DOI:
10.1039/D3RA03069E
(Paper)
RSC Adv., 2023,
13, 20351-20364
Fe3O4@ABA-aniline-CuI nanocomposite as a highly efficient and reusable nanocatalyst for the synthesis of benzothiazole-sulfide aryls and heteroaryls†
Received
8th May 2023
, Accepted 21st June 2023
First published on 12th July 2023
Abstract
Studying diaryl sulfides and benzothiazoles is important in organic synthesis because numerous natural and medicinal products contain these scaffolds. Over the past few years, research on the synthesis of compounds containing benzothiazole-sulfide aryls, as important biological molecules, has received significant attention. Multicomponent reactions are the most popular strategy for performing difficult reactions and the synthesis of complexed molecules such as benzothiazole-sulfide aryls. In this work, CuI was successfully immobilized on the surface of magnetic Fe3O4 nanoparticles modified with aniline and 4-aminobenzoic acid [Fe3O4@ABA-Aniline-CuI nanocomposite] and its catalytic activity was investigated in the preparation of a broad range of benzothiazole-sulfide aryls and heteroaryls through the one-pot three-component reactions of 2-iodoaniline with carbon disulfide and aryl or heteroaryl iodides in the presence of KOAc as base in PEG-400 as solvent. TEM and SEM images revealed that the shape of the Fe3O4@ABA-Aniline-CuI particles is spherical and the size of the particles is approximately between 12–25 nanometers.
Introduction
Catalysts are the most important materials in chemical processes, and during the last decade, research on them has become one of the most important topics among chemists.1–5 In the new era of chemistry, especially organic chemistry, chemists are always looking for environmentally friendly, cost-effective and efficient catalytic systems to perform chemical processes.6–11 Each type of catalyst has advantages and disadvantages.12–14 Two characteristics of efficient catalysts are their high activity and high selectivity.7 One of the most important goals of modern chemistry is to combine the benefits of both heterogeneous and homogeneous catalysts.15–19 Nanocatalysts have the advantages of both the mentioned systems and their activity, selectivity, high stability and ability to be recovered from the reaction medium.20–22 Nanoparticles are a group of materials that are artificially produced by combining atoms, molecules or groups of them.23–25 Magnetic nanoparticles are particles smaller than one hundred nanometers that have magnetic properties in the presence of an external magnetic field.26,27 Clumping is one of the disadvantages of magnetic nanoparticles as catalysts and functionalizing the surface of magnetic nanoparticles is a suitable way to solve this problem.28–30 Fe3O4 nanoparticles are well known and can be used as a suitable support for functionalization with metals, organic catalysts, N-heterocyclic carbenes and chiral catalysts.31–33 Recent advances have shown that the improvement of catalyst performance can be achieved through structural modifications of magnetic nanoparticles.34 Using Fe3O4 NPs as a support substrate, modern catalysts that have higher specific surface area than conventional catalysts can be obtained, and in addition to consuming fewer precious metals, their efficiency, which makes creating a catalyst cheaper and more effective, can be increased.35–37 Magnetic nanocatalysts are easily synthesized and can be reused several times without losing a significant amount of their activity by being recycled through an external magnetic field.38
The chemistry of heterocyclic compounds, which deals with the properties, synthesis, and applications of this class of compounds, is considered an important branch of organic chemistry.39,40 On the other hand, research on organosulfur chemistry (compounds containing S element) is one of the most important topics in medicinal, pharmaceutical and industrial chemistry.41,42 Benzothiazoles are a class of aberrant compounds that have a benzene ring fused to a thiazole ring.43,44 A useful central structure, benzothiazole forms part of the molecular structure of a large number of biological molecules, drugs, natural products and industrial chemicals.45–47 Recently, applications of benzothiazoles with different biological activities, such as anti-viral, anti-tumor, anti-fungal, anti-bacterial and anti-cancer activities, have been discovered.43,46 In the past few decades, the formation of carbon-sulfur bonds has been widely studied by chemists. Studying diaryl sulfides is important in organic synthesis because a large number of natural and medicinal products contain sulfide scaffolds.48–50 Diaryl sulfides are one of the most important sulfur-containing organic compounds in the chemical, biochemical, biological and industrial industries.51–53 Therefore, extensive studies have been conducted in order to provide new methods for the synthesis of these compounds. Compounds containing benzothiazole-sulfide aryls are unique, important heterocyclic and organosulfur compounds with many biological and pharmacological activities.54 Several bioactive molecules containing benzothiazole-sulfide scaffolds are listed in Fig. 1.54–56
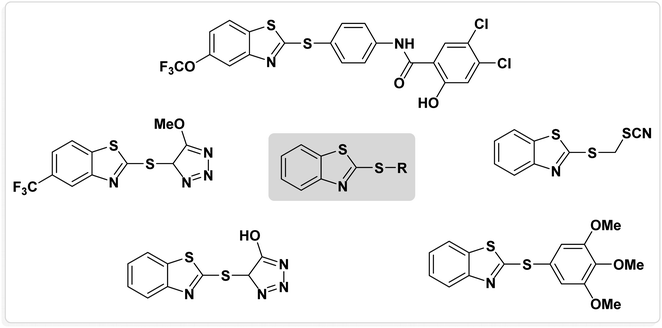 |
| Fig. 1 Several bioactive molecules containing benzothiazole-sulfide scaffolds. | |
Therefore, the development of an effective methodology for the synthesis of benzothiazole-sulfide aryls is an important research challenge with high potential for beneficial applications in the pharmaceutical industry. Multicomponent reactions are the most popular strategy for difficult reactions and the synthesis of complexed molecules such as benzothiazole-sulfide aryls. In order to explore the potential of benzothiazole-sulfide aryl compounds, we developed an efficient protocol to synthesize various analogues of benzothiazole-sulfide aryl compounds from 2-haloaniline, aryl halides and carbon disulfide as the sulfur source for both the benzothiazole and sulfide moieties. A typical reaction was carried out over heterogeneous Cu complex as catalyst and the target compounds were obtained in excellent yields.
Result and discussion
In this paper, we report the fabrication of Fe3O4@ABA-Aniline-CuI nanocomposite as a novel and efficient magnetic catalyst for the synthesis of a broad range of benzothiazole-sulfide aryls and heteroaryls through the one-pot three-component reactions of 2-iodoaniline with carbon disulfide and aryl or heteroaryl iodides in the presence of KOAc as base in PEG-400 as solvent. The steps of the fabrication of Fe3O4@ABA-Aniline-CuI nanocomposite are outlined in Scheme 1. First, magnetic iron nanoparticles were synthesized from Fe(II) and Fe(III) salts utilizing the coprecipitation procedure, then these nanoparticles were coated with 4-aminobenzoic acid. A suitable ligand (Fe3O4@ABA-Aniline nanocomposite) was prepared from the reaction of Fe3O4@ABA-BA (prepared from the treatment of Fe3O4@ABA with biacetyl) with aniline in ethanol solvent under reflux conditions. In the last step, by fixing copper iodide on the surface of Fe3O4@ABA-Aniline nanoparticles, the final catalyst [Fe3O4@ABA-Aniline-CuI] was successfully synthesized.
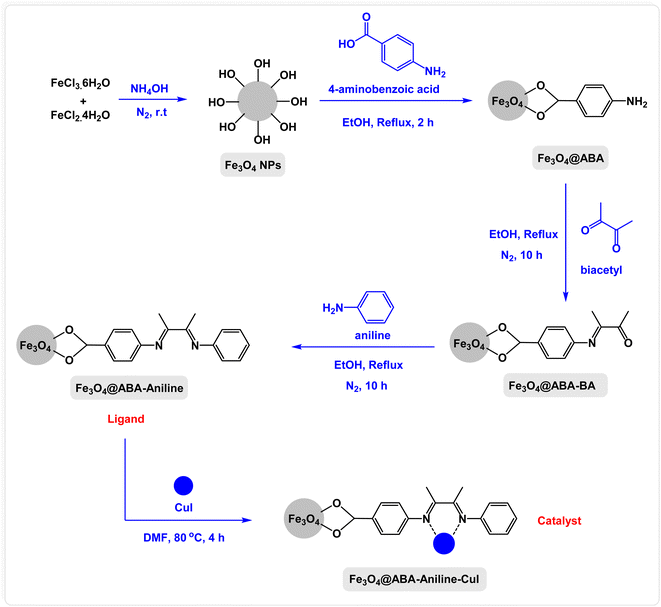 |
| Scheme 1 Steps of fabrication of Fe3O4@ABA-Aniline-CuI nanocatalyst. | |
Characterization of Fe3O4@ABA-Aniline-CuI nanocatalyst
After designing and fabricating the nanocatalyst (Fe3O4@ABA-Aniline-CuI), various techniques were used to identify the catalyst.
FR-IR spectroscopy
By using FT-IR spectroscopy and comparing the spectra of Fe3O4@ABA-Aniline ligand and Fe3O4@ABA-Aniline-CuI (Fig. 2), it is possible to understand the successful functionalization of the functional groups and CuI complex on the surface of magnetic Fe3O4 nanoparticles. As can be seen, Fe–O stretching vibrations appeared near 579 cm−1 and O–H stretching vibrations appeared at 3400 cm−1. As can be seen in the spectrum of Fe3O4@ABA-Aniline-CuI nanocatalyst, the C
N bending vibration bands show a clear shift towards lower frequency (1642 → 1624 cm−1) compared to the Fe3O4@ABA-Aniline spectrum, which indicates complex formation between CuI with C–N ligands.57
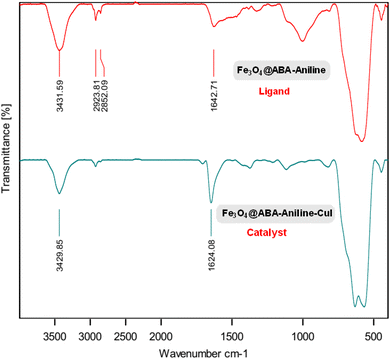 |
| Fig. 2 FT-IR spectra of Fe3O4@ABA-Aniline ligand and Fe3O4@ABA-Aniline-CuI nanocatalyst. | |
Scanning electron microscopy (SEM)
Scanning electron microscopy (SEM) shows images of the surface of Fe3O4@ABA-Aniline-CuI catalyst with high magnification (Fig. 3). In this analysis, the surface of the catalyst is shown at high magnification and the SEM image confirms the sphericity of Fe3O4@ABA-Aniline-CuI nanoparticles.
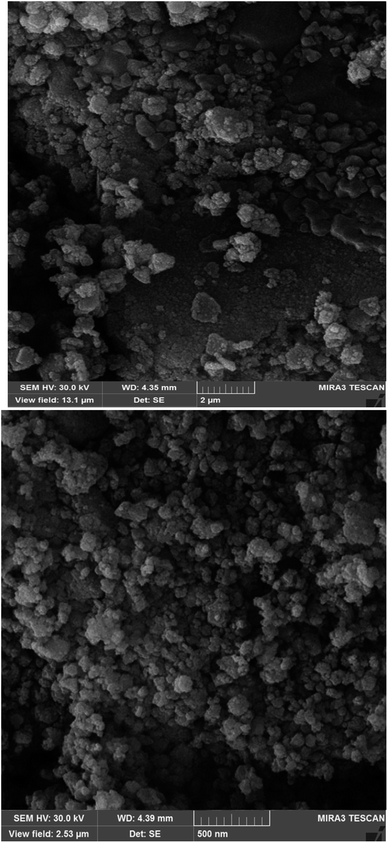 |
| Fig. 3 SEM images of Fe3O4@ABA-Aniline-CuI nanocatalyst at different magnifications. | |
Transmission electron microscopy (TEM)
Transmission electron microscopy (TEM) was used to accurately determine the shape and size of Fe3O4@ABA-Aniline-CuI particles. As shown in Fig. 4, the shape of the Fe3O4@ABA-Aniline-CuI particles is spherical and the size of the particles is approximately between 12–25 nanometers (nm).
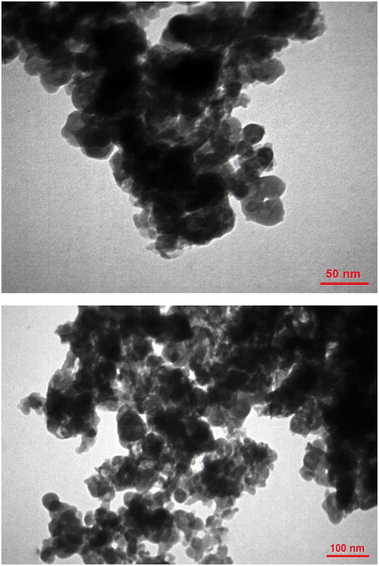 |
| Fig. 4 TEM images of Fe3O4@ABA-Aniline-CuI nanocatalyst at different magnifications. | |
X-ray diffraction analysis (XRD)
X-ray diffraction analysis (XRD) was used to determine the crystal structure and purity of the Fe3O4@ABA-Aniline-CuI nanocatalyst (Fig. 5). The peaks that appeared are attributed to the (220), (311), (400), (422), (511) and (440) planes, which indicate that the structure of the iron nanoparticle (Fe3O4) is maintained during functionalization.58
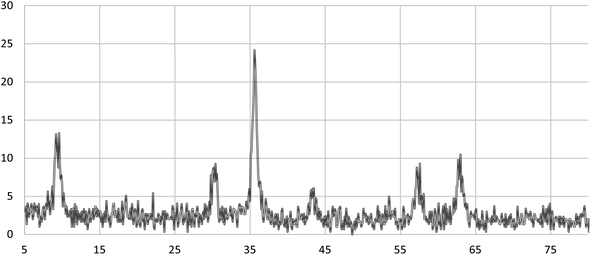 |
| Fig. 5 XRD analysis of Fe3O4@ABA-Aniline-CuI nanocatalyst. | |
Energy dispersive X-ray (EDX)
Energy dispersive X-ray spectroscopy (EDX) was applied in order to identify the successful formation of Fe3O4@ABA-Aniline-CuI nanocatalyst. As shown in Fig. 6, the presence of the O peak confirms that the magnetic iron nanoparticle is surrounded by 4-aminobenzoic acid. Also, in this spectrum, the peaks of Fe, N and Cu elements can be seen, which is a confirmation of the successful synthesis of the catalyst.
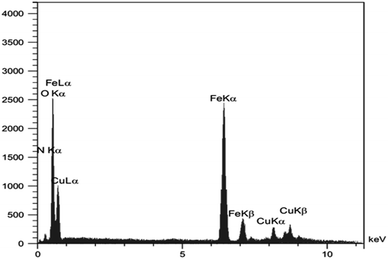 |
| Fig. 6 EDX analysis of Fe3O4@ABA-Aniline-CuI nanocatalyst. | |
Vibrating sample magnetometer (VSM)
The magnetic property of the synthesized nanocatalyst (Fe3O4@ABA-Aniline-CuI) was determined and investigated using a vibrating-sample magnetometer (VSM). As seen in Fig. 7, the magnetic property of the magnetic iron nanoparticle is 73.18 emu g−1. By functionalizing the surface of the nanoparticle with Fe3O4@ABA-Aniline-CuI, this property was decreased to 36.07 emu g−1, which indicates the stabilization of organic groups on the surface of the nanocatalyst.
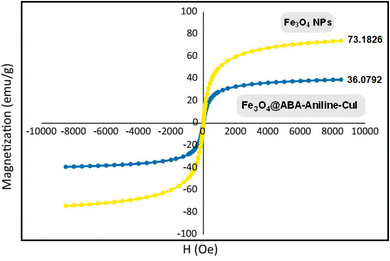 |
| Fig. 7 VSM analysis of Fe3O4 NPs and Fe3O4@ABA-Aniline-CuI nanocatalyst. | |
Thermogravimetric analysis (TGA)
Thermogravimetric analysis (TGA) was used to determine the percentage of organic functional groups stabilized on the surface of the magnetic nanoparticles (Fig. 8). The organic groups adsorbed on the nanoparticle surface were decomposed at a high temperature of 260 °C. The weight loss of 17% at temperatures between 250–700 °C is related to the decomposition of organic groups stabilized on the magnetic iron nanoparticles. In total, TGA analysis showed that the catalyst has a weight loss of about 22.9%.
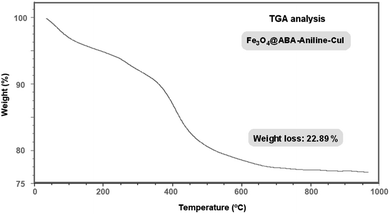 |
| Fig. 8 TGA analysis of Fe3O4@ABA-Aniline-CuI nanocatalyst. | |
Inductively coupled plasma optical emission spectroscopy (ICP-OES)
ICP-OES analysis was used to determine the amount of Cu immobilized on the surface of the magnetic nanoparticles and it was determined that the amount of copper is 13.28 × 10−5 mmol g−1.
Catalytic study
At the beginning of the laboratory work, the reaction of 2-iodoaniline (1, 0.5 mmol) with carbon disulfide (2, 1 mmol) and iodobenzene (3, 0.5 mmol) was selected as the model reaction and the optimization parameters for this reaction were investigated. First, the effect of the catalyst was evaluated on the preparation of model product 4a (Table 1): no product was observed in the absence of catalyst. To investigate the effect of the catalyst, the model reaction was investigated in the presence of different catalysts [Fe3O4 NPs (5 mg), Fe3O4@ABA (5 mg), Fe3O4@ABA-BA (5 mg), Fe3O4@ABA-Aniline (5 mg) and Fe3O4@ABA-Aniline-CuI (5 mg)]. The maximum yield was seen when the model reaction was catalyzed by Fe3O4@ABA-Aniline-CuI nanocatalyst. Then, the effect of the catalyst amount on the progress of the reaction was investigated and it was found that amounts greater than 20 mg of Fe3O4@ABA-Aniline-CuI catalyst do not have much effect on the progress of the reaction. In this reaction, the nature of the solvent plays a vital role in the activity of the catalyst and the yield of the products. It is evident from the results obtained in Table 2 that the best result is obtained in polyethylene glycol 400 (PEG-400) as solvent at 100 °C. The product 4a was obtained in good yields when the model reaction was carried out in dimethyl sulfoxide, dimethyl formamide and ethanol solvents. Also, the results showed that water solvent is not favorable for this reaction. Only 36% and 6% of product 4a were obtained in toluene and solvent-free conditions, respectively.
Table 1 Catalyst effect on the preparation of model product 4a
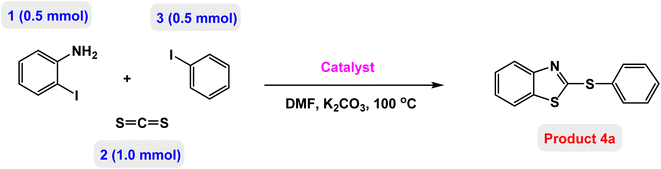
|
Entry |
Catalyst (mg) |
Time (h) |
Yielda (%) |
Isolated yields. |
1 |
No catalyst |
24 |
No |
2 |
Fe3O4 NPs (5 mg) |
6 |
4 |
3 |
Fe3O4@ABA (5 mg) |
6 |
9 |
4 |
Fe3O4@ABA-BA (5 mg) |
6 |
5 |
5 |
Fe3O4@ABA-Aniline (5 mg) |
6 |
10 |
6 |
CuI (5 mg) |
6 |
37 |
7 |
Fe3O4@ABA-Aniline-CuI (5 mg) |
6 |
62 |
8 |
Fe3O4@ABA-Aniline-CuI (10 mg) |
6 |
75 |
9 |
Fe3O4@ABA-Aniline-CuI (15 mg) |
6 |
81 |
10 |
Fe3O4@ABA-Aniline-CuI (20 mg) |
6 |
86 |
11 |
Fe3O4@ABA-Aniline-CuI (25 mg) |
6 |
86 |
Table 2 Solvent effect on the preparation of model product 4a
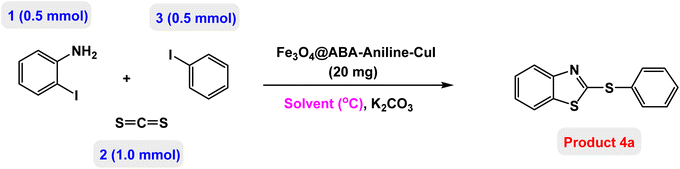
|
Entry |
Solvent (°C) |
Time (h) |
Yielda (%) |
Isolated yields. |
1 |
DMF (100 °C) |
6 |
86 |
2 |
EtOH (reflux) |
6 |
83 |
3 |
H2O (reflux) |
6 |
52 |
4 |
DMSO (100 °C) |
6 |
89 |
5 |
Toluene (100 °C) |
6 |
36 |
6 |
PEG-400 (100 °C) |
6 |
91 |
7 |
PEG-400 (110 °C) |
6 |
91 |
8 |
PEG-400 (120 °C) |
6 |
89 |
9 |
PEG-400 (90 °C) |
6 |
87 |
10 |
Solvent-free (100 °C) |
24 |
6 |
Next, the role of the base in the model reaction was investigated and the reaction was carried out in the presence of different bases (Table 3). A category of bases was used for the synthesis of product 4a; the reaction in the presence of two bases, potassium carbonate (K2CO3) and potassium acetate (KOAc) bicarbonate, gave the best results and KOAc was chosen as the optimal base. Then, to expand the scope of application of this catalytic system, a number of aryl and heteroaryl iodides were used for the synthesis of benzothiazole-sulfide aryl derivatives and the results of these experiments are summarized in Table 4. As shown in Table 4, iodobenzene derivatives carrying electron-withdrawing and electron-donating groups obtain products in high to excellent yields. Also, various derivatives of heteroaryl iodides were used in the reaction with carbon disulfide and 2-iodoaniline and the benzothiazole-sulfide heteroaryl products were synthesized with high yields. Moreover, aryl bromides were found to be more easily reactive than aryl chlorides due to the latter being less reactive as electrophilic partners. This is because the reactivity of electrophilic partners is based on their leaving groups, with iodine being the most reactive followed by bromine, chlorine, and fluorine. Chloride electrophiles are the least reactive as they are less willing to participate in reactions.
Table 3 Base effect on the preparation of model product 4a
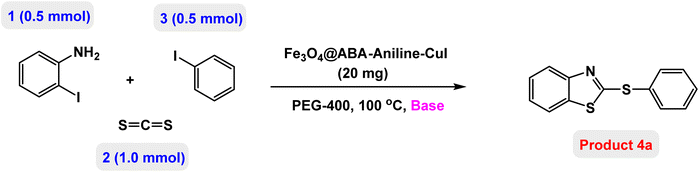
|
Entry |
Base |
Time (h) |
Yielda (%) |
Isolated yields. |
1 |
K2CO3 |
6 |
91 |
2 |
Pyridine |
6 |
72 |
3 |
DABCO |
6 |
61 |
4 |
Et3N |
6 |
82 |
5 |
Cs2CO3 |
6 |
90 |
6 |
NaOH |
6 |
55 |
7 |
t-BuOK |
6 |
13 |
8 |
DBU |
6 |
80 |
9 |
KOAc |
6 |
94 |
10 |
No base |
24 |
No |
Table 4 Scope of Fe3O4@ABA-Aniline-CuI nanocatalyst in synthesis of benzothiazole-sulfide arylsa,b,c
Based on previous reports on the synthesis of benzothiazoles and diaryl sulfides in the presence of copper catalysts, we propose the following scheme for the synthesis of benzothiazole-sulfide aryls (product 4a as model reaction) catalyzed by Fe3O4@ABA-Aniline-CuI nanocomposite (Scheme 2).
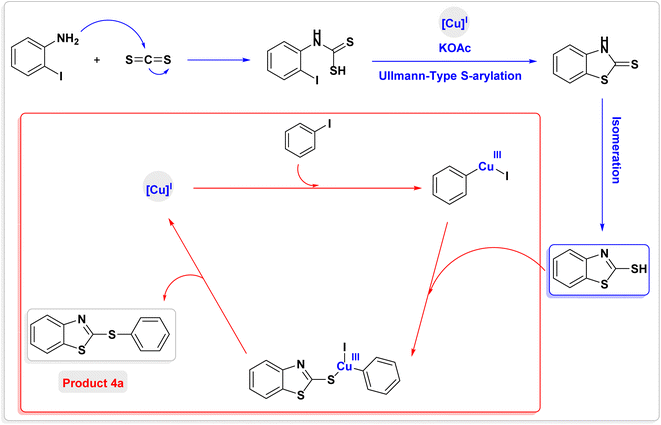 |
| Scheme 2 Plausible mechanism for preparation of benzothiazole-sulfide aryls (product 4a as model reaction) catalyzed by Fe3O4@ABA-Aniline-CuI nanocomposite. | |
Reusability of Fe3O4@ABA-Aniline-CuI nanocatalyst
The possibility of recycling and reusing a catalyst in catalytic reactions is a very valuable factor. To achieve this goal, the reusability of Fe3O4@ABA-Aniline-CuI nanocatalyst was evaluated for the synthesis of product 4d (as a model reaction) under the standardized conditions. After completion of the reaction, the catalyst was isolated by applying an external magnetic field. Then, the recovered catalyst was washed with ethyl acetate three times and used for the next reaction. The results clearly showed that the Fe3O4@ABA-Aniline-CuI catalyst can be reused at least 7 times without significant reduction in its catalytic activity (Fig. 9). ICP-OES analysis was used to determine the amount of Cu in the structure of the catalyst after 7 runs and results confirmed that the amount of copper is 13.22 × 10−5 mmol g−1. Also, SEM and TEM techniques were used to study the structure and shape of the recovered nanocatalyst after 7 runs. As shown in Fig. 10 and 11, the shape of the nanoparticles is spherical and a little clumping and accumulation is observed in the nanoparticle structure.
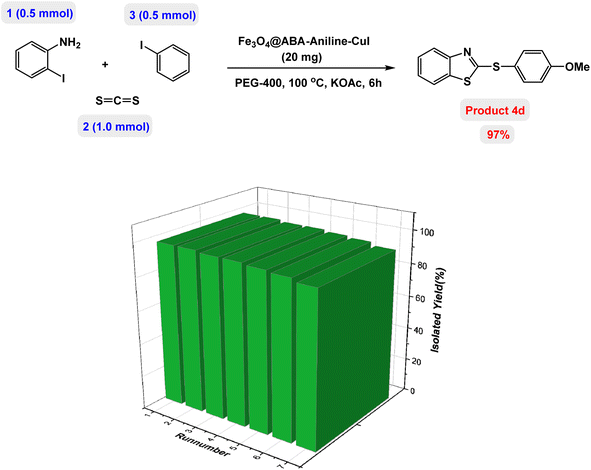 |
| Fig. 9 Reusability of Fe3O4@ABA-Aniline-CuI nanocatalyst in preparation of product 4d. | |
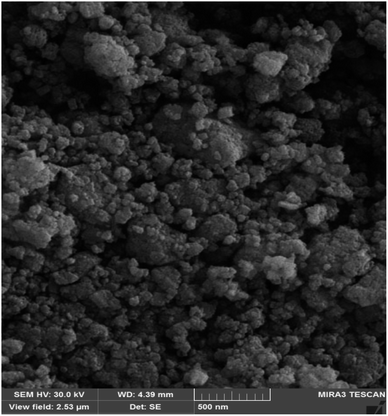 |
| Fig. 10 SEM image of the recovered Fe3O4@ABA-Aniline-CuI nanocatalyst after 7 runs. | |
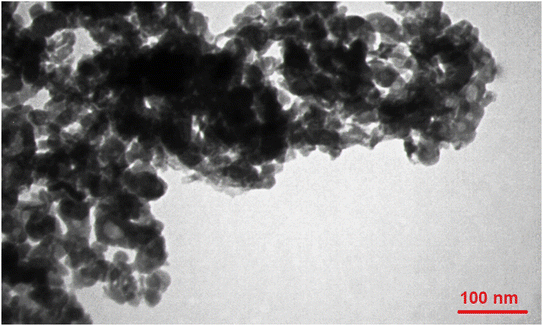 |
| Fig. 11 TEM image of the recovered Fe3O4@ABA-Aniline-CuI nanocatalyst after 7 runs. | |
Hot filtration and metal leaching tests
The nature of Fe3O4@ABA-Aniline-CuI composite catalyst was tested by hot filtration and ICP-OES metal leaching tests. The results showed that when the solid catalyst was removed, the conversion rate was only 1%, similar to the reaction without a catalyst. However, the ICP-OES analysis revealed that there was minimal Cu leaching into the reaction medium, indicating that the active components of the catalyst remained intact during the reaction.
Conclusion
In this paper, CuI was successfully immobilized on the surface of magnetic Fe3O4 nanoparticles modified with aniline and 4-aminobenzoic acid and its catalytic activity was investigated in the preparation of a broad range of benzothiazole-sulfide aryls and heteroaryls through the one-pot three-component reactions of 2-iodoaniline with carbon disulfide and aryl or heteroaryl iodides in the presence of KOAc as base in PEG-400 as solvent. The preparation of the catalyst from cheap and available raw materials, the efficiency of the catalyst in performing the reaction and its easy separation by applying an external magnetic field are the most important advantages of this catalytic system. The recycling results clearly showed that the Fe3O4@ABA-Aniline-CuI catalyst can be reused at least 7 times without significant reduction in its catalytic activity.
Experimental
Materials and methods
The chemicals and solvents used were purchased from Merck and Sigma-Aldrich. The purity of the products and the progress of the reactions were checked by TLC on silica gel plates (SILG/UV254). FTIR (USA, PerkinElmer, 400–4000 cm−1) was used to identify the catalyst functional groups. XRD patterns were examined at 2 theta = 20–80° (1.5405 Å = XRD-BRUKER) to define the nanoparticle crystallography. A STA503 instrument (Germany, BAHR, 30 °C to 800 °C, 10 °C min−1 rising rate, 70 cm3 min−1 argon flow) was used for thermogravimetric analysis. EDX analysis (VEGA II Detector, TESCAN, Czech Republic) determined the elemental components on the heterogeneous catalyst surface. FESEM (FESEM/TE/SCAN, Philips) and TEM (TEM/CM 120, Philips) analyses examined the catalyst surface morphology. A vibrating sample magnetometer (VSM, model EZ-9, G. Colombo 81, 20133 Milano, Italy) measured the nanocatalyst's magnetic characteristics.
Preparation of Fe3O4@ABA-Aniline-CuI nanocomposite
First, Fe3O4 magnetic particles were synthesized through co-precipitation of Fe2+/Fe3+ salt solution in an alkaline environment as previously reported.59 The nanoparticles of Fe3O4 (1.0 g) were ultrasonically dispersed in a solution containing ethanol (100 ml) by ultrasonic irradiation for 30 minutes. Then, an ethanolic solution of 4-aminobenzoic acid (3 mmol in 10 ml of ethanol) was added dropwise to the resulting suspension. After stirring for 2 h at reflux temperature, the Fe3O4@ABA particles were magnetically separated from the suspension and washed with DI water and ethanol. The desired magnetic nanoparticles were dried in the vacuum oven at 50 °C for 4 h. Aniline was introduced to the Fe3O4@ABA MNPs using a two-step procedure. The magnetic Fe3O4@ABA (1.0 g) was dispersed in 100 ml of ethanol by ultrasonic irradiation for 30 min. Then, biacetyl (3 mmol) was added to the reaction medium. After stirring for 10 h at reflux temperature, the as-prepared magnetic Fe3O4@ABA-BA powder was magnetically separated from the suspension, rinsed with ethanol and dried in the vacuum oven at 50 °C for 4 h. In the next step, 1.0 g of dried magnetic Fe3O4@ABA-BA dispersed in 100 ml ethanol (ultrasonication for 30 min) was treated with 3 mmol aniline. After stirring for 10 h at reflux conditions in an inert gas atmosphere, the Fe3O4@ABA-Aniline nanocomposite particles were separated by magnetic decantation and the obtained powder was rinsed twice with ethanol to remove excess aniline. The final particles were dried in an oven at 60 °C for 4 h. To synthesize Fe3O4@ABA-Aniline-CuI nanocatalyst, Fe3O4@ABA-Aniline (1.0 g) powder was sonicated for 30 min in 100 ml of DMF. Then, 3 mmol of CuI salt was added and the suspension was refluxed for 4 h in an inert gas atmosphere at 80 °C. The prepared particles were magnetically separated from the mixture and washed with ethanol three times. A vacuum oven was used to dry the final nanoparticles at 40 °C (Scheme 1).
General procedure for preparation of benzothiazole-sulfide aryls catalyzed by Fe3O4@ABA-Aniline-CuI nanocomposite
In a round bottomed flask, a mixture of 2-iodoaniline (0.5 mmol), carbon disulfide (1 mmol), KOAc (1.5 equiv) and Fe3O4@ABA-Aniline-CuI catalyst (20 mg) was stirred in PEG-400 at 100 °C for 2 h. Then, the aryl and heteroaryl iodides (0.5 mmol) were added to the reaction mixture and the reaction proceeded for 4 h, monitored by thin-layer chromatography (TLC). The Fe3O4@ABA-Aniline-CuI catalyst was easily separated with an external magnet, the organic layer was separated, and the aqueous layer was extracted with ethyl acetate. The obtained organic phase was dried over Na2SO4 and concentrated in vacuo. The crude material was purified with a chromatography column on silica gel (gradient eluent of EtOAc/petroleum ether) to give the benzothiazole-disulfide aryl and heteroaryl products.
NMR data for several examples of benzothiazole-sulfide aryls and heteroaryls
2-(Phenylthio)benzo[d]thiazole. 1H NMR (500 MHz, CDCl3) δ 8.04–8.01 (m, 2H), 7.62–7.60 (m, 2H), 7.59–7.45 (m, 5H); 13C NMR (126 MHz, CDCl3) δ 162.1, 135.9, 135.6, 134.8, 134.2, 130.5, 129.3, 129.2, 128.3, 127.2, 127.0, 126.1, 125.7, 124.3, 123.4.
2-(p-Tolylthio)benzo[d]thiazole. 1H NMR (500 MHz, CDCl3) δ 7.96 (dd, J = 7.8, 1.3 Hz, 1H), 7.54–7.51 (m, 2H), 7.51–7.47 (m, 3H), 7.46–7.42 (m, 2H), 7.40–7.26 (m, 1H), 2.49 (s, 3H); 13C NMR (126 MHz, CDCl3) δ 163.2, 138.4, 137.7, 135.9, 132.9, 132.7, 129.5, 129.3, 127.6, 1272, 124.8, 21.8.
2-((4-Ethylphenyl)thio)benzo[d]thiazole. 1H NMR (400 MHz, CDCl3) δ 8.08–8.02 (m, 2H), 7.62–7.56 (m, 1H), 7.56–7.42 (m, 2H), 7.42–7.30 (m, 2H), 7.28–7.24 (m, 1H), 2.30 (s, 2H), 1.3 (s, 3H); 13C NMR (101 MHz, CDCl3) δ 159.6, 143.6, 137.7, 136.4, 132.6, 130.8, 129.2, 128.7, 126.5, 125.8, 124.7, 26.5, 20.7.
2-((4-Methoxyphenyl)thio)benzo[d]thiazole. 1H NMR (600 MHz, CDCl3) δ 8.02 (d, J = 9.1 Hz, 2H), 7.60 (m, 2H), 7.45–7.43 (m, 2H), 6.97 (d, J = 9.0 Hz, 2H), 3.77 (s, 3H); 13C NMR (126 MHz, CDCl3) δ 158.6, 154.0, 136.1, 128.7, 128.4, 128.4, 128.2, 127.6, 113.8, 55.6.
2-((4-Nitrophenyl)thio)benzo[d]thiazole. 1H NMR (500 MHz, CDCl3) δ 8.07–8.02 (m, 2H), 7.51–7.50 (m, 2H), 7.50–7.43 (m, 2H), 7.19–7.15 (m, 2H); 13C NMR (126 MHz, CDCl3) δ 166.1, 164.0, 158.7, 136.1, 133.1, 133.1, 131.1, 131.0, 129.6, 129.3, 128.0, 117.0, 116.9.
1-(4-(Benzo[d]thiazol-2-ylthio)phenyl)ethan-1-one. 1H NMR (500 MHz, CDCl3) δ 8.11 (d, J = 8.0 Hz, 2H), 8.06 (d, J = 7.9 Hz, 2H), 7.52 (m, 2H), 7.50–7.46 (m, 2H), 2.67 (s, 3H); 13C NMR (151 MHz, CDCl3) δ 197.4, 163.7, 141.6, 139.9, 135.0, 130.8, 129.4, 128.6, 126.7, 125.7, 25.9.
2-((3-Methoxyphenyl)thio)benzo[d]thiazole. 1H NMR (500 MHz, CDCl3) δ 8.15 (d, J = 8.4 Hz, 2H), 8.06 (d, J = 8.6 Hz, 2H), 7.53–7.49 (m, 2H), 7.49–7.44 (m, 2H), 3.96 (s, 3H); 13C NMR (126 MHz, CDCl3) δ 165.1, 166.0, 138.9, 133.0, 133.4, 129.9, 128.7, 127.3, 126.4, 125.8, 52.8.
2-(Pyridin-2-ylthio)benzo[d]thiazole. 1H NMR (500 MHz, CDCl3) δ 9.24 (d, J = 1.7 Hz, 1H), 8.82 (dd, J = 4.8, 1.6 Hz, 1H), 8.28 (ddd, J = 8.0, 2.2, 1.7 Hz, 1H), 7.57–7.45 (m, 4H), 7.44 (ddd, J = 8.0, 4.9, 0.8 Hz, 1H); 13C NMR (126 MHz, CDCl3) δ 161.8, 155.2, 149.7, 136.0, 135.8, 132.3, 129.9, 128.4, 126.3, 122.6.
2-(Furan-2-ylthio)benzo[d]thiazole. 1H NMR (400 MHz, CDCl3) δ 8.02 (d, J = 9.0 Hz, 2H), 7.43 (d, J = 8.9 Hz, 2H), 6.97 (d, J = 8.9 Hz, 2H), 6.91 (d, J = 9.0 Hz, 1H); 13C NMR (101 MHz, CDCl3) δ 164.6, 161.4, 137.5, 130.1, 129.4, 119.1, 115.4, 114.1.
2-((1-Methyl-1H-benzo[d]imidazole-2-yl)thio)benzo[d]thiazole. 1H NMR (400 MHz, CDCl3) δ 8.13 (d, J = 8.1 Hz, 1H), 7.87 (d, J = 8.3 Hz, 1H), 7.79 (dd, J = 8.2, 1.1 Hz, 1H), 7.60 (dd, J = 7.1, 1.2 Hz, 1H), 7.51–7.41 (m, 3H), 2.32 (s, 3H); 13C NMR (101 MHz, CDCl3) δ 163.8, 136.0, 134.2, 132.6, 128.7, 126.4, 125.1, 124.9, 123.1, 122.1, 31.0.
Conflicts of interest
There are no conflicts to declare.
References
- M. J. Genzink, J. B. Kidd, W. B. Swords and T. P. Yoon, Chem. Rev., 2022, 122, 1654–1716 CrossRef CAS PubMed.
- A. D. Zahra Hoseini, Adv. J. Chem. A, 2021, 4, 68–77 Search PubMed.
- J. Luo, Y. Liu, H. Wang, C. Gong, Z. Zhou and Q. Zhou, Heterocycles, 2022, 104, 123 CrossRef.
- Z. Zhang, Z.-W. Hou, H. Chen, P. Li and L. Wang, Green Chem., 2023, 25, 3543–3548 RSC.
- X. Lei, Q. Tang, Y. Zheng, P. Kidkhunthod, X. Zhou, B. Ji and Y. Tang, Nat. Sustain., 2023, 1–11 Search PubMed.
- A. Dehno Khalaji, M. Jarosova and P. Machek, Asian J. Green Chem., 2021, 5, 351–358 Search PubMed.
- M. B. Chaudhari and B. Gnanaprakasam, Chem. – Asian J., 2019, 14, 76–93 CrossRef CAS PubMed.
- S. Gupta, J. Synth. Chem., 2022, 1, 37–41 Search PubMed.
- R. Qiu, W. Wang, Z. Wang and H. Wang, Catal. Sci. Technol., 2023, 13, 2566–2584 RSC.
- L. Kong, H. Sun, Y. Nie, Y. Yan, R. Wang, Q. Ding, S. Zhang, H. Yu and G. Luan, Molecules, 2023, 28, 2681 CrossRef CAS PubMed.
- W. Guo, H. Luo, Z. Jiang, D. Fang, J. Chi, W. Shangguan, Z. Wang, L. Wang and A. F. Lee, ACS Catal., 2022, 12, 12000–12013 CrossRef CAS.
- H. Li, S. Zhao, W. Zhang, H. Du, X. Yang, Y. Peng, D. Han, B. Wang and Z. Li, Fuel, 2023, 342, 127786 CrossRef CAS.
- J. Liu, X. Qu, C. Zhang, W. Dong, C. Fu, J. Wang and Q. Zhang, J. Cleaner Prod., 2022, 377, 134228 CrossRef CAS.
- B. Ji, J. Gou, Y. Zheng, X. Pu, Y. Wang, P. Kidkhunthod and Y. Tang, Adv. Mater., 2023, 2300381 CrossRef CAS PubMed.
- F. Dhaouadi, L. Sellaoui, S. Taamalli, F. Louis, A. El Bakali, T. R. S. Cadaval Junior, A. Bonilla-Petriciolet, J. L. Marques Junior, A. VallerãoIgansi, T. S. Frantz, S. Frantz lütke, G. L. Dotto, L. A. De Almeida Pinto and A. Ben Lamine, J. Mol. Liq., 2021, 343, 117617 CrossRef CAS.
- H. Yu, J. Zhu, R. Qiao, N. Zhao, M. Zhao and L. Kong, ChemistrySelect, 2022, 7(2), e202103668 CrossRef CAS.
- Z. Wan, T. Zhang, Y. Liu, P. Liu, J. Zhang, L. Fang and D. Sun, Environ. Res., 2022, 213, 113637 CrossRef CAS.
- D. Chen and T. Savidge, Science, 2015, 349, 936 CrossRef CAS PubMed.
- P. Dong, Y. Zhang, S. Zhu, Z. Nie, H. Ma, Q. Liu and J. Li, Metals, 2022, 12, 1160 CrossRef CAS.
- J. Singh, S. Juneja, R. K. Soni and J. Bhattacharya, J. Colloid Interface Sci., 2021, 590, 60–71 CrossRef CAS PubMed.
- L. Kong, Y. Liu, L. Dong, L. Zhang, L. Qiao, W. Wang and H. You, Dalton Trans., 2020, 49, 1947–1954 RSC.
- M. Ghobadi, J. Synth. Chem., 2022, 1, 84–96 Search PubMed.
- B. Baghernejad and A. Zakariayi, Asian J. Nanosci. Mater., 2022, 5, 225–233 CAS.
- G. Xia, Y. Zheng, Z. Sun, S. Xia, Z. Ni and J. Yao, Environ. Sci. Pollut. Res., 2022, 29, 39441–39450 CrossRef CAS PubMed.
- Z. Wang, C. Chen, H. Liu, D. Hrynshpan, T. Savitskaya, J. Chen and J. Chen, Sci. Total Environ., 2020, 708, 135063 CrossRef CAS.
- B. B. L. Nazari, Eurasian Chem. Commun., 2021, 3, 319–326 Search PubMed.
- P. Xu, Q. Yuan, W. Ji, R. Yu, F. Wang and N. Huo, Mater. Express, 2022, 12, 1493–1501 CrossRef CAS.
- M. Ghobadi, M. Kargar Razi, R. Javahershenas and M. Kazemi, Synth. Commun., 2021, 51, 647–669 CrossRef CAS.
- Y. Liu, B. Fan, B. Xu and B. Yang, Mater. Lett., 2023, 337, 133979 CrossRef CAS.
- L. Wang, B. Ji, Y. Zheng and Y. Tang, Angew. Chem., Int. Ed., 2023, 62(18), e202301711 CrossRef CAS PubMed.
- M. Kazemi and M. Ghobadi, Nanotechnol. Rev., 2017, 6, 549–571 CAS.
- H. Chen, C. Xu, F. Zhao, C. Geng, Y. Liu, J. Zhang, Q. Kang and Z. Li, Appl. Surf. Sci., 2023, 609, 155447 CrossRef CAS.
- Z. Wang, L. Dai, J. Yao, T. Guo, D. Hrynsphan, S. Tatsiana and J. Chen, Chemosphere, 2021, 281, 130718 CrossRef CAS PubMed.
- R. Hudson, Y. Feng, R. S. Varma and A. Moores, Green Chem., 2014, 16, 4493–4505 RSC.
- M. Lakshman, J. Synth. Chem., 2022, 1, 48–51 Search PubMed.
- V. K. Booramurthy, R. Kasimani, S. Pandian and D. Subramanian, Arab. J. Sci. Eng., 2022, 47, 6341–6353 CrossRef CAS.
- W. Huang, Q. Cheng and D. Ma, Synth. Commun., 2021, 51, 1321–1339 CrossRef CAS.
- N. Moeini, M. Ghadermazi and S. Molaei, J. Mol. Struct., 2022, 1251, 131982 CrossRef CAS.
- N. Alishahi, M. Nasr-Esfahani, I. Mohammadpoor-Baltork, S. Tangestaninejad, V. Mirkhani and M. Moghadam, Appl. Organomet. Chem., 2020, 34(8), e5681 CrossRef CAS.
- D. Chen, Q. Wang, Y. Li, Y. Li, H. Zhou and Y. Fan, Chemosphere, 2020, 247, 125869 CrossRef CAS PubMed.
- X. Zhang, M. Aqeel Ashraf, Z. Liu and D. Zhang, Synth. Commun., 2020, 50, 2705–2734 CrossRef CAS.
- J. Le Bescont, C. Breton-Patient and S. Piguel, Eur. J. Org. Chem., 2020, 2020, 2101–2109 CrossRef CAS.
- X. Gao, J. Liu, X. Zuo, X. Feng and Y. Gao, Molecules, 2020, 25, 1675 CrossRef CAS PubMed.
- Z. Liu, B. Fan, J. Zhao, B. Yang and X. Zheng, Corros. Sci., 2023, 212, 110957 CrossRef CAS.
- Y. I. Asiri, A. Alsayari, A. B. Muhsinah, Y. N. Mabkhot and M. Z. Hassan, J. Pharm. Pharmacol., 2020, 72, 1459–1480 CrossRef CAS PubMed.
- H. T. Nguyen, T. H. Nguyen, D. D. Pham, C. T. Nguyen and P. H. Tran, Heliyon, 2021, 7, e08309 CrossRef CAS PubMed.
- S. Dhadda, A. K. Raigar, K. Saini, Manju and A. Guleria, Sustainable Chem. Pharm., 2021, 24(1), 100521 CrossRef CAS.
- R. Isshiki, M. B. Kurosawa, K. Muto and J. Yamaguchi, J. Am. Chem. Soc., 2021, 143, 10333–10340 CrossRef CAS PubMed.
- T. Shibata, T. Iwaki and M. Ito, Adv. Synth. Catal., 2022, 364, 3472–3476 CrossRef CAS.
- S. Gupta, J. Synth. Chem., 2022, 1, 16–21 Search PubMed.
- P. Shinde and C. S. Rout, Mater. Chem. Front., 2021, 5, 516–556 RSC.
- L. Chen, A. Noory Fajer, Z. Yessimbekov, M. Kazemi and M. Mohammadi, J. Sulfur Chem., 2019, 40(4), 451–468 CrossRef CAS.
- N. Sundaravelu, S. Sangeetha and G. Sekar, Org. Biomol. Chem., 2021, 19, 1459–1482 RSC.
- Z. Gan, Q. Yan, G. Li, Q. Li, X. Dou, G. Li and D. Yang, Adv. Synth. Catal., 2019, 361, 4558–4567 CrossRef CAS.
- G. Kibriya, A. K. Bagdi and A. Hajra, J. Org. Chem., 2018, 83, 10619–10626 CrossRef CAS PubMed.
- K. Monir, A. K. Bagdi, M. Ghosh and A. Hajra, J. Org. Chem., 2015, 80, 1332–1337 CrossRef CAS PubMed.
- T. Cheng, D. Zhang, H. Li and G. Liu, Green Chem., 2014, 16, 3401–3427 RSC.
- M. F. Kamel Ariffin and A. Idris, Renewable Energy, 2022, 185, 1362–1375 CrossRef CAS.
- H. Khandaka and R. Kumar Joshi, Tetrahedron Lett., 2022, 111, 154163 CrossRef CAS.
|
This journal is © The Royal Society of Chemistry 2023 |
Click here to see how this site uses Cookies. View our privacy policy here.