DOI:
10.1039/D3RA02036C
(Paper)
RSC Adv., 2023,
13, 14210-14216
The solvent effect on the morphology and molecular ordering of benzothiadiazole-based small molecule for inkjet-printed thin-film transistors †
Received
29th March 2023
, Accepted 29th April 2023
First published on 10th May 2023
Introduction
Over the past few decades, inkjet printing techniques have been widely employed for the fabrication of various thin-film devices, such as field-effect transistors (OTFTs),1–5 light-emitting diodes (LEDs),6,7 solar cells,8–11 sensors,12–14 etc. These inkjet printing methods have garnered significant attention due to their potential benefits such as ultra-low-cost, non-vacuum, and environmentally friendly processability.1,15 Compared to the spin-coating technique, using inkjet techniques can minimize the waste of materials and simplify the manufacturing process. Furthermore, the materials are deposited via a solution process under mild conditions (i.e., room temperature, no vacuum assistance) during the inkjet printing process. This allows easy fabrication of flexible electronics on large-area substrates.16–18 Printed electronics can be applied to flexible substrates such as plastic, paper, and fabric, making them suitable for use in wearable devices, smart textiles, and other applications where flexibility is required. Furthermore, they can be easily integrated with other electronic components, such as sensors and batteries, facilitating the development of more complex systems and devices.
Conjugated polymers and small-molecules organic semiconductors have proven to be extremely effective materials in the development of printable electronic devices.19–26 There has been a growing interest in the small molecules-based optoelectronic application in recent years. Small molecules offer several advantages over polymer-based organic electronics, such as a well-defined chemical structure, molecular structure, and high purity, making them easy to reproduce.27–29 High-performance small molecule-based organic semiconductors are widely used in inkjet-printing devices due to their low-temperature processability and good solubility in various organic solvents, which are important advantages of the inkjet printing process.
Despite their potential benefits, there are numerous challenges that must be overcome in the development of p-type organic semiconductors to enable their widespread use in electronic devices. One of the key challenges is the attainment of high carrier mobility. Although significant advancements have been made in recent years, the mobility of p-type organic semiconductors generally remains lower than that of n-type organic semiconductors, which can restrict the overall performance and efficiency of devices employing p-type semiconductors. Another significant obstacle is the achievement of high stability and reliability of p-type organic semiconductors, particularly in harsh environments or over extended periods of use. Nevertheless, to realize flexible printed electronics, it is crucial to develop stable and durable p-type organic semiconductors. Moreover, printed TFTs are exposed to considerable quantities of H2O and O2 during the manufacturing process, which can exacerbate degradation during operation. Enhancing the molecular assembly between molecules can help minimize the capture of H2O and O2 in the channel, which can improve operational stability. Especially, the presence of insulating solubilizing groups, such as alkyl side chains, can hinder charge transport between molecules and affect the morphology of self-assembled films, thereby reducing intermolecular interaction. Hence, it is important to control the position of side chains on the molecular structure to avoid the twisted core and reduce π-conjugation. To address these issues, many researchers have investigated various small molecules with highly ordered structures and strong intermolecular interaction by controlling the ordering of the molecules, thereby enhancing the charge transport between them.30–34 By controlling the size and position of the alkyl chains and utilizing donor or acceptor moieties with high planarity and strong intermolecular interaction, molecular ordering between molecules can be improved.
In the present investigation, we have developed novel organic semiconductors, D(D′–A–D′)2, comprising benzothiadiazole (BT) as the acceptor (A) unit and 3-hexylthiophene (3HT) as the second donor (D′), to leverage the improved intermolecular interactions arising from the planar 3HT–BT–3HT structure.35–37 The attachment of hexyl chains to the fourth positions in the thiophene rings (from the central BT moiety) has facilitated solubility enhancement and avoided steric hindrance from insulating alkyl chains.35,38 Furthermore, the thiophene moiety as the donor unit in the middle of the system has played a pivotal role in boosting the π–π conjugated system, without compromising the planarity of the entire system. Finally, a new organic semiconductor material was successfully synthesized. In addition, we studied the effect of a dual solvent system with varying ratios of chloroform and toluene on the film morphology. A single solvent system, such as chlorobenzene, chloroform, or toluene, has demonstrated poor film morphologies and low crystallinity, resulting in extremely low carrier mobility in organic electronic devices.39–41 However, by modulating the ratios of CHCl3 to toluene, inkjet-printed TFT devices' electrical properties and uniformity have been substantially improved.
Experimental
General instruments and measurements
The small molecule was characterized by 1H and 13C NMR spectroscopy using a JEOL JNM-LA 400 FT-NMR at 25 °C. Differential scanning calorimetry (DSC) was performed on a TA instrument (DSC-TA Q-20 Instrument) at a 10 °C min−1 heating rate under N2. The absorptions of the small molecule, both in solution and as a film, were measured using a UV-vis spectrophotometer (Varian, Cary 5000). To prepare the film samples, 10 mg of a small molecule was dissolved in 1 ml of chloroform, and the film samples were prepared by spin-coating on a glass substrate. The molecular ordering and crystallinity of the thin films were confirmed by X-ray diffractometry using a Rigaku D/max-2500 diffractometer with Cu Kα radiation (λ = 1.5418 Å) at 40 kV and 100 mA. The surface roughness of the thin films was evaluated using an atomic force microscope (PSIA, XE-200).
Materials and synthesis
2,5-Bis(tributylstannyl)thiophene (97%), tetrakis(triphenylphosp-hine) palladium(0) (Pd(PPh3)4, 99%), n-bromosuccinimide (NBS, 99%), tetrahydrofuran (anhydrous, 99.9%), toluene (anhydrous, 99.8%) were purchased from Sigma-Aldrich company. 4,7-Dibromo-2,1,3-benzothiadiazole (98%), 4-hexyl-2-(4,4,5,5-tetramethyl-1,3,2-dioxaborolan-2-yl)thiophene (98%) were purchased from TCI company. All chemicals were used without further purification. 4,7-Bis(4-hexylthiophen-2-yl)benzo[c][1,2,5]thiazole (1) was prepared according to a previously published procedure.35
Synthesis of 4-(5-bromo-4-hexylthiophen-2-yl)-7-(4-hexylthiophen-2-yl)benzo[c][1,2,5] thiadiazole (2). A solution of 4,7-bis(4-hexylthiophen-2-yl)benzo[c][1,2,5] thiazole (1) (0.5 g, 1.07 mmol) in 12 ml of anhydrous THF was prepared in a 2-neck-flask. The mixture was degassed for 30 minutes and then n-bromosuccinimide (NBS) (0.21 mg, 1.17 mmol) dissolved in 10 ml of anhydrous THF was added dropwise over 30 minutes at 0 °C. The reaction was protected from light during the addition and stirred for an additional 30 minutes at 0 °C and 30 minutes at room temperature. The reaction mixture was then extracted with ethyl acetate and DI water, and the organic layer was dried over anhydrous Na2SO4 overnight. The solvent was removed by evaporation and the product was purified by column chromatography using hexane as the eluent. The yield was 72% (0.4 g) and the product was obtained as an orange solid. 1H NMR (400 MHz, CDCl3), δ (ppm): 7.98 (s, 1H), 7.81 (d, 1H), 7.76 (d, 1H), 7.35 (s, 1H), 7.04 (s, 1H), 2.70–2.61 (t, 4H), 1.69 (m, 4H), 1.51–1.27 (m, 12H), 0.88–0.86 (t, 6H). 13C NMR (100 MHz, CDCl3), δ (ppm): 152.6, 144.5, 143.1, 138.9, 138.7, 129.3, 126.4, 125.4, 125.0, 121.8, 111.4, 31.7, 30.7, 29.8, 29.1, 22.7, 14.2.
Synthesis of 7,7′-(3,3′′-dihexyl-[2,2′:5′,2′′-terthiophene]-5,5′′-diyl) bis(4-(4-hexylthiophen-2-yl)benzo[c][1,2,5]thiadiazole) (3HTBTT). Compound 2 (137 mg, 0.25 mmol), 2,5-bis(tributylstannyl)-thiophene (100 mg, 0.1 mmol), and Pd(PPh3)4 (13.8 mg, 0.012 mmol) were dissolved in 15 ml of anhydrous toluene and degassed with nitrogen for 30 min before refluxing at 90 °C for 7 h under an argon atmosphere. The reaction mixture was extracted with dichloromethane and DI-water and dried over anhydrous Na2SO4. The solvent was removed by evaporation, and the product was purified by column chromatography (hexane: CH2Cl2) to afford a dark purple solid (68 mg, yield: 68%). 1H NMR (400 MHz, CDCl3), δ (ppm): 8.02–8.01 (d, 4H), 7.86 (s, 2H), 7.28 (s, 4H), 7.05 (s, 2H), 2.74–2.71 (t, 8H), 1.81 (m, 8H), 1.53–1.28 (m, 24H), 0.95–0.92 (t, 12H). 13C NMR (100 MHz, CDCl3), δ (ppm): 153.1, 144.7, 140.6, 139.0, 137.0, 131.9, 130.9, 129.0, 126.3, 125.1, 125.3, 121.0, 32.2, 30.4, 29.7, 29.2, 22.4, 13.8. Anal. calcd for C56H64N4S7 (%): C, 66.10; H, 6.34; N, 5.51. Found: C, 66.05; H, 6.32; N, 5.48.
Devices fabrication and characterization of inkjet printing TFT
The hole-only device was fabricated by the following process. Patterned glass/ITO substrates (with a sheet resistance of 20 Ω per in.2) were procured commercially and subjected to a rigorous cleaning process involving sonication in water, acetone, and isopropyl alcohol (IPA) for a duration of 10 minutes. The cleaned substrates were then treated with O2 plasma for 1 minute at a power of 50 W. A uniform layer of PEDOT: PSS (Baytron AI4083) with a thickness of 50 nm was subsequently deposited on the ITO glass surface using a spin-coating process. The organic film was then formed on the PEDOT: PSS layer using inkjet printing. Finally, a shadow mask was utilized to deposit a 10 nm-thick layer of MoO3 and a 100 nm-thick layer of Ag electrode through thermal vacuum evaporation. The hole-only devices were structured as ITO/PEDOT: PSS/organic film/MoO3/Ag.
The TFT device was fabricated on a pre-patterned FET device that was designed on a p-doped Si gate substrate with a SiO2 layer of 300 nm thickness. The top source/drain electrodes, consisting of chromium (Cr) (5 nm) and gold (Au) (80 nm), were separated by varying channel distances of 20 to 150 μm. Semiconductor material was inkjet printed on the pre-patterned FET devices using different solvent systems. The film was subsequently dried in an 80 °C oven for 60 minutes. Each transfer and output curve was measured using a Keithley 4200 semiconductor characterization system at room temperature and under a vacuum pressure of 10−4 to 10−5 Torr. Mobility was calculated by
Results and discussion
Synthesis and characterization of 3HTBTT small molecules
Compound 2 was prepared by reacting 4,7-bis(4-hexylthiophen-2-yl)benzo[c][1,2,5] thiazole (1) with n-bromosuccinimide in anhydrous THF. Subsequently, 7,7′-(3,3′′-dihexyl-[2,2′:5′,2′′-terthiophene]-5,5′′-diyl)bis(4-(4-hexylthiophen-2-yl)benzo[c][1,2,5]-thiadiazole) small molecule (3HTBTT) was synthesized via stille coupling reaction of compound 2 and 2,5-bis(tributylstannyl) thiophene in the presence of Pd catalyst. The yield of the reaction was approximately 68%, as determined by NMR and elementary analysis (Scheme 1). The 1H NMR and 13C NMR of 3HTBTT are presented in ESI Fig. S2.† Due to the presence of two thiadiazole units, the chemical shift of this carbon nucleus (δ = 129.0 ppm) in the final product is likely shifted downfield compared to the corresponding carbon in compound 2. This is due to the electron-withdrawing effect of the thiadiazole rings. As we expected, the solubility of the final product in common organic solvents such as chloroform and THF was excellent due to the four hexyl chains. The self-assembly ability of the synthesized 3HTBTT was further evaluated using differential scanning calorimetry (DSC), which showed a glass temperature (Tg) of 94.9 °C (Fig. 1). The glass transition temperature (Tg) indicates the temperature at which a material undergoes a transition from a rigid, glassy state to a more flexible, rubbery state or vice versa, signifying a crucial point in the formation of amorphous glass. The relatively high Tg value of the material was attributed to non-covalent S⋯N interaction, indicating the ease of manipulating molecular alignment of 3HTBTT through well-organized structures and strong intermolecular interactions between molecules.42–46
 |
| Scheme 1 Synthesis route for 3HTBTT small molecule. | |
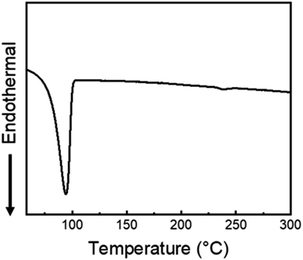 |
| Fig. 1 Differential scanning calorimetry (DSC) curve of 3HTBTT small molecule. The DSC showed a clear melting peak. | |
Optical properties
The UV-vis absorption spectra of 3HTBTT small molecule were shown in Fig. 2. The onset wavelength in the solid state (λonset = 709.4 nm) was red-shifted by approximately 100 nm compared to that of 3HTBTT in solution (λonset = 604.7 nm) due to the improved molecular ordering between molecules and improved π-stacking in the solid state.47–49 The optical band gap of the small molecule was also reduced from 2.05 eV in the solution to 1.75 eV in the film, which is consistent with the trend of λonset. All λmax, λonset, and optical band gaps (Eopg) are summarized in Table 1.
 |
| Fig. 2 UV absorption spectra of 3HTBTT small molecule in CHCl3 (black line) and solid-state film (red line). | |
Table 1 Optical properties of 3HTBTT small molecules
UV-vis absorption |
Material |
Solutiona |
Film |
λmax (nm) |
λonset (nm) |
Eopg b (eV) |
λmax (nm) |
λonset (nm) |
Eopg b (eV) |
Samples were prepared from chloroform solution. Optical band gap Eoptg was calculated from using the onset of the UV-vis spectrum (Eoptg = 1240/λonset). |
3HTBTT |
508.4 |
604.7 |
2.05 |
568.7 |
709.4 |
1.75 |
Film properties
To investigate the crystallinity, molecular ordering, and solvent effect on the morphology film before and after patterning with different ratios of CHCl3
:
toluene, XRD measurements were carried out (Fig. 3 and 4). The material was dissolved in different ratios of CHCl3
:
toluene, such as 0
:
1, 1
:
1, 1.5
:
1, and 2
:
1. The solvent plays a critical role in controlling the arrangement of molecules in the film.40,50 The fluidic dynamics in chloroform and toluene differ due to their influence on the ink's evaporation and convection behavior. Although the material readily dissolves in chloroform, its low boiling point of 61.15 °C, evaporation rate of 29.4 kJ mol−1, and combustion enthalpy of −473.21 kJ mol−1 impede the proper organization of the molecules during the drying process. In contrast, toluene higher boiling point of 110.6 °C, an evaporation rate of 38.064 kJ mol−1, and a combustion enthalpy of −3910.3 kJ mol−1. Therefore, a co-solvent system using CHCl3 and toluene effectively modulates the ink's fluidic dynamics without compromising the solubility of small molecules. Specific ratios of the co-solvent system provide the film with enough time to control the arrangement of molecules, resulting in enhanced crystallinity and morphology, as shown in Fig. 3 and 4.
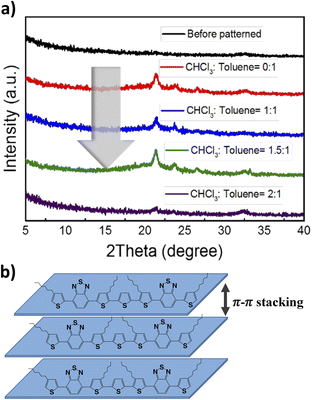 |
| Fig. 3 (a) XRD spectra of random 3HTBTT film (black line) and 3HTBTT film via inkjet printing with different ratios CHCl3 : toluene. (b) Schematic illustration of proposed 3HTBTT molecular arrangement after applying inkjet printing technique. | |
To provide a comprehensive comparison, a sample of randomly oriented 3HTBTT was fabricated using a spin-coating technique with a high boiling point solvent, but without heat treatment. However, due to the relatively low intermolecular interaction between the π–π orbitals of the small molecule compared to the polymer, the resulting film exhibited minimal self-assembly, and consequently, no diffraction peaks associated with the π–π intermolecular interaction between the molecules were observed. In contrast, the application of the inkjet printing technique resulted in the emergence of new peaks at 2θ = 21.38° corresponding to a d-spacing of 0.42 nm, as illustrated in Fig. 3. These peaks were attributed to the π–π stacking between the conjugated chains.45,46 It is postulated that the strong intermolecular interaction between the molecules was facilitated through solvent engineering during the inkjet process, improving the crystallinity of the films. The chemical arrangement of 3HTBTT after applying the inkjet printing technique is proposed as shown in Fig. 3b.
An increase in the volume of CHCl3 in the solvent mixture (CHCl3 and toluene) resulted in a stronger intensity of the diffraction peak related to π–π stacking, particularly when the ratio of CHCl3 to toluene was 1.5
:
1. This phenomenon can be attributed to the polarity of chloroform relative to toluene. However, as the ratio of chloroform was increased up to 2
:
1 compared to the volume of toluene, the peak associated with π–π stacking was observed to decrease. This was likely due to the rapid evaporation of the ink, which hindered the effective modulation of intermolecular interaction. Furthermore, the film morphology of inkjet-printed 3HTBTT on ITO substrate exhibited varying surface roughness depending on the ratio of CHCl3 to toluene (as shown in Fig. 4). The obtained surface roughness values were found to be 6.38 nm, 1.81 nm, 1.05 nm, and 10.02 nm for CHCl3 to toluene ratios of 0
:
1, 1
:
1, 1.5
:
1, and 2
:
1, respectively. It was observed that the XRD data showed a remarkable agreement with the AFM data, indicating a significant reduction in both aggregation and surface roughness of the thin films as the volume concentration of chloroform in the mixture was increased up to a ratio of 1.5
:
1. However, beyond this ratio, the thin film with the highest ratio of chloroform in the mixture exhibited the highest surface roughness. This confirms that the solvent mixture with the appropriate concentration induced the fine assembly of small molecules, thereby enhancing charge transport and ultimately leading to improved device performance.
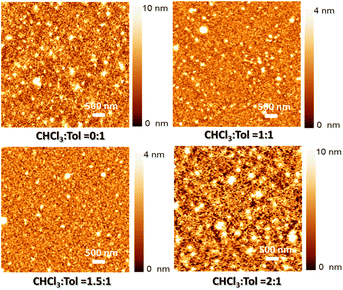 |
| Fig. 4 AFM images of 3HTBTT film via inkjet printing with different ratios CHCl3 : toluene. | |
Electrical properties of 3HTBTT film
To accurately evaluate the charge carrier transportation characteristics of molecular-scale ordered 3HTBTT films with varying ratios of CHCl3 and toluene, the hole mobility of each material was meticulously extracted from the corresponding hole-only device. To account for the asymmetry of the Fermi level in the PEDOT: PSS and MoO3 layers, a precisely calibrated built-in internal field of approximately 0.39 V was generated, thus ensuring that the measured J–V characteristics were accurately corrected by the corresponding built-in potential. Subsequently, the space-charge-limited conduction (SCLC) region was fitted using the Mott–Gurney law, including the built-in voltage (Vbuilt-in) correction term, expressed as
where μ is the charge carrier mobility, εs is the permittivity of the materials, and L is the thickness of the film. Assuming a dielectric constant of 3, the calculated hole mobility of 3HTBTT was found to be 1.5 × 10−5 cm2 V−1 s−1, 5.9 × 10−4 cm2 V−1 s−1, 9.5 × 10−4 cm2 V−1 s−1, and 1.6 × 10−6 cm2 V−1 s−1, for CHCl3 to toluene ratios of 0
:
1, 1
:
1, 1.5
:
1, and 2
:
1, respectively (Fig. 5a). We conducted additional measurements of our materials' conductivity to observe the intrinsic properties of the films. The observed conductivity values were 1.60 S cm−1, 1.45 S cm−1, 38 S cm−1, 0.23 S cm−1 for CHCl3 to toluene ratios of 0
:
1, 1
:
1, 1.5
:
1, and 2
:
1, respectively (Fig. 5b). As previously mentioned, the enhanced mobility and conductivity were attributed to the successful formation of a highly ordered 3HTBTT film using a CHCl3 and toluene ratio of 1.5
:
1. Finally, we successfully fabricated inkjet-printed TFTs using 3HTBTT small molecule with the optimized solvent system (i.e., CHCl3 to toluene ratio of 1.5
:
1). The transfer curve (Fig. 5c) and output curve (Fig. 5d) of 3HTBTT indicated relatively high hole mobility of approximately 0.01 cm2 V−1 s−1 (transconductance = 0.024 μS) with a high on/off ratio (=104), even without post-annealing. Although the mobility was still lower than desired due to the high number of interface defects under the pre-fabricated FET device structure, we believe that this value demonstrated quite a high performance among other small molecule-based inkjet printed TFTs published to date.
 |
| Fig. 5 (a) I–V curve for HOD devices with different ratios CHCl3 : toluene. (b) Conductance versus channel length plots with different ratios CHCl3 : toluene. (c) Transfer curve and (d) output curve for printed TFT device with 1.5 : 1 solution. | |
Conclusions
We successfully synthesized 3HTBTT small molecule with D(D′–A–D′)2 structure system. Various ratios of CHCl3
:
toluene used to control the morphology film and molecular arrangement via inkjet printing technology were studied by XRD and AFM. The results clearly showed that the morphology film and their crystallinity were dramatically enhanced with suitable ratios of CHCl3
:
toluene. This resulted in a significant improvement in charge carrier transport. The mobilities estimated from 3HTBTT-based hole-only devices enhanced with a CHCl3
:
toluene ratio from 0
:
1 to 1.5
:
1. Furthermore, inkjet-printed TFT based on 3HTBTT with an optimized solvent system was successfully fabricated and exhibited a hole mobility of 0.01 cm2 V−1 s−1. Optimizing the device structure is expected to further enhance the mobility of inkjet-printed TFTs with 3HTBTT in the future. Although the performance of this 3HTBTT-based inkjet-printed TFT was not high as our expectation, our work regarding morphology and crystallinity of newly designed organic semiconductors with the controlling solvent system can serve as a new avenue for optoelectronic applications.
Author contributions
C. K. Trinh: conceptualization, methodology, investigation, visualization, writing – original draft, review & editing, resources. H. S. Oh: investigation. H. Lee: methodology, investigation, writing – original draft, review & editing, resources.
Conflicts of interest
There are no conflicts to declare.
Acknowledgements
We would like to thank Van Lang University, Vietnam for the support of this research. This work was supported by the 2021 Research Fund of Myongji University.
Notes and references
- Z. Zhan, J. An, Y. Wei, V. T. Tran and H. Du, Nanoscale, 2017, 9, 965–993 RSC.
- Y. Fang, X. Wu, S. Lan, J. Zhong, D. Sun, H. Chen and T. Guo, ACS Appl. Mater. Interfaces, 2018, 10, 30587–30595 CrossRef CAS PubMed.
- P. F. Moonen, I. Yakimets and J. Huskens, Adv. Mater., 2012, 24, 5526–5541 CrossRef CAS PubMed.
- L. Feng, C. Jiang, H. Ma, X. Guo and A. Nathan, Org. Electron., 2016, 38, 186–192 CrossRef CAS.
- B. Kang, W. H. Lee and K. Cho, ACS Appl. Mater. Interfaces, 2013, 2302–2315 CrossRef CAS PubMed.
- L. Zhou, L. Yang, M. Yu, Y. Jiang, C.-F. Liu, W.-Y. Lai and W. Huang, ACS Appl. Mater. Interfaces, 2017, 9, 40533–40540 CrossRef CAS PubMed.
- J. Zhao, L.-W. Lo, H. Wan, P. Mao, Z. Yu and C. Wang, Adv. Mater., 2021, 33, 2102095 CrossRef CAS PubMed.
- X. Chen, R. Huang, Y. Han, W. Zha, J. Fang, J. Lin, Q. Luo, Z. Chen and C. -Q. Ma, Adv. Energy Mater., 2022, 12, 2200044 CrossRef CAS.
- X. Meng, Z. Xing, X. Hu and Y. Chen, Chin. J. Polym. Sci., 2022, 40, 1522–1566 CrossRef CAS.
- D. Stuwe, D. Mager, D. Biro and J. G. Korvink, Adv. Mater., 2015, 27, 599–626 CrossRef PubMed.
- Y. Sun, Y. Zhang, Q. Liang, Y. Zhang, H. Chi, Y. Shi and D. Fang, RSC Adv., 2013, 3, 11925–11934 RSC.
- C. Bax, R. Bernasconi, F. Massironi, L. Magagnin, F. Grizzi, L. Capelli and G. Taverna, J. Electrochem. Soc., 2021, 168, 047513 CrossRef CAS.
- Y. S. Rim, S.-H. Bae, H. Chen, N. De Marco and Y. Yang, Adv. Mater., 2016, 28, 4415–4440 CrossRef CAS PubMed.
- R. G. Scalisi, M. Paleari, A. Favetto, M. Stoppa, P. Ariano, P. Pandolfi and A. Chiolerio, Org. Electron., 2015, 18, 89–94 CrossRef CAS.
- Y. Song and Y.-G. Ha, Bull. Korean Chem. Soc., 2020, 41, 123–126 CrossRef CAS.
- M. Gao, L. Li and Y. Song, J. Mater. Chem. C, 2017, 5, 2971–2993 RSC.
- C. S. Buga and J. C. Viana, Adv. Mater. Technol., 2021, 6(6), 2001016 CrossRef.
- S. Fu, J. Tao, W. Wu, J. Sun, F. Li, J. Li, Z. Huo, Z. Xia, R. Bao and C. Pan, Adv. Mater. Technol., 2019, 1800703–1800711 CrossRef.
- T. M. Schmidt, T. T. Larsen-Olsen, J. E. Carle, D. Angmo and F. C. Krebs, Adv. Energy Mater., 2015, 5, 1500569–1500577 CrossRef.
- H. Lu, J. Lin, N. Wu, S. Nie, Q. Luo, C.-Q. Ma and Z. Cui, Appl. Phys. Lett., 2015, 106, 093302–093305 CrossRef.
- R. Mikkonen, P. Puistola, I. Jönkkäri and M. Mäntysalo, ACS Appl. Mater. Interfaces, 2020, 12(10), 11990–11997 CrossRef CAS PubMed.
- J. Lee, D. H. Kim, J.-Y. Kim, B. Yoo, J. W. Chung, J.-Il. Park, B.-L. Lee, J. Y. Jung, J. S. Park, B. Koo, S. Im, J. W. Kim, B. Song, M.-H. Jung, J. E. Jang, Y. W. Jin and S.-Y. Lee, Adv. Mater., 2013, 25(41), 5886–5892 CrossRef CAS PubMed.
- L. Mu, M. He, C. Jiang, J. Wang, C. Mai, X. Huang, H. Zheng, J. Wang, X.-H. Zhu and J. Peng, J. Mater. Chem. C, 2020, 8, 6906–6913 RSC.
- H.-S. Liao, Y.-X. Hu, X. Xia, D.-D. Xie, H.-J. Chi, Y. Dong, X.-C. Li, Y.-L. Lv, D.-Y. Zhang and X. Li, J. Organomet. Chem., 2022, 957, 122157 CrossRef CAS.
- C. Jin, H. Zeng, F. Zhang, H. Qiu, Z. Yang, M. Mutailipu and S. Pan, Chem. Mater., 2022, 34, 440–450 CrossRef CAS.
- K. S. Park, J. J. Kwok, P. Kafle and Y. Diao, Chem. Mater., 2021, 33, 469–498 CrossRef CAS.
- F. Liu, J. Zhang, Y. Wang, S. Chen, Z. Zhou, C. Yang, F. Gao and X. Zhu, ACS Appl. Mater. Interfaces, 2019, 11(38), 35193–35200 CrossRef CAS PubMed.
- Q. Zhang, B. Kan, F. Liu, G. Long, X. Wan, X. Chen, Y. Zuo, W. Ni, H. Zhang, M. Li, Z. Hu, Y. Cao, Z. Liang, M. Zhang, T. P. Russell and Y. Chen, Nat. Photonics, 2015, 9, 35–41 CrossRef CAS.
- J. Zhang, J. Lv, X. Dong, T. Xu, X. Dai, T. Duan, Z. Kan, P. Liu and S. Lu, J. Mater. Chem. C, 2020, 8, 9195–9200 RSC.
- C. K. Trinh, J. W. Choi, W. Kim and J.-S. Lee, Synth. Met., 2019, 256, 116149–116155 CrossRef CAS.
- C. K. Trinh, J. W. Choi, K. T. Tran, Z. Ahmad and J.-S. Lee, RSC Adv., 2022, 12, 26400–26405 RSC.
- C. K. Trinh and N. I. Abdo, J. Mol. Struct., 2022, 1269, 133764–133771 CrossRef CAS.
- K.-H. Kim, H. Yu, H. Kang, D. J. Kang, C.-H. Cho, J. H. Oh and B. J. Kim, J. Mater. Chem. A, 2013, 1, 14538–14547 RSC.
- S.-H. Kang, D. Lee, H. Kim, W. Choi, J. Oh, J. H. Oh and C. Yang, ACS Appl. Mater. Interfaces, 2021, 13(44), 52840–52849 CrossRef CAS PubMed.
- C. K. Trinh, H.-J. Lee, J. W. Choi, M. Shaker, W. Kim and J.-S. Lee, New J. Chem., 2018, 42, 2557–2563 RSC.
- D. K. Sagdullina, I. E. Kuznetsov, A. V. Akkuratov, L. I. Kuznetsova, S. I. Troyanov and P. A. Troshin, Synth. Met., 2019, 250, 7–11 CrossRef CAS.
- P. Sonar, E. L. Williams, S. P. Singh and A. Dodabalapur, J. Mater. Chem., 2011, 21, 10532–10541 RSC.
- A. A. El-Shehawy, N. I. Abdo, A. A. El-Barbary and J.-S. Lee, Eur. J. Org. Chem., 2011, 4841–4852 CAS.
- M. Lada, M. J. Starink, M. Carrasco, L. Chen, P. Miskiewicz, P. Brookes, M. Obarowskac and D. C. Smith, J. Mater. Chem., 2011, 21, 11232–11238 RSC.
- Z. He, Z. Zhang, K. Asare-Yeboah and S. Bi, Mater. Adv., 2023, 4, 769–786 RSC.
- Y. Lee, D. Ho, F. Valentini, T. Earmme, A. Marrocchi, L. Vaccaro and C. Kim, J. Mater. Chem. C, 2021, 9, 16506–16515 RSC.
- B. Liu, D. Rocca, H. Yan and D. Pan, ACS Au, 2021, 1(12), 2182–2187 CAS.
- M. Planells, M. Nikolka, M. Hurhangee, P. S. Tuladhar, A. J. P. White, J. R. Durrant, H. Sirringhaus and I. McCullocha, J. Mater. Chem. C, 2014, 2, 8789–8795 RSC.
- R. Ams, N. Trapp, A. Schwab, J. V. Milić and F. Diederich, Chem.–Eur. J., 2019, 25(1), 323–333 CrossRef PubMed.
- M. Echeverri, C. Ruiz, S. Gámez-Valenzuela, I. Martín, M. C. R. Delgado, E. Gutiérrez-Puebla, M. Á. Monge, L. M. Aguirre-Díaz and B. Gómez-Lor, J. Am. Chem. Soc., 2020, 142(40), 17147–17155 CrossRef CAS PubMed.
- S. J. Nam, S. J. Jeon, Y. W. Han and D. K. Moon, J. Ind. Eng. Chem., 2018, 63, 191–200 CrossRef CAS.
- M. Shaker, J.-H. Lee, C. K. Trinh, W. Kim, K. Lee and J.-S. Lee, RSC Adv., 2015, 5, 66005–66012 RSC.
- C. K. Trinh, G. M. Nassar, N. I. Abdo, S. Jung, W. Kim, K. Lee and J.-S. Lee, RSC Adv., 2022, 12, 17682–17688 RSC.
- M. Li, M. Xiao and Z. Li, RSC Adv., 2021, 11, 39625–39635 RSC.
- C. E. S. Bernardes, M. L. S. M. Lopes, J. R. Ascenso and M. E. M. da Piedade, Cryst. Growth Des., 2014, 14(11), 5436–5441 CrossRef CAS.
|
This journal is © The Royal Society of Chemistry 2023 |
Click here to see how this site uses Cookies. View our privacy policy here.