Pilot-scale evaluation of the sustainability of membrane desalination systems for the concentrate volume minimization of coal chemical wastewater†
Received
30th June 2023
, Accepted 31st October 2023
First published on 3rd November 2023
Abstract
The integrated process of reverse osmosis (RO) membrane and evaporative crystallization device is being implemented to target zero liquid discharge (ZLD) in the coal chemical industry. Minimizing the volume of RO concentrate (ROC) to the evaporation unit is critical to reducing the cost of the ZLD process. However, the pilot-scale evaluation of various minimization approaches for ROC volume is lacking in previous studies. Herein, the performance and cost of the vibratory shear enhanced process (VSEP), disc tube reverse osmosis (DTRO), and forward osmosis (FO) were compared for minimizing ROC in a pilot-scale study. Three scenarios were proposed first: VSEP, DTRO, and FO–RO to reconcentrate ROC and recover fresh water. Further comparisons are made between the levelized capital expenditures (CAPEX) and operational expenditure (OPEX) for the three scenarios. Results showed that the FO–RO scenario, followed by DTRO and VSEP, recovered around 90% of ROC as fresh water. FO system is more resistant to fouling than VSEP and DTRO during the reconcentrating ROC process. For a full-scale plant (2000 m3 d−1), DTRO offered the lowest CAPEX and OPEX at 0.95 USD m−3 and 1.68 USD m−3, respectively. This study provides insight into the selection of the optimal technology for designing the ZLD system.
Water impact
A side-by-side comparison of VSEP, DTRO, and FO in terms of technical performance and cost is necessary to choose the most cost-effective technology for concentrate volume minimization of coal chemical wastewater. This study provides insight into selecting the most suitable technology for brine concentration in designing a large-scale ZLD system, which has potential application for academic researchers and engineers.
|
1. Introduction
Freshwater scarcity and water quality deterioration have become global issues, and they are exacerbated by rapid urbanization and industrialization. Industrial sectors, such as the coal chemicals industry (CCI), consume large amounts of freshwater and generate vast quantities of wastewater.1 In China, water-stressed regions, such as Inner Mongolia and Ning Xia provinces, where there are abundant coal reserves but few freshwater resources, occupy the majority of CCI. Zero liquid discharge (ZLD) eliminates the pollution risk associated with wastewater discharge and maximizes water usage efficiency.2 Thus, ZLD is recommended for CCI in those areas to preserve local water resources and ecosystems.3
The current ZLD system in CCI generally includes pretreatment, reverse osmosis (RO), and evaporation crystallization unit.4 A significant amount of the total process cost is made up of capital expenditure (CAPEX) and operational expenditure (OPEX) related to the evaporation crystallization, which is proportional to feed volume. Therefore, minimizing the volume of RO concentrate (ROC) fed to the evaporator is critical to reduce the overall cost. The several-stage RO system has been applied to obtain more fresh water, while the total dissolved solids (TDS) in the last stage ROC reached 20
000–30
000 mg L−1.5 Meanwhile, organic components with high fouling potential also were concentrated in ROC.6 Consequently, the further concentration of ROC remains challenging due to the membrane fouling/scaling induced by a high concentration of retentates coupled with a diverse mix of substances present in ROC.7
Currently, the concentration technology for ROC mainly includes thermal concentration and membrane concentration. Thermal-based concentration technologies are relatively energy-intensive. Therefore, membrane technologies are generally used for ROC reduction. Several membrane technologies are attracting growing attention to reduce the brine volume fed to the evaporation crystallization unit in the ZLD,8 such as vibratory shear enhanced processing (VSEP), disc tube reverse osmosis (DTRO), forward osmosis (FO), electrodialysis (ED), membrane distillation (MD), osmotically assisted RO (OARO), and low-salt-rejection reverse osmosis (LSRRO). To generate higher turbulence at the membrane surface, torsional vibration is applied in VSEP. A high shear rate can decrease concentration polarization,9 increase permeate flux,10 and abate membrane fouling. High fluxes (50–100 L m−2 h−1 (LMH)) occurred when VSEP was used to control the deposition of colloidal silica on the membrane surface.11 VSEP has already been commercialized in recovering nutrient concentrate from pig slurry12 and reducing magnetic ion exchange concentrate volume.13 DTRO has a plate-and-frame configuration with large feed channels and a shorter flow path, which creates high turbulence, thus alleviating the membrane fouling potential. The DTRO system has been proven effective in processing salinity (TDS > 10
000 mg L−1) wastewater, such as nanofiltration concentrate14 and landfill leachate.15 Forward osmosis has also attracted attention in ROC treatment due to high salinity tolerance, low fouling tendency, and high water recovery.16 Unlike hydraulic pressure-driven RO, the concentration of saline wastewater by FO is driven by the concentration gradient between the draw solution (DS) and the feed water. FO is commonly coupled with an RO system to regenerate DS and recover the permeated water. Fouling in FO is almost reversible and can be effectively controlled by optimizing hydrodynamic operating conditions.17 Meanwhile, the fouling on the FO membrane surface can be removed easily by simple physical cleaning.18 ED is an established technology with industrial-scale applications in brackish water desalination. However, the treatment of FGD wastewater19 and cold-rolling wastewater20 with ED were investigated in lab or pilot scale recently, as well as MD towards achieving zero liquid discharge at a textile manufacturing plant21 and hypersaline brine concentration.22 Full-scale MD has not yet been reported due to scaling and wetting. In addition, emerging OARO and LSRRO have the advantages of high energy efficiency and high practicability, which are still in theoretical analysis. In order to confirm their large-scale performance and viability in pursuing ZLD, more pilot-scale studies are required because these technologies are less established compared to RO in CCI. Moreover, clear economic data on technologies for brine reduction are still missing and not fully addressed. Especially, a side-by-side comparison of VSEP, DTRO, and FO in terms of energy consumption and cost is necessary to choose the most cost-effective technology.
In this study, VSEP, DTRO, and FO systems were operated respectively at a pilot scale to further concentrate ROC for the first time. The water recovery rate and water flux of VSEP, DTRO, and FO were measured during the operating process. Then, the economic analysis of these three treatment processes was evaluated by contrasting CAPEX and OPEX. The main component of the CAPEX and OPEX was also recognized. A credible cost-reduction solution was offered in accordance with the largest cost contributor. Finally, the economic competitiveness of these emerging technologies was highlighted by comparison with thermal brine concentrators. This study will guide the construction of a full-scale ZLD process for coal chemical effluent.
2. Materials and method
2.1. ROC characteristics
Pilot-scale tests were conducted a wastewater reclamation plant for the CCI located in Ningxia, China. The wastewater reclamation plant employed chemical softening, poly-propylene fiber filter media, and ultrafiltration, followed by the two-stage reverse osmosis for water reclamation (Fig. S1†). The secondary RO concentrate was fed into the ZLD process in the wastewater reclamation plant, and the basic water qualities are provided in Table 1. The conductivity and pH were measured by a conductivity meter (DDS307, INESA) and a pH meter (PHS-3C, INESA), respectively. TDS and sulfate in the sample were quantified by gravimetric method. The concentrations of cations (Ca2+, Mg2+) and chloride were quantified by titration method. Total alkalinity was analyzed by acid–base indicator titration method. The sodium was quantified by a sodium ion meter (DWS-295F, INESA). Measurement of chemical oxygen demand (COD) was conducted using a 5B-3A multi-parameter water quality analyzer (Lianhua Technology Co., Ltd.). Anti-scalant was added into the feed at 3–5 mg L−1 prior to the pilot systems.
Table 1 Characteristics of two-stage RO concentrate
Item |
Unit |
Value |
pH |
— |
6.3 ± 0.3 |
COD |
mg L−1 |
252.8 ± 81.3 |
Ca2+ |
mg L−1 as CaCO3 |
217.0 ± 98.6 |
Mg2+ |
mg L−1 as CaCO3 |
18.9 ± 11.1 |
Total hardness |
mg L−1 as CaCO3 |
622.6 ± 247.5 |
Alkalinity |
mg L−1 as CaCO3 |
48.7 ± 20.9 |
SiO2 |
mg L−1 |
46.9 ± 22.8 |
Na+ |
mg L−1 |
10 823.9 ± 2678.0 |
Cl− |
mg L−1 |
7046.8 ± 1154.5 |
SO42− |
mg L−1 |
7111.0 ± 830.9 |
TDS |
mg L−1 |
20 868.5 ± 3878.6 |
Conductivity |
μS cm−1 |
27 813.9 ± 4847.8 |
2.2. Description of the three pilot-scale systems
2.2.1. VSEP system.
The VSEP system is a pilot-scale module manufactured by Dunwell Industrial (HOLDINGS) Co., Ltd (Hong Kong, China) (Fig. 1a). The VSEP system consists of multiple units, including the filter pack, motor shaft, and membrane. The filter pack is fitted with the annular-shaped membrane, which is composed of torsion springs and beatings and driven by the motor shaft. The membrane is flat-disk modules with an effective area of 1.54 m2. The system was operated at a constant feed pressure of 38 bar and a constant inflow of 0.6 m3 h−1 during the experiments, and the rotation frequency was ∼55 Hz regardless of the displacement. VSEP works in a semi-continuous mode, processing 50 L ROC at a time. Antiscalant was used at a dose of 5.0 mg L−1 over the operating period, according to the supplier's recommendation. Filtration occurs with the retentate stream recycled to the feed tank until the level falls to 30%. The water recovery rate of the VSEP system, as well as DTRO, was calculated according to eqn (1). Thus, the water recovery rate of the VSEP system was considered to be 70%. The remaining contents were drained into the waste tank and the vessel underwent flushing prior to the next batch. Samples of the feed and permeate were collected periodically throughout the run for subsequent chemical analysis. Detailed specifications of the elements are presented in Tables S1–S3.† | 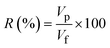 | (1) |
R is the water recovery rate of the VSEP or DTRO system, Vf is the initial feed volume, and Vp is the permeate volume.
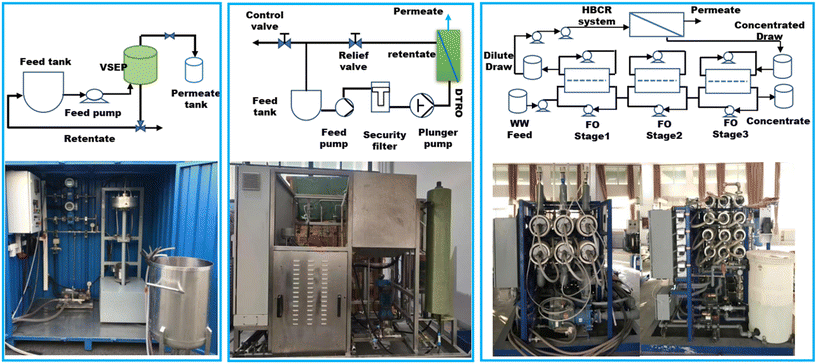 |
| Fig. 1 Schematic diagram and photograph of different scenarios, (a) VSEP, (b) DTRO, and (c) FO–RO. | |
2.2.2. DTRO system.
The pilot DTRO system was skid-mounted modules (Xiamen Jiarong Technology Co., Ltd.) (Fig. 1b). The RO retentate was divided into two streams. One stream was recycled to the feed tank, while the other was discharged into a concentrate tank. By adjusting the permeate volume and the retentate volume discharged, which was controlled by modifying the retentate control valve, the water recovery was controlled. The applied pressure of the DTRO process was between 60 and 76 bar at a recovery rate of 85%. 5 mg L−1 antiscalant was added to inhibit the scaling of the RO membrane. Experiments were performed twice, with a thorough cleaning process between each experiment. The cleaning period for VSEP and DTRO depended on the change in operational parameters of the membrane system, such as a decrease in membrane flux or an increase in operating pressure. When the membrane flux decreased by about 30% or the feed pressure continued to rise, the membrane systems required chemical washing. Chemical cleaning using NaOH solution (pH = 12–12.5) and HCl solution (pH = 1–2) was conducted every 168 h and 120 for VSEP and DTRO systems, respectively.
2.2.3. FO system.
FO pilot system (Fig. 1c) was designed and fabricated by Fluid Technology Solutions (FTS, USA). 12 spiral-wound cellulose tri acetate (CTA) based FO elements (FO CTA-8040-85, FTS Inc., USA) were used for the pilot-scale operation with an effective membrane area of 12 × 9.9 m2. Two elements stored in separated pressurized vessels were connected in serial to optimize the energy efficiency of the FO unit. 10% sodium chloride solution was used as the DS. The flow rate of feed and DS in the FO system was 1.21 m3 h−1 and 1.17 m3 h−1, respectively. During the operation process, the concentrated brine was directly sent to the next stage as feed in each FO stage, while the other part was cycled back as additional feed. After the FO unit, an RO unit with a high brine concentration and recovery (HBCR) membrane was used to regenerate the diluted DS and retrieve water. RO unit operated at a hydraulic pressure of 70–75 bar. The total design capacity of the FO pilot system was 21.8 m3 per day. The water production rate of the FO process is determined by eqn (2).23 |  | (2) |
Rf is the water recovery rate of the FO system, Vf is the initial feed volume, and Vp is the volume of liquid that permeated to the draw side.
2.3. Cost analysis of the three scenarios
An economic analysis of CAPEX and OPEX of the three systems was conducted, assuming a full-scale capacity of 2000 m3 per day and an operating time of 8640 h per year. The water quality parameters of 2-staged ROC were used as feeding water conditions. TDS of the ROC fluctuated between 20
000–25
000 mg L−1. The three systems vendors, including Dunwell Industrial (HOLDINGS) Co., Ltd (Hong Kong, China), Xiamen Jiarong Technology Co., Ltd (Xiamen, China) and Shanghai Yuanmai Environmental Technology Co., Ltd (holder of FTS solutions), gave the membrane cost data and equipment & instruments cost data. Equipment and instrument costs included the cost of flow meters, conductivity meters, pH monitors, pressure gauges, piping, valves, and pumps. The lifespans of three membrane modules are different. Therefore, in order to provide a fair comparison of three scenarios, the levelized cost of water (LCOW in USD per m3 feed wastewater) is introduced for comparative economic analysis of different schemes. The LCOW for the capital expenditure (Ccap) can be written as eqn (3):24 |  | (3) |
Ccc is the capital cost, N is the operating hours, and Q is the flow rate of the wastewater in m3 h−1. The amortization is based on the lifespan of the membrane and plant, and the interest rate is not considered here. The plant lifetime was assumed to be 20 years, and membrane replacement time was 3 or 5 years based on literature and operating experience.
The OPEX comprises the cost of membrane replacement, chemical and electricity consumption (Table 3), and the details are shown in Tables S4–S6.† The electricity price and chemical price data were given by the operator of the wastewater reclamation plant for a coal chemistry industry located in Ningxia, China. Hydrochloric acid was added to the ROC before feeding to VSEP, DTRO, and FO systems to control membrane scaling. The feed water was also dosed with antiscalant to reduce the scaling potential in the VSEP and DTRO system. Acid cleaning (1.0% w/w citric acid) and alkaline cleaning (1 mM NaOH with 0.25–1.0% w/w ethylenediaminetetraacetic acid, EDTA) were routinely performed to remove membrane fouling. The amount of chemical required for the cleaning process was calculated following the manufacturer's recommendation. VSEP and DTRO were chemically cleaned every 168 h and 336 h, respectively. Periodic hydraulic flushing was necessary for FO membrane cleaning. As the three membrane systems were equipped with automated operation and cleaning, less labor was required, and the cost could be neglected.
3. Results and discussion
3.1. Comparison of the three systems for concentrating ROC
The three pilot-scale systems were operated at a maximal water recovery rate under the premise of stable operation. The water recovery of VSEP, DTRO, and FO units are shown in Fig. 2a. The FO system operated at the highest water recovery rate of ∼90% during a 1008 h operation despite the appearance of fluctuation. The water recovery rate of the FO system fluctuated in the range of 80–100% in the first 240 h due to fluctuations in feed water conductivity (Fig. S2†). The water recovery rate decreased with the increasing conductivity in the feed, reflecting lower driving force caused by lower concentration gradients between feed water and DS. The recovery rate of the FO system became stable at 90% after 240 h operating time. In contrast, water recovery rates for the VSEP and DTRO were marginally lower (85% and 70%, respectively) than those observed in the FO system. Water permeation through membranes in VSEP and DTRO systems is driven by high hydraulic pressure. The increase in the feed conductivity reduces the water permeability. In this case, in order to ensure water permeability, the operating pressure needs to be increased. Higher water recovery needs a higher hydraulic pressure, and the rejected solute concentration in the concentrates increases. The foulant layer was more densely compacted and tightly held on the membrane under the action of high hydraulic pressure.25 Higher hydraulic pressure and concentration polarization caused the membrane to rapid and severe fouling, especially for the highly contaminated wastewater.26 Unlike pressure-driven RO processes, the osmotic pressure difference drives the movement of water across membrane in FO system. The fouling potential of the feed ROC to the FO membrane was lower than that of VSEP and DTRO membranes due to the lack of applied hydraulic pressure. Consequently, FO exceeded VSEP and DTRO in terms of water recovery and reduction of ROC in the wastewater reclamation plant for the CCI.
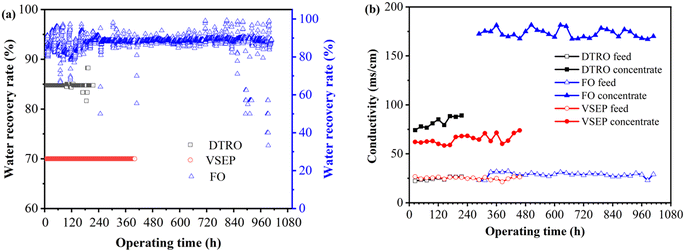 |
| Fig. 2 ROC reduction with VSEP, DTRO, and FO (a) and conductivity of VSEP, DTRO, and FO retentate (b). | |
The retentate volume reduced to 10%, 15%, and 30% of the ROC after FO, DTRO, and VSEP filtration, respectively. The membranes have high rejection of above 95% against salts. The substances in the feed were enriched in the concentrates, including salts and organic matter. The conductivity of feed and concentrate discharged from the VSEP and DTRO system was determined once a day during operational time. The conductivity data of retentate for the FO system was recorded online after the feed quality was relatively stable. As shown in Fig. 2b, the conductivity of concentrates discharged from the FO, VSEP, and DTRO systems increased by >2 folds compared to the feed conductivity. The average conductivity of the FO retentates was 174 mS cm−1, and the highest value was close to 190 mS cm−1. For VSEP and DTRO systems, the average conductivities of retentate were 82 mS cm−1 and 64 mS cm−1, respectively, which were half of that of FO retentate.
3.2. Comparison of water flux decline of VSEP, DTRO, and FO
Variations in water flux of VSEP, DTRO, and FO were evaluated under a long term of 24 h continuous operation. The decline of VSEP flux is depicted in Fig. 3a. Since the VSEP system was operated in semi-continuous mode, water flux increased and decreased periodically during VSEP operation. The recycling of retentate increased the salt content and organic concentration in the feeding solution, decreasing the net driving force across the membrane and the concentration polarization phenomenon.27 Water flux was highest at the start of the batch but reduced significantly throughout the cycle. The decline in water flux with operating time during the 192 h run is shown in Fig. 3a. Water flux decreased from 44 LMH to 24 LMH after 144 h operation (7 days). For the DTRO system, water flux was stabilized at 11 LMH before 96 h during the concentrating process and abruptly dropped to 9 LMH after 96 h, indicating the fouling of the membrane (Fig. 3b). Both the water flux of VSEP and DTRO membrane recovered after chemical cleaning with acid-alkali cleaning sequence.
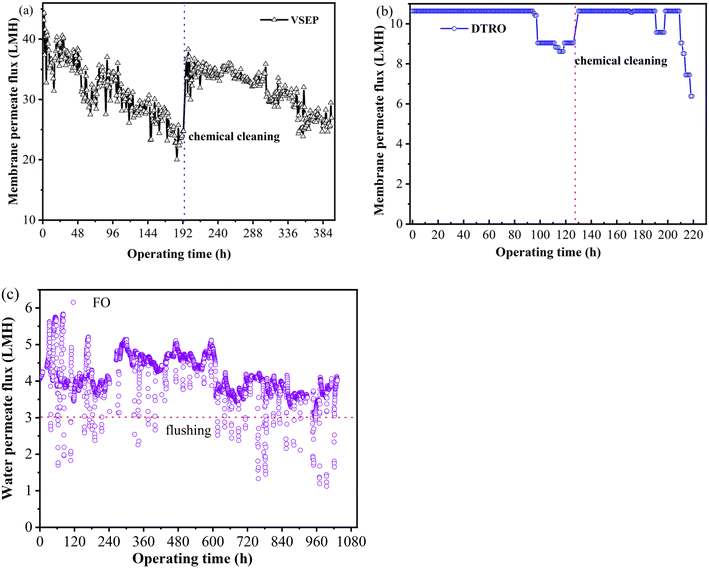 |
| Fig. 3 Water flux of VSEP (a), DTRO (b), and FO (c) during long-term operation. | |
The water flux of the FO system fluctuated with a change in feed conductivity during the initial 240 h. The feed conductivity fluctuated in the range of 10–50 mS cm−1 at the first 240 h and then stabilized at ∼25 mS cm−1 after 288 h (Fig. S2†). In the stable stage, the water flux of FO fluctuated within a narrow range of 4.3–5.1 LMH between 288 h and 672 h (Fig. 3c). It was also observed that the water flux of the FO system periodically declined to below 3.0 LMH every 24 h because of the membrane flushing with high feed flow rate every 24 h to eliminate reversible fouling on FO membrane surface. The momentary decrease in water permeate across the FO membrane resulted from hydraulic flushing. The water flux was restored after hydraulic flushing. However, this physical cleaning gradually lost its effectiveness after working for 672 h with the water flux reducing from 5.0 to 3.5 LMH. The adsorption of organic substances, scaling, or polymerization of silica colloids on the membrane surface could not be removed by high-speed flushing, which caused the drop in flux and the accompanying loss of fouling reversibility.28,29
The change of membrane flux depends on the membrane configuration, operational mode, and feed constituent. The linear motor in the VSEP system was applied to impose the axial membrane vibration and large shear rates at the membrane surface for control membrane fouling. DTRO comprises a modified RO module based on a plate-and-frame module. The special structure made it tolerant to higher pressure and less propensity to fouling, such as open channel design, short flow paths, and 180° reversal trace. A certain amount of scaling ions (Ca2+, Mg2+, and SO42−), silica, and organic matter co-exited with salts in the feed of the three membrane systems, which could induce scaling and fouling of the membrane. These constituents in the retentate of VSEP, DTRO, and FO were concentrated about 3.3, 6.6, and 10 times, respectively. Thus, the retentate from the FO system has the highest fouling potential compared to that of DTRO and VSEP. However, the water flux of VSEP and DTRO systems reduced by 30% in less than 168 h and 120 h, respectively. Calcium sulfate scaling and silica polymerization on the membrane surface of VSEP and DTRO system led the membrane flux to decrease, which could be removed by acid cleaning and alkaline cleaning, respectively. Of course, organic matter aggravated that scaling. VSEP had the highest initial water flux, followed by DTRO and FO. The membrane with higher water flux is prone to fouling. In comparison, the water flux of the FO system was maintained stable and achieved long-term stable operation (∼1008 h). Fouling and scaling were less prone to occur in the FO process since there was no hydraulic pressure-driven force. As a result, compared to pressure-driven membrane processes, less ROC pre-treatment and less regular chemical cleaning were required for FO membranes.
DTRO is extensively utilized for the treatment of leachate and FGD.30 However, the applications of DTRO in other industrial wastewater are not yet widespread. In contrast, the commercialization of the VSEP system has not been implemented. Moreover, the salinity range of feedwater to DTRO or VSEP system does not exceed 50
000 mg L−1. Unlike the RO, the FO system can be utilized for treating brine with a TDS of up to 100
000 mg L−1. The higher salinity limits and lower fouling propensity extend the applicability of FO to wastewater with high salinity or fouling potential. Large-scale implementation of FO has been reported in industrial wastewater, such as oil and gas, mining, agriculture and water supply, textile, pulp and paper, and pharmaceutical.31
3.3. Cost comparison of the three scenarios
The economic cost of the scenario has a great impact on the final decision of which technology/scenario should be adopted in a project besides technical performance. CAPEX and OPEX of VSEP, DTRO, and FO–RO scenarios were evaluated in this part, along with a sensitivity analysis of the cost. These costs were based on a 2000 m3 d−1 of ROC feed.
3.3.1. Comparison of levelized CAPEX and OPEX.
Levelized CAPEX and OPEX of the three scenarios are shown in Fig. 4a and b, respectively. CAPEX for all three scenarios consisted of the cost of membrane, equipment, and instruments. Levelized membrane costs of VSEP, DTRO scenario, and FO–RO scenario were 1.15 USD per m3, 0.65 USD per m3, and 0.80 USD per m3, respectively, accounting for about 77%, 68%, and 64.5% of their total levelized CAPEX. Generally, the cost of equipment and instruments accounted for 29.6–55% of the membrane cost due to longer lifespan, which was 0.34 USD per m3, 0.30 USD per m3, and 0.44 USD per m3 for VSEP, DTRO, and FO–RO scenarios, respectively. Levelized CAPEX of the DTRO scenario was the lowest, with 0.95 USD per m3, compared to VSEP and DTRO scenarios due to lower membrane, equipment, and instrument costs. The high cost of the VSEP module, which was 0.085 MUSD, was to blame for the higher membrane cost of VSEP scenario. For the FO–RO scheme, the low water flux and the large number of membrane elements led to the high cost of the membrane, equipment, and instruments. Moreover, the requirement for a RO system to reconcentrate the diluted DS accounted for 40% of the overall CAPEX in the FO–RO scenario (Table 2). Steel and equipment costs were also increased due to the need for tanks, additional pressure vessels, and larger pressure exchangers relative to conventional RO.
 |
| Fig. 4 Levelized CAPEX (a) and OPEX (b) of three scenarios. | |
Table 2 Levelized costs for CAPEX of the three scenarios
Item |
VSEP |
DTRO |
FO–RO |
Membrane cost (M USD) |
2.54 |
1.43 |
FO |
1.77 |
RO |
1.16 |
Membrane lifespan (year) |
3 |
3 |
5 |
CAPEX for membrane modules (USD per m
3
)
|
1.15
|
0.65
|
0.80
|
Equipment & instrument cost (M USD) |
5.0 |
4.34 |
6.5 |
Equipment & instrument lifespan (year) |
20 |
20 |
20 |
CAPEX for equipment & instrument (USD per m
3
)
|
0.34
|
0.30
|
0.44
|
Total CAPEX (USD per m
3
)
|
1.49
|
0.95
|
1.24
|
Table 3 OPEX of the three pilot-scale systems
Parameter |
VSEP |
DTRO |
FO–RO |
Energy consumption |
Specific electricity consumption (kWh m
−3
)
|
6.5 |
10 |
20.5 |
Electricity price (USD per kWh) |
0.09 |
0.09 |
0.09 |
Energy cost (USD per m
3
)
|
0.59
|
0.9
|
1.85
|
Membrane replacement |
Membrane element cost (M USD) |
254 |
143 |
293.54 |
Life span (year) |
3 |
3 |
5 |
Feed water per year (m3 per year) |
734 400 |
734 400 |
734 400 |
Membrane replacement cost (USD per m
3
)
|
1.15
|
0.65
|
0.80
|
Chemical reagent consumption |
Acid cost (USD per m
3
)
|
0.046
|
0.046
|
0.046
|
Antiscalant cost (USD per m
3
)
|
0.032
|
0.032
|
—
|
Chemical cleaning washing cost (USD per m
3
)
|
0.052
|
0.052
|
—
|
Draw solution (USD per m
3
)
|
—
|
—
|
0.185
|
Total OPEX (USD per m
3
)
|
1.87
|
1.68
|
2.88
|
Fig. 4b shows the calculated OPEX for the VSEP, DTRO, and FO–RO systems normalized to the total water treated. OPEX consisted of membrane replacement cost, electricity and chemical consumption costs. ∼90% of OPEX for the three scenarios was made up of the first two items. OPEX of DTRO scenarios was the lowest, followed by VSEP and FO–RO scenarios. Their OPEX were 1.68 USD per m3, 1.87 USD per m3, and 2.88 USD per m3, respectively. Due to the higher price of the VSEP module, the OPEX of the VSEP solution was higher than that of the DTRO, so the module replacement cost was higher. Unlike the VSEP scenario, a large number of FO/RO membrane elements incurred higher membrane replacement costs compared to DTRO scheme. In addition to membrane replacement, significantly high electricity costs were specifically responsible for the higher OPEX of the FO–RO scenario. RO system used to re-concentrate diluted draw solution consumed 75% of overall electricity with 15 kW h m−3.
For VSEP and DTRO, chemical cost includes adding acid and antiscalant to the feed wastewater in addition to frequent chemical cleaning. Supplementation of sodium chloride to the DS was the major part of the chemical consumption cost in FO–RO due to its draw solute loss through reverse salt diffusion. If sodium chloride is crystallized in a zero-liquid discharge plant, the cost of supplementing sodium chloride will be cut from the OPEX. The feed constituent had a larger impact on the OPEX than CAPEX for the three systems. Complex water quality easily caused scaling and fouling of VSEP and DTRO membranes. The chemical cleaning cycle of the membrane was 168 h and 336 h for VSEP and DTRO. In contrast, the FO–RO system operated for 1008 h without chemical washing. Frequent chemical cleaning will undoubtedly reduce the life of the membrane and increase the membrane replacement cost for VSEP and DTRO systems.
In addition, the cost of the three concentration technologies and other technologies, including ED, OARO, and LSRRO were compared to evaluate economic competitiveness. Table 4 presents only the OPEX and SEC of the three technologies in this work and other technologies from the literature due to the lack of CAPEX data. OPEX data from the literature were selected based on similar feed salinity to make the comparison fair. Indeed, non-standardized process and financial parameters (e.g., pump efficiencies, permeability coefficients, membrane costs) still caused the OPEX to be more optimistic or more conservative. The OPEX of ED for reducing desulfurization wastewater at a salinity of 30
000 mg L−1 was 1.1 $ per m3, which seemed lower than the OPEX for DTRO. Indeed, the OPEX of ED was only the electricity consumption and did not include the replacement cost of electrodes and membranes. The SEC of ED was 17.5 kWh, near to that of FO–RO. Thus, if the replacement cost of electrodes and membranes is considered, the OPEX for ED was higher than that of VSEP and DTRO. The OPEX and SEC for OARO and LSRRO were lower than VSEP, DTRO, and FO–RO systems. Although OARO and LSRRO have economic advantages over the three systems for concentrating media-salinity feed water, the two emerging technologies lack commercialization cases for desalination or concentration reduction, and even pilot studies are very limited.
Table 4 Comparison of OPEX and SEC in this work with other technologies reported in the literature
Technology |
Feed salinity (mg L−1) |
Recovery (%) |
LCOW ($ per m3) |
SEC (kWh m−3) |
Ref. |
VSEP |
20 868.5 ± 3878.6 |
70 |
1.87 |
6.5 |
This work |
DTRO |
80 |
1.68 |
10 |
FO–RO |
90 |
2.88 |
20.5 |
ED |
30 000 |
60 |
1.11 |
17.5 |
32
|
OARO |
25 000 |
70 |
0.4 |
2.6 |
33
|
LSRRO |
35 000 |
70 |
0.7 |
3.9 |
34
|
3.3.2. Sensitivity analysis.
The membrane cost of the VSEP scenario is higher than that of DTRO both in levelized CAPEX and OPEX due to the sharply high price of the VSEP module. Similarly, high CAPEX and OPEX of FO–RO contributed to a large amount of membrane elements required because of the low water flux of the FO membrane. Besides, a large number of FO membrane elements incur an increase in equipment and instrument cost. Therefore, the impact of the VSEP price drop and FO membrane flux increase on CAPEX and OPEX were assessed. Fig. 5a and b presents the levelized CAPEX and OPEX of the VSEP scenario with a decrease in VSEP price. Both decrease with reduced VESP price. When the VSEP price reduces by 45%, the CAPEX of VSEP scenario will decrease to 0.97 USD per m3, which will be comparable to the DTRO scenario; OPEX will decrease to 1.35 USD per m3, which will be even lower than that of DTRO scenario. It is evident that both levelized CAPEX and OPEX are sensitive to the cost of the membranes. Similarly, the levelized CAPEX and OPEX of the FO–RO scheme decrease with an increase in FO flux. When the water flux of the FO membrane increases from 5 LMH to 10 LMH, the levelized CAPEX is lower than that of the DTRO scheme and continually decreases as the water flux of the FO membrane continues to increase. However, both the levelized CAPEX and OPEX of the FO–RO scenario reduce slightly when the water flux of FO membrane increases from 20 LMH to 30 LMH. A flux threshold of 30 LMH was defined for FO economic viability.35 The OPEX of FO–RO scenario is still much higher than that of the DTRO scheme. This is because the electricity consumption by regeneration of diluted DS with RO system is a major part of OPEX besides FO membrane replacement. Thus, an optimal RO system is required to make the FO–RO scenario comparable to the DTRO system besides enhancing FO membrane flux.
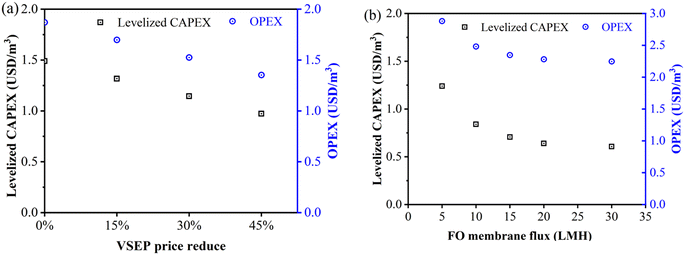 |
| Fig. 5 Impact of VSEP module price reduction on levelized CAPEX and OPEX of VSEP scenario (a); impact of FO membrane flux increase on CAPEX and OPEX of FO–RO scenario (b). | |
4. Implication
Many high-polluting/water-consuming industries are moving toward ZLD as a result of intensified freshwater scarcity and stricter environmental regulations on wastewater discharge. Incorporation of RO and mechanical vapor compressor (MVC) into ZLD systems improves energy and cost efficiencies. Recently, VSEP, FO, and DTRO have emerged as alternative ZLD technologies to further concentrate ROC volume to MVC. In this study, the DTRO scenario was second only to the FO–RO scenario in terms of ROC reduction, freshwater recovery, and fouling resistance. Both levelized CAPEX and OPEX of the DTRO scenario were 23% and 42% lower than that of FO–RO, far lower than the CAPEX and OPEX of MVC. Due to the extensive use of stainless steel and titanium for corrosion resistance, the specific CAPEX of MVC/MED (0.15 M USD per m3 h−1) was twice that of the DTRO scenario (0.07 M USD per m3 h−1). In addition, water treatment cost and energy consumption for the MEE-MVR system was 7.67 USD per m3,36 which was 4 times more than OPEX of the DTRO scenario. Therefore, DTRO in ZLD train offered a technologically and economically feasible solution for high saline wastewater reduction in CCI, which also could be extended to flue gas desulfurization wastewater in thermal power plants. The final cost can also be reduced by using solar or wind power to reduce electricity costs as well as scaling up the plant. It would become more cost-effective when the benefits of selling freshwater and salt are considered.
Nowadays, there are commercial TFC FO membranes with high water flux on the market, such as HTI, Oasys, and Porifera, whose water fluxes have been greatly increased from ∼10 to 30–40 LMH.37 Increasing water flux would decrease the number of membrane elements, thus reducing the cost of membrane, equipment, and instruments. Furthermore, reducing the electricity consumption of recovery freshwater from diluted DS is vital to decreasing OPEX in the FO–RO scenario. Without excessively high hydraulic pressures (≤70 bar), Wang et al. have developed a novel staged RO technology using a low-salt-rejection membrane to produce hypersaline brine (234 g L−1 NaCl).38 Thus, with the progress in the FO membrane and the emergence of a low-energy DS regeneration system, FO–RO may become a potential solution for further reduction of ROC volume in the future.
The selection of the most available technology for concentrate volume minimization depends mainly on the characteristics of RO concentrate, product water quality, energy consumption, and cost. By evaluating the performance of DTRO in wastewater treatment in terms of operating performance and operational costs, it was found that DTRO performed well in wastewater purification and concentration. However, it is noteworthy that the installation of DTRO might increase overall investment and operational cost, which depends on the specific design of the configuration for different wastewater types. In summary, if a high concentration of wastewater is desired, it is suggested to adopt FO–RO, otherwise DTRO process can be adopted.
5. Conclusions
In this study, three pilot-scale hybrid membrane systems have been adopted to reduce the secondary ROC from a CCI wastewater reclamation plant. The ROC reduction, water recovery rate, and flux change of VSEP, DTRO, and FO were compared. Subsequently, an economic analysis was conducted to evaluate the costs of the three systems. Key findings from the current study are highlighted as follows:
(1) VSEP, DTRO, and FO pilot units operated stably at the maximum water recovery rate of 70%, 85%, and ∼90% for reduction secondary ROC, respectively. The permeate produced by the three scenarios all met the regulation of cooling water in coal chemical factories.
(2) FO outperformed VSEP and DTRO in terms of the resistance of membrane fouling. The water flux of the FO system did not decline until 672 h of operation, while that of VSEP and DTRO reduced by 30% after 168 h and 120 h of operation, respectively.
(3) The DTRO scenario has the lowest CAPEX and OPEX, followed by the VSEP and FO–RO scenarios. The DTRO is more cost-effective than the evaporation unit. DTRO is currently proven to have a technological and financial advantage over VSEP and FO–RO scenarios.
(4) Membrane cost was the main part of CAPEX and OPEX for the three scenarios. The sensitivity analysis showed that the VSEP price was the most critical factor in terms of the economic feasibility of the VSEP scenario. When the price of the VSEP module reduces by 45%, VSEP will be comparable to DTRO in cost. For the FO–RO scenario, CAPEX will be lower than that of DTRO if the water flux of the FO membrane increases to 10 LMH. Further reduction in power consumption is required to reduce the OPEX of FO–RO to that of DTRO by reconcentrating diluted draw solution.
Author contributions
Fayuan Chen: methodology, validation, formal analysis, investigation, data curation, visualization, funding acquisition, writing – original draft. Linnan Ma: validation, formal analysis, visualization. Zhong Zhang: formal analysis, writing – review & editing. Xiao Wang: writing – review & editing. Xiaolong Wang: investigation, validation, data curation. Qinghong Wang: resources. Chunmao Chen: supervision, writing – review & editing. Linyu Jiang: conceptualization, methodology. Xianhui, Li: formal analysis, funding acquisition, writing – review & editing.
Conflicts of interest
There are no conflicts to declare.
Acknowledgements
The study is supported by the Guangdong Basic and Applied Basic Research Foundation (2020A1515110716), Science and Technology Planning Project of Guangdong Province (2021A0505110013), and Science Foundation of China University of Petroleum, Beijing (No. ZX20220091). The authors thank Dr Yi-Hsueh Chuang from National Chiao Tung University for his suggestions and grammar corrections.
References
- J. Shi, W. Huang, H. Han and C. Xu, Review on treatment technology of salt wastewater in coal chemical industry of China, Desalination, 2020, 493, 114640 CrossRef CAS.
- A. Panagopoulos and K.-J. Haralambous, Minimal Liquid Discharge (MLD) and Zero Liquid Discharge (ZLD) strategies for wastewater management and resource recovery – Analysis, challenges and prospects, J. Environ. Chem. Eng., 2020, 8, 104418 CrossRef CAS.
- R. Xiong and C. Wei, Current status and technology trends of zero liquid discharge at coal chemical industry in China, J. Water Process Eng., 2017, 19, 346–351 CrossRef.
- H. Ma, H. Wang, C. Tian, L. Wang, W. Yuan, Y. Qi, H. Ma, Z. Chao and W. Lv, An integrated membrane- and thermal-based system for coal chemical wastewater treatment with near-zero liquid discharge, J. Cleaner Prod., 2021, 291, 125842 CrossRef CAS.
- D. Blair, D. T. Alexander, S. J. Couperthwaite, M. Darestani and G. J. Millar, Enhanced water recovery in the coal seam gas industry using a dual reverse osmosis system, Environ. Sci.: Water Res. Technol., 2017, 3, 278–292 RSC.
- A. B. Schantz, B. Xiong, E. Dees, D. R. Moore, X. Yang and M. Kumar, Emerging investigators series: prospects and challenges for high-pressure reverse osmosis in minimizing concentrated waste streams, Environ. Sci.: Water Res. Technol., 2018, 4, 894–908 RSC.
- S. Kum, X. Tang and H. Liu, Treatment of brackish water inland desalination brine via antiscalant removal using persulfate photolysis, Environ. Sci.: Water Res. Technol., 2023, 9, 1137–1146 RSC.
- M. Yaqub, M. N. Nguyen and W. Lee, Treating reverse osmosis concentrate to address scaling and fouling problems in zero-liquid discharge systems: A scientometric review of global trends, Sci. Total Environ., 2022, 844, 157081 CrossRef CAS PubMed.
- V. Contreras-Jácquez, J. M. Virgo-Cruz, J. García-Fajardo, E. Obregón-Solís, J. C. Mateos-Díaz and A. Asaff-Torres, Pilot-scale nanofiltration vibratory shear enhanced processing (NF-VSEP) for the improvement of the separation and concentration of compounds of biotechnological interest from tortilla industry wastewater (nejayote), Sep. Purif. Technol., 2022, 300, 121921 CrossRef.
- T. Zsirai, H. Qiblawey, M. J. A-Marri and S. Judd, The impact of mechanical shear on membrane flux and energy demand, J. Membr. Sci., 2016, 516, 56–63 CrossRef CAS.
- A. Subramani, J. DeCarolis, W. Pearce and J. G. Jacangelo, Vibratory shear enhanced process (VSEP) for treating brackish water reverse osmosis concentrate with high silica content, Desalination, 2012, 291, 15–22 CrossRef CAS.
- A. Herrera, G. D'Imporzano, E. Clagnan, A. Pigoli, E. Bonadei, E. Meers and F. Adani, Pig Slurry Management Producing N Mineral Concentrates: A Full-Scale Case Study, ACS Sustainable Chem. Eng., 2023, 11, 7309–7322 CrossRef CAS.
- J. Leong, J. Tan, A. Heitz and B. P. Ladewig, Use of vibratory shear enhanced processing to treat magnetic ion exchange concentrate: A techno-economic analysis, Desalination, 2016, 383, 46–52 CrossRef CAS.
- X. Jing, J. Yuan, D. Cai, B. Li, D. Hu and J. Li, Concentrating and recycling of high-concentration printing and dyeing wastewater by a disc tube reverse osmosis-Fenton oxidation/low temperature crystallization process, Sep. Purif. Technol., 2021, 266, 118583 CrossRef CAS.
- C. Wu and Q. Li, Characteristics of organic matter removed from highly saline mature landfill leachate by an emergency disk tube-reverse osmosis treatment system, Chemosphere, 2021, 263, 128347 CrossRef CAS PubMed.
- B. G. Choi, M. Zhan, K. Shin, S. Lee and S. Hong, Pilot-scale evaluation of FO-RO osmotic dilution process for treating wastewater from coal-fired power plant integrated with seawater desalination, J. Membr. Sci., 2017, 540, 78–87 CrossRef CAS.
- M. Ahmed, R. K. Alambi, G. Bhadrachari, S. Al-Muqahwi and J. P. Thomas, Design and optimization
of a unique pilot scale forward osmosis integrated membrane distillation system for seawater desalination, J. Environ. Chem. Eng., 2023, 11, 109949 CrossRef CAS.
- C. Lee, T.-T. Nguyen, R. S. Adha, H. K. Shon and I. S. Kim, Influence of hydrodynamic operating conditions on organic fouling of spiral-wound forward osmosis membranes: Fouling-induced performance deterioration in FO-RO hybrid system, Water Res., 2020, 185, 116154 CrossRef CAS PubMed.
- X. Zhang, C. Zhang, F. Meng, C. Wang, P. Ren, Q. Zou and J. Luan, Near-zero liquid discharge of desulfurization wastewater by electrodialysis-reverse osmosis hybrid system, J. Water Process Eng., 2021, 40, 101962 CrossRef.
- G. Jiang, H. Li, M. Xu and H. Ruan, Sustainable reverse osmosis, electrodialysis and bipolar membrane electrodialysis application for cold-rolling wastewater treatment in the steel industry, J. Water Process Eng., 2021, 40, 101968 CrossRef.
- N. Dow, J. Villalobos García, L. Niadoo, N. Milne, J. Zhang, S. Gray and M. Duke, Demonstration of membrane distillation on textile waste water: assessment of long term performance, membrane cleaning and waste heat integration, Environ. Sci.: Water Res. Technol., 2017, 3, 433–449 RSC.
- R. Schwantes, L. Bauer, K. Chavan, D. Dücker, C. Felsmann and J. Pfafferott, Air gap membrane distillation for hypersaline brine concentration: Operational analysis of a full-scale module–New strategies for wetting mitigation, Desalination, 2018, 444, 13–25 CrossRef CAS.
- R. Jalab, A. M. Awad, M. S. Nasser, J. Minier-Matar and S. Adham, Pilot-scale investigation of flowrate and temperature influence on the performance of hollow fiber forward osmosis membrane in osmotic concentration process, J. Environ. Chem. Eng., 2020, 8, 104494 CrossRef CAS.
- U. Caldera, D. Bogdanov and C. Breyer, Local cost of seawater RO desalination based on solar PV and wind energy: A global estimate, Desalination, 2016, 385, 207–216 CrossRef CAS.
- M. Xie, J. Lee, L. D. Nghiem and M. Elimelech, Role of pressure in organic fouling in forward osmosis and reverse osmosis, J. Membr. Sci., 2015, 493, 748–754 CrossRef CAS.
- F. A. Siddiqui, Q. She, A. G. Fane and R. W. Field, Exploring the differences between forward osmosis and reverse osmosis fouling, J. Membr. Sci., 2018, 565, 241–253 CrossRef CAS.
- A. Altaee, A. Sharif, G. Zaragoza and A. F. Ismail, Evaluation of FO-RO and PRO-RO designs for power generation and seawater desalination using impaired water feeds, Desalination, 2015, 368, 27–35 CrossRef CAS.
- Y. Chun, F. Zaviska, S.-J. Kim, D. Mulcahy, E. Yang, I. S. Kim and L. Zou, Fouling characteristics and their implications on cleaning of a FO-RO pilot process for treating brackish surface water, Desalination, 2016, 394, 91–100 CrossRef CAS.
- Y. Kim, S. Li and N. Ghaffour, Evaluation of different cleaning strategies for different types of forward osmosis membrane fouling and scaling, J. Membr. Sci., 2020, 596, 117731 CrossRef CAS.
- Z. Zhang, Y. Wu, L. Luo, G. Li, Y. Li and H. Hu, Application of disk tube reverse osmosis in wastewater treatment: A review, Sci. Total Environ., 2021, 792, 148291 CrossRef CAS.
- L. Francis, O. Ogunbiyi, J. Saththasivam, J. Lawler and Z. Liu, A comprehensive review of forward osmosis and niche applications, Environ. Sci.: Water Res. Technol., 2020, 6, 1986–2015 RSC.
- W. An, J. Zhao, J. Lu, Y. Han and D. Li, Zero-liquid discharge technologies for desulfurization wastewater: A review, J. Environ. Manage., 2022, 321, 115953 CrossRef CAS PubMed.
- T. V. Bartholomew, N. S. Siefert and M. S. Mauter, Cost Optimization of Osmotically Assisted Reverse Osmosis, Environ. Sci.: Water Res. Technol., 2018, 52, 11813–11821 CAS.
- A. A. Atia, J. Allen, E. Young, B. Knueven and T. V. Bartholomew, Cost optimization of low-salt-rejection reverse osmosis, Desalination, 2023, 551, 116407 CrossRef CAS.
- G. Blandin, A. R. D. Verliefde, C. Y. Tang and P. Le-Clech, Opportunities to reach economic sustainability in forward osmosis–reverse osmosis hybrids for seawater desalination, Desalination, 2015, 363, 26–36 CrossRef CAS.
- V. C. Onishi, A. Carrero-Parreño, J. A. Reyes-Labarta, E. S. Fraga and J. A. Caballero, Desalination of shale gas produced water: A rigorous design approach for zero-liquid discharge evaporation systems, J. Cleaner Prod., 2017, 140, 1399–1414 CrossRef CAS.
- R. Valladares Linares, Z. Li, S. Sarp, S. S. Bucs, G. Amy and J. S. Vrouwenvelder, Forward osmosis niches in seawater desalination and wastewater reuse, Water Res., 2014, 66, 122–139 CrossRef CAS.
- Z. Wang, A. Deshmukh, Y. Du and M. Elimelech, Minimal and zero liquid discharge with reverse osmosis using low-salt-rejection membranes, Water Res., 2020, 170, 115317 CrossRef CAS PubMed.
|
This journal is © The Royal Society of Chemistry 2024 |
Click here to see how this site uses Cookies. View our privacy policy here.