DOI:
10.1039/D3RA00024A
(Paper)
RSC Adv., 2023,
13, 5859-5868
Ultrasonic spray pyrolysis synthesis of TiO2/Al2O3 microspheres with enhanced removal efficiency towards toxic industrial dyes
Received
2nd January 2023
, Accepted 3rd February 2023
First published on 16th February 2023
Abstract
Developing low-cost and highly effective adsorbent materials to decolorate wastewater is still challenging in the industry. In this study, TiO2-modified Al2O3 microspheres with different TiO2 contents were produced by spray pyrolysis, which is rapid and easy to scale up. Results reveal that the modification of γ-Al2O3 with TiO2 reduced the crystallite size of Al2O3 and generated more active sites in the composite sample. The as-synthesized Al2O3–TiO2 microspheres were applied to remove anionic methyl orange (MO) and cationic rhodamine B (RB) dyes in an aqueous solution using batch and continuous flow column sorption processes. Results show that the Al2O3 microspheres modified with 15 wt% of TiO2 exhibited the maximum adsorbing capacity of ∼41.15 mg g−1 and ∼32.28 mg g−1 for MO and RB, respectively, exceeding the bare γ-Al2O3 and TiO2. The impact of environmental complexities on the material's reactivity for the organic pollutants was further delineated by adjusting the pH and adding coexisting ions. At pH ∼5.5, the TiO2/Al2O3 microspheres showed higher sorption selectivity towards MO. In the continuous flow column removal, the TiO2/Al2O3 microspheres achieved sorption capacities of ∼31 mg g−1 and ∼19 mg g−1 until the breakthrough point for MO and RB, respectively. The findings reveal that TiO2-modified Al2O3 microspheres were rapidly prepared by spray pyrolysis, and they effectively treated organic dyes in water in batch and continuous flow removal processes.
1. Introduction
Organic dyes are widely used for many applications, for example, in coatings, paper making, leather tanning, food, textiles, and agriculture.1,2 However, the anthropogenic addition of these contaminants in the water now poses a significant concern because of their severe health impacts as they are proven carcinogens.3–5 This imposes a crucial need to develop new, rapid, and advanced remediation approaches capable of removing organic contaminants to provide drinkable water to people. Several physical, chemical, and biological techniques, such as adsorption, absorption, membrane separation, flocculation and coagulation, and electrochemical and catalysis, have been applied recently for the destruction and removal of organic contaminants before their release in wastewater.4,6–8 Among them, adsorption, an eco-friendly and efficient method, showed a promising route to handle various environmental contaminants.9,10 Nonetheless, eliminating organic dyes from industrial water is still challenging due to possible by-product formation.11,12 Therefore, designing new and efficient adsorbent materials to remove organic dyes is highly desirable.
Recently, various adsorbents, including metal oxides, activated carbon, biochar, metal–organic frameworks, etc., have been applied to treat organic dyes in water.11,13–15 Among them, metal oxides are the most commonly utilized materials to remove contaminants as they are cheap and widely manufactured. Besides, metal oxides exhibit good mechanical properties and resistance to thermal decomposition compared to others.16 Out of these, alumina oxide adsorbents, such as α-Al2O3, γ-Al2O3, and γ-AlOOH in various forms, which show eco-friendly nature, cost-effective, are easily synthesized.11,16–20 Hydrolysis and precipitation are easy, simple, and cost-effective routes for preparing these nanoparticles and their composites. The physicochemical properties of produced materials can be influenced by solvent, concentration, and temperature. Though alumina oxide adsorbents have been commonly used as adsorbent materials, the removal efficiency of these materials toward organic dyes is still not high owing to their low surface area and pore volume.19,21 To avoid these problems, there have been many studies on the modification of alumina to improve their physicochemical properties, enhancing adsorption. For instance, Ibrahim et al. prepared a Cr2O3–Al2O3 composite and found that the material exhibited improved adsorption ability toward Congo red dye.22 Recently, Barakat et al. developed an Al2O3/GO/halloysite nanotube composite with improved removal efficiency toward methylene blue and congo red dyes from wastewater. Singh et al. synthesized an Al2O3/GO cellulose-based 3D-hydrogel that showed enhanced adsorption ability compared to the bare Al2O3.23 Ding et al. prepared an Al2O3–TiO2 nanocomposite with enhanced adsorption performance to uranium from an aqueous solution.19 Despite many efforts, research on tailoring alumina oxide structures to improve their physicochemical properties and porosity is still limited.
Developing a highly efficient, cost-effective, and eco-friendly method for material preparation is also a critical issue, particularly when considering applying the material in the industry. So far, most materials have been prepared using batch mode synthesis, which usually requires a very long holding time and is challenging to scale.24–26 Recently, research has shown that spray pyrolysis has a high potential and advantage for preparing metal oxides as it is versatile, rapid, and scalable.27–31 The spray pyrolysis process includes four main steps: (i) generation of droplets from precursor solution, (ii) shrinkage of droplets, (iii) conversion of precursors to metal oxides, and (iv) solid particle formation.27,32 In addition, our previous work indicated that γ-Al2O3 microspheres prepared by spray pyrolysis exhibited considerably improved surface area and pore volume compared to that derived by the conventional precipitation method.24,33
Herein, various contents of TiO2 were in situ incorporated into γ-Al2O3 via the spry pyrolysis of boehmite sol and titania sol mixture, producing mesoporous Al2O3–TiO2 microspheres. It was realized that introducing TiO2 into γ-Al2O3 created synergetic effects that reduced the alumina's crystallite size and made more mesoporous structures as well as new active sites. The prepared TiO2/Al2O3 microspheres were first used as adsorbents to remove anionic methyl orange and cationic rhodamine B from water in the batch adsorption process. Then, the impact of environmental conditions, including concentration, pH, and coexisting ions, was systematically studied to optimize the removal efficiency. Finally, TiO2/Al2O3 microspheres were further tested for the continuous flow column adsorption of dyes to confirm the applicability of spray pyrolysis-derived TiO2/Al2O3 microspheres.
2. Experimental
2.1. Synthesis of TiO2/Al2O3 microspheres
Multi-grams of mesoporous microspheres, Al2O3, TiO2, and TiO2/Al2O3, were rapidly prepared by spray pyrolysis approach according to our previous work.25 First, stable boehmite sol and titania sol (0.25 M) were prepared by hydrolysis of aluminium isopropoxide and titania isopropoxide precursors, respectively. For spray pyrolysis, the calculated volumes of these solutions were mixed under constant stirring conditions. To the mixture, citric acid (CA), being a surfactant, was added to enhance the surface area and pore volume of the produced materials. The sol mixture was then transferred into a nebulizer to produce fine sol droplets before entering into a quartz column heated at 650 °C utilizing an air flow (Scheme 1). The resulting product was collected and heated in the air for 2 h to eliminate carbonaceous materials. The obtained microspheres were named TiO2/Al2O3 #x, where x is the weight percentage of TiO2.
 |
| Scheme 1 The schematic diagram for the spray pyrolysis synthesis of TiO2/Al2O3 microspheres. | |
2.2. Characterization
Electron micrographs of the prepared materials were collected by field-emission scanning electron microscopy (FE-SEM; Leo-Supra 55, Carl Zeiss STM, Germany) and TEM (Talos F200X). The specific area, pore volume, and pore size distribution of the prepared catalysts were determined using N2 porosimetry (ASAP 2020, Micromeritics Instrument Co., USA) at 77 K. Before measurements, the samples were activated at 450 K for 8 h. The surface areas of the materials were calculated using the Brunauer–Emmett–Teller (BET) equation. The Barrett–Joyner–Halender (BJH) approach with cylindrical pore size was estimated from the Kelvin equation. X-ray diffraction patterns were obtained by powder X-ray diffractometer (PXRD; MAC-18XHF, Rigaku, Japan) using a Cu Kα radiation source (λ = 1.54 Å). Further, the functional groups of the materials were recorded using FT-IR spectroscopy (Tensor 27, Bruker, Germany). The zeta potential was measured using ZETASIZER Nano-ZS from Malvern Instruments.
Ammonia temperature-programmed desorption (NH3-TPD) measurements were conducted to explore the acidic properties of the materials. First, the samples were pretreated at 500 °C for 1.5 h under He flow to eliminate the adsorbed moisture from the microspheres, followed by cooling to 115 °C. Afterwards, the materials were ammonia-saturated in a stream of 60 cm3 NH3 for 1 h. Finally, physically adsorbed NH3 was desorbed using a He flow of 60 cm3 min−1 for 4 h, and temperature increased from 100 °C to 900 °C with a heating rate of 10 °C min−1.
2.3. Adsorption experiments
2.3.1. Batch adsorption. The adsorption ability of the produced materials was elucidated using anionic methyl orange and cationic rhodamine B as simulated pollutants. For each run, 15 mg of degassed adsorbent was introduced in a 50 mL dye solution at the desired concentration and pH value with constant stirring at ambient temperature. The pH of the solution was adjusted by adding NaOH (0.15 M) or HCl (0.15 M) solutions. At regular intervals, the solution was withdrawn and filtered, and the dye concentration in the filtrates was determined using UV-vis spectroscopy (Optizen POP, Mecasys, Korea). The adsorption capacity of adsorbents was calculated using eqn (1): |
 | (1) |
where C0 and Ce (mg L−1) represent the initial and equilibrium concentrations of the contaminant, respectively; V (L), m (g), and q (mg g−1) are the volume of the solution, the adsorbent's weight, and the adsorption capacity, respectively.
2.3.2. Continuous flow adsorption. The continuous flow tests were carried out utilizing a column setup. A buret (48.6 cm × 1.2 cm) was used as the column, filled sequentially with a sponge, quartz sand (18 g), sand-adsorbent mixture (10 g + 1.8 g of adsorbent), quartz sand (18 g), and sponge. The column was packed and sealed with a pressurized rubber cork from the top end. For each run, dye solution prepared with a concentration of 40 mg L−1 and pH of 5.5 was passed in the column at a flow rate of 0.5 mL min−1 using a peristaltic pump. Herein, the flow direction was kept upward to achieve homogeneous contact. The elute was collected regularly and analyzed for effluents' contents. For the blank experiment, a sand quartz column was used.
3. Results and discussion
3.1. Characterization
Fig. 1(a–f) show the SEM and TEM images of Al2O3, TiO2/Al2O3, and TiO2 samples derived by spray pyrolysis. All samples are uniform spherical particles with diameters ranging from 0.3–2.5 μm. EDS mapping analysis revealed the existence of Al, O, and Ti species, which were well dispersed through the microspheres [Fig. 1(g and h)]. The crystallography analysis of all materials was performed, and the results are presented in Fig. 2(a). As shown, the XRD pattern obtained for the bare alumina and titania implies the formation of γ-Al2O3 and TiO2 anatase, respectively. For the TiO2-modified Al2O3 samples, the XRD patterns of TiO2/Al2O3 #5 and TiO2/Al2O3 #15 samples show only peaks of γ-Al2O3 but no sign of TiO2. This could be because the newly formed TiO2 particles were finely incorporated within the γ-Al2O3 matrix during the spray pyrolysis or could exist in the amorphous phase and beyond the XRD detection. Nonetheless, the XRD pattern of TiO2/Al2O3 #25 exhibits the peaks of TiO2 anatase at 2θ ∼25.4°. This suggests that TiO2 might grow well and agglomerate onto the surface of γ-Al2O3 at such a high content. Furthermore, the peaks of Al2O3 were observed to shift slightly and were broader [see the inset Fig. 2(a)], suggesting the incorporated titania could increase lattice strain and reduce the particle size of alumina. Indeed, the particle size of γ-Al2O3 was estimated by applying the Scherrer formula, and obtained results are presented in Table 1. As shown, the bare γ-Al2O3 had a crystallite size of ca. ∼3.75 nm; meanwhile, the crystallite size of Al2O3 in the composite TiO2/Al2O3 #5 and TiO2/Al2O3 #15 was ca. ∼3.60 and ∼3.44 nm, respectively. However, loading higher TiO2 content, up to 25 wt%, did not affect the crystallite size of Al2O3.
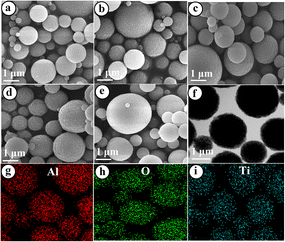 |
| Fig. 1 SEM images of the sample (a) Al2O3, (b) TiO2/Al2O3 #5, (c) TiO2/Al2O3 #15, (d) TiO2/Al2O3 #25, (e) TiO2; (f) TEM image of TiO2/Al2O3 #15 and EDS mapping analysis of (g) Al, (h) O, and (i) Ti of the TiO2/Al2O3 #15 sample. | |
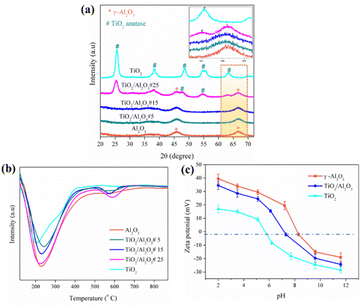 |
| Fig. 2 (a) XRD, (b) H3N-TPD profile, and (c) zeta potential measurements for the prepared samples. | |
Table 1 Crystallite size, surface area, and volume of the samples
Sample |
Mean crystallite size of Al2O3, nm |
BET surface area, m2 g−1 |
Total volume, cm3 g−1 |
Mean diameter, nm |
γ-Al2O3 |
3.75 |
320 |
0.31 |
3.28 |
TiO2/Al2O3 #5 |
3.60 |
298 |
0.29 |
3.81 |
TiO2/Al2O3 #15 |
3.44 |
265 |
0.27 |
4.14 |
TiO2/Al2O3 #25 |
3.77 |
175 |
0.25 |
4.45 |
TiO2 |
— |
124 |
0.18 |
5.34 |
The temperature-programmed desorption of NH3 was performed to evaluate the materials' content and types of acid sites. As demonstrated in Fig. 2(b), the TPD profile of the bare γ-Al2O3 and TiO2 exhibits a desorption peak of NH3 at a low temperature of ∼200 °C and 227 °C, respectively, which are ascribed to their weak acid sites. For the TiO2/Al2O3 composite, the TPD curve shows NH3 desorption peaks at approximately 230 °C and 578 °C, assigned to weak and strong acid sites, respectively. The results indicate that incorporating TiO2 into γ-Al2O3 generated more acid sites owing to the added Ti4+ sites or the newly formed bonds (e.g., –Al–O–Ti–) in the composite materials.24,34 Because of the electrostatic force, these acid sites would enhance the materials' adsorption ability toward anionic dyes. The acid density of the prepared materials was obtained by dividing total acid sites by surface area. Accordingly, the highest acid density of ca. ∼3.89 μmol m−2 was achieved for the synthesized TiO2/Al2O3 #15 sample. Moreover, the zeta potential and point of zero charges (pHPZC) of the spray pyrolysis-derived microspheres Al2O3, Al2O3–TiO2, and TiO2 were analyzed, and the obtained results are presented in Fig. 2(c). The bare γ-Al2O3 and TiO2 anatase had pHPZC values of ∼8.3 and 5.1, respectively. As can be seen that modifying γ-Al2O3 with TiO2 reduced the pHPZC value to ∼7.6, indicating the changes in surface chemistry of the Al2O3–TiO2 microspheres due to the incorporated TiO2 anatase.
N2 adsorption and pore size distributions of the fabricated adsorbents are presented in Fig. 3(a) and (b), respectively. As revealed in Fig. 3(a), the N2 adsorption curves of all samples are typical type IV curves with a hysteresis loop, suggesting capillary condensation in mesopores. Table 1 lists the calculated BET surface area and pore volume of the synthesized adsorbents. The bare γ-Al2O3 and TiO2 anatase microspheres had BET surfaces of ∼320 m2 g−1 and ∼124 m2 g−1, respectively. However, incorporating TiO2 into the alumina matrix decreased the surface area of the adsorbents. Specifically, the surface area of the composite fell from ∼298 to 175 m2 g−1 with increasing TiO2 content from 5 to 25 wt%, respectively. Noticeably, the modification of γ-Al2O3 with TiO2 by the spray pyrolysis method produced new mesopores and increased the mean pore diameters of the adsorbents, which are beneficial for capturing the organic contaminants.
 |
| Fig. 3 (a) N2 adsorption–desorption isotherm, (b) pore size distribution of the synthesized samples. | |
3.2. Batch adsorption experiments
The synthesized adsorbents were applied to remove the textile dyes, including methyl orange (MO) and rhodamine B (RB). Fig. 4(a–d) show the adsorption data (the discrete points) of contaminants as a function of contact time. As revealed, the adsorption of textile dyes reached equilibrium after approximately 6.5 h for both tested dyes. Furthermore, the results showed that modifying γ-Al2O3 with 5–15 wt% TiO2 increased the composites' adsorption compared to the bare oxide γ-Al2O3 and TiO2 titania despite decreased surface area. This is because adsorption depends on the porosity, adsorbent's particle size, and pore structures. As mentioned above, incorporating TiO2 generated new mesoporous forms favourable for the diffusion of the contaminants into the pore spaces from the bulk solution. In addition, loading TiO2 reduced the particle size of Al2O3, enhancing the contact area between the adsorbates and the adsorbent's active site and increasing the adsorption capacity. In addition, the TiO2-incorporated Al2O3 composites contained new adsorption sites, being proven through ammonia adsorption–desorption, which could also facilitate adsorbate–adsorbent interactions, enhancing the capture of these organic species. That is to say, introducing TiO2 anatase into the γ-Al2O3 host generated a synergistic effect that enhanced the adsorption of dyes onto the TiO2/Al2O3 microspheres. Nonetheless, increasing the TiO2 dopant content up to 25 wt% diminished the adsorption ability of the adsorbent owing to their significantly reduced porosity. Table 2 compares the removal of MO and RB over various adsorbents, showing that the spray pyrolysis-derived TiO2/Al2O3 microspheres exhibited high adsorption ability towards dyes compared to many counterparts.
 |
| Fig. 4 Pseudo-first order plots for (a) MO and (b) RB, and pseudo-second order (c) MO and (d) RB; intraparticle diffusion model for (e) MO and (f) RB (C0dye = 40 mg L−1, pH = 5.5). | |
Table 2 Removal of MO and RB over various adsorbents
Pollutant |
Adsorbent |
pH |
Adsorption capacity, mg g−1 |
Ref. |
MO |
de-Oiled soyga |
3.0 |
13.46 |
37 |
Natural skin almonds |
4.0 |
20.2 |
38 |
Orange peel |
>7 |
20.5 |
39 |
Hyper crosslinked polymeric adsorbent |
7 |
40 |
40 |
γ-Fe2O3/SiO2/chitosan composite |
— |
37 |
41 |
Spray pyrolysis-derived TiO2/Al2O3 microsphere |
5.5 |
41.15 |
This work |
RB |
Xanthium strumarium L. seed hull |
2 |
1.7 |
42 |
Microwave-activated rice husk ash |
5.5 |
21.89 |
43 |
Activated carbon from lignocellulosic waste |
7 |
33.3 |
44 |
Hyper crosslinked polymeric adsorbent |
7 |
58 |
40 |
Furfural residue |
3.0 |
37.93 |
45 |
Spray pyrolysis-derived TiO2/Al2O3 microsphere |
5.5 |
32.28 |
This work |
The adsorption behaviour of organic contaminants onto the produced adsorbents was uncovered by applying the nonlinear pseudo-first-order and pseudo-second-order models, as presented in Fig. 4(a–d) (the dash lines). The consistency between the experimental data and the models was evaluated via the average relative error (ARE), which is defined as follows:14
|
 | (2) |
where
qe,exp and
qe,cal are the experimental and estimated adsorbing amounts (mg g
−1), respectively.
The obtained fitted parameters are listed in Table 3. As shown, the higher value of the coefficient R2 and the lower value of ARE were obtained for the pseudo-second-order, suggesting that this kinetic model described the capture of dyes onto the adsorbents well. Accordingly, the rate constants obtained for the second-order model follow the order kMO > kRB, indicating that the adsorption rate of MO was faster than RB under the investigated conditions. The rate-limiting adsorption step was determined by applying the intraparticle diffusion (ID) model, which is expressed as follows:35,36
where
kID is the rate constant of the intraparticle diffusion model (mg g
−1 min
−1/2),
qt is the adsorbing amount (mg g
−1), and
C is a constant. As shown in
Fig. 4(e and f), these obtained ID plots included three separate linear portions, implying three diffusion stages during the adsorption process. The first stage is the external surface diffusion into macro-pores, in which the adsorbents enter into the less accessible spaces, so the diffusion resistance increases, and the diffusion rate decreases. The gradual adsorption step was the second stage, which was governed by intraparticle diffusion. The third stage was the final equilibrium stage, for which the molecules moved slowly from the larger pores to micropores, causing a slow adsorption rate. As shown in
Table 4, the diffusion rate gradually decreased (
k1 > k2 > k3), implying that the accessible path available for diffusion became narrower and the pores' dimensions diminished.
Table 3 Kinetic parameters obtained for MO and RB removal using the prepared adsorbents
Pollutant |
Adsorbent |
qe,exp. (mg g−1) |
Pseudo-first-order |
Pseudo-second-order |
qe,cal (mg g−1) |
k1 × 102 (min−1) |
ARE |
R2 |
qe,cal (mg g−1) |
k1 × 102 (g mg−1 min−1) |
ARE |
R2 |
MO |
Al2O3 |
33.81 ± 3.19 |
31.98 |
1.9 |
7.38 |
0.932 |
34.12 |
0.09 |
3.33 |
0.978 |
TiO2/Al2O3 #5 |
35.42 ± 3.67 |
34.04 |
2.7 |
7.27 |
0.944 |
36.0 |
0.12 |
1.21 |
0.996 |
TiO2/Al2O3 #15 |
41.15 ± 4.34 |
39.01 |
3.2 |
5.57 |
0.946 |
41.03 |
0.19 |
3.32 |
0.995 |
TiO2/Al2O3 #25 |
30.11 ± 2.78 |
29.18 |
1.47 |
4.42 |
0.961 |
31.19 |
0.07 |
2.12 |
0.989 |
TiO2 |
26.42 ± 2.15 |
24.4 |
1.09 |
4.75 |
0.960 |
27.08 |
0.05 |
2.25 |
0.985 |
RB |
Al2O3 |
24.52 ± 2.46 |
23.56 |
1.38 |
6.01 |
0.979 |
25.07 |
0.08 |
3.79 |
0.989 |
TiO2/Al2O3 #5 |
27.67 ± 2.81 |
25.89 |
2.21 |
4.89 |
0.977 |
28.11 |
0.09 |
2.28 |
0.995 |
TiO2/Al2O3 #15 |
32.28 ± 3.89 |
30.12 |
2.87 |
5.56 |
0.954 |
33.04 |
0.11 |
3.27 |
0.994 |
TiO2/Al2O3 #25 |
21.87 ± 2.75 |
19.59 |
1.29 |
4.17 |
0.968 |
22.34 |
0.05 |
3.26 |
0.986 |
TiO2 |
18.46 ± 2.04 |
16.97 |
0.83 |
3.98 |
0.978 |
19.29 |
0.03 |
2.91 |
0.998 |
Table 4 The parameters of the intraparticle diffusion model for the adsorption of MO and RB by the synthesized adsorbents
Pollutant |
Absorbent |
Stage I |
Stage II |
Stage III |
k1 (mg g−1 min−1/2) |
R2 |
k2 (mg g−1 min−1/2) |
R2 |
k3 (mg g−1 min−1/2) |
R2 |
MO |
Al2O3 |
2.36 |
0.978 |
0.31 |
0.967 |
0.08 |
0.991 |
TiO2/Al2O3 #5 |
2.94 |
0.965 |
0.39 |
0.959 |
0.10 |
0.973 |
TiO2/Al2O3 #15 |
3.39 |
0.985 |
0.42 |
0.968 |
0.05 |
0.968 |
TiO2/Al2O3 #25 |
2.17 |
0.974 |
0.47 |
0.987 |
0.10 |
0.971 |
TiO2 |
1.60 |
0.994 |
0.44 |
0.986 |
0.09 |
0.979 |
RB |
Al2O3 |
1.96 |
0.984 |
0.24 |
0.992 |
0.10 |
0.993 |
TiO2/Al2O3 #5 |
2.44 |
0.961 |
0.29 |
0.979 |
0.09 |
0.985 |
TiO2/Al2O3 #15 |
3.02 |
0.945 |
0.33 |
0.982 |
0.04 |
0.974 |
TiO2/Al2O3 #25 |
1.54 |
0.978 |
0.39 |
0.991 |
0.06 |
0.986 |
TiO2 |
0.91 |
0.994 |
0.45 |
0.998 |
0.05 |
0.997 |
3.3. Effects of internal factors
Effects of experimental conditions, including the initial concentration of dyes and pH, were investigated using the prepared TiO2/Al2O3 adsorbent. Fig. 5(a and b) show the maximum adsorption capacity of the simulated pollutants as a function of their initial concentrations. As revealed, the adsorbed amounts of textile dyes increased with their starting concentrations. This could be attributed to the enhanced contacting probability between the adsorbents and the adsorbates. In addition, it is noticed that the dye adsorption capacity slowly increased when increasing their initial concentration from 120 to 160 mg L−1, indicating the saturation of the adsorption sites. According to the results, the maximum adsorbed amounts of MO onto the prepared TiO2/Al2O3 #15 were ca. ∼29.5, 41.15, 47.87, 51.8, and 53.5 mg g−1 at concentrations of 20, 40, 80, 120, and 160 mg L−1, respectively; the maximum adsorbed amounts of RB by TiO2/Al2O3 #15 were ca. ∼19.7, 32.2, 40.7, 46.6, and 47.8 mg g−1 at concentrations of 20, 40, 80, 120, and 160 mg L−1, respectively.
 |
| Fig. 5 Effects of (a and b) initial concentration of dyes (pH = 5.5) and (c and d) pH on the adsorption of MO and RB over the TiO2/Al2O3 #15 adsorbent (C0dye = 40 mg L−1). | |
The adsorbent–adsorbate interaction could be changed by altering the solution pH, leading to a change in removal efficiency. Fig. 5(c and d) show the effects of pH on the adsorption of the investigated textile dyes onto the TiO2/Al2O3 microspheres. As shown, the adsorbing amount of MO decreased; meanwhile, the adsorbing amount of RB increased with an increase in pH, exhibiting pH sensitivity and dependent capture capacity of these molecules. In acidic media, the –OH groups on the surface of the TiO2/Al2O3 spheres were protonated by H+ ions to form –OH2+, giving a positively charged surface. Thus, this leads to restricting the approach of cationic RB dye owing to electrostatic repulsion. However, due to electrostatic attraction, the positively charged surface would increasingly attract more anionic MO molecules onto the adsorbent's exterior, enhancing adsorption. Conversely, in basic media, the TiO2/Al2O3 surface was deprotonated by OH− ions, producing a negatively charged surface favourable for the adsorption of cationic RB species. Besides electrostatic force, the interaction between TiO2/Al2O3 adsorbent materials and dye molecules might include hydrogen bonding.
3.4. Effects of coexisting ions
Industrial effluents usually contain many cations and anions, which would compete with textiles for the active adsorption sites onto the adsorbent. Thus, an efficient material should have a high selectivity toward the adsorbate. Herein, various coexisting anions with the same electric nature as MO, including Cl−, CO32−, HPO42−, F−, NO3−, CrO42−, and SO42− were selected for interference investigation at the designed concentration of 1.5 mmol L−1 and 5.0 mmol L−1, respectively. As demonstrated in Fig. 6, the adsorption efficiency of MO dye drops when the concentration of coexisting anions increases from 1.5 mmol L−1 to 5 mmol L−1. The presence of monovalent ions, such as F−, Cl−, and NO3−, did not affect the adsorption performance. Meanwhile, SO42− and CrO42− were observed to slightly impact the dye removal efficiency, suggesting that these ions would compete with methyl orange molecules for the adsorption sites of the adsorbent. This could be because these divalent ions have larger ionic diameters and higher ionic charge density than the above monovalent ions. Overall, the spray pyrolysis-derived TiO2/Al2O3 microspheres exhibited a good adsorption ability towards MO in water containing various coexisting anions.
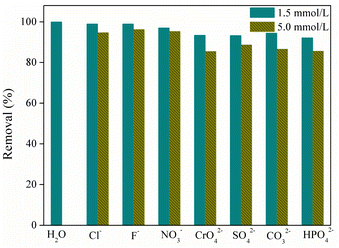 |
| Fig. 6 Effects of coexisting anions on MO adsorption (CMO0 = 40 mg L−1, pH = 5.5). | |
3.5. Simultaneous removal of dyes
Wastewater released from industry usually contains various textiles. Thus, evaluating the adsorbent's ability to remove multi-dyes in an aqueous solution is necessary. Here, the batch adsorption process was implemented using an equimolar solution of MO and RB (30 mg L−1, pH ∼ 5.5) utilizing the spray pyrolysis-derived TiO2/Al2O3 #15 microspheres. Fig. 7(a) shows the UV-vis spectrum of the solution, and Fig. 7(b) shows the FT-IR spectrum of TiO2/Al2O3 microspheres before and after the adsorption of textile dyes. Results reveal that the MO and RB were simultaneously removed over the TiO2-incorporated Al2O3 microspheres. After 6.5 h, the UV adsorption intensity of MO (λmax = 463 nm) was significantly reduced by approximately 87%, while that of RB (λmax = 554 nm) exhibited a decrease of roughly 32%. The findings suggested that the adsorbent preferentially adsorbed MO much more than the latter contaminant. This can be explained by the fact that MO, an anionic dye, was quickly adsorbed on the positively charged surface of TiO2/Al2O3 owing to the electrostatic attraction force. Moreover, the newly generated acid sites (e.g., Ti4+) of the composite could also contribute to the enhanced capture of anionic dyes.
 |
| Fig. 7 (a) UV-vis spectrum of the MO-RB solution and (b) FT-IR analyses of the TiO2/Al2O3 adsorbent before and after adsorption; (c) proposed competitive adsorption between MO and RB on the TiO2/Al2O3 microsphere (C0dye = 30 mg L−1, pH = 5.5). | |
Conversely, RB, a cationic dye, would not be favourable for adsorption onto the adsorbent because of the electrostatic repulsive force. Besides, the different adsorption behaviour of MO and RB onto the TiO2-incorporated Al2O3 microsphere could be attributed to their differences in chemical structures and molecular sizes. Indeed, pore/size-selective adsorption, monitored by the adsorbate molecule magnitude and adsorbent dimensions, is reportedly an effective adsorption mechanism.14,46 Herein, methyl orange has a molecular size of ∼1.2 nm, which is smaller than RB (∼1.8 nm).47 Therefore, MO is more likely to access the pores to occupy the adsorption sites of TiO2/Al2O3 microspheres, leading to the adsorption selectivity of the produced adsorbent. The proposed mechanism for the simultaneous adsorption of MO and RB onto the synthesized TiO2/Al2O3 microspheres is described in Fig. 7(c).
3.6. Contaminant removal in a continuous flow
The applicability of the produced TiO2/Al2O3 microspheres was further tested using continuous flow column setups, as illustrated in Fig. 8(a and b). As shown, the pollutants quickly passed through the column when using the blank sand bed column. For the column packed with sand and TiO2/Al2O3 mixture, the breakthrough point of the tested MO and RB is approximately ∼150 min and ∼120 min, respectively. The results indicated that the prepared TiO2/Al2O3 effectively removed pollutants in either batch or continuous mode. The obtained experimental data were then fitted with the Thomas and Yan models, which have been widely applied to the column behaviour of adsorbent–adsorbate systems:17,48 |
 | (4) |
|
 | (5) |
where t is the sampling time (in min), AY and KTh are the constants of the Yan and Thomas models, respectively; QY and QTh (mg g−1) are the adsorbing capacities estimated by the Yan and Thomas models, respectively. The experimental data were fitted to eqn (4) and (5) via nonlinear least square fitting. The mathematical modelling of the textile dye adsorption on the spray pyrolysis-derived TiO2/Al2O3 adsorbents is presented in Fig. 8(c and d) and Table 5. It can be seen that the high R2 values and low SSE values were achieved for both models, and the estimated QY and QTh values are very close to the experimental values. These results suggest that the applied models describe well the adsorption behaviour of both contaminants on the mesoporous TiO2/Al2O3 microspheres. The results in Table 5 show that the modelled sorption capacities of ∼31 mg g−1 and ∼19 mg g−1 for MO and RB, respectively. This states that it needs 1.0 g of TiO2/Al2O3 microspheres to purify approximately 31 L and 19 L of drinking water contaminated with 1 mg L−1 of textile dyes, respectively, in a continuous flow process.
 |
| Fig. 8 (a) Schematic diagram for the continuous flow column adsorption using TiO2/Al2O3 microspheres, (b) breakthrough curve results of MO and RB, and (c and d) Thomas and Yan models of the adsorption of dyes. | |
Table 5 Parameters obtained for the column transport models using TiO2/Al2O3 #15 adsorbent
Pollutant |
Thomas model |
Yuan model |
QTh, mg g−1 |
R2 |
SSE |
QY, mg g−1 |
R2 |
SSE |
MO |
30.79 |
0.998 |
0.041 |
30.77 |
0.998 |
0.052 |
RB |
19.14 |
0.997 |
0.062 |
19.11 |
0.996 |
0.073 |
4. Conclusions
This study shows that TiO2-incorporated Al2O3 microspheres were rapidly and effectively synthesized by combining sol–gel and spray pyrolysis approaches. The prepared TiO2/Al2O3 microspheres are uniform spherical particles with diameters ranging from 0.5–2.5 μm. With increasing TiO2 content from 5 to 25 wt%, the surface area reduced from 298 m2 g−1 to 175 m2 g−1, while the mean pore diameter increased from 3.81 to 4.45 nm, respectively. Furthermore, loading low TiO2 contents (5–15 wt%) reduced the crystallite size of the Al2O3 host. Dye adsorption in batch modes shows that loading 5 to 15 wt% TiO2 content enhanced the adsorption ability of the adsorbent compared to the bare metal oxides because of the reduced particle size of Al2O3, newly formed pore structures, and active sites. Furthermore, introducing TiO2 into Al2O3 created more active sites, enhancing the adsorption performance. The pH media significantly impacted the adsorption performance of TiO2/Al2O3 microspheres; meanwhile, adding the coexisting anions with a concentration range of 1.5–5.0 mmol L−1 caused insignificant effects. Notably, TiO2/Al2O3 microspheres showed a higher adsorption selectivity towards anionic MO than cationic RB dye in acidic media. The dye adsorption in continuous flow column processes indicates that the adsorption of MO and RB onto the TiO2/Al2O3 microspheres was described well by the Thomas and Yan models, and the adsorbing capacity of MO and RB was ∼31 mg g−1 and ∼19 mg g−1, respectively. The findings suggest that the TiO2/Al2O3 microspheres can be promising adsorption materials for treating organic pollutants in water.
Conflicts of interest
There are no conflicts to declare.
Acknowledgements
The authors also thank Professor Jinsoo Kim at the Chemical Engineering Department, Kyung Hee University, Korea, for sample analysis. The authors also thank you for the financial support from the Industrial University of Ho Chi Minh City and Ho Chi Minh City University of Food Industry.
References
- M. Madkour and F. Al Sagheer, Opt. Mater. Express, 2017, 7, 158–169 CrossRef CAS.
- R. Nivedhitha and S. Velmurugan, Int. J. Chem. Pharm. Sci., 2015, 6, 18–21 CAS.
- R. Koutavarapu, M. R. Tamtam, M. Rao, S. G. Peera and J. Shim, Chemosphere, 2021, 272, 129849 CrossRef CAS PubMed.
- J. Wang, Q. Zhang, X. Shao, J. Ma and G. Tian, Chemosphere, 2018, 207, 377–384 CrossRef CAS PubMed.
- T. K. Vo and J. Kim, Korean J. Chem. Eng., 2020, 37, 571–575 CrossRef CAS.
- T. K. Vo, J.-H. Kim, H. T. Kwon and J. Kim, J. Ind. Eng. Chem., 2019, 80, 345–351 CrossRef CAS.
- H. A. L. Pham, T. K. Vo, D. T. Nguyen, H. K. Huynh, Q. T. S. Pham and V. C. Nguyen, Green Chem. Lett. Rev., 2022, 15, 572–581 CrossRef CAS.
- T. K. Vo, M. T. Nguyen, V. C. Nguyen and J. Kim, Korean J. Chem. Eng., 2022, 39, 2532–2541 CrossRef CAS.
- X. You, R. Zhou, Y. Zhu, D. Bu and D. Cheng, J. Hazard. Mater., 2022, 430, 128445 CrossRef CAS PubMed.
- M. E. El-Naggar, E. K. Radwan, H. R. M. Rashdan, S. T. El-Wakeel, A. A. Koryam and A. Sabt, RSC Adv., 2022, 12, 18923–18935 RSC.
- S. Ali, Y. Abbas, Z. Zuhra and I. S. Butler, Nanoscale Adv., 2019, 1, 213–218 RSC.
- C. N. Britos, J. E. Gianolini, H. Portillo and J. A. Trelles, Biocatal. Agric. Biotechnol., 2018, 14, 221–227 CrossRef.
- B. Qiu, Q. Shao, J. Shi, C. Yang and H. Chu, Sep. Purif. Technol., 2022, 300, 121925 CrossRef CAS.
- T. K. Vo, T. P. Trinh, V. C. Nguyen and J. Kim, J. Ind. Eng. Chem., 2021, 95, 224–234 CrossRef CAS.
- K. Maru, S. Kalla and R. Jangir, New J. Chem., 2022, 46, 3054–3072 RSC.
- J. S. Yamani, A. W. Lounsbury and J. B. Zimmerman, Water Res., 2014, 50, 373–381 CrossRef CAS PubMed.
- N. Khandelwal, E. Tiwari, N. Singh and G. K. Darbha, ACS ES&T Water, 2021, 1, 641–652 Search PubMed.
- F. Ezati, E. Sepehr and F. Ahmadi, Sci. Rep., 2021, 11, 18831 CrossRef CAS PubMed.
- L. Ding, T. Xiong, Z. Zhao, J. Liao and Y. Zhang, J. Mol. Liq., 2022, 362, 119731 CrossRef CAS.
- V. The Ky, Int. J. Environ. Anal. Chem., 2022, 1–21, DOI:10.1080/03067319.2021.2023512.
- W. Zhang, S. Zhang, J. Wang, M. Wang, Q. He, J. Song, H. Wang and J. Zhou, Chemosphere, 2018, 203, 188–198 CrossRef CAS PubMed.
- M. M. Ibrahim, J. Environ. Chem. Eng., 2019, 7, 102848 CrossRef CAS.
- N. Singh, S. Kumari, N. Goyal and S. Khan, Environ. Nanotechnol., Monit. Manage., 2021, 15, 100444 CAS.
- T. K. Vo, W.-S. Kim, S.-S. Kim, K. S. Yoo and J. Kim, Energy Convers. Manage., 2018, 158, 92–102 CrossRef CAS.
- T. K. Vo, V. N. Le, D. T. Quang and J. Kim, Microporous Mesoporous Mater., 2021, 321, 111132 CrossRef CAS.
- T. K. Vo, J. Kim, T. H. Vu, V. C. Nguyen and D. T. Quang, Sep. Purif. Technol., 2022, 283, 120237 CrossRef CAS.
- S. C. Tsai, Y. L. Song, C. S. Tsai, C. C. Yang, W. Y. Chiu and H. M. Lin, J. Mater. Sci., 2004, 39, 3647–3657 CrossRef CAS.
- L. D. Hafshejani, S. Tangsir, H. Koponen, J. Riikonen, T. Karhunen, U. Tapper, V.-P. Lehto, H. Moazed, A. A. Naseri, A. Hooshmand, J. Jokiniemi, A. Bhatnagar and A. Lähde, Powder Technol., 2016, 298, 42–49 CrossRef CAS.
- A. I. Y. Tok, F. Y. C. Boey and X. L. Zhao, J. Mater. Process. Technol., 2006, 178, 270–273 CrossRef CAS.
- T. K. Vo, Environ. Sci. Pollut. Res., 2022, 29, 42991–43003 CrossRef CAS PubMed.
- J. Choi, K. S. Yoo and J. Kim, Korean J. Chem. Eng., 2018, 35, 2480–2486 CrossRef CAS.
- J. S. Cho, K. Y. Jung and Y. C. Kang, Phys. Chem. Chem. Phys., 2015, 17, 1325–1331 RSC.
- T. K. Vo, D. T. Quang and J. Kim, Catal. Commun., 2022, 169, 106478 CrossRef CAS.
- T. Rodseanglung, T. Ratana, M. Phongaksorn and S. Tungkamania, Energy Procedia, 2015, 79, 378–384 CrossRef CAS.
- C. Cheng, J. Deng, B. Lei, A. He, X. Zhang, L. Ma, S. Li and C. Zhao, J. Hazard. Mater., 2013, 263, 467–478 CrossRef CAS PubMed.
- J. Wang and X. Guo, Chemosphere, 2022, 309, 136732 CrossRef CAS PubMed.
- A. Mittal, A. Malviya, D. Kaur, J. Mittal and L. Kurup, J. Hazard. Mater., 2007, 148, 229–240 CrossRef CAS PubMed.
- F. Atmani, A. Bensmaili and A. Amrane, Desalin. Water Treat., 2010, 22, 174–181 CrossRef CAS.
- G. Annadurai, R.-S. Juang and D.-J. Lee, J. Hazard. Mater., 2002, 92, 263–274 CrossRef CAS PubMed.
- J.-H. Huang, K.-L. Huang, S.-Q. Liu, A. T. Wang and C. Yan, Colloids Surf., A, 2008, 330, 55–61 CrossRef CAS.
- H. Y. Zhu, R. Jiang, Y. Q. Fu, J. H. Jiang, L. Xiao and G. M. Zeng, Appl. Surf. Sci., 2011, 258, 1337–1344 CrossRef CAS.
- S. Khamparia and D. K. Jaspal, J. Environ. Manage., 2017, 197, 498–506 CrossRef CAS PubMed.
- N. V. Suc and D. Kim Chi, J. Dispersion Sci. Technol., 2017, 38, 216–222 CrossRef CAS.
- V. da Silva Lacerda, J. B. López-Sotelo, A. Correa-Guimarães, S. Hernández-Navarro, M. Sánchez-Báscones, L. M. Navas-Gracia, P. Martín-Ramos and J. Martín-Gil, J. Environ. Manage., 2015, 155, 67–76 CrossRef PubMed.
- X. Chen, H. Li, W. Liu, X. Zhang, Z. Wu, S. Bi, W. Zhang and H. Zhan, Colloids Surf., A, 2019, 583, 123976 CrossRef CAS.
- W. Xiong, G. Zeng, Z. Yang, Y. Zhou, C. Zhang, M. Cheng, Y. Liu, L. Hu, J. Wan, C. Zhou, R. Xu and X. Li, Sci. Total Environ., 2018, 627, 235–244 CrossRef CAS PubMed.
- Q.-y. Wu, H.-q. Liang, M. Li, B.-t. Liu and Z.-k. Xu, Chin. J. Polym. Sci., 2016, 34, 23–33 CrossRef CAS.
- T. K. Vo, V. N. Le, D. T. Quang, M. Song, D. Kim and J. Kim, Microporous Mesoporous Mater., 2020, 306, 110405 CrossRef CAS.
|
This journal is © The Royal Society of Chemistry 2023 |
Click here to see how this site uses Cookies. View our privacy policy here.