Mechanocatalytic partial depolymerization of lignocellulosic feedstock towards oligomeric glycans†
Received
29th January 2023
, Accepted 9th March 2023
First published on 13th March 2023
Abstract
The depolymerization of lignocellulosic feedstock with a heterogeneous composition is a major challenge and usually leads to the formation of monosaccharides as the main products. Our work aims to convert such feedstocks into oligomeric glycans which are more valuable products compared to sugars, by using mechanocatalysis in a planetary ball mill as an effective conversion route. Herein, we utilized raw materials such as wheat straw, beet pulp, cocoa shells and apple pomace as residual natural raw materials from food and feed production. Reaction parameters such as rotational speed, acid content and milling duration were investigated and optimized towards a maximum amount of soluble species and a minimum of monosaccharides. The optimization of cellulose as a substrate resulted in a nearly fully soluble fraction containing oligomeric glycans. Based on these results the reaction parameters were transferred and further optimized for lignocellulosic feedstock. For wheat straw a solubility of over 90% was achieved comprising a mixture of oligomeric glycans as well as partially depolymerized lignin.
1. Introduction
In the last few decades mechanochemistry has advanced quickly and has been acknowledged as one of the top ten emerging technologies in chemistry.1 One field of mechanochemistry is mechanocatalysis where a suitable catalyst for a reaction is added to reactants. For these reactions many different reactor types such as vibration mills, mortar mills and rotary mills can be used.2 In terms of green chemistry, this approach has the advantage that they are usually solvent-free while there are also approaches with solvents, the so-called liquid assisted grinding (LAG).3 Mechanochemistry is probably most known for processing inorganic materials such as alloys and intermetallic phases. Typical examples are the synthesis of oxides, nitrides and halides where long reaction times of up to several days are required.4 Besides the synthesis of inorganic materials there are also increasing numbers of mechanocatalytic organic synthesis e.g. Knoevenagel-condensations and polymerizations of insoluble polymers whereby the synthesis of thermoplastics is not favored due to the released heat during the process.2,5,6 In some cases, this typical solvent-free approach enables activation only due to mechanical forces, e.g. breaking the rigid structure of cellulose and lignocellulosic structures,7 thereby rendering this method highly attractive for the processing of lignocellulosic residues as reported previously.8–11 In contrast to the polymerization of specific polymers the depolymerization of lignocellulosic feedstocks and cellulose as readily available renewable feedstocks is of great interest.11–14 Cellulose and lignocellulosic feedstocks are commonly insoluble and therefore difficult to process.15 It is known that by mechanocatalytic processing of cellulosic biomass with a strong acid a soluble product mixture consisting of glycans (glucans and xylans), as well as partially depolymerized lignin is obtained.16,17 This is an advantage compared to classic wood saccharification since more valuable glycans instead of monomeric sugars can be formed. Furthermore, it was shown that glucose itself can oligomerize during mechanocatalysis, which means that complete depolymerization to monomeric sugars is not possible (Fig. 1).18
 |
| Fig. 1 Mechanocatalytic partial depolymerization of cellulose to oligomeric glycans without formation of monomeric sugars. | |
It should be emphasized that the energy required for a reaction can be reduced by scaling up which makes this method even more attractive.19 For successful depolymerization of the biomass a strong acid with a pKa below −1.8 such as hydrochloric or sulfuric acid is needed.18 The approach we investigated is based on sulfuric acid as a catalyst and a planetary ball mill. Hereby we aimed to obtain oligomeric glycans with a defined molecular weight of 1–10 kDa, which are precipitated in a second step followed by functionalization. These defined functionalized oligomeric glycans can be used in the packaging industry as hardeners in coating resins as well as in printing resins.20
2. Experimental
2.1 Materials
The biomasses for mechanocatalytic partial depolymerization were α-cellulose (Sigma-Aldrich, C8002-1KG), wheat straw (Louven-shop, 02063), cocoa shells (August Storck KG, GlyChem Kakaoschalen 2004_0151), beet pulp (Südzucker AG, 201817542) and apple pomace (Herbstreith & Fox GmbH & Co. KG Pektin Fabriken, Herbavital F12 2011_0530). For impregnation sulfuric acid (Roth, 4623.5) and diethyl-ether (Sigma-Aldrich, 24004-2.5L-M) were used while for precipitation ethanol (Höfer Chemie GmbH, Y2-M753-XKN0) was used.
2.2 Composition analysis of lignocellulosic feedstock
For composition analysis we refer to the regulations of the National Renewable Energy Laboratory. Within these regulations total solids,30 extractives,31 ash,32 structural carbohydrates and lignin33 were analyzed (see the ESI†).
2.3 Biomass impregnation
Before impregnation with sulfuric acid the lignocellulosic feedstock was shredded to a fine powder in a coffee grinder. For impregnation the required amount of 96% sulfuric acid was weighed in a 500 mL round bottom flask and diluted with about 50 mL diethyl ether respectively ethanol per 5 g biomass. Here, the acid content is given in % based on the total mass including the acid load itself. After adding the biomass the resulting suspension was stirred for 1 h at room temperature. The solvent was then removed under reduced pressure and the product was dried on a Schlenk line.
2.4 Mechanocatalytic partial depolymerization
For the experiments a planetary ball mill Retsch PM 100 was used. 5 g of the respective sample was placed into the grinding vessel followed by 163.48 g zirconia balls with a diameter of 3 mm. Mechanocatalytic partial depolymerization was analogously carried out in a Fritsch Pulverisette 6 with 144.15 g zirconia balls with a diameter of 10 mm. Due to heat development during the grinding process a program with a milling duration of 5 min at 500 rpm followed by a cooling cycle of 2 min was chosen. For clarity, only the effective milling duration without the cooling cycles is given. To show that mechanocatalytic partial depolymerization is a reproducible method for polysaccharide digestion towards oligomeric glycans, three identical experiments with apple pomace pre-extracted with hot water were carried out and compared with each other.
2.5 Product characterization after partial depolymerization
Directly after the milling process the temperature inside the grinding vessel is measured to confirm that the temperature is below 90 °C and no Maillard reaction as well as no following reactions such as dehydration of sugars to furfural and hydroxymethylfurfural occurs.34 In a first experiment without acid impregnation the influence of ball milling on the crystallinity of cellulose was determined by milling for 86 min followed by an XRD-measurement to verify the amorphization while milling. Therefore a Bruker D2 Phaser 2nd generation was used with a wavelength of Cu Kα = 1.5406 Å. The measurements were taken in a 2-theta range from 8° to 60° with a measurement speed of 0.239°·(1.1 s)−1 using a background-free silicon sample holder. After mechanocatalytic partial depolymerization an amount of product equal to a mass of 400 mg without acid load was weighed in and stirred with 40 g demineralized water at room temperature respectively 100 °C (Fraunhofer IWKS). Afterwards the insoluble fraction was filtered off, dried under vacuum at 40 °C overnight and weighed in again to determine the mass of the insoluble fraction. The filtrate was analyzed by HPLC (Agilent 1260 Infinity equipped with a HPX-87H-column at a flow rate of 0.5 mL min−1 at 60 °C). Additionally precipitation and purification were performed as reported by Wolf et al.20 GPC-measurements of the samples after milling were performed to determine the molecular weight distribution of the soluble fraction. For samples with cellulose as the substrate a PSS Suprema column at a flow rate of 1 mL min−1 0.05% NaN3 at 25 °C was used. The lignocellulosic samples were measured with a MCX 1000A column with a mixture of 0.1 mol L−1 NaOH and 0.1 mol L−1 NaCl at the same flow rate. At Fraunhofer IWKS SEC-MALS was performed using an Agilent 1260 Infinity II HPLC system combined with an Optilab and Dawn 8 detector (both from Wyatt Technology Europe GmbH) A PSS Suprema column with a flow rate of 0.8 mL min−1 100 mM NaNO3/0.05% NaN3 at 30 °C was used.
3. Results and discussion
3.1 Influence on crystallinity
Initially, an experiment with pure cellulose was carried out to verify the expected amorphization of cellulose after milling in a planetary ball mill. The resulting XRD-pattern (Fig. S1†) was obtained where the observed reflexes of untreated cellulose are in agreement with the ones from the literature.21 Based on the XRD-pattern after milling we could show that the amorphization was successful in the absence of depolymerization.
3.2 Cellulose as the substrate
The experiments carried out were run with milling cycles of five minutes milling followed by two minutes cooling so that temperatures of 90 °C were not exceeded to prevent subsequent reactions. Possible subsequent products starting from monomeric sugars which were formed in small amounts could be furfural and hydroxymethylfurfural.22,23 First insights into the effect of sulfuric acid as a catalyst were acquired through experiments with effective milling durations of 86 min and different acid contents. The acid content was varied between 0% and 9.48% as shown in Fig. 2.
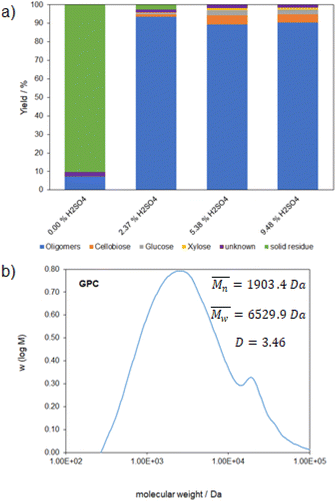 |
| Fig. 2 (a) Composition of the product mixture after mechanocatalytic partial depolymerization with different acid contents; reaction conditions: 500 rpm, 86 min effective milling duration, 5 g substrate and 163.48 g zirconia balls. (b) Molecular weight distribution from GPC-measurement of the experiment with 2.37% sulfuric acid. | |
The figure shows that the acid content has a large impact on the oligomer fraction. Without catalyst the amount of desired oligomers is below 10% which increases to above 90% by adding 2.37% sulfuric acid. What we also noticed is that a higher acid content reduces the oligomer fraction. This trend can be attributed to the higher catalyst content which brings about an even higher reaction rate and therefore a higher degree of depolymerization towards the sugar components. The desired 1–10 kDa glycans defined during this work can be used as the starting material for coating resins.20 To verify the desired molecular weight range the GPC measurement of the sample partially depolymerized with 2.37% sulfuric acid is shown (Fig. 2b).
The GPC measurement exhibits a broad molecular weight distribution with a maximum in the range of the desired molecular weight of 1–10 kDa. Based on this result we wanted to transfer the reaction parameters to the lignocellulosic feedstock.
3.3 Composition of lignocellulosic feedstock
Since every lignocellulosic feedstock has its own composition regarding the contents of water, extractives, ash, carbohydrates and lignin it is necessary to determine the composition of all used feedstocks which are shown in Fig. 3.
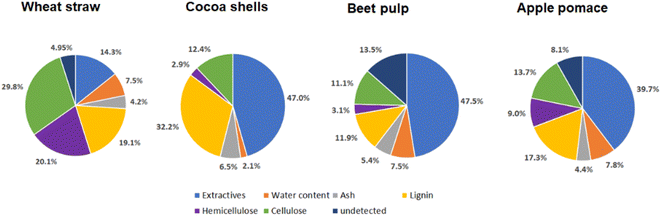 |
| Fig. 3 Composition of used wheat straw, cocoa shells, beet pulp and apple pomace analyzed according to NREL regulations. | |
The composition of the lignocellulosic feedstock is completely heterogeneous. The largest amount of the natural raw material, with the exception of wheat straw, consists of extractives such as non-structural low molecular weight saccharides and carboxylic acids. Valuable glycans will be obtained from cellulose and hemicellulose. Hereby wheat straw has the highest content of cellulose and hemicellulose with 30% and 20% respectively which make up 50% of the raw material. This amount is lower in the other natural raw materials with 23% for apple pomace, 15% for cocoa shells and 14% for beet pulp. On the other hand, the lignin content is highest in the cocoa shells with 32%, while it ranges between 12% and 19% in the other natural raw materials used. The structure of the biomass has a decisive influence on the mechanocatalytic partial depolymerization. Strong binding of the polysaccharides to the lignin matrix prevents depolymerization. Since cocoa shells have the highest lignin content and a low content of hemicellulose and cellulose we expect that the mechanocatalytic partial depolymerization under the same conditions will be more hindered than for wheat straw since it has the highest content of hemicellulose as well as cellulose.
3.4 Lignocellulosic feedstock as the substrate
This section discusses the results of using wheat straw, cocoa shells, apple pomace and beet pulp as lignocellulosic feedstock. Since the composition is more complex, as shown in the previous section, the following results are shown as soluble products and solid residues without further separation of the soluble products.
3.4.1 Wheat straw.
In an experiment with 3.6% acid content and a similar milling duration as for cellulose a lower soluble fraction was achieved compared to impregnated cellulose (Fig. 4a, second bar). This experiment showed that the milling duration has to be increased for the lignocellulosic feedstock, which is probably due to the lignin content that hardens the structure. The results after increasing the milling duration as well as varying the acid content are shown in Fig. 4a.
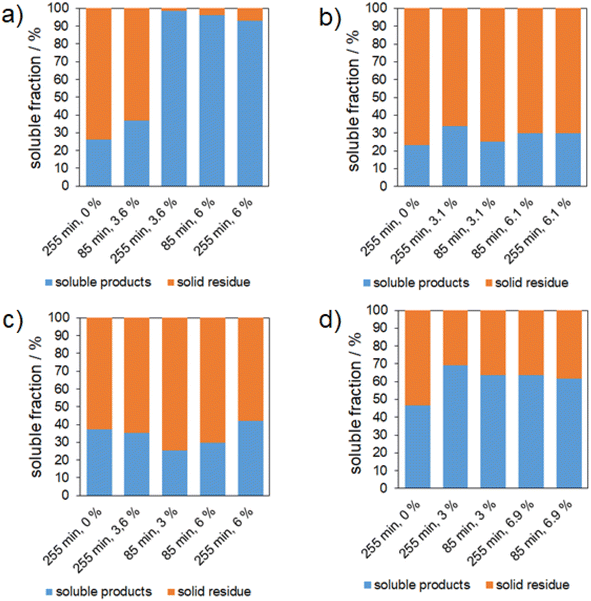 |
| Fig. 4 Amount of soluble products for (a) wheat straw, (b) cocoa shells, (c) apple pomace and (d) beet pulp dependent on the acid content and the milling duration. Reaction conditions: 500 rpm, 5 g substrate and 166.163.48 g zirconia balls. | |
Without acid a soluble fraction of around 25% is obtained. Hereby we have to keep in mind that wheat straw has 14.3% extractives which are included in the soluble products. This leads to an uptake of the soluble fraction of around 10% which is in the same range as for cellulose alone. For higher milling durations of 255 min and acid contents of 3.6 and 6%, a soluble fraction above 90% is achieved. Hereby, sufficient energy was supplied to the system to break the rigid structure and then depolymerize it.
3.4.2 Cocoa shells.
The reactions with cocoa shells were carried out in the same way as those with wheat straw (Fig. 4b).
For cocoa shells a 7–8% increase in the soluble fraction could be obtained. Compared to wheat straw this increase seems quite small. This small increase can be attributed to a high lignin content of 32.2% as well as a low carbohydrate content of 15.3% where the structure is very rigid. This is consistent with the expectation of a more hindered reaction for this natural raw material. In sum the energy input for depolymerization in this system is not sufficient.
3.4.3 Apple pomace.
As with the previous lignocellulosic feedstock, the reactions with apple pomace were carried out under the same reaction conditions (Fig. 4c).
It should be noted that the experiment series with apple pomace showed no trend of increasing soluble fraction for the reaction conditions of the first four bars in Fig. 4c. A possible reason could be non-structural inhibitors in the substrate which are blocking the acid content and the rigid structure where the energy input is not sufficient in the same way as for wheat straw. The hypothesis of non-structural substances which hinder the reaction fits with wheat straw where a relatively low content of extractives results in a nearly full soluble fraction. The experiment which increased the soluble fraction by 5% compared to the conditions without a catalyst was the one with the harshest reaction conditions of 255 min milling duration and 6% acid content.
3.4.4 Beet pulp.
The reactions with beet pulp were carried out under the same conditions as those for the previous substrates (Fig. 4d).
Beet pulp shows an increase in the soluble fraction from 45% without a catalyst up to around 65% which can be increased neither with a higher milling duration nor a higher acid content. The relatively high soluble fraction without acid can be explained by the high contents of extractives in water which are of course also soluble after the mechanical treatment.
3.5 Influence of pre-extraction
Cocoa shells and beet pulp also show an increase in soluble products while apple pomace seems to follow no clear trend. When comparing the composition of all lignocellulosic feedstocks we noticed that wheat straw has the lowest amount of extractives with 14.3% while the other substrates contain 39–47%. Since wheat straw showed the highest amount of soluble products after mechanocatalysis the influence of the extractives on the reaction is investigated under the assumption that extractives may hinder a successful reaction to soluble products due to blocking some acid amount and because soluble non-structural glycans are favored to depolymerize. Therefore, pre-extractions based on NREL regulations were carried out with beet pulp and apple pomace. Afterwards the processes were continued with 170 min milling duration and an acid content of 6%. The results are shown in Fig. 5.
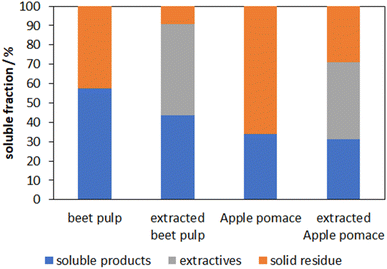 |
| Fig. 5 Amount of solid residue with and without pre-extraction of beet pulp and apple pomace with 6% acid content and 170 min milling duration. | |
Combining the extractives with the soluble products leads in total to a higher soluble fraction than for the non-extracted substrates. Considering that the extractives make up 39% and 47% for apple pomace and beet pulp respectively, a huge increase of up to 40% of the desired soluble glycan-containing product fraction can be seen. Also a lower content of solid residue for beet pulp compared to apple pomace was observed which can probably be explained by the lower lignin content. As mentioned previously, the obtained molecular weight distribution of the soluble product fraction is of interest and is therefore shown in Fig. 6 for the soluble glycan-containing fraction of the non-extracted as well as the pre-extracted apple pomace.
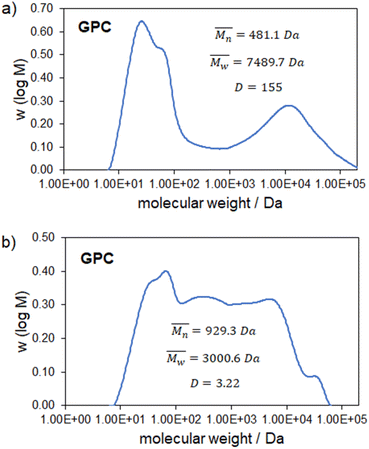 |
| Fig. 6 Molecular weight distribution from GPC-measurement of the experiment with (a) non-extracted apple pomace and (b) pre-extracted apple pomace. Reaction conditions: 6% acid content, 170 min milling duration, 500 rpm, 5 g substrate and 166.48 g zirconia balls. | |
The non-extracted apple pomace shows a bimodal molecular weight distribution in two non-favored regions below 1 kDa and above 10 kDa that supports the hypothesis that soluble non-structural glycans are favored to depolymerize while the structurally larger ones depolymerize afterwards. In contrast the pre-extracted apple pomace shows a broad molecular weight distribution in the favorable region. This circumstance can be attributed to the pre-extraction where low molecular weight compounds such as sugars and already soluble glycans are extracted from the sample and therefore the partial depolymerization of the macromolecules is less hindered. Since the mechanocatalytic partial depolymerization is statistical a broad molecular weight distribution was expected.
3.6 Reproducibility
The reactions were carried out with a milling duration of 170 min and an acid content of 6%. In Fig. 7 three overlaid HPLC-chromatograms of the soluble products that show identical cognition are shown as well as the amount of soluble products.
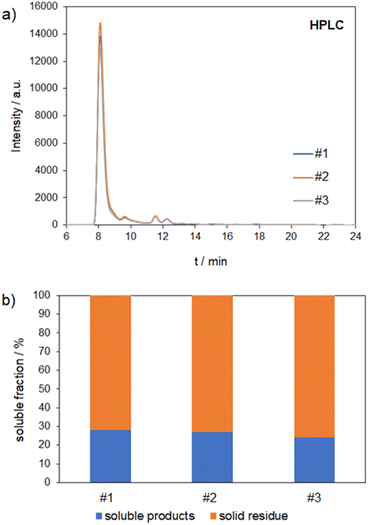 |
| Fig. 7 (a) Amount of soluble products and (b) HPLC-chromatograms for three experiments of pre-extracted apple pomace. Reaction conditions: 6% acid content, 170 min milling duration, 500 rpm, 5 g substrate and 166.48 g zirconia balls. | |
The results are in good agreement with each other and lead to a soluble product fraction of (26.5 ± 1.9)%. These reproducibility experiments show that mechanocatalytic partial depolymerization is a reliable and robust method.
3.7 Process application with extracted apple pomace
The extraction process of apple pomace at a pilot plant scale to yield about 5% glycans (purity ≥ 90%) has been established by using subcritical water.20 After extraction approx. 70% of insoluble apple pomace residue is recovered after removing the excess water by oven drying (80 °C). Apple pomace residue has been prepared as described and processed in a similar planetary ball mill. The purpose of adding mechanocatalytic partial depolymerization to the process chain was to increase the yield of glycans. Therefore, the milled apple pomace was extracted under atmospheric pressure in either hot or cold water.
The milling process was investigated by six independent experiments, each in triplicate, whose operating parameters are listed in Table 1.
Table 1 Experimental parameters for processing 5 g pre-extracted apple pomace at different milling durations and with acid contents in a planetary mill using a zirconia vessel and 144.15 g zirconia balls. The yields are based on the precipitated solid glycan product
Milling duration/min |
Acid content/wt% |
Yield/% |
84 |
0 |
1.1 |
170 |
0 |
1.6 |
84 |
1.5 |
1.6 |
170 |
1.5 |
2.0 |
84 |
3 |
1.3 |
170 |
3 |
1.9 |
Pre-extracted apple pomace has been milled into fine powder and impregnated with varying acid contents using 100% ethanol as solvent. Processing in the planetary mill was followed by cold water extraction and precipitation using 70% ethanol to obtain extracted hemicellulose. In comparison a longer milling duration has always had a higher impact on the yield than the acid content.
The different fractions (solid, soluble and precipitated glycans) shown in Fig. 8 show a good reproducibility of the process. The solid fraction was determined gravimetrically while the soluble fraction was the remaining amount left after subtracting the solid and glycan fractions. In both approaches, cold and hot water extractions, a total soluble fraction of 30 ± 1.5% and a precipitable glycan fraction of about 5 ± 0.5% could be achieved. To increase the precipitable amount of glycans two changes in the precipitation process can be considered. The first is increasing the ethanol concentration in combination with decreasing the precipitation temperature. It has been reported that these parameters influence the precipitation behavior. Short chained and small branched polysaccharides will be precipitated as well.24 The second approach would be the intermediate ultrafiltration step as described recently.20,25,26 With this process a concentrated raw glycan solution is achieved lowering the potential volume for polysaccharide to solubilize.
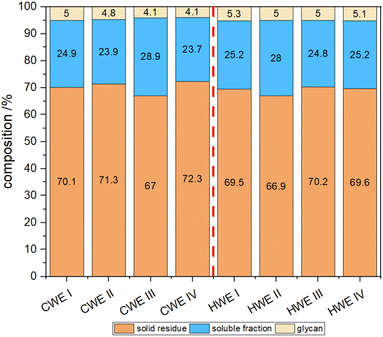 |
| Fig. 8 Composition of different fractions obtained by cold and hot water extraction (CWE/HWE) of milled apple pomace. Reaction conditions: 500 rpm, 170 min milling duration, 5 g substrate, 6% acid content and 144.15 g zirconia balls. | |
Fig. 9 shows the precipitated glycans from both extractions. While the glycans from cold water extraction are almost pure white, the hot water glycans show a brownish colour. Also, a different morphology could be observed.
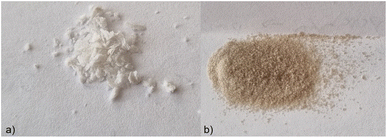 |
| Fig. 9 Samples of precipitated glycans from (a) cold water and (b) hot water extraction. | |
Due to earlier experiments the brownish color is known for impure products in our process. A purity analysis using the phenol sulfuric acid assay20,27 resulted in 62.4% (hot water glycan) and 86.5% (cold water glycan). Considering the cold water glycans 86.5% of the 52.1 mg precipitated crude product can be assigned to glycans which leads to a yield increase of 4.5%. In addition to the 5% glycans already obtained we achieved a yield increase of 90%. Furthermore, the molecular weight distribution of the precipitated glycans is analyzed. Therefore, a SEC-MALS measurement was carried out. The resulting chromatograms are shown in Fig. 10.
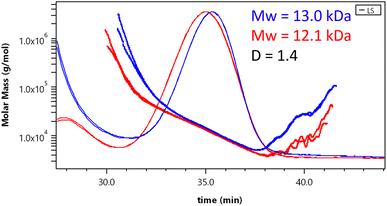 |
| Fig. 10 Molecular weight distribution from SEC-MALS measurement of cold (blue) and hot (red) water extracted glycans. | |
Molecular weights of 13.0 kDa (cold water glycans) and 12.1 kDa (hot water glycans) with a polydispersity of approx. 1.4 were measured. The increasing molar mass curve indicates anchoring effects between the branched macromolecule and the stationary phase.28 The effect of anchoring was considered during data processing and is in this case not decisive for the resulting Mw.
4. Conclusion
Mechanocatalytic partial depolymerization is proven to be a robust and reliable method for the depolymerization of cellulose and different lignocellulosic feedstocks towards glycans. Testing different acid contents of sulfuric acid as well as different milling durations led to a feasible partial depolymerization with an acid content of 6%. Milling durations were best at 85 min and 170 min depending on the composition of the feedstock. It could be shown that pretreatment by extraction increased the yield of the total soluble fraction to up to 40% and additionally led to a molecular weight distribution in the desired range of 1–10 kDa.29 In comparison to glycans from the hot water extraction process (pilot plant) the molecular weight of precipitated glycans was reduced to 1/3 and the polydispersity narrowed from 2.9 to 1.4. With this a molecular weight of 13.0 kDa (cold water glycans) and 12.1 kDa (hot water glycans) was achieved increasing the yield from 5% to nearly 10%. This makes the approach by mechanocatalytic partial depolymerization very promising for increasing yield and reaching the molecular weight range in one step. To further assess and improve the energy demand/product yield ratio a scale up of the process is planned. It could be shown that mechanocatalytic partial depolymerization is a robust and reproducible method to obtain lignocellulose-based glycans as sustainable biobased chemicals.
Conflicts of interest
The authors declare no conflict of interest.
Acknowledgements
We gratefully acknowledge the German Federal Ministry of Education and Research and the Projektträger Jülich for the financial support (FKZ: 031B0905B and 031B0905A) as well as Marion Trautmann from the working group of Prof. Biesalski for the GPC measurements.
References
- F. Gomollón-Bel, Chem. Int., 2019, 41, 12–17 Search PubMed.
-
W. Reschetilowski, Handbuch Chemische Reaktoren, SpringerSpektrum, Dresden, 2020 Search PubMed.
- D. Hasa, G. Schneider Rauber, D. Voinovich and W. Jones, Angew. Chem., 2015, 127, 7479–7483 CrossRef.
- H. Yang, X. Zhang, W. Ao and G. Qiu, Mater. Res. Bull., 2004, 39, 833–837 CrossRef CAS.
- W. Pickhardt, S. Grätz and L. Borchardt, Chem.–Eur. J., 2020, 26, 12903–12911 CrossRef CAS PubMed.
- S. Hwang, S. Grätz and L. Borchardt, Chem. Commun., 2022, 58, 1661–1671 RSC.
- Q. Liu, J. Tan, C. Cai, L. Ma and T. Wang, BioResources, 2016, 11, 1843–1854 CAS.
- T. Kleine, J. Buendia and C. Bolm, Green Chem., 2013, 15, 160–166 RSC.
- Q. Zhang and F. Jerome, ChemSusChem, 2013, 6, 2042–2044 CrossRef CAS PubMed.
- P. Dornath, H. J. Cho, A. Paulsen, P. Dauenhauer and W. Fan, Green Chem., 2015, 17, 769–775 RSC.
- R. Carrasquillo-Flores, M. Käldström, F. Schüth, J. A. Dumesic and R. Rinaldi, ACS Catal., 2013, 3, 993–997 CrossRef CAS.
- K. Thielemans, Y. De Bondt, S. Van den Bosch, A. Bautil, C. Roye, A. Deneyer, C. M. Courtin and B. F. Sels, Carbohydr. Polym., 2022, 119764 CrossRef CAS PubMed.
- L. Schneider, J. Haverinen, M. Jaakkola and U. Lassi, Chem. Eng. J., 2017, 327, 898–905 CrossRef CAS.
- K. S. Guiao, C. Tzoganakis and T. H. Mekonnen, Chemosphere, 2022, 293, 133647 CrossRef CAS PubMed.
- A. Pinkert, K. N. Marsh and S. Pang, Ind. Eng. Chem. Res., 2010, 49, 11121–11130 CrossRef CAS.
- M. Käldström, N. Meine, C. Farès, F. Schüth and R. Rinaldi, Green Chem., 2014, 16, 3528–3538 RSC.
- M. Käldström, N. Meine, C. Farès, R. Rinaldi and F. Schüth, Green Chem., 2014, 16, 2454–2462 RSC.
- N. Meine, R. Rinaldi and F. Schüth, ChemSusChem, 2012, 5, 1449–1454 CrossRef CAS PubMed.
- M. D. Kaufman Rechulski, M. Käldström, U. Richter, F. Schüth and R. Rinaldi, Ind. Eng. Chem. Res., 2015, 54, 4581–4592 CrossRef CAS.
- M. Wolf, F. Berger, S. Hanstein, A. Weidenkaff, H.-U. Endreß, A. M. Oestreich, M. Ebrahimi and P. Czermak, ACS Omega, 2022, 7, 13436–13447 CrossRef CAS PubMed.
- N. Terinte, R. Ibbett and K. C. Schuster, Lenzinger Ber., 2011, 89, 118–131 CAS.
- M. G. Davidson, S. Elgie, S. Parsons and T. J. Young, Green Chem., 2021, 23, 3154–3171 RSC.
- S. M. Hick, C. Griebel, D. T. Restrepo, J. H. Truitt, E. J. Buker, C. Bylda and R. G. Blair, Green Chem., 2010, 12, 468–474 RSC.
- S. Banerjee, A. F. Patti, V. Ranganathan and A. Arora, Food Bioprod. Process., 2019, 117, 38–50 CrossRef CAS.
- J. Bian, F. Peng, P. Peng, F. Xu and R.-C. Sun, Carbohydr. Res., 2010, 345, 802–809 CrossRef CAS PubMed.
- X. Hu and H. D. Goff, Trends Food Sci. Technol., 2018, 81, 108–115 CrossRef CAS.
- M. Dubois, K. A. Gilles, J. K. Hamilton, P. t. Rebers and F. Smith, Anal. Chem., 1956, 28, 350–356 CrossRef CAS.
-
S. Podzimek, Macromol. Symp., Wiley Online Library, 2019, vol. 384, p. 1800174 Search PubMed.
- V. Deloule, C. Boisset, D. Hannani, A. Suau, A. Le Gouellec, J. Chroboczek, C. Botté, Y. Yamaryo-Botté, C. Chirat and B. Toussaint, J. Funct. Foods, 2020, 64, 103688 CrossRef CAS.
-
B. H. A. Sluiter, D. Hyman, C. Payne, R. Ruiz, C. Scarlata, J. Sluiter, D. Templeton, and J. Wolfe, Determination of Total Solids in Biomass and Total Dissolved Solids in Liquid Process Samples, NREL, Colorado, 2008 Search PubMed.
-
R. R. A. Sluiter, C. Scarlata, J. Sluiter, and D. Templeton, Determination of Extractives in Biomass, NREL, Colorado, 2008 Search PubMed.
-
B. H. A. Sluiter, R. Ruiz, C. Scarlata, J. Sluiter, and D. Templeton, Determination of Ash in Biomass, NREL, 2008 Search PubMed.
-
B. H. A. Sluiter, R. Ruiz, C. Scarlata, J. Sluiter, D. Templeton and D. Crocker, Determination of Structural Carbohydrates and Lignin in Biomass, NREL, 2008 Search PubMed.
- S. I. Martins, W. M. Jongen and M. A. Van Boekel, Trends Food Sci. Technol., 2000, 11, 364–373 CrossRef CAS.
|
This journal is © The Royal Society of Chemistry 2023 |