y. Tang, M. Qiu, J. Yang, F. Shen, X. Wang and X. Qi, One-pot self-assembly synthesis of Ni-doped ordered mesoporous carbon for quantitative hydrogenation of furfural to furfuryl alcohol, Green Chem., 2021, 23(4), 1861–1870 RSC.
- W. Deng, L. Mi, X. Tan, Q. Zhang and W. Ye, Conversion of cellobiose into sorbitol in neutral water medium over carbon nanotube-supported ruthenium catalysts, J. Catal., 2010, 271(1), 22–32 CrossRef CAS.
- L. S. Ribeiro, J. J. Delgado, J. J. de Melo and M. F. R. Pereira, Direct conversion of cellulose to sorbitol over ruthenium catalysts: Influence of the support, Catal. Today, 2017, 279, 244–251 CrossRef CAS.
- J. Huo, J.-P. Tessonnier and B. H. Shanks, Improving Hydrothermal Stability of Supported Metal Catalysts for Biomass Conversions: A Review, ACS Catal., 2021, 11(9), 5248–5270 CrossRef CAS.
- F.-Z. Azar, M.Á Lillo-Ródenas and M. C. Román-Martínez, Mesoporous Activated Carbon Supported Ru Catalysts to Efficiently Convert Cellulose into Sorbitol by Hydrolytic Hydrogenation, Energies, 2020, 13(17), 4394 CrossRef CAS.
- Y. P. Zhu, C. Guo, Y. Zheng and S.-Z. Qiao, Surface and Interface Engineering of Noble-Metal-Free Electrocatalysts for Efficient Energy Conversion Processes, Acc. Chem. Res., 2017, 50(4), 915–923 CrossRef CAS PubMed.
- G. Zhang, T. Chen, Y. Zhang, T. Liu and G. Wang, The effect of physical morphology and the chemical state of Ru on the catalytic properties of Ru–carbon for cellulose hydrolytic hydrogenation, New J. Chem., 2020, 44(35), 15169–15176 RSC.
- H. Kobayashi, M. Yabushita, T. Komanoya, K. Hara, I. Fujita and A. Fukuoka, High-Yielding One-Pot Synthesis of Glucose from Cellulose Using Simple Activated Carbons and Trace Hydrochloric Acid, ACS Catal., 2013, 3(4), 581–587 CrossRef CAS.
- J. a. W. He, Z. Gu, Q. Liu, Y. Chu, S. Chen, S. Zhang, Y. Yang, B. Chen and T. Wang,
et al., Zeolite-Tailored Active Site Proximity for the Efficient Production of Pentanoic Biofuels, Angew. Chem., 2021, 133(44), 23906–23914 CrossRef.
- N. S. Hassan and A. A. Jalil, Cellulose conversion into renewable chemicals and fuels over supported metal catalysts, IOP Conf. Ser.: Mater. Sci. Eng., 2020, 808(1), 012002 CrossRef CAS.
- T. Deng, X. He and H. Liu, Insights into the Active Acid Sites for Isosorbide Synthesis from Renewable Sorbitol and Cellulose on Solid Acid Catalysts, Chem. Res. Chin. Univ., 2022, 38(1), 257–264 CrossRef CAS.
- Y. Wu, M. He, X. Liu, X. Wang, Y. Song, C. Li, S. Liu and L. Huang, One-pot Catalytic Conversion of Cellulose to Sorbitol and Isosorbide over Bifunctional Ni/TaOPO4 Catalysts, ChemistrySelect, 2022, 7(28), e202200341 CrossRef CAS.
- B. Zhang, X. Li, Q. Wu, C. Zhang, Y. Yu, M. Lan, X. Wei, Z. Ying, T. Liu and G. Liang, Synthesis of Ni/mesoporous ZSM-5 for direct catalytic conversion of cellulose to hexitols: modulating the pore structure and acidic sites via a nanocrystalline cellulose template, Green Chem., 2016, 18(11), 3315–3323 RSC.
- G. Chen, X. Wang, Y. Jiang, X. Mu and H. Liu, Insights into deactivation mechanism of sulfonated carbonaceous solid acids probed by cellulose hydrolysis, Catal. Today, 2019, 319, 25–30 CrossRef CAS.
- T. Komanoya, H. Kobayashi, K. Hara, W.-J. Chun and A. Fukuoka, Catalysis and characterization of carbon-supported ruthenium for cellulose hydrolysis, Appl. Catal., A, 2011, 407(1), 188–194 CrossRef CAS.
- G. Liang, L. He, H. Cheng, W. Li, X. Li, C. Zhang, Y. Yu and F. Zhao, The hydrogenation/dehydrogenation activity of supported Ni catalysts and their effect on hexitols selectivity in hydrolytic hydrogenation of cellulose, J. Catal., 2014, 309, 468–476 CrossRef CAS.
- S. Van de Vyver, J. Geboers, W. Schutyser, M. Dusselier, P. Eloy, E. Dornez, J. W. Seo, C. M. Courtin, E. M. Gaigneaux, P. A. Jacobs and B. F. Sels, Tuning the Acid/Metal Balance of Carbon Nanofiber-Supported Nickel Catalysts for Hydrolytic Hydrogenation of Cellulose, ChemSusChem, 2012, 5(8), 1549–1558 CrossRef CAS PubMed.
- J. Chen, S. Wang, J. Huang, L. Chen, L. Ma and X. Huang, Conversion of cellulose and cellobiose into sorbitol catalyzed by ruthenium supported on a polyoxometalate/metal–organic framework hybrid, ChemSusChem, 2013, 6(8), 1545–1555 CrossRef CAS PubMed.
- K. L. Fleming and J. Pfaendtner, Characterizing the Catalyzed Hydrolysis of β-1,4 Glycosidic Bonds Using Density Functional Theory, J. Phys. Chem. A, 2013, 117(51), 14200–14208 CrossRef CAS PubMed.
-
M. Yabushita, Mechanistic Study of Cellulose Hydrolysis by Carbon Catalysts, in A Study on Catalytic Conversion of Non-Food Biomass into Chemicals, Springer, 2016, pp. 77–112 Search PubMed.
- Z. Guo, D. Liu, S. H. Lim, Y. Liu and W. Chu, Confined PtNi catalysts for enhanced catalytic performances in one-pot cellobiose conversion to hexitols: a combined experimental and DFT study, Green Chem., 2019, 21(21), 5999–6011 RSC.
- J. K. Nørskov, T. Bligaard, J. Rossmeisl and C. H. Christensen, Towards the computational design of solid catalysts, Nat. Chem., 2009, 1(1), 37–46 CrossRef PubMed.
- L. Negahdar, J. U. Oltmanns, S. Palkovits and R. Palkovits, Kinetic investigation of the catalytic conversion of cellobiose to sorbitol, Appl. Catal., B, 2014, 147, 677–683 CrossRef CAS.
- L. Negahdar, P. J. C. Hausoul, S. Palkovits and R. Palkovits, Direct cleavage of sorbitol from oligosaccharides via a sequential hydrogenation-hydrolysis pathway, Appl. Catal., B, 2015, 166–167, 460–464 CrossRef CAS.
- B. Zada, L. Yan and Y. Fu, Effective conversion of cellobiose and glucose to sorbitol using non-noble bimetallic NiCo/HZSM-5 catalyst, Sci. China: Chem., 2018, 61(9), 1167–1174 CrossRef CAS.
-
J. W. Moore and R. G. Pearson, Kinetics and mechanism, John Wiley & Sons, 1981 Search PubMed.
- F. Garcia-Ochoa, P. Vergara, M. Wojtusik, S. Gutiérrez, V. E. Santos, M. Ladero and J. C. Villar, Multi-feedstock lignocellulosic biorefineries based on biological processes: An overview, Ind. Crops Prod., 2021, 172, 114062 CrossRef CAS.
- K. Abdelfatah, W. Yang, R. Solomon, B. Rajbanshi, A. Chowdhury, M. Zare, S. K. Kundu, A. Yonge, A. Heyden and G. Terejanu, Prediction of Transition-State Energies of Hydrodeoxygenation Reactions on Transition-Metal Surfaces Based on Machine Learning, J. Phys. Chem. C, 2019, 123(49), 29804–29810 CrossRef CAS.
- J. Sadeghi and K. R. Haapala, Optimizing a sustainable logistics problem in a renewable energy network using a genetic algorithm, Opsearch, 2019, 56(1), 73–90 CrossRef.
- H. S.-H. Wang and Y. Yao, Machine learning for sustainable development and applications of biomass and biomass-derived carbonaceous materials in water and agricultural systems: A review, Resour., Conserv. Recycl., 2023, 190, 106847 CrossRef.
- I. Jaramillo and A. Sanchez, Mass Flow Dynamic Modeling and Residence Time Control of a Continuous Tubular Reactor for Biomass Pretreatment, ACS Sustainable Chem. Eng., 2018, 6(7), 8570–8577 CrossRef CAS.
- Y. Sewsynker and E. B. Gueguim, Intelligent models to predict hydrogen yield in dark microbial fermentations using existing knowledge, Int. J. Hydrogen Energy, 2016, 41(30), 12929–12940 CrossRef CAS.
- C. Chang and A. J. Medford, Classification of biomass reactions and predictions of reaction energies through machine learning, J. Chem. Phys., 2020, 153(4), 044126 CrossRef CAS PubMed.
- I. Bonnin, R. Mereau, T. Tassaing and K. De Oliveira, One-pot synthesis of isosorbide from cellulose or lignocellulosic biomass: a challenge?, Beilstein J. Org. Chem., 2020, 16, 1713–1721 CrossRef CAS PubMed.
- G. Liang, C. Wu, L. He, J. Ming, H. Cheng, L. Zhuo and F. Zhao, Selective conversion of concentrated microcrystalline cellulose to isosorbide over Ru/C catalyst, Green Chem., 2011, 13(4), 839–842 RSC.
- A. Kamimura, K. Murata, Y. Tanaka, T. Okagawa, H. Matsumoto, K. Kaiso and M. Yoshimoto, Rapid conversion of sorbitol to isosorbide in hydrophobic ionic liquids under microwave irradiation, ChemSusChem, 2014, 7(12), 3257–3259 CrossRef CAS PubMed.
- F. Brandi and M. Al-Naji, Sustainable Sorbitol Dehydration to Isosorbide using Solid Acid Catalysts: Transition from Batch Reactor to Continuous-Flow System, ChemSusChem, 2022, 15(5), e202102525 CrossRef CAS PubMed.
- P. Sun, X. Long, H. He, C. Xia and F. Li, Conversion of Cellulose into Isosorbide over Bifunctional Ruthenium Nanoparticles Supported on Niobium Phosphate, ChemSusChem, 2013, 6(11), 2190–2197 CrossRef CAS PubMed.
- Y. Yang, Z. Ding, D. Ren, C. Shang, C. Li, F. Yang, B. Zhou, S. Hao, K. Sun and S. Lee, Dense Ru single-atoms integrated with sulfoacids for cellulose valorization to isosorbide, Mater. Today Sustain., 2023, 24, 100494 CrossRef.
- X. Yang, Z. Li, M. Guo, T. Zhao, X. Su, W. Jiang, G. Han and H. Ben, Synergistic effects of WO3 and NiCu bimetals for the One-Pot conversion of cellulose into ethylene glycol, Fuel, 2023, 341, 127560 CrossRef CAS.
- J. Zhang, F. Lu, W. Yu, R. Lu and J. Xu, Effects of alkaline additives on the formation of lactic acid in sorbitol hydrogenolysis over Ni/C catalyst, Chin. J. Catal., 2016, 37(1), 177–183 CrossRef CAS.
- I. M. Leo, M. L. Granados, J. L. G. Fierro and R. Mariscal, Sorbitol hydrogenolysis to glycols by supported ruthenium catalysts, Chin. J. Catal., 2014, 35(5), 614–621 CrossRef CAS.
- G. W. Huber, R. D. Cortright and J. A. D. Prof., Renewable alkanes by aqueous–phase reforming of biomass–derived oxygenates, Angew. Chem., 2004, 116(12), 1575–1577 CrossRef.
- G. W. Huber, J. N. Chheda, C. J. Barrett and J. A. Dumesic, Production of Liquid Alkanes by Aqueous-Phase Processing of Biomass-Derived Carbohydrates, Science, 2005, 308(5727), 1446–1450 CrossRef CAS PubMed.
- Q. Zhang, T. Jiang, B. Li, T. Wang, X. Zhang, Q. Zhang and L. Ma, Highly selective sorbitol hydrogenolysis to liquid alkanes over Ni/HZSM–5 catalysts modified with pure silica MCM–41, ChemCatChem, 2012, 4(8), 1084–1087 CrossRef CAS.
- N. Li and G. W. Huber, Aqueous-phase hydrodeoxygenation of sorbitol with Pt/SiO2-Al2O3: Identification of reaction intermediates, J. Catal., 2010, 270(1), 48–59 CrossRef CAS.
- A. V. Kirilin, A. V. Tokarev, L. M. Kustov, T. Salmi, J. Mikkola and D. Y. Murzin, Aqueous phase reforming of xylitol and sorbitol: Comparison and influence of substrate structure, Appl. Catal., A, 2012, 435, 172–180 CrossRef.
- S. Qiu, T. Wang and Y. Fang, High-efficient preparation of gasoline-ranged C5–C6 alkanes from biomass-derived sugar polyols of sorbitol over Ru-MoO3−x/C catalyst, Fuel Process. Technol., 2019, 183, 19–26 CrossRef CAS.
- C. Wang, X. Zhang, Q. Liu, Q. Zhang, L. Chen and L. Ma, A review of conversion of lignocellulose biomass to liquid transport fuels by integrated refining strategies, Fuel Process. Technol., 2020, 208, 106485 CrossRef CAS.
- M. Zhang, M. Wang, B. Xu and D. Ma, How to measure the reaction performance of heterogeneous catalytic reactions reliably, Joule, 2019, 3(12), 2876–2883 CrossRef.
|
This journal is © The Royal Society of Chemistry 2024 |
Click here to see how this site uses Cookies. View our privacy policy here.