A single-cell system of flow electrode capacitive mixing (F-CapMix) with a cross chamber for continuous energy production
Received
8th November 2022
, Accepted 30th November 2022
First published on 1st December 2022
Abstract
The generation of electricity from salinity difference energy between seawater and freshwater through a Capacitive Mixing (CapMix) system with solid electrodes was limited by intermittent energy production. In this study, a single-cell CapMix system using flow-electrode (F-CapMix) with a cross-chamber configuration was examined to produce electricity continuously from simulated seawater and freshwater. The effects of the flow-electrode electrolyte concentration, activated carbon loading, amounts of carbon black, and connected external resistance on the system performance were investigated. The results suggest that the system performance can be enhanced by increasing the activated carbon loading and carbon black amounts. Furthermore, to achieve the maximum power density of the system, the external resistance should be matched to the internal resistance. The maximum power density of the presented single-cell F-CapMix system was 74.3 mW m−2, which was comparable to those of previous CapMix and F-CapMix systems. In addition, this study also reveals that using only carbon black as the flow electrode is capable of producing electricity continuously for long-term operation. In summary, these results indicate the potential of F-CapMix and provide developing directions for further optimization.
1 Introduction
With continuous population growth and economic development, the global demand for accessible energy is growing. According to the BP Statistical Review of World Energy 2021, non-renewable energy sources, i.e., oil, natural gas, and coal, are the most used energy sources in world energy consumption, accounting for more than 80 percent.1 However, these non-renewable energy sources suffer from limited resources as well as environmental pollution from the production and transportation process.2 In contrast, renewable energy is regarded as a clean, sustainable, and affordable energy source.3 Based on these merits, the production and use of renewable energy have been strongly increasing in recent years. It has accounted for around 60% of the growth in global power generation from 2016 to 2020.1 Among the various renewable energy sources, salinity gradient energy (SGE) that utilizes the Gibbs free energy from the mixing of two solutions with different concentrations, i.e., seawater and freshwater, is an overlooked energy source but has great potential.4 Theoretically, around 0.81 kW h energy could be extracted from mixing 1 m3 of freshwater with the same amount of seawater, which is equivalent to the energy released from water falling over a dam of 270 m.5–7 It has been estimated that the practically extractable SGE around the world is about 625 TW h per year, which is equivalent to 3% of global electricity consumption.8
Given the tremendous potential of SGE worldwide, many technologies have been proposed and developed to harvest this sustainable energy source. To date, the leading methods of extracting SGE include pressure retarded osmosis (PRO),9 reverse electrodialysis (RED),10 and capacitive mixing (CapMix).11–13 PRO utilizes the osmotic pressure difference across a semipermeable membrane to drive the solution flow from the dilute water compartment to the concentrated water compartment. The expanding solution volume propels a hydroturbine to generate energy.6,9 In RED, the dilute water and the concentrated water alternatively flow through the compartments divided by a stack of cation and anion-exchange membranes, and the transportation of ions through the membranes leads to an electric current between the cathode and anode.2,10,14 In CapMix, the electrodes are periodically charging and discharging in the seawater and fresh water, resulting in a cyclically changing electric potential difference to transfer the chemical potential in the salinity difference to practical work.4,11–13 Among them, CapMix is the latest and is the focus of the present study.
In principle, three CapMix techniques have been proposed depending on the transportation pattern of ions into the electrodes from the bulk solution.15,16 The first one is capacitive energy extraction based on the capacitive double-layer expansion (CDLE), which is a membranes-free technology that utilizes an external power source to accomplish the energy extraction process.11 The second one is capacitive energy extraction based on the capacitive Donnan potential (CDP), in which the electrodes are covered by ion-exchange membranes (IEMs) that develop a Donnan potential to extract the SGE instead of using an external power source.12 The last one is a soft electrode (SE), in which the electrodes are coated with negatively or positively charged polyelectrolyte layers to generate a potential difference to harvest the SGE. No IEMs and external power sources are used in the SE.13 To date, many studies on CapMix have been conducted to enhance the system performance, including the development and modification of electrode materials;17–22 design and application of innovative cell configuration, i.e., using a wire geometry cell23 and stacking of cells;24 optimization of the operating parameters (e.g., temperature25,26 and the flow rate of the solution27); the combination of these techniques (e.g., CDP with CDLE,28 and CDLE with SE16) In addition to the extensive experimental studies, corresponding theoretical modeling studies were also performed to understand the process behavior.29–31 However, the use of solid electrodes in CapMix makes it produce energy in an intermittent way, i.e., the ions are first adsorbed into the electrodes by external power (e.g., voltage or current) or membrane potential until the electrodes are saturated with ions, and the adsorbed ions are then released from the electrodes. This discontinuous energy supply is insufficient to meet basic power requirements for practical applications.32,33
Recently, an innovative design using an activated carbon suspension as the electrode was introduced in the capacitive technique to overcome the finite ion storage capacity of solid electrodes.34 This flowable electrode's design was first applied in desalination (FCDI)34–36 and was then applied in the CapMix (F-CapMix) field for energy production.37,38 The research on F-CapMix is still at the initial stage, and limited studies have been reported so far.15,21,33,39,40 Theoretically, this F-CapMix technique is capable of producing energy continuously by unintermittently supplying fresh flow electrode (FE). However, this leads to a massive waste of activated carbon. For a practical F-CapMix system, the FE was recirculated within the system, and the activated carbon (AC) in the flow electrode (FE) slurry will be saturated without regeneration. It has been reported that the energy production and regeneration of the FE can be achieved simultaneously through a system with four cells connected in series.37 However, a system with extra cells will make the system more complex to operate. Therefore, designing a continuous system with only one cell performing energy production and FE regeneration at the same time is highly desirable. Recently, Liu et al.33 developed a single-cell system with a graphite brush and graphite plates (without caved channels) as current collectors to generate electricity continuously. While Liu et al.33 took the first step and developed a one-cell system suggesting that the system performance can be significantly enhanced by using a graphite brush as a current collector compared to flat graphite plates (without caved channels), for a large cell, the use of flat graphite plates (without caved channels) might lead to a great dead-zone of the FE due to the great viscosity of the FE. Here in this study, we use a more application-oriented method based on the utilization of graphite plates with caved channels as current collectors, which is now widely used in FCDI41,42 and F-CapMix systems,15,39 to produce electricity from salinity gradient energy. But using graphite plates with caved channels in a single cell F-CapMix system with a cross chamber design for continuous energy production, to the best of our knowledge, has not yet been detailed investigated.
It is generally believed that all techniques based on such a flowable electrode design depend heavily on the adsorption capacity of electrodes. Therefore, activated carbon (AC) with a high surface area is widely used in FCDI and F-CapMix systems.15,43,44 However, due to the poor electronic conductivity of AC suspension, the FE was made of a high AC loading or the mixture of AC with additional small amounts of conductive additives, such as carbon black (CB) with high conductivity, to elevate the electronic conductivity of the FE. And recently, it has been proved that using only carbon black with high conductivity and a low specific surface area as electrodes for desalination in FCDI can outperform microporous AC-based electrodes.45 To the best of our knowledge, there is low research on the F-CapMix system using only CB for extracting SGE, which will be addressed in the present study.
In the present study, we experimentally examined the feasibility of simultaneous energy extraction and regeneration of the FE in a single-cell F-CapMix system with a cross-chamber design. The system performance was investigated under different conditions, including the electrolyte concentration in the FE, carbon weight percentage or carbon loading, additional carbon black amounts, and external resistance. In addition, the performance of the F-CapMix system using CB solely as the electrodes was investigated.
2 Materials and methods
2.1 Materials
The sodium chloride (NaCl) used in the present study was analytical reagent grade and was purchased from Aladdin Industrial Co., Ltd. (Shanghai, China). The activated carbon used in the present study was YP-50F (Kuraray Chemical Company, Tokyo, Japan). Three different carbon black (CB) samples were applied as conductive additives and electrodes in this study: (1) CB (Ketjenblack ECP600JD, Lion Corporation, Tokyo, Japan), (2) CB2 (Ketjenblack ECP, Lion Corporation, Tokyo, Japan) and CB3 (DENKA acetylene black, Denka Company Limited, Tokyo, Japan). A synthetic 500 mM NaCl high concentration (HC) and a 20 mM NaCl low concentration (LC) water were used to simulate the seawater and freshwater, respectively.
2.2 Experimental setup and operation
The configuration of the F-CapMix cell used in this study is shown in Fig. 1. The F-CapMix cell was assembled with the following components: two acrylic-made plates (150 mm × 80 mm × 10 mm) as the supporting plates, two graphitic-made plates (150 mm × 80 mm × 7 mm) as the current collectors, two silicon gaskets (thickness: 0.5 mm) with hollow space (110 mm × 42 mm) as the flow channel of the feedwater (FW) of seawater and freshwater, two anion-exchange membranes (AEM, HMTECH—E18230, HUAMOTECH, China), and a cation-exchange membrane (CEM, HMTECH—E17270, HUAMOTECH, China) were placed on the joints between the silicon gaskets and graphitic plates. Each graphitic plate was engraved with flow channels (cross-section: 2 mm × 2 mm, length: 11 cm, and the number of paths: 11) on the surface for FE slurry flowing through. To ensure the uniform distribution of FW in the spacer, five nylon sheets (thickness: 0.1 mm and 100 mesh for each) were placed in the hollow part of the silicon gasket. All the components were fastened together with an M5 screw. The FE slurry and FW were pumped into the cell by two peristaltic pumps (L100-1S-1, Longer Precision Pump Co., Ltd., China). During the operation, the FE slurry was continuously recirculated in the cell, while the FW was pumped into the cell in a single-pass mode. The cell voltage of the F-CapMix system Vcell was recorded by using an electrochemical workstation (CS3104, Wuhan Corrtest Instrument Corp, China).
 |
| Fig. 1 Schematic of (a) the main components of an F-CapMix cell, (b) experimental setup, and (c) F-CapMix circuit. | |
There was no external power used in this system. The salinity gradient between the membrane generates an electrochemical potential that is known as the Nernst potential or the Donnan potential VD, as:
|  | (1) |
where
α is the permselectivity of the membrane,
z is the ion valence (
e.g.,
z = 1 for NaCl),
R is the gas constant (8.314 J (mol
−1 K
−1)),
T is the absolute temperature (298 K),
F is the Faraday constant (96
![[thin space (1/6-em)]](https://www.rsc.org/images/entities/char_2009.gif)
485 C mol
−1),
c is the mole concentration (mol m
−3), and the subscripts HC and LC represent water with high concentration and low concentration, respectively.
The sum of the Nernst potential across the membranes in a cell represents the membrane potential Vmem, which is also the cell's open circuit voltage.
To exploit the extracted salinity gradient energy from the CapMix system, it is necessary to connect the cell to a device, which was usually replaced by an external resistor in previous research.27,37,46 The performance of the system can be quantified by power density, which can be calculated from the cell voltage Vcell, external resistance Rext, and projection area of the membrane Am on the hollow part of the gasket (46.2 cm2 in the present study), as:
|  | (2) |
The overall performance is represented by the average power density of the experimental duration.
For an F-CapMix system, the cell is not ideally conductive but with some internal resistance that impedes the current in the circuit. In this way, an F-CapMix system can be represented as a power source Vmem that is in series with its internal resistance Rint and the external resistance Rext, as shown in Fig. 1c. The internal resistance Rint can be roughly calculated from the membrane potential Vmem, the value of external load Rext, and the cell voltage Vcell, as
|  | (3) |
In this study, a series of experiments were performed to evaluate the effects of different experimental parameters (contents of AC and CB, and external resistance value Rext) on the energy production of F-CapMix. The detailed experimental scheme is listed in Table 1. The FE slurry suspension was prepared by mixing different amounts of AC or CB materials with an 80 mL solution with different NaCl concentrations. The prepared FE slurry was continuously stirred overnight to wet AC/CB powders thoroughly. All experiments were conducted at room temperature (25 °C) in triplicate.
Table 1 Experimental scheme for the F-CapMix system in the present study
NaCl concentration (mM) |
Electrode content |
External resistance (Ω) |
140/260/380 |
5% AC |
5 |
260 |
2.5%/5%/7.5%/10% AC |
5 |
260 |
0.25% CB + 4.75% AC |
5 |
260 |
0.5% CB + 4.5% AC |
5 |
260 |
0.5% CB2 + 4.5% AC |
5 |
260 |
0.5% CB3 + 4.5% AC |
5 |
260 |
0.75% CB + 4.25% AC |
5 |
260 |
1.0% CB + 4.0% AC |
5 |
260 |
0.5%/1.0%/1.5% CB |
5 |
260 |
0.5%/1.0%/1.5% CB2 |
5 |
260 |
0.5%/1.0%/1.5% CB3 |
5 |
260 |
5% AC |
1/5/20/50/100 |
3 Results and discussion
3.1 Effect of FE concentration
The results obtained in a previous study using a four-cell F-CapMix revealed that the performance is dependent on the electrolyte concentration difference between FE and FW.37 In this study, the effect of FE concentration on the performance of the cross-chamber F-CapMix system was investigated at three FE concentrations: 140, 260, and 380 mM, while the external resistance was fixed at 5 Ω. As can be seen in Fig. 2a, three experimental cases gave similar OCV results, at ∼128 mV. After the circuit was connected with an external resistance, the cell voltage dropped from the OCV to a lower value (∼16 mV) and then remained stable during the period of 10 hours of experimental operation for the three experimental groups with different FE concentrations (Fig. 2b). These stable cell voltages resulted in a stable power density during the operation (Fig. 2c). In the triplicated experiments of 10 hours' operation, similar performance was found for different FE concentrations (Fig. 2d). The stable voltage and power densities during the process proved the feasibility of this two-chamber F-CapMix system, indicating that the movement of ions reaches dynamic equilibrium conditions, i.e., the number of ions transferred from FW into the FE on one side of the cell was equal to the number of ions released from the other side of the cell into FW. As a result, this system simultaneously realized the power production and regeneration of the FE within one cell unit, which is an improvement to the traditional F-CapMix system, whereas the regeneration of the FE requires an additional cell to accomplish.
 |
| Fig. 2 Plot of (a) the open circuit voltage, (b) the cell voltage, and (c) the power density during the experiments. (d) The average cell voltage and the average power density at different FE concentrations, and the error bars denote the standard deviation for the triplicate experiments. | |
Note that the similar OCVs of the present two-chamber F-CapMix system under the three different FE concentrations were not consistent with a prior reported F-CapMix system,37 in which the OCVs were dependent on the FE concentrations. The reason for the difference can be attributed to the different cell configurations. For the prior F-CapMix system, there is only one FW chamber in the cell, and the OCV was the sum of the Nernst potential across the two membranes (one AEM and one CEM) that can be calculated from eqn (1), as
. When the electrolyte concentration in the spacer cspacer was fixed (e.g., cspacer = HC or LC), different FE electrolyte concentrations led to different OCVs. Meanwhile for the present two-chamber F-CapMix system, the OCV was the sum of the Nernst potential across the three membranes (two AEMs and one CEM) that can be represented as
. As a result, the OCV of this two-chamber F-CapMix system was only dependent on the concentration difference between the HC and LC. And the identical OCVs also explain the similar performance of this two-chamber F-CapMix system under different NaCl concentrations (Fig. 2d). Since the performance of this two-chamber F-CapMix system is independent of the NaCl concentration, we only used one NaCl concentration (260 mM) to perform the subsequent experiments.
3.2 Effect of carbon loading on the system performance
The activated carbon (AC) in the FE plays an important role in conducting the electric charges and electrons in the F-CapMix system.47 For analyzing the relationship between the power production of the present cross-chamber F-CapMix system and carbon loading in FE, experiments were conducted at four different carbon loadings: 2.5, 5.0, 7.5, and 10 wt%. As shown in Fig. 3a, a relatively steady cell voltage Vcell was found for all the experimental cases, proving again that this F-CapMix successfully realized the energy production continuously for long-term operation. Meanwhile, Vcell was proportional to the carbon loading, increased by around 3-fold as the carbon loading increased from 2.5 to 10 wt%. The increased Vcell resulted in an enhanced power density P at a larger carbon loading as well (Fig. 3b). The power density increased from 5.5 to 46.1 mW m−2, when the carbon loading increased from 2.5 to 10 wt%. These power densities are comparable to the power densities obtained with solid electrodes11,12 as well as flow electrode systems of single38 and multiple37 reactor configurations. But the FE was continuously regenerated within the proposed single-cell F-CapMix system with a cross-chamber configuration, which greatly simplifies the cell configuration compared to the multiple-reactor configuration.37
 |
| Fig. 3 Plot of (a) the cell voltage and (b) the power density during the experiments of different carbon loadings. (c) The average cell voltage and the average power density at different carbon loadings, and the error bars denote the standard deviation for the triplicate experiments. | |
The greater Vcell and P of the cross-chamber F-CapMix system at a higher carbon loading are consistent with those in a previous study.37 The enhanced performance might be explained by the decreased internal resistance of the cell at a higher carbon loading. The internal resistance Rint can be calculated by using eqn (3), where Vmem is dependent on the electrolyte concentration of LC and HC, which was unchanged in the experiments (Vmem = ∼129 mV), and Rext (5 Ω) was unchanged for different carbon loadings as well. As a result, the higher Vcell at a higher carbon loading can only be attributed to the decrease of Rint. As shown in Fig. 4, Rint was decreased by 260% as the carbon loading increased from 2.5 to 10 wt%. In general, Rint consists of the setup resistance, the electronic resistance of flow electrodes, and the contact resistance between the electrode particles and the current collector.36 It has been previously reported that increasing the carbon loading from 5 to 20 wt% in FE could significantly reduce both electronic and ionic resistance in the FE.36 The reduced electronic resistance might be attributed to the larger average size of the percolating cluster of AC in the FE formed at a higher carbon loading, which facilitates the electron transport.48,49 As a result, the charge and electron transportation within the FE was improved, and hence the performance was enhanced at a higher carbon loading.38,50 Although the system performance can be enhanced by increasing the carbon loading in the FE, excessive AC amounts in the FE could increase the viscosity of the FE slurry and lead to the blockage of the FE channel and finally interrupt the experiments.50 The blockage problem has been reported previously,36,49 and the reason can be attributed to the hydrophobicity of AC and CB. In our study, the maximum carbon loading of the FE slurry that would not cause the clogging of the FE channel was 10 wt%, which is lower than the previously reported max carbon loading (e.g., 20 to 35%).35,50,51 The reason might be attributed to the different cell configurations (e.g., the size of the FE channel and silicon tubes for the transportation of the FE) and the rheological properties of the utilized FE materials. Future work can focus on reducing the viscosity of FE slurry, e.g., modifying the surface of AC materials through emulsion polymerization50 or oxidative methods52 to reduce its hydrophobicity.
 |
| Fig. 4 Plot of the system's internal resistance Rint at different carbon loadings. | |
3.3 Effect of carbon black on the system performance
The above results suggested that the system performance of the F-CapMix system can be improved by increasing the carbon loading in the FE due to the reduction in the resistance of the FE. Other than increasing the carbon loading, the resistance of the FE can also be reduced by adding additional carbon black in the FE slurry.35,53 To investigate the effects of CB amounts on the system performance, experiments were performed at five different CB amounts: 0.25, 0.5, 0.75, and 1.0 wt%, under a fixed total electrode (including AC and CB) loading of 5 wt%. As is expected, the cell voltage at different CB amounts was stable during the experiments. The performance of the system was increased with the additional amounts of CB (Fig. 5). The maximum average power density was found for the case of 4.0 wt% AC with 1.0 wt% additional CB amounts, at around 74.3 mW m−2, which is around 6-fold the average power density of the case without additional CB.
 |
| Fig. 5 Plot of (a) the cell voltage and (b) the power density during the experiments of different CB amounts. (c) The average cell voltage and the average power density at different CB amounts, and the error bars denote the standard deviation for the triplicate experiments. | |
The results in Fig. 5 proved that the system performance of F-CapMix can be enhanced by adding additional CB in the FE. The reason can be attributed to the decreased internal resistance of the FE. As shown in Fig. 6, Rint sharply reduced from 33.7 to 11.8 Ω when 0.75 wt% CB was added to the FE. Increasing the CB amount to 1.0 wt% only resulted in a minor reduction in Rint, from 11.8 to 10.7 Ω. The decreased resistance might be attributed to the mesoporous structures of CB. From the N2 adsorption–desorption experiments (Table 2), both the AC and CB in the present study have a high specific surface area, with a value of 1433.66 and 1405.33 m2 g−1, respectively. The main difference between these two materials is the pore size distribution (Fig. 8). The AC particles are mainly occupied by micropores with an average pore diameter of 2.14 nm. The microporous structure of AC might result in EDL overlap inside the pores and hinder the ions' transportation.45 The CB particles, on the other hand, have an average pore diameter of 5.17 nm, which was around 2.4 times larger than that of AC. More importantly, CB is dominated by mesoporous structures with a larger pore size, which might facilitate the ions' transportation and thus reduce the internal resistance.45 In addition, it should be noted that the performance of the case with 0.75 wt% CB (65 mW m−2) was already greater than that of 10 wt% AC without CB (46 mW m−2). This suggested that only a tiny portion of AC in the FE was able to transport and store the charged ions. Considering that the FE was continuously recirculating between the two graphite plates, the adsorbed ions from the HC were shortly released into the LC. It might be concluded that the charged ions were only stored in the outer part of AC. Therefore, the larger pore size of CB gave a greater system performance even with less AC contents.
 |
| Fig. 6 Plot of cell's internal resistance Rint at different carbon black amounts. | |
Table 2 The specific surface area (SBET), total pore volume (vpore), micropore volume (vm,pore), and average pore size (Dp) of activated carbon (AC) and three different carbon blacks (CB)
|
S
BET (m2 g−1) |
v
pore (cm3 g−1) |
v
m,pore (cm3 g−1) |
D
p (nm) |
AC |
1433.66 |
0.77 |
0.63 |
2.14 |
CB |
1405.33 |
1.82 |
0.04 |
5.17 |
CB2 |
805.13 |
0.93 |
0.14 |
4.63 |
CB3 |
49.67 |
0.12 |
0.01 |
10.01 |
3.4 Effect of different types of carbon materials on the system performance
The effect of different types of carbon blacks on the system performance was also investigated in the present study by using three different types of carbon blacks. As shown in Fig. 7a, all the experimental cases with additional CB produced greater power density compared with the case without CB, which proves again that the additional CB could enhance the system performance. In addition, it has been previously demonstrated that using only CB as the flow electrode could improve the desalination performance.45 The feasibility of using only CB to produce electricity was experimental examined in the present study. As shown in Fig. 7b, the experimental cases of CB and CB2 produced electricity in both F-CapMix systems, and the power density was proportional to the CB loading, suggesting that it is possible to use these two types of CBs to replace AC as the flow electrode in the F-CapMix system to produce energy. In addition, the power density of using 1.0 wt% amounts of CB and CB2 was greater than the power density of using 5.0 wt% amounts of AC solely, suggesting that these two CBs were more suitable than AC for the energy production of the F-CapMix system. On the other hand, the case of using CB3 produced little electricity in both F-CapMix systems, indicating that CB3 is not suitable as the FE material.
 |
| Fig. 7 (a) Power density of F-CapMix under different types of additional carbon black. (b) Power density of F-CapMix by using carbon black as the electrodes. The external resistance is 5 Ω for all the experiments. The error bars denote the standard deviation for the triplicate experiments. | |
The difference in the system performance under different CB types might be explained by their physical properties. Table 2 shows the N2 adsorption–desorption experimental results. CB3 has the smallest BET-specific surface area (49.67 m2 g−1), pore volume (0.12 cm3 g−1), and micropore volume (0.01 cm3 g−1) compared to other CBs. Such a low specific surface area and micropore volume of CB3 significantly restricted its ions' storage capacity, thus producing little energy in all the experimental cases (Fig. 7b). By comparing the results of AC with those of CB2, although AC has a higher specific surface area, the power density of AC with 2.5 wt% was lower than that of CB2 with 1.0 wt%, indicating that the specific surface area might not be the only critical factor determining the system performance. By contrast, the pore volume, especially the mesopore volume, seems to be an essential factor for the system performance. The total pore volumes for AC and CB2 are close, at 0.77 and 0.93 cm3 g−1, respectively. As shown in Fig. 8, AC was mainly occupied by micropores, while CB and CB2 were dominated by mesopores. The mesoporous structure with a larger pore size might facilitate the ions' transportation within the materials and enhance the performance.45,54,55 In addition, the CB and CB2 materials have similar pore sizes and mesoporous structures, but CB with a larger pore volume, which might explain the better system performance when using only CB as the electrodes. Therefore, it might be concluded that a material with a larger specific surface area and mesoporous structure is beneficial for increasing the performance of the F-CapMix system.
 |
| Fig. 8 (a) Nitrogen adsorption isotherms and (b) pore size distribution diagrams of activated carbon (AC) and three different carbon blacks (CB) used in the study. | |
3.5 Effect of the external resistance on the system performance
The system performance is dependent on both the cell voltage and the value of external resistance Rext (eqn (2)). In this study, four external resistors (Rext = 1, 20, 50, and 100 Ω) were connected to the cells to investigate the system performance under different resistances. As shown in Fig. 9, the cell voltage Vcell was increased with the external resistance Rext. By contrast, the corresponding instantaneous power density P increased with Rext and reached a maximum of 23.3 mW m−2 when Rext was 50 Ω. Increasing Rext to 100 Ω led to a 19% reduction in P (18.8 mW m−2). Note that the power density of Rext = 20 Ω (22.2 mW m−2) was very close to the maximum value at Rext = 50 (23.3 mW m−2). It has been suggested previously that the maximum power density can be obtained when the external resistance Rext equals the internal resistance Rint.56,57 Therefore, it might be speculated that Rint should be in the middle between 20 and 50 Ω. As can be seen in Fig. 4, the calculated Rint was similar for all the cases, at around 33.7 Ω, which explains the similar power density at these two Rext. Meanwhile, the similar Rint for all the cases can be explained by the identical FE components (5 wt% AC and 0 wt% CB) of these experiments.
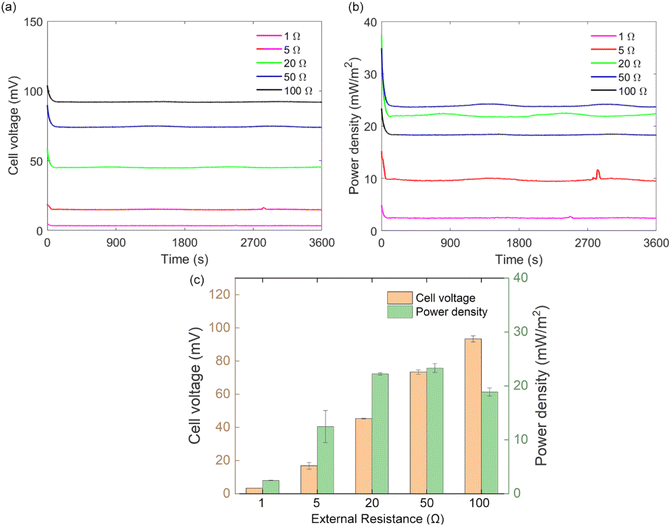 |
| Fig. 9 Plot of (a) the cell voltage and (b) the power density during the experiments of different external resistance. (c) The average cell voltage and the average power density at different external resistances, and the error bars denote the standard deviation for the triplicate experiments. | |
4 Conclusions
In this study, a single-cell F-CapMix system with a cross-chamber configuration has been developed to continuously generate stable electricity from salinity gradient energy between HC and LC solutions for long-term operation. The maximum power density of the system was 74.3 mW m−2, under the experimental conditions of using 4.0 wt% AC loading with additional 1.0 wt% CB under a Rext of 10 Ω. This performance was comparable to those of previous systems of both CapMix with solid electrodes and F-CapMix with flow electrodes. In general, the energy production performance of this single-cell F-CapMix system was dependent on the activated carbon loading, the amount of carbon black, and the external resistance. However, the performance of the single-cell F-CapMix system was independent of the FE electrolyte concentration, which was different from the multiple-cell F-CapMix system.37 The results suggest that the performance of the system can be enhanced by increasing either the AC loading or CB amounts due to the reduction in the internal resistance of the system. Furthermore, it is possible to use solely carbon black with a mesoporous structure as the flow electrodes in the F-CapMix system for energy production. In addition, the maximum power density was achieved when the external resistance matched the internal resistance of the system. In summary, these results indicate that the presented single-cell F-CapMix system with a cross-chamber design can produce electricity continuously from the salinity gradient difference between seawater and freshwater.
Author contributions
Zhi Zou: conceptualization, methodology, investigation, writing – original draft, and formal analysis. Shuo Meng: data curation. Xiaolei Bian: data curation. Longcheng Liu: supervision, writing – review, and editing.
Conflicts of interest
There are no conflicts to declare.
Acknowledgements
This work was funded by the Swedish Energy Agency (Energimyndigheten), project number 44606-1. Zhi Zou acknowledges the financial support from the China Scholarship Council (CSC).
References
-
BP, Statistical review of world energy, 2021 Search PubMed.
- C. Seyfried, H. Palko and L. Dubbs, Renewable Sustainable Energy Rev., 2019, 102, 111–120 CrossRef CAS.
- V. M. Ortiz-Martinez, L. Gomez-Coma, C. Tristan, G. Perez, M. Fallanza, A. Ortiz, R. Ibanez and I. Ortiz, Desalination, 2020, 482, 114389 CrossRef CAS.
- N. Y. Yip, D. Brogioli, H. V. M. Hamelers and K. Nijmeijer, Environ. Sci. Technol., 2016, 50, 12072–12094 CrossRef CAS PubMed.
- B. E. Logan and M. Elimelech, Nature, 2012, 488, 313–319 CrossRef CAS PubMed.
- N. Y. Yip and M. Elimelech, Environ. Sci. Technol., 2012, 46, 5230–5239 CrossRef CAS PubMed.
- R. E. Pattle, Nature, 1954, 174, 660 CrossRef CAS.
- O. A. Alvarez-Silva, A. F. Osorio and C. Winter, Renewable Sustainable Energy Rev., 2016, 60, 1387–1395 CrossRef.
- P. G. Harry, L. Octave and N. Noel de, Science, 1974, 185, 101–102 CrossRef.
- R. E. Lacey, Ocean Eng., 1980, 7, 1–47 CrossRef CAS.
- D. Brogioli, Phys. Rev. Lett., 2009, 103, 058501 CrossRef PubMed.
- B. B. Sales, M. Saakes, J. W. Post, C. J. N. Buisman, P. M. Biesheuvel and H. V. M. Hamelers, Environ. Sci. Technol., 2010, 44, 5661–5665 CrossRef CAS PubMed.
- S. Ahualli, M. L. Jimenez, M. M. Fernandez, G. Iglesias, D. Brogioli and A. V. Delgado, Phys. Chem. Chem. Phys., 2014, 16, 25241–25246 RSC.
- N. Y. Yip, D. A. Vermaas, K. Nijmeijer and M. Elimelech, Environ. Sci. Technol., 2014, 48, 4925–4936 CrossRef CAS PubMed.
- H. Kim, J. Choi, N. Jeong, H. J. Im, J. G. Yeo, S. I. Jeon, W. G. Chun, D. K. Kim and S. Yang, ACS Sustainable Chem. Eng., 2021, 9, 9199–9208 CrossRef CAS.
- G. R. Iglesias, S. Ahualli, A. V. Delgado, P. M. Arenas-Fernandez and M. M. Fernandez, J. Power Sources, 2020, 453, 227840 CrossRef CAS.
- M. Marino, L. Misuri, M. L. Jimenez, S. Ahualli, O. Kozynchenko, S. Tennison, M. Bryjak and D. Brogioli, J. Colloid Interface Sci., 2014, 436, 146–153 CrossRef CAS PubMed.
- H. H. Zhu, W. W. Xu, G. C. Tan, E. Whiddon, Y. Wang, C. G. Arges and X. P. Zhu, Electrochim. Acta, 2019, 294, 240–248 CrossRef CAS.
- G. R. Iglesias, M. M. Fernandez, S. Ahualli, M. L. Jimenez, O. P. Kozynchenko and A. V. Delgado, J. Power Sources, 2014, 261, 371–377 CrossRef CAS.
- F. Zhan, G. Wang, T. T. Wu, Q. Dong, Y. L. Meng, J. R. Wang, J. Yang, S. F. Li and J. S. Qiu, J. Mater. Chem. A, 2017, 5, 20374–20380 RSC.
- K. Smolinska-Kempisty, A. Siekierka and M. Bryjak, Desalination, 2020, 482, 114384 CrossRef CAS.
- A. Siekierka, K. Smolinska-Kempisty and M. Bryjak, Desalination, 2020, 495, 114670 CrossRef CAS.
- B. B. Sales, O. S. Burheim, F. Liu, O. Schaetzle, C. J. N. Buisman and H. V. M. Hamelers, Environ. Sci. Technol., 2012, 46, 12203–12208 CrossRef CAS PubMed.
- G. R. Iglesias, S. Ahualli, M. M. Fernandez, M. L. Jimenez and A. V. Delgado, J. Power Sources, 2016, 318, 283–290 CrossRef CAS.
- S. Ahualli, M. M. Fernandez, G. Iglesias, A. V. Delgado and M. L. Jimenez, Environ. Sci. Technol., 2014, 48, 12378–12385 CrossRef CAS PubMed.
- B. B. Sales, O. S. Burheim, S. Porada, V. Presser, C. J. N. Buisman and H. V. M. Hamelers, Environ. Sci. Technol. Lett., 2014, 1, 356–360 CrossRef CAS.
- M. Nasir, Y. Nakanishi, A. Patmonoaji and T. Suekane, Renewable Energy, 2020, 155, 278–285 CrossRef.
- F. Liu, O. Schaetzle, B. B. Sales, M. Saakes, C. J. N. Buisman and H. V. M. Hamelers, Energy Environ. Sci., 2012, 5, 8642–8650 RSC.
- M. L. Jimenez, M. M. Fernandez, S. Ahualli, G. Iglesias and A. V. Delgado, J. Colloid Interface Sci., 2013, 402, 340–349 CrossRef CAS PubMed.
- R. A. Rica, D. Brogioli, R. Ziano, D. Salerno and F. Mantegazza, J. Phys. Chem. C, 2012, 116, 16934–16938 CrossRef CAS PubMed.
- R. A. Rica, R. Ziano, D. Salerno, F. Mantegazza, M. Z. Bazant and D. Brogioli, Electrochim. Acta, 2013, 92, 304–314 CrossRef CAS.
- D. A. Vermaas, S. Bajracharya, B. B. Sales, M. Saakes, B. Hamelers and K. Nijmeijer, Energy Environ. Sci., 2013, 6, 643–651 RSC.
- F. Liu, O. Coronell and D. F. Call, J. Power Sources, 2017, 355, 206–210 CrossRef CAS.
- S. I. Jeon, H. R. Park, J. G. Yeo, S. Yang, C. H. Cho, M. H. Han and D. K. Kim, Energy Environ. Sci., 2013, 6, 1471–1475 RSC.
- L. Luo, Q. He, Z. X. Ma, D. Yi, Y. Chen and J. X. Ma, Water Res., 2021, 203, 117522 CrossRef CAS PubMed.
- F. Yang, Y. He, L. Rosentsvit, M. E. Suss, X. Zhang, T. Gao and P. Liang, Water Res., 2021, 200, 117222 CrossRef CAS PubMed.
- M. C. Hatzell, K. B. Hatzell and B. E. Logan, Environ. Sci. Technol. Lett., 2014, 1, 474–478 CrossRef CAS.
- S. Porada, D. Weingarth, H. V. M. Hamelers, M. Bryjak, V. Presser and P. M. Biesheuvel, J. Mater. Chem. A, 2014, 2, 9313–9321 RSC.
- I. Hwang, D. Lee, Y. Jung, K. Park, Y. G. Jung, D. Kim, G. H. Cho, S. I. Jeon, Y. K. Byeun, U. Paik, S. Yang and T. Song, ACS Sustainable Chem. Eng., 2021, 9, 13514–13525 CrossRef CAS.
- D. Kim, H. Kwon, G. H. Cho, H. Kim, H. Seo, Y. G. Jung, J. Choi, H. Kim, J. Yoo, D. Lee, I. Hwang, U. Paik, T. Song, H. Park and S. Yang, Sep. Purif. Technol., 2022, 290, 120859 CrossRef CAS.
- J. X. Du, P. M. Biesheuvel, W. W. Tang and T. D. Waite, J. Hazard. Mater., 2023, 442, 130023 CrossRef CAS PubMed.
- W. W. Tang, J. Liang, D. He, J. L. Gong, L. Tang, Z. F. Liu, D. B. Wang and G. M. Zeng, Water Res., 2019, 150, 225–251 CrossRef CAS PubMed.
- A. Rommerskirchen, A. Kalde, C. J. Linnartz, L. Bongers, G. Linz and M. Wessling, Carbon, 2019, 145, 507–520 CrossRef CAS.
- W. L. Xing, J. Liang, W. W. Tang, D. He, M. Yan, X. X. Wang, Y. Luo, N. Tang and M. Huang, Desalination, 2020, 482, 114390 CrossRef CAS.
- J. J. Ma, C. Y. Zhang, F. Yang, X. D. Zhang, M. E. Suss, X. Huang and P. Liang, Environ. Sci. Technol., 2020, 54, 1177–1185 CrossRef CAS PubMed.
- D. Brogioli, R. Zhao and P. M. Biesheuvel, Energy Environ. Sci., 2011, 4, 772–777 RSC.
- P. Liang, X. L. Sun, Y. H. Bian, H. L. Zhang, X. F. Yang, Y. Jiang, P. P. Liu and X. Huang, Desalination, 2017, 420, 63–69 CrossRef CAS.
- K. B. Hatzell, J. Eller, S. L. Morelly, M. H. Tang, N. J. Alvarez and Y. Gogotsi, Faraday Discuss., 2017, 199, 511–524 RSC.
- F. Yu, Z. Q. Yang, Y. J. Cheng, S. Y. Xing, Y. Y. Wang and J. Ma, Sep. Purif. Technol., 2022, 281, 119870 CrossRef CAS.
- H. R. Park, J. Choi, S. Yang, S. J. Kwak, S. I. Jeon, M. H. Han and D. K. Kim, RSC Adv., 2016, 6, 69720–69727 RSC.
- G. J. Doornbusch, J. E. Dykstra, P. M. Biesheuvel and M. E. Suss, J. Mater. Chem. A, 2016, 4, 3642–3647 RSC.
- K. B. Hatzell, M. C. Hatzell, K. M. Cook, M. Boota, G. M. Housel, A. McBride, E. C. Kumbur and Y. Gogotsi, Environ. Sci. Technol., 2015, 49, 3040–3047 CrossRef CAS PubMed.
- C. Y. Zhang, J. X. Ma, L. Wu, J. Y. Sun, L. Wang, T. Y. Li and T. D. Waite, Environ. Sci. Technol., 2021, 55, 4243–4267 CrossRef CAS PubMed.
- M. Tian, Y. Q. Sun, C. Zhang, J. T. Wang, W. M. Qiao, L. C. Ling and D. H. Long, J. Power Sources, 2017, 364, 182–190 CrossRef CAS.
- L. D. Zou, L. X. Li, H. H. Song and G. Morris, Water Res., 2008, 42, 2340–2348 CrossRef CAS PubMed.
- S. Cheng, H. Liu and B. E. Logan, Environ. Sci. Technol., 2006, 40, 2426–2432 CrossRef CAS PubMed.
- T. Kim, M. Rahimi, B. E. Logan and C. A. Gorski, Environ. Sci. Technol., 2016, 50, 9791–9797 CrossRef CAS PubMed.
|
This journal is © The Royal Society of Chemistry 2023 |
Click here to see how this site uses Cookies. View our privacy policy here.