DOI:
10.1039/D2TA09286G
(Review Article)
J. Mater. Chem. A, 2023,
11, 6796-6813
Various approaches to synthesize water-stable halide PeNCs
Received
29th November 2022
, Accepted 19th February 2023
First published on 22nd February 2023
Abstract
The “halide perovskite fever” is ongoing in material-based research due to the extraordinary properties of halide perovskites like high absorption coefficient, tunable band gap (throughout the visible range), near-unity emission quantum yield, large carrier diffusion length (exceeding 1 μm), and a long recombination time (∼μs order). However, the water instability of halide perovskites is an Achilles' heel that must be overcome. Recently, some approaches have been adopted to improve the water stability of ABX3 perovskites, including the substitution of A cations, ligand exchange, encapsulation in porous frameworks, passivation with inorganic or organic layers, and encapsulation in hydrophobic polymers and glass matrices. This review briefly introduces the degradation mechanisms according to the RH and summarizes various approaches to stabilize halide perovskites. An outlook for research directions of halide perovskites is also suggested.
1. Introduction
Solution-processed halide PeNCs have already set benchmarks in the research on optical devices1–4 and optoelectronic devices,5–7 especially solar cells8–11 (making them competitors to Si-based solar cells in terms of efficiency) and solid-state light-emitting diodes (providing outstanding colour purity and high luminescence efficiency).12–17 Despite the relatively short period of research, perovskite nanocrystals (PeNCs) achieved almost ∼30% power conversion efficiency (PCE),10 near-unity photoluminescence quantum yield (PLQY),14,18 large carrier lifetime (≥1 μs),19 and long carrier diffusion length (in the range of μm).20 However, instability in the presence of water impedes large-scale commercialization or daily use of products. Conventional emitters like inorganic chalcogenide nanocrystals and organic emitters exceed 106 hours of lifetime (LT50 = initial luminance dropping to 50% of the original value) with very low thermal stability.21 The PeNCs should meet the air/water stability criterion for commercialization, which is over 10
000 hours of lifetime at about 5000 cd m−2 needed for outdoor display applications.22 The instability is attributed largely to their low formation energy (0.1–0.6 eV) and the intrinsic ionic nature,23,24 making the PeNCs unstable in various external stimuli (water, light, and electric field).25,26 Another big concern in the case of lead halide perovskites is toxicity.27 These obstacles have brought extensive research on underwater stabilization of PeNCs and the reduction of toxicity, especially by encapsulating or replacing toxic Pb with Sn, Ag or Bi for industrial standards.
A variety of synthetic strategies have been explored to stabilize PeNCs under ambient conditions. Initially, the replacement of organic cations by inorganic cations like Cs+, Rb+, and Bi3+ was found to improve the thermal and water stabilities by many times even though it was not enough for commercialization.28,29 The hybrid perovskites may immediately degrade to their non-perovskite phase even under low humidity conditions because water molecules can form hydrogen bonding with the organic cations.26,30 Another important parameter to determine the stability of perovskites is the Goldschmidt tolerance factor (τ). It can be defined by
, where rA, rB, and rX are the effective ionic radii of the A, B, and X site atoms of the general form of the ABX3 perovskite. In a simple way, it indicates how the A cation can be fitted within the structural cage.31 Stability increases as the τ value approaches unity. Especially, since iodine-based perovskites have low τ values in the range of ∼0.85–0.9, they are prone to degradation compared to the bromide- or chloride-based perovskites (τ ≥ 0.9). It is often reported that inorganic perovskites can transform to 0D (Cs4PbI6), 3D (CsPbI3), and 2D (CsPb2X5) crystals at low relative humidity (RH) without much degradation in their optical properties;26 however, they degrade to the non-perovskite δ-phase in an aqueous solution (excess water). Now that commercial products are required to be stable in the water medium, this approach needs to be modified. Research has evolved to bi- or tri-cation substitutions to further enhance the stability under humid conditions.32,33 Also, the 2D/3D hybrid perovskite strategies are often used to utilize both exceptional optical properties of 3D perovskites and water immunity by 2D perovskites.34,35 Recently, new approaches have been explored. Surface passivation with a hydrophobic layer,36 porous materials,37,38 polymers,39 or inorganic materials has improved the stability of PeNCs under robust ambient conditions. Polymer coating of the PeNC surface and embedding PeNCs in a polymer matrix or glass matrix are good ways in terms of protecting water penetration as well as retention of PLQY.40–42
In this review, we provide a summary of recent advances in water stability, with a particular emphasis on the passivation and embedding of PeNCs or films as novel stabilization approaches. Section 2 briefly summarizes the degradation mechanism of PeNCs in the presence of water. Section 3 discusses conventional stabilization strategies such as cation substitution and ligand exchange. Section 4 introduces relatively new passivation strategies including insertion of PeNCs in a porous medium, encapsulation with inorganic nanomaterials, surface passivation with a hydrophobic/hydrophilic organic layer, and in situ growth in a polymer/glass matrix. This article ends with an outlook for future research directions.
2. Degradation by water: hydration, transformation, decomposition, and dissolution
The structure, composition, and optical characteristics of PeNCs are significantly affected by water molecules. The type of interaction with water molecules is dependent on the molar ratio of water to NCs. Formamidinium lead halide (FAPbX3), methyl ammonium lead halide (MAPbX3), and lead-free hybrid perovskites are likely to be hydrated by water molecules under low RH conditions (Fig. 1A–C).30,43–45 Water molecules can interact through hydrogen bonding with the uncoordinated ions and form mono-hydrated and di-hydrated structures (Fig. 1B). This hydration is a reversible process.46 Mosconi et al. thoroughly investigated the interaction of water molecules and MAPbI3, and they presented a model in which water molecules can penetrate into the MAPbI3 crystals to form hydrogen bonds with the methyl ammonium (MA) cations.47 The formation of the intermediate hydrated phase was experimentally proved through time-resolved photoluminescence (PL) measurements and infrared (IR) spectroscopy.47,48 Christians et al. reported that water molecules are also able to form a di-hydrated complex with the MAPbI3 even under dark conditions.49 The hydration leads to significant changes in the crystal structure, thereby in optical and electronic properties.50 Yang et al.51 systematically investigated the perovskite degradation process under controlled RH conditions by using in situ absorption spectroscopy and in situ grazing incidence X-ray diffraction. These studies confirmed the formation of hydrated products in the initial degradation step. The sequential perovskite hydration can be described using eqn (1): | 4CH3NH3PbI3 + 4H2O ⇌ 4[CH3NH3PbI3·H2O] ⇌ (CH3NH3)4PbI6·2H2O + 3PbI2 + 2H2O | (1) |
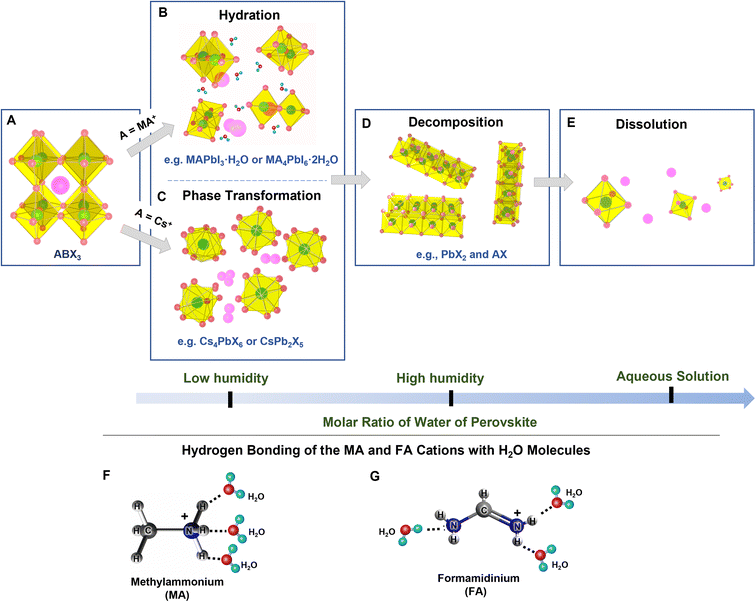 |
| Fig. 1 (A–E) Schematic representations of the interactions between water molecules and halide PeNCs (modified with permission from ref. 26). (F and G) Schematic representations of the formation of the hydrogen bonding of methylammonium (F) and formamidinium (G) cations with water molecules. | |
Unlike hybrid perovskites, all-inorganic perovskites undergo phase transformation under a low relative humidity atmosphere (Fig. 1C). For instance, Turedi et al. found that the interaction between water and three-dimensional (3D) perovskite CsPbBr3 can induce the phase transformation to two-dimensional (2D) perovskite-related CsPb2Br5 where the coordination number of Pb(II) changes from six to eight.52 Similarly, Lin et al. reported that a stable hydration shell can be formed on the surface of the Cs4PbBr6 (0D) crystals in the presence of water and the Cs4PbBr6 transforms into 3D corner-sharing CsPbBr3, and then into 2D edge-sharing CsPb2Br5,53 which can be illustrated using eqn (2) and (3).54
| Cs4PbBr6 → CsPbBr3 + 3CsBr | (2) |
| 2CsPbBr3 → CsPb2Br5 + CsBr | (3) |
Yu et al. reported reversible restoration of the luminescent CsPbBr3 phase from the non-luminescent CsPb2Br5 phase upon the removal of water.55 In contrast to the reversible hydration and phase transformation taking place at low RH, irreversible degradation occurs when PeNCs are continuously exposed to a high RH atmosphere and hence PbX2 and AX are formed spontaneously (Fig. 1D) which can be explained using eqn (4) and (5).46,56,57
| CH3NH3PbI3(s) → CH3NH3I(aq) + PbI2(s) | (4) |
| CH3NH3I(aq) ⇌ CH3NH2(aq) + HI(aq) | (5) |
Recently, Siegler et al. revealed that the degradation kinetics of MAPbI3 NC also can take place through a water-accelerated photo-oxidation.58 Moreover, the degradation process takes place more rapidly under UV irradiation and oxygen exposure because the CH3NH3+ bonding becomes weakened.59 Ho et al. reported that FA0.85Cs0.15PbI3 could be completely degraded to δo-CsPbI3, δ-FAPbI3, FA, and PbI2 through a multistep pathway at a high RH.60 In this case, the optical and electrical properties are mostly lost. For instance, Huang et al. reported a 90% loss of PL intensity in CsPbBr3 under high RH conditions.61 Christians et al. found a significant drop in photovoltaic efficiency of the CH3NH3PbI3 perovskite from 12% to 1% after 3 days of exposure to 90% RH.49 Caddeo et al. studied the degradation process by finite-temperature molecular dynamics and revealed that the decomposition kinetics is temperature dependent with an activation energy of 0.36 eV and the aggregated water molecules act as a catalyst to form the defects on PeNCs during the degradation process.62 Wu et al. reported that Pb-containing PeNCs has a high solubility constant (Ksp = 10−8) in an aqueous solution.63 Thus, the complete dissolution of perovskite crystals takes place in the aqueous precursor solution when the amount of water increases up to a threshold (Fig. 1E). For example, Hailegnaw et al. reported the complete decomposition of MAPbI3-based solar cells under exposure to rainwater where methylammonium lead iodide was decomposed to hydroiodic acid, methylamine, and lead iodide.64 The original black/dark brown color turned yellow and the device performance was significantly reduced. Ionized ions of Pb2+, Cs+, and X− could be formed in the presence of an excess amount of water (eqn (6)), but sometimes X− can inhibit the ionization of PbX2 and form [PbXn]2−n as shown in eqn (7).65
| PbBr2(s) ⇌ Pb2+(aq) + 2Br−(aq) | (6) |
| PbBr2(s) + (n − 2)Br−(aq) ⇌ [PbBrn]2−n(aq) | (7) |
Overall, a thorough knowledge of the interaction between water molecules and PeNCs is of significant importance in the development of water-stable perovskites and devices for real-life applications.66,67
3. Stabilization of PeNCs
3.1. Substitution of A cations
The ABX3 formula is commonly used to describe halide perovskites, where the A-site is an inorganic cation (often Cs+, Rb+, or K+) or an organic alkyl cation (typically, CH3NH3+ (MA+) or NH2CHNH2+ (FA+)) (Fig. 2A), which fills the cuboctahedral voids. Trimethyl sulphonium ions are also used to synthesize air-stable lead halide perovskites,68 in order to counterbalance [BX6]4− and stabilize the perovskite lattice. The cations can be categorized as mono, double, triple, or quadruple A-cation perovskites according to the number of A-site cations present in the crystal lattice. The crystal structures can be varied especially depending on the Goldschmidt tolerance factor (GTF) which normally falls in the range of 0.8–1.0.32 The GTF determines the ambient stability as well as the phase stability of PeNCs. When the GTF is close to 1, it leads to maximum ambient stability. In the case of organic–inorganic hybrid perovskites, the organic counterpart is responsible for the lower ambient stability due to its volatile nature. For example, the absorption intensity of MAPbI3 was considerably reduced at a high RH (98%) within 4 h with a blue-shifted absorption band edge, but the degradation took approximately 10
000 h at a lower RH (20%).69 Even doping with inorganic chalcogenides like PbSe enhances the stability as well as device performance of MAPbX3-based solar cells, with moisture stability enhanced 200 fold.70
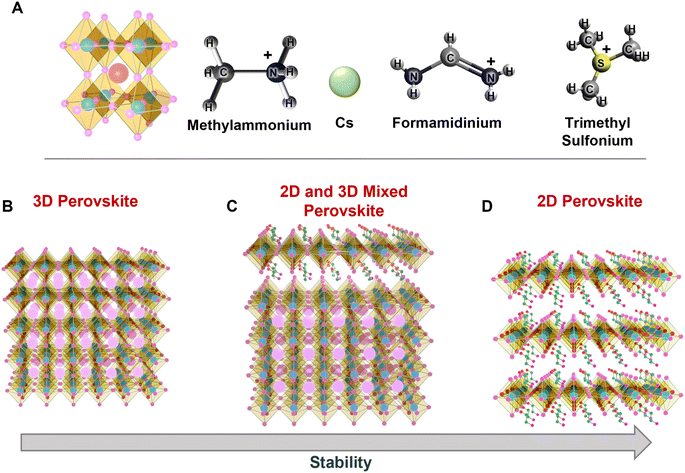 |
| Fig. 2 (A) The perovskite unit cell consisting of an A cation (methylammonium, Cs, formamidinium, trimethyl sulfonium) at the center, (B–D) schematic illustration depicting the crystalline structure of 3D perovskites (B), mixed-dimensionality perovskites (C), and 2D perovskites (D). | |
3.1.1. Inorganic cations.
It is well known that water molecules quickly transform the photoactive black phase of FAPbI3 into a photo-inactive yellow phase. The effective hydrogen bonding of the methylammonium cation (MA+) and formamidinium cation (FA+) with water molecules is responsible for the instability of MAPbI3 and FAPbI3.71 Also, weak electrostatic interaction between the MA+ and [PbI6]4− is another potential reason for the prompt degradation.69 In that sense, inorganic halide perovskites exhibit better thermal water stability than their hybrid family because of the absence of the bonding between Cs+ with the water molecule.26 Simply mixing the A-site cations with metals has been employed for improved water stability. Mixing a small fraction of stable Cs+ with the FA or MA-based perovskite successfully suppressed the formation of the optically inactive δ-phase by adjusting the GTF factor.72 Park et al. demonstrated that when 10% of FA+ was replaced by Cs+ in FAPbI3 the water stability was improved and photodegradation under constant UV illumination was minimized.73 Under continuous UV illumination (intensity = ∼100 mW cm−2) for 19 h, the FAPbI3 film showed 86% degradation, but the FA0.9Cs0.1PbI3 film showed 65% degradation. Under 85% humidity conditions for 7 h, the FAPbI3 film had 77.8% degradation; meanwhile, the FA0.9Cs0.1PbI3 film showed 50% degradation. Wu et al. further observed that using triple cation Cs/MA/FA was more robust in terms of stability, reproducibility, and efficiency. They have reported that perovskite NCs showed long-term stability for up to one month under 30% RH and PCE above 20%.74
3.1.2. Organic cations.
2D perovskites have recently drawn immense attention due to their superior stability and water resistance compared to 3D perovskites. 2D layered perovskites are represented as R2(CH3NH3)n−1BnX3n+1 , where n, R, B, and X denote the number of inorganic layers, organic cations such as C6H5(CH2)2NH3+ (phenyl-ethyl ammonium, PEA), a metal cation, and a halide, respectively. The improved moisture resistance of 2D perovskites comes from the presence of the hydrophobic R group shown in Fig. 2B. The R-groups occupy the surface site of the crystals and protect them from water penetration. Sargent and colleagues generated a series of dimension-controlled quasi-2D MAPbBr3 perovskites via partial substitution of MAs by hydrophobic phenethylamine (PEA) molecules.75 The moisture stability was improved after this process. The PEA-substituted MAPbI3 film showed a negligible change in the adsorption edge and PL intensity after storage under 90% humidity conditions for 3 months. Romani et al. recently synthesized a 2D lead-free metal halide perovskite (PEA2SnBr4) showing impressive and unprecedented water resistance in both structural and optical properties.76 PEA2SnBr4 did not alter its Sn2+ oxidation peak position (487.6 eV) in XPS even after continuous stirring in water for 4 h. It is notable that partial substitution of the anions by SCN functional groups also improved the moisture stability.77 The SCN-substituted film exhibited prolonged stability for 4 h under 95% high humid conditions compared to the normal CH3NH3PbI3 film (2.5 h). One of the concerns regarding organic molecular capping is that the dielectric organic layer hinders efficient carrier insertion and anisotropic charge transport. Coating a 2D layer on top of the 3D perovskite (2D/3D hybrid) has been investigated as a promising approach to simultaneously obtain water stability and good charge transport. Liu et al. achieved extraordinary long-term stability (>10
000 h, or >400 days) with no reduction in efficiency over a vast area by depositing pentafluorophenyl ethylammonium (FEA) lead iodide [(FEA)2PbI4], which is a superhydrophobic 2D perovskite, onto the 3D FAPbI3 perovskite films.78 The highly stable perovskites allowed the fabrication of a fully printable, low-cost, high-efficiency solar module that can be assessed under standard settings and in the presence of oxygen and moisture.79
3.2. Ligand exchange
Ligands in perovskites play a vital role in stability and morphology. Oleic acid (OA) and oleyl amine (OLAm) are a common pair used for the synthesis of perovskites. It is well known that the OA/OLAm pair causes feasible degradation of perovskites through proton exchange under ambient conditions. In addition, the purification process of perovskite NCs causes ligand losses which accelerates the degradation to the non-perovskite δ-phase. Generally, organic ligands with a polar head group increase their size in the presence of moisture or polar solvents, leading to detachment from the surface of PeNCs and giving a chance to be replaced by other ligands with comparatively strong interaction with PeNCs. For example, the commonly used OA, O-polar head group has lower interactions compared to the S-head group of other alkyl-polymers. The O-polar ligands are replaced with the S-containing ligands and thus the stability and dispersability of PeNCs are enhanced.80 Different types of ligands have been exploited either during the reaction as well as in the post-synthetic treatment.81–84 It is observed that the ligand chain length, ligand concentration, and molecular structure of the ligand (denticity, linear/branched structure) have direct effects in determining the shape and size of the NCs (Fig. 3A). Bulky ligands have less coverage on the surface, which leads to rapid attachment to the respective facets to form perovskite nanocubes.85,86 Long-chain alkyl ammonium salts can increase the hydrophobicity and solubility of organic solvents of PeNCs.87 PeNCs passivated by zwitterionic and bidentate ligands have enhanced colloidal stability, thermal stability as well as moisture stability compared to PeNCs with monodentate ligand caps.88 Liu et al. carried out an in-depth investigation on the roles of organic amines and acids in the ligand-mediated synthesis of colloidal CsPbBr3 NCs. They discovered that ammonium ions can lead to the growth of anisotropic nanoplatelets and carboxylate ligands are essential for the size-tunability of isotropic nanocubes.89 During the purification process of perovskite NCs, ligands are detached from the surface of the NCs which causes low colloidal stability and thus a lengthy washing step is not desirable (Fig. 3B).
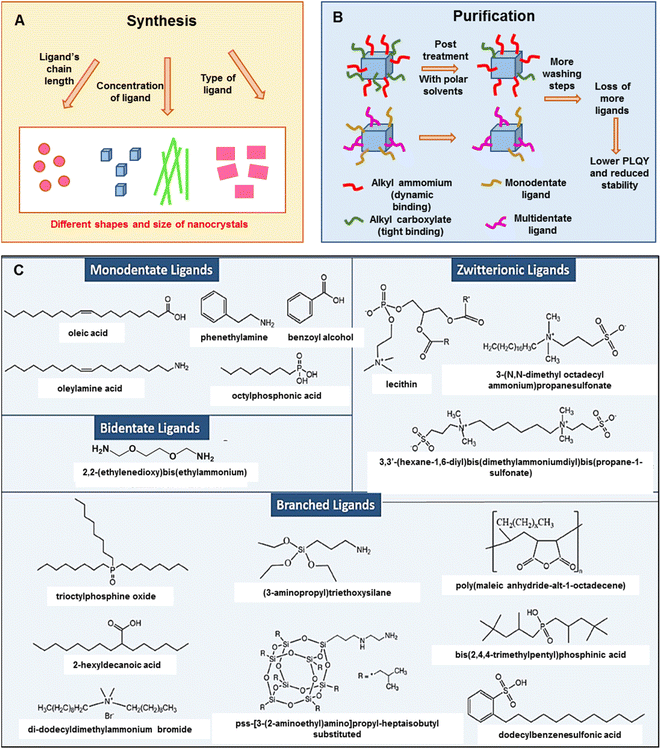 |
| Fig. 3 (A and B) A schematic representation of the role of ligands in the synthesis and purification of PeNCs (modified with permission from ref. 92). (C) Chemical representation of different types of capping ligands used for PeNCs (adopted with permission from ref. 92). | |
High-density insulating ligand passivation deteriorates optoelectronic properties; hence different types of ligands have been explored to balance between stability and optoelectronic performance. Surfactants (didodecyldimethylammonium sulfide (DDA+S2−),81 sodium dodecyl sulfate (SDS),82 dodecylbenzenesulfonic acid (DBSA),90etc.), bi-dentate ligands (succinic acid, 2,2′-iminodibenzoic acid,83N1,N2-didodecyl-N1,N1,N2,N2-tetramethylethane-1,2-diaminium bromide (DTDB),91etc.), branched ligands,84,92 and zwitterionic ligands84,93 have been proved to enhance the ambient stability of PeNCs (Fig. 3C). Branched or zwitterionic ligands have an additional advantage on the smaller and mono-dispersed size distribution of PeNCs especially due to the presence of substantial steric hindrance.94,95 Additionally, zwitterionic ligand-capped PeNCs often reduce the tedious purification process and form highly packed films with high PLQY and have good stability compared to straight-chain ligands.94 Furthermore, the perovskites can even be sheltered from water by bidentate ligands that link with one another between molecules. For example, Nag et al. demonstrated that long-range cation-stacking is one method by which aromatic diamine ligands like 4,4′-trimethylenedipyridine shield perovskites from water.96 They have shown that there was no difference in PL after keeping in water for six months. Similarly, Huang et al. reported that silane ligands like 3-aminopropyl triethoxysilane (APTES) form a cross-linking matrix by hydrolyzing the silyl ether groups. The APTES ligand effectively protected the perovskite from humidity and increased the resistance to UV and polar solvents.97 Recently, Shu et al. synthesized CsPbBr3 NCs with high PL intensity through the modified ligand-assisted reprecipitation in which an amphiphilic polymer ligand, octylamine-modified polyacrylic acid (OPA), was used for the synthesis. The PLQY of the OPA-capped CsPbBr3 NCs remained at 80% of the initial value in water for 15 days.98 Kim et al. proposed a new strategy to synthesize stable PeNCs by controlling the peripheral layer of the octahedral perovskite geometry.99 A series of rod-shaped fluorescent hybrid perovskites were synthesized under both acidic and basic conditions without using any capping ligands. They claimed that lead bromide perovskites were stable for up to 6 months underwater without any structural change. Even though there has been significant stability improvement in bromide-based perovskites, there have been almost no reports on water-stable iodide-based perovskites because they are very prone to degradation compared to bromide-based perovskites.
4. Novel passivation approaches to achieving water stability
There have been significant efforts made to advance passivation of PeNCs for improved water stability,100–102 which include inserting the NCs in pores in a porous matrix, embedding in a polymer matrix or in a glass matrix, creating an inorganic coating layer, and superhydrophobic/superhydrophilic functionalization (Fig. 4).103–105 A large density of defect states inside the energy bandgap of conventional semiconductors can function as trapping states which originate from the corresponding structural defects. Brandt et al. explained the defect tolerance of halide perovskites in their electronic structures.106 They revealed that intrinsic defects generating from the vacancies or interstitial atoms appear as resonances inside the bands; therefore, the surface states are unlikely to develop the intragap states. It means that it is not strictly necessary to use surface ligands or other forms of electronic surface passivation to maintain the purity of the energy bandgap and high PLQY.107 On the basis of this theoretical prediction, various synthetic approaches have been developed for high-performance stable PeNCs.
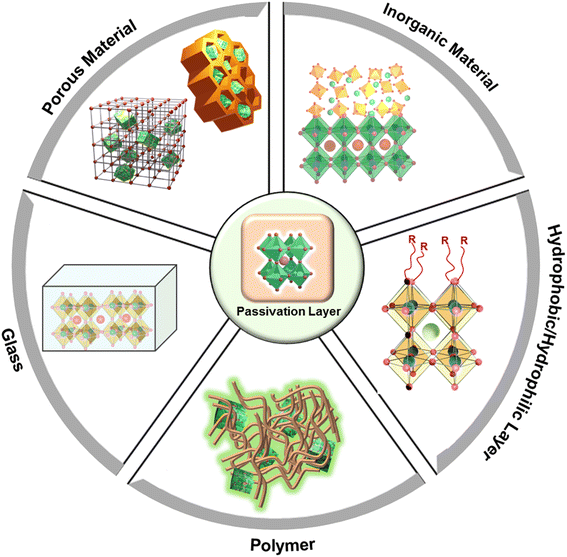 |
| Fig. 4 A schematic representation of the various methods for surface passivation of PeNCs. | |
4.1. Surface passivation by using a porous matrix
Various species of porous matrices (e.g., mesoporous silica, zeolites, molecular sieves, porous polymeric frameworks etc.) have provided promise for the synthesis of water-stable PeNCs. The porous matrix acts as a template to confine PeNCs inside and keep them intact with water molecules.108,109 Superhydrophobic modification can further enhance the aqueous stability of PeNCs. Recently, Xuan et al. developed water-stable Sr2+-doped CsPbBr3 which was encapsulated by a molecular sieve matrix and PbBr(OH) composite matrix (Fig. 5A).110 These composites exhibited 75% PLQY and showed high resistance to heat and water. Impressively, they sustained 99.5% of their initial PLQY even after 200 days when submerged in water, and 63.1% when exposed simultaneously to blue light and water. Wang et al. used crystalline inorganic zeolites (AlPO-5) as a porous framework where MAPbBr3 NCs were in situ synthesized in the nanopores of zeolite (Fig. 5B).111 The nanoconfinement substantially reduced the formation of structural defects in the PeNCs and significantly reduced the lattice vibration so that PL could be maintained at 80 °C. Bright green luminescence of the MAPbBr3/zeolite composite was sustained for fifteen months under ambient conditions and maintained for two weeks under aqueous conditions. Although the PL intensity of this composite was reduced to 5% of its initial value at 135 °C, PL was gradually restored during the cooling process. Xuan et al. demonstrated that porous organic polymeric frameworks also serve as a protection shield to stabilize PeNCs under real-life conditions (Fig. 5C).107 The organic framework had a hierarchical porous architecture which contained pores ranging from the nano-to micrometer scale. The superhydrophobicity of the organic framework with a water contact angle larger than 150° facilitated selective absorption of CsPbX3 NCs and made the resultant composite completely phase separated from water (floating on the water phase). Even after 6 months of being submerged in water, this composite sustained its bright luminescence without signs of hydrolytic degradation. In addition, Ma et al. fabricated a superhydrophobic polymeric (polydivinylbenzene) porous matrix which provided a confined space to absorb Cs4PbBr6 QDs (Fig. 5D).112 Initially the composite was non-luminescent; however, the Cs4PbBr6 phase was transformed into a luminescent CsPbBr3 phase with underwater exposure through the dissolution of CsBr. This structural transformation was reversible, turning back to the non-luminescent Cs4PbBr6 after evaporation of water through the reintegration of CsBr. Here, the superhydrophobic encapsulation prevented the migration of dissolved CsBr, resulting in the stabilization of the CsPbBr3 phase. It showed high water stability and retained more than 80% of initial PLQY after prolonged immersion in water for 12 days. The reversible luminescence was used to fabricate an anticounterfeiting device with high-water stability.
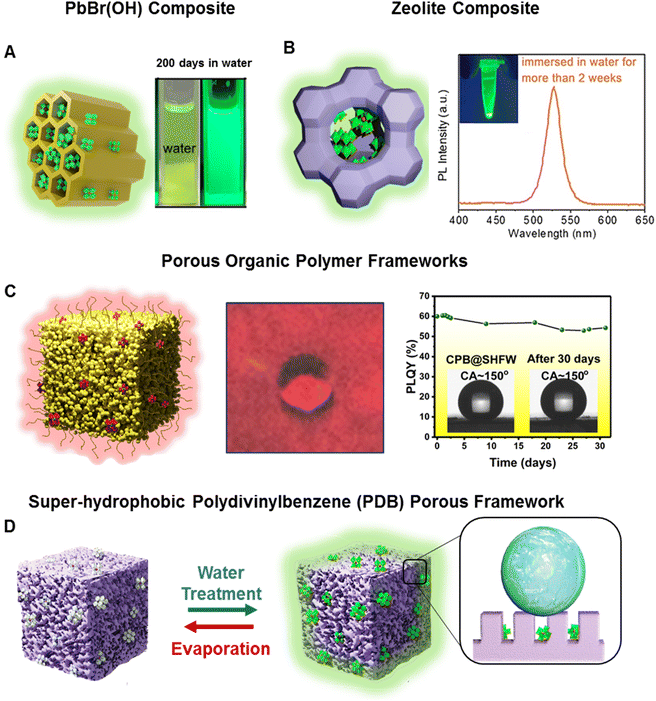 |
| Fig. 5 Passivation in a porous matrix. (A) Scheme of the Sr2+-doped CsPbBr3/molecular sieve/PbBr(OH) composite and digital image after being stored for 200 days in an aqueous solution (modified with permission from ref. 110). (B) Scheme of the zeolite/perovskite composite and its PL spectra after being immersed in water for more than 2 weeks (modified with permission from ref. 111). (C) Scheme of the porous organic polymeric frameworks embedded with CsPbX3 NCs, digital image of beaded water drops on the composite films, graph representing the change in photoluminescence quantum yield (PLQY) of the composite in the water medium (inset: the CA pictures before and after being submerged in water for 31 days) (modified with permission from ref. 107). (D) Scheme of the PeNCs embedded in the super-hydrophobic polydivinylbenzene (PDB) porous framework. The non-luminescent Cs4PbBr6 and luminous CsPbBr3 were reversible by alternating water treatment and drying (modified with permission from ref. 112). | |
4.2. Surface passivation by using inorganic encapsulation
Placing a wide-bandgap inorganic passivation layer on the surface of PeNCs decreased the surface recombination rate of charge carriers and provided durability under harsh environmental conditions.113 Recently, various types of inorganic passivating materials (SiOx, InBr3, ZnCl2, ZnBr2, PbBr2, AgNO3, BiCl3, SnCl4, CuBr2, etc.) have been widely investigated to stabilize PeNCs.114–117 For instance, Hu et al. reported a facile approach to developing a superhydrophobic SiOx-coated CsPbBr3 film by hydrolyzing tetramethyl orthosilicate and then surface-modifying with CH3- groups (Fig. 6A).118 The superhydrophobic perovskite film exhibited good water repellence showing a 25% PL decrease under aqueous conditions for 10 days, self-cleaning characteristics, and enhanced thermal stability at 70 °C. Interestingly, the PL intensity of the film was enhanced by 46% after three months of storage under ambient conditions. XRD spectra and HRTEM images revealed the formation of mixed phases including CsPbBr3, CsPb2Br5, and Pb(OH)Br during the prolonged ambient exposure.
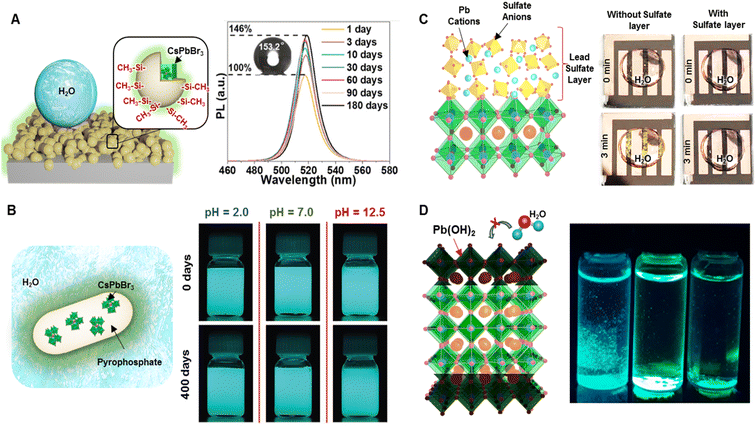 |
| Fig. 6 Surface passivation by inorganic encapsulation. (A) Scheme illustrating the film of the superhydrophobic SiO2-encapsulated CsPbBr3 composite and PL spectra of the composite film at various time points after being stored in an ambient environment, (inset: water contact angle of the water droplet on the composite film after 3 months of storage in the ambient atmosphere) (modified with permission from ref. 118). (B) Scheme of the encapsulated CsPbX3 nanocrystal with inorganic pyrophosphate and a digital image of the composite dispersed in an aqueous solution of different pH (modified with permission from ref. 119). (C) Scheme depicting the top layer of lead sulfate on the perovskite surface as a passivation layer and photographs of the device after being exposed to a water droplet for three minutes without (left) and with (right) the top layer lead sulfate (modified with permission from ref. 113). (D) Scheme showing the formation of the Pb(OH)2 layer which can protect the PeNCs from water molecules and the digital image of the Pb(OH)2 layer coated on different PeNCs after being immersed in water under UV light (modified with permission from ref. 99). | |
Zhong et al. reported the encapsulation of CsPbX3 NCs with inorganic pyrophosphate (NH4AlP2O7) (Fig. 6B).119 One of the important requirements for the inorganic passivation layer is the strong interactions between the perovskite surface and passivation layer so that it can be sustained under harsh environmental conditions. Density functional theory (DFT) calculation confirmed the formation of a strong Pb–O bond between the P2O74− group and the Pb atom in CsPbBr3. The strong bond provided remarkable stability against water, heat, and UV irradiation. Interestingly, pyrophosphate-encapsulated CsPbBr3 could make highly stable dispersion in a water medium due to its negative zeta potential (−30.2 mV). The PL intensity of their aqueous dispersion remained intact even after storing for 400 days. Moreover, the dispersed composite material retained its PL even in extremely acidic (pH 2.0) and basic (pH 12.5) solutions after 400 days. The core–shell encapsulation protected the PeNCs from heat deterioration and UV light-induced degradation. This highly stable aqueous dispersion was used in high-resolution inkjet printing on paper which was kept in an aqueous medium for 100 days without any noticeable loss of PL intensity and any trace of lead leakage. Water-insoluble lead salts such as PbSO4, PbCO3, and Pb3(PO4)2 have been used for surface passivation in perovskite-based solar cells. Although hydration and dissolution in an aqueous medium are the main reasons for the PeNC degradation, the lead(II) oxysalt layer was robust enough to prevent water from permeating into the perovskite. For instance, Yang et al. developed PbSO4 and Pb3(PO4)2 layers on perovskite films and demonstrated an enhanced water resistance of the perovskite surface (Fig. 6C).113 X-ray photoemission spectroscopy measurements and DFT calculation confirmed the strong preferential interaction of SO42− and PO43− with Pb atoms of the perovskite surface. When the lead sulfate-coated perovskite device was submerged in water, it remained black instead of turning yellow, which was caused by the formation of PbI2. The coating layer allowed a fast carrier recombination lifetime and increased the solar conversion efficiency up to 21.1%. The solar cell maintained 96.8% of the original efficiency for 1200 h at 65 °C. The formation of the Pb(OH)2 layer was also able to stabilize PeNCs. Jana et al. reported a simple aqueous synthesis of rod-shaped PeNCs in basic or acidic media where a layer of Pb(OH)2 was formed on the surface of perovskites as confirmed by XRD and TEM analysis (Fig. 6D).99 The Pb(OH)2 layer effectively prevented water diffusion into the perovskite, thus retaining the PL intensity even when immersed in water over 6 months.
4.3. Passivation by post-treatment with a hydrophobic/hydrophilic organic layer
Degradation of PeNCs is usually initiated from the defect sites in the grain boundaries and surfaces. These defects are reactive towards oxygen and water which makes them vulnerable even under ambient conditions.120 Recently, various electron-donating hydrophobic molecules have been investigated to effectively reduce the defect-nucleating sites or heal the existing defects on perovskite films, which has been performed by chemically binding organic molecules on the undercoordinated lead ion sites (Fig. 7A).36 Mathews et al. demonstrated that passivating the perovskite surface and grain boundaries with hydrophobic pentafluoropropyl ammonium iodide could improve the device efficiency by reducing charge carrier recombination and increasing its lifetime.121 This passivated perovskite solar cell exhibited remarkable stability under ambient conditions for 169 days without any structural change and maintained above 95% of its initial efficiency. Superhydrophobic modification could further improve the water stability of PeNCs.122–124 For instance, Zhang et al. developed a superhydrophobic lead PeNC film by creating a self-assembled monolayer of 1H,1H,2H,2H-perfluorodecanethiol.36 The thiol group of the perfluorocarbon chains passivated the uncoordinated sites on the perovskite surface by forming the Pb–S bond.
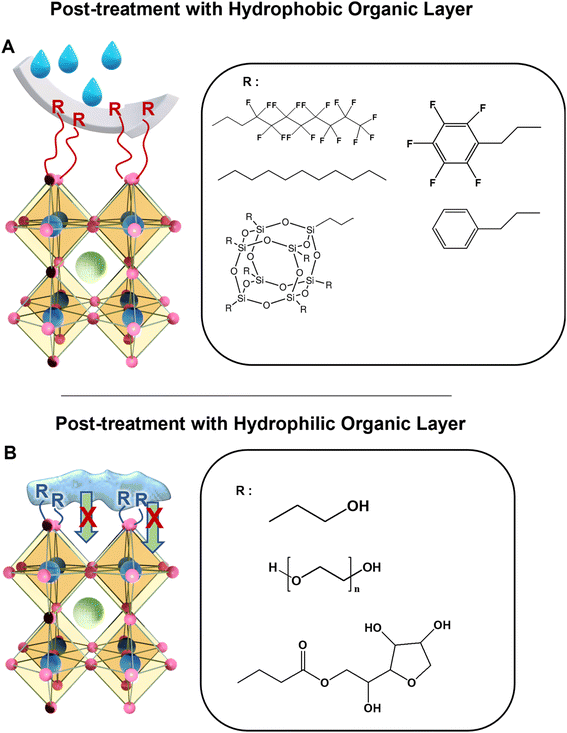 |
| Fig. 7 (A) Schematic diagram representing hydrophobic passivation of the perovskite surface by using different hydrophobic molecules. (B) Schematic representation of the hydrophilic passivation of the perovskite surface utilizing several hydrophilic molecules. | |
Despite the common belief that the hydrophilic layer can help water penetration, the hydrophilic passivation layer can also improve the stability of the perovskite against moisture (Fig. 7B). For example, Ma et al. showed that the post-treatment of a perovskite film with hydroxyl group-containing amine molecules could help to sustain the device efficiency under high humidity conditions.125 The water-holding capability of the hydrophilic layer was considered to prevent water inclusion underneath the perovskite surface. No significant decrease in the power conversion efficiency was observed in an 80% RH atmosphere for 24 h. Additionally, Kim et al. demonstrated that surface passivation with a thin hygroscopic polymer such as poly(ethylene glycol) allowed perovskite-based solar cells to become stable under ambient conditions.126 More than 95% of the initial value of the device efficiency was maintained after 15 h in an ambient environment. Recently, Chen et al. have developed a passivation method for perovskite films by using superhydrophilic sorbitan monolaurate molecules.127 Multiple ether, carbonyl, and hydroxyl groups found in sorbitan monolaurate molecules could absorb water molecules and serve as a potent water diffusion barrier. After being submerged in water for 6 h, the passivated perovskite film continued to be black with no structural changes.
4.4. Encapsulation with polymers
Polymer encapsulation is advantageous, in addition to surface passivation of PeNCs, in chemical modification of the composite surface, tunable mechanical properties, easy processability, and optical transparency.128,129 Encapsulation with crosslinked polymers creates an oxygen barrier and chemical resistance layer to polar solvents.130–132 Because the miscibility of nanomaterials is limited with polymers, in situ conversion of precursors mixed in a polymer matrix has been considered as an effective method for large-scale synthesis of perovskite composites. Wang et al. introduced a swelling/deswelling approach for in situ growth of PeNCs in a polymer matrix by using different polymer solubilities in solvents (Fig. 8A).133 The perovskite precursors were incorporated inside the polymer matrix when the polymer matrix was swollen in a relatively good solvent. The evaporation of the solvent initiated rapid homogeneous crystallization of the PeNCs in the shrunk polymer matrix. Several polymer matrices have been utilized, but polystyrene, polyvinyl chloride, acrylonitrile butadiene styrene, and polycarbonate polymer composites exhibited superior water stability. The perovskite/polymer composites were kept immersed in water for 120 days with less than a 7% loss in PLQY. On the other hand, in situ synthesis of PeNCs has also been conducted by using a UV-curable polymer. For instance, Zhang et al. synthesized PeNCs from the precursor absorbed in the photo-polymerizable hydrophobic polyacrylate matrix which improved the protection of the PeNCs from water (Fig. 8B).40 Owing to low water permeability and high chemical durability of the polyacrylate matrix, the perovskite/polymer matrix survived in harsh aqueous media in pH 2 to pH 12. The lead leakage in an aqueous medium was significantly reduced, allowing for its usage in biomedical applications. Wang et al. employed two-dimensional silica nanosheets as nanoreactors in which a hydrophobic poly(acrylic acid)-block-polystyrene brush was grafted (Fig. 8C).134 The polymer brush produced a thick hydrophobic barrier. The brush collapsed when it came into contact with water molecules due to their hydrophobicity.
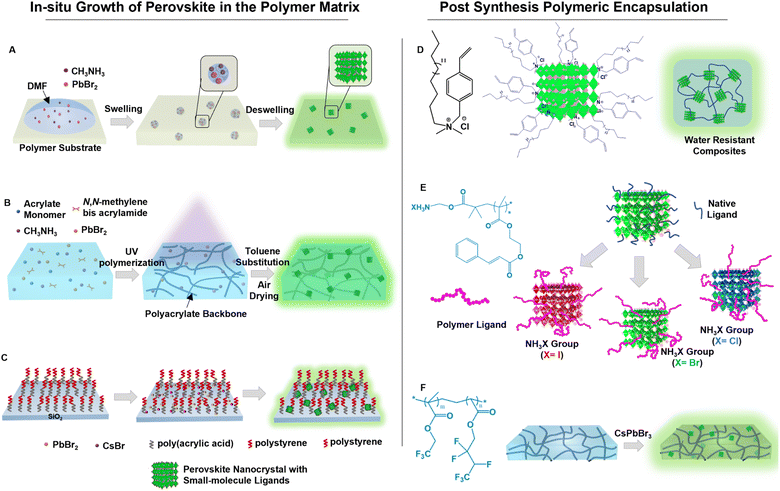 |
| Fig. 8 Passivation by embedding in the polymer matrix. (A) Scheme representing the swelling–deswelling approach for the in situ growth of PeNCs in the polymer matrix (modified with permission from ref. 133). (B) Scheme depicting the synthesis of PeNCs inside the photo-polymerizable hydrophobic polyacrylate matrix (modified with permission from ref. 40). (C) Scheme illustrating hydrophobic two-dimensional silica nanosheets grafted with poly(acrylic acid)-block-polystyrene. The nanosheets were used as nanoreactors for in situ synthesis of PeNCs (modified with permission from ref. 134). (D) Scheme of the post-synthesis using 4-vinyl-benzyl-dimethyl octadecyl ammonium chloride as a photo-crosslinkable and polymerizable ligand onto PeNCs (modified with permission from ref. 135). (E) Scheme of post-encapsulation of PeNCs with ammonium halide-terminated poly(2-cinnamoyloxyethylmethacrylate) (modified with permission from ref. 42). (F) Scheme representing a self-healable hydrophobic elastomer with dipole–dipole interaction used for post-synthesis encapsulation of PeNCs (modified with permission from ref. 135). | |
Modification by post-synthesis treatment has also been investigated. In this method, photo-crosslinking of the unsaturated hydrocarbon ligands on the PeNC surfaces has been used to develop water-stable uniform PeNCs and a polymer composite layer. For example, Park et al. reported a novel method for improving perovskite stability by using 4-vinyl-benzyl-dimethyl octadecyl ammonium chloride as a photo-crosslinkable and polymerizable ligand (Fig. 8D).135 The ammonium sites of the ligand enabled adequate ionic interaction with the perovskite surface, the styryl group enabled the crosslinking of two neighbouring nanocrystals through radical polymerization, and the alkyl side chain provided the hydrophobic protection to enhance resistance to hydrolytic degradation. Similarly, Sun et al. also used 4-vinylbenzyl-dimethyloctadecylammonium chloride as a photo-crosslinkable ligand for MAPbBr3. This composite showed no significant change in PL intensity after prolonged water exposure for 90 days.136 In another report, Jang et al. developed highly water-stable PeNC composites using a UV-induced free-radical reaction of a methacrylate-functionalized matrix resin. This composite could maintain high PLQY (∼70%) for more than 600 days in high abrasive liquid medium (e.g., in water, acid and basic solutions, and in different organic solvents).137 Ligand exchange by long polymer chains has also been successful in passivation. Ko et al. reported the ligand exchange by ammonium halide-terminated poly(2-cinnamoyloxyethylmethacrylate) (Fig. 8E).42 The cinnamoyl group could undergo the UV-induced cycloaddition reaction which significantly reduced lead leakage and increased stability toward diverse polar solvents (such as water or alcohol). Recently, Liu et al. used a self-healable hydrophobic fluoroelastomer as the polymer matrix for post-synthesis encapsulation of PeNCs (Fig. 8F), in which the ion–dipole interactions between the positively charged perovskite QDs and the CF3 dipoles on the polymers provided excellent compatibility.138 Moreover, abundant dipole–dipole interactions of CF3 groups enabled the underwater healing process of this material. After being submerged for months under a variety of harsh conditions (water, pH 1, pH 7, pH 13, and salty water), the optical and mechanical characteristics of the composite remained intact.
Recently, the encapsulation of PeNCs with block copolymers has been proven to be a potential method to increase stability due to the self-assembly of the polymer chains and the effective interaction between block copolymers and PeNCs. For instance, Zhou et al. prepared air- and water-stable stretchable MAPbBr3 PeNC composites in the polystyrene-block-poly(ethylene butylene)-block-polystyrene (SEBS) matrix. The average PL lifetime of the composite varied from 368.3 ns to 599.8 nm before and after being submerged for 70 days in water. However, PL intensity was significantly increased to 225% after 70 days of immersion in water due to the oxidation of Pb atoms which quenched excitons and created the platelet structures with reduced surface defects.139 Similarly, Park and coworkers developed a moisture stable MAPbX3 NC film by passivating with polystyrene-block-poly(2-vinylpyridine).140 The poly(2-vinylpyridine) chains effectively prohibited water molecules from entering the MAPbBr3 NCs. PLQY of this PeNC film remained unaltered at high temperature (150 °C) and high RH (70%) for 24 h. As demonstrated by Liu et al.,141 a colloidal solution including MAPbBr3/SiO2 NCs passivated by starlike trilobe poly(2-hydroxyethyl methacrylate)-graft-poly(acrylic acid)-block-polystyrene (partially crosslinked) exhibited no significant change in the PL emission peak for 300 min in the presence of 20% water. Further, Yang et al. reported that MAPbBr3 QDs passivated by polystyrene-block-poly(ethyl oxide) were stored in an aqueous solution for more than 7 months and exhibited a slight PLQY decrease (from 43% to 33%) and a slight red-shift (1 nm) of the PL emission.142 In another report, He et al. fabricated a MAPbBr3/SiO2 NC thin film, in which the NCs were capped with polystyrene block copolymers, and showed strong PL intensity after 30 min in water.143 In another report, Avugadda et al. developed the synthesis of PeNCs in the capsules of polystyrene-block-poly(acrylic acid). The encapsulated PeNCs retained the initial PLQY (60%) even after being dispersed in water for 2 years.144
4.5. Perovskite crystallization in a glass matrix
Encapsulation in glass has been one of the main approaches for the passivation of implantable devices. The perovskite crystallization inside a glass matrix can provide exceptional chemical and physical stability.145 Laser-induced in situ crystallization has been widely employed to produce highly stable 3D perovskite patterns for advanced photonic applications. For instance, Huang et al. used femtosecond laser irradiation and thermal annulation to demonstrate reversible encryption by creating 3D perovskite patterns and removing the patterns within the glass matrix (Fig. 9).41 Here, the femtosecond laser provided an extremely high power density which allowed formation of the CsPbBr3 QDs deep inside the glass. By employing a computer-controlled stage, this method also made it possible to print complicated three-dimensional patterns. The size and luminescence intensity of the CsPbBr3 QDs could be tuned by adjusting the laser exposure time, laser power density, and moving speed of the sample stage. No discernible loss of PL intensity was observed in ethanol and deionized water for 90 days. Similarly to this work, Dong et al. fabricated CsPb(Cl/Br)3 patterns within a borosilicate glass by using femtosecond laser irradiation and subsequent low-temperature thermal treatment.146 Femtosecond laser irradiation assisted localized collapse of the glass matrix which enabled the atoms to migrate into the glass and form crystal nuclei. The nuclei grew into PeNCs during heat treatment at 400 °C. The laser-printed PeNC patterns remained intact even after a month of immersion in deionized water.
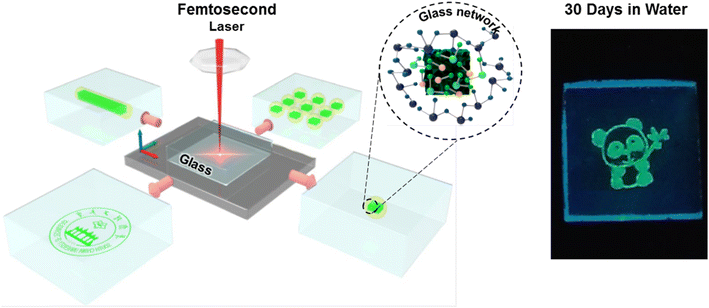 |
| Fig. 9 Scheme of the 3D perovskite patterns generated inside the glass matrix by using femtosecond laser irradiation and the digital image of CsPbBr3 patterns after being stored in water for 30 days (modified with permission from ref. 41). | |
5. Conclusion and outlook
The superior optoelectronic properties of the halide PeNCs necessitate moisture stability for practical applications. We have summarized the synthetic strategies to obtain water stability without degrading their intrinsic optical properties. Hydrocarbons such as polymers, ligands, or mesoporous hydrophobic organic frameworks have been intensively employed to achieve remarkable underwater stability. In Table 1, we have summarized recent progress in the synthesis of water-stable PeNCs by employing different approaches.
Table 1 Summary of recent progress in moisture or water stability of perovskites adopting different approaches
Perovskite |
Passivation agent |
Ambient atmosphere |
Under water |
Under acidic or basic solution |
Ref. |
Sr2+ doped CsPbBr3 |
Molecular sieve/PbBr(OH) composite matrix |
— |
99.5% PLQY retention after 200 days |
— |
110
|
MAPbBr3 |
Zeolite (AlPO-5) encapsulation |
Stable for 15 months |
Stable for >2 weeks |
— |
111
|
CsPbBr3 |
Superhydrophobic porous polymer matrix |
— |
Stable for 6 months. |
— |
107
|
CsPbBr3 |
Superhydrophobic poly(divinylbenzene) porous matrix |
— |
>80% PLQY retention after 12 days |
— |
155
|
CsPbBr3 |
Silicon-based molecular sieve encapsulation |
— |
∼100% PL retention after 50 days |
100% PL retention after 50 days in 1 M HCl solution |
156
|
CsPbBr3 |
Mesoporous SiO2 encapsulation |
— |
95% PL retention after 30 days |
55% PL retention after 30 days |
157
|
CsPbBr3 |
Superhydrophobic SiO2 encapsulation |
46% PL enhancement after 3 months |
75% PL retention after 10 days |
— |
118
|
CsPbBr3 |
Inorganic pyrophosphate (NH4AlP2O7) encapsulation |
— |
Stable for 400 days |
Stable for 400 days (pH 2.0 and 12.5) |
119
|
Cs0.05FA0.81MA0.14PbI2.55Br0.45 |
PbSO4 and Pb3(PO4)2 layers |
96.8% PCE retention for 1200 hours at 65 °C |
Stable for 3 min |
— |
113
|
MAPbBr3, MAPbBr3−xClx, CsPbBr3 |
Pb(OH)2 layer |
— |
Stable over over 6 months |
— |
99
|
FAPbI3 |
Pentafluoropropylamonium iodide layer |
95% PCE retention for 169 days |
— |
— |
121
|
Cs0.05(FA0.85MA0.15)0.95Pb(I0.85Br0.15)3 |
Self-assembled monolayers of 1H,1H,2H,2H-Perfluorodecanethiol |
100% PCE retention for 7 days at 55% RH |
|
Stable for 45 s in an acidic solution |
36
|
(FEA)2PbI4 |
Pentafluorophenylethyl ammonium (FEA) lead iodide bilayer |
90% PCE retention after 1000 h at 40% RH |
— |
— |
78
|
FAPbI3 |
Hydroxyl group-containing amine layer |
90% PCE retention after 1000 h at 20% RH |
— |
— |
125
|
MAPbI3 |
Hygroscopic poly(ethylene glycol) (PEG) layer |
Stable for 15 days at 88% RH |
— |
— |
126
|
FA0.85MA0.15PbI3 |
Hydrophilic sorbitan monolaurate molecules layer |
90% PCE retention after 29 days at 80% RH |
Stable for six h |
— |
127
|
MAPbBr3 |
Polystyrene, polyvinyl chloride, acrylonitrile butadiene styrene, and polycarbonate polymer encapsulation |
Stable for 5 months |
<7% loss in PLQY after 120 days |
— |
133
|
MAPbBr3 |
Hydrophobic polyacrylate matrix |
— |
Stable for 110 days |
Stable for 16 days (pH 2 and 12) |
40
|
CsPbBr3 |
Hydrophobic poly(acrylic acid)-block-polystyrene grafted two-dimensional silica nanosheets |
>95.5% PL retention after 60 days |
Maintained 81.8% of emission after 24 h |
— |
134
|
MAPbBr3 |
4-Vinyl-benzyl-dimethyl octadecyl ammonium chloride as a photo-cross-linkable and polymerizable ligand encapsulation |
Stable for more than 100 days |
Stable for more than 100 days |
Stable for more than 100 days (pH 1 and pH 13) |
135
|
CsPbBr3 |
Post-encapsulation with ammonium halide-terminated poly(2-cinnamoyloxyethylmethacrylate) |
Stable for 20 days. |
Maintaining 60% of its initial PL over a week |
— |
42
|
CsPbBr3 |
Post-synthesis encapsulation with fluorine elastomer |
— |
Stable for 30 days |
Stable for 30 days (pH 1 and pH 13) |
78
|
CsPbBr3 |
Glass matrix encapsulation |
— |
Stable for 90 days |
— |
41
|
Although the use of long-chain organic hydrocarbons or mesoporous organic/inorganic frameworks drastically improves the optical stability of PeNCs, optoelectronic or electronic applications are difficult due to their insulating nature. Adopting an extremely thin organic/inorganic insulating layer that allows electron tunneling but prevents water penetration, is a promising research direction. Commercial products needed a balance between water stability and optoelectronic performance to explore optimal conditions for target applications. It has been demonstrated that adding conductive conjugated polymers147,148(such as PEDOT149 and P3HT150) increases stability, passivates surfaces, and increases intrinsic conductivity. Future research can concentrate on the synthesis of conducting polymer-coated perovskite NCs to enhance the transport characteristics in the films which is rarely explored. Since the encapsulated PeNCs offer down-conversion of light from LEDs, they may be used for conventional displays as a color filter layer. To date, the majority of research studies using the passivated PeNCs have been devoted to centimetre-scale devices or simple-structured optical uses.151,152 Therefore, future research might concentrate on creating large-area devices that are stable over time even under extremely robust conditions.
Other future aspects of the polymer/perovskite composite are to study the precise mechanisms of how the polymer interacts with PeNCs and how it depends upon the terminal functional groups and the surface energy of the polymers. It is also necessary to clarify how polymer chain packing and composition affect the water/oxygen transport as well as the overall contribution of the polymers to the electrical band structure.130,131 The production of PNC/polymer nanocomposites with improved characteristics and the comprehension of polymer–PNC interactions could benefit from computational modelling. Lead toxicity of perovskites is one of the big concerns, so far SnII, SnIV, SbIII, BiIII, PdIV, CuII, InIII, and AgI have been used to replace the Pb-counter part.153 Nonetheless, polymer composites with lead-free perovskite nanostructures are still in the beginning stage and need more attention. Another, upcoming hot topic is polymer-directed or guided self-assembly of PeNCs to improve their optical and electrical properties along with desired stability in water. Using self-assembly techniques, the morphology of the perovskites may be fine-tuned.154
Conflicts of interest
The authors declare no competing financial interest.
Acknowledgements
This work was supported by the National Research Foundation of Korea grant NRF-2022M3H4A1A02074314.
References
- Z. Ji, Y. Liu, M. Yao, Z. Zhang, J. Zhong and W. Mai, Adv. Funct. Mater., 2021, 31, 2104320 CrossRef CAS.
- A. P. Litvin, X. Zhang, E. v. Ushakova and A. L. Rogach, Adv. Funct. Mater., 2021, 31, 2010768 CrossRef CAS.
- T. Dey, A. Ghorai, S. Das and S. K. Ray, Nanotechnology, 2023, 34, 065201 CrossRef PubMed.
-
M. D. Irwin and V. V. Dhas, US Pat., US010333082B2, 2019 Search PubMed.
-
T.-W. Lee, S. Im, Y.-H. Kim and H. Cho, US Pat., US10193088B2, 2019 Search PubMed.
- Y.-H. Kim, J. Park, S. Kim, J. S. Kim, H. Xu, S.-H. Jeong, B. Hu and T.-W. Lee, Nat. Nanotechnol., 2022, 17, 590–597 CrossRef CAS PubMed.
-
H. Snaith and M. Lee, US Pat., US010079320B2, 2018 Search PubMed.
- S. Mahato, A. Ghorai, S. K. Srivastava, M. Modak, S. Singh and S. K. Ray, Adv. Energy Mater., 2020, 10, 2001305 CrossRef CAS.
- J. Jeong, M. Kim, J. Seo, H. Lu, P. Ahlawat, A. Mishra, Y. Yang, M. A. Hope, F. T. Eickemeyer, M. Kim, Y. J. Yoon, I. W. Choi, B. P. Darwich, S. J. Choi, Y. Jo, J. H. Lee, B. Walker, S. M. Zakeeruddin, L. Emsley, U. Rothlisberger, A. Hagfeldt, D. S. Kim, M. Grätzel and J. Y. Kim, Nature, 2021, 592, 381–385 CrossRef CAS PubMed.
- A. Al-Ashouri, E. Köhnen, B. Li, A. Magomedov, H. Hempel, P. Caprioglio, J. A. Márquez, A. B. Morales Vilches, E. Kasparavicius, J. A. Smith, N. Phung, D. Menzel, M. Grischek, L. Kegelmann, D. Skroblin, C. Gollwitzer, T. Malinauskas, M. Jošt, G. Matič, B. Rech, R. Schlatmann, M. Topič, L. Korte, A. Abate, B. Stannowski, D. Neher, M. Stolterfoht, T. Unold, V. Getautis and S. Albrecht, Science, 1979, 2020(370), 1300–1309 Search PubMed.
-
J. M. Luther, A. Swarnkar, A. R. Marshall and E. M. Sanehira, US Pat., US010273403B2, 2019 Search PubMed.
- Y. Liu, Y. Dong, T. Zhu, D. Ma, A. Proppe, B. Chen, C. Zheng, Y. Hou, S. Lee, B. Sun, E. H. Jung, F. Yuan, Y. Wang, L. K. Sagar, S. Hoogland, F. P. García de Arquer, M.-J. Choi, K. Singh, S. O. Kelley, O. Voznyy, Z.-H. Lu and E. H. Sargent, J. Am. Chem. Soc., 2021, 143, 15606–15615 CrossRef CAS PubMed.
- A. Fakharuddin, M. K. Gangishetty, M. Abdi-Jalebi, S.-H. Chin, A. R. bin Mohd Yusoff, D. N. Congreve, W. Tress, F. Deschler, M. Vasilopoulou and H. J. Bolink, Nat. Electron., 2022, 5, 203–216 CrossRef CAS.
- K. Lin, C. Yan, R. P. Sabatini, W. Feng, J. Lu, K. Liu, D. Ma, Y. Shen, Y. Zhao, M. Li, C. Tian, L. Xie, E. H. Sargent and Z. Wei, Adv. Funct. Mater., 2022, 32, 2200350 CrossRef CAS.
- S. Pal, A. Ghorai, D. K. Goswami and S. K. Ray, Nano Energy, 2021, 87, 106200 CrossRef CAS.
- J. S. Kim, J.-M. Heo, G.-S. Park, S.-J. Woo, C. Cho, H. J. Yun, D.-H. Kim, J. Park, S.-C. Lee, S.-H. Park, E. Yoon, N. C. Greenham and T.-W. Lee, Nature, 2022, 611, 688–694 CrossRef CAS PubMed.
- J.-M. Heo, H. Cho, S.-C. Lee, M.-H. Park, J. S. Kim, H. Kim, J. Park, Y.-H. Kim, H. J. Yun, E. Yoon, D.-H. Kim, S. Ahn, S.-J. Kwon, C.-Y. Park and T.-W. Lee, ACS Energy Lett., 2022, 7, 2807–2815 CrossRef CAS.
- G. Xiong, Y. Jin, K. Deng, L. Yuan, H. Wu, G. Ju, L. Chen and Y. Hu, J. Mater. Chem. C, 2022, 10, 12316–12322 RSC.
- J. Jiang, X. Sun, X. Chen, B. Wang, Z. Chen, Y. Hu, Y. Guo, L. Zhang, Y. Ma, L. Gao, F. Zheng, L. Jin, M. Chen, Z. Ma, Y. Zhou, N. P. Padture, K. Beach, H. Terrones, Y. Shi, D. Gall, T.-M. Lu, E. Wertz, J. Feng and J. Shi, Nat. Commun., 2019, 10, 4145 CrossRef PubMed.
- R. Dong, Y. Fang, J. Chae, J. Dai, Z. Xiao, Q. Dong, Y. Yuan, A. Centrone, X. C. Zeng and J. Huang, Adv. Mater., 2015, 27, 1912–1918 CrossRef CAS PubMed.
- N. B. Kotadiya, P. W. M. Blom and G.-J. A. H. Wetzelaer, Nat. Photonics, 2019, 13, 765–769 CrossRef CAS.
- L. Kong, X. Zhang, C. Zhang, L. Wang, S. Wang, F. Cao, D. Zhao, A. L. Rogach and X. Yang, Adv. Mater., 2022, 34, 2205217 CrossRef CAS PubMed.
- Y. Zhou, I. Poli, D. Meggiolaro, F. de Angelis and A. Petrozza, Nat. Rev. Mater., 2021, 6, 986–1002 CrossRef.
-
Y. Dong, Y. Wang, S.-T. Wu, J. He, H. Chen and J. Chen, US Pat., US20180010039A1, 2018 Search PubMed.
- W. Xiang, S. Liu and W. Tress, Energy Environ. Sci., 2021, 14, 2090–2113 RSC.
- S. Cheng and H. Zhong, J. Phys. Chem. Lett., 2022, 13, 2281–2290 CrossRef CAS PubMed.
- J. Li, H.-L. Cao, W.-B. Jiao, Q. Wang, M. Wei, I. Cantone, J. Lü and A. Abate, Nat. Commun., 2020, 11, 310 CrossRef CAS PubMed.
- A. Ghorai, A. Midya and S. K. Ray, ACS Omega, 2019, 4, 12948–12954 CrossRef CAS PubMed.
- S. Mahato, A. Ghorai, A. Mondal, S. K. Srivastava, M. Modak, S. Das and S. K. Ray, ACS Appl. Mater. Interfaces, 2022, 14, 9711–9723 CrossRef CAS PubMed.
- U.-G. Jong, C.-J. Yu, G.-C. Ri, A. P. McMahon, N. M. Harrison, P. R. F. Barnes and A. Walsh, J. Mater. Chem. A, 2018, 6, 1067–1074 RSC.
- Z. Li, M. Yang, J.-S. Park, S.-H. Wei, J. J. Berry and K. Zhu, Chem. Mater., 2016, 28, 284–292 CrossRef CAS.
- M. M. Byranvand, C. Otero-Martínez, J. Ye, W. Zuo, L. Manna, M. Saliba, R. L. Z. Hoye and L. Polavarapu, Adv. Opt. Mater., 2022, 10, 2200423 CrossRef CAS.
- D. W. Ferdani, S. R. Pering, D. Ghosh, P. Kubiak, A. B. Walker, S. E. Lewis, A. L. Johnson, P. J. Baker, M. S. Islam and P. J. Cameron, Energy Environ. Sci., 2019, 12, 2264–2272 RSC.
- W. Zhou, L. Jia, M. Chen, X. Li, Z. Su, Y. Shang, X. Jiang, X. Gao, T. Chen, M. Wang, Z. Zhu, Y. Lu and S. Yang, Adv. Funct. Mater., 2022, 32, 2201374 CrossRef CAS.
- X. Zhang, W. Zhou, X. Chen, Y. Chen, X. Li, M. Wang, Y. Zhou, H. Yan, Z. Zheng and Y. Zhang, Adv. Energy Mater., 2022, 12, 2201105 CrossRef CAS.
- H. Zhang, K. Li, M. Sun, F. Wang, H. Wang and A. K.-Y. Jen, Adv. Energy Mater., 2021, 11, 2102281 CrossRef CAS.
- Z. Li, Z. Zhang, R. Nie, C. Li, Q. Sun, W. Shi, W. Chu, Y. Long, H. Li and X. Liu, Adv. Funct. Mater., 2022, 32, 2112553 CrossRef CAS.
- G.-Y. Qiao, D. Guan, S. Yuan, H. Rao, X. Chen, J.-A. Wang, J.-S. Qin, J.-J. Xu and J. Yu, J. Am. Chem. Soc., 2021, 143, 14253–14260 CrossRef CAS PubMed.
- Q. Cao, Y. Li, H. Zhang, J. Yang, J. Han, T. Xu, S. Wang, Z. Wang, B. Gao, J. Zhao, X. Li, X. Ma, S. M. Zakeeruddin, W. E. I. Sha, X. Li and M. Grätzel, Sci. Adv., 2021, 7, eabg0633 CrossRef CAS PubMed.
- Y. Zhang, Y. Zhao, D. Wu, J. Xue, Y. Qiu, M. Liao, Q. Pei, M. S. Goorsky and X. He, Adv. Mater., 2019, 31, 1902928 CrossRef PubMed.
- X. Huang, Q. Guo, D. Yang, X. Xiao, X. Liu, Z. Xia, F. Fan, J. Qiu and G. Dong, Nat. Photonics, 2020, 14, 82–88 CrossRef CAS.
- J. Ko, K. Ma, J. F. Joung, S. Park and J. Bang, Nano Lett., 2021, 21, 2288–2295 CrossRef CAS PubMed.
- R. T. Wang, A. F. Xu, W. Li, Y. Li and G. Xu, J. Phys. Chem. Lett., 2021, 12, 5332–5338 CrossRef CAS PubMed.
- A. A. Babaryk, Y. Pérez, M. Martínez, M. E. G. Mosquera, M. H. Zehender, S. A. Svatek, E. Antolín and P. Horcajada, J. Mater. Chem. C, 2021, 9, 11358–11367 RSC.
- W. Zhou, Y. Zhao, C. Shi, H. Huang, J. Wei, R. Fu, K. Liu, D. Yu and Q. Zhao, J. Phys. Chem. C, 2016, 120, 4759–4765 CrossRef CAS.
- A. M. A. Leguy, Y. Hu, M. Campoy-Quiles, M. I. Alonso, O. J. Weber, P. Azarhoosh, M. van Schilfgaarde, M. T. Weller, T. Bein, J. Nelson, P. Docampo and P. R. F. Barnes, Chem. Mater., 2015, 27, 3397–3407 CrossRef CAS.
- E. Mosconi, J. M. Azpiroz and F. de Angelis, Chem. Mater., 2015, 27, 4885–4892 CrossRef CAS.
- Z. Song, N. Shrestha, S. C. Watthage, G. K. Liyanage, Z. S. Almutawah, R. H. Ahangharnejhad, A. B. Phillips, R. J. Ellingson and M. J. Heben, J. Phys. Chem. Lett., 2018, 9, 6312–6320 CrossRef CAS PubMed.
- J. A. Christians, P. A. Miranda Herrera and P. v. Kamat, J. Am. Chem. Soc., 2015, 137, 1530–1538 CrossRef CAS PubMed.
- M. A. Haque, A. Syed, F. H. Akhtar, R. Shevate, S. Singh, K.-V. Peinemann, D. Baran and T. Wu, ACS Appl. Mater. Interfaces, 2019, 11, 29821–29829 CrossRef CAS PubMed.
- J. Yang, B. D. Siempelkamp, D. Liu and T. L. Kelly, ACS Nano, 2015, 9(2), 1955–1963 CrossRef CAS PubMed.
- B. Turedi, K. J. Lee, I. Dursun, B. Alamer, Z. Wu, E. Alarousu, O. F. Mohammed, N. Cho and O. M. Bakr, J. Phys. Chem. C, 2018, 122, 14128–14134 CrossRef CAS.
- Q. Lin, S. Bernardi, B. Shabbir, Q. Ou, M. Wang, W. Yin, S. Liu, A. S. R. Chesman, S. O. Fürer, G. Si, N. Medhekar, J. Jasieniak, A. Widmer-Cooper, W. Mao and U. Bach, Adv. Funct. Mater., 2022, 32, 2109442 CrossRef CAS.
- G. Niu, W. Li, F. Meng, L. Wang, H. Dong and Y. Qiu, J. Mater. Chem. A, 2014, 2, 705–710 RSC.
- X. Yu, L. Wu, D. Yang, M. Cao, X. Fan, H. Lin, Q. Zhong, Y. Xu and Q. Zhang, Angew. Chem., Int. Ed., 2020, 59, 14527–14532 CrossRef CAS PubMed.
- B. Akbali, G. Topcu, T. Guner, M. Ozcan, M. M. Demir and H. Sahin, Phys. Rev. Mater., 2018, 2, 034601 CrossRef CAS.
- G. Niu, W. Li, F. Meng, L. Wang, H. Dong and Y. Qiu, J. Mater. Chem. A, 2014, 2, 705–710 RSC.
- T. D. Siegler, W. A. Dunlap-Shohl, Y. Meng, Y. Yang, W. F. Kau, P. P. Sunkari, C. E. Tsai, Z. J. Armstrong, Y.-C. Chen, D. A. C. Beck, M. Meilă and H. W. Hillhouse, J. Am. Chem. Soc., 2022, 144, 5552–5561 CrossRef CAS PubMed.
- B. Chen, S. Wang, Y. Song, C. Li and F. Hao, Chem. Eng. J., 2022, 430, 132701 CrossRef CAS.
- K. Ho, M. Wei, E. H. Sargent and G. C. Walker, ACS Energy Lett., 2021, 6, 934–940 CrossRef CAS.
- S. Huang, Z. Li, B. Wang, N. Zhu, C. Zhang, L. Kong, Q. Zhang, A. Shan and L. Li, ACS Appl. Mater. Interfaces, 2017, 9, 7249–7258 CrossRef CAS PubMed.
- C. Caddeo, M. I. Saba, S. Meloni, A. Filippetti and A. Mattoni, ACS Nano, 2017, 11, 9183–9190 CrossRef CAS PubMed.
- S. Wu, Z. Li, M.-Q. Li, Y. Diao, F. Lin, T. Liu, J. Zhang, P. Tieu, W. Gao, F. Qi, X. Pan, Z. Xu, Z. Zhu and A. K.-Y. Jen, Nat. Nanotechnol., 2020, 15, 934–940 CrossRef CAS PubMed.
- B. Hailegnaw, S. Kirmayer, E. Edri, G. Hodes and D. Cahen, J. Phys. Chem. Lett., 2015, 6, 1543–1547 CrossRef CAS PubMed.
- E. Radicchi, F. Ambrosio, E. Mosconi, A. A. Alasmari, F. A. S. Alasmary and F. de Angelis, J. Phys. Chem. B, 2020, 124, 11481–11490 CrossRef CAS PubMed.
- W. Kaiser, D. Ricciarelli, E. Mosconi, A. A. Alothman, F. Ambrosio and F. de Angelis, J. Phys. Chem. Lett., 2022, 13, 2321–2329 CrossRef CAS PubMed.
- A. Aziz, N. Aristidou, X. Bu, R. J. E. Westbrook, S. A. Haque and M. S. Islam, Chem. Mater., 2020, 32, 400–409 CrossRef CAS.
- A. Kaltzoglou, C. C. Stoumpos, A. G. Kontos, G. K. Manolis, K. Papadopoulos, K. G. Papadokostaki, V. Psycharis, C. C. Tang, Y.-K. Jung, A. Walsh, M. G. Kanatzidis and P. Falaras, Inorg. Chem., 2017, 56, 6302–6309 CrossRef CAS PubMed.
- M. M. Rahman, C. Ge, K. Yoo and J.-J. Lee, Mater. Today Energy, 2021, 21, 100803 CrossRef CAS.
-
T. Xu, US Pat., US010388898B2, 2019 Search PubMed.
- D. Ghosh, A. R. Smith, A. B. Walker and M. S. Islam, Chem. Mater., 2018, 30, 5194–5204 CrossRef CAS.
- A. Ghorai, S. Mahato, S. K. Srivastava and S. K. Ray, Adv. Funct. Mater., 2022, 32, 2202087 CrossRef CAS.
- J.-W. Lee, D.-H. Kim, H.-S. Kim, S.-W. Seo, S. M. Cho and N.-G. Park, Adv. Energy Mater., 2015, 5, 1501310 CrossRef.
- X. Wu, Y. Jiang, C. Chen, J. Guo, X. Kong, Y. Feng, S. Wu, X. Gao, X. Lu, Q. Wang, G. Zhou, Y. Chen, J. Liu, K. Kempa and J. Gao, Adv. Funct. Mater., 2020, 30, 1908613 CrossRef CAS.
- L. N. Quan, M. Yuan, R. Comin, O. Voznyy, E. M. Beauregard, S. Hoogland, A. Buin, A. R. Kirmani, K. Zhao, A. Amassian, D. H. Kim and E. H. Sargent, J. Am. Chem. Soc., 2016, 138, 2649–2655 CrossRef CAS PubMed.
- L. Romani, A. Bala, V. Kumar, A. Speltini, A. Milella, F. Fracassi, A. Listorti, A. Profumo and L. Malavasi, J. Mater. Chem. C, 2020, 8, 9189–9194 RSC.
- Q. Jiang, D. Rebollar, J. Gong, E. L. Piacentino, C. Zheng and T. Xu, Angew. Chem., Int. Ed., 2015, 54, 7617–7620 CrossRef CAS PubMed.
- Y. Liu, S. Akin, L. Pan, R. Uchida, N. Arora, J. v. Milić, A. Hinderhofer, F. Schreiber, A. R. Uhl, S. M. Zakeeruddin, A. Hagfeldt, M. I. Dar and M. Grätzel, Sci. Adv., 2019, 5, eaaw2543 CrossRef CAS PubMed.
- G. Grancini, C. Roldán-Carmona, I. Zimmermann, E. Mosconi, X. Lee, D. Martineau, S. Narbey, F. Oswald, F. de Angelis, M. Graetzel and M. K. Nazeeruddin, Nat. Commun., 2017, 8, 15684 CrossRef CAS PubMed.
- J. C. Hamill, O. Romiluyi, S. A. Thomas, J. Cetola, J. Schwartz, M. F. Toney, P. Clancy and Y.-L. Loo, J. Phys. Chem. C, 2020, 124, 14496–14502 CrossRef CAS.
- M. I. Bodnarchuk, S. C. Boehme, S. ten Brinck, C. Bernasconi, Y. Shynkarenko, F. Krieg, R. Widmer, B. Aeschlimann, D. Günther, M. v. Kovalenko and I. Infante, ACS Energy Lett., 2019, 4, 63–74 CrossRef CAS PubMed.
- J. Zhang, C. Yin, F. Yang, Y. Yao, F. Yuan, H. Chen, R. Wang, S. Bai, G. Tu and L. Hou, J. Phys. Chem. Lett., 2021, 12, 2437–2443 CrossRef CAS PubMed.
- Y. Chen, S. R. Smock, A. H. Flintgruber, F. A. Perras, R. L. Brutchey and A. J. Rossini, J. Am. Chem. Soc., 2020, 142, 6117–6127 CrossRef CAS PubMed.
- K. Hills-Kimball, H. Yang, T. Cai, J. Wang and O. Chen, Adv. Sci., 2021, 8, 2100214 CrossRef CAS PubMed.
- Y. Bai, M. Hao, S. Ding, P. Chen and L. Wang, Adv. Mater., 2022, 34, 2105958 CrossRef CAS PubMed.
- J. Khan, X. Zhang, J. Yuan, Y. Wang, G. Shi, R. Patterson, J. Shi, X. Ling, L. Hu, T. Wu, S. Dai and W. Ma, ACS Energy Lett., 2020, 5, 3322–3329 CrossRef CAS.
- G. Liu, H. Zheng, X. Xu, S. Xu, X. Zhang, X. Pan and S. Dai, Adv. Funct. Mater., 2019, 29, 1807565 CrossRef CAS.
- F. Krieg, S. T. Ochsenbein, S. Yakunin, S. ten Brinck, P. Aellen, A. Süess, B. Clerc, D. Guggisberg, O. Nazarenko, Y. Shynkarenko, S. Kumar, C.-J. Shih, I. Infante and M. v. Kovalenko, ACS Energy Lett., 2018, 3, 641–646 CrossRef CAS PubMed.
- A. Pan, B. He, X. Fan, Z. Liu, J. J. Urban, A. P. Alivisatos, L. He and Y. Liu, ACS Nano, 2016, 10, 7943–7954 CrossRef CAS PubMed.
- Y. Liu, Y. Li, X. Hu, C. Wei, B. Xu, J. Leng, H. Miao, H. Zeng and X. Li, Chem. Eng. J., 2023, 453, 139904 CrossRef CAS.
- Y. Li, M. Cai, M. Shen, Y. Cai and R.-J. Xie, J. Mater. Chem. C, 2022, 10, 8356–8363 RSC.
- F. Haydous, J. M. Gardner and U. B. Cappel, J. Mater. Chem. A, 2021, 9, 23419–23443 RSC.
- H. Kim, N. Hight-Huf, J. Kang, P. Bisnoff, S. Sundararajan, T. Thompson, M. Barnes, R. C. Hayward and T. Emrick, Angew. Chem., Int. Ed., 2020, 59, 10802–10806 CrossRef CAS PubMed.
- F. Montanarella, K. M. McCall, K. Sakhatskyi, S. Yakunin, P. Trtik, C. Bernasconi, I. Cherniukh, D. Mannes, M. I. Bodnarchuk, M. Strobl, B. Walfort and M. v. Kovalenko, ACS Energy Lett., 2021, 6, 4365–4373 CrossRef CAS PubMed.
- B. Luo, Y. Pu, S. A. Lindley, Y. Yang, L. Lu, Y. Li, X. Li and J. Z. Zhang, Angew. Chem., 2016, 128, 9010–9014 CrossRef.
- T. Sheikh, S. Maqbool, P. Mandal and A. Nag, Angew. Chem., Int. Ed., 2021, 60, 18265–18271 CrossRef CAS PubMed.
- H. Huang, W. Zhao, H. Yang, X. Zhang, J. Su, K. Hu, Z. Nie, Y. Li and J. Zhong, J. Mater. Chem. C, 2021, 9, 5535–5543 RSC.
- Y. Shu, Y. Wang, J. Guan, Z. Ji, Q. Xu and X. Hu, Anal. Chem., 2022, 94, 5415–5424 CrossRef CAS PubMed.
- A. Jana and K. S. Kim, ACS Energy Lett., 2018, 3, 2120–2126 CrossRef CAS.
- B. Chen, P. N. Rudd, S. Yang, Y. Yuan and J. Huang, Chem. Soc. Rev., 2019, 48, 3842–3867 RSC.
- Y. Shao, Z. Xiao, C. Bi, Y. Yuan and J. Huang, Nat. Commun., 2014, 5, 5784 CrossRef CAS PubMed.
- A. Abate, M. Saliba, D. J. Hollman, S. D. Stranks, K. Wojciechowski, R. Avolio, G. Grancini, A. Petrozza and H. J. Snaith, Nano Lett., 2014, 14, 3247–3254 CrossRef CAS PubMed.
- Y. Ogomi, A. Morita, S. Tsukamoto, T. Saitho, Q. Shen, T. Toyoda, K. Yoshino, S. S. Pandey, T. Ma and S. Hayase, J. Phys. Chem. C, 2014, 118, 16651–16659 CrossRef CAS.
- J. Kim, A. Ho-Baillie and S. Huang, Solar RRL, 2019, 3, 1800302 CrossRef.
- L. Romani, A. Speltini, F. Ambrosio, E. Mosconi, A. Profumo, M. Marelli, S. Margadonna, A. Milella, F. Fracassi, A. Listorti, F. de Angelis and L. Malavasi, Angew. Chem., Int. Ed., 2021, 60, 3611–3618 CrossRef CAS PubMed.
- R. E. Brandt, V. Stevanović, D. S. Ginley and T. Buonassisi, MRS Commun., 2015, 5, 265–275 CrossRef CAS.
- T. Xuan, J. Huang, H. Liu, S. Lou, L. Cao, W. Gan, R.-S. Liu and J. Wang, Chem. Mater., 2019, 31, 1042–1047 CrossRef CAS.
- L. Wu, Y. Mu, X. Guo, W. Zhang, Z. Zhang, M. Zhang and T. Lu, Angew. Chem., 2019, 131, 9591–9595 CrossRef.
- V. Malgras, J. Henzie, T. Takei and Y. Yamauchi, Angew. Chem., Int. Ed., 2018, 57, 8881–8885 CrossRef CAS PubMed.
- T. Xuan, S. Guo, W. Bai, T. Zhou, L. Wang and R.-J. Xie, Nano Energy, 2022, 95, 107003 CrossRef CAS.
- P. Wang, B. Wang, Y. Liu, L. Li, H. Zhao, Y. Chen, J. Li, S. Liu and K. Zhao, Angew. Chem., Int. Ed., 2020, 59, 23100–23106 CrossRef CAS PubMed.
- P. Ma, Y. Hou, Y. Zheng, J. Su, L. Li, N. Liu, Z. Zhang, Y. Ma and Y. Gao, Chem. Eng. J., 2022, 436, 135077 CrossRef CAS.
- S. Yang, S. Chen, E. Mosconi, Y. Fang, X. Xiao, C. Wang, Y. Zhou, Z. Yu, J. Zhao, Y. Gao, F. de Angelis and J. Huang, Science, 1979, 2019(365), 473–478 Search PubMed.
- S. Huang, B. Wang, Q. Zhang, Z. Li, A. Shan and L. Li, Adv. Opt. Mater., 2018, 6, 1701106 CrossRef.
- Y. Wu, C. Wei, X. Li, Y. Li, S. Qiu, W. Shen, B. Cai, Z. Sun, D. Yang, Z. Deng and H. Zeng, ACS Energy Lett., 2018, 3, 2030–2037 CrossRef CAS.
- R. K. Behera, S. das Adhikari, S. K. Dutta, A. Dutta and N. Pradhan, J. Phys. Chem. Lett., 2018, 9, 6884–6891 CrossRef CAS PubMed.
- H. Li, Y. Qian, X. Xing, J. Zhu, X. Huang, Q. Jing, W. Zhang, C. Zhang and Z. Lu, J. Phys. Chem. C, 2018, 122, 12994–13000 CrossRef CAS.
- Y. Hu, S. Kareem, H. Dong, W. Xiong, S. Tian, J. Shamsi, L. Li, X. Zhao and Y. Xie, ACS Appl. Nano Mater., 2021, 4, 6306–6315 CrossRef CAS.
- Q. Zhong, X. Wang, M. Chu, Y. Qiu, D. Yang, T. Sham, J. Chen, L. Wang, M. Cao and Q. Zhang, Small, 2022, 18, 2107548 CrossRef CAS PubMed.
- M. I. Saidaminov, J. Kim, A. Jain, R. Quintero-Bermudez, H. Tan, G. Long, F. Tan, A. Johnston, Y. Zhao, O. Voznyy and E. H. Sargent, Nat. Energy, 2018, 3, 648–654 CrossRef CAS.
- K. M. M. Salim, T. M. Koh, D. Bahulayan, P. C. Harikesh, N. F. Jamaludin, B. Febriansyah, A. Bruno, S. Mhaisalkar and N. Mathews, ACS Energy Lett., 2018, 3, 1068–1076 CrossRef CAS.
- S. Ruidas, A. Das, S. Kumar, S. Dalapati, U. Manna and A. Bhaumik, Angew. Chem., Int. Ed., 2022, 61, e202210507 CrossRef CAS PubMed.
- A. Shome, A. Das and U. Manna, Chem. Mater., 2021, 33, 8941–8959 CrossRef CAS.
- M. Dhar, A. Das, A. Shome, A. Borbora and U. Manna, Mater. Horiz., 2021, 8, 2717–2725 RSC.
- C. Ma and N.-G. Park, ACS Energy Lett., 2020, 5, 3268–3275 CrossRef CAS.
- M. Kim, S. G. Motti, R. Sorrentino and A. Petrozza, Energy Environ. Sci., 2018, 11, 2609–2619 RSC.
- H. Chen, H. Wang, Y. Xue, Q. Ge, Y. Du, J. Yin, B. Yang, S. Yang, X. Liu, M. Cai and S. Dai, Chem. Eng. J., 2022, 450, 138028 CrossRef CAS.
- F. Li and M. Liu, J. Mater. Chem. A, 2017, 5, 15447–15459 RSC.
- S. Liang, M. Zhang, G. M. Biesold, W. Choi, Y. He, Z. Li, D. Shen and Z. Lin, Adv. Mater., 2021, 33, 2005888 CrossRef CAS PubMed.
- Q. A. Akkerman, G. Rainò, M. v. Kovalenko and L. Manna, Nat. Mater., 2018, 17, 394–405 CrossRef CAS PubMed.
- M. Dhar, A. Das, D. Parbat and U. Manna, Angew. Chem., Int. Ed., 2022, 61, e202116763 CrossRef CAS PubMed.
- A. Das and U. Manna, Nanoscale, 2020, 12, 24349–24356 RSC.
- Y. Wang, J. He, H. Chen, J. Chen, R. Zhu, P. Ma, A. Towers, Y. Lin, A. J. Gesquiere, S. Wu and Y. Dong, Adv. Mater., 2016, 28, 10710–10717 CrossRef CAS PubMed.
- J. Wang, M. Zhang, Y. Liu, Y. Huang, Y. Zhang, J. Jiang, H. Li, J. Chen and Z. Lin, Nano Energy, 2022, 98, 107321 CrossRef CAS.
- J.-M. Park, J. Park, Y.-H. Kim, H. Zhou, Y. Lee, S. H. Jo, J. Ma, T.-W. Lee and J.-Y. Sun, Nat. Commun., 2020, 11, 4638 CrossRef CAS PubMed.
- H. Sun, Z. Yang, M. Wei, W. Sun, X. Li, S. Ye, Y. Zhao, H. Tan, E. L. Kynaston, T. B. Schon, H. Yan, Z.-H. Lu, G. A. Ozin, E. H. Sargent and D. S. Seferos, Adv. Mater., 2017, 29, 1701153 CrossRef PubMed.
- J. Jang, Y. Kim, S. Park, D. Yoo, H. Cho, J. Jang, H. B. Jeong, H. Lee, J. M. Yuk, C. B. Park, D. Y. Jeon, Y. Kim, B. Bae and T. Lee, Adv. Mater., 2021, 33, 2005255 CrossRef CAS PubMed.
- Y. Liu, T. Chen, Z. Jin, M. Li, D. Zhang, L. Duan, Z. Zhao and C. Wang, Nat. Commun., 2022, 13, 1338 CrossRef CAS PubMed.
- H. Zhou, J. Park, Y. Lee, J. Park, J. Kim, J. S. Kim, H. Lee, S. H. Jo, X. Cai, L. Li, X. Sheng, H. J. Yun, J. Park, J. Sun and T. Lee, Adv. Mater., 2020, 32, 2001989 CrossRef CAS PubMed.
- H. Han, B. Jeong, T. H. Park, W. Cha, S. M. Cho, Y. Kim, H. H. Kim, D. Kim, D. Y. Ryu, W. K. Choi and C. Park, Adv. Funct. Mater., 2019, 29, 1808193 CrossRef.
- Y. Liu, Z. Wang, S. Liang, Z. Li, M. Zhang, H. Li and Z. Lin, Nano Lett., 2019, 19, 9019–9028 CrossRef CAS PubMed.
- S. Yang, F. Zhang, J. Tai, Y. Li, Y. Yang, H. Wang, J. Zhang, Z. Xie, B. Xu, H. Zhong, K. Liu and B. Yang, Nanoscale, 2018, 10, 5820–5826 RSC.
- Y. He, Y. J. Yoon, Y. W. Harn, G. v. Biesold-McGee, S. Liang, C. H. Lin, V. v. Tsukruk, N. Thadhani, Z. Kang and Z. Lin, Sci. Adv., 2019, 5, eaax442 Search PubMed.
- S. K. Avugadda, A. Castelli, B. Dhanabalan, T. Fernandez, N. Silvestri, C. Collantes, D. Baranov, M. Imran, L. Manna, T. Pellegrino and M. P. Arciniegas, ACS Nano, 2022, 16, 13657–13666 CrossRef CAS PubMed.
- K. Sun, D. Tan, X. Fang, X. Xia, D. Lin, J. Song, Y. Lin, Z. Liu, M. Gu, Y. Yue and J. Qiu, Science, 1979, 2022(375), 307–310 Search PubMed.
- X. Huang, Q. Guo, S. Kang, T. Ouyang, Q. Chen, X. Liu, Z. Xia, Z. Yang, Q. Zhang, J. Qiu and G. Dong, ACS Nano, 2020, 14, 3150–3158 CrossRef CAS PubMed.
- H. Zhu, A. Liu, H. L. Luque, H. Sun, D. Ji and Y.-Y. Noh, ACS Nano, 2019, 13, 3971–3981 CrossRef CAS PubMed.
- Y. Zhang, Y. Ren, X. Xie, Y. Wei, L. He, L. Fang, J. Zhang, Y. Yuan and P. Wang, Adv. Funct. Mater., 2022, 32, 2108855 CrossRef CAS.
- X. Zhu, R. Zhang, M. Li, X. Gao, C. Zheng, R. Chen, L. Xu and W. Lv, J. Phys. Chem. Lett., 2022, 13, 6101–6109 CrossRef CAS PubMed.
- D. Xu, Z. Gong, Y. Jiang, Y. Feng, Z. Wang, X. Gao, X. Lu, G. Zhou, J.-M. Liu and J. Gao, Nat. Commun., 2022, 13, 7020 CrossRef CAS PubMed.
- D. Yao, X. Mao, X. Wang, Y. Yang, N. D. Pham, A. Du, P. Chen, L. Wang, G. J. Wilson and H. Wang, ACS Appl. Mater. Interfaces, 2020, 12, 6651–6661 CrossRef CAS PubMed.
- G. B. Adugna, S. Y. Abate, W.-T. Wu and Y.-T. Tao, ACS Appl. Mater. Interfaces, 2021, 13, 25926–25936 CrossRef CAS PubMed.
- M. A. Triana, E.-L. Hsiang, C. Zhang, Y. Dong and S.-T. Wu, ACS Energy Lett., 2022, 7, 1001–1020 CrossRef CAS.
- A. S. de León, M. de la Mata, I. R. Sanchez-Alarcon, R. Abargues and S. I. Molina, ACS Appl. Mater. Interfaces, 2022, 14, 20023–20031 CrossRef PubMed.
- J. Wang, Y. Zhang, Y. Huang, G. Li, H. Chen, H. Li, Y. Liu and S. Chen, Chem. Eng. J., 2022, 434, 133866 CrossRef CAS.
- Q. Zhang, B. Wang, W. Zheng, L. Kong, Q. Wan, C. Zhang, Z. Li, X. Cao, M. Liu and L. Li, Nat. Commun., 2020, 11, 31 CrossRef CAS PubMed.
- M. N. An, S. Park, R. Brescia, M. Lutfullin, L. Sinatra, O. M. Bakr, L. de Trizio and L. Manna, ACS Energy Lett., 2021, 6, 900–907 CrossRef CAS PubMed.
Footnote |
† They contributed equally. |
|
This journal is © The Royal Society of Chemistry 2023 |
Click here to see how this site uses Cookies. View our privacy policy here.