DOI:
10.1039/D3GC03858K
(Paper)
Green Chem., 2024,
26, 2903-2911
Ethylene production: process design, techno-economic and life-cycle assessments†
Received
11th October 2023
, Accepted 26th January 2024
First published on 29th January 2024
Abstract
Replacing the steam cracking process with oxidative dehydrogenation for ethylene production offers potential energy and environmental benefits. To evaluate these possibilities, a study combining conceptual process design, techno-economic analysis, and life cycle assessments of the oxidative dehydrogenation of ethane (ODHE) for producing ethylene at an industrial scale is performed. For comparison, the conventional steam cracking process of ethane is also simulated and optimized. The techno-economic analysis results for ODHE with a boron-containing zeolite chabazite (B-CHA) catalyst, as developed in our group, demonstrate that it is economically competitive ($790 per t ethylene production) compared to the steam cracking process ($832 per t ethylene production). However, a “cradle-to-gate” life-cycle assessment shows that the ODHE process emits more greenhouse gases (2.42 kg CO2 equiv. per kg ethylene) compared to the steam cracking counterpart (1.34 kg CO2 equiv. per kg ethylene). The discrepancy between the initial hypothesis and the results arises from the significant refrigerant input required by the ODHE process to recover ethylene from byproducts such as CO, CH4, and unreacted oxygen and ethane. Further scenario analysis reveals that plausible improvements in the C2H6 conversion per pass, the selectivity to ethylene and the ratio of ethane to oxygen in the current ODHE process could render it both economically and environmentally viable as a replacement for the steam cracking process.
1. Introduction
Ethylene is widely used in the chemical industry, and serves as a fundamental building block in the petrochemical industry, with a global production capacity reaching 214 million metric tons in 2021.1,2 In the U.S., the recent expansion of ethylene production owing to the shale gas boom is influencing the energy and greenhouse gas emissions footprint of the country's chemical industry.3 Ethylene occupies a central role in the production of diverse plastics, most notably polyethylene, one of the most prevalent plastics globally. Furthermore, ethylene serves as a precursor in the synthesis of a multitude of chemicals such as ethanol, ethylene oxide, and acetaldehyde and many others.4 A range of technologies exist for ethylene production, including steam cracking (also known as thermal cracking or pyrolysis),5 catalytic cracking,6 and dehydrogenation.7 Presently, the most widely adopted method is the steam cracking of hydrocarbons. Nonetheless, the steam cracking process is remarkably energy-intensive, with its efficiency affecting the production costs of ethylene.8 This energy intensity results from the elevated reaction temperatures (>800 °C) needed to surmount the thermodynamic and kinetic barriers of this endothermic reaction.9,10 In addition, ethylene production is the second-largest contributor to greenhouse gas emissions within the chemical industry, giving rise to 1–2 tons of CO2-equivalent emissions per ton of ethylene produced.11,12 As a consequence, there is a global search for technological advancements and process optimizations that could improve the efficiency and sustainability of ethylene manufacturing.13,14
Since commercial ethylene production methods, notably the steam cracking of ethane and naphtha, have been optimized for the last eight decades—with thermal (first law) efficiencies that can reach 95%—process replacement is a formidable challenge.12 Hence, novel avenues for ethylene production are being explored, encompassing sustainable feedstocks,15,16 clean energy technologies,17,18 and advanced performance catalysts.19,20 Li et al. (2022)21 investigated bio-ethylene production pathways in China and demonstrated that indirect thermochemical synthesis (a process in which ethylene is produced through the conversion of hydrocarbons into ethylene using heat as the primary driving force) and the methanol-to-olefins process can lead to competitive minimum ethylene selling prices ($822 per t, $1061 per t) while reducing carbon emissions by 3.2% to 15.1%. Gu et al. (2022)22 reported an electrified steam cracking process designed for carbon-neutral ethylene production. Their results supported the viability of steam cracking powered by hydropower to attain carbon neutrality, factoring in technological development, economic feasibility, and environmental impact. Nonetheless, the oxidative dehydrogenation of ethane (ODHE) retains its appeal due to its minimal energy requirements and the intrinsic coke removal facilitated by the oxygen-containing feedstock.23
To date, a wide variety of vanadium and nickel oxides mixed with Mo, Nb, Mg, and Ce also catalyze the ODHE.23 Among them, M1 catalyst showed >95% ethylene selectivity and is considered very promising at the commercial scale.13,24–26 On the other hand, boron-containing catalysts also emerge as potential candidates. For example, hexagonal boron nitride (h-BN) was known for catalyzing the oxidative dehydrogenation of propane (ODHP) to propene with excellent selectivity.27 Zhou et al. reported a boron-containing MFI-type zeolite catalyst with 55% propene selectivity and 26% ethylene selectivity at 41% propane conversion. h-BN has also been utilized in ODHE:28–32 Zhou et al. reported 79% and 68% ethylene selectivity at 36% and 44% ethane conversions over activated h-BN at 575 and 590 °C,33 and Wu et al. presented 80% ethylene selectivity at 20% ethane conversion over commercial h-BN at 600 °C.34
Replacing steam cracking with oxidative dehydrogenation of ethane (ODHE) for ethylene production has numerous advantages but also shortcomings.35 Academic and industrial researchers continue to investigate the ODHE process to improve economic competitiveness. To this end, we have investigated ODHE conceptual process design, using techno-economic analysis, and life-cycle assessment for large-scale ethylene production. Specifically, we explore the use of a boron-containing zeolite chabazite (B-CHA) catalyst developed in our own laboratory. Rigorous process simulation within Aspen Plus is conducted to assess the proposed ODHE process using our experimental data for validation. To provide a point of comparison, a simulation of ethane steam cracking was also undertaken. This work represents a novel contribution as there is currently no existing research available that delves into the industrial-scale process simulation, along with economic and environmental assessments, for ODHE-based ethylene production. The findings obtained in our study demonstrate that the ODHE process is economically competitive compared to steam cracking. However, contrary to our initial hypothesis, the ODHE process results in higher carbon emissions. Nonetheless, a scenario analysis shows that improvements in the ethane conversion rate per pass, selectivity to ethylene, and the ethane-to-oxygen ratio in feedstocks offer opportunities for environmental benefits.
2. Methodology
2.1. Process design and simulation
Process flowsheets for ethylene production from both ethane steam cracking and ODHE have been developed based on published reports,36 and experimental findings from our laboratory.37 Kinetic-driven process simulations are executed using Aspen Plus v12.38 The RPlug reactor unit is employed to model both ethane steam cracking and ODHE. Due to limited experimental data, side reactions within the ODHE process are modeled using the RStoic reactor block, based on experimental conversions. The reaction kinetics for ethane steam cracking are directly taken from published works.39,40 On the other hand, the kinetic parameters for the main reaction within ODHE are derived from the experimental data reported in our lab.37
2.2. Technoeconomic analysis
A techno-economic model that combines the total capital investment and manufacturing costs of ethylene production from both ethane steam cracking and ODHE technologies was implemented under the following assumptions: a discount rate of 10%, a tax rate of 30%, a straight-line depreciation method (7 years), and an operational period of 8000 hours annually. A 20-year discounted cash flow rate-of-return analysis is executed to estimate the minimum selling price (MSP) of ethylene, which renders the net present value (NPV) of the project as zero. To facilitate optimal heat network design, the Aspen Energy Analyzer V12 is used, and the Aspen Process Economic Analyzer V12 is employed to support the technoeconomic analysis. Section 3 of the ESI† provides additional details.
2.3. Life-cycle assessment
Life-Cycle Assessment (LCA) was used for the comparison of ethane steam cracking and ODHE. A “cradle-to-gate” system boundary is adopted for the ethylene production processes, encompassing the raw material extraction, utility generation, and production stages. For each production route, the unit-specific inventory is detailed in Table S3.† Characterization data are sourced from Ecoinvent 3.9
41 and subsequently characterized for lifecycle impact assessment using the ReCiPe 2016 method.42 Section 4 of the ESI† provides more details about the LCA protocols.
3. Results and discussion
3.1. Ethane steam cracking process
The ethylene production process using steam cracking (Fig. 1) is based on the work by Ranjan et al.36 The process is comprised of three stages: (1) steam cracking: ethane and steam (3
:
1, vol%: vol%) are introduced into the cracking reactor R-1, where they undergo steam cracking at 950 °C and ambient pressure. This results in the production of ethylene as the main product along with H2 and CH4 byproducts. The yields from this reaction are: 37.7 mol% ethylene, 40.7 mol% H2, 3.3 mol% CH4, and 15.1 mol% remaining C2H6. An essential side reaction in R-1 is the cracking of C3 and C4 hydrocarbons into H2 and CH4. (2) Water removal: the product stream from R-1 contains unreacted water, which is removed through an absorption tower (T-A) utilizing triethylene glycol (TEG) at 25 °C and ambient pressure. The absorbed water is then separated, and the TEG solvent is regenerated in distillation tower T-R. Regenerated TEG is recycled to the absorption tower T-A. (3) Ethylene recovery: the dehydrated product stream is compressed using compressor C101 and cooled to −140 °C in heat exchanger E104 before entering distillation tower T-D1. In T3, the byproducts H2 and CH4 are separated from the ethylene-rich stream, which is sent for further processing. The H2 and CH4 are collected at the top of T-D1 and are directed to the flue gas network. The stream at the bottom of T-D1, containing mostly CH4 and unreacted C2H6, is fed into column T-D2 at −25 °C and 34 bar for additional separation. At the top of T-D2, an industrial-grade C2H4 product with a molar purity of 99.9% is obtained. Meanwhile, the C2H6 collected at the bottom of T-D2 is recycled back to the reactor after being mixed with make-up C2H6 and steam.
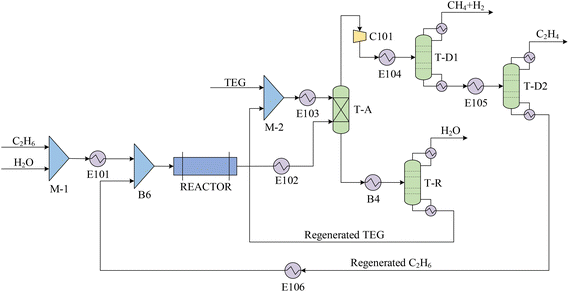 |
| Fig. 1 Process flow diagram for the ethylene production via ethane steam cracking. | |
Through a rigorous process simulation carried out in Aspen Plus V12, the production of 79.4 t h−1 C2H4 is achieved from 88 t h−1 ethane and 35 t h−1 water. Table 1 provides the key operating parameters of the main units in the steam cracking process.
Table 1 Key operating parameters of the main units in the ODHE and steam cracking processes
ODHE process |
Steam cracking process |
Unit |
T/°C |
P/bar |
Reflux ratio |
Unit |
T/°C |
P/bar |
Reflux ratio |
Reactor |
580 |
1.0 |
— |
Reactor |
950 |
4.5 |
— |
T-B |
30 |
1.0 |
— |
T-A |
40 |
1.0 |
— |
T-R2 |
30 |
1.0 |
0.3 |
T-D1 |
−140 |
30.0 |
1.0 |
T-A |
25 |
1.0 |
— |
T-R |
50 |
0.1 |
1.0 |
T-R1 |
50 |
0.3 |
5.0 |
T-D2 |
100 |
30.0 |
10.0 |
T-D1 |
−140 |
1.0 |
1.0 |
|
|
|
|
T-D2 |
−28 |
20.0 |
24.0 |
|
|
|
|
3.2. ODHE process
The ethylene production process utilizing ODHE technology (Fig. 2) comprises four primary stages: (1) oxidative dehydrogenation: ethane (20 vol%), oxygen (12 vol%), and steam (68 vol%) are introduced into reactor R-1, where the oxidative dehydrogenation of ethane occurs using B-CHA. This reaction takes place at 580 °C and ambient pressure,37 leading to ethylene production along with by-products such as H2O, CO, and CO2. The yields are as follows: 18.8 mol% ethylene, 29.7 mol% H2O, 1.19 mol% CO, 1.08 mol% CO2. The major side reaction involves the oxidation of C2H4 into CO and H2O. The data were obtained from an experimental scale with a 15 mL min−1 gas feed using a 750 mg catalyst B-CHA. (2) Dehydration and decarbonization: a flash drum F-1 operating at 25 °C and ambient pressure to condense the majority of water from the gas stream. This is followed by a decarbonization process. (3) Decarbonization and purification: absorption column T-A1 is employed to remove CO2, a byproduct, using methyldiethanolamine (MDEA) solvent. The CO2-rich stream collected at the bottom of T-A1 is directed to distillation tower T-R1 for MDEA regeneration and eventual return to T-A1, mixed with 1.4% make-up water (12.7 t h−1). Concurrently, the decarbonized stream proceeds to another absorption tower T-A2, utilizing triethylene glycol (TEG) for dehydration before progressing to the product recovery stage. (4) Product recovery: after compression in C101 and heating in heat exchanger E110, the dehydrated and decarbonized stream enters distillation column T-D1. Here, a mixture of O2, CO, and CH4 is obtained at the top and directed to the oxygen-enrichment furnace. The C2H4-rich stream is sent to distillation column T-D2 for further purification. Finally, an industrial-grade C2H4 product with a molar purity of 99.9% is collected at the top of T-D2. The unreacted C2H6, concentrated at the bottom of the column, is recycled back to the reactor after being mixed with the feedstock. Using Aspen Plus V12, the production of 91.6 t h−1 of ethylene is achieved by reacting 113 t h−1 of ethane with 298 t h−1 of oxygen. The key operating parameters of the main units in the ODHE process can also be found in Table 1.
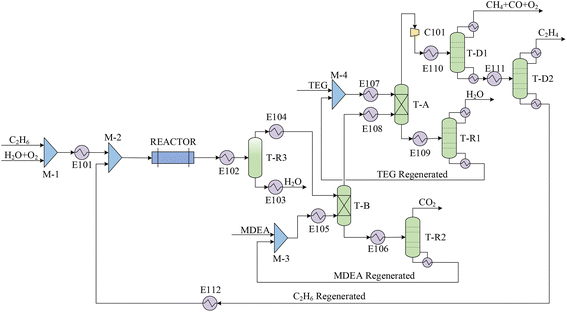 |
| Fig. 2 Process flow diagram for the ethylene production via oxidative dehydrogenation of ethane. | |
3.3. Techno-economic analysis
The ODHE catalyst and process technology (Fig. 2) demonstrates a competitive advantage with a minimum selling price (MSP) of $790 per ton of ethylene, in contrast to the steam cracking technology which leads to MSP of $832 per ton of ethylene (Fig. 3). While the total cost of manufacturing (TCM) for the steam cracking process is slightly lower at 496 million USD per year compared to its ODHE 578 million USD per year, the ODHE process has lower total capital investment (TCI), allowing for a reduced ethylene price. This is because the steam cracking process operates at 950 °C since it is an endothermic reaction, and therefore a high-cost furnace is required. On the other hand, the exothermic ODHE process operates at 580 °C, does not need a high-temperature furnace and generates over 246 t h−1 of high-pressure (HP) steam. Steam cracking demands 416.76 GJ h−1 of high-temperature energy to sustain high reaction rates. Part of this energy requirement can be covered by the fuel gas (H2 and CH4) generated alongside C2H4 during the cracking process. The favorable operating reactor temperature of the ODHE process leads to better energy efficiency, lower capital investment, and a more competitive ethylene minimum selling price.
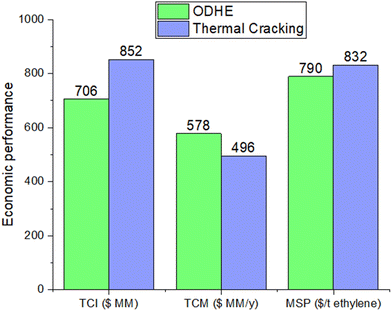 |
| Fig. 3 Cost comparison between oxidative dehydrogenation and steam cracking processes. | |
The total capital investment and manufacturing cost breakdowns for the ODHE and steam cracking processes are presented in Fig. 4(a) and (b), respectively (see Table S1† for more details). Although the cost of raw materials constitutes the major component of the total cost for both the ODHE and steam cracking technologies, the proportion of this cost in the ODHE process (39.23%) is greater than that in the steam cracking process (33.75%). This is because a higher fraction of ethane is transformed into ethylene in the steam cracking process (90.3 mol%) than in the ODHE process (80.8 mol%). This underscores the importance of high ethylene selectivity in the reactor. The second most significant contributor to the cost of the steam cracking process is other operation cost including operating labor, waste treatment, maintenance, repairs, insurance and plant overhead. For the ODHE process, utilities constitute nearly 18% cost due to the large inventory of refrigerants in the ethylene recovery stage. Thus, efficient heat integration and management strategies in the ODHE process is essential to improve its economic outlook. Table 2 compares the utility consumptions for the operating units in the ODHE and steam cracking processes.
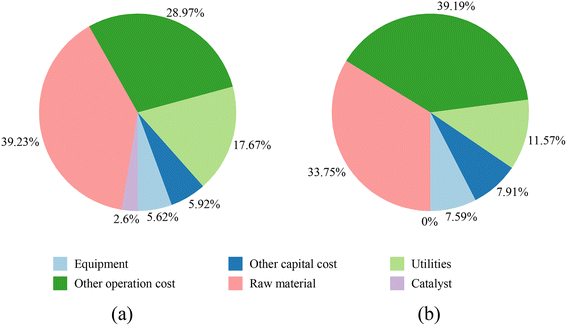 |
| Fig. 4 Cost breakdown for ethylene production via the (a) ODHE and (b) steam cracking process. | |
Table 2 Utility consumptions for the operating units in the ODHE and steam cracking processes
ODHE process |
Steam cracking process |
Unit |
Energy inputs (103 kW) |
Utility category |
Unit |
Energy inputs (103 kW) |
Utility category |
LP: low pressure; HP: high pressure; REFR L: refrigerant level. |
T-R3 |
50.8 |
LP-STEAM |
T-R |
71.3 |
HP-STEAM |
T-R2 |
73.0 |
LP-STEAM |
T-D1 |
16.8 |
REFR L-5 |
T-R1 |
204.3 |
HP-STEAM |
|
28.7 |
LP-STEAM |
T-D1 |
38.5 |
REFR L-5 |
T-D2 |
57.8 |
REFR L-1 |
51.6 |
LP-STEAM |
|
51.6 |
LP-STEAM |
T-D2 |
173.8 |
REFR L-2 |
E104 |
54.0 |
REFR L-5 |
142.6 |
LP-STEAM |
E105 |
12.1 |
LP-STEAM |
C101 |
30.0 |
ELECTRICITY |
E106 |
2.3 |
LP-STEAM |
E103 |
96.2 |
REFR L-1 |
B4 |
1.5 |
LP-STEAM |
E107 |
96.2 |
REFR L-1 |
C101 |
29.4 |
ELECTRICITY |
E108 |
9.4 |
REFR L-1 |
REACTOR |
115.8 |
FUEL GAS |
E109 |
1.6 |
LP-STEAM |
|
|
|
E110 |
134.8 |
REFR L-5 |
|
|
|
E111 |
72.0 |
LP-STEAM |
|
|
|
E112 |
34.7 |
LP-STEAM |
|
|
|
Sensitivity analysis is performed under uncertainties in catalyst costs (±50%) and other costs (±20%): ethane price, equipment expenses, utility costs, and byproduct incomes (see Fig. 5). As expected, the prices of the raw material (C2H6) predominantly contribute to the production costs across various scenarios. Other important cost factors are utility expenses, equipment operation and catalyst costs, and the price of HP steam. Similar sensitivity analyses are conducted for the steam cracking process, considering the effects of ethane price, equipment expenses, utility costs, byproducts price, including liquefied petroleum gas (LPG) and fuel gas.
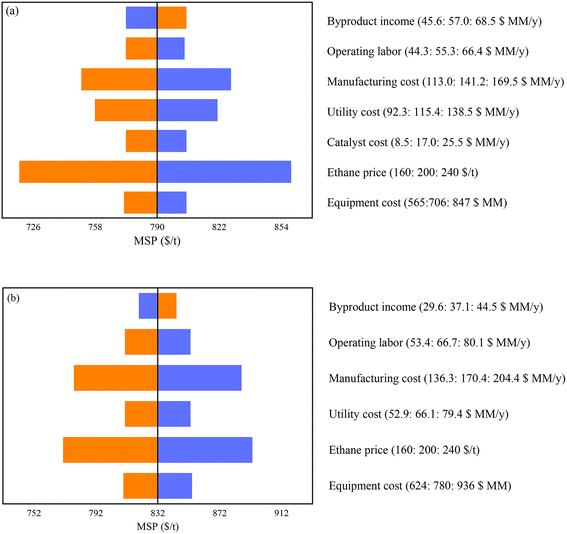 |
| Fig. 5 Sensitivity analysis on the MSP of ethylene production to ethane price, operational factors, utility costs, equipment expenses, and byproduct income via (a) the ODHE and (b) steam cracking process. | |
Monte Carlo simulations (10
000 scenarios) have been conducted, considering uncertainties in equipment costs, raw material prices, energy-related expenditures, and operating labor, manufacturing costs. The results are used to estimate the variability of the process net present value (NPV) based on a practical ethylene selling price. In this analysis, we have used the average global price of ethylene spanning from 2017 to 2022.43 The variability in the estimated NPV is depicted in Fig. 6 assuming an ethane price of $969 per t. To quantify the investment risk, we use the ratio of the cumulative frequency of NPV values falling below zero (Fig. 6) to the total simulation frequency of 10
000. The ODHE process has an investment risk of 1.9%, which is better than the value of 9.2% obtained for the steam cracking process.
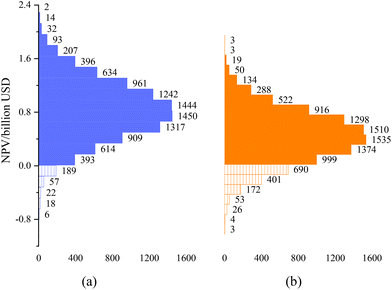 |
| Fig. 6 Net present value range based on 10 000 Monte Carlo simulations for (a) ODHE and (b) steam cracking process. | |
3.4. Life-cycle assessment
The global warming potentials (GWPs) associated with producing 1 kg of ethylene using the ODHE and steam cracking processes are 8.24 and 3 (kg CO2 equiv.), respectively. Utilities contribute to more than 71% of carbon emissions in the ODHE process, even though their contribution to the minimum selling price (MSP) of ethylene accounts for only 21%. This is the result of the large demands of steam and refrigerant in the ethylene recovery section in this process, as provided in Table 2. Consequently, the ODHE process exhibits notably higher greenhouse gas emissions compared to the steam cracking process. For the steam cracking process, 1.85 out of 3 (CO2 equiv. per kg ethylene) is contributed by the consumption of utilities. For this reason, we investigated the potential of heat integration to improve energy utilization efficiency.
Heat integration significantly reduces the carbon emissions of both ODHE and steam cracking processes. It also notably narrows the gap in environmental impact between the ODHE (2.42 kg CO2 equiv. per kg ethylene) and steam cracking (1.34 kg CO2 equiv. per kg ethylene) processes, as shown in Fig. 7. The primary contributors to the GWP of the ODHE process are: refrigeration (1.30 kg CO2 equiv. per kg ethylene), other utilities (0.22 kg CO2 equiv. per kg ethylene), ethane (1.00 kg CO2 equiv. per kg ethylene), oxygen (0.77 kg CO2 equiv. per kg ethylene), and byproduct (−0.87 kg CO2 equiv. per kg ethylene). For the steam cracking process, the GWP includes carbon emissions linked to refrigerants (0.32 kg CO2 equiv. per kg ethylene), other utilities (0.16 kg CO2 equiv. per kg ethylene), ethane (0.96 kg CO2 equiv. per kg ethylene), byproducts (−0.10 kg CO2 equiv. per kg ethylene) and others (0.0022 kg CO2 equiv. per kg ethylene). Improved separation technology is necessary to render the ODHE process environmentally competitive for replacing the conventional steam cracking approach in industrial applications.
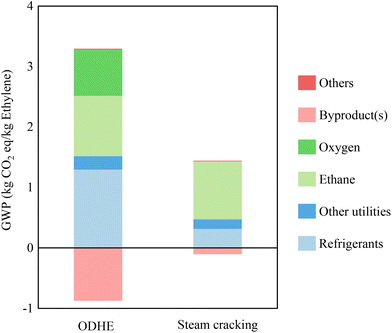 |
| Fig. 7 Global warming potential (GWP) breakdown of 1 kg ethylene produced by ODHE and steam cracking processes. | |
We identified the following areas for improvement: firstly, enhancing the ethane conversion rate and the selectivity of ethylene over other byproducts to minimize the presence of excess ethane and oxygen during ethylene recovery; secondly, reducing the ratio of oxygen-to-ethane to decrease oxygen consumption as well as minimize the excess oxygen during ethylene recovery; thirdly, replacing carbon-intensive distillation with other separation techniques, such as membranes or pressure swing adsorption, to avoid the need for large refrigerant inputs.
3.5. Scenario analysis
Although the ODHE process is economically more viable over steam cracking, it underperforms with respect to the environmental impacts. Here we will use a scenario analysis to prioritize the process elements and variables that will improve its environmental impact. Fig. 8 shows that improvement in the C2H6 conversion per pass have a much higher impact than the O2/ethane ratio. This is mainly due to reduction in refrigeration load required in the ethylene recovery stage. The ODHE process reaches a break-even point when any combination of the C2H6 conversion per pass and O2-to-C2H6 ratio (in Fig. 8) and any combination of the C2H6 conversion per pass and selectivity to C2H4 (in Fig. 9) is located at the intersection line between the curved surface and the plane corresponding to GWP = 1.34 kg CO2 equiv. per kg C2H4. This analysis provides insights into the key points on the GWP performance of ODHE technology, helping to chart the trajectory for ODHE's industrial implementation. In addition, a scenario analysis on TEA is performed to study the effect of reactor variables on the MSP of the ethylene product. As illustrated in Fig. 10, further cost reductions in producing ethylene through OHDE technology can be achieved by improving the selectivity to C2H4, optimizing the C2H6-to-steam ratio, and, in particular, increasing C2H6 conversion per pass.
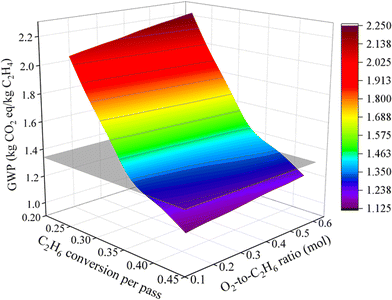 |
| Fig. 8 Scenario analysis on C2H6 conversion (per pass) and the O2-to-C2H6 ratio's impact on the environmental performance of the ODHE process. | |
 |
| Fig. 9 Scenario analysis on C2H6 conversion (per pass) and the selectivity to C2H4 impact on the environmental performance of the ODHE process. | |
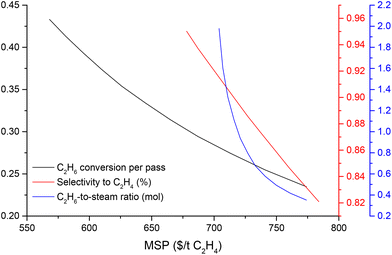 |
| Fig. 10 Scenario analysis on C2H6 conversion (per pass), the selectivity to C2H4 and C2H6-to-steam ratio impact on the MSP of ethylene in the ODHE process. | |
4. Conclusions
We have assessed the feasibility of substituting the steam cracking process with the ODHE process, utilizing a B-CHA catalyst, for industrial-scale ethylene production. TEA results demonstrate that due to a lower total capital investment, the ODHE process is already economically competitive ($790 per t ethylene production) compared to the steam cracking process ($832 per t ethylene production). However, the steam cracking process has lower refrigerant and steam requirements, leading to lower greenhouse gas emissions (1.34 kg CO2 equiv. per kg ethylene) compared to the ODHE process (2.42 kg CO2 equiv. per kg ethylene). The sensitivity analysis shows that enhancement in ethane conversion per pass in the ODHE process will greatly decrease the process environmentally impact to a point in which it can improve over the steam cracking process. In addition to improving the catalyst's performance and optimizing the reaction conditions, replacing cryogenic distillation with other separation techniques, such as membrane separation, pressure swing adsorption, solvent-based absorption, or even hybrid separation techniques, should also be a focus in the further work for improving the process's environmental performance.
In summary, the ODHE process presented and optimized here has the capability to produce ethylene at lower costs and under milder, more flexible reaction conditions. A scenario analysis shows that increasing the conversion per pass and selectivity for ethylene production could substantially enhance the environmental performance. A scenario analysis on LCA shows that increasing the conversion per pass could substantially enhance the environmental performance of the ODHE process. Meanwhile, an increase in the selectivity to ethylene and a decrease in the oxygen-to-ethane ratio in the feedstocks have the potential to positively influence the environmental performance of the ODHE process. Additionally, a scenario analysis on TEA demonstrates that improvements in C2H6 conversion per pass, selectivity to C2H4, as well as the C2H6-to-steam ratio could further lower the MSP of the ethylene product, leading to a higher competitiveness of ODHE in ethylene production. This study aims in providing a comprehensive analysis of the ODHE process and the comparison with the steam cracking for the production of ethylene in large scale. Sensitivity analysis points into the promising directions of improvement required to implement ODHE in industry.
Conflicts of interest
There are no conflicts to declare.
Acknowledgements
The authors gratefully acknowledge the financial support from NSF grants 1908982 and 2134471.
References
- The Essential Chemical Industry – online: Ethene (Ethylene), https://www.essentialchemicalindustry.org/chemicals/ethene.html, accessed 07 July 2023.
- Statista: Production Capacity of Ethylene Worldwide from 2018 to 2021, https://www.statista.com/statistics/1067372/global-ethylene-production-capacity/, accessed 03 June 2023.
- Q. Wang, X. Chen, A. N. Jha and H. Rogers, Renewable Sustainable Energy Rev., 2014, 30, 1–28 CrossRef.
-
D. Schubert, T. Gessmann and J. Kim, Boron Hydrides, Heteroboranes, and their Metalla Derivatives, 2011 Search PubMed.
- S. Sadrameli, Fuel, 2015, 140, 102–115 CrossRef CAS.
- S. Sadrameli, Fuel, 2016, 173, 285–297 CrossRef CAS.
- A. M. Gaffney, J. W. Sims, V. J. Martin, N. V. Duprez, K. J. Louthan and K. L. Roberts, Catal. Today, 2021, 369, 203–209 CrossRef CAS.
- M. Fakhroleslam and S. M. Sadrameli, Fuel, 2019, 252, 553–566 CrossRef CAS.
- J. G. Speight, Pet. Sci. Technol., 1999, 17, 445–445 CrossRef CAS.
- H. Saito and Y. Sekine, RSC Adv., 2020, 10, 21427–21453 RSC.
- M. Ghanta, D. Fahey and B. Subramaniam, Appl. Petrochem. Res., 2014, 4, 167–179 CrossRef CAS.
- Y. Gao, L. Neal, D. Ding, W. Wu, C. Baroi, A. M. Gaffney and F. Li, ACS Catal., 2019, 9, 8592–8621 CrossRef CAS.
- A. M. Gaffney and O. M. Mason, Catal. Today, 2017, 285, 159–165 CrossRef CAS.
- R. Chauhan, R. Sartape, N. Minocha, I. Goyal and M. R. Singh, Energy Fuels, 2023, 37, 12589–12622 CrossRef CAS.
- P. Haro, P. Ollero and F. Trippe, Fuel Process. Technol., 2013, 114, 35–48 CrossRef CAS.
- A. T. Penteado, M. Kim, H. R. Godini, E. Esche and J.-U. Repke, Chem. Eng. Trans., 2017, 61, 589–594 Search PubMed.
- Z. Wang, R. Shi and T. Zhang, Curr. Opin. Electrochem., 2021, 30, 100789 CrossRef CAS.
- S. Wang, K. Uwakwe, L. Yu, J. Ye, Y. Zhu, J. Hu, R. Chen, Z. Zhang, Z. Zhou and J. Li, Nat. Commun., 2021, 12, 7072 CrossRef CAS PubMed.
- A. Akah, J. Williams and M. Ghrami, Catal. Surv. Asia, 2019, 23, 265–276 CrossRef CAS.
- S. Zhu, E. P. Delmo, T. Li, X. Qin, J. Tian, L. Zhang and M. Shao, Adv. Mater., 2021, 33, 2005484 CrossRef CAS PubMed.
- H. Li, S. Zhang, J. Zhou, Z. Wang, X. Zhao and T. Qiu, Biofuels, Bioprod. Biorefin., 2022, 16, 1568–1582 CrossRef CAS.
- J. Gu, H. Kim and H. Lim, Energy Convers. Manage., 2022, 270, 116256 CrossRef CAS.
- S. Najari, S. Saeidi, P. Concepcion, D. D. Dionysiou, S. K. Bhargava, A. F. Lee and K. Wilson, Chem. Soc. Rev., 2021, 50, 4564–4605 RSC.
- D. Melzer, P. Xu, D. Hartmann, Y. Zhu, N. D. Browning, M. Sanchez-Sanchez and J. A. Lercher, Angew. Chem., Int. Ed., 2016, 55, 8873–8877 CrossRef CAS PubMed.
-
S. C. Arnold, A. M. Gaffney, R. Song and C. Y. Yeh, Google Pat., US20100256432A1, 2013 Search PubMed.
-
S. Nehlsen, Clariant Unveils Groundbreaking Catalysts Developed Jointly with Linde Engineering for Novel Ethylene Production Technology, https://www.clariant.com/en/Corporate/News/2021/10/Clariant-unveils-groundbreaking-catalysts-developed-jointly-with-Linde-Engineering-for-novel-ethylen, accessed 31 August 2023.
- J. T. Grant, C. A. Carrero, F. Goeltl, J. Venegas, P. Mueller, S. P. Burt, S. Specht, W. McDermott, A. Chieregato and I. Hermans, Science, 2016, 354, 1570–1573 CrossRef CAS PubMed.
- L. Shi, Y. Wang, B. Yan, W. Song, D. Shao and A.-H. Lu, Chem. Commun., 2018, 54, 10936–10946 RSC.
- L. Shi, B. Yan, D. Shao, F. Jiang, D. Wang and A.-H. Lu, Chin. J. Catal., 2017, 38, 389–395 CrossRef CAS.
- L. Shi, D. Wang and A.-H. Lu, Chin. J. Catal., 2018, 39, 908–913 CrossRef CAS.
- R. Huang, B. Zhang, J. Wang, K. H. Wu, W. Shi, Y. Zhang, Y. Liu, A. Zheng, R. Schlögl and D. S. Su, ChemCatChem, 2017, 9, 3293–3297 CrossRef CAS.
- C. Xu, C. Ge, D. Sun, Y. Fan and X.-B. Wang, Nanotechnology, 2022, 33, 432003 CrossRef PubMed.
- Y. Zhou, J. Lin, L. Li, X. Pan, X. Sun and X. Wang, J. Catal., 2018, 365, 14–23 CrossRef CAS.
- Z. Wu, Y. Zhou, H. Ying, J. Lin and W.-Q. Han, Chem. Phys. Lett., 2020, 746, 137294 CrossRef.
- J. Chen, Z. Sun, V. Balakotaiah and P. Bollini, Chem. Eng. J., 2022, 445, 136605 CrossRef CAS.
- P. Ranjan, P. Kannan, A. Al Shoaibi and C. Srinivasakannan, Chem. Eng. Technol., 2012, 35, 1093–1097 CrossRef CAS.
- M. J. Kuo, X. Huang, S. Kim, N. Houck, S. Bai, D. G. Vlachos and R. F. Lobo, Appl. Catal., A, 2024, APCATA-D-23-01533 Search PubMed.
-
K. I. Al-Malah, Aspen plus: chemical engineering applications, John Wiley & Sons, 2022 Search PubMed.
- K. Sundaram and G. Froment, Chem. Eng. Sci., 1977, 32, 601–608 CrossRef CAS.
- A. Tarafder, B. C. Lee, A. K. Ray and G. Rangaiah, Ind. Eng. Chem. Res., 2005, 44, 124–141 CrossRef CAS.
-
D. FitzGerald and T. Sonderegger, https://ecoinvent.org/wp-content/uploads/2022/12/Change-Report-v3.9.1.pdf, accessed 30 January 2024.
-
M. A. Huijbregts, Z. J. Steinmann, P. M. Elshout, G. Stam, F. Verones, M. D. Vieira, A. Hollander, M. Zijp and R. van Zelm, https://www.rivm.nl/bibliotheek/rapporten/2016-0104.pdf, accessed 30 January 2024.
- Statista: Price of ethylene worldwide from 2017 to 2022, https://www.statista.com/statistics/1170573/price-ethylene-forecast-globally/, accessed 15 August 2023.
Footnote |
† Electronic supplementary information (ESI) available: Catalyst characterization (Fig. S1(A–C), Table S1); experimental procedure; additional TEA assumptions and cost summary of ODHE and steam cracking process (Table S2); additional LCA assumptions and inventory data for ethylene production (Table S3) and activities for conducting life cycle impact assessment (Table S4). See DOI: https://doi.org/10.1039/d3gc03858k |
|
This journal is © The Royal Society of Chemistry 2024 |
Click here to see how this site uses Cookies. View our privacy policy here.