DOI:
10.1039/D3CS00495C
(Tutorial Review)
Chem. Soc. Rev., 2024,
53, 9-24
3D-hosted lithium metal anodes
Received
31st August 2023
First published on 20th November 2023
Abstract
Lithium metal anodes are an appealing choice for rechargeable batteries due to their exceptionally high theoretical capacity of about 3860 mA h g−1. However, the uneven plating/stripping of lithium metal anodes leads to serious dendrite growth and low coulombic efficiency, curtailing their practical applications. The 3D scaffold/host strategy emerges as a promising approach that concurrently mitigates volume changes and dendrite growth. This review provides an overview of the regulating mechanisms behind scaffold/host materials for dendrite-free applications, tracing their historical development and recent progress across five key stages: material texture selection, lithiophilic modification, structural design, multi-strategy integration, and practical implementation. Additionally, scaffold/host materials are categorized based on their material texture, with a thorough examination of their respective advantages and drawbacks. Furthermore, this tutorial outlines the obstacles and complexities associated with implementing scaffold/host strategies. Finally, the determining factors that affect the electrochemical performances of scaffold/host materials are discussed, along with possible design criteria and future development prospects. This tutorial aims to provide guidance for researchers on the design of advanced scaffold/host materials for advanced Li metal anodes for batteries.
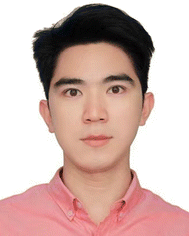
Xin He
| Xin He has been an Assistant Professor at Hunan University (China) since 2022. He obtained his PhD from Nankai University in 2021 under the supervision of Prof. Jun Chen. His current research focuses on metal anodes, metal–air batteries, solid electrolytes and halogen batteries. |
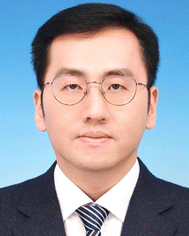
Kai Zhang
| Kai Zhang received his PhD from Nankai University in 2015 and worked as a postdoctoral scholar at Dongguk University during 2015–2019. He has started his independent research career as a full Professor at Nankai University in 2019. His research focuses on the design of advanced electrode materials and electrolytes for lithium/sodium-ion batteries and the analysis of their electrochemical processes. |
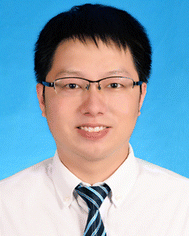
Zhiqiang Zhu
| Zhiqiang Zhu received his PhD from Nankai University in 2015 and worked as a postdoctoral fellow at Nanyang Technological University during 2015–2019. He started his independent research career as a full Professor at Hunan University in 2019. His research focuses on the design of novel secondary battery materials and devices, including lithium/sodium-ion batteries, aqueous zinc-ion batteries, and organic batteries. |
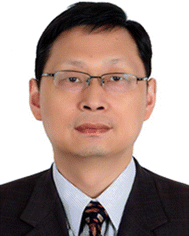
Zhangfa Tong
| Zhangfa Tong received his PhD from Beijing University of Chemical and Technology in 1991. Then, he started his independent research career as a full Professor at Guangxi University. In 2006, he was a visiting professor at the University of Waterloo and the University of Ottawa. His research focuses on energy materials and chemical process intensification. |
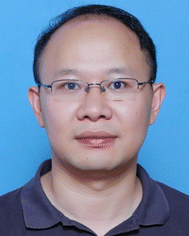
Xiao Liang
| Xiao Liang received his PhD from the Shanghai Institute of Ceramics, Chinese Academy of Sciences in 2012 under the supervision of Prof. Zhaoyin Wen and worked as a postdoctoral scholar with Prof. Linda F. Nazar at the University of Waterloo during 2012–2017. In 2017, he started his independent research career as a full Professor at Hunan University. His main research interests include new chemistries and materials for high energy density batteries, such as halogen-based batteries, Li–S batteries, and solid-state batteries. |
Key learning points
(1) The benefits and challenges of Li metal-based batteries.
(2) Regulatory mechanisms of scaffold/host strategies for dendrite free lithium metal anodes.
(3) History, classifications, and physicochemical characteristics of scaffold/host materials.
(4) Advantages and drawbacks of different types of scaffold/host materials and composite Li anode preparation methods.
(5) Design criteria and development trends for scaffold/host materials.
|
1. Introduction
With the development of modern society, the demand for more high-energy-density renewable devices is sharply increasing.1–3 Lithium-ion batteries (LIBs) as the most successful batteries have been widely used in various fields; however, their energy density has almost reached the critical limit after many years of research.4–6 The intercalation chemistry characteristic of LIBs is the primary limiting factor for pursuing high energy, and one of the related problems is the low-specific-capacity of carbon-based anode materials.7,8 Thus, it is commonly believed that novel higher energy density battery chemistries beyond Li-ions are in urgent need of development.9,10
Lithium metal anodes (LMAs) are a promising potential solution, owing to their ultrahigh theoretical capacity of ∼3860 mA h g−1 and the lowest redox electrode potential (−3.04 V vs. the standard hydrogen electrode).11 LMAs operate via a different mechanism from traditional graphite anodes, involving a simple conversion between Li metal and Li+ without intercalation chemistry.12 This feature makes LMAs a vital material for next-generation high-energy batteries, which have garnered significant interest among researchers. Fig. 1a shows that commercial LIBs reached the highest specific energy of about 300 W h kg−1 in 2023, which pales in comparison to ∼1700 W h kg−1 for petrol. However, replacing graphite-based anodes with Li metal-based anodes can bolster the specific energy of Li–LiMn2O4 (Li–LMO), Li–S, and Li–air batteries to 440, 650, and 950 W h kg−1, respectively.13–15 This significant advantage in energy density makes LMAs prospective candidates for next-generation batteries.16 Nonetheless, the practical deployment of LMAs in batteries remains challenging due to some disadvantages, such as low coulombic efficiency (CE), poor cycling stability, and risk of thermal run-away and even fire/explosion. The above issues mainly stem from infinite volume change of the anode and uneven plating/stripping of Li+ during battery operation, which very easily cause the rupture and rebirth of the solid electrolyte interphase (SEI), and dendrite growth. These problems will give rise to the sustained loss of Li and electrolyte and lead to the formation of dead Li, resulting in low CE and battery failure,17–20 as shown in Fig. 1b. In addition, lithium metal's intrinsic reactivity and dendrite growth also increase the likelihood of thermal run-away and fire/explosion.
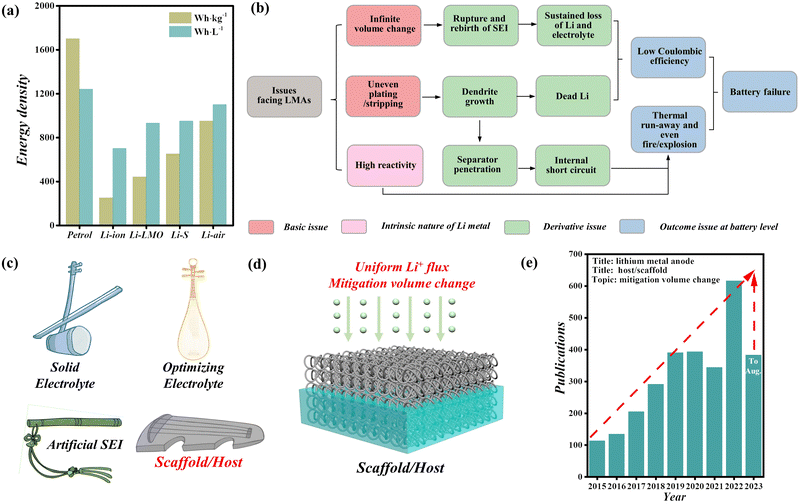 |
| Fig. 1 (a) The energy density of petrol and typical Li-ion or Li metal batteries. (b) The challenges of Li metal batteries including low coulombic efficiency and risk of thermal run-away and even fire/explosion. (c) The solving strategies of Li metal anodes for infinite volume changes and dendrite growth. (d) The scaffold/host strategy for the Li metal anode. (e) The related publications of scaffold/host strategies for Li metal anodes. | |
To address the aforementioned issues of LMAs, various strategies have been proposed, including the utilization of solid electrolytes, optimization of electrolytes, creation of an artificial SEI, and implementation of 3D scaffold/host methods (as illustrated in Fig. 1c).21–34 A few of the above strategies have made some progress towards the suppression of dendrites, but are still far from satisfying the requirements for practical applications of LMAs. It is worth noting that the scaffold/host strategy is deemed as the only method that can mitigate the volume change and inhibit dendrite growth simultaneously.35–39 This is owing to its porous structure that provides room for Li+ deposition and lithiophilic modification for decreasing the nucleation barrier and achieving uniform deposition of Li+ flux, as shown in Fig. 1d. These advanced materials hold great potential for overcoming longstanding challenges associated with lithium metals, such as dendrite growth and capacity loss. By incorporating various scaffold/host strategies, researchers have made significant strides in enhancing the performance and safety of Li metal anodes, as will be summarized in this review. These innovations have opened new avenues for the development of high-energy-density batteries, with implications for diverse applications ranging from electric vehicles to grid storage systems.
The scaffold/host strategy has attracted more and more attention from scientific workers in recent years. According to literature statistics based on the title about LMAs and scaffolds or hosts, the number of related published papers has exceeded 2870 since the start of 2015 and still maintains a growth trend (Fig. 1e). This indicates that the scaffold/host strategy has great potential applications for LMAs in batteries. However, there are only three related reviews about the Li scaffold/host strategy.40–42 In addition, these reviews still lack some important parts, such as the developmental stages and tendency of scaffolds/hosts, the detailed working mechanisms of scaffolds/hosts for free-dendrites, and their possible design criteria. These aspects are crucial for guiding the future design of advanced scaffolds/hosts.
Therefore, in this review, we conduct a synthetic analysis of the regulating mechanism of scaffolds/hosts for dendrite-free growth and discuss its developmental history and recent key advancements in this area. The working mechanisms of scaffolds/hosts can be summarized into four points: (1) The 3D porous scaffold/host decreases the local current density and increases Sand's time, resulting in delayed dendrite formation; (2) the modified scaffold/host reduces nucleation barriers and promotes uniform deposition through element doping or alloying; (3) the modified scaffold/host can change the composition of the SEI and facilitate uniform Li+ deposition; (4) the scaffold/host with a designed structure can induce preferential Li+ deposition at the bottom (e.g. a lithiophilic gradient structure) or horizontal deposition (e.g. an egg roll structure). We further analyze the scaffold/host's developmental stages, including material texture selection, lithiophilic modification, structure design, multi-strategy combination, and practicality. Additionally, we classify scaffolds/hosts based on their materials into three categories: carbon, metals, and polymers and evaluate their respective advantages and disadvantages. Then, we briefly outline the challenges and difficulties faced in using scaffold/host strategies.
Finally, we discuss the effect of physicochemical characteristics of scaffolds/hosts on electrochemical performance and provide possible design criteria and development tendencies for future scaffold/host designs. Our review aims to provide valuable guidance for researchers on the scaffold/host design.
2. Working mechanisms of scaffolds/hosts
The scaffold/host strategy is initially intended to provide enough space for Li+ deposition to mitigate volume changes and prevent SEI breakage. For instance, a fixed reversible areal capacity of 1.0 mA h cm−2 requires Li plating/stripping of about 5 μm thick Li metal.43–45 The tremendous volume change of Li metals creates huge interfacial pressure fluctuations and presents serious engineering challenges for batteries. Therefore, the scaffold/host must possess sufficient porous structures to effectively relieve these problems. According to the latest reports, Song's group prepared a lithiophilic matrix with polyacrylic acid (PAA) coating showing near-zero volume change upon cycling.46 Other related scaffolds/hosts also exhibited small volume change values (<10%).47–56
For the scaffold/host strategy, based on the success of mitigation of volume change, researchers simultaneously started to focus on the mechanisms behind the scaffold/host working to inhibit Li dendrite growth. Before delving into these mechanisms, it is important to understand how Li dendrites form. After examining related studies, three main factors can be classified as influencing Li dendrite growth: the space-charge factor,57,58 the deposition matrix factor,59–61 and the SEI film factor.62–66
To date, the space-charge model proposed by Prof. J.N. Chazalviel is the most widely accepted explanation for the growth of dendrites.57 This model puts forward the idea that dendrites are caused by the space-charge layer in the low concentration electrolyte. When the concentration of Li+ at the metal anode surface drops to zero with the increase of current density, dendrite nucleation occurs. This process is referred to as Sand's behavior, and the time is also called Sand's time (τ) for the concentration of Li+ dropping to zero, as shown in Formula (1).
| 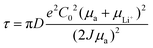 | (1) |
where
μa,
μLi+,
C0 and
J are anionic and Li
+ mobilities, initial Li
+ concentration and current density, respectively.
D is the ambipolar diffusion coefficient, which is related to the diffusion coefficients and mobilities of Li
+ cation and anion.
(1) Based on the above Sand's time model, we can know that Li dendrites will be formed under the conditions of high current density or low ionic diffusion coefficients. Therefore, the first working mechanism of scaffolds/hosts for free dendrites is decreasing local current density and increasing Sand's time through its porous structure, as shown in Fig. 2a. For instance, if the scaffold/host possesses a specific surface area of about 100 cm2 mg−1 and a mass density of about 100 mg cm−3, it can provide an actual surface area of 104 cm2 for a nominal 1 cm2 electrode. At a current density of 1 mA cm−2, the local current density of the Li+ deposition on the scaffold/host is reduced to about 0.1 μA cm−2, and the corresponding τ (Sand's time) increases by a factor of 108.
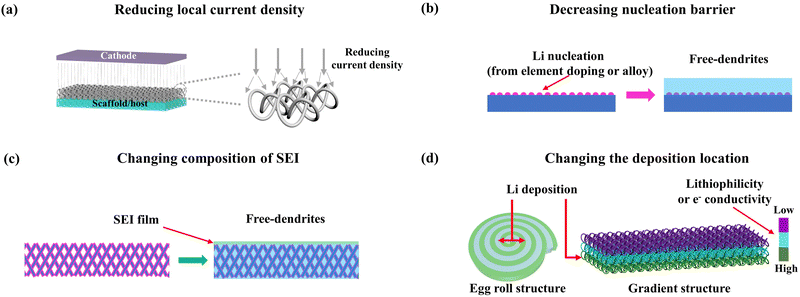 |
| Fig. 2 The working mechanism of scaffold/host strategies for lithium anodes towards dendrite suppression and interfacial regulation. (a) The 3D porous scaffold/host for reducing local current density and increasing Sand's Time. (b) The modified scaffold/host by element doping or alloying for decreasing the nucleation barrier and uniform deposition. (c) The modified scaffold/host for changing the composition of the SEI, resulting in enhanced properties. (d) The scaffold/host with a designed structure for changing the deposition location. | |
(2) The deposition matrix has an important effect on the deposition behavior of Li+. Therefore, the second working mechanism of the scaffold/host is modifying it by element doping or alloying to decrease the nucleation barrier and induce uniform deposition, as shown in Fig. 2b. A lower nucleation barrier will accelerate Li+ deposition and decrease polarization, resulting in smaller particle sizes and more two-dimensional Li metal deposition.60,67 This initial Li+ deposition morphology has a significant impact on subsequent deposition. Therefore, researchers focus on improving the lithiophilic level of scaffolds/hosts. One of the normal modifications is doping elements, and scholars screen out the ideal elements by calculating the binding energies between doping elements and Li atoms. Another one is alloying, researchers screen out the elements of a Li alloy through a phase diagram, such as Zn, Ag, Al, and so on.68–72
(3) The formation of lithium dendrites is not only dependent on the diffusion and mobility of Li+ and anions in the electrolyte but also strongly related to the SEI film, which is the only pathway for Li+ transport.46,73,74 During cycling, the huge volume change of the Li metal anode and the instability of the SEI film may lead to the rupture of the SEI film, and the resulting cracks will become hot spots for electrochemical deposition forming tip effect to induce dendrite generation.75–77 Furthermore, the intrinsic characteristics of the SEI film also have an important influence on the morphology of lithium deposition.78–82 According to the classic mosaic model of SEI films, the various compositions of SEI have different transfer rates of Li+ and are also not distributed homogeneously, which leads to the uneven Li+ flux on the surface of the SEI film and aggravate the inhomogeneous deposition resulting in the formation of dendrites. Therefore, the third working mechanism of the scaffold/host is modifying it to alter the composition of SEI, as shown in Fig. 2c. The content change in SEI originates from the side reactions between the modification of scaffolds/hosts and Li+ or electrolyte. The increase of N or F content in SEI can accelerate Li+ transportation and induce uniform deposition. For example, the F-terminated Ti3C2Tx leads to the formation of LiF-rich SEI.82
(4) The final working mechanism of the scaffold/host is designing the structure, primarily for changing the deposition location of Li+ to ensure the safety of batteries, as shown in Fig. 2d. The location of Li dendrites on the anode has a crucial role in battery safety, and only dendrites on the side of the membrane can easily lead to short circuits. The common design approach is to induce Li+ preferentially towards the bottom of the anode by using a gradient structure. Another approach is to prompt Li+ to deposit horizontally by using an egg structure.
3. Development of scaffolds/hosts
The development of typical scaffold/host materials for lithium metal anodes is sketched out as shown in Fig. 3. These dates correspond to the first published development of typical scaffolds/hosts. The group of Prof. Guo first prepared a 3D Cu current collector (Cu/Li, material 1) with a submicron skeleton and high electroactive surface area for offering sufficient room to regulate Li+ deposition resulting in free-dendrites and well electrochemical performance in 2015.20 The 3D current collector-based Li anode can operate stably for more than 600 hours and has a low voltage hysteresis. It can be regarded as a preliminary prototype of the scaffold/host strategy. That same year, the group of Prof. Cui formally brought forward the concept of a scaffold/host strategy to mitige volume changes and reported a layered Li-reduced graphene oxide (rGO/Li, material 2) composite anode by the melting-diffusion method.11 The rGO/Li exhibits eminent mechanical flexibility, small dimension changes, low overpotential (∼80 mV at 3 mA cm−2), and a flat voltage profile during cycling.
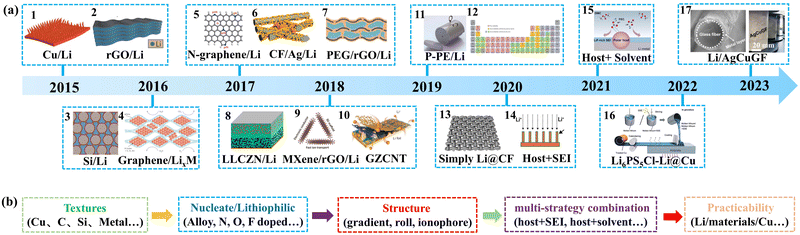 |
| Fig. 3 (a) The development of scaffold/host materials for lithium metal anodes. The first published scaffold/host for each year was selected as the representative. (b) The development history of the scaffold/host can be summarized and divided into five stages. Materials 1–17 in (a) are reproduced with permission from ref. 20 (Copyright 2015, Nature Publishing Group), ref. 11 (Copyright 2016, Nature Publishing Group), ref. 83 (Copyright 2016, Natl. Acad. Sciences Publishing Group), ref. 84 (Copyright 2017, Nature Publishing Group), ref. 85 (Copyright 2017, Wiley Publishing Group), ref. 86 (Copyright 2018, Elsevier Publishing Group), ref. 87 (Copyright 2017, Science Publishing Group), ref. 88 (Copyright 2018, Natl. Acad. Sciences Publishing Group), ref. 89 (Copyright 2018, Wiley Publishing Group), ref. 90 (Copyright 2018, Nature Publishing Group), ref. 91 (Copyright 2019, Science Publishing Group), ref. 92 (Copyright 2019, Nature Publishing Group), ref. 93 (Copyright 2020, Wiley Publishing Group), ref. 95 (Copyright 2020, Wiley Publishing Group), ref. 96 (Copyright 2022, Elsevier Publishing Group), ref. 97 (Copyright 2021, Wiley Publishing Group) and ref. 98 (Copyright 2023, Wiley Publishing Group), respectively. | |
After achieving this outstanding performance, the group of Prof. Cui explored other scaffold/host materials in 2016, such as the silicon-coated porous carbon framework (C/Si/Li, material 3)83 and the freestanding graphene/LixM foil (material 4, M = Si, Sn, or Al, namely the materials that can form alloys with Li).84 The C/Si possesses a high conductive surface area and exhibits admirable battery performance with a small interfacial impedance and a stable voltage profile with a low overpotential (<90 mV at 3 mA cm−2) during cycling. As for graphene/LixM, it can be extremely stable in the air on account of its distinct structure in which graphene encapsulates a mass of LixSi nanoparticles and shows excellent cyclability for more than 400 cycles with 98% capacity retention in half batteries.
At this stage (from 2015 to 2016), scientists explored the possibility and electrochemical performance of different materials for inhibiting dendrites, such as Cu-based (material 1), carbon-based (materials 2 and 4), silicon-based (material 3), Ni-based and other metal-based materials. This phase can be summarized as the texture selection stage.
The group of Prof. Zhang used a graphene-based scaffold with nitrogen functional groups (N-graphene/Li, material 5), such as pyridinic-N and pyrrolic-N, to guide the uniform deposition of Li+ ions in 2017.85 In the same year, the group of Prof. Zhang prepared a silver-coated carbon fiber scaffold (CF/Ag/Li, material 6) based composite LMA by the melting diffusion method.86 The CF/Ag/Li‖Li batteries exhibit excellent cycling stability performance at a high current density of about 10 mA cm−2 and a large deposition capacity of about 10 mA h cm−2 and can run stably for more than 160 cycles at low overpotential.
At this stage (in 2017), scientists studied the lithiophilic modification methods for decreasing the nucleation barrier and inducing uniform deposition. The common methods are elements doping (material 5, such as N, O, F, and so on) and alloying (material 6). This phase can be called the lithiophilic modification stage.
To resolve the high interfacial resistance and low area capacity in lithium metal based solid-state batteries, the group of Prof. Cui prepared the 3D porous Li-rGO composite anode incorporating a flowable interphase by thermal infiltration of PEG-LiTFSI (PEG/rGO/Li, material 7).87 This flowable interfacial layer can snap to the solid electrolyte and adapt to the volume deformation all the time. The PEG/rGO/Li‖LiFePO4 solid-state full cells exhibit a high-capacity retention of about 93.6% over 300 cycles at 3 mA cm−2 and an operating temperature of about 80 °C. To improve the deposition behavior of LMA in solid-state batteries, the group of Prof. Hu synthesized a garnet-type ion-conductive host with a Cu substrate (LLCZN/Li, material 8) in 2018.88 The 3D structure of the LLCZN host can induce Li+ ions to deposit from the bottom for inhibiting the growth of dendrite. The LLCZN based solid-state Li anode can stably run over 300 hours under 0.5 mA cm−2 and 1.0 mA h cm−2 with a small overpotential, which is superior to other reported ceramic-based Li anodes. This novel design of scaffold's structure for the Li metal anode becomes more realistic for the practical application of solid electrolytes. In the same year, the group of Prof. Luo first prepared a 2D MXene (Ti3C2) based scaffold for a high-rate Li metal anode (MXene/rGO/Li, material 9).89 It exhibits excellent Li+/electron transport kinetics and high lithiophilicity due to the abundance of functional groups (–OH, –O and –F), which result in good cycling stability and low overpotential at a current density of about 10 mA cm−2. This work demonstrated that the non-carbon based 2D material (MXene) is also one of the potentially promising materials for the scaffold/host of the Li metal anode.
After the stages of materials texture selection and lithiophilic modification, researchers focussed on structural design of scaffolds/hosts for inhibiting Li dendrite growth. The group of Prof. Mai prepared the lithiophilic–lithiophobic gradient interfacial layer (GZCNT, material 10) for a high cycling stable lithium metal anode.90 This scaffold is composed of the bottom lithiophilic zinc oxide/carbon nanotube (ZnO/CNT) layer and the top lithiophobic CNT layer. The lithiophilic–lithiophobic structure can effectively induce lithium ions to preferentially deposit at the bottom of the GZCNT scaffold for inhibiting the dendrite growth and ensure ultralong-term stable cycling. The results show that the cycle and rate performances of 10 cm2 GZCNT-coated Li pouch symmetry cells and Li–S batteries have been significantly improved.
The group of Prof. Cui designed and synthesized a composite lithium electrode with egg roll structure (P-PE/Li, material 11) for inducing the lithium ions preferentially horizontal deposit for suppression of dendrite growth in 2019.91 The composite electrode was prepared so that the thin porous polyethylene (PE) layer was fitted onto Li foil, then pressed tightly and rolled and cut into round disks. The mesoscale composite anode exhibits excellent electrochemical performances, such as long cycling life and low polarization at high current density in both symmetric and full batteries. In the same year, the group of Prof. Guo classified and explored the wettability of each element in the periodic table for molten lithium metal (material 12).92 The feasible chemical strategy is proposed for adjusting the wetting behavior of molten lithium metal and is applicable to various substrates, and a series of ultrathin lithium electrodes (10–40 μm) are prepared with the aid of a functional organic coating or an elemental additive.
At this stage (from 2017 to 2019), researchers explored the ion-conductive design of the scaffold/host to fit in all-solid-state batteries (materials 7 and 8), and the structural design for changing the deposition location for inhibiting dendrite growth, such as a gradient structure for preferential deposition at the bottom (materials 10 and 11) and an egg roll structure for the horizontal direction. This phase can be deemed as the structure design stage.
Significant progress in mitigating volume changes and suppressing dendrite growth has been made using the strategies involving material texture selection, lithiophilic modification and structural design stages. However, the high cost and complex preparation of scaffolds still inhibit their practical application. Herein, some researchers started working on the simplified preparation of scaffolds/hosts with high electrochemical performance by using cheap ingredients. The group of Prof. Luo reported a simplified modification strategy for tuning the wettability of hydrophilic and hydrophobic carbon scaffolds/hosts for liquid lithium through mild surface ozonolysis and ammoniation methods.93 Based on this strategy, a lightweight Li@carbon film (Li@CF, material 13) anode was prepared and exhibited long-term cycling stability performance and rate capability in the full cell.
In addition, the inhomogeneous Li deposition during cycling is a complex coupling process, which is largely determined by an uneven distribution of current density and running temperature, Li+/electron transport kinetics, and lithiophilicity (nucleation barrier or local potential).94 Therefore, it is hard to completely overcome dendrite growth using a single scaffold/host strategy. Scientists began to work on the multi-strategy combination based on scaffolds/hosts, such as optimizing electrolytes or engineering artificial protection layers. The group of Prof. Gong prepared a 3D porous Cu current collector and in situ generated a Li2S layer on its surface as an artificial SEI (Li2S-SEI@Cu, material 14).95 The results indicated that the Li2S SEI can balance the migration rate of Li+ and electrons and passivate the Cu scaffold. This Li2S-SEI@Cu exhibited ultra-long cycling stability over 500 cycles at 1 mA cm−2 in a symmetric battery and superior stability and rate performance in a Li2S-SEI@Cu/Li ‖ LiFePO4 full battery. It means that this multi-strategy combination based on scaffolds/hosts can produce high-performance Li metal anodes. The group of Prof. Huang used the synergistic effect of a 3D scaffold/host and solvent molecules to improve the uniformity of Li deposition through the polar interaction of electrospinning polyacrylonitrile (ELPAN) host and fluoroethylene carbonate (FEC) solvent molecules (Li/ELPAN, material 15).96 This polar interaction can induce the formation of the LiF-rich SEI on the surface of the Li/ELPAN composite electrode.
At this stage (from 2020 to 2021), researchers explored the multi-strategy combination for inhibiting dendrites, such as host-combined SEI strategy (material 14) and host-combined solvent modification (material 15). This may be the trend for further development and design due to the complexity of Li deposition. This phase can be called the multi-strategy combination stage.
However, the scaffold/host-based lithium anodes still face many challenges on the way to practical applications, such as lithium pulverization, associated loss of electrical contact and poor mechanical strength. The group of Prof. Chen synthesized an antipulverization and high-continuity lithium metal composite electrode with a handful of solid-state-electrolyte nanoparticles and a Cu foil (Li6PS5Cl-Li@Cu, material 16).97 The results indicated that the embedded Cu current collector in the Li6PS5Cl-Li@Cu anode not only enhances the mechanical strength but also improves the efficient charge transfer among active lithium filaments, resulting in well electrode structural integrity and electrical continuity. This Li6PS5Cl-Li@Cu anode exhibited a high average coulombic efficiency of about 99.6% over 300 cycles at 1 mA cm−2. In view of the facile process and robustness, this composite lithium electrode shows great application potential. This work also demonstrated that the Cu current collector plays a significant role in enhancing the mechanical strength of the composite anode. However, the Cu current collectors of lithium batteries do not contribute to the storage capacity. Thus, decreasing the weight of Cu foil can effectively increase the energy density of batteries. The group of Prof. Zheng reported a new 3D metallic glass fiber fabric (MGFs, Li-AgCuGF, material 17) current collector with a super-lightweight (2.9–3.2 mg cm−2) and flexibility suitable for roll-to-roll electrode fabrication.98 The results indicated that MGFs show outstanding electrochemical stability, fire resistance and high strength. As a result, the replacement of metal foils by MGFs can effectively improve the gravimetric energy densities of lithium batteries by about 9–18%. The GMF based symmetrical cell and full cells (Li/AgCuGF||LCO/NiGF) can maintain excellent cycle life for more than 10
000 and 1000 cycles, respectively, without significant performance decays. Therefore, the MGFs show great commercial application potential for replacing metal foil current collectors due to the cheap raw materials and simple production process in a wide variety of energy storage industries.
At this stage (from 2022 to 2023), researchers explored the practical applications of the scaffold/host through the combination of a Cu foil current collector and scaffold materials for improving antipulverization, high-continuity (material 16) and mechanical strength and energy density (material 17). This marks the scaffold/host step into the commercialization exploration phase, which can be called the practicability stage.
Therefore, the development history of scaffolds/hosts can be summarized and divided into five main stages: materials texture selection, lithiophilic modification, structure designing, multi-strategy combination and practicality, as shown in Fig. 3b.
4. Classification of scaffolds/hosts
In order to clearly understand the advantages/disadvantages of different scaffolds/hosts, we synthetically divided the strategy into three categories (carbon materials, metal materials and polymer materials) according to the main material types, as shown in Fig. 4.
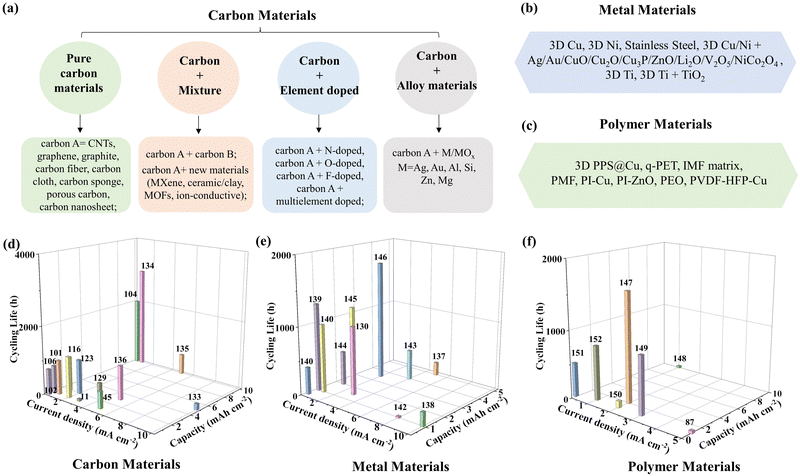 |
| Fig. 4 The classification of scaffolds/hosts from material aspects and their electrochemical performances. (a) carbon materials, (b) metal materials and (c) polymer materials. The cycling life and operation parameters of typical (d) Carbon-based,11,45,101,102,104,106,116,123,129,132–136 (e) metal-based130,137–146 and (f) polymer-based scaffolds/hosts in symmetric batteries.87,147–152 | |
4.1 Carbon-based materials
The carbon-based materials can be further subdivided into pure carbon materials, carbon combined mixture, carbon materials with elements doped, and carbon materials combined alloy (Fig. 4a). (1) First, the most common pure carbon scaffolds/hosts are CNTs,99 graphene,100 graphite,101 carbon fiber,102 carbon cloth,103,104 carbon sponges,105 porous carbon106 and carbon nanosheets,107 and so on. (2) The second one is a pure carbon materials combined mixture, and the mixture can be another pure carbon materials or new materials, such as MXene,89,108–110 ceramic/clay,18,42,111 MOFs and some ion-conductive.21,112–114(3) The third one is pure carbon materials modified with lithiophilic elements (such as N, O, F) or multi-elements.85,115–124 (4) The last one is pure carbon materials modified with alloy materials (M/MOx, M = Ag, Au, Cu, Si, Zn, Co, Sn, and so on).125–131 These categories possess diverse structural attributes, which subsequently confer specific performance advantages.
It is worth noting that the structure, specific surface area and surface functional groups, conductivity and mechanical properties of a low-cost carbon-based scaffold/host are easily regulated during the preparation process. In addition, carbon materials possess an advantageous lower mass density than other materials, which is beneficial to increasing the active Li capacity of scaffold/host-based composite anodes on account of the pursuit of high-energy batteries. But it is worth noting that the feature of carbon-based scaffolds/hosts about high surface area, although conducive to reducing local current density according to Sand's law, has aggravated a series of side reactions due to high electrode–electrolyte interfacial area resulting in lots of consuming of Li metals and the low CE. In addition, the lithiation may impair the mechanical properties of carbon-based scaffolds/hosts, which will further affect the cycling stability of composite anodes. Therefore, we should put our endeavors into designing and constructing high Li capacity of scaffolds/hosts with excellent mechanical and electrochemical properties. For example, the combination of a carbon-based host and a Cu foil is one of the effective strategies to enhance the mechanical strength of composite anode, as shown in material 17.
4.2 Metal-based materials
As for the metal texture, the common scaffolds/hosts are 3D Cu, 3D Ni, stainless steel, 3D Cu or Ni combined with lithiophilic metal materials (Ag, Au, CuO, Cu2O, Cu3P, ZnO, Li2O, V2O5, NiCo2O4), 3D Ti and 3D Ti combined with TiO2, and so on (Fig. 4b).137,139–142,153–161 In addition, the single lithium alloy materials can be also fabricated into scaffolds/hosts. Among these, the Li+ ions can integrate into lithiophilic metal crystals to form a lithiation alloy phase (such as Li–Sn, Li–Ag, Li–Zn, Li–Mg, Li–Si, Li–Ge, Li–Ga, Li–Cu, Li–B, and so on).162–167 Such in situ formation of 3D active alloys represents an efficient method in inhibiting lithium dendrite growth. It is worth noting that the introduction of lithium alloy can effectively increase the Li+ diffusion coefficients to enhance migration kinetics, and lower the reaction activity between composite anodes with electrolyte and improve the stability of anode in air or even humid environments.
Generally, the metal-based scaffold/host possesses the advantages of high electronic conductivity, chemical–physical and electrochemical stability, satisfactory mechanical properties, low processing cost, and easy large-scale preparation. However, excluding alloy, the amount of metal elements is lithiophobic, which easily increases the energy barrier of Li nucleation and results in dendrite growth. Moreover, the mass densities of metal-based scaffolds/hosts are higher than other materials, which lowers the Li loading capacity of composite anodes and is unfavorable for the requirement of high energy density lithium metal batteries. Therefore, we should devote resources to developing high Li capacity, lightweight and high specific surface area metal-based scaffolds/hosts.
4.3 Polymer materials
As for polymer materials, the common scaffolds/hosts are 3D PPS@Cu,147 IMF matrix,148 PVDF-HFP-Cu,149 q-PET,150 PI-Cu,151 PMF,152 PI-ZnO,168 and PEO, and so on (Fig. 4c). It should be noted that the nonconducting polymer matrix must be attached to the conductive substrate. Therefore, the Li+ deposition behavior of the polymer-based scaffold/host is bottom-up deposition, resulting in inhibiting dendrite growth. Meantime, the polymer matrix possesses more favorable flexibility than other materials, which can accommodate the volume change of the composite anode. Because of this property, it can always stick closely to solid electrolytes to lower interfacial impedance in solid-state batteries. In addition, some polymers can migrate Li+ ions, and this peculiarity shows a great advantage over other materials in solid-state batteries. However, the polymer matrix is attached to the current collector, which also means that there is the risk of shedding. It has a strong impact on the stability of lithium metal anodes. Meantime, the ionic conductivity of the polymer matrix is not too high, which suggests the sluggish migration kinetics of Li+ ions during recycling. Therefore, we should put effort into designing well flexibility and mechanical properties, and high ion conductive polymer-based scaffolds/hosts.
4.4 Electrochemical performances of different textures
To further understand the electrochemical performance of the different kinds of scaffolds/hosts, the cycling life, current density and corresponding deposition capacity of all kinds of symmetric batteries in recent studies are compared, as shown in Fig. 4d–f. The carbon-based scaffold/host demonstrates significant advantages in managing cycling stability and rate performance when compared with the other two material types. Most carbon-based scaffolds can run up to 1000 h, while a few can reach up to 3800 h (Fig. 4d). As for metal-based (Fig. 4e) and polymer-based (Fig. 4f) scaffolds, the cycling life rarely runs beyond 1500 h and 900 h, respectively. The current density and area capacity of most carbon-based scaffolds can operate at 1–10 mA cm−2 and 1–10 mA h cm−2, respectively. In contrast, the deposition capacity of metal-based scaffolds and the current density of polymer-based scaffolds have seldom exceeded 5 mA h cm−2 and 5 mA cm−2, respectively. Compared with polymer-based scaffolds/hosts, the cycling life and endurance for high current density and capacity of the metal-based scaffold/host exhibit outstanding superiority. It is worth noting that the three kinds of typical scaffolds/hosts from highest to lowest are carbon-based, metal-based and polymer-based materials, which further demonstrate the above electrochemical advantage of related materials. Therefore, carbon-based scaffolds/hosts maybe the mainstream direction of research for free-dendrite lithium anodes.
4.5 Physicochemical properties of different textures
In order to figure out the development trend of the scaffold/host strategy, physicochemical properties (stiffness/modulus, density/capacity and ionic/electron conductivity), preparation cost and industrialization ease of three kinds of materials are further quantitatively analyzed, as shown in Fig. 5a. Each indicator is given a score of one to five, and the higher value means a greater advantage. Compared with metal-based and polymer-based materials, the carbon-based scaffold/host exhibits the lowest density, which corresponds to a high active Li capacity, as well as the lowest preparation cost and the greatest ease of industrialization peculiarities. The cost-effectiveness of the carbon-based scaffold/host is attributed to the abundance of carbon sources, combined with their straightforward preparation and processing methods with notably lower production costs. Therefore, the corresponding indicators of carbon-based scaffolds/hosts achieve the highest score of about five. But for the mechanical properties (stiffness and Young's modulus) and electron conductivity, carbon-based materials got only three, which is slightly lower than the score of four and five of metal-based materials, respectively. The most obvious disadvantage of carbon-based and metal-based materials is non-ion conductor, which is significantly weaker than polymer-based materials. In view of scores of various indicators and synthetic performance, the score of three kinds of typical scaffold/host from highest to lowest are carbon-based, polymer-based and metal-based materials. This means that the tendency of future development maybe is carbon-based materials. In the second place, the potential development of polymer-based materials is higher than that of metal-based materials for free-dendrite anodes.
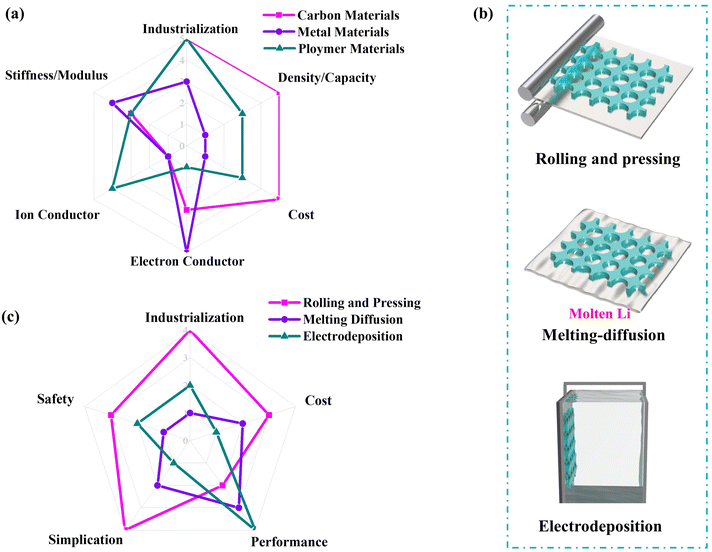 |
| Fig. 5 (a) The radar image of physicochemical properties of different texture scaffolds/hosts. (b) The preparation methods of composite scaffold-based lithium metal anodes. (c) The radar image of the advantages/disadvantages of different scaffold/host preparation methods. | |
4.6 Preparation methods of composite scaffold-based anodes
We have conducted further analysis on the preparation methods of composite lithium anodes based on scaffolds/hosts, which can be categorized into three methods: mechanical (rolling and pressing), melting–diffusion, and electrodeposition, as depicted in Fig. 5b. The mechanical strategy involves bonding a thin lithium foil onto a scaffold/host, followed by rolling and pressing processes to achieve the desired composite lithium anode. This strategy offers the advantages of simplicity, moderate conditions, low cost, thickness control, and high safety, making it suitable for large-scale preparation and industrialization. However, the excessive pressure during the rolling and pressing process can potentially damage the scaffold structure. In addition, it may have limitations in precisely controlling the porosity of the scaffold. The melting–diffusion method entails the infusion of molten lithium metal into a lithiophilic scaffold/host to form the target composite lithium anode. This method requires high temperature to melt the lithium metal, and as such, requires an anhydrous and oxygen-free atmosphere during the preparation process due to the high reactivity of the Li metal. Furthermore, the lithiophilicity of the scaffold/host must be improved before immersion in molten Li. The melting-diffusion strategy has the disadvantages of high cost, complex preparation process, low uniformity of quality, and stringent safety requirements, limiting its industrial readiness. However, it is suitable for fundamental research and in situ observation in button or pouch cells. The electrodeposition method stands out for its ability to meticulously regulate the active Li capacity of composite lithium anodes, ensuring a consistent coating that bolsters overall performance. Nonetheless, this approach comes with a higher cost and involves a more intricate preparation process. It necessitates additional steps for impurity removal, which renders it less practical for large-scale production.
We have also conducted a quantitative analysis of the score of each indicator for the various preparation methods based on their respective advantages and disadvantages concerning safety, industrialization, cost, simplification, and electrode performance. Each indicator received a score of one to four, with higher ratings indicating greater advantages. As shown in Fig. 5c, compared to the melting-diffusion and electrodeposition methods, the mechanical (rolling and pressing) method receives the highest score on various indicators except electrochemical performance. This indicates that the mechanical method offers the best overall advantages and may be the preferred direction for future development.
5. Challenges and difficulties
While 3D scaffold structures offer promising advantages in enhancing the performance of lithium metal batteries, several technical difficulties and practical issues need to be addressed. For instance, before considering the fabrication of a Li composite metal anode, it is essential to understand and resolve the weight and volume ratios between Li and inactive scaffolds/hosts. It is indeed crucial to acknowledge that the introduction of an inactive scaffold inevitably results in a reduction in energy density. To achieve comparable volumetric or gravimetric energy density with conventional LIBs, let's consider a practical example of a 20 μm thick lithium metal foil. For composite lithium metal anodes in lithium metal-based batteries (LMBs), the content of scaffolds/hosts should ideally be kept below 30 wt% in terms of weight and 20 vol% in terms of volume to maintain similar energy densities. However, if the goal is to attain a high energy density of 350 W h kg−1, this would necessitate the use of a thicker lithium metal foil, approximately 50 μm, along with a reduced amount of electrolyte, a high-capacity cathode, and a low N
:
P ratio. Under these conditions, it could be permissible to have a higher mass content of inactive scaffolds/hosts, approximately 50 wt% in the composite Li anode42 Therefore, it is important to note that the minimum quantity of inactive scaffolds/hosts in the composite Li anode for LMBs varies depending on factors such as the thickness of the anode and the desired energy density. The quantitative relationships governing these parameters merit further exploration and investigation to optimize the design and performance of composite Li anodes in LMBs.
The electrolyte compatibility and long-term stability in the context of 3D scaffold/host materials are the critical importance key aspects. The inherent porosity of scaffold structures can pose challenges in achieving uniform wetting by the electrolyte. Ensuring effective electrolyte penetration into the scaffold is vital for optimizing ion transport and facilitating electrochemical reactions. To address this, it is imperative to tailor the electrolyte formulation to enhance wetting and compatibility with the scaffold. This may involve the incorporation of additives or solvents that promote even distribution of the electrolyte throughout the scaffold's porous structure. Simultaneously, the porous nature of the scaffold can have a detrimental effect on the mechanical properties. The continuous cycling of LMAs can lead to the formation of uneven deposits and structural degradation within the scaffold, which can significantly impact the long-term stability and overall performance of the battery. Therefore, dedicated efforts should be directed towards the design and construction of porous scaffold/host materials that exhibit excellent mechanical integrity. This dual focus on electrolyte compatibility and mechanical robustness is pivotal for advancing the practicality and reliability of 3D scaffold/host materials in energy storage applications.
Besides, the challenges of translating composite LMAs prepared using scaffold/host strategies to pouch cells are significant, which is closer to the actual level. The dendrite growth can lead to internal short circuits and even thermal runaway, which is a serious safety hazard, due to the thin and flexible packaging of pouch batteries. Besides, managing the volume changes and associated stresses is crucial. In pouch cells, where space is limited and mechanical constraints are more pronounced, dealing with these volume changes becomes even more challenging. Finding robust and durable materials for the scaffold and designing suitable architectures are crucial for accommodating these volume changes. Moreover, in pouch cells with limited thermal dissipation capabilities, the interfacial reaction and cycling stability of LMAs are becoming horrible. This is the reason why translating the composite LMA prepared using scaffold/host strategy to a practical pouch cell is challenging. Therefore, considering the characteristics of pouch batteries, we should conduct further design and optimization of the scaffold/host.
Furthermore, one significant technical challenge is achieving uniform and stable scaffold/host structures at large-scale production. While laboratory-scale fabrication methods may be feasible, translating these techniques into scalable manufacturing processes for commercial batteries can be difficult. It means the raw material cost and preparation processes should be low and simple, respectively, without compromising the performance of scaffolds/hosts. Finally, optimizing the scaffold's design and integrating it into existing battery configurations necessitate interdisciplinary efforts and material innovations.
6. Criterion and prospect
We must establish specific design criteria or reference factors for scaffolds/hosts that are essential for obtaining optimal electrochemical performance in batteries. To create a scaffold/host that is both ideal and practical, we must consider various physicochemical properties such as electronic and ionic conductivity, mechanical strength, thermal/chemical stability, cost/processability, lithiophilicity, surface area/BET/porosity, and density. These properties have a direct influence on the electrochemical performance of the scaffold/host, as shown in Fig. 6a. Electronic and ionic conductivity, for example, can effectively reduce impedance resistance and improve ion transport kinetics, respectively, leading to decreased cell polarization. Enhancing the mechanical strength and thermal/chemical stability of scaffolds/hosts can increase the stability of composite anodes and prevent dendrite growth, which extends battery cycling life. Additionally, increasing the lithiophilicity of scaffolds/hosts can lower the nucleation barrier of Li+ in batteries, resulting in uniform deposition and improved cycling stability/life. Moreover, increasing the specific surface area/BET/porosity of the scaffold/host mitigates volume changes, reduces local current density, and improves rate performance, while lowering the mass density of the scaffold/host increases active Li deposition capacity and energy density in batteries. The cost and preparation process of the scaffold/host should also be considered, with lower costs and simpler preparation methods being more suitable for commercialization.
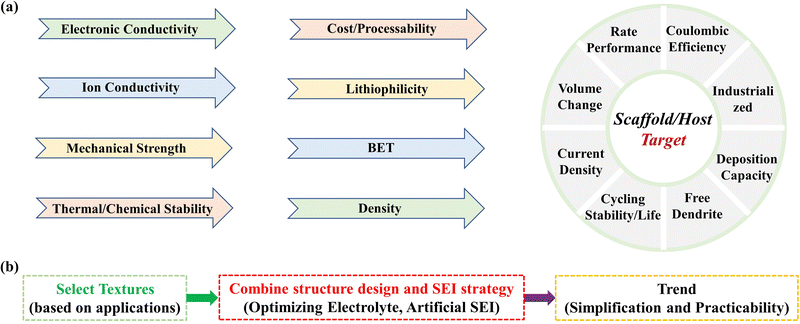 |
| Fig. 6 (a) The performance and physicochemical characteristics of scaffolds/hosts. (b) The prospects of preparation scaffold/host materials for Li metal anodes. | |
From the foregoing, we can discern that each electrochemical performance parameter is determined by multiple physicochemical properties of scaffolds/hosts. Creating an ideal scaffold/host that has all the desired properties is a complex task. Pursuing perfection in one property may result in the sacrifice of another. For example, increasing the specific surface area/BET/porosity of scaffolds/hosts to improve battery performance may have a detrimental effect on its mechanical properties. Therefore, we must make informed choices based on the application of scaffolds/hosts, taking into account all relevant physicochemical properties.
So, what principles should we adopt for the design of scaffolds/hosts? It can be summarized into three steps, as shown in Fig. 6b.
(1) First, when selecting material textures for scaffolds/hosts, the applications must be taken into account
For all-solid-state battery (ASSB) applications, polymer-based scaffolds/hosts are preferred due to their ion-conductive properties. The solid electrolyte, the key component in the ASSB system, can only make contact with the upper surface of the anode, which means that the scaffolds/hosts of the anode should possess favorable ionic/electronic conductivity, which is achieved through the combination of polymer and carbon materials or metal materials. With the exception of solid-state-batteries, carbon-based scaffolds/hosts maybe the primary choice due to their high potential for future development, as analyzed in Fig. 5a. Additionally, in terms of practical applications of scaffolds/hosts, combining Cu foil current collectors with carbon-based scaffold materials can be an effective strategy to improve continuity, mechanical strength, and energy density.
(2) Second, we should work on the multi-strategy combination
Given the complexity of Li+ ion deposition, it is challenging to completely overcome dendrite growth with a single scaffold/host strategy. Structural design is an effective and convenient strategy for inhibiting dendrite growth, and when combined with optimizing electrolytes or engineering artificial protection layers, it produces a 1 + 1 > 2 effect.
(3) Third, the preparation process for scaffolds/hosts and composite anodes should be simplified, and the preparation cost should be reduced to meet future practical application requirements
The raw materials for scaffolds/hosts and the alloying or doping elements for increasing lithiophilicity should be easily obtained and inexpensive. Moreover, to satisfy industrial production requirements, the preparation conditions and costs should be mild and inexpensive.
In addition to this, the following research aspects of scaffolds/hosts are also worthy of our attention to make progress in battery technology.
(1) First, we should further explore the growth mechanism of Li dendrites and build a generic model
This is due to the currently proposed models being limited to several specific conditions, and it is hard to give a full explanation. It could provide key guidance for the design of an advanced scaffold/host.
(2) Second, the investigation of the structural/morphological evolution of scaffolds/hosts for battery failure could help us understand the relationship between material nature and electrochemical deposition behaviour
The above investigation requires developing various advanced in situ characterization methods to explore the Li plating/stripping behaviors because of the sensitivity of Li metals and SEI to the electron beam and air atmosphere, such as cryo-electron microscopy, fluorescence probing and synchrotron X-ray tomography, and so on. This could offer constructive feedback on the design of the scaffold/host.
(3) Third, the advanced scaffold/host-based anode should be studied to further explore its feasibility and electrochemical performance in pouch cells
Compared with coin cells, the application of composite anodes in pouch cells is close to the actual level, which means the industrial standard, including small N
:
P ratio, lean electrolyte, high-capacity loading cathode and density. In addition, the 3D printing technology might help scientists to accelerate and normalize the above research. Overall, there is still a long way to achieve an advanced scaffold/host, and there is still a lot of research room in this area.
7. Conclusion
In this work, we provide a comprehensive summary of the working mechanisms of scaffolds/hosts for dendrite-free lithium metal anodes and provide a further review of their history and recent key progress. The working mechanisms of scaffolds/hosts mainly include decreasing the nucleation barrier and promoting uniform deposition, reducing local current density and increasing Sand's time, changing the deposition location by designing structure, and altering the composition of SEI. As for developing the history of scaffolds/hosts, it can be compartmentalized into five phases: material texture selection, lithiophilic modification, structure design, multi-strategy combination, and practicality. We further classify scaffolds/hosts based on material texture (carbon-based, metal-based and polymer-based materials) and analyze the corresponding advantages and disadvantages. Based on this classification, we analyze the future development potential and trends of various scaffold/host materials. Then, we briefly outline the challenges and difficulties faced in using scaffold/host strategies. Finally, we further discuss the determining factors of physicochemical characteristics of scaffolds/hosts and their impact on the electrochemical performance. We also consider the possible design criteria and development tendencies for advanced scaffolds/hosts. Overall, this comprehensive review aims to provide enlightenment and guidance for the design of advanced scaffold/host materials for dendrite-free lithium metal anodes.
Conflicts of interest
There are no conflicts of interest to declare.
Acknowledgements
This work is supported by the National Key Research and Development Program of China (2022YFB3807700, 2021YFE0109700 and 2019YFA0210600), the National Natural Science Foundation of China (51972107 and 22309048), the Natural Science Foundation of Hunan Province (2023JJ40121), the Fundamental Research Funds for the Central Universities (531118010762), and the Opening Project of Guangxi Key Laboratory of Petrochemical Resource Processing and Process Intensification Technology (2022K006).
Notes and references
- S. Chu and A. Majumdar, Nature, 2012, 488, 294–303 CrossRef CAS PubMed
.
- X. B. Cheng, R. Zhang, C. Z. Zhao and Q. Zhang, Chem. Rev., 2017, 117, 10403–10473 CrossRef CAS
.
- M. Winter and K. X. B. Barnett, Chem. Rev., 2018, 118, 11433–11456 CrossRef CAS PubMed
.
- M. Li, J. Lu, Z. W. Chen and K. Amine, Adv. Mater., 2018, 30, 1800561 CrossRef PubMed
.
- J. M. Tarascon and M. Armand, Nature, 2001, 414, 359–367 CrossRef CAS PubMed
.
- J. B. Goodenough and K. S. Park, J. Am. Chem. Soc., 2013, 135, 1167–1176 CrossRef CAS PubMed
.
- J. W. Choi and D. Aurbach, Nat. Rev. Mater., 2016, 1, 16013 CrossRef CAS
.
- C. Heubner, K. Kristian, S. Reuber, M. Schneider, M. Wolter and A. Michaelis, Batteries Supercaps, 2020, 4, 268–285 CrossRef
.
- L. G. Lu, X. B. Han, J. Q. Li, J. F. Hua and M. G. Ouyang, J. Power Sources, 2013, 226, 272–288 CrossRef CAS
.
- V. Etacheri, R. Marom, R. Elazari, G. Salitra and D. Aurbach, Energy Environ. Sci., 2011, 4, 3243–3262 RSC
.
- D. C. Lin, Y. Y. Liu, Z. Liang, H. W. Lee, J. Sun, H. T. Wang, K. K. Yan, J. Xie and Y. Cui, Nat. Nanotechnol., 2016, 11, 626–632 CrossRef CAS PubMed
.
- Y. P. Guo, H. Q. Li and T. Y. Zhai, Adv. Mater., 2017, 29, 1700007 CrossRef PubMed
.
- Y. X. Hu, T. R. Zhang, F. Y. Cheng, Q. Zhao, X. P. Han and J. Chen, Angew. Chem., Int. Ed., 2015, 54, 4338–4343 CrossRef CAS PubMed
.
- X. Liang, C. Hart, Q. Pang, A. Garsuch, T. Weiss and L. F. Nazar, Nat. Commun., 2015, 6, 5682 CrossRef
.
- X. F. Hu, J. B. Wang, Z. F. Li, J. Q. Wang, D. H. Gregory and J. Chen, Nano Lett., 2017, 17, 2073–2078 CrossRef CAS PubMed
.
- Q. Zhang, Y. Y. Lu, L. C. Miao, Q. Zhao, K. X. Xia, J. Liang, S. L. Chou and J. Chen, Angew. Chem., Int. Ed., 2018, 57, 14796–14800 CrossRef CAS PubMed
.
- Y. Q. Chen, Y. Luo, H. Z. Zhang, C. Qu, H. M. Zhang and X. F. Li, Small Methods, 2019, 3, 1800551 CrossRef
.
- C. Z. Wang, A. X. Wang, L. X. Ren, X. Z. Guan, D. H. Wang, A. P. Dong, C. Y. Zhang, G. J. Li and J. Y. Luo, Adv. Funct. Mater., 2019, 29, 1905940 CrossRef CAS
.
- X. Y. Zhang, A. X. Wang, X. J. Liu and J. Y. Luo, Acc. Chem. Res., 2019, 52, 3223–3232 CrossRef CAS PubMed
.
- C. P. Yang, Y. X. Yin, S. F. Zhang, N. W. Li and Y. G. Guo, Nat. Commun., 2015, 6, 8058 CrossRef CAS
.
- W. Q. Guo, S. Liu, X. Z. Guan, X. Y. Zhang, X. J. Liu and J. Y. Luo, Adv. Energy Mater., 2019, 9, 1900193 CrossRef
.
- C. Yan, R. Xu, Y. Xiao, J. F. Ding, L. Xu, B. Q. Li and J. Q. Huang, Adv. Funct. Mater., 2020, 30, 1909887 CrossRef CAS
.
- R. Wang, J. Yu, J. T. Tang, R. J. Meng, L. F. Nazar, L. Z. Huang and X. Liang, Energy Storage Mater., 2020, 32, 178–184 CrossRef
.
- X. B. Cheng, R. Zhang, C. Z. Zhao, F. Wei, J. G. Zhang and Q. Zhang, Adv. Sci., 2016, 3, 1500213 CrossRef PubMed
.
- W. L. Feng, X. L. Dong, Z. Z. Lai, X. Y. Zhang, Y. G. Wang, C. X. Wang, J. Y. Luo and Y. Y. Xia, ACS Energy Lett., 2019, 4, 1725–1731 CrossRef CAS
.
- W. Y. Li, H. B. Yao, K. Yan, G. Y. Zheng, Z. Liang, Y. M. Chiang and Y. Cui, Nat. Commun., 2015, 6, 7436 CrossRef CAS PubMed
.
- N. W. Li, Y. X. Yin, C. P. Yang and Y. G. Guo, Adv. Mater., 2016, 28, 1853–1858 CrossRef CAS PubMed
.
- W. J. Tang, S. Tang, X. Z. Guan, X. Y. Zhang, Q. Xiang and J. Y. Luo, Adv. Funct. Mater., 2019, 29, 1900648 CrossRef
.
- C. W. Wang, Y. H. Gong, B. Y. Liu, K. Fu, Y. G. Yao, E. Hitz, Y. J. Li, J. Q. Dai, S. M. Xu, W. Luo, E. D. Wachsman and L. B. Hu, Nano Lett., 2017, 17, 565–571 CrossRef CAS PubMed
.
- Y. Guo, S. C. Wu, Y. B. He, F. Y. Kang, L. Q. Chen, H. Li and Q. H. Yang, eScience, 2022, 2, 138–163 CrossRef
.
- X. Liang, Q. Pang, I. Kochetkov, M. S. Sempere, H. Huang, X. Sun and L. F. Nazar, Nat. Energy, 2017, 2, 17119 CrossRef CAS
.
- A. L. Chen, N. Shang, Y. Ouyang, L. L. Mo, C. Y. Zhou, W. W. Tjiu, F. L. Lai, Y. E. Miao and T. X. Liu, eScience, 2022, 2, 192–200 CrossRef
.
- H. R. Zhang, L. Huang, H. T. Xu, X. H. Zhang, Z. Chen, C. H. Gao, C. L. Lu, Z. Liu, M. F. Jiang and G. L. Cui, eScience, 2022, 2, 201–208 CrossRef
.
- S. M. Chai, Y. P. Zhang, Y. J. Wang, Q. He, S. Zhou and A. Q. Pan, eScience, 2022, 2, 494–508 CrossRef
.
- Z. M. Hu, H. Su, M. F. Zhou, J. Z. Liu, Y. Z. Wan, J. M. Hu and Y. H. Xu, Small, 2022, 18, e2104735 CrossRef
.
- H. B. Song, T. T. He, J. Y. Liu, Y. Wang, X. L. Li, J. Liu, D. D. Zhang, H. Y. Yang, J. P. Hu and S. Z. Huang, Carbon, 2021, 181, 99–106 CrossRef CAS
.
- X. J. Qian, X. Q. Fan, Y. L. Peng, P. Xue, C. Sun, X. L. Shi, C. Lai and J. J. Liang, Adv. Funct. Mater., 2020, 31, 2008044 CrossRef
.
- Y. M. Chen, X. Ke, Y. F. Cheng, M. P. Fan, W. L. Wu, X. Y. Huang, Y. H. Liang, Y. C. Zhong, Z. M. Ao, Y. Q. Lai, G. X. Wang and Z. C. Shi, Energy Storage Mater., 2020, 26, 56–64 CrossRef
.
- X. Y. Zhao, S. X. Xia, X. Zhang, Y. P. Pang, F. Xu, J. H. Yang, L. X. Sun and S. Y. Zheng, ACS Appl. Mater. Interfaces, 2021, 13, 20240–20250 CrossRef CAS
.
- S. Park, H. J. Jin and Y. S. Yun, Adv. Mater., 2020, 32, e2002193 CrossRef PubMed
.
- Y. F. Cheng, J. B. Chen, Y. M. Chen, X. Ke, J. Li, Y. Yang and Z. C. Shi, Energy Storage Mater., 2021, 38, 276–298 CrossRef
.
- C. Jin, O. Sheng, M. Chen, Z. Ju, G. Lu, T. Liu, J. Nai, Y. Liu, Y. Wang and X. Tao, Mater. Today Nano, 2021, 13, 100103 CrossRef CAS
.
- K. Yan, H. W. Lee, T. Gao, G. Y. Zheng, H. B. Yao, H. T. Wang, Z. D. Lu, Y. Zhou, Z. Liang, Z. F. Liu, S. Chu and Y. Cui, Nano Lett., 2014, 14, 6016–6022 CrossRef CAS PubMed
.
- J. Y. Chen, J. Zhao, L. N. Lei, P. Li, J. Chen, Y. Zhang, Y. Z. Wang, Y. W. Ma and D. Wang, Nano Lett., 2020, 20, 3403–3410 CrossRef CAS PubMed
.
- L. Chen, X. L. Fan, X. Ji, J. Chen, S. Hou and C. S. Wang, Joule, 2019, 3, 732–744 CrossRef CAS
.
- Y. Y. Feng, C. F. Zhang, X. X. Jiao, Z. X. Zhou and J. X. Song, Energy Storage Mater., 2020, 25, 172–179 CrossRef
.
- C. Y. Wang, C. P. Yang and Z. J. Zheng, Adv. Sci., 2022, 9, e2105213 CrossRef PubMed
.
- R. H. Hou, S. J. Zhang, Y. S. Zhang, N. Li, S. B. Wang, B. Ding, G. S. Shao and P. Zhang, Adv. Funct. Mater., 2022, 32, 2200302 CrossRef CAS
.
- F. F. Liu, R. Xu, Z. X. Hu, S. F. Ye, S. F. Zeng, Y. Yao, S. Q. Li and Y. Yu, Small, 2019, 15, e1803734 CrossRef PubMed
.
- Y. H. Kim, G. W. Lee, Y. J. Choi, H. S. Choi and K. B. Kim, Adv. Funct. Mater., 2022, 2113316 CrossRef CAS
.
- D. D. Li, H. H. Hu, B. Chen and W. Y. Lai, Small, 2022, e2200010 CrossRef PubMed
.
- N. Lucero, D. Vilcarino, D. Datta and M. Q. Zhao, J. Energy Chem., 2022, 69, 132–149 CrossRef CAS
.
- H. Y. Zhang, S. L. Ju, G. L. Xia and X. B. Yu, Sci. Adv., 2022, 8, eabl8245 CrossRef CAS PubMed
.
- S. Y. Ni, J. Z. Sheng, C. Zhang, X. Wu, C. Yang, S. F. Pei, R. H. Gao, W. Liu, L. Qiu and G. M. Zhou, Adv. Funct. Mater., 2022, 32, 2200682 CrossRef CAS
.
- P. L. Li, Z. Fang, X. L. Dong, C. X. Wang and Y. Y. Xia, Natl. Sci. Rev., 2022, 9, nwac031 CrossRef CAS PubMed
.
- Y. X. Ren, Z. H. Cui, A. Bhargav, J. R. He and A. Manthiram, Adv. Funct. Mater., 2021, 32, 2106680 CrossRef
.
- J. N. Chazalviel, Phys. Rev. A, 1990, 42, 7355–7367 CrossRef CAS
.
- Z. Y. Tu, P. J. Nath, Y. Y. Lu, M. D. Tikekar and L. A. Archer, Acc. Chem. Res., 2015, 48, 2947–2956 CrossRef CAS PubMed
.
- Q. Xu, Y. F. Yang and H. X. Shao, Phys. Chem. Chem. Phys., 2015, 17, 20398–20406 RSC
.
- K. Yan, Z. D. Lu, H. W. Lee, F. Xiong, P. C. Hsu, Y. Z. Li, J. Zhao, S. Chu and Y. Cui, Nat. Energy, 2016, 1, 16010 CrossRef CAS
.
- D. R. Ely and R. E. García, J. Electrochem. Soc., 2013, 160, A662–A668 CrossRef CAS
.
- A. Kushima, K. P. So, C. Su, P. Bai, N. Kuriyama, T. Maebashi, Y. Fujiwara, M. Z. Bazant and J. Li, Nano Energy, 2017, 32, 271–279 CrossRef CAS
.
- Z. Y. Zeng, W. I. Liang, H. G. Liao, H. L. Xin, Y. H. Chu and H. M. Zheng, Nano Lett., 2014, 14, 1745–1750 CrossRef CAS PubMed
.
- A. Pei, G. Y. Zheng, F. F. Shi, Y. Z. Li and Y. Cui, Nano Lett., 2017, 17, 1132–1139 CrossRef CAS PubMed
.
- S. S. Shi, P. Lu, Z. Y. Liu, Y. Qi, L. G. Hector, Jr., H. Li and S. J. Harris, J. Am. Chem. Soc., 2012, 134, 15476–15487 CrossRef CAS PubMed
.
- E. Peled, D. Golodnitsky and G. Ardel, J. Electrochem. Soc., 1997, 144, L208–L210 CrossRef CAS
.
- M. Jackle and A. Gross, J. Chem. Phys., 2014, 141, 174710 CrossRef PubMed
.
- E. Gumbmann, F. D. Geuser, C. Sigli and A. Deschamps, Acta Mater., 2017, 133, 172–185 CrossRef CAS
.
- M. Kawasaki, K. Kubota, K. Higashi and T. G. Langdon, Mater. Sci. Eng., A, 2006, 429, 334–340 CrossRef
.
- Z. Z. Shi, X. X. Gao, H. J. Zhang, X. F. Liu, H. Y. Li, C. Zhou, Y. X. Yin and L. N. Wang, Bioact. Mater., 2020, 5, 210–218 Search PubMed
.
- H. Li, L. H. Shi, Q. Wang, L. Q. Chen and X. J. Huang, Solid State Ionics, 2002, 148, 247–258 CrossRef CAS
.
- M. N. Obrovac and V. L. Chevrier, Chem. Rev., 2014, 114, 11444–11502 CrossRef CAS PubMed
.
- I. Yoon, S. Jurng, D. P. Abraham, B. L. Lucht and P. R. Guduru, Energy Storage Mater., 2020, 25, 296–304 CrossRef
.
- N. Mahmood, J. H. Zhu, S. Rehman, Q. Li and Y. L. Hou, Nano Energy, 2015, 15, 755–765 CrossRef CAS
.
- K. J. Harry, K. Higa, V. Srinivasan and N. P. Balsara, J. Electrochem. Soc., 2016, 163, A2216–A2224 CrossRef CAS
.
- A. Lahiri and A. Choudhury, Comp. Mater. Sci., 2019, 158, 209–218 CrossRef CAS
.
- A. X. Wang, Q. B. Deng, L. J. Deng, X. Z. Guan and J. Y. Luo, Adv. Funct. Mater., 2019, 29, 1902630 CrossRef
.
- S. T. Hong, J. S. Kim, S. J. Lim and W. Y. Yoon, Electrochimi. Acta, 2004, 50, 535–539 CrossRef CAS
.
- S. A. Fernando, Y. G. Ma, J. M. M. L. Hoz, J. M. Seminario and P. B. Balbuena, Chem. Mater., 2015, 27, 7990–8000 CrossRef
.
- W. J. Li, H. Zheng, G. Chu, F. Luo, J. Y. Zheng, D. D. Xiao, X. Li, L. Gu, H. Li, X. L. Wei, Q. Chen and L. Q. Chen, Faraday Discuss., 2014, 176, 109–124 RSC
.
- M. B. Pinson and M. Z. Bazant, J. Electrochem. Soc., 2013, 160, A243–A250 CrossRef CAS
.
- F. F. Zhao, P. B. Zhai, Y. Wei, Z. L. Yang, Q. Chen, J. H. Zuo, X. K. Gu and Y. J. Gong, Adv. Sci., 2022, 9, 2103930 CrossRef CAS PubMed
.
- Z. Liang, D. C. Lin, J. Zhao, Z. D. Lu, Y. Y. Liu, C. Liu, Y. Y. Lu, H. T. Wang, K. Yan, X. Y. Tao and Y. Cui, P. Natl. Acad. Sci. USA, 2016, 113, 2862–2867 CrossRef CAS PubMed
.
- J. Zhao, G. M. Zhou, K. Yan, J. Xie, Y. Z. Li, L. Liao, Y. Jin, K. Liu, P. C. Hsu, J. Y. Wang, H. M. Cheng and Y. Cui, Nat. Nanotechnol., 2017, 12, 993–999 CrossRef CAS PubMed
.
- R. Zhang, X. R. Chen, X. Chen, X. B. Cheng, X. Q. Zhang, C. Yan and Q. Zhang, Angew. Chem., Int. Ed., 2017, 56, 7764–7768 CrossRef CAS PubMed
.
- R. Zhang, X. Xiang, X. Shen, X. Q. Zhang, X. R. Chen, X. B. Cheng, C. Yan, C. Z. Zhao and Q. Zhang, Joule, 2018, 2, 764–777 CrossRef CAS
.
- Y. Y. Liu, D. C. Lin, Y. Jin, K. Liu, X. Y. Tao, Q. H. Zhang, X. K. Zhang and Y. Cui, Sci. Adv., 2017, 3, eaao0713 CrossRef PubMed
.
- C. P. Yang, L. Zhang, B. Y. Liu, S. M. Xu, T. Hamann, D. McOwen, J. Q. Dai, W. Luo, Y. H. Gong, E. D. Wachsman and L. B. Hu, Proc. Natl. Acad. Sci. U. S. A., 2018, 115, 3770–3775 CrossRef CAS PubMed
.
- X. Y. Zhang, R. J. Lv, A. X. Wang, W. Q. Guo, X. J. Liu and J. Y. Luo, Angew. Chem., Int. Ed., 2018, 57, 15028–15033 CrossRef CAS PubMed
.
- H. M. Zhang, X. B. Liao, Y. P. Guan, Y. Xiang, M. Li, W. F. Zhang, X. Y. Zhu, H. Ming, L. Lu, J. Y. Qiu, Y. Q. Huang, G. P. Cao, Y. S. Yang, L. Q. Mai, Y. Zhao and H. Zhang, Nat. Commun., 2018, 9, 3729 CrossRef PubMed
.
- Z. Liang, K. Yan, G. M. Zhou, A. Pei, J. Zhao, Y. M. Sun, J. Xie, Y. B. Li, F. F. Shi, Y. Y. Liu, D. C. Lin, K. Liu, H. Wang, H. X. Wang, Y. Y. Lu and Y. Cui, Sci. Adv., 2019, 5, eaau5655 CrossRef CAS PubMed
.
- S. H. Wang, J. P. Yue, W. Dong, T. T. Zuo, J. Y. Li, X. L. Liu, X. D. Zhang, L. Liu, J. L. Shi, Y. X. Yin and Y. G. Guo, Nat. Commun., 2019, 10, 4930 CrossRef
.
- L. Tao, A. Y. Hu, Z. J. Yang, Z. R. Xu, C. E. Wall, A. R. Esker, Z. F. Zheng and F. Lin, Adv. Funct. Mater., 2020, 30, 2000585 CrossRef CAS
.
- X. He, S. Jin, L. C. Miao, Y. C. Cai, Y. P. Hou, H. X. Li, K. Zhang, Z. H. Yan and J. Chen, Angew. Chem., Int. Ed., 2020, 59, 16705–16711 CrossRef CAS
.
- P. B. Zhai, Y. Wei, J. Xiao, W. Liu, J. H. Zuo, X. K. Gu, W. W. Yang, S. Q. Cui, B. Lin, S. B. Yang and Y. J. Gong, Adv. Energy Mater., 2020, 10, 1903339 CrossRef CAS
.
- P. Shi, Z. Y. Liu, X. Q. Zhang, X. Chen, N. Yao, J. Xie, C. B. Jin, Y. X. Zhan, G. Ye, J. Q. Huang, S. Ifan, E. L. T. Maria-Magdalena and Q. Zhang, J. Energy Chem, 2022, 64, 172–178 CrossRef CAS
.
- Y. Ye, Y. Zhao, T. Zhao, S. Xu, Z. Xu, J. Qian, L. Wang, Y. Xing, L. Wei, Y. Li, J. Wang, L. Li, F. Wu and R. Chen, Adv. Mater., 2021, 33, e2105029 CrossRef PubMed
.
- J. Shang, W. Yu, L. Wang, C. Xie, H. Xu, W. Wang, Q. Huang and Z. Zheng, Adv. Mater., 2023, e2211748 CrossRef PubMed
.
- L. Ye, M. Liao, H. Sun, Y. Yang, C. Tang, Y. Zhao, L. Wang, Y. Xu, L. Zhang, B. Wang, F. Xu, X. Sun, Y. Zhang, H. Dai, P. G. Bruce and H. Peng, Angew. Chem., Int. Ed., 2019, 58, 2437–2442 CrossRef CAS
.
- L. H. Pan, Z. F. Luo, Y. T. Zhang, W. L. Chen, Z. H. Zhao, Y. Y. Li, J. Wan, D. D. Yu, H. Y. He and D. Y. Wang, ACS Appl. Mater. Inter., 2019, 11, 44383–44389 CrossRef CAS PubMed
.
- Q. Zhao, X. G. Hao, S. M. Su, J. B. Ma, Y. Hu, Y. Liu, F. Y. Kang and Y. B. He, J. Mater. Chem. A, 2019, 7, 15871–15879 RSC
.
- Y. Zhang, Y. Shi, X. C. Hu, W. P. Wang, R. Wen, S. Xin and Y. G. Guo, Adv. Energy Mater., 2019, 10, 1903325 CrossRef
.
- Y. Zhou, Y. Han, H. T. Zhang, D. Sui, Z. H. Sun, P. S. Xiao, X. T. Wang, Y. F. Ma and Y. S. Chen, Energy Storage Mater., 2018, 14, 222–229 CrossRef
.
- Q. Wang, C. K. Yang, J. J. Yang, K. Wu, L. Y. Qi, H. Tang, Z. Y. Zhang, W. Liu and H. H. Zhou, Energy Storage Mater., 2018, 15, 249–256 CrossRef
.
- G. J. Yang, Y. J. Li, Y. X. Tong, J. L. Qiu, S. Liu, S. M. Zhang, Z. R. X. Guan, B. Xu, Z. X. Wang and L. Q. Chen, Nano Lett., 2019, 19, 494–499 CrossRef CAS PubMed
.
- Z. H. Li, X. L. Li, L. Zhou, Z. C. Xiao, S. K. Zhou, X. H. Zhang, L. D. Li and L. J. Zhi, Nano Energy, 2018, 49, 179–185 CrossRef CAS
.
- M. Chen, J. H. Zheng, O. W. Sheng, C. B. Jin, H. D. Yuan, T. F. Liu, Y. J. Liu, Y. Wang, J. W. Nai and X. Y. Tao, J. Mater. Chem. A, 2019, 7, 18267–18274 RSC
.
- H. D. Shi, C. F. J. Zhang, P. F. Lu, Y. F. Dong, P. C. Wen and Z. S. Wu, ACS Nano, 2019, 13, 14308–14318 CrossRef CAS PubMed
.
- W. T. Li, Y. F. Zhang, H. Li, Z. J. Chen, T. X. Shang, Z. T. Wu, C. Zhang, J. Li, W. Lv, Y. Tao and Q. H. Yang, Batteries Supercaps, 2020, 3, 892–899 CrossRef CAS
.
- Y. Qian, C. L. Wei, Y. Tian, B. J. Xi, S. L. Xiong, J. K. Feng and Y. T. Qian, Chem. Eng. J., 2021, 421, 129685 CrossRef CAS
.
- J. W. Sun, B. Li, C. Jin, L. Peng, D. M. Dai, J. H. Hu, C. H. Yang, C. Y. Lu and R. Z. Yang, J. Power Sources, 2021, 484, 229253 CrossRef CAS
.
- W. L. Liu, J. Z. Man, K. Liu, X. D. Sun, Q. Wang and J. C. Sun, J. Alloy. Compd., 2022, 909, 164659 CrossRef CAS
.
- T. S. Wang, X. B. Liu, X. D. Zhao, P. G. He, C. W. Nan and L. Z. Fan, Adv. Funct. Mater., 2020, 30, 2000786 CrossRef CAS
.
- X. Z. Zhang, S. Jin, M. H. Seo, C. Q. Shang, G. F. Zhou, X. Wang and G. Li, Nano Energy, 2022, 93, 106905 CrossRef CAS
.
- L. J. Chen, H. Chen, Z. Wang, X. Z. Gong, M. Y. Wang and S. Q. Jiao, Chem. Eng. J., 2019, 363, 270–277 CrossRef CAS
.
- L. Liu, Y. X. Yin, J. Y. Li, S. H. Wang, Y. G. Guo and L. J. Wan, Adv. Mater., 2018, 30 Search PubMed
.
- H. J. Yoon, N. R. Kim, H. J. Jin and Y. S. Yun, Adv. Energy Mater., 2018, 8, 1701261 CrossRef
.
- X. Chen, X. R. Chen, T. Z. Hou, B. Q. Li, X. B. Cheng, R. Zhang and Q. Zhang, Sci. Adv., 2019, 5, eaau7728 CrossRef CAS PubMed
.
- Y. S. Yun, D. H. Kim, S. J. Hong, M. H. Park, Y. W. Park, B. H. Kim, H. J. Jin and K. Kang, Nanoscale, 2015, 7, 15051–15058 RSC
.
- Y. S. Yun, D. H. Kim, S. J. Hong, M. H. Park, Y. W. Park, B. H. Kim, H. J. Jin and K. Kang, Nanoscale, 2015, 7, 15051–15058 RSC
.
- L. Tao, A. Y. Hu, Z. J. Yang, Z. R. Xu, C. E. Wall, A. R. Esker, Z. F. Zheng and F. Lin, Energy Storage Mater., 2020, 24, 129–137 CrossRef
.
- K. Liu, Z. H. Li, W. F. Xie, J. B. Li, D. M. Rao, M. F. Shao, B. S. Zhang and M. Wei, Energy Storage Mater., 2018, 15, 308–314 CrossRef
.
- X. H. Zhou, W. J. Huang, C. G. Shi, K. Wang, R. Zhang, J. C. Guo, Y. F. Wen, S. J. Zhang, Q. Wang, L. Huang, J. T. Li, X. D. Zhou and S. G. Sun, ACS Appl. Mater. Interfaces, 2018, 10, 35296–35305 CrossRef CAS PubMed
.
- Y. M. Liu, X. Y. Qin, S. Q. Zhang, Y. L. Huang, F. Y. Kang, G. H. Chen and B. H. Li, Energy Storage Mater., 2019, 18, 320–327 CrossRef
.
- C. P. Yang, Y. G. Yao, S. M. He, H. Xie, E. Hitz and L. B. Hu, Adv. Mater., 2017, 29 Search PubMed
.
- H. S. Wang, Y. Z. Li, Y. B. Li, Y. Y. Liu, D. C. Lin, C. Zhu, G. X. Chen, A. K. Yang, K. Yan, H. Chen, Y. Y. Zhu, J. Li, J. Xie, J. W. Xu, Z. W. Zhang, R. Vila, A. Pei, K. C. Wang and Y. Cui, Nano Lett., 2019, 19, 1326–1335 CrossRef CAS
.
- S. J. Qu, W. S. Jia, Y. Wang, C. Li, Z. Y. Yao, K. Y. Li, Y. C. Liu, W. Zou, F. Zhou, Z. H. Wang and J. Z. Li, Electrochim. Acta, 2019, 317, 120–127 CrossRef CAS
.
- Y. M. Liu, S. Q. Zhang, X. Y. Qin, F. Y. Kang, G. H. Chen and B. H. Li, Nano Lett., 2019, 19, 4601–4607 CrossRef CAS PubMed
.
- X. S. Wang, Z. H. Pan, Y. Wu, X. Y. Ding, X. J. Hong, G. G. Xu, M. N. Liu, Y. G. Zhang and W. S. Li, Nano Res., 2018, 12, 525–529 CrossRef
.
- S. H. Liu, J. Li, X. Yan, Q. F. Su, Y. H. Lu, J. S. Qiu, Z. Y. Wang, X. D. Lin, J. L. Huang, R. L. Liu, B. N. Zheng, R. L. Y. Chen, W. Fu and D. C. Wu, Adv. Mater., 2018, 30, e1706895 CrossRef
.
- Y. Zhang, C. W. Wang, G. Pastel, Y. D. Kuang, H. Xie, Y. J. Li, B. Y. Liu, W. Luo, C. J. Chen and L. B. Hu, Adv. Energy Mater., 2018, 8, 1800635 CrossRef
.
- C. Z. Sun, T. Wu, J. N. Wang, W. W. Li, J. Jin, J. H. Yang and Z. Y. Wen, J. Mater. Chem. A, 2018, 6, 19159–19166 RSC
.
- Y. Deng, H. M. Lu, Y. Cao, B. B. Xu, Q. S. Hong, W. Cai and W. W. Yang, J. Power Sources, 2019, 412, 170–179 CrossRef CAS
.
- S. Jin, Z. W. Sun, Y. L. Guo, Z. K. Qi, C. K. Guo, X. H. Kong, Y. W. Zhu and H. X. Ji, Adv. Mater., 2017, 29, 1700783 CrossRef PubMed
.
- J. Xie, J. L. Ye, F. Pan, X. M. Sun, K. Ni, H. Yuan, X. Y. Wang, N. Shu, C. H. Chen and Y. W. Zhu, Adv. Mater., 2019, 31, e1805654 CrossRef PubMed
.
- C. Y. Zhang, S. Liu, G. J. Li, C. J. Zhang, X. J. Liu and J. Y. Luo, Adv. Mater., 2018, 30, 1801328 CrossRef PubMed
.
- S. S. Chi, Y. C. Liu, W. L. Song, L. Z. Fan and Q. Zhang, Adv. Funct. Mater., 2017, 27, 1700348 CrossRef
.
- S. L. Wu, T. P. Jiao, S. R. Yang, B. Liu, W. J. Zhang and K. L. Zhang, J. Mater. Chem. A, 2019, 7, 5726–5732 RSC
.
- Q. Li, S. P. Zhu and Y. Y. Lu, Adv. Funct. Mater., 2017, 27, 1606422 CrossRef
.
- X. Huang, X. Y. Feng, B. Zhang, L. Zhang, S. C. Zhang, B. Gao, P. K. Chu and K. F. Huo, ACS Appl. Mater. Interfaces, 2019, 11, 31824–31831 CrossRef CAS PubMed
.
- H. Liu, E. Wang, Q. Zhang, Y. B. Ren, X. W. Guo, L. Wang, G. Y. Li and H. J. Yu, Energy Storage Mater., 2019, 17, 253–259 CrossRef
.
- L. G. Qin, H. Xu, D. Wang, J. F. Zhu, J. Chen, W. Zhang, P. G. Zhang, Y. Zhang, W. B. Tian and Z. M. Sun, ACS Appl. Mater. Interfaces, 2018, 10, 27764–27770 CrossRef CAS PubMed
.
- K. Tantratian, D. X. Cao, A. Abdelaziz, X. Sun, J. Z. Sheng, A. Natan, L. Chen and H. L. Zhu, Adv. Energy Mater., 2019, 10, 1902819 CrossRef
.
- L. L. Lu, J. Ge, J. N. Yang, S. M. Chen, H. B. Yao, F. Zhou and S. H. Yu, Nano Lett., 2016, 16, 4431–4437 CrossRef CAS PubMed
.
- J. R. He and A. Manthiram, Adv. Energy Mater., 2019, 10, 1903241 CrossRef
.
- J. Pu, J. C. Li, K. Zhang, T. Zhang, C. W. Li, H. X. Ma, J. Zhu, P. V. Braun, J. Lu and H. G. Zhang, Nat. Commun., 2019, 10, 1896 CrossRef PubMed
.
- G. X. Li, Z. Liu, Q. Q. Huang, Y. Gao, M. Regula, D. W. Wang, L. Q. Chen and D. H. Wang, Nat. Energy, 2018, 3, 1076–1083 CrossRef CAS
.
- S. Matsuda, Y. Kubo, K. Uosaki and S. Nakanishi, ACS Energy Lett., 2017, 2, 924–929 CrossRef CAS
.
- B. Q. Xu, H. W. Zhai, X. B. Liao, B. Y. Qie, J. Mandal, T. Y. Gong, L. Y. Tan, X. J. Yang, K. Sun, Q. Cheng, M. J. Chen, Y. P. Miao, M. Wei, B. Zhu, Y. K. Fu, A. J. Li, X. Chen, W. Min, C. W. Nan, Y. H. Lin and Y. Yang, Energy Storage Mater., 2019, 17, 31–37 CrossRef
.
- W. D. Zhang, H. L. L. Zhuang, L. Fan, L. N. Gao and Y. Y. Lu, Sci. Adv., 2018, 4, eaar4410 CrossRef PubMed
.
- C. Pan, S. J. Chen, Y. H. Huang, L. Wang, J. L. Luo and X. Z. Fu, J. Power Sources, 2022, 528, 231207 CrossRef CAS
.
- L. Fan, H. L. L. Zhuang, W. D. Zhang, Y. Fu, Z. H. Liao and Y. Y. Lu, Adv. Energy Mater., 2018, 8, 1703360 CrossRef
.
- Y. P. Tang, K. Shen, Z. Y. Lv, X. Xu, G. Y. Hou, H. Z. Cao, L. K. Wu, G. Q. Zheng and Y. D. Deng, J. Power Sources, 2018, 403, 82–89 CrossRef CAS
.
- H. Zhao, D. N. Lei, Y. B. He, Y. F. Yuan, Q. B. Yun, B. Ni, W. Lv, B. H. Li, Q. H. Yang, F. Y. Kang and J. Lu, Adv. Energy Mater., 2018, 8, 1800266 CrossRef
.
- H. L. Qiu, T. Y. Tang, M. Asif, X. X. Huang and Y. L. Hou, Adv. Funct. Mater., 2019, 29, 1808468 CrossRef
.
- H. L. Fan, C. H. Gao, Q. Y. Dong, B. Hong, Z. Fang, M. Y. Hu and Y. Q. Lai, J. Electroanal. Chem., 2018, 824, 175–180 CrossRef CAS
.
- K. R. Adair, M. Iqbal, C. H. Wang, Y. Zhao, M. N. Banis, R. Y. Li, L. Zhang, R. Yang, S. G. Lu and X. L. Sun, Nano Energy, 2018, 54, 375–382 CrossRef CAS
.
- Y. Ma, Y. T. Gu, Y. Z. Yao, H. D. Jin, X. H. Zhao, X. T. Yuan, Y. B. Lian, P. W. Qi, R. Shah, Y. Peng and Z. Deng, J. Mater. Chem. A, 2019, 7, 20926–20935 RSC
.
- K. Huang, Z. Li, Q. J. Xu, H. M. Liu, H. X. Li and Y. G. Wang, Adv. Energy Mater., 2019, 9, 1900853 CrossRef
.
- F. Zhao, X. F. Zhou, W. Deng and Z. P. Liu, Nano Energy, 2019, 62, 55–63 CrossRef CAS
.
- G. X. Huang, P. M. Guo, J. Wang, S. R. Chen, J. Y. Liang, R. M. Tao, S. Tang, X. F. Zhang, S. J. Cheng, Y. C. Cao and S. Dai, Chem. Eng. J., 2020, 384, 123313 CrossRef CAS
.
- J. X. Xing, L. Yan, T. Chen, Z. C. Song, Z. H. Wang, Y. C. Liu, L. J. Zhou and J. Z. Li, J. Colloid Interf. Sci., 2023, 652, 627–635 CrossRef CAS PubMed
.
- Z. H. Wang, J. Xue, Y. C. Liu, J. X. Xing, A. J. Zhou, J. Z. Li, W. Zou, F. Zhou and H. Li, Sci. China Mater., 2022, 65, 69–77 CrossRef CAS
.
- Y. C. Liu, T. Chen, J. Xue, Z. H. Wang, J. X. Xing, A. J. Zhou and J. Z. Li, Electrochim. Acta, 2022, 405, 139787 CrossRef CAS
.
- C. Wu, H. F. Huang, W. Y. Lu, Z. X. Wei, X. Y. Ni, F. Sun, P. Qing, Z. J. Liu, J. M. Ma, W. F. Wei, L. B. Chen, C. L. Yan and L. Q. Mai, Adv. Sci., 2020, 7, 1902643 CrossRef CAS PubMed
.
- Z. Y. Yao, W. S. Jia, Z. H. Wang, J. Ruan, X. G. Kong, X. Guan, Zh Wang, J. Z. Li, Y. Wang, W. Zou and F. Zhou, J. Energy Chem., 2020, 51, 285–292 CrossRef
.
- W. S. Jia, Y. C. Liu, Z. H. Wang, F. Z. Qing, J. Z. Li, Y. Wang, R. J. Xiao, A. J. Zhou, G. B. Li, X. Q. Yu, Y. S. Hu, H. Li, Z. X. Wang, X. J. Huang and L. Q. Chen, Sci. Bull., 2020, 65, 1907–1915 CrossRef CAS PubMed
.
- Y. Y. Liu, D. C. Lin, Z. Liang, J. Zhao, K. Yan and Y. Cui, Nat. Commun., 2016, 7, 10992 CrossRef CAS PubMed
.
|
This journal is © The Royal Society of Chemistry 2024 |
Click here to see how this site uses Cookies. View our privacy policy here.