DOI:
10.1039/D2RA07527J
(Paper)
RSC Adv., 2023,
13, 4890-4897
Catalytic behavior of a ZnO/TiO2 composite in the synthesis of polycarbonate diol†
Received
26th November 2022
, Accepted 22nd December 2022
First published on 7th February 2023
Abstract
ZnO/TiO2 catalysts with different ZnO contents have been prepared through equal volume impregnation method, characterized by XRD, SEM, Py-IR, ICP, XPS, NH3-TPD and N2 adsorption/desorption, and evaluated in the synthesis of polycarbonate diol (PCDL) through transesterification. The results showed that titanium zinc oxide formed in these catalysts, and the content of acidic sites varied with the ZnO content, and ZnO/TiO2 (10%) has the highest acid amount. The ZnO/TiO2 (20%) with medium acidic sites showed the highest catalytic activity. The synthesis process of polycarbonate glycol was also optimized. Under the optimal reaction conditions, the yield of PCDL was 72.5%, and the Mn reached 4829 g mol−1 with a PDI of 1.6.
1. Introduction
Polycarbonate diol (PCDL) is an oligomer polyol with a regular molecular structure and a repeating carbonate group in the main chain.1 The carbonate group has the characteristics of large polarity and high cohesion energy, and it is easy to form intermolecular hydrogen bonds, so that PCDL has good mechanical properties, wear resistance and oil resistance. The small steric resistance of carbonate bonds also allows some molecular chain segments to rotate and vibrate, thus giving PCDL low temperature compliance.2 In recent years, the polycarbonate glycol (PCDL) market consumption has grown rapidly; the main downstream uses are in electronic appliances, plates and automobiles, the other main use is for blending with other polymers, such as the production of polyethylene terephthalate and polyether.3–6 In summary, PCDL has received widespread attention in the industry for its excellent performance.
The synthesis of PCDL by phosgene method is seriously polluting the environment, so it has been gradually eliminated.7,8 The non-phosgene method mainly includes cyclic carbonate open-ring copolymerization method, carbon dioxide epoxy copolymerization method and transesterification method.9 The cyclic carbonate open-loop copolymerization method has the problem of equilibrium between the cyclic reaction and the polymerization reaction.10,11 And the carbon dioxide epoxy copolymerization method can only synthesize PCDL with specific epoxide structure. Transesterification method normally catalysts use to be added in little amount only, mild reaction conditions, flexibility for preparing PCDLs with multiple structures, and controllability of relative molecular mass of the target products.12,13 Therefore, transesterification is considered to be a promising method of PCDL synthesis.
CH3COONa,13 tetrabutyl titanate(IV),14 Zn(OAc)2 (ref. 15) and (CH3COO)2Mg16 are commonly used as homogeneous catalysts in transesterification and exhibit excellent catalytic activity, but it is difficult to separate and regenerate from the products. In this context, the development of heterogeneous catalysts is desirable considering the demerits of homogeneous catalysts.17 Several heterogeneous catalysts have been reported in literature. For example, Wang et al.9 synthesized Mg–Fe/Ti layered double hydroxides (LDHs) for the transesterification between dimethyl carbonate (DMC) and aliphatic diols. Under optimal conditions with a catalyst amount of 1 wt%, the number-average molecular weight (Mn) of PCDL reached 3030 g mol−1, the yield of PCDL was 89.1%. Unfortunately, due to the formation of azeotrope between methanol and DMC during the reaction, it is difficult to control the Mn of the target product.18 In order to address these problems, the synthesis of PCDL using diphenyl carbonate (DPC) are disclosed.19 Therefore, the development of effective heterogeneous catalysts is of great significance for the synthesis of PCDL by transesterification of DPC with BDO.
TiO2 is commonly used as a heterogeneous support due to its high surface area and good availability.20–22 TiO2 loaded with metallic oxide, such as La,23 Pt,24 Pt–Ru Bi metal alloy,25 Fe and Cu,26 and Zn27–33 have been widely used in photocatalysis field. Chen et al.34 synthesized a catalyst of SO42− loaded on TiO2 for transesterification in the production of biodiesel. On the other hand, various catalysts has also been prepared based on ZnO for transesterification,35,36 because the rich oxygen vacancies on the surface of ZnO can enhance the Lewis acidity of the catalyst and improve the catalytic activity.37 However, it is not easy to recycle, because ZnO is difficult to be extracted from the product. In order to solve the drawback, we envisioned that loading ZnO on TiO2 would result in a recycled catalyst with high catalytic activity for the transesterification reaction.38 In this work, ZnO/TiO2 catalysts with different zinc mass fractions were prepared by equal volume impregnation, and the catalytic performance in the synthesis of PCDL via transesterification was evaluated. Furtherly, the transesterification process was also optimized.
2. Experimental
2.1 Materials
The chemical materials involved were obtained as follows: 1,4-butanediol (C4H19O2, CP), tetrabutyl titanate (C16H36O4Ti, AR), diphenyl carbonate (C13H10O3, CP) and dichloromethane (CH2Cl2, AR) were purchased from Shanghai Lingfeng Chemical Reagent Co., Ltd, ethanol (C2H6O, 95%) was purchased from Jiangsu Yongfeng Co., Ltd, zinc nitrate hexahydrate [Zn(NO3)2·6(H2O) AR], was purchased from Sinopharm Chemical Reagent Co., Ltd.
2.2 Preparation of catalysts
TiO2 was prepared by hydrolysis method.38,39 Mix 0.5 M tetrabutyl titanate with 7 M ethanol; mix 2 M deionized water with 7 M ethanol. In which the mixture of ionic water and ethanol was dripped into the mixture of tetrabutyl titanate and ethanol, constant stirring for about 1 hour and the mixture was aged at ambient temperature for 3 h. The precipitate was filtered out, dried, grounded into powder, and then calcined in a muffle furnace at 450 °C for 4 h to give TiO2.
The ZnO/TiO2 catalysts were prepared by an incipient wetness impregnation method. Taking the synthesis of 10% supported catalyst as an example, 0.005 M zinc nitrate hexahydrate dissolved in 0.2 M deionized water, and the aqueous solution of zinc nitrate hexahydrate slowly added dropwise to 0.05 M TiO2, and stirred at ambient temperature for 3 h. After being filtered, the residue was dried, grinded, and then roasted at 450 °C in muffle furnace for 4 h. The obtained catalyst was denoted as ZnO/TiO2 (20%). ZnO/TiO2 (10%), ZnO/TiO2 (30%) and ZnO/TiO2 (40%) were prepared via the similar method.
2.3 Catalyst characterizations
X-ray diffraction (XRD) of the materials were carried out on a D/max 2500 PC diffractometer (Rigaku Company, Japan). The test conditions were Cu Kα radiation (λ = 0.15406 nm), 40 kV, 150 mA, 2θ 5°–80° and step length 0.02°. N2 adsorption isotherms were measured on an ASAP2460 sorption analyzer (Micromeritics, Norcross, Georgia, USA). NH3-TPD tests were performed on a CHEMBET3000 chemical adsorption instrument (Quantachrome Company, USA). Scanning electron microscope (SEM) of the materials were carried out on SUPRA55 instrument (Zeiss Company, Japan). X-ray photoelectron spectroscopy (XPS) of the materials were carried out on K-Alpha instrument (Thermo Fisher Scientific Company, USA). Test conditions: the excitation source was Al-Kα (1486.8 eV), the background vacuum was 5.0 × 10−7 mBar, and the variable carbon C 1s = 284.80 eV was used as the standard for nuclear power correction. Electron-coupled plasma atomic emission spectrometry (ICP) of the materials were carried out on Vista-AX instrument (Varian Company, USA). FT-IR spectra after adsorption of pyridine (Py-IR) of the materials were carried out on Nicolet 9700 instrument (Thermo Fisher Scientific Company, USA).
2.4 Reaction procedure and catalyst performance evaluation
In a typical process, DPC (107.1 g, 0.5 mol), BDO (49.6 g, 0.55 mol) and ZnO/TiO2 (0.32 g, 0.3 wt%) catalyst were successively charged into a three-necked round-bottom flask, which was stirred and heated to melt under nitrogen protection. The total reaction time of synthesis PCDL is 6 h. Prepolymerization 3 h, polycondensation 3 h, in the polycondensation 3 h vacuum pumping to −0.095 MPa stop the reaction. The resulting mixture was dissolved in dichloromethane (2 equivalent) and the catalyst was filtered off for the next run, and PCDL product was precipitated upon adding excessive ethanol in the mixture.
The distillate was determined using a gas chromatograph (Agilent HP-5) fitted with a flame ionization detector (GC-FID). The column temperature was 120 °C and injection temperature was 320 °C.
The Mn and polydispersity index (PDI) were determined by gel permeation chromatography (GPC) at 40 °C in tetrahydrofuran. GPC analysis was carried out using a Shimadzu apparatus equipped with a LC-20AD HPLC pump, a refractive index detector (RID-10A, 120 V) and a Waters Styragel guard column (20 μm, 4.6 × 30 mm) followed by two Waters Styragel columns (HR 4E, 5 μm, mixed bed, 7.8 × 300 mm, and HR 5E, 5 μm, mixed bed, 7.8 × 300 mm). Tetrahydrofuran was used as eluent with a flow rate of 0.6 mL min−1 and calibrated with polystyrene standards (Mn = 1770, 17
300, 135
000 and 305
000 Da).
The product was dried in vacuum oven at 40 °C for 12 h and weighed. The yield was calculated by formula (1).
|
 | (1) |
Among them, m (g) is the actual mass of the PCDL product and mt (g) is the theoretical mass of the PCDL product.
3. Results and discussion
3.1 Catalyst characterization
As can be seen from Fig. 1, the catalysts with different ZnO mass fractions have characteristic diffraction peaks of anatase TiO2 at 2θ of 25.4°, 37.8°, 48.3°, 54.2° and 63.1°. It is shown that the structure of the carrier does not change after ZnO loading and roasting, and the characteristic diffraction peaks of ZnO appear at 2θ of 34.6°, 36.4° and 56.6°. From the XRD spectra, it can be seen that Zn4TiO6 formed in different loading catalysts. With the increase of the loading amount of ZnO, the peak for the composite oxide gradually becomes sharper.33,40
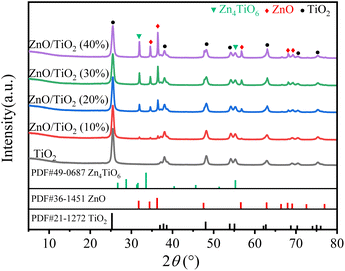 |
| Fig. 1 XRD of ZnO/TiO2 with different ZnO mass fractions. | |
The chemical environments of the titanium, oxygen and zinc were investigated by XPS (Fig. 2). Full-spectrum XPS (Fig. 2A) indicates the presence of Ti, Zn and O in the ZnO/TiO2. The spectrum for Ti 2p (Fig. 2B) contains two peaks: the first one at about 463.98 eV refers to the Ti 2p1/2, and the second one at about 458.28 eV corresponds to the Ti 2p3/2.41,42 XPS Zn 2p spectra (Fig. 2C) also show two peaks approximately at 1044.58 eV and 1021.48 eV, which are characteristics of Zn 2p1/2 and Zn 2p3/2, respectively,27,32,41 and the energy interval between the peaks is ∼23 eV. The above information confirms that Zn is completely oxidized and is in the +2-valence state.39 The XPS spectra indicate the presence of Ti4+ for titanium, Zn2+ for zinc28 on the surface of composites. It can be seen from Table 1 that the content of Zn on the catalyst surface increases slowly with the increase of ZnO loading. Among them, the surface Zn content increased the most when the ZnO loading increased from 10% to 20%. In addition, we investigated the O 1s XPS spectrum (Fig. 2D) of ZnO/TiO2. Results show that the peak positioned at 529.48 eV is due to the lattice oxygen anions (O2−) including Ti
O, Zn
O.43 The peak at 531.28 eV corresponds to loosely bound oxygen species, such as C–O, C
O, H2O, and OH groups.44,45 The results illustrated that the samples were composited of metal oxides, namely that of Ti and Zn.
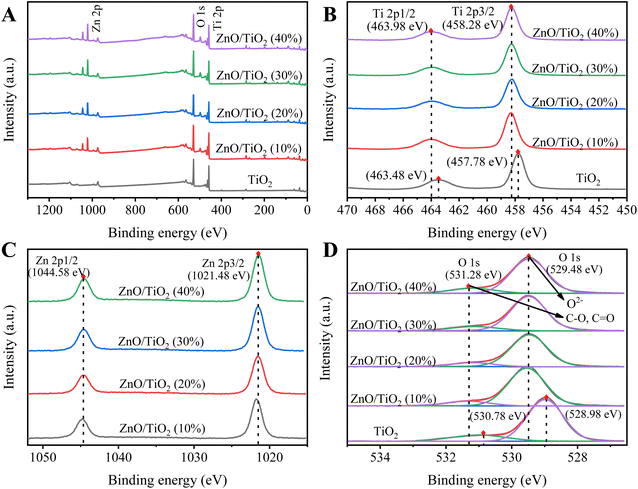 |
| Fig. 2 XPS spectra of ZnO/TiO2 with different ZnO mass fractions: (a) survey, (b) Ti 2p, (c) Zn 2p, and (d) O 1s. | |
Table 1 ZnO/TiO2 ICP, acid content and pore structure with different ZnO mass fractions
Catalyst |
w (Zn)/% |
Content of acidic site (mmol g−1) |
SBET (m2 g−1) |
Volume (cm3 g−1) |
Pore diameter (nm) |
Measured values of ICP |
Measured values of XPS |
Theoretical values |
TiO2 |
— |
— |
— |
0.38 |
87.23 |
0.17 |
10.03 |
ZnO/TiO2 (10%) |
7.31 |
10.81 |
8.03 |
0.71 |
54.65 |
0.13 |
9.86 |
ZnO/TiO2 (20%) |
15.10 |
12.77 |
16.05 |
0.51 |
42.74 |
0.10 |
9.46 |
ZnO/TiO2 (30%) |
22.73 |
13.65 |
24.08 |
0.50 |
39.26 |
0.10 |
8.83 |
ZnO/TiO2 (40%) |
29.82 |
14.16 |
32.10 |
0.42 |
36.32 |
0.09 |
8.53 |
Comparison between the binding energy of TiO2 and ZnO/TiO2, the binding energy of TiO2 increases significantly after loading ZnO, which demonstrates that positively charged Ti4+ and Zn2+ is enhanced. There is an interaction between titanium, zinc and oxygen on the catalyst, which leads to a deviation from the electron cloud of titanium and zinc.46 Based on the above analysis, the heterostructures were formed in ZnO/TiO2 composite due to that the well-defined morphology and intimate interfacial contact between TiO2 and ZnO, in consistent with the XRD pattern. The ICP analysis show that the measured content of ZnO is slightly lower than the theoretical value (Table 1), indicating that not all the Zn was successfully loaded into TiO2.
3.2 Analysis of surface acidity
NH3-TPD analysis of ZnO/TiO2 samples with different ZnO mass fractions and the Py-IR curve of ZnO/TiO2 (20%) are depicted in Fig. 3. As shown in Fig. 3A, the NH3-TPD study confirms that catalysts with different ZnO mass fractions have a weak acid site at 100 and 155 °C, and a moderately strong acidic site at 330 °C. Comparing different temperature ranges of desorption peaks, the area of desorption peak in the low temperature rang changes slightly, revealing that loading ZnO has little effect on the strength of the weak acid site; the area of desorption peak in the high temperature rang shows a decreasing trend with the increase of Zn loading, which is possibly due to the fact that part of the strong acid sites on the surface were covered by ZnO and further resulted in decreased strength of strong acid sites. NH3-TPD results confirm that the strength of strong acid sites on ZnO/TiO2 samples weakens with the increase of ZnO loading, which is consistent with the results of Giuseppe Marcì et al.31 The band at 1489 cm−1 is attributed to a mixture of Lewis and Brønsted acidic sites of pyridine adsorbed;47 the band at 1539 cm−1 is caused by the adsorption of pyridine on the Brønsted acidic site.48,49 The ratio of Brønsted to Lewis acidic site in ZnO/TiO2 (20%) catalyst is 0.3, suggesting that ZnO/TiO2 (20%) is a Lewis acid-based catalyst.
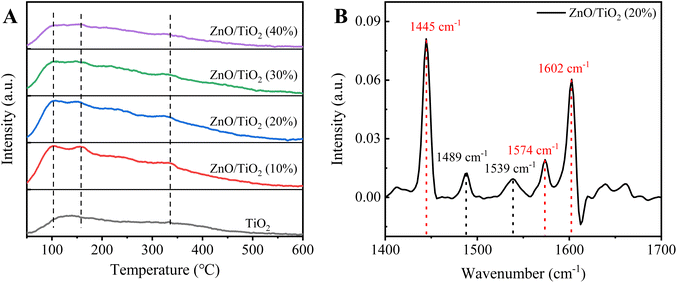 |
| Fig. 3 (A) ZnO/TiO2 NH3-TPD with different ZnO mass fractions (B) Py-IR of ZnO/TiO2 (20%). | |
As can be seen from Fig. 4A–E, when the mass fraction of ZnO is 10%, there are clear active component particles on the surface of the catalyst. With the increase of ZnO mass fraction, the agglomeration of particles of the surface-active components of the catalyst was obvious, and the ZnO/TiO2 (40%) catalyst was the most serious.
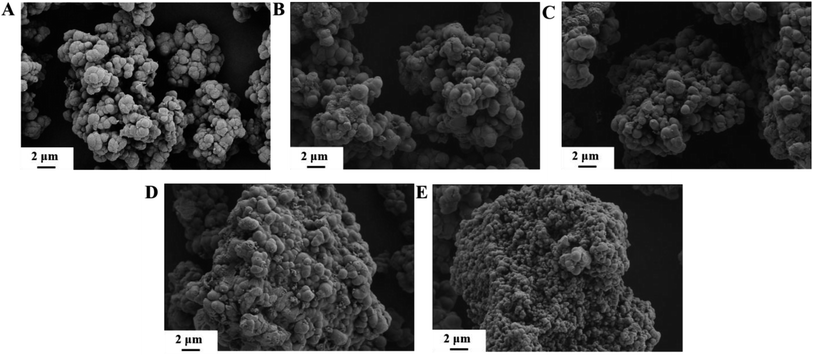 |
| Fig. 4 SEM of (A) 10%, (B) 20%, (C) 30%, (D) 40%, (E) 50% ZnO/TiO2. | |
It can be seen from Fig. 5 and Table 1 that with the increase of ZnO mass fraction, the specific surface area, pore volume and pore size of the catalyst are reduced, and the specific surface area decreases significantly, which is due to the continuous deposition of ZnO particles on the surface of the support, consistent with the results of SEM and NH3-TPD. From the N2 adsorption/desorption curves, it can be seen that the catalyst has a mesoporous structure, which can help the diffusion of raw materials and products on the surface of the catalyst, and change from single-layer adsorption to multi-layer adsorption with the rise of pressure.
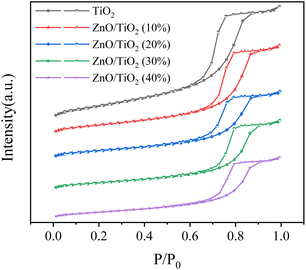 |
| Fig. 5 N2 adsorption/desorption curves of ZnO/TiO2 with different ZnO mass fractions. | |
3.3 Catalytic performance of ZnO/TiO2 on transesterification reaction
The catalytic activities of ZnO/TiO2 catalysts with different ZnO contents can be found in Fig. 6.
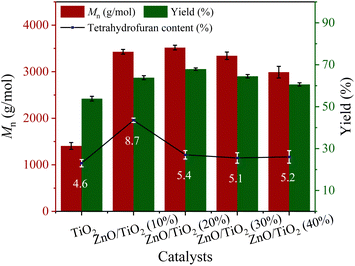 |
| Fig. 6 Effect of ZnO loading on catalyst performance (reaction conditions: DPC : BDO = 1 : 1.1; catalyst amount: 0.3 wt%; transesterification temperature: 200 °C). Data points were mean of triplicate experiments with the error bars showing standard deviations. | |
When using pure TiO2 as the catalyst, only a small amount of PCDL was detected and the Mn was only 1404 g mol−1. When the loading amount of ZnO is 10%, the yield and Mn are significantly improved. However, the content of by-product tetrahydrofuran was as high as 8.7% over 10% ZnO/TiO2. The results should be related to its largest amount of the surface acidic site, because acidic site can also promote the dehydration of BDO to form tetrahydrofuran.50 To our delight, ZnO/TiO2 (20%) catalyst with appropriate amount of acidic site gave the highest Mn value of PCDL and good yield. Further increasing the ZnO loading amount results in the gradually decease of yield and Mn. It can be seen from the SEM (Fig. 4) that ZnO agglomerates on the surface of TiO2 for ZnO/TiO2 (30%) catalyst, and part of the active center of TiO2 is covered by ZnO, and the synergy between Ti–O–Zn is weakened, so the yield and Mn decreases. Concerning on the PDI, the value changes slightly for all the catalysts except ZnO/TiO2 (10%). Titanium and zinc oxides are presumed to be active centers of Lewis acid. The carbonyl oxygen in DPC molecule interacts with the Lewis acid active site on ZnO/TiO2, leading to transfer of electron cloud to ZnO/TiO2 to form catalyst transition state.51,52 The reaction enhances the electrophilicity of carbonyl carbon in DPC molecule, and the carbonyl carbon in DPC molecule is more susceptible to the attack of nucleophilic species.48 Subsequently, C–O is broken, and the intermediate compound S-1 is generated. The intermediate compound S-1 then reacts under the action of Lewis acid active center of ZnO/TiO2 catalyst to produce PCDL and by-product phenol.1 The by-product phenol can formed with dimethyl carbonate into the raw material DPC, forming a “zero emission” green process (Scheme 1).53–55
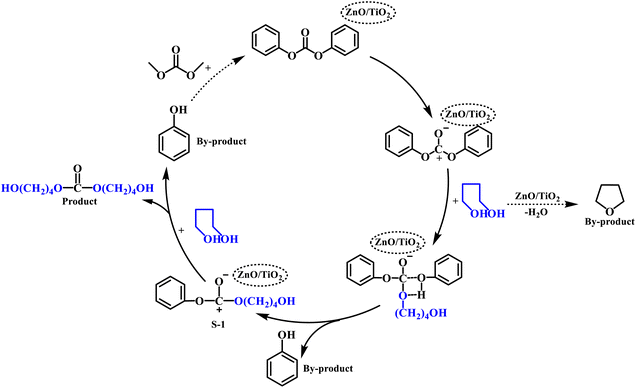 |
| Scheme 1 The possible reaction pathways. | |
3.4 Optimization of process conditions and reusability of catalyst
The ZnO/TiO2 (20%) catalyst was used to investigate the effect of reaction temperature on the transesterification process. When the transesterification reaction temperature is too low, the reaction rate is slow. And as the vacuum degree continues to increase, the oligomers are pumped away, resulting in low yield and Mn value; when the temperature is too high, the by-product phenol is easier to remove, which further increases the molecular chain of PCDL. However, the high temperature causes thermal degradation of PCDL, and the low molecular weight product is pumped away with the increasing vacuum, resulting in a significant decrease in yield. Therefore, the appropriate reaction temperature is 210 °C.
Alcohol excess is conducive to the reaction in a positive direction, the molecular weight distribution becomes smaller. On the other hand, excess alcohol also causes one or both ends of the product molecular chain to be blocked by ethyl, resulting in lower molecular weight4 (Fig. 7B). Therefore, the molar feeding ratio of the appropriate raw material is 1
:
1.1.
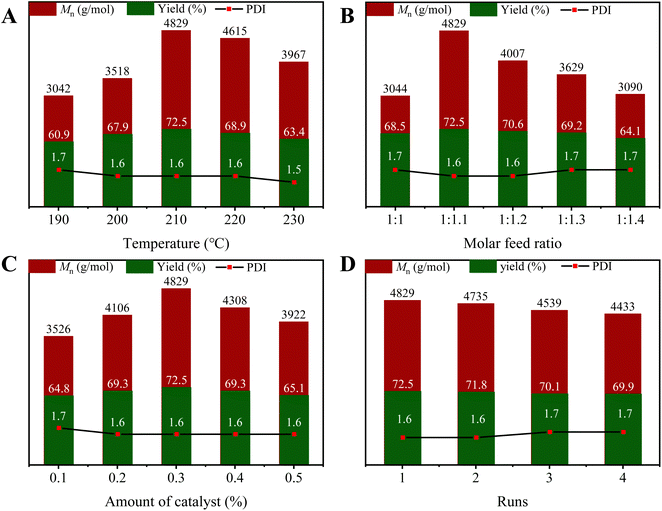 |
| Fig. 7 Effect of (A) transesterification temperature, (B) molar feed ratio and (C) catalyst amount on the Mn, yield and PDI of PCDL; (D) reusability of ZnO/TiO2 catalysts. | |
As depicted in Fig. 7C, the Mn gradually increases with increasing catalyst amount. And the maximum Mn of 4829 g mol−1 was reached when the catalyst amount was 0.3%. This is mainly because polycondensation rate is fast at a high catalyst amount. Additionally, the Mn of PCDL decreases from 4829 to 3922 g mol−1 with the increase of catalyst amount all the time. On the basis of these results, the most suitable catalyst amount was 0.3%. Song et al.13 reported the synthesis of PCDLs using CH3COONa as a homogeneous catalyst, with a number average molecular weight of 2800 g mol−1 and the yield of PCDL is 64.7% were achieved under the optimum reaction conditions. Feng et al.18 used calcined Mg Al hydrotalcites (HTc) as a solid base catalyst to synthesis PCDL, a high yield of PCDLs up to 95% was obtained, but the molecular weight is only about 1500 g mol−1. The Mn and yield of PCDL prepared by ZnO/TiO2 (20%) is higher than that of CH3COONa and Mg Al hydrotalcite. At the same time, the raw materials for the catalyst in this research is readily available, and the reaction process is simple, so the cost of preparing PCDL can be significantly reduced.
The used ZnO/TiO2 (20%) catalyst was recovered by centrifugation and washed three times with dichloromethane for the next use.17 It was found that the molecular weight of PCDL decreased slowly with the increase of reuse times. After the catalyst was reused four times, no obvious change of the yield of PCDL was observed. These results indicate that the catalyst has good stability in the synthesis of PCDL.
4. Conclusions
ZnO/TiO2 catalysts with different ZnO mass fractions were prepared by equal volume impregnation method, characterized and evaluated in the synthesis of polycarbonate diol via transesterification. The results showed that with the increase of ZnO mass fraction, the content of surface acidic site decrease, and ZnO/TiO2 catalyst was dominated by Lewis acidic sites. ZnO/TiO2 (20%) catalyst appropriate amount of acidic site showed the best catalytic performance. Furtherly, the transesterification process for the synthesis of PCDL was optimized, and the Mn reached 4829 g mol−1 with a yield of 72.5% under the optimized conditions. Compared with the reported metal catalysts for the synthesis of polycarbonate diol via transesterification, the ZnO/TiO2 (20%) catalyst is cheaper and easier in preparation.
Author contributions
Ran Chong: investigation, data curation, methodology, writing-original draft. Fei Qian: investigation, data curation. Zhong-Hua Sun: data curation, funding acquisition, writing-review & editing, conceptualization. Mei-Jun Wei: investigation, methodology. Wei-You Zhou: conceptualization, methodology. Ming-Yang He: supervision, validation. Qun Chen: supervision, conceptualization. Jun-Feng Qian: conceptualization, funding acquisition, writing-review & editing.
Conflicts of interest
The authors declare no conflict of interest.
Acknowledgements
We gratefully acknowledge the financial support from A Project Funded by the Priority Academic Program Development of Jiangsu Higher Education Institutions (PAPD) and Jiangsu Key Laboratory of Advanced Catalytic Materials and Technology (Grant BM2012110).
Notes and references
- L. Wang, J. He, X. Chen and Y. Lv, J. Iran. Chem. Soc., 2020, 17, 2335–2343 CrossRef CAS.
- H. Fang, H. Wang, J. Sun, H. Wei and Y. Ding, RSC Adv., 2016, 6, 13589–13599 RSC.
- K. Fukushima and K. Nozaki, Macromolecules, 2020, 53, 5018–5022 CrossRef CAS.
- X.-Q. Wang, H. Li, Q.-Y. Yuan, X.-Q. Liu and D.-H. Liu, Catal. Lett., 2020, 150, 3174–3183 CrossRef CAS.
- H.-I. Mao, C.-W. Chen, L.-Y. Guo and S.-P. Rwei, J. Appl. Polym. Sci., 2022, 139, e52986 CAS.
- W. Yu, E. Maynard, V. Chiaradia, M. C. Arno and A. P. Dove, Chem. Rev., 2021, 121, 10865–10907 CrossRef CAS PubMed.
- J. Sun and D. Kuckling, Polym. Chem., 2016, 7, 1642–1649 RSC.
- L. Wang, B. Xiao, G. Wang and J. Wu, Sci. China: Chem., 2011, 54, 1468–1473 CrossRef CAS.
- Y. Wang, L. Yang, X. Peng and Z. Jin, RSC Adv., 2017, 7, 35181–35190 RSC.
- M. Honda and H. Abe, Green Chem., 2018, 20, 4995–5006 RSC.
- S. Tempelaar, L. Mespouille, O. Coulembier, P. Dubois and A. P. Dove, Chem. Soc. Rev., 2013, 42, 1312–1336 RSC.
- L. Zhu, W. Xue and Z. Zeng, New J. Chem., 2018, 42, 15997–16004 RSC.
- M. Song, X. Yang and G. Wang, Chem. Res. Chin. Univ., 2018, 34, 578–583 CrossRef CAS.
- Z. Terzopoulou, E. Karakatsianopoulou, N. Kasmi, V. Tsanaktsis, N. Nikolaidis, M. Kostoglou, G. Z. Papageorgiou, D. A. Lambropoulou and D. N. Bikiaris, Polym. Chem., 2017, 8, 6895–6908 RSC.
- Z. Wang, X. Yang, S. Liu, J. Hu, H. Zhang and G. Wang, RSC Adv., 2015, 5, 87311–87319 RSC.
- Z. Wang, X. Yang, S. Liu, H. Zhang and G. Wang, Chem. Res. Chin. Univ., 2016, 32, 512–518 CrossRef CAS.
- M. Song, X. Yang and G. Wang, RSC Adv., 2018, 8, 35014–35022 RSC.
- Y. X. Feng, N. Yin, Q. F. Li, J. W. Wang, M. Q. Kang and X. K. Wang, Ind. Eng. Chem. Res., 2008, 47, 2140–2145 CrossRef CAS.
- Z. Wang, X. Yang, J. Li, S. Liu and G. Wang, J. Mol. Catal. A: Chem., 2016, 424, 77–84 CrossRef CAS.
- Y.-K. Yang, S.-W. Yoon, Y.-T. Hwang and B.-G. Song, Bull. Korean Chem. Soc., 2012, 33, 3445–3447 CrossRef CAS.
- K. Stępień, C. Miles, A. McClain, E. Wiśniewska, P. Sobolewski, J. Kohn, J. Puskas, H. D. Wagner and M. El Fray, ACS Sustainable Chem. Eng., 2019, 7, 10623–10632 CrossRef.
- Y. Liang, K. Su, L. Cao and Z. Li, Mol. Catal., 2019, 465, 16–23 CrossRef CAS.
- X. Chen, Y. Huang, Y. Li, H. Li, G. Fan, R. Zhang and X. Xu, Mater. Lett., 2021, 293, 129709–129713 CrossRef CAS.
- S. Yurdakal, Ş. Ö. Yanar, S. Çetinkaya, O. Alagöz, P. Yalçın and L. Özcan, Appl. Catal., B, 2017, 202, 500–508 CrossRef CAS.
- T. Zhang, S. Wang and F. Chen, J. Phys. Chem. C, 2016, 120, 9732–9739 CrossRef CAS.
- S. Ahadi, N. S. Moalej and S. Sheibani, Solid State Sci., 2019, 96, 105975–105985 CrossRef CAS.
- B. Bozkurt Çırak, B. Caglar, T. Kılınç, S. Morkoç Karadeniz, Y. Erdoğan, S. Kılıç, E. Kahveci, A. Ercan Ekinci and Ç. Çırak, Mater. Res. Bull., 2019, 109, 160–167 CrossRef.
- T. A. Dontsova, O. I. Yanushevska, S. V. Nahirniak, A. S. Kutuzova, G. V. Krymets, P. S. Smertenko and S. Ali, J. Chem., 2021, 2021, 1–11 CrossRef.
- J. Hou, Y. Wang, J. Zhou, Y. Lu, Y. Liu and X. Lv, Surf. Interfaces, 2021, 22, 100889–100896 CrossRef CAS.
- R. Madhuvilakku and S. Piraman, Bioresour. Technol., 2013, 150, 55–59 CrossRef CAS PubMed.
- G. Marcì, V. Augugliaro, M. J. López-Muñoz, C. Martín, L. Palmisano, V. Rives, M. Schiavello, R. J. D. Tilley and A. M. Venezia, J. Phys. Chem. B, 2001, 105, 1033–1040 CrossRef.
- M. Pérez-González and S. A. Tomás, Catal. Today, 2021, 360, 129–137 CrossRef.
- D. Tekin, H. Kiziltas and H. Ungan, J. Mol. Liq., 2020, 306, 112905–112911 CrossRef CAS.
- C. Chen, L. Cai, X. Shangguan, L. Li, Y. Hong and G. Wu, R. Soc. Open Sci., 2018, 5, 181331 CrossRef CAS PubMed.
- M. M. A. Soliman, A. Karmakar, E. C. B. A. Alegria, A. P. C. Ribeir, G. M. D. M. Rúbio, M. S. Saraiva, M. F. C. G. d. Silva and A. J. L. Pombeiro, Catal. Today, 2020, 348, 72–79 CrossRef CAS.
- L. Yang, Z. Yang, F. Zhang, L. Xie, Z. Luo and Q. Zheng, Polymers, 2018, 10, 796–815 CrossRef PubMed.
- S. Yu and H. Zhang, Catal. Lett., 2020, 150, 3359–3367 CrossRef CAS.
- J. Yang, C. Hu, Y. Jin, H. Chen, W. Zhu and X. Zhou, Res. Chem. Intermed., 2021, 47, 3453–3468 CrossRef.
- S. Ponnada, D. B. Gorle, M. S. Kiai, S. Rajagopal, R. K. Sharma and A. Nowduri, Adv. Mater., 2021, 2, 5986–5996 RSC.
- X. Zhao, C. Peng and J. You, J. Therm. Spray Technol., 2017, 26, 1301–1307 CrossRef CAS.
- A. Kutuzova, T. Dontsova and W. Kwapinski, J. Inorg. Organomet. Polym. Mater., 2020, 30, 3060–3072 CrossRef CAS.
- Y. Yu, J. Wang, W. Li, W. Zheng and Y. Cao, CrystEngComm, 2015, 17, 5074–5080 RSC.
- M. Zhu, X. Deng, X. Lin, L. Zhang, W. Zhang, Y. Lv and J. Pan, J. Mater., 2018, 29, 11449–11456 CAS.
- H.-T. Wang, Y.-P. Liu, H. Zhang, N. Chang, W. Shao, M.-S. Shi, D. Ao and M.-C. Lu, Microporous Mesoporous Mater., 2019, 288, 109548–109557 CrossRef CAS.
- Y. Wang, X. Liu, L. Guo, L. Shang, S. Ge, G. Song, N. Naik, Q. Shao, J. Lin and Z. Guo, J. Colloid Interface Sci., 2021, 599, 566–576 CrossRef CAS PubMed.
- F. Xiao, J. Mater. Chem., 2012, 22, 7819–7830 RSC.
- M. A. A. Aziz, K. Puad, S. Triwahyono, A. A. Jalil, M. S. Khayoon, A. E. Atabani, Z. Ramli, Z. A. Majid, D. Prasetyoko and D. Hartanto, Chem. Eng. J., 2017, 316, 882–892 CrossRef CAS.
- Y. Mao, J. Cheng, H. Guo, Y. Shao, L. Qian and W. Yang, Fuel, 2023, 331, 125795–125808 CrossRef CAS.
- W. Xiang, C. Shen, Z. Lu, S. Chen, X. Li, R. Zou, Y. Zhang and C.-j. Liu, Chem. Eng. Sci., 2021, 233, 116429–116440 CrossRef CAS.
- H. Li, H. Yin, T. Jiang, T. Hu, J. Wu and Y. Wada, Catal. Commun., 2006, 7, 778–782 CrossRef CAS.
- W. Shi, J. Zhao, X. Yuan, S. Wang, X. Wang and M. Huo, Chem. Eng. Technol., 2012, 35, 347–352 CrossRef CAS.
- H. Yang, Z. Xiao, Y. Qu, T. Chen, Y. Chen and G. Wang, Res. Chem. Intermed., 2017, 44, 799–812 CrossRef.
- Z. Xiao, H. Yang, H. Zhang, T. Chen and G. Wang, Chem. Pap., 2018, 72, 2347–2352 CrossRef CAS.
- J. Zhang, Y. Gao, J. Zhang, J. Zhao and H. Shen, Chem. Cent. J., 2018, 12, 104–112 CrossRef CAS PubMed.
- Y. Zhang, S. Wang, Z. Xiao, T. Chen and G. Wang, Res. Chem. Intermed., 2016, 42, 7213–7222 CrossRef CAS.
|
This journal is © The Royal Society of Chemistry 2023 |
Click here to see how this site uses Cookies. View our privacy policy here.