DOI:
10.1039/D3SU00080J
(Critical Review)
RSC Sustainability, 2023,
1, 1065-1084
Bioethanol, internal combustion engines and the development of zero-waste biorefineries: an approach towards sustainable motor spirit
Received
5th March 2023
, Accepted 15th May 2023
First published on 17th May 2023
Abstract
Nature is a huge reservoir of energy, aiding the proliferation of life on Earth. However, recently, the human race has understood the importance of conserving the energy sources that are available in nature and prone to depletion. Lately, it has been well understood that either the use of fossil fuels should be restricted or the potential of other energy sources should be explored. In this context, the concept of biofuel has emerged, which in its neat form or as a blend with petroleum products can achieve the above-mentioned goals. In this review, we depict the potential of bioethanol as a future transportation fuel. Furthermore, the compatibility, advantages, and shortcomings of bioethanol as a fuel for internal combustion engines are also discussed. Studies revealed that blending ethanol in petrol or Motor Spirit (MS) improves important engine features such as octane number (up to 5–10%), compression ratio (up to 2%), combustion efficiency (up to 30%), and engine torque (up to 8%). The use of biofuel is also considered significantly beneficial to the environment in terms of the emission of greenhouse gases. This aspect of bioethanol is also briefly presented in this review. The possibility of the large-scale production of bioethanol has attracted global interest, and consequently, the concept of a ‘biorefinery’ has been proposed recently. The development of biorefineries with a ‘zero-waste’ approach is an important aspect for the future global energy demand as well as the environment. The overall goal of this review is to analyze the potential of bioethanol as a sustainable Motor Spirit in the near future.
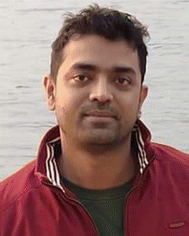 Shaswat Barua | Shaswat Barua is currently working as an Assistant Manager (Quality Control) in the Indian Oil Corporation Limited, Bongaigaon Refinery, Assam, India. His research interests include materials science, polymers, biomaterials, nanotechnology and sustainable energy. |
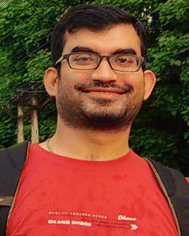 Debojeet Sahu | Debojeet Sahu is currently working as an Assistant Professor in the Department of Chemistry, Royal Global University, Assam, India. He has been involved in experimental research in the field of inorganic materials, catalysis and energy. |
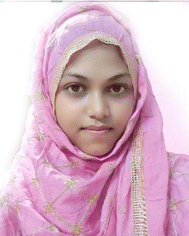 Firdous Sultana | Firdous Sultana is a Master's Student in the Department of Chemistry, Royal Global University, Assam, India. She has undertaken her Master's thesis under the supervision of Debojeet Sahu. |
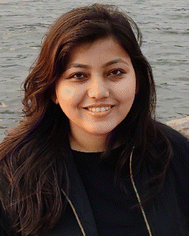 Swagata Baruah | Swagata Baruah is working as an Assistant Professor in the Department of Chemistry, Morigaon College, Assam, India. She has been involved in teaching undergraduate chemistry and research in chemical science. |
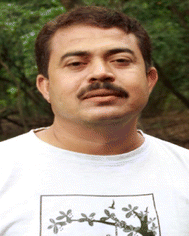 Sadhan Mahapatra | Sadhan Mahapatra is currently holding the position of Professor & Head in the Department of Energy, Tezpur University, Assam, India. He has years of experience in the fields of biomass gasification, climate responsive buildings, decentralized energy options and energy conservation. |
Sustainability spotlight
This review article is a one-stop source for readers to gain all the important information on bioethanol. Firstly, the generations of bioethanol and their sustainability are described. Secondly, the compatibility of bioethanol and its blended fuels with motor engines is described. Further, approaches towards zero-waste biorefineries are highlighted. This review also includes the vital environmental issues related to bioethanol and blended fuels. The insight applied in this review article is a completely novel approach. The emergence of biorefineries for the production of sustainable fuels is the focus herein.
|
1. Introduction
1.1 The global energy scenario
Energy is a primary requirement for economic development globally. The use of energy has become an essential requirement for life with the evolution of human civilization. The injudicious exploitation of petroleum products has also led to the quick depletion of their natural feedstock.1 Further, rapid industrialization and increasing population have accelerated energy consumption worldwide.2 Accordingly, advanced technologies have been employed to fulfil the ever-increasing energy demand.3 Although society depends on fossil fuels, it is an accepted fact that fossil fuels are responsible for adverse environmental effects, including poor air quality, depleting crude oil reserves, increase in global temperature, and climate change.4,5
According to the BP Statistical Review of World Energy, liquid petroleum products are the most widely consumed fuels globally, which is followed by coal and natural gas.6 The International Energy Outlook 2017 (IEO2017) predicts that the global energy demand will increase by 28% from 2015 to 2040.7 This prediction further assumes that this growth will be highly influenced by most of the non-OECD (Organization for Economic Cooperation and Development) countries of Asia, particularly India and China (Fig. 1). Hence, it is necessary to replace fossil fuels with alternative sources of energy to meet the high energy demand and considering the environmental concerns. Extensive research works have been carried out in the field of renewable energy, which is regarded as an eco-friendly and sustainable source of energy. During the last few decades, the concept of clean energy sources has emerged, which are gradually replacing conventional energy sources. Amongst the alternative fuels, biomass-based fuels, also known as biofuels, offer many advantageous attributes over conventional petroleum-based fuels. The natural abundance of biomass sources, environment friendly potential, economic viability and sustainability are the main merits of biofuels. Due to the abundance of natural resources, low-cost labour, and favourable climatic conditions in developing countries, they have shown immense potential for biofuel production.8
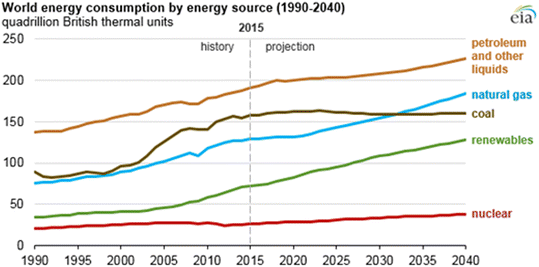 |
| Fig. 1 Global energy consumption pattern between 1990–2040 (reproduced from ref. 7: US Energy Information Administration, International Energy Outlook, 2017). | |
1.2 Biofuels and present global scenario
Renewability and sustainability are the fundamental principles in the management of natural resources. It has become apparently clear that the dependence on fossil fuels will lead to their gradual depletion. Consequently, intense research is focused on alternative fuels. The ever-increasing global energy demand, high price of fossil fuels, and the alarming increase in global temperature are the main factors behind the extensive exploration of new and sustainable energy sources. Accordingly, energy analysts and giant stakeholders around the world have steadily started exploring the possibilities of using bio-based feedstock as energy sources.9 Generally, renewable energy sources have the capacity to replenish themselves naturally. Renewable energy includes bioenergy, hydropower, geothermal energy, ocean energy, solar energy, and wind energy. Amongst them, bio-based energy derived from biofuels has some further advantages such as cheap and abundantly available feedstock, low cost production methods and potential for implementation on a large scale especially in developing countries.10 Biomass energy alone contributes 70% (as of 2016) as the primary energy source to the overall renewable energy supply (Fig. 2).
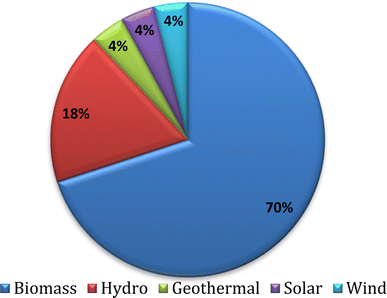 |
| Fig. 2 Renewable energy supply in 2016.10 (Reproduced from ref. 10: Global Bioenergy Statistics 2019 World Bioenergy Association.). | |
‘Biofuels’ refer to solid, liquid and gaseous fuels primly produced from biomass such as animal and plant wastes and residues. Bioethanol, biodiesel, biomethanol, biogas, and syngas are the main categories of biofuels. The International Energy Agency (IEA) projected an estimate showing the current bioenergy supply to be about 11% of the total global primary energy demand. India and China are regarded as the largest biomass producers in the world.11 OECD countries, together with several developing countries including India, Brazil and the countries of Latin America and Africa are trying to produce biomass-based electricity in recent times. Despite the tremendous R&D works on biofuels, the cost of their production still does not meet the desired standard. However, it is expected that due to the environmental merits and extensive use/misuse of conventional fuels, biofuels related to automotive industries will grow rapidly in the coming decades. Accordingly, in the last decade, around 40 million hectares worldwide, which are about 2.5% of the global cropland, are used for the growth of bioenergy crops.12 Presently, Brazil shares 21% of the global road transport fuels produced from bioresources, while the European Union (EU) and the United States (US) share about 4% and 3%, respectively.13 In 2012, the global biodiesel production was around 22.5 billion litres. In this regard, 41% of the total production was credited to the EU, mainly Germany. Secondly, the US contributed 16%, followed by China (>10%). Contrarily, about 60 billion litres of bio-based ethanol have been produced globally in 2012, where the US is the largest supplier (corn-based ethanol), followed by Brazil (sugarcane-based ethanol). EU, Canada and Southeast Asian countries also started producing bioethanol from other sources such as cereals and maize. According to the targets of the IEA, the EU and US are in line to replace 6% of petroleum fuels with bio-based fuels.14 However, according to the IEA and economists, the EU requires 5% of available cropland for growing energy crops to meet the target of 5% displacement of gasoline fuels. This differs in the case of the US, with a requirement of 8% of available cropland. The US government has committed a three-fold increment in biofuel production in the coming 10 years.15
Gradually, bioenergy is becoming a larger contributor to the overall global energy, which is expected to be up to 20–30% of the total primary energy demand by 2035. The Indian National Policy on Biofuels, 2018 requires the set-up of proper mechanisms to produce biofuels from non-edible bioresources. This policy aims at blending biofuels (up to 20%) with conventional fuels by 2030. The current percentage of ethanol in MS is 10% in India. However, blend studies are ongoing to increase this to 12% initially and 20% by the end of 2030 according to the Ministry of Petroleum and Natural Gas, Govt of India. A similar percentage of blending is applicable in the USA.
Further, one of the ambitious targets of this policy includes the production of electricity (>40%) from non-fossil fuels by the next decade.16 Biofuels are derived from living organisms or waste through different processes. Some of the approaches employed for the extraction of biofuels from biomass feedstock include pyrolysis, liquification, gasification, and biochemical and thermochemical treatments.17–20 In this review, we focus on bioethanol produced from different conventional and non-conventional sources. Currently, it is expected that bioethanol has the potential to substitute gasoline in the near future either in its neat form or by blending with conventional fuels. Thus, in the quest of investigating the wider production and potential of bioethanol, different countries around the world are highlighting their concerns.
1.3 Bioethanol
Bioethanol is the most extensively explored biofuel across the world mainly due to its potential as a transportation fuel. Bioethanol–gasoline blends have been considered for the last few decades as alternative transportation fuels. The concept of bioethanol was first proposed by Johann Tobias Lowitz in 1796.21 In comparison to petroleum fuel, bioethanol is readily decomposable and less noxious. The production of bioethanol is executed by using a number of plants and plant-based feedstocks. Plant residues such as leaves, seeds, roots, stems, and fruits together with their peels have been proven to be successfully used in the production of bioethanol.22–24 The process of producing bioethanol can be explained by a wide array of elements including the implication of pre-treatment process, pre-treatment chemicals, pressure, temperature, and sugar contents.25–27 Bioethanol has a high content of oxygen, which helps in the efficient oxidation of gasoline hydrocarbons during blending with gasoline.28 Thus, the emission of carbon monoxide (CO) and aromatic compounds due to incomplete/inefficient combustion is reduced to a considerable extent.29 Further, some significant merits of bioethanol include its high octane number (∼108), high heat of vaporization, and wide flammability limit.30 These attributes enable a shorter burning time together with a high compression ratio, thereby making it good fuel for internal combustion (IC) engines. Generally, bioethanol is blended with gasoline/Motor Spirit (MS) rather than high-speed diesel (HSD). This is due to the low cetane-rating (low ability to ignite) of bioethanol.31 The cetane rating is the fundamental requisite for a compression engine (CI) or diesel engine, which is analogous to the octane rating/octane number of spark ignition (SI) IC or petrol engines. However, the addition of a cetane improver and modification of the engine have also been done to use diesel–ethanol blends as engine fuels.32 The octane number, precisely the research octane number (RON), is a measure of the quality of MS. This determines the ability of the fuel to prevent early ignition, thereby preventing cylinder knocking. Thus, fuels, such as bioethanol a with higher RON, are preferred in spark-ignition internal combustion engines (SI-ICEs).33 The current percentage of ethanol in MS is 10% in India. However, blend studies are being conducted to increase this to 12% initially and 20% by the end of 2030 according to the Ministry of Petroleum and Natural Gas, Govt of India. A similar percentage of blending is applicable in the USA. In the following sections of this review, we elaborately explain the fuel quality and engine behaviour in terms of prospects of bioethanol-based SI-ICEs.
1.4 Biorefinery
With the aim of producing clean and sustainable biofuels, the concept of ‘biorefinery’ has been introduced recently. This concept is analogous to a petroleum refinery, which uses crude oil to produce a broad spectrum of marketable petroleum products, such as petrol, diesel and liquefied petroleum gas (LPG). Alternatively, biorefineries are designed for the sustainable processing of biomass to obtain a range of commercial products such as bioethanol, biodiesel, and biogas.34 The most attractive part of biorefineries is that they do not produce any hazardous by-products like a petroleum refinery. Further, the concept of biorefinery has been constantly upgraded to make it a ‘zero-waste’ refinery system.35 Some fully functional biorefineries across the world are operated by Blue Marble Energy Company (Odessa, Missoula), Himark BioGas (Alberta, Canada), Chemrec's Technology (Stockholm, Sweden), Numbitrax (South Africa), etc.36 The concept of biorefinery is relevant to developing countries, where different biomasses are abundantly available. Also, this will immensely aid rural development and the generation of employment. In this review, we outline the origin of bioethanol and its relevance in motor engines. Furthermore, requisite features of bioethanol are critically analyzed herein. The environmental impact of biofuels, especially bioethanol is also related to the present discussion. Further, for the sustainable production and utility of bioethanol, the importance of biorefineries is highlighted. Fig. 3 pictorially depicts the overall goal of this review.
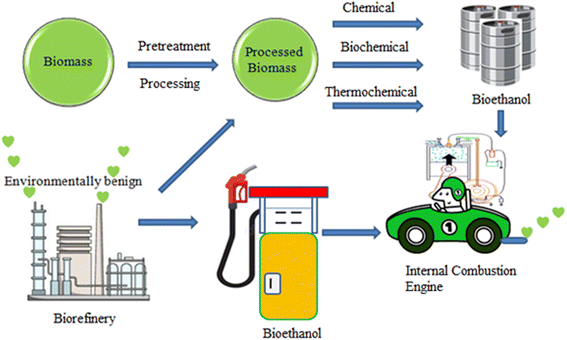 |
| Fig. 3 Bioethanol, internal combustion engines and the development of zero-waste biorefineries. | |
2. Development of bioethanol
Alcohol-based fuels are oxygenated fuels, which contain one or more oxygen that helps in reducing the heat of combustion. Thus, alcohols have been extensively studied as motor fuels. A few recent reviews have demonstrated the potential of methanol, ethanol, propanol and butanol as fuels for motor engines, especially in SI-ICEs.30,37–39 Among them, methanol and ethanol have been mostly recommended for SI-ICEs. Further, ethanol has attracted tremendous attention due to its clear colourless liquid state and agreeable odour. Again, the synthesis of ethanol from biomass has been widely probed for mass production.30 As already stated, ethanol is superior to MS in terms of RON, heat of vaporization, limit of flammability and flame speed.40 These attributes of ethanol impart a high compression ratio and shorter burning time, making ethanol as a superior fuel for SI-ICEs. However, the lower vapour pressure and lower energy density of ethanol than gasoline restrict its use as a motor fuel in its neat form. Further, the metal corrosiveness and environmental toxicity of use of pure ethanol hinder its commercial use.41 The feedstock for bioethanol production can be categorized into three major groups, as follows: (a) sucrose-based (e.g., sugar beet, sweet sorghum and sugarcane), (b) starch-based materials (e.g., wheat, corn, and barley), (c) lignocellulosic-based feedstock (e.g., wood, straw, and grass) and (d) algal feedstock.42Fig. 4 pictorially demonstrates the biochemical and thermochemical conversion of biomass into bioethanol and the production of syn-gas from the residual lignin. The research in the field of biofuels has recommended different generations of biofuels based on the types of feedstock. Accordingly, the following generations of bioethanol are highlighted in the following sections.
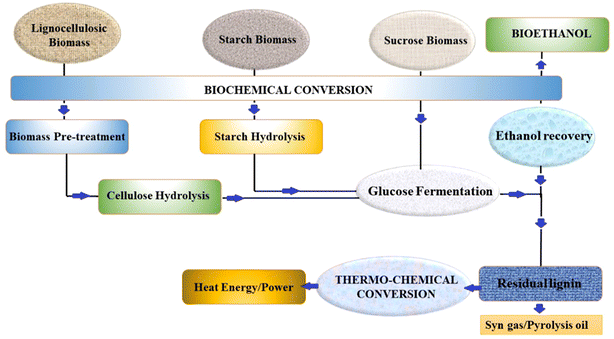 |
| Fig. 4 Schematic representation of the biochemical and thermochemical conversion of biomass into bioethanol. | |
2.1 First-generation bioethanol
First-generation (1G) biofuels are derived mainly from food crops and food-based feedstock. The production technologies and market viability of these biofuels have been well established. 1G bioethanol is produced via the direct fermentation of sugar and starch-based biomass, such as sugarcane, corns, maize, and wheat. The fermentation process is simple and it generates clean bioethanol, which has immense utility as a transportation fuel in its neat form or as a blend with commercial MS. The industrial production of 1G bioethanol mainly depends on the feedstock such as sugarcane, corn, and wheat, as mentioned above. Besides, some tuber-crops such as sweet sorghum, cassava, and sweet potato have also been used for mass-scale production.43
Bioethanol is derived from biomass by different chemical, biochemical and thermochemical routes. Most of the bio-derived ethanol has been produced by the alcoholic fermentation of biomass. The economic viability of 1G bioethanol plants relies on the mass production and market availability as well as the generation of value-added by-products such as carbon dioxide and animal feed.44 This implicates the up-gradation of 1G bioethanol plants to biorefineries to produce a wide range of products. The choice of feedstock depends largely on geographic locations and varies considerably from season to season. According to a survey in 2008, only 2% of fertile land globally is used to grow biomass to produce 1G biofuel.45 This has encouraged crops such as maize, beet, wheat, and others to be harvested, which can supply the requisite bioethanol for future sustainability without hampering food production. At present, several countries have already developed infrastructure for growing and cultivating grains that are now being fully used as the source of 1G bioethanol for conversion into ethanol. Currently, 1G bioethanol is produced industrially from agricultural sources rich in starch or sucrose by the fermentation process.
Brazil is the leading sugarcane-producing country, with approximately 300 industrial plants and most of them are dedicated fully for the production of sugar and ethanol.46,47 Sugarcane contains almost 12–17% total sugar by weight with 90% sucrose and 10% glucose or fructose. The production of ethanol can be carried out by two processes, where in one process the extracted juice is heated to ∼110 °C in factories to remove any contamination by microbes (Fig. 5).48 In the second process, the juice is filtered, followed by chemical treatment with SO2 and Ca(OH)2 to remove any coloration, and then pasteurized.49 The latter process is mostly performed in sugar–ethanol plants (annexed distilleries). Subsequently, the juice is made highly concentrated by the slow evaporation process, which results in the formation of clear sucrose crystals. The remaining juices are removed by centrifugation, leaving a product mixture of crystals and syrup-type stuff called molasses, which contains approximately 65% (w/w) sugars.50 Subsequently, molasses is subjected to a series of pre-treatments to remove any remaining impurities. Both the sugarcane juice and sterilized molasses naturally contain sufficient minerals and nutrients to be readily suitable for the fermentation process to produce ethanol via the addition of yeast (Saccharomyces cerevisiae).
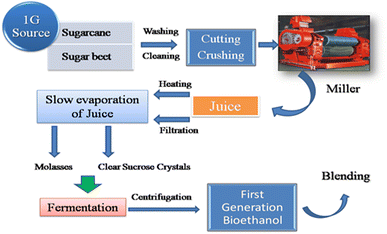 |
| Fig. 5 Schematic representation of a typical synthetic pathway for bioethanol production from 1G feedstock. | |
The efficiency of this fermentation can be improved by reducing the formation of acetic acid, which serves as an undesirable by-product in fuel production.51,52 The yeast can be recovered by centrifugation and ethanol can be separated by distillation process from the mixture containing sugars, minerals, and gases such as CO2 and SO2. The product obtained after distillation is hydrated ethanol, which is dehydrated by treatment with cyclohexane.53 Similarly, ethanol from sugar beets can also be produced from purified juices, syrups, and molasses by following the above-mentioned steps.54 An economic feedstock is an essential factor in setting up sustainable and cost-effective technology.55 An important concern associated with the production of 1G bioethanol is the weather in different regions and the cost of the process.56 The recent emphasis on corn production, improved processing technologies, and low use of chemicals dramatically improved the yield in the last decade.57
There are two ways by which ethanol can be produced from corn, i.e., either by dry-grinding or wet milling process.58 These two processes differ mainly in the steps involving feedstock preparation and recovery of the by-products. When starch is extracted using one of the above-mentioned processes, the procedure of converting it to fuel ethanol is the same regardless of its recovery. The first step for bioethanol production from corn is the hydrolysis of the starch content. The common corns mainly consist of starch, which is amylase (∼27%), and the rest is amylopectin. Generally, the liquefied starch slurry mash is prepared from corn and the pH is adjusted, followed by the addition of enzymes to break the complex starch unit into simple six-carbon sugars by the addition of enzymes.59 During this step, the polymeric content, i.e., amylose, mostly linear α-D-(1–4)-glucan and branched amylopectin, α-D-(1–4)-glucan, which has α-D-(1–6) linkages at the branch points, gets converted into sugars. The advancement in the development of thermostable α-amylases (enzymes for catalyzing the hydrolysis of α-D-(1–4)-glycosidic linkages in starch) and efficient glucoamylases (the saccharifying enzymes catalyzing the hydrolysis of the α-D-(1–4) and α-D-(1–6)-glycosidic bonds of starch from its non-reducing ends) is very useful in the conversion process.60 Specifically, α-amylase cleaves the starch polymer to produce the soluble dextrins by quickly hydrolyzing the α-1-4 bonds. Sebayang et al. reported a hydrolysis method in which sorghum starch was treated with α-amylase and glucoamylase enzymes.61 The starch-amylase mixture in distilled water was heated at a temperature of 90 °C and different stirring speeds, which provided the necessary energy and mechanical shear, respectively, to break down and rupture starch molecules of high molecular weight. This process was carried out for 90 min to reduce the size of the starch polymer and achieve liquefaction. In the liquefied dextrinized mixture, glucoamylase enzyme was added, which finally converted the liquefied starch into glucose. The as-obtained glucose could be conveniently converted to bioethanol in good yield with the help of microorganisms such as Saccharomyces cerevisiae (yeast) and Zymomonas mobilis (bacteria).62 The major advantage of this enzyme-assisted process is its low energy utilization and lower amount of non-glycosidic side products, which result in a sustainable outcome for ethanol production from starch-based crops or lignocellulosic biomass.63 The advantage associated with the sugar-rich crops is that these plants can be directly fermented and converted into ethanol without any extensive modification, unlike starches, which require hydrolysis. However, the difficulty is their storage for a prolonged period, where the depletion of sugar content takes place due to certain enzymatic reaction.64
The top global leaders in bioethanol production are the USA with 50.3 billion litres per year, Brazil with 25.5 billion litres per year, and then the European Union (EU) with 4.5 billion litres per year. The prime feedstock for the production of bioethanol in the USA, Brazil and EU are corn/maize, sugarcane, and cereal/sugar beet, respectively.65 With the increasing rise in petroleum prices, many countries are engaged in the generation of energy from biofuels. At present, the demand for ethanol in the USA is being fulfilled by the conversion of corn carbohydrates (i.e., starchy grains) as feedstock. The Renewable Fuels Standards (RFS) program of the USA projects the substitution of up to 20% of transportation fuel with bioethanol by the end of 2022.66 The USA developed 200 biorefineries operating in 28 different states and has been successful in producing 15.25 billion gallons of ethanol, which is equivalent to 58% of the global ethanol production, to achieve this target.66,67 However, a major concern with bioethanol is that a vast portion of the population is highly dependent on the calories obtained from these food sources, where corn is among the three principal types of cereals in addition to wheat and rice. Thus, the utilization of corn feedstocks for ethanol production is challenging, which may contribute to an extensive price hike for foods and promote global hunger, thereby leading to alarming social and environmental situations. This has encouraged the harvesting of crops such as maize, beet, wheat, and others, which can supply the requisite bioethanol for future sustainability, without hampering food production. The urge for biofuel production by these global leaders has simultaneously raised the concern of utilizing land or water for the cultivation of energy crops. Alternatively, these lands or water can be used to grow a huge amount of food crops to feed numerous people. Rulli et al. estimated that 200 million people can be fed by different countries in this regard [Table 1, (ref. 68)]. These facts and figures are of serious concern related to global food security. Thus, alternative sources for bioethanol production have been highly recommended worldwide. This has prompted research on further generations of bioethanol with a focus on economic viability and food security.
Table 1 Summary of biofuel energy consumed in each country during 2013 (ref. 68)a
Country |
Biofuel energy consumed (103 TJ per year) |
Water consumed for biofuel (106 m3 per year) |
Area cultivated for biofuel (103 Ha) |
People 1, 106 (—) |
People 2, 106 (—) |
The associated consumption of water and cultivated land area, and the number of people who could be fed by the food calories used for biofuel production considering the diets of the consumer (1) and producer (2), respectively (this table is reproduced from ref. 68: Rulli, M. C., Bellomi, D., Cazzoli, A., De Carolis, G. and D'Odorico, P. (2016). The water-land-food nexus of first-generation biofuels, Sci. Rep., 6(1), 1–10 under Creative Commons CC BY license.).
|
USA |
1162.4 |
88498.6 |
11245.4 |
143.3 |
147.9 |
Brazil |
506.7 |
30254.6 |
2752.0 |
29.1 |
28.6 |
Canada |
69.3 |
6853.5 |
1127.7 |
9.3 |
8.8 |
China |
62.0 |
7744.6 |
1212.1 |
10.0 |
8.8 |
Germany |
32.0 |
1960.8 |
331.5 |
3.4 |
3.7 |
UK |
19.2 |
1718.1 |
237.9 |
2.1 |
2.1 |
France |
16.6 |
694.4 |
122.6 |
1.6 |
1.9 |
India |
9.0 |
1097.4 |
60.7 |
1.0 |
1.0 |
Columbia |
8.6 |
505.5 |
160.5 |
0.6 |
0.4 |
Sweden |
7.6 |
598.6 |
106.4 |
0.8 |
0.8 |
Spain |
7.1 |
665.5 |
95.1 |
1.0 |
1.0 |
Poland |
6.0 |
387.5 |
99.3 |
0.7 |
0.7 |
Netherlands |
5.0 |
593.0 |
93.6 |
0.6 |
0.6 |
Italy |
3.1 |
229.2 |
39.6 |
0.4 |
0.4 |
Total
|
1914.7
|
141801.4
|
17684.4
|
203.9
|
206.7
|
2.2 Second-generation bioethanol
Second-generation bioethanol has emerged from extensive research and economic analysis, which put a restriction on the use of food crops for energy production. Thus, 2G bioethanol has shown immense commercial potential in terms of feedstock availability. The feedstock of second-generation bioethanol is inexpensive and abundantly available. The lignocellulosic biomass from plant and agricultural waste is pre-treated by chemical or biochemical means. The subsequent fermentation process yields bioethanol.69 The conversion of lignocellulosic biomass to reducing sugars is quite challenging compared to starch. Pre-treatment is a process that makes cellulose and hemicellulosic materials of the biomass more vulnerable to hydrolytic enzymes. Hydrolytic enzymes such as cellulase and hemicellulase convert the complex cellulosic structure to simple sugars.70 However, the pre-treatment process needs to be regulated carefully to maintain the overall cost of bioethanol production. Further, environmental concerns are also associated with the harsh chemicals such as acids and bases used in the process of pre-treatment. The crystallinity of cellulose gets reduced during the pre-treatment process together with de-lignification. High temperature (∼320 °C) and pressure (∼25 MPa) are required for converting the rigid crystalline structure of cellulose to an amorphous structure. Hemicelluloses are heteropolymers consisting of different short-chain, branched sugar units. They also contain uronic acid units such as D-galacturonic acids and D-glucuronic acid. Pentoses and hexoses are the prime building blocks of the monosaccharides present the hemicellulose structure.71 The largest hemicellulose component is xylan, which is regarded as the third most abundant biopolymer on Earth.72 A typical hardwood plant contains about 35% hemicellulose, while it is 28% in the case of softwood plants.
The three-dimensional biopolymer lignin is a major constituent of lignocellulosic biomass. Lignin is also resistant to the action of enzymes. Thus, delignification is an important step in the production of bioethanol from 2G feedstock. Significantly, the lignin extracted from lignocellulosic biomass has high commercial value. It is used as a substrate for many commercially available chemicals, polymeric foams, composites, etc. Thus, lignin valorization in the pre-treatment stage is important. Typically, lignocellulosic biomass consists of cellulose (40–60%), hemicellulose (20–40%) and lignin (10–25%).73 This type of biomass can be extracted from different parts of plants such as their leaves, seeds, stem, roots, and fruits and their peels. However, the processing steps for the production of bioethanol involved in these plant parts depend on a number of factors such as the presence of deductible sugars, the pre-treatment process, the chemicals used, temperature, and pressure. The pre-treatment of lignocellulose is one of the vital steps in bioethanol production, where the cross-linked cellulose and lignin are hydrolyzed into free sugars. This is further degraded using certain microorganisms for fermentation to obtain ethanol.74 The pre-treatment process can be carried out via different methods using diluted acid and alkali, microbial organisms, catalysts, ultrasonic radiation, etc., depending on the composition of the material.75Phanerochaete chrysosporium (crust fungi) is the commonly used microbe for breaking the β-glucoside linkages present in lignin. The use of microorganisms can dramatically reduce the gross chemical requirement and makes the method cost-effective and sustainable for pre-treatment strategies.76 Combined pre-treatment of lignocellulosic materials represents another effective method. Combining P. chrysosporium and diluted H2SO4 shows better potential compared to traditional means.77 The efficacy of the combined treatment depends largely on the sites available for interaction, which can be tuned easily by particle resizing to obtain the desired yield.
One of the important food-based sources that contains a high amount of lignocellulosic material is sesame (Sesamum indicum), which is a commonly grown crop in South-Asian countries.78 Burning of this biomass emits a high amount of heat and gases, and thus has unfavorable environmental consequences. Kumar et al. reported for the first time the production of bioethanol from sesame plant residue.79 Their study investigated particle sizes of 400, 850, and 1300 μm, which were treated with Phanerochaete chrysosporium for degradation, followed by soaking in 1% H2SO4 up to 60 min at 100 °C. The pre-treated sample was treated with HCl and NaOH solutions (1 N), after which fermentation was carried out in a nitrogen environment using fermentative yeast (S. cerevisiae). The analytical and kinetic studies showed that the particle size of 400 μm resulted in the highest yield of reducing sugars with a maximum yield of 1.90 g L−1 ethanol after 60 h of fermentation. Although 1G resources are very popular and effective, they are mostly food-based raw materials, and therefore further research on second- and third-generation biofuels is being carried out. Even though 2G bioethanol production may not be as developed as 1G, the benefits related to the feedstock availability in 2G bioethanol holds tremendous potential for sustainable development. With the increased interest and investment in 2G bioethanol production, the experts predict that it may even replace 1G technologies in the near future.80
2.3 Third-generation bioethanol
Critical concerns related to the availability of feedstock and processing difficulty inspired the scientific community to think beyond 1G and 2G bioethanol. In this context, the concept of using algae opens a newer avenue for the mass production of bioethanol of third-generation (3G). Algae and microalgae have been identified as important feedstocks for the production of 3G bioethanol due to the easy and direct conversion of algal mass to energy.81 However, the technology involved in the extraction and isolation of algae from the marine environment influences the production of 3G bioethanol. Algae are broadly classified as unicellular or microalgae and multicellular or macroalgae. Due to their high lipid content, microalgae can float on water surfaces.82 Different types of microalgae such as green algae (Chlorophyceae), golden algae (Chrysophyceae), and diatoms (Bacillariophyceae) have been identified by researchers. Different species of microalgae have different protein, lipid and carbohydrate contents. Some microalgal species such as Scenedesmus and Chlorella were found to possess about 50% carbohydrate.83,84 Again, macroalgae or commonly termed seaweeds are widely found in Asia, Japan, and China, with the three main types being red algae (Rhodophyceae), brown algae (Phaeophyceae), and green algae (Chlorophyceae). They mainly contain carbohydrates, proteins, and lipids, the composition of which differ from species to species.85 Jambo et al. depicted the composition of different species of microalgae and macroalgae in detail (Table 2).86
Table 2 Chemical composition of different algal species (ref. 86)a
Algal species |
Compositions (%) |
Protein |
Carbohydrate |
Lipid |
This table is reproduced with permission from ref. 86: Jambo, S. A., Abdulla, R., Azhar, S. H. M., Marbawi, H., Gansau, J. A. and Ravindra, P., A review on third generation bioethanol feedstock, enewable Sustainable Energy Rev., 2016, 65, 756–769.
|
Microalgae
|
Chlamydomonas reinhardtii
|
48 |
17 |
21 |
Chlorella vulgaris
|
41–58 |
12–17 |
10–22 |
Porphyridium cruentum
|
28–39 |
40–57 |
9–14 |
Prymnesium parvum
|
28–45 |
25–33 |
22–39 |
Scenedesmus dimorphus
|
8–18 |
21–52 |
16–40 |
Scenedesmus obliquus
|
50–56 |
10–17 |
12–14 |
![[thin space (1/6-em)]](https://www.rsc.org/images/entities/char_2009.gif) |
Macroalgae
|
Eucheuma cottonii
|
9–10 |
26 |
1 |
Gelidium amansii
|
20 |
66 |
0.2 |
Laminaria japonica
|
8 |
51 |
1 |
Sargassum ilicifolium
|
8–9 |
32–33 |
2 |
Ulva lactuca
|
17 |
59 |
3–4 |
Undaria pinnatifida
|
24 |
43 |
3–4 |
The synthesis of 3G bioethanol from algal feedstock involves several steps. Firstly, algal cultivation and harvesting play a major role in the overall process of bioethanol production. Significantly, the ease of cultivation of this type of feedstock has attracted global attention. The crude algal feedstock extracted from the sea needs proper drying to avoid gelation of the mass. Subsequently, the dried algal feedstock is powdered to reduce the size of the mass. This powdered form is used for the next steps, which involves hydrolysis and subsequent fermentation processes.87 The hydrolysis process depolymerizes the cellular structure of algae, which exposes the polysaccharides. The main polysaccharides found in algal cells are alginates, agarans, fucans and carrageenans.88 Hydrolysis converts these polysaccharides to simple sugars. Acid hydrolysis is a common process in this regard, where dilute sulfuric acid (H2SO4) has been widely used. The acid treatment first breaks the crystallinity of the polysaccharide structure, and finally cleaves the glycosidic bonds.89,90 Again, enzymatic hydrolysis employs cellulose-degrading enzymes such as cellulase, which can directly convert the polysaccharides to simple sugars for the fermentation process. The common enzymes used in this context are β-glucosidase and endo- and exo-cellulases.86 However, the interaction of the algal biomass with the enzyme is a crucial factor that determines the hydrolysis process. The simple sugars generated by the hydrolysis process can be easily converted to bioethanol by microbial fermentation. The most widely used microorganism for fermentation of sugars is yeast (Saccharomyces cerevisiae). With the advancement of technologies, advanced fermentation processes have been developed by researchers for economic viability and mass scale fermentation. The commonly used industrial fermentation techniques are separated hydrolysis and fermentation (SHF) and simultaneous saccharification and fermentation (SSF). Jambo et al. summarized the overall production of 3G bioethanol in a pictorial manner (Fig. 6).86
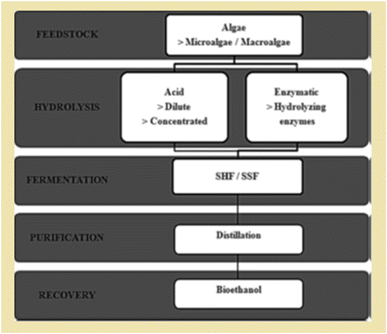 |
| Fig. 6 Separated hydrolysis and fermentation (SHF) and simultaneous saccharification and fermentation (SSF) (reproduced with permission from ref. 86: Jambo S. A., Abdulla R., Azhar S. H. M., Marbawi H., Gansau J. A. and Ravindra P., A review on third generation bioethanol feedstock, Renewable Sustainable Energy Rev., 2016, 65, 756–769.). | |
Besides the aforementioned generations, another generation, i.e., fourth generation (4G), bioethanol has recently emerged. The feedstock for this generation is genetically modified microalgae.91 This modification enhances the quality and productivity of the 4G feedstock. Algal strains such as Dunaliella and Chlorella have the capacity to accumulate >50% carbohydrates. Therefore, these microalgae may be utilized as promising feedstock by altering their genetic and metabolic pathways.92 In this context, the use of cyanobacteria through pyruvate decarboxylase (pdc) and alcohol dehydrogenase II (adhII) gene transformation is a prudent step for producing 4G bioethanol. Researchers across the world have been investigating various other techniques for the mass production of 4G feedstock to fulfil the demand of blended fuels.
3. Bioethanol and internal combustion engines
In the 1860s, Étienne Lenoir invented the first commercially viable internal combustion engine (ICE).93 However, the modern ICE was created by Nicolaus Otto around 1876.94 An ICE is a type of heat engine consisting of a combustion chamber, where the high temperature and high pressure produced by the combustion of fuel generate force to drive the engine. The chemical energy stored inside the chemical bonds of the fuel is transformed to mechanical energy inside an ICE. The low cost, efficient power to weight ratio, and simple and robust operating properties of these engines are the primary reasons for their wide acceptance and continuous usage in different sectors for decades. The working fluids in an ICE are fuel–air mixtures (before combustion) and burned products (after combustion). The work transfer occurring between the working fluids and mechanical components of the engine such as cylinder walls and piston produces the desired power.95 The high efficiency, low cost and high power-to-weight ratio of SI and CI engines make them suitable for a wide range of applications in the transportation sector.96,97 These engines have been developed to meet the major criteria such as low cost, high efficiency, high mileage, and lowest possible emission of environmental pollutants. Thus, gasoline has become the first choice of manufacturers and customers for SI-IECs. The volatile nature of gasoline offers easy starting of the engine together with excellent cold-weather performance.98
The air introduced in the cylinder is mixed with the vaporized fuel in an SI-IEC. The carburetor, a single-point injection system, regulates the flow of air and fuel to the engine. The desirable engine characteristics include high efficiency, good combustion features and minimum emission of air pollutants through the exhaust. These characteristics are attained by close monitoring of the engine operating state, air and fuel flow and exhaust gas features.95 Gasoline-based SI-ICEs have gained popularity during the 20th century. However, during the late 20th century, two major drawbacks have been recognized, which prompted researchers to think beyond the conventional ICEs. These two major factors are the depleting crude reserve across the globe and the environmental pollution due to exhaust.99 This has raised concerns for the development of engines, the replacement and modification of fuels, or both. In this case, various studies have been performed, which suggest that the complete replacement of gasoline or petrol is practically not possible because of the lack of a similar alternative. Therefore, blending alternative fuel(s) with conventional gasoline or MS is regarded as a prudent step to minimize the dependence on fossil fuels and attain environmental benefits.100 Researchers have witnessed that MS-ethanol blends of up to 10% can be used for motor vehicles with conventional SI-ICEs.101 However, ethanol beyond 10% creates corrosion in some parts of SI-ICEs.102 This requires the modification of the engine to use ethanol-blended MS above 20%. In this quest, the concept of flex-fuel vehicles (FFVs) was introduced, which are capable of operating on MS-ethanol blends in the range of 0–85%.103 FFVs have been widely accepted in Brazil and a great percentage of old vehicles have been replaced to cope with the blended E27 and E100 hydrous ethanol fuels. Other countries are also adopting new engine technologies to make vehicles compatible with higher percentages of ethanol.104 However, this will inevitably increase the cost of the vehicles to a certain extent. Therefore, the selection of fuel and optimization of the engine characteristics need to be considered thoroughly in the coming years. It has been observed that the vehicles operating on MS-ethanol blends show similar efficiency to that of MS-operated vehicles.105
Biofuels are capable of reducing greenhouse gas (GHG) emissions, which directly helps to maintain the environmental and statutory norms. Thus, ethanol-blended MS is expected to act as a sustainable and greener fuel.101 Further, these blends are highly attractive because of their compatibility with SI-ICEs. The main reasons for this compatibility have been recognized as the high RON and high temperature- and pressure-withstanding capability of MS-ethanol blends.106 Controlled ignition at high temperature and pressure is also an advantageous feature of these blends. Researchers have observed that high-octane fuels such as ethanol are favorable for high compression ratios. Thus, MS-ethanol blends can impart higher efficiency to SI-ICEs. Recent studies have revealed that blending ethanol (85%) with MS can improve the engine performance up to 9% compared to unblended MS fuel.107 In the above-mentioned cases, the importance of bioethanol has been investigated thoroughly in the last few years. Thangavelu et al. depicted the impact of using bioethanol-blended MS on SI-ICEs in detail.95 This study presented a comparative account of the basic engine features such as ignition time, combustion efficiency, engine torque, flame speed, anti-knocking characteristics, cylinder pressure, and temperature, and combustion duration when bioethanol is blended with MS or pure gasoline/MS. Bayraktar investigated the performance of ethanol-blended MS and suggested that normal SI-ICEs do not require modification for up to 16.5% of ethanol-MS blends.108 Further, the combustion efficiency of four-stroke SI-ICE was studied by Ozsezen et al., which revealed that blended MS can provide higher efficacy compared to pure MS.109 Again, the higher brake thermal efficiency of SI-ICEs is attributed to the higher octane number. It has been witnessed that blending ethanol up to 5% to 10% in MS can profoundly increase the brake thermal efficiency of SI-ICEs. This may be due to the decrease in the break specific fuel combustion, as stated by Chansauria and Mandloi.110 Another important feature of SI-ICE engines is the engine torque, which signifies the rotation force of the engine. A slight increment in engine torque was observed in the case of 5–20% of ethanol-blended MS used in an SI-ICE.111 Yucesu et al. and Topgul et al. observed an increment of 8% and 4.26% in engine torque, respectively, on blending 60% ethanol in MS.112,113
In SI-ICEs, the compression ratio (CR) signifies the ratio between the maximum and minimum volume of the cylinder, which is expressed as follows:
where ‘
Vd’ is the displacement volume and ‘
Vc’ is the clearance volume. The CR of these engines has been improved by the incorporation of ethanol-blended MS.
114 However, the ethanol content directly dictates the extent of the increment of CR. Researchers observed a 1.5–2% improvement in CR when 30% ethanol is blended with MS.
110 The increase in CR directly affects the specific fuel consumption of the engine. Thus, it can be assumed that ethanol blending not only improves the efficiency of SI-ICEs but also contributes to the cost-effectiveness of the engine by decreasing the fuel consumption.
115–117 Beyond the pure blending of ethanol in MS, recent studies have also endorsed hydrated ethanol for SI-ICEs. In this context, an improvement in engine torque was observed by 1.6% in the case of flexi fuel SI engine, when 100% ethanol (hydrated ethanol) was used instead of 22% blending (E22).
118Table 3 shows a representation of some of the improvements in the features of SI-ICEs when ethanol is blended with MS and used as fuel.
Table 3 Improvement in SI-ICE features on blending ethanol in MS than pure MS
Engine feature |
Improvement up to (%) |
Ethanol (%) |
Ref. |
Compression ratio (CR) |
1.5–2 |
30 |
110
|
Brake thermal efficiency |
1.9–2.5 |
5–10 |
110
|
Wheel power |
2.2 |
5–10 |
119
|
Combustion efficiency |
31.12 |
40 |
120
|
Engine torque |
8 |
10–60 |
121
|
RON |
∼5–10 |
5–30 |
122
|
Brake specific fuel consumption |
5.5 |
5–10 |
119
|
Brake mean effective pressure (BMEP) |
∼0.5 |
100 (undiluted bioethanol) |
123
|
Brake power |
14.7 |
40 |
120
|
Volumetric efficiency |
Slight increment |
5–20 |
124
|
The above discussion clearly presents an understanding of the importance of ethanol-blending in MS. The development of bioethanol in terms of process and production is crucial for the sustainable utilization of these blended fuels. The global scenario of bioethanol production is still in its infancy. In comparison to giant petroleum refineries, bioethanol plants still need to be developed. However, this concern germinated the idea of commissioning biorefineries, which can efficiently utilize bio-based feedstock for the large-scale production of bioethanol to meet the increasing energy demand.
4. Biorefineries for sustainable motor spirit
The biorefinery concept mainly aims to produce commercial products and green energy, together with better economic sustainability.125 The growth of urbanization has resulted in a tremendous increase in energy demand, and it has also resulted in the huge consumption of natural resources as well as the generation of large anthropogenic waste. Therefore, to meet the ever-increasing demands for power and energy, the utilization of waste for the production of bioenergy through biorefineries is becoming an alternative in recent times. The concept of a biorefinery is analogous to that of a petroleum refinery, where many marketable products including chemicals, energy, and fuels can be refined from crude oil. The main difference between the two is that biorefineries use renewable materials as feedstock such as biomass and biowaste, whereas traditional petroleum refineries use crude oil as the feedstock.126 Thus, biorefineries can be considered to be one of the key sources for future sustainable energy supply. The concept of biorefineries started in the 1990s, when much emphasis was given to the utilization of biomass as renewable sources for energy production.127 A biorefinery facility does not represent fixed technology; in fact, it provides a facility where different routes can be adopted for different feedstocks to produce a spectrum of valuable products from biomass.128 The International Energy Agency also provides a similar type of definition for biorefineries.129 The main purpose of a biorefinery is to optimize the use of biomass instead of using expensive and specialized crops, which can minimize the cost of the input, and therefore improve the profit of the production processes. Biorefineries have the potential to replace petroleum refineries, and thus can provide an alternative to fossil fuel, which can play a major role in reducing carbon emissions and improving the economy of a country.
The biorefinery approach is a multistep process, which can be categorized considering the types of feedstock such as lignocellulosic, manure, and marine, the technologies involved (thermochemical and biochemical conversion), and lastly on the nature of products.130 The appropriate characterization of the feedstock, technologies, and products is necessary for any biorefining process to understand how the individual biomass components and reaction products interact at each stage in the process. The choice of feedstock plays a crucial role in biorefineries, aiming at large-scale production. Due to the challenges faced with many 1G and 2G raw materials, researchers have investigated different sources that can provide a sustainable supply chain network.131 Lignocellulosic biomass as the most abundant natural resource obtained primarily from the woods and plants is widely explored in many biorefineries given that it is one of the most inexpensive and high-energy density raw materials.132 Because of its many advantages, many pilot and demonstration biorefinery plants have been developed and various commercial projects are evolving for the selective production of cellulosic ethanol.133Table 4 presents the biorefineries/pilot plants around the world presently producing bioethanol.
Table 4 Biorefineries around the world producing bioethanol
Company name |
Country |
Feedstock |
Process |
Product |
Capacity |
Ref. |
Bankchak petroleum |
Thailand |
Cassava algae |
Thermochemical |
Bioethanol |
120 000 barrels per day |
134
|
LanzaTech |
Chicago, USA |
Woody biomass |
Thermochemical |
Bioethanol |
15 000 t per year |
135
|
INBICON |
Denmark |
Straw, corn |
Autohydrolysis |
Bioethanol, lignin pellets |
4300 t per year |
136
|
BioFlex® |
Brazil |
Sugarcane straw |
Steam explosion |
Bioethanol electricity |
65 000 t per year 50 MWe |
ABENGOA |
Spain |
Corn |
Steam explosion |
Bioethanol biogas |
75 000 t per year |
BETA-RENEWABLES |
Italy |
Wheat straw |
Uncatalyzed steam explosion |
Bioethanol biogas |
60 000 t per year |
Alto Ingredients Pekin Inc. |
Pekin, USA |
Corn |
— |
Bioethanol |
60 MGY |
137
|
KAAPA ethanol Ravenna |
Ravenna, USA |
Corn |
— |
Bioethanol |
125 MGY |
Reeve Agri-energy Inc. |
Garden City, USA |
Corn, sorghum |
— |
Bioethanol |
13 MGY |
Red River biorefinery |
Grand Forks, USA |
Waste sugars/starch |
— |
Bioethanol |
17 MGY |
Seaboard energy Kansas |
Hugoton, USA |
Cellulosic biomass |
— |
Bioethanol |
25 MGY |
Gírio et al. described the details of biorefineries and biofuel pilot/demonstration plants around the world.136 Many biofuel plants and biorefineries have been developed in the last few decade. The prime factors influencing the commissioning of biorefineries are the availability of feedstock, process feasibility, demand, and supply ratio and sustainability. Two techniques are commonly adopted in biorefineries to convert lignocellulose to bioethanol, which are biochemical and thermochemical conversions. Thermochemical conversion is a robust technique, in which a wide range of biomass can be employed.137 The conversion of ethanol from wood chips and agricultural residues instead of corn, sorghum, or soybean stover is used in the thermochemical conversion due to their robustness. In the thermochemical process, high temperature is used to achieve faster conversion rates in the presence or absence of a catalyst. Generally, this process proceeds through three stages, as follows: (i) partial degradation of lignocellulose, (ii) fractioning of the degraded substances and further processing of each fraction and (iii) finally the separated component undergoes complete decomposition at high temperature to syngas, from which mixtures of alcohols can be obtained by regulating the reaction components such as catalysts, temperature, and pressure.138,139 Subsequently, the resulting alcohol is cooled and condensed, which undergoes further distillation and purification to recover the pure bioethanol.140 Technically, thermochemical conversion can be classified into two types. In gasification, the depolymerization of lignocellulose is carried out in the presence of oxygen at high temperatures (>850 °C), resulting in a gaseous intermediate (syngas). Another process is pyrolysis, which is comparatively the milder depolymerization of biomass. Here, an intermediate liquid (bio-oil) is produced in the absence of oxygen at lower temperatures (400–650 °C).141 The thermal conversion is generally applicable to solid biomass. The use of water in most cases prevents the use of some additional chemicals, which aids to the cost efficiency of biorefineries.142
Another platform for cellulosic ethanol production is biochemical conversion. This is a popular choice for selective bioethanol production and is expected to be commercialized within a short period.143 It involves biological pre-treatment employing different micro-organisms or bio-enzymes, which selectively degrade lignin and hemicelluloses. Thus, enhanced biomass saccharification, and consequently improved bioethanol production are achieved. In biochemical conversion, the intermediate products are the sugars that can be fermented or biocatalysed into a range of advanced biofuels and valuable chemicals such as ethanol. In contrast to thermochemical conversion, the biochemical process occurs at lower temperatures, and due to this, the conversion often has lower reaction rates. The major advantages associated with the microbe-based pre-treatment are its low cost, low chemical consumption, moderate energy requirement, zero-waste generation, and easy downstream processing. The crucial steps in these biorefineries are feedstock supply, pre-treatment using micro-organisms, enzymatic hydrolysis, biological conversion (fermentation) and bioethanol recovery.144 This approach can provide more purified bioethanol production compared to thermal and hydrothermal degradation. However, the major drawback reported with biochemical operation is its limited flexibility, the common obstacle being the longer incubation time with some microbial treatment. Nevertheless, by choosing selective lignin-degrading bacteria, this issue can be resolved considerably. Moreover, these bacteria can easily be modified genetically to make them highly adaptable in de-lignification.145
The quality and quantity of ethanol yield largely depend on the selection and effective pre-treatment of feedstock. It has been found that about 40–60% of the total manufacturing costs in a typical biorefinery is associated with the processing of the feedstock. If ethanol production is examined on a per-gallon basis, then this value is approximately 30–32% of the total production cost.146 A detailed cost analysis of biochemical conversion was estimated in the literature.147 This study concluded that the cost of the enzymes and feedstocks are two major contributors to the overall cost of the technology. Thus, effective pre-treatment of the lignocellulosic material at minimal cost and energy with an abundant source of feedstock that generates zero waste is of utmost importance to start the full-scale commercialization of lignocellulosic biorefineries.148 Requejo et al. demonstrated a conceptual biorefinery using olive oil tree trimmings (OTT) as second-generation (2G) bioethanol feedstock and assessed the temperature and autohydrolysis time effects.149 The processes involved in the production of 2G bioethanol are pictorially presented in Fig. 7.
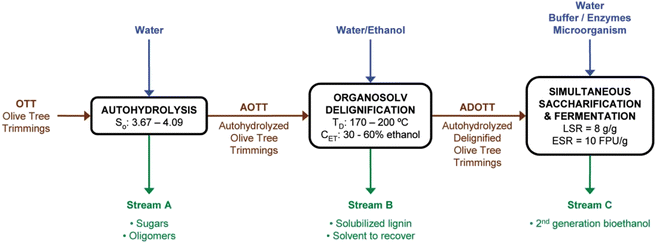 |
| Fig. 7 Representation of the conceptual biorefinery scheme. S0: autohydrolysis severity; TD: delignification temperature; CET: ethanol concentration in pulping liquor; LSR: liquid to solid ratio; and ESR: enzyme to substrate ratio (reproduced with permission from ref. 149: Requejo A., Peleteiro S., Rodríguez A., Garrote G. and Parajó J. C., Second-generation bioethanol from residual woody biomass. Energy Fuels, 2011, 25(10), 4803–4810). | |
Larragoiti-Kuri et al. proposed a design to simultaneously study the economic, environmental and safety indexes for an optimized biorefinery.150 This study utilized a multi-objective optimization technique in a lignocellulosic biorefinery using corn cob as the feedstock. The method was successful for the manufacturing of multiple products, among which bioethanol could be recovered in up to 95% yield. Zondervan et al. suggested a biorefinery model for the generation of various products such as ethanol, butanol, and succinic acid.151 The primary aim of this study is to analyse the cost of a complete biorefinery and propose an optimized production scheme that will provide maximum commercial output with minimum investment. Liu et al. designed an integrated industrial approach for the generation of the minimum amount of waste. This study proposed a scheme where wastewater from a forest site consisting of suspended wood chunks was used as feedstock for the production of cellulosic ethanol in a biorefinery facility.152 Thus, it can be concluded that the economic sustainability, feedstock availability and treatment together with ‘zero-waste’ generation is the current focus of researchers for the establishment of a full-scale biorefinery.
4.1 Zero-waste biorefineries
The prime objective of biorefineries needs to be clean and green energy making use of the mostly ‘zero waste’ production approach, where the by-products are value-added substances. The ‘zero waste’ approach is based on the recycling, reducing, and reusing concept that applies to waste generated from a production process.153Fig. 8 schematically presents the concept of a zero-waste biorefinery. Here, the focus is on the utilization of biomass for producing useful products. Further, the use of by-products for the preparation of value-added products is another goal of these biorefineries. Thus, this aids in the mitigation of hazardous wastes, and also significantly reduces the emission of environmental pollutants. This can further diversify the use of biomass to generate the maximum output from a single biorefinery, and therefore more advantageous than conventional approaches.
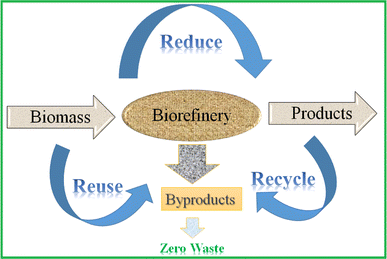 |
| Fig. 8 Concept of a zero-waste biorefinery. | |
Recently, the use of zero-waste biorefineries for the production of various valuable products has been reported in the literature.154–156 Thus, utilizing biobased leftovers (waste) and processing them further in biorefineries to yield ethanol with zero-waste generation to promote economic and green fuel production is the current interest of researchers. One of the popular methods in recent times to achieve this economic conversion is by using the consolidated bioprocessing (CBP) approach.157 The key benefit of this integrated process is to select one or more microorganisms that can collectively perform multiple functions in a single operation, thereby significantly reducing the total cost of the process, and also promoting the ‘zero waste’ policy for the production of bioethanol.158 Carrillo-Nieves et al. developed a CBP strategy, where second-generation lignocellulosic materials such as brewer's spent grain, orange peel, and wheat bran obtained as agricultural waste were evaluated for zero-waste bioethanol production that can be incorporated in biorefineries.159 This study used the Mexican native microorganism white-rot fungus Trametes hirsuta CS5, which served as an effective lignin degrader, avoiding the pre-treatment step. Mishra and Mohanty inspected the possibility of domestic sewage wastewater as a ‘zero waste’ and economic feedstock that can be integrated in biorefineries.160 This study reported that eight indigenous microalgal strains exhibited better growth in raw domestic sewage wastewater, as the wastewater is enriched with optimal nutrients for microalgal cultivation. Among them, Monoraphidium sp. KMC4 provided a superior source of biomass feedstock for bioethanol and other biogas and bio-oil production. Chatterjee and Mohan reported the concept of a circular biorefinery, where sugarcane bagasse is used as a raw material for the production of bio-hydrogen and bioethanol.161 After carrying out the initial pre-treatment and dark fermentation process to collect the bio-hydrogen, the unhydrolyzed sugarcane bagasse was exposed to simultaneous saccharification and fermentation for the production of bioethanol. This study utilized the acidogenic effluent obtained from the bio-hydrogen process as an organic fertilizer for chickpea cultivation, thus making the whole process ‘zero waste’ discharge bioenergy production. The above discussion elaborates the feasibility, sustainability and, cost-efficiency of a ‘zero waste’ biorefinery. In another approach, the utilization of microalgal biomass is presented for designing a ‘zero waste’ biorefinery’.4 The advantages and disadvantages of using microalgae as biorefinery feed were well depicted in this report. The production of bioethanol and its blending with MS for sustainable transport fuel can promote the commissioning of biorefineries around the world. However, another major factor that needs to be monitored critically is the environmental concern associated with ethanol-blended MS.
5. Cost efficiency of bioethanol production
Bioethanol blending in MS faces several issues including cost efficiency. Therefore, it is pertinent to investigate the various domains associated with bioethanol production cost and blending. NITI Aayog, Ministry of Petroleum and Natural Gas, Govt. of India published a ‘Roadmap for Ethanol Blending in India 2020–2025’ in 2021, in which the cost analysis of ethanol production is described in detail.162 The conversion cost of bioethanol using different raw materials is presented in Table 5.
Table 5 Cost of feedstock and ethanol production (data taken from the Roadmap for Ethanol Blending in India 2020–2025)
Feedstock |
Cost/MT of the feedstock (rs) |
Quantity of ethanol per MT of feedstock |
Ex-mill ethanol price (rs per litre) |
Sugarcane juice/sugar/sugar syrup |
2850 (price of sugarcane at 10% sugar recovery) |
70 litre per ton of sugarcane |
62.65 |
B molasses |
13 500 |
300 litre |
57.61 |
C molasses |
7123 |
225 litre |
45.69 |
Damaged food grains (broken rice#) |
16 000 |
400 litre |
51.55 |
Rice available with FCI (food Corporation of India) |
20 000 |
450 litre |
56.87 |
Maize |
15 000 |
380 litre |
51.55 |
Any new initiative made for the betterment of society and environment needs the initial investment of ideas, manpower and money. This is also applicable to the newly conceived concept of blended fuels. Firstly, the production of biofuels requires a dedicated set-up. Secondly, the efficiency of conversion of feedstock to biofuel/bioethanol is to be optimized for better yield. In comparison to crude oil exploration and petroleum refining, the process of biofuel production will be much cheaper in the near future. Further, at the present stage, blending of ethanol (5–20%) will not significantly increase the price of MS. However, this cost analysis depends on the time, market scenario, government policies and geographical location of feedstock production.
6. Environmental aspects
Fossil fuels are generally responsible for the adverse environmental impacts caused by the emission of different toxic and greenhouse gases, together with particulate matters. The main components of automobile exhaust include carbon monoxide (CO), carbon dioxide (CO2), nitrogen and sulfur oxides (SOx and NOx), and unburnt hydrocarbons. It has been witnessed by many research groups that CO emission is restricted in ethanol-blended MS compared to pure MS.163 A decrease in the emission of CO (from 10% to 90%) through automobile exhaust was witnessed for 5–30% ethanol blending in MS. The higher blends further showed a higher reduction in CO emission. A 50% blend (E50) showed about 53% decrease in the emission of CO. However, ethanol blends beyond 70% resulted in an increase in CO emission.164 Moreover, an increase in the percentage of ethanol in MS increased the emission of ground-level ozone and smog. Therefore, in view of environmental concerns, it is necessary to optimize the use of bioethanol in MS. Thangavelu et al. summarized that 10–60% ethanol blends can efficiently reduce the emission of CO from 15–80%.93 Further, hydrated ethanol contributes to the increase in CO emission through automobile exhaust.165 Contrary observations were reported for CO2 emission, which has been found to increase with an increment in ethanol blending in MS.109,111,164 This is attributed to the higher oxygen content of the blended fuel, which aids in the complete oxidation of the fuel carbon.166 The increase in the CO2 emission may be also due to the higher latent heat of vaporization of ethanol.110 Ethanol beyond 20% is still a matter of debate in terms of CO2 emission. However, some reports revealed that ethanol blending can reduce the emission of CO2, especially in the case of hydrated ethanol. Some recent literature reported that NOx emission can be restricted by blending ethanol in MS.167 Again, some research groups witnessed an increase in the emission of NOx after blending.168,169 However, it has been repeatedly observed that hydrated ethanol can reduce the emission of NOx to a considerable extent.170 Another vital pollutant emitted from automobile exhaust is unburnt hydrocarbons. Due to different reasons such as inadequate combustion temperature and weak flame, some of the fuel hydrocarbons leave the combustion chamber without burning. The unburnt hydrocarbon decreases the engine efficacy, creates wastage of fuel, and most importantly emits environmental pollutants. Thus, it is crucial to regulate or restrict the emission of hydrocarbons in the environment. Ethanol-blended MS significantly decreased the emission of these hydrocarbons. Up to 12% reduction in the emission of unburnt hydrocarbons was observed upon blending 25–100% ethanol in MS.163 The above discussion presented the effect of ethanol blending on the emission of environmental pollutants. Most of the reports highlight the fact that ethanol, especially bioethanol can significantly contribute to this. A higher amount of bioethanol blending can restrict the emission of most of the environmental pollutants. However, the feasibility and sustainability of blending a higher amount of ethanol need to be studied thoroughly.
7. Disadvantages of bioethanol blending in MS
Despite its numerous merits, bioethanol has some genuine issues that have to be overcome for its successful blending in MS. Firstly, the feedstock of bioethanol still relies on crops having food value such as maize, corn, and sugarcane. This directly limits the huge production of bioethanol worldwide.68 However, the commercial production of bioethanol from 2G and 3G sources can address this issue to a significant extent. Secondly, the high water affinity of ethanol creates corrosion in motor engines. Therefore, a higher percentage of ethanol blending may require engine modification to tackle this problem.103 Further, the huge energy consumption in the distillation of ethanol after its fermentation is another disadvantage of bioethanol production.
8. Conclusions
In this review, we elaborately explain the need for alternative fuels and the efforts made globally to achieve this goal. MS, as the most widely used transportation fuel, has undergone research & development (R&D). Consequently, researchers have found that blending ethanol in MS can improve its performance in automobile engines. This also targets two major issues including gradual minimization in the use of fossil fuels, and also mitigation of emission of environmental pollutants. This has instigated further research in the domain of blended fuels. The different feedstock and production routes have been investigated thoroughly to produce ethanol on a large scale. Second-generation feedstock, mainly lignocellulosic biomass has attracted significant attention from the scientific fraternity because of its availability, cost effectiveness, no significant food value and environment friendliness. Further advancement of R&D works has shown the reliance on algae-based feedstock for the mass-scale production of bioethanol. The compatibility of bioethanol blended MS with spark ignition internal combustion engines was discussed herein. Most of the important engine features such as compression ratio, wheel power, combustion efficiency, engine torque, and brake thermal efficiency are significantly enhanced in the case of ethanol-blended MS compared to the pure MS. The research octane number (RON) of MS increases notably upon blending ethanol, which increases the overall performance of the engine. The present review also critically depicted the importance of the large-scale bioethanol production to achieve a sustainable future. In this context, the importance of ‘zero-waste’ biorefineries has been described. A present-day-picture of bioethanol–biorefineries around the world was also included briefly in the discussion. Finally, the environmental impact of ethanol-blended MS was analyzed in terms of the emission of CO2, CO, unburnt hydrocarbons and, NOx through automobile exhausts. Ethanol-blended MS has shown a significant reduction in the emission of these environmental pollutants. The overall description in this review presented a clear picture of bioethanol, its production processes, biorefineries with zero-waste generation capacity, and the environmental impact of ethanol-blended MS. According to this critical analysis, it is expected that bioethanol will shortly overcome the drawbacks associated with pure MS. Thus, bioethanol in its neat form or as a blend with MS will serve as a new generation, sustainable motor spirit in the coming future.
Declaration
It is declared that the manuscript has not been published or under consideration for publication elsewhere. The submission is approved by all authors and if accepted, it will not be published elsewhere including electronically in the same form, in English or in any other language, without the written consent of the copyright-holder. The manuscript has no direct or indirect conflict of interest with anyone.
References
- N. L. Panwar, S. C. Kaushik and S. Kothari, Role of renewable energy sources in environmental protection: A review, Renewable Sustainable Energy Rev., 2011, 15(3), 1513–1524 CrossRef.
- A. Arumugam, V. V. Malolan and V. &Ponnusami, Contemporary Pretreatment Strategies for Bioethanol Production from Corncobs: A Comprehensive Review, Waste Biomass Valorization, 2020, 1–36 Search PubMed.
- S. H. M. Azhar, R. Abdulla, S. A. Jambo, H. Marbawi, J. A. Gansau, A. A. M. Faik and K. F. Rodrigues, Yeasts in sustainable bioethanol production: A review, Biochem. Biophys. Rep., 2017, 10, 52–61 Search PubMed.
- R. C. Rajak, S. Jacob and B. S. Kim, A holistic zero waste biorefinery approach for macroalgal biomass utilization: A review, Sci. Total Environ., 2020, 716, 137067 CrossRef CAS PubMed.
- H. B. Aditiya, T. M. I. Mahlia, W. T. Chong, H. Nur and A. H. &Sebayang, Second generation bioethanol production: A critical review, Renewable Sustainable Energy Rev., 2016, 66, 631–653 CrossRef CAS.
-
BP: Statistical Review of World Energy, Workbook (Xlsx), London, 2016 Search PubMed.
-
US Energy Information Administration, International Energy Outlook, 2017 Search PubMed.
- M. Balat, Production of bioethanol from lignocellulosic materials via the biochemical pathway: a review, Energy Convers. Manage., 2011, 52(2), 858–875 CrossRef CAS.
- S. Gold, Bio-energy supply chains and stakeholders, Mitigation and Adaptation Strategies for Global Change, 2011, 16(4), 439–462 CrossRef.
-
Global Bioenergy Statistics 2019 World Bioenergy Association, https://www.worldbioenergy.org/uploads/191129WBAGBS2019_HQ.pdf Search PubMed.
- P. McKendry, Energy production from biomass (part 1): overview of biomass, Bioresour. Technol., 2002, 83(1), 37–46 CrossRef CAS PubMed.
- R. Lemus and R. Lal, Bioenergy crops and carbon sequestration, Crit. Rev. Plant Sci., 2005, 24(1), 1–21 CrossRef CAS.
-
W. T. Coyle, The Future of Biofuels: a Global Perspective, 2007, pp. 24–29 Search PubMed.
- P. Fairley, Introduction: Next generation biofuels, Nature, 2011, 474(7352), S2–S5 CrossRef CAS PubMed.
- G. Sorda, M. Banse and C. Kemfert, An overview of biofuel policies across the world, Energy Policy, 2010, 38(11), 6977–6988 CrossRef.
- A. P. Saravanan, T. Mathimani, G. Deviram, K. Rajendran and A. Pugazhendhi, Biofuel policy in India: a review of policy barriers in sustainable marketing of biofuel, J. Cleaner Prod., 2018, 193, 734–747 CrossRef.
- M. Ertas and M. H. Alma, Slow pyrolysis of chinaberry (Melia azedarach L.) seeds: Part I. The influence of pyrolysis parameters on the product yields, Energy Educ. Sci. Technol., Part A, 2011, 26(2), 143–154 CAS.
-
M. J. De Kam, R. V. Morey and D. G. Tiffany, Biomass integrated gasification combined cycle for heat and power at ethanol plants, in 2008 Providence, Rhode Island, June 29–July 2, American Society of Agricultural and Biological Engineers, 2008, p. 1 Search PubMed.
- Z. Liu and F. S. Zhang, Effects of various solvents on the liquefaction of biomass to produce fuels and chemical feedstocks, Energy Convers. Manage., 2008, 49(12), 3498–3504 CrossRef CAS.
- S. K. Mohanty, S. Behera, M. R. Swain and R. C. Ray, Bioethanol production from mahula (Madhuca latifolia L.) flowers by solid-state fermentation, Appl. Energy, 2009, 86(5), 640–644 CrossRef CAS.
- H. Uthman and A. &Jimoh, The production and characterization of ethanol fuel from agricultural products as an alternative fuel for gasoline, Energy Sources, Part A, 2012, 34(22), 2041–2047 CrossRef CAS.
- A. Almodares and M. R. &Hadi, Production of bioethanol from sweet sorghum: A review, Afr. J. Agric. Res., 2009, 4(9), 772–780 Search PubMed.
- M. O. Dias, A. V. Ensinas, S. A. Nebra, R. Maciel Filho, C. E. Rossell and M. R. W. &Maciel, Production of bioethanol and other bio-based materials from sugarcane bagasse: integration to conventional
bioethanol production process, Chem. Eng. Res. Des., 2009, 87(9), 1206–1216 CrossRef CAS.
- R. Lal, Crop residues as soil amendments and feedstock for bioethanolproduction, Waste Manage., 2008, 28(4), 747–758 CrossRef CAS PubMed.
-
M. Galbe and G. Zacchi, Pretreatment of lignocellulosic materials for efficient bioethanol production, in Biofuels, Springer, Berlin, Heidelberg, 2007, pp. 41–65 Search PubMed.
- F. Talebnia, D. Karakashev and I. Angelidaki, Production of bioethanol from wheat straw: an overview on pretreatment, hydrolysis and fermentation, Bioresour. Technol., 2010, 101(13), 4744–4753 CrossRef CAS PubMed.
- J. J. Ko, S. L. Yun, S. W. Kang and S. K. Kim, A review on thermochemical pretreatment in lignocellulosic bioethanol production, J. Korea Org. Resour. Recycl. Assoc., 2008, 16(1), 79–88 Search PubMed.
- V. Hönig, M. Orsák, M. Pexa and Z. &Linhart, The distillation characteristics of automotive gasoline containing biobutanol, bioethanol and the influence of the oxygenates, Agron. Res., 2015, 13(2), 558–567 Search PubMed.
- S. H. Park, S. H. Yoon and C. S. Lee, Bioethanol and gasoline premixing effect on combustion and emission characteristics in biodiesel dual-fuel combustion engine, Appl. Energy, 2014, 135, 286–298 CrossRef CAS.
-
R. Ilves, A. Küüt and J. Olt, Ethanol as Internal Combustion Engine Fuel, in Ethanol, Elsevier, 2019, pp. 215–229 Search PubMed.
- Z. Xu, X. Duan, Y. Liu, B. Deng and J. Liu, Spray combustion and soot formation characteristics of the acetone-butanol-ethanol/diesel blends under diesel engine-relevant conditions, Fuel, 2020, 280, 118483 CrossRef CAS.
- İ. Örs, Experimental investigation of the cetane improver and bioethanol addition for the use of waste cooking oil biodiesel as an alternative fuel in diesel engines, J. Braz. Soc. Mech. Sci. Eng., 2020, 42(4), 1–14 Search PubMed.
- S. R. Jhang, Y. C. Lin, K. S. Chen, S. L. Lin and S. Batterman, Evaluation of fuel consumption, pollutant emissions and well-to-wheel GHGs assessment from a vehicle operation fueled with bioethanol, gasoline and hydrogen, Energy, 2020, 209, 118436 CrossRef CAS.
-
A. Paul, S. Ghosh, S. Konar and A. Ray, Biorefinery: A Future Key of Potential Energy, Biorefinery Production Technologies for Chemicals and Energy, 2020, p. 77 Search PubMed.
- G. De Bhowmick, A. K. Sarmah and R. Sen, Zero-waste algal biorefinery for bioenergy and biochar: a green leap towards achieving energy and environmental sustainability, Sci. Total Environ., 2019, 650, 2467–2482 CrossRef CAS PubMed.
- R. Ciriminna, R. Delisi, L. Albanese, F. Meneguzzo and M. Pagliaro, Opuntia ficus-indica seed oil: Biorefinery and bioeconomy aspects, Eur. J. Lipid Sci. Technol., 2017, 119(8), 1700013 CrossRef.
- S. Verhelst, J. W. Turner, L. Sileghem and J. &Vancoillie, Methanol as a fuel for internal combustion engines, Prog. Energy Combust. Sci., 2019, 70, 43–88 CrossRef.
- Y. Qian, J. Guo, Y. Zhang, W. Tao and X. Lu, Combustion and emission behavior of N-propanol as partially alternative fuel in a direct injection spark ignition engine, Appl. Thermal Eng., 2018, 144, 126–136 CrossRef CAS.
- W. R. da Silva Trindade and R. G. dos Santos, Review on the characteristics of butanol, its production and use as fuel in internal combustion engines, Renewable Sustainable Energy Rev., 2017, 69, 642–651 CrossRef.
-
C. S. Wibowo, B. Sugiarto, A. Zikra, A. Budi and T. Mulya, The Effect of Gasoline-Bioethanol Blends to The Value of Fuel's Octane Number, in E3S Web of Conferences, EDP Sciences, 2018, vol. 67, p. 02033 Search PubMed.
-
A. Datta, A. Hossain and S. Roy, An Overview on Biofuels and Their Advantages and Disadvantages, 2019 Search PubMed.
- M. Balat, H. Balat and O. Z. Cahide, Progress in bioethanol processing, Prog. Energy Combust. Sci., 2008, 34, 551–573 CrossRef CAS.
-
E. Bertrand, L. P. Vandenberghe, C. R. Soccol, J. C. Sigoillot and C. Faulds, First generation bioethanol, in Green Fuels Technology, Springer, Cham, 2016, pp. 175–212 Search PubMed.
- A. Gupta and J. P. Verma, Sustainable bio-ethanol production from agro-residues: a review, Renewable Sustainable Energy Rev., 2015, 41, 550–567 CrossRef CAS.
-
J. Laustsen, Energy efficiency requirements in building codes, energy efficiency policies for new buildings, IEA Information Paper, Support of the G8 Plan of Action, 2008 Search PubMed.
- J. D. Van den Wall Bake, M. Junginger, A. Faaij, T. Poot and A. Walter, Explaining the experience curve: Cost reductions of Brazilian ethanol from sugarcane, Biomass Bioenergy, 2009, 33(4), 644–658 CrossRef.
- P. Gallagher, G. Schamel, H. Shapouri and H. Brubaker, The international competitiveness of the US corn-ethanol industry: A comparison with sugar-ethanol processing in Brazil, Agribusiness, 2006, 22(1), 109–134 CrossRef.
- M. O. de Souza Dias, R. Maciel Filho, P. E. Mantelatto, O. Cavalett, C. E. V. Rossell, A. Bonomi and M. R. L. V. Leal, Sugarcane processing for ethanol and sugar in Brazil, Environ. Dev., 2015, 15, 35–51 CrossRef.
- O. Cavalett, T. L. Junqueira, M. O. Dias, C. D. Jesus, P. E. Mantelatto, M. P. Cunha, H. C. Franco, T. F. Cardoso, R. Maciel Filho, C. E. Rossell and A. Bonomi, Environmental and economic assessment of sugarcane first generation biorefineries in Brazil, Clean Technol. Environ. Policy, 2012, 14(3), 399–410 CrossRef CAS.
- M. L. G. Renó, O. A. del Olmo, J. C. E. Palacio, E. E. S. Lora and O. J. Venturini, Sugarcane biorefineries: Case studies applied to the Brazilian sugar–alcohol industry, Energy Convers. Manage., 2014, 86, 981–991 CrossRef.
- B. G. Ooi and K. R. Lankford, Strategy for adapting wine yeasts for bioethanol production, Int. J. Mol. Sci., 2009, 10(1), 385–394 CrossRef CAS PubMed.
- T. D'Amore, Cambridge prize lecture improving yeast fermentation performance, J. Inst. Brew., 1992, 98(5), 375–382 CrossRef.
- G. M. Walker and R. S. Walker, Enhancing yeast alcoholic fermentations, Adv. Appl. Microbiol., 2018, 105, 87–129 Search PubMed.
- M. Salazar-Ordóñez, P. P. Pérez-Hernández and J. M. Martín-Lozano, Sugar beet for bioethanol production: An approach based on environmental agricultural outputs, Energy Policy, 2013, 55, 662–668 CrossRef.
- D. F. Correa, H. L. Beyer, H. P. Possingham, S. R. Thomas-Hall and P. M. Schenk, Biodiversity impacts of bioenergy production: Microalgae vs. first generation biofuels, Renewable Sustainable Energy Rev., 2017, 74, 1131–1146 CrossRef.
-
S. Mohapatra, R. C. Ray and S. Ramachandran, Bioethanol from biorenewable feedstocks: technology, economics, and challenges, in Bioethanol Production from Food Crops, Academic Press, 2019, pp. 3–27 Search PubMed.
- B. V. Ayodele, M. A. Alsaffar and S. I. Mustapa, An overview of integration opportunities for sustainable bioethanol production from first-and second-generation sugar-based feedstocks, J. Cleaner Prod., 2020, 245, 118857 CrossRef.
-
S. K. Mohanty and M. R. Swain, Bioethanol production from corn and wheat: food, fuel, and future, in Bioethanol Production from Food Crops, Academic Press, 2019, pp. 45–59 Search PubMed.
- L. Mojović, S. Nikolić, M. Rakin and M. Vukasinović, Production of bioethanol from corn meal hydrolyzates, Fuel, 2006, 85(12–13), 1750–1755 CrossRef.
- A. M. Castro, L. R. Castilho and D. M. Freire, An overview on advances of amylases production and their use in the production of bioethanol by conventional and non-conventional processes, Biomass Convers. Biorefin., 2011, 1(4), 245–255 CrossRef CAS.
- A. H. Sebayang, H. H. Masjuki, H. C. Ong, S. Dharma, A. S. Silitonga, F. Kusumo and J. Milano, Optimization of bioethanol production from sorghum grains using artificial neural networks integrated with ant colony, Ind. Crops Prod., 2017, 97, 146–155 CrossRef CAS.
- F. A. Gonçalves, H. A. Ruiz, E. S. dos Santos, J. A. Teixeira and G. R. de Macedo, Bioethanol production by Saccharomyces cerevisiae, Pichia stipitis and Zymomonas mobilis from delignified coconut fibre mature and lignin extraction according to biorefinery concept, Renewable Energy, 2016, 94, 353–365 CrossRef.
- C. R. Fischer, D. Klein-Marcuschamer and G. Stephanopoulos, Selection and optimization of microbial hosts for biofuels production, Metab. Eng., 2008, 10(6), 295–304 CrossRef CAS PubMed.
- S. Dodić, S. Popov, J. Dodić, J. Ranković, Z. Zavargo and R. J. Mučibabić, Bioethanol production from thick juice as intermediate of sugar beet processing, Biomass Bioenergy, 2009, 33(5), 822–827 CrossRef.
- S. Niphadkar, P. Bagade and S. Ahmed, Bioethanol production: insight into past, present and future perspectives, Biofuels, 2018, 9(2), 229–238 CrossRef CAS.
- C. Hellwinckel, C. Clark, M. Langholtz and L. Eaton, Simulated impact of the renewable fuels standard on US Conservation Reserve Program enrollment and conversion, GCB Bioenergy, 2016, 8(1), 245–256 CrossRef.
- C. Manochio, B. R. Andrade, R. P. Rodriguez and B. S. Moraes, Ethanol from biomass: A comparative overview, Renewable Sustainable Energy Rev., 2017, 80, 743–755 CrossRef.
- M. C. Rulli, D. Bellomi, A. Cazzoli, G. De Carolis and P. D'Odorico, The water-land-food nexus of first-generation biofuels, Sci. Rep., 2016, 6(1), 1–10 CrossRef PubMed.
- G. Brodeur, E. Yau, K. Badal, J. Collier, K. B. Ramachandran and S. Ramakrishnan, Chemical and physicochemical pretreatment of lignocellulosic biomass: a review, Enzyme Res., 2011, 2011, 1–17 CrossRef PubMed.
- K. Robak and M. Balcerek, Review of second generation bioethanol production from residual biomass, Food Technol. Biotechnol., 2018, 56(2), 174–187 CAS.
- F. Peng, P. Peng, F. Xu and R. C. Sun, Fractional purification and bioconversion of hemicelluloses, Biotechnol. Adv., 2012, 30(4), 879–903 CrossRef CAS PubMed.
- A. J. Ragauskas, G. T. Beckham, M. J. Biddy, R. Chandra, F. Chen, M. F. Davis, B. H. Davison, R. A. Dixon, P. Gilna, M. Keller and P. Langan, Lignin valorization: improving lignin processing in the biorefinery, Science, 2014, 344(6185), 1246843 CrossRef PubMed.
- Q. Kang, L. Appels, T. Tan and R. Dewil, Bioethanol from lignocellulosic biomass: current findings determine research priorities, Sci. World J., 2014, 2014, 1–14 Search PubMed.
- S. H. Mood, A. H. Golfeshan, M. Tabatabaei, G. S. Jouzani, G. H. Najafi, M. Gholami and M. Ardjmand, Lignocellulosic biomass to bioethanol, a comprehensive review with a focus on pretreatment, Renewable Sustainable Energy Rev., 2013, 27, 77–93 CrossRef.
- A. Limayem and S. C. Ricke, Lignocellulosic biomass for bioethanol production: current perspectives, potential issues and future prospects, Prog. Energy Combust. Sci.ce, 2012, 38(4), 449–467 CrossRef CAS.
- S. Kuhar, L. M. Nair and R. C. Kuhad, Pretreatment of lignocellulosic material with fungi capable of higher lignin degradation and lower carbohydrate degradation improves substrate acid hydrolysis and the eventual conversion to ethanol, Can. J. Microbiol., 2008, 54(4), 305–313 CrossRef CAS PubMed.
- X. Gui, G. Wang, M. Hu and Y. Yan, Combined fungal and mild acid pretreatment of Glycyrrhiza uralensis residue for enhancing enzymatic hydrolysis and oil production, BioResources, 2013, 8(4), 5485–5499 CrossRef.
- G. T. Tang, S. S. Xing, R. B. Huang, X. Cao and Y. Guo, Determination of content of cellulose and hemicellulose in stem of Sesamum indicum L, Crop Res., 2012, 26(1), 53–55 Search PubMed.
- P. Kumar, V. Kumar, S. Kumar, J. Singh and P. Kumar, Bioethanol production from sesame (Sesamum indicum L.) plant residue by combined physical, microbial and chemical pretreatments, Bioresour. Technol., 2020, 297, 122484 CrossRef CAS PubMed.
- P. R. Lennartsson, P. Erlandsson and M. J. Taherzadeh, Integration of the first and second generation bioethanol processes and the importance of by-products, Bioresour. Technol., 2014, 165, 3–8 CrossRef CAS PubMed.
- M. Y. Menetrez, An overview of algae biofuel production and potential environmental impact, Environ. Sci. Technol., 2012, 46(13), 7073–7085 CrossRef CAS PubMed.
- A. Singh, P. S. Nigam and J. D. Murphy, Mechanism and challenges in commercialisation of algal biofuels, Bioresour. Technol., 2011, 102(1), 26–34 CrossRef CAS PubMed.
- J. Singh and S. Gu, Commercialization potential of microalgae for biofuels production, Renewable Sustainable Energy Rev., 2010, 14(9), 2596–2610 CrossRef CAS.
- S. H. Ho, X. Ye, T. Hasunuma, J. S. Chang and A. Kondo, Perspectives on engineering strategies for improving biofuel production from microalgae—a critical review, Biotechnol. Adv., 2014, 32(8), 1448–1459 CrossRef CAS PubMed.
- J. Marimuthu, P. Essakimuthu, J. Narayanan, B. Anantham, R. J. J. M. Tharmaraj and S. Arumugam, Phytochemical characterization of brown seaweed Sargassum wightii, Asian Pac. J. Trop. Dis., 2012, 2, S109–S113 CrossRef CAS.
- S. A. Jambo, R. Abdulla, S. H. M. Azhar, H. Marbawi, J. A. Gansau and P. Ravindra, A review on third generation bioethanol feedstock, Renewable Sustainable Energy Rev., 2016, 65, 756–769 CrossRef CAS.
- J. A. V. Costa and M. G. De Morais, The role of biochemical engineering in the production of biofuels from microalgae, Bioresour. Technol., 2011, 102(1), 2–9 CrossRef CAS PubMed.
- J. Vera, J. Castro, A. Gonzalez and A. Moenne, Seaweed polysaccharides and derived oligosaccharides stimulate defense responses and protection against pathogens in plants, Mar. Drugs, 2011, 9(12), 2514–2525 CrossRef CAS PubMed.
- T. S. El-Tayeb, A. A. Abdelhafez, S. H. Ali and E. M. Ramadan, Effect of acid hydrolysis and fungal biotreatment on agro-industrial wastes for obtainment of free sugars for bioethanol production, Braz. J. Microbiol., 2012, 43(4), 1523–1535 CrossRef CAS PubMed.
- P. Binod, E. Gnansounou, R. Sindhu and A. Pandey, Enzymes for second generation biofuels: recent developments and future perspectives, Bioresour. Technol. Rep., 2019, 5, 317–325 CrossRef.
- Z. Shokravi, H. Shokravi, M. A. Aziz and H. Shokravi, The fourth-generation biofuel: a systematic review on nearly two decades of research from 2008 to 2019, Fossil Free Fuels, 2019, 213–251 Search PubMed.
- J. Lü, C. Sheahan and P. Fu, Metabolic engineering of algae for fourth generation biofuels production, Energy Environ. Sci., 2011, 4(7), 2451–2466 RSC.
-
History of Technology: Internal Combustion engines, Encyclopædia Britannica, retrieved 2012-03-20, http://www.britannica.com Search PubMed.
-
M. Noga, Five-stroke Internal Combustion Engine-yesterday, today and tomorrow, in IOP Conference Series: Materials Science and Engineering, IOP Publishing, 2018, vol. 421, supp. 4, p. 042058 Search PubMed.
- S. K. Thangavelu, A. S. Ahmed and F. N. Ani, Review on bioethanol as alternative fuel for spark ignition engines, Renewable Sustainable Energy Rev., 2016, 56, 820–835 CrossRef CAS.
- G. T. Kalghatgi, Developments in internal combustion engines and implications for combustion science and future transport fuels, Proc. Combust. Inst., 2015, 35(1), 101–115 CrossRef CAS.
- H. Hao, F. Liu, Z. Liu and F. Zhao, Compression ignition of low-octane gasoline: Life cycle energy consumption and greenhouse gas emissions, Appl. Energy, 2016, 181, 391–398 CrossRef CAS.
- A. J. Harrison, Enthalpy requirement-a new fundamentally based gasoline volatility parameter for predicting cold weather driveability, SAE Trans., 1988, 1021–1029 Search PubMed.
- D. Petitjean, L. Bernardini, C. Middlemass and S. M. Shahed, Advanced gasoline engine turbocharging technology for fuel economy improvements, 2004-01-0988, SAE [Tech. Pap.], 2004 Search PubMed.
- A. Demirbas, Bioalcohols as alternatives to gasoline, Energy Sources, Part A, 2009, 31(12), 1056–1062 CrossRef CAS.
-
I. E. A. Etsap and T. Brief, Ethanol Internal Combustion Engines, Technology Brief T06, 2010, pp. 1–6 Search PubMed.
- H. Jafari, M. H. Idris, A. Ourdjini, H. Rahimi and B. Ghobadian, EIS study of corrosion behavior of metallic materials in ethanol blended gasoline containing water as a contaminant, Fuel, 2011, 90(3), 1181–1187 CrossRef CAS.
- M. B. Giroldo, E. Werninghaus, E. Coelho and W. Makant, Development of 1.6 l flex fuel engine for Brazilian market (No. 2005-01-4130), SAE [Tech. Pap.], 2005 Search PubMed.
- M. Delavarrafiee and H. C. Frey, Real-world fuel use and gaseous emission rates for flex fuel vehicles operated on E85 versus gasoline, J. Air Waste Manage. Assoc., 2018, 68(3), 235–254 CrossRef CAS PubMed.
- A. Elfasakhany, Gasoline engine fueled with bioethanol-bio-acetone-gasoline blends: Performance and emissions exploration, Fuel, 2020, 274, 117825 CrossRef CAS.
- J. E. Anderson, U. Kramer, S. A. Mueller and T. J. Wallington, Octane numbers of ethanol− and methanol− gasoline blends estimated from molar concentrations, Energy Fuels, 2010, 24(12), 6576–6585 CrossRef CAS.
- J. W. G. Turner, R. J. Pearson, B. Holland and R. Peck, Alcohol-based fuels in high performance engines, SAE Trans., 2007, 55–69 Search PubMed.
- H. Bayraktar, Experimental and theoretical investigation of using gasoline–ethanol blends in spark-ignition engines, Renewable Energy, 2005, 30(11), 1733–1747 CrossRef CAS.
- A. N. Ozsezen and M. Canakci, Performance and combustion characteristics of alcohol–gasoline blends at wide-open throttle, Energy, 2011, 36(5), 2747–2752 CrossRef CAS.
- P. Chansauria and R. K. Mandloi, Effects of ethanol blends on performance of spark ignition engine-a review, Mater. Today: Proc., 2018, 5(2), 4066–4077 CAS.
- M. Al-Hasan, Effect of ethanol–unleaded gasoline blends on engine performance and exhaust emission, Energy Convers. Manage., 2003, 44(9), 1547–1561 CrossRef CAS.
- H. S. Yücesu, T. Topgül, C. Cinar and M. Okur, Effect of ethanol–gasoline blends on engine performance and exhaust emissions in different compression ratios, Appl. Therm. Eng., 2006, 26(17–18), 2272–2278 CrossRef.
- T. Topgül, H. S. Yücesu, C. Cinar and A. Koca, The effects of ethanol–unleaded gasoline blends and ignition timing on engine performance and exhaust emissions, Renewable Energy, 2006, 31(15), 2534–2542 CrossRef.
- A. Ganguly, P. K. Chatterjee and A. Dey, Studies on ethanol production from water hyacinth-A review, Renewable Sustainable Energy Rev., 2012, 16(1), 966–972 CrossRef CAS.
- R. A. Stein, J. E. Anderson and T. J. Wallington, An overview of the effects of ethanol-gasoline blends on SI engine performance, fuel efficiency, and emissions, SAE Int. J. Engines, 2013, 6(1), 470–487 CrossRef.
- B. C. Saha, N. N. Nichols and M. A. Cotta, Ethanol production from wheat straw by recombinant Escherichia coli strain FBR5 at high solid loading, Bioresour. Technol., 2011, 102(23), 10892–10897 CrossRef CAS PubMed.
- S. Prasad, A. Singh, N. Jain and H. C. Joshi, Ethanol production from sweet sorghum syrup for utilization as automotive fuel in India, Energy Fuels, 2007, 21(4), 2415–2420 CrossRef CAS.
- R. C. Costa and J. R. Sodré, Compression ratio effects on an ethanol/gasoline fuelled engine performance, Appl. Therm. Eng., 2011, 31(2–3), 278–283 CrossRef CAS.
- M. Canakci, A. N. Ozsezen, E. Alptekin and M. Eyidogan, Impact of alcohol–gasoline fuel blends on the exhaust emission of an SI engine, Renewable Energy, 2013, 52, 111–117 CrossRef CAS.
- M. K. Mohammed, H. H. Balla, Z. M. H. Al-Dulaimi, Z. S. Kareem and M. S. Al-Zuhairy, Effect of ethanol-gasoline blends on SI engine performance and emissions, Case Studies in Thermal Engineering, 2021, 25, 100891 CrossRef.
- M. Koç, Y. Sekmen, T. Topgül and H. S. Yücesu, The effects of ethanol–unleaded gasoline blends on engine performance and exhaust emissions in a spark-ignition engine, Renewable energy, 2009, 34(10), 2101–2106 CrossRef.
- J. E. Anderson, D. M. DiCicco, J. M. Ginder, U. Kramer, T. G. Leone, H. E. Raney-Pablo and T. J. Wallington, High octane number ethanol–gasoline blends: Quantifying the potential benefits in the United States, Fuel, 2012, 97, 585–594 CrossRef CAS.
- S. H. Yoon, S. Y. Ha, H. G. Roh and C. S. Lee, Effect of bioethanol as an alternative fuel on the emissions reduction characteristics and combustion stability in a spark ignition engine, Proc. Inst. Mech. Eng., Part D, 2009, 223(7), 941–951 CrossRef.
- M. K. D. Kiani, B. Ghobadian, T. Tavakoli, A. M. Nikbakht and G. Najafi, Application of artificial neural networks for the prediction of performance and exhaust emissions in SI engine using ethanol-gasoline blends, Energy, 2010, 35(1), 65–69 CrossRef.
- J. H. Clark and F. E. Deswarte, The biorefinery concept—an integrated approach, Introd. Chem. Biomass, 2008, 1, 1–20 Search PubMed.
-
K. Biernat and P. L. Grzelak, Biorefinery systems as an element of sustainable development, Biofuels–status and Perspective, 2015 Search PubMed.
-
Biorefineries-industrial Processes and Products (No. 1), ed. Kamm, B., Gruber, P. R. and Kamm, M., Wiley-VCH, Weinheim, 2006 Search PubMed.
- J. J. Bozell and G. R. Petersen, Technology development for the production of biobased products from biorefinery carbohydrates—the US Department of Energy's “Top 10” revisited, Green Chem., 2010, 12(4), 539–554 RSC.
-
I. E. A. Bioenergy, Task 42 Biorefinery, Bio Based Chemicals Value Added Products from Biorefineries, 2009 Search PubMed.
- B. Khoshnevisan, N. Duan, P. Tsapekos, M. K. Awasthi, Z. Liu, A. Mohammadi, I. Angelidaki, D. C. Tsang, Z. Zhang, J. Pan and H. Liu, A critical review on livestock manure biorefinery technologies: Sustainability, challenges, and future perspectives, Renewable Sustainable Energy Rev., 2021, 135, 110033 CrossRef.
- I. S. Tan, M. K. Lam, H. C. Y. Foo, S. Lim and K. T. Lee, Advances of macroalgae biomass for the third generation of bioethanol production, Chin. J. Chem. Eng., 2020, 28(2), 502–517 CrossRef CAS.
- G. De Bhowmick, A. K. Sarmah and R. Sen, Lignocellulosic biorefinery as a model for sustainable development of biofuels and value added products, Bioresour. Technol., 2018, 247, 1144–1154 CrossRef CAS PubMed.
- G. Rødsrud, M. Lersch and A. Sjöde, History and future of world's most advanced biorefinery in operation, Biomass Bioenergy, 2012, 46, 46–59 CrossRef.
-
C. N. Bloyd, An Update on Ethanol Production and Utilization in Thailand (No. PNNL-19060), Pacific Northwest National Lab. (PNNL), Richland, WA (United States), 2009 Search PubMed.
-
Technology Status and Reliability of the Value Chains: 2018 Update 28 December, ed. I. Landälv, L. Waldheim and K. Maniatis, 2018 Search PubMed.
-
F. Gírio, S. Marques, F. Pinto, A. C. Oliveira, P. Costa, A. Reis and P. Moura, Biorefineries in the World, in Biorefineries, Springer, Cham, 2017, pp. 227–281 Search PubMed.
-
Renewable Fuels Association, https://ethanolrfa.org/biorefinery-locations/.
- K. Özdenkçi, C. De Blasio, H. R. Muddassar, K. Melin, P. Oinas, J. Koskinen and M. Järvinen, A novel biorefinery integration concept for lignocellulosic biomass, Energy Convers. Manage., 2017, 149, 974–987 CrossRef.
- P. Tanger, J. L. Field, C. E. Jahn, M. W. DeFoort and J. E. Leach, Biomass for thermochemical conversion: targets and challenges, Front. Plant Sci., 2013, 4, 218 Search PubMed.
- T. D. Foust, A. Aden, A. Dutta and S. Phillips, An economic and environmental comparison of a biochemical and a thermochemical lignocellulosic ethanol conversion processes, Cellulose, 2009, 16(4), 547–565 CrossRef CAS.
-
P. L. Spath and D. C. Dayton, Preliminary Screening-Ttechnical and Economic Assessment of Synthesis Gas to Fuels and Chemicals with Emphasis on the Potential for Biomass-Derived Syngas, 2003 Search PubMed.
- S. Czernik and A. V. Bridgwater, Overview of applications of biomass fast pyrolysis oil, Energy Fuels, 2004, 18(2), 590–598 CrossRef CAS.
-
Fundamentals of Thermochemical Biomass Conversion, ed. Overend, R. P., Milne, T. and Mudge, L., Springer Science & Business Media, 2012 Search PubMed.
-
F. K. Kazi, J. Fortman, R. Anex, G. Kothandaraman, D. Hsu, A. Aden and A. Dutta, Techno-economic Analysis of Biochemical Scenarios for Production of Cellulosic Ethanol (No. NREL/TP-6A2-46588), National Renewable Energy Lab. (NREL), Golden, CO (United States), 2010 Search PubMed.
- H. M. Zabed, S. Akter, J. Yun, G. Zhang, F. N. Awad, X. Qi and J. N. Sahu, Recent advances in biological pretreatment of microalgae and lignocellulosic biomass for biofuel production, Renewable Sustainable Energy Rev., 2019, 105, 105–128 CrossRef CAS.
- X. Yan, Z. Wang, K. Zhang, M. Si, M. Liu, L. Chai and Y. Shi, Bacteria-enhanced dilute acid pretreatment of lignocellulosic biomass, Bioresour. Technol., 2017, 245, 419–425 CrossRef CAS PubMed.
- D. Klein-Marcuschamer, B. A. Simmons and H. W. Blanch, Techno-economic analysis of a lignocellulosic ethanol biorefinery with ionic liquid pre-treatment, Biofuels, Bioprod. Biorefin., 2011, 5(5), 562–569 CrossRef CAS.
- R. Parajuli, T. Dalgaard, U. Jørgensen, A. P. S. Adamsen, M. T. Knudsen, M. Birkved and J. K. Schjørring, Biorefining in the prevailing energy and materials crisis: a review of sustainable pathways for biorefinery value chains and sustainability assessment methodologies, Renewable Sustainable Energy Rev., 2015, 43, 244–263 CrossRef CAS.
- A. Requejo, S. Peleteiro, A. Rodríguez, G. Garrote and J. C. Parajó, Second-generation bioethanol from residual woody biomass, Energy Fuels, 2011, 25(10), 4803–4810 CrossRef CAS.
- J. Larragoiti-Kuri, M. Rivera-Toledo, J. Cocho-Roldán, K. Maldonado-Ruiz Esparza, S. Le Borgne and L. Pedraza-Segura, Convenient product distribution for a lignocellulosic biorefinery: optimization through sustainable indexes, Ind. Eng. Chem. Res., 2017, 56(40), 11388–11397 CrossRef CAS.
- E. Zondervan, M. Nawaz, A. B. de Haan, J. M. Woodley and R. Gani, Optimal design of a multi-product biorefinery system, Comput. Chem. Eng., 2011, 35(9), 1752–1766 CrossRef CAS.
- J. Liu and D. R. Shonnard, Life cycle carbon footprint of ethanol and potassium acetate produced from a forest product wastewater stream by a co-located biorefinery, ACS Sustainable Chem. Eng., 2014, 2(8), 1951–1958 CrossRef CAS.
- S. Mishra, M. Roy and K. Mohanty, Microalgal bioenergy production under zero-waste biorefinery approach: recent advances and future perspectives, Bioresour. Technol., 2019, 292, 122008 CrossRef CAS PubMed.
- A. Mhatre, S. Gore, A. Mhatre, N. Trivedi, M. Sharma, R. Pandit and A. Lali, Effect of multiple product extractions on bio-methane potential of marine macrophytic green alga Ulva lactuca, Renewable Energy, 2019, 132, 742–751 CrossRef CAS.
- M. Zollmann, A. Robin, M. Prabhu, M. Polikovsky, A. Gillis, S. Greiserman and A. Golberg, Green technology in green macroalgal biorefineries, Phycologia, 2019, 58(5), 516–534 CrossRef.
- Y. I. Mandik, B. Cheirsilp, S. Srinuanpan, W. Maneechote, P. Boonsawang, P. Prasertsan and S. Sirisansaneeyakul, Zero-waste biorefinery of oleaginous microalgae as promising sources of biofuels and biochemicals through direct transesterification and acid hydrolysis, Process Biochem., 2020, 95, 214–222 CrossRef CAS.
- S. Brethauer and M. H. Studer, Consolidated bioprocessing of lignocellulose by a microbial consortium, Energy Environ. Sci., 2014, 7(4), 1446–1453 RSC.
- A. Amore and V. Faraco, Potential of fungi as category I Consolidated BioProcessing organisms for cellulosic ethanol production, Renewable Sustainable Energy Rev., 2012, 16(5), 3286–3301 CrossRef CAS.
- D. Carrillo-Nieves, S. Saldarriaga-Hernandez, G. Gutiérrez-Soto, M. Rostro-Alanis, C. Hernández-Luna, A. J. Alvarez and R. Parra-Saldívar, Biotransformation of agro-industrial waste to produce lignocellulolytic enzymes and bioethanol with a zero waste, Biomass Convers. Biorefin., 2020, 1–12 Search PubMed.
- S. Mishra and K. Mohanty, Comprehensive characterization of microalgal isolates and lipid-extracted biomass as zero-waste bioenergy feedstock: an integrated bioremediation and biorefinery approach, Bioresour. Technol., 2019, 273, 177–184 CrossRef CAS PubMed.
- S. Chatterjee and S. V. Mohan, Simultaneous Production of Green Hydrogen and Bioethanol from Segregated Sugarcane Bagasse Hydrolysate Streams with Circular Biorefinery Design, Chem. Eng. J., 2021, 130386 CrossRef CAS.
-
Roadmap for Ethanol Blending in India 2020-25, https://www.niti.gov.in/sites/default/files/202106/EthanolBlendingInIndia_compressed.pdf Search PubMed.
- M. B. Celik, Experimental determination of suitable ethanol–gasoline blend rate at high compression ratio for gasoline engine, Appl. Therm. Eng., 2008, 28(5–6), 396–404 CrossRef CAS.
- W. D. Hsieh, R. H. Chen, T. L. Wu and T. H. Lin, Engine performance and pollutant emission of an SI engine using ethanol–gasoline blended fuels, Atmos. Environ., 2002, 36(3), 403–410 CrossRef CAS.
- I. D. L. G. J. P. G. Schifter, L. Diaz, J. P. Gómez and U. Gonzalez, Combustion characterization in a single cylinder engine with mid-level hydrated ethanol–gasoline blended fuels, Fuel, 2013, 103, 292–298 CrossRef CAS.
- A. Elfasakhany, Investigations on the effects of ethanol–methanol–gasoline blends in a spark-ignition engine: performance and emissions analysis, Eng. Sci. Technol., 2015, 18(4), 713–719 Search PubMed.
- S. H. Yoon and C. S. Lee, Effect of undiluted bioethanol on combustion and emissions reduction in a SI engine at various charge air conditions, Fuel, 2012, 97, 887–890 CrossRef CAS.
- C. Liang, C. Ji, B. Gao, X. Liu and Y. Zhu, Investigation on the performance of a spark-ignited ethanol engine with DME enrichment, Energy Convers. Manage., 2012, 58, 19–25 CrossRef CAS.
- D. H. Qi and C. F. Lee, Combustion and emissions behaviour for ethanol–gasoline-blended fuels in a multipoint electronic fuel injection engine, Int. J. Sustainable Green Energy, 2016, 35(4), 323–338 CrossRef.
- G. Najafi, B. Ghobadian, T. Tavakoli, D. R. Buttsworth, T. F. Yusaf and M. J. A. E. Faizollahnejad, Performance and exhaust emissions of a gasoline engine with ethanol blended gasoline fuels using artificial neural network, Appl. Energy, 2009, 86(5), 630–639 CrossRef CAS.
|
This journal is © The Royal Society of Chemistry 2023 |
Click here to see how this site uses Cookies. View our privacy policy here.