Removal of metals and inorganics from rendered fat using polyamine-modified cellulose nanocrystals†
Received
17th April 2023
, Accepted 9th June 2023
First published on 20th June 2023
Abstract
Meatpacking and poultry operations produce an enormous amount of co-products including offal, fat, blood, feathers etc. that are collected and processed by the rendering industry into value-added materials such as various protein meals and rendered fat products. Rendered fats (mainly composed of triglycerides from the adipose tissue of animals or used cooking oil from the restaurant industry) are sold for a variety of applications including animal feed formulations. Nonetheless, in the current context of energy scarcity, their use as feedstocks for the generation of renewable fuels including biodiesel and renewable diesel represents a growing market. The diverse composition of the source material can impose significant challenges in terms of compliance, requiring the control (and reduction) of the concentration of elements such as phosphorus, sulfur, calcium, magnesium, sodium, potassium, and other undesirable metals that can otherwise interfere with critical aspects of the refining process or contaminate the renewable fuel products. To address this critical need, we describe the application of poly(ethylenimine)-modified cellulose nanocrystals as a low-cost material for the removal of unwanted metal/inorganic cations from rendered fat. A total of 28 real samples including poultry, white pork grease, and beef tallow were analyzed. Test results showed that the approach can effectively decrease the concentration of the target elements by 95 ± 2%, suggesting that this treatment protocol could dramatically improve the application of rendered fat products for renewable fuel refining.
Sustainability spotlight
Although the current use of animal fat as feedstocks for the generation of renewable fuels including biodiesel and renewable diesel represents a growing market, the metals present in the source material can impose significant challenges in terms of compliance. Unless removed, these metals can not only inhibit the catalysts used in the production process but more importantly, be released to the atmosphere when the diesel produced is burned. With the purpose of removing unwanted inorganic cations from rendered fat, we describe the application of poly(ethylenimine)-modified cellulose nanocrystals. Not only does the material show an overall decrease in the concentration of the target elements by 95 ± 2% but it also allows the application of fat as a source for diesel; an option that reduces the use of fossil fuels while solving a waste management problem.
|
1. Introduction
Farms, feedlots, and meat-packing operations produce enormous amounts of animal byproducts not typically consumed by humans that are processed by the rendering industry.1 In North America alone, more than 62 billion pounds of renderable raw material including offal, bones, fat, blood, feathers, and dead-stock animals are produced annually.2 These materials are collected and transported as aggregated byproducts, which are then typically processed in rendering plants,3 leading to various rendered products that re-enter the industrial cycle as meat byproducts, various protein meals, and rendered animal fats.4 While the traditional destination of animal fats was the production of lard, soaps, oleochemicals, and animal feed/food formulations, the current market has also allowed their application as a source for renewable fuels including renewable diesel and biodiesel,5 an option that not only reduces the use of fossil fuels but also contributes to solving a waste management problem.6 In this regard, the production of renewable fuels from rendered fat and used cooking oil is presented as one of most the economically attractive options,7 due to the low cost of the feedstock (that represents 75–90% of the overall cost of production) and high value of its final product.8 Moreover, the renewable fuel produced from rendered animal fats and used cooking oil typically presents a better emissions profile than that of vegetable sources9 and does not affect food cost.10 Currently, due to international socio-political considerations and the scarcity of natural gas, diesel has gained importance as a fuel source for the generation of electricity and heat.11
The production of biodiesel from rendered materials typically involves the generation of fatty acid esters (transesterification)12 from triglycerides by means of homogeneous, heterogeneous, or enzymatic catalysis.1,13 Although various sources of triglycerides can be used to produce biodiesel, the diverse composition of the source material14 (and the presence of free fatty acids) imposes great challenges in terms of compliance with the standards from the American Society for Testing and Materials (ASTM B6751 for B100, and D7467 for B6 to B20). In this regard, it is critical to control (and reduce) the concentration of inorganic contaminants such as phosphorus, sulfur, calcium, magnesium, sodium, potassium, and other metals that would otherwise interfere with the transesterification process, reduce the activity of the catalysts, and/or remain in the refined diesel product.6,15–24 Although the two processes are different, renewable diesel processes can benefit from the removal of inorganic/metal contaminants in source material.14,25 In this regard, and while not necessarily applied towards the use production of biodiesel, various methods have been described for the cleanup of oily raw materials and for the removal of undesirable inorganics or metals.26,27 Attempts have been made by washing in an aqueous medium and drying with MgO, using ion exchange resins.6 Metal removal processes have also been carried out through the use of clays (EP2591081A1), hollow fibers containing cellulose,21 surfactants,28 and even extraction through the use of deep eutectic solvents.19,22,29 These pre-process techniques are also applied to increase biodiesel yield from rendered fat.30,31 Considering that none of these steps typically involve extractions, it is important to note that the concentration of these interferents is strongly dependent on the composition of the feedstock32 and can remain in the biofuel products. At present, there are no feasible strategies to remove undesirable inorganic/metal contaminants from rendered fat prior to use as biofuel feedstocks. An effective, economic, and simple method for the removal of relevant species could not only give rendered fat an added value but also significantly contribute to the development of this emerging industry.
Towards that goal, we describe the use of poly(ethylenimine)-modified cotton-derived cellulose nanocrystals (PEI-CNC)33 for the removal of various metallic cations (i.e. sodium, potassium, iron, calcium, magnesium) as well as sulfur and phosphorus, from rendered fat. The PEI-CNC material features high surface area,34 great versatility towards chemical modifications,35 and low cost.36 The effectiveness of the process was assessed by inductively coupled plasma (ICP) with optical emission spectrometry (OES) detection under various experimental conditions. Our results showed that PEI-CNC treatment of rendered fat effectively removed 95 ± 2% of target analytes, providing a reasonable option to purify rendered fats and used cooking oil to reduce metal/inorganic contamination. The successful application of this approach offers the potential to purify rendered fat or used cooking oil prior to use as biofuel feedstocks. The removal of undesirable metal/inorganic contaminants from rendered fat products may also benefit their application in livestock feed and pet food formulations as well. To the best of our knowledge, this is the first report of the use of PEI-CNC materials to purify metal/inorganic-contaminated rendered fat prior to use as biofuel feedstocks.
2. Experimental section
2.1 Materials and methods
Specific details regarding the preparation of the CNC and CNC-PEI can be found elsewhere.37,38 The experimental procedure involved the oxidation of cellulose nanocrystals (CNC) using TEMPO-mediated oxidation. The CNC suspension was combined with TEMPO and sodium bromide, and then sodium hypochlorite was added to initiate the oxidation reaction. After stirring at room temperature for 5 hours, the solution was washed to remove any unreacted reagents and adjusted to a pH of 2.5. The oxidized CNC was subsequently functionalized with poly(ethylenimine) using N-(3-dimethylaminopropyl)-N′-ethylcarbodiimide hydrochloride (EDC) as a coupling agent. The resulting modified cellulose nanocrystals were washed, freeze-dried, and stored for further characterization and testing. Modified nanocrystals were used dry as a solid reagent.
For the synthesis and the extraction steps, 10–15% sodium hypochlorite solution, (2,2,6,6-tetramethylpiperidin-1-yl) oxidanyl (TEMPO), cellulose microcrystals (type 20, 20 μm), poly(ethyleneimine) solution (PEI) (1200–1300 MW, 50% in H2O), N-(3-dimethylaminopropyl)-N′-ethylcarbodiimide hydrochloride (EDC), sodium hydroxide, nitric acid, and sodium bromide were purchased from Sigma-Aldrich (Saint Louis, MO). 6 M hydrochloric acid was purchased from Ricca Chemical Company (Arlington, TX).
2.2 Instrumentation
For the element determination, a Thermo-Fisher Scientific iCAP 7400 ICP-OES Analyzer was used. All the elements were measured in the original sample extraction solution, at the same time. The peristaltic pump, used for sample delivery, was set at 45 rpm and furnished with PVC tubbing (1.4 mL min−1). All the analytes' determinations were made in axial direction.
2.3 Element removal
To determine the fraction of the metals removed by the CNC, all fat samples were first melted by placing them in a water bath at 60 °C to facilitate interfacial exchange. Then, 10 mL of each sample was transferred to a 50 mL falcon tube, also kept at the same temperature. 10 mL of ultrapure water (also at 60 °C) was then added to the rendered fat and vortexed for 5 min, and the two phases were allowed to separate by resting the tube for another 5 min, also in the water bath. The water washing procedure ensured the removal of large-sized particles, dirt, as well as the most hydrophilic ions. Next, most of the aqueous layer was removed with a syringe. Then, 300 mg of CNC-PEI was added to the fat sample and the sample was vigorously shaken to disperse the sorbent. The tube was maintained in the bath (at 60 °C) for another 5 min and then centrifuged for 2 min at 9000 rpm. Most of the tubes presented a small aqueous lower layer (remains of the water extraction) mixed with the CNC-PEI and an upper layer containing the purified rendered fat. At this point the rendered fat appears to be much more translucent than the original sample. Finally, the upper layer was separated and processed for element determination via ICP-OES.
2.4 Analyte determination
For the determination of the analytes, an extraction with 2% aq. nitric acid was performed. Two 10 mL samples of melted rendered fat were always processed in parallel. One of the samples was processed as previously described to remove undesirable inorganic/metals elements while the other sample was taken as a control and was directly extracted for measurement. For that purpose, 10 mL of the original rendered fat (or 5 mL of the clarified one) at 60 °C were mixed with 10 mL of 2% aqueous HNO3, vigorously vortexed for 2 min, and then immersed in the water bath for 8 additional min, to complete a 10 min extraction step. The upper organic layer was discarded, and the lower aqueous layer was filtered with a 0.05 μm syringe filter to avoid injecting oil droplets into the ICP-OES nebulizer. Aqueous 2% nitric acid was also used as carrier for samples and as baseline for element quantification. The plasma power was set at 1150 W. The auxiliary and coolant gas flow were set to 0.5 L min−1 and 12 L min−1, respectively. The detection of all elements herein described were made in radial mode and all the determinations were obtained from individual signals (no interferences observed).
For the sake of simplicity, the removal for each analyte was calculated individually and then averaged. The results for each analyte (supporting the values summarized in the figures) are provided as ESI.† All datapoints and error bars presented in the manuscript represent the average and standard deviation, respectively, of at least 3 independent measurements.
3. Results and discussion
3.1 HNO3 extraction
Prior to analyzing the effectiveness of CNC-PEI as sorbent on these studies, a sample of canola oil (liquid at room temperature) was spiked with various inorganic/metal species (i.e. CaCl2, FeSO4, KNO3, MgSO4, NaCl, and Na2HPO4) and used as model sample. 2% aq. nitric acid was selected as extractant considering its metal extraction capacity,39 oxidizing properties that remove metals from organometallic compounds,40 its lower interference for this method than HCl and H2SO4, and compatibility with the instrument. To determine the optimum sample/extractant ratio, the effect of the volume of nitric acid (added to a 10 mL sample), was investigated considering the total amount of elements extracted. As it can be observed in Fig. 1, only a small fraction of the metallic cations was extracted when 1 mL or 2 mL of 2% nitric acid were used as extractant. However, that fraction increased to 83% when at least 5 mL were added to the selected sample volume. Based on these results, a volume of 5 mL was selected as optimum, and used for the remaining experiments. It is worth mentioning that the extractant volume was increased to 10 mL when processing real samples, to avoid saturation due to the high concentration of some of the elements in the as-received rendered fat samples.
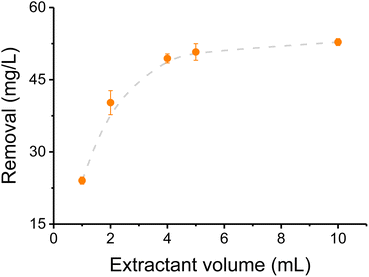 |
| Fig. 1 Effect of extraction volume in analyte determination by ICP-OES. Sample volume 10 mL, 300 mg CNC-PEI, temperature 60 °C, 5 min vortexing, 2 min centrifugation at 9000 rpm. Sample: spiked canola oil. | |
3.2 Calibration curves
To calculate the concentration of each analyte in the processed samples, calibration curves were obtained using a multianalyte standard solution, also diluted in 2% aq. HNO3. Multiple measurements of blank samples (n = 5) were made to enable determining the limit of detection (LOD) and limit of quantification (LOQ) for each element. Table 1 shows the results of the calibration curves obtained for each element. Sensitivity values reported for metals are consistent with literature,41 supporting the validity of the method selected for the determination of the metals in the selected samples.
Table 1 Calibration curves information for the different analytesa
Element |
Range (mg L−1) |
Wavelength (nm) |
Sensitivity (mg L−1/IAU) |
LOD (mg L−1) |
LOQ (mg L−1) |
Elements marked with * rendered a calculated LOD that was lower than the lowest concentration measured.
|
Na |
0.2–155 |
588.995 |
786.4 |
0.2 |
0.6 |
K |
0.2–155 |
766.490 |
207.5 |
0.3 |
0.9 |
Ca |
0.2–155 |
393.366 |
15 312 |
* |
0.2 |
Mg |
0.1–142 |
280.270 |
3685 |
* |
0.0 |
Fe |
0.1–155 |
259.940 |
182 |
0.1 |
0.2 |
P |
0.1–105 |
177.495 |
12.5 |
* |
0.1 |
S |
0.1–270 |
180.731 |
12.3 |
0.2 |
0.6 |
3.3 Effect of sorbent type and amount
A model system based on spiked canola oil was used to analyze the effect of sorbents on the efficiency of the removal process. For these experiments a sample of canola oil was fortified with CaCl2, FeSO4, KNO3, MgSO4, NaCl, and Na2HPO4 by adding aliquots of concentrated aqueous solutions. This solution was then maintained at 60 °C under continuous stirring for approximately 48 h to evaporate the water and ensure adequate dispersion of the metallic cations in the oil. These samples were then used to investigate the performance of the sorbent materials. To this end, two CNC materials were tested and compared: unmodified CNC (featuring –OH functional groups) and poly(ethylenimine)-modified CNC (PEI-CNC, featuring –NH2 functional groups on the surface).37,38 The latter is especially important considering that the addition of the polyethyleneimine groups can enhance the adsorptive characteristics of these materials.42 The resulting primary and secondary amino groups would have the ability to be electron donors, allowing the formation of a coordination complex with the metal ions in the sample.43 Also, the porous structure of the CNC-PEI would facilitate the diffusion of the ions while increasing the adsorption surface area.44
To compare the performance of both sorbents and determine the optimum amount needed for the extraction, both materials (CNC and CNC-PEI) were applied to the same model matrix using different sorbent quantities. Three amounts of sorbents were tested: 50 mg, 150 mg and 300 mg per 10 mL of spiked canola oil. As it can be observed, a significant reduction in the content of the metallic cations was observed (Fig. 2, blue columns). In all cases, the use of CNC-PEI allowed extracting significantly higher amounts (66.0 ± 0.7, at 150 mg) of metals/inorganics as compared to unmodified nanocrystals (52.1 ± 0.6, also at 150 mg).
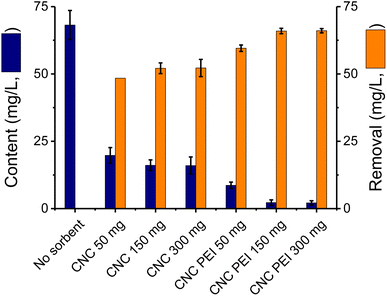 |
| Fig. 2 Comparison of the performance of unmodified and PEI-modified cellulose nanocrystals for the removal of selected analytes. Blue bars indicate the final concentration for each extraction procedure. The reduction in concentration is shown in orange columns. Sample volume 10 mL, temperature 60 °C, 10 min sorbent extraction, 2 min 9000 rpm centrifugation. Sample: spiked canola oil. | |
Upon demonstrating that the overall extraction capacity of CNC-PEI was superior to that of CNC, studies were carried out to optimize the amount of CNC-PEI needed to address authentic samples of rendered fat. With that purpose, the effect of different quantities of CNC-PEI over the range of 50 to 500 mg on the extraction capacity was investigated using a sample of rendered poultry fat. For this purpose, a control sample was not treated with CNC-PEI, and four more samples from the same lot were treated with 50, 150, 300, and 500 mg of CNC-PEI, respectively. The results, summarized in Fig. 3, show that removal improved with the mass of CNC-PEI added up to 300 mg (reaching a 92% removal), above which no additional improvements in removal were evident.
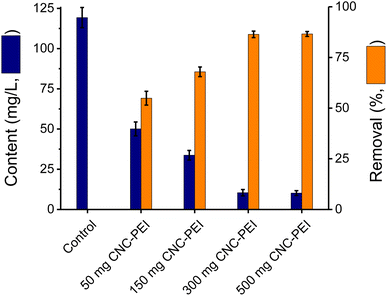 |
| Fig. 3 Effect of CNC-PEI mass used for removal of analytes in rendered poultry fat. Sample volume 10 mL, temperature 60 °C, 10 min extraction time, 2 min 9000 rpm centrifugation. Sample: poultry rendered fat. | |
3.4 Water wash
Aiming to demonstrate the broad applicability of the proposed approach, rendered fat samples were obtained from multiple rendering plants around United States. Participating plants contributed samples of rendered chicken fat, various grades of beef tallow, choice white grease (pork), and used cooking oil. The chemical and organoleptic characteristics of individual samples were extremely variable, but all of them presented significant amounts of solid residues. Thus, an additional washing step was explored to clean the samples before treating them with CNC-PEI.45 The proposed step was carried out with distilled water, pre-heated at 60 °C, to avoid solidification of the sample and negatively impact the contact surface for the proposed extraction. It was hypothesized that some of the free ionic species could be removed with the water wash enhancing the results of the overall procedure. For this reason, a comparison between water-washed, CNC-PEI treated, and a sequential extraction with water (followed by CNC-PEI) was performed. Spiked canola oil was used as a model sample and three different approaches were evaluated: a water wash, CNC-PEI extraction, and a combination of a water wash followed by a CNC-PEI extraction (Fig. 4). Thus one 10 mL spiked canola oil sample was washed with 10 mL of water (60 °C), another one was treated with 300 mg CNC-PEI, and a third sample was first washed with 10 mL of water and then the oil layer was separated and treated with 300 mg CNC-PEI. According to our results, the inclusion of a water wash resulted in a significant reduction of ions (61 ± 4%) and the clarification of the sample (see inset in Fig. 4). The results also confirmed that treatment with CNC-PEI as removal agent outperformed a water wash (82 ± 4%, overall removal of the metallic cations). This also confirmed that not all undesired elements were forming polar ions. Combining both strategies lead to a better remediation of the rendered fat sample with a 94 ± 4% overall removal of the metallic cations. In this way it was demonstrated that a 10 minute wash (1
:
1 sample
:
water) at 60 °C significantly enhanced the removal of the metals/inorganics from rendered fat samples.
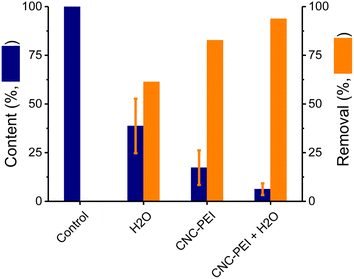 |
| Fig. 4 Results of metal/inorganic removal with water, CNC-PEI, and sequential water wash/CNC-PEI treatments. Sample volume 10 mL, temperature 60 °C, 5 min water wash, 10 min sorbent extraction, 2 min 9000 rpm centrifugation. Sample: spiked canola oil. | |
3.5 Effect of temperature in the removal of analytes
Along the rendering process in plants, fat is melted, degummed, neutralized, and sometimes bleached in order to simplify any further treatment.46,47 The general procedure in a regular factory regardless of the rendering method involves a heating step to release the fat from fat cells and to melt the mixture. Studying how temperature affects the CNC-PEI removal of analytes is crucial to optimize the extraction process.
The functionality of CNC-PEI for removing metals/inorganics was investigated at different temperatures, using spiked canola oil as a model sample. By using oil, the possibility of solidification of the rendered fat influencing the results of the study was avoided. The control for this test was a spiked canola oil sample processed at room temperature (18 °C). 10 mL aliquots of the spiked sample were heated at different temperatures and then they were extracted with 300 mg CNC-PEI, centrifuged, and measured. Our results (Fig. SI 1†) showed that the removal of analytes (total content) is dependent on the temperature, where increases in the temperature led to better extraction efficiencies, reaching a maximum at 60 °C. Further increases in the temperature (up to 80 °C) did not provide additional improvements. This behavior can be explained considering the decrease in the viscosity of the medium,48 which favors the interaction between the target species and the sorbent. An additional advantage of these findings is that the optimum temperature for the extraction coincides with the temperature required for the transesterification and degumming processes,49 probably for similar reasons.
3.6 Effect of contact time in washing step
Once it was demonstrated that a water washing step (with vortexing) would enhance the removal of metals/inorganics, the duration of that process was optimized. Considering that the process would be ultimately applied to rendered fat samples, both the water and the sample of canola oil were heated at 60 °C. Spiked canola oil samples were extracted with water at different times and quantified. It was observed that the overall extraction of metallic species increased rapidly during the first few minutes but reached a plateau at approximately 4 min (see Fig. 5). Additional experiments are currently underway to determine the kinetic parameters of the interaction50 but considering that no further improvements were obtained within the selected timeframe (<20 min), a 5 min washing step was added to the process. Once the extraction with warm water was completed, the samples were allowed to stand for 5 min, to separate the phases adequately. It is also important to note that the moisture level in the treated fat samples does not increase after the water-wash procedure. Specifically, the moisture levels were obtained for tallow before (0.51 ± 0.07%) and after the water treatment (0.52 ± 0.08%), not showing statistically significant differences (t-test, tcrit = 2.77 and tstat = 0.20).
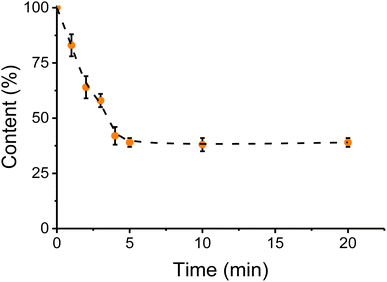 |
| Fig. 5 Effect of time in the water wash step. Sample volume 10 mL, temperature 60 °C, water volume 10 mL, 2 min centrifugation 9000 rpm. Sample: spiked canola oil. | |
3.7 Effect of contact time with CNC-PEI
The extraction time with CNC-PEI was studied to obtain a compromise between the best extraction and the fastest procedure. Spiked canola oil control samples were used with 300 mg of CNC-PEI sorbent contact time was investigated over different periods of time. Once the desired time was over, falcon tubes were centrifuged for 2 min (9000 rpm). The upper layer was separated and analyzed to determine the total content of metal/inorganic analytes. An untreated oil sample was analyzed as a control and a sample that was centrifuged for 2 min immediately after CNC-PEI addition was taken as time 0. Results were plotted as extraction percentage as a function of contact time and fitted. Fig. 6 shows the extraction rate for calcium, as a representative example (results for other ions are provided in Fig. SI 2†). As it can be observed, the reaction proceeds rather quickly, reaching 82 ± 3% of the extraction within the first 5 minutes of contact. Additional contact time (up to 60 min) only produced slight additional enhancements, leading to a maximum extraction of 87 ± 3%, during the selected experimental window. In order to further understand this behavior and support the hypothesis that this reaction is determined by the adsorption capacity of the CNC-PEI, and not by the concentration of the analytes,51 removal kinetic studies were also performed.
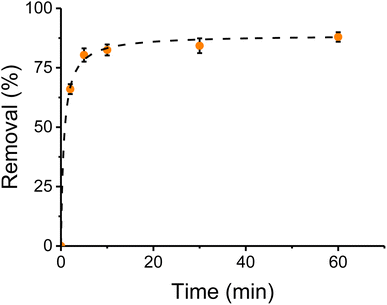 |
| Fig. 6 Effect of time in CNC-PEI removal of calcium analytes experimentally obtained (orange datapoints). Sample volume 10 mL, temperature 60 °C, 300 mg CNC-PEI, 2 min centrifugation. The figure also shows the results of pseudo-second order fitting (R2 = 0.9996). Sample: spiked canola oil. | |
Experimental results obtained for calcium were fitted against a pseudo-first order kinetics and a pseudo-second order kinetics with nonlinear regression to analyze kinetic mechanism.28,50 A pseudo-second-order model showed a R2 = 0.9996, against a 0.9923 obtained with a pseudo-first order fitting.52 These results suggest that a pseudo-second-order kinetics is taking place, depending on adsorption capacity of CNC-PEI and being independent from adsorbate concentration.53 This same behavior has been reported in other oily viscous matrices.54 The same procedure was applied to the rest of the analytes showing identical results (Fig. SI 1†).
3.8 Analysis of rendered fat samples
Twenty-eight rendered fat samples from different plants in the USA were collected and analyzed individually. The origin of the samples was diverse including beef tallow, choice white grease (pork), and poultry rendered fat. Samples (10 mL) were treated with a 1
:
1 water wash, followed by 500 mg of CNC-PEI. The detailed metal/inorganic composition for every sample was determined, to show the removal of individual species. The initial content of analytes in every sample was taken as the control for each treatment. The degree of metal and inorganic contamination varied considerably between samples. A summary of individual results of all samples and analytes is provided as part of the ESI Section (Table SI 1).† In all cases, the extent of metal/inorganic removal is above 91%, showing that the proposed remediation strategy is not only versatile in terms of sample origin but also slightly superior than strategies28,45 (including those described for fat samples, see Table SI 2†). The final concentration of the analyzed species was greatly decreased, even in samples with very high concentration of such analytes. In most of the samples, the final concentration of Ca/Mg and Na/K is reduced below ASTM standards requirements.6 The initial total analyte concentration in samples ranged from 100 to 1000 ppm demonstrating a wide working range without decreased efficacy. The treatment results showed that the proposed method could be used in different rendered fat samples (i.e. poultry, white pork grease, or beef tallow), having outstanding removal rates for all samples. Aggregated results from the entire set of samples showed that the proposed treatment reaches up to 95 ± 2% removal of a variety of metal/inorganic contaminants, feature that significantly enhances the number of options for removal of contaminants (see Table SI 2†).
4. Conclusions
In this work, the potential of poly(ethylenimine) modified cellulose nanocrystals (PEI-CNCs) to significantly reduce the metal/inorganic burden in rendered fat samples was studied and tested. Kinetic studies revealed pseudo-second-order kinetics in the removal process, demonstrating that the CNC-PEI adsorption rate depends on its absorption capacity and not on the analyte concentration. Preliminary results showed that rendered fat after the proposed combined extraction had an enhanced quality for biofuel production. A general procedure, including a washing step was proposed for the treatment of rendered animal fat. With the aim of evaluating the feasibility of the proposed method, the treatment protocol was applied to a series of 28 poultry, pork white grease, and beef tallow samples from rendering plants across the United States. The total content of studied analytes in the authentic samples was reduced by 95 ± 2% applying the proposed strategy, yielding materials with significantly higher commercial value. In most cases, the final concentration of Na–K and Ca–Mg were lower than expected for typical biofuel standards. To the best of our knowledge, this study represents the first application of CNC-based materials for the removal of metal/inorganic contaminants from rendered fat, to allow out-of-specification samples to be ameliorated for biofuel refining.
Conflicts of interest
The authors declare that they have no known competing financial interests or personal relationships that could have influenced the work reported in this paper.
Acknowledgements
Financial support for this project has been provided by the Department of Chemistry at Clemson University and the Fats & Proteins Research Foundation, Inc. through the Clemson University Animal Co-Products Research & Education Center. D. C. W.'s laboratory is partially supported by NIH NIGMS grant 1P20GM146584-01. E. Vidal wish to thank Consejo Nacional de Investigaciones Científicas y Técnicas (CONICET). Authors would also like to thank Dr R. Sachdeva for his initial assistance with the ICP experiments.
References
- F. Toldrá-Reig, L. Mora and F. Toldrá, Appl. Sci., 2020, 10, 3644 CrossRef.
-
NARA (North American Renderers Association), Sustainability and Economic Analysis, 2020 Search PubMed.
- S. Woodgate and J. Van Der Veen, Biotechnol., Agron., Soc. Environ., 2004, 283–294 Search PubMed.
- A. Milbrandt, T. Seiple, D. Heimiller, R. Skaggs and A. Coleman, Resour., Conserv. Recycl., 2018, 137, 32–47 CrossRef.
- B. Riazi, J. M. Mosby, B. Millet and S. Spatari, Resour., Conserv. Recycl., 2020, 161, 104944 CrossRef.
- T. M. Mata, N. Cardoso, M. Ornelas, S. Neves and N. S. Caetano, Energy Fuels, 2011, 25, 4756–4762 CrossRef CAS.
- A. Keskin, M. Şen and A. O. Emiroğlu, Fuel, 2020, 276, 118000 CrossRef CAS.
- H. Esmaeili, Fuel Process. Technol., 2022, 230, 107224 CrossRef CAS.
- U. Rajak and T. N. Verma, Energy Convers. Manage., 2018, 166, 704–718 CrossRef CAS.
- S. A. Jambo, R. Abdulla, S. H. Mohd Azhar, H. Marbawi, J. A. Gansau and P. Ravindra, Renewable Sustainable Energy Rev., 2016, 65, 756–769 CrossRef CAS.
- P. Bórawski, L. Holden, M. B. Bórawski and B. Mickiewicz, Energies, 2022, 15, 4332 CrossRef.
- R. García-Morales, A. Zúñiga-Moreno, F. J. Verónico-Sánchez, J. Domenzain-González, H. I. Pérez-López, C. Bouchot and O. Elizalde-Solis, Fuel, 2022, 313, 122706 CrossRef.
- M. Ramos, A. P. S. Dias, J. F. Puna, J. Gomes and J. C. Bordado, Energies, 2019, 12, 4408 CrossRef CAS.
- M. Hájek, A. Vávra, H. de Paz Carmona and J. Kocík, Catalysts, 2021, 11, 1118 CrossRef.
- I. B. Banković-Ilić, I. J. Stojković, O. S. Stamenković, V. B. Veljkovic and Y.-T. Hung, Renewable Sustainable Energy Rev., 2014, 32, 238–254 CrossRef.
- A. C. Alba-Rubio, M. L. Alonso Castillo, M. C. G. Albuquerque, R. Mariscal, C. L. Cavalcante and M. López Granados, Fuel, 2012, 95, 464–470 CrossRef CAS.
- M. Ndiaye, A. Arhaliass, J. Legrand, G. Roelens and A. Kerihuel, Renewable Energy, 2020, 145, 1073–1079 CrossRef CAS.
- V. B. Veljković, I. B. Banković-Ilić and O. S. Stamenković, Renewable Sustainable Energy Rev., 2015, 49, 500–516 CrossRef.
- A. Shishov, S. Savinov, N. Volodina, I. Gurev and A. Bulatov, Microchem. J., 2022, 179, 107456 CrossRef CAS.
- T. Mahmudiono, D. Bokov, G. Widjaj, A. S. Konstantinov, K. Setiyawan, W. K. Abdelbasset, H. S. Majdi, M. M. Kadhim, H. A. Kareem and K. Bansal, Food Sci. Technol., 2022, 42, e111721 CrossRef.
- J. T. F. Keurentjes, T. G. J. Bosklopper, L. J. van Dorp and K. van't Riet, J. Am. Oil Chem. Soc., 1990, 67, 28–32 CrossRef CAS.
- A. Petračić, A. Sander and M. Cvetnić, Sep. Sci. Technol., 2020, 55, 3487–3501 CrossRef.
-
S. Kumar, R. B. Kumar, A. Sharma, B. Kumar, S. Semwal, A. K. Arora, S. K. Puri, S. Ahmed, V. Kagdiyal, S. Rajagopal, R. K. Malhotra and A. Kumar, Patent: Process for Removal of Metals from Oils/Fats, EP2591081A1, 2011 Search PubMed.
- A. Wang, J. Wang, S. Sheti, S. Dahlin, J. Han, J. Woo, K. Xie, L. J. Pettersson and L. Olsson, Catal. Sci. Technol., 2020, 10, 5602–5617 RSC.
- N. K. Guthalugu, M. Balaraman and U. S. Kadimi, Biochem. Eng. J., 2006, 29, 220–226 CrossRef CAS.
- S. Gharby, Sci. World J., 2022, 2022, 6627013 Search PubMed.
- J.-G. Lee, J.-Y. Hwang, H.-E. Lee, T.-H. Kim, J.-D. Choi and G.-J. Gang, Appl. Biol. Chem., 2019, 62, 64 CrossRef.
- J. Tang, J. He, T. Liu and X. Xin, RSC Adv., 2017, 7, 33385–33401 RSC.
- T. Mahmudiono, D. Bokov, G. Widjaja, I. S. Konstantinov, K. Setiyawan, W. K. Abdelbasset, H. S. Majdi, M. M. Kadhim, H. A. Kareem and K. Bansal, Food Sci. Technol., 2022, 42, e111721 CrossRef.
-
S. R. Yenumala, B. Sarkhel and S. K. Maity, in Green Diesel: an Alternative to Biodiesel and Petrodiesel, Springer, 2022, pp. 219–248 Search PubMed.
- G. R. Srinivasan and R. Jambulingam, J. Environ. Sci. Technol., 2018, 11, 157–166 CrossRef CAS.
- N. A. M. Salleh, M. S. Hassan, J. Jumal, F. W. Harun and M. Z. Jaafar, AIP Conf. Proc., 2018, 1972, 030015 CrossRef.
- D. Trache, M. H. Hussin, M. K. M. Haafiz and V. K. Thakur, Nanoscale, 2017, 9, 1763–1786 RSC.
- L. Fan, Y. Lu, L.-Y. Yang, F. Huang and X.-k. Ouyang, J. Colloid Interface Sci., 2019, 554, 48–58 CrossRef CAS PubMed.
- H. Tao, N. Lavoine, F. Jiang, J. Tang and N. Lin, Nanoscale Horiz., 2020, 5, 607–627 RSC.
- H. Ibrahim, N. Sazali, W. N. W. Salleh and A. F. Ismail, Water, Air, Soil Pollut., 2021, 232, 1–16 CrossRef.
- F. D. Guerra, M. L. Campbell, M. F. Attia, D. C. Whitehead and F. Alexis, ChemistrySelect, 2018, 3, 5495–5501 CrossRef CAS.
- B. R. Brummel, C. J. Narangoda, M. F. Attia, M. I. Swasy, J. G. D. Smith, F. Alexis and D. C. Whitehead, Polymers, 2021, 13, 3060 CrossRef CAS.
- D. Hristozov, C. E. Domini, V. Kmetov, V. Stefanova, D. Georgieva and A. Canals, Anal. Chim. Acta, 2004, 516, 187–196 CrossRef CAS.
- P. N. Nomngongo and J. C. Ngila, Spectrochim. Acta, Part B, 2014, 98, 54–59 CrossRef CAS.
- J. M. Harrington, D. J. Young, A. S. Essader, S. J. Sumner and K. E. Levine, Biol. Trace Elem. Res., 2014, 160, 132–142 CrossRef CAS.
- C. B. Godiya, X. Cheng, G. Deng, D. Li and X. Lu, J. Environ. Chem. Eng., 2019, 7, 102806 CrossRef CAS.
- M. Chen and N. P. Hankins, J. Water Process. Eng., 2020, 34, 101170 CrossRef.
- C. Liu, R.-N. Jin, X.-k. Ouyang and Y.-G. Wang, Appl. Surf. Sci., 2017, 408, 77–87 CrossRef CAS.
- C. Wang, J. S. Buchanan, W. R. Kliewer and K. Qian, Fuel, 2015, 155, 63–67 CrossRef CAS.
- H. Sharma, R. Giriprasad and M. Goswami, J. Food Process. Technol., 2013, 4, 1000252 Search PubMed.
- A. Yavari, A. Heshmati, M. Hamedi and S. Haghbin, J. Am. Oil Chem. Soc., 2010, 87, 109–114 CrossRef CAS.
- P. Travnicek, E. Krcalova and T. Vitez, Pol. J. Environ. Stud., 2013, 22, 1499–1504 Search PubMed.
- M. Kirubakaran and V. A. M. Selvan, Renewable Sustainable Energy Rev., 2018, 82, 390–401 CrossRef CAS.
- A. Daochalermwong, N. Chanka, K. Songsrirote, P. Dittanet, C. Niamnuy and A. Seubsai, ACS Omega, 2020, 5, 5285–5296 CrossRef CAS PubMed.
- T. Luo, R. Wang, F. Chai, L. Jiang, P. Rao, L. Yan, X. Hu, W. Zhang, L. Wei, A. Khataee and N. Han, Chemosphere, 2022, 303, 134925 CrossRef CAS PubMed.
- X. Yu, W. Liao, Q. Wu, Z. Wei, X. Lin, R. Qiu and Y. Chen, J. Hazard. Mater., 2022, 130312 Search PubMed.
-
T. R. Sahoo and B. Prelot, in Nanomaterials for the Detection and Removal of Wastewater Pollutants, ed. B. Bonelli, F. S. Freyria, I. Rossetti and R. Sethi, Elsevier, 2020, pp. 161–222, DOI:10.1016/B978-0-12-818489-9.00007-4.
- A. Akinlua and R. M. Smith, Talanta, 2010, 81, 1346–1349 CrossRef CAS PubMed.
|
This journal is © The Royal Society of Chemistry 2023 |
Click here to see how this site uses Cookies. View our privacy policy here.