DOI:
10.1039/D3RA00222E
(Paper)
RSC Adv., 2023,
13, 13516-13525
Developing novel imidazoline-modified glucose derivatives as eco-friendly corrosion inhibitors for Q235 steel
Received
11th January 2023
, Accepted 27th March 2023
First published on 2nd May 2023
Abstract
Many natural compounds and imidazoline derivatives have been previously evaluated as eco-friendly corrosion inhibitors for application in the food, pharmaceutical and chemical industries. Herein, a novel alkyl glycoside cationic imaginary ammonium salt (FATG) was designed via the grafting of imidazoline molecules into the skeleton of a glucose derivative, and its effects on the electrochemical corrosion behavior of Q235 steel in 1 M HCl were systemically investigated by electrochemical impedance spectroscopy (EIS), potentiodynamic polarization curves (PDP), and gravimetric measurements. The results indicated that its maximum inhibition efficiency (IE) was 96.81% at a concentration as low as 500 ppm. The adsorption of FATG on the Q235 steel surface followed the Langmuir adsorption isotherm. The scanning electron microscopy (SEM) and diffraction X-ray (XRD) results suggested the formation of inhibitor film on the metal surface, which significantly impeded the corrosion of Q235 steel. Additionally, FATG showed a high biodegradability efficiency (98.4%), which had great potential as a green corrosion inhibitor based on concepts of greenness and biocompatibility.
1 Introduction
Acid-driven corrosion is mainly caused by acidic materials that react with metallic surfaces, primarily causing the corrosion of steel structures such as buildings, high-value assets, working machines and statues, which also indirectly affect industrial sectors and even human health.1 Various approaches, including adding corrosion inhibitors,2 surface modification, anticorrosive coatings3 and electrochemical means4 have been carried out to address this issue. Among them, due to their excellent adsorbability and structure stability, the use of corrosion inhibitors, such as imidazoline derivatives,5–7 thiourea derivatives,8 isoxazolium derivatives,9 inorganic chromates,10 and organophosphorus derivatives,11 has been considered as an economical, efficient and versatile strategy to improve the corrosion-resistance of metals. Despite their popularity, most of these derivatives also negatively impact the environmental profile. In contrast, natural resources, such as those extracted or modified from plants or agro-industrial waste, for instance, coffee bagasse oil,12 rice bran oil,13,14 wasted mango seeds,15 wasted avocado oil,16 and Rosa canina fruit,17 have been used to synthesize corrosion inhibitors and have received great attention due to their non-toxicity, biodegradability, and they have no negative influence on the environment.18 However, problematic extraction and storage still limit their large-scale commercialization.
Carbohydrates, such as chitosan,19 starch,20 exudate gums,21 and glucose,22–24 have great potential as feedstocks for corrosion inhibitor material because of their high molecular weight, and high adsorption performance.25–27 Among them, glucose exhibits more excellent solubility performance as compared to others since it bears numerous polar functional groups. Additionally, it is more cost-effective and easily obtainable from natural sources. Unfortunately, glucose by itself could fail to achieve a good inhibiting effect, therefore, Wang et al.22 have reported that thiocarbohydrazide was introduced to glucose to increase its corrosion inhibition performance. Additionally, the presence of alkyl glycosides might increase the adsorption sites due to numerous hydroxyl groups promoting adsorption and increasing the coverage on the steel surface to improve the inhibition performance.
Monomer acid (MA), shows great potential for the development of high-value products such as imidazoline due to its eco-friendly, cost-effective, abundant and easily accessible28 properties. In general, it is a good source of high-quality fatty acids since it contains stearic acid, octadecenoic acid, palmitic acid and oleic acid. Unfortunately, MA, an inexpensive by-product of the manufacturing of dimer acid, has not attracted enough attention, even though it has been commonly used in some fields.29,30 As far as we know, no research has focused on the preparation of an acceptable corrosion inhibitor from waste MA.
In this context, synthesized glucose derivatives of novel acceptable corrosion inhibitors featured in inexpensive raw materials and green production are an excellent solution to the problem of corrosion. Herein, we report the synthesis of a novel alkyl glycoside cationic imaginary ammonium salt, (FATG) from modified glucose and waste MA. The target of this research was to develop a novel surfactant that could be used as a green inhibitor for the HCl corrosion of Q235 steel. Potentiodynamic polarization (PDP) and electrochemical impedance spectroscopy (EIS) techniques have been applied to the study of inhibitory behavior. The adsorption behavior of the inhibitor on the Q235 steel surface has been studied through density functional theory (DFT) to explain the mechanism of adsorption, further offering theoretical information for designing and synthesizing novel inhibitors.
2 Experiments and methods
2.1 Material
N-(2-Aminoethyl) ethanolamine (AR), chlorinated alkyl glycosides,31 monomeric acid (wt%: palmitic acid 23.10, oleic acid 31.24, stearic acid 37.13, octadecadienoic acid 4.73, and arachidic acid 3.62) were used to synthesize the imidazoline derivative inhibitors. All of these materials were directly used without further purification.
The chemical composition of Q235 steel is given in Table 1. The steel was mechanically cut into 10 mm × 10 mm × 0.5 mm coupons. Prior to the corrosion test, the working surface was scraped with 1200-grade abrasive paper, washed, and degreased with deionized water.
Table 1 Chemical composition of Q-235 steel
Fe |
C |
Si |
Mn |
P |
S |
Cr |
Ni |
Al |
Bal. |
0.012 |
0.001 |
0.001 |
0.011 |
0.008 |
0.01 |
0.001 |
0.006 |
2.2 Synthesis and evaluation of imidazoline inhibitors
As shown in Fig. 1, the FATG was prepared via a series of reactions. Here, 0.5 mol MA and 0.8 mol N-(2-hydroxyethyl)ethylenediamine were added to the reactor, heated from 150 °C to 230 °C until no more water came from the water segregator, and then steamed. Subsequently, 0.5 mol chloroalkyl glycoside and 10 mL methanol were added to the reactor. The reaction was kept at 80 °C for 5 h to obtain a light brown crude product, which was then extracted in EtOAc-n-hexane for further purification.
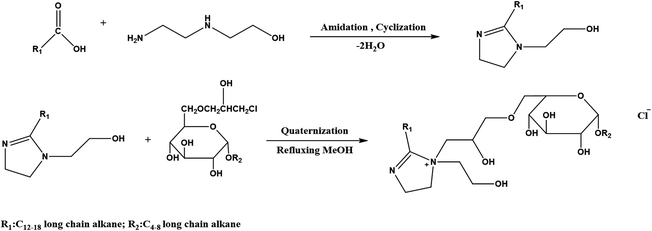 |
| Fig. 1 Synthesis route of FATG. | |
The FATG was characterized by FTIR (German VERTEX 80V) between 4000 and 500 cm−1, 1H NMR, and 13C NMR.
2.3 Inhibition performance of synthesized inhibitors
Gravimetric experiments were conducted to determine the corrosion rate of the metal hanging sheet before and after studying the corrosion mass change to judge the corrosion resistance of the material. The previously weighed Q235 steel strips of size 10 mm × 10 mm × 0.5 mm with a total exposed area of 2 cm2 were dried and then immersed in 100 mL of 1 M HCl without and with different concentrations of FATG inhibitors for 6 h. Also, considering the effect of the corrosive medium temperature on the inhibition efficiency of FATG, gravimetric experiments were carried out at temperatures ranging from 298 K to 338 K.
The inhibition performance of the synthesized inhibitors in 1 M HCl solution was investigated by electrochemical measurements, which were carried out in a Corrtest CS2350H electrochemical workstation with a three-electrode system including the working electrode (Q235 steel), auxiliary electrode (platinum electrode), and a reference electrode (saturated calomel electrode). The working electrode was shielded with silica gel and an uncovered zone of 1 cm2 was the test surface. Before the test, the working surface was immersed in 1 M HCl solution for 1 h.
Electrochemical impedance spectroscopy (EIS) tests were conducted with a 10 mV AC disturbance to obtain the amplitude, setting the frequency range from 100 kHz to 0.05 Hz. Potentiodynamic polarization curves (PDP) were obtained after EIS tests with a 2 mV s−1 scanning rate from −1.0 to 0.2 V vs. SCE.32 As mentioned above, the operations should not be started until the open circuit is stable.
2.4 Characterizations of surface films
The inhibited surface morphology and element distribution of Q235 steel immersed without or with 500 ppm FATG for 7 days were determined with an FEI Quanta 200 scanning electron microscope (SEM-EDX). Prior to SEM observation, the specimens were taken from the 1 M HCl solution and gently scrubbed, washed with deionized water, and dried under gas streams. X-ray diffraction (XRD) was used as an effective method to analyse the crystal structures of corrosion products. Steel sheets were tested under the conditions of a scattering angle range of 2θ = 10 to 80°.
2.5 Biodegradability study
The degradation behavior of FATG was investigated by the test method for the biodegradability of surfactants (GB/T 15818-2018). The cultured activated sludge of the surfactant samples was used as the biodegradation source, which was added to the test part of the oscillating culture. The reduction of the surfactant during the culture period was measured, and the biodegradability of the specified time was obtained.
2.6 Quantum chemistry calculation
The quantum chemical calculations were conducted using the DFT-based program Gaussian 09W at the B3LYP/6-31G(d,p) basis set. The solvent (water) effect was considered. Geometry optimization was performed, and the highest occupied molecular orbital (EHOMO), lowest unoccupied molecular orbital (ELUMO), and other parameters were determined.33–35
3 Results and discussion
3.1 Characterization of FATG
The FTIR spectrum of FATG is shown in Fig. 2. The absorption peak at about 3320 cm−1 corresponds to the stretching vibration peak of O–H. The characteristic peak at about 1606 cm−1 was observed in the spectra of products, which matched the C
N double bond stretching vibration.15,36 The absorption peaks at about 1363 cm−1 and 1301 cm−1 were due to the C–N vibrations.22,37 A new strong band at 1029 cm−1 was attributed to the C–O–C vibration, suggesting that an alkyl glycoside structure was present in the imidazoline structure. The FT-IR results also revealed that imidazoline was successfully synthesized. 1H NMR and 13C NMR spectra are displayed in Fig. 3 to further confirm the structure. For FATG, 1H NMR (600 MHz, chloroform-d) δ 5.39 (s, 1H, C–OH), 4.84 (s, 1H, C–OH), 4.24 (s, 2H, CH2–O), 3.91 (s, 4H, N–CH2), 3.80 (s, 2H, N–CH2), 3.78-3.48 (m, 8H, GluCH/CH
N/CH2–O), 3.45 (d, J = 26.7 Hz, 4H, CH2–O), 2.58 (s, 2H, C
N–CH2), 1.97 (s, 2H, CH2), 1.60 (s, 4H, CH2), 1.26 (s, 30H, CH2), 0.89 (s, 6H, CH3). 13C NMR (151 MHz, CDCl3) δ 151.30, 142.70, 110.25, 109.33, 78.43, 77.11, 71.21, 69.91, 65.17, 50.76, 44.13.6,37–39
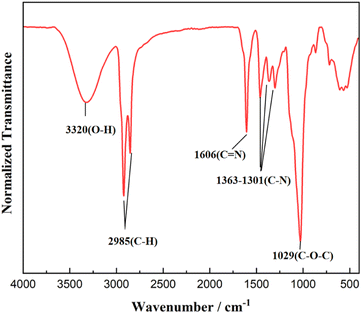 |
| Fig. 2 Infrared spectra of FATG. | |
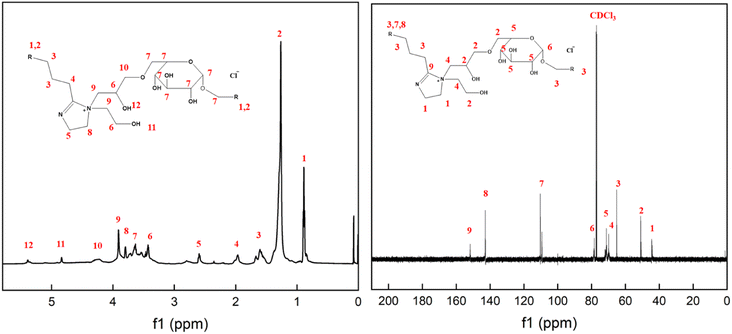 |
| Fig. 3 1H NMR spectra and 13C NMR spectra of FATG. | |
3.2 Gravimetric measurements
The weight loss-time data, as depicted in Table 2, revealed that the FATG inhibitor acted as a good inhibitor when Q235 steel was immersed in 1 M HCl solution for 6 h at temperatures below 338 K. The inhibition efficiency in the presence of FATG increased with the increasing concentration of the inhibitor in 1 M HCl. The surface coverage was calculated using the following formula:40 |
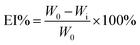 | (1) |
where W0 is the weight loss in uninhibited acid solution and Wi is the weight loss in inhibited acid solution.
Table 2 Corrosion parameters for Q235 steel in 1 M HCl in the absence and presence of different concentrations of FATG at 298–338 K from weight loss measurements
Inhibitor com. (ppm) |
Weight loss (mg cm−2) |
Corrosion inhibition efficiency of FATG (%) |
298 K |
308 K |
318 K |
328 K |
338 K |
298 K |
308 K |
318 K |
328 K |
338 K |
Blank |
7.3 |
16.4 |
29.3 |
66.7 |
141.5 |
— |
— |
— |
— |
— |
100 |
0.9 |
2.3 |
2.2 |
3.0 |
3.4 |
87.67 |
85.98 |
92.49 |
95.50 |
97.60 |
200 |
0.7 |
1.9 |
2.0 |
2.6 |
3.1 |
90.41 |
88.41 |
93.17 |
96.10 |
97.81 |
300 |
0.6 |
1.4 |
1.9 |
2.2 |
2.5 |
91.78 |
91.46 |
93.52 |
96.70 |
98.23 |
400 |
0.5 |
1.3 |
1.6 |
1.1 |
2.8 |
93.15 |
92.07 |
94.54 |
98.35 |
98.02 |
500 |
0.3 |
1.0 |
1.4 |
1.0 |
2.1 |
95.89 |
93.90 |
95.22 |
98.50 |
98.52 |
FATG demonstrated outstanding inhibiting properties at temperatures in the range of 298–338 K. It was apparent from the results that the corrosion inhibition efficiency of the inhibitor also depended on the factor of temperature. At room temperature, the FATG inhibitor formed a protective film through physical or chemical adsorption on the metal surface. Coincidentally, it was seen that the corrosion inhibition efficiency of the solution temperature gradually increased and was finally stabilized at around 98%, with the increase in solution temperature. It was seen that heating without an inhibitor would make the Fe atoms more likely to lose electrons and enter the solution in the form of Fe2+ to accelerate the dissolution of Q235 steel. Whereas, it was effective to add the inhibitor to slow the loss of metal weight. Based on the data, the phenomenon implied that chemisorption was the main mechanism when heated. Heating would accelerate the thermal movement of the inhibitor molecules on the metal surface to promote the formation of chemical bonding between them. This led to the inhibitor being firmly attached to the metal surface and it was difficult to desorb once it had been absorbed.40–42
3.3 EIS measurements
EIS measurements for Q235 steel dipped in a corrosive medium (1 M HCl solution) were plotted using Nyquist and Bode graphs in the absence and presence of various concentrations of FATG, as portrayed in Fig. 4. The Nyquist plot showed that the semicircular curves of the FATG increased with concentration in Fig. 4a. When an inhibitor concentration of 500 ppm was reached, the impedance value was the maximum. Moreover, in the EIS test of solid electrodes, the curve deviated from the semicircle trajectory to show a deformed semicircular shape, a phenomenon known as the “dispersion effect”, which was generally considered to be caused by the active site of the metal surface being heterogeneous, or the poor conductivity of the solution.43 Therefore, by combining the Nyquist and Bode diagrams obtained by the experiment, the equivalent circuit shown in Fig. 5 was selected to fit the impedance spectrum, and the fitted parameters are listed in Table 3.
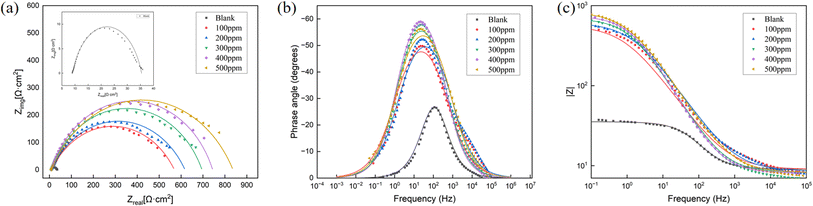 |
| Fig. 4 Nyquist and Bode plots for Q235 steel in 1 M HCl solution without and with various concentrations of FATG at 298 K. | |
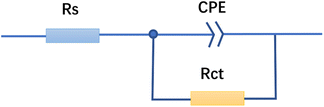 |
| Fig. 5 Equivalent circuit for Q235 steel in 1 M HCl solution. | |
Table 3 Electrochemical parameters to fit the EIS data of Q-235 steel corroded in 1 M HCl solution containing different concentrations of FATG
Dose (ppm) |
Rs (Ω cm2) |
CPE |
Rct (Ω cm2) |
EI/% |
Y0 (Sn cm−2 Ω × 104) |
n |
0 |
9.034 |
4.1127 |
0.72379 |
26.4 |
— |
100 |
8.954 |
5.3684 |
0.65745 |
560.7 |
95.29 |
200 |
8.535 |
3.527 |
0.67273 |
609.5 |
95.67 |
300 |
8.313 |
3.2794 |
0.73724 |
687.3 |
96.16 |
400 |
8.144 |
2.8902 |
0.84314 |
736.1 |
96.41 |
500 |
8.185 |
3.092 |
0.80332 |
828.6 |
96.81 |
The equivalent circuit model was simulated in Fig. 5, based on the EIS spectra of the FATG to further imitate the combined physical processes occurring at the metal electrode/electrolyte interface. The capacitive loop of the first quadrant was generated in parallel by resistance and capacitance.43 From the Nyquist diagram, the starting point of the capacitive loop did not pass through the origin, indicating that there was a solution resistance in the electrolytic cell.7 Moreover, in the equivalent circuit, CPE, an electrochemical element, was introduced to reflect the “dispersion effect”, which could be used as a gauge of the heterogeneity or roughness of the FATG surface.43–45 Therefore, the equivalent circuit shown in Fig. 5 was selected as the equivalent circuit. Rs is the solution resistance, Rct is the charge transfer resistance, and CPE is the constant phase angle element.
Table 3 lists the electrochemical corrosion parameters of CPE (Y0), the dispersion index (n), as well as the percentage inhibition efficiency (IE%), etc. The inhibition efficiency (IE%) was calculated from the following equation:46
|
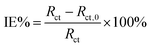 | (2) |
Rct,0 and
Rct are the charge transfer resistance values without and with inhibitor, respectively. The fitting results are recorded in
Table 3. The best inhibition efficiency was about 96.81% at the concentration of 500 ppm. With increasing concentration of the inhibitor, the
Rct value increased from 26.4 Ω cm
2 to 828.6 Ω cm
2. This could be because the imidazoline molecule could offer “attachment points” and adsorb on the metal surface, then, where they formed monomolecular layers, increase the shielding effect to promote the improvement of corrosion inhibition efficiency. Moreover, the increase in the
n-value after adding the FATG inhibitor in the corrosive solution could facilitate the reduction of surface inhomogeneity due to the adsorption of inhibitor molecules on the most active adsorption sites at the surface.
47 Generally, when there was a diffusion effect on the electrode surface, the value of
n was always between 0.5 and 1, which was consistent with the fitting results.
3.4 PDP measurements
The Tafel curves recorded for Q235 steel in 1 M HCl solution at various concentrations in the presence and absence of FATG inhibitor are shown in Fig. 6. The change in the self-corrosion potential was insignificant so it was considered that the cationic imidazoline belonged to a mixed-type corrosion inhibitor, with anodic oxidative dissolution corrosion and cathodic depolarization reduction being similarly impeded in the electrolytic cell.44,46,48 In addition, it was apparent that the corrosion rate of the Q235 steel was slowed down due to the corrosion current density (Icorr) dropping significantly to a lower value. The current density of the anodic polarization curve increased sharply in the later stages, developing a “plateau” as the corrosion inhibitor underwent desorption behavior on the metal surface. It can be seen that the synthesized FATG is an adsorption-type corrosion inhibitor, and a dynamic equilibrium was formed between adsorption and desorption.46
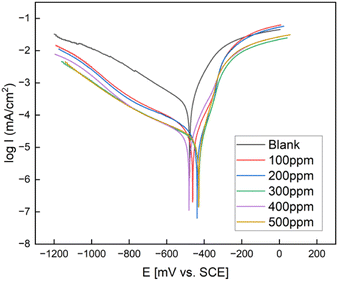 |
| Fig. 6 Polarization curves of Q235 steel in 1 M HCl solution without and with various concentrations of inhibitor. | |
Table 4 lists the corrosion potential (Ecorr), anode and cathode Tafel ramps (βa and βb), corrosion current density (Icorr), surface coverage (θ), as well as percentage rejection rate (IE%) electrochemical corrosion parameters. The inhibition efficiency was calculated based on the following equation:
|
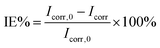 | (3) |
where
Icorr,0 and
Icorr are corrosion current densities in solution without and with inhibitor, respectively.
Table 4 Electrochemical parameters and inhibition efficiency obtained from polarization curves for Q-235 steel immersed in 1 M HCl solution containing FATG
Dose/ppm |
Ecoor/mV |
βa/(mV dec−1) |
βb/(mV dec−1) |
Icoor/(μA cm−2) |
IE/% |
0 |
−473.83 |
118.24 |
286.19 |
562.58 |
— |
100 |
−461.52 |
74.878 |
365.09 |
27.654 |
95.08 |
200 |
−480.75 |
88.574 |
380.12 |
25.182 |
95.52 |
300 |
−437.82 |
64.945 |
206.72 |
23.715 |
95.78 |
400 |
−429.01 |
71.629 |
204.16 |
19.556 |
96.52 |
500 |
−429.68 |
71.099 |
232.16 |
18.747 |
96.67 |
As shown in Table 4, as the concentration increased, the corrosion current density (Icoor) remarkably dropped to a lower value, and the best inhibition efficiency (IE%) was about 96.67% at a concentration of 500 ppm, showing excellent corrosion inhibition performance. At the same time, the corrosion potential (Ecorr) and the Tafel slope (βa and βb) changed slightly, suggesting that the synthesized FATG did not affect the reactions of both the anode and cathode, whose corrosion inhibition mechanism was to form a protective film on the surface of steel carbon and inhibit the active site of the reaction.34
The variation of the inhibition efficiency with the (FATG) inhibitor concentration at room temperature was calculated using three different techniques and is presented in Fig. 7.
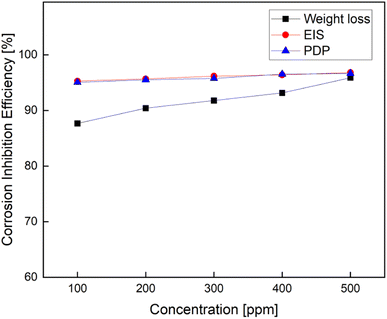 |
| Fig. 7 Variation of the inhibition efficiency from three different techniques. | |
3.5 Adsorption isotherm and thermodynamic parameters
The way adsorption occurs on metal surfaces could be clarified by making use of adsorption isotherms. Among the different models,34 the best fit was obtained with the Langmuir model, shown in Fig. 8, according to the following equation:48 |
 | (4) |
where Kads is the adsorption equilibrium constant. This constant has some connection with the standard free energy of adsorption (ΔGads) according to the following equation:49 |
ΔG0ads = −RT ln(55.5Kads)
| (5) |
where R is the universal gas constant and T is the absolute temperature. The value of 55.5 is the concentration of water in the solution in molarity units.
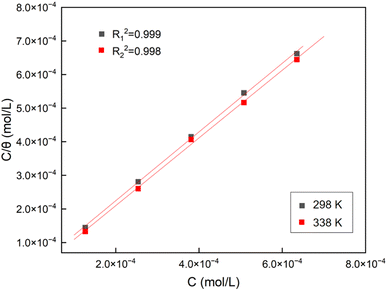 |
| Fig. 8 Langmuir adsorption isotherm for Q235 steel in 1 M HCl solution. | |
As shown in Fig. 8, the adsorption of FATG in solution at 298 K and 338 K accorded with the Langmuir adsorption isotherm with correlation factors R12 = 0.999 and R22 = 0.998. It can be concluded that the adsorption mode of corrosion inhibitor molecules on the electrode surface was likely to be monolayer adsorption, and the interaction force between adsorbed molecules could be ignored. Moreover, the values of ΔGads (ΔGads1 = −38.11 kJ mol−1 and ΔGads2 = −39.76 kJ mol−1) implied that the adsorption process of the FATG on the Q235 steel surface was spontaneous and worked with physisorption and chemisorption.50,51
3.6 Surface analysis
Fig. 9a and b show that without the inhibitor, the Q235 steel surface was heavily concave and pitted. In the presence of the FATG compound, shown in Fig. 9c and d, the surface of Q235 steel images retained intact scratches, maximizing the protection of the iron surface against acid corrosion. Thus, we concluded that the inhibitor could be stably present in the system and build a defensive shield on the steel surface.7,42 Furthermore, it was shown that Q235 was oxidized in an acidic solution, producing C and O from the EDX microchemical analysis. Comparing the two sets of reactions in Fig. 9e and f, in the presence of 500 ppm of inhibitor, the amount of C and O on the corroded steel was lower. Correspondingly, the content of Fe remained higher (96.6%), indicating that the inhibitor could effectively prevent the oxidation of Q235 steel.22,52,53
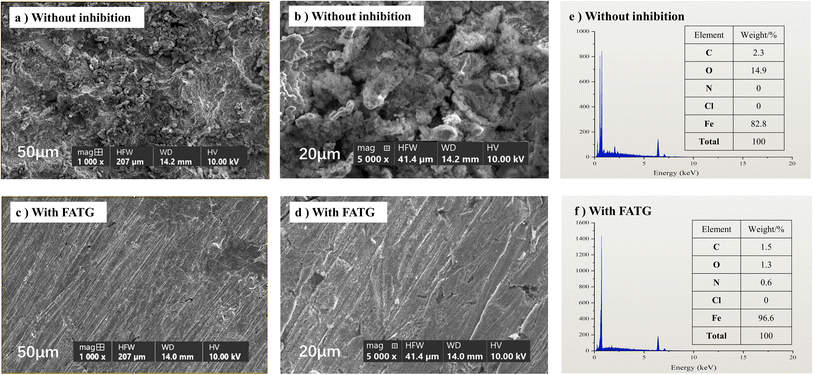 |
| Fig. 9 SEM (a–d) and EDX (e and f) images of the sample after corrosion without or with 500 ppm FATG for 7 days. | |
The XRD pattern in Fig. 10 shows that at room temperature, the crystal structures of corrosion products formed on the surface of Q235 steel were mainly FeCl3 and Fe2O3. Without the protection of the inhibitor, Q235 steel in an acidic solution was naturally unstable. It was eroded by acid, leading to the oxidation of iron and the formation of a variety of oxidation products. On the contrary, it could be observed that in the presence of the FATG compound, there only appeared a small number of crystals of corrosion product FeCl3 on the surface, and the peak value corresponding to the iron still maintained a high level. This was consistent with the results of the SEM-EDX. It could be seen that the FATG corrosion inhibitors could prompt the anchor to form a dense protective coating on the metal surface to reduce the contact between the corrosion medium and the metal surface.40,54
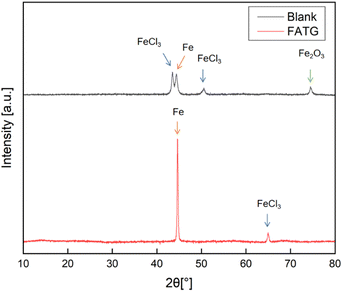 |
| Fig. 10 XRD image of the sample after corrosion in the medium without or with 500 ppm of FATG for 48 h at 298 K. | |
3.7 Biodegradability
The surfactant used in the metal corrosion inhibitor would inevitably be transferred quantitatively into the environment. Therefore, it was of great significance to study the biodegradation of the FATG surfactant. Under natural conditions or artificial control, the life process of organisms could be decomposed or converted into small molecules. In this study, the biodegradability of the inhibitor was evaluated by the Golden orange-2 method in 28 days. The results showed that its biodegradability was 98.4%, which was higher than previously reported.55 FATG showed excellent biodegradable properties, probably due to the rapid biodegradation of imidazolinium compounds and alkyl glycosides.56
3.8 Quantum chemical calculations
The use of density functional theory (DFT) to evaluate the corrosion inhibition mechanism is an important method.57 According to quantum chemical calculations, the optimal structure and molecular frontier orbital (HOMO, LUMO) distribution of FATG are presented in Fig. 11. The image of the HOMO showed that the electron cloud surrounded the double bond, which could provide electrons to some of the acceptor molecules with low energy or vacant electron orbitals. The LUMO image mainly surrounded the field of nitrogen atoms that could accept electrons from the surface of Q235 steel. The calculation results showed that green corrosion inhibition could be achieved by introducing imidazoline into alkyl glycosides since the imidazoline ring and double bonds are the active sites of the inhibitor that could be firmly adsorbed on the Fe surface by giving and receiving electrons.33
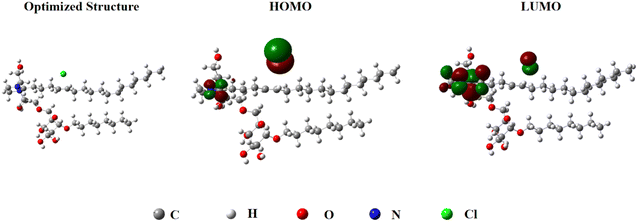 |
| Fig. 11 Optimized geometry of FATG in the solvent, HOMO orbitals, and LUMO orbitals. | |
3.9 Corrosion inhibition mechanism
The working mechanism of the inhibitor is based on the direct or indirect adsorption of the inhibitor molecules on the metal surface, thus reducing the contact of the metal surface with the aggressive medium. Q235 steel in acid solution was naturally unstable so it tended to undergo chemical/electrochemical reactions with erosive media in the environment to form more stable substances such as FeCl3 or Fe2O3.24,42 In this paper, grafting imidazoline molecules on the skeleton of glucose derivatives made the prepared inhibitors rich in oxygen and nitrogen atoms, which allowed a large number of connection sites, thus improving their stability on the metal surface.22
Based on quantum chemical calculations and related test experiments, the inhibitive mechanism of FATG on Q235 steel in aerated 1 M HCl solution could be explained as seen in Fig. 12. The C
N double bond in the FATG molecular structure having loan pairs of electrons could be adsorbed by donating electrons to the d-orbitals of Q235 steel in a parallel position. Moreover, heterocyclic atoms such as N atoms were prone to accepting the 4s orbital electrons of Fe atoms to adsorb in an acceptor manner.58,59 In addition, in acidic media, due to electrostatic interaction, FATG molecules carried ammonium cations, which could be quickly adsorbed in the cathode region of the metal. Subsequently, it was difficult for the H+ in the acid solution to approach the metal, greatly decreasing the corrosion efficiency.59,60 Simultaneously, the hydrophobic groups kept water molecules away from metals. Based on the result of the gravimetric measurements, heating would promote the formation of chemical bonding between the N atoms of the inhibitor molecule and the ions on the metal surface; accordingly, the inhibitor was firmly attached to the metal surface. Hence, from what has been discussed above, we may conclude that the FATG molecules were adsorbed on the metal surface by physisorption and chemisorption.
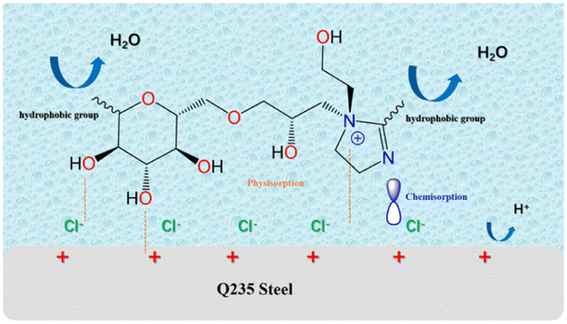 |
| Fig. 12 Corrosion inhibition mechanism of FATG. | |
4 Conclusion
In summary, a novel alkyl glycoside cationic imaginary ammonium salt (FATG) was synthesized and used as an environmentally friendly corrosion inhibitor for Q235 in 1 M HCl. The inhibition property of FATG was characterized by using chemical and electrochemical measurements. The results revealed that the inhibition efficiency in the presence of FATG increased with increasing the concentration of the inhibitor. The best inhibition efficiency was about 96.81% at the concentration of 500 ppm (298 K). The adsorption of FATG on the Q235 steel surface conformed to the Langmuir adsorption isotherm. According to thermodynamic parameters, the value of ΔGads indicated that it was adsorbed on the metal surface by physisorption and chemisorption. As we expected, the inhibitor could be stably present in the system, building a defensive shield on the metal surface to prevent metal oxidation. Moreover, the results of SEM-EDX and XRD supported the formation of inhibitor film on the metal surface. Quantum chemistry calculations had shown that imidazoline rings and double bonds were active sites of this inhibitor, and they could be firmly adsorbed to the metal surface by supplying electrons to iron atoms and accepting electrons.
Conflicts of interest
There are no conflicts to declare.
Acknowledgements
This work was supported by the National Key R&D Program of China (2022YFD2200802) and the Jiangsu Province Key R&D Program (BE2019111). Authors are grateful to Priority Academic Program Development of Jiangsu Higher Education Institutions (PAPD) for their financial support. Authors are also grateful to Mr Jihuai Tan (Chemical Engineering of Nanjing Forestry University) for his assistance with the manuscript.
References
- B. S. Hou, Q. H. Zhang, Y. Y. Li, G. Y. Zhu, Y. Lei, X. Wang, H. F. Liu and G. A. Zhang, Corros. Sci., 2021, 181, 109236 CrossRef CAS.
- Z. Yakun, L. F. Michael, W. Richard and D. William, Prog. Mater. Sci., 2017, 90, 159–223 CrossRef.
- G. Cui, Z.-X. Bi, S.-H. Wang, J.-G. Liu, X. Xing, Z.-L. Li and B.-Y. Wang, Prog. Org. Coat., 2020, 148, 105821 CrossRef CAS.
- Y.-S. Kim, J. Kim, D. Choi, J.-Y. Limd and J.-G. Kim, Eng. Anal. Bound. Elem., 2017, 77, 36–48 CrossRef.
- H.-G. Liu, C.-Y. Chen, X. Yuan, Y. Tan, G.-Z. Meng, H.-F. Liu and Y. F. Cheng, Corros. Sci., 2022, 203, 110345 CrossRef CAS.
- W.-C. Zhuang, X.-Q. Wang, W.-Y. Zhu, Y. Zhang, D. Sun, R. Zhang and C.-Y. Wu, ACS Omega, 2021, 6, 5653–5660 CrossRef CAS PubMed.
- M. M. Shaban, N. A. Negm, R. K. Farag, A. A. Fadda, A. E. Gomaa, A. A. Farag and M. A. Migahed, J. Mol. Liq., 2022, 351, 118610 CrossRef CAS.
- L. Guo, S. Kaya, I. B. Obot, X.-W. Zheng and Y.-J. Qiang, J. Colloid Interface Sci., 2017, 506, 478–485 CrossRef CAS PubMed.
- N. A. Negm, F. M. Ghuiba and S. M. Tawfik, Corros. Sci., 2011, 53, 3566–3575 CrossRef CAS.
- J. Sinko, Prog. Org. Coat., 2001, 42, 267–282 CrossRef CAS.
- L. Ning, D.-D. Wang, L.-X. Wang, L.-F. Wu, J.-Y. Yang, X.-M. Wang, H.-Y. Ma, S.-Y. Feng and H.-F. Lu, Silicon, 2020, 12, 1455–1468 CrossRef CAS.
- N. B. Guzman, D. M. Escalera, J. P. Calderon, J. G. Rodriguez and L. M. Gomez, Green Chem. Lett. Rev., 2019, 12, 49–61 CrossRef.
- G. S. Solano, J. P. Calderonc, L. M. Escalera, J. Canto, M. C. Diaz, O. S. Mazon, J. Henao and L. M. Gomez, Ind. Crops Prod., 2018, 119, 111–124 CrossRef.
- E. R. Dorantes, J. Z. Díaz, A. Q. Hernandez, J. P. Calderon, J. G. Rodriguez and L. M. Gomez, J. Chem., 2017, 2871034 Search PubMed.
- E. S. Salazar, E. V. Velez, J. Uruchurtu, J. P. Calderon, M. Casales, I. R. Cadena, R. L. Cecenes and J. G. Rodriguez, Mater, 2021, 14, 4206 CrossRef PubMed.
- A. C. Zabalegui, E. V. Velez, G. G. Aguilar, M. C. Diaz, R. L. Sesenes, J. G. Rodriguez and L. M. Gomez, Ind. Crops Prod., 2019, 133, 203–211 CrossRef.
- Z. Sanaeia, M. Ramezanzadeha, G. Bahlakehb and B. Ramezanzadeh, J. Ind. Eng. Chem., 2018, 4159 Search PubMed.
- P. B. Raja and M. G. Sethuraman, Mater. Lett., 2008, 62, 113–116 CrossRef CAS.
- V. Srivastava, D. S. Chauhan, P. G. Joshi, V. Maruthapandian, A. A. Sorour and M. A. Quraishi, ChemistrySelect, 2018, 3, 1990–1998 CrossRef CAS.
- M. Mobin, M. Khan and M. Parveen, J. Appl. Polym. Sci., 2011, 121, 1558–1565 CrossRef CAS.
- C. Verma and M. Quraishi, Int. J. Biol. Macromol., 2021, 184, 118–134 CrossRef CAS.
- X. Wang, Y. Lei, Z.-N. Jiang, Q.-H. Zhang, Y.-Y. Li, H.-F. Liu and G.-A. Zhang, Ind. Crops Prod., 2022, 188, 115680 CrossRef CAS.
- M. Rbaa, F. Benhib, R. Hssisou, Y. Lakhrissi, B. Lakhrissi, M. E. Touhami, I. Warad and A. Zarrouk, J. Mol. Liq., 2021, 322, 114549 CrossRef CAS.
- D. S. Chauhan, A. M. Kumar and M. A. Quraishi, Chem. Eng. Res. Des., 2019, 150, 99–115 CrossRef CAS.
- S. Banerjee, V. Srivastava and M. M. Singh, Corros. Sci., 2012, 59, 35–41 CrossRef CAS.
- M. M. Solomon, S. A. Umoren, I. B. Obot, A. A. Sorour and H. Gerengi, ACS Appl. Mater. Interfaces, 2018, 10, 28112–28129 CrossRef CAS PubMed.
- M. Mobin and M. Rizvi, Carbohydr. Polym., 2017, 160, 172–183 CrossRef CAS PubMed.
- X.-F. Liu and X.-Y. Cao, Adv. Mater. Res., 2013, 781, 72–75 Search PubMed.
- J.-H. Tan, Q.-H. Fu, Y.-Q. Qu, F. Wang, W.-G. Wang, F. Wang, Y.-F. Cao and X.-B. Zhu, J. Cleaner Prod., 2021, 289, 125821 CrossRef CAS.
- X. Lu, Adv. Mater. Res., 2016, 521, 629–632 Search PubMed.
- Y. Huang, X.-W. Zhou, L.-S. Fang, Z.-R. Jia, Z.-Z. Yu and X.-B. Zhu, Fine Chem., 2021, 38, 2312–2321 Search PubMed.
- B. Lin, J.-X. Wang, H.-L. Zhang, Y.-Y. Wang, H.-L. Zhang, J.-L. Tang, J. Hou, H.-B. Zhang and M.-X. Sun, Corros. Sci., 2022, 197, 110084 CrossRef CAS.
- M. Behpour, S. M. Ghoreishi, N. Soltani, M. S. Niasari, M. Hamadanian and A. Gandomi, Corros. Sci., 2008, 50, 2172–2181 CrossRef CAS.
- F. G. Liu, M. Du, J. Zhang and M. Qiu, Corros. Sci., 2009, 51, 102–109 CrossRef CAS.
- A. Fitoz, H. Nazır, M. Özgür, E. Emregül and K. C. Emregül, Corros. Sci., 2018, 133, 451–464 CrossRef CAS.
- W.-T. Xu, J.-X. Wei, Z.-G. Yang, P. Xu and Q.-J. Yu, Constr. Build. Mater., 2020, 250, 118861 CrossRef CAS.
- L.-R. Ma, W.-Q. Lu, D. Yang, J.-J. Shen, Z.-S. Gao, S.-Y. Zhang and Q.-Q. Liao, Sustainable Chem. Pharm., 2021, 22, 100488 CrossRef CAS.
- C. Bonaccorso, G. Grasso, N. Musso, V. Barresi, D. F. Condorelli, D. La Mendol and E. Rizzarelli, J. Inorg. Biochem., 2018, 182, 92–102 CrossRef CAS PubMed.
- M. P. Sathisha, S. Budagumpi, N. V. Kulkarni, G. S. Kurdekar, V. K. Revankar and K. S. R. Pai, Eur. J. Med. Chem., 2010, 45, 106–113 CrossRef CAS PubMed.
- M. A. Migahed, E. G. Zaki and M. M. Shaban, RSC Adv., 2016, 6, 71384–71396 RSC.
- M. Mobin and M. Rizvi, Carbohydr. Polym., 2017, 160, 172–183 CrossRef CAS.
- H.-Y. Wei, B. Heidarshenas, L.-S. Zhou, G. Hussain, Q. Li and K. Ostrikov, Mater. Today Sustain., 2020, 10, 100044 CrossRef.
- S. Satpati, A. Suhasaria, S. Ghosal, A. Saha, S. Dey and D. Sukul, J. Mol. Liq., 2021, 324, 115077 CrossRef CAS.
- A. Fitoz, H. Nazır, M. Özgür, E. Emregül and K. C. Emregül, Corros. Sci., 2018, 133, 451–464 CrossRef CAS.
- G. Bahlakeh, B. Ramezanzadeh, A. Dehghani and M. Ramezanzadeh, J. Mol. Liq., 2019, 283, 174–195 CrossRef CAS.
- F. Bentiss, M. Traisnel and M. Lagrenee, Corros. Sci., 2000, 42, 127–146 CrossRef CAS.
- D. K. Yadav, D. S. Chauhan, I. Ahamad and M. A. Quraishi, RSC Adv., 2013, 3, 632–646 RSC.
- M. Bouanis, M. Tourabi, A. Nyassi, A. Zarrouk, C. Jama and F. Bentiss, Appl. Surf. Sci., 2016, 389, 952–966 CrossRef CAS.
- G. Bahlakeh, B. Ramezanzadeh, A. Dehghani and M. Ramezanzadeh, J. Mol. Liq., 2019, 283, 174–195 CrossRef CAS.
- A. Yurt, S. Ulutas and H. Dal, Appl. Surf. Sci., 2006, 253, 919–925 CrossRef CAS.
- A. Döner and G. Kardas, Corros. Sci., 2011, 53, 4223–4232 CrossRef.
- M. Ouakki, M. Galai, M. Rbaa, A. S. Abousalem, B. Lakhrissi, M. E. Touhami and M. Cherkaoui, J. Mol. Liq., 2020, 319, 114063 CrossRef CAS.
- A. S. Fouda, M. A. Ismail, A. M. Temraza and A. S. Abousalem, New J. Chem., 2019, 43, 768–789 RSC.
- Y. Hua, S.-S. Xu, Y. Wang, W. Taleb, J.-B. Sun, L. Zhang, R. Barkera and A. Neville, Corros. Sci., 2019, 157, 392–405 CrossRef CAS.
- I. T. Gawali and G. A. Usmani, J. Dispersion Sci. Technol., 2020, 41, 450–460 CrossRef CAS.
- D. Bajpal and V. K. Tyagi, J. Oleo Sci., 2006, 55, 319–329 CrossRef.
- A. Zarrouk, H. Zarrok, Y. Ramli, M. Bouachrine, B. Hammouti, A. Sahibed and F. Bentiss, J. Mol. Liq., 2016, 222, 239–252 CrossRef CAS.
- L.-R. Ma, W.-Q. Lu, D. Yang, J.-J. Shen, Z.-S. Gao, S.-Y. Zhang and Q.-Q. Liao, Sustainable Chem. Pharm., 2021, 22, 100488 CrossRef CAS.
- C. Vermal, E. E. Ebenso, M. A. Quraishil and C. M. Hussain, Mater. Adv., 2021, 2, 3806–3850 RSC.
- R. O. Medupin, K. Ukoba, K. O. Yoro and T. C. Jen, Mater. Today Sustain., 2023, 5, 100373 CrossRef.
|
This journal is © The Royal Society of Chemistry 2023 |
Click here to see how this site uses Cookies. View our privacy policy here.