DOI:
10.1039/D3RA03873D
(Paper)
RSC Adv., 2023,
13, 22281-22286
Improvement of optical properties of AISI 304 as a solar absorber using a pulsed fiber laser†
Received
9th June 2023
, Accepted 18th July 2023
First published on 24th July 2023
Abstract
Solar energy is an environmentally friendly and inexhaustible natural resource. It can be converted into thermal energy by using concentrated solar power (CSP) methods. One of the key components of CSP is a solar absorber, which absorbs concentrated solar radiation and converts it into heat. Recently, there have been many studies on enhancing the solar-to-thermal conversion efficiency of solar absorbers. In this work, a pulsed fiber laser was used to modify the surface of AISI 304 stainless steel as a solar absorbing material. By varying the energy density, surface roughness and oxide films can be formed, which affect the solar absorptance and thermal emittance of the substrate. The surface characteristics and corresponding optical properties were investigated. The surface roughness was measured to be in the range of 9–158 nm. Due to heat generated during engraving, metal surface oxidation occurs on the AISI 304 substrate, resulting in different values of solar absorptance and thermal emittance. Compared with the unmodified surface, the modified AISI 304 surfaces resulted in solar absorptance ranging from 58.57% to 91.78%, and the thermal emittance ranged from 10.56% to 32.90%. Consequently, the solar-to-thermal conversion efficiency was improved from 50.09% to 81.69%, and the technique can be used for solar absorbing applications.
Introduction
To generate electricity, conventional resources such as fossil fuels or coal have been used. However, they have adverse effects on the environment, so the use of alternative resources has been explored. Concentrated solar power (CSP) technology can convert solar irradiance into thermal energy, which can be used for electricity generation.1 In general, solar radiation is reflected by a reflector and concentrated onto a solar absorber to generate heat. The heat is then transferred to a heat-transfer fluid (HTF), which is later used for electricity generation with a conventional steam turbine.2 The operation of CSP is demonstrated in Fig. 1(a). One of the key elements to control solar-to-thermal conversion efficiency is the optical properties of the solar selective absorber (SSA) which deposited and enveloped the absorber tube as shown in Fig. 1(b). The quality of the solar selective absorber layer also controls achieve high solar absorptance (αs) and low thermal emittance (εt) in order to obtain the best conversion efficiency.3
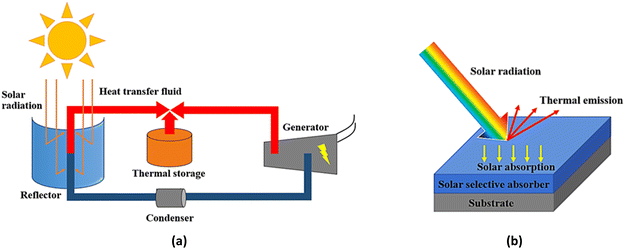 |
| Fig. 1 Parabolic-trough solar concentrated power technology (a) schematic operation of parabolic-trough solar concentrated power (b) optical reaction mechanism on solar selective absorber which deposited on metal substrate. | |
There are many ways to obtain spectrally selective solar absorbers by surface modification, such as surface texturing,4 creating surface roughness,5 intrinsic structure or nanostructure formation,6 cermet coating7,8 and multilayer absorber coating.9 The creation of an oxide layer as an intrinsic structure and surface roughness is quite simple and produces good conditions for high solar absorptance and low thermal emittance. It is well-known that cermet-based is the most recent widely used as solar selective absorbers, which exhibit outstanding in spectral selectivity. The cermet-based absorber as selective surfaces have high solar absorptance at 0.96 and low thermal emittance at 0.09, which deposited on stainless steel surface under sputtering technique.
An oxide layer and surface roughness can be created with two types of atmospheric systems: vacuum-based and ambient-based systems. Sputtering10 and electron evaporation are vacuum-based methods, and these high-cost processes use high amount of energy to create the oxide layer and surface roughness. Khelifa et al.9 used electron beam evaporation to create multilayer absorbers based on Cr2O3/Cr/Cr2O3, which could improve the optical properties.
Sintering11 and laser treatment12–15 are ambient-based methods, and these low-cost processes can easily create the oxide layer and surface roughness. Laser treatment uses low energy and takes a short time for processing, while sintering operates at a high temperature and a longer time for processing. Wu et al.11 created a solar absorber on AISI 304 by sintering, and a thick Fe2O3 oxide film layer was formed on the surface with roughness of 114.3 nm. As a result, the optical properties were improved. Jalil et al.16 used femtosecond laser treatment to create a solar absorber with a variety of metals (copper, aluminum, steel, and tungsten). They controlled the scanning speed and frequency to activate the absorption due to plasmonic resonance of the oxide particles on the surface, and tungsten had the highest solar absorptance of 92% and the lowest thermal emittance of 18%.
In this research, AISI 304 was used as a solar absorbing material. Its surface was modified with a pulsed fiber laser to create an oxide layer for intrinsic structure formation17 and roughness on the substrate.18 Most current commercial technology enhances the photo-thermal conversion by fabricating the solar selective absorber under vacuum based conditions, such as sputtering technique. To compare with the pulsed fiber laser in this paper, this technique is under atmospheric conditions which make it easy to apply on an industrial scale. The pulsed fiber laser helps in growing intrinsic absorbers with rapid processing, which is easier, lower in energy and cost-effective. Moreover, there is no need for target materials as a solar selective absorber. These factors can affect the solar absorptance and thermal emittance of the substrate.19 This process is scalable for commercial applications by utilizing a laser array for large surface modification, which also facilitates higher moving speeds, resulting in shorter completion times.20 The microstructures and optical properties of specimens were investigated, and the solar-to-thermal conversion efficiency was evaluated.21
Experimental
Materials and methods
AISI 304 stainless steel sheets (1 inch × 1 inch and 1.0 mm thick) were cleaned with isopropyl alcohol by ultrasonic vibration for 5 minutes. Subsequently, the surfaces were treated with a pulsed fiber laser with a wavelength of 1064 nm in air, using an energy density ranging from 0.00 to 6.61 kJ inch−2 to promote roughness and oxidation. The pulse diameter was 50 μm, the pulse frequency was 20 kHz, and the scanning speed was 200 mm min−1. The laser spacing from center to center was maintained at 10 μm. The laser was operated in line scanning mode.22 The energy density can be calculated from the following equation:23 |
 | (1) |
where P is the laser power in watts, t is the exposure time in seconds counted from the onset of the pulse, and A is the surface area of the treatment in inch2. The energy density of all specimens is shown in Table 1.
Table 1 Calculated energy densities of the laser
Specimen |
A |
B |
C |
D |
E |
F |
G |
H |
I |
J |
Energy density (kJ inch−2) |
0.00 |
1.37 |
1.71 |
2.05 |
2.39 |
2.74 |
3.08 |
3.42 |
4.79 |
6.16 |
Characterization
The surface roughness was investigated by confocal microscopy, and the surface morphology was characterized by scanning electron microscopy (SEM; Hitachi SU-8230). The surface elements were characterized by energy-dispersive X-ray spectroscopy (EDS; Oxford Instruments) and an electron probe microanalyzer (Shimadzu EPMA-8050G). The oxide formation was studied by X-ray diffractometer (XRD; Bruker/D8 Advance) with 2θ ranging from 20° to 90°. The optical properties were measured for the solar absorptance (αs) using spectrophotometry (Agilent technologies, Cary 5000 UV-Vis-NIR), and the solar absorptance was computed as follows: |
 | (2) |
where Is(λ) is the solar spectral radiation of air mass 1.5 from the ASTM G173 standard. R(λ) is the measured reflectance at a specific wavelength λ (wavelength interval λ1 to λ2 = 0.3 to 2.5 μm).7 The thermal emittance (εt) was tested at 120 °C using an emissometer (Devices & Services Company, Model AE-ADI). Solar to thermal conversion efficiency was calculated from the eqn (3) as follow: |
Conversion efficiency = (1 − εt) × αs
| (3) |
Results and discussion
Surface appearance
Fig. 2 shows the different surface appearances of the specimens after being treated with the pulsed fiber laser. Compared to unmodified specimen A, specimens B and C exhibited a slightly brighter surface, while specimen D appeared more yellowish. Specimen E had a dark blue surface, while the color of specimens F to H gradually faded out. Specimens I and J had a darker surface due to the higher laser power. The differences in surface appearance were attributed to the roughness and oxide formation during laser engraving.24–26 The specimens also showed horizontal lines, which were caused by the line-scanning laser.
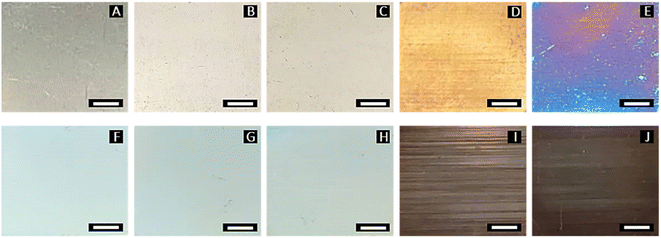 |
| Fig. 2 Surface appearance of AISI 304 specimens treated by pulsed fiber laser with different energy densities (A = 0.00, B = 1.37, C = 1.71, D = 2.05, E = 2.39, F = 2.74, G = 3.08, H = 3.42, I = 4.79, and J = 6.16 kJ inch−2) as shown in Table 1 (scale bars are 5.0 mm). | |
Roughness analysis
The surface roughness (Ra) at different power was measured, and the result is presented in Fig. 3. From specimen A to C, the roughness decreased from 47 to 9 nm due to the surface treatment by the pulsed fiber laser, which smoothened the surface. Then, the roughness slightly increased from 9 to 27 nm from specimen C to H. This could have occurred because of metal oxide formation on the surface. From specimen I and J, the roughness significantly increased from 27 to 158 nm. Since heat accumulated at high laser power, the oxide layer could grow much faster and result in a rougher surface.27,28 The height images presenting the roughness are shown in ESI.†
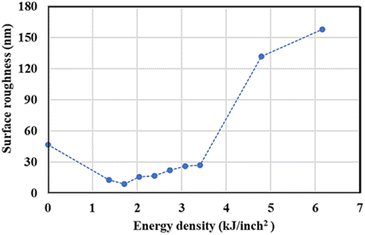 |
| Fig. 3 Surface roughness of AISI 304 stainless steel before and after modification by the pulsed fiber laser method with energy density between 0.00 and 6.16 kJ inch−2 (specimen A to J). | |
Surface morphology and elemental analysis
The surface morphology of specimens was investigated by SEM, which showed that higher energy density created different surface structures, as shown in Fig. 4. Compared with non-laser treated specimen A (Fig. 4(a)), nano-sized particles were formed on the surfaces of specimen B to E. Accordingly, at higher laser energies, more particles were formed and uniformly distributed over the surfaces (Fig. 4(b)). However, specimen F to H presented a combination of nano-sized particles and circle islands formed non-uniformly over the surfaces (Fig. 4(c)). Such the structure could contribute to a rougher surface. Formation of highly porous structure on specimen I and J was observed after they were modified with high laser energies. As a result, it could greatly increase the surface roughness (Fig. 4(d)).
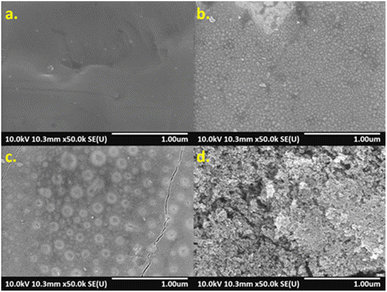 |
| Fig. 4 SEM images of AISI 304 surfaces. (a) specimen A, (b) specimen E, (c) specimen G, and (d) specimen J. | |
The microstructural transformation of specimen B to J was expected to be a result of metal oxide formation generated from the laser treatment.29,30 The elemental analysis showed that oxygen content was increased on the specimens treated with higher energy density, as shown in Fig. 5. The results indicated that surface oxidation occurred during the laser engraving.31
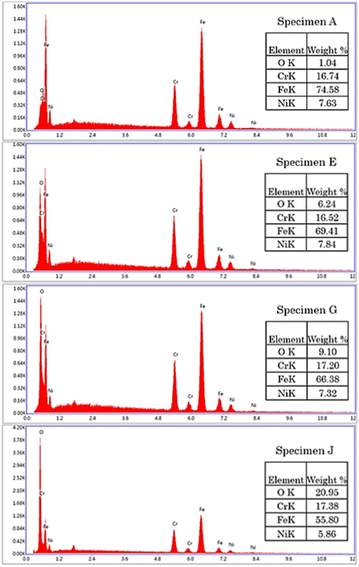 |
| Fig. 5 EDS of AISI 304 stainless steel before and after modification by the pulsed fiber laser method from specimen A, specimen E, specimen G, and specimen J. | |
In addition, the XRD results showed that the non-modified stainless steel mainly consisted of α-Fe and γ-Fe phases. However, the constituent phases changed when the surface was modified by the pulsed fiber laser. The diffraction peaks in Fig. 6 presents Cr2O3 and Fe2O3 phases on the specimens treated with laser, which agreed well with a report by Cui et al.32
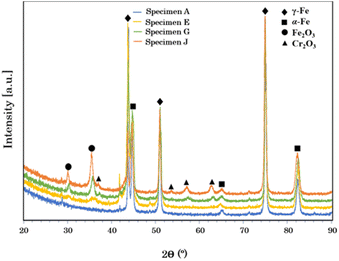 |
| Fig. 6 XRD patterns of AISI 304 stainless steel before and after modification by the pulsed fiber laser method from specimen A, specimen E, specimen G, and specimen J. | |
Although the metal oxides found on surfaces were characterized, the nano-sized particles and circle islands found on specimens (Fig. 4) were further investigated. Specimen E and G were studied using elemental mapping. Consequently, the results revealed different elemental concentrations of oxygen (O), chromium (Cr), and iron (Fe), over the surfaces as seen in Fig. 7. Specimen E, which consisted of nano-sized particles, presented uniform elemental concentrations of O, Cr, and Fe for entire surface (Fig. 7(a1)–(a4)). In contrast, there was a combination of nano-sized particles and large circle islands in specimen G observed in the diagonal band in Fig. 7(b1). From elemental mapping analysis (Fig. 7(b2)–(b4)), the circle islands were rich in Fe and O that could form an iron oxide while, within the band, the surrounded nano-sized particles were rich in Cr and O that could form a chromium oxide. The difference in roughness and metal oxides on the surfaces treated by laser could lead to an improvement of the optical properties.33–36
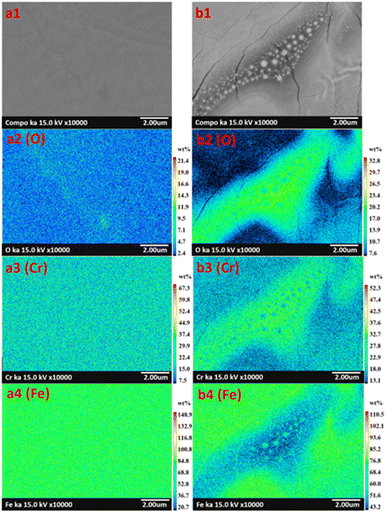 |
| Fig. 7 Elemental image classification with color of modified AISI 304 surfaces presenting oxygen (O), chromium (Cr), and iron (Fe) in specimen E (image a1–a4), and in specimen G (image b1–b4). | |
Optical property analysis
The non-modified and modified AISI 304 specimens were tested for αs and εt, and the results are presented in Fig. 8. Initially, αs of non-modified specimen A was 58.57% and was then improved up to 91.78% on specimen E. This improvement may be a result of the extended growth of Cr2O3 particles, which significantly influence the solar absorptance.37 This influence is due to the regular distribution and plasmonic resonance of the oxide particles on the surface,38,39 which originates from the resonance of collective conduction electrons with incident electromagnetic radiations. Moreover, small and uniform-sized nanoparticles with a narrow size distribution gives a sharp absorbance, whereas nanoparticles with a wide size distribution or any kind of aggregation show broad absorptance.40 Next, αs was reduced and remained around 78.47% from specimen F to H. It was observed that, at higher laser energy, Fe2O3 could form on the surface while Cr2O3 particles were reduced and became non-uniformly distributed. In fact, the solar absorptance of Fe2O3 is lower compared with that of Cr2O3, as reported by Thakur and Yadav.41 Then, αs slightly increased again up to 86.14% from specimen H to J, and a porous Fe2O3 structure with high roughness was introduced. In general, when the roughness increases, the solar absorptance and thermal emittance also increase.42,43 However, Bergström et al.44 reported that if the surface roughness is below 150 nm, it may not affect the solar absorptance. Thus, the increase in αs of specimen I and J could be from thicker Fe2O3 formation. The spectral reflectance data of modified specimens are presented in ESI.†
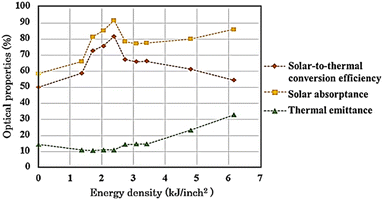 |
| Fig. 8 Optical properties and solar-to-thermal conversion efficiency of AISI 304 stainless steel before and after modification by the pulsed fiber laser method with energy density of 0.00 to 6.16 kJ inch−2. | |
From Fig. 8, εt decreased initially from 14.46% to 10.56% for specimen A to C, respectively. Afterwards, εt remained relatively low and tended to increase from 11.13% to 32.90% for specimen D to J, respectively. The surface roughness and metal oxide formation were considered for the corresponding change in εt. Voinea et al.45 reported that surface roughness could affect the thermal emittance proportionally. In this case, the resulting roughness (Fig. 3) had influenced the thermal emittance similarly. In addition, metal oxides also affect εt. Chromium oxide has a lower εt compared to that of iron oxide.41 Consequently, specimen D and E still kept εt relatively low even though the roughness increased. Then, the solar-to-thermal conversion efficiency was calculated from αs and εt, presented in Fig. 8. Overall, the efficiency was initially enhanced from 50.09% up to 81.69% for specimen A to E, respectively. After that, from specimen F to J, the higher energy density caused both αs and εt to increase. Nonetheless, αs increased at a lower ratio. As a result, the efficiency decreased from 81.69% to 54.37%.
Conclusions
This study presents the surface modification of AISI 304 stainless steel using a pulsed fiber laser. By varying the energy density, surface roughness and oxide formations were introduced, which can affect the optical properties. Initially, the surface roughness was found to be mostly lower than 150 nm, which had an insignificant effect on the solar absorptance. Based on the microstructural and elemental analyses, nano sized Cr2O3 particles and Fe2O3 islands were formed disparately depending on the laser power. At low power, Cr2O3 particles were dominant, and the solar absorptance of 91.78% was achieved. Although Fe2O3 became dominant at higher power, it yielded slightly lower solar absorptance up to 78.47%. The resulting oxide formation clearly enhanced the solar absorptance. Thermal emittance was also measured and found to be mainly affected by surface roughness. Rougher surfaces increased thermal emittance in a range of 9–158 nm in this study. Finally, with the pulsed fiber laser modification on AISI 304, a solar-to-thermal conversion efficiency from 50.09% up to 81.69% could be achieved. The process was quick and effective, and therefore has great potential for use in solar-absorbing applications in CSP technology.
Conflicts of interest
There are no conflicts to declare.
Acknowledgements
The authors are greatly thankful to Thailand Graduate Institute of Science and Technology (TGIST) for financial support.
References
- L. A. Weinstein, J. Loomis, B. Bhatia, D. M. Bierman, E. N. Wang and G. Chen, Chem. Rev., 2015, 115, 12797–12838 CrossRef CAS.
- Q. Chen, Y. Wang, J. Zhang and Z. Wang, Energies, 2020, 13, 1988 CrossRef.
- M. Bello, S. Subramani and M. M. Bin Mohd Rashid, Results Phys., 2020, 19, 103582 CrossRef.
- C. Niu, T. Zhu and Y. Lv, Int. J. Photoenergy, 2019, 2019, 1476217 CrossRef.
- E. S. P. Leong, Y. J. Liu, B. Wang and J. Teng, ACS Appl. Mater. Interfaces, 2011, 3, 1148–1153 CrossRef CAS PubMed.
- X.-H. Gao, Z.-M. Guo, Q.-F. Geng, P.-J. Ma, A.-Q. Wang and G. Liu, Sol. Energy Mater. Sol. Cells, 2017, 163, 91–97 CrossRef CAS.
- Z. Li, J. Zhao and L. Ren, Sol. Energy Mater. Sol. Cells, 2012, 105, 90–95 CrossRef CAS.
- J. Yang, H. Shen, Z. Yang and K. Gao, ACS Appl. Mater. Interfaces, 2021, 13, 14587–14598 CrossRef CAS.
- A. B. Khelifa, S. Khamlich, Z. Y. Nuru, L. Kotsedi, A. Mebrahtu, M. Balgouthi, A. A. Guizani, W. Dimassi and M. Maaza, J. Alloys Compd., 2018, 734, 204–209 CrossRef CAS.
- A. Dan, K. Chattopadhyay, H. C. Barshilia and B. Basu, Thin Solid Films, 2016, 620, 17–22 CrossRef CAS.
- S. Wu, C.-H. Cheng, Y.-J. Hsiao, R.-C. Juang and W.-F. Wen, Renewable Sustainable Energy Rev., 2016, 58, 574–580 CrossRef CAS.
- X. Pang, Q. Wei, J. Zhou and H. Ma, Materials, 2018, 11, 1037 CrossRef PubMed.
- L. Wang, K. Yin, Q. Deng, Q. Huang, J. He and J.-A. Duan, Adv. Sci., 2022, 9, 2204891 CrossRef CAS.
- Y. He, L. Wang, T. Wu, Z. Wu, Y. Chen and K. Yin, Nanoscale, 2022, 14, 9392–9400 RSC.
- K. Yin, Z. Wu, J. Wu, Z. Zhu, F. Zhang and J.-A. Duan, Appl. Phys. Lett., 2021, 118, 211905 CrossRef CAS.
- S. A. Jalil, B. Lai, M. ElKabbash, J. Zhang, E. M. Garcell, S. Singh and C. Guo, Light: Sci. Appl., 2020, 9, 14 CrossRef CAS PubMed.
- X. Ma, X. Nie, J. Zhao, P. Shrotriya, Y. Zhang, Y. Cui and J. Wang, Opt. Laser Technol., 2020, 126, 106104 CrossRef CAS.
- K. Mroczkowska, A. Antonczak, B. Szubzda, M. Wójcik, B. Stepak, P. Szymczyk-Ziółkowska, M. Trzcinski, M. Ozimek and K. Abramski, J. Laser Appl., 2016, 28, 032009 CrossRef.
- C. Y. Cui, X. G. Cui, Y. K. Zhang, K. Y. Luo, Q. Zhao, J. D. Hu, Z. Liu and Y. M. Wang, Appl. Surf. Sci., 2010, 256, 6782–6786 CrossRef CAS.
- F. Ihsan, L. Daniault, S. Bellanger, M. Veinhard, J. Bourderionnet, C. Larat, E. Lallier, E. Durand, A. Brignon and J. C. Chanteloup, Opt. Express, 2020, 28, 20152–20161 CrossRef PubMed.
- H. Kügler and F. Vollertsen, J. Manuf. Mater. Process., 2018, 2, 84 Search PubMed.
- M. Radmanesh and A. Kiani, Mater. Sci. Appl., 2015, 6, 634 Search PubMed.
- T. Mileto and F. Azambuja, RGO, Rev. Gaucha Odontol., 2017, 65, 13–19 CrossRef CAS.
- Y. Lu, X. Shi, Z. Huang, T. Li, M. Zhang, J. Czajkowski, T. Fabritius, M. Huttula and W. Cao, Sci. Rep., 2017, 7, 7092 CrossRef.
- J.-T. Wang, C.-I. Weng, J.-G. Chang and C.-C. Hwang, J. Appl. Phys., 2000, 87, 3245–3253 CrossRef CAS.
- Y. Tamamura and G. Miyaji, Opt. Mater. Express, 2019, 9, 2902–2909 CrossRef CAS.
- M. G. S. Ferreira, N. E. Hakiki, G. Goodlet, S. Faty, A. M. P. Simões and M. Da Cunha Belo, Electrochim. Acta, 2001, 46, 3767–3776 CrossRef CAS.
- G. Schnell, U. Duenow and H. Seitz, Materials, 2020, 13, 969 CrossRef CAS PubMed.
- V. P. Veiko, G. Odintsova, E. Ageev, J. Karlagina, A. Loginov, A. Skuratova and E. Gorbunova, Opt. Express, 2014, 22, 24342–24347 CrossRef CAS PubMed.
- J.-M. Guay, A. Calà Lesina, G. Côté, M. Charron, D. Poitras, L. Ramunno, P. Berini and A. Weck, Nat. Commun., 2017, 8, 16095 CrossRef CAS PubMed.
- S. K. Lawrence, D. P. Adams, D. F. Bahr and N. R. Moody, Surf. Coat. Technol., 2016, 285, 87–97 CrossRef CAS.
- C. Y. Cui, X. G. Cui, X. D. Ren, M. J. Qi, J. D. Hu and Y. M. Wang, Appl. Surf. Sci., 2014, 305, 817–824 CrossRef CAS.
- P. Gupta and M. Ramrakhiani, Open Nanosci. J., 2009, 3, 15–19 CrossRef CAS.
- P. Bonin, M. Gelin and A. Bugaiska, Memory Cognition, 2013, 42, 370–382 CrossRef.
- C. Garfinkel, I. White, E. Gerber, M. Jucker and M. Erez, J. Clim., 2020, 33, 5611–5633 Search PubMed.
- H.-B. Fu and J.-N. Yao, J. Am. Chem. Soc., 2001, 123, 1434–1439 CrossRef CAS.
- A. B. Khelifa, A. Soum-Glaude, S. Khamlich, H. Glénat, M. Balghouthi, A. A. Guizani, M. Maaza and W. Dimassi, J. Alloys Compd., 2019, 783, 533–544 CrossRef CAS.
- X. Ding, C. H. Liow, M. Zhang, R. Huang, C. Li, H. Shen, M. Liu, Y. Zou, N. Gao, Z. Zhang, Y. Li, Q. Wang, S. Li and J. Jiang, J. Am. Chem. Soc., 2014, 136, 15684–15693 CrossRef CAS PubMed.
- M. Roy, S. Ghosh and M. K. Naskar, Mater. Chem. Phys., 2015, 159, 101–106 CrossRef CAS.
- J. Singh, V. Jaswal, A. Arora, M. Kinger and V. Gupta, Orient. J. Chem., 2014, 30, 559–566 CrossRef.
- P. Thakur, A. Thakur and K. Yadav, Springer Proc. Phys., 2017, 178, 145–155 Search PubMed.
- E. Sani, L. Mercatelli, M. Meucci, L. Zoli and D. Sciti, Sci. Rep., 2017, 7, 718 CrossRef PubMed.
- D. Bergstrom, J. Powell and A. Kaplan, J. Appl. Phys., 2008, 103, 103515 CrossRef.
- D. Bergstrom, J. Powell and A. Kaplan, J. Appl. Phys., 2007, 101, 113504 CrossRef.
- M. Voinea, M. Dudita, C. Cristina and A. Duta, J. Optoelectron. Adv. Mater., 2009, 1, 1130 Search PubMed.
|
This journal is © The Royal Society of Chemistry 2023 |
Click here to see how this site uses Cookies. View our privacy policy here.